微孔发泡成型技术简介
微孔塑料注射成型技术 1.

一、微孔塑料的定义、特点及成型原理
二、微孔塑料的形态 微孔塑料(MCP):在整个制品厚度中泡孔尺寸均匀分 布或者具有由发泡芯层和坚硬表层组成的夹芯结构材料, 其泡孔有闭孔或开孔两种。
二、微孔塑料的形态 MCP的微观结构随生产工艺方法和条件的不同会有很大 的变化。
通常MCP微观结构受基体材 料均匀性的影响,在多相材料 中,当气体过饱和度较低时, 泡孔优先在相界面上成核,当 气体过饱和度较高时,均相和 异相成核同时发生。 理想的闭孔MCP微观结构可 设计成紧密堆积、蜂窝状、部 分扩散和椭圆形等不同结构。
4)提高了塑件的精度。因塑件的翘曲变形更小,没有明 显的缩痕,制品尺寸稳定性更高。
微孔塑料成型技术
概述
一、微孔塑料的定义、特点及成型原理 微孔塑料的基本观点:让细小的泡孔进入聚合物,从而 减少每个制品的原料用量,并保持其韧性水平,泡孔的尺 寸应比聚合物中已存在的缺陷尺寸小。 微孔塑料:指泡孔均匀且孔径小于100μm(通常泡孔直 径在5~50μm)的发泡材料。 通常传统泡沫塑料的泡孔直径在250μm~1mm之间。
三、微孔塑料注射成型装置 气体泵送系统:因使用氮气 作发泡剂,且很容易与辅助计 量装置一起使用,是目前应用 最广泛的系统。 超临界流体泵为两级泵,一 级泵将气体压力从1.4MPa增压 到14MPa,二级泵再将气体压 力增大到最大压力52MPa左右。 该系统需对超临界流体进行 质量计量和控制,以定量、定 压的注入注射机塑化装置。
二、微孔塑料的形态 若塑料原料不均匀,泡孔尺寸就会不均匀,微观结构将 会受到第二相的尺寸、分布、取向和界面能的影响。 不相容聚合物的共混物,沿界面边界可能形成泡孔,当 界面边界为直线时,则可能形成开孔结构。 当原料有两种不相同材料在分子级水平混合时,成核密 度可能非常大,在一定的发泡密度下,平均泡孔体积与泡 孔密度成反比。
微发泡注塑成型
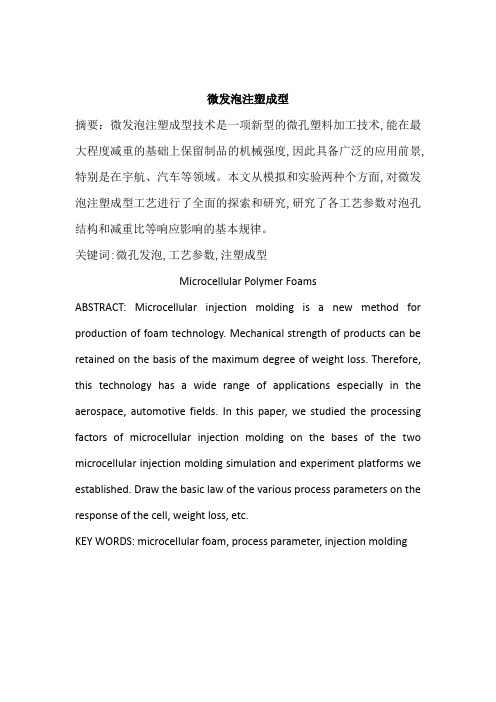
微发泡注塑成型摘要:微发泡注塑成型技术是一项新型的微孔塑料加工技术,能在最大程度减重的基础上保留制品的机械强度,因此具备广泛的应用前景,特别是在宇航、汽车等领域。
本文从模拟和实验两种个方面,对微发泡注塑成型工艺进行了全面的探索和研究,研究了各工艺参数对泡孔结构和减重比等响应影响的基本规律。
关键词:微孔发泡,工艺参数,注塑成型Microcellular Polymer FoamsABSTRACT: Microcellular injection molding is a new method for production of foam technology. Mechanical strength of products can be retained on the basis of the maximum degree of weight loss. Therefore, this technology has a wide range of applications especially in the aerospace, automotive fields. In this paper, we studied the processing factors of microcellular injection molding on the bases of the two microcellular injection molding simulation and experiment platforms we established. Draw the basic law of the various process parameters on the response of the cell, weight loss, etc.KEY WORDS: microcellular foam, process parameter, injection molding1前言微孔发泡技术起源于20世纪80年代美国麻省理工大学,是一项新型的微孔塑料加工技术,其生产制品的最大特点就是泡孔小而密。
高质量低成本的MuCell微发泡注塑成形技术.总结
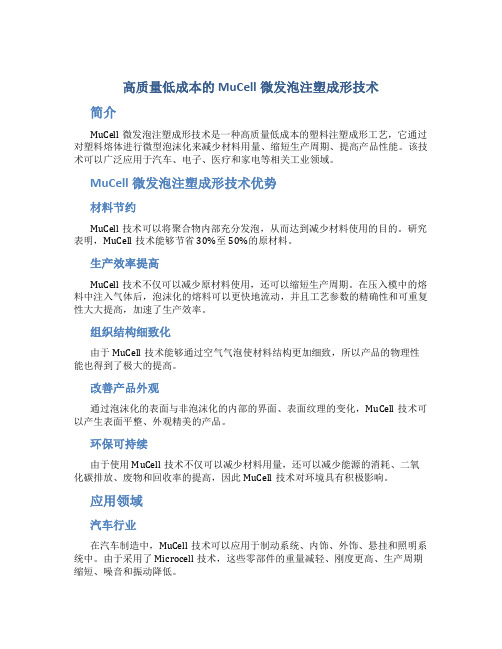
高质量低成本的MuCell微发泡注塑成形技术简介MuCell微发泡注塑成形技术是一种高质量低成本的塑料注塑成形工艺,它通过对塑料熔体进行微型泡沫化来减少材料用量、缩短生产周期、提高产品性能。
该技术可以广泛应用于汽车、电子、医疗和家电等相关工业领域。
MuCell微发泡注塑成形技术优势材料节约MuCell技术可以将聚合物内部充分发泡,从而达到减少材料使用的目的。
