φ950可逆式轧机压下装置设计
轧钢机下压机构设计-正文

1 引言轧机的压下装置是轧机的重要结构之一,用于调整辊缝,也称辊缝调整装置,其结构设计的好坏,直接关系着轧件的产量与质量。
压下装置按传动方式可分为手动压下、电动压下和液压压下,手动压下装置一般多用于不经常进行调节、轧件精度要求不严格、以及轧制速度要求不高的中、小型型钢、线材和小型热轧板带轧机上。
电动压下装置适用于板坯轧机、中厚板轧机等要求辊缝调整范围大、压下速度快的情况,主要由压下螺丝、螺母及其传动机构组成。
在中厚板轧机中,工作时要求轧辊快速、大行程、频繁的调整,这就要求压下装置采用惯性小的传动系统,以便频繁的启动、制动,且有较高的传动效率和工作可靠性。
这种快速电动压下装置轧机不能带钢压下,压下电机的功率一般是按空载压下考虑选用,所以常常由于操作失误、压下量过大等原因产生卡钢、“坐辊”或压下螺丝超限提升而发生压下螺丝无法退回的事故,这时上辊不能动,轧机无法正常工作,压下电动机无法提起压下螺丝,为了克服这种卡钢事故,必须增设一套专用的回松机构。
电动压下装置的主要缺点之一是运动部分的惯性大,因而在辊缝调节过程中反应慢、精度低,对现代化的高速度、高精度轧机已不适应,提高压下装置响应速度的主要途径是减少其惯性,而用液压控制可以收到这样的效果。
液压压下装置,就是取消了传统的电动压下机构,其辊缝的调节均由液压缸来完成。
在这一装置中,除液压缸以及与之配套的伺服阀和液压系统外,还包括检测仪表及运算控制系统。
全液压压下装置有以下优点:1、惯性小、动作快,灵敏度高,因此可以得到高精度的板带材,其厚度偏差可以控制到小于成品厚度的1%,而且缩短了板带材的超差部分长度,提高了轧材的成品率,节约金属,提高了产品质量,并降低了成本;2、结构紧凑,降低了机座的总高度,减少了厂房的投资,同时由于采用液压系统,使传动效率大大提高;3、采用液压系统可以使卡钢迅速脱开,这样有利于处理卡钢事故,防止了轧件对轧辊的刮伤、烧伤,再启动时为空载启动,降低了主电机启动电流,并有利于油膜轴承工作;4、可以实现轧辊迅速提升,便于快速换辊,提高了轧机的有效作业率,增加了轧机的产量。
中厚板压下规程设计

一.制定生产工艺及工艺制度1.生产工艺:选择坯料——原料清理——加热——除鳞——纵轧一道(使宽度接近成品宽度)——转90˚横轧到底——矫直——冷却——表面检查——切边——定尺——表面尺寸形状检查——力学性能试验——标记——入库——发货2.工艺制度:在保证压缩比的条件下,坯料尺寸尽量小。
加热时出炉温度应在1120˚—1150˚,温度不要过高,以免发生过热或过烧现象;用高压水去除表面的氧化铁皮,矫直时选用辊式矫直机矫直,开始冷却温度一般要尽量接近终轧温度,轧后快冷到相变温度以下,冷却速度大多选用5—10˚C或稍高一些。
切边用圆盘式剪切机进行纵剪,然后用飞剪定尺。
二.选择坯料1.根据生产经验和实践,目前生产中厚板选择连铸坯已成为主流,所以选择连铸坯2.坯料尺寸的确定坯。
(1)坯料厚度的确定:根据经验,压缩比在6—10之间较好,本设计取10,由成品厚度h=13mm知H=10h=130mm。
(2)坯料宽度的确定假设先轧两道,压下量分别为20mm和10mm,且设两道轧后其长度等于宽度。
假设轧后金属烧损不计,考虑切头尾,切边。
在我国切头尾一般为500mm—2500mm取Δl=500mm,切边Δb=100mm,由体积不变定理得Bˊ×Lˊ×[H-(20+10)]=(l+2×500)×(b+2×100)×13因为Bˊ=Lˊ所以Bˊ=Lˊ=(9000+2×500)(1900+2×100)×13/[130-(20+10)]=1650mm(3)坯料长度的确定由H,B,Bˊ,Lˊ由体积不变定理得H×B×L=Hˊ×Bˊ×Lˊ得L=1270mm三.变形量分配1.根据经验,中厚板压下量在Δh=12mm左右,这里取Δh=12mm2.分配各道次压下量,计算各道次变形程度,轧件尺寸及轧制道次(1)由H=130mm,h=13mm,取轧制道次n=12(二辊7道四辊五道)(2)第一道,先用展宽轧制把坯料的宽度B轧成b(或接近b)且不考虑长度变化由体积不变定理得B×L×H=B×L×(H-Δh1)得Δh1=17mm则变形程度ε1=Δh/H×100%=13.08%轧后轧件尺寸为113×1900×1270mm同理其余道次压下量分配,变形程度,轧件尺寸如下表所示四.设计变形工具1.设计二辊(1)辊身长度L:由L=bmax+a bmax=1900mm 当b=1000-2500mm a=150-200mm 取a=200mm所以L=1900+200=2100mm(2)辊径尺寸中厚板轧机L/D=2.2-2.8 取L/D=2.6 得D=808mm 取810mm(3)辊颈尺寸查表3-5 取d/D=0.75(轧钢机械邹家祥主编) 得d=608mm取d=600mm辊颈长度l 取d/l=1 得l=600mm(3)辊头设计因为对于中厚板轧机来说轧辊调整行程比较大,倾角在8˚-12˚间所以应选择万向辊头。
轧机压下装置设计计算
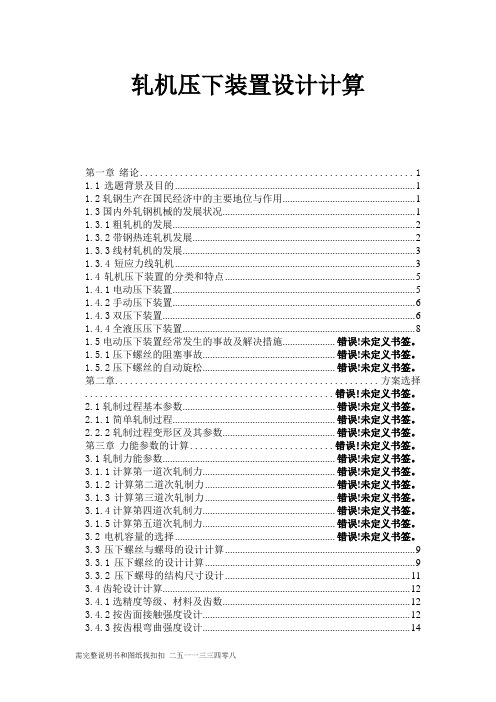
轧机压下装置设计计算第一章绪论 (1)1.1选题背景及目的 (1)1.2轧钢生产在国民经济中的主要地位与作用 (1)1.3国内外轧钢机械的发展状况 (1)1.3.1粗轧机的发展 (2)1.3.2带钢热连轧机发展 (2)1.3.3线材轧机的发展 (3)1.3.4短应力线轧机 (3)1.4轧机压下装置的分类和特点 (5)1.4.1电动压下装置 (5)1.4.2手动压下装置 (6)1.4.3双压下装置 (6)1.4.4全液压压下装置 (8)1.5电动压下装置经常发生的事故及解决措施..................... 错误!未定义书签。
1.5.1压下螺丝的阻塞事故..................................................... 错误!未定义书签。
1.5.2压下螺丝的自动旋松..................................................... 错误!未定义书签。
第二章..................................................... 方案选择.................................................. 错误!未定义书签。
