船舶结构材料防腐措施及相关标准
关于海洋工程结构与船舶防腐技术措施分析

关于海洋工程结构与船舶防腐技术措施分析海洋工程结构和船舶是在海洋环境中运行和工作的,因此防腐技术是非常重要的。
下面将对海洋工程结构和船舶防腐技术措施进行分析。
海洋工程结构包括钻井平台、海底管道、海上风力发电设施等。
由于它们长期在海洋环境中受到潮湿、盐分、温度变化和海水的腐蚀,而且海洋环境条件复杂,所以必须采取有效的防腐技术措施。
针对海洋工程结构的防腐技术主要有以下几种:1. 防腐涂层:采用防腐涂料对结构物进行涂覆,以阻隔结构物与海水的接触,减少结构物的腐蚀。
常见的防腐涂层材料有环氧树脂、聚氨酯、煤沥青等,这些涂层具有良好的耐腐蚀性能和耐海水侵蚀能力。
2. 金属防腐:采用金属的防腐技术,如热浸镀锌、热镀铝等,对结构物表面进行处理,增加金属表面对海水的抵抗能力。
金属防腐技术适用于钢结构和铁制结构,可以有效地延长结构物的使用寿命。
3. 材料选择:在海洋工程结构的设计和施工过程中,选择具有良好耐腐蚀性的材料,如不锈钢、合金材料等。
这些材料具有较强的耐腐蚀性能,能够有效地抵抗海水的侵蚀。
船舶作为在海洋中长时间运行的大型设备,也需要采取防腐技术措施来延长其使用寿命和保证航行安全。
船舶防腐技术主要包括以下几种:1. 防腐涂层:船舶在制造过程中常常使用防腐涂层对船体进行防腐处理。
防腐涂层可以有效隔绝海水和船体的接触,减少船体的腐蚀。
常见的船舶涂层包括船底防污涂料、船舶外壳涂料等。
2. 阳极保护:船舶使用金属阳极对船体进行保护。
阳极通常由锌或铝等金属材料制成,它们能够吸收腐蚀电流,从而减少船体的腐蚀。
阳极保护是一种被广泛应用于船舶的防腐技术。
3. 尽量避免海水侵蚀:船舶在停泊期间,特别是长时间停泊时,应该尽量避免船体与海水的接触,如使用船舶停泊设备,在船底加装船垫或使用船坞进行船体检修等措施。
海洋工程结构和船舶防腐技术措施非常重要。
通过采用适当的防腐技术措施,可以有效地保护海洋工程结构和船舶的表面,减少腐蚀损失,延长使用寿命,保证运行安全。
关于海洋工程结构与船舶防腐技术措施分析

关于海洋工程结构与船舶防腐技术措施分析海洋工程结构与船舶是不可避免的会遭受海洋环境侵蚀和破坏的,特别是在海洋气候恶劣、海水腐蚀性强的环境下,结构和船体的防腐技术措施显得尤为重要。
本文通过阐述海洋工程结构与船舶常见的主要腐蚀类型、腐蚀原因及其对应的防腐技术措施,旨在提高相关从事海洋工程与船舶防腐工作的技术人员的理论水平和实践能力。
一、海洋工程结构的腐蚀类型(1)普通腐蚀这是一种比较常见的海洋环境下的腐蚀类型,它主要是指金属物质与海水接触时发生的氧化反应。
普通腐蚀主要特点是腐蚀均匀,不易发现,但可能会在长时间内对设施造成不可逆的损害。
(2)点蚀腐蚀点蚀是一种表面腐蚀现象,由于金属表面的小区域发生了腐蚀而导致局部脱落。
点蚀所造成的海洋工程设施损害比较严重,因为这种腐蚀往往会在很短的时间内形成一个不稳定的局部区域,从而导致致命性的连锁反应,使腐蚀不断扩大。
(3)应力腐蚀开裂应力腐蚀开裂是海洋工程结构腐蚀的重要类型之一,发生的主要原因是金属表面存在一定的应力,使其在潮汐或海水运动的条件下发生腐蚀。
由于应力腐蚀开裂是一种相对较严重的腐蚀类型,因此对于劣质的金属材料以及制造不良的工程项目容易发生。
二、船舶的腐蚀类型船舶的腐蚀类型主要有以下几种:(1)海水生物附着海水生物附着是船舶上最常见的一种腐蚀类型,主要起源于海洋环境中的微生物,如藻类、贝类和海藻等。
这些生物附着的细胞会在船壳表面引起生长和聚集,对船壳表面的金属物质进行侵蚀和腐蚀,最终可能导致重大的结构损害。
流动腐蚀是船舶结构的另一种常见腐蚀类型,通常发生在船骨板连接处、轮廓线处等处。
这种腐蚀类型的发生主要依赖于海水中的流动,而流动越强的地方,则更容易受到腐蚀性的影响。
(3)电化学腐蚀电化学腐蚀是通过电化学反应而产生的腐蚀,这种腐蚀发生在未涂层的、散热器和金属管道等金属结构上。
由于船舶常常要依赖金属和金属合金来进行制造,因此电化学腐蚀的发生无法避免。
为了避免海洋工程结构和船舶受到海洋气候和海水腐蚀的侵蚀,防腐技术措施是非常必要的。
船舶腐蚀原因及防腐措施分析

船舶腐蚀原因及防腐措施分析船舶作为重要的海洋运输工具,承担着大量的货物和人员的运输任务。
随着船舶在海洋环境中长时间航行,船舶表面会受到各种腐蚀的影响,导致船舶结构的损坏和性能下降。
船舶腐蚀的原因及防腐措施成为了船舶运营管理中一个重要的课题。
本文将对船舶腐蚀的原因及防腐措施进行分析和探讨。
一、船舶腐蚀原因1. 海水腐蚀海水中所含的氯离子是造成船舶腐蚀的主要因素之一。
氯离子可以破坏金属结构表面的保护层,使金属暴露在海水中,进而发生腐蚀。
海水中的硫化物、硫酸盐和碱性物质等也会对船舶材料产生腐蚀作用。
2. 生物腐蚀海水中富含各种微生物和海洋生物,它们会附着在船舶船体表面,形成生物膜,并且分泌酸性物质,对船舶金属表面进行腐蚀。
特别是在热带海域,生物腐蚀更为严重。
3. 电化学腐蚀船舶在海水中航行时,由于船体结构的接触和相互作用,导致不同金属间产生电位差,形成电化学腐蚀。
这种腐蚀会使船舶金属材料出现电化学腐蚀反应,加速金属表面的腐蚀速度。
4. 氧化腐蚀船舶在海洋中航行时,受到海水中氧气的影响,金属表面会发生氧化腐蚀。
尤其是在高温和高湿度环境下,氧化腐蚀会更为严重。
二、船舶腐蚀防腐措施1. 材料选用船舶在设计和建造时,需要根据航行环境的不同选择适合的材料。
一般来说,航行在海洋中的船舶需要选择具有良好抗腐蚀性能的材料,如不锈钢、铝合金等,以提高船舶的抗腐蚀能力。
2. 防腐涂层船舶表面覆盖一层防腐涂层是常用的防腐措施之一。
防腐涂层可以形成一层保护膜,遮断金属与海水的直接接触,起到防腐蚀的作用。
防腐涂层还可以抵挡生物附着和污染物的侵蚀。
3. 保护电流防腐保护电流防腐是通过在船舶表面施加一定的电流,使金属处于一种电化学平衡状态,从而防止电化学腐蚀的方法。
这种方法可以延缓船舶的金属腐蚀速度,并且对船舶结构的保护效果比较好。