研究表明,MuCell技术能够节省30%至50%的原材料。
生产效率提高MuCell技术不仅可以减少原材料使用,还可以缩短生产周期。
在压入模中的熔料中注入气体后,泡沫化的熔料可以更快地流动,并且工艺参数的精确性和可重复性大大提高,加速了生产效率。
组织结构细致化由于MuCell技术能够通过空气气泡使材料结构更加细致,所以产品的物理性能也得到了极大的提高。
改善产品外观通过泡沫化的表面与非泡沫化的内部的界面、表面纹理的变化,MuCell技术可以产生表面平整、外观精美的产品。
环保可持续由于使用MuCell技术不仅可以减少材料用量,还可以减少能源的消耗、二氧化碳排放、废物和回收率的提高,因此MuCell技术对环境具有积极影响。
应用领域汽车行业在汽车制造中,MuCell技术可以应用于制动系统、内饰、外饰、悬挂和照明系统中。
由于采用了Microcell技术,这些零部件的重量减轻、刚度更高、生产周期缩短、噪音和振动降低。
电子和家电行业在电子和家电制造业中,Microcell技术可以用于生产更轻、更细节、更高性能的产品。
例如,通过Microcell技术,可以生产更轻、更细节化的电脑外壳,增加了生产效率和热释放效率。
医疗行业在医疗行业,Microcell技术的应用轻质化各种手术器械、生产更浅薄、更精细的医疗器械等都可以得到很好的应用。
MuCell微发泡注塑成形技术发展趋势目前,该技术的研究和应用一直在不断发展。
在未来,随着人们对环境保护和材料利用率的更高要求,该技术必将得到更广泛和深入的应用。
微孔注塑成型技术

微孔注塑成型技术1.定义:利用注塑成型生产有气孔注塑件的成型工艺;它分为化学发泡和物理发泡注塑。
化学发泡注塑是将化学发泡剂加入到塑料粒子中;物理发泡注塑是将液氮、液态二氧化碳溶入熔融塑料中。
2.常用化学发泡剂:AC,短时间能分解完毕,分解放热,放出氮气,发气量190~260ML/G,使熔体粘度波动,为了适用多种注塑塑料一般需要添加:热稳定剂、发泡促进剂、发泡调节剂。
3.物理发泡注塑:将溶有氮气或二氧化碳的均相塑料熔体通过专门的注塑装置注射入模具中。
4.如何得到溶有氮气或二氧化碳的均相塑料熔体?是将超临界状态的氮气或二氧化碳注入塑料熔体中;超临界流体(SCF)—就是温度和压力都在临界温度和临界压力之上的流体。
5.物理发泡注塑与普通注塑设备方面的不同点:截流式喷嘴、专门的螺杆/料筒、专门的微孔成型控制系统、SCF输送系统。
6.为什么溶有氮气或二氧化碳的熔体注塑后能得到有微孔结构的产品?注塑机料筒内聚合物熔体压力很高,进入模腔时压力突然降低很多,这时发生热力学不稳定变化,溶入塑料熔体的氮气或二氧化碳开始和塑料分离产生气核,一旦成核作用完成,泡孔就开始长大。
当熔体已建立起足够的刚性承受泡孔中的气体压力,泡孔不再持续长大。
于是在注塑件中形成微孔结构。
7.理论计算公式:SCF用量=SCF流率*阀门打开时间*27.8/总注射量。
SCF流率单位是KG/H;阀门打开时间单位是S;总注射量是G.1)内泡:将气泡切开如果气泡中表面光滑、壁厚,就是内泡。
原因是SCF 没有溶于单相熔体而被注入注塑件;另一个原因是SCF用量低,泡孔大。
针对前一个原因需要降低SCF用量、提高背压MPP、提高熔体温度。
2)表面气泡:原因是物料通过浇口时剪切过高,需要降低注射速度。
3)爆裂:爆裂从外表看与内泡一样,但是延长冷却时间,爆裂会减少,而内泡则不会发生什么变化。
产生爆裂是注塑件局部物料不够硬,不能承受泡孔内残存的气体压力。
发泡成型工艺—泡沫塑料成型原理(塑料成型加工课件)

二、泡沫塑料
按泡孔类型
开孔泡沫塑料:泡孔相互连通
闭孔泡沫塑料:泡孔互相分隔 软质泡沫塑料
按软硬程度 硬质泡沫塑料
半硬质泡沫塑料
按发泡程度 高发泡
中发泡
低泡沫塑料与纯塑料相比:质轻、比强度高、吸湿性 低、回弹性好,隔音吸音性能,热导率低,隔热性能好, 优良的电绝缘性能。
三、发泡成型原理
气发性发泡成型原理:将气体溶解在液态聚合物中 或将聚合物加热到熔融态同时产生气体并形成饱和溶液; 当体系中的液体超过其溶解度时,气体就逸出形成无数 微小气泡,泡核增长而形成气泡。气泡稳定后保留在塑 料,形成泡沫塑料。
气泡的形成
气泡的膨胀
气泡的稳定
1.气泡的形成
均匀混合在树脂的发泡剂在受热作用达到一定温度 后产生气体,并且也均匀分散在基体树脂中。气泡的形 成阶段对泡体中泡孔的密度和分布情况起着决定性的作 用,是控制泡沫塑料性能和质量的关键。
若熔体形成大量均匀分布的气泡,将有利于得到泡 空细密而均匀的泡沫材料;若熔体形成少量而不均匀的 气泡,得到的泡沫材料性能也较差。
2.气泡的膨胀
气泡的膨胀阶段紧接在气泡的形成阶段之后。在 该阶段气相已经形成,膨胀的动力来自气泡内压,膨 胀的阻力是聚合物熔体或液体的黏弹性和外压,黏弹 性太大或太小都不利于气泡的膨胀,黏弹性太大会使 气泡膨胀阻力过大,太小又会使气泡膜没有足够的强 度保不住气体。
