合成氨原料气脱CO2.
合成氨原料气脱CO2

三、吸收设备
1、表面吸收器
2、鼓泡式吸收器
3、碰洒式吸收器
合成氨原料气脱CO2
初氨原料气的净化
粗原料气经CO变换以后,变换气中除H2外,还 有CO2、CO和CH4等组分,其中以CO2含量最多(15%35%)。CO2既是氨合成催化剂的毒物,又是制造尿 素、碳酸氢铵等氨肥的重要原料。因此变换气中CO2 的脱除必须兼顾这两方面的要求。 脱除CO2的方法很多,工业上常用的是溶液吸收 法,分为物理吸收和化学吸收两种。
物理吸收
• 利用CO2溶解于水或有机溶剂的性质完成。如 加压水洗法、低温甲醇洗涤法、碳酸丙烯酯法, 聚乙醇二甲醚。 吸收CO2后的溶液可用减压解析法再生。
•
合成氨生产的原则流程:
二、气体分离方法
变压吸附法
吸附分离是利用吸附剂只对特定气体吸附和解吸能力上 的差异进行分离的。为了促进这个过程的进行,常用的有加 压法和真空法等。 变压吸附法制氧、氮是在常温下进行的,其工艺有加压 吸附/常压解吸或常压吸附/真空解吸两种。 常见吸附剂:活性炭;硅胶;活性氧化铝;沸石分子筛。
合成氨几种原料气的净化工艺浅析

合成氨几种原料气的净化工艺浅析摘要简述了铜洗、联醇、双甲、醇烃化等几种原料气净化的方法及其特点。
关键词合成氨原料气净化合成氨原料气的净化是生产中至关重要的工序,原料气微量(C0+C02)超高将导致氨合成催化剂中毒而无法运行,目前我国以煤为原料固定层气化的大多数中小氮肥厂采用铜洗法脱除微量(C0+C02)。
传统的铜洗法是一种较为落后的净化工艺,存在着设备多、工艺复杂、操作麻烦而物耗高,又是生产中的主要环境污染源等缺点。
随着耐硫低温变换催化剂的开发和精脱硫技术的发展,近期中小氮肥厂在原料气净化中相继出现各级压力的联产甲醇、甲烷化、双甲和醇烃化工艺替代铜洗净化,这些原料气净化工艺正逐渐完善和成熟,比传统铜洗法具有明显优势。
1 铜洗净化工艺的不足传统的铜洗净化工艺已在中小氮肥厂应用了几十年,现仍然继续在大多数厂中运行。
尽管铜洗净化在各厂运行效果不一,但普遍存在着许多不足。
1.1铜洗是合成氨生产事故的易发工序由于铜洗工艺流程长,设备多,铜液组分受各种因素的影响,各厂铜洗生产都出现过大小不同的事故。
许多厂都出现过微量(CO+CO2) 超高、铜塔带液、设备填料堵塞、铜液成分波动、铜比难调等问题,是事故易发工序。
1.2 铜洗法净化物耗高铜洗在气体净化过程中,铜液要补充氨、铜和酸,铜液在低温下吸收脱除微量而在高温下解吸再生,既消牦热量又消耗冷量(蒸汽和电),铜液在净化过程吸收了(CO+CO2),同时亦溶解了H2有效气体,即使设置了再生回收,仍然存在着气体的损失。
铜洗运行成本各厂水平不一物耗有所差异,但一般不低于50元/tNH3,甚至高达100元/tNH3以上。
1.3 铜洗是生产现场环境较差,污染多的工序铜洗现场的跑冒滴漏是管理难点。
铜液渗漏和再生气排放污染水体和大气,不利企业环保工作的提高。
2 联产甲醇减轻了铜洗净化的生产负荷目前已有相当多的中小氮肥厂于铜洗前增加了联产甲醇工艺,联醇生产不仅增加了企业化工产品,更为重要的是减轻了铜洗净化的负荷,变换和脱碳的生产亦相对变得宽松,其综合效益是明显的。
合成氨工艺及反应原理简介

合成氨工艺及反应原理简介合成氨工艺采用烃类蒸汽转化法。
天然气经加压至4.05MPa,经预热升温在脱硫工序脱硫后,与水蒸汽混合,进入一段转化炉进行转化制H2,随后进入二段转化炉,在此引入空气,转化气在炉内燃烧放出热量,供进一步转化,同时获得N2。
工艺气经余热回收后,进入变换系统,将CO变为CO2,随后经脱碳、甲烷化反应除去CO和CO2,分离出的CO2送往尿素工艺。
工艺气进入分子筛系统除去少量水份,为合成氨提供纯净的氢氮混合气。
氢氮混合气经压缩至14MPa,送入合成塔进行合成氨的循环反应,少量惰性气体经过普里森系统分离进行回收利用。
产品氨送往尿素工艺和氨罐保存。
合成氨工艺的5个过程:1、天然气脱硫:R-SH+H2=RH+H2S H2S+ZnO=H2O(汽)+ZnS2、转化CH4+H20(汽)=CO+3H2 CH4+2H2O(汽)=CO2+4H2 (H2+ 1/2 O2=H2O)3、变换:CO+H2O(汽)=CO2+H24、脱碳:1)K2CO3+CO2+H2O⇔2KHCO32KHCO3⇔K2CO3+CO2+H2O2)甲烷化:CO+3H2=CH4+H2O CO2+4H2=CH4+2H2O5、N2+3H2=2NH31 脱硫系统工艺流程及原理1.1流程天然气进入界区后分为两路:一路作原料气,另一路作燃料气。
原料天然气进入原料气压缩机吸入罐116-F,除去携带的液体,经过原料气压缩机102-J被压缩到4.05MPa(G),经过原料气预热盘管预热到399℃,接着原料气与来自合成气压缩机103-J一段的富氢气混合。
经过Co-Mo加氢器101-D把有机硫转换成H2S,将3 ml/m3的有机硫转化为无机硫,原料气中总硫为30~90ml/m3左右,经氧化锌脱硫槽脱硫至总硫小于0.5mg/m3。
随后进入氧化锌脱硫槽,天然气中的硫化物被ZnO所吸附,制得合格原料气。
ZnO脱硫槽共二个,可以串联或并联操作,一般串联操作。
阀门及管线的配置可以使任何一个脱硫槽停止使用而另一个继续运转。
碳酸丙烯酯(PC)脱除合成氨原料气中CO2填料塔的设计 精

