消失模铸钢件气孔缺陷的分析及解决措施
消失模粘沙气孔 夹渣 的缺陷防治

3)在铸件的最高处或死角处设置集渣冒口;
4)制作模样时,加大模型顶部的加工余量,用金属切削的方法消除气和夹。
1)模样气化后生成大量气体和一定残渣,这是气孔和夹渣主要来源;
2)此外,浇注系统或内浇道结构不合理,容易使气体和残渣裹在铁水中,形成气孔和夹渣;
3)另外,浇注温度低,不能使气体和残渣充分排出也易产生气孔和夹渣。
解决措施
1)采用底注式浇注系统,提高浇注温度;
2)合理填砂造型,控制模样浇注时的发气量,提高涂层透气性,提高真空系统抽气能力,使气体及时排出;
解决措施
1)合理控制真空度和浇注温度,在保证浇注顺利进行的前提下,尽量降低真空度和浇注温度,以抑制高温金属液的穿透能力
2)应该分批加砂,改善振实设备,适当增加涂层厚度,提高涂层耐火度等。
2、气孔和夹渣
气孔和夹渣存在于铸件上部或死角处的表皮下,只有经过机械加工后才能看到。
产生原因
消失模铸造(简称EPC)是一种常见的铸造方式,但与普通砂型铸造相比,还有一些技术不成熟,易出现粘砂、气孔、夹渣缺陷。
粘砂
产生原因
1)浇注温度过高,实践证明适当的提高浇注温度有利于改善铸件表面质量,对于浇不足和表面皱皮也大有改善,但浇注温度太高会出现粘砂;
2)此外型砂充填紧实度不够,比如振实设备不理想、涂料透气性太高或涂层太薄等。
消失模铸造产生气孔的10种原因,7种解决工艺措施
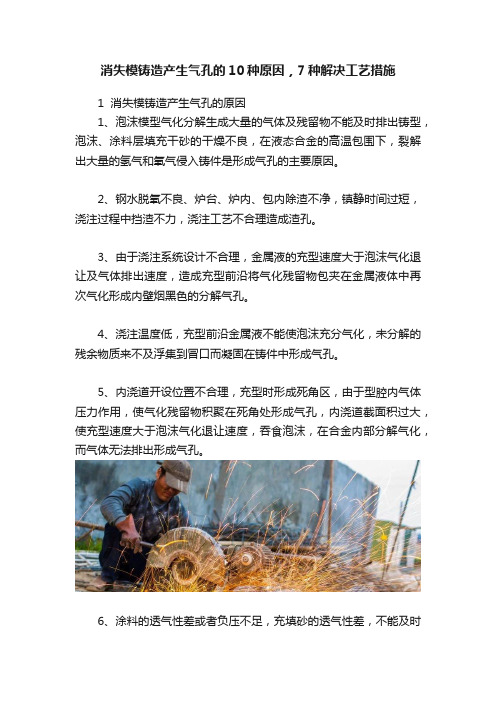
消失模铸造产生气孔的10种原因,7种解决工艺措施1 消失模铸造产生气孔的原因1、泡沫模型气化分解生成大量的气体及残留物不能及时排出铸型,泡沫、涂料层填充干砂的干燥不良,在液态合金的高温包围下,裂解出大量的氢气和氧气侵入铸件是形成气孔的主要原因。
2、钢水脱氧不良、炉台、炉内、包内除渣不净,镇静时间过短,浇注过程中挡渣不力,浇注工艺不合理造成渣孔。
3、由于浇注系统设计不合理,金属液的充型速度大于泡沫气化退让及气体排出速度,造成充型前沿将气化残留物包夹在金属液体中再次气化形成内壁烟黑色的分解气孔。
4、浇注温度低,充型前沿金属液不能使泡沫充分气化,未分解的残余物质来不及浮集到冒口而凝固在铸件中形成气孔。
5、内浇道开设位置不合理,充型时形成死角区,由于型腔内气体压力作用,使气化残留物积聚在死角处形成气孔,内浇道截面积过大,使充型速度大于泡沫气化退让速度,吞食泡沫,在合金内部分解气化,而气体无法排出形成气孔。
6、涂料的透气性差或者负压不足,充填砂的透气性差,不能及时排出型腔内的气体及残留物,在充型压力下形成气孔。
7、浇注速度太慢,未能充满浇口杯,暴露直浇道,卷入空气,吸入渣质,形成携裹气孔和渣孔。
8、浇口杯容量太小,金属液形成涡流,侵入空气生成气孔。
9、浇口杯与直浇道以及浇注系统之间的连接处密封不好,尤其是直浇道与浇口杯的连接密封不好,在负压的作用下很容易形成夹砂及气孔,这种现象可以用伯努利方程计算和解释。
10、型砂的粒度太细,粉尘含量高,透气性差,负压管道内部堵塞造成负压度失真,使型腔周围的负压值远远低于指示负压,气化物不能及时排出涂层而形成气孔或皱皮2 控制气孔缺陷的工艺措施1、选择适宜的模型材料采用共聚泡沫作模型材料,由于共聚物是拉链式分解,一次性气化程度高,液相比例小,小分子气体很容易从涂层溢出。
白模密度在强度和光洁度保证的前提下尽可能小一些,减少发气总量,浇注系统采用空心直浇道并加设过滤器,对液体合金进行机械挡渣、吸附梳流,使充型更平稳。
消失模铸造缺陷产生的原因及解决措施

消失模铸造缺陷产生的原因及解决措施一、消失模铸造缺陷的原因:1.模具设计不合理:模具的设计不合理是导致消失模铸造缺陷的主要原因之一、例如,模具的冷却系统设计不良或者模具结构不稳定,都会对铸件的形状和内部结构造成影响。
2.熔融金属冷却不均匀:熔融金属冷却不均匀也是导致消失模铸造缺陷的一个重要原因。
由于冷却速度不均匀,可能会导致铸件中出现热裂纹、气孔等缺陷。
3.模芯破损或散粘:消失模铸造过程中,如果模芯破损或散粘,会导致熔融金属进入模芯使其变形或者破裂。
4.硅溶胶合成不当:硅溶胶在消失模铸造中被用于形成陶瓷壳体,如果硅溶胶的合成过程不当,可能会导致模具的整体性能下降,从而产生各种缺陷。
5.炭化物形成不完全:在消失模铸造中,树脂炭化后形成的剩余炭化物对于确保铸件的完整性非常重要。
如果炭化物形成不完全,可能会导致铸件出现裂纹、气孔等缺陷。
二、消失模铸造缺陷的解决措施:1.设计合理的模具:在消失模铸造过程中,通过合理设计模具的冷却系统,可以提高铸件的冷却均匀性,减少缺陷的发生。
此外,模具的结构也应当稳定,以确保铸件形状和内部结构的准确性。
2.控制熔融金属温度和冷却速度:通过控制熔融金属的温度和冷却速度,可以减少热裂纹和气孔等缺陷的发生。
合理的工艺参数能够提高铸件的材质均匀性和密度。
3.检查模芯质量:在消失模铸造过程中,应该定期检查模芯的质量,以确保其完整性和稳定性。
如果发现模芯破损或者散粘,应及时更换或修复。
4.合理合成硅溶胶:在合成硅溶胶的过程中,应严格按照工艺要求进行操作。
确保硅溶胶的质量和性能,以避免模具整体性能下降。
5.控制炭化物的形成:合理控制炭化物的形成可以避免铸件的裂纹和气孔等缺陷的发生。
在树脂炭化的过程中,应注意控制炭化的温度和时间,确保炭化物的形成充分和均匀。
综上所述,消失模铸造缺陷的产生原因有模具设计不合理、熔融金属冷却不均匀、模芯破损或散粘、硅溶胶合成不当以及炭化物形成不完全等因素。
消失模铸造缺陷及解决措施

