油气管道内检测新技术举例
无损检测技术在石油与天然气行业中的应用案例与经验分享

无损检测技术在石油与天然气行业中的应用案例与经验分享在石油与天然气行业中,无损检测技术是一项关键的技术手段,其应用具有重要意义。
无损检测技术通过使用不破坏测试的方法来评估材料和构件的完整性和性能,可以有效地检测和识别潜在的材料缺陷和错误,提高工作效率、确保安全性,并减少生产过程中的故障和损耗。
本文将就石油与天然气行业中无损检测技术的应用案例与经验进行分享。
首先,无损检测技术在石油与天然气行业的设备维护和安全检查中具有广泛的应用。
例如,对管道系统进行无损检测可以及时发现管道壁厚度的减小、气体泄漏、腐蚀和裂纹等问题,避免了潜在的灾难事故。
此外,无损检测技术还可以用于检测储罐的泄漏、结构裂纹和变形等问题,确保储油设施的可靠性和安全性,从而避免了大量资源的浪费和环境污染的风险。
其次,在石油与天然气勘探中,无损检测技术也发挥了重要作用。
无损检测技术可以用于地下油气管道和储层的探测,帮助石油工程师准确评估地下油气资源的储量和分布情况。
此外,无损检测技术还可以用于探测地下水源和溶解气体等,提供重要的勘探信息,为石油和天然气的开发和利用提供科学依据。
再次,无损检测技术在石油与天然气产品的加工过程中扮演重要角色。
例如,在石油炼油过程中,无损检测技术可以用于检测石油产品中的硫、水分和杂质等,确保产品质量并满足相关标准要求。
在天然气加工过程中,无损检测技术可以用于检测天然气的组分和纯度,以及液化天然气的质量指标,为相关企业的生产运营提供重要的技术支持。
此外,无损检测技术在石油与天然气行业中的经验积累也是非常宝贵的。
在实际应用中,尤其是在大型石油与天然气企业中,无损检测技术需要经过长期的实践和总结,才能形成相对成熟的应用方案。
在实施无损检测技术时,操作人员首先需要具备相关的专业知识和技能,并接受专业的培训和认证。
同时,还需要建立完善的无损检测技术体系和管理制度,确保技术的可靠性和操作的准确性。
此外,还需要不断改进和创新无损检测技术,以满足石油与天然气行业日益增长的需求。
油气管道内检测新技术举例
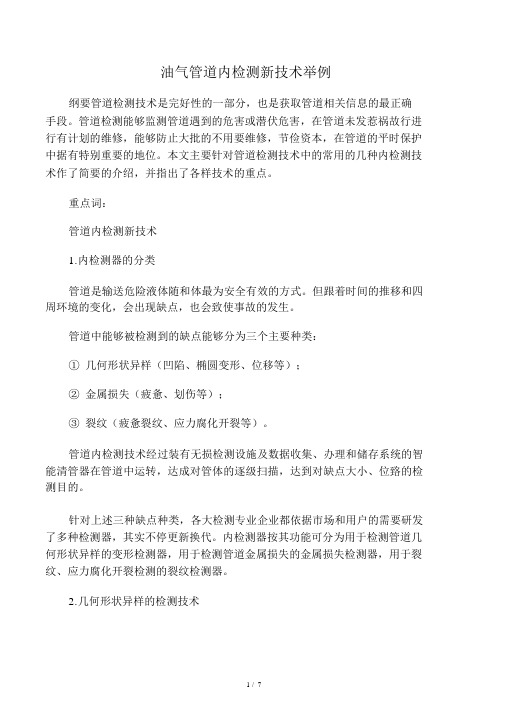
油气管道内检测新技术举例纲要管道检测技术是完好性的一部分,也是获取管道相关信息的最正确手段。
管道检测能够监测管道遇到的危害或潜伏危害,在管道未发惹祸故行进行有计划的维修,能够防止大批的不用要维修,节俭资本,在管道的平时保护中据有特别重要的地位。
本文主要针对管道检测技术中的常用的几种内检测技术作了简要的介绍,并指出了各样技术的重点。
重点词:管道内检测新技术1.内检测器的分类管道是输送危险液体随和体最为安全有效的方式。
但跟着时间的推移和四周环境的变化,会出现缺点,也会致使事故的发生。
管道中能够被检测到的缺点能够分为三个主要种类:① 几何形状异样(凹陷、椭圆变形、位移等);② 金属损失(疲惫、划伤等);③ 裂纹(疲惫裂纹、应力腐化开裂等)。
管道内检测技术经过装有无损检测设施及数据收集、办理和储存系统的智能清管器在管道中运转,达成对管体的逐级扫描,达到对缺点大小、位臵的检测目的。
针对上述三种缺点种类,各大检测专业企业都依据市场和用户的需要研发了多种检测器,其实不停更新换代。
内检测器按其功能可分为用于检测管道几何形状异样的变形检测器,用于检测管道金属损失的金属损失检测器,用于裂纹、应力腐化开裂检测的裂纹检测器。
2.几何形状异样的检测技术管道几何形状的异样多因遇到外面机械力或焊接剩余应力等原由造成,经过使用适合的检测装臵能够检测各样原由造成的、影响管道有效内径的几何异样现象并确立其程度和位臵。
测径器是用于检测、定位和丈量管壁几何形状异样的大小。
正常的管线,应该有一个圆环形横断面。
在管道铺设过程或长久运转中,第三方的扰乱能够造成凹陷。
合格的测经器应可对任何管段横断面的临界变化进行检测并确立大小,是进行管道金属损失或裂纹内检测以前特别重要的一步。
常用的测径器使用必定摆列的机械抓手或有机械抓手的辐射架。
机械抓手压着管道内壁并会因横断面的任何变化惹起偏移。
这些偏移可能是因为一个凹陷、偏圆、褶皱或附着在管壁上的碎屑惹起的。
科技成果——长输油气管道内检测系统

科技成果——长输油气管道内检测系统所属领域油气储运成果简介近20年来,管线工业得到迅速发展,长输管道运行安全性成了一个关系到国计民生的重大问题。
管道内检测系统由管道漏磁内检测系统(俗称智能PIG)和管道变径内检测系统组成,管道漏磁内检测系统应用漏磁检测原理对输送管道进行在线无损检测,为管道运行、维护及安全评价提供科学依据。
管道漏磁内检测系统以管道输送介质为行进动力,在管道中行走,对管道进行在线直接无损检测是当前国内外公认的主要的管道检测手段。
该系统完成长输油/气管道缺陷检测,完成管道缺陷、管壁变化、管壁材质变化、缺陷内外分辨、管道特征(管箍、补疤、弯头、焊缝和三通等)识别检测,可提供缺陷面积、程度、方位和位置等全面信息。
管道变径内检测系统完成管道机械变形的检测功能,变径管道检测器在管道中由输送介质推动,在管道内运行,完成管道机械变形检测,变径管道检测器由机械变形传感器、计算机数据处理系统和定位系统组成。
应用范围φ159-φ1400各规格钢质长输油/气管技术特点管道漏磁内检测系统性能指标获奖情况2001年11月通过了国家自然科学基金委员会组织的鉴定,认为在主要指标上达到国际先进水平。
该项目2004年获国家科技进步二等奖,2003年获辽宁省科技进步一等奖。
该项目取得了一系列漏磁管道探伤理论成果,添补国内空白,打破国际垄断,同时为项目应用企业取得了巨大的经济效益和社会效益。
专利情况授权发明专利1项,申请发明专利9项。
技术水平国际先进生产使用条件适用于国内外已使用的钢质长输油气管道。
市场前景目前我国在役长距离油/气输送管道总长约3万公里,在建和拟建的西部十余条管线长达近万公里。
近年来,国内管道故障时常发生,一般事故将造成上百万乃至几百万的经济损失,且造成环境污染,所以管道运行检测在国内已引起高度关注。
