碳纤维复合材料缠绕修复的压力管道断裂分析_柳军
碳纤维补强技术在石化管道修复中的应用-岳阳长岭设备研究所有限公司
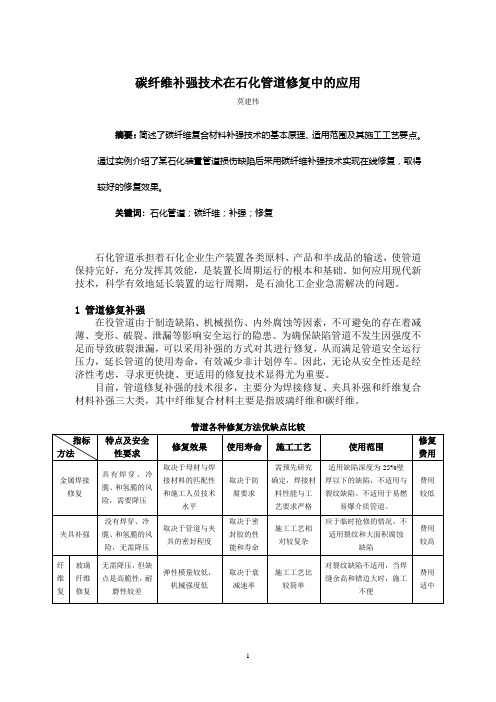
碳纤维补强技术在石化管道修复中的应用莫建伟摘要:简述了碳纤维复合材料补强技术的基本原理、适用范围及其施工工艺要点。
通过实例介绍了某石化装置管道损伤缺陷后采用碳纤维补强技术实现在线修复,取得较好的修复效果。
关键词: 石化管道;碳纤维;补强;修复石化管道承担着石化企业生产装置各类原料、产品和半成品的输送,使管道保持完好,充分发挥其效能,是装置长周期运行的根本和基础。
如何应用现代新技术,科学有效地延长装置的运行周期,是石油化工企业急需解决的问题。
1 管道修复补强在役管道由于制造缺陷、机械损伤、内外腐蚀等因素,不可避免的存在着减薄、变形、破裂、泄漏等影响安全运行的隐患。
为确保缺陷管道不发生因强度不足而导致破裂泄漏,可以采用补强的方式对其进行修复,从而满足管道安全运行压力,延长管道的使用寿命,有效减少非计划停车。
因此,无论从安全性还是经济性考虑,寻求更快捷、更适用的修复技术显得尤为重要。
目前,管道修复补强的技术很多,主要分为焊接修复、夹具补强和纤维复合材料补强三大类,其中纤维复合材料主要是指玻璃纤维和碳纤维。
管道各种修复方法优缺点比较碳纤维补强技术可在不卸料、不泄压、不动火情况下对管道实施修复补强,可以避免由于焊接施工所带来焊穿、氢脆、冷脆等风险,施工成本比卡具补强低。
碳纤维补强技术相比玻璃纤维补强可承受的压力及机械强度更高,耐磨性能及耐腐蚀性能更优越,同时也克服了玻璃纤维不适用于裂纹,管道补强及寿命随时间衰减等问题。
碳纤维补强技术能更好的保障管道运行的连续性,有效的消除承压管道带病运行的安全隐患,同时也避免了非计划停车修复带来的经济损失。
该技术是 20 世纪 90 年代以后发展起来的一种高效快捷的新型补强技术,因其综合性能最优,近年来在国内外管道修补方面的应用越来越多。
2 碳纤维补强技术2.1 基本原理碳纤维补强技术是利用碳纤维材料在纤维方向的高强度特性,依靠热固性树脂基体增强,采用湿铺工艺在服役管道外包覆一个复合材料修复层,与管道形成一体,分担管道承受的内压,降低含缺陷处管道的应力水平,从而达到对管道补强的目的,以恢复管道的正常承载能力。
浅谈压力管道射线无损检测的质量控制措施

浅谈压力管道射线无损检测的质量控制措施浅谈压力管道射线无损检测的质量控制措施摘要:压力管道是管道中的一部分,具有非常广泛的用途,在石油、天然气等等各种自然资源的运送中发挥着巨大作用,涉及到生活的各个方面。
目前,压力管道可分为油气管道、公用管道及工业管道三种,对其进行质量控制,是为了保证各种资源的正常供给及生活环境的安全。
而作为无损检验技术中的一种,射线检测在管道焊缝内部质量检测中的应用越来越广泛,其重要性不言而喻。
因而,对压力管道射线无损检测的深入研究,对其质量控制措施进行探讨,具有十分重要的意义。
本文主要分析压力管道的特点及射线无损检验的相关内容,并对压力压力管道射线无损检测的质量控制措施进行研究。
关键词:压力管道特点射线无损检测质量控制前言压力管道是管道中的一部分,主要负责石油、天然气等等各种自然资源的输送、分配、混合、分离、排放、计量和控制等方面,可分为油气管道、公用管道及工业管道三种[1]。
随着社会生产力的不断发展及人们生活水平的不断提高,压力管道的应用越来越广泛,已发展成现代社会人们生活中不可或缺的重要组成部分。
压力管道的安全运行,直接关系到国家财产及人们生命安全,该影响到生态环境建筑,其重要性不言而喻。
对压力管道的检验检测工作包括:外观检验、无损检测、硬度测定、耐压试验等等,而射线无损检测是无损检验技术中的一种,在保障压力管道稳定、安全输送流体等方面发挥着巨大作用。
因而,对射线无损检测的质量控制,十分有必要。
1.压力管道的主要特点压力管道是一个整体的系统,其特点主要包括:(1)种类多,数量大。
不同于压力容器,管道工程中,相关设计、制造、按照、检验及应用管理的环节众多,技术要求和质量管理难度大。
(2)材料选用较为复杂。
管道组成件和支承件的种类繁多,且各具特点,技术要求高。
(3)长径比大,极易失稳。
压力管道内的流体流动状态相对复杂,缓冲余地小。
在受力方面,压力管道受高温、高压、低温、低压、位移变形、风、雪、地震等工作条件影响大,比压力容器更为复杂。
复合材料的断裂力学分析

复合材料的断裂力学分析在现代工程应用中,复合材料广泛应用于航空航天、汽车、建筑等领域,其具有优异的力学性能和轻质化特点。
然而,复合材料在使用过程中可能会遭遇断裂问题,这对于确保结构的可靠性和安全性具有重要影响。
因此,对复合材料的断裂力学进行分析和研究,对于优化设计和应用格局具有重要意义。
断裂问题是复合材料研究领域中的一个核心问题。
复合材料的断裂行为受到许多因素的影响,如纤维和基体的相互作用、界面特性、纤维排布和纤维/基体的粘合强度等。
研究断裂力学,可以通过分析断裂失效的基本原因和机理,提高复合材料的断裂韧性和延展性,以适应多样化的应用需求。
对于复合材料的断裂力学分析,一种常用的方法是基于线弹性断裂力学理论。
这种方法适用于强度较高、刚度较大的复合材料。
通过应力场和应变场的分析,可以确定关键断裂参数,如断裂韧性、断裂能量释放率等。
此外,还可以分析复合材料中的微观缺陷和损伤,如纤维和基体的断裂、纤维断裂和层间剪切等。
通过研究复合材料的断裂行为,可以深入了解其力学性能,并提供指导优化设计和材料使用的依据。
在断裂力学分析中,还需要考虑几种常见的断裂失效模式,如纤维断裂、纤维/基体界面剪切断裂、层间剪切断裂等。
纤维断裂是复合材料最常见的失效模式之一,对于纤维增强复合材料而言,其断裂韧性和拉伸性能是至关重要的。
纤维/基体界面剪切断裂是在纤维和基体之间形成的界面失效模式,其对于界面剪切强度和界面粘结力的研究有重要的指导意义。
层间剪切断裂是复合材料中的一种失效模式,主要发生在纤维层之间,影响复合材料整体性能的重要因素之一。
在复合材料的断裂力学分析中,有几个关键的参数需要考虑。
首先是断裂韧性,它描述了材料抵抗断裂的能力。
其次是断裂能量释放率,它表示断裂过程中单位面积的能量释放情况,可以用于评估断裂的严重性。
另外,断裂的扩展速率也是一个重要的参数,通过分析断裂速率,可以判断断裂行为的临界点和材料的强度性质。
综上所述,复合材料的断裂力学分析是复合材料研究和应用中不可忽视的重要内容。
碳纤维缠绕复合铝圆管轴向压溃力学性能研究

吸能( EA) 、比吸能率( SEA) 和压缩力效率( CFE) ꎬ
计算方法见公式(1) 至公式(4) ꎮ
峰值力表示在轴压过程中载荷达到的最大峰
值ꎬ表达式为:
PCF = max{ f( x) ∀x ∈ [0ꎬl] }
(1)
总吸能表示在压溃过程中样件吸收能量的总
缠有玻璃纤维和碳纤维ꎮ 张亮泉等
[10]
分析了铺层
方式对 CFPR 圆管的强度特性影响ꎬ通过实验对两
种直径不同的 CFRP 圆管抗压和抗拉特性进行研
收稿日期:
基金项目:
作者简介:
通讯作者:
2 性能实验
2 1 样件制备
为研究纤维缠绕复合管轴向力学性能ꎬ本次实
验选用 1 根铝合金圆管ꎬ9 根碳纤维缠绕铝合金复
和ꎬ表达式为:
EA =
图 1 湿法缠绕过程
Fig 1 Filament winding process
∫
l
0
f( x) dx
(2)
比吸能率表示单位质量的能量吸收效率ꎬ表达
铝管( 直径为 60 mm) 和缠绕后的复合管样件长
式为:
度均为 150 mmꎮ 表 1 列出了样件的几何参数和实
验结果ꎬ其中样件编号中 A 的含义为复合管内层为
崔政粱 (1995 ̄) ꎬ 男ꎬ 硕士ꎬ 主要从事结构轻量化方面的研究ꎮ
刘强 (1981 ̄) ꎬ 男ꎬ 博士ꎬ 教授ꎬ 主要从事结构轻量化和安全方面的研究ꎬ Liu5168198110@126 comꎮ