铸造缺陷及解决措施:1、砂眼(或白灰):是铸件的致命缺陷,重则报废。
要做到:①、浇口杯、直浇道、横浇道、内浇道与铸件封闭结合严密。
如不严密,在负压的作用下就会吸入砂子,所以装箱者一定要精心操作,把好各关口。
任何一个薄弱环节或疏忽都会造成此类缺陷。
②浇注系统多刷一遍涂料以增强其强度。
③涂料的强度、透气性、刚度、耐火度、暴热抗烈性也很重要,因为在运输、装填砂、震动时都会出现破坏、变形、开裂、脱落。
④震实时,开始幅度要小,待填满砂时再振幅大些。
⑤浇口杯无浮砂、尘土等杂物。
⑥浇注时,浇包嘴尽量靠近浇口杯,以免压力头过大。
⑦负压过大,使金属液流经开裂、裂纹处时,吸入干砂和杂物可能性加大,粘砂严重。
⑧过快的充型速度使冲刷力加大。
2、气孔:①浇注温度低,充型前沿金属液不能使泡沫充分分解汽化,未分解的残留物质来不及浮集到上面及冒口中,汽化分解生成的气体及残留物不能及时排出铸型而凝固在铸件中,另外,摸样分解不充分,液相残留物会堵塞涂料层,使热解气体排出受阻,腔内形成反压力,充型流动性下降,凝固快。
②涂料透气性差或负压不足,砂子透气性差,不能及时排除型腔内的气体及残留物,在充型压力下形成气孔。
③浇注速度慢,浇口杯未充满,暴露直浇道卷入空气,吸入杂质,形成携裹气孔和渣孔。
④浇杯容量小,金属液形成涡流,侵入空气生成气孔。
⑤浇口杯及浇注系统之间的连接处密封不好,尤其是直浇道和浇口杯。
在负压作用下很容易形成夹砂及气孔。
⑥型砂粒度太细,粉尘含量高,透气性差,负压管道内部堵塞,造成负压度失真,使型腔周围的负压值远低于指示负压,汽化物不能及时排出涂料层而形成气孔或皱皮。
⑦合理的浇注工艺和负压度。
消失模浇注工艺是以充满封闭直浇道为原则,不能忽快忽慢、紊流、断流,更不允许暴露直浇道。
浇注速度,尤其是在行车提升停顿瞬间力求平衡,不断流。
进入尾期慢慢收包,使渣、气、及汽化残留物有充分时间浮集到浇冒口中。
负压度过大,加剧金属液渗透粘砂,并造成附壁效应,不利于液相泡沫被涂层吸附,生成很多气孔。
铸钢件气孔缺陷的分析及预防

铸钢件气孔缺陷的分析及预防铸钢件是一种广泛应用于制造工业的产品,在各行各业都有着广泛的应用。
然而,在铸钢件的生产过程中,常常会出现气孔缺陷。
在本文中,将对铸钢件气孔缺陷的分析及预防进行详细的介绍。
气孔缺陷是铸钢件生产过程中经常出现的一种缺陷,其原因主要是由于铸造过程中,铸钢件内的气体无法顺利释放,而形成的空气泡所致。
具体分析如下:1.铸造温度过高或过低铸造温度过高或过低会导致铸造过程中熔化金属与气体相互作用不充分,或者是在凝固时,金属凝固异常迅速,导致铸造件内部气体排放不及时,进而形成气孔缺陷。
2.金属液中气体含量过高铸钢件气孔缺陷的一个重要原因是金属液中气体含量过高。
这主要是由于铸造过程中,将熔化的金属液错流于模具中时,金属液中气体无法快速排出,而形成的气泡后来就会形成气孔缺陷。
3.模具设计不合理模具是制造铸造件的核心部分之一。
如果模具设计不合理,例如模具壁厚不符合要求、孔隙率过高等造成模具过于松散、不好密封,使熔融金属鼓荡时容易进入焦模震荡区域,从而使气体被气团包裹形成气泡,而成为铸钢件气孔缺陷.了解了铸钢件气孔缺陷发生的原因,我们可以采取一些技术性措施来预防气孔缺陷的出现。
1.合适的铸造温度我们可以在铸造前对熔融金属的净化处理,或者使用真空、熔覆反应等特殊工艺。
这些技术手段可以有效地去除金属液中的气体,减少气孔的发生。
合理的模具设计可以有效地避免铸造中应力集聚,提供良好的流动通道和顺畅的气流通道,避免产生气泡,降低气孔发生的概率。
对于大型铸钢件,可以采用完整的、结构合理的模具,避免模具的壁厚不符合要求等情况。
4.严格的生产工艺控制在生产过程中,我们还需要严格执行质量控制方案,不断优化铸造工艺,并加强现场监督管理。
避免铸造过程中出现偏差,加强对炉温、铸型、冷却等关键环节的控制,并在浇注后及时进行冷却处理,以提高铸钢件的质量。
总结:铸钢件气孔缺陷的原因主要是铸造温度过高或过低导致气体无法充分释放,金属液中气体含量过高,模具设计不合理等情况所致。
浅析铸钢件消失模铸造常见缺陷与防治措施
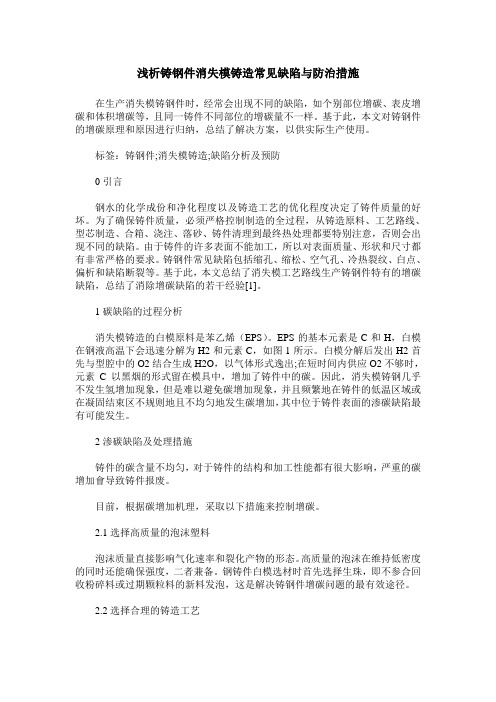
浅析铸钢件消失模铸造常见缺陷与防治措施在生产消失模铸钢件时,经常会出现不同的缺陷,如个别部位增碳、表皮增碳和体积增碳等,且同一铸件不同部位的增碳量不一样。
基于此,本文对铸钢件的增碳原理和原因进行归纳,总结了解决方案,以供实际生产使用。
标签:铸钢件;消失模铸造;缺陷分析及预防0引言钢水的化学成份和净化程度以及铸造工艺的优化程度决定了铸件质量的好坏。
为了确保铸件质量,必须严格控制制造的全过程,从铸造原料、工艺路线、型芯制造、合箱、浇注、落砂、铸件清理到最终热处理都要特别注意,否则会出现不同的缺陷。
由于铸件的许多表面不能加工,所以对表面质量、形状和尺寸都有非常严格的要求。
铸钢件常见缺陷包括缩孔、缩松、空气孔、冷热裂纹、白点、偏析和缺陷断裂等。
基于此,本文总结了消失模工艺路线生产铸钢件特有的增碳缺陷,总结了消除增碳缺陷的若干经验[1]。
1碳缺陷的过程分析消失模铸造的白模原料是苯乙烯(EPS)。
EPS的基本元素是C和H,白模在钢液高温下会迅速分解为H2和元素C,如图1所示。
白模分解后发出H2首先与型腔中的O2结合生成H2O,以气体形式逸出;在短时间内供应O2不够时,元素C以黑烟的形式留在模具中,增加了铸件中的碳。
因此,消失模铸钢几乎不发生氢增加现象,但是难以避免碳增加现象,并且频繁地在铸件的低温区域或在凝固结束区不规则地且不均匀地发生碳增加,其中位于铸件表面的渗碳缺陷最有可能发生。
