浅析锌电积过程节能措施
锌电积一种“烧板”的原因分析及处理

锌电积一种“烧板”的原因分析及处理文章阐述一种锌电积“烧板”的特征,并详细分析“烧板”产生的原因,结合生产实际提出处理措施。
标签:锌电积;有机物;烧板前言锌电解沉积是湿法炼锌系统的末端,是将净化后的硫酸锌溶液(新液)送入电解槽内通以直流电在阴极上析出金属锌(阴极锌),通过下面反应式进行反应:ZnSO4+H2O=Zn↓+H2SO4+1/2O2↑当电解溶液内存在杂质时析出的阴极锌会在杂质作用下重新溶解到液体内,并放出氢气,我们称之为阴极锌的返溶,俗称“烧板”。
[1]电积过程大面积”烧板”使得阴极锌产量下降,直流电单耗升高,大量电能损失,资源浪费,也使生产成本增加。
因此,需要严加控制“烧板”发生。
1 “烧板”发生及其特征2014年下半年净化工序更改除钴工艺,由原来的锌粉两段高温锑盐除钴更改为β-萘酚除钴工艺。
除钴工艺的优化大幅降低了锌粉和蒸汽消耗,按年产10万吨锌计算,年生产成本节约近1000万。
但新工艺运行以来,电解工序先后出现4次阴极锌大面积“烧板”事故,“烧板”时间一般持续3-5天,最长可达半月之久。
这几次发生的“烧板”事故与过去都不同。
表现为阴极锌大面积针眼,背面发黑,透酸严重,电解槽内出现大量白色泡沫且厂房内酸雾很浓。
阴极锌的边缘和中间出现局部返溶。
在阴极锌板面的中间出现3-5厘米不等的窟窿,板面出现反复析锌,表面形成年轮状。
在未返溶部分,致密度非常好,板面光亮,熔铸直产率也比较高。
2 原因分析(1)由于烧板的初期存在针眼和透酸,因此,曾怀疑常规元素超标导致,于是对新液和废液内的常规元素进行分析。
从表1可以看出常规元素除氯根外都在合格范围内,特别是对电解影响比较大的砷、锑、锗等含量都比较低,氯根基本不会对阴极锌板面产生影响,因此,可以排出常规元素影响。
(2)排除常规元素后,我们将关注的重点落在系统内添加的有机物上。
且这几次的“烧板”与资料内介绍的有机物烧板特征相似,如阴极锌下部和边缘有返溶现象,现场酸雾突起,槽内沸腾泛白等[2]。
浅析热镀锌退火炉节能措施和发展方向
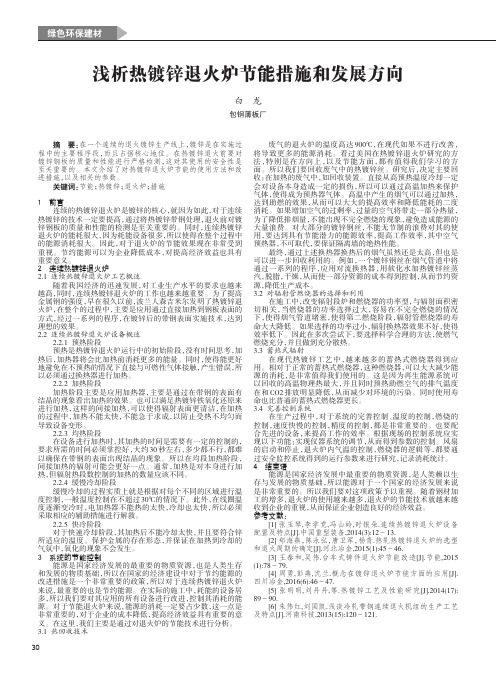
浅析热镀锌退火炉节能措施和发展方向白龙包钢薄板厂摘要:在一个连续的退火镀锌生产线上,镀锌是在实施过程中的主要程序段,而且占据核心地位。
在热镀锌退火前要对镀锌钢板的质量和性能进行严格检测,这对其使用的安全性是至关重要的。
本文介绍了对热镀锌退火炉节能的使用方法和改进措施,以及相关的参数。
关键词:节能;热镀锌;退火炉;措施1前言连续的热镀锌退火炉是镀锌的核心,就因为如此,对于连续热镀锌的技术一定要提高,通过将热镀锌带钢处理,退火前对镀锌钢板的质量和性能的检测是至关重要的。
同时,连续热镀锌退火炉的能耗很大,因为耗能设备很多,所以使得在整个过程中的能源消耗很大。
因此,对于退火炉的节能效果现在非常受到重视。
节约能源可以为企业降低成本,对提高经济效益也具有重要意义。
2连续热镀锌退火炉2.1连续热镀锌退火炉工艺概述随着我国经济的迅速发展,对工业生产水平的要求也越来越高,同时,连续热镀锌退火炉的工作也越来越重要。
为了提高金属钢的强度,早在很久以前,波兰人森吉米尔发明了热镀锌退火炉,在整个的过程中,主要是应用通过直接加热到钢板表面的方式,经过一系列的程序,在镀锌后的带钢表面实施技术,达到理想的效果。
2.2连续热镀锌退火炉设备概述2.2.1预热阶段预热是热镀锌退火炉运行中的初始阶段,没有时间思考,加热后,加热器将会比加热前消耗更多的能量。
同时,使得能更好地避免在不预热的情况下直接与可燃性气体接触,产生错误,所以必须通过换热器进行加热。
2.2.2加热阶段加热阶段主要是应用加热器,主要是通过在带钢的表面有结晶的现象看出加热的效果。
也可以满足热镀锌铁氧化还原来进行加热,这样的间接加热,可以使得辐射表面更清洁,在加热的过程中,加热不能太快,不能急于求成,以防止受热不均匀而导致设备变形。
2.2.3均热阶段在设备进行加热时,其加热的时间是需要有一定的控制的,要求所需的时间必须掌控好,大约30秒左右,多少都不行,都难以确保在带钢的表面出现结晶的现象。
热镀锌生产线上的成本控制和节能减排的方法

带钢热镀锌线生产成本的控制和节能减排的方法案例1 概述目前国外带钢连续热镀锌生产线有600余条,生产能力约为1.2亿t/a;我国宽带钢连续热镀锌线已发展到195条,年生产能力达到3950万[1]。
可见,热镀锌板的市场竞争相当激烈,而竞争的焦点是产品质量和生产成本。
据作者多年的实践经验,现提出几项有效控制带钢热镀锌线生产成本的措施。
2 一次性投入成本的控制带钢连续热镀锌线建设期一次性投入成本的有效控制,应注意以下几方面:(1)应搞好市场调研,确立市场定位。
(2)应根据市场定位确定产品大纲,选择规格品种。
(3)根据所生产的品种规格,确定生产工艺和设备组成。
(4)应建设经济型机组。
①建设专业化机组而不建一机多用机组,即不建一机双锅线,既生产热镀锌板又生产铝锌硅板;既生产大锌花板又生产无锌花板;既生产纯锌层板又生产铁锌合金层板,这种机组不经济;不建厚度跨度太大的热镀锌机组,如可生产厚度规格为0.2~2.Omm、0.3~3.Omm等镀锌板;不建冷轧板退火和热镀锌线兼容机组;不建冷轧板和热轧酸洗板兼容热镀锌机组。
②根据企业经济实力和产品定位选择机组年产量。
工艺段速度为80m/min时,年产量应达到10万t,产量偏低不经济;工艺段速度为120m/min时,年产量为15万t,卧式炉长应增加30m,比年产10万t的机组总投资会增加400万元,但产量可增加5万t,是经济型机组;工艺段速度为150m/min,年产量为20万t,卧式炉应改为立式炉,年产量可增加5万t,但总投资要增加1500万元。