2.1轧制过程基本参数............................................................. 错误!未定义书签。
2.1.1简单轧制过程................................................................. 错误!未定义书签。
2.2.2轧制过程变形区及其参数............................................. 错误!未定义书签。
第三章力能参数的计算............................. 错误!未定义书签。
950可逆式轧机结构设计说明书

目录引言 (5)第1章概述 (6)1.1 1轧钢机的发展 (6)1.2 1轧钢机类型及组成 (6)1.3轧钢机压下系统的发展 (6)1.3.1 万能式板坯初轧机迅速发展。
(6)1.3.2 向重型化发展。
(6)1.3.3 缩短轧机辅助机械工作时间。
(6)1.3.4 采用自动化控制。
(7)1.3.5 总结 (7)1.4φ950可逆式轧机主传动 (7)第2章总体设计方案 (8)2.1主传动 (8)2.2机架 (8)2.3轧辊 (8)2.4轧辊轴承 (8)2.5万向接轴 (8)2.6压下装置 (8)2.6.1 压下装置的作用: (8)2.6.2 快速压下装置工艺特点: (9)2.6.3 平衡装置 (9)第3章力能参数的计算 (10)3.1轧制力能参数 (10)3.1.1 轧制时接触弧上平均单位压力 (10)3.1.2 轧制力的计算 (12)3.1.3 轧制力矩的计算 (13)3.1.4 主电动机力矩 (15)3.2各道次轧件断面和当量长度 (17)3.3各道次轧制时间的确定 (18)3.4主电动机的选用 (19)3.4.1 选择电动机的原则: (19)3.4.2 根据过载条件选择电动机容量 (19)3.4.3 电动机的发热校核 (20)第4章零件的强度计算和校核 (23)4.1机架的设计 (23)4.1.1 机架的形式: (23)4.1.2 机架强度的计算 (23)4.1.3 机架应力的计算和校核 (27)4.2轧辊强度的校核 (28)4.2.1 轧件咬入条件的校核 (29)4.2.2 辊身、辊颈强度的校核 (30)4.3万向接轴的选用及校核 (32)4.3.1 开口式扁头受力分析和强度计算 (32)4.3.2 闭口式扁头受力分析和强度计算 (35)4.3.3 叉头受力分析和强度计算 (36)第5章轧钢机械的润滑 (37)5.1轧钢机械润滑的特点 (37)5.2润滑的方法 (37)5.3润滑的种类 (37)5.4Φ950可逆式轧机部件的润滑方式 (38)第6章压下装置的设计 (39)6.1压下螺丝的设计 (39)6.1.1 压下螺丝的计算 (39)6.1.2 压下螺丝的校核: (40)6.2压下螺母的设计 (40)6.2.1 压下螺母的计算 (41)6.2.2 压下螺母的校核 (41)6.3压下螺丝的传动力矩 (41)6.4压下电动机的选择 (43)6.5压下装置的耐磨校核 (44)6.6压下装置螺纹牙的强度校核 (44)6.7压下装置自锁的校核及松脱的措施 (45)结论 (46)附录A (48)表目录表3.1Ф950钢坯轧制图表(MM) (10)表3.2第一道次数据 (12)表3.3第二道次数据 (13)表3.4第三道次数据 (15)表3.5第五道次数据 (17)表3.6各道次轧件断面和当量长度(MM) (18)表3.7各道次轧制时间(S) (19)表5.1润滑方式 (38)图目录图3-1简单轧制时作用在轧辊上的力 (14)图3-2可逆运转电动机转速和力矩与时间的关系图 (20)图4-1矩形自由框架弯曲力矩图 (24)图4-2横梁简图 (25)图4-3立柱简图 (26)图4-4闭式机架中的应力图 (27)图4-5开始咬入(A)及咬入后(B)作用于轧件上的力 (29)图4-6轧辊的弯曲、扭转力矩图 (31)图4-7开口式扁头受力分析简图 (33)图4-8闭口式扁头受力简图 (35)图6-1压下螺丝受力平衡图 (42)引言Φ950可逆轧机的设计- 压下装置的设计是我毕业项目的内容。
950轧机设计说明书
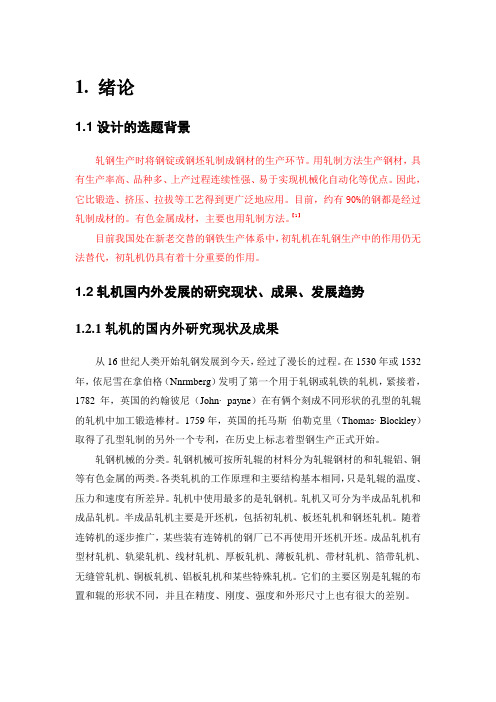
1. 绪论1.1设计的选题背景轧钢生产时将钢锭或钢坯轧制成钢材的生产环节。
用轧制方法生产钢材,具有生产率高、品种多、上产过程连续性强、易于实现机械化自动化等优点。
因此,它比锻造、挤压、拉拔等工艺得到更广泛地应用。
目前,约有90%的钢都是经过轧制成材的。
有色金属成材,主要也用轧制方法。
【1】目前我国处在新老交替的钢铁生产体系中,初轧机在轧钢生产中的作用仍无法替代,初轧机仍具有着十分重要的作用。
1.2轧机国内外发展的研究现状、成果、发展趋势1.2.1轧机的国内外研究现状及成果从16世纪人类开始轧钢发展到今天,经过了漫长的过程。
在1530年或1532年,依尼雪在拿伯格(Nnrmberg)发明了第一个用于轧钢或轧铁的轧机,紧接着,1782年,英国的约翰彼尼(John·payne)在有俩个刻成不同形状的孔型的轧辊的轧机中加工锻造棒材。
1759年,英国的托马斯伯勒克里(Thomas· Blockley)取得了孔型轧制的另外一个专利,在历史上标志着型钢生产正式开始。
轧钢机械的分类。
轧钢机械可按所轧辊的材料分为轧辊钢材的和轧辊铝、铜等有色金属的两类。
各类轧机的工作原理和主要结构基本相同,只是轧辊的温度、压力和速度有所差异。
轧机中使用最多的是轧钢机。
轧机又可分为半成品轧机和成品轧机。
半成品轧机主要是开坯机,包括初轧机、板坯轧机和钢坯轧机。
随着连铸机的逐步推广,某些装有连铸机的钢厂已不再使用开坯机开坯。
成品轧机有型材轧机、轨梁轧机、线材轧机、厚板轧机、薄板轧机、带材轧机、箔带轧机、无缝管轧机、铜板轧机、铝板轧机和某些特殊轧机。
它们的主要区别是轧辊的布置和辊的形状不同,并且在精度、刚度、强度和外形尺寸上也有很大的差别。
1.2.2初轧机的发展趋势总的来说,轧钢机械向着大型、连续高速和计算机控制方向发展。
初轧机的发展,在发展连铸的同时,国外仍在新建或扩建初轧机,以扩大开坯能力。
这是由于开坯机具有产品变化灵活,便于实现自动化等优点,如日本1969年有三台板坯初轧机和一台方坯初轧机投入生产。
中厚板轧机压下规程设计说明
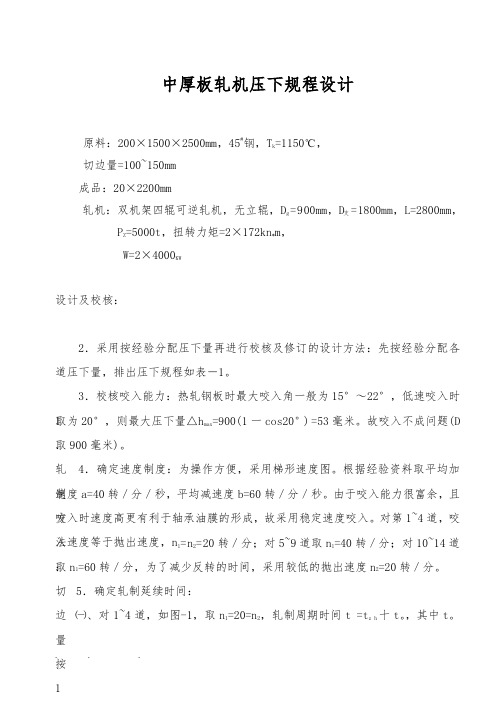