一、概述:吸收是利用各组分溶解度的不同而分离气体混合物的操作。
混合气体与适当的液体接触,气体中的一个或几个组分便溶解于液体中而形成溶液,于是原组分的一部分气体分离。
对与此题中的易溶气体是CO2。
依题意:年工作日以330天,每天以24小时连续运行计,合成氨原料气处理量为23500m3/ h。
变换气组成及分压如下表表变换气的组成及分压工业上脱除二氧化碳的方法主要有物理吸收法,化学吸收法,物理化学吸收法。
本次设计是小合成氨厂原料气中二氧化碳的脱除,化学吸收法对工人素质要求较高,因此采用物理吸收法。
物理吸收法适合于CO2分压较高,净化度要求低的情况,再生时不用加热,只需降压或汽提,总能耗比化学吸收法低,但CO2分离回收率低,在脱CO2前需将硫化物去除。
物理吸收是利用原料气中的溶质(CO2)在吸收剂中的溶解度较大而除去的方法。
一般吸收采用高压及低温,解吸时采用减压或升温,减压解吸所需再生能量相当少。
此法的关键是选择优良的吸收剂。
所选的吸收剂必须对CO2的溶解度大、选择性好、沸点高、无腐蚀、无毒性、性能稳定。
典型的物理吸收法有加压水洗法、N2甲基吡咯烷酮法、低温甲醇法、碳酸丙烯酯法(Flour 法)等。
碳酸丙烯酯法是碳酸丙烯酯为吸收剂的脱碳方法。
碳酸丙烯酯对CO2、H2S的溶解度较大,具有溶解热低、黏度小、蒸汽压低、无毒、化学性质稳定、无腐蚀等优点。
此法CO2的分离回收率较高,能耗低已得到小合成氨厂的广泛应用,经过各种方法的比较,最后选择用碳酸丙烯酯法吸收二氧化碳。
二、生产流程说明碳酸丙烯酯脱碳工艺流程一般由吸收、闪蒸、汽提(即溶剂再生)和气相中带出的溶剂回收等部分组成。
(见下图)参考[4]吸收过程:由氮氢压缩工段来的约1.6MP a的变换气,经油分离器再次分离气体中的油沫后,从脱碳塔底部进入,变换气与塔中喷淋的碳酸丙烯酯液逆流接触,变换气中大部分的二氧化碳被碳酸丙烯酯溶液吸收,出脱碳塔的净化气中含CO2<1.1%.再经碳酸丙烯酯回收器、碳酸丙烯酯分离器除去气体中夹带的碳酸丙烯酯雾沫后送出工段去氮氢气压缩工段。
原料气中二氧化碳的脱除

6 工艺流程
甲醇 原料气
半贫液 H2S尾气
CO+H2
氨冷
闪蒸
第一吸 收塔
再沸器
H2S再 生塔
CO变换 CO2
甲醇
净化气
富液
氨冷
氮气
气提再 生塔
第二吸 收塔
二、碳酸丙烯酯法
(一)特点:
1 碳酸丙烯酯是具有一定极性的有机溶剂,对二氧化碳、硫化氢
等酸性气体有较大的溶解能力,而氢、氮、一氧化碳等气体在其
4 流程配置原则
保证净化气指标:H2S\CO2
吸收系统 降温系统
保证溶液循环使用:
原
料
再生系统
气
减 压 再 生
净 化 气
吸
收
塔
热量移出
保证低温
气
热
提
源
再
再
生
生
空 气
蒸 气
保证回收二氧化碳的纯度 保证硫化氢满足后工序要求 合理用能 注意溶液中水分对吸收能力的影响 安全措施
5 主要工艺条件 吸收压力 吸收温度 溶液最小循环量和吸收塔液气比 净化气二氧化碳含量 再生条件
CO
0.01
N2
3、因H2\N2溶解能力小,损失小。
H2
0.001
-60 -40 -20
0 20 40
℃
各种气体在甲醇中溶解度系数
3.3 二氧化碳的脱碳—物理方法
低温甲醇洗涤法的特点 可脱除H2S、COS、CS2、RSH、CO2 、HCN、NH3、NO、H2O等 净化度高, H2S<0.1cm3/m3 ,CO2<10cm3/m3 可选择性脱除 H2S,CO2 甲醇热稳定性好,不降解,不起泡,损耗少 和最终净化的液氮洗涤匹配节省投资和动力消耗 流程长、再生复杂,有毒。
粗原料气的净化—硫化物的脱除(合成氨生产)

由脱随塔流出的富液,送至脱硫闪蒸槽而后进人H2S提浓塔,塔顶进液 为脱硫贫液,中部进液为脱硫富液。在H2S提浓塔后还有一个闪蒸槽。 闪 蒸气压缩后作为H2S提浓塔的气提气。由H2S提浓塔出来的气体含H2S25% 左右,可直接送至克劳斯法制硫装置。由脱碳闪蒸槽出来的闪蒸气含CO2 99%左右,可作尿素生产原料之用。
本书仅对近年来备受人们关注的Slexol怯(中国称为NHD法)脱硫作简介。此法 1965 年首先由美国Alied Chenical公司采用,至今已有 40多套装置在各国运 行。脱硫剂的主体成分为聚乙二醇二甲醒,商品名为Selexol。它是一种聚乙 二醇二甲醚同系物混合体。分子式为CH3O CH-O- CH2 nCH。 式中n为3-9。 平均相对分子质量为22-242。各种同系物的质量分数,%大致如下。
3、脱硫剂活性好,容易再生,定额消耗低
脱硫剂活性好,容易再生,可以降低生产的费用,符合工业生 产的经济性。
4、不易发生硫堵
硫堵:进脱硫塔气体的成分不好,杂志耗量较高;反应时析出的 硫不能及时排出;脱硫塔淋喷密度不够;再生空气量不足,吹风强度 低等原因造成硫堵。
5、脱硫剂价廉易得
采用最多的是廉价的石灰、石灰石和用石灰质药剂配制的碱性溶 液。以提高生产的经济性。
酞菁钴价格昂贵,但用量很少,脱硫液中PDS含量仅在数十个cm3/ m3左右。PDS的吨氨耗量一般在1.3-2.5g左右,因而运行的经济效益也较 显著。
此法也可脱除部分有机硫。若脱硫液中存在大量的氰化物,仍能导致 PDS中毒,但约经60h靠其自身的排毒作用,其脱硫活性可以逐渐恢复。 PDS对人体无毒,不会发生设备硫堵,无腐蚀性。
再
较高的温度有利于硫磺的分离,使析出的硫易于凝聚,
生
(完整版)年产30万吨合成氨原料气脱碳工段工艺设计毕业论文

