轧制理论基础
轧制理论基础..
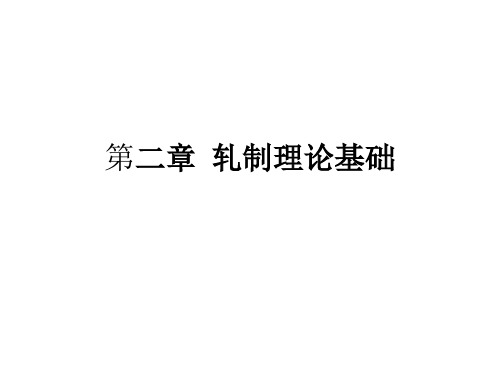
H
bB b 100 % 100 % B B
b ln B l ln L
相对延伸量
lL l 100 % 100 % L L
变形系数的表示法
轧制时表示各向变形系数的关系式
1
或
1
.
ln 1/η +lnω +lnμ =0
3)鼓形宽展
• 轧件侧面变成鼓形而造成的展宽量,用ΔB3表示, 此时轧件的最大宽度为 B3 =B2+ΔB3=B1+ΔB1+ΔB2 +ΔB3
轧件的总展宽量为: ΔB=ΔB1 +ΔB2 +ΔB 3
• 上述宽展的组成及其相互的关系,由下图清楚地 表示出来。
宽展的组成及其相互的关系
4 轧制过程中的纵变形—前滑和后滑
2)提高β的方法
• (1) 改善轧辊或轧件表面状态,以使β升高 • 初轧粗轧在轧辊刻槽焊点滚花等目的均使f升, β升. • 精轧通过立轧高压水去除氧化皮等办法改善轧 件表面状态,使f升, β升. • (2) 合理调节轧制速度 • 利用稳定轧制条件下的剩余摩擦力,采用低速 咬入,高速轧制.
作业
• 已知 某1150轧机钢锭尺寸 880*880/635*635*1400 热轧,该条件下允 许咬入角28°问: • 1)从理论讲,改钢锭如何轧制可使轧件轧一 道次厚度最小,轧后厚度为多大 • 2)求该轧制条件下的最大咬入角和接触弧长.
物理概念
• 根据物理概念: • 摩擦系数可用摩擦角表示,即摩擦角的正 切就是摩擦系数f。 • tgβ=f • 则 tgβ≥tgα • β≥α!!! • 轧制过程中的咬入条件为摩擦角大于咬入 角, Β=α为临界条件。
咬入的几何意义
α
β
轧制理论)轧制原理PPT

开发专门的数值模拟软件,如MSC.Marc、ABAQUS等,可实现轧制过程的可视化模拟, 提高模拟的准确性和效率。
模拟结果验证
通过与实际轧制实验数据的对比,验证计算机模拟结果的准确性和可靠性,为实际生产 提供指导。
人工智能技术在轧制理论中的应用
神经网络模型
应用神经网络模型对轧制过程进行建模和预测,可以实现轧制参数 的优化和自适应控制,提高产品质量和生产效率。
制压力和力矩。
05 轧制过程中的温度场和应力场分析
CHAPTER
温度场分析的基本原理和方法
热传导方程
描述物体内部温度分布随时间变 化的偏微分方程,是温度场分析 的基础。
初始条件和边界条
件
确定热传导方程的解,初始条件 为物体初始时刻的温度分布,边 界条件为物体表面与周围环境之 间的热交换情况。
有限差分法
02 轧制变形基本原理
CHAPTER
轧制变形的基本概念
轧制变形
指金属坯料在两个旋转轧辊的缝 隙中受到压缩,产生塑性变形, 获得所需断面形状和尺寸的加工
方法。
轧制产品
通过轧制变形得到的产品,如板材、 带材、线材、棒材等。
轧制方向
金属在轧辊作用下变形的方向,通 常与轧辊轴线平行。
轧制变形的力学基础
利用塑性变形区的滑移线 场,通过数学解析计算轧 制压力。
上限法
基于塑性变形理论的上限 定理,通过构建速度场计 算轧制压力的上限值。
轧制力矩的计算方法
能量法
根据轧制过程中的能量守恒原理,通过计算变形 功来计算轧制力矩。
解析法
基于弹性力学和塑性力学理论,通过数学解析计 算轧制力矩。
有限元法
利用有限元分析软件,对轧制过程进行数值模拟, 从而计算轧制力矩。
轧钢工艺基础理论培训讲义
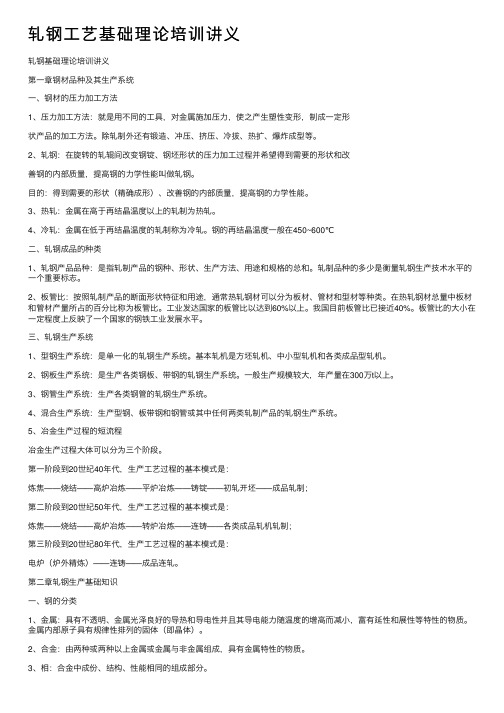
轧钢⼯艺基础理论培训讲义轧钢基础理论培训讲义第⼀章钢材品种及其⽣产系统⼀、钢材的压⼒加⼯⽅法1、压⼒加⼯⽅法:就是⽤不同的⼯具,对⾦属施加压⼒,使之产⽣塑性变形,制成⼀定形状产品的加⼯⽅法。
除轧制外还有锻造、冲压、挤压、冷拔、热扩、爆炸成型等。
2、轧钢:在旋转的轧辊间改变钢锭、钢坯形状的压⼒加⼯过程并希望得到需要的形状和改善钢的内部质量,提⾼钢的⼒学性能叫做轧钢。
⽬的:得到需要的形状(精确成形)、改善钢的内部质量,提⾼钢的⼒学性能。
3、热轧:⾦属在⾼于再结晶温度以上的轧制为热轧。
4、冷轧:⾦属在低于再结晶温度的轧制称为冷轧。
钢的再结晶温度⼀般在450~600℃⼆、轧钢成品的种类1、轧钢产品品种:是指轧制产品的钢种、形状、⽣产⽅法、⽤途和规格的总和。
轧制品种的多少是衡量轧钢⽣产技术⽔平的⼀个重要标志。
2、板管⽐:按照轧制产品的断⾯形状特征和⽤途,通常热轧钢材可以分为板材、管材和型材等种类。
在热轧钢材总量中板材和管材产量所占的百分⽐称为板管⽐。
⼯业发达国家的板管⽐以达到60%以上。
我国⽬前板管⽐已接近40%。
板管⽐的⼤⼩在⼀定程度上反映了⼀个国家的钢铁⼯业发展⽔平。
三、轧钢⽣产系统1、型钢⽣产系统:是单⼀化的轧钢⽣产系统。
基本轧机是⽅坯轧机、中⼩型轧机和各类成品型轧机。
2、钢板⽣产系统:是⽣产各类钢板、带钢的轧钢⽣产系统。
⼀般⽣产规模较⼤,年产量在300万t以上。
3、钢管⽣产系统:⽣产各类钢管的轧钢⽣产系统。
4、混合⽣产系统:⽣产型钢、板带钢和钢管或其中任何两类轧制产品的轧钢⽣产系统。
5、冶⾦⽣产过程的短流程冶⾦⽣产过程⼤体可以分为三个阶段。
第⼀阶段到20世纪40年代,⽣产⼯艺过程的基本模式是:炼焦——烧结——⾼炉冶炼——平炉冶炼——铸锭——初轧开坯——成品轧制;第⼆阶段到20世纪50年代,⽣产⼯艺过程的基本模式是:炼焦——烧结——⾼炉冶炼——转炉冶炼——连铸——各类成品轧机轧制;第三阶段到20世纪80年代,⽣产⼯艺过程的基本模式是:电炉(炉外精炼)——连铸——成品连轧。
轧制原理第一章第一讲

3) 稳定轧制阶段 轧件前端运行出轧辊后,一般情况下就不存在咬入问题了,
。 故此时为稳定轧制阶段,见图1(c)
a
(a)
(b)
(c)
图1 轧制过程三阶段示意