中厚板轧机压下规程设计原料:200×1500×2500mm ,45#钢,T k =1150℃, 切边量=100~150mm 成品:20×2200mm轧机:双机架四辊可逆轧机,无立辊,D g =900mm ,D 支=1800mm ,L=2800mm ,P Z =5000t ,扭转力矩=2×172kn *m , W=2×4000KW设计及校核:1.轧制方法:切边量2.采用按经验分配压下量再进行校核及修订的设计方法:先按经验分配各道压下量,排出压下规程如表-1。
3.校核咬入能力:热轧钢板时最大咬入角一般为15°~22°,低速咬入时取为20°,则最大压下量△h max =900(1一cos20°) =53毫米。
故咬入不成问题(D 取900毫米)。
4.确定速度制度:为操作方便,采用梯形速度图。
根据经验资料取平均加速度a=40转/分/秒,平均减速度b=60转/分/秒。
由于咬入能力很富余,且咬入时速度高更有利于轴承油膜的形成,故采用稳定速度咬入。
对第1~4道,咬入速度等于抛出速度,n 1=n 2=20转/分;对5~9道取n 1=40转/分;对10~14道取n 1=60转/分,为了减少反转的时间,采用较低的抛出速度n 2=20转/分。
5.确定轧制延续时间:㈠、对1~4道,如图-1,取n 1=20=n 2,轧制周期时间t =t z h 十t 。
,其中t 。
为间隙时间,t zh 为纯轧时间,v 为t zh 时间的轧制速度,l +为在t zh 时间轧过的轧件长度,l 为该道轧后轧件长度,则:l BHL h =v = 160D n π米/秒t zh =图 1对第1道 v = 160D n π米/秒 = 3.149002060⨯⨯=0.942米/秒t zh =166795942+=1.87秒 计算各道次v 、t zh 列入表-1。
四辊可逆轧机设计说明(新)
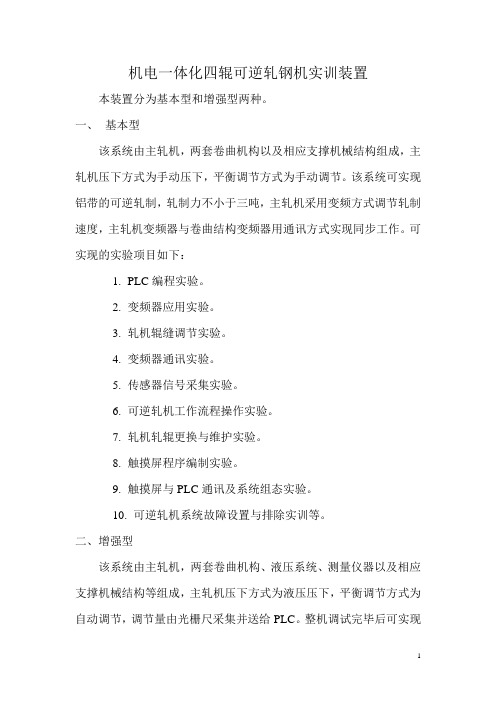
机电一体化四辊可逆轧钢机实训装置本装置分为基本型和增强型两种。
一、基本型该系统由主轧机,两套卷曲机构以及相应支撑机械结构组成,主轧机压下方式为手动压下,平衡调节方式为手动调节。
该系统可实现铝带的可逆轧制,轧制力不小于三吨,主轧机采用变频方式调节轧制速度,主轧机变频器与卷曲结构变频器用通讯方式实现同步工作。
可实现的实验项目如下:1.PLC编程实验。
2.变频器应用实验。
3.轧机辊缝调节实验。
4.变频器通讯实验。
5.传感器信号采集实验。
6.可逆轧机工作流程操作实验。
7.轧机轧辊更换与维护实验。
8.触摸屏程序编制实验。
9.触摸屏与PLC通讯及系统组态实验。
10.可逆轧机系统故障设置与排除实训等。
二、增强型该系统由主轧机,两套卷曲机构、液压系统、测量仪器以及相应支撑机械结构等组成,主轧机压下方式为液压压下,平衡调节方式为自动调节,调节量由光栅尺采集并送给PLC。
整机调试完毕后可实现铝带的自动可逆轧制,轧制参数由触摸屏输入。
轧制力不小于三吨,主轧机采用变频方式调节轧制速度,主轧机变频器与卷曲机构变频器用通讯方式实现同步工作。
可实现的实验项目如下:1. PLC编程实验。
2. 变频器应用实验。
3. 轧机辊缝调节实验。
4. 变频器通讯实验。
5. 传感器信号采集实验。
6. 可逆轧机工作流程操作实验。
7. 轧机轧辊更换与维护实验。
8. 触摸屏程序编制实验。
9. 触摸屏与PLC通讯及系统组态实验。
10. 可逆轧机系统故障设置与排除实训等。
11. PLC数据采集与闭环调节编程实验。
12. 光栅尺应用试验。
13. 液压系统调试试验。
14. 液压系统自动控制实验。
三、两种系统配置清单如下:基础型:增强型:基础型报价:35万元增强型报价:53万元。
2150四辊可逆式粗轧机压下系统设计
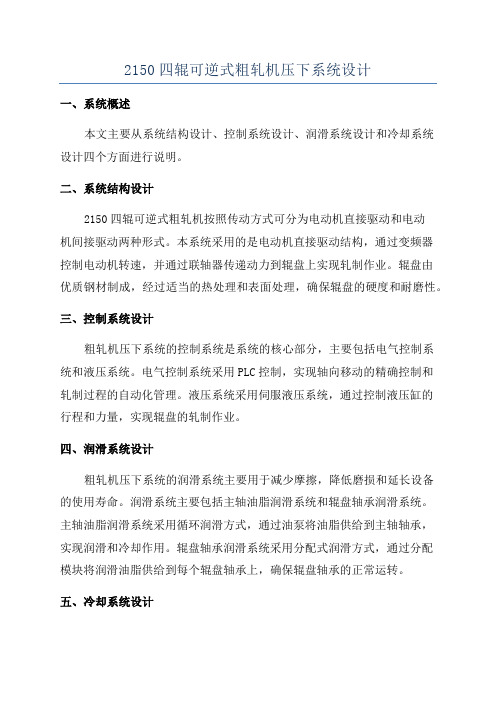
2150四辊可逆式粗轧机压下系统设计一、系统概述本文主要从系统结构设计、控制系统设计、润滑系统设计和冷却系统设计四个方面进行说明。
二、系统结构设计2150四辊可逆式粗轧机按照传动方式可分为电动机直接驱动和电动机间接驱动两种形式。
本系统采用的是电动机直接驱动结构,通过变频器控制电动机转速,并通过联轴器传递动力到辊盘上实现轧制作业。
辊盘由优质钢材制成,经过适当的热处理和表面处理,确保辊盘的硬度和耐磨性。
三、控制系统设计粗轧机压下系统的控制系统是系统的核心部分,主要包括电气控制系统和液压系统。
电气控制系统采用PLC控制,实现轴向移动的精确控制和轧制过程的自动化管理。
液压系统采用伺服液压系统,通过控制液压缸的行程和力量,实现辊盘的轧制作业。
四、润滑系统设计粗轧机压下系统的润滑系统主要用于减少摩擦,降低磨损和延长设备的使用寿命。
润滑系统主要包括主轴油脂润滑系统和辊盘轴承润滑系统。
主轴油脂润滑系统采用循环润滑方式,通过油泵将油脂供给到主轴轴承,实现润滑和冷却作用。
辊盘轴承润滑系统采用分配式润滑方式,通过分配模块将润滑油脂供给到每个辊盘轴承上,确保辊盘轴承的正常运转。
五、冷却系统设计粗轧机压下系统的冷却系统主要用于散热和降低工作温度。
冷却系统主要包括辊盘冷却系统和主轴冷却系统。
辊盘冷却系统采用内循环冷却方式,通过水冷却器将冷却水供给到辊盘内部,实现辊盘的冷却作用。
主轴冷却系统采用外循环冷却方式,通过水冷却器将冷却水供给到主轴内部,实现主轴的冷却作用。
六、安全保护措施粗轧机压下系统在设计过程中应考虑安全保护措施,包括安全防护装置和紧急停机装置。
安全防护装置主要包括防护罩和安全开关,确保操作人员的安全。
紧急停机装置主要采用紧急停机按钮或绳索开关,一旦发生紧急情况,能够立即停机,保护设备和操作人员的安全。
综上所述,本文针对2150四辊可逆式粗轧机压下系统进行了系统结构设计、控制系统设计、润滑系统设计和冷却系统设计,并提出了相应的安全保护措施。
热轧机电气条件
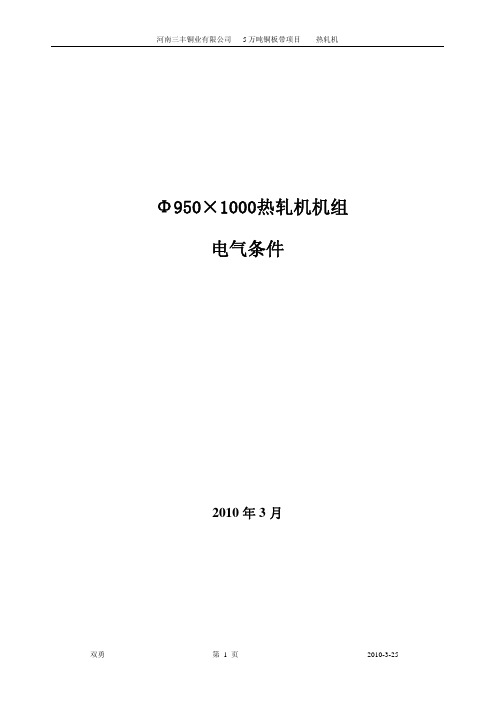
Φ950×1000热轧机机组电气条件2010年3月第一章设计依据、设备主要技术参数1.1 工艺流程简述厚:150—290mm、宽:400—650mm、长:4500—8000mm的铸锭在加热炉中均热或加热后,送至二辊热轧机,在高温下热轧开坯,当带坯厚度减至需要厚度时,进行在线剪切、垛板或在线淬火/冷却后卷取。
1.2 设计依据1.2.1 轧制材料:铜及铜合金C10100、C10200、C11000、C26000、C27000、C19400、C19210。