本科毕业设计年产30万吨合成氨原料气脱碳工段工艺设计Decarbonization Process design on synthetic ammonia目录摘要 ............................................................................................................................................................ Abstract ........................................................................................................................ 错误!未定义书引言 ............................................................................................................................................................第一章总论 ....................................................................................................................................1.1 概述..........................................................................................................................1.1.1 氨的性质...................................................................................................................1.1.2 氨的用途及在化工生产中的地位 ..........................................................................1.2 合成氨的发展历史......................................................................................................1.2.1 氨气的发现...............................................................................................................1.2.2 合成氨的发现及其发展 ..........................................................................................1.2.3 世界合成氨工业发展 ..............................................................................................1.3 文献综述......................................................................................................................1.3.1合成氨脱碳................................................................................................................1.3.2合成氨脱碳的方法概述 ...........................................................................................1.4 设计的依据..................................................................................................................第二章流程方案的确定 ...............................................................................................................2.1各脱碳方法对比...........................................................................................................2.1.1化学吸收法................................................................................................................2.1.2物理吸收法................................................................................................................2.1.3物理化学吸收法........................................................................................................2.2碳酸丙烯酯(PC)法脱碳工艺基本原理 .................................................................2.2.1 PC法脱碳技术国内外现状 .....................................................................................2.2.2发展过程....................................................................................................................2.2.3技术经济....................................................................................................................第三章生产流程的简述 ...............................................................................................................3.1 气体流程......................................................................................................................3.1.1 原料气流程...............................................................................................................3.1.2 解吸气体回收流程...................................................................................................3.2液体流程.......................................................................................................................3.2.1 碳酸丙烯酯脱碳流程简述 ......................................................................................3.2.2 稀液流程循环...........................................................................................................3.3存在的问题及解决的办法 ..........................................................................................3.3.1综合分析PC法脱碳存在的主要问题有 ................................................................3.3.2解决办法....................................................................................................................第四章物料衡算和热量衡算 ....................................................................................................4.1工艺参数及指标...........................................................................................................4.1.1计算依据CO2在PC中的溶解度关系 ...................................................................4.1.2 PC的密度与温度的关系 .........................................................................................4.1.3 PC的蒸汽压 .............................................................................................................4.1.4 PC的黏度 .................................................................................................................4.2物料衡算.......................................................................................................................4.2.1各组分在PC中的溶解量 ........................................................................................4.2.2溶剂夹带量................................................................................................................4.2.3溶液带出的气量........................................................................................................4.2.4出脱碳塔净化气量....................................................................................................4.2.6 入塔液中CO2夹带量..............................................................................................4.2.7 带出气体的质量流量 ..............................................................................................4.2.8 验算吸收液中净化气中CO2的含量 .....................................................................4.2.9出塔气的组成............................................................................................................4.3热量衡算.......................................................................................................................第五章吸收塔的结构设计..........................................................................................................5.1确定吸收塔塔径及相关参数 ......................................................................................5.1.1基础数据....................................................................................................................5.1.2求取塔径....................................................................................................................5.1.3核算数据....................................................................................................................5.1.4填料层高度的计算....................................................................................................5.1.5 气相总传质单元高度 ..............................................................................................5.1.6塔附属高度................................................................................................................第六章塔零部件和辅助设备的设计与选取.....................................................................6.1 吸收塔零部件的选取..................................................................................................6.1.1筒体、封头等部件的尺寸选取 ...............................................................................6.1.2防涡流挡板的选取....................................................................................................6.1.3液体初始分布器........................................................................................................6.1.4 液体再分布器...........................................................................................................6.1.5 填料支撑装置...........................................................................................................6.1.6接管管径的确定........................................................................................................6.2 解吸塔的选取..............................................................................................................6.3贮槽的选择...................................................................................................................结论..........................................................................................................................................................致谢.......................................................................................................................... 错误!未定义书参考文献 ...............................................................................................................................................年产30万吨合成氨原料气脱碳工段工艺设计摘要:本设计为年产30万吨合成氨原料气脱碳工段工艺设计,是由指导老师指定的产量和生产规模,结合生产实习中收集的各类生产技术指标以及参考文献所提供的数据为依据而设计的。
合成氨工艺流程