F0 1F1,F1 2 F2,F2 3 F3 ,Fn1 n Fn
而
n
F0 Fn 12 3 n
i
n p
i 1
有
p n
③ 压下率之间的关系
这里指积累压下率与道次压下率(与)之间的关系,根据定
义,积累压下率为 道次压下率为
h0 hn h0
1
h0 h0
h1
2
h1 h2 h1
n
1.1.2 变形区基本参数计算
1. 压下,宽展及延伸变形
设工件在轧制前的尺寸为及(断面积),轧制后变为及 (断面积),则变形区内的高度、宽度及长度方向的变形 参数可列为下表1-1
表1-1 各种变形参数的表示
压下
绝对变形 相对变形 变形系数 对数变形系数
h H h e1 h H H h
lnH h
2. 各参数之间的关系 ① 变形系数之间的关系:
根据体积不变条件,有 H B L h b l 1
h b l 1, 1 1, 也即 ln 1 ln ln 0
H BL
可见变形系数之间满足体积不变条件。
② 延伸系数之间的关系 这里指总延伸系数、道次延伸系数、平均延伸系数,即三者 之间的关系。根据定义,有
宽展 b b B e2 b B b B
lnb B
延伸 l l L e3 l L l L
第一节 轧钢基础知识
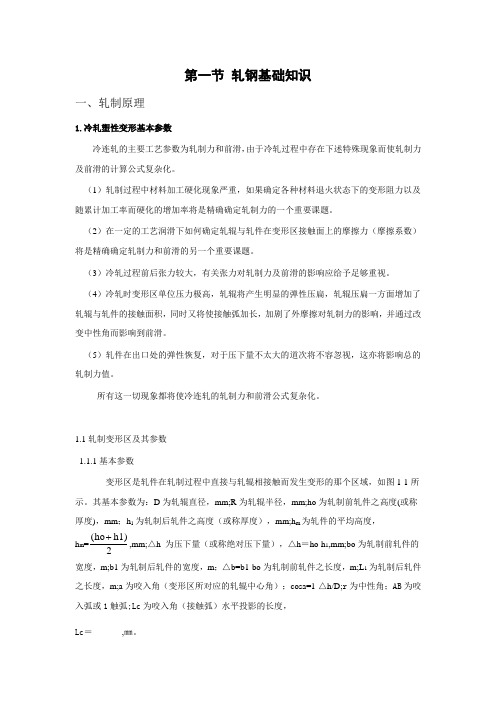
第一节轧钢基础知识一、轧制原理1.冷轧塑性变形基本参数冷连轧的主要工艺参数为轧制力和前滑,由于冷轧过程中存在下述特殊现象而使轧制力及前滑的计算公式复杂化。
(1)轧制过程中材料加工硬化现象严重,如果确定各种材料退火状态下的变形阻力以及随累计加工率而硬化的增加率将是精确确定轧制力的一个重要课题。
(2)在一定的工艺润滑下如何确定轧辊与轧件在变形区接触面上的摩擦力(摩擦系数)将是精确确定轧制力和前滑的另一个重要课题。
(3)冷轧过程前后张力较大,有关张力对轧制力及前滑的影响应给予足够重视。
(4)冷轧时变形区单位压力极高,轧辊将产生明显的弹性压扁,轧辊压扁一方面增加了轧辊与轧件的接触面积,同时又将使接触弧加长,加剧了外摩擦对轧制力的影响,并通过改变中性角而影响到前滑。
(5)轧件在出口处的弹性恢复,对于压下量不太大的道次将不容忽视,这亦将影响总的轧制力值。
所有这一切现象都将使冷连轧的轧制力和前滑公式复杂化。
1.1轧制变形区及其参数1.1.1基本参数变形区是轧件在轧制过程中直接与轧辊相接触而发生变形的那个区域,如图1-1所示。
其基本参数为:D为轧辊直径,mm;R为轧辊半径,mm;ho为轧制前轧件之高度(或称厚度),mm;h1为轧制后轧件之高度(或称厚度),mm;h m为轧件的平均高度,h m=2h1)(ho,mm;△h 为压下量(或称绝对压下量),△h=ho-h1,mm;bo为轧制前轧件的宽度,m;b1为轧制后轧件的宽度,m;△b=b1-bo为轧制前轧件之长度,m;L1为轧制后轧件之长度,m;a为咬入角(变形区所对应的轧辊中心角);cosa=1-△h/D;r为中性角;AB为咬入弧或1触弧;Lc为咬入角(接触弧)水平投影的长度,Lc=,㎜。
1.1.2 变形系数轧制时轧件塑性变形,使轧件尺寸在三个方向上都发生了变化,即:轧制之高度由ho减少到h1,比值h1/ho=η为轧件高度方向上的变形,η叫做压下系数。
图1-1 变形区基本参数轧件之宽度bo增加到b1,比值b1/bo=X为轧机宽度方向上的变形,X叫做宽度系数。
轧钢基础知识2

19、轧制速度:轧制速度就是与金属接触处的轧辊圆 周速度。
20、终轧速度:最后一架轧机的速度即成品架速度称 之为终轧速度。 21、升速轧制:轧制带钢时,低速穿带的带钢头部被 卷取机咬住之后,带钢与卷取机同步升速进行高速轧制 的方法。 22、连轧和连轧常数:一根轧件同时在几架轧机上轧 制并保持在单位时间内轧件通过各轧机的体积相等的轧 制叫连轧。单位时间内通过每架轧机的金属体积等于一 个常数,这个常数就叫连轧常数。 23、张力:在连轧过程中,前后两架轧机存在金属秒 流量差,当后架的秒流量大于前架时,造成前、后架之 间的轧件受到前架轧机的拉力作用,此力通常称为张力。
C、摩擦系数的影响 摩擦系数和宽展成正比,这是因为摩擦系数增加时,金属纵向流动所受 的阻力比横向流动所受到的阻力增加得快,这就是说,凡是影响摩擦系 数的因素对宽展都有影响。生产过程中,钢种的更换对摩擦系数 值影响 很大。在编制作业计划时应尽量避免频繁调换钢种。 D、轧制速度的影响 当轧制速度超过2-3m/s时,摩擦系数值随着速度增加而急剧下降,这就 影响到宽展,因摩擦系数 减小,宽展亦随之减小。源自变形抗力的概念
金属是由原予组成的质点系统.在原子间除有引力外,还有 斥力存在.当原子间的距离较大时,原子间的相互作用表现 为引力;随着距离的减小,斥力比引力增大的快,因此在距 离较小时斥力将超过引力,原子间的作用将表现为斥力。当 原子间的吸引力和斥力相互平衡时,原子的势能最低,原子 所处的位置将是稳定平衡位置,此时我们称物体处于自由状 态。 当有外力作用于物体上时,原子将离开其稳定平衡位置而 被激发。结果物体的势能增高并且产生尺寸和形状的弹性改 变。被激发的原子力图回到其稳定平衡位置上去,原子偏离 离稳定平衡位置愈严重.力图回到稳太平衡放置的趋向愈大。 随着外力的增大,原子相对其本身稳定平衡位置的偏离将 增大,当超过一定数值时,原子即转向新的稳定平衡位置, 结果物体开始产生塑性变形。可见塑性变形的单元过程乃是 大量原子定向地由一些稳定平衡位置向另一些稳定平衡体置 的非同步地移动。这种过程的多次重演,将使物体的尺寸和 形状产生可觉察的塑性改变。
轧制理论基础
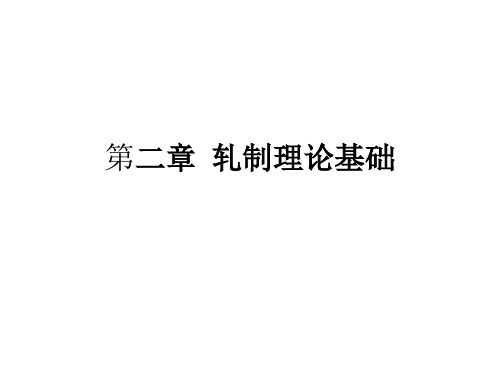
水平合力 :
∑ F = T cos α − p sin α 当 ∑ F ≥ 0 轧件才可能被咬入
x x
, 完成轧制 .
