真空热处理技术
热处理新技术

现代热处理新技术热处理技术是金属材料在经过多道加工过程后为改善其机械性质所作的一种技术。
一个不当的表面处理,将使产品在制程中使前面所作的加工处理全成为泡影,无形间降低了产品的生产力及质量并且提高制造的成本,相对地也降低产业的竞争力,有鉴以此我们将介绍几种现代热处理新技术供各产业参考应用。
1、真空热处理技术方法:真空热处理将为金属工件置于已抽真空的容器中,然后依所需之目的进行各种反复加热、冷却操作的一种技术。
用途或优点:工件表面为光辉面、工件变形小、工件不会被氧化及脱碳或渗碳、无腐蚀和公害问题、质量稳定等,适合于工具或模具之热处理,为未来热处理技术的主流。
2、零下处理技术方法:零下处理是将金属工件置于零度低温的环境中,迫使金属工件改变材料性能的一种热处理法,传统的零下处理通常是在钢铁材料作淬火处理后施行,以有效降低残留奥斯田铁含量,可以使钢铁材料尺寸稳定性及提高耐磨耗特性,尤其是高碳含量的工具钢材,效果最好。
用途或优点:零下处理的应用将应用到超硬合金及铜合金等非铁类金属,以改善工件内部应用残留的问题,以提升工件的寿命为原来的两倍以上。
3、离子氮化技术方法:先将金属工件置于真空容器中,再通入氮气,将容器本身当作阳极、工件当作阴极,然后通以高压直流电,强迫将氮气解离成正电的氮离子,并以极高的速度冲向阴极金属工件,使得金属工件表面得以瞬间氮化的一种表面热处理技术。
用途或优点:有效提高金属材料之耐磨耗、耐疲劳、耐腐蚀等性质,另外它也具有工件变形量小、无公害及省能源的特点。
广泛应用于各种钢铁工件及非铁金属工件之氮化处理。
4、低压渗氮技术方法:低压渗氮技术系在大约300mba的作用压力下,打入NH3,N2O及N2等进行的气体渗氮,亦可再加CH4进行气体渗氮及碳化。
处理温度约在400~600℃左右。
低压渗氮及渗氮碳化可使工件表面得到较高硬度的渗氮层,增加工件表面压缩应力,提高其耐磨耗性及耐疲劳性;渗氮速度快,渗氮层组织可选择为纯扩散层或为致密白层,可渗氮深孔狭缝,工件表面洁净,量产性佳,省人工、省气体能源,作业环境优良,应用日益广泛。
真空热处理工艺精选全文完整版
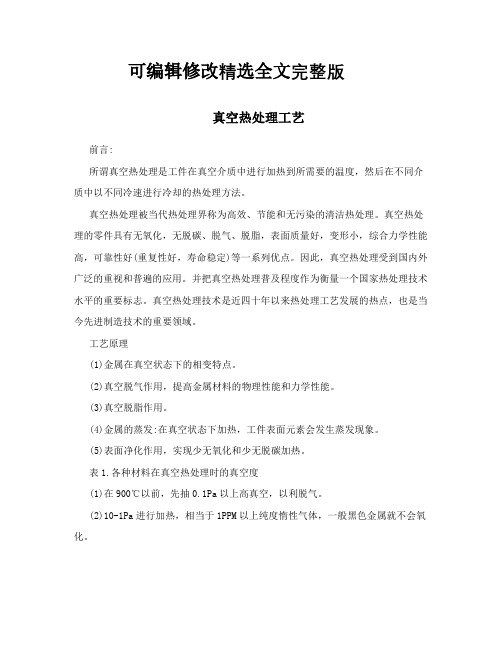
可编辑修改精选全文完整版真空热处理工艺前言:所谓真空热处理是工件在真空介质中进行加热到所需要的温度,然后在不同介质中以不同冷速进行冷却的热处理方法。
真空热处理被当代热处理界称为高效、节能和无污染的清洁热处理。
真空热处理的零件具有无氧化,无脱碳、脱气、脱脂,表面质量好,变形小,综合力学性能高,可靠性好(重复性好,寿命稳定)等一系列优点。
因此,真空热处理受到国内外广泛的重视和普遍的应用。
并把真空热处理普及程度作为衡量一个国家热处理技术水平的重要标志。
真空热处理技术是近四十年以来热处理工艺发展的热点,也是当今先进制造技术的重要领域。
工艺原理(1)金属在真空状态下的相变特点。
(2)真空脱气作用,提高金属材料的物理性能和力学性能。
(3)真空脱脂作用。
(4)金属的蒸发:在真空状态下加热,工件表面元素会发生蒸发现象。
(5)表面净化作用,实现少无氧化和少无脱碳加热。
表1.各种材料在真空热处理时的真空度(1)在900℃以前,先抽0.1Pa以上高真空,以利脱气。
(2)10-1Pa进行加热,相当于1PPM以上纯度惰性气体,一般黑色金属就不会氧化。
(3)充入惰性气体时,如充133Pa,(50%N2+50%H2)的氮氢混合气体,其效果比10-2,10-3Pa真空还好。
此时氧分压66.5Pa是安全的。
(4)真空度与钢表面光亮度有对应关系。
(5)一般10-3~133Pa真空范围内,真空度温差为±5℃,如气压上升,温度均匀性下降,所以充气压力应尽量可能低些。
2、加热和预热温度: 表2 预热温度参考表3、真空淬火加热时间图1真空加热时的特性曲线图2炉温和被加热工件表面与中心温度t总=t均+t保 t均=a`×ht保为相变时间,t均为均热时间,a`为透热系数(分/mm),h为有效厚度(mm)。
三(真空淬火冷却在淬火时我们都要考虑到所热处理工件的材质、形状、技术要求,以及该材质“5” 曲线来选择合理的淬火冷速,一般情况下有真空油淬和真空气淬( 在这里主要分析真空油淬)。
JB-T 9210-1999真空热处理技术标准(1)

书山有路勤为径,学海无涯苦作舟
JB/T 9210-1999 真空热处理技术标准(1)
前言
本标准是对ZB J36 01590《真空热处理》的修订.
本标准与ZB J36 01590 在以下主要技术内容上有所改变:
真空淬火炉,真空回火炉有效加热区的温度偏差由通常不得超过
±10℃改为±5℃;真空退火炉有效加热区的温度偏差由不得超过±15℃改为±8℃;
真空淬火炉和真空退火炉的加热元件对地绝缘电阻应大于2 kΩ,回火炉应大于500 kΩ改为真空淬火炉,回火炉和退火炉的加热元件对地绝缘电阻应大于2 kΩ;
按有关规定作了编辑性修改.
本标准自实施之日起代替ZB J36 01590.
本标准由全国热处理标准化技术委员会提出并归口.
本标准负责起草单位:上海市机械制造工艺研究所.
本标准主要起草人:屠恒悦,梅志强.
本标准于1990 年4 月19 日首次发布.
1、范围
本标准规定了真空热处理设备的特殊要求,真空热处理常用金属材料,真空热处理的工艺过程及其基本工艺参数.
本标准适用于金属的真空淬火,真空回火,真空退火,真空固溶热处理及真空时效等工艺.
