冷轧酸洗线工艺介绍
《冷轧酸洗线工艺》课件

02
冷轧酸洗线工艺流程
酸洗前的准备
设备检查
确保酸洗线设备处于良好状态,无故障隐 患。
清洗和Байду номын сангаас处理
去除待酸洗钢板表面的杂质和氧化物,确 保酸洗效果。
《冷轧酸洗线工艺》PPT课件
CONTENTS
• 冷轧酸洗线工艺简介 • 冷轧酸洗线工艺流程 • 冷轧酸洗线工艺设备 • 冷轧酸洗线工艺操作要点 • 冷轧酸洗线工艺的优化与改进
01
冷轧酸洗线工艺简介
冷轧酸洗线工艺的定义
冷轧酸洗线工艺是一种金属加工技术,主要用于生产高质量 的冷轧钢板。它通过酸洗去除金属表面的氧化物和杂质,以 提高钢板的表面质量和性能。
致酸洗液分解和设备腐蚀。
01
酸洗浓度
02 适当提高酸洗液的浓度可以提高
酸洗效果,但浓度过高会增加生
产成本和环境污染。
酸洗时间
延长酸洗时间可以提高酸洗效果
,但时间过长会导致金属过度腐
03
蚀和设备损坏。
酸洗液流速
04 合理控制酸洗液流速可以提高酸
洗效果,同时还能减少金属杂质
在设备中的沉积。
谢谢您的聆听
。
04
冷轧酸洗线工艺操作要点
酸洗液的配制与调整
总结词
酸洗液的配制与调整是冷轧酸洗线工艺 中的重要环节,直接影响到酸洗效果和 产品质量。
VS
详细描述
在配制酸洗液时,需要选择合适的酸种类 和浓度,并根据实际情况调整酸洗液的成 分比例。同时,需要定期检测酸洗液的浓 度和酸度,确保其处于最佳状态。
酸洗原理及工艺

酸洗中速度、温度和紊流度的关系
谈完超浅槽紊流酸洗的两个主要优势之后,再来看 看在应用中的综合效果,这是其工艺优越性的具体体现。
一定规格的板带,酸洗中就需要相应的板带速度、 酸液紊流度和酸液温度,这是各种不同酸洗工艺中共同 的要求。而超浅槽紊流酸洗的优势就是体现在这些参数 需要变更的时候。
邯钢冷轧项目酸轧联合机组
酸洗工艺原理及结构
设备材料组
前言
SMS Demag公司为邯钢提供的 超浅槽紊 流盐酸酸洗线,是当今世界上最先进的盐酸酸 洗工艺之一。值得一提的是,其先进性并不意 味着此工艺的不成熟,在我们这条生产线之前, SMS Demag公司在全世界已经建设了24套同 类工艺酸洗线。
今天,我就来给大家介绍一下我们酸洗线 的工艺特点和结构组成。
相对于其他公司的浅槽酸洗工艺,SMS Demag由于不需要另 外的回酸通道,因而酸槽更窄,更加有效地减少了酸液的挥发面积。 酸槽变窄,同时也使得酸洗段和漂洗段可采用同样长度的挤干辊, 降低了操作成本和减少了备件量。同时酸槽变窄也使得槽盖变窄, 结果是打开槽盖维护时设备的最高点得以降低,使得厂房高度可以 相应降低,降低了投资成本。
目录
• 酸洗工艺 • 酸槽结构 • 酸液循环
一、酸洗工艺
氧化层的构成
酸洗的目标 就是去除钢板表 面的氧化铁皮, 因此在介绍酸洗 工艺之前,我想 先给大家介绍一 下,通常情况下 钢板表面氧化层 的结构。
酸洗时发生的主要化学反应
针对钢板表面氧化层的成份,酸洗时发 生的主要化学反应如下:
为什么叫超浅槽酸洗?
紊流度
酸液温度
板带运行速度
需要的酸液温度
冷轧酸洗工艺流程介绍

冷轧酸洗工艺流程介绍工艺流程:热轧钢卷→步进梁运输机→钢卷拆捆带→中间运输车→钢卷小车→钢卷测径测宽→开卷机→带夹送辊的矫直机→带夹送辊的切分剪→焊接及冲孔→张紧辊→纠偏辊→入口活套→张紧装置→破鳞机→酸洗→漂洗→干燥→张紧装置→纠偏辊→中间活套→纠偏辊→纠偏辊→切边(碎边)→张紧辊→出口活套→纠偏辊→张紧辊→纠偏辊→液压横切剪→入口测厚仪→张紧装置→冷连轧机组→板形仪→飞剪分卷→卷取机→卸卷(离线检查)→步进梁运输机→称重→打捆→标示→入库其工艺过程主要由开卷、矫直、焊接、轧制、剪切和卷取6个过程组成。
其中开卷、矫直和焊接是连轧的准备过程,轧制是主要加工过程,剪切和卷取是轧制过程的结束过连轧前的带钢呈卷状,是经过酸洗已清除氧化铁皮的热轧卷,当采用全连续式轧制方式时,热轧带钢经酸洗后不涂油而代之以钝化方法对带钢进行表面防锈处理。
钢卷将通过空中行车装载在步进梁运输机上的钢卷滑轨上,并从热轧钢卷库运离。
在钢卷通过步进梁运输机运输期间,将自动地进行钢卷宽度和直径的测量。
在钢卷通过运卷小车分配给钢卷小车后,钢卷将被各自的钢卷小车装载到开卷机的卷筒上。
这些操作将自动进行。
由于要满足工艺(酸洗)段满意的不间断稳定操作的原因,生产线的入口段将配置2套开卷机,在带钢从一台开卷机开卷期间,一个新的钢卷将被插入另一台卷取机,一个旋转液压缸将膨胀心轴以牢固地固定钢卷。
一个缓冲辊将用于防止钢卷外圈由于弹跳效果松开。
于是开卷机旋转,一个钢卷头端开卷装置,包括另一个缓冲辊和剥带器将打开带卷的头端并穿入夹紧辊。
带钢开卷后经由夹送辊进入矫直机,夹送辊控制着带钢的进料速度。
矫直的目的是为了使带钢能顺利穿入入口剪,为下一步焊接作准备。
矫直辊依靠压辊字完成矫直工作。
在矫直以后,钢带的头部和尾端的超差部分根据设定的长度将被入口剪切断,剩下的超差(废料)将在生产线内处理。
