DFMEA案例
DFMEA案例分析方法

潜在失效模式
失效后果
严重度
潜在失效原因
失效模式1 组件1(具体包括那些零件) 失效模式2 … 失效模式1 组件2(具体包括那些零件) 失效模式2 … 功能2… 重要部件 如:外壳或本体 失效模式1 …
怎么失效,后果如何? 严重度多少? … … … …
原因1 原因2 … … 原因1 原因2 … … … 原因1 原因2
DFMEA分析方法-案例(8#喷枪) 组件 功能/组件 组件1(如进水组件) 功能1(爆破压500PSI) 功能2(110LBS拉脱力测试) 功能3(20-125psi功能正常) √ √ √ √ √ 组件2(如开关组件) √ 组件3(如出水组件)
功能/组件 例如:功能1…(爆破压500PSI) (涉及的组件:)
怎么失效,后果如何? 严重度多少? … … … … … …
怎么失效,后果如何? 严重度多少?
组件3(出水组件)
组件2(开关
冲压模具dfmea案例
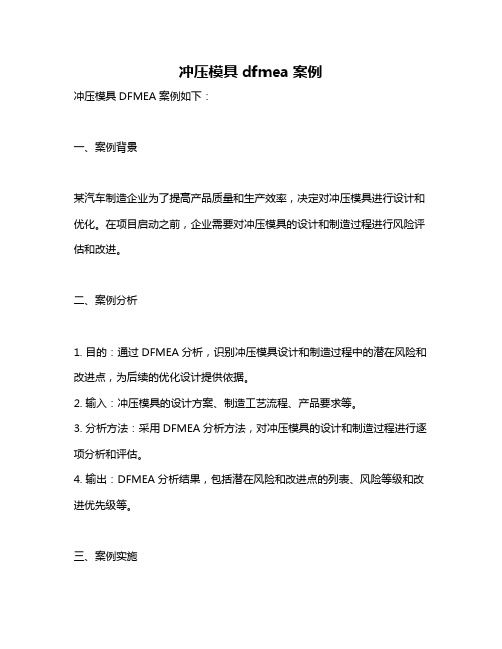
冲压模具dfmea案例
冲压模具DFMEA案例如下:
一、案例背景
某汽车制造企业为了提高产品质量和生产效率,决定对冲压模具进行设计和优化。
在项目启动之前,企业需要对冲压模具的设计和制造过程进行风险评估和改进。
二、案例分析
1. 目的:通过DFMEA分析,识别冲压模具设计和制造过程中的潜在风险和改进点,为后续的优化设计提供依据。
2. 输入:冲压模具的设计方案、制造工艺流程、产品要求等。
3. 分析方法:采用DFMEA分析方法,对冲压模具的设计和制造过程进行逐项分析和评估。
4. 输出:DFMEA分析结果,包括潜在风险和改进点的列表、风险等级和改进优先级等。
三、案例实施
1. 根据DFMEA分析结果,对冲压模具的设计和制造过程进行优化改进。
2. 针对潜在风险和改进点,制定相应的解决措施和优化方案。
3. 对优化后的冲压模具进行试验和验证,确保改进效果符合预期。
4. 将改进后的冲压模具应用于生产线上,观察其效果并进一步优化。
四、案例总结
通过DFMEA分析,企业成功地识别了冲压模具设计和制造过程中的潜在风险和改进点,并采取有效的措施进行了优化改进。
改进后的冲压模具在质量和生产效率方面都有了显著提升,为企业的可持续发展奠定了坚实基础。
设计失效分析DFMEA经典案例剖析

过程FMEA当中也应标明那些特殊的过程控制。
严重度分级:
a) 确定级别要根据经验、要小组讨论,大家形成共识.
b) 对整车的影响,假设零件(分析)装入整体运行
5
c) 可依FMEA手册参考制作自己的FMEA中严重度分级,
但要遵守大原则:
CC(关键性特性)9-10级
SC(重要特性)
5-8级
(5级以上均要措施对策,5级以下可以考虑。)
五:DFMEA应用与表格制作实战第2步 ——找失效点之2-失效模式
•是指系统、子系统或零部件有可能未达到设计意 图的形式。它可能引起更高一级子系统、系统的 潜在失效,也可能是它低一级的零部件潜在失效 的影响后果。
•对一个特定项目及其功能,列出每个潜在失效模 式。前提是这种失效可能发生,但不是一定发生。 可以将以往运行不良的研究、问题报告以及小组 的集思广益的评审作为出发点。
DFMEA基本概念相关——FMEA的类型
三:DFMEA基本概念相关——定义
DFMEA •Design Failure Mode Effect Analysis:
设计失效模式及后果分析 •失效模式: 指设计(制造)过程无法达到预定或规定的要求 所表现出的特征;如:坏品、不良设备状况等; •后果: 指失效模式对客户(包括下工序)所造成的影响;
• 要根据顾客可能发现或经历的情况来描述失效的后果,
要记住顾客可能是内部的顾客,也能是外部最终的顾客。要
清楚地说明该功能是否会影响到安全性或与法规不符。失效
的后果必须依据分析的具体系统、子系统或零部件来说明。
还应记住不同级别系统、子系统和零件之间还存在着系统层
次上的关系。比如,一个零件的断裂可能引起总成的振动,
单击添加副标题
飞机结构设计DFMEA案例分析
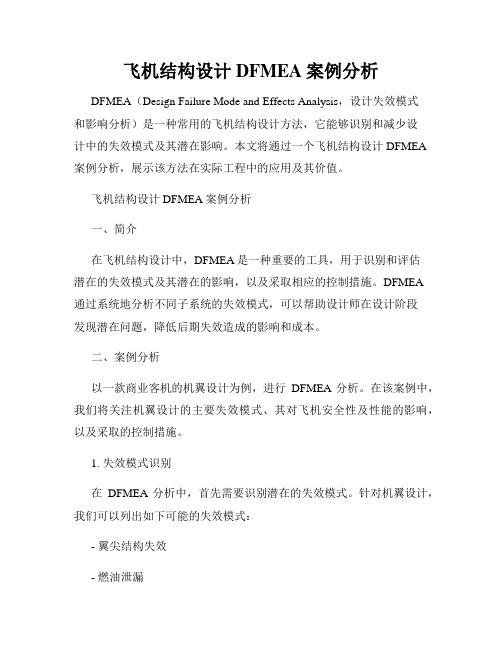
飞机结构设计DFMEA案例分析DFMEA(Design Failure Mode and Effects Analysis,设计失效模式和影响分析)是一种常用的飞机结构设计方法,它能够识别和减少设计中的失效模式及其潜在影响。
本文将通过一个飞机结构设计DFMEA 案例分析,展示该方法在实际工程中的应用及其价值。
飞机结构设计DFMEA案例分析一、简介在飞机结构设计中,DFMEA是一种重要的工具,用于识别和评估潜在的失效模式及其潜在的影响,以及采取相应的控制措施。
DFMEA通过系统地分析不同子系统的失效模式,可以帮助设计师在设计阶段发现潜在问题,降低后期失效造成的影响和成本。
二、案例分析以一款商业客机的机翼设计为例,进行DFMEA分析。
在该案例中,我们将关注机翼设计的主要失效模式、其对飞机安全性及性能的影响,以及采取的控制措施。
1. 失效模式识别在DFMEA分析中,首先需要识别潜在的失效模式。
针对机翼设计,我们可以列出如下可能的失效模式:- 翼尖结构失效- 燃油泄漏- 防冰系统故障- 翼梢削弱- 螺旋桨碰撞导致破损2. 失效影响评估接下来,需要评估上述失效模式对飞机安全性及性能的影响。