碳纤维缠绕复合铝圆管轴向压溃力学性能研究
6
2缠绕张力和充分的树脂浸泡ꎻ其次ꎬ纤维通过做
往返直线运动的绕丝嘴缠绕在自转的铝合金圆管
碳纤维复合材料力学性能研究进展

包 装 工 程第44卷 第21期 ·36·PACKAGING ENGINEERING 2023年11月收稿日期:2023-05-30基金项目:国家自然科学基金(12172344) *通信作者碳纤维复合材料力学性能研究进展段裕熙,张凯*,徐伟芳,陈军红,龚芹(中国工程物理研究院总体工程研究所,四川 绵阳 621999)摘要:目的 综述碳纤维复合材料这一热结构材料的力学性能研究进展,推进碳纤维复合材料的研制和应用。
方法 采用文献调研法,梳理和汇总国内外有关碳纤维复合材料力学性能的研究内容,对二维复合材料、针刺复合材料及三维编织复合材料3种结构进行性能影响因素分析。
结论 影响碳纤维复合材料静态和动态力学性能的因素主要有温度、应变率、密度等,提出应进一步开展碳纤维复合材料在多因素耦合及高温动态性能方面的研究。
关键词:碳纤维复合材料;静态力学性能;动态力学性能;三维编织复合材料 中图分类号:TB332 文献标识码:A 文章编号:1001-3563(2023)21-0036-10 DOI :10.19554/ki.1001-3563.2023.21.005Mechanical Property of Carbon Fiber CompositesDUAN Yu-xi , ZHANG Kai *, XU Wei-fang , CHEN Jun-hong , GONG Qin(Institute of Systems Engineering, China Academy of Engineering Physics, Sichuan Mianyang 621999, China) ABSTRACT: The work aims to explore recent advancements in the mechanical properties of carbon fiber composites for thermal structural applications, with the objective of promoting the development and utilization of carbon fiber composites. Through a comprehensive literature review, the current research status on the mechanical properties of carbon fiber composites was summarized, and the factors affecting the static and dynamic mechanical properties of 2D composites, needled composites, and 3D woven composites were analyzed. The results indicate that factors affecting the static and dynamic mechanical properties of carbon fiber composites include temperature, strain rate, density, et al. And further investigations are necessary in multi-factor coupling and high temperature dynamic properties of carbon fiber composites. KEY WORDS: carbon fiber composite; static mechanical properties; dynamic mechanical properties; three-dimensional weaving composite碳纤维由有机纤维经过一系列热处理转化而成,它是含碳量高于90%的无机高性能纤维,既具有碳材料的固有本征,又兼具纺织纤维的柔软可加工性。
海底管道外腐蚀复合材料水下缠绕补强修复技术应用

至关重要由于海上服役环境比较恶劣海底管道
=!引!言
本身也会存在一定的缺陷同时运行期间还会存
随着海上油气资源产量的增长海底管道作为 在第三方破坏自然灾害海底管道服役期间的腐
油气资源输送的重要设施其安全和可靠的服役将 蚀等诸多因素影响海底管道的运行寿命其中
!作者简介刘军!'.,!男学士中级工程师主要从事海底管道材料性能研究WOA7K%+'%%",!$"ee-S/O
关键词!海底管道服役寿命复合材料补强修复
中图分类号 文献标志码 文章编号 DW',&-'" ,"',"$"&$$"% $(
!"#!$-!"$.,/001-"$'+ ,"',-"$"&-$%-$%
822/#)'4#"-"0G-!%(<'4%($%#-0"()%7%-4$%2'#(6%)*-#MB%<#4* 5('2 ."72"%J'4%(#'/&"0NO4%(-'/."(("&#"-0"(1B97'(#-%+#2%/#-%
89&4(')4!DH0LA@0L0NQ7S0/@L?JOAN790I7I0K790L79/7K;:ALA98MA10N1NA9LI/N1A17/97LQ0NP7OI/N1A91;A981H0 K/9:XL1A9879:S/NN/L7/9 IN/JK0O AKL/A@@0S1L1H0L0NQ7S0K7@0/@L?JOAN790I7I0K790LRDH0S/OI/L710 OA10N7AK N079@/NS0O091A98N0IA7N10SH9/K/:PHALJ009M780KP?L0879/9LH/N0I7I0K790L;J?171HAL9/1J009AIIK708791H0 N0IA7N/@L?JOAN790I7I0K790LR*L?JOAN790I7I0K790A8/I1L1H0S/OI/L710OA10N7AK?980NMA10NM79879:N079@/NS0O091A98 N0IA7N10SH9/K/:P1/SANNP/?1INAS17SAKAIIK7SA17/9RDH0INAS17SAKAIIK7SA17/9IN/Q0L1HA11H0S/OI/L710 OA10N7AK ?980NMA10NM79879:N079@/NS0O091A98N0IA7N10SH9/K/:P7LALA@0A98N0K7AJK0N079@/NS0O091A98N0IA7N10SH9/K/:PR DH7LIAI0NM7KK791N/8?S01H0N0IA7NOA10N7AKIN/I0N170L/@1H0S/OI/L710?980NMA10NM79879:N079@/NS0O091N0IA7N 10SH9/K/:P;1H0AIIK7SA17/980L7:9/@1H0N0IA7NLPL10O;A981H0S/9L1N?S17/910SH9/K/:P/@1H0N0IA7NLPL10OR :%;<"(!&!L?JL0AI7I0K790VL0NQ7S0K7@0VS/OI/L710OA10N7AKLVN079@/NS0O091N0IA7N
碳纤维复合芯棒断裂原因与金具质量的探讨

2 0 1 3 年 第2 期
电力 金 具
4 3
案 例2