4. 防腐剂添加在船舶的冷却水、锅炉水和发动机润滑油中添加一定的防腐剂,可以防止相关设备的内部腐蚀,延长设备的使用寿命。
船体防腐方案

船体防腐方案一、背景介绍船体作为船舶的重要组成部分,承载着船舶的结构和性能。
随着船舶运输业的快速发展,船体防腐工作显得尤为重要。
本文旨在提出一种有效的船体防腐方案,以确保船舶的安全和耐用性。
二、船体防腐的重要性船体是船舶最核心的部分,直接承受着外部环境的恶劣因素,如海水、紫外线、海洋生物等。
没有有效的船体防腐措施,船体将容易受到腐蚀、磨损和氧化的影响,进而导致船舶结构破损、安全性降低以及寿命缩短。
三、船体防腐的基本原则1. 材料选择:选用具有良好防腐性能、抗氧化性能和耐磨性能的材料,以保证船体长时间使用的安全性和稳定性。
2. 前期处理:在进行船体防腐之前,应对船体进行充分的清洁和除锈处理,以确保涂层的附着力和防腐效果。
3. 防护涂层:在船体的表面涂覆一层具有良好防腐性能的防护涂层,以提高船体的抗腐蚀能力和耐久性。
四、船体防腐的具体方案1. 环氧涂层方案:选择具有良好耐候性和耐腐蚀性的环氧防腐漆,将其涂刷在船体表面。
该涂层能够有效隔离船体与外界环境的接触,并具备较高的耐化学腐蚀性,可在恶劣环境下保持船体的耐久性。
2. 防污涂层方案:以保护环境为导向的防污涂层方案可减少海洋生物的黏附,防止生物腐蚀和磨损船体。
同时,这种涂层还能减少船舶的阻力,提高燃油效率,降低航行成本。
3. 防锈涂层方案:选择耐腐蚀性较强的富锌涂层,形成一层锌铁合金保护膜,有效隔离空气和水分对船体的腐蚀。
该方案具备良好的防腐性能和耐久性,适用于长期使用的船舶。
五、船体防腐方案的实施1. 前期准备:对船体进行全面的清洁、除锈和修复工作,确保表面光滑平整。
2. 涂刷防腐涂层:按照防腐方案选择的涂层类型和施工要求,对船体进行涂刷。
确保涂膜的均匀性和厚度符合要求。
3. 定期检查和维护:定期检查船体涂层的状况,对有损坏和腐蚀的部分及时修复和维护,以保证防腐涂层的有效性和船体的完整性。
六、总结船体防腐是船舶维护中不可或缺的一环,对船体的安全性和耐久性具有重要影响。
船舶腐蚀原因及防腐措施分析

船舶腐蚀原因及防腐措施分析
船舶腐蚀是指船舶结构部件受到各种外界环境因素作用下,发生表面金属材料物质的损失和结构破坏的现象。
船舶腐蚀的主要原因有以下几个方面:
1.海水腐蚀:海水中含有大量的氯离子和溶解性氧,这些物质会与金属结构发生电化学反应,导致金属腐蚀。
海水中的微生物和海洋生物也会对金属结构产生腐蚀作用。
2.大气腐蚀:船舶在大气环境中暴露,不断受到大气中的氧、水蒸气、二氧化硫、酸雨等化学物质的侵蚀,从而引起金属表面的腐蚀。
3.电化学腐蚀:船舶结构中不同金属材料之间的电位差异会产生电流,在浸泡在电解质中的金属表面形成阳极和阴极,从而引起电化学腐蚀。
为了防止船舶腐蚀,可以采取以下一些防腐措施:
1.防护涂料:通过在金属表面涂覆防护涂料,形成一层保护膜,可以阻止氧气和水分进入金属表面,减少腐蚀的发生。
2.电位保护:通过在金属结构上加装阴极保护设备,使金属结构成为阴极,从而牺牲阴极以保护金属结构不被腐蚀。
3.合理设计:在船舶结构的设计中,应合理选择材料和结构形式,避免或减少不同金属材料之间的电位差,从而减少电化学腐蚀的发生。
4.定期检测和维护:船舶应定期进行腐蚀检测和维护,及时修复受损的防腐层和金属结构,避免腐蚀进一步扩大。
5.使用防腐材料:在船舶建造和维修过程中,应选择具有良好耐腐蚀性能的材料,如不锈钢、铝合金等,以提高船舶的抗腐蚀能力。
船舶腐蚀是一个常见的问题,需要采取一系列的防腐措施,从材料选择到定期检测和维护,都能有效减少船舶腐蚀的发生,延长船舶的使用寿命。
船舶腐蚀原因及防腐措施分析
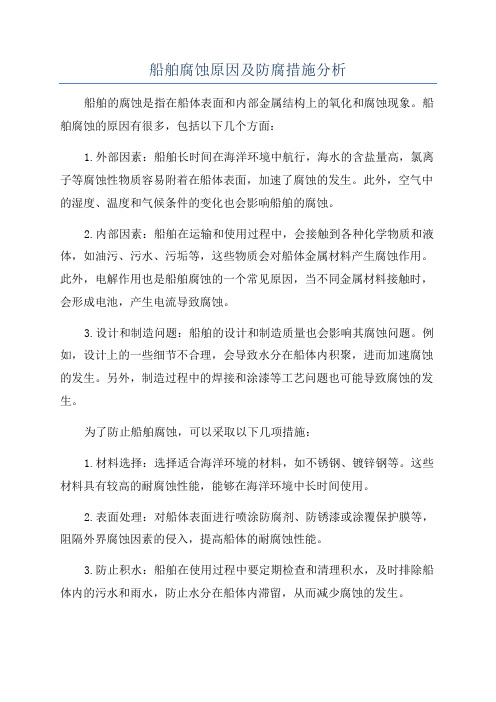
船舶腐蚀原因及防腐措施分析船舶的腐蚀是指在船体表面和内部金属结构上的氧化和腐蚀现象。
船舶腐蚀的原因有很多,包括以下几个方面:1.外部因素:船舶长时间在海洋环境中航行,海水的含盐量高,氯离子等腐蚀性物质容易附着在船体表面,加速了腐蚀的发生。
此外,空气中的湿度、温度和气候条件的变化也会影响船舶的腐蚀。
2.内部因素:船舶在运输和使用过程中,会接触到各种化学物质和液体,如油污、污水、污垢等,这些物质会对船体金属材料产生腐蚀作用。
此外,电解作用也是船舶腐蚀的一个常见原因,当不同金属材料接触时,会形成电池,产生电流导致腐蚀。
3.设计和制造问题:船舶的设计和制造质量也会影响其腐蚀问题。
例如,设计上的一些细节不合理,会导致水分在船体内积聚,进而加速腐蚀的发生。
另外,制造过程中的焊接和涂漆等工艺问题也可能导致腐蚀的发生。
为了防止船舶腐蚀,可以采取以下几项措施:1.材料选择:选择适合海洋环境的材料,如不锈钢、镀锌钢等。
这些材料具有较高的耐腐蚀性能,能够在海洋环境中长时间使用。
2.表面处理:对船体表面进行喷涂防腐剂、防锈漆或涂覆保护膜等,阻隔外界腐蚀因素的侵入,提高船体的耐腐蚀性能。
3.防止积水:船舶在使用过程中要定期检查和清理积水,及时排除船体内的污水和雨水,防止水分在船体内滞留,从而减少腐蚀的发生。
4.涂层保护:对于船舶的船底和水线等易受海洋环境侵蚀的部位,可以使用具有良好耐蚀性能的防腐涂层进行保护。
这些涂层能够形成一层保护膜,减少海水和氧气接触金属材料的机会,从而延缓腐蚀的发生。
5.定期维护:定期检查船体表面和内部金属结构的状态,及时修复和更换受腐蚀的部件,保持船舶的良好状态。
6.腐蚀监测:利用腐蚀监测技术,如电化学腐蚀监测、超声波腐蚀监测等,对船舶的腐蚀情况进行实时监测和评估,及时采取措施进行修复和保护。
综上所述,船舶腐蚀是在船体表面和内部金属结构上发生的氧化和腐蚀现象。
腐蚀的原因包括外部因素、内部因素以及设计和制造问题。
船舶建造质量标准
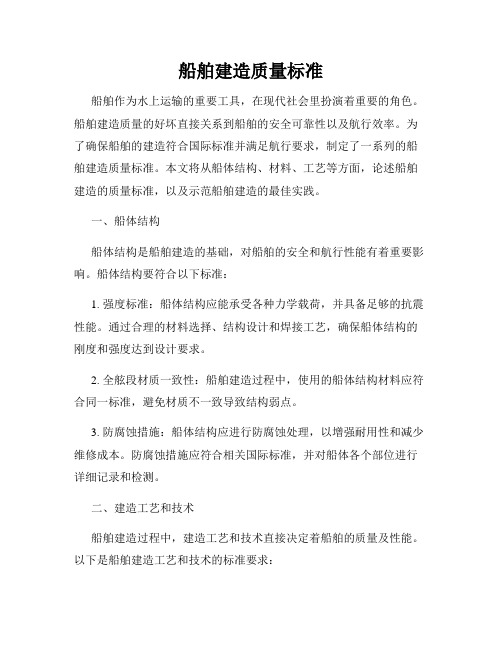
船舶建造质量标准船舶作为水上运输的重要工具,在现代社会里扮演着重要的角色。