2、引用标准。
真空热处理
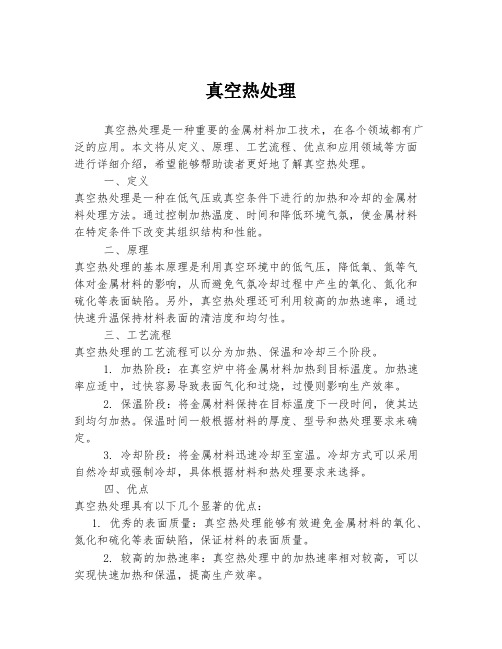
真空热处理真空热处理是一种重要的金属材料加工技术,在各个领域都有广泛的应用。
本文将从定义、原理、工艺流程、优点和应用领域等方面进行详细介绍,希望能够帮助读者更好地了解真空热处理。
一、定义真空热处理是一种在低气压或真空条件下进行的加热和冷却的金属材料处理方法。
通过控制加热温度、时间和降低环境气氛,使金属材料在特定条件下改变其组织结构和性能。
二、原理真空热处理的基本原理是利用真空环境中的低气压,降低氧、氮等气体对金属材料的影响,从而避免气氛冷却过程中产生的氧化、氮化和硫化等表面缺陷。
另外,真空热处理还可利用较高的加热速率,通过快速升温保持材料表面的清洁度和均匀性。
三、工艺流程真空热处理的工艺流程可以分为加热、保温和冷却三个阶段。
1. 加热阶段:在真空炉中将金属材料加热到目标温度。
加热速率应适中,过快容易导致表面气化和过烧,过慢则影响生产效率。
2. 保温阶段:将金属材料保持在目标温度下一段时间,使其达到均匀加热。
保温时间一般根据材料的厚度、型号和热处理要求来确定。
3. 冷却阶段:将金属材料迅速冷却至室温。
冷却方式可以采用自然冷却或强制冷却,具体根据材料和热处理要求来选择。
四、优点真空热处理具有以下几个显著的优点:1. 优秀的表面质量:真空热处理能够有效避免金属材料的氧化、氮化和硫化等表面缺陷,保证材料的表面质量。
2. 较高的加热速率:真空热处理中的加热速率相对较高,可以实现快速加热和保温,提高生产效率。
3. 均匀的加热效果:真空热处理具有良好的温度均匀性和恒温性能,可以使金属材料达到均匀加热的效果,避免因加热不均导致的质量问题。
4. 可控性强:真空热处理过程中可以根据具体需要调节加热温度、时间和气压等参数,提高处理的可控性和灵活性。
五、应用领域真空热处理广泛应用于航空航天、汽车制造、机械制造、电子设备和医疗器械等领域。
1. 航空航天领域:真空热处理可应用于制造航空发动机叶片、涡轮叶片、航空零件等高温、高强度要求的金属材料。
真空热处理操作流程

真空热处理操作流程
真空热处理是一种利用特殊工艺,将材料加热到一定温度并在真空环
境下进行处理的方法。
下面将详细介绍真空热处理的操作流程。
一、材料准备
在进行真空热处理前,需要对材料进行准备。
首先要对材料进行分类,并根据材料的性质选择合适的加工方法。
其中最重要的便是确定适宜
的加热温度和持温时间。
二、真空加热
当材料准备就绪后,需要进行真空加热。
首先将加工好的材料放入真
空炉内,然后将炉门关闭。
随后,要进行抽真空,将炉内空气排除,
直到达到预定的真空度。
接下来,设定加热温度,将温度控制在预定的范围内,并保持一定的
持温时间。
此时,材料就可以在高温条件下进行处理,以达到预定的
目的。
三、冷却处理
完成真空热处理后,需要进行冷却处理。
通常采用的方法是通过水循环来进行快速冷却,以降低材料的温度。
此时,需要注意控制冷却速度和冷却时间,避免材料受到过度温度变化的影响。
四、处理结束
当冷却操作完成后,即可打开炉门,取出处理好的材料。
此时,需要对材料进行检测,以确保热处理效果达到要求。
如果材料质量符合要求,即可完成真空热处理,否则需要重新处理。
总之,真空热处理是一种非常重要的材料加工方法,其操作流程必须严格按照工艺要求进行。
只有这样才能确保材料的质量和性能达到最佳的状态。
真空热处理技术

真空热处理技术
真空热处理技术是一种在低于一个大气压的气氛环境中进行热处理的工艺,包括真空环境下的加热、冷却和保温等。
真空热处理可以实现无氧化、无脱碳、无渗碳,去掉工件表面的磷屑,并有脱脂除气等作用,从而达到表面光亮净化的效果。
同时,真空热处理技术还可以实现气氛控制热处理,将金属工件在1个大气压以下加热,加速化学热处理的吸附和反应过程。
真空热处理技术广泛应用于各种特殊合金热处理和一般工程用钢的热处理中,可以提高热处理质量和产品性能,同时降低生产成本和维护成本。
此外,真空热处理还可以实现多元共渗等特殊热处理工艺,如渗碳、渗氮、渗铬、渗硼等。
在设备方面,真空热处理炉的维修是真空炉管理的重要内容之一,需要定期进行维修和保养。
同时,根据不同的生产需求和工艺要求,选择合适的真空炉和热处理工艺也是非常重要的。
总的来说,真空热处理技术是一种高效、高质量、低成本的热处理工艺,在制造业和材料科学领域有着广泛的应用前景。
真空热处理技术的发展

M nCrW V 5CrW 2Si 9M n2V Cr5M o1V Cr12 Cr12M oV 5CrNiM o 5CrNiM o 4Cr5M oSiV 4Cr5M oSiV1 4Cr13 W 6M o5Cr4V2
W 2M o9Cr4VCo8
-
G C r15 35Cr2Ni2M oA
-
相应压力下淬火
200
200
54
100
140
160
50
160
200
200
52
-
100
120
56
-
140
160
50
100
160
200
66
120
180
200
66
140
200
200
67
-
10
20
63
20
40
60
54
5
10
25
64
4 真空渗碳
• 真空渗碳多采用真空-充气脉冲式渗碳工艺,以避 免渗碳过程中产生内氧化等缺陷。该工艺具有工件表 面光亮、生产效率高、成本低、可进行盲孔或小孔渗 碳等优点,但工件表面碳黑多、尖角过渗等问题突出, 应予防止。
( wt% )
750
910
1000
0.005
等轴晶
粗大针状
粗大针状
0.2
等轴晶
细小针状
细小针状
1.5
等轴晶
细小针状
细小针状
2.1
等轴晶
细小针状
细小针状
断面收缩率 (%) 16 9
1100 粗大针状 粗大针状 粗大针状 粗大针状
7 真空炉设计和制造
金属表面真空热处理技术

金属表面真空热处理技术金属表面真空热处理技术是一种重要的表面改性技术,广泛应用于航空航天、汽车、能源、机械等领域。