项 目单 位 : 国家 电 网公 司 问题 描 述 :江 苏 省宏 源 电力 建 设 监 理 有 限 公 司 受 国家 电 网公 司委 托 ,对 改 造 工 程 应 用 碳 纤 维 复 合 芯 导 线 进 行 抽 检 。 按 照G B / T 4 9 0 9 . 3 要 求 进 行 试 验 ,取 样 三 件 ,校 直 、夹 持 ,启 动 拉 力 机 ,控 制 拉 力 机 速 度 ,加 载 、记 录 拉 力 强 度 。 导 线 芯径 在 金 具 线 夹 管 口处 断裂 和 位 移 大 于2 mm,试 验 结 果 则 为 不 合 格 。 原 因分 析 :夹 持 试 件 的 金 具 加 工 质 量 低 劣 ,粗 糙 度 超 标 ,精 度 低 ,更 换 江 苏 易 鼎 电 力 科 技 有 限 公 司 生 产 的优 质 耐 张线 夹 和 接 续 管 ,进 行 试 验 ,试 验 全 部 合 格 ,判 定 该 公 司 生产 的 碳 纤 维 复 合 芯 导 线 合 格 。 防 范 措 施 :从 碳 纤 维 复 合 芯 导 线 生 产 工 艺 、施 工 和 运 行 中 发 生 质 量 问题 与 生 产 工 艺 ,特 殊 结 构 及 相 匹配 金 具 质 量 紧 密相 关 。
2 0 1 3 年 第2 期
电 力 金 具
4 2
碳 纤维复合芯棒断裂原 因与金具质量 的探讨
宋 丹 张春 宁 仝 伟 严行 建
1 、江 苏 省 宏 源 电 力 建设 监 理 有 限公 司 南 京 2 1 0 0 3 6 2 、江 苏 易 鼎 电力 科 技 有 限公 司 宿迁 2 2 3 8 0 0 3 、江 苏 省 电力 公 司 2 1 0 0 2 4
碳纤维增强复合材料层间断裂韧度

算时间和资源。矫桂琼等[6]采用铰链式双悬臂梁试 件研究了纤维桥连和试件厚度对复合材料层板断 裂韧度的影响。ENF 实验方法由 Barrett 和 Foschi 研究木质梁层间断裂首次提出,Russell 等[7]将此方 法用于先进复合材料Ⅱ型层间断裂韧度应变能释 放率的研究[7]。于志成[8]对复合材料Ⅱ型层间断裂 韧度实验方法进行了研究,发现试件尺寸和加载速 率对计算结果没有影响。肖军等[9]研究了单向层和 多向层对复合材料层合板Ⅱ型断裂韧度的影响。 吴妙生等[10]对纤维增强复合材料断裂韧度细观机 理进行了分析,研究了纤维材料和纤维走向、基体 韧性对复合材料层板断裂韧度的影响。侯大寅[11] 从纤维增强复合材料的断裂机理,分析了影响其断 裂韧度的主要因素。
1 实验材料及方法
1.1 试件设计及实验设备 根据 ASTM 5528(01)和 HB7403—1996 标准Βιβλιοθήκη 138航 空 材 料 学 报
第 38 卷
设计了Ⅰ型和Ⅱ层间断裂韧度实验试件,试件材料 为 T300/CYCOM970,在 177 ℃ 环境下固化 2 h 制 成。每种类型断裂韧度实验分别采用热压罐和热 补仪固化方式制造尺寸相同的两组试件。Ⅰ型试 件尺寸如图 1(a)所示,试件长 140 mm,宽 20 mm, 预制裂纹 65 mm。层合板铺层为[0]16,总厚度
碳纤维增强复合材料由于其高的比强度和比 模量、耐高温、耐疲劳等优点被广泛应用于航空航 天领域。据统计,复合材料的各种损伤破坏形式 中,分层失效约占 60%[1],分层会导致复合材料承 载力显著下降,分层的扩展使得层合结构的刚度和 强度迅速下降[2]。由于层间强度远低于纤维强度, 故层间强度是层板强度的弱环,低的层间强度和高 的层间应力容易导致分层损伤,层合板抗分层的能 力是由基体的韧性决定,提高基体的韧性可以改善 层合板抗分层的能力,国内外复合材料已将层间断 裂韧度作为表征基体性能的重要指标,层间断裂韧 度问题是工程中的研究热点。
碳纤维复合材料力学断口分析研究
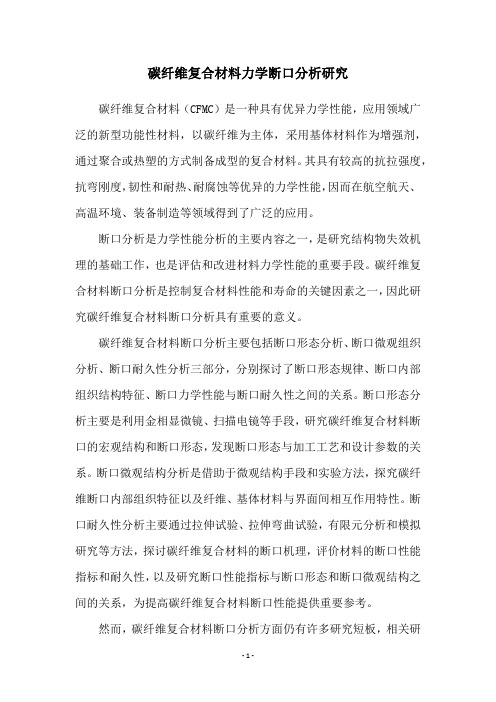
碳纤维复合材料力学断口分析研究碳纤维复合材料(CFMC)是一种具有优异力学性能,应用领域广泛的新型功能性材料,以碳纤维为主体,采用基体材料作为增强剂,通过聚合或热塑的方式制备成型的复合材料。
其具有较高的抗拉强度,抗弯刚度,韧性和耐热、耐腐蚀等优异的力学性能,因而在航空航天、高温环境、装备制造等领域得到了广泛的应用。
断口分析是力学性能分析的主要内容之一,是研究结构物失效机理的基础工作,也是评估和改进材料力学性能的重要手段。
碳纤维复合材料断口分析是控制复合材料性能和寿命的关键因素之一,因此研究碳纤维复合材料断口分析具有重要的意义。
碳纤维复合材料断口分析主要包括断口形态分析、断口微观组织分析、断口耐久性分析三部分,分别探讨了断口形态规律、断口内部组织结构特征、断口力学性能与断口耐久性之间的关系。
断口形态分析主要是利用金相显微镜、扫描电镜等手段,研究碳纤维复合材料断口的宏观结构和断口形态,发现断口形态与加工工艺和设计参数的关系。
断口微观结构分析是借助于微观结构手段和实验方法,探究碳纤维断口内部组织特征以及纤维、基体材料与界面间相互作用特性。
断口耐久性分析主要通过拉伸试验、拉伸弯曲试验,有限元分析和模拟研究等方法,探讨碳纤维复合材料的断口机理,评价材料的断口性能指标和耐久性,以及研究断口性能指标与断口形态和断口微观结构之间的关系,为提高碳纤维复合材料断口性能提供重要参考。
然而,碳纤维复合材料断口分析方面仍有许多研究短板,相关研究主要集中于断口结构形态、断口力学性能分析,对于断口耐久性分析仅有非常有限的深入研究。
在此基础上,还要加强有关力学性能分析技术的研究,例如建立断口形态、断口微观结构、断口力学性能与断口耐久性之间的建模关系,进一步推动碳纤维复合材料在航空航天、环境安全、能源储罐等领域的应用。
综上所述,碳纤维复合材料断口分析是评估碳纤维复合材料力学性能和寿命的重要手段,断口分析涉及断口形态分析、断口微观组织分析、断口耐久性分析三个方面,至今仍存在许多未解决的问题,但在结构优化技术的应用进展快,将有助于为碳纤维复合材料力学性能分析和耐久性评价提供导向。
纤维缠绕复合材料压力容器渐进损伤分析

柱段部分: 由于每一单层的厚度和纤维缠绕角 在整个柱段上是常数, 这部分的建模相对比较简单。
为了保证单元形状的规则, 不使局部区域出现 较大的计算误差或矩阵奇异而终止计算, 均使用映 射网格。最后得到压力容器及封头部位有限元模型 如图 2 所示。 21 21 3 加载与求解
由于压力容器是轴对称结构, 故选择容器沿轴 线上的单元进行分析, 当压力为 41 5 M Pa 时, 容器 最外层沿纤维方向, 应变的分布如图 3 所示。同时, 选取容器上左封头( 点 1) , 桶身( 点 2) , 右封头上 ( 点 3) 点的模拟结果与试验结果[ 3] 的比较如图 4 所示。说明该有限元模型真实反映压力容器的力学 特性, 可用于进一步的分析。
3 压力容器渐进损伤分析
复合材料结构的破坏是一个十分复杂的问题, 它具有多种破坏模式, 对于不同的破坏模式, 复合 材料有不同的强度, 因此如何知道一个实际的复合 材料结构, 在复杂外载荷条件下的破坏模式及破坏 强度, 一直是人们十分关心的问题。过去通常只能 采用结构试验的方法, 这种方法一般来说既费时又 费钱。随着计算机软、硬件的不断发展, 利用计算机
S12
0 0 0 0 0 0 C12 S12
E11 0
0
0
0
0
E11
0 kE 22 0
0
0
0
E22
0
碳纤维复合材料结构R区褶皱缺陷研究

碳纤维复合材料结构R区褶皱缺陷研究
张琛;张栋梁
【期刊名称】《纤维复合材料》
【年(卷),期】2024(41)2
【摘要】本文针对碳纤维织物预浸料阳模成型L/C型梁结构,在R区出现的面外纤维褶皱缺陷进行了研究。
通过控制工艺方法得到了不同毛坯厚度的试验件;对试验件固化前后厚度压缩量进行了对比;并对褶皱进行了金相显微镜分析。
结果表明,复合材料R区出现褶皱是由于成型过程中,预浸料在R区层间滑移受到限制,纤维方向不可压缩导致;固化前后厚度压缩程度对R区成型质量有很大影响,压缩量越大,R区越容易出现褶皱;相比于L型结构,C型结构对纤维滑移的限制更大,更容易在R区出现褶皱。
【总页数】6页(P20-25)
【作者】张琛;张栋梁