超差部分将自动被切成钢板并通过斜道转向进入设置在入口剪下的废料箱内。
首钢1850冷轧线酸洗工艺

首钢1850冷轧线酸洗工艺1. 引言冷轧是钢材加工过程中的重要工艺之一,能够使钢材变薄、变窄、提高表面质量,并增加机械性能。
然而,在冷轧过程中,钢材表面常常会形成一层氧化皮和其他杂质,这会影响产品质量,降低其应用价值。
因此,冷轧后需要进行酸洗处理,以去除这些杂质。
本文将介绍首钢1850冷轧线的酸洗工艺,包括工艺流程、主要设备和操作要点等方面的内容。
2. 工艺流程首钢1850冷轧线酸洗工艺的主要流程包括预处理、酸洗和后处理。
2.1 预处理在进入酸洗环节之前,首先需要进行预处理。
预处理的目的是去除表面油污和氧化皮,以减少酸洗液的消耗和延长酸洗槽的使用寿命。
预处理工序主要有以下几个步骤:1.布料:将冷轧钢卷送入预处理设备,经过传动装置将钢卷送入预处理槽中。
2.水洗:使用清水对钢卷进行冲洗,去除表面的油污。
3.预酸洗:使用酸性溶液对钢卷进行浸泡处理,去除氧化皮。
2.2 酸洗酸洗环节是首钢1850冷轧线工艺中的核心环节,其主要目的是去除钢材表面的氧化皮和其他杂质。
酸洗工序主要步骤如下:1.酸洗槽:将预处理后的钢卷送入酸洗槽中,保证钢卷表面充分接触酸洗溶液。
2.洗涤:在酸洗槽中,通过机械搅拌和水流冲洗,将钢材表面的氧化皮和杂质溶解和冲刷掉。
3.酸洗液处理:酸洗槽中的酸洗液会逐渐被消耗和污染,需要定期进行处理,以维持酸洗液的使用寿命。
2.3 后处理在酸洗后,钢材表面可能残留有一定量的酸洗液,需要进行后处理工序。
后处理工序主要包括以下几个步骤:1.水洗:对酸洗后的钢材进行水洗,以去除残留的酸洗液和杂质。
2.除锈处理:使用除锈剂对钢材表面进行处理,去除可能残留的氧化物。
3.酸洗槽清洗:对酸洗槽进行清洗,将其中的酸洗液和杂质清除。
3. 主要设备首钢1850冷轧线酸洗工艺所需的主要设备包括预处理设备、酸洗槽、洗涤设备、酸洗液处理设备和后处理设备等。
•预处理设备:用于对冷轧钢卷进行表面油污和氧化皮预处理,包括布料装置和冲洗设备等。
冷轧生产线酸洗工艺
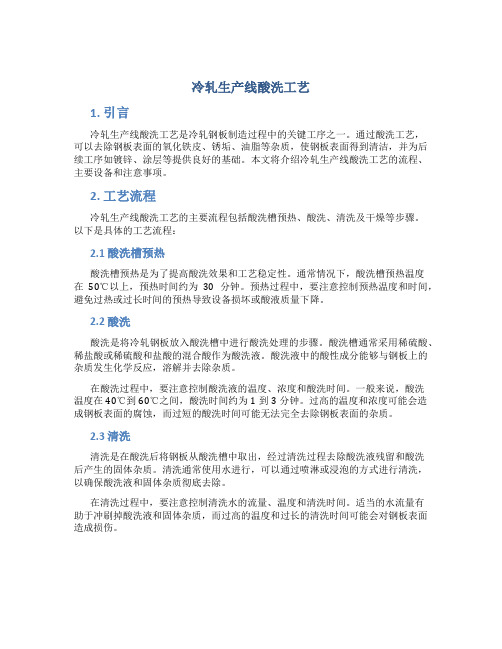
冷轧生产线酸洗工艺1. 引言冷轧生产线酸洗工艺是冷轧钢板制造过程中的关键工序之一。
通过酸洗工艺,可以去除钢板表面的氧化铁皮、锈垢、油脂等杂质,使钢板表面得到清洁,并为后续工序如镀锌、涂层等提供良好的基础。
本文将介绍冷轧生产线酸洗工艺的流程、主要设备和注意事项。
2. 工艺流程冷轧生产线酸洗工艺的主要流程包括酸洗槽预热、酸洗、清洗及干燥等步骤。
以下是具体的工艺流程:2.1 酸洗槽预热酸洗槽预热是为了提高酸洗效果和工艺稳定性。
通常情况下,酸洗槽预热温度在50℃以上,预热时间约为30分钟。
预热过程中,要注意控制预热温度和时间,避免过热或过长时间的预热导致设备损坏或酸液质量下降。
2.2 酸洗酸洗是将冷轧钢板放入酸洗槽中进行酸洗处理的步骤。
酸洗槽通常采用稀硫酸、稀盐酸或稀硫酸和盐酸的混合酸作为酸洗液。
酸洗液中的酸性成分能够与钢板上的杂质发生化学反应,溶解并去除杂质。
在酸洗过程中,要注意控制酸洗液的温度、浓度和酸洗时间。
一般来说,酸洗温度在40℃到60℃之间,酸洗时间约为1到3分钟。
过高的温度和浓度可能会造成钢板表面的腐蚀,而过短的酸洗时间可能无法完全去除钢板表面的杂质。
2.3 清洗清洗是在酸洗后将钢板从酸洗槽中取出,经过清洗过程去除酸洗液残留和酸洗后产生的固体杂质。
清洗通常使用水进行,可以通过喷淋或浸泡的方式进行清洗,以确保酸洗液和固体杂质彻底去除。
在清洗过程中,要注意控制清洗水的流量、温度和清洗时间。
适当的水流量有助于冲刷掉酸洗液和固体杂质,而过高的温度和过长的清洗时间可能会对钢板表面造成损伤。
2.4 干燥干燥是将清洗后的钢板进行烘干的步骤,以防止钢板表面的水分引起锈蚀。
通常采用热风或热轧过程中的余热进行干燥。
干燥温度和时间要根据钢板厚度和材质的不同进行调整,以确保钢板表面干燥均匀。
3. 主要设备冷轧生产线酸洗工艺中的主要设备包括酸洗槽、清洗设备和干燥设备。
以下是这些设备的主要功能:3.1 酸洗槽酸洗槽可以用于储存和加热酸洗液,起到预热和酸洗钢板的作用。
冷轧酸洗工艺流程 (1)
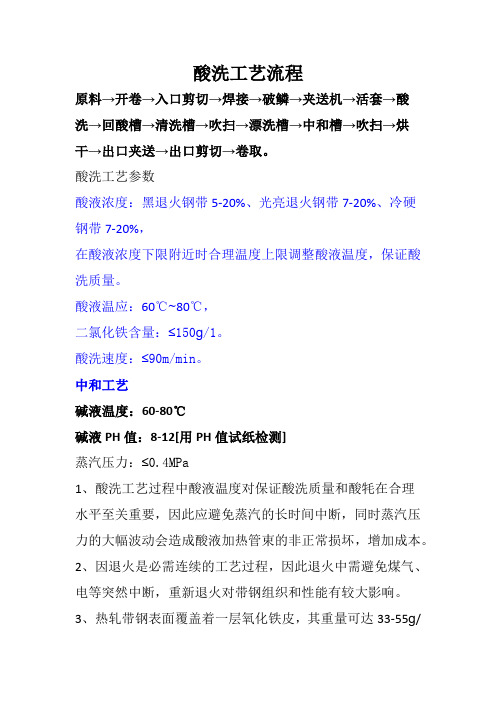
酸洗工艺流程原料→开卷→入口剪切→焊接→破鳞→夹送机→活套→酸洗→回酸槽→清洗槽→吹扫→漂洗槽→中和槽→吹扫→烘干→出口夹送→出口剪切→卷取。
酸洗工艺参数酸液浓度:黑退火钢带5-20%、光亮退火钢带7-20%、冷硬钢带7-20%,在酸液浓度下限附近时合理温度上限调整酸液温度,保证酸洗质量。
酸液温应:60℃~80℃,二氯化铁含量:≤150ɡ/1。
酸洗速度:≤90m/min。