由此可见,年产10、15、20万t的机组中,最经济型机组是工艺段速度为120m/min,年产15万t的机型。
但也不能一概而论,年产20万t机组能否建,应具体情况具体分析,主要由产品大纲决定,如生产汽车板、高级家电外板等高附加值产品,利润空间较大,即使多投入1000多万元,也能很快收回投资。
③完整的冷轧深加工产业链应具备冷轧、镀锌、彩涂3道工序。
炼锌过程节能控制文献综述
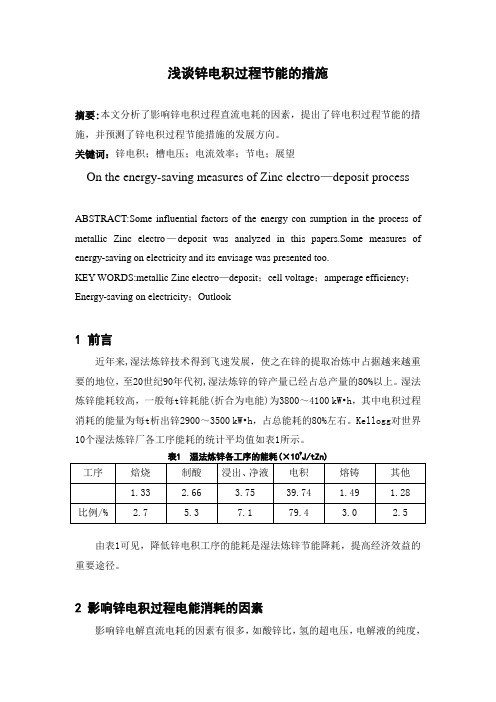
浅谈锌电积过程节能的措施摘要:本文分析了影响锌电积过程直流电耗的因素,提出了锌电积过程节能的措施,并预测了锌电积过程节能措施的发展方向。
关键词:锌电积;槽电压;电流效率;节电;展望On the energy-saving measures of Zinc electro—deposit processABSTRACT:Some influential factors of the energy con sumption in the process of metallic Zinc electro—deposit was analyzed in this papers.Some measures of energy-saving on electricity and its envisage was presented too.KEY WORDS:metallic Zinc electro—deposit;cell voltage;amperage efficiency;Energy-saving on electricity;Outlook1 前言近年来,湿法炼锌技术得到飞速发展,使之在锌的提取冶炼中占据越来越重要的地位,至20世纪90年代初,湿法炼锌的锌产量已经占总产量的80%以上。
湿法炼锌能耗较高,一般每t锌耗能(折合为电能)为3800~4100 kW•h,其中电积过程消耗的能量为每t析出锌2900~3500 kW•h,占总能耗的80%左右。
Kellogg对世界10个湿法炼锌厂各工序能耗的统计平均值如表1所示。
表1 湿法炼锌各工序的能耗(×109J/tZn)工序焙烧制酸浸出、净液电积熔铸其他1.332.663.75 39.74 1.49 1.28 比例/% 2.7 5.3 7.1 79.4 3.0 2.5由表1可见,降低锌电积工序的能耗是湿法炼锌节能降耗,提高经济效益的重要途径。
降低电积锌直流电耗分析

降低电积锌直流电耗分析传统的湿法炼锌过程中,电积能耗直接影响冶炼的生产成本。
锌电积直流电耗受各种因素影响,联系当前生产实践分析了这些影响因素,并提出了相应的解决方法及节电措施。
湿法炼锌是在低温(25-250℃)及水溶液中进行的冶金过程。
目前,世界上锌产量的80%以上都是采用湿法工艺生产的。
在湿法炼锌工艺中,电积是主要的耗电工序,其电耗占整个工艺能耗的70%以上,因此,降低电积电耗,对于湿法炼锌厂降低生产成本有着积极的意义。
锌电积电耗锌电积电耗主要包括交流电耗和直流电耗2部分。
交流电耗主要发生在循环酸泵、冷却塔风机、掏槽真空泵等机械设备上,其在锌电积系统中占总能耗的比例仅为3%-4%,因此,电积电耗以直流电耗为主。
在锌电积过程中,析出1t阴极锌需要的电能为:W=U×103/Q·η(1)式中W-直流电耗,kW·h/t;U-槽电压V,η-电流效率%,q-锌的电化当量, 1.219.5g。
A·h)。
从。
1)式可以看出,锌电积电耗与槽电压成正比,与电流效率成反比。
因此,要降低锌电积电耗,必须降低槽电压或提高电流效率。
锌电积的节能措施降低槽电压槽电压对锌电积的电能消耗有重要影响。
电积过程中槽电压的情况见表1由表1可以看出,一个电解槽的电压降(U)由硫酸锌分解电压(U分)。
电积液电阻电压降(U液)。
阴、阳极电阻电压降(U极)。
接触点上电压降(U 接)。
阳极泥电压降(U泥)阳极泥等5项组成即:U=U分+U液+U极+U接+U泥。
(2)式(2)表明,通过降低分解电压和电阻电压,可以降低槽电压。
降低硫酸锌的分解电压硫酸锌分解电压由理论分解电压。
E理)、阴极超电压(η阴)和阳极超电压(η阳)组成,如下式:U=)()(1303.2)([)]()(1303.2)0([222Zn Zn ga FRT Zn E O OH ga F RT E o o ηη++-+++=)()()](1303.2)([)](1303.2)([222ZN O Zn ga FRT Zn E OH ga F RT O E o o ηη+++-++。
锌电积过程中直流电单耗较高的原因分析与处理措施

锌电积过程中直流电单耗较高的原因分析与处理措施摘要:现代锌冶金的生产方法主要为湿法炼锌。
湿法炼锌是对ZnSO4和H2SO4的水溶液在通以直流电的作用下锌由溶液析出至阴极板,获得电积锌。
湿法炼锌具有生产规模大、能耗相对较低、环保指标较好、自动化程度较高、有利于综合回收有价金属等优点而得到迅速发展。
湿法炼锌电解过程是电解液在直流电作用下析出锌的电化学反应过程,锌电解过程的电能消耗占整个湿法炼锌电能能耗的80%以上。
因此,降低直流电单耗刻不容缓,本文就锌电积氧压浸出工艺过程中电耗高的原因及降低电耗的措施作以综述。
关键词:锌电积;直流电单耗;阳极板;电效工厂采用锌电积氧压浸出工艺,主要生产工序包括:磨矿、氧压浸出、酸中和、压滤除铁、净化除杂、锌电积、成品铸型、硫回收、综合回收等。
锌电积采用3.2m2大极板,所用剥锌机、洗刷机、多功能行车等设备,自动化、智能化程度较高。