【作者单位】中航复合材料有限责任公司
【正文语种】中文
【中图分类】TB3
【相关文献】
1.先进复合材料创新研究和工程化平台——先进复合材料国防科技重点实验室和结构性碳纤维复合材料国家工程实验室
2.包含细微缺陷的碳纤维增强复合材料管件结构弯曲性能表征
3.碳纤维增强复合材料褶皱缺陷的超声成像
4.飞机结构中碳纤
维增强复合材料缺陷的先进检测5.S型碳纤维褶皱夹芯结构低速冲击响应特性实验研究
因版权原因,仅展示原文概要,查看原文内容请购买。
碳纤维复合材料纵向拉伸失效机制
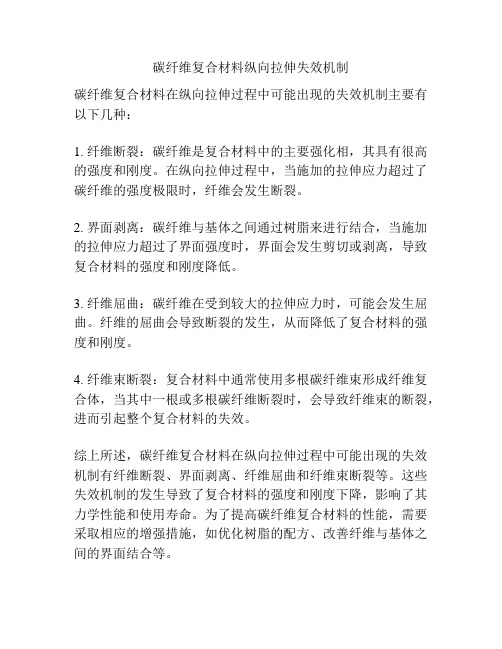
碳纤维复合材料纵向拉伸失效机制
碳纤维复合材料在纵向拉伸过程中可能出现的失效机制主要有以下几种:
1. 纤维断裂:碳纤维是复合材料中的主要强化相,其具有很高的强度和刚度。
在纵向拉伸过程中,当施加的拉伸应力超过了碳纤维的强度极限时,纤维会发生断裂。
2. 界面剥离:碳纤维与基体之间通过树脂来进行结合,当施加的拉伸应力超过了界面强度时,界面会发生剪切或剥离,导致复合材料的强度和刚度降低。
3. 纤维屈曲:碳纤维在受到较大的拉伸应力时,可能会发生屈曲。
纤维的屈曲会导致断裂的发生,从而降低了复合材料的强度和刚度。
4. 纤维束断裂:复合材料中通常使用多根碳纤维束形成纤维复合体,当其中一根或多根碳纤维断裂时,会导致纤维束的断裂,进而引起整个复合材料的失效。
综上所述,碳纤维复合材料在纵向拉伸过程中可能出现的失效机制有纤维断裂、界面剥离、纤维屈曲和纤维束断裂等。
这些失效机制的发生导致了复合材料的强度和刚度下降,影响了其力学性能和使用寿命。
为了提高碳纤维复合材料的性能,需要采取相应的增强措施,如优化树脂的配方、改善纤维与基体之间的界面结合等。
碳纤维复合材料楔形件压铆过程的数值模拟

碳纤维复合材料楔形件压铆过程的数值模拟杜宝瑞;李振宇;屈力刚;李静【摘要】为了研究碳纤维复合材料楔形件压铆过程中铆钉的成型规律和复材损伤失效情况,在ABAQUS中建立了复合材料楔形件双面埋头压铆的分析模型.对ABAQUS进行二次开发,创建碳纤维复合材料的VUMAT用户子程序材料模型,材料模型采用三维Hashin失效准则作为累计损伤的判据,并使用合理的材料退化方式对损伤部位的刚度系数进行折减,来模拟复合材料的失效情况.通过有仿真模拟,得到了铆钉在压铆过程中的应力应变分布规律和材料流动趋势,以及复合材料层合板的损伤类型和损伤区域,为复合材料楔形结构铆接工艺的设计提供了一种参考依据.【期刊名称】《锻压装备与制造技术》【年(卷),期】2018(053)003【总页数】5页(P98-102)【关键词】碳纤维复合材料;楔形结构;压铆;仿真模拟;失效准则【作者】杜宝瑞;李振宇;屈力刚;李静【作者单位】沈阳航空航天大学机电工程学院,辽宁沈阳110136;沈阳航空航天大学机电工程学院,辽宁沈阳110136;沈阳航空航天大学机电工程学院,辽宁沈阳110136;沈阳航空航天大学机电工程学院,辽宁沈阳110136【正文语种】中文【中图分类】V260.5飞机在高速飞行中,要求采用密封铆缝和受力蒙皮,要求部件外表面具有精确的外形,而且对精加工的质量要求很高,这样就提高了对铆接结构的连接和装配工艺的要求[1]。
为了达到上述要求可以从提高连接部位连接质量、连接强度、加工精度和轻量化等方面着手,所以使得碳纤维复合材料等具有较低密度但高强度的材料得到广泛使用[2-4]。
但是目前国内各航空企业对复合材料楔形件的双面埋头铆接采用的是锤铆的方式[5-8]。
劳动强度大,铆接质量主要取决于操作者的技术水平,并且操作者的工作效率也比较低[9]。
为了解决上述难题,遂开展了复合材料楔形部件双面埋头压铆工艺方面的研究。
传统铆接工艺实验过程需要消耗大量财力和人力,且实验耗费时间较长[10-12]。
两种国产T800级碳纤维界面状态及复合材料力学性能研究

第1期纤维复合材料㊀No.1㊀32024年3月FIBER ㊀COMPOSITES ㊀Mar.2024两种国产T800级碳纤维界面状态及复合材料力学性能研究王㊀涵,周洪飞,张㊀路,李是卓(中航复合材料有限责任公司,北京100000)摘㊀要㊀研究了两种国产T800级碳纤维界面状态及复合材料力学性能,结果表明,与B 类纤维相比,A 类纤维表面形貌粗糙度高约23%㊁O /C 含量高约7.4%㊁活性C 含量高约20%,微观剪切强度高约10%,A 类纤维增强的复合材料冲击后压缩强度比B 类纤维高约8%㊂A 类纤维与树脂形成更好的化学与物理结合,界面结合作用较好㊂关键词㊀T800级碳纤维;界面;表面活性;力学性能Study on the Interface State of Different Domestic T 800Carbon Fibers and the Mechanical Properties of CompositesWANG Han,ZHOU Hongfei,ZHANG Lu,LI Shizhuo(AVIC Composites Co.,Ltd.,Beijing 100000)ABSTRACT ㊀The interface state and mechanical properties of two kinds of domestic T800carbon fibers were studied.The results showed that compared with class B fibers,the surface roughness of class A fibers was about 23%higher,the O /C content was about 7.4%higher,the active C content was about 20%higher,and the microscopic shear strength was about 10%higher.The compressive strength of Class A fiber reinforced composites after impact is about 8%higher than that of class B fiber.Class A fiber and resin form a better chemical and physical bond,and the interface bond is better.KEYWORDS ㊀T800carbon fiber;interface;surface activity;mechanical properties项目支持:国家重点研发计划资助(2022YFB3709100)通讯作者:周洪飞,男,研究员㊂研究方向为先进树脂基复合材料㊂E -mail:wanghan6583@1㊀引言碳纤维复合材料是由增强体碳纤维和基体树脂复合而成,具有明显优于原组分性能的一类新型材料[1],具有较高的比强度㊁高比模量和优异的耐腐蚀的性能,被广泛的应用于航空㊁船舶㊁航天等领域㊂在碳纤维复合材料里,碳纤维起到增强作用,承接作用力和传递载荷,树脂作为基体通过界面作用将载荷传递到纤维㊂因此当复合材料受到外力作用时,界面起到传递载荷的作用就显得尤为重要,界面的性质和状态直接影响复合材料的综合力学性能[2],是影响复合材料力学性能的关键点,也是近期国内外学者研究的热点之一㊂碳纤维增强树脂基复合材料的界面不是特指增纤维复合材料2024年㊀强体纤维和基体树脂之间的单纯几何层,而是泛指纤维与树脂之间的包括几何层在内的界面层[3]㊂在该结构层内,增强体纤维与基体树脂的微观结构与性质都存在不同程度的差异,这不仅取决于纤维与树脂的结构和性质,还受到复合材料固化工艺㊁成型工艺等其他因素影响,如碳纤维在出厂前会进行上浆处理,上浆剂的浓度㊁厚度及种类都会大大影响纤维与树脂的界面结合㊂目前国内外学者对纤维与树脂的界面结合提出几种理论,如化学键结合理论㊁机械啮合理论㊁树脂浸润理论等[4]㊂经过大量的实验研究,结果表明,纤维与树脂的界面结合不是由某一种理论完全解释的,这是多种作用相互协调㊁共同作用的结果[5]㊂Thomsomn等人[6]通过对比多种纤维与多种树脂的界面结合实验,认为纤维与树脂复合使得纤维表面的分子链活动受到限制,根据界面浸润理论,纤维经过树脂浸润后,纤维选择性吸收树脂组分,而后表面形成一层具有刚性结构的界面层,当纤维增强复合材料经过一定温度㊁压力条件下固化成型后,界面层会变得非常复杂,界面层显得更加尤为重要[7]㊂而化学键理论认为,纤维与树脂结合的过程中,主要是范德华力起主导作用[8]㊂目前对于纤维与树脂的界面表征主要包括纤维微观结构㊁纤维表面活性以及纤维与树脂的界面结合强度㊂纤维微观结构可以通过扫描电镜㊁原子力纤维镜等手段实现,纤维表面活性可以通过IGC直接测得纤维活化能,也可以通过间接方式XPS对纤维表面元素及官能团表征计算,从而间接获得纤维活化能;或者通过接触角实验,纤维与不同极性和非极性溶剂接触,通过接触力衡量纤维表面活性㊂纤维与树脂的界面结合强度主要有微脱粘实验和复合材料层间剪切强度,前者是单丝级别,后者是宏观力学级别,数据可靠度都很高,也是目前国内外大量学者常用的表征纤维与树脂界面的方式㊂本文首先通过观察纤维表面形貌㊁测试纤维表面原子含量和纤维与树脂微观结合力,对比两种国产T800级碳纤维界面状态,并制备了复合材料层合板,目的为国产T800级碳纤维应用及其增强的复合材料界面性能研究提供一定的数据支撑和参考意义㊂2㊀实验材料及方法2.1㊀原材料实验采用两种同级别但不同界面的国产A类碳纤维和B类碳纤维,两种纤维的具体信息如表1所示,实验所用树脂为某国产高性能高温环氧类树脂㊂表1㊀两种纤维基本信息批次拉伸强度/MPa拉伸模量/GPa断裂伸长率/%线密度/(g/km)体密度/(g/cm3)直径/mm长㊁短径比A6324300 2.10450 1.8 5.10 1.04 B6334297 2.13453 1.8 5.13 1.02㊀㊀2.2㊀试样制备2.2.1㊀碳纤维去上浆剂碳纤维在出厂前会在表面涂刷一层上浆剂,目的减少纤维在后续使用过程中造成的磨损㊁打结和并丝现象发生,提高纤维集束性,增加纤维与树脂的浸润性,保护纤维[9]㊂为了更加直观清晰的观察和研究碳纤维本征性能与碳纤维增强树脂基复合材料界面之间的关系,需要对已经上过浆的碳纤维进行去剂㊂本实验按照国标中索式萃取试验方法对两种不同界面的国产T800级A类碳纤维和B类碳纤维进行去剂处理㊂首先将一定长度的碳纤维放置在温度23ʃ2ħ㊁相对湿度50ʃ10%的标准环境下调湿6h以上,将调湿后的碳纤维放置于索氏提取器中,并加入足量的丙酮以确保回流循环,调节加热炉功率,使索氏提取器2h至少完成8次循环,而后萃取36h,关掉加热炉㊂经过一定时间萃取后的碳纤维从索氏提取器中取出,冷却10min,放置于105ʃ5ħ的鼓风烘箱内干燥5h,最后再放入干燥器中进行冷却,温度降至室温即可㊂2.2.2㊀微脱粘制样制备将单根碳纤维(单丝)从碳纤维试样丝束中分离出来,将其拉直并粘贴在回型支架上,如图1所示,高性能高温环氧类树脂在烘箱内50ħ保温30 min,再与二氯乙烷10ʒ1的比例配制树脂液,并迅速搅拌均匀,将配制好的树脂液常温下在真空烘箱里抽真空20min,取出树脂,用大头针蘸取少量配制好的树脂液,轻涂抹于碳纤维单丝上,将试样放于鼓风烘箱里在130ħ下固化30min㊂4㊀1期两种国产T800级碳纤维界面状态及复合材料力学性能研究图1㊀微脱粘试样示意图2.3㊀测试与表征使用Quanta 450FEG 场发射扫描电子显微镜(SEM)两种不用界面的T800级碳纤维表面形貌㊂将一束碳纤维用手术刀平齐切断,分别用导电胶带将平齐切断的碳纤维垂直粘贴在铝制载物台上,对粘在导电胶上的纤维表面喷金,经过两次喷金后放入SEM 内观察,电子加速电压为20~50kV,束流1pA,放大倍数50~8000X㊂采用Dimension ICON 原子力显微镜(AFM)观察碳纤维三维立体形貌,通过探针针尖与样品微弱作用力获取纤维表面粗糙度,扫描面积为5μm ˑ5μm,扫描频率为1.0Hz㊂采用X 射线光电子能谱仪(美国ThermoFisch-er,ESCALAB 250Xi)测试碳纤维表面元素组成及化学官能团,分析室真空度8ˑ10-10Pa,激发源采用Al ka 射线(hv =1486.6eV),工作电压12.5kV,灯丝电流16mA,进行5~10次循环的信号累加㊂通过微脱粘试验测试纤维与树脂的微观剪切性能㊂将带有已经固化好的尺寸均匀且正圆的树脂小球碳纤维固定在微脱粘仪器上,移动卡刀,使其将其中一个树脂小球从左右两侧卡住,移动回形架使得纤维匀速自下而上移动,直至卡刀恰好将树脂小球剥落,此时仪器会记录纤维与树脂小球分离瞬间的最大结合力,如何计算纤维与树脂的微观界面结合强度如公式(1)所示㊂IFSS =F max ΠDL(1)式中,IFSS 为纤维与树脂微观界面剪切强度;F 为树脂与纤维剥离时的最大剪切力;L 为纤维迈入树脂球的长度㊂碳纤维增强树脂基复合材料力学性能在Intron 公司的Instro5967万能力学试验机上进行㊂复合材料冲击后压缩强度按照ASTMD7137开展㊂3㊀结果与讨论3.1㊀碳纤维表面形貌两种不同界面的国产T800纤维去除上浆剂后的表面形貌SEM 如图2所示,由图A (a)和A (b)看出未上浆的A 类碳纤维表面整体光滑,但具有相对明显的沿着轴向排列均匀分布的较浅沟槽,由A (c)可看出,纤维截面致密,形状呈正圆形,具有明显的干喷湿纺纺丝工艺特征,干喷湿纺工艺生产的碳纤维兼具了拉伸强度和机械啮合的优势[10]㊂与A 类纤维相比,B 类纤维表面明显沟槽更浅,根据界面机械啮合理论,纤维表面沟槽的数量越小㊁深度越浅,纤维与树脂的界面结合面积越小,界面结合强度越弱㊂图2㊀两种碳纤维表面形貌图5纤维复合材料2024年㊀㊀㊀为了进一步对比两种碳纤维界面状态,采用AFM 对其观察三维立体形貌,如图3所示,由图3可以看出,A㊁B 类纤维表面存在明显的沿着纤维轴向排列的深浅不一沟槽,但A 类沟槽深度更深,数量更多,对两类碳纤维随机抽取三个试样进行粗糙度测试,数据如表2所示,A 类纤维平均粗糙度要高于B 类纤维约23%,根据界面机械啮合理论,纤维表面积越大,粗糙度越高,纤维与树脂结合越牢固㊂图3㊀两种纤维三维表面形貌图表2㊀两种纤维表面粗糙度序号A B 130524622972513303237平均值/nm302245CV1.382.90㊀㊀3.2㊀碳纤维表面元素及含氧官能团通过XPS 表征测试两种碳纤维表面化学特性,如图4所示,对XPS 图谱分峰处理,纤维表面主要存在C㊁O㊁Si㊁N 四种元素,纤维表面原子含量具体如表3所示,数据显示A 类纤维O /C 含量略高于B 类,约7.4%㊂而经过阳极氧化处理过的碳纤维表面O 含量越高,表面活性越高,纤维与树脂的界面结合越牢固㊂图4㊀两种碳纤维XPS 峰图6㊀1期两种国产T800级碳纤维界面状态及复合材料力学性能研究表3㊀两种碳纤维表面原子含量样品Si2p /%C1s /%N1s /%O1s /%102.02eV 284.49eV 399.48eV 532.23eV Si㊁N 总量/%O /C /%A (a) 3.1373.24 3.6819.95 6.8127.24A (b) 2.3774.31 3.4619.86 5.8326.73A (c) 2.2975.22 3.1719.32 5.4625.68B (a) 3.8174.25 4.117.857.9124.04B (b) 2.4774.96 3.818.76 6.2725.03B (c)2.6975.223.7718.32 6.4624.36㊀㊀利用C1s 电子XPS 窄扫描,并对测试后的C1s 图谱进行分峰处理,分峰图如图5所示,碳纤维含C 