该技术主要是通过在真空环境中对金属表面进行加热处理,从而实现金属表面的硬化、耐磨、耐腐蚀等性能的提高。
本文将详细介绍金属表面真空热处理技术的原理、工艺及应用。
1. 金属表面真空热处理技术的原理金属表面真空热处理技术的基本原理是在真空环境中对金属表面进行加热,使金属表面达到一定的温度,保持一定的时间,然后进行冷却。
在这个过程中,金属表面与内部的组织发生相应的变化,从而达到改善金属表面性能的目的。
金属表面真空热处理技术主要包括以下几个阶段:1.真空环境建立:将金属工件放入真空加热炉中,通过抽真空的方式,使炉内压力降至一定范围内,一般为10-3~10-1 Pa。
2.加热:开启加热器,将金属工件加热到指定的温度,温度范围一般为200~700℃。
3.保持:在指定温度下保持一定时间,使金属表面发生相变和组织变化。
4.冷却:关闭加热器,停止抽真空,让金属工件在真空环境中自然冷却,或者采用气体冷却等方式。
2. 金属表面真空热处理技术的工艺金属表面真空热处理技术的工艺主要包括以下几个方面:1.真空度:真空度是影响真空热处理效果的关键因素之一。
真空度越高,金属表面的氧化物越少,表面质量越好。
一般要求真空度在10-3~10-1 Pa范围内。
2.加热温度:加热温度是影响金属表面真空热处理效果的另一个关键因素。
加热温度越高,金属表面的硬化层越厚,硬度越高。
但加热温度过高,容易导致金属内部出现裂纹等缺陷。
一般加热温度范围为200~700℃。
3.保持时间:保持时间是指金属工件在指定温度下保持的时间。
保持时间越长,金属表面的硬化层越厚,硬度越高。
但保持时间过长,容易导致金属内部出现裂纹等缺陷。
一般保持时间为0.5~3小时。
4.冷却方式:金属表面真空热处理后的冷却方式有自然冷却、气体冷却等。
自然冷却是将金属工件在真空环境中自然冷却,冷却速度较慢,但可以避免表面氧化。
真空热处理的工艺

真空热处理的工艺
真空热处理是将材料加热到一定温度,然后在真空环境中保温一段时间,最后以合适的速率冷却材料的工艺。
真空热处理的工艺包括以下几个步骤:
1. 加热:将待处理的材料放入真空炉中,通过电阻加热器或感应加热器加热材料到设定的温度。
加热过程需要控制加热速率和最终温度,以确保材料达到所需的热处理效果。
2. 保温:在材料达到设定温度后,保持一段时间进行保温处理。
在真空环境下进行保温,可以避免材料表面的氧化或其他化学反应。
3. 冷却:保温结束后,需要将材料迅速冷却到室温。
冷却速率可以影响材料的组织结构和性能,因此需要精确控制冷却速度。
4. 排放:冷却完毕后,打开真空炉,将热处理过的材料取出。
真空热处理的目的是改善材料的硬度、强度、韧性、耐腐蚀性和其他性能。
常见的真空热处理方法包括退火、淬火、回火和固溶处理等。
不同材料和热处理目的需要采用不同的真空热处理工艺和参数。
真空热处理具有许多优点,例如可以避免氧化、减少变形、提高材料品质、确保加热和冷却的均匀性等。
因此,真空热处理在航空航天、汽车制造、电子产业和其他高端制造领域得到广泛应用。
热处理新技术简介

(1)离子渗氮
离子渗氮是在低于一个大气压的渗氮气氛中利用工件(阴极)和阳极之间产生的辉 光放电进行渗氮的工艺。离子渗氮常在真空炉内进行,通入氨气或氮、氢混合气体,炉 压在133~1 066 Pa。接通电源,在阴极(工件)和阳极(真空器)间施加400~700 V直 流电压,使炉内气体放电,在工件周围产生辉光放电现象,并使电离后的氮正离子高速 冲击工件表面,获得电子还原成氮原子而渗入工件表面,并向内部扩散形成氮化层。
电子束加热工件时,表面温度和淬硬深度取决于电子束的能量大小和轰击时间。试 验表明,功率密度越大,淬硬深度越深,但轰击时间过长会影响自激冷作用。
电子束热处理的应用与激光热处理相似,其加热效率比激光高,但电子束热处理需 要在真空下进行,可控制性也差,而且要注意X射线的防护。
8
3)离子热处理
离子热处理是利用低真空中稀薄气体辉光放电产生的等离子体 轰击工件表面,使工件表面成分、组织和性能改变的热处理工艺。 离子热处理主要包括离子渗氮和离子渗碳等工艺。
可以在零件选定表面局部加 热,解决拐角、沟槽、盲孔 底部、深孔内壁等一般热处 理工艺难以解决的强化问题。
生产效率高,易实现自动化, 无需冷却介质,对环境无污 染。
度为0.25~0.35 mm,表面硬度 为64 HRC的四条淬火带。处理 后使用寿命提高10倍,而费用 仅为高频感应加热淬火和渗氮 处理的 1 。
5
4 高能束表面改性热处理
高能束表面改性热处理是利用激光、电子束、等离子弧等高功率、高能量密度 能源加热工件的热处理工艺的总称。
1)激光热处理
激光热处理是利用激光器发射的高能激光束扫描工件表面,使表面迅速加热到高温, 以达到改变局部表层组织和性能的热处理工艺。目前工业用激光器大多是二氧化碳激光器。
真空炉热处理工艺

真空炉热处理工艺引言:真空炉热处理工艺是一种广泛应用于金属材料加工领域的热处理技术。
它通过在高温下将材料置于真空环境中进行处理,以改变材料的物理和化学性质,从而提高材料的性能和品质。
本文将详细介绍真空炉热处理工艺的原理、应用和优势。
一、真空炉热处理工艺的原理真空炉热处理工艺是在无氧或低氧环境中进行的,由于真空环境中几乎没有气体分子,因此可以避免材料在高温下与氧气发生反应,防止材料表面氧化和变质。
在真空炉中,通过加热和冷却等步骤,对材料进行控制加热和冷却,以实现材料的相变、组织结构改变和性能提升。
二、真空炉热处理工艺的应用1. 金属材料的强化处理:真空炉热处理工艺可以通过控制加热和冷却速度,改变金属材料的晶体结构,提高其强度、硬度和耐磨性。
2. 金属材料的退火处理:真空炉热处理工艺可以通过控制温度和保温时间,使金属材料内部的应力得到释放,消除材料的变形和裂纹。