2渗碳缺陷及处理措施铸件的碳含量不均匀,对于铸件的结构和加工性能都有很大影响,严重的碳增加會导致铸件报废。
目前,根据碳增加机理,采取以下措施来控制增碳。
2.1选择高质量的泡沫塑料泡沫质量直接影响气化速率和裂化产物的形态。
高质量的泡沫在维持低密度的同时还能确保强度,二者兼备。
钢铸件白模选材时首先选择生珠,即不参合回收粉碎料或过期颗粒料的新料发泡,这是解决铸钢件增碳问题的最有效途径。
2.2选择合理的铸造工艺为了防止白模气化和燃烧速度过快,模型装箱采取“能站不要躺”的原则,确保白模不会太快燃烧发气。
消失模铸钢件气孔缺陷及解决措施
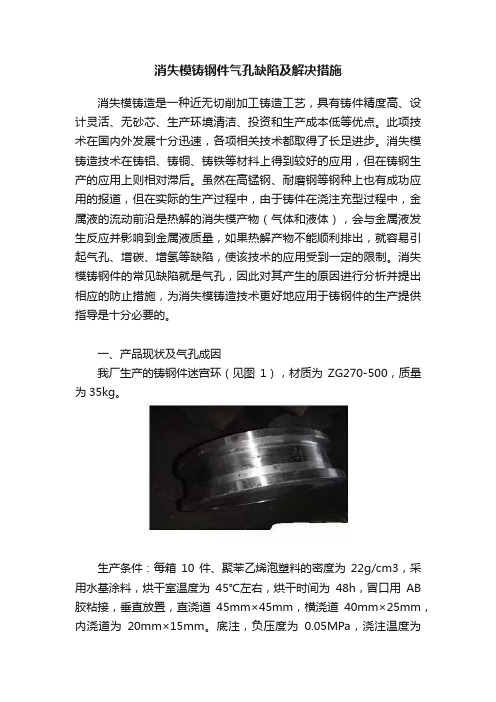
消失模铸钢件气孔缺陷及解决措施消失模铸造是一种近无切削加工铸造工艺,具有铸件精度高、设计灵活、无砂芯、生产环境清洁、投资和生产成本低等优点。
此项技术在国内外发展十分迅速,各项相关技术都取得了长足进步。
消失模铸造技术在铸铝、铸铜、铸铁等材料上得到较好的应用,但在铸钢生产的应用上则相对滞后。
虽然在高锰钢、耐磨钢等钢种上也有成功应用的报道,但在实际的生产过程中,由于铸件在浇注充型过程中,金属液的流动前沿是热解的消失模产物(气体和液体),会与金属液发生反应并影响到金属液质量,如果热解产物不能顺利排出,就容易引起气孔、增碳、增氢等缺陷,使该技术的应用受到一定的限制。
消失模铸钢件的常见缺陷就是气孔,因此对其产生的原因进行分析并提出相应的防止措施,为消失模铸造技术更好地应用于铸钢件的生产提供指导是十分必要的。
一、产品现状及气孔成因我厂生产的铸钢件迷宫环(见图1),材质为ZG270-500,质量为35kg。
生产条件:每箱10件、聚苯乙烯泡塑料的密度为22g/cm3,采用水基涂料,烘干室温度为45℃左右,烘干时间为48h,冒口用AB 胶粘接,垂直放置,直浇道45mm×45mm,横浇道40mm×25mm,内浇道为20mm×15mm。
底注,负压度为0.05MPa,浇注温度为1550℃,浇注时间为13~17s,浇注3min后停止抽真空,30min后落砂。
机加工后在补缩冒口处发现大量分散性气孔,出现在铸件内部和铸件表面上(见图1),最大的直径达3mm,深度达4mm,不合格品率达60%。
我们对气孔缺陷进行系统的整理和分析,认为形成的气孔主要是侵入性气孔和析出性气孔,并对产生的原因进行了较深入的探讨。
气孔的形成来源于气体。
消失模铸造铸钢迷宫环上的气孔主要是由泡沫汽化产生的气体侵入金属液析出而形成的侵入性气孔,以及钢液中带入的析出性气孔。
1.侵入性气孔的成因侵入性气孔是消失模铸钢件气孔产生的主要形式,其形成原因有以下几方面。
铸钢件气孔缺陷的分析及预防

铸钢件气孔缺陷的分析及预防铸钢件在工业生产中起着至关重要的作用,然而在铸钢件的制造过程中,气孔缺陷是一种常见的质量问题。
气孔缺陷会降低铸钢件的强度和硬度,影响其使用性能,严重时甚至会导致零部件的失效。
对铸钢件气孔缺陷进行分析并采取有效的预防措施,对于提高铸钢件的质量、延长零部件的使用寿命具有重要意义。
一、铸钢件气孔缺陷的成因分析1. 原料质量不良:铸造过程中使用的铸造原料如熔剂、砂型、砂芯等质量不良或含有杂质,会促使气体聚集并形成气孔。
2. 浇注过程不当:浇注过程中铸钢件内部的气体未能得到有效的排除,导致气孔的产生。
这与铸钢件的设计、浇注方式、浇注温度、浇注速度等因素密切相关。
3. 砂型和砂芯的设计不合理:砂型和砂芯的设计不合理、结构松散、容易剥落等都会导致气孔的产生。
4. 浇注温度过高:浇注温度过高会导致铸造原料的气体释放不完全,造成气孔缺陷。
5. 铸造工艺控制不当:在铸造工艺中,未能有效控制气体的排除和熔化金属的充填速度,是导致气孔缺陷产生的重要原因之一。
6. 熔化金属中含气过多:熔化金属中含气过多,未能得到有效的排除,会在铸钢件中形成气孔。
1. 优化原料选择:选择质量良好的铸造原料,尽可能减少熔剂、砂型、砂芯中的杂质含量。
2. 浇注过程的优化:合理设计浇注系统,采用适当的浇注方式和浇注温度,加强浇注过程中的气体排除。
3. 砂型和砂芯的优化:优化砂型和砂芯的设计,保证其结构紧密,避免砂型和砂芯剥落。
4. 控制熔化金属中的气体含量:采用适当的炉料和合理的炉前处理工艺,减少熔化金属中的气体含量。
5. 增强铸造工艺控制:加强铸造工艺中气体排除和熔化金属的充填控制,确保铸造工艺的稳定性和可靠性。
6. 合理设计铸造结构:在铸钢件的设计中,合理设计零部件的结构和形状,避免零部件内部的气体积聚,减少气孔的产生。
7. 强化检验和管控:强化对原料、砂型、砂芯、熔化金属和铸造工艺的检验和管控,确保所有加工环节都符合要求。
消失模铸造缺陷产生的原因及解决措施
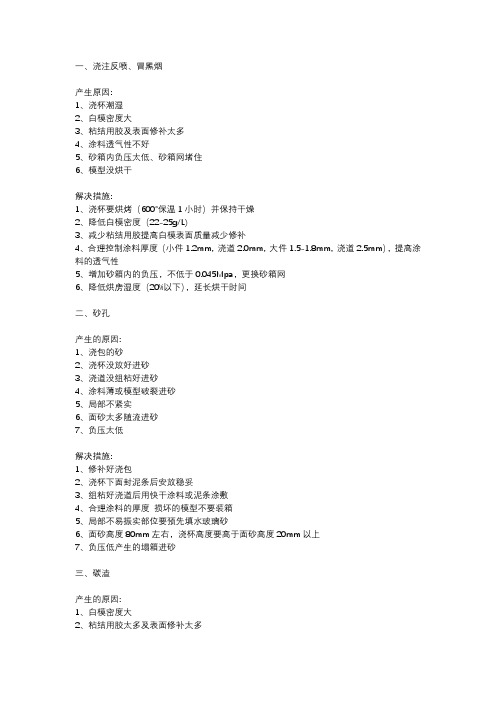