管道内检测是管道检测的直接有效手段,在国际上属于垄断技术,每套设备标价几百万至几千万美元,且不易购买。
国外公司在我国进行管道检测的服务费用亦十分昂贵,每公里检测费用达上万美元。
油气管道变形检测的技术方法有哪些

油气管道变形检测的技术方法有哪些油气管道的变形检测是为了保障管道的安全运营,预防泄漏和爆炸等事故的发生。
目前主要的油气管道变形检测技术方法包括:1.无损检测技术:无损检测技术是一种通过对管道表面进行检测,不需要对管道进行破坏或取样的方法。
主要包括超声波检测、磁粉检测、涡流检测和射线检测等。
这些技术能够检测到管道内部或外部的腐蚀、裂纹、疲劳等问题,从而确定管道的变形情况。
2.激光检测技术:激光检测技术通过激光束的测量,计算出管道的形状和尺寸,从而确定管道的变形情况。
激光检测技术具有高度精确度和快速性的特点,能够对管道的变形进行在线实时监测。
3.声波检测技术:声波检测技术通过对管道内部发送声波信号,并通过接收信号的回波进行分析,确定管道的变形情况。
该技术非常适用于检测管道内部的缺陷或损伤,如裂纹、腐蚀等。
4.振动检测技术:振动检测技术通过对管道应力状态下的振动信号进行检测和分析,确定管道的变形情况。
该技术可以根据振动信号的变化识别管道的变形或异常情况。
5.计算机视觉技术:计算机视觉技术通过对管道的照片或视频图像进行分析,提取出有关管道变形的特征信息,从而确定管道的变形情况。
该技术具有非接触、高效率和自动化的特点。
6.应力分析技术:应力分析技术通过对管道的应力状态进行数值分析,确定管道的变形情况。
该技术可以基于管道的物理性质和外部载荷,计算出管道的应力分布和变形情况。
7.光纤传感技术:光纤传感技术通过将光纤安装在管道表面或内部,利用光纤光学特性的变化来监测管道的变形情况。
该技术具有高度灵敏度和实时监测的特点。
以上是目前常用的油气管道变形检测技术方法,各种方法都有其适用的场景和特点。
在实际应用中,通常需要结合多种技术来进行综合检测,以提高检测的准确性和可靠性。
油气管道内部清洗与检测方法
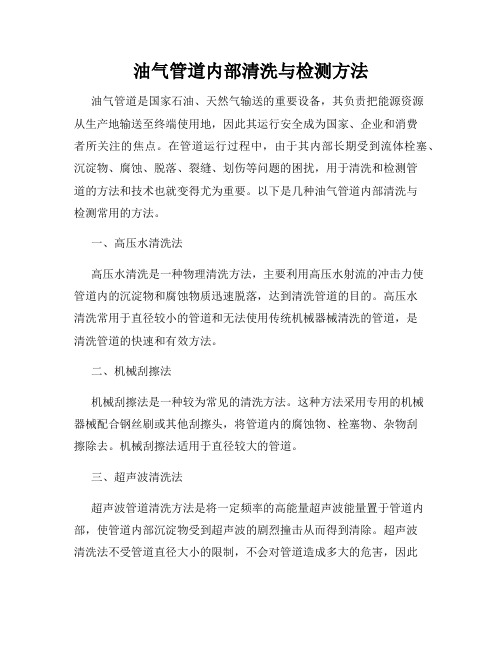
油气管道内部清洗与检测方法油气管道是国家石油、天然气输送的重要设备,其负责把能源资源从生产地输送至终端使用地,因此其运行安全成为国家、企业和消费者所关注的焦点。
在管道运行过程中,由于其内部长期受到流体栓塞、沉淀物、腐蚀、脱落、裂缝、划伤等问题的困扰,用于清洗和检测管道的方法和技术也就变得尤为重要。
以下是几种油气管道内部清洗与检测常用的方法。
一、高压水清洗法高压水清洗是一种物理清洗方法,主要利用高压水射流的冲击力使管道内的沉淀物和腐蚀物质迅速脱落,达到清洗管道的目的。
高压水清洗常用于直径较小的管道和无法使用传统机械器械清洗的管道,是清洗管道的快速和有效方法。
二、机械刮擦法机械刮擦法是一种较为常见的清洗方法。
这种方法采用专用的机械器械配合钢丝刷或其他刮擦头,将管道内的腐蚀物、栓塞物、杂物刮擦除去。
机械刮擦法适用于直径较大的管道。
三、超声波清洗法超声波管道清洗方法是将一定频率的高能量超声波能量置于管道内部,使管道内部沉淀物受到超声波的剧烈撞击从而得到清除。
超声波清洗法不受管道直径大小的限制,不会对管道造成多大的危害,因此被广泛应用于清洗小直径管道、内壁光滑的管道或无法使用机械刮擦法的管道。
四、超声波检测法超声波检测法是在管道内部放置特制的超声波探头,检测探头发射回来的超声波信号,通过对超声波信号的位移和衰减来判断管道的内部状态。
该技术主要用于材料检测、管道壁面损伤检测和管道流水中氧化铁沉淀的粒度分析。
红外扫描技术检测也可用于定位管道故障点。
五、普及式管道检测仪普及式管道检测仪是油气管道内部检测技术的一种重要进展。
普及式管道检测仪是由多个小型探头及相应的信息采集、传输、处理器组成的机械。
其主要适用于对大直径管道的整体性能评估,检测管道中的设备、垃圾或其他异物、松散的沉积物、内壁沟槽、不同类型的腐蚀或裂缝、管道变形等问题。
总之,油气管道内部清洗与检测方法的不断革新也能预防和减少来自管道运行方。
油气管道泄漏检测方法研究

油气管道泄漏检测方法研究随着能源需求的不断增长,世界各国对于油气能源的探索和开发越来越重视,石油和天然气管道已成为世界各国最主要的能源输送方式之一。
然而,油气管道泄漏事件时有发生,给环境和人类带来极大的威胁和危害,因此,油气管道泄漏检测方法研究日益受到重视。
一、常见的油气管道泄漏检测方法1. 声波检测法声波检测法是利用检测仪器测量油气管道内的声波振动情况,通过音频信号分析出疑似泄漏点,进而进行确认和修复。
该方法具有非侵入性、高效性、定位精度高等优点,适用于长距离和大口径管道的泄漏检测。
2. 热成像检测法热成像检测法是利用热成像相机或热像仪等设备对管道表面进行扫描,通过检测管道表面的温度变化,分析出疑似泄漏位置。
该方法具有高灵敏度、非侵入性、无需直接接触管道等优点,适用于在表面上的小型泄漏检测。
3. 化学检测法化学检测法是利用气体检测仪或其他化学检测设备对泄漏处周围空气进行采样和分析,通过检测出泄漏气体种类和浓度,分析出泄漏位置。
该方法具有高灵敏度、准确度高等优点,适用于天然气等易燃易爆气体泄漏监测。
二、油气管道泄漏检测方法的研究进展1. 基于机器视觉技术的泄漏检测当前,基于机器视觉技术的泄漏检测方法是油气管道泄漏检测领域的研究热点。
该方法通过安装高清晰度摄像机等设备对管道进行拍摄,利用图像分析技术对管道表面进行分析,能够有效地检测出管道表面的微小裂缝和渗漏处。
2. 基于机器学习技术的泄漏检测机器学习是一种基于人工智能的方法,能够通过对大量数据的学习和分析,将数据中的规律和模式提取出来,并对新数据进行判断和分类。
近年来,研究人员开始将机器学习应用于油气管道泄漏检测领域。
机器学习较传统方法的优势在于能够对泄漏点进行分类,从而更加快速准确地定位泄漏点。
三、总结油气管道泄漏是一种十分危险的事件,为保障能源安全和环境保护,需要采用有效的泄漏检测方法。