将无烟煤(或焦炭)由炉顶加入固定床层煤气发生炉中,并交替向炉内通入空气和水蒸汽,燃料气化所生成的半水煤气经燃烧室、废热锅炉回收热量后送入气柜。
? ???? 半水煤气由气柜进入电除尘器,除去固体颗粒后依次进入压缩机的Ⅰ、Ⅱ、Ⅲ段,加压到1.9~2.0Mpa,送入脱硫塔,用溶液或其他脱硫溶液洗涤,以除去硫化氢,随后,气体经饱和塔进入热交换器,加热升温后进入一氧化碳变换炉,用水蒸汽使气体中的一氧化碳变为氢。
变换后的气体,返回热交换器进行降温,并经热水塔的进一步降温后,进入变换器脱硫塔,以除去变换时产生的硫化氢。
然后,气体进入二氧化碳吸收塔,用水洗法除去大部分二氧化碳。
脱碳后的原料进入压缩机Ⅳ、Ⅴ段,升压到压缩机12.09~13.0Mpa后,依次进入铜洗塔和碱洗塔,使气体中残余的一氧化碳和二氧化碳含量进一步降至20(ppm)以下,以满足合成氨的要求。
????? 净化后的原料气进入压缩机的最后一段,升压到30.0~32.0?MPa进入滤油器,在此与循环压缩机来的循环气混合,经除油后,进入冷凝塔和氨冷器的管内,再进入冷凝塔的下部,分离出液氨。
分离出液氨后的气体进入冷凝塔上部的管间,与管内的气体换热升温后进入氨合成塔。
在高温高压并有催化剂存在的条件下,将氮氢气合成氨。
出合成塔的气体中,约含氨10~20%,经水冷器与氨冷器将氨液化并分离后,其气体进入循环压缩机循环使用。
分离出的液氨进入液氨贮槽。
?原料气的制备:制备氢氮比为3:1的半水煤气???? ?即造气。
将无烟煤(或焦炭)由炉顶加入固定床层煤气发生炉中,并交替向炉内通入空气和水蒸汽,燃料气化后生成氢氮比为3:1的半水煤气。
整个生产过程由煤气发生炉、燃烧室、废热锅炉、气柜等设备组成。
????? 固定床半水煤气制造过程由吹风、上吹制气、下吹制气、二次上吹、空气吹净等5个阶段构成,为了调节氢氮比,在吹风末端要将部分吹风气吹入煤气,这个过程通常称为吹风回收。
????? 吹风阶段:空气从煤气炉的底部吹入,使燃料燃烧,热量贮存于燃料中,为制气阶段碳与水蒸汽的反应提供热量。
合成氨脱碳工艺
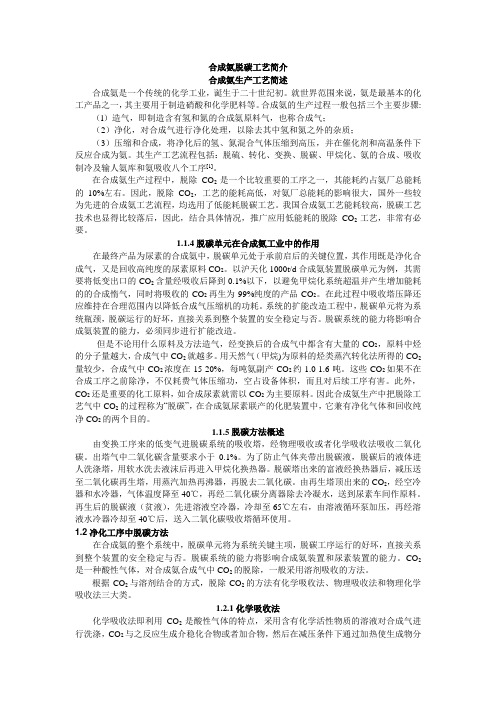
合成氨脱碳工艺简介合成氨生产工艺简述合成氨是一个传统的化学工业,诞生于二十世纪初。
就世界范围来说,氨是最基本的化工产品之一,其主要用于制造硝酸和化学肥料等。
合成氨的生产过程一般包括三个主要步骤: (l)造气,即制造含有氢和氮的合成氨原料气,也称合成气;(2)净化,对合成气进行净化处理,以除去其中氢和氮之外的杂质;(3)压缩和合成,将净化后的氢、氮混合气体压缩到高压,并在催化剂和高温条件下反应合成为氨。
其生产工艺流程包括:脱硫、转化、变换、脱碳、甲烷化、氨的合成、吸收制冷及输人氨库和氨吸收八个工序[1]。
在合成氨生产过程中,脱除CO2是一个比较重要的工序之一,其能耗约占氨厂总能耗的10%左右。
因此,脱除CO2,工艺的能耗高低,对氨厂总能耗的影响很大,国外一些较为先进的合成氨工艺流程,均选用了低能耗脱碳工艺。
我国合成氨工艺能耗较高,脱碳工艺技术也显得比较落后,因此,结合具体情况,推广应用低能耗的脱除CO2工艺,非常有必要。
1.1.4脱碳单元在合成氨工业中的作用在最终产品为尿素的合成氨中,脱碳单元处于承前启后的关键位置,其作用既是净化合成气,又是回收高纯度的尿素原料CO2。
以沪天化1000t/d合成氨装置脱碳单元为例,其需要将低变出口的CO2含量经吸收后降到0.1%以下,以避免甲烷化系统超温并产生增加能耗的的合成惰气,同时将吸收的CO2再生为99%纯度的产品CO2。
在此过程中吸收塔压降还应维持在合理范围内以降低合成气压缩机的功耗。
系统的扩能改造工程中,脱碳单元将为系统瓶颈,脱碳运行的好坏,直接关系到整个装置的安全稳定与否。
脱碳系统的能力将影响合成氨装置的能力,必须同步进行扩能改造。
但是不论用什么原料及方法造气,经变换后的合成气中都含有大量的CO2,原料中烃的分子量越大,合成气中CO2就越多。
用天然气(甲烷)为原料的烃类蒸汽转化法所得的CO2量较少,合成气中CO2浓度在15-20%,每吨氨副产CO2约1.0-1.6吨。
合成氨的环保措施
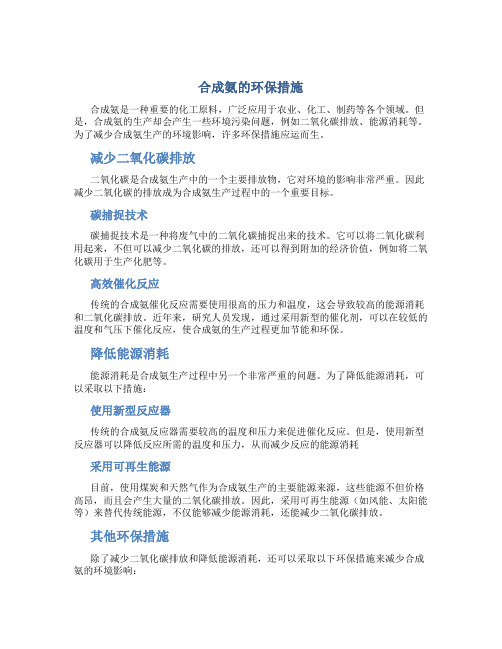
合成氨的环保措施合成氨是一种重要的化工原料,广泛应用于农业、化工、制药等各个领域。
但是,合成氨的生产却会产生一些环境污染问题,例如二氧化碳排放、能源消耗等。
为了减少合成氨生产的环境影响,许多环保措施应运而生。
减少二氧化碳排放二氧化碳是合成氨生产中的一个主要排放物,它对环境的影响非常严重。
因此减少二氧化碳的排放成为合成氨生产过程中的一个重要目标。
碳捕捉技术碳捕捉技术是一种将废气中的二氧化碳捕捉出来的技术。
它可以将二氧化碳利用起来,不但可以减少二氧化碳的排放,还可以得到附加的经济价值,例如将二氧化碳用于生产化肥等。
高效催化反应传统的合成氨催化反应需要使用很高的压力和温度,这会导致较高的能源消耗和二氧化碳排放。
近年来,研究人员发现,通过采用新型的催化剂,可以在较低的温度和气压下催化反应,使合成氨的生产过程更加节能和环保。
降低能源消耗能源消耗是合成氨生产过程中另一个非常严重的问题。
为了降低能源消耗,可以采取以下措施:使用新型反应器传统的合成氨反应器需要较高的温度和压力来促进催化反应。
但是,使用新型反应器可以降低反应所需的温度和压力,从而减少反应的能源消耗采用可再生能源目前,使用煤炭和天然气作为合成氨生产的主要能源来源,这些能源不但价格高昂,而且会产生大量的二氧化碳排放。
因此,采用可再生能源(如风能、太阳能等)来替代传统能源,不仅能够减少能源消耗,还能减少二氧化碳排放。
其他环保措施除了减少二氧化碳排放和降低能源消耗,还可以采取以下环保措施来减少合成氨的环境影响:废物处理合成氨生产过程中会产生一些废物,如尿素气、废水等。
这些废物需要进行处理,以减少对环境的污染。
绿色化学近年来,绿色化学成为一个新兴的概念,旨在通过环保技术来实现化学反应的绿色化。
对于合成氨生产来说,可以采用绿色化学方法来减少有毒有害物质的使用,从而减少对环境的影响。
国家政策的支持国家政策的支持是促进合成氨环保的另一个关键因素。
政府可以制定环保税收政策,鼓励企业采用环保技术,从而促进合成氨工业的绿色发展。
合成氨工艺原料气净化方法