一、浇注反喷、冒黑烟产生原因:1、浇杯潮湿2、白模密度大3、粘结用胶及表面修补太多4、涂料透气性不好5、砂箱内负压太低、砂箱网堵住6、模型没烘干解决措施:1、浇杯要烘烤(600°保温1小时)并保持干燥2、降低白模密度(22-25g/L)3、减少粘结用胶提高白模表面质量减少修补4、合理控制涂料厚度(小件1.2mm, 浇道2.0mm, 大件1.5-1.8mm, 浇道2.5mm),提高涂料的透气性5、增加砂箱内的负压,不低于0.045Mpa,更换砂箱网6、降低烘房湿度(20%以下),延长烘干时间二、砂孔产生的原因:1、浇包的砂2、浇杯没放好进砂3、浇道没组粘好进砂4、涂料薄或模型破裂进砂5、局部不紧实6、面砂太多随流进砂7、负压太低解决措施:1、修补好浇包2、浇杯下面封泥条后安放稳妥3、组粘好浇道后用快干涂料或泥条涂敷4、合理涂料的厚度损坏的模型不要装箱5、局部不易振实部位要预先填水玻璃砂6、面砂高度80mm左右,浇杯高度要高于面砂高度20mm以上7、负压低产生的塌箱进砂三、碳渣产生的原因:1、白模密度大2、粘结用胶太多及表面修补太多3、砂箱内负压低抽气率低4、浇注温度低5、涂料透气性差6、成分或球化孕育不当7、浇注速度没控制好8、白模气化后残渣多9、工艺不合理解决措施:1、降低白模密度2、提高白模表面质量减少修补量及粘结胶量3、增加砂箱内负压提高抽气率反喷会产生碳渣4、提高浇注温度,减少浇注过程温度损失5、合理化碳含量控制铸钢表面增碳6、合理涂料的透气性7、合理控制铸件成分及提高球化孕育效果8、合理浇注速度使其快速充型9、模型按要求烘干10、选用共聚料11、合理工艺尽量采取顶注方式,铸钢先烧后浇四、涂料产生的缺陷:1、涂料孔洞2、强度不够3、涂料不干4、涂料易返潮5、涂料透气性6、耐火度7、涂料厚度8、涂料变质解决措施:1、局部不易振实部位及尖角部位涂料脱落造成的涂料孔(一般伴随有砂孔)2、提高涂料的常温高温强度防止变形粘砂等缺陷3、确保涂料干燥4、涂料配制合理注意返潮5、合理涂料透气性6、耐火度高涂料不剥壳低了易粘砂7、根据铸件情况确定涂料厚度8、加防腐剂等措施防止变质五、粘砂产生的原因:1、涂料强度差不够2、涂料的骨料粉粗或者砂子粗引起机械粘砂粘涂料3、高温粘砂4、涂料厚度不够5、局部振实不好粘砂6、负压与温度与涂料的技术参数不对粘砂7、模型不干解决措施:1、合理涂料配方提高涂料强度2、合理选用骨料及型砂(批量换新砂时要注意)3、根据铸件壁厚情况选择合理的浇注温度,根据模型选择涂料厚度4、不易振实部位预填砂5、根据负压涂料厚度温度合理选择参数6、确保模型干燥六、渣孔产生的原因:1、炉渣2、拦渣不好3、炉辅料4、化学反应渣5、燃烧残渣6、随流产生的渣解决措施:1、出炉前炉内浇包内除渣2、浇注时茶壶包防渣或包咀硅酸铝纤维板拦渣3、用干净无锈蚀的原料4、球化孕育后要扒渣5、白模粘结修补尽量少6、浇包咀勤修,浇注工艺合理减少冲刷等七、塌箱产生的原因:1、负压太低2、浇注速度慢3、涂料厚度不够4、没有振实到位5、工艺设计不合理6、浇注温度解决措施:1、提高负压2、合理浇注速度3、增加涂料厚度4、不易振实部位预填砂,提高振实度5、合理设计浇注系统(避免大的水平面)6、根据铸件情况选择浇注温度八、铁豆、多肉、橘皮产生的原因:1、涂料产生气泡,露白产生铁豆2、朝下平面涂料剥离产生多肉3、局部振实不良产生粘砂多肉4、靠近模型的砂子中有杂物产生多肉5、浇温低薄壁件浇道附近橘皮解决措施:1、合理搅拌涂料,涂挂防止露白,露白的要补涂2、涂料朝下平面要注意涂料凸出剥离3、不易振实部位预填,振实一定要紧实4、砂子除杂等5、薄壁件提高浇注温度。
消失模铸件表面孔眼、凹陷和网纹及防止

消失模铸件表面孔眼、凹陷和网纹及防止铸造工业网今天进铸造行业群,加微信:132****1807消失模铸件表面除上述的气孔、皱皮、积碳、亮碳、粘砂等外,也会出现同砂型铸造一样的孔眼(渣孔、砂孔、缩孔)、缩坑(凹陷)等缺陷和特有的网纹和较深的龟纹等缺陷。
(1)产生原因1.渣孔。
液体金属带入熔渣及模样裂解的固相产物不能排出而积存,漂浮在铸件表面,喷丸清理后,铸件表面仍会有渣痕的不规则的孔洞。
2.砂孔。
浇注时,干砂粒进入液体金属中,最后积集到铸件表面,其颗粒状分布,抛丸清理后,砂子未清除掉,则铸件表面形成砂粒镶嵌物,若喷掉砂粒,则表面留下眼孔。
3.缩松、缩孔及缩坑(凹陷)。
铸件与内浇道及冒口连接处的热区,由于补缩不良,形成缩孔、缩松缺陷。
铸件厚大部分由于补缩不足形成缩坑(凹陷),往往出现在最后凝固较大表面上。
4.网纹、龟纹。
模样表面珠粒间融合不良,连接处的凹沟间隙和细小珠粒纹路粗而深的龟纹(严重时形成粒珠状表面)。
细小如网状纹的为网纹,主要是因模样珠粒质量不好、粘接不良,尤其是取用泡沫塑料板(型)材加工成模样时,表面粗糙涂料渗入其间,其表面龟纹、网统复印在涂料层上,浇注后铸件表面也出现这些缺陷。
(2)防止措施1.渣孔防止措施。
金属液熔炼除渣要干净,严格挡渣操作,浇冒口系统设计应便于排渣、集渣,提高浇注温度以便渣浮集,也可选用除渣滓性能较好的浇包及设置过滤网挡渣。
2.砂孔防止措施。
模样组合粘接处必须严密,中空直浇道必须密封好;模样避免在砂箱内组合粘接,浇冒口连接处和模样转角处要圆滑过度(避免角缝而夹干砂)。
3.缩孔、缩松及缩坑(凹陷)防止措施。
提高金属液的浇冒口补缩能力,液流从冒口处经过,保持冒口最后凝固;采用发热、保温冒口;充分利用直浇道补缩(组串铸件);合理的浇冒口系统。
4.网纹、龟纹的防止措施。
改善模样表面质量,选用细小的珠粒;合适的发泡剂含量;改进发泡成型的工艺;模样干燥工艺合理,防止局部急剧过热;对模样表面修饰,在模样表面涂料上光洁材料如塑料、浸挂一层薄薄的石蜡、涂上一层硝酸纤维素涂层等都可以改善模样的表面粗糙度,使浇注出的铸件没有晶粒网状及龟纹。
铸钢件气孔缺陷的分析及预防
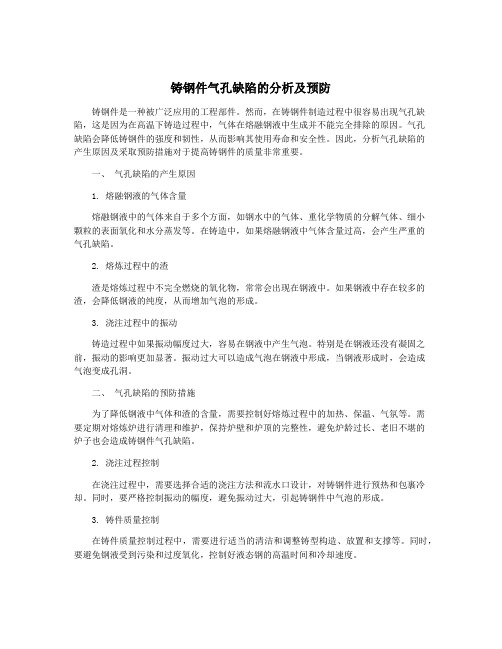
铸钢件气孔缺陷的分析及预防铸钢件是一种被广泛应用的工程部件。
然而,在铸钢件制造过程中很容易出现气孔缺陷,这是因为在高温下铸造过程中,气体在熔融钢液中生成并不能完全排除的原因。
气孔缺陷会降低铸钢件的强度和韧性,从而影响其使用寿命和安全性。
因此,分析气孔缺陷的产生原因及采取预防措施对于提高铸钢件的质量非常重要。