当前,主要的油气管道泄漏检测方法有声波检测法、热成像检测法和化学检测法。
油气管道内检测的类型及现状

油气管道内检测的类型及现状管道发生腐蚀后,主要表现为管壁减薄、蚀损斑、腐蚀点坑、应力腐蚀裂纹等。
管道内检测就是应用各种检测技术真实地检测和记录包括管道的基本尺寸(壁厚及管径)、管线直度、管道内外腐蚀状况(腐蚀区大小、形状、深度及发生部位)、焊缝缺陷以及裂纹等情况。
目前,国内外在油气管线内腐蚀方面做了大量的工作,提出了多种检测技术,其中部分技术已被应用并取得了良好的效果。
这些技术包括:漏磁检测技术、超声波检测技术、涡流检测技术、射线检测技术、基于光学原理的无损检测技术。
1漏磁检测技术漏磁检测技术是建立在如钢管、钢棒等铁磁性材料的高磁导率这一特性上的。
其基本原理如图1所示,钢管中因腐蚀而产生缺陷处的磁导率远小于钢管的磁导率;钢管在外加磁场作用下被磁化,当钢管中无缺陷时,磁力线绝大部分通过钢管,此时磁力线均匀分布;当钢管内部有缺陷时,磁力线发生弯曲,并且有一部分磁力线泄漏出钢管表面,检测被磁化钢管表面逸出的漏磁通,就可判断缺陷是否存在,通过分析磁敏传感器的测量结果,即可得到缺陷的有关信息。
图1漏磁检测原理该方法以其在线检测能力强、自动化程度高等独特优点而满足管道运营中的连续性、快速性和在线检测的要求,使得漏磁检测成为到目前为止应用最为广泛的一种磁粉检测方法,在油田管道检测中使用极为广泛。
此外与常规的磁粉检测相比,漏磁检测具有量化检测结果、高可靠性、高效、低污染等特点。
2超声波检测仪超声波检测是用灵敏的仪器接收和处理采集到的声发射信号,通过对声发射源特征参数的分析和研究,推断出材料或结构内部活动缺陷的位置、状态变化程度和发展趋势。
其基本原理如图2所示。
图2超声波裂纹检测原理该方法是利用超声波的脉冲反射原理来测量管壁腐蚀后的厚度,检测时将探头垂直向管道内壁发射超声脉冲,探头首先接受到由管壁内表面的反射脉冲,然后超声探头又会接受到来自管壁外表面的反射脉冲,这两个反射脉冲之间的间距反映了管壁的厚度。
超声检测是管道腐蚀缺陷深度和位置的直接检测方法,测量精度高,被测对象范围广、检测数据简单,缺陷定位准确且无需校验,检测数据非常适合用于管道最大允许输送压力的计算,为检测后确定管道的使用期限和维修方案提供了极大的方便;适用于大直径、厚管壁管道的检测;能够准确检测出管道的应力腐蚀破裂和管壁内的缺陷如夹杂等。
油气管道仪表检测及自动化控制技术 第21部分
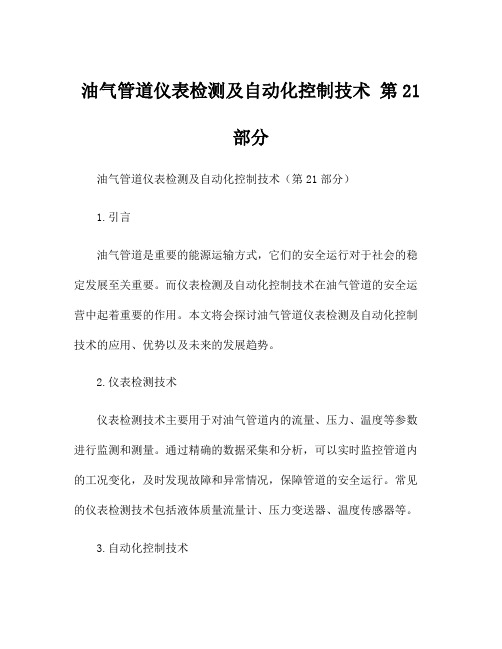
油气管道仪表检测及自动化控制技术第21部分油气管道仪表检测及自动化控制技术(第21部分)1.引言油气管道是重要的能源运输方式,它们的安全运行对于社会的稳定发展至关重要。
而仪表检测及自动化控制技术在油气管道的安全运营中起着重要的作用。
本文将会探讨油气管道仪表检测及自动化控制技术的应用、优势以及未来的发展趋势。
2.仪表检测技术仪表检测技术主要用于对油气管道内的流量、压力、温度等参数进行监测和测量。
通过精确的数据采集和分析,可以实时监控管道内的工况变化,及时发现故障和异常情况,保障管道的安全运行。
常见的仪表检测技术包括液体质量流量计、压力变送器、温度传感器等。
3.自动化控制技术自动化控制技术主要通过仪表检测技术获取的数据,实现对油气管道运行状态的自动控制。
自动化控制系统能够根据预设参数和运行要求,自动调节流量、压力和温度等,保证管道的安全运行。
自动化控制技术能够实现管道系统的远程控制和集中管理,大大提高了管道运行的效率和安全性。
4.仪表检测及自动化控制技术的优势仪表检测及自动化控制技术具有以下优势:-提高安全性:通过实时监测和控制,避免了人为操作错误和设备故障等因素引起的安全事故。
-提高效率:自动化控制系统能够根据实际需求进行精确调节,提高管道运输效率,并降低能耗和运输成本。
-减少人力投入:自动化控制系统能够实现远程控制和集中管理,减少了对人力资源的需求。
-增强数据分析能力:仪表检测技术能够实时采集大量的管道运行参数,并通过数据分析提供决策支持和预测分析。
-可追溯性:仪表检测技术能够记录管道运行状态的历史数据,为事故调查和质量追溯提供有力支持。
5.仪表检测及自动化控制技术的发展趋势随着科技的进步和人们对安全生产的重视,油气管道仪表检测及自动化控制技术也在不断发展和创新。
未来,可以预见以下几个发展趋势:-高精度测量技术:随着计算机和传感技术的不断进步,仪表检测技术将会实现更高的测量精度和稳定性,并且能够适应各种复杂工况。
《油气输送管道检测方法及安全评价》
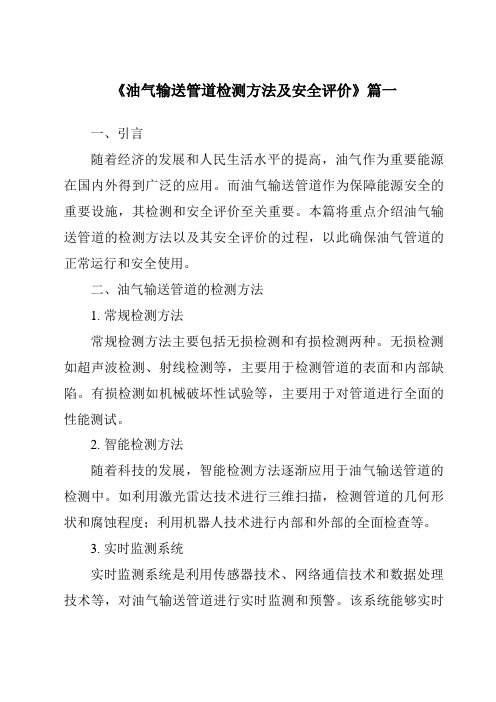
《油气输送管道检测方法及安全评价》篇一一、引言随着经济的发展和人民生活水平的提高,油气作为重要能源在国内外得到广泛的应用。
而油气输送管道作为保障能源安全的重要设施,其检测和安全评价至关重要。
本篇将重点介绍油气输送管道的检测方法以及其安全评价的过程,以此确保油气管道的正常运行和安全使用。
二、油气输送管道的检测方法1. 常规检测方法常规检测方法主要包括无损检测和有损检测两种。
无损检测如超声波检测、射线检测等,主要用于检测管道的表面和内部缺陷。
有损检测如机械破坏性试验等,主要用于对管道进行全面的性能测试。
2. 智能检测方法随着科技的发展,智能检测方法逐渐应用于油气输送管道的检测中。
如利用激光雷达技术进行三维扫描,检测管道的几何形状和腐蚀程度;利用机器人技术进行内部和外部的全面检查等。
3. 实时监测系统实时监测系统是利用传感器技术、网络通信技术和数据处理技术等,对油气输送管道进行实时监测和预警。
该系统能够实时监测管道的压力、温度、流量等参数,及时发现并预警可能的安全隐患。
三、油气输送管道的安全评价安全评价是对油气输送管道的运行状态进行全面的评估,以确定其安全性和可靠性。
主要步骤如下:1. 收集数据:收集管道的基本信息、运行数据、历史事故记录等。