摘要:氨合成反应需要高纯度的H2和N2,无论以固体(煤或焦炭)还是用烃类(天然气、石脑油等)为原料获得的原料气中,都含有一氧化碳、二氧化碳、硫化物等不利于合成反应的成分,需要在进入合成塔之前除去,否则将导致氨合成催化剂中毒而无法运行。在多年的实践和探索中,合成氨工艺原料气净化方法不断创新和改进,由原来高污染高能耗的铜洗法发展到如今的高效节能净化技术。本文简述了铜洗、双甲、醇烃化等几种合成氨原料气净化的工艺原理、方法及其特点,对几种净化工艺进行了对比分析。并介绍了新型节能净化技术。
2.3 甲醇甲烷净化工艺法(双甲工艺)
“双甲”工艺,实际上就是合成氨厂将联醇、甲烷化技术引入原料气净化系统,从而省去落 后的铜洗再生工艺。该工艺由两部分组成,在甲醇合成之后,再是传统的甲烷化工艺工序。工艺原理:
甲醇化工艺CO+2H2 = CH3OH CO2+3H2 = CH3OH +H2O;
甲烷化工艺CO+3H2= CH4 +H2O CO2 +4H2=CH4+2H2 O
四.
合成氨厂原料气净化工艺随着时代发展,已从较为落后的铜洗工艺法逐渐发展到 工艺较为先进的醇烃化及醇烷化净化工艺,并不断向节能减排方向发展,如通过增加1台换热器来改进分子筛再生系统,用新增换热器来对系统内氮气进行换热,降低了其他换热器外部供能,从而提高能源利用率,达到节能的效果;合成氨原料气节能净化装置,回收了合成氨原料气中的甲烷,增加了产出,提高了原料利用率,同时有效减少了氨合成工序弛放气的排放量等等。
醇烃化工艺就是醇醚化、醇烃化精制工艺。第一步将双甲工艺中甲醇化催化剂更换成醇醚复 合催化剂,使CO+CO2与H2反应生成甲醇,并随即水解为二甲醚。第二步将双甲工艺的甲烷化催化剂更换为烃化催化剂,使 CO+CO2与H2反应生成低碳烃化物、低碳醇化物,低碳烃化物、低碳醇化物在水冷温度下可冷凝为液相,与气体分离。优点:①脱除CO+CO2的量低且稳定,并能较大幅度地提高联产甲醇的产量;②烃化生产烃类物质,高压常温下冷凝分离;③烃化操作温度较甲烷化低60~80℃,烃化反应床层更易维持自热操作;④烃化催化剂活性温区宽,不易烧结、老化,使用寿命长;⑤烃化催化剂价格便宜;⑥甲醇在烃化塔内无逆反应发生。
合成氨工艺脱碳方法评述

收稿日期:2011-11-17作者简介:唐俊丽(1978-),女,工程师,2002年毕业于河南大学化学工程与工艺专业工学学士,主要从事合成氨和膜分离技术工作。
文章编号:1002-1124(2011)12-0034-03Sum 195No.12化学工程师ChemicalEngineer2011年第12期化学降解和操作管理等因素所致,损耗量是影响操作成本的关键因素。
目前,高效回收及分级回收等工艺的成功开发降低了溶剂损耗,吸收效率得到进一步提高。
(2)腐蚀问题溶剂回收系统溶液浓度<10%,碳钢设备、管道、管件腐蚀严重,因而采用不锈钢管道、管件及运转设备。
(3)净化气中CO2含量高产生该问题原因较多,如再生效果不好等,然而根本原因是溶剂吸收CO2能力低,特别是在低分压、低酸性组分时尤为突出。
针对该问题,杭州市脱碳化工技术开发公司等单位研究成功复合脱碳溶剂。
该产品主要由碳丙与碳丙添加剂组成,在同等条件下,净化度可提高20%,而价格比碳丙低。
1.2活化MDEA法该法由德国巴斯夫公司(BASF)开发,吸收CO2的速率较慢,为提高溶液吸收和再生速率,通常加入少量DEA等活化剂。
因此,活化MDEA吸收CO2的过程具有物理吸收和化学吸收的特点。
该法自问世以来,受到了广泛关注,称为现代低能耗脱碳法。
80年代末至90年代初,南京化工研究院、华东理工大学、川化研究院先后推出具有各自特色的活化MDEA脱碳工艺。
由于该工艺具有吸收能力大、反应速度快、适应范围广、再生能耗低、净化度高、溶液基本无腐蚀性、大部分设备及填料可用碳钢制作、操作简化等优点,因此,在较短的时间里它被国内20多家中小型合成氨厂广泛采用。
然而,该法也存在以下主要问题:(1)溶液降解和腐蚀M DEA溶液在脱碳过程中有一定的腐蚀和降解。
对于腐蚀问题,除了要尽量减少降解程度外,仍须加入缓蚀剂。
实验表明,在MDEA溶液中加入适当缓蚀剂后,溶液腐蚀性得到大幅度降低。
合成氨脱碳毕业设计

毕业设计题目:年产6万吨合成氨原料气脱碳工艺设计学院:河南城建学院专业:化学工程与工艺姓名:学号:指导老师:刘伟完成时间:2013年5月设计说明二氧化碳的吸收再生过程主要是由吸收、闪蒸和气提三部分组成。
本次设计选用的脱碳剂是聚乙二醇二甲醚(NHD ),属于物理吸收法。
主要的设备是吸收塔和气提塔。
在计算的过程中,首先根据所给的物料组成和工艺条件进行物料恒算和热量恒算,再进行塔设备的计算、校核及辅助设备的计算或选型。
吸收段的计算结果如下:二氧化碳的脱除量2909.43m /h ,NHD 的用量184.23m /h ;塔底流出的富液带出的热量14269139.99kJ/h ,溶液温度升高了5℃;塔径为1.6m ,填料层高度为13.47m ,塔压降为3002.7Pa 。
解吸段的计算结果如下:闪蒸出的二氧化碳的量2735.73m /h ,二氧化碳的回收率为94%,溶液带出的热量10142141.09kJ/h ,闪蒸的容积为0.263m 。
气提出的二氧化碳的量157.153m /h ,氮气的用量1105.23m /h ;塔底流出的贫液带出的热量6022054.3kJ/h ,溶液温度为26℃;上段塔径1.4m ,下段塔径1.5m ,填料层高度为5.7m ,塔压降为2021.4Pa 。
[关键词] 吸收、闪蒸、气提Design InstructionsThe decarbon and regeneration of carbon dioxide process is primarily composed by three parts: absorption, flash vaporization and gas stripping. This design uses polyethylene glycol dimethl ether (NHD) to decarbon, which is the physical absorption method. The main device is absorption column and stripper. In the process of calculation, firstly make material constant calculation and heat constant calculation, and then is the calculation of tower equipment, checking and ancillary equipment’s calculation or selection.Absorption segment’s results are as follows:The amount of carbon dioxide removel is 2909.4m³/h and the amount of NHD is 1 84.2m³/h; the heat of liquid-rich flow from tower bottom is 14269139.99kJ/h and the temperature of solution rises 5℃; the tower diameter is 1.6m, the height of packing layer is 13.47m and the column pressure dropping is 3002.7Pa.The desorption segment’s results are as follows:The amount of carbon dioxide flashes is 2735.7m³/h, the recovery rate of carbon dioxide is 94%, the heat brought out from solution is 10142141.09kJ/h and the volume of flash trough is 0.26m³.The amount of carbon dioxide stripped out is 157.15m³/h and the amount of nitwgen is 1105.2m³/h; the heat of barren liquor from tower bottom is 6022054.3kJ/h and the temperature of solution is 26℃; the upper column diameter is1.4m, the lower column diameter is 1.5m and the column pressure dropping is 2 021.4Pa.Key Words: absorption,flash,stripping目录设计说明 ............................................................ I I Design Instructions ................................................ I II 目录 .............................................................. I V 主要符号说明 ........................................................ V I 引言 . (1)1 总论 (2)1.1概述 (2)1.2文献综述 (3)1.3设计任务的依据 (4)1.4主要原材料及公用工程情况 (5)2 生产方案的确定 (6)2.1脱碳的方法 (6)2.2 NHD的脱碳原理 (6)2.2.1 NHD溶剂的物理性质 (6)2.2.2 计算的热力学基础 (7)2.2.3计算的动力学基础 (8)2.3 脱碳工艺参数的选定 (8)2.3.1 脱碳流程的选择 (8)2.3.2气提剂的选择 (9)2.3.4 脱碳再生操作温度的选定 (9)2.3.5 脱碳操作压力的选定 (10)2.3.6脱碳塔气液比的确定 (10)2.3.7 冷凝器的位置及选定 (11)2.3.8腐蚀及材料选择 (12)3 脱碳生产流程说明 (13)4 吸收过程的工艺计算 (15)4.1物料恒算 (16)4.2热量恒算 (18)4.2.1原料气带入的热量 (18)4.2.2单位时间内气体的溶解热 (19)4.2.3进塔溶液带入的热量 (19)4.2.4净化气带出的热量 (19)4.2.5塔底富液带出的热量 (20)4.3吸收塔的工艺设计 (20)4.3.1 塔径及气速的计算[]7 (20)4.3.2填料层高度的计算 (22)4.3.3塔厚度的计算 (23)4.3.4塔压降的计算 (24)4.3.5辅助设备的计算和选型[]8 (24)4.3.6塔体的强度校核 (26)5 解吸过程的工艺计算 (30)5.1物料恒算 (30)5.1.1闪蒸过程的物料恒算 (30)5.1.2气提过程的物料恒算[]10 (30)5.2热量恒算 (31)5.2.1闪蒸过程的热量恒算 (31)5.2.2气提过程的热量恒算 (32)5.3气提塔的工艺设计 (32)5.3.1塔径及气速的计算 (32)5.3.2 填料层高度的计算 (34)5.3.3塔厚度的计算 (36)5.3.4塔压降的计算 (36)5.3.5辅助设备的计算和选型 (36)5.3.6塔体的强度校核[]12 (38)设计结果 (42)参考文献 (44)附录 (45)致谢 (46)主要符号说明 序号 符号意义 单位 01 i G气体体积流量 3m /h 02 i L液体体积流量 3m /h 03 S2CO 在NHD 中的溶解度 3m (标) /3m 04 L ρNHD 的密度 3kg /m 05 gi Q气体的热量 k J /h 06 Li Q液体的热量 k J /h 07 S Q气体的溶解热 k J /h 08 gi T气体温度 K 09 Li T液体温度 K 10 2CO q2CO 在NHD 中的溶解度热 kJ /kmol 11 X Q气体的焓值 k J /h 12 m,V q气体的质量流量 k g /h 13 0P气体压力 M P a 14 F u空塔气速 k J /h 15 m相平衡常数 1 16 i D塔径 m 17 Z填料高度 m 18 i P风载荷 2N /m 19 W M风弯矩 N m ⋅ 20 F地震载荷 N 21 I惯性距4mm引言氨是重要的无机化工产品之一,在国民经济中占有重要地位。
合成氨co2吸收塔原理