要控制气泡的膨胀过程,必须了解影响气泡膨胀 动力和阻力的各种因素及它们之间额关系。
3.气泡的稳定
气泡不断生产和膨胀之后,需要形成均匀稳定的 泡空,一般采用两种方法: (1)加压
在熔体中施加压力,使熔体内气派不逸出,固定 在熔体内形成气孔。 (2)交联
加入交联剂,使熔体形成交联网络结构,提高熔 体黏弹性,使气泡稳定。
微孔发泡技术

冰箱发泡技术2007-11-15 16:22发泡塑料是以热塑性或热固性树脂为基体,其内部具有无数微小气孔的塑料。
发泡是塑料加工的重要方法之一,塑料发泡得到的泡沫塑料含有气固两项 - 气体和固体。
气体以泡孔的形式存在于泡沫体中,泡孔与泡孔互相隔绝的称为闭孔,连通的称为开孔,从而有闭孔泡沫塑料和开孔泡沫塑料之分。
泡沫结构的开孔或闭孔是由原材料性能及其加工工艺所决定的。
塑料发泡的技术渊源久远。
最早是20年代初期的泡沫胶木,用类似制造泡沫橡胶的方法制取;30年代出现硬质聚氨酯泡沫和聚苯乙烯泡沫;40年代有聚乙烯、聚氯乙烯、环氧树脂、酚醛泡沫;50年代则有可发性聚苯乙烯泡沫和软质聚氨酯泡沫。
现在,基本上所有的塑料,包括热塑性和热固性的都可以发泡为泡沫塑料。
工业上的制备方法有:挤出发泡、注塑发泡、模塑发泡、压延发泡、粉末发泡和喷涂发泡等等。
其中,注塑发泡是最重要的成型方法之一,在这里重点讲述注塑成型发泡。
发泡成型原理塑料的发泡方法根据所用发泡剂的不同可以分为物理发泡法和化学发泡法两大类。
在这里首先简单介绍一下发泡剂。
◆ 发泡剂发泡剂可简单粗分为物理发泡剂与化学发泡剂两类。
对物理发泡剂的要求是:无毒、无臭、无腐蚀作用、不燃烧、热稳定性好、气态下不发生化学反应、气态时在塑料熔体中的扩散速度低于在空气中的扩散速度。
常用的物理发泡剂有空气、氮气、二氧化碳、碳氢化合物、氟利昂等;化学发泡剂是一种受热能释放出气体诸如氮气、二氧化碳等的物质,对化学发泡剂的要求是:其分解释放出的气体应为无毒、无腐蚀性、不燃烧、对制品的成型及物理、化学性能无影响,释放气体的速度应能控制,发泡剂在塑料中应具有良好的分散性。
应用比较广泛的有无机发泡剂如碳酸氢钠和碳酸铵,有机发泡剂如偶氮甲酰胺和偶氮二异丁腈。
◆ 物理发泡法简单地讲,就是利用物理的方法来使塑料发泡,一般有三种方法:(1)先将惰性气体在压力下溶于塑料熔体或糊状物中,再经过减压释放出气体,从而在塑料中形成气孔而发泡;(2)通过对溶入聚合物熔体中的低沸点液体进行蒸发使之汽化而发泡;(3)在塑料中添加空心球而形成发泡体而发泡等。
微发泡注塑成型

微发泡注塑成型工艺目录编辑本段简介微发泡注塑成型工艺,是一种革新的精密注塑技术,微发泡注塑成型工艺突破了传统注塑的诸多局限,可显著减轻制件的重量、缩短成型周期,并极大地改善了制件的翘曲变形和尺寸稳定性。
在生产高质量要求的精密制品上,微发泡注塑成型工艺具有很大的优势。
在注塑成型领域中,Trexel公司的MuCell微发泡成型工艺表现得尤为突出,也是精密成型技术中发展最快、应用最广泛的成型技术之一。
[1]编辑本段技术需求原材料价格不断飙升,对制造相对低廉的亚洲市场带来了巨大的冲击,很多加工商已经开始意识到,即使在中国也不再是廉价制品的产地。
但是另一方面,为了占据有利市场先机,越南、印尼和其他一些国家的供应商却又不得不通过削减价格的方式适应消费者的需求。
然而,随着产品越来越复杂,制件的公差要求和表面外观质量要求也越来越高,采用传统的注塑加工技术生产这些制件,往往会出现多种质量问题,如制品存在较大的内应力、由于收缩不均而导致产品变形等,达不到要求的品质或成本要求。
可以说,塑料加工商遇到了前所未有的挑战,他们迫切需要寻求新的加工技术来改变现在的困境。
精密注塑成型技术越来越受到人们的关注。
微发泡注塑成型工艺,这种技术可以将制件的生产尺寸精度控制在0.01~0.001mm之间,有时甚至能够达到0.001mm以下。
与传统的注塑工艺相比,由该技术生产的制件具有良好的力学性能以及尺寸稳定性,而且制件的尺寸精度和重复精度高,公差范围小。
由于其自身的多种性能优势,加上塑料加工领域的“突变”,为该技术提供了广阔的发展空间。
在对制品规格要求很高的医疗和电子电器领域,精密注塑成型已经发展成为一种非常成熟和完善的注塑工艺。
随着汽车市场的异军突起,司机们在寻找油耗更小的汽车的同时,也更需要配置高精度的汽车配件和修饰件,而这些精密部件的生产同样离不开精密注塑成型工艺。
[2]编辑本段原理图1 MuCell微发泡注塑成型的工艺过程[3]MuCell微发泡成型工艺主要靠气孔的膨胀来填充制品,并在较低且平均的压力下完成制件的成型。
Mucell微孔发泡成型技术简介