船舶建造质量的好坏直接关系到船舶的安全可靠性以及航行效率。
为了确保船舶的建造符合国际标准并满足航行要求,制定了一系列的船舶建造质量标准。
本文将从船体结构、材料、工艺等方面,论述船舶建造的质量标准,以及示范船舶建造的最佳实践。
一、船体结构船体结构是船舶建造的基础,对船舶的安全和航行性能有着重要影响。
船体结构要符合以下标准:1. 强度标准:船体结构应能承受各种力学载荷,并具备足够的抗震性能。
通过合理的材料选择、结构设计和焊接工艺,确保船体结构的刚度和强度达到设计要求。
2. 全舷段材质一致性:船舶建造过程中,使用的船体结构材料应符合同一标准,避免材质不一致导致结构弱点。
3. 防腐蚀措施:船体结构应进行防腐蚀处理,以增强耐用性和减少维修成本。
防腐蚀措施应符合相关国际标准,并对船体各个部位进行详细记录和检测。
二、建造工艺和技术船舶建造过程中,建造工艺和技术直接决定着船舶的质量及性能。
以下是船舶建造工艺和技术的标准要求:1. 设计标准:船舶建造前,需制定详细的设计方案,包括船体结构、动力系统、配套设备等方面。
设计方案需要满足船级社和国际标准,确保船舶建造的可行性和安全性。
2. 检验与监控:船舶建造过程中,应设立检验与监控机构,对各个节点进行检测和监控。
通过全过程质量控制,确保船舶建造的质量符合要求。
3. 焊接技术:船舶建造过程中,焊接是关键工艺之一。
焊接工艺应满足国际标准,确保焊缝强度和密封性。
需要进行焊接质量检验,并进行焊接人员的培训和证书资格认证。
三、船用材料船用材料的选择和使用,对于船舶的建造质量至关重要。
以下是对船用材料的标准要求:1. 材料强度和耐腐蚀性:船舶建造使用的材料应具备足够的强度和耐腐蚀性能,保证船体结构的可靠性和航行寿命。
2. 材料认证和检验:船用材料需要符合国际标准,并进行合格证明。
应进行材料检验,确保材料符合设计要求。
轮船外层结构防腐措施

轮船外层结构防腐措施
轮船外层结构防腐措施对于船体的保护至关重要,特别是在海洋环境中,暴露在水和空气中的船体容易受到腐蚀。
以下是常见的轮船外层结构防腐措施:
1.船体材料选择:
在设计和建造船舶时,选择耐腐蚀性能较好的材料,例如不锈钢、铝合金等。
这些材料能够抵抗海水、盐雾和大气中的腐蚀。
2.防腐涂层:
在船体表面涂覆防腐涂层,以隔绝海水和空气对船体的侵蚀。
防腐涂层通常包括底漆、防锈漆和面漆,其具有耐腐蚀性、耐磨损性和耐海水性。
3.阳极保护:
利用阳极保护系统来保护船体。
阳极通常采用锌或铝等金属制成,通过牺牲阳极上的金属来保护船体不受腐蚀。
4.防腐补漆:
定期进行船体表面的防腐补漆工作,修补和更新防腐涂层,确保其持久性和有效性。
5.防污涂层:
在船底和船体水线以下区域使用防污涂层,减少生物附着和污物积累,降低海洋生物腐蚀的风险。
6.防锈处理:
定期检查船体结构,及时发现和处理生锈的部位,防止锈蚀扩散。
7.海水冷却系统防腐:
对海水冷却系统的管道和设备采取防腐措施,如使用耐腐蚀材料、防腐涂层等,以防止海水对冷却系统的腐蚀。
8.适当的维护保养:
定期清洗船体表面,去除盐分和污物,保持船体清洁。
另外,及时修补船体表面的破损和腐蚀部位,防止腐蚀的进一步发展。
以上措施综合应用可以有效地延长船体的使用寿命,减少因腐蚀而引起的安全隐患,确保船舶的安全航行和运营。
关于海洋工程结构与船舶防腐技术措施分析

关于海洋工程结构与船舶防腐技术措施分析海洋工程结构和船舶在海洋环境中长期暴露于水和风的作用下,容易受到海水腐蚀和氧化的影响。
海洋工程结构和船舶防腐技术措施显得尤为重要。
本文将对海洋工程结构和船舶在防腐方面的技术措施进行分析。
一、海洋工程结构防腐技术措施1. 防腐涂料海洋工程结构通常采用防腐涂料进行保护,以阻挡海水对金属结构或混凝土结构的侵蚀。
防腐涂料通常包括底漆、中间层和面漆三层结构,以确保涂层的附着力和防腐能力。
在选择防腐涂料时,需要考虑涂料的防腐性能、适用环境、施工工艺等因素,以确保其在海洋环境中长期使用。
2. 防腐覆盖材料在海洋工程结构中,除了防腐涂料外,还可以通过覆盖防腐材料来进行保护。
使用合成树脂、玻璃纤维、聚合物等覆盖材料来覆盖金属或混凝土结构,以提高其防腐性能和使用寿命。
3. 防腐防护系统海洋工程结构通常需要建立完善的防腐防护系统,包括防腐设施、监测系统和维护保养计划等。
通过定期检查和维护,及时修复和更换受损防腐涂层或覆盖材料,可以有效延长海洋工程结构的使用寿命。
二、船舶防腐技术措施1. 防腐涂料船舶防腐涂料是船舶防腐技术的重要组成部分。
船舶在长期航行中容易受到海水腐蚀和氧化的影响,因此需要采用高性能的防腐涂料进行保护。
防腐涂料可以分为船体外部、船体内部和甲板三个部分,根据不同部位的使用条件和需求选择相应的防腐涂料。
2. 电化学防护除了防腐涂料外,船舶还可以采用电化学防护技术进行防腐。
电化学防护是通过在船体表面加设阳极和阴极,以形成电化学反应来保护金属结构,从而防止腐蚀的技术措施。
3. 防腐防护系统船舶需要建立完善的防腐防护系统,包括定期对船体进行防腐检查、维护涂层、清洗海水管道等工作。
在航行过程中,船舶还需要在不同的海域和水质条件下进行不同的防腐处理,以确保船体的防腐性能。
海洋工程结构和船舶在海洋环境中容易受到海水腐蚀和氧化的影响,因此需要采取有效的防腐技术措施进行保护。
防腐涂料、防腐覆盖材料、电化学防护和建立完善的防腐防护系统都是有效的防腐技术手段,可以确保海洋工程结构和船舶在海洋环境中长期安全使用。
船舶钢板腐蚀标准

船舶钢板腐蚀是一个影响船舶安全和寿命的重要问题。
根据相关标准,船舶钢板腐蚀程度的判定标准可以分为轻微腐蚀、中度腐蚀和重度腐蚀三个等级。
首先,轻微腐蚀是指船体表面形成均匀的薄锈,并且不影响船体的强度和外观。
此时,船体钢板表面应保持清洁,避免进一步腐蚀。
清洁方法可以使用机械清理或化学清理法,但要注意不要破坏已经形成的氧化膜。
其次,中度腐蚀是指船体表面锈迹较多,但未出现大的裂纹或局部锈透的情况。