对于每个失效模式,我们需要考虑以下方面:- 安全性影响:是否会导致事故、伤亡等- 性能影响:是否会影响飞机的飞行性能、燃油消耗等3. 控制措施制定在评估失效影响后,需要制定相应的控制措施以控制或消除失效模式的潜在影响。
例如:- 对翼尖结构进行加强设计,以防止失效- 使用可靠的防冰系统,减少故障发生的可能性- 对翼梢进行特殊设计,提高其抗损伤能力- 加装螺旋桨碰撞保护装置,避免机翼受损4. 重要性评估根据控制措施的实施情况和效果,需要对各个失效模式的重要性进行评估,以确定应优先考虑的控制措施。
三、DFMEA的价值通过以上案例分析,我们可以看到DFMEA在飞机结构设计中的重要价值,主要体现在以下几个方面:1. 早期发现问题:DFMEA能够在设计阶段发现潜在问题,避免在后期出现成本高昂的修复和改进。
设计失效分析DFMEA经典案例剖析通用课件
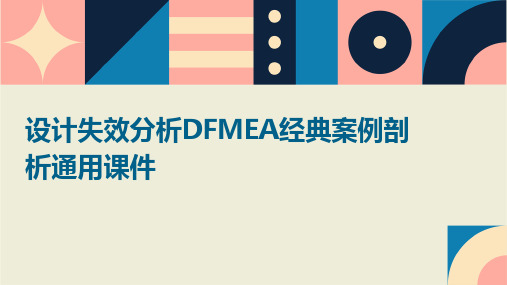
将DFMEA的应用范围从汽车行业 扩展到其他制造业领域,为更多产 品的可靠性设计和改进提供支持。
引入新技术
随着技术的不断发展,DFMEA 可引入新的工具和方法,提高 分析的效率和准确性。
加强培训与意识提升
通过培训和宣传活动,提高企业员 工对DFMEA的认识和应用能力, 促进其在产品设计和管理中的广泛 应用。
01
确定产品或系统的研究范围,明确分析对象和目标 。
02
考虑产品或系统的生命周期,包括研发、生产、使 用和维修等阶段。
03
确定研究的重点,如关键功能、高风险区域或特定 设计领域。
构建功能、性能、可靠性和安全性清单
01
列出产品或系统的所有功能和性能要求。
02 分析各功能和性能对可靠性、安全性的需求和影 响。
评估失效模式对设备操作准确性和安全性的影响程度。
改进措施
提出针对失效模式的改进措施,如优化按钮设计、改善 显示效果等。
04
案例剖析与启示
案例一剖析与启示
案例名称
某汽车刹车系统设计失效
案例描述
某汽车在行驶过程中突然出现刹车失灵,导致严重事故。经过调查发 现,设计阶段未充分考虑高温环境下刹车油膨胀问题。
提出改进措施和建议,降 低设计失效风险,提高产 品或系统的可靠性、安全 性。
03
经典案例选择与介绍
案例选择标准
案例的典型性
选择具有代表性的案例,能够体现DFMEA分析的基本原则和方 法。
案例的实用性
案例应具有实际应用价值,能够帮助企业解决实际问题。
案例的完整性
案例应包含完整的DFMEA分析过程,包括功能定义、功能分析 、失效模式分析、失效影响分析和改进措施等。
Dfmea案例

2
整体震动挤压试验
6
108
现场做防震处理
绝缘注塑件 电池壳体
注塑件起火 电解液挥发 电池漏液
安全事故 电池 容量降低 安全事 故
10
1
阻燃、绝缘试验
6
20
更换绝缘注塑件 更换电池 更换电池
7 9
2 2 单体震动挤压试验
6 6
84 108
高压箱
漏电 过电流 输出不受控制
安全事故 安全事故 安全事故
10 9 9
5
120
定期检查和更新BMS系统
4 10 8 4
6 1 5 5
更换SOC算法 BMS 控制系统升级 BMS 控制系统升级
充放电性能测试 充放电性能测试 充放电性能测试
6 6 6 6
144 60 240 120
定期检查和更新BMS系统 定期检查和更新BMS系统 定期检查和更新BMS系统 定期检查和更新BMS系统
电池组整体温度过高 影响电池工作 电池组整体温度过低 影响电池工作 噪音过大 影响乘车环境
电池间温度一致性差 影响电池工作 整体温度高,管理目 影响电池工作 标无法实现 连接片过热 安全事故
电池管理系
数据采样干扰性大和 影响用户使用 采样不准确 SOC异常 影响用户使用
4
6
BMS 控制系统升级
老化试验
电池组过充未报警和 安全事故 未保护 电池组过放未报警和 影响电池寿命或永久性损 未保护 坏 BMS通信异常 影响电池工作
'01 PSW'!H6 '01 PSW'!F25
现行探测性设计控制
现场电池组无输出电 电池组无法工作 压
探 测 度 数 3
R P N 63
太阳能逆变器设计DFMEA案例分析

太阳能逆变器设计DFMEA案例分析DFMEA(Design Failure Modes and Effects Analysis)是用于评估产品设计可能出现的故障、效应以及相应的预防措施的方法。
今天我们将运用DFMEA方法,对一款太阳能逆变器的设计进行案例分析。
一、产品描述该太阳能逆变器为一款出口型产品,主要用于太阳能发电系统中,将直流电转换为交流电。
产品工作电压范围为DC 200-600V,最大输出功率为3.5KW,具备防雷、过温、短路、过压、过流等保护功能。
产品尺寸为320 * 190 * 85mm,重量约为4KG。