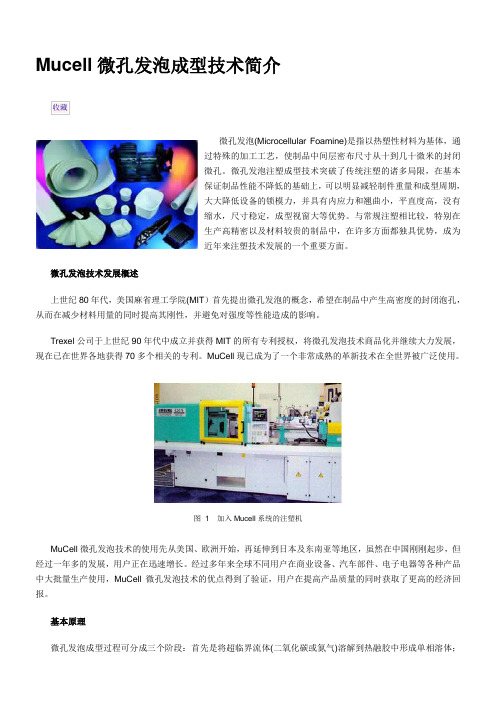
Mucell 微孔发泡成型技术简介微孔发泡(Microcellular Foamine)是指以热塑性材料为基体,通过特殊的加工工艺,使制品中间层密布尺寸从十到几十微米的封闭微孔。
微孔发泡注塑成型技术突破了传统注塑的诸多局限,在基本保证制品性能不降低的基础上,可以明显减轻制件重量和成型周期,大大降低设备的锁模力,并具有内应力和翘曲小,平直度高,没有缩水,尺寸稳定,成型视窗大等优势。
与常规注塑相比较,特别在生产高精密以及材料较贵的制品中,在许多方面都独具优势,成为近年来注塑技术发展的一个重要方面。
微孔发泡技术发展概述上世纪80年代,美国麻省理工学院(MIT )首先提出微孔发泡的概念,希望在制品中产生高密度的封闭泡孔,从而在减少材料用量的同时提高其刚性,并避免对强度等性能造成的影响。
Trexel 公司于上世纪90年代中成立并获得MIT 的所有专利授权,将微孔发泡技术商品化并继续大力发展,现在已在世界各地获得70多个相关的专利。
MuCell 现已成为了一个非常成熟的革新技术在全世界被广泛使用。
图 1 加入Mucell 系统的注塑机MuCell 微孔发泡技术的使用先从美国、欧洲开始,再延伸到日本及东南亚等地区,虽然在中国刚刚起步,但经过一年多的发展,用户正在迅速增长。
经过多年来全球不同用户在商业设备、汽车部件、电子电器等各种产品中大批量生产使用,MuCell 微孔发泡技术的优点得到了验证,用户在提高产品质量的同时获取了更高的经济回报。
基本原理微孔发泡成型过程可分成三个阶段:首先是将超临界流体(二氧化碳或氮气)溶解到热融胶中形成单相溶体;然后通过开关式射嘴射人温度和压力较低的模具型腔,由于温度和压力降低引发分子的不稳定性从而在制品中形成大量的气泡核,这些气泡核逐渐长大生成微小的孔洞。
图 2 微泡成型过程发泡后的制品横切面放大图如下,我们从中可以明显看到表层还是未发泡的实体层,这是由于模具温度较低,表面树脂冷却迅速,细胞核没有成长的时间,所以还是未发泡的实体。
微孔发泡注塑成型技术概述李兵
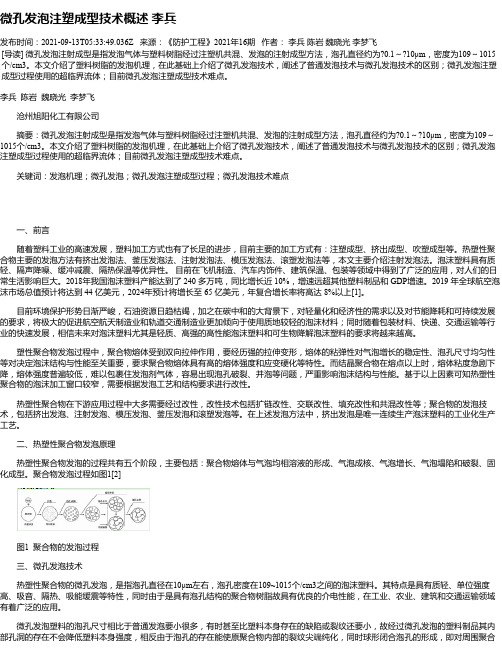
微孔发泡注塑成型技术概述李兵发布时间:2021-09-13T05:33:49.036Z 来源:《防护工程》2021年16期作者:李兵陈岩魏晓光李梦飞[导读] 微孔发泡注射成型是指发泡气体与塑料树脂经过注塑机共混、发泡的注射成型方法,泡孔直径约为?0.1~?10μm,密度为109~1015个/cm3。
本文介绍了塑料树脂的发泡机理,在此基础上介绍了微孔发泡技术,阐述了普通发泡技术与微孔发泡技术的区别;微孔发泡注塑成型过程使用的超临界流体;目前微孔发泡注塑成型技术难点。
李兵陈岩魏晓光李梦飞沧州旭阳化工有限公司摘要:微孔发泡注射成型是指发泡气体与塑料树脂经过注塑机共混、发泡的注射成型方法,泡孔直径约为?0.1~?10μm,密度为109~1015个/cm3。
本文介绍了塑料树脂的发泡机理,在此基础上介绍了微孔发泡技术,阐述了普通发泡技术与微孔发泡技术的区别;微孔发泡注塑成型过程使用的超临界流体;目前微孔发泡注塑成型技术难点。
关键词:发泡机理;微孔发泡;微孔发泡注塑成型过程;微孔发泡技术难点一、前言随着塑料工业的高速发展,塑料加工方式也有了长足的进步,目前主要的加工方式有:注塑成型、挤出成型、吹塑成型等。
热塑性聚合物主要的发泡方法有挤出发泡法、釜压发泡法、注射发泡法、模压发泡法、滚塑发泡法等,本文主要介绍注射发泡法。
泡沫塑料具有质轻、隔声降噪、缓冲减震、隔热保温等优异性。
目前在飞机制造、汽车内饰件、建筑保温、包装等领域中得到了广泛的应用,对人们的日常生活影响巨大。
2018年我国泡沫塑料产能达到了 240 多万吨,同比增长近 10%,增速远超其他塑料制品和 GDP增速。
2019 年全球航空泡沫市场总值预计将达到 44 亿美元,2024年预计将增长至 65 亿美元,年复合增长率将高达 8%以上[1]。
目前环境保护形势日渐严峻,石油资源日趋枯竭,加之在碳中和的大背景下,对轻量化和经济性的需求以及对节能降耗和可持续发展的要求,将极大的促进航空航天制造业和轨道交通制造业更加倾向于使用质地较轻的泡沫材料;同时随着包装材料、快递、交通运输等行业的快速发展,相信未来对泡沫塑料尤其是轻质、高强的高性能泡沫塑料和可生物降解泡沫塑料的要求将越来越高。
微发泡注塑PP及其工艺影响因素

微发泡注塑PP及其工艺影响因素微孔发泡PP是指泡孔分布均匀、泡孔平均直径在1~100m,泡孔密度大约为106~1011个/cm3,材料的密度相比于未发泡削减8~15%的发泡材料,由于微孔发泡PP中的微孔更改了原始聚合物材料中应力的分布以及应力在材料中的传递方式,使得微发泡聚合物表现出有别于其他连续材料的力学特性。