此时,需要清除中度腐蚀区域内的部分或全部锈层,并采取防锈措施,如涂防锈漆或富锌底漆。
最后,重度腐蚀是指船体钢板表面出现大面积的锈透、脱落或破损等情况,严重影响船舶的外观和强度。
此时,需要彻底清除重锈,修复破损部位,并进行除锈处理,为后续涂装工作做好准备。
除了上述表面腐蚀问题,船体的内部腐蚀也是一个不容忽视的问题。
内部腐蚀通常是由水中的氯离子或其他腐蚀性物质引起的,对船体的金属结构造成严重破坏。
因此,船舶应定期进行内部检测和维修,确保船舶的安全和寿命。
综上所述,船舶钢板腐蚀标准涉及到腐蚀程度、锈层清除、修复破损部位、除锈处理等多个方面。
在船舶制造和使用过程中,应严格遵守相关标准和规范,加强船舶维护和保养,确保船舶的安全和寿命。
同时,随着科技的发展和应用,新型防腐材料和技术也在不断涌现,为船舶防腐工作提供了更多的选择和可能性。
船舶防腐标准

船舶防腐标准一、目的和适用范围本标准规定了船舶防腐涂料的技术要求、试验方法、检验规则及包装、运输、贮存等。
本标准适用于钢质船体及船用钢结构材料的防腐蚀涂料。
二、技术要求1. 船舶防腐涂料应具有良好的耐候性、耐水性、耐化学品性、耐油性、耐腐蚀性和防霉性能。
2. 船舶防腐涂料应符合环境保护的要求,无毒、无害、无污染,符合国家相关环保标准。
3. 船舶防腐涂料应具有良好的附着力和耐磨性,能有效地保护船体及钢结构材料不受腐蚀和损坏。
4. 船舶防腐涂料应有可靠的物理性能和化学性能,能在不同的环境下长期保持其性能。
三、试验方法1. 耐候性试验:按照GB/T 1771的规定进行。
将试样涂层置于模拟自然环境中,经过一定的时间后,观察其外观变化,检测其性能变化。
2. 耐水性试验:按照GB/T 1733的规定进行。
将试样涂层浸泡在水中一定时间,观察其外观变化,检测其性能变化。
3. 耐化学品性试验:按照相应标准的试验方法进行。
将试样涂层置于规定的化学药品中,经过一定的时间后,观察其外观变化,检测其性能变化。
4. 耐油性试验:按照GB/T 1737的规定进行。
将试样涂层置于规定的油类中,经过一定的时间后,观察其外观变化,检测其性能变化。
5. 防霉性能试验:按照GB/T 17711的规定进行。
将试样涂层置于规定的条件下,观察其防霉性能。
6. 无毒、无害、无污染试验:按照国家相关标准进行。
对涂料中的有害物质进行检测,确保其符合国家相关环保标准。
7. 附着力试验:按照GB/T 9286的规定进行。
测试涂层与基材之间的附着力,确保其具有良好的附着力。
8. 耐磨性试验:按照相应标准的试验方法进行。
对涂层进行磨损试验,检测其耐磨性能。
四、检验规则1. 出厂检验:每批产品均应进行出厂检验,检验项目包括耐候性、耐水性、附着力等主要技术指标。
合格产品应附有合格证明文件。
2. 型式检验:当有下列情况之一时,应进行型式检验:a) 新产品或老产品转厂生产的试制定型鉴定;b) 当制造工艺、配方发生较大变化时;c) 国家质量监督机构或行业主管部门提出型式检验要求时。
船舶腐蚀原因及防腐措施分析

船舶腐蚀原因及防腐措施分析船舶作为重要的运输工具,长期受到海水腐蚀的影响,容易发生腐蚀现象。
腐蚀会严重影响船舶的安全性能和使用寿命,因此对船舶腐蚀原因及防腐措施进行分析十分重要。
本文将从船舶腐蚀的原因入手,结合船舶腐蚀的分类,介绍船舶腐蚀的主要原因及防腐措施。
一、船舶腐蚀的分类船舶腐蚀主要可以分为结构腐蚀和设备腐蚀两大类。
结构腐蚀是指船舶主体结构受到海水等环境因素影响产生的腐蚀,主要包括船体、甲板、船底、舱口等部位。
设备腐蚀是指船舶设备、机械零部件等受到海水等环境因素影响产生的腐蚀,主要包括船用机械设备、管道、阀门、泵等。
结构腐蚀和设备腐蚀都是船舶腐蚀的重要类型,对船舶的使用寿命和安全性能影响较大。
二、船舶腐蚀的主要原因1. 海水中的含盐量海水中含有大量的盐分,盐分可以加速金属材料的腐蚀,尤其是在海水中的金属材料在受到机械损伤后更容易发生腐蚀。
海水中的盐分是船舶腐蚀的主要原因之一。
2. 电化学腐蚀船舶是一个复杂的电化学系统,船舶结构及设备上的金属材料产生电流并与海水中的盐分产生电化学反应,从而发生电化学腐蚀。
电化学腐蚀是船舶腐蚀的常见原因之一。
3. 海水的温度和湿度海水的温度和湿度对船舶腐蚀也有一定的影响,海水温度越高,湿度越大,船舶腐蚀就会越严重。
海水的温度和湿度也是船舶腐蚀的重要原因。
4. 金属材料的选择和质量船舶上所使用的金属材料的选择和质量也会影响船舶腐蚀的严重程度,质量较差的金属材料容易受到海水腐蚀的影响,从而引发船舶腐蚀问题。
5. 机械损伤和使用年限船舶在使用过程中可能会受到各种机械损伤,机械损伤会使船舶结构及设备上的金属材料暴露在海水中,加速发生腐蚀。
船舶的使用年限也会导致金属材料老化,降低其抗腐蚀性能。
三、船舶腐蚀防腐措施1. 选用耐腐蚀材料在船舶结构及设备的设计和制造过程中,应该选择耐腐蚀的金属材料,如不锈钢、铝合金等,以提高船舶对海水腐蚀的抵抗能力。
2. 防腐涂层在船舶结构及设备表面涂刷防腐蚀涂层,以形成一层保护膜,防止金属材料接触到海水,减缓金属材料的腐蚀速度。
船舶和海洋工程结构的防腐蚀技术分析

船舶和海洋工程结构的防腐蚀技术分析摘要:为了保证船舶和海洋工程结构的正常使用,维护好海洋环境,必须大力开发防锈涂料和防腐蚀技术,同时要使海洋工业得到最大限度的发展。
海水中含有大量的物质,许多是会侵蚀金属的物质,所以无论是海洋建筑还是船舶,都会采用防锈技术,但这种方法所带来的经济损失是巨大的。
海上交通作为世界经济发展的主要推动力,运载能力虽然相对缓慢,但是重量和数量却是其他交通工具无法相比的。
随着科学技术的飞速发展,人们对能量的需求量越来越大,其中包括石油、燃气和风力。
在进行海上发展时,应特别关注船舶和海洋工程建设的侵蚀问题,这已成为制约我国海上发展步伐的重要因素。
关键词:船舶;海洋工程结构;防腐蚀技术1 船舶防腐蚀漆的特殊要求1.1 安全性由于船舶在航行时会与海水产生直接接触,船体表面的防腐蚀涂层若存在毒性,就会更容易渗入水中。