结论
T sin α ≥ ≥ tgα ⇒ P cos α f ≥ tgα (咬入条件) 说明咬入角的正切等于 轧件与轧辊之间的摩擦系数
物理概念
• 根据物理概念: • 摩擦系数可用摩擦角表示,即摩擦角的正 切就是摩擦系数f。 • tgβ=f • 则 tgβ≥tgα • β≥α!!! !!! • 轧制过程中的咬入条件为摩擦角大于咬入 角, Β=α为临界条件。
①等径
α
B C
Δh/2
A
由几何关系 : L = R −
2 2
∆h R− 2
2
D
得L = R ⋅ ∆h −
∆h 2 ( ) 2
= R ⋅ ∆h
② 不等径
L1 R1 R1 − ∆h1
2
=
2
−
(
)
2
= 2
R1 ∆h ∆h1
1− 2
2
L1≈ D1∆h1 L R R 2 − ∆h 2
• 纵轧:金属在两个旋转方向相反的轧辊之间通过,并 纵轧: 金属在两个旋转方向相反的轧辊之间通过, 两个旋转方向相反的轧辊 之间通过 在其间产生塑性变形的过程。 在其间产生塑性变形的过程。 • 横轧 :轧件变形后运动方向与轧辊轴线方向一致 轧件变形后运动方向与轧辊轴线方向一致 • 斜轧:轧件作螺旋运动,轧件与轧辊轴线非特角 斜轧:轧件作螺旋运动, 螺旋运动
第二章 轧制理论基础 二章
• • • • • • •
1 轧制变形基本概念 2 实现轧制过程的条件 3 轧制过程中的横变形宽展 4 轧制过程中的纵变形――前滑与后滑 5 轧制压力及力矩 6 连轧 7 斜轧
轧制加工基础知识
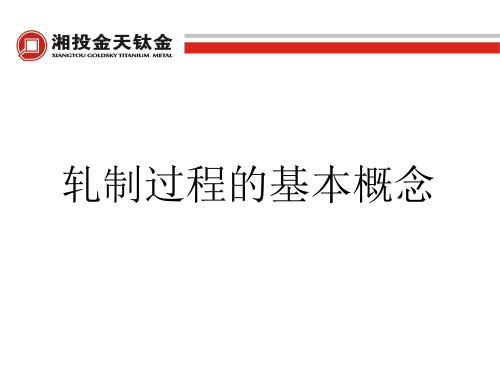
实际与理论的不同 并不否定简单轧制情况的理论学习意义 非简单轧制情况: 张力轧制、变速轧制、异步轧制、孔型轧制 简单轧制的非理想情况: 变形沿轧件断面高度和宽度不是完全均匀的 金属质点沿轧件断面高度和宽度运动速度不是均匀的 是加速过程而非匀速过程 轧制压力和摩擦力沿接触弧长度上分布不是均匀的 摩擦-粘着状态不是确定的 轧机轧辊不是刚性的
2
T P tan
2 T P
tan f
tan
2
2
可见:按照金属进入轧辊的程度,咬入条件向有利 的一方面转化,亦即最初咬入时,所需的摩擦条件 最高。随轧件逐渐进入轧辊,越易咬入。
3 中性面—相对运动(水平)、绝对运动
中性面对应的圆心角叫中性角,常用γ表示。 金属质点相对轧辊向入口流动形成后滑。 金属质点相对轧辊向出口流动形成前滑。 向两侧流动形成宽展。 前滑和后滑是相对轧辊的。 但绝对速度是向前的。
v h v v H
轧件出口速度大于轧辊圆周速度
vh v
轧件入口速度小于轧辊入口处 水平分速度
v H v co s
中性面处轧件水平速度等 于此处轧辊水平速度
v v co s
问答: 1 在中性面处,哪两个速度相等? 思考: 根据上边的初步分析,已经揭示了轧制过程的内在矛盾:如要加大压下量以 提高轧机生产能力,根据咬入条件则应增加摩擦,但由于金属质点与轧辊表面有 相对滑动,摩擦增加导致轧辊磨损,是轧件表面质量变坏,而且增加了力、能消 耗。为了解决这一矛盾,在开坯轧机,咬入条件成为主要矛盾时,甚至在轧辊上 人为刻痕,以增加摩擦改善咬入条件来提高压下量。而当冷轧薄板时,表面质量 成为组要矛盾时,则采用润滑剂来降低摩擦,改善表面质量,同时降低力、能消 耗。 从公式Δh=D(1-cosα)和咬入条件α≤β可知,在相同摩擦条件下,增加辊径可 以提高压下量,同时可以提高轧辊强度,这是有利的一面。但是随着辊径增加, 接触弧长度增加,因而使应力状态增强,引起轧制力急剧增加。这是不利的一面。 当轧薄板道次压下量不大而工具强度和刚度成为主要矛盾时,不得不采用小直径 轧辊的轧机来生产,这时要采用支撑辊,因而引起了轧机辊系结构的复杂化。 下节课讲各类型的轧机。
轧制理论知识点
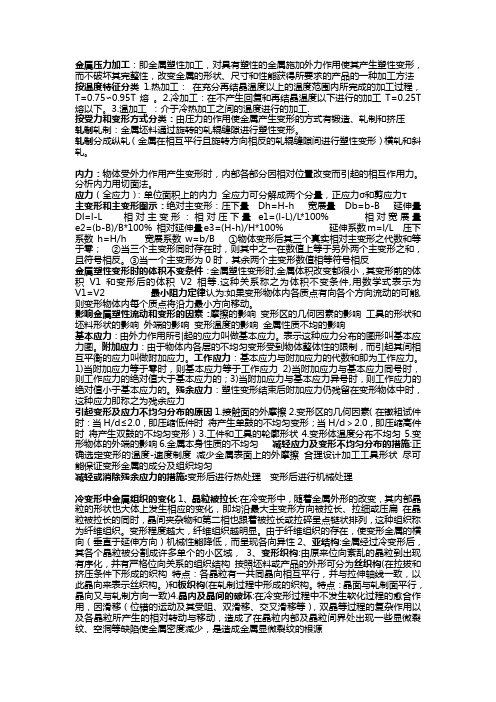
金属压力加工:即金属塑性加工,对具有塑性的金属施加外力作用使其产生塑性变形,而不破坏其完整性,改变金属的形状、尺寸和性能获得所要求的产品的一种加工方法按温度特征分类1.热加工:在充分再结晶温度以上的温度范围内所完成的加工过程,T=0.75∽0.95T熔。
2.冷加工:在不产生回复和再结晶温度以下进行的加工T=0.25T 熔以下。
3.温加工:介于冷热加工之间的温度进行的加工.按受力和变形方式分类:由压力的作用使金属产生变形的方式有锻造、轧制和挤压轧制轧制:金属坯料通过旋转的轧辊缝隙进行塑性变形。
轧制分成纵轧(金属在相互平行且旋转方向相反的轧辊缝隙间进行塑性变形)横轧和斜轧。
内力:物体受外力作用产生变形时,内部各部分因相对位置改变而引起的相互作用力。
分析内力用切面法。