1.2.2 铸锭规格:铸锭规格:150~290mm×400~630mm×4500~8000(mm)最大锭重:按220mm×620mm×8000(mm)计算:9700kg1.2.3 成品规格:带卷规格范围:9~16mm×400~650mm,成品带卷内径:Φ600~Φ800 mm,成品带卷外径:Φ1000~Φ2000 mm,成品带卷长度:136000 mm,热轧板规格范围:7~150mm×400~650mm,板材长度:max.4000mm,最大堆垛重量:5000kg 。
1.2.4 开轧温度:780℃~980℃1.2.5 终轧温度:一般紫铜、黄铜550~650℃,要求淬火的C19400铸锭,终轧温度大于700℃,在线淬火,淬火后带坯温度≤300℃。
1.2.6 产品精度:厚度偏差(厚度为13mm时):横向偏差0.1mm纵向偏差0.2mm侧弯:<1.0mm/m,总长范围内不超过35mm(头尾各3m内不考核)板形:小于100I单位。
1.2.7 生产能力:60t/h,6块锭/h。
1.3 设备主要技术参数1.3.1 轧机型式:二辊、电动压下加液压微调;1.3.2 机列全长:270000 mm;1.3.3 轧件最小厚度:7mm;1.3.4 轧件宽度:max 650㎜;轧辊尺寸:φ950/φ910×1000(mm);1.3.5 道次加工率:5%~50%1.3.6 轧制速度:120m∕min(额定), 240m∕min(最高).1.3.7 轧制力:max 15000kN;1.3.8 主电机功率:2×1800KW;1.3.9 最大轧制扭距:1500kNm;1.3.10 轧制方向:右向;1.3.11 轧制线标高:~900㎜;1.3.12 工艺冷却液最大流量: 3000 l/min;1.3.13 过滤精度:≤15μm;1.3.14 工艺冷却液温控精度(净乳液箱出口处):(45℃-60℃)±5℃;1.3.15 淬火、冷却水流量:7500M3/h。
毕业设计(论文)-四辊冷轧机压下系统设计[管理资料]
![毕业设计(论文)-四辊冷轧机压下系统设计[管理资料]](https://img.taocdn.com/s3/m/032e7c0e04a1b0717ed5ddb6.png)
四辊冷轧机压下系统设计摘要轧辊调整装置的作用主要是调整轧辊在机架中的相对位置,以保证要求的压下量、精确的轧件尺寸和正常的轧制条件。
压下装置也称上辊调整装置,它是用途最广的一种轧辊调整装置,安装在所有的二辊、三辊、四辊和多辊轧机上,就驱动方式而言,压下装置可分为手动的、电动的、和液压三类。
本论文介绍了轧机的发展历史和未来,介绍并分析了轧机的几种压下形式,列举了其各自的优缺点以及各种压下形式的工作原理。
首先通过实习和所查资料确定设计方案并进行方案评述,根据实际情况选择了电动压下方式。
其次根据所给定的基本参数计算轧制力以及选择电动机容量,设计压下螺丝和压下螺母并进行强度和刚度校核;选择轴承并进行寿命校核,设计蜗杆传动和减速器中的齿轮传动,并进行环保性和经济性分析等。
关键词: 冷轧机;电动压下;压下螺丝;蜗杆传动;齿轮Design on Pressure System of Four-roller coldrolling millAbstractThe role of roller adjustment device to adjust roll mainly the relative position in the rack to ensure that the requirements reduction, precise size and normal rolling Rolling. Reduction device, also known as the roller adjustment device, which is the most widely used as a roller adjustment device, installed in all of the two rollers, three rollers, four rollers and multi-roll rolling mill, the drive mode, the pressure device divided manually, electric, and hydraulic three. This paper describes the history and future of the mill, rolling mill introduced and analyzed several pressure form, listed with their respective advantages and disadvantages, and various forms of pressure works. First of all, to find information through the established practice and the design and conduct programs reviewed, according to the actual way to choose a power reduction. Second, according to the calculation of basic parameters of a given choice of rolling force and motor capacity, design pressure once again screws and screw down nuts and check the strength and rigidity; choice for life bearings and check the design of the worm drive and gear box transmission, and for environmental protection and economic analysis.Key words:cold rolling mill; electric pressure; pressure nut; worm; Gear目录1 绪论 (1)选题背景 (1)国内外研究成果 (1)课题研究的内容 (3)2总体方案设计 (4)3 压下电机的选择 (6)轧制力的计算 (6)第一道次的轧制力计算 (6)第二道次的轧制力计算 (7)第三道次的轧制力计算 (9)第四道次的轧制力计算 (10)第五道次的轧制力计算 (12)压下螺旋传动设计 (14)材料选择 (14)压下螺丝和螺母主要尺寸的确定 (14)驱动压下螺丝的力矩 (15)压下螺丝的强度计算 (16)螺母的强度计算 (17)压下电机的容量选择 (18)速比分配 (19)4. 