因此在船舶建造时使用的防腐蚀材料必须满足使用安全、可靠的要求。
1.2 水性化水基油漆是一种以水为分散剂或溶剂的涂料,目前已被广泛应用于船舶防腐蚀漆。
水性油漆不仅性能好,使用起来也比较方便,而且更注重环境保护,更适用于船舶生产。
1.3 高分子固化在油漆内舱时,对油漆的毒性和挥发性有较高的要求。
相对于目前广泛应用的溶剂型油漆,高固体分子涂层具有较小的毒性和较小的挥发性。
1.4 多元化由于船舶本身体积大、结构复杂,因此在不同部位的防腐要求也就相应地有所侧重。
就船舶外部情况而言,所选用的防腐漆应具有很强的防腐性能,以避免海水腐蚀;就船体内部舱段而言,选择的防腐蚀涂层应该具有较低的挥发性。
要根据不同部位的不同防腐要求,选择不同的防腐蚀涂层。
2 加强船舶和海洋工程结构防腐技术的对策2.1 防锈涂料在船舶和海洋工程结构建造中,建筑材料主要为钢材,对其耐腐蚀性需要进行全面而细致的分析,以便推动我国海洋工程结构的发展。
国内的技术和材质都有了很大的提高,抗腐蚀的材料也有了很多不同的选择,最常见的是铝合金、耐蚀钢筋等材料。
关于海洋工程结构与船舶防腐技术措施分析

关于海洋工程结构与船舶防腐技术措施分析海洋工程结构需要面对恶劣的海洋环境,如海水的腐蚀、冲击以及大风大浪等,因此船舶和海洋工程结构需要采取一系列的防腐技术措施,以延长使用寿命和提高安全性能。
船舶和海洋工程结构需要选用高强度、耐腐蚀的材料。
常见的选材包括碳钢、不锈钢和铝合金等。
碳钢具有良好的强度和刚性,但容易被海水腐蚀。
碳钢需要进行防腐处理,如铸铁锈层处理和镀锌等,以提高其抗腐蚀能力。
不锈钢具有优良的耐腐蚀性能,但价格较高。
铝合金具有良好的强度和耐腐蚀性能,同时重量轻,但容易被海水侵蚀。
选材时需要根据具体情况综合考虑材料的性能和成本等因素。
采用防腐涂层是一种常见的防腐技术措施。
防腐涂层可以有效地防止海水的侵蚀和腐蚀。
常用的防腐涂层包括环氧涂料、聚氨酯涂料和丙烯酸涂料等。
这些涂料具有良好的耐腐蚀性和耐候性能,可以有效地保护船舶和海洋工程结构表面免受海水的侵蚀。
防腐涂层还可以起到减少摩擦阻力、提高航行速度和减少燃油消耗的作用。
进行防腐维护和修复是必不可少的。
船舶和海洋工程结构经过一段时间的使用后,可能会出现各种腐蚀和损伤问题。
定期进行防腐维护和修复工作十分重要。
这包括清洗表面的污垢和盐分、检查和修复防腐涂层的损伤等。
还需要进行海水质量监测,了解海水中的盐分、酸碱度以及其他对结构材料具有腐蚀危害的物质,以便采取对应的措施。
船舶和海洋工程结构还需要考虑其他防腐技术措施。
可以采用阴极保护技术,即通过在结构表面放置SAC(Sacrificial Anode Cathodic Protection Sacrificial Anode Cathodic Protection)或ICC(Impressed Current Cathodic Protection体)来防止金属腐蚀。
还可以采取防腐缝隙处理、防腐封堵和防腐填缝等技术手段,进一步提高防腐效果。
船舶和海洋工程结构的防腐技术措施涉及选材、防腐涂层、防腐维护和修复等方面,需要根据具体情况综合考虑,以提高结构的耐腐蚀性能和安全性能。
船舶腐蚀原因及防腐措施分析
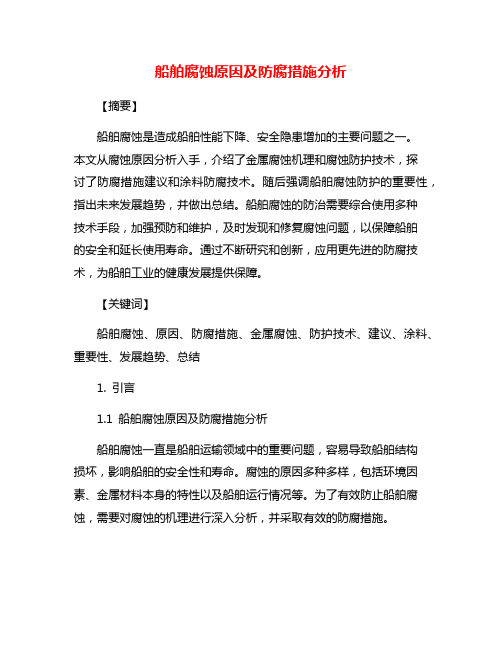
船舶腐蚀原因及防腐措施分析【摘要】船舶腐蚀是造成船舶性能下降、安全隐患增加的主要问题之一。
本文从腐蚀原因分析入手,介绍了金属腐蚀机理和腐蚀防护技术,探讨了防腐措施建议和涂料防腐技术。
随后强调船舶腐蚀防护的重要性,指出未来发展趋势,并做出总结。
船舶腐蚀的防治需要综合使用多种技术手段,加强预防和维护,及时发现和修复腐蚀问题,以保障船舶的安全和延长使用寿命。
通过不断研究和创新,应用更先进的防腐技术,为船舶工业的健康发展提供保障。
【关键词】船舶腐蚀、原因、防腐措施、金属腐蚀、防护技术、建议、涂料、重要性、发展趋势、总结1. 引言1.1 船舶腐蚀原因及防腐措施分析船舶腐蚀一直是船舶运输领域中的重要问题,容易导致船舶结构损坏,影响船舶的安全性和寿命。
腐蚀的原因多种多样,包括环境因素、金属材料本身的特性以及船舶运行情况等。
为了有效防止船舶腐蚀,需要对腐蚀的机理进行深入分析,并采取有效的防腐措施。
金属腐蚀的机理主要包括电化学腐蚀、化学腐蚀和微生物腐蚀等多种方式。
在海洋环境中,盐雾、潮湿和氧气是导致金属腐蚀的主要因素,特别是海水中的氯离子会加速金属的腐蚀速度。
为了有效防止船舶腐蚀,船舶建造和维护时需要采用各种腐蚀防护技术,如防腐涂层、防腐涂料和阳极保护等。
定期检查和保养船舶结构也是预防腐蚀的重要措施。
在未来,随着科技的不断发展,船舶腐蚀防护技术将会更加智能化和高效化,为船舶的安全性和寿命提供更好的保障。
船舶腐蚀防护的重要性不可忽视,需要持续关注和改进相关技术,确保船舶运行的安全和稳定。
2. 正文2.1 腐蚀原因分析腐蚀是船舶制造和运营过程中普遍存在的问题,严重影响船舶的使用寿命和安全性。
船舶腐蚀的主要原因可以分为以下几个方面:1. 海水氧化腐蚀:船舶在海上长期接触海水,海水中含有各种盐类和氧气,使金属表面形成一层氧化物,从而加速了金属的腐蚀速度。
2. 海洋生物腐蚀:海洋中存在各种微生物和海洋生物,它们会在船舶表面产生生物膜,导致金属腐蚀。
船舶建筑物的防腐与防水技术研究

船舶建筑物的防腐与防水技术研究引言:船舶建筑物的防腐与防水技术是海洋工程中至关重要的一环。
海洋环境的高湿度、高盐度、腐蚀性气候和物理力量的作用,对船舶构建材料的防腐与防水性能提出了很高的要求。
本文将针对船舶建筑物的防腐与防水技术进行研究,分析常用材料和方法,并探究未来的发展趋势。
一、常用防腐材料1. 防腐漆防腐漆是一种广泛使用的防护材料,其特点是防腐蚀性能和施工便利性。
常见的防腐漆有沥青漆、环氧漆、氯化橡胶漆等。
这些防腐漆膜可以有效地隔离船舶建筑物与海水的接触,防止氧化和腐蚀。
2. 防腐剂防腐剂是一种能渗透到材料内部并抑制微生物生长的化学物质。
常见的防腐剂包括酚醛树脂、磷酸盐等。