二、DFMEA分析2.1 确认可能出现的失效模式失效模式 | 效应 | 潜在原因 | 严重程度 | 发生频率 | 检测方法 | 措施---|---|---|---|---|---|---1. 输出电压不稳定 | 安全隐患、影响发电效率 | 元器件老化、电路设计不合理 | 10 | 5 | 防雷测试、故障监测 | 加强过电压、过流保护,采用优质元器件2. 输出电压、电流过大 | 电路烧毁、安全隐患 | 过流、过压等保护措施失效、元器件老化 | 10 | 5 | 防雷测试、故障监测 | 加强过电压、过流保护,采用优质元器件3. 输出电压有过大波动 | 影响发电效率 | 电容故障、电路设计不合理 | 8 | 3 | 产品测试 | 采用优质元器件,加强 PCB 线路电磁兼容性设计4. 输入电压不稳定 | 影响发电效率 | 电池老化、外界电压波动 | 7 | 4 | 故障监测、产品测试 | 采用输入电源波动范围更大的元件,加强电池保护5. 元器件老化 | 失效 | 元器件过度发热、使用寿命达到 | 9 | 7 | 测试、监测 | 采用易于更换的元器件,定期维护,加强散热设计2.2 计算风险优先等级风险优先等级 = 严重程度 ×发生频率 ×检测方法失效模式 | 风险优先等级 | 处理优先级---|---|---1. 输出电压不稳定 | 250 | 12. 输出电压、电流过大 | 250 | 23. 输出电压有过大波动 | 72 | 34. 输入电压不稳定 | 112 | 45. 元器件老化 | 441 | 52.3 制定预防措施- 对于风险优先等级为1、2的失效模式,我们将加强过电压、过流保护,并采用优质元器件,以降低失效的可能性。
汽车空调系统设计DFMEA案例分析

汽车空调系统设计DFMEA案例分析DFMEA简介DFMEA(Design Failure Mode and Effects Analysis,设计失效模式与影响分析)是一种常用的质量管理工具,用于在产品设计阶段识别并解决潜在的失效模式及其影响。
本文将以汽车空调系统设计为案例,探讨如何应用DFMEA来提高汽车空调系统设计的安全性和可靠性。
一、设计失效模式与影响分析(DFMEA)DFMEA是一种以系统化和有序方式对产品设计进行评估和分析的方法。
它的主要目的是识别可能的失效模式、评估其严重程度以及制定相应的纠正和预防措施。
下面我们将根据DFMEA的步骤,对汽车空调系统进行案例分析。
1. 制定DFMEA团队与范围首先,确定参与DFMEA的团队成员,包括汽车空调系统设计的工程师、质量控制专家、测试工程师等。
明确DFMEA的范围和目标,以汽车空调系统各个子系统为分析对象。
2. 识别失效模式对汽车空调系统设计进行全面的分析,列举可能的失效模式。
比如,制冷剂泄漏、温度控制失效、空调系统过热等。
3. 确定失效模式的可能原因针对每个失效模式,分析其潜在的原因,如设计不当、材料选择不当、制造工艺缺陷等。
以制冷剂泄漏为例,可能的原因包括密封件老化、接口松动等。
4. 评估失效的严重程度对每个失效模式进行严重程度评估,考虑其对汽车空调系统性能、安全性和可靠性的影响。
以温度控制失效为例,可能导致车内温度无法调节,对车内乘客的舒适度产生较大影响。
5. 确定控制措施针对每个失效模式确定相应的预防和纠正措施,以减少失效概率和降低失效的严重程度。
比如,在设计阶段增加密封件的检测和更换计划,严格控制安装过程中的接口紧固力矩。
6. 跟踪执行和评估效果实施控制措施后,跟踪其执行情况,并对效果进行评估。
通过实际数据的反馈,不断优化和改善汽车空调系统的设计。
二、汽车空调系统DFMEA案例分析以下是针对汽车空调系统的DFMEA案例分析,以帮助读者更好地理解DFMEA方法的应用。
DFMEA新版案例(收放机-AM收音功能)
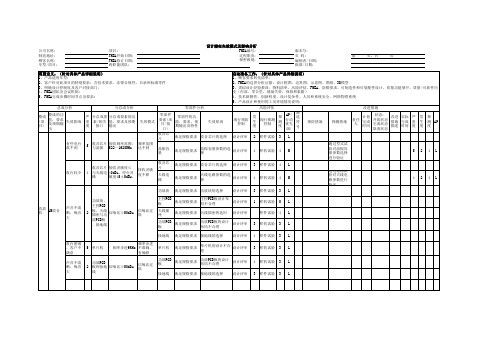
设计评审
5
收音芯片 接收频率范围: 频率范围 与晶振 522~1620KHz 达不到
晶振容 量
满足规格要求
晶振容量参数的选 择
设计评审
风险评估
发 生 度
现行探测 控制
探 测 度
AP( 行动 优先 级)
筛 选 符 号
2 样件试验 3 L
4 样机试验 4 M
收台较少
4
收音芯片 与天线电 路
接收灵敏度≤ 40dBu,停台灵 敏度45±5dBu,
4 样机试验 3 3 样不准确,
有偏移
单片机
满足规格要求
单片机的设计不合 理
设计评审
3 样机试验 3
L
声音不清 晰,噪音 大
功放PCB 2 板和接地 信噪比≥50dBu
线
信噪比过 低
功放PCB 板
满足规格要求
功放PCB板的设计 布局不合理
设计评审
接地线 满足规格要求 接地线的选择 设计评审
启动准备工作:(针对具体产品详细说明) 1、顾客要求转化清单: 2、FMEA的边界分析证据:设计框图、边界图、示意图、图纸、3D模型 3、类似设计经验教训:物料清单、风险评估、FMEA、防错要求、可制造性和可装配性设计、质量功能展开、质量/可靠性历 史(内部、零公里、现场失效、保修和索赔) 4、技术新颖性、创新程度、设计复杂性、人员和系统安全、网络物理系统 5、产品设计和使用的工况环境情况说明:
主控PCB 板
满足规格要求
主控PCB板设计布 局不合理
设计评审
天线插 座
满足规格要求 天线插座的选用
设计评审
功放PCB 板
满足规格要求
功放PCB板的设计 布局不合理
新版dfmea系统分析案例

新版DFMEA系统分析案例案例背景一家汽车制造公司正在推出一款全新的SUV车型,为了确保车辆的质量和可靠性,公司决定采用新版的DFMEA(设计失效模式和影响分析)系统进行系统分析。
DFMEA是一种在设计阶段评估和减少系统风险的方法,它能够识别潜在的失效模式、分析其影响和严重性,并提供相应的改进措施。
系统分析步骤步骤一:定义系统首先,团队需要明确系统边界、系统功能和设计要求。
在这个案例中,团队需要定义SUV车型的关键系统和子系统,例如发动机、悬挂系统、制动系统、安全气囊等。