合成氨co2吸收塔原理
合成氨CO2吸收塔的工作原理基于化学吸收的原理。
当高浓度二氧化碳气体通过塔层时,吸收剂会与其发生化学反应,吸收二氧化碳并将其转化为其它化合物。
常用的吸收剂包括氨水、碱性溶液或有机物。
这些吸收剂具有较高的亲和力,能够有效地吸附二氧化碳分子。
在合成氨工艺中,CO2吸收塔主要用于吸收合成氨原料气中的二氧化碳气体,使合成氨原料气中的CO2与CO、H2等分离。
现有的技术中,常采用热钾碱法分离二氧化碳气体。
这种方法采用逆流吸收模式,含二氧化碳的原料气从塔体下部进入,钾碱溶液从塔体上部进入,在塔体内气液两相逆向接触,二氧化碳气体被钾碱溶液吸收,生成碳酸氢钾,进入液相,从而达到分离CO2与其他气体的目的。
此外,二氧化碳气体与吸收剂之间的化学反应会产生热量。
为了保持吸收塔的稳定运行,通常需要实施冷却措施。
以上信息仅供参考,如需了解更多信息,建议咨询专业人士或查阅相关书籍资料。
脱碳岗位操作规程

脱碳岗位操作规程一、概述合成氨原料气经除尘、脱硫、变换后,含有一定数量的二氧化碳,在气体进入合成氨之前,必须清除干净。
因为二氧化碳是氨合成不需用的气体,而且对氨合成催化剂有毒害作用。
同时在气体净化工序,回收高纯度的二氧化碳气体,提供合成尿素的使用。
合成氨厂常用的脱除二氧化碳方法为溶液吸收循环法。
即溶液吸收二氧化碳气体,在再生系统解吸释放出较纯的二氧化碳,再生的溶液循环使用。
溶液吸收循环法可分为物理吸收法、化学吸收法、物理----化学吸收法。
物理吸收法是利用二氧化碳在溶剂中有一定的溶解度的特性,吸收清除气体中的二氧化碳。
如NHD法,低温甲醇洗涤法等。
化学吸收法则是以碱性溶液为吸收剂,可以和弱酸性气体,二氧化碳进行化学反应的特性,将其吸收。
如碳酸钾法,氨水吸收法等。
既用二氧化碳能溶解于其中的物理特性,又利用溶剂和二氧化碳进行化学反应,清除气体中二氧化碳的方法称中和物理---化学法,如MDEA法。
二、脱碳岗位的目的和任务本岗位的目的和任务是脱除变换后原料气中的二氧化碳,为氨合成提供合格的净化气(CO2≤0.5%)。
同时得到CO2≥98%的二氧化碳气体供尿素使用。
三、脱碳的原理(一)NHD法脱碳机理NHD化学名称为聚乙二醇二甲醚,属于一种物理吸收二氧化碳的方法。
变换气中的CO2、H2S气体在NHD溶剂中溶解度大,且随压力的升高、温度的降低吸收能力增大,而且变换气中N2、H2在其溶解度很小。
因此,在低温高压的条件下,NHD溶剂吸收CO2、H2S,降低压力后,NHD溶液中被吸收的CO2气体解吸释放。
用空气气提NHD溶剂,使其被彻底再生为贫液循环使用。
四、NHD溶剂的物理性质NHD溶剂的主要成份是聚乙二醇二甲醚的同系物。
它的分子式为:CH3----O----(C2H4O)n----CH3式中:n=2----8 平均分子量:250----270燃点:157℃闪点:151℃聚乙二醇二甲醚同系物的物理性质表溶剂分子量沸点(℃)蒸汽压(mmHg)粘度(CP)二乙二醇二甲醚134 131 0.007 1.45三乙二醇二甲醚178 199 0.007 2.08四乙二醇二甲醚202 267 0.007 2.99五乙二醇二甲醚266 335 0.007 4.30六乙二醇二甲醚310 404 0.007 6.58七乙二醇二甲醚354 472 0.007 8.87作为一种脱碳溶剂它具有较高的沸点,较低的蒸汽压和较低的粘度。
原料气精制方法1
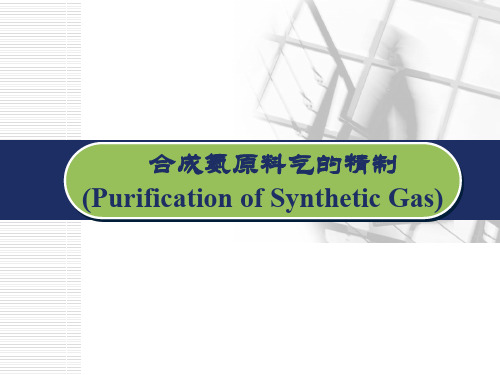
二、甲烷化法
与铜洗工艺的比较 双甲新工艺与铜洗法比较,有四个明显优点,节能、节物、
运行稳定、净化环境。 1. 节约蒸汽 2. 节约原料气 3. 节约电耗 4. 节约铜、醋酸、液氨。 5. 铜洗的微量一般都在20PPM以上,且经常带液喷液,生
流到铜氨液再生系统的回流塔3的顶部,与再生器4逸出的气体相遇,
捕集其中氨及部分CO2后,由回流塔底部流至还原器7中。还原器 的上下两段均上设有蒸汽加热管,底部有空气加入管 ,中部有旁通
管线(即副线)。铜氨液首先经过下加热器6加热,随即向上流,
经还原器内几层有孔折板后进入上加热器5。在必要时,可开用旁
合成氨原料气的精制 (Purification of Synthetic Gas)
合成氨原料气的精制
变换、脱碳后的原料气组成
组成 H2 含量% 72~75
N2
CO
CO2
CH4、Ar
17~20 0.3~3.5 0.2~0.5 0.5~1.0
为防止CO和CO2造成氨合成催化剂的中毒,原料气送往 合成工段前须进一步净化,此过程称“原料气的精制”。
吸收二氧化碳、氧和硫化氢
反应特点:可逆、放热
5
一、铜氨液洗涤法
(2)铜氨溶液的再生 铜液再生的作用:使吸收的CO和CO2解析出来; 把被氧化的高价铜还原成低价铜。 此外,铜液在使用过程中消耗的氨和铜也在再生过程
中加以补充。 铜液经减压加热可使吸收的CO、CO2、H2S等按吸收的逆
反应释放出来。 高价铜的还原:
CO2+4H2≒CH4+2H2O 甲烷化反应的平衡常数随温度的升高而下降。工业一 般控制280~420℃,该温度范围内,平衡常数都很大。此 外原料气中水蒸气含量低级加压操作对甲烷化反应有利。 甲烷化反应速率随温度升高和压力增加而加快。
粗原料气的净化—二氧化碳的脱除(合成氨生产)