比如具有质轻、比强度高、隔音、冲击强度更高等优点,并且其抗疲乏寿命甚至可以数十倍地提高,同时其绝缘、保温性能等也会大幅度地加添。
因此,微发泡PP特别适用于对材料轻量化要求较高的领域,如汽车、轨道交通,船舶,风机叶片等。
目前,微发泡PP重要有以下几种成型方法:①间歇成型法②连续挤出成型法③注塑成型法。
但是,间歇成型法,生产周期长,不适合应用于大规模工业化;连续挤出成型法虽然可以缩短生产周期,但是连续挤出成型法仅能制造结构简单的制品,限制了其应用范围。
而注塑成型法具有生产周期短,又能制造多而杂结构原件,可在传统注塑机的基础上进行改进,因此是目前工业上重要采纳的方法。
1.微发泡注塑成型技术的工艺与原理注塑成型技术的原理是利用快速更改温度来使聚合物/气体均相体系进行微孔发泡,下图为典型的微孔塑料注塑成型技术的系统结构示意图。
其工艺过程为:聚合物粒料通过料斗加入机筒,通过螺杆的机械摩擦和升温加热器使粒料熔为聚合物熔体,N2或CO2等小分子气体通过计量阀的掌控以肯定的速率注入机筒内的聚合物熔体中(或通过在聚合物中添加化学发泡剂分解产生气体),与聚合物熔体混合均匀,形成聚合物/气体均相体系。
随后,聚合物/气体均相体系由静态混合器进入扩散室,通过分子扩散使体系进一步均化,在这里通过快速升温加热器(例如,在1s内使熔体温度由190℃上升至240℃)使气体在聚合物熔体中的溶解度急剧下降,过饱和气体由熔体中析出形成大量的微小气泡核。
为了抑制扩散室内已形成的气泡核快速生长,扩散室内必需保持高压状态。
在进行注射操作前,模具型腔中充分压缩气体。
微发泡注塑成型技术
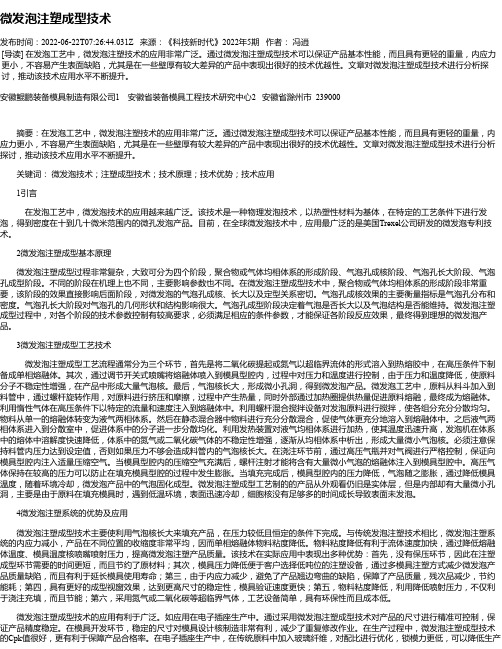
微发泡注塑成型技术发布时间:2022-06-22T07:26:44.031Z 来源:《科技新时代》2022年5期作者:冯逍[导读] 在发泡工艺中,微发泡注塑技术的应用非常广泛。
通过微发泡注塑成型技术可以保证产品基本性能,而且具有更轻的重量,内应力更小,不容易产生表面缺陷,尤其是在一些壁厚有较大差异的产品中表现出很好的技术优越性。
文章对微发泡注塑成型技术进行分析探讨,推动该技术应用水平不断提升。
安徽鲲鹏装备模具制造有限公司1 安徽省装备模具工程技术研究中心2 安徽省滁州市 239000摘要:在发泡工艺中,微发泡注塑技术的应用非常广泛。
通过微发泡注塑成型技术可以保证产品基本性能,而且具有更轻的重量,内应力更小,不容易产生表面缺陷,尤其是在一些壁厚有较大差异的产品中表现出很好的技术优越性。
文章对微发泡注塑成型技术进行分析探讨,推动该技术应用水平不断提升。
关键词:微发泡技术;注塑成型技术;技术原理;技术优势;技术应用1引言在发泡工艺中,微发泡技术的应用越来越广泛。
该技术是一种物理发泡技术,以热塑性材料为基体,在特定的工艺条件下进行发泡,得到密度在十到几十微米范围内的微孔发泡产品。
目前,在全球微发泡技术中,应用最广泛的是美国Trexel公司研发的微发泡专利技术。
2微发泡注塑成型基本原理微发泡注塑成型过程非常复杂,大致可分为四个阶段,聚合物或气体均相体系的形成阶段、气泡孔成核阶段、气泡孔长大阶段、气泡孔成型阶段。
不同的阶段在机理上也不同,主要影响参数也不同。
在微发泡注塑成型技术中,聚合物或气体均相体系的形成阶段非常重要,该阶段的效果直接影响后面阶段,对微发泡的气泡孔成核、长大以及定型关系密切。
气泡孔成核效果的主要衡量指标是气泡孔分布和密度。
气泡孔长大阶段对气泡孔的几何形状和结构影响很大。
气泡孔成型阶段决定着气泡是否长大以及气泡结构是否能维持。
微发泡注塑成型过程中,对各个阶段的技术参数控制有较高要求,必须满足相应的条件参数,才能保证各阶段反应效果,最终得到理想的微发泡产品。
微发泡注塑成型工艺
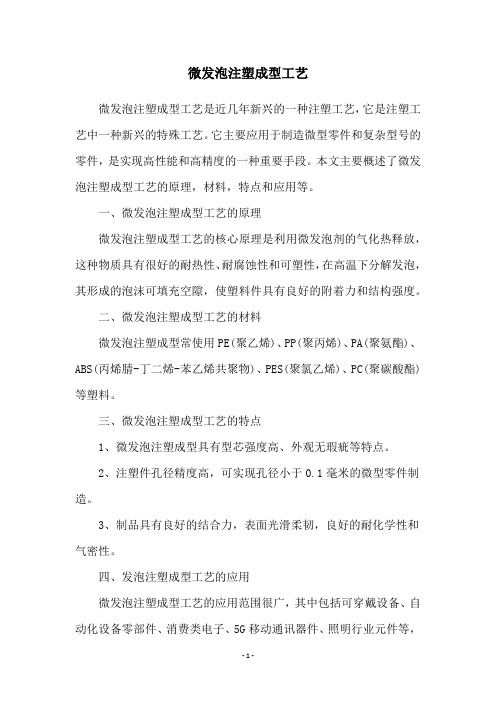
微发泡注塑成型工艺
微发泡注塑成型工艺是近几年新兴的一种注塑工艺,它是注塑工艺中一种新兴的特殊工艺。
它主要应用于制造微型零件和复杂型号的零件,是实现高性能和高精度的一种重要手段。
本文主要概述了微发泡注塑成型工艺的原理,材料,特点和应用等。
一、微发泡注塑成型工艺的原理
微发泡注塑成型工艺的核心原理是利用微发泡剂的气化热释放,这种物质具有很好的耐热性、耐腐蚀性和可塑性,在高温下分解发泡,其形成的泡沫可填充空隙,使塑料件具有良好的附着力和结构强度。
二、微发泡注塑成型工艺的材料
微发泡注塑成型常使用PE(聚乙烯)、PP(聚丙烯)、PA(聚氨酯)、ABS(丙烯腈-丁二烯-苯乙烯共聚物)、PES(聚氯乙烯)、PC(聚碳酸酯)等塑料。
三、微发泡注塑成型工艺的特点
1、微发泡注塑成型具有型芯强度高、外观无瑕疵等特点。