步骤二:识别失效模式在这一步骤中,团队需要对每个系统和子系统逐一进行分析,识别潜在的失效模式。
以发动机系统为例,可能的失效模式包括发动机无法启动、发动机自动熄火等。
步骤三:分析影响和严重性对于每个失效模式,团队需要评估其对系统和用户的影响,并确定其严重性。
影响可以包括安全风险、性能降低、故障率增加等。
严重性通常可以按照某个评估标准进行定量评估,例如使用1-10的等级评定。
步骤四:确定改进措施针对每个失效模式和其严重性,团队需要制定相应的改进措施。
例如,在发动机无法启动的失效模式下,可能的改进措施包括增加备用电池、加强电路连接等。
步骤五:实施改进措施在这一步骤中,团队需要逐一实施确定的改进措施,并对其进行记录和追踪。
例如,在实施了增加备用电池的改进措施后,团队需要跟踪发动机启动失效模式的发生率,以评估该措施的有效性。
案例分析结果通过对SUV车型各个系统和子系统的分析,团队得出以下结论:•发动机系统中,发动机自动熄火失效模式对车辆安全性有较大影响,严重性评级为8,建议增加燃油供给系统的检测和报警机制。
•悬挂系统中,悬挂系统异常噪声失效模式对乘坐舒适度和驾驶体验有较大影响,严重性评级为7,建议改进悬挂系统的阻尼设计。
•制动系统中,制动距离过长失效模式对行车安全性有较大影响,严重性评级为9,建议优化刹车片材料和刹车系统的液压传动机制。
结论随着汽车制造业的快速发展,确保车辆质量和可靠性变得至关重要。
dfmea案例
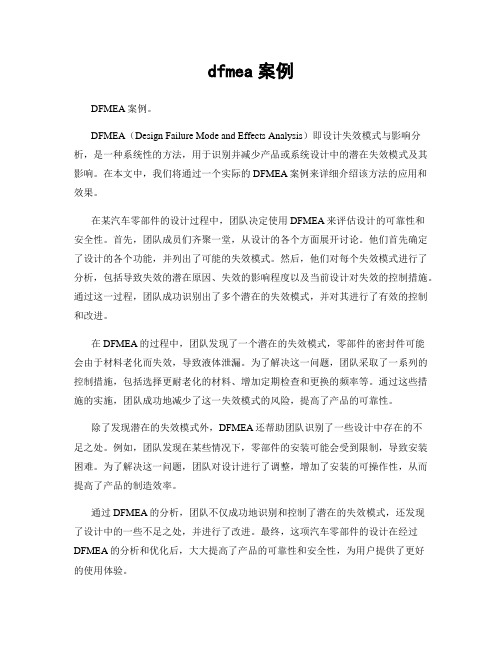
dfmea案例DFMEA案例。
DFMEA(Design Failure Mode and Effects Analysis)即设计失效模式与影响分析,是一种系统性的方法,用于识别并减少产品或系统设计中的潜在失效模式及其影响。
在本文中,我们将通过一个实际的DFMEA案例来详细介绍该方法的应用和效果。
在某汽车零部件的设计过程中,团队决定使用DFMEA来评估设计的可靠性和安全性。
首先,团队成员们齐聚一堂,从设计的各个方面展开讨论。
他们首先确定了设计的各个功能,并列出了可能的失效模式。
然后,他们对每个失效模式进行了分析,包括导致失效的潜在原因、失效的影响程度以及当前设计对失效的控制措施。
通过这一过程,团队成功识别出了多个潜在的失效模式,并对其进行了有效的控制和改进。
在DFMEA的过程中,团队发现了一个潜在的失效模式,零部件的密封件可能会由于材料老化而失效,导致液体泄漏。
为了解决这一问题,团队采取了一系列的控制措施,包括选择更耐老化的材料、增加定期检查和更换的频率等。
通过这些措施的实施,团队成功地减少了这一失效模式的风险,提高了产品的可靠性。
除了发现潜在的失效模式外,DFMEA还帮助团队识别了一些设计中存在的不足之处。
例如,团队发现在某些情况下,零部件的安装可能会受到限制,导致安装困难。
为了解决这一问题,团队对设计进行了调整,增加了安装的可操作性,从而提高了产品的制造效率。
通过DFMEA的分析,团队不仅成功地识别和控制了潜在的失效模式,还发现了设计中的一些不足之处,并进行了改进。
最终,这项汽车零部件的设计在经过DFMEA的分析和优化后,大大提高了产品的可靠性和安全性,为用户提供了更好的使用体验。
综上所述,DFMEA作为一种系统性的方法,能够帮助团队全面地识别并减少产品或系统设计中的潜在失效模式及其影响。
通过对失效模式的分析和控制,团队不仅可以提高产品的可靠性和安全性,还能够发现设计中的不足之处,并进行相应的改进。
智能家居节能设备设计DFMEA案例分析
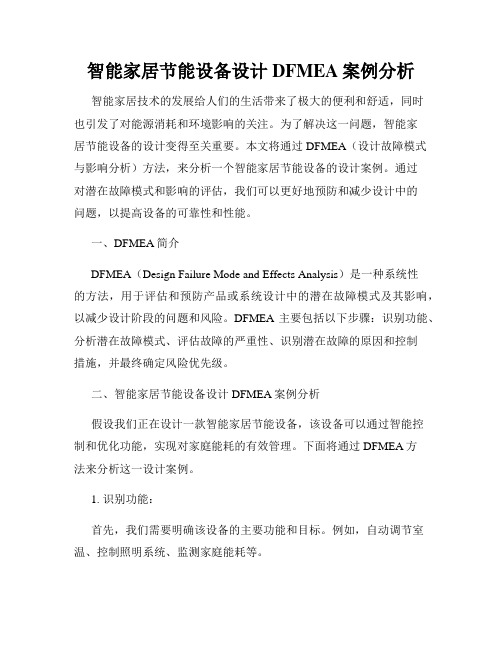
智能家居节能设备设计DFMEA案例分析智能家居技术的发展给人们的生活带来了极大的便利和舒适,同时也引发了对能源消耗和环境影响的关注。
为了解决这一问题,智能家居节能设备的设计变得至关重要。
本文将通过DFMEA(设计故障模式与影响分析)方法,来分析一个智能家居节能设备的设计案例。
通过对潜在故障模式和影响的评估,我们可以更好地预防和减少设计中的问题,以提高设备的可靠性和性能。
一、DFMEA简介DFMEA(Design Failure Mode and Effects Analysis)是一种系统性的方法,用于评估和预防产品或系统设计中的潜在故障模式及其影响,以减少设计阶段的问题和风险。
DFMEA主要包括以下步骤:识别功能、分析潜在故障模式、评估故障的严重性、识别潜在故障的原因和控制措施,并最终确定风险优先级。
二、智能家居节能设备设计DFMEA案例分析假设我们正在设计一款智能家居节能设备,该设备可以通过智能控制和优化功能,实现对家庭能耗的有效管理。
下面将通过DFMEA方法来分析这一设计案例。
1. 识别功能:首先,我们需要明确该设备的主要功能和目标。
例如,自动调节室温、控制照明系统、监测家庭能耗等。
2. 分析潜在故障模式:针对每一项功能,我们需要识别可能出现的故障模式。
以自动调节室温功能为例,可能会出现以下故障模式:温度传感器失效、控温装置故障、温度误差过大等。
3. 评估故障的严重性:对于每个故障模式,我们需要评估其对整个系统的影响严重性。
以温度传感器失效为例,可能会导致室温无法监测和调节,进而影响家庭能耗控制。
4. 识别潜在故障的原因和控制措施:针对每个故障模式,我们需要识别潜在的故障原因,并提出相应的控制措施。