一、锌电积过程直流电单耗较高的原因分析:直流电单耗是指:每析出一吨锌所用的直流电量;锌电积过程直流电的作用主要用于析出锌,有一小部分转化为热能,因此要降低直流电单耗就要尽可能的使直流电作用于析出锌,减少转化为热能的部分。
(1)建立生产车间时,厂内变电所供电机组与电积车间电解槽之间距离较远,造成电解槽供电母排距离较长。
在酸性条件下母排极易产生结晶,造成一部分电能在输送过程转化为热能而有所损耗。
(2)槽内极板状况:如果在装槽时阴极板弯板、带锌角板、绝缘条脱落板进入槽内,阴阳极接触短路。
在损坏极板的情况下电能转化为热能,增加直流电单耗。
(3)电解槽槽壁结晶主要成分为CaSO4、MgSO4,钙镁化合物在槽内温度较低的情况下极易析出附在槽壁形成结晶、电解槽漏电等原因也会造成直流电单耗较高。
(4)由于新液纯度不够,造成电解槽烧板现象发生,电解槽不能平稳运行,影响析出锌产量,进而增加直流电单耗。
(5)电解液含锌较高(160g/l-165g/l),由于新液不足等原因电流密度较低的情况下,电解液电阻值较大,电效较低。
浅析锌电积过程节能措施
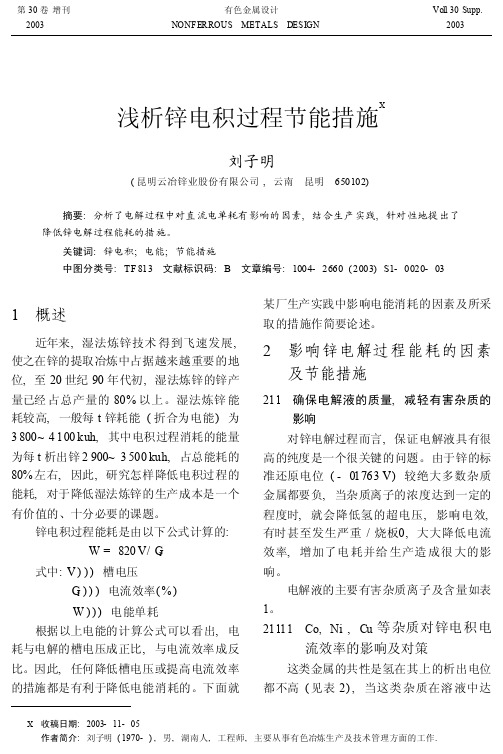
浅析锌电积过程节能措施X刘子明(昆明云冶锌业股份有限公司,云南昆明650102)摘要:分析了电解过程中对直流电单耗有影响的因素,结合生产实践,针对性地提出了降低锌电解过程能耗的措施。
关键词:锌电积;电能;节能措施中图分类号:TF813文献标识码:B文章编号:1004-2660(2003)S1-0020-031概述近年来,湿法炼锌技术得到飞速发展,使之在锌的提取冶炼中占据越来越重要的地位,至20世纪90年代初,湿法炼锌的锌产量已经占总产量的80%以上。
湿法炼锌能耗较高,一般每t锌耗能(折合为电能)为3800~4100kuh,其中电积过程消耗的能量为每t析出锌2900~3500kuh,占总能耗的80%左右,因此,研究怎样降低电积过程的能耗,对于降低湿法炼锌的生产成本是一个有价值的、十分必要的课题。
锌电积过程能耗是由以下公式计算的:W=820V/G i式中:V)))槽电压G i)))电流效率(%)W)))电能单耗根据以上电能的计算公式可以看出,电耗与电解的槽电压成正比,与电流效率成反比。
因此,任何降低槽电压或提高电流效率的措施都是有利于降低电能消耗的。
下面就某厂生产实践中影响电能消耗的因素及所采取的措施作简要论述。
2影响锌电解过程能耗的因素及节能措施211确保电解液的质量,减轻有害杂质的影响对锌电解过程而言,保证电解液具有很高的纯度是一个很关键的问题。
由于锌的标准还原电位(-01763V)较绝大多数杂质金属都要负,当杂质离子的浓度达到一定的程度时,就会降低氢的超电压,影响电效,有时甚至发生严重/烧板0,大大降低电流效率,增加了电耗并给生产造成很大的影响。
电解液的主要有害杂质离子及含量如表1。
21111Co,Ni,Cu等杂质对锌电积电流效率的影响及对策这类金属的共性是氢在其上的析出电位都不高(见表2),当这类杂质在溶液中达第30卷增刊有色金属设计Vol130Supp. 2003NONFERROUS METALS DESIGN2003X收稿日期:2003-11-05作者简介:刘子明(1970-),男,湖南人,工程师,主要从事有色冶炼生产及技术管理方面的工作.到一定的浓度后,它们将优先于锌在阴极析出,由于氢的放电而使锌不能在这里沉积,且析出的杂质金属和锌组成微电池,在这种微电池中,由于锌的电位更负而发生溶解,给电解过程带来很大的干扰,严重时即产生所谓/烧板0,增加电解能耗。
降低湿法炼锌电积能耗、提高企业生存竞争能力材料

降低湿法炼锌电积能耗、提高企业生存竞争能力(白银有色集团股份有限公司西北铅锌冶炼厂)1 实施背景湿法炼锌是在低温及水溶液中进行的冶金过程。
目前,世界上锌产量的80%以上都是采用湿法工艺生产的。
主要包括精矿焙烧一浸出一中浸液净化一电积一阴极锌熔铸为主流。
据分析,湿法炼锌的总能耗为50.07GJ/t锌,各工序的能耗分配如表1所示:表1 湿法炼锌各工序的能耗能耗104J/tZn 1.33 2.66 3.75 39.74 1.49 1.28比例% 2.7 5.3 7.1 79.4 3.0 2.5 由表1可见,在湿法炼锌工艺中,电积是主要的耗能工序, 其能耗占整个工艺能耗的80%,占锌产品加工总成本的35%,约占电积工序生产成本的95%,因此,降低电积电耗, 是电解车间成本控制的长效技术攻关项目,是提高湿法炼锌厂经济效益的重要措施,也是衡量企业技术管理水平的重要标志,对于湿法炼锌厂降低生产成本有着积极的意义,对企业的生存发展有非常重要的作用。
白银有色集团股份有限公司西北铅锌冶炼厂(以下简称西北冶)是国家“七五”计划重点建设项目之一,厂区占地1平方公里,现有职工1703人。
锌系统采用焙烧—热酸浸出—黄钾铁矾全湿法炼锌工艺,1992年5月1日开车, 目前已超过设计能力, 年产电锌11 万t , 硫酸20 万t。
随着白银集团公司的不断发展和壮大,作为其主体冶炼厂之一的西北冶锌产量也将达到每年约12万t,随着铅锌厂后续技改的完成和产能的扩大,阴极锌的产量还将继续增加,达到23~25万吨的规模。
在国家加强对企业节能减排监管力度和白银公司“挖潜增效”的严格要求下,解决湿法炼锌电积电耗较高的技术难题是有效降低生产成本、保障企业生存的迫切需要。