应力(全应力):单位面积上的内力全应力可分解成两个分量,正应力σ和剪应力τ主变形和主变形图示:绝对主变形:压下量Dh=H-h 宽展量Db=b-B 延伸量Dl=l-L 相对主变形:相对压下量e1=(l-L)/L*100% 相对宽展量e2=(b-B)/B*100% 相对延伸量e3=(H-h)/H*100% 延伸系数m=l/L 压下系数h=H/h 宽展系数w=b/B ①物体变形后其三个真实相对主变形之代数和等于零;②当三个主变形同时存在时,则其中之一在数值上等于另外两个主变形之和,且符号相反。
③当一个主变形为0时,其余两个主变形数值相等符号相反金属塑性变形时的体积不变条件:金属塑性变形时,金属体积改变都很小,其变形前的体积V1和变形后的体积V2相等.这种关系称之为体积不变条件,用数学式表示为V1=V2 最小阻力定律认为:如果变形物体内各质点有向各个方向流动的可能,则变形物体内每个质点将沿力最小方向移动。
影响金属塑性流动和变形的因素:摩擦的影响变形区的几何因素的影响工具的形状和坯料形状的影响外端的影响变形温度的影响金属性质不均的影响基本应力:由外力作用所引起的应力叫做基本应力。
轧制理论基础
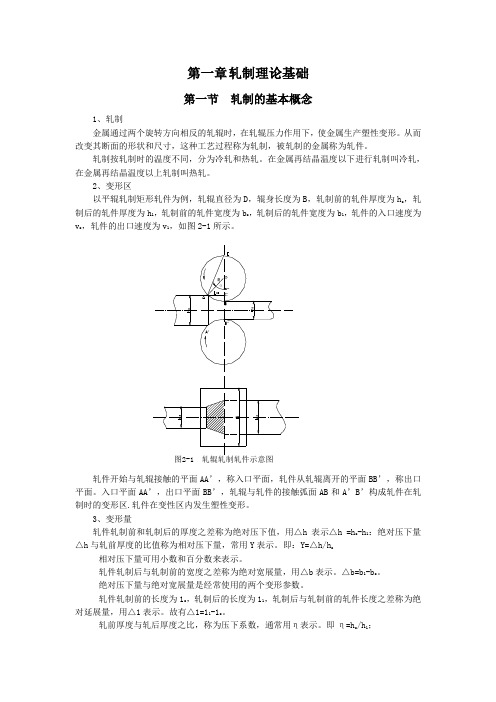
第一章轧制理论基础第一节轧制的基本概念1、轧制金属通过两个旋转方向相反的轧辊时,在轧辊压力作用下,使金属生产塑性变形。
从而改变其断面的形状和尺寸,这种工艺过程称为轧制,被轧制的金属称为轧件。
轧制按轧制时的温度不同,分为冷轧和热轧。
在金属再结晶温度以下进行轧制叫冷轧,在金属再结晶温度以上轧制叫热轧。
2、变形区以平辊轧制矩形轧件为例,轧辊直径为D,辊身长度为B,轧制前的轧件厚度为ho,轧制后的轧件厚度为h1,轧制前的轧件宽度为bo,轧制后的轧件宽度为b1,轧件的入口速度为v o ,轧件的出口速度为v1,如图2-1所示。
轧件开始与轧辊接触的平面AA’,称入口平面,轧件从轧辊离开的平面BB’,称出口平面。
入口平面AA’,出口平面BB’,轧辊与轧件的接触弧面AB和A’B’构成轧件在轧制时的变形区.轧件在变性区内发生塑性变形。
3、变形量轧件轧制前和轧制后的厚度之差称为绝对压下值,用△h表示△h =ho -h1:绝对压下量△h与轧前厚度的比值称为相对压下量,常用Y表示。
即:Y=△h/ho 相对压下量可用小数和百分数来表示。
轧件轧制后与轧制前的宽度之差称为绝对宽展量,用△b表示。
△b=b1-bo。
绝对压下量与绝对宽展量是经常使用的两个变形参数。
轧件轧制前的长度为1o ,轧制后的长度为11,轧制后与轧制前的轧件长度之差称为绝对延展量,用△1表示。
故有△1=11-1o。
轧前厚度与轧后厚度之比,称为压下系数,通常用η表示。
即η=ho /h1;轧后宽度与轧前宽度之比,称为侧压系数,通常用k 表示。
即 k=b 1/b 0; 轧后长度与轧前长度之比,称为延伸系数,通常用μ表示。
即μ=l 1/l 0。
4、咬入弧与咬入角轧辊与轧件接触部分的A ⌒B 和A ’⌒B ’弧称为咬入弧(又称接触弧)。
与咬入弧 A ⌒B 和A ’⌒B ’所对应的圆心角α称为咬入角。
由图2-1中的几何关系可知,△ABC ∽△EBA ,由此可得: AB 2=BE ⨯BC 式中 BE=2R BC=(h o -h 1)/2=△h/2所以咬入弧所对的弦长AB=hR ∆。
冷轧基础理论知识
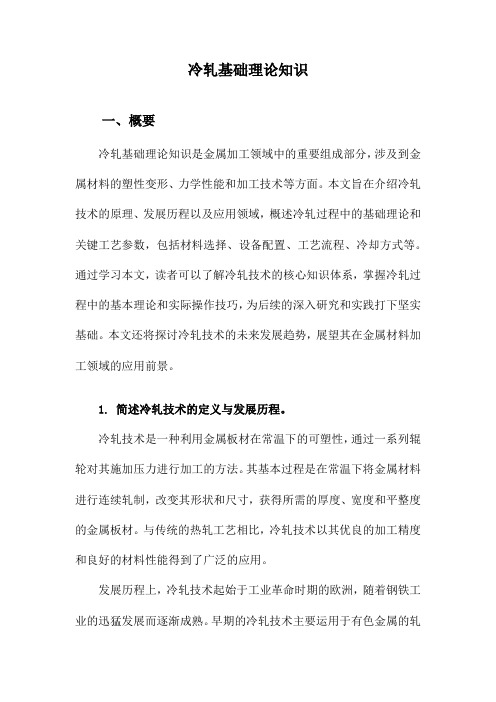
冷轧基础理论知识一、概要冷轧基础理论知识是金属加工领域中的重要组成部分,涉及到金属材料的塑性变形、力学性能和加工技术等方面。
本文旨在介绍冷轧技术的原理、发展历程以及应用领域,概述冷轧过程中的基础理论和关键工艺参数,包括材料选择、设备配置、工艺流程、冷却方式等。
通过学习本文,读者可以了解冷轧技术的核心知识体系,掌握冷轧过程中的基本理论和实际操作技巧,为后续的深入研究和实践打下坚实基础。
本文还将探讨冷轧技术的未来发展趋势,展望其在金属材料加工领域的应用前景。
1. 简述冷轧技术的定义与发展历程。
冷轧技术是一种利用金属板材在常温下的可塑性,通过一系列辊轮对其施加压力进行加工的方法。
其基本过程是在常温下将金属材料进行连续轧制,改变其形状和尺寸,获得所需的厚度、宽度和平整度的金属板材。
与传统的热轧工艺相比,冷轧技术以其优良的加工精度和良好的材料性能得到了广泛的应用。
发展历程上,冷轧技术起始于工业革命时期的欧洲,随着钢铁工业的迅猛发展而逐渐成熟。
早期的冷轧技术主要运用于有色金属的轧制,随着技术的进步,逐渐扩展到黑色金属的轧制领域。
随着材料科学和工艺技术的不断进步,冷轧技术也在不断地发展。
从简单的单机轧制到现代化的连续自动化生产线,从传统的模拟控制到数字化和智能化控制,冷轧技术已经成为现代制造业不可或缺的重要工艺手段。
其发展历程不仅体现了技术的进步,也反映了人类对材料性能的不断追求和探索。
2. 阐述冷轧技术在工业领域中的重要性。
冷轧技术在工业领域中的重要性不言而喻。
随着现代工业的发展,对于材料性能的要求越来越高,而冷轧技术作为一种先进的金属加工技术,能够满足这种高性能的需求。