以温度传感器失效为例,可能的原因包括零部件老化、电路连接松动等,相应的控制措施可以是定期检查和维护零部件连接及更换传感器。
5. 确定风险优先级:基于故障的严重性和潜在故障的发生概率,我们可以对各个故障模式进行风险优先级排序。
嵌入式工控板卡DFMEA范例

芯片组本身实际抗高温与规格 书不符合(或策划采用筛选的 2 办法来过高温) PCB布局不合理导致散热器设 计受结构限制,主板上大热源 3 间距小互相影响。
MOS选取不满足要求
2
其他元器件选取不满足要求 2
PCB走线不当
3
内存时钟带负载能力不够
3
CF接口设计没有DMA功能
2
7
显示芯片电源纹波太大
3
显示
2
42 / 28 / 28 /
沈晖 沈晖
1.用测试开发板验证 2.根据实际样板结果更改
2
参与PCB布局和评审,合理解 决散热结构问题。
2
仔细计算所选MOS能否满足功 耗需求,参考以前成熟项目
3
选用规格符合温度范围的要 求的元件
2
1:PCB走线尽量按照design
guide的要求,实在不能满足
的参考其他成熟方案。
XXXX 版本:XX
行动结果 已采取的行动
S O D RP N
XXX 版本:XX
6
网络灯 电源IC 电源 CPU
网络灯接反
网络灯异常
5
TPS51116为新导入 IC,没有验证过
无法满足内存供电需 求
8
无法满足主板上电 时序要求
主板无法正常工作
9
纹波电流大
系统在运行过程中不
稳定,特别是跑大的 8
系统时,容易死机
网络变压器的电源与RTL8111C 冲突
3
设计规范和实际指示灯的连接 不一致,或线材连接反
2
IC供货来源
2
新导入的IC,设计中存在缺陷 4
全新chipset,没有验证
3
电源纹波控制没有满足芯片的 要求
dfmea案例

DFMEA案例背景介绍DFMEA(Design Failure Mode and Effects Analysis)是一种用于产品设计和开发过程中的风险评估方法。
它旨在识别和评估设计过程中可能存在的潜在故障模式及其对产品性能和可靠性的影响,以便制定相应的风险控制和改进措施,确保产品的质量和安全性。
案例描述本案例以电动汽车的电池管理系统设计为例,通过DFMEA方法来评估设计过程中的潜在故障和对电池管理系统性能的影响。
1. 制定DFMEA项目计划首先,制定DFMEA项目计划。
明确项目目标、参与人员和资源分配,确定每个阶段的时间表和里程碑。
2. 确定设计功能确定电池管理系统的设计功能,即系统需要实现的功能和性能指标。
例如,确保电池充电和放电过程的安全性、性能和效率。
3. 识别潜在故障模式通过团队讨论和技术文献调研,识别可能导致故障的潜在模式。
例如,电池温度过高、电池充电过程中的电流过大等。
4. 评估故障严重性对于每个潜在故障模式,评估其对电池管理系统性能的影响严重性。
根据影响的程度,分为低、中、高三个等级进行评估。
5. 评估故障原因和控制措施对于每个潜在故障模式,分析造成故障的原因,并制定相应的控制措施。
例如,对于电池温度过高的故障模式,可以通过安装温度传感器并设计合适的散热系统来控制温度。
6. 评估故障检测和容错措施对于每个潜在故障模式,评估故障的检测和容错措施。
例如,对于电池充电过流的故障模式,可以通过设计电流传感器和过流保护装置来检测和避免过大的电流。
7. 定义风险优先级根据故障严重性、故障概率和故障检测和容错措施的可靠性,定义每个故障模式的风险优先级。
优先级高的故障模式应该得到更加紧急的关注和处理。
8. 实施改进措施根据风险优先级,制定并实施相应的改进措施。
例如,对于优先级高的故障模式,可以进行重新设计、更换材料或改进生产工艺等。
9. 风险评估复审定期复审DFMEA,对已实施的改进措施进行评估和监控。
dfmea案例
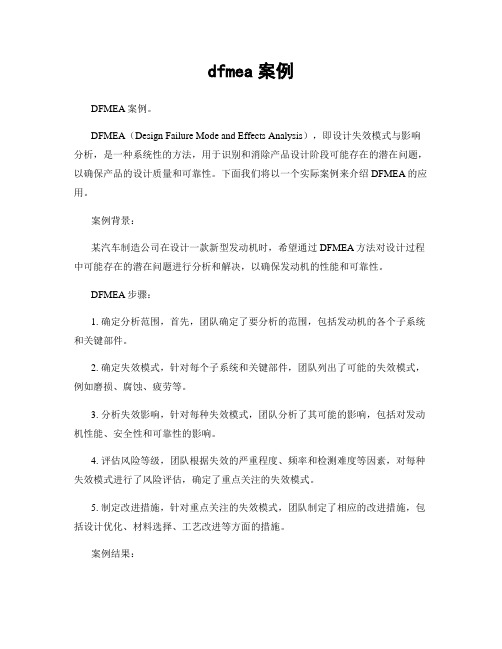
dfmea案例DFMEA案例。
DFMEA(Design Failure Mode and Effects Analysis),即设计失效模式与影响分析,是一种系统性的方法,用于识别和消除产品设计阶段可能存在的潜在问题,以确保产品的设计质量和可靠性。
下面我们将以一个实际案例来介绍DFMEA的应用。
案例背景:某汽车制造公司在设计一款新型发动机时,希望通过DFMEA方法对设计过程中可能存在的潜在问题进行分析和解决,以确保发动机的性能和可靠性。
DFMEA步骤:1. 确定分析范围,首先,团队确定了要分析的范围,包括发动机的各个子系统和关键部件。
2. 确定失效模式,针对每个子系统和关键部件,团队列出了可能的失效模式,例如磨损、腐蚀、疲劳等。
3. 分析失效影响,针对每种失效模式,团队分析了其可能的影响,包括对发动机性能、安全性和可靠性的影响。
4. 评估风险等级,团队根据失效的严重程度、频率和检测难度等因素,对每种失效模式进行了风险评估,确定了重点关注的失效模式。
5. 制定改进措施,针对重点关注的失效模式,团队制定了相应的改进措施,包括设计优化、材料选择、工艺改进等方面的措施。
案例结果:通过DFMEA分析,团队发现了一些潜在的设计问题,并及时采取了相应的改进措施。
例如,在分析润滑系统时,团队发现了润滑油管路设计存在潜在的腐蚀和堵塞风险,因此对润滑油管路进行了优化设计,采用耐腐蚀材料,并增加了清洗通道,以确保润滑系统的可靠性。