一、气孔缺陷的产生原因1. 熔融钢液的气体含量熔融钢液中的气体来自于多个方面,如钢水中的气体、重化学物质的分解气体、细小颗粒的表面氧化和水分蒸发等。
在铸造中,如果熔融钢液中气体含量过高,会产生严重的气孔缺陷。
2. 熔炼过程中的渣渣是熔炼过程中不完全燃烧的氧化物,常常会出现在钢液中。
如果钢液中存在较多的渣,会降低钢液的纯度,从而增加气泡的形成。
3. 浇注过程中的振动铸造过程中如果振动幅度过大,容易在钢液中产生气泡。
特别是在钢液还没有凝固之前,振动的影响更加显著。
振动过大可以造成气泡在钢液中形成,当钢液形成时,会造成气泡变成孔洞。
二、气孔缺陷的预防措施为了降低钢液中气体和渣的含量,需要控制好熔炼过程中的加热、保温、气氛等。
需要定期对熔炼炉进行清理和维护,保持炉壁和炉顶的完整性,避免炉龄过长、老旧不堪的炉子也会造成铸钢件气孔缺陷。
2. 浇注过程控制在浇注过程中,需要选择合适的浇注方法和流水口设计,对铸钢件进行预热和包裹冷却。
同时,要严格控制振动的幅度,避免振动过大,引起铸钢件中气泡的形成。
3. 铸件质量控制在铸件质量控制过程中,需要进行适当的清洁和调整铸型构造、放置和支撑等。
同时,要避免钢液受到污染和过度氧化,控制好液态钢的高温时间和冷却速度。
综上所述,铸钢件气孔缺陷是由于多种因素所引起的。
防止气孔缺陷的产生需要通过控制钢液中气体和渣的含量、严格控制振动幅度以及在铸件质量控制过程中进行适当的准备来实施。
只有采取有效的预防措施,才能提高铸钢件的质量和使用寿命。
铸钢件气孔缺陷的分析及预防

铸钢件气孔缺陷的分析及预防铸钢件气孔缺陷是一种常见的铸造缺陷,其主要原因是在熔融金属凝固过程中,金属中的气体不完全排出,形成气孔。
气孔缺陷不仅会降低铸钢件的强度和韧性,还会对其密封性和机械性能产生不利影响。
对于气孔缺陷的分析和预防具有重要意义。
气孔缺陷的形成与以下几个方面密切相关:1. 熔融金属中的气体含量较高:熔融金属中的气体主要来自于金属中的气体溶解度和金属液的气泡,而气泡往往是由于金属液中的杂质和气体不能及时排出而形成的。
要减少熔融金属中的气体含量,首先要提高金属液的纯净度和气体排出能力。
2. 浇注过程中的气体吸附:在金属液注入模具的过程中,气体往往会与铸钢件接触的模具表面接触,然后被吸附到铸钢件表面形成气孔。
为了减少这种情况的发生,可以在模具表面涂覆一层特殊的涂层或使用具有吸附气体能力的材料来减少气体的吸附。
3. 硅、锰等元素含量较高:铸钢件中的硅、锰等元素对气孔的形成有一定的影响,其中硅元素会使金属液变稠,增加气泡的数量,锰元素则会提高金属液的表面张力,使气泡难以排出。
在调整合金配方时要注意控制硅、锰等元素的含量。
4. 浇注温度过高或过低:浇注温度过高会导致金属液中的气体溶解度降低,造成气泡形成;而浇注温度过低则会使得金属凝固过程过长,气体排出不畅,同样会形成气孔。
要选择适宜的浇注温度,避免温度过高或过低。
为了预防铸钢件中气孔缺陷的发生,可以采取以下措施:1. 提高熔化金属的质量:要选择优质的原料,并进行严格的质量控制,确保金属液的纯净度和气体排出能力。
2. 优化模具设计:合理设计铸造系统,使得金属液能够顺畅地流动,减少气体的吸附和困留;采用有利于气体排出的模具结构,如设置适当的浇口和排气道。
3. 控制浇注工艺参数:包括浇注温度、浇注速度、浇注压力等。
要根据具体情况,选择合适的参数,以确保金属液能够充分流动,气体能够及时排出。
4. 加强铸造工艺监控:通过对浇注过程的实时监测,及时发现异常情况并采取相应的措施,避免气孔缺陷的发生。
常见的铸件气孔缺陷及防止措施
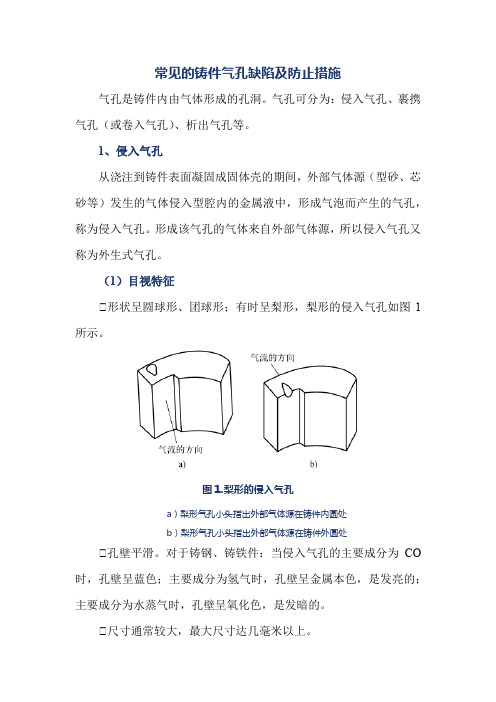
常见的铸件气孔缺陷及防止措施气孔是铸件内由气体形成的孔洞。
气孔可分为:侵入气孔、裹携气孔(或卷入气孔)、析出气孔等。
1、侵入气孔从浇注到铸件表面凝固成固体壳的期间,外部气体源(型砂、芯砂等)发生的气体侵入型腔内的金属液中,形成气泡而产生的气孔,称为侵入气孔。
形成该气孔的气体来自外部气体源,所以侵入气孔又称为外生式气孔。
(1)目视特征①形状呈圆球形、团球形;有时呈梨形,梨形的侵入气孔如图1所示。
图1.梨形的侵入气孔a)梨形气孔小头指出外部气体源在铸件内圆处b)梨形气孔小头指出外部气体源在铸件外圆处①孔壁平滑。
对于铸钢、铸铁件:当侵入气孔的主要成分为CO 时,孔壁呈蓝色;主要成分为氢气时,孔壁呈金属本色,是发亮的;主要成分为水蒸气时,孔壁呈氧化色,是发暗的。
①尺寸通常较大,最大尺寸达几毫米以上。
①常为内部气孔,按浇注位置,常处于铸件上表面的截面中。
①大多数情况下,是单个或几个聚集的尺寸较大的气孔。
有时成为局部聚集的蜂窝状气孔,很少成为弥散性气孔或针孔。
(2)形成机理侵入气孔分三个阶段形成:第一阶段,气体侵入金属液;第二阶段,型壁上气泡形成;第三阶段,气泡在型腔金属液中的滞留或排出。
侵入性气孔形成的条件如下:p A>(p0+p m+p z)式中:p A为“金属—铸型”界面上气泡所在处的压力;p0为型腔中的气体压力,一般为标准大气压力;p m为金属液静压力;p z为金属液的表面阻力。
(3)防止措施防止侵入气孔产生应主要从减小p A,增加气体进入金属液的阻力和使气泡容易从金属液中浮出等方面入手。
具体措施如下:①减少砂型(芯)在浇注时的发气量,严格控制湿型的含水量等。
①使浇注时产生的气体容易从砂型(芯)中排出,如多扎出气孔等。
①提高气体进入金属液的阻力,如表面施用涂料等。
2、裹携气孔(或卷入气孔)浇注系统中的金属液流裹携着气泡,气泡随液流进入型腔,或液流冲击型腔内金属液面,将气泡卷入金属液中。