中和工艺碱液温度:60-80℃碱液PH值:8-12[用PH值试纸检测]蒸汽压力:≤0.4MPa1、酸洗工艺过程中酸液温度对保证酸洗质量和酸牦在合理水平至关重要,因此应避免蒸汽的长时间中断,同时蒸汽压力的大幅波动会造成酸液加热管束的非正常损坏,增加成本。
2、因退火是必需连续的工艺过程,因此退火中需避免煤气、电等突然中断,重新退火对带钢组织和性能有较大影响。
3、热轧带钢表面覆盖着一层氧化铁皮,其重量可达33-55ɡ/㎡,厚度为7.5~15um,甚至可达20um,现代化热连轧机生产的带钢,其表面氧化铁皮厚度也约为10um。
4、为孓保证成口带钢的表面质量,降低力能消牦,减少轧辊磨损和有利带钢深加工,因此钢带冷轧前必须将氧化铁皮处除掉。
5、我们利用氧化铁皮与酸发生化学反应的基本原理,将钢带浸泡在一定浓度和温度的酸液中,并使钢带与酸液相对运动,加速化学反应速度,从而达到清除氧化铁皮的目的。
酸再生工艺流程:废酸收集→废酸过滤→废酸预浓缩→培烧再生→再生酸收集酸再生是将废酸液定量的送往酸再生装置再生成游离酸返回酸洗机组,同时得到氧化铁粉的一个体系。
酸再生过程是一个化学过程,浓缩废酸通过啧抢以雾状喷入焙烧炉内,焙烧炉通过两个喷嘴进行操作,操作期间煤气和空气流量自动控制,流量由孔板和差压传感器测量并在显示屏上显示。
煤气流量:200~300m /h,煤气压力:0.01mpa轧制工艺流程酸洗卷上卷→开卷→矫头→切头→焊接→活套入口夹送→充套→活套出口夹送→连轧(三机架或五机架)→测厚→卷取→分卷剪切→打包→卸卷→吊运技术参数工作辊直径:168mm~175mm(175-550-1388mm)中间辊直径:185mm~190mm(190-520-1244mm)外部支承辊直径:550mm(550-520-1576mm)轧辊辊面宽度:520mm轧制压力:550t~700t设计速度每秒:6米轧制:带钢不经加热而在室温下进行的轧制变形,我们称之为冷轧。
酸洗线主要工艺流程
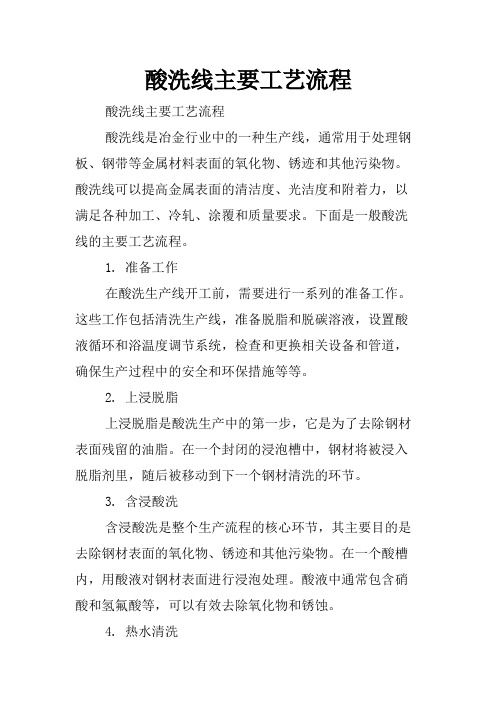
酸洗线主要工艺流程酸洗线主要工艺流程酸洗线是冶金行业中的一种生产线,通常用于处理钢板、钢带等金属材料表面的氧化物、锈迹和其他污染物。
酸洗线可以提高金属表面的清洁度、光洁度和附着力,以满足各种加工、冷轧、涂覆和质量要求。
下面是一般酸洗线的主要工艺流程。
1. 准备工作在酸洗生产线开工前,需要进行一系列的准备工作。
这些工作包括清洗生产线,准备脱脂和脱碳溶液,设置酸液循环和浴温度调节系统,检查和更换相关设备和管道,确保生产过程中的安全和环保措施等等。
2. 上浸脱脂上浸脱脂是酸洗生产中的第一步,它是为了去除钢材表面残留的油脂。
在一个封闭的浸泡槽中,钢材将被浸入脱脂剂里,随后被移动到下一个钢材清洗的环节。
3. 含浸酸洗含浸酸洗是整个生产流程的核心环节,其主要目的是去除钢材表面的氧化物、锈迹和其他污染物。
在一个酸槽内,用酸液对钢材表面进行浸泡处理。
酸液中通常包含硝酸和氢氟酸等,可以有效去除氧化物和锈蚀。
4. 热水清洗在进行酸洗之后,钢材表面会留下一定的酸液残留物。
在这一步,需要将钢材浸在高温热水中,以便清洗处理掉这些酸液残留物。
5. 脱碳脱碳是为了去除尚未被去除的硫酸盐和硝酸盐等酸性盐的残留。
在脱碳槽中,钢材将被浸泡在碱性溶液中,以便去除剩余的酸性盐,并将钢材表面呈现出最终的清洁状态。
6. 热风干燥在将钢材从清洁水中取出之后,需要进行干燥处理。
在热风干燥室中,将热空气引入烘干室,使钢材逐渐干燥。
其中,烘干机的温度、风速和烘干时间都需要根据不同的钢材材质和规格进行调节。
7. 油喷涂覆在烘干室的出口处,需要对钢材表面进行拍打、去鳞和喷涂油脂处理。
这样可以在起到润滑和保护钢材表面的同时,避免钢材变色、锈蚀等情况的出现。
以上就是一般酸洗生产线的主要工艺流程,无论是钢铁生产厂、汽车制造厂等都需要使用酸洗生产线来进行金属表面的清洗处理。
通过精细的操作和严密的监控,可以达到保证钢材质量的目的。
冷轧生产线酸洗工艺

紊流酸洗
引言
• 热轧带钢的表面铁鳞与酸液的化学反应速度受多方面因 素的影响,如酸液的浓度和温度、钢板表面温度等,不 可能无限制的提高。但另一方面,在实用的范围内,通 过提高酸洗速度,达到促进扩散,使钢板表面温度迅速 达到酸液的温度,这样就必须加快钢板表面的物质传递, 即酸和化学反应物的扩散,改善传导率。其方法就是使 酸液在带钢表面形成高速紊流,促进物质传递,达到使 钢板表面急速升温的目的,从而大大缩短酸洗时间。
浅槽酸洗
70年代中期。酸液深400~1000mm。
浅槽紊流酸洗
70年代末期,1983年德国MDS公司开发了紊流酸洗。酸液深小于 400mm 。
酸洗概述—三种酸洗技术的比较
参数比较 酸洗时间*,% 酸雾量*,% 电耗量*,% 热传递*,% 槽内带钢提升器 槽内带钢位置控制
深槽
浅槽
紊流
100
80
65
100
影响酸洗的因素
其它