圆柱齿轮的设计 (20)选定齿轮相关参数及工作情况 (20)按齿面接触强度设计 (20)按齿根弯曲强度设计 (22)几何尺寸计算 (23)5 蜗杆传动的设计 (25)选择蜗杆传动类型 (25)选择材料 (25)按齿面接触疲劳强度进行设计 (25)蜗杆与蜗轮的主要参数与几何尺寸 (26)齿根弯曲疲劳强度校核 (27)受力分析 (28) (28)6.设备可靠性与经济评价 (32)结论 (33)致谢 (34)参考文献 (35)1 绪论选题背景钢产量是一个国家经济实力的体现,为了生产更多的钢材就要有更先进的炼钢轧钢技术,现代轧机发展的趋向是连续化、自动化、专业化和大型化,产品质量高,消耗低。
Φ950轧机压下传动装置离合器问题分析与改造
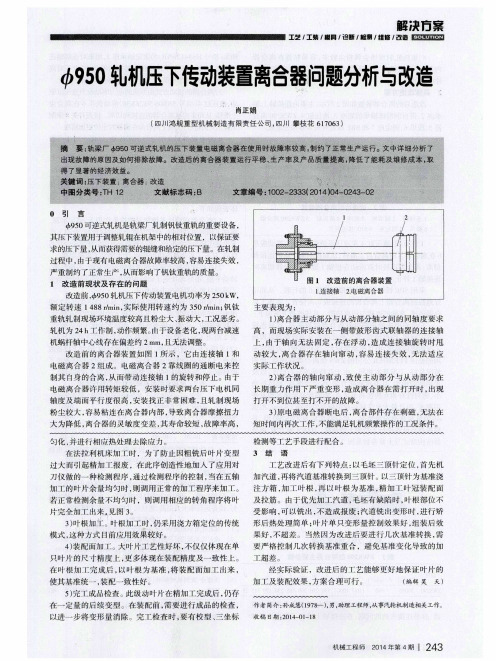
经 实 际验 证 ,改 进 后 的 _ T艺 能够 更 好地 保 证 叶 片 的
加 工及装配效果 , 方案合理可行。
( 编辑 昊 天)
作者简介 : 孙成慧( 1 9 7 8 一) , 男, 助理工程师, 从事汽轮机制造相关工作
收稿 日期 : 2 0 1 4 — 0 l — l 8
机 械工程师 2 0 1 4 年第4 期 ;2 4 3
工艺 改进 后 有 下 列特 点 : 以毛 坯 三 顶针 定位 , 首 先 机 加汽 道 , 再将 汽 道基 准 转换 到 三顶 针 。 以三 顶针 为基 准 浇
加T的叶片余量均匀时, 则调用正常的加_ T程序来加工。
片 完全 加 r : 出来 见图 3 。
注方箱 , 加工叶根 , 再以叶根 为基准 , 精加 T叶冠装配 面
其 压下装置用 于调整轧 辊在机架 中的相 对位置 ,以保证要 求 的压 下量 , 从而获得需要 的辊缝 和给定的压下量 。在轧制
过程中, 由于现有电磁离合器故障率较高 , 容易连接失效,
严 重制 约 了正 常生产 , 从 而影 响了钒钛 重轨 的质量 。
1 改造 前现 状及 存在 的 问题
有 效地 改 善 了连 接 轴旋 转 时 的甩 动 , 减少 了对离 内部 , 使摩擦扭力大大降低 , 离合器 的灵敏度变差 , 摩擦 行 支撑 ,
合器离合齿的冲击和磨损 , 离合器的轴向窜动明显减少。 3 ) 离合器的驱动方式由原来的电力驱动改为液压缸驱
匀化, 并进 行 相应 热处 理 去除应 力。 检测 等工 艺 手段 进行 配 合 。
语
在 法拉 利 机床 加 工时 ,为 了防 止 囚粗铣 后 叶 片 变型 3 结
900四辊可逆冷轧机压下规程设计及机架设计与分析

1200四辊可逆冷轧机压下规程设计及机架设计与分析学院:机械工程学院班级:09级轧钢2班组员:岳猛超付振冲张刚廉慧祁福亮指导教师:许秀梅王健燕山大学专业综合训练(论文)任务书院(系):机械工程学院基层教学单位:冶金系一、 原料及设计技术参数1.1、原料:08F 来料尺寸4.2mm ×1050mm 成品尺寸0.6mm ×1050mm Q235 来料尺寸4.2mm ×1050mm 成品尺寸0.6mm ×1050mm Q195 来料尺寸3.5mm ×1050mm 成品尺寸0.65mm ×1050mm1.2、成品出口速度v=8m/s 。
1.3、开卷机最大张力6吨,卷取机最大张力35吨。
二、 轧辊尺寸的预设定设计课题为“1200四辊可逆冷轧机压下规程设计及机架设计与分析”,则工作辊的辊身长度 L=1200mm ,辊身长度确定后即可根据经验比例值法确定轧辊直径,冷轧板带轧机1L / 2.3~3.0D = 常用比值为2.5 ~ 2.9;2L /0.8~1.8,D = 常用比值为0.9~ 1.4;21/ 2.3~3.5,D D =常用比值为2.5 ~ 2.9;对于支撑辊传动的四辊轧机,一般取21/3~4,D D =其中L 为辊身长度,1D 为工作辊直径,2D 为支承辊直径。
取 L/1D =2.5,12/3,D D =L=1200mm , 1D =480mm , 2D =1440mm三、 压下规程制定3.1、压下规程制定的原则及要求压下规程设计的主要任务是确定由一定来料厚度的板坯经过几个道次后轧制成为用户所需求的,满足用户要求的板带产品。
在此过程中确定所需采用的轧制方法,轧制道次及每个道次压下量的大小,在操作上就是要确定各道次辊缝的位置和转速。
因此,还要涉及到各道次的轧制速度,轧制温度,前后张力及道次压下量的合理分配。
在此过程中,主要考虑设备能力和产品质量,设备能力主要包括咬入条件,轧辊强度和电机功率三个要素,而产品质量主要包括几何精度和力学性能。
φ950可逆式轧机压下装置设计

1 绪论1.1 毕业设计的意义毕业设计是对大学期间的理论课程与实际相结合的一种综合教学环节。
使我们学到的专业理论和知识应用到工作中,培养独立思考、分析和解决实际工作问题的能力,为以后的工作打下坚实的基础。
1.2 轧钢机械定义轧钢机械亦称轧钢机。
一般把能将被加工材料在旋转的轧辊间受压力产生塑性变形即轧制加工的机器,称为轧钢机。
在大多数情况下,轧材的生产过程要经过几个轧制阶段,还要完成一系列的辅助工序,如将原材料由仓库运出、加热、轧件送往轧辊、轧制、翻转、剪切、矫直、打印、轧件的收集、卷曲成卷等等[1]。
1.3 初轧机的作用及生产要点1.作用:初轧机是以最少的轧制道次,最短的时间,将钢锭轧制成规定的尺寸及优制高精度的坯材的一种轧机。
2.生产要点:在不产生裂纹的范围内,尽可能增大压下量,确定合适的钢坯的尺寸关系,轴承的安装维修和轧辊的调整精度要高。
要使轧辊充分冷却,但要防止钢坯降温,正确的孔型设计,操作要熟练。
1.4 轧钢机及初轧机的发展情况19世纪中叶轧钢机械只是轧制一些熟铁条的小型轧机,设备简陋,产量不高;有的轧机是用原始的水轮来驱动。
十九世纪五十年代以后,钢的产量大增;各先进工业国的铁路建设与远洋航运的发展,蒸汽驱动的中型、大型轧机先后出现了。
二十世纪的电气化使功率更大的初轧机迅速发展起来。
本世纪50~70年代末,由于汽车、石油、天然气的输送,钢材生产是以薄板占优势为特征的。
至1970年止,世界上有初轧机达200多台,拥有初轧机最多的国家为美国,达130台,日本42台,绝大部分为二辊可逆式轧机,开坯能力达3亿吨以上,七十年代的初轧机轧辊直径增大到1500毫米。