当气泡不能从型腔金属液中排除,就会使铸件产生气孔,又称卷入气孔。
铸钢件气孔缺陷的分析及预防

铸钢件气孔缺陷的分析及预防铸钢件作为工业制造中常见的零部件,其质量的好坏直接影响着整个产品的性能和安全性。
铸钢件在生产过程中常常会出现气孔缺陷,这种缺陷会严重影响铸钢件的质量和使用寿命。
对于铸钢件气孔缺陷的分析和预防具有非常重要的意义。
一、气孔缺陷的产生原因1.1 原料质量问题铸钢件的气孔缺陷的产生原因之一可能是原料的质量问题。
原料中含有过多的杂质或含氧量过高,会导致铸钢件的气孔缺陷。
1.2 浇注过程中的问题在铸造过程中,如果浇注温度控制不当或者浇注速度过快,都有可能造成气孔缺陷。
1.3 模具设计问题模具设计不合理或者模具使用过程中磨损严重,也会导致铸钢件的气孔缺陷。
1.4 涂料和砂芯问题在铸造过程中使用的涂料和砂芯,如果质量不过关,也会导致铸钢件的气孔缺陷。
二、气孔缺陷的危害气孔缺陷对铸钢件的性能和安全性都会造成严重影响。
气孔缺陷会降低铸钢件的力学性能,使得其承载能力大大降低。
气孔缺陷还会对铸钢件表面造成影响,使得表面粗糙度增加,从而影响其准确度。
最重要的是,气孔缺陷会严重影响铸钢件的耐久性和使用寿命,一旦出现气孔缺陷,铸钢件就容易出现断裂或者损坏,给使用带来了极大的安全隐患。
3.1 外观检查法通过外观检查法可以初步判断铸钢件是否存在气孔缺陷,一般来说,气孔缺陷的铸钢件表面会出现突起或凹槽。
3.3 X射线检测法X射线检测法是一种非破坏性检测方法,通过对铸钢件进行X射线检测可以清晰地观察到其中的气孔缺陷情况。
四、气孔缺陷的预防措施4.1 优化原料首先要做好原料的筛选工作,保证原料的质量符合要求,避免其中含有过多的杂质或氧化物。
4.3 设计优化模具对于模具的设计和使用,要进行优化和维护,确保模具的质量符合要求,避免因此造成气孔缺陷。
4.5 定期检测定期对铸钢件进行外观检查和X射线检测,发现问题及时进行处理,避免气孔缺陷的出现。
消失模铸件增碳缺陷及其防止措施
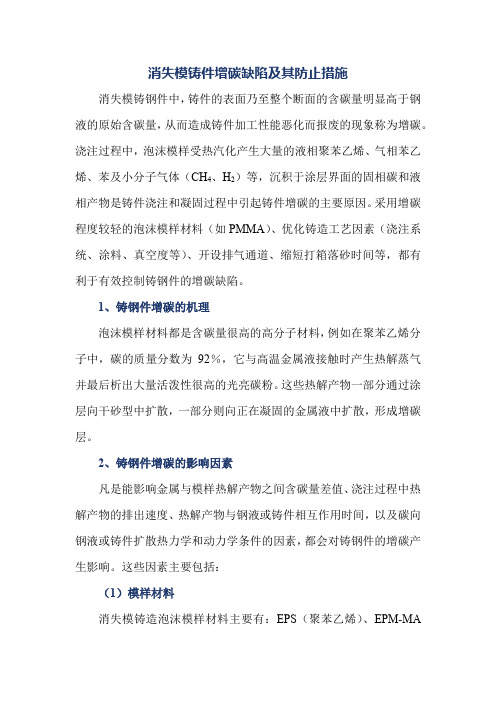
消失模铸件增碳缺陷及其防止措施消失模铸钢件中,铸件的表面乃至整个断面的含碳量明显高于钢液的原始含碳量,从而造成铸件加工性能恶化而报废的现象称为增碳。
浇注过程中,泡沫模样受热汽化产生大量的液相聚苯乙烯、气相苯乙烯、苯及小分子气体(CH4、H2)等,沉积于涂层界面的固相碳和液相产物是铸件浇注和凝固过程中引起铸件增碳的主要原因。
采用增碳程度较轻的泡沫模样材料(如PMMA)、优化铸造工艺因素(浇注系统、涂料、真空度等)、开设排气通道、缩短打箱落砂时间等,都有利于有效控制铸钢件的增碳缺陷。
1、铸钢件增碳的机理泡沫模样材料都是含碳量很高的高分子材料,例如在聚苯乙烯分子中,碳的质量分数为92%,它与高温金属液接触时产生热解蒸气并最后析出大量活泼性很高的光亮碳粉。
这些热解产物一部分通过涂层向干砂型中扩散,一部分则向正在凝固的金属液中扩散,形成增碳层。
2、铸钢件增碳的影响因素凡是能影响金属与模样热解产物之间含碳量差值、浇注过程中热解产物的排出速度、热解产物与钢液或铸件相互作用时间,以及碳向钢液或铸件扩散热力学和动力学条件的因素,都会对铸钢件的增碳产生影响。
这些因素主要包括:(1)模样材料消失模铸造泡沫模样材料主要有:EPS(聚苯乙烯)、EPM-MA(聚甲基丙烯酸甲酯)、STMMA(共聚物,EPS∶EPMMA=3∶7)等。
采用EPS材料时,出现增碳缺陷的可能大;而采用EPMMA材料,可大大减轻铸钢件的增碳缺陷;而STMMA材料综合了EPS和EPMMA的优点,为解决铸钢件增碳和气孔缺陷提供了可能。
用EPS与STMMA模件材料生产铸钢件时的增碳情况对比,如下表所示。
低碳钢消失模铸件增碳情况为了减少铸钢件的增碳,采用EPMMA或STMMA是十分有效的;但EPM-MA发气量大,发气速度也快,浇注时容易产生喷溅、呛火现象,造成气孔等缺陷;而STMMA则要好得多。
因此,STMMA 成为生产铸钢件的首选材料。
除模样材料种类的选择之外,模样的密度也是不可忽视的重要因素。
铸钢件气孔缺陷的分析及预防

铸钢件气孔缺陷的分析及预防
铸钢件是一种重要的金属零件,广泛应用于各种机械设备和工程结构中。
然而,由于制造和铸造过程中可能发生气孔缺陷,影响其性能和寿命。
因此,对铸钢件气孔缺陷的分析和预防是非常重要的。
首先,分析铸钢件气孔缺陷的原因。
气孔缺陷是在铸造过程中由于气体存在所产生的孔洞。
常见的原因有以下几点:
1.铸造工艺不合理。
例如,铸造温度过低或过高,浇注速度过快或过慢,模具设计不合理等,都会导致气孔的产生。
2.原料质量问题。
铸造原料杂质含量高或含水量过多也会导致气孔的产生。
3.浇注系统不完善。
例如,浇口设计不合理、浇注系统中存在堵塞或过多的曲折通道等都会导致气孔的产生。
其次,预防铸钢件气孔缺陷可以从以下几个方面入手。
2.选择优质的原材料。
减少杂质含量、控制含水量等,有助于减少气孔的产生。
3.完善浇注系统。
设计合理的浇口和通道,以及设置无死角的通道,可以避免气孔的产生。
最后,对于已经产生的铸钢件气孔缺陷,可以采用以下方法处理。
1.打孔。
对于小型的气孔,可以通过钻孔或冲孔等方式将气孔的部分打通,减少对零件性能的影响。
2.热处理。
通过热处理的方式,可以将气孔的位置和体积减小,并达到改善铸钢件性能的目的。
综上所述,铸钢件气孔缺陷的分析和预防是非常重要的。
在铸造工艺、原材料选择和浇注系统设计等方面采取合理的措施,可以有效地降低气孔的产生,从而提高铸钢件的性能和寿命。