官能团具体含量如表4所示,其中C -O㊁C =O 为活性C,C -C 为非活性C,活性C 占比越高,纤维表面活性越高,整体来看,与B 类纤维相比,A 类纤维表面原子中活性C 含量更高,即其表面活性更高,根据界面化学键结合理论,这意味着A 类碳纤维与树脂的界面结合强度较高㊂图5㊀两种碳纤维C1s 分峰图表4㊀C1s 分峰结果样品C -C /%C -O /%C =O /%284.8eV 286.39eV 288.85eV 活性碳比例/%A (a)67.3729.94 2.6948.43A (b)64.3133.46 2.2355.50A (c)67.530.32 2.1848.15B (a)73.3719.467.1736.30B (b)68.6129.36 2.0345.75B (c)69.6128.36 2.0343.66㊀㊀3.3㊀单纤维/树脂微脱粘采用微脱粘法从微观角度测试两种不同界面的T800级碳纤维与树脂的界面结合作用,具体数据如表5所示,数据显示A 类纤维与高性能环氧树脂的界面剪切力高于B 类纤维约10%,即A 类纤维与该树脂界面结合作用更强㊂㊀㊀3.4㊀复合材料宏观力学性能制备A㊁B 类纤维增强复合材料层合板,并按照ASTM D7137(6.67J /mm)进行冲击后压缩强7纤维复合材料2024年㊀度测试,测试结果如表6所示,表中数据显示两类纤维增强树脂基复合材料均具有较高的冲击后压缩强度,但相比与B类纤维,A类纤维增强树脂基复合材料冲击后压缩强度要高于B类约8%,这可能归功于A类纤维与树脂的界面结合牢固所致㊂表5㊀两批次T800级碳纤维与某高温环氧树脂界面剪切强度样品界面剪切强度平均值/MPa CV/%A(a)120.15 5.03A(b)118.358.08A(c)119.357.61B(a)112.04 4.41B(b)110.37 4.48B(c)103.23 5.36表6㊀纤维增强复合材料冲击后压缩强度序号A类纤维复合材料/MPa B类纤维复合材料/MPa 1348313 2330299 3338318 4326311 5335311 6342321平均值337312CV/% 2.38 2.434㊀结语实验选取了两种不同界面的国产T800级碳纤维及复合材料力学性能,通过对其界面状态和复合材料力学研究,结果表明,相同级别的T800级国产碳纤维,A类纤维表面形貌粗糙度高于B类约23%㊁O/C含量高约7.4%㊁活性C含量高约20%,微观剪切强度高约10%㊂A类纤维增强的复合材料冲击后压缩强度比B类纤维高约8%㊂即A 类纤维与树脂形成更好的化学与物理结合,界面结合作用较好㊂参考文献[1]贺福.碳纤维及其应用.北京:化学工业出版社,2004.[2]梁春华.高性能航空发动机先进风扇和压气机叶片综述[J].航空发动机,2006(03):48-52.[3]王运英,孟江燕,陈学斌,白杨.复合材料用碳纤维的表面技术.处理技术,36(3):53-57.[4]陈祥宝,张宝艳,邢丽英.先进树脂基复合材料技术发展及应用现状.中国材料进展,2009,28(6):2-11. [5]易楠,顾轶卓,李敏.碳纤维复合材料界面结构的形貌与尺寸表征[J].复合材料学报,2010,27(5):36-40. [6]Thomson A W,Starzl T E.New Immunosuppressive Drugs:Mecha-nistic Insights and Potential Therapeutic Advances[J].Immunolog-ical Reviews,1993,136(1):71-98.[7]张巧蜜.聚丙烯腈基碳纤维[M].东华大学出版社,2005-7.[8]何宏伟.碳纤维/环氧树脂复合材料改性处理[M].国防工业出版社,2014.[9]谢云峰,王亚涛,李顺常.碳纤维工艺技术研究及发展现状[J].可化工新型材料,2013,41(5)-27. [10]张焕侠.碳纤维表面和界面性能研究及评价[D].东华大学, 2014.8。
纤维缠绕复合材料管道等径三通的强度分析

材料弯管的强度 , 岑章志等 对各 向同性管道三通作了应力分析。本文根据复合材料的经典强度理
论— —Ta— si Wu失效 准则 , 利用有 限元分 析软件 A S S对 复合 材料 管道等 径三通 进行强度 分析 , NY 预测 了 复合 材料管道 三通破 坏点 , 推导 了复合材 料管道 三通 的承载 能力及 其影 响因素 , 为分析复 合材料 管道三 通 的强度提供 了一种 有效 的方法 , 方法 可 以为复合材 料管道 三通 的设计 制造提 供参考 。 该
itr a p e s r e sr s l b o u e n T p p d f r n au fsrn t a t r a s d b i ee td r cin ff e , ne n r su e t t swi fc s d o ie, i e t l e o t g h fc sa e c u e y d f rn i t s o b r l h e le e v e e o i a d t e s e gh i b s w e h n l ff ri i ew e 0 a d 6 。 T e rs l p o ie n e i in e ee c e d sg n t n t e t h n te a g eo b n b t e n 5 。 n 0 . h e ut r vd sa f ce t fr n e t t e i — h r s i e s r oh n n n n fc u n ff rr i oc d p a t s pp e s ig a d ma u a t r g o b en re lsi ie te . i i e f c
元分析 软件 , 对纤 维缠 绕 复合 材料 管道等 径三通 强度进行 分析 。分析 结果表 明 , 复合 材料
基于内聚力模型的碳纤维与钢复合结构断裂性能分析

-机械研究与应用-2019年第6期(第32卷,总第164期)研究与试验doi:10.16576/ki.1007-4414.2019.06.011基于内聚力模型的碳纤维与钢复合结构断裂性能分析”王少勃,王斌华(长安大学道路施工技术与装备教育部重点实验室,陕西西安710064)摘要:针对复合结构的粘接界面断裂性能分析,在有限元软件ABAQUS中基于CZM(Cohesive Zone Model)中的co-hesive单元来模拟粘接层并建立有限元模型,模拟分析了钢板和碳纤维树脂粘接界面的损伤情况,得到了碳纤维与钢I型断裂的载荷位移曲线,并通过双悬臂梁实验测试验证了模拟结果的准确性,为实际工程结构加固提供指导。
关键词:复合结构;粘接界面;CZM;有限元法中图分类号:TB331文献标志码:A文章编号:1007-4414(2019)06-0033-02Analysis of Bonding Properties of Carbon Fiber and Steel Composite Structure Based on CZMWANG Shao-bo,WANG Bin-hua(Key Laboratory far Highway Construction Technology and Equipment of Ministry of Education,Chang'an University,Xi'an Shaanxi710064,China)Abstract:For the analysis on the fracture properties of the bonded interface of the composite structure,the cohesive element in CZM(Cohesive Zone Model)was used to simulate the bonding layer