3. 金属材料的淬火处理:真空炉热处理工艺可以通过控制加热和冷却速度,将金属材料迅速冷却至室温,使其快速形成马氏体结构,提高材料的硬度和强度。
4. 金属材料的回火处理:真空炉热处理工艺可以通过控制温度和保温时间,使金属材料内部的脆性组织转变为韧性组织,提高材料的韧性和抗冲击性。
三、真空炉热处理工艺的优势1. 高精度控制:真空炉热处理工艺可以精确控制加热、保温和冷却过程的温度和时间,以满足不同材料和工艺要求。
2. 无氧环境:真空炉热处理工艺在无氧或低氧环境中进行,可以避免材料表面的氧化和变质,保持材料的原有性能。
3. 均匀加热:真空炉热处理工艺通过辐射加热和对流传热相结合的方式,可以实现对材料的均匀加热,避免温度梯度过大引起的变形和裂纹。
4. 环保节能:真空炉热处理工艺中不需要使用传统的加热介质,如气体或液体,减少了能源的消耗和污染的排放。
结论:真空炉热处理工艺作为一种先进的热处理技术,广泛应用于金属材料加工领域。
它通过在无氧或低氧环境中对材料进行控制加热和冷却,改变材料的物理和化学性质,提高材料的性能和品质。
真空热处理工艺
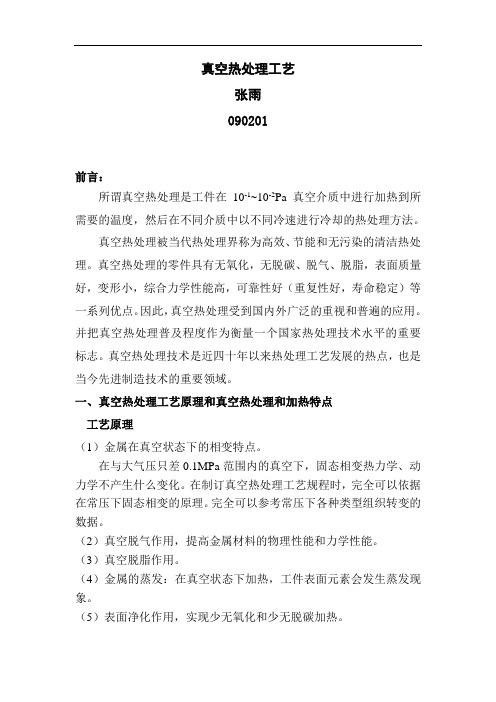
真空热处理工艺张雨090201前言:所谓真空热处理是工件在10-1~10-2Pa真空介质中进行加热到所需要的温度,然后在不同介质中以不同冷速进行冷却的热处理方法。
真空热处理被当代热处理界称为高效、节能和无污染的清洁热处理。
真空热处理的零件具有无氧化,无脱碳、脱气、脱脂,表面质量好,变形小,综合力学性能高,可靠性好(重复性好,寿命稳定)等一系列优点。
因此,真空热处理受到国内外广泛的重视和普遍的应用。
并把真空热处理普及程度作为衡量一个国家热处理技术水平的重要标志。
真空热处理技术是近四十年以来热处理工艺发展的热点,也是当今先进制造技术的重要领域。
一、真空热处理工艺原理和真空热处理和加热特点工艺原理(1)金属在真空状态下的相变特点。
在与大气压只差0.1MPa范围内的真空下,固态相变热力学、动力学不产生什么变化。
在制订真空热处理工艺规程时,完全可以依据在常压下固态相变的原理。
完全可以参考常压下各种类型组织转变的数据。
(2)真空脱气作用,提高金属材料的物理性能和力学性能。
(3)真空脱脂作用。
(4)金属的蒸发:在真空状态下加热,工件表面元素会发生蒸发现象。
(5)表面净化作用,实现少无氧化和少无脱碳加热。
(6)金属实现无氧化加热所需的真空度。
二、真空热处理工艺参数的确定1、真空度:表1.各种材料在真空热处理时的真空度(1)在900℃以前,先抽0.1Pa以上高真空,以利脱气。
(2)10-1Pa进行加热,相当于1PPM以上纯度惰性气体,一般黑色金属就不会氧化。
(3)充入惰性气体时,如充133Pa,(50%N2+50%H2)的氮氢混合气体,其效果比10-2~10-3Pa真空还好。
此时氧分压66.5Pa是安全的。
(4)真空度与钢表面光亮度有对应关系。
(5)一般10-3~133Pa真空范围内,真空度温差为±5℃,如气压上升,温度均匀性下降,所以充气压力应尽量可能低些。
2、加热和预热温度:表2 预热温度参考表800~900 550-600-600 800-8501200以上550-60 -10503、真空淬火加热时间图1真空加热时的特性曲线图2炉温和被加热工件表面与中心温度t总=t均+t保t均=a`×ht保为相变时间,t均为均热时间,a`为透热系数(分/mm),h为有效厚度(mm)。
真空高压气淬炉热处理技术要求
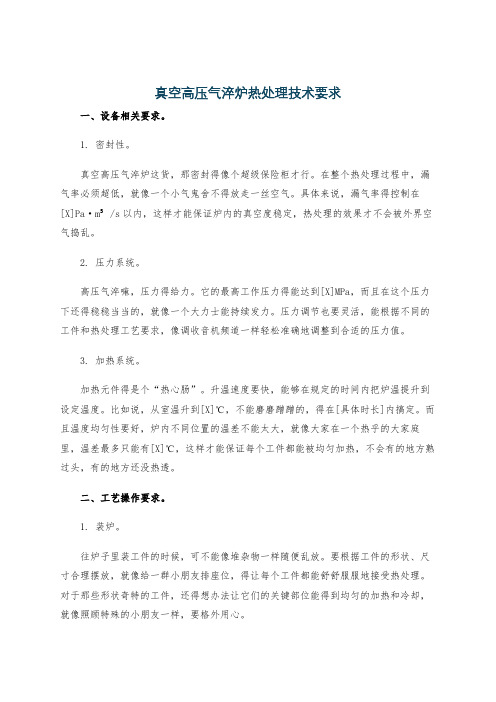
真空高压气淬炉热处理技术要求一、设备相关要求。
1. 密封性。
真空高压气淬炉这货,那密封得像个超级保险柜才行。
在整个热处理过程中,漏气率必须超低,就像一个小气鬼舍不得放走一丝空气。
具体来说,漏气率得控制在[X]Pa·m³/s以内,这样才能保证炉内的真空度稳定,热处理的效果才不会被外界空气捣乱。
2. 压力系统。
高压气淬嘛,压力得给力。
它的最高工作压力得能达到[X]MPa,而且在这个压力下还得稳稳当当的,就像一个大力士能持续发力。
压力调节也要灵活,能根据不同的工件和热处理工艺要求,像调收音机频道一样轻松准确地调整到合适的压力值。
3. 加热系统。
加热元件得是个“热心肠”。
升温速度要快,能够在规定的时间内把炉温提升到设定温度。
比如说,从室温升到[X]℃,不能磨磨蹭蹭的,得在[具体时长]内搞定。
而且温度均匀性要好,炉内不同位置的温差不能太大,就像大家在一个热乎的大家庭里,温差最多只能有[X]℃,这样才能保证每个工件都能被均匀加热,不会有的地方熟过头,有的地方还没热透。
二、工艺操作要求。
1. 装炉。
往炉子里装工件的时候,可不能像堆杂物一样随便乱放。
要根据工件的形状、尺寸合理摆放,就像给一群小朋友排座位,得让每个工件都能舒舒服服地接受热处理。
对于那些形状奇特的工件,还得想办法让它们的关键部位能得到均匀的加热和冷却,就像照顾特殊的小朋友一样,要格外用心。
2. 真空度控制。
在开始热处理之前,先得把炉内抽成真空。
这个真空度要达到[X]Pa,就像把炉子里的空气都赶得干干净净。
在整个热处理过程中,真空度也要一直保持在这个水平,要是真空度突然下降,就像有人突然闯进了一个安静的房间,会影响热处理的质量。
3. 加热曲线。
加热过程得按照预定的加热曲线来。
这个加热曲线就像一张烹饪菜谱,不同的工件材质和要求有不同的“菜谱”。
要严格控制升温速度、保温时间和降温速度。
比如说,对于[某种材质]的工件,升温速度要控制在[X]℃/min,在[X]℃下保温[X]分钟,然后降温速度也要按照规定来,不能太快也不能太慢,太快了工件会像被冷水突然泼到一样受不了,太慢了又会影响生产效率。
真空光亮热处理技术
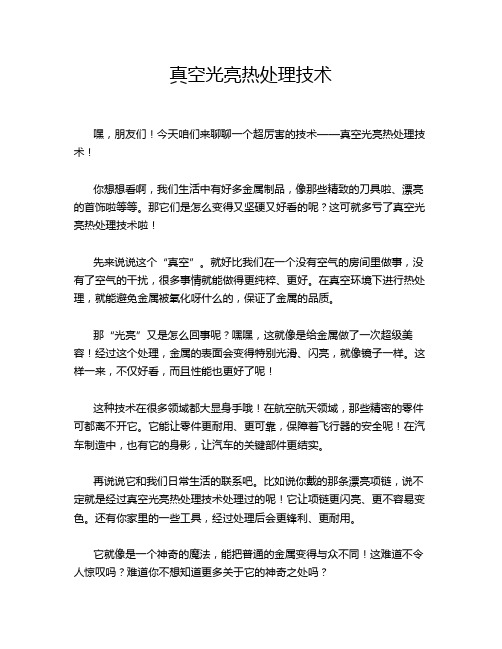
真空光亮热处理技术
嘿,朋友们!今天咱们来聊聊一个超厉害的技术——真空光亮热处理技术!