同时,对于已经产生的气孔缺陷,也可以通过打孔和热处理等方式来得到有效地处理。
消失模铸件易出现的缺陷及消除措施
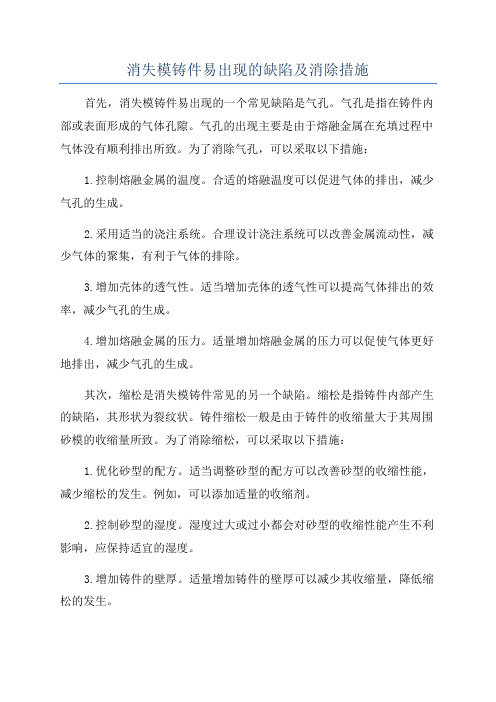
消失模铸件易出现的缺陷及消除措施首先,消失模铸件易出现的一个常见缺陷是气孔。
气孔是指在铸件内部或表面形成的气体孔隙。
气孔的出现主要是由于熔融金属在充填过程中气体没有顺利排出所致。
为了消除气孔,可以采取以下措施:1.控制熔融金属的温度。
合适的熔融温度可以促进气体的排出,减少气孔的生成。
2.采用适当的浇注系统。
合理设计浇注系统可以改善金属流动性,减少气体的聚集,有利于气体的排除。
3.增加壳体的透气性。
适当增加壳体的透气性可以提高气体排出的效率,减少气孔的生成。
4.增加熔融金属的压力。
适量增加熔融金属的压力可以促使气体更好地排出,减少气孔的生成。
其次,缩松是消失模铸件常见的另一个缺陷。
缩松是指铸件内部产生的缺陷,其形状为裂纹状。
铸件缩松一般是由于铸件的收缩量大于其周围砂模的收缩量所致。
为了消除缩松,可以采取以下措施:1.优化砂型的配方。
适当调整砂型的配方可以改善砂型的收缩性能,减少缩松的发生。
例如,可以添加适量的收缩剂。
2.控制砂型的湿度。
湿度过大或过小都会对砂型的收缩性能产生不利影响,应保持适宜的湿度。
3.增加铸件的壁厚。
适量增加铸件的壁厚可以减少其收缩量,降低缩松的发生。
4.增加充填缓慢度。
适当降低熔融金属的充填速度可以减少金属流动过快造成的收缩不均,减少缩松的发生。
此外,消失模铸件还可能出现其他缺陷,如未充填、冷隔离、裂纹等。
为了消除这些缺陷,可以采取以下措施:1.控制熔融金属的温度。
适当降低熔融金属的温度可以减少未充填和冷隔离的发生。
2.增加砂型的强度。
优化砂型的配方、增加砂型的固化时间和温度,以及采用合适的固化剂等措施可以提高砂型的强度,减少裂纹的发生。
3.控制熔融金属的充填速度。
适当降低金属的充填速度可以减少未充填和冷隔离的发生。
4.增加浇注口的大小。
适当增加浇注口的大小可以改善金属的流动性,减少未充填和冷隔离的发生。
综上所述,消失模铸件易出现的缺陷包括气孔、缩松、未充填、冷隔离等。
针对这些缺陷,可以采取相应的措施来消除,如控制熔融金属的温度和压力、优化砂型的配方和固化条件、增加浇注口的大小等。
消失模铸件易出现的缺陷及消除措施

消失模铸件易出现的缺陷及消除措施―钢铁研究院试验中心建钢1、粘砂金属液渗入型砂中,形成金属与型砂的机械混合物,其中有两种情况:一种是金属液通过涂层开裂处渗入型砂中,形成铁包砂(即机械粘砂),此种缺陷一般可以清除掉;另一种情况是金属透过涂层渗入型砂中,形成难以清除的化学粘砂。
(一)产生的原因(1)在涂层开裂的情况下,由于型砂紧实度不够,型砂颗粒过大及真空度过高产生第一种粘砂情况;(2)在涂层过薄或局部未刷到的情况下,由于金属液温度较高,真空度较大时产生第二种粘砂。
(二)防止措施(1)提高涂层的厚度和耐火度。
(2)造型时紧实力不宜过大以免破坏涂层。
(3)选择合适的负压。
(4)选用较细的原砂。
(5)浇注温度不宜过高。
(6)选择合适的压力头。
2、气孔(一)气孔的分类(1)浇注时卷入空气形成的气孔。
(2)泡沫塑料模样分解产生的气孔。
(3)模样涂层不干引起的气孔。
(4)金属液脱氧不好引起的气孔。
(二)浇注时卷入空气形成的气孔消失模铸造浇注过程中如果直浇道不能充满就会卷入空气,这些气体若不能及时排出,就有产生气孔缺陷的可能。
防止卷入气体的措施:(1)采用封闭式的浇注系统。
(2)浇注时维持浇口盆有一定的液体金属以保持直浇道处于充满状态。
(3)正确掌握浇注方法,采用慢—快—慢的浇注方法。
(三)泡沫塑料模样分解产生的气孔EPS和STMMA热解后产生大量的气体,如果充型平稳,金属与模样逐层置换,这些气体就会顺利通过液体前沿与模样间的气隙经铸型排出,特别在铸型处于负压状态下更有利气体排放,铸件不易产生气孔缺陷。
但是如果充型过程产生紊流或者顶注,侧注情况下、部分模样被金属液包围后进行分解产生的气体不能从金属液中排出时就会产生缺陷,这种气孔表面有炭黑存在。
防止措施:(1)改进浇注方案,使充型过程逐层置换,不产生紊流。
(2)提高浇注温度。
(3)在不发生紊流的情况下,适当提高真空度,如果发生紊流而产生气孔时,可适当降低真空度。
- 1、下载文档前请自行甄别文档内容的完整性,平台不提供额外的编辑、内容补充、找答案等附加服务。
- 2、"仅部分预览"的文档,不可在线预览部分如存在完整性等问题,可反馈申请退款(可完整预览的文档不适用该条件!)。
- 3、如文档侵犯您的权益,请联系客服反馈,我们会尽快为您处理(人工客服工作时间:9:00-18:30)。
机加 工 后 在 补 缩 冒 口处 发 现 大 量 分 散 性 气 孔 , 出
现在铸件 内部 和铸件 表 面上 , 图 1 见 。最 大 的 直 径 达
图 2 浇 注时 的气 体压 力变化
Fi . Ch n e o a e s r n p u i g g 2 a g fg s pr s u e o o rn
析 出 性 气 孔 是 指 在 熔 炼 过 程 中金 属 液 吸 气 , 金 在 属凝 固 过 程 中 , 金 属 中析 出 而 形 成 气 孔 。 当 金 属 液 从
化 , 气 隙压 力较 小 及 保 持 平 衡 。 使
( )浇 注 系 统 优 先 选 用 封 闭 式 的 底 注 、 梯 浇 注 2 阶
这 些 小 冒 口可 有 效 地 消 除 铸 件 的夹 渣 及 气 孔 缺 陷 。
35 选择 正确的浇注工 艺 .