国外初轧机的发展可分为三个阶段。
1945年前的初轧机,一般称为第一代初轧机。
1945~1960年是初轧机发展的中期,称为第二代初轧机。
60年代后建的初轧机,称为第三代初轧机。
70年代初的初轧机轧辊直径增大到1500mm,到如今的二十一世纪,初轧机的发展更是迅速。
四辊冷轧机设计之压下系统设计说明书
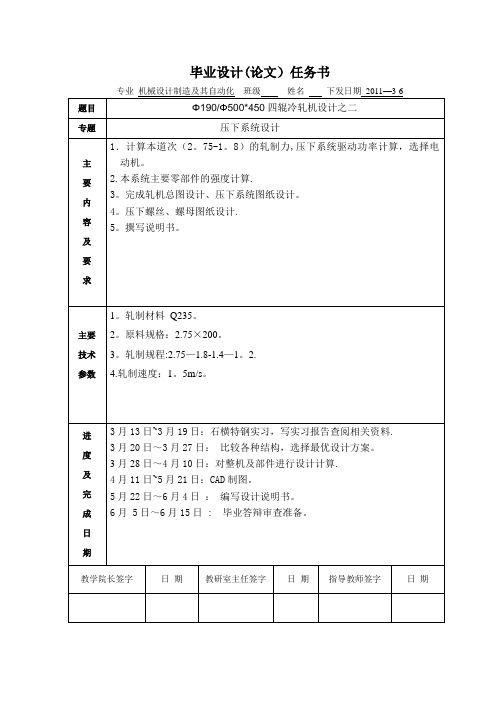
毕业设计(论文)任务书摘要近年来世界上的冶金工业技术及设备又有长足进步,新工艺、新技术、新设备的出现,使冶金生产过程发生了本质的变化,特别是中国的钢铁工业迅速发展,这就要求对轧钢设备进行充实和更新.本轧机为Φ190/Φ500*450四辊冷轧机小型四辊冷轧机,本次设计重点为电动压下部分.电动压下是最常用的上辊调整装置,通常包括:电动机、减速机、制动器、压下螺丝、压下螺母、压下位置指示器和球形垫片等,其特点有轧辊调整量小、调整精度高、动作快,灵敏度高等.同时,该轧机的主传动方式为传动工作辊,这种形式对于轧制过程比较有利。
设计中运用斯通公式计算轧制力,传动方式采用不可逆式轧机工作制度,电动压下装置是电动机通过蜗轮减速箱传递运动的,其移动距离可达到较大的数值,速度和加速度亦可达到一定的要求,压下能力较大,采用电动压下装置。
关键词:四辊冷轧机,上辊调整,电动压下AbstractIn recent years the metallurgical industry in the world technology and equipment and rapid progress,new technology,new technology,new equipment, metallurgy process appears essential changes happened, especially in China's steel industry developing rapidly,it is required to rolling equipment to enrich and updated.This mill for Φ 190 / Φ 500 * 450 four cold rolling mi ll small four cold rolling mill, and this graduation project focused on the design of the electrical pressure. Electric pressure is the most commonly used on the roll of the adjustment device, usually including:electromotor, reducer,arrester,pressure screws,pressure nut,ball pressure pads, etc。
950轧机设计说明书

1. 绪论1.1设计的选题背景轧钢生产时将钢锭或钢坯轧制成钢材的生产环节。
用轧制方法生产钢材,具有生产率高、品种多、上产过程连续性强、易于实现机械化自动化等优点。
因此,它比锻造、挤压、拉拔等工艺得到更广泛地应用。
目前,约有90%的钢都是经过轧制成材的。
有色金属成材,主要也用轧制方法。
【1】目前我国处在新老交替的钢铁生产体系中,初轧机在轧钢生产中的作用仍无法替代,初轧机仍具有着十分重要的作用。
1.2轧机国内外发展的研究现状、成果、发展趋势1.2.1轧机的国内外研究现状及成果从16世纪人类开始轧钢发展到今天,经过了漫长的过程。
在1530年或1532年,依尼雪在拿伯格(Nnrmberg)发明了第一个用于轧钢或轧铁的轧机,紧接着,1782年,英国的约翰彼尼(John·payne)在有俩个刻成不同形状的孔型的轧辊的轧机中加工锻造棒材。
1759年,英国的托马斯伯勒克里(Thomas· Blockley)取得了孔型轧制的另外一个专利,在历史上标志着型钢生产正式开始。
轧钢机械的分类。
轧钢机械可按所轧辊的材料分为轧辊钢材的和轧辊铝、铜等有色金属的两类。
各类轧机的工作原理和主要结构基本相同,只是轧辊的温度、压力和速度有所差异。
轧机中使用最多的是轧钢机。
轧机又可分为半成品轧机和成品轧机。
半成品轧机主要是开坯机,包括初轧机、板坯轧机和钢坯轧机。
随着连铸机的逐步推广,某些装有连铸机的钢厂已不再使用开坯机开坯。
成品轧机有型材轧机、轨梁轧机、线材轧机、厚板轧机、薄板轧机、带材轧机、箔带轧机、无缝管轧机、铜板轧机、铝板轧机和某些特殊轧机。
它们的主要区别是轧辊的布置和辊的形状不同,并且在精度、刚度、强度和外形尺寸上也有很大的差别。
1.2.2初轧机的发展趋势总的来说,轧钢机械向着大型、连续高速和计算机控制方向发展。
初轧机的发展,在发展连铸的同时,国外仍在新建或扩建初轧机,以扩大开坯能力。
这是由于开坯机具有产品变化灵活,便于实现自动化等优点,如日本1969年有三台板坯初轧机和一台方坯初轧机投入生产。
四辊可逆式冷轧机设计计算书

四辊轧机设计计算书3.1 冷轧轧辊的组成冷轧辊是冷轧机的主要部件。
轧辊由辊身、辊颈和轴头三部分组成。
辊颈安装在轴承中,并通过轴承座和压下装置把轧制力传给机架。
轴头和连接轴相连,传递轧制力矩。
工作辊和支撑辊的结构如图所示。
工作辊结构支撑辊结构3.2、 冷轧辊系尺寸的选择冷轧过程中,轧辊表面承受很大的挤压应力和强烈的磨损,因此,冷轧工作辊应具有极高而均匀的硬度,一定深度的硬化层,以及良好的耐磨性与抗烈性。
降低轧辊硬度,虽然改善抗烈性,但耐磨性降低,因此,必须正确选择轧辊表面硬度。
冷轧辊用钢均多为高碳合金钢,如29r C 、o r M C 29等,我们这里选工作辊的材质为o r M C 29。
轧件对冷轧工作辊巨大的轧制压力,大部分传递给支撑辊上。
支撑辊既要能承受很大的弯曲应力,还要具有很大的刚性来限制工作辊的弹性变形,以保证钢板厚度均匀。
轧机支撑辊的表面肖氏硬度一般为HS45左右。
目前为提高板厚精度与延长轧辊的寿命,支撑辊硬度有提高的趋势。
支撑辊常用钢号为o r M C 29、V C r 9、及o n r M M C 60,我们这里选支撑辊材质为o r M C 29。
3.3、 辊系尺寸的确定1) 辊身长度L 及直径D 的确定。