2、注塑件孔径精度高,可实现孔径小于0.1毫米的微型零件制造。
3、制品具有良好的结合力,表面光滑柔韧,良好的耐化学性和气密性。
四、发泡注塑成型工艺的应用
微发泡注塑成型工艺的应用范围很广,其中包括可穿戴设备、自动化设备零部件、消费类电子、5G移动通讯器件、照明行业元件等,
目前正迅速地发展着,这些都对微发泡注塑成型工艺的发展提出了更高的要求,同时也促进了该工艺的更新换代。
总之,微发泡注塑成型工艺具有速度快、工艺复杂程度低、能够制造微型零件等诸多优势,在各种行业,如建筑、机械、航空航天等领域得到了广泛应用。
未来,随着科技的不断发展,微发泡注塑成型工艺还将发挥更大的作用,使生产更高效,建立更完善的工艺系统,更好地满足我们日常生活的需求。
微孔发泡成型技术

微孔发泡成型技术
微孔发泡成型技术是一种新型的发泡成型技术,在材料科学和工程领域得到广泛应用。
该技术利用发泡剂在高温高压条件下在材料中形成微小孔洞,从而改善材料的物理和化学性质。
它与传统发泡技术相比,具有更高的发泡效率、更小的孔径和更均匀的孔洞分布等优点。
微孔发泡成型技术适用于各种材料,如塑料、橡胶、金属、纤维等,可以制造出具有优异性能的高品质产品,如隔热材料、吸音材料、过滤器材料等。
该技术在环保、能源、汽车、建筑等领域具有广阔的应用前景。
- 1 -。
微孔发泡材料体系及挤出发泡(华南理工大学彭响方)20161112

微孔发泡塑料的制备技术
制备技术
相分离法
单体聚合法
超临界流 体法
超饱和气 体法
间歇发泡
挤出发泡
注塑发泡
何为超临界流体?
超临界流体(supercritical fluid)是指温 度及压力均处于临界点以上的液体, 具有许多独特的性质,如粘度小、密 度、扩散系数、溶剂化能力等性质。
间歇发泡成型 快速升温法:
微孔塑料泡孔结构影响因素
影响泡孔结构的因素主要分为两类:一类是聚合物材料本身的物性参数; 另一类影响泡孔结构的是发泡工艺参数
聚合物的粘度或熔体强度 材料物性
松弛时间 CO2在聚合物中的溶解度及扩散速率
相界面的表面张力等
影响因素
发泡温度和压力 发泡时间, 工艺参数 饱和时间 剪切速率 降压速率等
发泡温度因素
图1-7 PLA2003D在饱和压力16 MPa和不同发泡温度条件下发泡样品的SEM图及泡孔 尺寸分布图:(a) 80 ℃;(b) 90 ℃;(c) 100 ℃;(d) 110 ℃;(e) 120 ℃ 随着温度的升高气体在聚合物中的溶解度降低,成核数量会相对减少,体系 的粘度或熔体强度降低,气泡成核后长大的阻力降低,泡孔尺寸较大。如果 进一步提高温度,熔体强度将继续降低,会加剧泡孔塌陷或合并现象 发泡温度太低,体系的粘度增大,气体在聚合物中的扩散速率降低,聚合物 的熔体强度增加,气泡长大过程受到限制,气泡难以长大,如果温度降低到 聚合物的玻璃化温度以下,聚合物因粘度太大而不能发泡
微发泡聚合物注塑件成型技术
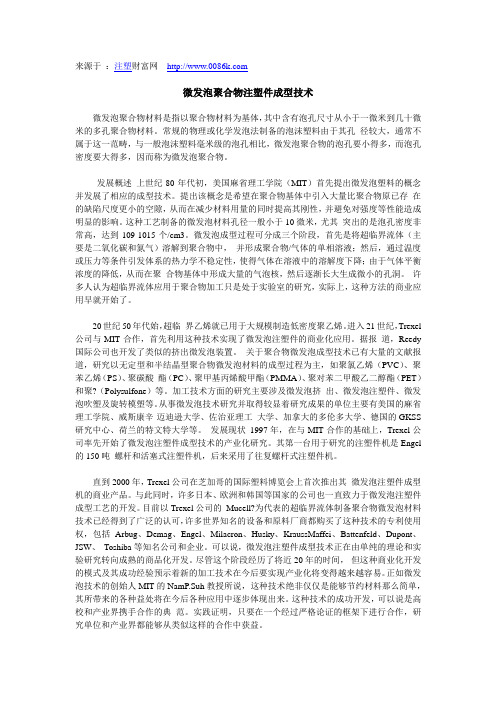
来源于:注塑财富网微发泡聚合物注塑件成型技术微发泡聚合物材料是指以聚合物材料为基体,其中含有泡孔尺寸从小于一微米到几十微米的多孔聚合物材料。
常规的物理或化学发泡法制备的泡沫塑料由于其孔径较大,通常不属于这一范畴,与一般泡沫塑料毫米级的泡孔相比,微发泡聚合物的泡孔要小得多,而泡孔密度要大得多,因而称为微发泡聚合物。
发展概述上世纪80年代初,美国麻省理工学院(MIT)首先提出微发泡塑料的概念并发展了相应的成型技术。
提出该概念是希望在聚合物基体中引入大量比聚合物原已存在的缺陷尺度更小的空隙,从而在减少材料用量的同时提高其刚性,并避免对强度等性能造成明显的影响。
这种工艺制备的微发泡材料孔径一般小于10微米,尤其突出的是泡孔密度非常高,达到109-1015个/cm3。
微发泡成型过程可分成三个阶段,首先是将超临界流体(主要是二氧化碳和氮气)溶解到聚合物中,并形成聚合物/气体的单相溶液;然后,通过温度或压力等条件引发体系的热力学不稳定性,使得气体在溶液中的溶解度下降;由于气体平衡浓度的降低,从而在聚合物基体中形成大量的气泡核,然后逐渐长大生成微小的孔洞。
许多人认为超临界流体应用于聚合物加工只是处于实验室的研究,实际上,这种方法的商业应用早就开始了。
20世纪50年代始,超临界乙烯就已用于大规模制造低密度聚乙烯。
进入21世纪,Trexel 公司与MIT合作,首先利用这种技术实现了微发泡注塑件的商业化应用。
据报道,Reedy 国际公司也开发了类似的挤出微发泡装置。
关于聚合物微发泡成型技术已有大量的文献报道,研究以无定型和半结晶型聚合物微发泡材料的成型过程为主,如聚氯乙烯(PVC)、聚苯乙烯(PS)、聚碳酸酯(PC)、聚甲基丙烯酸甲酯(PMMA)、聚对苯二甲酸乙二醇酯(PET)和聚?(Polysulfone)等。