你想想看啊,我们生活中有好多金属制品,像那些精致的刀具啦、漂亮的首饰啦等等。
那它们是怎么变得又坚硬又好看的呢?这可就多亏了真空光亮热处理技术啦!
先来说说这个“真空”。
就好比我们在一个没有空气的房间里做事,没有了空气的干扰,很多事情就能做得更纯粹、更好。
在真空环境下进行热处理,就能避免金属被氧化呀什么的,保证了金属的品质。
那“光亮”又是怎么回事呢?嘿嘿,这就像是给金属做了一次超级美容!经过这个处理,金属的表面会变得特别光滑、闪亮,就像镜子一样。
这样一来,不仅好看,而且性能也更好了呢!
这种技术在很多领域都大显身手哦!在航空航天领域,那些精密的零件可都离不开它。
它能让零件更耐用、更可靠,保障着飞行器的安全呢!在汽车制造中,也有它的身影,让汽车的关键部件更结实。
再说说它和我们日常生活的联系吧。
比如说你戴的那条漂亮项链,说不定就是经过真空光亮热处理技术处理过的呢!它让项链更闪亮、更不容易变色。
还有你家里的一些工具,经过处理后会更锋利、更耐用。
它就像是一个神奇的魔法,能把普通的金属变得与众不同!这难道不令人惊叹吗?难道你不想知道更多关于它的神奇之处吗?
总之,真空光亮热处理技术真的是超级厉害的!它让我们的生活变得更加美好,让金属制品有了更高的品质和更好的性能。
这就是科技的魅力啊!。
真空光亮热处理

真空光亮热处理1. 简介真空光亮热处理是一种常用于金属材料的表面改性技术。
通过在真空环境中加热金属材料,使其表面发生化学物质的变化,从而改善材料的性能和外观。
这项技术在航空航天、汽车制造、电子设备等领域有着广泛的应用。
2. 工艺流程真空光亮热处理一般包括以下几个主要步骤:2.1 清洗首先,需要对待处理的金属材料进行清洗,以去除表面的污垢和氧化物。
常用的清洗方法包括机械清洗、溶剂清洗和酸碱清洗等。
2.2 加热待处理的金属材料放置在真空炉中,并通过加热使其达到所需温度。
加热过程中需要控制好温度和时间,以确保金属材料达到适合处理的状态。
2.3 真空处理当金属材料达到所需温度后,开始进行真空处理。
通过抽取真空,将周围的气体和杂质排除,使金属材料处于真空环境中。
真空环境可以有效减少氧化、脱气和污染等问题,从而保证处理效果的稳定性和一致性。
2.4 光亮处理在真空环境下,对金属材料表面进行光亮处理。
光亮处理可以通过化学反应或物理作用改变金属表面的化学成分和结构,从而提高其耐腐蚀性、抗磨损性和美观度。
2.5 冷却光亮处理后,需要对金属材料进行冷却。
冷却过程需要控制好速度和方式,以避免产生内部应力和变形。
2.6 检测与包装最后,对处理后的金属材料进行检测,以确保其质量符合要求。
合格的产品经过包装后即可出厂。
3. 应用领域真空光亮热处理在以下领域有着广泛应用:3.1 航空航天工业航空航天工业对材料的要求非常高,在极端条件下仍需保持良好的性能。
真空光亮热处理可以提高材料的耐腐蚀性、抗疲劳性和抗氧化性,从而增强航空航天材料的可靠性和使用寿命。
3.2 汽车制造业汽车制造业对金属材料的强度、硬度和耐磨性要求较高。
真空光亮热处理可以通过改变金属表面的化学成分和结构,提高材料的硬度和耐磨性,从而增强汽车零部件的使用寿命。
3.3 电子设备工业电子设备对金属材料的导电性、散热性和稳定性有着较高要求。
真空光亮热处理可以优化金属表面的导电特性,并提高散热效率,从而提升电子设备的性能和可靠性。
真空热处理 0.0 mm
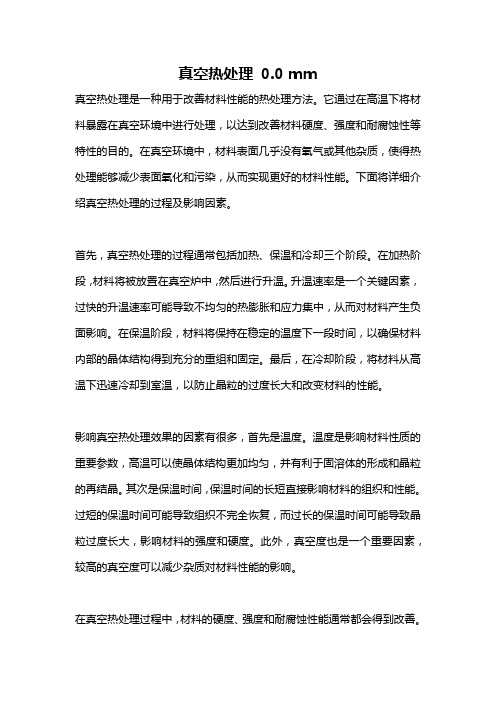
真空热处理0.0 mm真空热处理是一种用于改善材料性能的热处理方法。
它通过在高温下将材料暴露在真空环境中进行处理,以达到改善材料硬度、强度和耐腐蚀性等特性的目的。
在真空环境中,材料表面几乎没有氧气或其他杂质,使得热处理能够减少表面氧化和污染,从而实现更好的材料性能。
下面将详细介绍真空热处理的过程及影响因素。
首先,真空热处理的过程通常包括加热、保温和冷却三个阶段。
在加热阶段,材料将被放置在真空炉中,然后进行升温。
升温速率是一个关键因素,过快的升温速率可能导致不均匀的热膨胀和应力集中,从而对材料产生负面影响。
在保温阶段,材料将保持在稳定的温度下一段时间,以确保材料内部的晶体结构得到充分的重组和固定。
最后,在冷却阶段,将材料从高温下迅速冷却到室温,以防止晶粒的过度长大和改变材料的性能。
影响真空热处理效果的因素有很多,首先是温度。
温度是影响材料性质的重要参数,高温可以使晶体结构更加均匀,并有利于固溶体的形成和晶粒的再结晶。
其次是保温时间,保温时间的长短直接影响材料的组织和性能。
过短的保温时间可能导致组织不完全恢复,而过长的保温时间可能导致晶粒过度长大,影响材料的强度和硬度。
此外,真空度也是一个重要因素,较高的真空度可以减少杂质对材料性能的影响。
在真空热处理过程中,材料的硬度、强度和耐腐蚀性能通常都会得到改善。
通过真空处理,材料表面的氧化物和其他杂质得到去除,从而降低了表面的氧化程度,提高了材料的抗氧化能力。
此外,真空处理还有助于提高材料的致密性和晶粒尺寸的均匀性,从而提高了材料的硬度和强度。
通过控制真空热处理的参数,还可以改变材料的组织结构,使其具有更好的机械性能和耐腐蚀性能。
然而,真空热处理并不适用于所有材料。
某些材料在真空环境下可能会发生特殊的反应,导致材料性能的恶化。
此外,真空热处理的设备成本相对较高,需要较大的投资。
因此,在选择真空热处理方法时需要考虑材料特性、成本和应用要求等因素。
总的来说,真空热处理是一种用于改善材料性能的有效方法。
真空热处理原理与设备应用

真空热处理原理与设备应用简介真空热处理是一种利用真空环境进行热处理的技术,它可以对材料进行去气、除污、退火、固溶、强化等处理,从而改变材料的物理和化学性质。