另外,在分析发动机散热系统时,团队发现了散热片设计存在的疲劳裂纹风险,因此对散热片的材料和结构进行了改进,提高了其抗疲劳性能。
结论:通过DFMEA分析,团队及时发现并解决了潜在的设计问题,确保了发动机的性能和可靠性。
这个案例充分展示了DFMEA方法在产品设计过程中的重要作用,通过系统性的分析和改进措施,帮助企业提高了产品的质量和竞争力。
在实际应用中,DFMEA需要团队成员的密切合作和专业知识的支持,以确保分析的全面性和准确性。
汽车座椅系统设计DFMEA案例分析
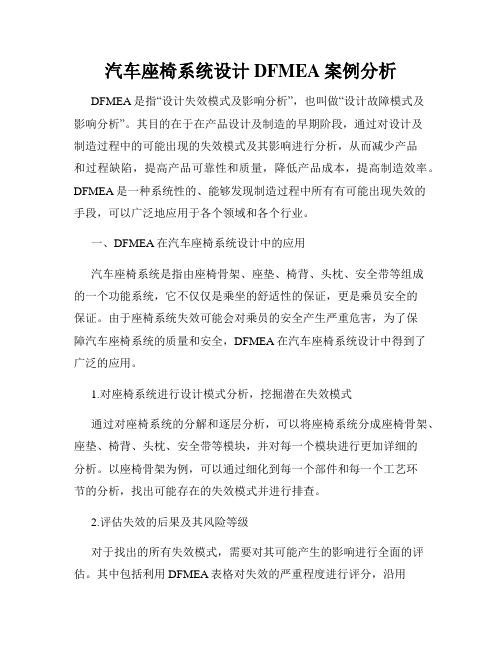
汽车座椅系统设计DFMEA案例分析DFMEA是指“设计失效模式及影响分析”,也叫做“设计故障模式及影响分析”。
其目的在于在产品设计及制造的早期阶段,通过对设计及制造过程中的可能出现的失效模式及其影响进行分析,从而减少产品和过程缺陷,提高产品可靠性和质量,降低产品成本,提高制造效率。
DFMEA是一种系统性的、能够发现制造过程中所有有可能出现失效的手段,可以广泛地应用于各个领域和各个行业。
一、DFMEA在汽车座椅系统设计中的应用汽车座椅系统是指由座椅骨架、座垫、椅背、头枕、安全带等组成的一个功能系统,它不仅仅是乘坐的舒适性的保证,更是乘员安全的保证。
由于座椅系统失效可能会对乘员的安全产生严重危害,为了保障汽车座椅系统的质量和安全,DFMEA在汽车座椅系统设计中得到了广泛的应用。
1.对座椅系统进行设计模式分析,挖掘潜在失效模式通过对座椅系统的分解和逐层分析,可以将座椅系统分成座椅骨架、座垫、椅背、头枕、安全带等模块,并对每一个模块进行更加详细的分析。
以座椅骨架为例,可以通过细化到每一个部件和每一个工艺环节的分析,找出可能存在的失效模式并进行排查。
2.评估失效的后果及其风险等级对于找出的所有失效模式,需要对其可能产生的影响进行全面的评估。
其中包括利用DFMEA表格对失效的严重程度进行评分,沿用“Severity(S)”、“Occurrence(O)”和“Detection(D)”三个评分维度,以确定失效风险等级和失效预防的措施。
3.采取有效的应对措施DFMEA表格所反映出来的失效预防措施,需要通过跟踪监测、检查验证等手段,不断地优化和完善。
特别是,在实现座椅系统设计关键措施的绩效目标时,应该依据风险等级严重程度作加权决策。
二、DFMEA案例分析1.座椅整体结构优化1.1 步骤使用CAD软件,对座椅骨架的结构进行分析和优化。
分析虚拟端口位置,确定合适的结构参数。
确定结构材料和工艺条件,进一步分析结构强度问题,检验设计的可行性。
设计失效分析DFMEA经典案例剖析
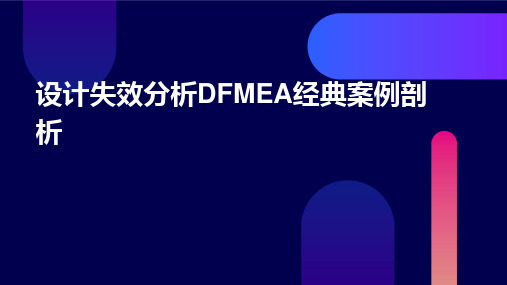
优质的产品是企业赢得市场 份额的关键因素之一。通过 DFMEA分析优化产品设计, 可以提高产品的竞争力,帮
助企业抢占市场份额。
增加企业收益
提高产品质量、降低生产成 本和增强市场竞争力都可以 为企业带来更多的收益。
07
总结与展望
DFMEA应用现状及挑战
01
应用现状
02 广泛应用于产品设计阶段,以预防潜在的设计缺 陷。
根据风险等级划分结果,优先处 理高风险失效模式,制定相应的 改进措施。
02
改进措施实施与验 证
实施改进措施后,对产品进行重 新评估,确保改进措施的有效性。
03Βιβλιοθήκη 持续改进在产品生命周期中持续进行 DFMEA分析,不断优化产品设 计,提高产品质量和可靠性。
03
经典案例一:汽车零部件设计 失效分析
案例背景介绍
改进措施实施及效果验证
改进措施
针对识别出的失效模式和原因,采取了相应的改进措施,如优化散热设计、改进电源管理模块、修复软件编码错误和 内存泄漏等。
效果验证
在实施改进措施后,对设备进行了重新测试和验证。结果显示,电池温度明显降低,屏幕闪烁问题得到解决,应用程 序运行稳定且不再崩溃。
经验教训
该案例表明,在设计阶段充分考虑潜在失效模式和影响至关重要。通过DFMEA等方法进行预防性分析, 可以及早发现并解决潜在问题,提高产品的可靠性和安全性。同时,持续改进和优化设计也是提升产品 质量和用户满意度的关键所在。
探测度评估
评估现有控制措施在多大程度上能够探测到失效模式的发生。
风险优先数计算
计算风险优先数(RPN)
将严重度、频度、探测度的评估结果相乘,得到每种失效模式的风险优先数。
dfmea案例

dfmea案例
DFMEA是产品设计过程中的一种风险管理工具,通过对设计
过程中的潜在失效模式及其影响进行分析,识别风险并提出风险控制措施,以确保产品设计的可靠性和质量。
下面是一则DFMEA案例,以一款自动洗衣机的设计为例:
1. 设计阶段:自动洗衣机的设计,主要风险是洗涤过程中出现故障,导致无法正常完成洗涤任务。
2. 风险识别:在洗涤过程中,可能存在以下潜在失效模式及其影响:
- 水泵失效:导致无法排出洗涤液,影响清洁效果,甚至导
致洗衣机内部泄漏;
- 电机失效:导致洗涤筒无法正常旋转,影响洗涤效果;
- 控制电路失效:导致洗衣机无法启动、停止或切换程序,
影响使用者的操作体验。
3. 风险评估:针对每个潜在失效模式,对其发生的可能性、严重性和检测难度进行评估。
例如,水泵失效的可能性较低,但影响严重,检测难度中等;电机失效的可能性较高,影响严重,检测难度较低;控制电路失效的可能性中等,但影响严重,检测难度较低。