and establish the finite element model in the finite element software ABAQUS.The damage of the bonding interface between the steel plate and the carbon fiber was simulated and analyzed.In the case,the load-d isplacement curves of carbon fiber and steel type1fracture were obtained,and the accuracy of the simulation results was verified by double cantilever beam experimental test.It would provide guidance for the reinforce・ment of actual engineering structures.Key words:composite structure;bonding interface;CZM;finite element method0引言近年来,随着复合材料的开发,复合材料的力学性能不断提高、生产成本随之降低、材料性能成熟稳定,已广泛应用于钢结构的修复和加固中。
油气管道碳纤维复合材料修复技术及应用

油气管道碳纤维复合材料修复技术及应用李枢一;张建兴;赵丽恒;张宇坤;辛成庆【摘要】随着管道完整性管理的应用和发展,开展管道修复受到了极大的关注.针对碳纤维复合材料修复技术的现状,国内外公司都致力发展相应的碳纤维复合材料修复技术.通过实例介绍了碳纤维复合材料修复技术应用于带有焊接补丁缺陷的天然气管道,取得较好的修复效果,使管道安全运行得到了保证.【期刊名称】《管道技术与设备》【年(卷),期】2013(000)002【总页数】3页(P38-40)【关键词】油气管道;碳纤维;补强;修复【作者】李枢一;张建兴;赵丽恒;张宇坤;辛成庆【作者单位】中石化天然气榆济管道分公司,山东济南250101【正文语种】中文【中图分类】TE88随着对油气资源需求的不断增加,国内油气管道事业快速发展。
然而随着管道总长度的增加,由于外力损伤、腐蚀、管材缺陷等原因[1],油气管道失效事故频繁发生。
许多早期建设的油气管道运行年限已接近或超过其设计寿命,进入事故多发期。
相关资料表明[2-3]:国内早期投用的油气管道的爆裂事故高达7~10次/(km·a),每年用于更新和维修旧管道的费用约占新建管道总投资的10%~20%,每年因外腐蚀造成的管道更换率达到2.5%。
因此,为了避免因管道事故而造成的巨大损失,需要开展管道修复工作。
随着检测技术、检测设备和修复技术等的发展,管道完整性管理也得到了发展。
碳纤维复合材料修复技术主要是利用碳纤维复合材料的高强度特性,采用粘结树脂在缺陷管道上缠绕一定厚度的纤维层,树脂固化后与管道结成一体,从而恢复缺陷管道的强度。
由于碳纤维复合材料修复具有不需动火焊接、工艺简单、施工迅速、操作安全、可实现不停输修复,并且成本相对较低等优势,已被管道行业普遍接受。
1997年,国外成功地将碳纤维复合材料修复技术应用在埋地钢质管道上[4]。
1.1 碳纤维复合材料修复技术进展情况随着复合材料的广泛应用,各国管道行业都致力于发展这项新技术,主要有国外的Armor Plate、T.D.Williamson、Neptune Research、3X Engineering、Furmanite等公司和国内的北京安科管道工程科技有限公司等,相应开发出Clock Spring、Armor Plate Pipe Wrap、Syntho-Glass®、Black-DiamondTM和AnkoWrapTM等一系列复合材料修复技术,这些修复技术在工程上都得到了很好的应用。
纤维缠绕CFRP圆管力学性能的试验及数值模拟研究
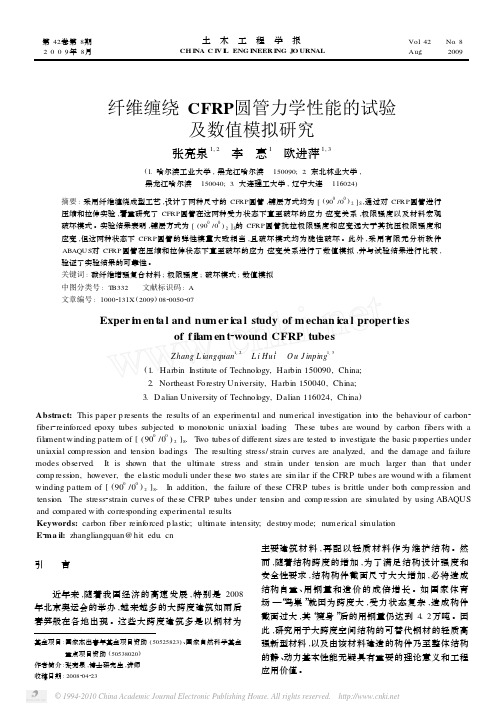
东丽公司 )和环氧树脂 , 其性能见表 1 和表 2, 纤维按 纵向和环向铺设 , 纵向纤维主要提供抗拉和抗压能 力 ,环向纤维作为环向补强 , 并抵抗偶然横向剪力 , 铺 0 0 层方式为 [ ( 90 /0 ) 2 ] S ,共 8 层 。
第 42 卷第 8 期 2 0 0 9 年 8月
土 木 工 程 学 报
CH INA C IV I L ENG INEER ING JO URNAL
Vol . 42 No. 8 Aug . 2009
纤维缠绕 CFRP圆管力学性能的试验 及数值模拟研究
张亮泉
1, 2
李 惠 欧进萍
2009 年
2 CFRP 管的拉伸和压缩试验的加载设备及采集
系统 试验是在哈尔滨工业大学力学与结构实验中心 的美国 M TS公司电液伺服试验机上进行的 。该试验 机最大拉 、 压载荷为 2500kN。 受压试件管内布置钢帽与 M TS试验机接触 ,通过 钢帽将荷载传递给试件 , 使试件受压 。试件的加强端 外套钢环 ,增加端部约束 ,保证荷载的正确传递 。 受拉试件管内也布置钢帽 , 但是在管的加强端粘 接长为 150mm 的钢外环 , 粘接材料为环氧树脂 、 固化 剂、 铁砂和增进剂的混合物 ,比例为 20 ∶ 6∶ 30 ∶ 1。这样 就可以将试件的加强端直接夹持在 M TS 试验机的上 下夹头上 ,施加荷载
在这些准则破坏面是以有效的应力空间有效抗力作用面上的应力表述的考虑了四种不同的破坏触发的机理1纤维受拉112纤维受压113基体受拉224基体受压222s2stycsl在公式xt为纤维增强复合材料在纤维方向的抗拉强度xc为纤维增强复合材料在纤维方向的抗压强度yt为纤维增强复合材料在垂直于纤维方向的抗拉强度yc为纤维增强复合材料在垂直于纤维方向的抗压强度sl为纤维增强复合材料纵向剪切强度st为纤维增强复合材料横向剪切强度一般中可以看出无论是压缩试验还是拉伸12是评估触发准则时使用的有效应力向量成分由公式5得到单向cfrp材料的力学参数tableunidirectionacfrpxtmpa1229
- 1、下载文档前请自行甄别文档内容的完整性,平台不提供额外的编辑、内容补充、找答案等附加服务。
- 2、"仅部分预览"的文档,不可在线预览部分如存在完整性等问题,可反馈申请退款(可完整预览的文档不适用该条件!)。
- 3、如文档侵犯您的权益,请联系客服反馈,我们会尽快为您处理(人工客服工作时间:9:00-18:30)。
参数值
0.69
29.6
0.69
注:①x、y、z 分别对应管道径向、轴向和环向方向;G 为切 变模量
采用耦合的 FEM/EFG 数值计算方法对碳纤维 缠绕修复压力管道进行数值分析。为了减少计算 量,考虑到含裂纹压力管道结构的对称性,取 1/4 部分作为计算模型。在裂纹前沿附近区域采用 EFG 节点离散,其余区域采用 FEM 单元离散, 充分利用了有限元方法的计算高效率和无网格方
⎝b⎠
⎝b⎠
式中,2a 为裂纹长度;2b 有限宽板宽度。由上述
公式计算得到的应力强度因子的理论值为 245.4
MPa ⋅ mm−1/ 2 。耦合的 FEM/EFG 方法计算得到的 应力强度因子与该计算值的比较如图 3 所示。由 图 3 可知,2 种方法的计算结果一致,除上下表 面 2 点的应力强度因子外,两者间的最大相对误
图 6 修复前 FEM/EFG 数值模型 Fig. 6 FEM/EFG Numerical Model with
Through-Wall Crack before Repair
图 8 不同套袖长度的横向贯穿裂纹应力强度因子 Fig. 8 Stress Intensity Factors of Traverse Through-