各种改良热钾碱法脱碳
CO2在苯菲尔溶液中的吸收过程,其传质机理属于化学吸收范围,即 速度较慢的化学反应是整个吸收过程的控制步骤。CO2吸收及其再生的过 程可用如下可逆反应式表示:
CO2(g) K2CO3+CO2(l) +H2O
2KHCO3
(1-1)
由于受反应速度的限制,气体中CO2与溶液中K2CO3的反应速度较慢。 为了加快CO2在K2CO3溶液中的吸收速度,通常在K2CO3溶液中又添加了 一种催化剂二乙醇胺(di-ethanol-amine或R1R2NH,简称为DEA )。
不同原料制氨需要脱除的二氧化碳量差别很大。
不同原料和制气方法需脱除的CO2 的量
脱碳目的
由上表知:天然气为原料生产氨时,脱除的CO2量仅为以渣油或煤为 原料的1/2至1/3左右。对生产尿素而言,分别用天然气、渣油为原料的 合成氨厂,在选择脱碳方法时,前者应采用二氧化碳回收率高的,而后者可 采用回收率稍低的,但应满足尿素生产对CO的需求。对生产碳酸氢铵的合 成氨厂,则不论采用何种原料,二氧化碳量都嫌不足,这就是中国一些中、 小型氨厂存在氨剩余的原因。
上(1-1)式是一可逆反应。假定气相中二氧化碳在溶液中的溶解度 符合亨利定律,则由上述反应的化学平衡和气液相平衡关系式可得:
c KHCO
2
p
3
c CO 2
K H
K CO
W
23
p — 气相中二氧化碳的平衡分压,MPa CO 2
K — 化学反应的平衡常数; W
, , — 分别为碳酸氢钾 、 碳酸钾、 水的活度系数 ;
碳酸钾溶液对气体中二氧化碳的吸收:
(a)加入活化剂DEA(2,2—二羟基二乙胺) 加入DEA改变机理,反应速度提高10-100倍。
合成氨过程中二氧化碳的脱除