( )浇 注 位 置 应 尽 量 使 重 要 的 大 表 面 处 于竖 直 或 1
倾 斜 , 利 于金 属 液 的 平 稳 充 型 和 塑 料 模 样 的 逐 渐 气 有
二是 泡 沫 塑 料 模样 由于 干 燥 不 充 分 , 沫 粒 珠 中 仍 残 泡 留较 多 的 水 蒸 气 ; 是 来 自型砂 中 的水 分 。 三 2 析 出性 气 孔
( )水 分 也 是 形 成 铸 钢 件 气 孔 的 因 素 之 一 。 浇 注 4 时 水 分 的来 源 主要 有 以下 几 方 面 : 是 涂 料 没 有 彻 底 一 烘干 , 由于水 基 涂料 中含 有 C 或 MC、 乙 烯 醇 、 乳 聚 白
物 来 不 及 充 分 裂 解 气 化 , 液 态 产 物 或 残 留 物 往 往 积 使 聚 在 铸 件 的死 角 或 顶 部 , 这 些 部 位 易 形 成 气 孔 。 因 使
3 1 减 少泡 沫 塑料 模 样 的发 气 量 , 低 发 气速 度 . 降
提高浇注温度可 有效地减 少 气孔 等一 系列铸 造缺 陷 。
铸 钢 件 浇 注 温 度 应 在 16 0℃ 以 上 , 时 应 保 证 涂 料 0 此 有 较 高 的高 温 强 度 , 则 会 导 致 较 严 重 的粘 砂 。 否
行 了分 析 , 为 形 成 的 气 孔 主 要 是 侵 入 性 气 孔 和 析 出 认
性 气 孔 , 对 产 生 的原 因进 行 了较 深 入 的探 讨 。 并 1 侵 入 性 气 孔
然 在 高 锰 钢 、 磨 钢 等 钢 种 上 也 有 成 功 应 用 的 报 耐
道 引, 在 实 际 的 生 产 过 程 中 , 于 铸 件 的 气 孔 、 但 由 增 碳 、 氢 等 缺 陷使 该 技 术 的应 用 受 到 一 定 的 限 制 。 因 增 此 , 消失 模 铸 钢 件 的 常 见 缺 陷 进 行 探 讨 , 消失 模 铸 对 为
摘 要 : 析 了 消 失 模 铸 钢 件 气 孔 缺 陷 的 形 成 原 因 , 出 了 综 合 解 决 的 措 施 , 践 证 明 这 些 措 施 可 有 效 地 解 决 铸 钢 件 的 气 孔 分 提 实
缺 陷 。
关 键 词 : 失 模 铸 造 ; 钢 件 ; 孔 消 铸 气
Ana y i f Bl wh l f c s o t e s i g n Lo tFoa s i nd I s Pr v n i e M e s r s l ss o o o e De e t f S e lCa tn s i s m Ca tng a t e e tv a u e
能 及 时 浇 注 , 会 吸 收 空 气 中 的水 分 。另 外 , 料 中 的 就 涂
膨 润 土 等 悬 浮 剂 多 含 有 结 构 水 和 结 合 水 , 于 模 样 烘 由 干温 度 一 般 只 有 4 0℃左 右 , 结 构 水 和 结 合 水 一 般 仍 其
存 留 于 涂 料 中 , 部 分 水 在 高 温 钢 液 的 作 用 下 汽 化 这
急 剧 增 大 , 23为 浇 注 时 气 体 压 力 随 浇 注 时 间 的 变 图 _ 化 , 以 看 出 , 注 的 瞬 时气 体 压 力 急剧 升 高 。 由于铸 可 浇
钢 浇 注 温 度 较 高 , 注 时 瞬 间 发 气 量 很 大 , 体 不 能被 浇 气 及 时 排 出 , 别 是 钢 液 在 紊 流状 态 时 将 气 体 卷 入 其 中 , 特
形成气孔 。
( )粘 结 泡 沫 塑 料 模 样 用 粘 结 剂 使 用 不 当是 形 3
成 侵 入 性 气 孔 的 重 要 原 因 。实 际 生 产 中 发 现 , 钢 铸
日
蛙
图 1 Байду номын сангаас毂 上 的气孔 缺 陷
F g 1 Bl wh t e e to h e lh b i. o o e d f c n t e wh e u
3mm, 度 达 4mm, 品 率 达 8 。 对 气 孔 缺 陷 进 深 废 0
维普资讯
《 造技 术》 2 2 0 铸 1/0 4
经验 交流
件在泡 沫塑料模 样 粘结 处 往 往产 生 大量 的 气孔 。如
果 用 插 接 或 钢 钉 连 接 泡 沫 塑 料 模 样 , 处 就 不 会 产 该 生 气 孔 。这 是 由 于 在 连 接 处 使 用 了 较 多 的 粘 结 剂 , 无 论 用 8 1强 力 胶 还 是 AB胶 , 们 的密 度 是 泡 沫 塑 5 它 料 的 几 倍 甚 至 几 十 倍 , 气 化 速 度 远 比 泡 沫 塑 料 慢 其
造 技 术 更 好 地 应 用 于 铸 钢 件 的生 产 提 供 指 导是 十 分 必
要 的。
侵 入 性 气 孔 是 消 失 模 铸 钢 件 气 孔 产 生 的 主 要 形 式 , 形 成 原 因有 以下 几 方 面 。 其 ( )浇 注 过 程 中 , 沫 塑 料 模 样 不 能 被 迅 速 气 化 , 1 泡 裂 解 的 液 态 产 物 被 卷 入 金 属 液 中 , 件凝 固后 , 体 不 铸 气
中圈分类 号 : TG2 9 6 4 . 文献 标识码 : B 文章编 号 :0 08 6 ( 0 4 1 —9 00 1 0 —3 5 2 0 ) 20 6 —2
消 失 模 铸 造 技 术 在 铸 铝 、 铜 、 铁 等 材 料 上 得 到 铸 铸 较 好 的应 用 。但 在 铸 钢 生 产 的应 用 上 则 相 对 滞 后 。虽
此 , 在 这 些 部 位 设 置 小 冒 口 , 口顶 部 不 刷 涂料 。 以 应 冒 利 于 积 聚 的 液 态 产 物 最 后 汽 化 时将 气 体 排 出 。 冒 口尺 寸 为 2 i 0 Fm×1 l 0mm×2 0 mm, 理 方 便 。实 践 证 明 , 清
胶 、 粉 等 有 机 粘 结 剂 , 果 挂 有 涂 料 的 模 样 烘 干 后 不 淀 如
或 侧 注 , 证 金 属 液 的 平 稳 流 动 及 避 免 浇 注 过 程 中 大 保
量 空气进入型腔 。
吸 入 水 蒸 气 时 , 高 温金 属 液 的 热 作 用 下 , 裂 解 产 生 在 水
氢 气 , 气溶 解 后 裂 解 成 氢 原 子 。 这 些 原 子 在 金 属 液 氢
LI AO —in 。FAN i — u Xil g a Jn h i.J ANG n — e I Qig h
( . c o l fM e h n c lEn ie rn 1 S h o c a ia gn e ig,S a d n nv r i o h n o g U iest y,Jn n 2 0 6 , ia;2 H e e nv riy o ce c n c oo y, i a 5 0 Chn 1 . b iU ie st fS in ea d Te hn lg
维普资讯
经 验 交 流
《 造 技 术 》 2 2 0 铸 1/ 0 4
消 失 模 铸 钢 件 气 孔 缺 陷 的分 析 及 解 决 措 施
廖 希 亮 ,范金 辉 ,姜 青 河
(. 1 山东 大 学 机 械 工 程 学 院 , 东 济 南 2 0 6 ;2 河 北 科 技 大 学 材 料 学 院 , 北 石 家 庄 0 0 5 ) 山 501 . 河 5 0 4
34 设置集渣与排 气冒 口 .
将 胶 裹 住 , 随 后 的 冷 却 过 程 中 不 断 气 化 , 而 在 铸 在 从
件 中形 成 气 孔 。
聚 苯 乙烯 泡 沫塑 料 模 样 的 气 体 分 解 产 物 都 要 通 过
涂 层 逸 出型 腔 , 由于 金 属 液 充 型速 度 很 快 , 态热 解 产 液
( )提 高 金 属 液 的 浇 注 温 度 , 小 浇 注 速 度 , 利 3 减 有 于 泡 沫 塑 料 模 样 的充 分 汽 化 和 迅 速 地 排 出 。实 践 证 明
凝 固过 程 中重 新 聚 合 , 成 氢 气 , 法 排 除 , 形 成 了 生 无 就 析 出性 气 孔 缺 陷 。这 种 气 孔 特点 : 壁 比较 光 滑 , 金 气 有 属光泽 , 气孔 比较 小 但 数 目较 多 。 3 解 决 的 措 施
能被排 出, 而在 铸 件 中形 成 气孔 。 ( )泡 沫 塑 料 模 样 的发 气 量 随 浇 注 温 度 的升 高 而 2
图 1是 某 厂 生 产 的挖 掘 机 上 一 轮 毂 零 件 , 产 条 生 件 为 : 箱 一 件 ,聚 苯 乙 烯 泡 沫 塑 料 的 密 度 为 每
2 / m。 采用 水 基 涂 料 , 干室 温 度 为 4 2g c , 烘 5℃左 右 , 烘 干 时 间 为 4 , 口用 AB胶 粘 结 , 平 放 置 , 注 , 8h 冒 水 底 负 压 度 为 0 0 a 浇 注 温 度 为 l 5 0 ℃ , 注 时 间 . 5 MP , 5 浇 2 , 注 3ri 停 止 抽 真 空 , 0mi 落砂 。 0S浇 n后 a 3 n后