2 项目概述西北冶2009年以前电积能耗高达3200kwh/tZn以上,随着2010年起多项降低锌电积能耗技术创新项目改造和实施,以及2011年起降低锌电积能耗技术攻关创新项目的大力开展,锌电积能耗取得重大突破,2011年跨越了3200kwh/tZn和3100kwh/tZn两个大关,达到3088kwh/tZn,但与国内外同行业先进水平相比仍有不小的差距;2012年采取诸多切实可行的技术及管理措施,继续深入开展降低锌电积能耗技术攻关创新项目,并取得明显的效果和较好的成绩,锌电积能耗指标逐年优化,2012年降至3065kwh/tZn,2013年降至3046kwh/tZn。
锌冶炼渣综合利用与节能减排

锌冶炼渣综合利用与节能减排摘要:随着社会经济的快速发展,金属冶炼行业越来越受到人们的关注,各种金属对人们的工作和生活都很重要;在锌冶炼过程中,锌渣的产生往往会造成一些环境污染;然而,尽管它具有很高的危害性,但可以作为一种重要的资源,针对这种情况,本文探讨了锌冶炼渣的综合利用和节能减排,以进一步促进我国金属冶炼行业的发展。
关键词:锌冶炼渣;综合利用;节能减排引言近年来,我国向世界供应的锌精矿和锌金属的数量不断增加,这也使我国成为锌生产大国,但在这一过程中,废渣不仅造成有价金属的严重损失,而且对周边居民的生活环境造成严重污染,数据显示,冶炼系统每生产10000吨锌,就会形成9600吨锌渣,导致锌的累积量达到数亿吨,因此,在炼锌过程中,我们不仅要充分利用锌渣,还要重视节能减排。
1.含锌冶炼渣危害含锌炉渣中含有锌、铅、钴、铜、镍等有价金属,含锌矿渣中的重金属元素具有持久毒性且迁移性、隐藏性和富集能力强,不易降解,如果长期堆积,伴随着雨水天气,土壤中的可溶元素随水从表面渗入土壤和水系,使堆场周围的土壤酸化、碱化,一些重金属在经过生物富集后通过食物链进入人体,很容易引起慢性中毒,对人体的生命造成危害。
2.含锌冶炼渣的来源锌是一种重要的有色金属,广泛应用于各个行业,中国锌矿石类型复杂,与澳大利亚和加拿大等其他国家相比,锌矿石质量较差,尽管近年来金属价格大幅下跌,有色金属价格波动较大,但我国锌产量的增长总体保持势头,然而,由于环境保护的影响,我国锌精矿的产量逐年下降;锌的各种生产工艺导致含锌渣的成分和性质不同,这使得含锌渣处理更加困难和昂贵,近年来,国家明确要求企业节能减排,发展低碳经济,导致废渣处理的经济效益低,所以大多数企业都会选择堆积的方式来处理含锌冶炼渣,废渣回收率低,浪费了宝贵的金属。
3.锌冶炼渣的综合利用3.1铅银渣铅和银渣是在锌焙烧的高酸性过程中产生的,铅、银渣中的主要元素为Zn、In、Ag、Pb、Cu等,回收这些高价金属的主要工艺为Ausmelt工艺和烟化挥发工艺,采用烟化挥发法处理废渣的成本较低,回收废热可提高高价值金属的产值,生产的固化渣对环境污染较小,可以销售,适合大多数公司进行废渣输送;但Ausmelt工艺中,铅、锌和高价金属的回收率较低;此外,烟化法不能从废渣中回收银和铜,因此在处理废渣时有必要考虑这两种方法的缺点。
湿法炼锌焙烧节能途径探讨
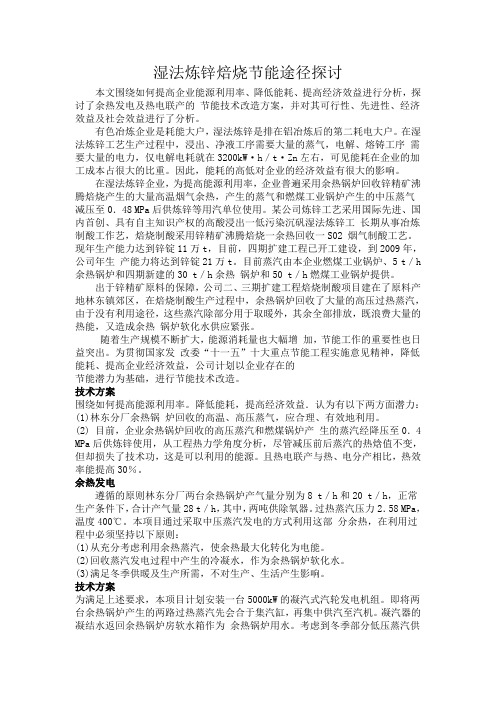
湿法炼锌焙烧节能途径探讨本文围绕如何提高企业能源利用率、降低能耗、提高经济效益进行分析,探讨了余热发电及热电联产的节能技术改造方案,并对其可行性、先进性、经济效益及社会效益进行了分析。
有色冶炼企业是耗能大户,湿法炼锌是排在铝冶炼后的第二耗电大户。
在湿法炼锌工艺生产过程中,浸出、净液工序需要大量的蒸气,电解、熔铸工序需要大量的电力,仅电解电耗就在3200kW·h/t·Zn左右,可见能耗在企业的加工成本占很大的比重。
因此,能耗的高低对企业的经济效益有很大的影响。
在湿法炼锌企业,为提高能源利用率,企业普遍采用余热锅炉回收锌精矿沸腾焙烧产生的大量高温烟气余热,产生的蒸气和燃煤工业锅炉产生的中压蒸气减压至0.48 MPa后供炼锌等用汽单位使用。
某公司炼锌工艺采用国际先进、国内首创、具有自主知识产权的高酸浸出一低污染沉矾湿法炼锌工长期从事冶炼制酸工作艺,焙烧制酸采用锌精矿沸腾焙烧一余热回收一S02 烟气制酸工艺。
现年生产能力达到锌锭11万t,目前,四期扩建工程已开工建设,到2009年,公司年生产能力将达到锌锭21万t。
目前蒸汽由本企业燃煤工业锅炉、5 t/h 余热锅炉和四期新建的30 t/h余热锅炉和50 t/h燃煤工业锅炉提供。
出于锌精矿原料的保障,公司二、三期扩建工程焙烧制酸项目建在了原料产地林东镇郊区,在焙烧制酸生产过程中,余热锅炉回收了大量的高压过热蒸汽,由于没有利用途径,这些蒸汽除部分用于取暖外,其余全部排放,既浪费大量的热能,又造成余热锅炉软化水供应紧张。
随着生产规模不断扩大,能源消耗量也大幅增加,节能工作的重要性也日益突出。
为贯彻国家发改委“十一五”十大重点节能工程实施意见精神,降低能耗、提高企业经济效益,公司计划以企业存在的节能潜力为基础,进行节能技术改造。
技术方案围绕如何提高能源利用率。
降低能耗,提高经济效益.认为有以下两方面潜力:(1)林东分厂余热锅炉回收的高温、高压蒸气,应合理、有效地利用。
锌电积的节电探讨

电压降-通常占槽电压的 678"7.随着电积时
间的延续-阳极表面上的泥层变厚-阳极泥电阻
增 加-因此必须定期清除.阳极泥的清理周期
+‘,对槽电压的影响如下式 L @’A
a? ’&’!(= :&:6P*‘
+6,
+6,式说明-阳极清扫周期 +天,越短-槽
电压越低.日本饭岛冶炼厂阳极清扫周期由 !!b
改为 *:b-槽电压降低 :&(:(# 以上-实现节电
= :&*5(6
+!,
式中LMDD 电导率-3STGU
N12JNO*34!DD 分 别 为 电 积 尾 液 中 锌 和 游 离 硫 酸 浓 度 - FSVU
NQFDD 电积液中镁浓度-FSVU
RDD 电积液温度-W .