• 最后应当指出的是,一些含碳量较高强度较大的中、 高碳钢,为了便于轧制,在酸洗之前都要进行退火 处理(初退火)。这些经过初退火的带钢,长时间 (大约24小时)在高温(约780℃)下加热,使得钢板
表面的氧化膜加厚,加之钢中的硅、铬等元素的原子在高 温下较多地从钢板内部向外扩散并与钢板表面的氧原子结 成难溶的氧化物,从而增加了酸洗的困难。为了除去这些 初退火后带钢表面生成的氧化铁皮,就必须增加酸的浓度、 延长酸洗时间或采用混合酸酸洗(如硫酸、酸洗时加入食 盐,形成硫酸和盐酸的混合酸)。
影响酸洗的因素
机械拉矫影响
• 带钢经拉伸矫直机反复弯曲变形后,由于氧化 铁皮与基铁的塑性不同,氧化铁皮将会不同程 度地从带钢表面上剥落下来或产生裂缝,因此, 破鳞将能明显地增加酸洗速度。实验指出,用 硫酸酸洗时,采用破鳞机可减少10%~50%的 酸洗时间。
山钢日照冷轧推拉式酸洗线工艺及设备特点简述
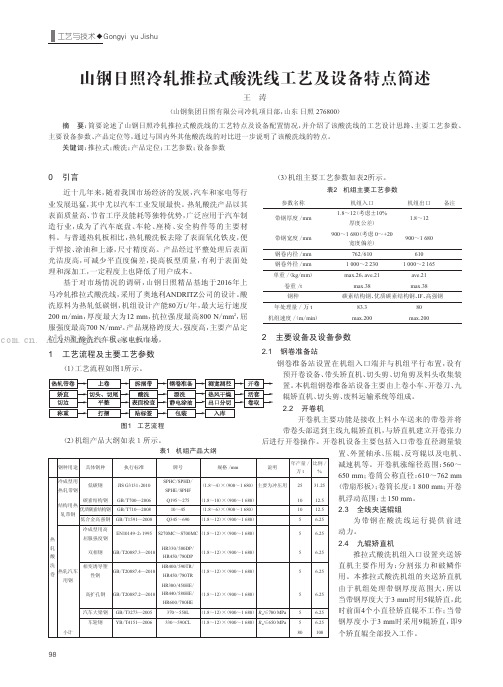
5
6.25
减速机等。 开卷机涨缩径范围:560~ 650 mm;卷筒公称直径:610~762 mm (带扇形板);卷筒长度:1 800 mm;开卷 机浮动范围:±150 mm。 2.3 全线夹送辊组
为带钢在酸洗线运行提供前进
冷成型用高
EN10149-2:1995 S270MC~S700MC (1.8~12)×(900~1 680)
牌号
规格 /mm
说明
年产量 / 比例 /
万t
%
SPHC/SPHD/ (1.8~4)×(900~1 680) 主要为冲压用 25
SPHE/SPHF
31.25
Q195~275 (1.8~10)×(900~1 680)
10
12.5
10~45
(1.8~6)×(900~1 680)
10
12.5
Q345~690 (1.8~12)×(900~1 680)
热
屈服强度钢
轧
HR330/580DP/
双相钢 GB/T20887.3—2010
(1.8~12)×(900~1 680)
酸
HR450/780DP
5
6.25
动力。
2.4 九辊矫直机
5
6.25
推拉式酸洗机组入口设置夹送矫
洗
相变诱导塑
卷 热轧汽车
性钢Байду номын сангаас
GB/T20887.4—2010
用钢
高扩孔钢 GB/T20887.2—2010
HR400/590TR/ (1.8~12)×(900~1 680)
HR450/780TR HR300/450HE/ HR440/580HE/ (1.8~12)×(900~1 680) HR600/780HE
冷轧酸洗工艺流程-(1)资料
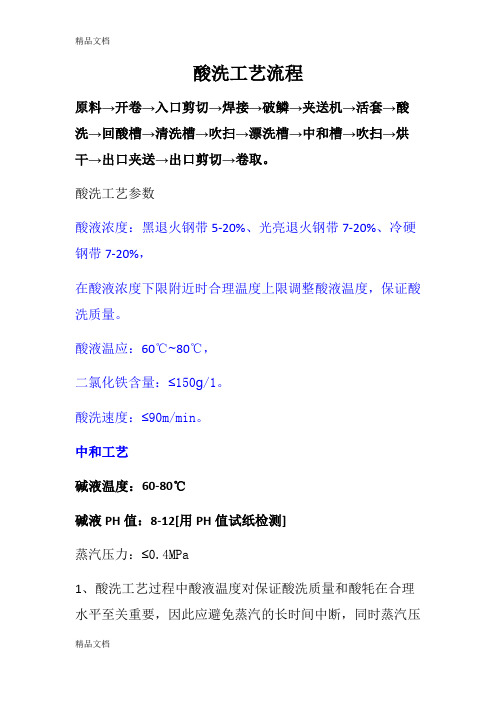
酸洗工艺流程原料→开卷→入口剪切→焊接→破鳞→夹送机→活套→酸洗→回酸槽→清洗槽→吹扫→漂洗槽→中和槽→吹扫→烘干→出口夹送→出口剪切→卷取。
酸洗工艺参数酸液浓度:黑退火钢带5-20%、光亮退火钢带7-20%、冷硬钢带7-20%,在酸液浓度下限附近时合理温度上限调整酸液温度,保证酸洗质量。
酸液温应:60℃~80℃,二氯化铁含量:≤150ɡ/1。
酸洗速度:≤90m/min。
中和工艺碱液温度:60-80℃碱液PH值:8-12[用PH值试纸检测]蒸汽压力:≤0.4MPa1、酸洗工艺过程中酸液温度对保证酸洗质量和酸牦在合理水平至关重要,因此应避免蒸汽的长时间中断,同时蒸汽压力的大幅波动会造成酸液加热管束的非正常损坏,增加成本。
2、因退火是必需连续的工艺过程,因此退火中需避免煤气、电等突然中断,重新退火对带钢组织和性能有较大影响。
3、热轧带钢表面覆盖着一层氧化铁皮,其重量可达33-55ɡ/㎡,厚度为7.5~15um,甚至可达20um,现代化热连轧机生产的带钢,其表面氧化铁皮厚度也约为10um。
4、为孓保证成口带钢的表面质量,降低力能消牦,减少轧辊磨损和有利带钢深加工,因此钢带冷轧前必须将氧化铁皮处除掉。
5、我们利用氧化铁皮与酸发生化学反应的基本原理,将钢带浸泡在一定浓度和温度的酸液中,并使钢带与酸液相对运动,加速化学反应速度,从而达到清除氧化铁皮的目的。
酸再生工艺流程:废酸收集→废酸过滤→废酸预浓缩→培烧再生→再生酸收集酸再生是将废酸液定量的送往酸再生装置再生成游离酸返回酸洗机组,同时得到氧化铁粉的一个体系。
酸再生过程是一个化学过程,浓缩废酸通过啧抢以雾状喷入焙烧炉内,焙烧炉通过两个喷嘴进行操作,操作期间煤气和空气流量自动控制,流量由孔板和差压传感器测量并在显示屏上显示。
煤气流量:200~300m /h,煤气压力:0.01mpa轧制工艺流程酸洗卷上卷→开卷→矫头→切头→焊接→活套入口夹送→充套→活套出口夹送→连轧(三机架或五机架)→测厚→卷取→分卷剪切→打包→卸卷→吊运技术参数工作辊直径:168mm~175mm(175-550-1388mm)中间辊直径:185mm~190mm(190-520-1244mm)外部支承辊直径:550mm(550-520-1576mm)轧辊辊面宽度:520mm轧制压力:550t~700t设计速度每秒:6米轧制:带钢不经加热而在室温下进行的轧制变形,我们称之为冷轧。