4. 风险控制措施:
- 水泵失效:选择可靠稳定的水泵供应商,进行质量把关,
并设置水位传感器来监测水位,当水位过高时,自动停止进水,
避免因水泵失效导致泄漏;
- 电机失效:选择高品质、耐用的电机,并定期进行维护和保养,以延长使用寿命并降低故障率;
- 控制电路失效:采用双备份设计,避免单点故障,同时进行严格的质量控制,确保控制电路的可靠性。
通过DFMEA分析和改进措施的实施,可以减少洗衣机故障发生的可能性,并提升产品的可靠性和质量。
这个案例仅作为示例,实际DFMEA过程中,需要根据具体产品和设计过程确定潜在失效模式,评估风险,制定相应的风险控制措施。
dfmea第五版模板分析实例
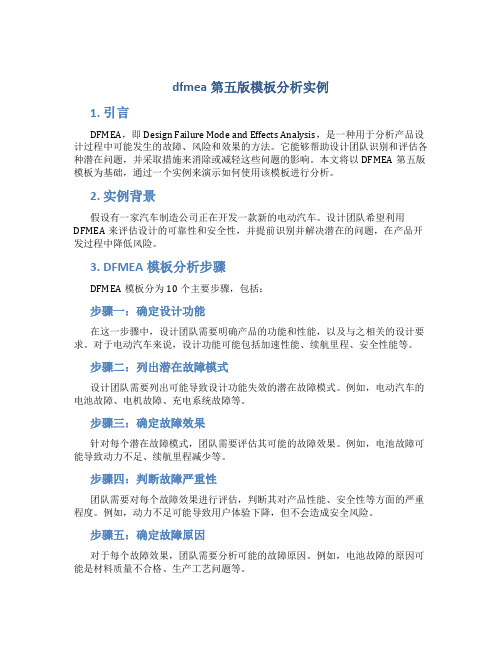
dfmea第五版模板分析实例1. 引言DFMEA,即Design Failure Mode and Effects Analysis,是一种用于分析产品设计过程中可能发生的故障、风险和效果的方法。
它能够帮助设计团队识别和评估各种潜在问题,并采取措施来消除或减轻这些问题的影响。
本文将以DFMEA第五版模板为基础,通过一个实例来演示如何使用该模板进行分析。
2. 实例背景假设有一家汽车制造公司正在开发一款新的电动汽车。
设计团队希望利用DFMEA来评估设计的可靠性和安全性,并提前识别并解决潜在的问题,在产品开发过程中降低风险。
3. DFMEA模板分析步骤DFMEA模板分为10个主要步骤,包括:步骤一:确定设计功能在这一步骤中,设计团队需要明确产品的功能和性能,以及与之相关的设计要求。
对于电动汽车来说,设计功能可能包括加速性能、续航里程、安全性能等。
步骤二:列出潜在故障模式设计团队需要列出可能导致设计功能失效的潜在故障模式。
例如,电动汽车的电池故障、电机故障、充电系统故障等。
步骤三:确定故障效果针对每个潜在故障模式,团队需要评估其可能的故障效果。
例如,电池故障可能导致动力不足、续航里程减少等。
步骤四:判断故障严重性团队需要对每个故障效果进行评估,判断其对产品性能、安全性等方面的严重程度。
例如,动力不足可能导致用户体验下降,但不会造成安全风险。
步骤五:确定故障原因对于每个故障效果,团队需要分析可能的故障原因。
例如,电池故障的原因可能是材料质量不合格、生产工艺问题等。
步骤六:评估现有的设计控制措施团队需要评估当前设计中已有的控制措施,以减轻或消除潜在故障模式的影响。
例如,对于电池故障,是否存在电池过压保护功能等。
步骤七:确定潜在控制措施对于未能完全消除潜在故障模式的控制措施,团队需要确定额外的潜在控制措施。
例如,对于电池故障,可以增加电池故障检测系统。
步骤八:评估控制措施效果对于已确定的控制措施,团队需要评估其对潜在故障模式的效果。
dfmea案例结构件

dfmea案例结构件DFMEA(Design Failure Mode and Effects Analysis)是一种设计故障模式和影响分析的方法,用于评估和减少产品或系统设计中的潜在故障和风险。
下面是一个关于结构件的 DFMEA 案例示例:假设我们正在设计一个机械零件,这个零件是一个连接两个部件的关键连接器。
我们可以使用 DFMEA 来评估这个连接器设计中可能发生的潜在故障和风险。
1. 识别设计要素:我们首先需要识别连接器的设计要素,例如几何形状、材料、制造工艺等。
2. 确定潜在故障模式:针对每个设计要素,我们要考虑可能的故障模式。
例如,设计要素可能包括连接器的强度、刚度、密封性等,对应的潜在故障模式可能是强度不足、变形、漏气等。
3. 评估故障后果:对于每个潜在故障模式,我们评估其可能导致的后果。
后果可以分为功能故障、安全风险、性能下降等方面。
例如,连接器强度不足可能导致断裂,从而导致系统失效。
4. 确定故障发生的原因:对于每个故障模式,我们要分析可能的故障原因。
这通常涉及到错误的设计、制造缺陷、材料问题等。
例如,连接器强度不足可能是由于设计计算错误或材料强度不符合要求。
5. 评估和确认风险等级:根据故障的潜在后果和发生概率,给每个故障模式分配风险等级。
这通常是一个定性评估,可以根据风险矩阵或相关的评估工具进行。
6. 提出风险控制措施:为每个高风险故障模式提出相应的风险控制措施,以减轻或消除其影响。
这可能包括改进设计、选择更适合的材料、加强制造过程等。
7. 实施控制措施并持续监测:根据评估的措施,进行设计和制造改进,并确保实施措施的有效性。
同时,持续监测产品性能和故障数据,以便在需要时进行修订和改进。
通过进行 DFMEA,我们可以识别潜在的设计故障模式和风险,并采取相应的控制措施来改进产品设计和减少潜在风险。
这样可以提高产品的可靠性、性能和安全性。
- 1、下载文档前请自行甄别文档内容的完整性,平台不提供额外的编辑、内容补充、找答案等附加服务。
- 2、"仅部分预览"的文档,不可在线预览部分如存在完整性等问题,可反馈申请退款(可完整预览的文档不适用该条件!)。
- 3、如文档侵犯您的权益,请联系客服反馈,我们会尽快为您处理(人工客服工作时间:9:00-18:30)。
经验不
线
足
无尘
计算其零件的绝缘
Hi-Pot不良
性能达不到要求 环境
客户提供规格方法
重要原因
调查方法
1.计算绝缘规格时失误,达
不到电压要求
2.选材不当,材料的绝缘规
格与产品规格不配
3.材料的结构设计不合理.