2. 风险评估:根据收集的数据,对管道的运行风险进行评估,包括事故发生的可能性、后果严重程度等。
3. 安全评价:根据风险评估的结果,对管道的安全性和可靠性进行评价。
包括管道的强度、刚度、稳定性等。
4. 制定措施:根据安全评价的结果,制定相应的措施,如维修、更换、加固等,以提高管道的安全性和可靠性。
四、结论油气输送管道的检测和安全评价是保障能源安全和人民生活的重要措施。
常规检测方法、智能检测方法和实时监测系统等方法可以全面检查和监控管道的状态。
同时,安全评价的全面实施能够确保管道的长期稳定运行和安全使用。
在未来的发展中,应进一步研究和应用新的检测技术和方法,提高油气输送管道的检测和安全评价水平,确保能源安全和人民生活的正常进行。
在役油气管道缺陷检测与监测关键技术成果

在役油气管道缺陷检测与监测关键技术成果一、前言在当今社会,石油和天然气作为重要的能源资源,对于维护国家经济安全和社会稳定发挥着不可替代的作用。
然而,随着油气管道的不断延伸和使用,管道安全问题也日益突出。
管道的缺陷检测与监测技术成为保障管道运行安全稳定的重要手段。
本文将就在役油气管道缺陷检测与监测关键技术成果展开深入探讨。
二、X-ray探伤技术X-ray探伤技术是一种应用先进的射线技术来检测管道内部缺陷的技术。
它可以穿透金属材料,将管道内部的结构缺陷、材料变异等情况显示在辐射膜或屏幕上,方便工作人员快速准确地判别管道内部是否存在缺陷。
X-ray探伤技术的应用为管道的及时修补提供了科学依据,保障了管道的安全运行。
近年来,国内外对X-ray探伤技术进行了深入研究,并取得了一系列关键技术成果,如高能X-ray探伤技术、微焦点X-ray探伤技术等。
这些成果的应用,使得X-ray探伤技术在管道缺陷检测与监测领域拥有更广阔的前景。
三、超声波检测技术超声波检测技术是一种利用超声波在介质中传播的特性,探测管道内部缺陷的技术。
它能够准确地检测管道内部的表面裂纹、壁厚变薄、管道腐蚀、孔隙度等情况,进而为管道的维修提供重要数据支持。
近年来,通过对超声波探测技术的深入研究,国内外学者不断取得关键技术成果,如多频段超声波探测技术、相控阵超声波探测技术等。
这些成果的应用,使得超声波检测技术在油气管道缺陷检测与监测领域具有更广泛的应用前景。
四、电磁无损检测技术电磁无损检测技术是一种利用电磁场感应原理,对管道内部缺陷进行检测的技术。
它具有无损、快速、准确的特点,能够有效地检测出管道内部的腐蚀、裂纹、材料变异等情况,提供了可靠的数据支持。
在最近的研究中,国内外学者对电磁无损检测技术进行了深入探索,取得了一系列关键技术成果,如高灵敏度电磁无损检测技术、多频段电磁无损检测技术等。
这些成果的应用,为油气管道缺陷检测与监测提供了更加可靠和准确的手段。
油气集输管道腐蚀检测技术及应用
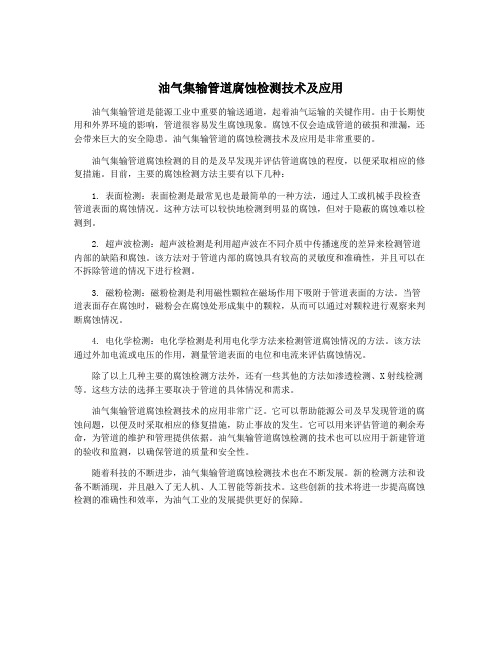
油气集输管道腐蚀检测技术及应用油气集输管道是能源工业中重要的输送通道,起着油气运输的关键作用。
由于长期使用和外界环境的影响,管道很容易发生腐蚀现象。
腐蚀不仅会造成管道的破损和泄漏,还会带来巨大的安全隐患。
油气集输管道的腐蚀检测技术及应用是非常重要的。
油气集输管道腐蚀检测的目的是及早发现并评估管道腐蚀的程度,以便采取相应的修复措施。
目前,主要的腐蚀检测方法主要有以下几种:1. 表面检测:表面检测是最常见也是最简单的一种方法,通过人工或机械手段检查管道表面的腐蚀情况。
这种方法可以较快地检测到明显的腐蚀,但对于隐蔽的腐蚀难以检测到。
2. 超声波检测:超声波检测是利用超声波在不同介质中传播速度的差异来检测管道内部的缺陷和腐蚀。
该方法对于管道内部的腐蚀具有较高的灵敏度和准确性,并且可以在不拆除管道的情况下进行检测。
3. 磁粉检测:磁粉检测是利用磁性颗粒在磁场作用下吸附于管道表面的方法。
当管道表面存在腐蚀时,磁粉会在腐蚀处形成集中的颗粒,从而可以通过对颗粒进行观察来判断腐蚀情况。
4. 电化学检测:电化学检测是利用电化学方法来检测管道腐蚀情况的方法。
该方法通过外加电流或电压的作用,测量管道表面的电位和电流来评估腐蚀情况。
除了以上几种主要的腐蚀检测方法外,还有一些其他的方法如渗透检测、X射线检测等。
这些方法的选择主要取决于管道的具体情况和需求。
油气集输管道腐蚀检测技术的应用非常广泛。
它可以帮助能源公司及早发现管道的腐蚀问题,以便及时采取相应的修复措施,防止事故的发生。
它可以用来评估管道的剩余寿命,为管道的维护和管理提供依据。
油气集输管道腐蚀检测的技术也可以应用于新建管道的验收和监测,以确保管道的质量和安全性。
随着科技的不断进步,油气集输管道腐蚀检测技术也在不断发展。
新的检测方法和设备不断涌现,并且融入了无人机、人工智能等新技术。
这些创新的技术将进一步提高腐蚀检测的准确性和效率,为油气工业的发展提供更好的保障。
油气管道无损检测技术

油气管道无损检测技术管道作为大量输送石油、气体等能源的安全经济的运输手段,在世界各地得到了广泛应用,为了保障油气管道安全运行,延长使用寿命,应对其定期进行检测,以便发现问题,采取措施。
一、管道元件的无损检测(一)管道用钢管的检测埋地管道用管材包括无缝钢管和焊接钢管。
对于无缝钢管采用液浸法或接触法超声波检测主要来发现纵向缺陷。
液浸法使用线聚焦或点聚焦探头,接触法使用与钢管表面吻合良好的斜探头或聚焦斜探头。
所有类型的金属管材都可采用涡流方法来检测它们的表面和近表面缺陷。
对于焊接钢管,焊缝采用射线抽查或100 %检测,对于100 %检测,通常采用X射线实时成像检测技术。
(二)管道用螺栓件对于直径> 50 mm 的钢螺栓件需采用超声来检测螺栓杆内存在的冶金缺陷。
超声检测采用单晶直探头或双晶直探头的纵波检测方法。
二、管道施工过程中的无损检测(一)各种无损检测方法在焊管生产中的配置国外在生产中常规的主要无损检测配置如下图一中的A、B、C、E、F、G、H工序。
我国目前生产中的检测配置主要岗位如下图中的A、C、D、E、F、G、H工序。