由 +!,式不难看出-电积液的电导率 M 值-
随 着 电 积 液 中 12*= 浓 度JQF*= 等 杂 质 浓 度 的 增
;实 ?;理 = +<= =<> ,
+’,
锌电积的阴极超电压 +<> ,值甚小-仅为 :&:*8
:&:’#-因阳极超电压 +<= ,是氧在阳极上析出
所 引 起- 由 计 算 得 知 - @(A 其 值 占 阳 极 总 电 压 的
!6&"7-占槽电压的 *!&*7.故要使槽电压降低-
降低氧的超电压为重中之重.
选择适宜的阳极材料是降低氧的析出超电压
的 重要手段.锌电积的阳极一般采用 BCDEF合 金-其阳极电位比纯铅阳极的 低 6:G# 以上-且 随着电积时间的延长-其差值更大.生产上试用 的 BCDEFDHI合 金 阳 极 也 可 明 显 降 低 析 氧 的 超 电压-例如-使用 BCDEF+:&597,DHI+8 *7,阳极时-阳极电位比 BCDEF+(7,的低 (*: G#-而且腐蚀减少 . @*A /&/ 降低总电阻
科技成果——高电流密度锌电解节能技术

科技成果——高电流密度锌电解节能技术适用范围有色金属行业锌湿法冶金电解工序行业现状湿法炼锌产量占世界锌总产量的80%以上,目前国内锌电解多采用低酸低电流密度(300-400A/m2)生产。
低电流密度电解技术的锌电解工序能耗高,直流电耗约3250kWh/t锌,直流电耗对应的碳排放量为2.27tCO2/t锌。
2013年,我国精锌产量为530.2万t,按电解锌占80%计算,约生产电解锌424.2万t,电解锌直流电耗约为137.9亿kWh,排放量约960.9万tCO2。
降低锌电解工序能耗对于锌冶炼行业的节能具有重要作用。
目前该技术可实现节能量0.2万tce/a,减排约0.5万tCO2/a。
成果简介1、技术原理该技术围绕电解前端工序的电解液质量、电解槽结构及槽电压分布、极板类型结构及沉积机理、硅整流供电系统供电效率等方向,通过电解整流系统非同相逆并联谐波抑制技术、深度净化技术和ASEP 阳极板技术的集成创新应用,可实现谷电期按600-800A/m2高电流密度的生产常态化,改变传统只能采用低电流密度(300-400A/m2)的生产工艺,使整流和电解系统关键节能指标得到进一步优化,提升硅整流效率,降低直流电耗,最终降低吨锌综合能耗。
2、关键技术锌电解高电流密度节能技术通过硅整流系统扩容升级、新型特型尺寸极板和电解配套设施的集成优化,突破电流密度和电流效率相互制约的技术瓶颈,提高电解电流密度及硅整流效率,使整流和电解系统关键节能指标得到进一步优化。
其主要的关键技术如下:(1)电解整流系统非同相逆并联谐波抑制技术将电流相等、方向相反的两个导电臂靠拢,达到交变磁场相互抵消、减小导电母排压降、提高功率因数、消除柜体涡流;(2)电解液深度净化技术SZP(Subside Zine Process)优先沉锌技术和超细金属锌粉置换技术。
SZP优先沉锌技术是以焙砂或石灰石作为沉锌剂保持系统水平衡,控制F、Mg、Mn、Cl、K、Na等杂质的深度净化技术;超细金属锌粉置换技术是避免杂质带入系统、提高浸出液除杂效率的深度置换净化技术;(3)ASEP(Anode Surface Embossing Plate)阳极板技术一种合金成分优化、金相组织致密的、适用于在高电流密度条件下长周期使用的波纹阳极板压延工艺技术。
降低锌电积电耗的探讨

1 引言
现代锌冶炼主要是湿法冶炼, 据2 0 0 7年统计 : 湿 法冶炼所产锌 占全 国锌产量 8 0 %以上。湿法冶炼 由焙 烧、 浸 出、 净化、 电积 、 熔铸 5个工序组成 , 湿 法炼锌 的电 耗 中锌 电积约 占 8 0 %, 锌 电积 过程 的实 际电耗为 理论 电耗 ( 1 5 0 0度 ) 的 2倍 左右 , 节 能空 间非 常 大。电积 电 耗是 衡量 生产及 工艺技 术水平 的重要 指标 , 同时对 电 锌 的生产成本有很大影 响 , 。因此 , 电锌 厂实现 节能 降 耗, 提高经济效益 的重中之重是 降低 电积 电耗 。 国内 电 锌 厂 锌 电 积 电 耗 一 般 为 3 0 0 0— 3 3 0 0 k w h / t , 个 别达 到 3 4 0 0 k w h / t , 甚至更 高 , 大 大 超 出 国外 2 8 0 0—3 1 0 0 k h w / t 的 同行 业 水 平 , 降 低 锌 电 积 电耗成 为业 界 一个 重要 的课题 。本文 针对 降低锌 电积电耗作些探讨 。
要: 以 目前 国际主要采用 的湿法炼锌为对象 , 从 多角度对锌 电积 电耗进 行分析 、 探讨 。提 出了 电积液 的纯
Hale Waihona Puke 度要求 , 对不 同电流密度下 的工艺参数进行优化 , 分析了 系统 电能 损耗和 新液底 流对 电积 电耗 的影 响并 提 出降低 系统 电能损 耗的办法及增加降低系统 电能损耗 装置和新液底流 的必要性 , 分析了不 同添加 剂对 电积 电耗 的影 响并
T o t a l 1 2 1
No. 3 2 01 3
铜
业
工
程
总第 1 2 1 期 2 0 1 3年第 3期
浅谈冶金行业电气节能的几项措施
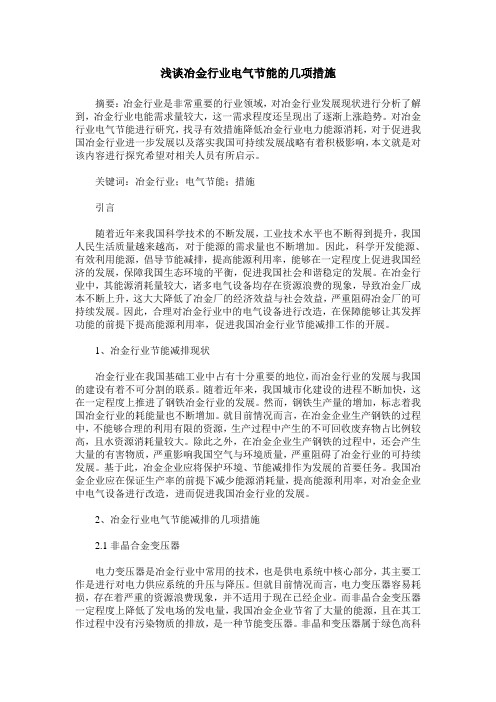
浅谈冶金行业电气节能的几项措施摘要:冶金行业是非常重要的行业领域,对冶金行业发展现状进行分析了解到,冶金行业电能需求量较大,这一需求程度还呈现出了逐渐上涨趋势。
对冶金行业电气节能进行研究,找寻有效措施降低冶金行业电力能源消耗,对于促进我国冶金行业进一步发展以及落实我国可持续发展战略有着积极影响,本文就是对该内容进行探究希望对相关人员有所启示。
关键词:冶金行业;电气节能;措施引言随着近年来我国科学技术的不断发展,工业技术水平也不断得到提升,我国人民生活质量越来越高,对于能源的需求量也不断增加。
因此,科学开发能源、有效利用能源,倡导节能减排,提高能源利用率,能够在一定程度上促进我国经济的发展,保障我国生态环境的平衡,促进我国社会和谐稳定的发展。