这些化学物质可以有效地控制船舶建筑物上的微生物生长,延长使用寿命。
3. 形状记忆合金形状记忆合金是一种具有形状记忆效应的金属合金,其特点是可形变且具有良好的耐腐蚀性。
形状记忆合金可以应用在船舶建筑物的防腐与防水中,通过调节温度以及外部应力的控制,使其具备防腐和防水的能力。
二、防水方法1. 防水胶防水胶是一种应用广泛的防水材料,具有良好的粘结性、耐水性和柔韧性。
在船舶建筑物的防水中,可以使用防水胶填充船身结构的接缝、裂缝和孔洞,以达到防止海水渗漏的作用。
2. 橡胶密封条橡胶密封条具有优异的弹性和耐腐蚀性能,可以用于船舶建筑物的密封以及防水。
其主要应用在船舶门窗、舱口和船体连接部位,以确保船舶内部干燥以及防止海水渗透。
3. 高分子聚合物涂层高分子聚合物涂层是一种具有优异耐腐蚀性和耐候性能的涂层材料。
在船舶建筑物的防水中,可以使用高分子聚合物涂层涂覆在船体表面,形成一层坚固的防水层,以防止海水侵蚀。
三、未来发展趋势1. 新型防腐材料的研发随着科技的发展,新型材料的研发将成为未来船舶建筑物防腐的趋势。
例如,纳米材料的应用能够显著提高防腐性能,使船舶建筑物更加耐用。
2. 智能化防腐与防水随着智能化技术的发展,未来的船舶建筑物防腐与防水可能会借助传感器、控制系统等技术,实现防腐与防水的自动化管理和监测,提高防护效果。
船舶腐蚀原因及防腐措施分析
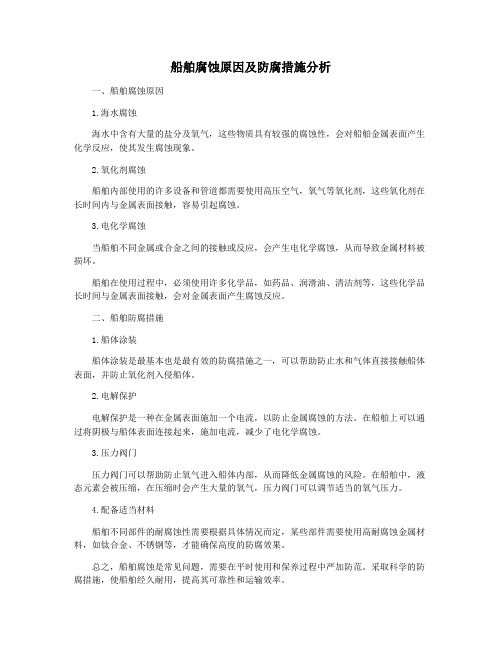
船舶腐蚀原因及防腐措施分析
一、船舶腐蚀原因
1.海水腐蚀
海水中含有大量的盐分及氧气,这些物质具有较强的腐蚀性,会对船舶金属表面产生化学反应,使其发生腐蚀现象。
2.氧化剂腐蚀
船舶内部使用的许多设备和管道都需要使用高压空气,氧气等氧化剂,这些氧化剂在长时间内与金属表面接触,容易引起腐蚀。
3.电化学腐蚀
当船舶不同金属或合金之间的接触或反应,会产生电化学腐蚀,从而导致金属材料被损坏。
船舶在使用过程中,必须使用许多化学品,如药品、润滑油、清洁剂等,这些化学品长时间与金属表面接触,会对金属表面产生腐蚀反应。
二、船舶防腐措施
1.船体涂装
船体涂装是最基本也是最有效的防腐措施之一,可以帮助防止水和气体直接接触船体表面,并防止氧化剂入侵船体。
2.电解保护
电解保护是一种在金属表面施加一个电流,以防止金属腐蚀的方法。
在船舶上可以通过将阴极与船体表面连接起来,施加电流,减少了电化学腐蚀。
3.压力阀门
压力阀门可以帮助防止氧气进入船体内部,从而降低金属腐蚀的风险。
在船舶中,液态元素会被压缩,在压缩时会产生大量的氧气,压力阀门可以调节适当的氧气压力。
4.配备适当材料
船舶不同部件的耐腐蚀性需要根据具体情况而定,某些部件需要使用高耐腐蚀金属材料,如钛合金、不锈钢等,才能确保高度的防腐效果。
总之,船舶腐蚀是常见问题,需要在平时使用和保养过程中严加防范。
采取科学的防腐措施,使船舶经久耐用,提高其可靠性和运输效率。
船体钢结构的防腐方法及性能

船体钢结构的防腐方法及性能摘要:随着我国经济实力不断加强,我国航运物流行业获得良好的发展,船舶安全性越来越受到各国的重视,其中船舶钢结构的防腐被要求达到更高的标准,以满足安全性和使用寿命的需求。
近年来在海洋重防腐方面取得了重大进展,新材料和新技术层出不穷。
关键词:船体钢结构;防腐方法;性能引言在我国经济实力逐渐壮大,科学技术不断创新的今天,大部分船舶的船体采用的是钢结构,钢结构在恶劣的环境下,与海水中的水分、盐分等发生化学、电化学腐蚀反应,这些腐蚀情况会使船体产生锈蚀的情况,最终导致船体的承载能力减少,使船舶的安全受到威胁。
除了海水的腐蚀,高温、高湿、酸雨、寒冷等天气环境也会对船体钢结构产生腐蚀破坏。
因此,船体钢结构的防腐对船舶的安全、稳定航行有着至关重要的作用。
传统的船体钢结构防腐方法存在着防腐性能差的缺陷,无法适应现今社会的需求,为此提出船体钢结构防腐方法及性能研究。
1水上船体部分的腐蚀及防腐措施船体中处于水上的部分主要包括甲板、上层建筑以及干舷。
这些部分在平时主要受到雨雪、海水飞沫以及海洋大气的影响,而且这些因素都是造成船体水上部分严重腐蚀的重要原因。
船体中的火工校正部位由于其金属组织在结构上发生了较大的变化,因此使其耐腐蚀性大大低于船体中的其他部位。
所以说,船体中的火工校正部位如没有较好的涂膜,则比其他部位更容易被破坏,最终使船体的腐蚀速率大大加快。
水上船体的防腐维护是船舶日常维护的重点,一般分春季和秋季保养,采用适宜的船舶涂料,并且能够用恰当的施工工艺将船舶的某些部位进行有效覆盖,使船舶上各个部位的钢铁表面都与外界的各种环境相隔离,那么就能够使船体得到有效的保护,从而减少船体结构的腐蚀。
涂装工艺包括敲铲、打磨、除盐、除尘、喷涂或刷涂等。
2船体水下部位船体水下部位主要包括主船体结构、球鼻艏以及与主船体直接相连的螺旋桨、舭龙骨、舵、减摇鳍等附体,船体水下部位暴露在海水中,受波浪载荷等的冲击,易造成涂层脱落。
船体钢结构的防腐方法及性能
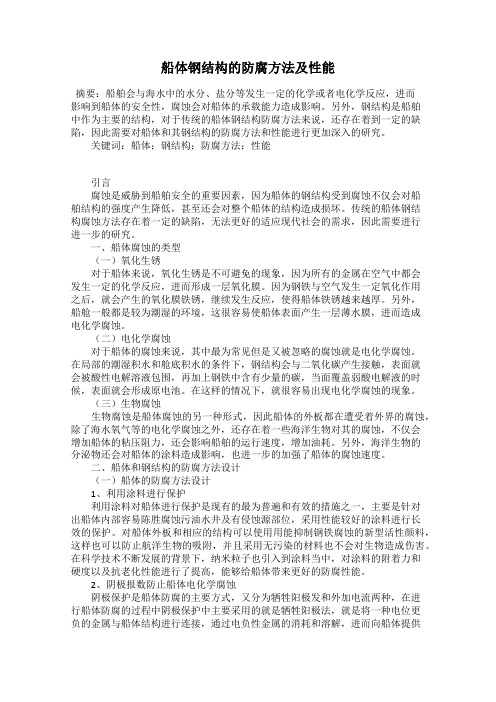
船体钢结构的防腐方法及性能摘要:船舶会与海水中的水分、盐分等发生一定的化学或者电化学反应,进而影响到船体的安全性,腐蚀会对船体的承载能力造成影响。
另外,钢结构是船舶中作为主要的结构,对于传统的船体钢结构防腐方法来说,还存在着到一定的缺陷,因此需要对船体和其钢结构的防腐方法和性能进行更加深入的研究。
关键词:船体;钢结构;防腐方法;性能引言腐蚀是威胁到船舶安全的重要因素,因为船体的钢结构受到腐蚀不仅会对船舶结构的强度产生降低,甚至还会对整个船体的结构造成损坏。
传统的船体钢结构腐蚀方法存在着一定的缺陷,无法更好的适应现代社会的需求,因此需要进行进一步的研究。
一、船体腐蚀的类型(一)氧化生锈对于船体来说,氧化生锈是不可避免的现象,因为所有的金属在空气中都会发生一定的化学反应,进而形成一层氧化膜。
因为钢铁与空气发生一定氧化作用之后,就会产生的氧化膜铁锈,继续发生反应,使得船体铁锈越来越厚。