本文将介绍真空热处理的原理和常见的设备应用。
原理真空热处理是在真空环境下进行热处理的过程。
真空环境的优势在于可以防止材料表面氧化、脱气以及降低大气对材料的侵蚀等不良影响,从而提高热处理的效果和材料的品质。
真空热处理的原理包括以下几个方面:1.去气:真空环境下,材料表面和内部的气体会被抽取出来,从而避免气体对材料的影响。
去气可以通过真空泵等设备实现。
2.除污:真空热处理过程中,材料表面的污秽物质会被气体抽取出来,使得材料表面更加干净。
3.退火:真空热处理过程中,材料会被加热到一定温度,使得材料结构发生改变,从而达到提高材料硬度、塑性和韧性,减少内应力等目的。
4.固溶:真空热处理过程中,可以在材料中加入其他元素,通过加热使其溶解,从而改变材料的组织和性能。
5.强化:真空热处理过程中,可以通过快速冷却或其他方法,使材料的组织更加致密,提高材料的硬度和强度。
设备应用真空热处理设备广泛应用于各个领域,以下是一些常见的设备应用:1.真空退火炉:真空退火炉是真空热处理中最常见的设备之一。
它可以对金属材料进行退火,从而改善材料的硬度、塑性和韧性。
2.真空淬火炉:真空淬火炉可以在高温状态下对材料进行快速冷却,从而使材料的组织更加致密,提高材料的硬度和强度。
3.真空回火炉:真空回火炉可以对材料进行回火处理,从而消除材料内部的应力,提高材料的韧性和尺寸稳定性。
4.真空固溶炉:真空固溶炉用于对材料进行固溶处理,可以通过加热使其他元素溶解在材料中,从而改变材料的组织和性能。
5.真空热处理装置:除了上述常见的热处理设备外,还有一些特殊用途的真空热处理装置,如真空沉积装置、真空淬火回火装置等,它们可以实现更加复杂和精细的热处理工艺。
应用领域真空热处理广泛应用于各个领域,以下是一些应用领域的例子:1.金属加工工业:真空热处理可以改善金属材料的机械性能,提高其耐热、耐腐蚀和耐磨损性,广泛应用于航空、汽车、机械等行业。
济南真空热处理

济南真空热处理一说到济南真空热处理,脑袋里是不是马上浮现出一堆复杂的机器、技术术语,甚至觉得自己好像被搞得一头雾水?别着急,今天咱们就简单聊聊这个热处理的事儿。
说白了,真空热处理就是把一堆金属放进一个“密闭的空间”,通过高温加热,做一些“神奇”的改变,让这些金属更坚硬、更耐用。
是不是听起来就像变魔术一样?这不,济南在这方面可有一手,技术的手艺活儿做得那叫一个地道。
你要是觉得这种技术和老祖宗烧菜的道理差不多,那真是不完全错,简单点说,就是“调味儿”的过程。
啥意思呢?就是通过高温、低氧,配合一系列操作,让这些金属的“脾气”变得更好,硬起来,耐得住磨,扛得住压力。
想象一下,一块金属就像一个年纪轻轻的年轻小伙子,经过“烈火淬炼”后,变得老成稳重,这不就是我们说的“金属的逆袭”吗?说到济南的真空热处理,其实有个特别的地方,那就是这座城市不仅在做金属的“面子工程”,还注重“内涵”。
你看看,真空热处理不仅仅是让金属变得坚硬,这中间的“火候”和“时间”控制可得要拿捏得准。
举个例子,你要是做个菜,火候掌握不好,火大了不熟,火小了糊了,金属也是如此。
如果操作不当,金属的性质可能会变得脆弱,甚至“歪门邪道”,这可不是开玩笑的。
所以,真空热处理的精细度就像你做饭时候的火候,少了点火,可能没味道;多了点火,可能就烧焦了。
济南的技术团队,就是在这种“火候”的掌控上做得特别到位,他们对每一项金属的“性格”了如指掌。
简直是个“化学天才”,一眼就能知道这些金属“想要什么”。
大家可能会想,真空热处理到底能给金属带来什么好处呢?别急,咱慢慢说。
想象一下,如果你手里的金属零件需要在车间里经历高强度的工作,它们的耐磨性、抗压性和抗腐蚀性是不是得好一点?当然了!不然你就得天天给机器“打点滴”,不断更换零件,太麻烦了。
通过真空热处理,金属的表面结构可以变得更加密实,强度增加,耐用性提升,甚至能在高温、重负荷的环境下保持良好的性能。
这就好比你给一辆车加了高性能的发动机,不仅跑得快,质量也高。
真空热处理技术的研究及应用

真空热处理技术的研究及应用随着近年来先进制造技术的不断发展和新材料的出现,热处理技术也在不断推陈出新。
其中,真空热处理技术以其特殊的热处理环境和热处理方式,受到了人们的广泛关注和青睐。
在此背景下,本文将围绕着真空热处理技术进行探讨,深入分析其研究现状和应用前景。
一、真空热处理技术的概念和特点所谓真空热处理技术,就是在真空环境中对物体进行热处理的技术。
与常规的热处理方式不同,真空热处理技术具有以下一些独特的特点和优势:1. 避免氧化和污染真空热处理技术可以避免氧化和污染,减少或避免由于氧化和化学反应带来的质量损失、热处理后的表面质量劣化等问题。
2. 控制热处理温度和压力真空热处理技术可以控制热处理过程中的温度和压力,使热处理过程更加均匀和稳定,提高产品质量和一致性。
3. 适合高温、高压等复杂环境真空热处理技术适用于高温、高压等复杂环境下的材料处理,大大拓展了热处理技术的应用范围。
4. 提高热处理效率真空热处理技术可以提高热处理效率,减少热处理时间,降低生产成本。
二、真空热处理技术的研究现状目前,真空热处理技术已经在制造业、航空航天、光学仪器、医疗器械和电子信息等领域得到广泛应用。
随着现代科技水平的提高,人们在真空热处理技术的研究和应用方面也取得了一些进展和成果。
1. 真空热处理技术的理论研究真空热处理技术的理论研究主要涉及热传输机理、热力学性质和热处理参数等方面。
近年来,随着计算机技术和数值模拟技术的不断提高,真空热处理技术的理论研究也得到了很大的发展。
例如,先进的数值模拟和计算机模拟技术可以很好地研究真空热处理过程中的热量传递和热力学性质,为真空热处理技术的应用提供了理论支撑。