冷轧线酸洗工艺

冷轧线酸洗工艺1. 引言冷轧线酸洗工艺是冷轧钢板生产中的一个重要工艺环节。
通过酸洗工艺可以去除钢板表面的铁氧化物、锈蚀、尺寸偏差等缺陷,提高钢板的表面质量和尺寸精度。
本文将介绍冷轧线酸洗工艺的原理、流程以及常见的酸洗剂和设备。
2. 酸洗工艺原理在冷轧线酸洗工艺中,酸洗液主要起到去除表面缺陷和清洁钢板的作用。
酸洗液通常由一种或几种酸性溶液组成,如硫酸、盐酸、硝酸等。
这些酸洗剂可以与钢板表面的氧化物和锈蚀发生化学反应,使其溶解或转化为易于清洁的物质。
酸洗液还可以降低钢板表面的粗糙度,提高表面质量。
3. 酸洗工艺流程冷轧线酸洗工艺一般包括以下几个步骤:3.1 准备工作在进行酸洗之前,需要对待处理的钢板进行准备工作。
首先,需要检查钢板表面是否有明显的氧化物和锈蚀,如果发现有,则需要进行预处理,如机械除锈或喷砂处理。
其次,需要对酸洗设备进行检查和维护,确保其正常运行。
3.2 油脂去除将待处理的钢板放入去油槽中,使用油脂去除剂进行清洗。
油脂去除剂可以将钢板表面的油污和涂层去除,以减少酸洗液的消耗和污染。
3.3 酸洗将经过油脂去除处理的钢板放入酸洗槽中,浸泡一定时间,使酸洗液与钢板表面的铁氧化物和锈蚀发生反应。
酸洗时间一般根据钢板的厚度和表面质量要求进行调整。
3.4 清洗酸洗后的钢板需经过清洗工艺,以去除表面的酸洗液残留。
常用的清洗方法包括水清洗和碱洗。
水清洗可以将酸洗液冲洗掉,碱洗可以中和酸洗液的酸性残留。
3.5 防锈处理为防止酸洗后的钢板再次氧化和锈蚀,需要对其进行防锈处理。
常见的方法包括喷涂防锈液和烘干。
4. 常见的酸洗剂和设备4.1 酸洗剂•硫酸:具有强酸性和去除氧化物的能力,适用于处理高碳钢和不锈钢。
•盐酸:对于低碳钢和冷轧钢板,盐酸是一种常用的酸洗剂。
•硝酸:对于高碳钢和合金钢的酸洗具有较好的效果。
4.2 设备•酸洗槽:由耐酸材料制成的槽体,用于盛放酸洗液和钢板。
•喷淋装置:用于将酸洗液均匀地喷洒到钢板表面,以加速化学反应的进行。
冷轧不锈钢的退火及酸洗工艺

冷轧不锈钢的退火及酸洗工艺冷轧不锈钢的退火及酸洗工艺不锈钢热轧带钢经热带退火酸洗后,为了到达一定的性能及厚度要求,需进行常温轧制处理,即冷轧。
不锈钢冷轧时发生加工硬化,冷轧量越大,加工硬化的程度也越大,假设将加工硬化的材料加热到200—400℃就可以消除变形应力,进一步提高温度那么发生再结晶,使材料软化。
冷轧后的退火按退火方式分为连续卧式退火和立式光亮退火;按退火工序分为中间退火和最终退火。
顾名思义,中间退火是指中间轧制后的退火,而最终退火是指最终轧制后的退火,两者在工艺控制和退火目的上无根本区别,因此下文统称为冷轧退火或者退火。
一、连续卧式退火〔连退炉〕连退炉是目前广为使用的退火设备,广泛用于带钢的热处理,其特点是带钢在炉内呈水平状态,边加热边前进。
炉子的结构一般主要由预热段、加热段和冷却段组成。
卧式退火炉通常与开卷机、焊机、酸洗线等组成一条连续退火酸洗机组。
冷轧退火对不锈钢成品材料的机械性能有很大影响,如晶粒度、抗拉强度、硬度、延伸率和粗糙度等。
其中退火温度和退火时间对冷轧材料再结晶后的晶粒度具有最直接的影响。
晶粒度〔ASTM〕退火时间〔分〕图1.SUS304带钢1100℃时退火时间与晶粒度关系示意图如前所述,连退炉一般由预热、加热、冷却三大局部组成。
预热段没有烧嘴燃烧,而是利用后面加热段的辐射热来加热带钢,这样可以有效的利用热能,节约能源本钱。
加热段利用燃料燃烧直接对带钢进行加热,该段一般分为假设干各区,每个区都有高温计来控制和显示温度。
燃烧后高达700多度的废气被废气风机抽出加热室后进入换热器,在换热器内将冷的燃烧空气进行加热〔可加热到400多度〕,加热后的燃烧空气直接被送到各个烧嘴。
换热器的目的在于有效回收废气热量。
l炉内燃烧条件的管理。
燃料〔液化石油气或天然气〕在炉内的燃烧状况对质量、本钱、热效率等都有很大影响。
空燃比是燃烧管理的一个重要指标。
空燃比越高,燃烧越充分,但是排废量也相应增加,炉内氧含量提高,增加了带钢的氧化程度。
冷轧退火酸洗线

调质轧延机(SPM): 采用高光泽度的镜面辊对钢 带进行轧延,使钢带表面具 备一定的光泽度。 经由SPM轧延过的冷轧钢带 被称为冷轧2B钢带。
调质轧延机采用液压作为轧延力,轧延力工作范围在2000-10000KN之 间。 调质轧延机的工辊直径约800mm,辊面粗糙度约0.02um。 调质轧延机的配套附属设套分为四层,每层可以储存100米钢带,总共可以储存400米钢 带。 入口活套内有六台支撑小车,用来支撑活套内的钢带,当活套满套时, 支撑小车均匀分布在活套中;当活套空套时,支撑小车受活套车的牵 引收拢在一起。 入口活套有一台活套车,由入口活套卷扬机通过钢索牵引在活套中移 动以配合完成储存和释放钢带的过程。
冷轧退火酸洗线简介