合成氨过程中二氧化碳的脱除经变换的原料气含有大量的二氧化碳,二氧化碳是制造尿素、碳酸氢铵和纯碱的重要原料。
原料气在进合成工序前,必须将二氧化碳清除干净。
因此,合成氨生产中,二氧化碳的脱除及其回收利用具有双重目的。
习惯上,将二氧化碳的脱除过程称为脱碳。
目前,脱碳多采用溶液吸收法。
根据吸收剂性能的不同,分为化学吸收法和物理吸收法两类。
化学吸收法是二氧化碳与碱性溶液反应而被除去,常用的有改良热钾碱法、氨水法和乙醇胺法。
物理吸收法是利用二氧化碳比氢气、氨气在吸收剂中溶解度大的特性,用吸收的方法除去原料气中的二氧化碳,常用的有低温甲酵法、聚乙二酵二甲醚法和碳酸丙烯酯法。
(l)改良热钾碱法改良热钾碱法也称本菲尔法,该法采用热碳酸钾吸收二氧化碳:K2CO3+CO2+H2O = 2KHCO3碳酸钾溶液吸收二氧化碳后,应进行再生以使溶液循环使用,再生反应为2KHCO3 = K2CO3+H2O+CO2↑产生的二氧化碳可回收利用。
加压利于二氧化碳的吸收,故吸收在加压下操作;减压加热利于二氧化碳的解吸,故再生过程是在减压和加热的条件下完成的。
吸收溶液中,除碳酸钾之外,并有活化剂二乙醇胺,并加有缓蚀剂偏钒酸钾、消泡剂聚醚或硅酮乳状液等。
近几年,美国UOP公司开发了一种可取代二乙醇胺的新活化剂ACT-l。
(2)聚乙二酵二甲醚法也称谢列克索法,属于物理吸收。
聚乙二醇二甲醚能选择性脱除气体中的COz和H2S,无毒,能耗较低。
20世纪80年代初,美国将此法用于以天然气为原料的大型合成氨厂,至今世界上仍有许多工厂采用。
中国南化公司研究院开发的同类脱碳工艺(NHD净化技术)在中型氨厂试验成功,NHD溶液吸收c0.和H.S的能力均优于国外的Selexol溶液,而价格便宜,技术与设备全部国产化。
- 1、下载文档前请自行甄别文档内容的完整性,平台不提供额外的编辑、内容补充、找答案等附加服务。
- 2、"仅部分预览"的文档,不可在线预览部分如存在完整性等问题,可反馈申请退款(可完整预览的文档不适用该条件!)。
- 3、如文档侵犯您的权益,请联系客服反馈,我们会尽快为您处理(人工客服工作时间:9:00-18:30)。
CO+3H2→CH4+H2O =-206.2kJ/mol 0298HΔ CO2+4H2→CH4+2H2O =-165.1kJ/mol 0298HΔ
2、气体分离原理
分离的基本原理是:将经过净化的带压或加压的原料气逐级冷却至 各分离组分的冷凝温度进行分凝(单级或逐级冷凝);或使原料气加压 冷却、液化、再精馏进行分离。常用的气体冷凝温度(在101.325千 帕压力下)见表1[常见的气体冷凝温度 法( 以 冷 密 分化 分 却 度 离学 为 , 不 。) : 根 同 反压据、 应缩沸扩 吸气点散 附体温速 气,度度 体物不不 等理同同 方 可,
甲烷化法是在催化剂存在下使少量CO、CO2与H2反应生成CH4和 H2O的一种净化工艺,要求入口原料气中碳的氧化物含量(体积分数) 一般应小于0.7%。甲烷化法可以将气体中碳的氧化物(CO+CO2)含量 脱除到10cm3/m3以下,但是需要消耗有效成分H2,并且增加了惰 性气体CH4的含量。甲烷化反应如下:
CO2既是氨合成催化剂的毒物,又是制造尿素、碳酸氢铵等氮肥的 重要原料。因此变换气中CO2的脱除必须兼顾这两方面的要求。
③ 气体精制过程
经CO变换和CO2脱除后的原料气中尚含有少量残余的CO和 CO2。为了防止对氨合成催化剂的毒害,规定CO和CO2总含量 不得大于10cm3/m3(体积分数)。因此,原料气在进入合成工 序前,必须进行原料气的最终净化,即精制过程。 目前在工业生产中,最终净化方法分为深冷分离法和甲烷化法。
初步方案的制定
一、合成氨的工艺物料
(1)原料气制备 将煤和天然气等原料制成含氢和 氮的粗原料气。对于固体原料煤和焦炭,通常 采用气化的方法制取合成气;渣油可采用非催 化部分氧化的方法获得合成气;对气态烃类和 石脑油,工业中利用二段蒸汽转化法制取合成 气。 (2)净化 对粗原料气进行净化处理,除去氢气和 氮气以外的杂质,主要包括变换过程、脱硫脱 碳过程以及气体精制过程。
产品气CO2压力:≤0.015MPa
Байду номын сангаас
故选用变压溶液吸收法来吸附脱除CO2,本系统利 用硅胶作为吸附剂
二.合成氨的工艺流程
1. 变换气、净化气流程:
由变脱送来的CO2约25%,温度约40℃的变换气送入变压吸附系统 经气水分离器除去游离水后进入提纯吸附塔组中同时处于吸附步骤 的四个塔,由下而上通过床层,出塔中间气进入净化段。当被吸附 CO2的浓度前沿接近床层出口时,关闭该吸附塔的原料气进口阀和 产品气出口阀,使其停止吸附,通过二十次均压降步骤回收床层死 空间的产品气,逆着吸附方向放出,易吸附组分CO2被排放至CO2 气柜,吸附剂得到初步再生。吹扫出来的气部分送CO2气柜,部分 放空。之后,吸附塔逐渐均升压至吸附压力开始下一个吸附循环过 程。出提纯吸附塔的中间气CO2约6-8%,再进入净化吸附阶段,经 历相同吸附、解吸过程,进一步分离中间气中的CO2,出净化吸附 段净化气CO2再0.25%以下,送往合成。净化段CO2解吸通过四次 均压降,先回收床层H2、N2后,再通过三次顺放、逆放、三次吹扫 出来的气回收到提纯段。
① 一氧化碳变换过程
在合成氨生产中,各种方法制取的原料气都含有CO,其体积分 数一般为12%~40%。合成氨需要的两种组分是H2和N2,因此 需要除去合成气中的CO。变换反应如下:
CO+H2OH→2+CO2 =-41.2kJ/mol 0298HΔ
由于CO变换过程是强放热过程,必须分段进行以利于回收反应热, 并控制变换段出口残余CO含量。第一步是高温变换,使大部分 CO转变为CO2和H2;第二步是低温变换,将CO含量降至0.3%左 右。因此,CO变换反应既是原料气制造的继续,又是净化的过程, 为后续脱碳过程创造条件。
3、变压吸附脱碳基本原理:
变压吸附的基本原理是吸附剂对吸附质在不同分压下有不同的吸附 容量,并且在一定压力下对被分离的气体混合物的各组分又有选择 吸附的特性,加压吸附除去原料气中杂质组分,减压脱附这些杂质 使吸附剂获得再生。本系统利用硅胶作为吸附剂,选择性吸附脱除 变换气中大部分的CO2、有机硫等。采用多吸附床,循环地变动所 组合的各吸附床压力,并达到连续分离。 本系统采用两段分离,提纯段采用26-4-20均压工艺,即26个塔, 4塔同时吸附,20次均压降流程。净化段采用11-3-4-3均压工艺, 即11个吸附塔,3塔同时吸附,4次均压降流程,3次吹扫流程。充 分回收床层死空间的有效H2、N2,增加床层死空间中CO2的浓度, 将CO2富集为96%以上回收送往尿素CO2气柜。
2、CO2流程:
由净化段吸附塔解吸出来的CO2经逆放和吹扫送往提纯吸附段 置换出提纯吸附塔内的H2、N2混合气体后,进一步经提纯吸附 段解吸、再生、富集为9%以上浓度后经提纯吸附段逆放和吹扫 送往CO2气柜。
3、循环油流程:
蓄能器主油箱→箱内过滤器→油泵→止逆阀→节 流阀→截止阀→压力油管→油器缸→阀站→回油 管→油冷器→副油箱→主油箱循环使用。
② 脱硫脱碳过程
各种原料制取的粗原料气,都含有一些硫和碳的氧化物,为了防止 合成氨生产过程催化剂的中毒,必须在氨合成工序前加以脱除,以 天然气为原料的蒸汽转化法,第一道工序是脱硫,用以保护转化催 化剂,以重油和煤为原料的部分氧化法,根据一氧化碳变换是否采 用耐硫的催化剂而确定脱硫的位置。工业脱硫方法种类很多,通常 是采用物理或化学吸收的方法,常用的有低温甲醇洗法(Rectisol)、 聚乙二醇二甲醚法(Selexol)等。 粗原料气经CO变换以后,变换气中除H2外,还有CO2、CO和 CH4等组分,其中以CO2含量最多。
4、循环水流程:
循环水上水→油泵→水池→送水泵→ 循环水回水
三.合成氨的工艺指标
1、温度:
循环水上水温度:≤25℃ 循环水回水温度:≤45℃ 循环油温度: ≤45℃
变换气温度: 净化气温度: 产品气温度: ≤40℃ ≤40℃ ≤40℃
2、压力
变换气压力: 净化气压力: 升降压压力: 循环油压力:
≤2.0MPa ≤2.0MPa ≤0.2MPa/min. 6.0-7.0MPa