图一大口径埋弧焊街钢管生产无损检测岗位配置(二)超声检测全自动超声检测技术目前在国外已被大量应用于长输管线的环焊缝检测,与传统手动超声检测和射线检测相比,其在检测速度、缺陷定量准确性、减少环境污染和降低作业强度等方面有着明显的优越性。
全自动相控阵超声检测系统采用区域划分方法,将焊缝分成垂直方向上的若干个区,再由电子系统控制相控阵探头对其进行分区扫查,检测结果以双门带状图的形式显示,再辅以TOFD (衍射时差法)和B扫描功能,对焊缝内部存在的缺陷进行分析和判断。
全自动超声波现场检测时情况复杂,尤其是轨道位置安放的精确度、试块的校准效果、现场扫查温度等因素会对检测结果产生强烈的影响,因此对检测结果的评判需要对多方面情况进行综合考虑,收集各种信息,才能减少失误。
(三)射线检测射线检测一般使用X 射线周向曝光机或γ射线源,用管道内爬行器将射线源送入管道内部环焊缝的位置,从外部采用胶片一次曝光,但胶片处理和评价需要较长的时间,往往影响管道施工的进度,因此,近年来国内外均开发出专门用于管道环焊缝检测的X 射线实时成像检测设备。
油气管道安全监测技术的研究与应用

油气管道安全监测技术的研究与应用近年来,随着石油和天然气的需求不断增大,油气管道的建设和使用也越来越普遍。
然而,油气管道作为一种高压、高温、高爆炸性的设施,一旦出现泄漏、爆炸等安全事故,就会造成严重的环境和人身伤害。
因此,对于油气管道的安全监测技术和应用显得尤为重要。
一、油气管道安全监测技术的现状目前,油气管道安全监测技术主要包括以下几种:1. 红外断层检测技术:通过检测管道表面的红外辐射,实现对管道断层的检测。
该技术具有检测范围广、精度高、误差小等优点。
2. 声波检测技术:通过对管道传播的声波进行分析,实现对管道的泄漏和破损等情况的检测。
该技术具有检测范围广、灵敏度高等优点,但误判率较高。
3. 核磁共振检测技术:通过对管道表面的核磁共振进行检测,实现对管道内部结构和质量的检测。
该技术具有高精度、高灵敏度等优点,但设备成本高,适用范围较为有限。
二、油气管道安全监测技术的研究现状目前,油气管道安全监测技术的研究主要围绕以下几个方向展开:1. 新技术的研究:针对上述现有的油气管道监测技术存在的缺陷和不足,研究新的监测技术,如热像仪监测技术、激光光纤监测技术等,以提高监测的灵敏度和准确性。
2. 降低设备成本:在研究新技术的同时,提高技术设备的制造水平和降低制造成本,以便更广泛地应用于实际的管道监测中。
3. 数据采集和处理:对管道监测中产生的海量数据进行机器学习和数据挖掘等处理,以实现对监测数据的快速分析和预警,保障管道的安全稳定运行。
三、油气管道安全监测技术的应用现状目前,油气管道安全监测技术已经在实际中得到了广泛的应用。
1. 中国石油:中国石油通过对石油管道的检测和预警,实现了对管道运行状态的及时监测和管理。
2. 环保部:环保部利用地理信息系统,在油气管道周围设立环境监测站点,对管道周边环境进行实时监测。
3. 美国Transocean公司:Transocean公司通过对深海油气管道的监测技术,为深海油气钻探提供了重要支撑。
《2024年油气输送管道检测方法及安全评价》范文
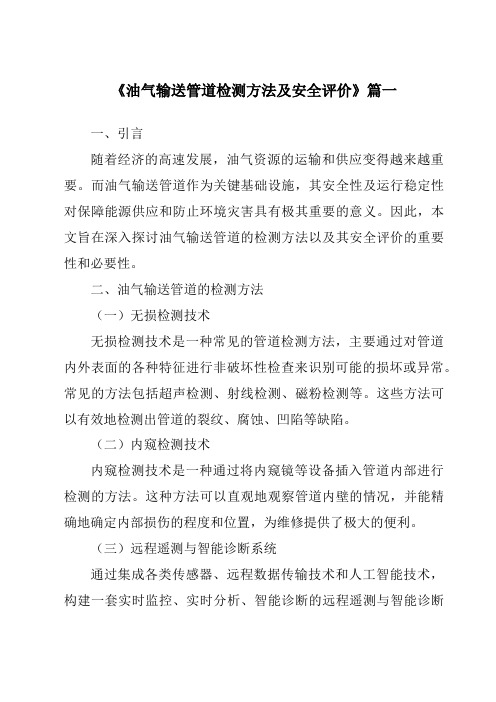
《油气输送管道检测方法及安全评价》篇一一、引言随着经济的高速发展,油气资源的运输和供应变得越来越重要。
而油气输送管道作为关键基础设施,其安全性及运行稳定性对保障能源供应和防止环境灾害具有极其重要的意义。
因此,本文旨在深入探讨油气输送管道的检测方法以及其安全评价的重要性和必要性。
二、油气输送管道的检测方法(一)无损检测技术无损检测技术是一种常见的管道检测方法,主要通过对管道内外表面的各种特征进行非破坏性检查来识别可能的损坏或异常。
常见的方法包括超声检测、射线检测、磁粉检测等。
这些方法可以有效地检测出管道的裂纹、腐蚀、凹陷等缺陷。
(二)内窥检测技术内窥检测技术是一种通过将内窥镜等设备插入管道内部进行检测的方法。
这种方法可以直观地观察管道内壁的情况,并能精确地确定内部损伤的程度和位置,为维修提供了极大的便利。
(三)远程遥测与智能诊断系统通过集成各类传感器、远程数据传输技术和人工智能技术,构建一套实时监控、实时分析、智能诊断的远程遥测与智能诊断系统。
该系统可以实时监测管道的运行状态,及时发现异常情况并给出预警,为管道的安全运行提供了有力保障。
三、油气输送管道的安全评价(一)风险评估风险评估是安全评价的重要环节,主要是通过识别和评估可能存在的危险源、事件及后果,来确定其安全风险等级。
风险评估过程中需综合考虑管道的物理性质、化学性质、运行环境、设备情况等因素。
(二)完整性评价完整性评价主要针对管道的结构和功能进行评价。
其主要是通过对管道进行检测,包括前面所提及的几种检测方法,综合评估管道的结构完整性、防腐保护、内外壁腐蚀等指标。
这种评价能够及时发现问题并进行处理,对提高管道的运行效率和安全性有着至关重要的作用。
(三)综合安全评价综合安全评价是对整个油气输送系统进行全面评价的过程。
其包括了风险评估和完整性评价的所有环节,同时还包括对管理和操作的评估。
该评价的目的是确定整个系统的安全水平,并为改进措施提供依据。
油气管道内检测技术

港口科技•中国港口协会科学技术奖优秀成果油气管道内检测技术毕建阳(烟台港集团有限公司,山东烟台264000)摘要:为减缓油气管道腐蚀,保证长输管道运输安全,通过管道内检测技术进行检测,并记录管体变形和磁场变化,转化为可视图像。
根据检测图像,确认管壁实际情况,并以此制定管道维修计划,提高查找管道薄弱点效率和修复效率。
关键词:油气管道;内检测技术;漏磁检测;几何变形检测0引言烟淄输油管道是烟台港液化油品储运体系的重要组成部分之一,全长约540km,起点为烟台港西港区,途经烟台、青岛、潍坊、淄博、东营、滨州等6个地级市,其主要功能是将港口接卸的油品输送至上述各地炼油厂,是连结上游油品贸易商和下游用户的纽带,与港口是一体化工程,相互依托。