辊身长度L 应大于所轧钢板的最大宽度m ax b ,即 []2max a b L += (3.1)当m ax b =400—1200 mm 时,a=50—100 mm ,现m ax b =500mm ,取a=50mm 所以 mm a b L 55050500max =+=+= 四辊轧机的辊身L 确定以后,根据经验数据:8.18.02-=D L来确定支撑辊直径2D ,取7.12=D L所以 mm LD 3207.12==对于支撑辊传动的四辊轧机,一般选4312-=D D ,现取2.312=D D则 mm D D 1002.33202.321===2) 轧辊辊颈尺寸d 和l 的确定。
单机架可逆轧机

单机架可逆式冷轧机AGC系统刘建星(山东泰钢集团冷轧薄板厂)摘要:对单机架可逆式轧机厚度自动控制原理进行了介绍,并依据冷轧厂950 单机架可逆式冷轧机的实际情况,重点介绍了轧机的厚度控制系统数学模型。
关键词:单机架可逆式轧机厚度自动控制系统模型1前言随着生产的发展和技术的进步,用户对板厚精度的要求也越来越高,如何选择一个适合自身设备条件及工艺要求的厚度自动控制系统(Automatic Gauge control简称AGC),对于一个轧钢厂来说至关重要。
本文以西安重型机械研究所为泰钢设计的950mm冷轧机为例,重点介绍了轧机AGC自动控制系统数学模型。
2单机架可逆式轧机AGC技术介绍2.1厚度自动控制(AGC) 策略在进行厚度自动控制时,要用到轧制时的弹塑性曲线来表示轧件和轧机的相互作用,如图1所示。
图1 轧制时的弹塑性曲线根据轧制时的弹塑性曲线可得出弹跳方程:h = S0 + ( P - P0 )/K (1)式中S0 ———预压靠时的原始辊缝P ———轧制时轧制压力P0 ———预压靠时轧制压力K———轧机刚度系数为了消除各种原因造成的厚差,运用轧制时的弹塑性曲线,可采用各种不同的厚度调节方案和措施,具体有如下几种方法。
2.1.1 调压下。
调压下是厚度控制最主要的方式,常用来消除由于轧件和工艺方面的原因影响轧制压力而造成的厚度差,调压下方法包括反馈式、厚度计式、前馈式、秒流量法液压式等厚度自动控制系统,广泛应用于热连轧、冷连轧的头几机架、单机架冷轧机上。
2.1.2 调张力。
调张力即利用前后张力的变化来改变轧件塑性变形线的斜率以控制厚度。
这种方法在冷轧薄板时用得较多。
但目前在冷轧厚度控制时不单独应用此法,往往采用调压下与调张力互相配合的联合方法。
2.1.3 调轧制速度。
轧制速度的变化影响到张力、温度和摩擦系数等因素的变化,故可通过调速来调张力和温度,从而改变厚度。
2.2单机架冷轧机厚度自动控制技术对于单机架冷轧机的AGC控制,由于其结构简单,因而厚控方式也多种多样。
- 1、下载文档前请自行甄别文档内容的完整性,平台不提供额外的编辑、内容补充、找答案等附加服务。
- 2、"仅部分预览"的文档,不可在线预览部分如存在完整性等问题,可反馈申请退款(可完整预览的文档不适用该条件!)。
- 3、如文档侵犯您的权益,请联系客服反馈,我们会尽快为您处理(人工客服工作时间:9:00-18:30)。
1 绪论1.1 毕业设计的意义毕业设计是对大学期间的理论课程与实际相结合的一种综合教学环节。
使我们学到的专业理论和知识应用到工作中,培养独立思考、分析和解决实际工作问题的能力,为以后的工作打下坚实的基础。
1.2 轧钢机械定义轧钢机械亦称轧钢机。
一般把能将被加工材料在旋转的轧辊间受压力产生塑性变形即轧制加工的机器,称为轧钢机。
在大多数情况下,轧材的生产过程要经过几个轧制阶段,还要完成一系列的辅助工序,如将原材料由仓库运出、加热、轧件送往轧辊、轧制、翻转、剪切、矫直、打印、轧件的收集、卷曲成卷等等[1]。
1.3 初轧机的作用及生产要点1.作用:初轧机是以最少的轧制道次,最短的时间,将钢锭轧制成规定的尺寸及优制高精度的坯材的一种轧机。
2.生产要点:在不产生裂纹的范围内,尽可能增大压下量,确定合适的钢坯的尺寸关系,轴承的安装维修和轧辊的调整精度要高。
要使轧辊充分冷却,但要防止钢坯降温,正确的孔型设计,操作要熟练。
1.4 轧钢机及初轧机的发展情况19世纪中叶轧钢机械只是轧制一些熟铁条的小型轧机,设备简陋,产量不高;有的轧机是用原始的水轮来驱动。
十九世纪五十年代以后,钢的产量大增;各先进工业国的铁路建设与远洋航运的发展,蒸汽驱动的中型、大型轧机先后出现了。
二十世纪的电气化使功率更大的初轧机迅速发展起来。
本世纪50~70年代末,由于汽车、石油、天然气的输送,钢材生产是以薄板占优势为特征的。
至1970年止,世界上有初轧机达200多台,拥有初轧机最多的国家为美国,达130台,日本42台,绝大部分为二辊可逆式轧机,开坯能力达3亿吨以上,七十年代的初轧机轧辊直径增大到1500毫米。
国外初轧机的发展可分为三个阶段。
1945年前的初轧机,一般称为第一代初轧机。
1945~1960年是初轧机发展的中期,称为第二代初轧机。
60年代后建的初轧机,称为第三代初轧机。
70年代初的初轧机轧辊直径增大到1500mm,到如今的二十一世纪,初轧机的发展更是迅速。
我国拥有1000毫米以上大型初轧机七套,还有750—850毫米小型初轧机八套,主要用于合金钢厂,为数不多的650毫米轧机是中小钢厂的主要开坯设备。
1959年我国开始自行设计制造开坯机,已制成的开坯机有700、750、825、850/650、1150等毫米初轧机。
1.5 初轧机的发展趋势目前初轧机的发展趋势有如下几点:1.万能式板坯初轧机迅速发展。
近20年来随着热连轧和中厚板轧机的发展,板坯需要量不断增加。
因此初轧机有半数以上是专门轧制板坯的高生产率的万能式板坯初轧机,由于万能式板坯初轧机带有立辊,可以减少翻钢道次、减少轧制时间,轧出的板坯质量好,易于实现自动控制。
2.向重型化发展。
初轧机的重型化是指大钢锭、大辊径、大功率。
轧制钢锭重量达45~70t,最高年产量达500~600万。
3.缩短轧机辅助机械工作时间。
4.采用自动化控制。
20年来,初轧机自动化发展较快,由均热炉到板坯精整已逐步采用自动控制。
初轧机的自动操作,已由电子计算机在线控制。
5.提高钢坯质量,改进精整工序,采用大吨位板坯剪切机(剪切力可达40MN)及在线火焰清理机。
6.九十年代及其以后的发展动向,随着连铸技术的发展,连铸与轧机相结合的连续轧机组将进一步发展。
1.6 φ950可逆式轧机主传动轧钢机主传动装置的作用是将电动机的运动和力矩传递给轧辊。
φ950可逆式轧机的主传动装置由电动机、联轴器、齿轮座及联接轴组成。