入口区简介 除油区简介
酸区简介 脱硝系统简介
活套区简介
炉区简介
SPM和TLL简介
出口区简介
简介
英文全称:
Cool Rolled Annealing and Pickling Line
原因:
不锈钢经冷轧成薄板后,强度和硬度大大提高,成型性能差,无法直接 进入市场中使用,CAPL的作用是:对冷轧薄板进行加工退火,消除带钢应力, 通过中型电解和混酸酸洗将加工退火过程中产生的锈皮去除,最后经调质
除油区可分为喷洗区、刷洗区、清洗段和干燥机四个功能区段: 喷洗段:将脱脂剂溶液喷洗在钢带表面以去除钢带表面的轧延油。 刷洗段:通过高速旋转的刷洗滚轮对钢带表面进行刷洗。 清洗段:高温水冲洗去除钢带表面残留的脱脂剂。 干燥机:通过高温热空气去除钢带表面残留的液体。
入口活套区: 入口段运行的时候,入口活 套储存钢带;当入口段停下 来焊接的时候,入口活套释 出钢带以便中间制程段维持 稳定的速度生产。
冷轧酸洗工艺流程-完整

酸洗工艺流程原料→开卷→入口剪切→焊接→破鳞→夹送机→活套→酸洗→回酸槽→清洗槽→吹扫→漂洗槽→中和槽→吹扫→烘干→出口夹送→出口剪切→卷取。
酸洗工艺参数酸液浓度:黑退火钢带5-20%、光亮退火钢带7-20%、冷硬钢带7-20%,在酸液浓度下限附近时合理温度上限调整酸液温度,保证酸洗质量。
酸液温应:60℃~80℃,二氯化铁含量:≤150ɡ/1。
酸洗速度:≤90m/min。
中和工艺碱液温度:60-80℃碱液PH值:8-12[用PH值试纸检测]蒸汽压力:≤0.4MPa1、酸洗工艺过程中酸液温度对保证酸洗质量和酸牦在合理水平至关重要,因此应避免蒸汽的长时间中断,同时蒸汽压力的大幅波动会造成酸液加热管束的非正常损坏,增加成本。
2、因退火是必需连续的工艺过程,因此退火中需避免煤气、电等突然中断,重新退火对带钢组织和性能有较大影响。
3、热轧带钢表面覆盖着一层氧化铁皮,其重量可达33-55ɡ/㎡,厚度为7.5~15um,甚至可达20um,现代化热连轧机生产的带钢,其表面氧化铁皮厚度也约为10um。
4、为孓保证成口带钢的表面质量,降低力能消牦,减少轧辊磨损和有利带钢深加工,因此钢带冷轧前必须将氧化铁皮处除掉。
5、我们利用氧化铁皮与酸发生化学反应的基本原理,将钢带浸泡在一定浓度和温度的酸液中,并使钢带与酸液相对运动,加速化学反应速度,从而达到清除氧化铁皮的目的。
酸再生工艺流程:废酸收集→废酸过滤→废酸预浓缩→培烧再生→再生酸收集酸再生是将废酸液定量的送往酸再生装置再生成游离酸返回酸洗机组,同时得到氧化铁粉的一个体系。
酸再生过程是一个化学过程,浓缩废酸通过啧抢以雾状喷入焙烧炉内,焙烧炉通过两个喷嘴进行操作,操作期间煤气和空气流量自动控制,流量由孔板和差压传感器测量并在显示屏上显示。
煤气流量:200~300m/h,煤气压力:0.01mpa轧制工艺流程酸洗卷上卷→开卷→矫头→切头→焊接→活套入口夹送→充套→活套出口夹送→连轧(三机架或五机架)→测厚→卷取→分卷剪切→打包→卸卷→吊运技术参数工作辊直径:168mm~175mm(175-550-1388mm)中间辊直径:185mm~190mm(190-520-1244mm)外部支承辊直径:550mm(550-520-1576mm)轧辊辊面宽度:520mm轧制压力:550t~700t设计速度每秒:6米轧制:带钢不经加热而在室温下进行的轧制变形,我们称之为冷轧。
冷轧生产线酸洗工艺
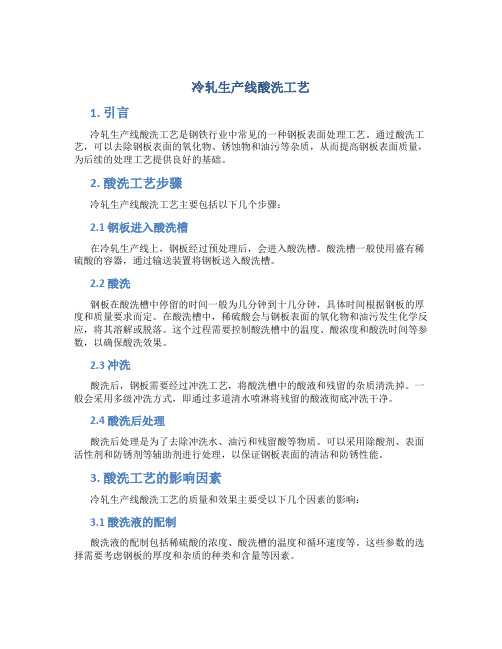
冷轧生产线酸洗工艺1. 引言冷轧生产线酸洗工艺是钢铁行业中常见的一种钢板表面处理工艺。
通过酸洗工艺,可以去除钢板表面的氧化物、锈蚀物和油污等杂质,从而提高钢板表面质量,为后续的处理工艺提供良好的基础。
2. 酸洗工艺步骤冷轧生产线酸洗工艺主要包括以下几个步骤:2.1 钢板进入酸洗槽在冷轧生产线上,钢板经过预处理后,会进入酸洗槽。
酸洗槽一般使用盛有稀硫酸的容器,通过输送装置将钢板送入酸洗槽。
2.2 酸洗钢板在酸洗槽中停留的时间一般为几分钟到十几分钟,具体时间根据钢板的厚度和质量要求而定。
在酸洗槽中,稀硫酸会与钢板表面的氧化物和油污发生化学反应,将其溶解或脱落。
这个过程需要控制酸洗槽中的温度、酸浓度和酸洗时间等参数,以确保酸洗效果。
2.3 冲洗酸洗后,钢板需要经过冲洗工艺,将酸洗槽中的酸液和残留的杂质清洗掉。
一般会采用多级冲洗方式,即通过多道清水喷淋将残留的酸液彻底冲洗干净。
2.4 酸洗后处理酸洗后处理是为了去除冲洗水、油污和残留酸等物质。
可以采用除酸剂、表面活性剂和防锈剂等辅助剂进行处理,以保证钢板表面的清洁和防锈性能。
3. 酸洗工艺的影响因素冷轧生产线酸洗工艺的质量和效果主要受以下几个因素的影响:3.1 酸洗液的配制酸洗液的配制包括稀硫酸的浓度、酸洗槽的温度和循环速度等。
这些参数的选择需要考虑钢板的厚度和杂质的种类和含量等因素。
3.2 酸洗时间酸洗时间是指钢板在酸洗槽中停留的时间。