烟淄输油管道依托烟台港西港区3个5万~10万吨级液化油品码头和30万吨级原油码头,可充分发挥烟台港西港区深水码头的优势,使港口液化油品的直接腹地向内陆延伸,打造一条全新的能源物流通道,形成码头接卸、保税仓储、管道输送构成的综合物流体系。
该管道材质为钢管,建设期近5a,由于建设周期长,穿越地区地形复杂,野外环境条件恶劣,施工难度较大,地下管道难免会产生各类腐蚀。
管道受到腐蚀后,管道壁厚度下降,将导致管道最大承压能力下降。
在不知情的情况下,若仍按照管道设计运行压力继续运行,极易导致管道破裂,输送介质泄漏,发生安全事故,带来经济损失和环境污染,造成较严重的社会影响。
因此,如何经济、有效、准确地评估地下钢质管道的现有状态并准确查找管道薄弱点,是必须解决的问题。
1管道检测常规技术为达到对管道状况有全面准确的掌握,防止管道事故的发生,长期以来行业内研究开发许多方法和技术,管道检测水平不断提高。
国内早期采用水压试验方法对管道进行检测,该方法只能证明水压试验时管道哪些部分不能承受试验压力.并不能提供管道的详细信息,而且,水压试验需要停止输送进行试验,检测成本较大。
利用检测器进行检测,是在不停输的情况下检测管道状况,不仅成本低而且可靠性高。
油气管道无损检测技术

油气管道无损检测技术管道作为大量输送石油、气体等能源的安全经济的运输手段,在世界各地得到了广泛应用,为了保障油气管道安全运行,延长使用寿命,应对其定期进行检测,以便发现问题,采取措施。
一、管道元件的无损检测(一)管道用钢管的检测埋地管道用管材包括无缝钢管和焊接钢管。
对于无缝钢管采用液浸法或接触法超声波检测主要来发现纵向缺陷。
液浸法使用线聚焦或点聚焦探头,接触法使用与钢管表面吻合良好的斜探头或聚焦斜探头。
所有类型的金属管材都可采用涡流方法来检测它们的表面和近表面缺陷。
对于焊接钢管,焊缝采用射线抽查或100 %检测,对于100 %检测,通常采用X射线实时成像检测技术。
(二)管道用螺栓件对于直径> 50 mm 的钢螺栓件需采用超声来检测螺栓杆内存在的冶金缺陷。
超声检测采用单晶直探头或双晶直探头的纵波检测方法。
二、管道施工过程中的无损检测(一)各种无损检测方法在焊管生产中的配置国外在生产中常规的主要无损检测配置如下图一中的A、B、C、E、F、G、H工序。
我国目前生产中的检测配置主要岗位如下图中的A、C、D、E、F、G、H工序。
图一大口径埋弧焊街钢管生产无损检测岗位配置(二)超声检测全自动超声检测技术目前在国外已被大量应用于长输管线的环焊缝检测,与传统手动超声检测和射线检测相比,其在检测速度、缺陷定量准确性、减少环境污染和降低作业强度等方面有着明显的优越性。
全自动相控阵超声检测系统采用区域划分方法,将焊缝分成垂直方向上的若干个区,再由电子系统控制相控阵探头对其进行分区扫查,检测结果以双门带状图的形式显示,再辅以TOFD (衍射时差法)和B扫描功能,对焊缝内部存在的缺陷进行分析和判断。
全自动超声波现场检测时情况复杂,尤其是轨道位置安放的精确度、试块的校准效果、现场扫查温度等因素会对检测结果产生强烈的影响,因此对检测结果的评判需要对多方面情况进行综合考虑,收集各种信息,才能减少失误。
(三)射线检测射线检测一般使用X 射线周向曝光机或γ射线源,用管道内爬行器将射线源送入管道内部环焊缝的位置,从外部采用胶片一次曝光,但胶片处理和评价需要较长的时间,往往影响管道施工的进度,因此,近年来国内外均开发出专门用于管道环焊缝检测的X 射线实时成像检测设备。
油气管道无损检测技术的应用
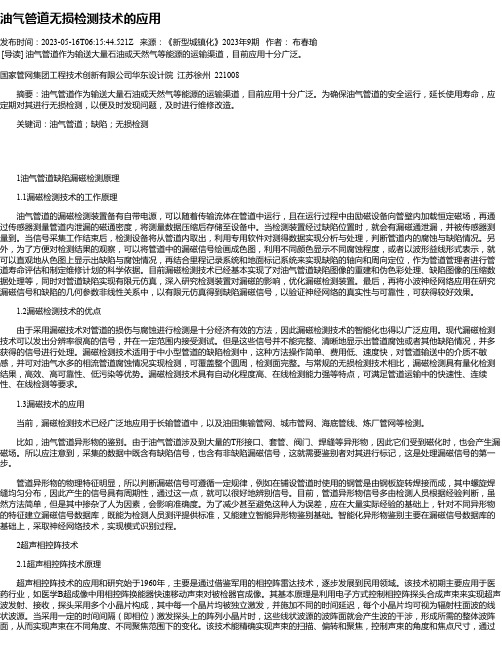
油气管道无损检测技术的应用发布时间:2023-05-16T06:15:44.521Z 来源:《新型城镇化》2023年9期作者:布春瑜[导读] 油气管道作为输送大量石油或天然气等能源的运输渠道,目前应用十分广泛。
国家管网集团工程技术创新有限公司华东设计院江苏徐州 221008摘要:油气管道作为输送大量石油或天然气等能源的运输渠道,目前应用十分广泛。
为确保油气管道的安全运行,延长使用寿命,应定期对其进行无损检测,以便及时发现问题,及时进行维修改造。
关键词:油气管道;缺陷;无损检测1油气管道缺陷漏磁检测原理1.1漏磁检测技术的工作原理油气管道的漏磁检测装置备有自带电源,可以随着传输流体在管道中运行,且在运行过程中由励磁设备向管壁内加载恒定磁场,再通过传感器测量管道内泄漏的磁通密度,将测量数据压缩后存储至设备中。
当检测装置经过缺陷位置时,就会有漏磁通泄漏,并被传感器测量到。
当信号采集工作结束后,检测设备将从管道内取出,利用专用软件对测得数据实现分析与处理,判断管道内的腐蚀与缺陷情况。
另外,为了方便对检测结果的观察,可以将管道中的漏磁信号绘画成色图,利用不同颜色显示不同腐蚀程度,或者以波形益线形式表示,就可以直观地从色图上显示出缺陷与腐蚀情况,再结合里程记录系统和地面标记系统来实现缺陷的轴向和周向定位,作为管道管理者进行管道寿命评估和制定维修计划的科学依据。
目前漏磁检测技术已经基本实现了对油气管道缺陷图像的重建和伪色彩处理、缺陷图像的压缩数据处理等,同时对管道缺陷实现有限元仿真,深入研究检测装置对漏磁的影响,优化漏磁检测装置。
最后,再将小波神经网络应用在研究漏磁信号和缺陷的几何参数非线性关系中,以有限元仿真得到缺陷漏磁信号,以验证神经网络的真实性与可靠性,可获得较好效果。
1.2漏磁检测技术的优点由于采用漏磁技术对管道的损伤与腐蚀进行检测是十分经济有效的方法,因此漏磁检测技术的智能化也得以广泛应用。
现代漏磁检测技术可以发出分辨率很高的信号,并在一定范围内接受测试。
油气管道内检测技术现状及发展趋势

油气管道内检测技术现状及发展趋势摘要:由于油气管道的运行,产生的腐蚀程度和管道的变形,需要通过管道的内检测技术了解管道结构的内部情况。
检测管道可以通过检测技术确定管道情况,并在检测过程中进行必要的监控。
记录管道管状形式,磁场的变化以图像形式呈现。