另外,船舱一般都是较为潮湿的环境,这很容易使船体表面产生一层薄水膜,进而造成电化学腐蚀。
(二)电化学腐蚀对于船体的腐蚀来说,其中最为常见但是又被忽略的腐蚀就是电化学腐蚀。
在局部的潮湿积水和舱底积水的条件下,钢结构会与二氧化碳产生接触,表面就会被酸性电解溶液包围,再加上钢铁中含有少量的碳,当面覆盖弱酸电解液的时候,表面就会形成原电池。
在这样的情况下,就很容易出现电化学腐蚀的现象。
(三)生物腐蚀生物腐蚀是船体腐蚀的另一种形式,因此船体的外板都在遭受着外界的腐蚀,除了海水氧气等的电化学腐蚀之外,还存在着一些海洋生物对其的腐蚀,不仅会增加船体的粘压阻力,还会影响船舶的运行速度,增加油耗。
另外,海洋生物的分泌物还会对船体的涂料造成影响,也进一步的加强了船体的腐蚀速度。
二、船体和钢结构的防腐方法设计(一)船体的防腐方法设计1、利用涂料进行保护利用涂料对船体进行保护是现有的最为普遍和有效的措施之一,主要是针对出船体内部容易陈胜腐蚀污油水井及有侵蚀源部位,采用性能较好的涂料进行长效的保护。
- 1、下载文档前请自行甄别文档内容的完整性,平台不提供额外的编辑、内容补充、找答案等附加服务。
- 2、"仅部分预览"的文档,不可在线预览部分如存在完整性等问题,可反馈申请退款(可完整预览的文档不适用该条件!)。
- 3、如文档侵犯您的权益,请联系客服反馈,我们会尽快为您处理(人工客服工作时间:9:00-18:30)。
1.铝合金的表面防护处理方法铝合金的表面防护处理方法主要有阴极保护法、锌系磷化法、稀土元素保护法、激光熔覆法、凝胶法等。
1.1阴极保护法阴极保护技术是一项经济效益十分显著的控制腐蚀的电化学保护技术。
将被保护的金属进行阴极极化,使电位负移到金属表面阳极的平衡电位,消除其电化学不均匀性所引起的腐蚀电池,使金属免遭腐蚀。
它可以成倍地延长被保护件的使用寿命,阴极保护与防护涂料联合使用时,阴极保护使涂层缺陷处和毛细孔处金属构件免遭腐蚀。
根据施加阴极极化电流的方法不同,阴极保护方法可分为两大类:外加电流法和牺牲阳极法。
1.2锌系磷化法中化化工科学技术研究总院研制出可以同时处理钢铁、铝及铝合金、锌及锌合金的磷化液WES一01。
该磷化液的使用有2个突出的特点:①可用于喷淋线;②磷化温度为低温或常温,一般30~40℃。
传统的铝及铝合金的锌系磷化,由于设置出光工序,所以一般采用浸泡工艺处理,而且处理温度不能低于50℃,否则不能获得良好的磷化膜。
而WES-01则突破了这一缺陷,推动了铝材锌系磷化的技术进步。
在工作液的总酸度为20~25点、游离酸度为O.6—1.4点、促进剂为2~3点、温度为30~40℃、喷淋时间为60~90s的情况下,纯铝的磷化膜略暗或呈浅灰色,铝合金由于其材质不同而呈浅灰色、灰色、深灰色不等。
漆膜的连续中性盐雾试验为268h,湿热试验大于50h。
所处理的工件可以是薄铝板,也可以是形状复杂的铝合金件,如冰箱铝制蒸发器及电视机后壳、工具、门窗、汽车配件等。
该磷化液不仅能在喷淋线上使用,而且还可以在浸泡线上使用,同样都能进行钢、铝、锌的单独处理或混装处理。
值得注意的是,铝制蒸发器涂装后还需要在120℃下覆膜,再于180℃下流化,涂层也不起泡和脱落;还有一种铝件,涂装后还需要进行剪切,然后再于120℃覆膜,涂层也不起泡和脱落。
这种产品对前处理和涂层的要求非常高,任何一点质量隐患都会在覆膜和流化过程中出现问题,而且这样的产品肯定要进行覆膜和流化,客户要求不能有任何起泡现象发生,更不能出现涂层脱落。
用户曾经将涂装后的产品放置1个月后再进行覆膜及流化,涂层也没有起泡和脱落现象发生。
1.3稀土元素保护法稀土铝合金材扦是在金属铭中加入稀土元素,它能够起到净化、提高纯度、填补表层缺陷、细化晶粒、减少偏析,消除显微不均而导致的局部腐性的作用、同时也带来铝的电极电位负移,具有了栖牲阳极效应和优异的导电性能,从而大大提高了铝的耐蚀性能。
这种材抖配之首创的热浸披、热喷极工艺。
可以使防腐工程达到百年超长使用寿命。
稀土带来的这些优异的性能改善使稀土铝合金能够在石油、化工、建筑、市政、交通、电力、冶金、船铂、军工、航空航天、水电热电、热工、天然气钢瓶、机械轻工系统中广泛使用稀土铝合金干离子TC产品是对稀土铝合金敏层进行徽弧子离子式化来实现铰层表面稀土铝的陶瓷化。
它不但能够耐数千度高温,在航空、航天、宇宙飞船等领城使用,而且彻底解决了绝大多数(少数未及试脸)任意浓度的强酸、强碱、强乳化剂、井下条件等极为苛刻的腐蚀环境下的防腐问题。
1.4激光熔覆法激光熔覆法是在高能光束的作用下,将一种或多种合金元素和基体表面快速加热熔化,光束移开后自然冷却的一种表面强化方法。
通过该方法可以在铝合金表面熔覆铜基、镍基复合材料以及陶瓷粉末,提高铝合金表面的耐腐蚀性。
但是该方法的不足之处是界面上易形成脆性相和裂纹,实际应用中涂层的尺寸精度、对基体复杂形状的容许度、表面粗糙度等问题较难解决。
1.5凝胶法用过渡金属醇盐作为合成氧化物的前驱体,采用一凝胶工艺可以在铝合金表面形成一层氧化物保溶胶一以对铝合金起到防腐蚀的作用。
腐蚀相关标准:ASTM G66-99GBT22639铝合金加工产品剥落腐蚀试验方法GBT7998铝合金晶间腐蚀测定方法GBT22640GBT26491GBT19746金属和合金腐蚀盐溶液周浸试验GBT26323色漆和清漆铝及铝合金表面涂膜的耐丝状腐蚀试验GBT19822铝及铝合金硬质阳极氧化膜规范GB8013-87铝及铝合金阳极氧化GBT12967.1铝及铝合金阳极氧化膜检测方法GBT8753.4铝及铝合金阳极氧化GBT8013-2***铝及铝合金阳极氧化膜的总规范GBT16545金属和合金的腐蚀腐蚀试样上腐蚀产物的清除GBT18590金属和合金的腐蚀点蚀评定方法GBT21621危险品金属腐蚀性实验方法2钢结构的防腐蚀措施2.1耐候钢耐腐蚀性能优于一般结构用钢的钢材称为耐候钢,一般含有磷、铜、镍、铬、钛等金属,使金属表面形成保护层,以提高耐腐蚀性。
其低温冲击韧性也比一般的结构用钢好。
标准为《焊接结构用耐候钢》(GB4172-84)。