时间过短会导致酸洗效果不好,时间过长则浪费资源。
因此,酸洗时间的控制非常关键。
3.3 温度控制酸洗槽中的温度对酸洗效果有重要影响。
一般情况下,较高的温度可以加快化学反应速率,但过高的温度可能会导致钢板表面脱碳,影响钢板的性能。
3.4 冲洗水质量冲洗水的质量对去除酸液和杂质有很大影响。
如果冲洗水质量不好,可能会带来新的污染问题。
因此,冲洗水的净化和循环利用非常重要。
4. 酸洗工艺的优缺点冷轧生产线酸洗工艺具有如下优点:•能够有效去除钢板表面的氧化物、锈蚀物和油污等杂质;•提高钢板表面质量,使其更适合后续加工工艺;•可以改善钢板的防锈性能。
- 1、下载文档前请自行甄别文档内容的完整性,平台不提供额外的编辑、内容补充、找答案等附加服务。
- 2、"仅部分预览"的文档,不可在线预览部分如存在完整性等问题,可反馈申请退款(可完整预览的文档不适用该条件!)。
- 3、如文档侵犯您的权益,请联系客服反馈,我们会尽快为您处理(人工客服工作时间:9:00-18:30)。
酸液种类
酸液种类 比较项目 1.溶解氧化物的能力 2.浓度提高时,去除氧化物 机理 3.提高酸洗效率途径
4.对带钢基体溶解的能力 5.洗完好带钢表面的质量
盐酸
硫酸
快
慢
主要靠溶解
提高浓度显 著 小 好
主要靠机械剥 离 提高温度显著
大 差
结论——总体来说,酸洗效果:盐酸>硫酸
影响酸洗的因素
酸液温度、浓度(以盐酸为例)
酸洗原理—氧化铁皮的形成
Fe
FeO Fe3O4 Fe2O3
O
酸洗原理—氧化铁皮的形成
温度
1200
Fe3O4
γFe+FeO
Fe2O3
FeOБайду номын сангаасFe3O4 FeO
1000
Fe3O4 + Fe2O3
800
αFe+FeO
600
αFe+Fe3O4
400
含氧量
22
24
26
铁氧状态图
28
30
32
酸洗原理—氧化铁皮的形成
酸洗原理—带钢表面氧化铁皮的可酸洗性
所用酸液因素
酸洗可能性
外部拉矫因素
氧化铁皮因素
酸洗原理—酸洗机理
• 溶解作用:氧化铁皮与酸发生化学 反应而被溶解。 • 机械剥离作用:金属铁与酸作用生 成氢气,机械地剥离氧化铁皮。 • 还原作用:生成的原子氢使铁的氧 化物还原成易于酸作用的亚铁氧化 物,然后再与酸作用而被除去。
深槽酸洗
70年代中期。酸液深400~1000mm。
浅槽酸洗
浅槽紊流酸洗
70年代末期,1983年德国MDS公司开发了紊流酸洗。酸液深 小于400mm 。
酸洗概述—三种酸洗技术的比较
参数比较 酸洗时间*,% 酸雾量*,% 电耗量*,% 热传递*,% 槽内带钢提升器 槽内带钢位置控制 槽内断带事故处理 深槽 100 100 100 100 有必要 不可能准确检测 困难,费时 浅槽 80 60 70 200 没必要 可以准确检测 容易 紊流 65 60 70 700 没必要 可以准确检 测 容易
酸洗原理—有利于酸洗的氧化铁皮
• 卷曲温度
FeO Fe3O4 Fe2O3 体积总分子量
FeO
Fe3O4
温度(摄氏度)700 900
Fe2O3
1100
氧化温度对氧化铁皮的影响图
酸洗原理—有利于酸洗的氧化铁皮
•轧辊粗糙度
酸洗原理—有利于酸洗的氧化铁皮
结论: 对酸洗有利影响的带钢应满足 低的终轧温度和较高的轧制速度 低的卷曲温度 较高的冷却速度 光滑的轧辊
酸 洗 时 间
某浓度酸液在一定 温度下,酸洗时间 随铁盐含量的变化 曲线
FeCl2含量
• 酸含量增加和温度升高时,酸洗时间可减少,且随着 FeCl2含量的增加,酸洗时间急剧减少到最小,此时 FeCl2的浓度比饱和浓度低4%~8%。以后,酸洗时间又 急剧增加,一直到FeC12达到饱和,酸洗时间最长。酸溶 液温度越低,酸洗时间的最小值也就越明显。最短的酸洗 时间是在FeCl2最佳含量的情况下得到的,即FeCl2的浓 度低于饱和浓度4~8%。
H H2
Fe2O3+H
→ FeO+H2O
基铁
Fe3O4+H → FeO+H2O
FeCl3+H → FeCl2+HCl
影响酸洗的因素
• 材料物理性因素 • 工艺因素
影响酸洗的因素
影响酸洗的因素
材料性因素 氧化铁皮组成 氧化铁皮厚度 钢铁成份及合金组成 酸液种类 酸液温度 酸液浓度 工艺因素
带钢厚度
影响酸洗的因素
其它 • 最后应当指出的是,一些含碳量较高强度较大的 中、高碳钢,为了便于轧制,在酸洗之前都要进 行退火处理(初退火)。这些经过初退火的带钢, 长时间(大约24小时)在高温(约780℃)下加热, 使得钢板表面的氧化膜加厚,加之钢中的硅、铬 等元素的原子在高温下较多地从钢板内部向外扩 散并与钢板表面的氧原子结成难溶的氧化物,从 而增加了酸洗的困难。为了除去这些初退火后带 钢表面生成的氧化铁皮,就必须增加酸的浓度、 延长酸洗时间或采用混合酸酸洗(如硫酸、酸洗 时加入食盐,形成硫酸和盐酸的混合酸)。
酸洗原理—带钢氧化铁皮组织结构
磁性体Fe3O4
富氏体FeO 带钢基体