在冶金行业中,其能源消耗量较大,诸多电气设备均存在资源浪费的现象,导致冶金厂成本不断上升,这大大降低了冶金厂的经济效益与社会效益,严重阻碍冶金厂的可持续发展。
因此,合理对冶金行业中的电气设备进行改造,在保障能够让其发挥功能的前提下提高能源利用率,促进我国冶金行业节能减排工作的开展。
1、冶金行业节能减排现状冶金行业在我国基础工业中占有十分重要的地位,而冶金行业的发展与我国的建设有着不可分割的联系。
随着近年来,我国城市化建设的进程不断加快,这在一定程度上推进了钢铁冶金行业的发展。
然而,钢铁生产量的增加,标志着我国冶金行业的耗能量也不断增加。
就目前情况而言,在冶金企业生产钢铁的过程中,不能够合理的利用有限的资源,生产过程中产生的不可回收废弃物占比例较高,且水资源消耗量较大。
除此之外,在冶金企业生产钢铁的过程中,还会产生大量的有害物质,严重影响我国空气与环境质量,严重阻碍了冶金行业的可持续发展。
基于此,冶金企业应将保护环境、节能减排作为发展的首要任务。
我国冶金企业应在保证生产率的前提下减少能源消耗量,提高能源利用率,对冶金企业中电气设备进行改造,进而促进我国冶金行业的发展。
金属冶炼中的能源利用和节约措施
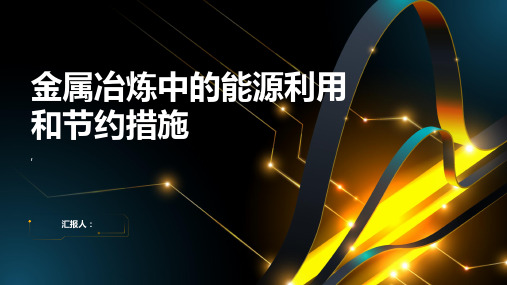
推广可再生能源:如太阳能、 风能等,减少对传统能源的依 赖
Part Four
金属冶炼中的新能 源利用
新能源在金属冶炼中的应用现状
太阳能:用于金属冶炼过程中的加热和冷却 风能:用于金属冶炼过程中的动力和通风 水能:用于金属冶炼过程中的冷却和清洗 生物质能:用于金属冶炼过程中的加热和动力 地热能:用于金属冶炼过程中的加热和冷却 核能:用于金属冶炼过程中的加热和动力
推广清洁能源:推广使用清洁能源, 减少对传统能源的依赖,降低环境 污染。
添加标题
添加标题
添加标题
添加标题
加强能源管理:建立健全能源管理 体系,加强能源管理,降低能源消 耗。
加强技术创新:加强技术创新,研 发新的冶炼技术和设备,提高能源 利用效率。
Part Six
政策与法规对能源 利用的影响
国内外相关政策与法规的制定和实施情况
Part Five
企业实践案例分析
成功实现能源节约的金属冶炼企业案例
节能措施:采用高效节能设 备,优化生产工艺,提高能 源利用效率
效果:每年节约能源成本数 百万元,减少碳排放量
案例企业:某大型钢铁企业
启示:企业应重视能源节约, 采用先进技术和管理手段, 实现可持续发展
能源利用和节约的实践经验总结
金属冶炼中的能源利用 和节约措施
,
汇报人:
目录
01 添 加 目 录 项 标 题 03 节 约 能 源 的 必 要 性 及 措 施 05 企 业 实 践 案 例 分 析 07 未 来 展 望 与 研 究 方 向
02 金 属 冶 炼 中 的 能 源 利 用 现 状
04 金 属 冶 炼 中 的 新 能 源 利 用 06 政 策 与 法 规 对 能 源 利 用 的
降低电积锌直流电耗分析
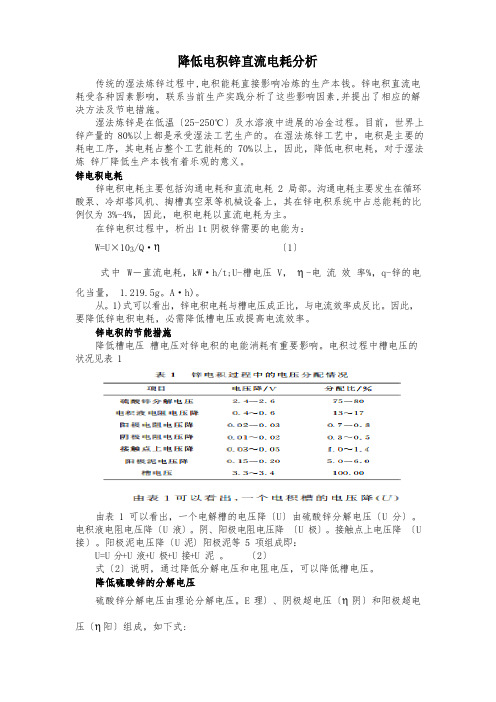
降低电积锌直流电耗分析传统的湿法炼锌过程中,电积能耗直接影响冶炼的生产本钱。
锌电积直流电耗受各种因素影响,联系当前生产实践分析了这些影响因素,并提出了相应的解决方法及节电措施。
湿法炼锌是在低温〔25-250℃〕及水溶液中进展的冶金过程。
目前,世界上锌产量的 80%以上都是承受湿法工艺生产的。
在湿法炼锌工艺中,电积是主要的耗电工序,其电耗占整个工艺能耗的 70%以上,因此,降低电积电耗,对于湿法炼锌厂降低生产本钱有着乐观的意义。
锌电积电耗锌电积电耗主要包括沟通电耗和直流电耗 2 局部。
沟通电耗主要发生在循环酸泵、冷却塔风机、掏槽真空泵等机械设备上,其在锌电积系统中占总能耗的比例仅为 3%-4%,因此,电积电耗以直流电耗为主。
在锌电积过程中,析出1t 阴极锌需要的电能为:W=U×103/Q·η〔1〕式中 W-直流电耗,kW·h/t;U-槽电压 V,η-电流效率%,q-锌的电化当量, 1.219.5g。
A·h)。
从。
1)式可以看出,锌电积电耗与槽电压成正比,与电流效率成反比。
因此,要降低锌电积电耗,必需降低槽电压或提高电流效率。
锌电积的节能措施降低槽电压槽电压对锌电积的电能消耗有重要影响。
电积过程中槽电压的状况见表 1由表 1 可以看出,一个电解槽的电压降〔U〕由硫酸锌分解电压〔U 分〕。
电积液电阻电压降〔U 液〕。
阴、阳极电阻电压降〔U 极〕。
接触点上电压降〔U 接〕。
阳极泥电压降〔U 泥〕阳极泥等 5 项组成即:U=U 分+U 液+U 极+U 接+U 泥。
〔2〕式〔2〕说明,通过降低分解电压和电阻电压,可以降低槽电压。
降低硫酸锌的分解电压硫酸锌分解电压由理论分解电压。
E 理〕、阴极超电压〔η阴〕和阳极超电压〔η阳〕组成,如下式:+η η-+ η-+ U= [E o (0 2.303RT 2.303RT ) 1ga (OH ) (O )] [E o (Zn ) 1ga (Zn 2+ ) (Zn ) =2 F 2 F [E o (O 2.303RT 2.303RT ) 1ga (OH )] [E o (Zn ) 1ga (Zn 2+ )] (O ) +η(ZN ) 。
如何在锌电解过程中进行节能减耗

如何在锌电解过程中进行节能减耗摘要:本文分析了锌电解电耗的影响因素,并针对性地提出了根据槽电压和电流效率来降低电耗的措施。
关键词:湿法炼锌 锌电解 电耗 节能措施论文主体:一、前言在全国锌冶炼行业中,使用湿法炼锌工艺的企业占绝大部分比列。
而在湿法炼锌中,锌电解过程是该工艺中的主要耗能工序。
湿法炼锌能耗较高,一般每吨锌在电解过程中耗能占总能耗的80%以上。
因此,电解电耗是作为湿法炼锌中最重要的技术经济指标之一,它直接影响到生产成本,也标志着生产的好坏程度以及工艺技术水平的高低。
所以,降低电解过程中的能耗,成为我们节约生产成本中的重点之一。
锌电解中电耗主要包括交流电耗和直流电耗两部分。