2. 真空热处理技术的应用真空热处理技术的应用除了常规的热处理外,还广泛应用于金属加工、陶瓷、玻璃、光学材料等领域。
例如,硬质合金、高速钢等金属材料的真空热处理可以提高材料的硬度和耐磨性,并且可以保持其微观结构的一致性;陶瓷材料的真空热处理可以去除材料中的气孔和微裂纹,以提高其密度和强度;玻璃材料的真空热处理可以改善其耐热性和耐性等方面的性能,从而扩大其应用范围。
- 1、下载文档前请自行甄别文档内容的完整性,平台不提供额外的编辑、内容补充、找答案等附加服务。
- 2、"仅部分预览"的文档,不可在线预览部分如存在完整性等问题,可反馈申请退款(可完整预览的文档不适用该条件!)。
- 3、如文档侵犯您的权益,请联系客服反馈,我们会尽快为您处理(人工客服工作时间:9:00-18:30)。
真空热处理技术真空热处理真空热处理是真空技术与热处理技术相结合的新型热处理技术,真空热处理所处的真空环境指的是低于一个大气压的气氛环境,包括低真空、中等真空、高真空和超高真空,真空热处理实际也属于气氛控制热处理。
真空热处理是指热处理工艺的全部和部分在真空状态下进行的,真空热处理可以实现几乎所有的常规热处理所能涉及的热处理工艺,但热处理质量大大提高。
与常规热处理相比,真空热处理的同时,可实现无氧化、无脱碳、无渗碳,可去掉工件表面的磷屑,并有脱脂除气等作用,从而达到表面光亮净化的效果。
真空热处理其实还分成以下四个技术要点1.真空高压气冷淬火技术当前真空高压气冷淬火技术发展较快,相继出现了负压(<1×105Pa)高流率气冷、加压(1×105~4×105Pa)气冷、高压(5× 105~10×105Pa)气冷、超高压一(10×105~20×105Pa)气冷等新技术,不但大幅度提高了真空气冷淬火能力,且淬火后工件表面光亮度好,变形小,还有高效、节能、无污染等优点。
真空高压气冷淬火的用途是材料的淬火和回火,不锈钢和特殊合金的固溶、时效,离子渗碳和碳氮共渗,以及真空烧结,钎焊后的冷却和淬火。
用6×105Pa高压氮气冷却淬火时、被冷却的负载只能是松散型的,高速钢(W6Mo5Cr4V2)可淬透至70~100mm,高合金热作模具钢(如 4Cr5MoSiV)可达25~100mm。
用10×105Pa高压氮气冷却淬火时,被冷却负载可以是密集型的,比6×105Pa 冷却时负载密度提高约30%~4O%。
用20×105Pa超高压氮气或氦气和氮气的混合气冷却淬火时,被冷却负载是密集的并可捆绑在一起。
其密度较6×105Pa氮气冷却时提高80%~150%,可冷却所有的高速钢、高合金钢、热作工模具钢及Cr13%的铬钢和较多的合金油淬钢,如较大尺寸的9Mn2V钢。
具有单独冷却室的双室气冷淬火炉的冷却能力优于相同类型的单室炉。
2×105Pa氮气冷却的双室炉的冷却效果和4×105Pa的单室炉相当。
但运行成本、维修成本低。
由于我国基础材料工业(石墨、钼材等)和配套元器件(电动机)等水平有待提高。
所以在提高6×105Pa单室高压真空护质量的同时,发展双室加压和高压气冷淬火炉比较符合我国的国情。
2.真空高压气冷等温淬火形状复杂的较大工件从高温连续进行快速冷却时容易产生变形甚至裂纹。
以往可用盐浴等温淬火解决。
在单室真空高压气冷淬火炉中能否进行气冷等温淬火呢?图1为在带有对流加热功能的单室高压气冷淬火炉中对两组φ320mm×120mm两块叠装的碳素结构钢用不同冷却方式淬火后的对化结果。
图中一组曲线是在102O?加热后,在6×105Pa压力下连续用高纯氮气冷却(风向是上、下相互交替,40s切换一次)的结果。
另一组是对试样表面、心部进行370?时的控制冷却。
从两组曲线的对比可以看出,心部温度通过50O?的时间(半冷时间)只差约2min。
从表面进行控制冷却开始到心部温度到达 370?附近,需27min。
由此可见,在单室真空高压气淬火炉进行等温气冷淬火是可行的。
3.真空渗氮技术真空渗氮是使用真空炉对钢铁零件进行整体加热、充入少量气体,在低压状态下产生活性氮原子渗入并向钢中扩散而实现硬化的;而离子渗氮是靠晖光放电产生的活性N 离子轰击并仅加热钢铁零件表面,发生化学反应生成核化物实现硬化的。
真空渗氛时,将真空炉排气至较高真空度0.133Pa(1×10-3Torr)后,将工件升至,530~560?,同时送入以氨气为主的,含有活性物质的多种复合气体,并对各种气体的送入量进行精确控制,炉压控制在0.667Pa(5Torr),保温3~5h后,用炉内惰性气体进行快速冷却。
不同的材质,经此处理后可得到渗层深为20~80μm、硬度为600~1500HV的硬化层。
真空渗氮有人称为真空排气式氮碳共渗,其特点是通过真空技术,使金属表面活性化和清净化。
在加热、保温、冷却的整个热处理过程中,不纯的微量气体被排出,含活性物质的纯净复合气体被送入,使表面层相结构的调整和控制、质量的改善、效率的提高成为可能。
经X射线衍射分析证实,真空渗氮处理后,渗层中的化合物层是ε单相组织,没有其他脆性相(如Fe3C、Fe3O4)存在,所以硬度高,韧性好,分布也好。
“白层”单相ε化合物层可达到的硬度和材质成分有关。
材质中含Cr量越高,硬度也呈增加趋势。
Cr13%时,硬度可达到1200HV;含Cr18%(质量分数,余同)时,硬度可达 1500HV;含Cr25%时,硬度可达1700HV。
无脆性相的单相ε化合物层的耐磨性比气体氮碳共渗组织的耐磨性高,抗摩擦烧伤、抗热胶合、抗熔敷、抗熔损性能都很优异。
但该“白层”的存在对有些模具和零件也有不利之处,易使锻模在锻造初期引起龟裂,焊接修补时易生成针孔。