冷轧过程通过控制金属的塑性变形和再结晶行为,可以显著提高金属的强度和硬度,同时保持良好的韧性和表面质量。
这使得冷轧材料在汽车、航空、建筑、电子等多个行业中得到广泛应用。
在汽车行业,冷轧技术用于生产高质量的钢板和带材,用于制造车身、发动机等关键部件。
轧制理论)轧制原理

轧制理论的发展趋势与未来展望
1 2
智能化发展
随着人工智能和大数据技术的应用,轧制理论的 智能化发展成为趋势,实现轧制过程的自动化和 智能化控制。
新材料和新工艺研究
未来轧制理论将继续在新材料、新工艺的研究方 面发挥重要作用,推动行业的创新发展。
3
绿色可持续发展
轧制理论将注重绿色可持续发展,致力于降低能 耗和减少环境污染,实现行业的可持续发展。
轧制理论)轧制原理
目录
量 • 轧制过程的模拟与优化 • 轧制理论的应用与发展
01
轧制原理概述
轧制的基本概念
轧制是一种金属加工工艺,通过两个 旋转的轧辊将金属坯料压缩,使其发 生塑性变形,从而获得所需形状和性 能的金属制品。
轧制过程中,金属坯料通过轧辊的摩 擦力作用被牵引,经过连续的塑性变 形,形成一定规格和形状的成品或半 成品。
智能算法进行故障诊断和预警,提高轧制过程的稳定性和可靠性。
05
轧制理论的应用与发展
轧制理论在钢铁工业中的应用
轧制工艺优化
轧制理论为钢铁工业提供了优化轧制工艺的方法,提高了产品质 量和生产效率。
新材料研发
轧制理论在新材料研发中发挥了重要作用,推动了钢铁材料的不 断升级和革新。
节能减排
轧制理论的应用有助于钢铁工业实现节能减排,降低生产过程中 的能耗和污染物排放。
利用测厚系统实时监测板材厚度, 反馈调整轧制参数,以实现厚度 控制的自动化和精细化。
04
轧制过程的模拟与优化
轧制过程的数值模拟技术
有限元法
01
通过将轧制过程划分为一系列小的单元,利用数学方程描述每
个单元的行为,从而模拟整个轧制过程。
有限差分法
轧制理论
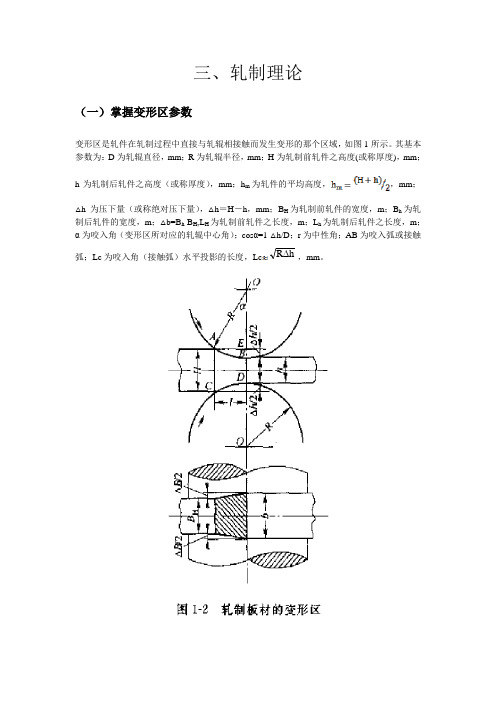
三、轧制理论(一)掌握变形区参数变形区是轧件在轧制过程中直接与轧辊相接触而发生变形的那个区域,如图1所示。
其基本参数为:D为轧辊直径,mm;R为轧辊半径,mm;H为轧制前轧件之高度(或称厚度),mm;h为轧制后轧件之高度(或称厚度),mm;h m为轧件的平均高度,,mm;△h 为压下量(或称绝对压下量),△h=H-h,mm;B H为轧制前轧件的宽度,m;B h为轧制后轧件的宽度,m;△b=B h-B H,L H为轧制前轧件之长度,m;L h为轧制后轧件之长度,m;α为咬入角(变形区所对应的轧辊中心角);cosα=1-△h/D;r为中性角;AB为咬入弧或接触R ,mm。
弧;Lc为咬入角(接触弧)水平投影的长度,Lc hΔh=D(1-)(二)轧辊咬入轧件的条件为建成轧制过程,必须使轧辊咬人轧件,只有当轧件上作用有外力,使其紧贴在轧辊上时才可能咬入。
这种使轧件紧贴轧辊的力,可能是轧件运动的惯性力,也可能是由施力装置给的,还可以是轧钢工喂入时的撞击力。
在这种力作用下,轧辊与轧件前端接触,前端边缘被挤压时产生摩擦力,由摩擦力把轧件拽入辊缝中。
分析轧件拽入时的平衡条件(见图1-5),应当是有利于咬入的水平投影力的总和大于阻碍咬入的水平投影力的总和:(Q-F)+2Tx>2Px式中:Px――正压力P的水平投影;Tx――摩擦力T的水平投影;Q――外推力F――惯性力采用库仑摩擦定律,则有,式中,――咬入角――边缘挤压角当时,P=T;T/P=/==μ。
咬入角α的正切等于轧件与轧辊之间的摩擦系数μ时,是咬入的临界条件,当时,能咬入,如果时,则不能咬入。
根据物理概念,摩擦系数可以用摩擦角来表示,亦即摩擦角β的正切就是摩擦系数μ,,即轧制过程之咬入条件为摩擦角β大于咬入角α。
(三)轧制时的前滑、后滑轧件在轧制时,高度方向受压下的金属一部分流向纵向,使轧件伸长,另一部分流向横向,使轧件展宽,轧件的延伸是被压下金属向轧辊入口和出口两方面流动的结果;轧件进入轧辊的速度小于轧辊在该点处线速度v的水平分量;而轧件的出口速度大于轧辊在该处的线速度v这种>v的现象叫做前滑,而<的现象叫做后滑。
必学-金属材料热处理轧制原理基本理论知识
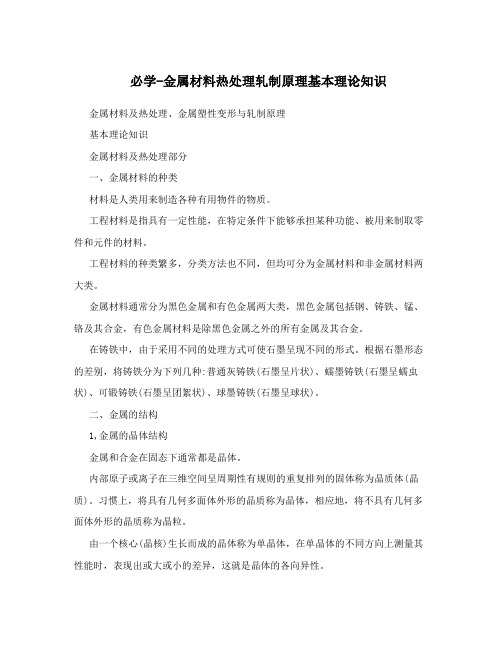
必学-金属材料热处理轧制原理基本理论知识金属材料及热处理、金属塑性变形与轧制原理基本理论知识金属材料及热处理部分一、金属材料的种类材料是人类用来制造各种有用物件的物质。
工程材料是指具有一定性能,在特定条件下能够承担某种功能、被用来制取零件和元件的材料。
工程材料的种类繁多,分类方法也不同,但均可分为金属材料和非金属材料两大类。
金属材料通常分为黑色金属和有色金属两大类,黑色金属包括钢、铸铁、锰、铬及其合金,有色金属材料是除黑色金属之外的所有金属及其合金。
在铸铁中,由于采用不同的处理方式可使石墨呈现不同的形式。