交流电耗主要是指行车、剥锌机、循环泵、冷却塔风机、真空泵等机械设备所耗电能,然而交流电耗在锌电解过程总电耗中所占比重很少,所以直流电耗成为锌电解过程中能耗中的重中之重,因此,我们在下文中主要讨论锌电解过程中的直流电耗问题。
锌电解能耗是是指每生产1t 析出锌所消耗的电能,单位为kWh/t.它是电解生产中的一个重要技术经济指标。
其计算公式如下: W=)析出锌产量()实际消耗电能(t kWh =Nt q I N t I U *******η*1000 式中 W ——电能单耗,kWh/t ·Zn ;U ——槽电压,V ;η——电流效率(%);I——电流,A;t——电解时间,h;N——电解槽数目;q——电化当量,1.2202g/(A·h)。
从上式得知,电耗与电解的槽电压成正比,与电流效率成反比。
因此,任何能降低槽电压和提高电流效率的措施都能减少电能消耗。
下面就某厂生产实践中影响电能消耗的因素及所采取的措施作简要论述。
二、降低槽电压减少电能消耗的措施分槽电压是由电解槽内相邻阴阳极间的电压降数值,主要由ZnSO4解电压、电解液电阻电压降、阴阳极及接点电压降、导电板及触点电压降、阳极泥电阻电压降等部分组成。
其优化前组成情况见表1。
- 1、下载文档前请自行甄别文档内容的完整性,平台不提供额外的编辑、内容补充、找答案等附加服务。
- 2、"仅部分预览"的文档,不可在线预览部分如存在完整性等问题,可反馈申请退款(可完整预览的文档不适用该条件!)。
- 3、如文档侵犯您的权益,请联系客服反馈,我们会尽快为您处理(人工客服工作时间:9:00-18:30)。
浅析锌电积过程节能措施Ξ刘子明(昆明云冶锌业股份有限公司,云南 昆明 650102)摘要:分析了电解过程中对直流电单耗有影响的因素,结合生产实践,针对性地提出了降低锌电解过程能耗的措施。
关键词:锌电积;电能;节能措施中图分类号:TF813 文献标识码:B 文章编号:1004-2660(2003)S1-0020-031 概述近年来,湿法炼锌技术得到飞速发展,使之在锌的提取冶炼中占据越来越重要的地位,至20世纪90年代初,湿法炼锌的锌产量已经占总产量的80%以上。
湿法炼锌能耗较高,一般每t 锌耗能(折合为电能)为3800~4100kuh ,其中电积过程消耗的能量为每t 析出锌2900~3500kuh ,占总能耗的80%左右,因此,研究怎样降低电积过程的能耗,对于降低湿法炼锌的生产成本是一个有价值的、十分必要的课题。
锌电积过程能耗是由以下公式计算的:W =820V /ηi式中:V ———槽电压 ηi ———电流效率(%) W ———电能单耗根据以上电能的计算公式可以看出,电耗与电解的槽电压成正比,与电流效率成反比。
因此,任何降低槽电压或提高电流效率的措施都是有利于降低电能消耗的。
下面就某厂生产实践中影响电能消耗的因素及所采取的措施作简要论述。
2 影响锌电解过程能耗的因素及节能措施211 确保电解液的质量,减轻有害杂质的影响对锌电解过程而言,保证电解液具有很高的纯度是一个很关键的问题。
由于锌的标准还原电位(-01763V )较绝大多数杂质金属都要负,当杂质离子的浓度达到一定的程度时,就会降低氢的超电压,影响电效,有时甚至发生严重“烧板”,大大降低电流效率,增加了电耗并给生产造成很大的影响。
电解液的主要有害杂质离子及含量如表1。
21111 Co ,Ni ,Cu等杂质对锌电积电流效率的影响及对策这类金属的共性是氢在其上的析出电位都不高(见表2),当这类杂质在溶液中达第30卷增刊 有色金属设计 Vol 130Su pp. 2003 NON FERROUS M ETALS DESI G N 2003 Ξ收稿日期35作者简介刘子明(),男,湖南人,工程师,主要从事有色冶炼生产及技术管理方面的工作:200-11-0:1970-.到一定的浓度后,它们将优先于锌在阴极析出,由于氢的放电而使锌不能在这里沉积,且析出的杂质金属和锌组成微电池,在这种微电池中,由于锌的电位更负而发生溶解,给电解过程带来很大的干扰,严重时即产生所谓“烧板”,增加电解能耗。
表1 电解液主要杂质及含量表金属Cu Ni C o As Sb G e含量/(mg L-1)011~012012~1012~0170105~011011~0120101~0104表2 氢在几种金属上析出的超电压(电流密度:400A/m2)金属Zn Co Ni Cu 氢的超电压/V1110014801440168因为在净化过程中铜很容易被除去,要获得含铜0100015g/L以下的电解液并不困难,但停产后重新开槽或出、装槽时操作不当有可能因导电头上的氧化层污染电解液,造成电解液含铜过高而影响了析出锌质量和电效,这一点通过规范操作、加强管理是可以避免的。
镍是一种危害较大的杂质。
某厂上世纪七八十年代电解液含镍在01002~01005g/L 之间,经常出现镍引起的“烧板”。
通过严格控制精矿配料含镍,强化溶液净化过程,现在含镍基本上能控制在01001g/L以下,很少出现镍“烧板”。
钴是目前生产中经常制造麻烦的一种元素。
钴的来源主要是锌精矿,钴以氧化物的形态进入锌焙砂,在浸出过程绝大部分进入溶液中形成硫酸盐,生产实践中我们一般要求电解液含钴小于01001g/L,当配料后的混合锌精矿含钴达到010075%以后,进入上清液的钴就会达到0102g/L左右,净化过程就很难将它除到要求的含量以下。
对付杂质钴的措施目前主要是控制原料含钴、加强净化操作以及在镉工序增加钴的开路。
21112 G e,As,Sb等杂质对锌电积电流效率的影响及对策当这类杂质在溶液中达到一定浓度时,它们就会优先在阴极放电沉积,随之而来的就是氢在其上放电,同时产生活性氢原子,这2种原子进一步结合产生气体氢化物,这种氢化物并不马上逸出溶液,而是吸附在阴极表面,这种气态绝缘物将阻止锌在该处继续沉积,对电解的危害很大。
克服As,Sb,G e引起的“烧板”,要严格控制锌精矿配料中它们的含量,控制好浸出的工艺条件,强化净化操作,适当限制氧化锌的投入量。