真空渗氮还有一个优点,就是通过对送入炉内的含活化物质的复合气体的种类和量的控制,可以得到几乎没有化合物层(白层),而只有扩散层的组织。
其原因可能是在真空炉排气至 0.l33Pa(1×10-3Torr)后形成的,另一个原因是带有活性物质的复合气体在短时间内向钢中扩散形成的组织。
这种组织的优点是耐热冲击性、抗龟裂性能优异。
因而对实施高温回火的热作模具,如用高速钢或4Cr4MoSiV(H13)钢制模具可以得到表面硬度高、耐磨性好、耐热冲击性好、抗龟裂而又有韧性的综合性能;但仅有扩散层组织时,模具的抗咬合性、耐熔敷、熔损性能不够好。
由于模具或机械零件的服役条件和对性能的要求不一,在进行表面热处理时,必需调整表面层的组织和性能。
真空渗氮除应用于工模具外,对提高精密齿轮和要求耐磨耐蚀的机械零件以及弹簧等的性能都有明显效果,可接受处理的材质也比较广泛。
4.真空清洗与干燥技术目前有的热处理还离不开清洗干燥工序,尤其需油冷的各类热处理,清洗干燥的任务更繁重、难度也更大。
国际上使用效果最佳的清洗剂是卤素系清洗剂。
发达国家,如日本使用的卤素系清洗剂的比例如表1所示。
其中三氯乙烷、氟里昂因属破坏大气臭氧层物质,已被禁止使用。
其他卤素系物质也因对生态环境、人、畜有害而被限制使用。
所以各国都在研究各种替代型的清洗干燥技术。
表 1 卤素系剂在热处理生产中使用情况真空水系清洗干燥技术是替代技术中发展的主流,其原理是水蒸气蒸馏和真空蒸馏。
所谓水蒸气蒸馏是指一边向带有不溶于水的油类等物质的工件上吹水蒸气,一边加热,是把油分等挥发成分和水一齐蒸馏出的方法。
应用该法时,油等挥发成分的蒸气随水蒸气同时发生,所以油分的沸点被降低。
这就是用共沸的方法使油分和填加剂形成低沸点物质,使在回火温度以下的较低温度的洗净成为可能。
所谓真空蒸馏是因为,在常压下进行水蒸气蒸馏时,油分的蒸汽压很低,伴随水蒸气而挥发的油分量很少。
如果在真空状态下进行蒸气蒸馏,油分的沸点会被进一步降低。
同时利用水蒸气蒸馏和真空蒸馏,就可将高沸点热处理淬火油在回火温度下被清洗并干燥了。
这种方法适合在大、中型企业和大批量生产的流水线上使用,效率比较高。
缺点是清洗液的回收和处理及循环使用的成本高。
真空油系清洗干燥技术,是指用蒸汽压比较高的轻质溶剂油去溶解和洗净工件上附着的蒸汽压化较低的切削油、冲压油、淬火油;然后再加热减压将溶剂油蒸发分离,从而达到洗净的目的。
选择药溶剂油燃点应尽量高,粘度要低,对被清洗工件上附着的油脂有较强的溶解能力;对工件无腐蚀,且成本较低。
我国国家标准中介绍的190号和20O号溶剂油可作为选择时的参考。
刀具真空热处理技术具有一系列突出的优点:真空热处理具有防氧化的作用。
表面不氧化、不脱碳、并有还原除锈作用,省却刀具的粗加工工序,可节约昂贵的刀具钢材和原辅材料的消耗,节省加工时间,降低产品成本;真空热处理具有真空脱气、脱脂作用并无氢脆危险,防止刀具材料难熔金属的表面脆化,使刀具材料表面纯度提高,提高刀具的疲劳强度、塑性和韧性及耐腐蚀性,提高刀具的使用寿命;真空热处理具有淬火变形小,可减少常规淬火变形的校正应力存在,降低刀片使用过程中断裂的可能性,真空热处理刀片的变形为盐浴淬火的1/2-1/10,淬火后一般不需要校正就可精磨加工至成品;真空热处理工艺的稳定性和重复性好。
一旦工艺确定,只要输入工艺程序,热处理操作将自动运行。
避免常规热处理工艺不稳定造成的刀具质量波动;真空热处理耗电少,电能消耗为常规热处理的80%,生产成本低,但一次性投资成本大;真空热处理操作安全、自动化程度高,工作环境好,无污染无公害,符合我国工业企业清洁生产和持续发展的要求。
深冷技术在刀具产品上的应用是从模具工业应用演变而来。
深冷处理与热处理一样,它与材料特性,处理温度,处理速度有很大关系,不同的处理方法其效果有明显不同。
深冷技术是对材料在低于-130?进行处理的一种工艺方法,深冷处理不仅可以显著提高刀具的力学性能和使用寿命,稳定尺寸,改善均匀性、减少变形,而且操作简便,不破坏工件,无污染,成本低,对刀具质量的提高有很大的帮助。
工件淬火后继续在液氮或液氮蒸气中冷却的工艺。
深冷处理主要是采用液态氟为冷却剂(-196摄氏度),利用气化潜热的快速冷却方式,将淬火后的模具冷至-120摄氏度以下,并保持一段时间。
深冷处理的效果主要有:残余奥氏体几乎可全部转变成马氏体;材料组织细化并可析出微细碳化物;耐磨性比未深冷处理的模具高2--7倍,比普通冷处理的模具高1--8倍。
为了防止深冷处理时产生开裂,深冷处理前须在100摄氏度热水中进行一次回火,并且深冷处理在50——60摄氏度的热水中快速升温,由于表面膨胀而收到减小应力的效果。
深冷处理可提高耐磨性外,还可作为稳定模具尺寸的一种处理方法简单地说吧,这是为了消除淬火件中的残余奥氏体。
工件在淬火的时候,奥氏体转化成马氏体,体积会膨胀,从而产生压力。
压力的存在会阻止剩余的奥氏体向马氏体转化。
因而会有一部分奥氏体不能转变,从而保存下来。
残余奥氏体的存在不仅会降低工件的强度,而且会在以后的使用中,由于受到外来应力,诱发马氏体相变,从而导致工件尺寸变化。
为了消除残余奥氏体,从理论上讲有两种方法,其一是释放应力,其二是降低温度,即所谓的冷处理。
第一种方法实际上不太可能,因此生产上采用的是第二种方法。
冷处理的般是将工件的温度降至温室以下。
深冷处理又称超低温处理,是指在-130?以下对材料进行处理的一种方法,它是常规冷处理的一种延伸。
可以提高多种金属材料的力学性能和使用寿命。
该项技术是20世纪60年代发展的一门新技术,经过近40年的研究和应用,取得了长足的进步,80年代,美国成立了若干个专业化的深冷处理公司和一个国际深冷处理研究会,对深冷处理技术的研究更加深入。