根据石墨形态的差别,将铸铁分为下列几种:普通灰铸铁(石墨呈片状)、蠕墨铸铁(石墨呈蠕虫状)、可锻铸铁(石墨呈团絮状)、球墨铸铁(石墨呈球状)。
二、金属的结构1,金属的晶体结构金属和合金在固态下通常都是晶体。
内部原子或离子在三维空间呈周期性有规则的重复排列的固体称为晶质体(晶质)。
习惯上,将具有几何多面体外形的晶质称为晶体,相应地,将不具有几何多面体外形的晶质称为晶粒。
由一个核心(晶核)生长而成的晶体称为单晶体,在单晶体的不同方向上测量其性能时,表现出或大或小的差异,这就是晶体的各向异性。
金属材料通常由许多不同位向的小晶粒所组成,称为多晶体;多晶体中各晶粒的各向异性互相抵消,故一般不显示各向异性,所以在工业用的金属材料中,通常见不到各向异性特征,称之为伪各向同性。
工业上使用的金属元素中,除了少数具有复杂的晶体结构外,绝大多数都具有比较简单的晶体结构,其中最典型、最常见的金属晶体结构有三种类型,即体心立方结构,面心立方结构和密排六方结构。
2,金属的同素异构转变大部分金属只有一种晶体结构,但也有少数金属如Fe、Mn、Ti、Co等具有两种或几种不同的晶体结构,即具有多晶型。
当外部条件(如温度和压力)改变时,金属可能由一种晶体结构转变成另一种晶体结构。
这种固态金属在不同温度下具有不同晶格的现象称为多晶型性或同素异晶性。
轧制理论

咬入之后,在金属逐渐充填变形区的过程中,径向力的合力作用点相应地
向轧件出口平面方向移动,而使合力作用方向逐渐向出口倾斜。因此而使得Tx逐 步增加,Nx相应减少。这样一来,摩擦力的水平分力就有了剩余,其值为Tx-Nx。 由于剩余摩擦力的出现,而使得轧件一旦被咬入,就能更顺利地使轧件充满变形
由置于出口和入口两侧的测厚仪,测出带钢厚度,反馈到高速的计算机系统,再去控制 一个“电--液压”系统来实现对带钢厚度的控制。
测厚仪简图
3.2.AGC系统控制方法
➢前 馈:把前面的测厚仪测得厚度与目标厚度相比。 ➢后 馈:把后面的测厚仪测得厚度与目标厚度相比,只有1pass时使用 。 ➢质量流:轧机出入口的秒流量相等的原理控制,左右测厚仪同时使用
轧辊把轧件拉入旋转方向相反的两个轧辊辊缝 之中叫轧件的咬入。轧辊能够顺利地将轧件咬入是 轧制的必要条件。 轧件与轧辊接触时,轧辊对轧件的作用力和摩擦 力如图所示。N和T分解成的水平分力为:
不能咬入 临界状态 可以咬入 设摩擦角为β,则摩擦系数:
图3 轧辊对轧件的作用力和摩擦力
可以推出:
3.2.轧制过程建立
延伸率是带钢长度变化率,其表示式为: 在忽略宽展时,延伸率μ与压下率ε有如下关系:
2.SPM的目的
➢消除退火带钢的屈服平台,改善力学性能,保证产品的成形加工性; ➢修正板形,改善平直度; ➢根据用户的使用要求,加工光面或麻面板,并改善表面质量。
中性面:在整个变形区中,存在一个前后滑的过渡面。轧件在该面上运动的速度与 该处轧辊线速度的水平分速度相等,这个平面就叫中性面。由出口平面到中性面称 前滑区,由入口平面到中性面称后滑区。
5.2前滑的计算式
如图,在中性面轧件运动的速度与轧辊水平分速度相等,即 中性面与出口截面的秒体积相等,并忽略宽展时,可得 上式,经整理得到 :
冷轧工序轧制基础理论培训教学大纲

冷轧工序轧制基础理论培训教学大纲(初级)一、教学目的和要求本课程设置的目的是使学员了解基本的轧制原理及影响冷轧变形的基本因素二、课程内容第一章金属塑性变形的实质教学要求:掌握金属变形及应力的产生与计算,了解变形过程,金属的弹性、塑性变形的基本概念教学内容:1、金属变形及其应力2、金属弹性变形、塑性变形第二章塑性变形及对性能的影响教学要求:掌握金属受压力加工时的受力条件,冷热变形的特点及对性能的影响,了解恢复和实用文档再结晶的概念教学内容:1、冷变形、热变形、冷热轧区别2、冷变形对金属组织和性能的影响3、恢复、再结晶第三章塑性变形的基本理论教学要求:掌握塑性变形的基本原理,了解轧制中的体积不变和最小阻力定律教学内容:1、体积不变定律2、最小阻力定律第四章轧制过程参数及其表示方法教学要求:了解变形过程的各参数的意义,了解变形区长度、变形系数、压下量、宽展量、延伸量的概念及咬入条件实用文档教学内容:1、变形区及其计算2、变形系数(压下、宽展、延伸系数的概念)3、绝对压下量,相对压下量、宽展量、延伸量及表示方法4、不均匀变形及对产品的影响5、轧辊咬入金属的条件6、咬入角,轧辊直径与压下量之间的关系7、影响咬入的因素第五章轧制中的宽展、延伸、前后滑及其影响因素教学要求:掌握轧制中几种变形现象的产生原因及影响因素教学内容:1、宽展及影响因素2、轧制中金属的前后滑3、影响前后滑的因素第六章金属对轧辊的压力实用文档教学要求:掌握轧制中变形抗力,轧制压力,接触面积及单位压力分布规律教学内容:1、轧制压力,接触面积2、轧制中金属的前后滑3、影响变形抗力的因素第七章特殊条件下的轧制教学要求:掌握特殊轧制过程中受力状态变化,轧制过程,特殊轧制的优缺点及应用教学内容:1、张力轧制2、异步轧制第八章轧制中的不均匀变形教学要求:实用文档掌握轧制中变形不均匀的产生对产品质量的影响教学内容:1、不均匀变形产生的原因2、不均匀变形产生的后果实用文档。