油气管道检测工作人员还可以增加限定管道的实际位置,根据问题提出合理的维护计划,确保油气运输管道结构满足安全性和可行性的运行效果。
关键词:油气管道;检测新技术;应用分析1油气管道内检测技术现状1.1超声波检测超声波检测主要运用超声波来扫描油气管道内的破损、腐蚀以及缺陷,并对其进行有效定位,从而对油气管道运行现状与将来运行情况进行更好、更精准的判断与预判。
超声波检测的效果比较直接、高效,具有极小的检测误差,在油气管道检测领域应用的范围非常广泛且普遍。
与此同时,通过对超声波脉冲反射原理的应用,能够对油气管道管壁腐蚀后的厚度进行测量,该方法具有较高的检测精度、较广的检测范围,能够对管道缺陷部位进行更好的定位,检测的数据较为简单且不用反复校验,其在油气管道最大允许输送压力方面计算数据的检测非常适用,且该检测数据能够为油气管道维修方案的制定、使用期限的测量提供很大的帮助和参考。
同时超声波检测对于管壁厚、直径大的油气管道的检测也比较适用,对于油气管道内的杂质、管道缺陷以及管道应力腐蚀破裂有着精准的检测效果。
因此,在国内外应用频率最高、范围最广泛、结果最精准、发展最快的检测技术就是超声波检测法。
除此之外,超声波检测技术在管道检测过程中也会有一些局限和不足存在,如检测探讨和管壁之间需要水或者油等声波传播介质以及连续的耦合剂作为辅助。
同时由于在空气中超声波衰减的速度非常快,如果将该技术应用到气体管道中实施检测,其会有很大的困难存在。
因而超声波检测技术的应用也要结合油气管道实际检测现状才能够发挥出其恰到好处的作用与价值。
1.2管道漏磁内检测技术管道漏磁内检测技术以铁磁性材料的高磁导率特性为基础,利用磁化器使管壁局部达到磁饱和,产生高磁通量。
油气管道内检测技术探讨

油气管道内检测技术探讨摘要:油气管道长期埋于地下,不可避免的受到土壤中酸、碱和盐侵蚀,造成管道防腐层受到外力影响产生损坏,造成管道腐蚀严重,进一步增加油气管道出现泄漏现象的几率,进而引发一系列中毒、火灾等生产事故,增加油气运输成本,降低企业综合效率,同时对周围自然环境和人民群众带来较大危害。
人们需要进一步研究油气管道腐蚀检测技术,提升技术应用的有效性,采用防腐措施,保证油气管道的安全可靠性。
本文对油气管道内检测技术进行分析,以供参考。
关键词:油气管道;内检测;技术探讨引言油气运输企业应当针对性地加强油气运输管道的防腐蚀性能,通过各种方法对管道腐蚀情况进行检测,及时发现管道中腐蚀严重的部位并进行修补,防止事故的发生,保证油气资源安全、稳定地供应。
1油气管道腐蚀检测与防护的必要性油气运输管道大多都埋藏在地下,地下的环境比较复杂,土壤中含有多种物质,其中酸、碱、盐等物质可能会对管道进行腐蚀。
管道一旦被腐蚀而产生破损情况,就有可能会导致油气发生泄漏,原油和天然气等都属于易燃易爆类物质,泄漏后极易引发火灾,造成不可挽回的后果,威胁到周边居住人员的生命财产安全。
有研究结果显示,油气管道在使用两年左右的时间就会发生比较严重的腐蚀,因此对油气管道腐蚀进行检测,并采取有效的防护手段是十分重要的。
及时检测能够在问题发生之前就对管道中腐蚀较严重的部分进行修补,防止油气泄漏的情况发生。
而有效的腐蚀防护措施也能够在一定程度上延长油气管道的使用寿命,一方面能够更高效地防止事故的发生,另一方面也能降低成本,提高企业的经济效益。
2油气管道防腐措施2.1内部防腐措施石油天然气包含较多化学物质,对管道不可避免的产生腐蚀现象,尤其其中含量最高的二氧化碳具有最强的腐蚀性。
因此,相关工作人员需要分析二氧化碳的腐蚀原因,制定相应的防腐措施,在管道设计过程中安装腐蚀监控系统,实时观察管道是否能够承受住当前的腐蚀程度,结合监控信息和数据应用相关防护措施,保证油气管道的安全性。
- 1、下载文档前请自行甄别文档内容的完整性,平台不提供额外的编辑、内容补充、找答案等附加服务。
- 2、"仅部分预览"的文档,不可在线预览部分如存在完整性等问题,可反馈申请退款(可完整预览的文档不适用该条件!)。
- 3、如文档侵犯您的权益,请联系客服反馈,我们会尽快为您处理(人工客服工作时间:9:00-18:30)。
油气管道内检测新技术举例
摘要管道检测技术是完整性的一部分,也是获取管道有关信息的最佳手段。
管道检测可以监测管道受到的危害或潜在危害,在管道未发生事故前进行有计划的修理,可以避免大量的不必要维修,节约资金,在管道的日常维护中占有非常重要的地位。
本文主要针对管道检测技术中的常用的几种内检测技术作了简要的介绍,并指出了各种技术的要点。
关键词:管道内检测新技术
1.内检测器的分类
管道是输送危险液体和气体最为安全有效的方式。
但随着时间的推移和周围环境的变化,会出现缺陷,也会导致事故的发生。
管道中可以被检测到的缺陷可以分为三个主要类型:
①几何形状异常(凹陷、椭圆变形、位移等);
②金属损失(疲劳、划伤等);
③裂纹(疲劳裂纹、应力腐蚀开裂等)。
管道内检测技术通过装有无损检测设备及数据采集、处理和存储系统的智能清管器在管道中运行,完成对管体的逐级扫描,达到对缺陷大小、位臵的检测目的。
针对上述三种缺陷类型,各大检测专业公司都根据市场和用户的需要研发了多种检测器,并不断更新换代。
内检测器按其功能可分为用于检测管道几何形状异常的变形检测器,用于检测管道金属损失的金属损失检测器,用于裂纹、应力腐蚀开裂检测的裂纹检测器。
2.几何形状异常的检测技术
管道几何形状的异常多因受到外部机械力或焊接残余应力等原因造成,通过使用适当的检测装臵可以检测各种原因造成的、影响管道有效内径的几何异常现象并确定其程度和位臵。
测径器是用于检测、定位和测量管壁几何形状异常的大小。
正常的管线,应当有一个圆环形横断面。
在管道铺设过程或长期运行中,第三方的干扰可以造成
凹陷。
合格的测经器应可对任何管段横断面的临界变化进行检测并确定大小,是进行管道金属损失或裂纹内检测之前非常重要的一步。
常用的测径器使用一定排列的机械抓手或有机械抓手的辐射架。
机械抓手压着管道内壁并会因横断面的任何变化引起偏移。