图 3 中心裂纹板应力强度因子 Fig. 3 Stress Intensity Factors of Center Cracked Panel
差不超过 0.6%。由于理论公式没有考虑表面效 应,所以上下表面处的应力强度因子不便比较。
3 含裂纹压力管道碳纤维复合材料缠绕 修复技术
压力管道中的裂纹分为表面裂纹和贯穿裂 纹;表面裂纹又分为内表面裂纹和外表面裂纹。 目前普遍采用破前漏技术(LBB)对压力管道裂 纹进行安全性评估,将压力管道中的表面裂纹简 化为椭圆型裂纹(图4a)。贯穿裂纹的简化如图4b 所示,裂纹前沿与管径方向一致。
第 32 卷 第 2 期 2011 年 4 月
文章编号:0258-0926(2011)02-0048-06
核动力工程
Nuclear Power Engineering
Vol.32. No.2 Apr. 2011
碳纤维复合材料缠绕修复的压力管道断裂分析
柳 军 1,严 波 1 ,卢岳川 2,孙英学 2,姜乃斌 2,常学平 3
1 2
θ
−
cos
3 2
θ
⎤ ⎥⎦
+
K II
⎢⎣⎡(9
−
8ν
)sin
1θ 2
+
sin
3 2
θ
⎤⎫ ⎥⎦⎭⎬
(9)
v = 1+v 4E
2r π
⎧ ⎨KI ⎩
⎢⎣⎡(7
−
8ν
)cos
1 2
θ
−
sin
3 2
θ
⎤ ⎥⎦
+
K II
⎢⎣⎡(3
−
8ν
)cos
1θ 2
+
cos
3θ 2
⎤⎫ ⎥⎦⎭⎬
(10)
式中, E 为材料弹性模量;v 为泊松比;KI、KII
(2)
[ qM = uˆ1 vˆ1 wˆ1 " uˆi vˆi wˆi "
] uˆm vˆm wˆ m T
(3)
式中,u、v、w 分别为 x、y、z 方向的位移;下
标 n 和 m 分别为 FEM 和 EFG 节点数。
收稿日期:2010-01-05;修回日期:2010-09-12 基金项目:核反应堆系统设计技术国家级重点实验室基金资助(ZDS-A-0908)和四川省青年基金资助(09ZB101)
(1. 重庆大学工程力学系,重庆,400044;2. 中国核动力研究设计院核反应堆系统设计 技术重点实验室,成都,610041;3. 西南石油大学工程力学系,成都,610500)
摘要:采用耦合的有限元-无网格 Galerkin 数值算法,计算了碳纤维增强型复合材料缠绕修复的压力管道 横向贯穿裂纹以及横向椭圆型表面裂纹前沿应力强度因子,据此分析了碳纤维增强型复合材料套袖长度对压 力管道裂纹应力强度因子的影响。结果表明,本文所提算法能有效计算三维问题应力强度因子;含裂纹压力 管道采用碳纤维增强型复合材料缠绕修复后,裂纹前沿的应力强度因子显著降低;修复套袖越长,修复效果 越显著,但套袖长度超过一定范围后,应力强度因子的降低趋于缓慢,对修复效能的进一步提高贡献甚微。
柳 军等:碳纤维复合材料缠绕修复的压力管道断裂分析
49
为了满足 2 子域交界面上位移连续性要求,
如果一个节点 i 处于交界面上且属于 FEM 子域的
某个单元中的一个节点,则该节点的位移由 EFG
子域中节点位移通过插值的形式得到。该单元节
点位移矢量可以由式(2)表示如下:
[ q~F,e = u1 v1 w1 " uˆi1 vˆi1 wˆ i1 "
分析的典型含裂纹压力管道外直径为 323.9 mm,壁厚为12.7 mm,E=2.07×105 MPa, ν = 0.3 ,工作内压均匀分布在管内壁,p=4.0 MPa, 远端横截面上作用有由内压引起的等效反力。采 用碳纤维增强型复合材料对裂纹区域进行缠绕修 复。在缠绕区域涂上油灰(图5);油灰厚1 mm; 油灰材料E=1.74×103 MPa,ν = 0.45 ;碳纤维增强 型复合材料修复层厚7 mm。材料性能参数见表1。
关键词:有限元-无网格耦合算法;裂纹压力管道;碳纤维复合材料;缠绕修复;应力强度因子 中图分类号:O346. 1 文献标识码:A
1引言
碳纤维增强型复合材料(CFRC)在各种航天 结构、船舶结构和建筑结构的修复中显示了明显 的优势[1~3]。使用该型材料修复压力管道是一种较 新的技术,目前对这一技术的研究还很有限。 Wilson等对碳纤维/环氧树脂复合材料修复压力 容器缺陷进行了断裂分析实验;结果表明这种修 复方法效果很好,修复后的压力容器强度接近无 缺陷的压力容器[4]。Cereone等给出了不同工作环 境下管道修复用复合材料的选择方法[5];Liu等提 出了一种碳纤维缠绕修复管道方法[6];Duell等针 对压力管道的腐蚀性缺陷提出了另一种碳纤维缠 绕修复管道方法,并分别采用有限元方法和实验 方法分析了这种修复方法的效果[7];Ha等提出采 用玻璃纤维缠绕方法修复地下管道[8];Houssam等 对各种纤维增强型复合材料缠绕修复压力管道进 行了研究,分析了不同套袖下损伤管壁的环向应 力分布,指出碳纤维修复压力管道的效果要优于 其他纤维增强型复合材料[9]。
本文采用一种耦合的有限元-无网格Galerkin
数值算法(FEM-EFG)对碳纤维缠绕修复压力管
道裂纹前沿应力强度因子进行计算,研究了压力
管道横向贯穿裂纹和横向表面椭圆型裂纹应力强
度因子分布规律,并比较了修复前后的裂纹前沿
ห้องสมุดไป่ตู้
应力强度因子,最后分析了CFRC套袖长度对修复 效果的影响。
2 应力强度因子的数值计算方法
] uˆij vˆij wˆ ij " uˆk vˆk wˆ k (4)
式中,下标 k 为 FEM 单元节点数;j 为 EFG 子域
中节点 i 影响域内的 EFG 节点数。该单元节点位
移矢量可通过转换矩阵表示为:
qF,e = T q~F,e
(5)
式中,qF,e 为未考虑耦合作用的 FEM 子域的单元
柳 军等:碳纤维复合材料缠绕修复的压力管道断裂分析
51
法的高精度性的特点(图 6、图 7)。在远离裂纹 前沿的区域可以设置较为稀疏的网格或节点,在 裂纹前沿附近区域可以设置密集节点,不存在常 规有限元中单元畸变问题。计算中,位于管道纵 向切开截面上的节点 x 方向的位移被约束,位于 横向切开截面上的节点(裂纹面上节点除外)z 方向的位移被约束,为了限制管道刚体位移,横 向切开截面最下端节点 y 方向位移被约束。
为裂纹应力强度因子。
利用耦合的 FEM/EFG 方法计算得到位移场 后,可用直接位移法计算应力强度因子[13]。对于
I 型裂纹,只需计算 KI。令θ = π ,由式(10)可 以得到裂尖附近的节点位移:
图 1 裂纹尖端局部坐标系 Fig. 1 Local Co-Ordinate in Vicinity of Crack Tip
得到相应裂尖处的应力强度因子。
为了模拟裂纹尖端附近的应力1 r 奇异性,
在无网格 Galerkin 方法中采用如下形式的增强型
基函数:
{ } P = 1 x y z r
(13)
式中,P 为基函数向量;x、y、z 为笛卡尔坐标;
r 为当前位置与裂尖的距离。
2.3 数值算例
中心裂纹板的几何尺寸为70 mm×50 mm×
碳纤维复合材料缠绕修复压力管道技术是利
a 横向表面裂纹
b 横向贯穿裂纹
图 4 裂纹形状 Fig. 4 Crack Shape
图 5 碳纤维复合材料缠绕修复压力管道 Fig. 5 Repair Cracked Pressure Pipe with
CFRC Wind-up
4 碳纤维复合材料缠绕修复压力管道数 值分析
个8节点六面体有限元背景网格。在计算得到位移
后,可采用直接位移法计算裂纹尖端的应力强度
因子。带贯穿中心裂纹的有限宽板的应力强度因
子可由下式计算[14]
KI = F ⋅σ πa
(14)
F = 1 + 0.128⎜⎛ a ⎟⎞ − 0.288⎜⎛ a ⎟⎞2 + 1.525⎜⎛ a ⎟⎞3 (15)
⎝b⎠
10 mm,中心裂纹长为2a=14 mm,板的两端承受
均匀拉力σ = 50 MPa 。考虑到结构和载荷的对称
性,取其1/4模型进行计算(图2)。裂纹尖端附近