轧钢
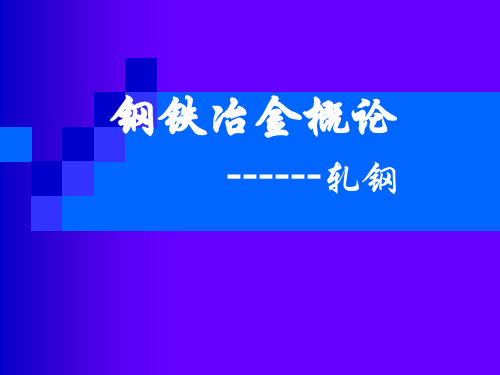
2.变形区的主要参数
1)轧制时的变形区:图示ABCD所围
成的区域;
2)接触弧长度(咬入弧长度)(l):
轧件和轧辊相接触的圆弧的水平投影长 度;
⑵按其用途分:
* 常用型钢(方钢、圆钢、扁钢、角钢、槽钢、工字钢等); * 特殊用途型钢(钢轨、钢桩、球扁钢、窗框钢、汽车挡圈等)。
⑶按其生产方法分:
* 轧制型钢、弯曲型钢、焊接型钢等。
简单断面型钢
简 单 断 面Leabharlann 型 钢①方钢:用断面边长尺寸的毫米数表示规格,规格范围:4~250mm, 可用来制造各种设备的零部件等。
l Rh
R-轧辊工作半径; △h-该道次的压下量, △h=H-h。
3)咬入角(α):轧件和轧辊所接触
的圆弧对应的轧辊的圆心角。
R/h
4)压下量、轧辊直径和咬入角的关系 △h=D(1-cosα)
3.纵轧变形的表示方法
⑴ 绝对变形量表示方法
压下量 宽展量 延伸量
△h=H-h
⑶ 变形系数表示法
(2)质量增加的方法:
铸造、电解沉积、焊接与铆接、烧结与胶结等;
(3)质量保持不变的方法:
金属压力加工(轧制、锻造、冲压、拉拔、挤压)。
2.金属压力加工的方法
★金属压力加工:
金属在受到外力作用并不破坏自身完整性的条件下, 稳定改变其几何形状与尺寸,从而获得所需要的几何形状 与尺寸的加工方法。
★金属压力加工的分类:
三. 轧钢生产基本问题
1.轧制钢材的品种及用途 2.轧钢机
- 1、下载文档前请自行甄别文档内容的完整性,平台不提供额外的编辑、内容补充、找答案等附加服务。
- 2、"仅部分预览"的文档,不可在线预览部分如存在完整性等问题,可反馈申请退款(可完整预览的文档不适用该条件!)。
- 3、如文档侵犯您的权益,请联系客服反馈,我们会尽快为您处理(人工客服工作时间:9:00-18:30)。
2)提高β的方法
• (1) 改善轧辊或轧件表面状态 以使 升高 改善轧辊或轧件表面状态,以使 以使β升高 • 初轧粗轧在轧辊刻槽焊点滚花等目的均使 升, 刻槽焊点滚花等目的均使 初轧粗轧在轧辊刻槽焊点滚花等目的均使f升 β升. 升 • 精轧通过立轧高压水去除氧化皮等办法改善轧 精轧通过立轧高压水去除氧化皮 去除氧化皮等办法改善轧 件表面状态,使 升 升 件表面状态 使f升, β升. • (2) 合理调节轧制速度 • 利用稳定轧制条件下的剩余摩擦力 采用低速 利用稳定轧制条件下的剩余摩擦力,采用 采用低速 咬入,高速轧制 高速轧制. 咬入 高速轧制
α = arcCos1 − D ∆h一定D增加α降, D一定∆h降α降.
•实际生产中以带有楔形端咬入后利用稳定轧制阶段剩余摩擦力,实现咬入 实际生产中以带有楔形端咬入后利用稳定轧制阶段剩余摩擦力 实现咬入 实际生产中以带有楔形端咬入后利用稳定轧制阶段剩余摩擦力 实现咬入. •利用外推力将轧件强制推入轧辊中 外力作用使轧件前端被压扁 相当于楔形外 利用外推力将轧件强制推入轧辊中,外力作用使轧件前端被压扁 利用外推力将轧件强制推入轧辊中 外力作用使轧件前端被压扁,相当于楔形外 端降低压下量,有利于咬入 有利于咬入. 端降低压下量 有利于咬入
第二章 轧制理论基础 二章
• • • • • • •
1 轧制变形基本概念 2 实现轧制过程的条件 3 轧制过程中的横变形宽展 4 轧制过程中的纵变形――前滑与后滑 5 轧制压力及力矩 6 连轧 7 斜轧
1轧制变形区的概念及轧制变形基本理论
• 1.1轧制过程及分类: • 1)轧制过程 轧件由摩擦力拉进旋转轧辊 轧制过程: 旋转轧辊之间, 轧制过程 旋转轧辊 受到压缩进行塑性变形的过程,通过轧制使金 属具有一定尺寸、形状和性能。 一定尺寸、 一定尺寸 形状和性能。 • 2) 分类 轧制方式按轧件运动分:有纵轧、横轧、斜轧 纵轧、 纵轧 横轧、斜轧。
轧制时表示各向变形系数的关系式
1
η
或
⋅ω ⋅ µ = 1
η = µ.ω
ln 1/ +lnω+lnμ=0 1/η ln ln =0
l 式中 μ= —延伸系数 L b ω = .宽展系数 B H η = 压下系数 h
5)变形区参数
α
B C
D
Δb/2
Δh/2
A
• (1)咬入角:α 是 指轧件开始轧入轧辊 时,轧件和轧辊最先 接触的点和轧辊中 心连线与轧辊中心 心连线 轧辊中心 圆心角。 线所构成的圆心角 圆心角
作业
• 已知 某1150轧机钢锭尺寸 880*880/635*635*1400 热轧,该条件下允 许咬入角28°问: • 1)从理论讲,改钢锭如何轧制可使轧件轧一 道次厚度最小,轧后厚度为多大 • 2)求该轧制条件下的最大咬入角和接触弧长.