这些偏移可能是由于一个凹陷、偏圆、褶皱或附着在管壁上的碎屑引起的。
捕捉到的偏移信号被转换为电子信号存储到机载的存储器上。
讲一次运行后的数据取出并使用合适的软件加以分析和显示,从而确定那些可影响到管道完整性的异常点。
目前,市场上的测径器,提供的被测管径范围从100-1500mm不等,其灵敏度通常为管段直径的0.2%~1%,精度大约为0. 1%-2%。
3.金属损失检测技术
漏磁(MFL)技术因其可检测出腐蚀或擦伤造成的管道金属损失缺陷,甚至能够检测到那些不足以威胁管道结构完整性的小缺陷(硬斑点、毛刺、结疤、夹杂物和各种其他异常和缺陷),偶尔也可检测到裂纹缺陷、凹痕和起皱。
漏磁技术应用相对较为简单,对检测环境的要求不高,具有很高的可信度,而且可兼用于输油和输气管道,所以,这种技术被广泛应用并在不断的发展。
对于很浅、长且窄的金属损失缺陷,MFL信号就难以检测出来。
检测精度也受多种因素的影响。
在对管道进行检测时,要求管壁达到完全磁性饱和,因此测试精度与管壁厚度有关,厚度越大,精度越低,其使用的壁厚范围通常在12mm 以下。
另外,检测器在管道中的运行速度也可影响检测结果的准确性。
有关研究机构正在研究其速度控制技术,指在不影响正常输量的前提下提高检测的准确性。
近来,美国哥伦比亚输气公司结合现场经验及有关研究发现并已证实了MFL 数据的采集受管内废杂物的影响,影响有三个:损坏设备、速度偏差、检测器脱离管壁。
设备损坏、脱离管壁和速度过高的现象可同时发生,也可互不相干,可对磁通泄露数据和结果分析产生很多影响。
这些影响可能导致缺陷几何形状的确定及位臵估算错误,也可能失去探测腐蚀和管道特征的能力。
为了确保能获得良好的检测结果,在管道内检测之前,进行清管作业是极为重要的,尤其对于含蜡高的原油管线、所有含铁锈的流体管线、含极细粉尘的干燥气管线等更为关键。
通过适当地维护和初步清理可减少或消除废杂物的影响。
目前,对废杂物如何影响MFL数据的理解仍处于初级阶段,有待继续研究。
常规MFL检测器的磁铁方向是沿管道的主轴方向,缺陷产生的磁通扰动较小,因此在探测轴向缺陷方面的精度较差。
通过把磁铁方向或磁力线方向调整为绕管道轴向,增大缺陷对此通的切面积,可增加对轴向缺陷的检测精度。
表1.MFL检测器规格及精度
4.裂纹检测技术
裂纹可能有管材的缺陷、材料空隙、夹杂物或者凹陷、局部脆性区域及应力、疲劳、腐蚀等造成。
裂纹类缺陷是管道中存在的最为严重的缺陷,对管道的威胁极大。
最适于检测裂纹的技术是超声波方法。
经过管壁的超声波受到来自管壁的各
种不同情况的影响,从而可以测量并描绘出管道的现有状况。
超声波检测器的主要优点是能够提供对管壁的定量检测。
其提供的内检测数据精度高和臵信度高。
缺点是需要耦合剂,应用于输气管道时较复杂。
GE-PII公司通过使用一个内臵有压电发生器的充液轮与管壁紧密接触,使所充液体提供一个良好的耦合机制,更好的传输和接收信号。
这项技术以应用于PII公司开发的弹性波裂纹检测器上。
英国BG公司采用了以弹性剪切波为基础的裂纹检测仪器在北美(加拿大IPL 和美国 Colonial)的油气管道上成功的检测出了管道裂纹。
PII公司研发的UltraScan WM和UltraScan CD牌号的超声波检测装臵,可对断面窄和长距离不变的内部沟蚀提供比漏磁方法更精确的测量,可检测到管壁中间的缺陷,对于管壁厚度变化大的管线和管壁厚度超出漏磁设备的规格时,在UltraScan WM的限度内能很好的适应需要。
表2. UltraScan WM检测器的技术规格
UltraScan CD检测器使用超声横波,以使其在管壁内传播角度为45°,如果超声波遇到一个裂纹就会返回传感器。
这就能以高灵敏度和精确性检测内部或外部纵向的裂纹。
通过检测声音传播的时间和折射波的振幅,缺陷的位臵和大小就能被计算出来。
表3. UltraScan CD 检测器的技术规格
多达896个传感器装在可伸缩的聚氨酯传感器携带滑架上,当检测器通过管道时,持续向管壁内“开火”。
这保证每个裂纹都被许多传感器检测到。
为了进一步提高可靠性,对每节管壁都重复测量两次,一次顺时针方向,另一次逆时针方向。
目前,UltraScan CD是可靠地检测各种最浅的和最窄的裂纹以及细微的应力腐蚀开裂(SCC)的唯一的检测器。
检测器检测到的缺陷位臵和大小已经为200多次开挖证明,而且测量到的所有严重开裂都被证实。
在所有开挖中没有错误信号,而且所有被预测为不严重的裂纹,也被证实确实如此。
德国TUV公司以确定将UltraScan WM 和UltraScan CD 检测的组合,作为替代管道液压试验的选择。
此外,一种最新的超声波检测技术即电磁声波传感检测技术(EMAT)正在研发中,该技术的最大优点就是可借助电子声波传感器,使超声波能在一种弹性导电介质中得到激励,而不需要机械接触或液体耦合。
该技术利用电磁原理,以新的传感器代替了超声波检测技术中传统的压电传感器。
当电磁传感器在管壁上激
发出超声波时,波的传播采用以管壁内、外表面作为“波导器”的方式进行,当管壁是均匀的,波沿管壁传播只会受到衰减作用,当管壁上有异常出现时,在异常边界处的声阻抗的突变产生波的反射、折射和漫反射,接收到的波形就会发生明显的改变。
由于基于电磁声波传感器的超声波检测最重要的特征是不需要液体耦合剂来确保其工作性能,因此该技术可应用于输气管道,是替代漏磁通检测的有效方法。
然而,这种检测技术也同样存在着不足,检测器需距离被检测物体表面1mm,传递超声波能力相对较低。
正是由于这个原因,在许多情况下是通过电磁声来确定其动态范围,而不能使用高频。
PII公司研发的EMAT检测器在914.4mm 和609.6mm输气管道上试运行后,目前已经通过了商业运行。
超声波技术虽已成功的用于管道的缺陷检测,但在用于输气管道上仍有大量的工作要做。
例如,研究如何利用EMAT和垂直于水平剪切波的方法充分的诠释管道的缺陷,正确的选择波的模式和传感器的定位方法充分捕获管道的裂纹缺陷。
将裂纹缺陷模式化,加强实验确认使EMAT设计的有效性最大化。