1. 计算后,需有人审查; 2. 对选择材料需测试后使用
测试
调查结果验证
主要判定
无法使用,产生HI-POT不良
DPS-200PB-156 A DFMEA
1
PDF 文件使用 "pdfFactory Pro" 试用版本创建
目錄
•組員 •品質展開表 •系統展開表 •魚骨圖分析 •柏拉圖分析 •DFMEA
2
PDF 文件使用 "pdfFactory Pro" 试用版本创建
A SS S
CA CC
BB
中
19 20 要 求 品 质 重 要 度
5
5 3
3 1 1
3
3
3
1 1
3
1 1 1 1 1
3
要求品质企划
顾客
竞争分析
企
重要 满意 竞争 划
度
度(本 公司)
者
水 准
改销 善售 比重 率点
矩阵中◎表示强关连 ○表示中关连
△表示弱关连 销售重点◎表示乘1.5
○表示乘1.2 无记号则为1
直接原因 间接原因
7
PDF 文件使用 "pdfFactory Pro" 试用版本创建
失效项目
失效影响
调查地点
调查时间
调查数量
如何发现
调查者
现状描述 光耦合器
绝缘不够
材料
原
材质不符设计要 求
工程部
HI-POT 儀
04/08’04
机器
3
人
经验不 足
测试
HI-POT不良
特
出壓地電寸 電測測流
A
T
性 壓試試
S B量 音 壓 流
過 材 散 Hold 功 輸 屏
Up
入
溫 料 熱 Time 率 電 敝
對對要 權權度 重重區
零
EF
壓
﹪分
組
材
性
件
質
01Case
△
02線材
03Hsk
◎
B
04Label
05Fan
◎
◎
A
06Socket
○△
07Screw
△○○
C
08Fuse
△
09IC
機構部分設計失誤發生不良柏拉圖
15
100.0% 100.0%
93.3%
86.7%
73.3%
80.0%
75.0%
10
60.0%
50.0%
40.0%
5
25.0%
0
數列2 數列1
FAN / 散熱
6 40.0%
Cas e/固 定 連 接 外觀、屏蔽 3 60.0%
Secondly Team member
金偉志 李明 張良 張勝屏 李樹 李正龍 林秀春
3
PDF 文件使用 "pdfFactory Pro" 试用版本创建
品 质 特 性
要 求 品 质
品質展開表(一)
1
2
3
4
5
6
7
8
9
10
11 12
13 14 15 16 17 18
CLA
ion
SSB
4
溫度
PDF 文件使用 "pdfFactory Pro" 试用版本创建
品質展開表(二)
品
123456
7 8 9 10 11 12 13 14 15 16 17 18 19 20 21 22 23 24 25 絕 相 重
質
輸 高 接 漏 尺 C M重 噪 過 過
调查结果验证 產品NOP
主要判定 直接原因 直接原因
11
失效项目 现状描述 Y電容
失效影响 绝缘不够
调查地点 工程部
调查时间 04/08’04
调查数量 3
如何发现 测试
调查者
材料
机器
人
原 材质不符设计要
因 分
求
HI-POT儀
经验不 足
HI-POT不良
析
无尘
计算失误,选材不当 客户提供规格方法
环境
重要原因: 1). 审查客户规格失误; 2). 计算单体失误,造成选材不当
2. 计算电压,電流 大小时失误. 3.对于材料的选择達 不到產品要求.
检查客户规格,并测试
1. 对客户提供的规格,需詳細計算.
2. 不同材料都需進行審查,並滿載測試.
调查结果验证 主品燒机
主要判定
直接原因 直接原因
9
PDF 文件使用 "pdfFactory Pro" 试用版本创建
C
输 出 电 压
高接 压地 测测 试试
漏 电 流
尺 寸
A S E 材
M T 重噪 过 B 量音 压
F
过过 流温
材 料
散 热 性
hold up 功 tim 率
输 入 电
屏 蔽
e
压
质
◎/25 01 Out Put电 压稳 定
◎ /25
02 符 合 产 品 安 规 要 求
◎ ◎ /25 ◎ /25 /2 5
B10 光耦器
B 11 Y 電容
輸出線材
A21 FA N 線 材
A22
HSK1 A31
HSK2 A32
HSK3 A33
HSK4 A34 Spec A41
Bar Code A42
Warning A 43
FG A71
FAN A72
PWB A73
Case A74
Fuse----F1
NTC----NTC1 ZD901
调查数量
如何发现
现状描述 开关管
击穿
工程部
04/08’04
3
测试
材料
電子負 机器
经验不
人
載
足
材质不符设计要
产品烧机
原求
因
无尘
分
客户提供规格方法
析
选材电压不符要求
环境
调查者
重要原因: 1). 客户要求产品功率,设计计算失误; 2).选材不符要求 ;
原 因 調 查 驗 証
建议对 策拟定
重要原因
调查方法
1. 对于客户提供 的规格产生误解
△
○△
10電阻
△
△○○
C
11電解電容 △
△
12變壓器
◎○
○
◎
◎
S
13Choke
○
14M osfet er
○○
◎
A
15二极体
○
△
16三极体
○
△
17光耦器
◎○
◎
A
18Y電容
◎◎◎
S
絕對權重
相對權重﹪
重要度區分
5
PDF 文件使用 "pdfFactory Pro" 试用版本创建
穩壓管
ZD952
IC1
ZD10
IC903
IC601
IC602
IC701
R1X X X ---R9X X X
C1X X X ---C9X X X
T1
TZ01
FL1
L901
FL2
L3
Q1 Q3
L1,L2 IC701 C 10 1 ,L 1 0 2
D 1----D 9X X X CR101
CR151 CR301
◎
○ /9
/15
◎/5
◎ /5
◎ /1 5
绝对权重 相对权重﹪ 重要项目 竞争分析 优
55 25 25 25 17 15 15 6 30 55 30 30 15 13 5 47 20 8
436 436 436 436 436 436 436 436 436 436 436 436 436 436 436 436 436 436 12.6% 5% 5% 5% 3.4% 12.6% 3% 1% 7% 12.6% 7% 7% 12.6% 2% 1% 10% 4% 1.8%
○ /5 ○ /5 ○ /5 ○ /5 ○ /5
03 外观无瑕疵
△ /3 ◎ /15
◎
04 使用寿命长
/15
05 安装方便
◎ /5
◎ /5
06 体积小
◎ /5
07 效率高
◎/15
◎
08 噪音低
/1 5
09 ( 过 压 ) 保 护 功 能 ◎/15 (输出)
◎ /15 ◎ ◎ /15 /15
10 搞干扰能力强 11 适应环境能力强
失效项目
失效影响
调查地点
调查时间
调查数量
如何发现
现状描述 風扇
散熱效杲不好
工程部
04/08’04
3
测试
机器
人
材料
原 因
分 材质不符设计要 析求
電子負載
经验不 足
产品烧机
无尘
选材轉速不符要求
环境
客户提供规格方法
调查者
重要原因: 1). 客户要求产品功率,设计计算失误; 2).选材不符要求 ;
原 因 調 查 驗 証
POWER SUPPLY 系統展開