21113 有机物对电解的影响及对策有机物对电解过程的影响也越来越多地引起我们的关注,由于系统中经常进行的机械设备的检修以及设备运行中将油、脂等有机物带入系统,以及In或G e的萃余液返回系统,使得系统溶液中有机物含量时有上升,有机物附着在阴极表面,妨碍电解液和阴极的充分接触,大大增加能耗。
在实际生产中,由于有机物的影响,可使每吨析出锌的电耗增加20~50kuh。
目前,主要措施是对In,G e萃余液进行氧化处理,对机械设备操作、维修进行规范化管理,可取得显著效果。
杂质对电解过程的影响十分复杂,有时,单一的或少数杂质超过我们要求的范12增刊 刘子明:浅析锌电积过程节能措施围,而其他杂质含量很低,电解的条件(如槽温、酸锌比、流量等)控制很稳定,操作很规范,也不会对电解电流效率产生很大的影响;但也可能出现各种杂质含量都在我们要求的范围内,而由于电解的条件控制不好,或是操作不当,或者溶液中混有有机物等上述原因也可能造成电解条件急剧恶化,电流效率大幅下降,甚至出现较严重的“烧板”现象;也存在单一杂质超标并不“烧板”,而与其他某种或几种杂质都超标就出现的所谓“复合杂质烧板”现象,这些都还有待于进一步总结和研究。
212 选用合理的阳极材料目前,各电锌厂均采用铅-银系列(二元或三元)合金作为阳极。
阳极中银的含量控制恰当,不仅能延长阳极寿命、提高阴极锌的质量,而且能降低阳极电位,减少阴极锌的能耗。
某厂曾使用过含银1%和017%的铅银阳极,通过大量的对比数据测定表明,相同电解条件下,使用前者的槽电压比后者低20mV,能节电20kWh/t析出锌,因此从1998年起全面使用含银1%的阳极。
也有一些厂家采用铅银钙三元阳极,取得了较好效果,其原因是三元阳极其含银量相对较低,对阳极成本的降低起明显的作用,但也存在阳极泥成片状、阴极锌含铅不易控制、电阻较高、不适宜高电流密度电解等缺点,各电锌厂根据自己的具体情况进行选择。
20世纪90年代中期以来,一些厂家开始使用穿孔阳极板,实践证明,穿孔阳极的使用可以有效地改善电解槽内的电解液的循环,而且因为打孔后阳极的附着力减小,使沉积的阳极泥减少,从而使电解的槽电压降低0102~0105V,可降低电耗20~50kWh/t 锌。
13 合理控制电积条件131 控制适宜的酸锌含量电解反应方程式为:ZnSO4+H2O=Zn+H2SO4+(1/2)O2从电解反应方程式来看,锌的浓度高,硫酸的浓度低有利于反应向右进行,即电流效率随着硫酸浓度的增加而降低,随着锌离子的浓度升高而升高。
但是,随着溶液含锌的升高、含酸降低,又会增加电解液的比电阻(见表3),使槽电压上升。
某厂生产实践中采用170~190g/L的含酸和45~55g/L的含锌取得了很好的效果。
表3 硫酸锌溶液的比电阻与酸锌成分的关系H2SO4/(g L-1)溶液含锌/(g L-1)406080100 120218831143147317314021442170310031251601190211621392164180118111992122142200116911852104212421312 控制恰当的电流密度电流密度增加,一方面会使氢的超电压增加,有利于电流效率的提高和电耗的降低,但另一方面,却使得槽电压上升而增加电耗,槽电压随着电流密度的升高而上升,在实际生产过程中,我们通过大量数据进行比较发现,电流密度对槽电压的影响比对电流效率的影响要显著得多,尤其是在目前电解液质量稳定,杂质含量很低的情况下。
在38~40℃的槽温,含锌45~50g/L,H2SO 180~190g/L的电解条件下,电流密度为200A/m2,450A/m2,560A/m2时测得槽电压分别为2197V,3125V,3150V。
根据某厂目前的溶液和电解条件的特性,电流密度控制在~55能够获得较好的技术经济指标。
22 有色金属设计 第30卷2214000A/m221313 严格控制电解的槽温电解过程的槽内温度是一个很重要的工艺控制条件。
一般锌电解厂的电解温度控制在30~45℃。
提高温度,有利于减小电解液的比电阻,可以降低槽电压,但却会降低氢的超电压,从而降低电流效率,甚至使电解出现“返溶”或“烧板”,使能耗急剧上升,这种情况在溶液含杂质偏高的情况下会更加严重。
生产中把槽温控制在37~42℃,电解液采用空气冷却塔进行冷却,槽温过高时,则采取降低电流或在电解槽内加水以避免其进一步升高而发生“烧板”。
21314 采用尽可能小的同极距离电解液的电阻正比于电极之间的距离,所以缩小同极之间的间距,对于降低电解液的电压降,从而减小槽电压和电解能耗是很有价值的,1997年某厂将某系列原来的62 mm的同极距缩短为58mm,不仅增加了电解槽的生产能力,同时也使槽压下降0102V,较缩距前节电016%左右。
但缩短极距不是可以无限制进行的,极距太短,容易造成槽内接触增多,给槽面操作与管理增加很多困难,影响电流效率,反而增加电耗。
214 合理使用添加剂电解过程中使用一定量的添加剂,一方面能锌沉积反应的过电位,使阴极结晶细化,使阴极析出致密,表面平整,另一方面能减弱有害杂质的影响,能阻止H+的扩 散,增加氢的超电压,但使用方法要得当,否则反而会使电流效率降低,增加电耗。
常用的添加剂有骨胶、酒石酸锑钾(吐酒石)。
215 严格加强操作管理电解的操作对其能耗指标,也起着至关重要的作用。
控制尽可能大的流量有利于带走电解产生的热量,而且有利于Zn2+的扩散,减少浓差极化,缓解杂质危害;及时清理阳极泥,减小阳极泥电阻,某厂清理周期由原来的3个月/次缩短为每月/次后,对降低槽电压,减少能耗效果显著;尽量杜绝槽内、槽面接触,减少漏电现象。
3 结语锌电解过程节能应主要从降低槽电压、提高电流效率,减少漏电损失等方面考虑,其中保证电解液的质量,稳定电解条件,加强操作管理是比较关键的因素。
科技工作者们仍在积极探索大幅度降低能耗的新途径,如采用新型材料作为阳极以期降低锌析出的分解电压与超电压之和,有人寻求新的电解体系希望大大降低能耗。
参考文献:32增刊 刘子明:浅析锌电积过程节能措施。