蓝灰色氧化铁皮表面,生成温度大于1100℃
酸洗原理—带钢氧化铁皮组织结构
结论: 经过一般的热轧和退火后,氧化铁皮由FeO 相组成,Fe3O4层仅为氧化铁皮层的4~18%, 在许多情况下没有Fe2O3。且氧化铁皮层不 分层的,在铁被氧化的同时,体积增大使 氧化铁皮层出现裂缝和起皮,从而使生成 的氧化铁相互渗透而且是不规则的。
FeO Fe3O4 Fe2O3 体积总分子量
FeO
Fe3O4
温度(摄氏度)700 900
Fe2O3
1100
氧化温度对氧化铁皮的影响图
酸洗原理—带钢氧化铁皮组织结构
由于热轧带钢的化学成分、轧制温度、轧 制后的冷却速度及卷取温度的不同,所以 带钢表面上所生成的氧化铁皮的结构、厚 度性质亦有所不同。
酸洗原理—有利于酸洗的氧化铁皮
影响带钢表面氧化铁皮的因素 终轧温度及速度 冷却速度 卷曲温度 轧辊粗糙度
酸洗原理—有利于酸洗的氧化铁皮
• 终轧温度和轧制速度
氧化铁皮厚度
氧化时间
氧化速度
轧制速度
准确 控制 轧制 速度
温度(摄氏度)400
600 800
1200
卷曲温度
FeO
Fe3O4
酸洗原理—有利于酸洗的氧化铁皮
酸洗概述—酸洗定义
酸洗是用化学方法除去金属表面氧化铁皮的 过程,通常采用盐酸(HCl),因此也叫化 学酸洗。
酸洗概述—酸洗目的
目的:去除热轧带钢表面的氧化铁皮(铁锈)
• 轧制时会将氧化铁皮压入带钢基体,影响 冷轧板表面质量及加工性能。 • 氧化铁皮破碎后进入冷却润滑的乳化液系 统,损坏设备并缩短乳化液使用寿命。 • 损坏轧辊。
@ @
@ @ @ @ @
穿带速度高
运行速度高
@
@
酸洗原理—氧化铁皮的形成
氧化铁皮是金属在加热、热处理或在热状态 进行加工时形成的一层附着在金属表面上的 金属氧化物。
酸洗原理—氧化铁皮的形成
轧件经粗轧后沿辊道向热连轧轧机运行时,温度 为1000℃左右,这时在轧件表面上已生成了一层 薄的氧化铁皮,而轧前高压水除鳞机可将它们清 除掉。当轧件在连轧机上轧制时,板坯在各机架 轧机间暴露的时间极短,而且大的压下阻碍了带 钢表面上形成厚的氧化铁皮,而所形成的氧化薄 膜立即被破坏并受到水的冲洗,因此,可以说刚 刚从精轧末机架出来的带钢,虽然温度有780~ 850℃的较高温度,但带钢表面的氧化铁皮是极 薄的。带钢从精轧末机架出来后,进入喷水装置, 而后卷成带钢卷并缓慢冷却,就是在这段时间里, 带钢表面被氧化而生成氧化铁皮。
酸洗概述—酸洗机组的比较:推拉式酸洗机组
• 推拉式酸洗机组酸洗,每根带钢经夹送辊依次 咬入,不用焊接,推送向前,直至卷取,逐卷 带钢间断地通过酸洗机组。
酸洗概述—酸洗机组的优缺点比较
比较项目 连续 推拉
设备简单 设备重量轻
厂房高度较低 投资省 组织生产灵活性 酸洗时间短,加热启动快,调节酸液成分快 重新启动时无需引带 动力剪外还可使用拉剪 改善带钢平直度能力较好 @ @ @
酸洗原理—酸洗机理
溶解作用
FeO+HCl→FeCl2+H2O Fe3O4+HCl→FeCl3+FeCl2+H2O
反应能力
Fe2O3+HCl →FeCl3+H2O
Fe+HCl→FeCl2+H2 Fe+H2SO4→FeSO4+H2 FeO+H2SO4→FeSO4+H2O Fe3O4+H2SO4→Fe2(SO4)3+FeSO4+H2O
酸洗原理—氧化铁皮的形成
结论:带钢表面的氧化铁皮是热轧带钢在 终轧后、卷曲时及冷却时产生的。
酸洗原理—氧化铁皮的形成
在从精轧末机架出来的带钢表面上,铁原 子首先与空气中的氧原子结合形成第一层 氧化物,这层氧化物可能是致密的Fe3O4, 或者是疏松的FeO。在第一种情况下,氧化 铁皮的进一步增长过程可能只靠氧和铁的 离子扩散来进行的;在第二种情况下,空 气中的氧可自由地通过多孔、疏松的氧化 铁皮,而使氧化铁皮加厚和致密化。无论 上述哪种情况,最终结果就是形成了我们 通常所看到的带钢表面的氧化铁皮。
酸洗原理—带钢氧化铁皮组织结构
酸洗原理—带钢氧化铁皮组织结构 氧化铁Fe2O3 磁性体Fe3O4 富氏体FeO 带钢基体
红色氧化皮表面,生成温度570~1100℃
酸洗原理—带钢氧化铁皮组织结构 氧化铁Fe2O3
磁性体Fe3O4
带钢基体
红色氧化皮表面,生成温度570~1100℃, 但从570℃开始缓冷
反应能力
Fe2O3+H2SO4→Fe2(SO4)3+H2O
酸洗原理—酸洗机理
机械剥离作用
Fe2O3 Fe3O4 FeO
Fe+HCl →FeCl2+H2
(占33%)
Fe+H2SO4→FeSO4+H2
(占78%)
基铁
酸洗原理—酸洗机理
还原作用
Fe2O3 Fe3O4 FeO Fe+HCl →FeCl2+H2
• 提高酸液的浓度和温度也同样能够增加酸洗速度。如前 所述,在盐酸酸洗中,浓度对酸洗速度的影响大于温度 对酸洗速度的影响。例如,当酸浓度从2%增大至经 25%时,盐酸酸洗的速度增加约10倍。当温度自18℃升 高至60℃时,盐酸酸洗速度提高9~10倍。