加工技术方面的研究主要涉及微发泡挤出、微发泡注塑件、微发泡吹塑及旋转模塑等。
从事微发泡技术研究并取得较显着研究成果的单位主要有美国的麻省理工学院、威斯康辛-迈迪逊大学、佐治亚理工大学、加拿大的多伦多大学、德国的GKSS 研究中心、荷兰的特文特大学等。
浅析微孔发泡成型技术

浅析微孔发泡成型技术塑料加工使用发泡技术可以减轻制品重量,所以目前微孔发泡成型技术已经渐渐的被广泛运用,下面我们一起来浅析微孔发泡成型技术。
一、微孔发泡成型属于物理发泡法。
常规泡沫塑料的泡孔直径一般大于50mm,泡孔的密度(单位体积内泡孔的数量)小于106个/cm3。
这些大尺寸的泡孔受力时常常成为初始裂纹的发源地,降低了材料的机械性能。
为了充足工业上要求降低某些塑料产品的成本而不降低其机械性能的要求,20世纪80时代初期,美国麻省理工大学(MIT)的学者J.E.MartiniJ.Colton以及N.P.Suh等以CO2、N2等惰性气体作为发泡剂研制出泡孔直径为微米级的泡沫塑料,并将泡孔直径为1mm~10mm,泡孔密度为109~1012个/cm3的泡沫塑料定义为微孔塑料(MicrocelluarPlastics)。
二、注射成型是微孔塑料制品的重要成型方法之一。
塑料原材料加入注塑机的料筒后,在螺杆剪切力及加热圈外加热作用下塑化,发泡剂直接注入注射螺杆熔融段末与熔体均匀混合,然后高压高速注入模腔。
在模腔内蓦地降压,使熔体中大量的过饱和气体离析出来,发泡、膨胀、成型、定型形成微孔塑料制品。
另外,也可以采纳更改温度的方法形成泡核,与更改压力法相比,比较简单掌控,但对于气体溶解度对温度不敏感的塑料不适用。
开发微孔塑料注塑技术难度比较大,由于和常规泡沫塑料相比,泡孔的尺寸要小得多,要想得到良好的微孔塑料制品,必需要保证对进入机筒熔体中的超临界流体计量,要求塑料熔体必需充分混合、均化、分散,形成均相混合体,保证熔体中的成核点必需多于109个/cm3、适时掌控成核气泡的膨胀等等。
这对设备本身及注塑工艺参数的要求都特别之高。
采纳该技术的特点是:1、制品重量约削减50%;2、注射压力约降低30~50%;3、锁模力降低20%;4、循环周期削减10~15%;5、采纳一套带计量掌控装置的气体输入设备。
据报道,国外一些注塑机生产商已成功开发出微孔塑料注塑机,比如美国Trexel公司、德国Arburg公司、奥地利Engel公司等。
微孔发泡技术
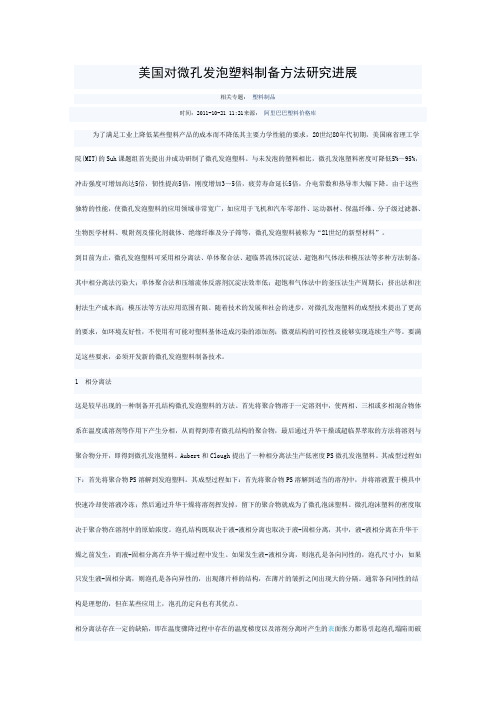
美国对微孔发泡塑料制备方法研究进展相关专题:塑料制品时间:2011-10-21 11:21来源:阿里巴巴塑料价格库为了满足工业上降低某些塑料产品的成本而不降低其主要力学性能的要求,20世纪80年代初期,美国麻省理工学院(MIT)的Suh课题组首先提出并成功研制了微孔发泡塑料。
与未发泡的塑料相比,微孔发泡塑料密度可降低5%~95%,冲击强度可增加高达5倍,韧性提高5倍,刚度增加3~5倍,疲劳寿命延长5倍,介电常数和热导率大幅下降。
由于这些独特的性能,使微孔发泡塑料的应用领域非常宽广,如应用于飞机和汽车零部件、运动器材、保温纤维、分子级过滤器、生物医学材料、吸附剂及催化剂载体、绝缘纤维及分子筛等,微孔发泡塑料被称为“21世纪的新型材料”。
到目前为止,微孔发泡塑料可采用相分离法、单体聚合法、超临界流体沉淀法、超饱和气体法和模压法等多种方法制备,其中相分离法污染大;单体聚合法和压缩流体反溶剂沉淀法效率低;超饱和气体法中的釜压法生产周期长;挤出法和注射法生产成本高;模压法等方法应用范围有限。
随着技术的发展和社会的进步,对微孔发泡塑料的成型技术提出了更高的要求,如环境友好性,不使用有可能对塑料基体造成污染的添加剂;微观结构的可控性及能够实现连续生产等。
要满足这些要求,必须开发新的微孔发泡塑料制备技术。
1 相分离法这是较早出现的一种制备开孔结构微孔发泡塑料的方法。
首先将聚合物溶于一定溶剂中,使两相、三相或多相混合物体系在温度或溶剂等作用下产生分相,从而得到带有微孔结构的聚合物,最后通过升华干燥或超临界萃取的方法将溶剂与聚合物分开,即得到微孔发泡塑料。
Aubert和Clough提出了一种相分离法生产低密度PS微孔发泡塑料。
其成型过程如下:首先将聚合物PS溶解到发泡塑料。
其成型过程如下:首先将聚合物PS溶解到适当的溶剂中,并将溶液置于模具中快速冷却使溶液冷冻;然后通过升华干燥将溶剂挥发掉,留下的聚合物就成为了微孔泡沫塑料。
微孔发泡技术

微孔发泡技术的应用
目前发泡工艺中,最为热门的前沿研究课题之一就是微孔发泡(包括超微孔发泡)工艺。
微孔泡沫塑料是指气孔直径为1~10μm,泡孔密度为109~1012个/cm,泡孔分布非常均匀的新型泡沫塑料。
此类塑料是20世界80年度初在美国麻省理工学院(MIT)实验室里研制成功的。