2.2热浸锌热浸锌是将除锈后的钢构件浸入600℃左右高温融化的锌液中,使钢构件表面附着锌层,锌层厚度对5mm以下薄板不得小于65μm,对厚板不小于86μm。
从而起到防腐蚀的目的。
这种方法的优点是耐久年限长,生产工业化程度高,质量稳定。
因而被大量用于受大气腐蚀较严重且不易维修的室外钢结构中。
如大量输电塔、通讯塔等。
近年来大量出现的轻钢结构体系中的压型钢板等。
也较多采用热浸锌防腐蚀。
热浸锌的首道工序是酸洗除锈,然后是清洗。
这两道工序不彻底均会给防腐蚀留下隐患。
所以必须处理彻底。
对于钢结构设计者,应该避免设计出具有相贴合面的构件,以免贴合面的缝隙中酸洗不彻底或酸液洗不净。
造成镀锌表面流黄水的现象。
热浸锌是在高温下进行的。
对于管形构件应该让其两端开敞。
若两端封闭会造成管内空气膨胀而使封头板爆裂,从而造成安全事故。
若一端封闭则锌液流通不畅,易在管内积存。
2.3热喷铝(锌)复合涂层这是一种与热浸锌防腐蚀效果相当的长效防腐蚀方法。
具体做法是先对钢构件表面作喷砂除锈,使其表面露出金属光泽并打毛。
再用乙炔-氧焰将不断送出的铝(锌)丝融化,并用压缩空气吹附到钢构件表面,以形成蜂窝状的铝(锌)喷涂层(厚度约80μm~100μm)。
最后用环氧树脂或氯丁橡胶漆等涂料填充毛细孔,以形成复合涂层。
此法无法在管状构件的内壁施工,因而管状构件两端必须做气密性封闭,以使内壁不会腐蚀。
这种工艺的优点是对构件尺寸适应性强,构件形状尺寸几乎不受限制。
大到如葛洲坝的船闸也是用这种方法施工的。
另一个优点则是这种工艺的热影响是局部的,受约束的,因而不会产生热变形。
与热浸锌相比,这种方法的工业化程度较低,喷砂喷铝(锌)的劳动强度大,质量也易受操作者的情绪变化影响。
2.4涂层法涂层法防腐蚀性一般不如长效防腐蚀方法(但目前氟碳涂料防腐蚀年限甚至可达50年)。
所以用于室内钢结构或相对易于维护的室外钢结构较多。
它一次成本低,但用于户外时维护成本较高。
涂层法的施工的第一步是除锈。
优质的涂层依赖于彻底的除锈。
所以要求高的涂层一般多用喷砂喷丸除锈,露出金属的光泽,除去所有的锈迹和油污。
现场施工的涂层可用手工除锈。
涂层的选择要考虑周围的环境。
不同的涂层对不同的腐蚀条件有不同的耐受性。
涂层一般有底漆(层)和面漆(层)之分。
底漆含粉料多,基料少。
成膜粗糙,与钢材粘附力强,与面漆结合性好。
面漆则基料多,成膜有光泽,能保护底漆不受大气腐蚀,并能抗风化。
不同的涂料之间有相容与否的问题,前后选用不同涂料时要注意它们的相容性。
涂层的施工要有适当的温度(5~38℃之间)和湿度(相对湿度不大于85%)。
涂层的施工环境粉尘要少,构件表面不能有结露。
涂装后4小时之内不得淋雨。
涂层一般做4~5遍。
干漆膜总厚度室外工程为150μm,室内工程为125μm,允许偏差为25μm。
在海边或海上或是在有强烈腐蚀性的大气中,干漆膜总厚度可加厚为200~220μm。
2.5阴极保护法在钢结构表面附加较活泼的金属取代钢材的腐蚀。
常用于水下或地下结构。
钢腐蚀相关标准:GB/T 1223-1975 不锈耐酸钢晶间腐蚀倾向试验方法GB/T 18982集装箱用腐蚀钢板及刚带GB/T 19285埋地钢制管道腐蚀防护工程检验GB/T 19355钢铁结构耐腐蚀防护锌和铝覆盖层指南GB/T 21447钢制管道外腐蚀控制规程GB/T 22316电镀锡钢板耐腐蚀性试验方法GB/T 23258钢制管道内腐蚀控制规范GB/T 25834金属和合金的腐蚀钢铁户外大气加速腐蚀试验GB/T 28907耐硫酸露点腐蚀钢板和钢带GB/T 31940流体输送用双金属复合耐腐蚀钢管标准GB/T 32120钢结构氧化聚合型包覆防腐蚀技术GB/T 50393钢制石油罐防腐蚀工程技术规范GB/T 8923涂装前钢材表面锈蚀等级和除锈等级GB4172-84焊接结构用耐候钢SY/T 0078-1993钢质管道内腐蚀控制标准SY/T 0087.1-2006钢制管道及储罐腐蚀评价标准埋地钢质管道外腐蚀直接评价SY/T 87-1995钢质管道及储罐腐蚀与防护调查方法标准3船舶腐蚀的种类及解决船体腐蚀的相关措施船舶的防腐措施主要包括防海水腐蚀和防微生物。
3.1船舶防海水腐蚀措施。
船体、压载舱、舵和螺旋桨的防海水腐蚀措要措施有:阴极保护技术和涂料保护,其中螺旋桨是阴极保护技术和涂料保护相互协作,共同防腐。
3.1.1阴极保护技术牺牲阳极保护是利用电化学原理,由活泼金属如锌铝等在海水介质中与钢铁构成电性连接,使钢铁在总体上成为阴极而得到保护。
船舶牺牲阳极主要有锌与锌合金阳极或铝与铝合金阳极,它们有足够负的电位并且很稳定;工作阳极极化小且溶解均匀,腐蚀产物容易脱落;电流效率高等特点。
主要应用于船舶船体、压载舱、舵。
牺牲阳极保护的特点:a)初始费用较低,不需要日常监控;b)寿命较短,坞修时需要更换,维护费用高;c)航行中阳极失落,会造成船体部分得不到保护;d)通过阳极材料的消耗来提供保护电流;e)安装简便可直接焊接或用螺钉固定在船壳上;f)阳极发生电流小,只有有限的自调节输出电流的功能;g)安装阳极数量较多,又突出船壳板,增加航行阻力。
3.1.2外加电流保护外加电流保护系统一般有直流电源、辅助阳极、阳极屏蔽层和参比电极四部分构成。
辅助阳极作用是使电流从电极经介质到被保护体表面,参比电极是用来测量被保护体的电位,并向控制系统传递信号,以护时,可以根据具体情况根据阴极保护的特点选择牺牲阳极还是外加电流法。
通常,小型船舶或低速船采用牺牲阳极保护,大型船舶或航速较高的船,外加电流系统更为适合。
3.1.3其他防腐措施海水管系防腐措施,通常在海水吸入总管或海底阀箱处加装防污和防腐蚀电极。
海水管系防污系统主要通过外加电流的防污电极和防腐蚀电极来实现,通常防污电极材料用电解铜,通过电解后的铜离子杀灭海水中的微生物。
防腐蚀系统通常用纯铁电极或铝电极,或纯铁电极和铝电极同时加用,电解后的铁/铝离子随海水的流动,分布沉积在被保护的管壁上,形成许许多多细小的牺牲阳极,从而达到保护海水管系不被腐蚀。