1.3 轧制过程中横变形 宽展 轧制过程中横变形---宽展 • 1.3.1宽展及其分类 1、宽展与研究宽展的意义 1)宽展:在轧制过程中,当轧件受到压下后, 金属除按最小阻力法则沿纵向延伸外,在 横向也产生变形,称之为横变形。轧制前、 后轧件沿横向尺寸的绝对差值,称为绝对 宽展简称为宽展.
①等径
α
B C
Δh/2
A
由几何关系 : L = R −
2 2
∆h R− 2
2
D
得L = R ⋅ ∆h −
∆h 2 ( ) 2
= R ⋅ ∆h
② 不等径
L1 R1 R1 − ∆h1
2
=
2
−
(
)
2
= 2
R1 ∆h ∆h1
1− 2
2
L1≈ D1∆h1 L R R 2 − ∆h 2
其他分类
根据金属状态分: 热轧、冷轧。 根据金属状态分 热轧、冷轧。 根据外部介质分类: 空气,真空, 惰性气体 轧机工作制度: 可逆 连轧 等
2)轧制过程中基本现象和建立轧制过程的条件
• 在生产实践中遇到不同的轧辊组合方式 不同的轧辊组合方式,但实际上金属 不同的轧辊组合方式 承受压下而产生塑性变形是在一对工作轧辊中进行的。 特殊辊系结构(如行星轧机,Y型轧机)外, • 除了一些特殊辊系结构 特殊辊系结构 均在一对轧辊 一对轧辊间轧制的简单情况。 一对轧辊 二辊作为研究轧制过程的开端。 • 一般都以二辊 二辊
• 纵轧:金属在两个旋转方向相反的轧辊之间通过,并 纵轧: 金属在两个旋转方向相反的轧辊之间通过, 两个旋转方向相反的轧辊 之间通过 在其间产生塑性变形的过程。 在其间产生塑性变形的过程。 • 横轧 :轧件变形后运动方向与轧辊轴线方向一致 轧件变形后运动方向与轧辊轴线方向一致 • 斜轧:轧件作螺旋运动,轧件与轧辊轴线非特角 斜轧:轧件作螺旋运动, 螺旋运动
H −h ∆h ×100% = ×100% H H
相对压下量 相对宽展量 相对延伸量
H −h ×100% h h ln
b−B × 100% b l−L × 100% l
H
b−B ∆b ×100% = ×100% B B
b ln B l ln L
l−L ∆l × 100% = × 100% L L
变形系数的表示法
2、宽展的种类
• 根据金属沿横向上流动的自由程度,宽展可分为:自 根据金属沿横向上流动的自由程度,宽展可分为: 由宽展、限制宽展和强迫宽展. 由宽展、限制宽展和强迫宽展
• 1)自由宽展 :坯料在轧制过程中,被压下的 ) 坯料在轧制过程中, 金属体积可以自由展宽的量。 金属体积可以自由展宽的量
• 此时,金属流动除来自轧辊的摩擦阻力外,不受任何其它的阻 此时,金属流动除来自轧辊的摩擦阻力外, 碍和限制。因此,自由宽展的轧制是轧制变形中的最简单的 最简单的情 碍和限制。因此,自由宽展的轧制是轧制变形中的最简单的情 平辊上或者是沿宽度上有很大富余的扁平孔型内轧制时 上或者是沿宽度上有很大富余的扁平孔型内轧制时, 况。在平辊上或者是沿宽度上有很大富余的扁平孔型内轧制时, 就属于这种情况。 就属于这种情况。
3)强迫宽展 强迫宽展
• 被压下的金属受轧辊孔型凸峰的切展 强制金属沿横向流动, 孔型凸峰的切展而强制金属沿横向流动 孔型凸峰的切展 强制金属沿横向流动, 使轧件的宽度增加,这种变形叫做强迫度展。 • 在立轧 立轧孔内轧制钢轨时是强制宽展的最好例子,如下图所示。 立轧 宽扁钢时采用的'切展'孔型也是说明强制宽展的实例。 轧制宽扁钢 宽扁钢
2
= 2
2
− 2
(
)
2
=2
R 2∆h ∆h 2
− 2
L2 ≈ D2∆h2 R1∆h1=R 2∆h2 =R 2∆h −R 2∆h1 R2 ∆h1= R + R ∆h 2 1 L=L1=L2=
2R R R +R
2 2
1 1
∆h
△h2
假定
L1=L2
因
∆h1+ ∆h2=∆h
△
1.2 实现轧制过程的条件
• 轧制过程是否能建立,决定于轧件能否被旋转 轧制过程是否能建立, 的轧辊咬入。因此, 的轧辊咬入。因此,研究分析轧辊咬入轧件的 条件,具有非常重要的实际意义。 条件,具有非常重要的实际意义
• 1.2.1 咬入条件
• 1) 咬入:依靠回转的轧辊与轧件之间 的摩擦力,轧辊将轧件拖入轧辊之间 的现象。
2) 咬入条件的确定(分析金属刚被咬入时的受力)
α
α
p
α
轧辊受力分析
轧件受力分析
α
受力分析
α
p
α
轧辊受力分析
轧件受力分析
轧件受垂直合力
: ( 使轧件受压变形
)
∑F
y
= T sin α + p cos α (T = Pf )
送 料 支 承 工 平 作 整
图
1 星 行 轧 机
3)简单轧制过程图示
α
简单轧制过程:
Δh/2
A
(1)上下轧辊直径相同 辊直径相同 (2)转速相等 转速相等 (3)轧辊无切槽 无切槽 (3)均为主动 主动(传动)辊 主动 (4)无外力或推力 辊为刚性的 (5)轧辊为刚性 辊为刚性
B C
D
Δb/2
(6)轧件在入辊处和出辊 处速度均匀 速度均匀 (7)轧件的力学性质均匀
咬入角α与轧辊直径 D和压下量∆h 之间的关系
∆h = H − h = 2 R(1 − COSα ) = D(1 − COSα )
式中 R ---- 轧辊半径。
α
(1
B C
D
Δb/2
Δh/2
A
(2)接触弧长与变形区长
• 根据几何关系,接触弧长s为: s=Rα • 接触弧之水平投影 接触弧之水平投影叫做变形区长度 变形区长度 • 变形区长度的确定(接触弧长与轧制条件有关, 可分为三种情况)
2)研究宽展的意义
• (1)拟订轧制工艺时需要确定轧件宽展. • (2) 孔型轧制中,必须正确地确定宽展的大小,否则不 不 是孔型充不满,就是过充满. 是孔型充不满,就是过充满 • 由于问题本身的复杂性,到目前为止,还没有一个能 适应多种情况下准确地计算宽展的理论公式。所以在 生产实际中习惯于使用一些经验公式和数据,来适应 各自的具体情况。
箱形孔型轧制自由宽展
2)限制宽展
• 轧制中,被压下的金属与孔型两侧壁 孔型两侧壁接触,孔型的 孔型两侧壁 侧壁限制着金属沿横向自由流动,金属被迫取得孔 型侧边轮廓的形状。 • 此时,轧件得到的宽展不是自由的,除受摩擦力外, 还受到孔型的限制。 受到孔型的限制。 受到孔型的限制 • 此外,在斜配孔型内轧制时,宽展可能为负值。 •
4)轧制变形的表示方法
轧制时绝对变形量(压下,延伸,宽展)表示 轧制时绝对变形量(压下,延伸,宽展) 绝对变形量
• • • • • •