微孔发泡工艺过程在1984年获得美国专利。
其主要设计思想在于:当泡沫塑料中泡孔的尺寸小于泡孔内部材料的裂纹时,泡孔的存在将不会降低材料的力学性能,而且,微孔的存在将使材料原来存在的裂纹尖端钝化,有利于阻止裂纹在应力作用下得扩展,从而使材料的性能得到提高。
因此,与未发泡的塑料相比,除密度可降低5%~95%外,微孔泡沫塑料还具有以下优点:冲击强度高(可达未发泡塑料的5倍);韧性高(可达未发泡塑料的5倍);比刚度高(可达未发泡塑料的3~5倍);疲劳寿命长(可达未发泡塑料的5倍);介电常数低;热导率低。
因此,微孔泡沫塑料在汽车、飞机及各种运输器材领域具有特殊的应用价值。
另外,它还可用于食品包装、生物医学、建筑材料、家电产品、信息工程及运动器材等方面,被誉为是21世纪的新型材料。
随着加工技术的不断进步,现在又开发出泡孔直径为0.1~10μm、泡孔密度为1012~1015个/cm3的超微孔泡沫塑料。
这些微孔泡沫塑料可用做可染色的塑料用品和计算机芯片用得微小绝缘体,并且由于其泡孔直径小于可见光的波长,故可制成透明的泡沫塑料,大大扩展了泡沫塑料的应用范围。
因此,开发微孔泡沫塑料具有非常广阔的空间。
- 1、下载文档前请自行甄别文档内容的完整性,平台不提供额外的编辑、内容补充、找答案等附加服务。
- 2、"仅部分预览"的文档,不可在线预览部分如存在完整性等问题,可反馈申请退款(可完整预览的文档不适用该条件!)。
- 3、如文档侵犯您的权益,请联系客服反馈,我们会尽快为您处理(人工客服工作时间:9:00-18:30)。
微孔发泡成型技术简介
目录
微孔发泡成型技术背景
微孔发泡成型技术原理
微孔发泡注塑成型优势
微孔发泡注塑成型技术装备 微孔发泡成型技术应用产品
料加使用发技术减轻制但传发塑料加工使用发泡技术可以减轻制品重量,但传统的发泡工艺采用石油气(如丁烷、戊烷)为发泡剂,随着当前环保问题以及生产安全问题的日益突出,对于节能、环保、安全稳定的新型发泡剂的需求不断扩大。
全稳定的新型发泡剂的需求不断扩大
常规状态下,二氧化碳或氮气在熔融树脂中溶解量非常少,不足以用来发泡但在超临界状态下二氧化碳或氮气的溶不足以用来发泡,但在超临界状态下,二氧化碳或氮气的溶解度和扩散速度将大幅提高,从而完全具备微孔发泡所需的条件在完善的技术装备配合下超临界状态气体工艺条件,在完善的工艺技术装备配合下,超临界状态气体实现了微孔发泡的完美效果。
在注塑、挤出以级吹塑成型工艺中,先将超临界状态的二氧化碳或氮气注入到特殊的塑化装置中,使气体与熔融原料充分均匀混合/扩散后,形成单相混合溶胶:
将该溶胶导入模具型腔或口模,使混合溶胶产生巨大的压力
降,从而使其内部析出形成大量的气泡核;在随后的冷却成降从而使其内部析出形成大量的气泡核在随后的冷却成型过程中,溶胶内部的气泡核不断长大成型,最终获得微孔
发泡的塑料制品。
在预定背压下熔融塑化树脂,向熔融树脂中定量注入SCF N2
或CO2;通过进一步混合/扩散后形成均相溶液,并在进入模具型腔之前保持该状态;注射进入到型腔中,通过注射过程中的热力学不稳定性,瞬时形成大量的气泡核;在填充和冷却过程中,气泡长大并被固定,获得微孔发泡制品。
却过程中气泡长大并被固定获得微孔发泡制品
技术优势主
技术优势主:
-大幅提高制品尺寸精度,缩短产品开发周期;
-大幅减少产品残余应力,减少改善制品翘曲变形,提高尺寸精度;-消除表面缩痕,制品表面无缩水痕;
-有效缩短薄壁制品的成型周期,提高生产效率;
有效节约原材料减轻产品质量节约原材料;
-有效节约原材料,减轻,节约原材料;
-减少锁模力需求,节约制造成本;
-发泡剂成本低廉,环保,适用于所有应用领域;
-改善制品尺寸精度和稳定性;
-混合溶胶流动性增强20%-40%,粘度低,充填效果明显;
-微孔结构有效改善内部应力分布;
-超临界气体设备工艺简单,成本低廉,绿色环保;
超临界气体设备工艺简单成本低廉绿色环保
-制造过程中污染物零排放,制品不含化学残留物。
经济优势:
-获得长期降低制造成本的手段
-获得改善制品质量的简捷方法
-获取战略性发展机会
超临状态氮气获得装超临气体注控制设备
1、超临界状态氮气获得装置
2、超临界气体注入控制设备
3、混合溶胶专用塑化装置与螺杆
1、工业电器、家用电器、办公及商业电子类产品零部件,也是微孔发泡注塑成型技术应用极具潜力的发展空间领域。
2、汽车内外装饰件,发动机舱内部零部件等产品是微孔发泡注塑
汽车内外装饰件发动机舱内部零部件等产品是微孔发泡注塑成型技术应用最为广泛的空间领域,具有深远意义。
3、TPV/TPE密封条、PVC型材、PP/PE/PS片材,更是微孔发泡注塑成型技术应用全面发展的空间领域。
注塑成型技术应用全面发展的空间领域
谢谢TCL集团股份有限公司
@TCL创意感动生活。