(1) 电动机:为轧机提供动力源。
(2) 联轴器:联接电动机与齿轮座。
(3) 齿轮座:当工作机座由一个电动机带动时,通过齿轮座将电动机传递的运动和力矩分配给两个轧辊。
(4) 联接轴:轧钢机电动机、齿轮座的运动和力矩都是通过联接轴传递给轧辊的。
1.7 连轧生产工艺流程图及Φ950可逆式轧机性能1. 图1.1为炼钢厂连轧作业区生产工艺流程图:图1.1 生产工艺流程图2.炼钢厂连轧作业区Φ950可逆式轧机性能:轧机型式:二辊可逆式轧机原料规格:410320/380280/280280⨯⨯⨯mm 轧辊直径:Φ900~Φ1050mm 轧辊长度:5840mm 轧辊重量:22.747t 辊身长度:2500mm 辊颈直径:Φ560mm最大轧制力:9.81M·N额定力矩:63.5t·m轧制速度:0~5.5m/s轧辊最大开口度:550mm工作行程:500mm下辊轴向调整量: 5mm压下速度:50~100~120mm/s轧辊平衡形式:液压轧辊材质:60CrMnMo锻钢接轴扁头重量:1.475t接轴扁头材质:40CrNiMo轧辊转速:0~70-120r/min主电机功率:4560KW轧辊轴承型号:四列滚子轴承FCD1121646301.8 压下螺丝的阻塞事故快速电动压下装置由于压下行程大,压下速度高而且不带钢压下,故在生产中易发生压下螺丝阻塞事故,这通常是由于卡钢,或者由于误操作使两辊过分压靠或上辊超限提升造成的,此时压下螺丝上的载荷超过了压下电机允许的能力,电动机无法启动,上辊不能提升。
所以在轧机设计时,考虑发生阻塞事故时的回松措施是十分必要的,回松力可按每个压下螺丝上最大轧制力的1.6~2.0倍考虑。
1.9 上辊平衡装置的用途由于上轧辊及其轴承座,以及压下螺丝自重的影响,在轧件未进入轧辊之前,上轧辊及其轴承座与压下螺丝之间,以及压下螺丝和压下螺母之间有间隙存在,这些间隙使轧件进入轧辊时产生很大的冲击,恶化了轧件的工作条件。
为了防止这种冲击,几乎所有轧机都设有上辊平衡装置,Φ950可逆式轧机也设有上辊平衡装置。
2 总体设计方案υ950可逆式轧机的主要组成部分有:主传动、机架、轧辊、轧辊轴承、万向接轴、压下装置及平衡装置。
2.1主传动υ950可逆式轧机主传动装置作用是把电动机的转动传递给工作机座中的轧辊,使其旋转,实现对金属的轧制。
2.2机架在轧制过程中,被轧制的金属作用到轧辊上的全部轧制力,通过轧辊轴承、轴承座、压下螺丝及螺母传给机架。
因此,机架必须有足够的刚度和强度。
本设计υ950可逆式轧机机架采用闭式机架。
机架的材料选用ZG35铸钢。
2.3轧辊轧辊是使轧件产生塑性变形的主要部件,在轧制过程中,轧辊承受着轧制压力,并将此负荷传给轴承。
轧辊选用的材料是60CrMnMo锻钢。
2.4轧辊轴承轧辊轴承用来支承转动的轧辊,并保持轧辊在机架中正确的位置。
轧辊轴承应具有较小的磨损系数,足够的强度和刚度,并便于更换轧辊。
轧辊轴承型号选用四列滚子轴承FCD112164630。
轧辊轴承的润滑方式是自动干油润滑。
2.5万向接轴υ950可逆式轧机的联接轴选用滑块式万向接轴,它能传递很大的扭矩和允许有较大的倾角。
万向接轴的扁头选用开口式扁头。
万向接轴的等速条件:1.主动轴与被动轴要平行2.接轴(传动轴)上的叉头或镗口要平行。
2.6压下装置υ950可逆式轧机的压下装置采用快速电动压下装置。
1.压下装置的作用:(1) 调整两个轧辊之间的相互距离,以获得需要的辊缝和给定的压下量;(2) 调整两个轧辊的平行度;(3) 在轧制过程中发生轧卡等事故时,能使轧辊迅速脱离轧件。
2.快速压下装置工艺特点:(1) 工作时要求大行程、快速和频繁地升降轧辊。
(2) 轧辊调整时,不“带钢”压下,即不带轧制负荷压下。
为适应上述特点,要求传动系统惯性小,以便在频繁的启动和制动情况下实现快速调整;由于工作条件繁重,要求有较高的传动效率和工作可靠性。
2.7平衡装置υ950可逆式轧机的平衡装置选用液压式平衡装置。
液压式平衡装置是用液压缸的推力来平衡上辊重量的。
1. 轧辊平衡的目的:为了消除在轧制过程中,因工作机座中有关零件间的配合间隙所造成的冲击现象,以保证轧件的轧制精度,改善咬入条件,以及防止工作辊与支承辊之间产生打滑现象等原因所设置了轧辊平衡装置.2. 液压式平衡装置的特点:优点:(1) 结构紧凑,适于各种高度的上轧辊的平衡;(2) 动作灵敏,能满足现代化的板厚自动控制系统的要求;(3) 在脱开压下螺丝的情况下,上辊可停在任何要求的位置,同时拆卸方便,因此加速了换辊过程;(4) 平衡装置装于地平面以上,基础简单、维修方便、便于操作。
缺点:(1) 调节高度不宜过高,否则制造、维修困难;(2) 需要一套液压系统,增加了设备投资。
现代化的轧钢车间中,液压已成了普遍采用的必不可少的动力。
因此,缺点之二相对来说就不突出了。
3 力能参数的计算3.1轧制力能参数典型钢件:20CrMnTiH化学成份:C=0.20%,Mn=1.0%,Cr=1.2%,Ti=0.07%如下表3.1为Φ950钢坯轧制图表:表3.1 Ф950钢坯轧制图表(mm)铸坯规格:280⨯380道次孔型指针读数断面尺寸压下量宽展量高度宽度0 380 2801 I 180 330 502 I 120 270K 300 60 203 I 100 240 604 I 30 180K 300 60 305 III 110 240 606 III 60 190K 200 50 207 III 30 160 200 40 103.1.1 轧制时接触弧上平均单位压力由于单位压力在接触弧上的分布是不均匀的,为便于计算,一般均以单位压力的平均值——平均单位压力来计算轧制总压力。
由文献[1]可知,利用艾克隆德公式计算轧制时的平均单位压力:pm=(1+m)(k+ηu) (3.1) 式中:m——考虑外摩擦对单位压力的影响系数;k——轧制材料在静压缩时变形阻力,MPa;η——轧件粘性系数,kg·s/mm2;u——变形速度,s1-。
计算第一道次:m=101010)(2.1)(6.1h h h h h h R +---μ (3. 2)式中:μ——摩擦系数。
对钢轧辊μ=1.05-0.0005t ;t ——轧制温度;h 0、h 1——轧制前后轧件的高度,mm ; R ——轧辊半径,mm 。
μ=1.05-0.0005⨯1120=0.49 R=950/2=475mm h 0=380mm ,h 1=330mm 数据代入公式(3.2)中得: m=0.0861. 利用L .甫培(Pomp)热轧方坯的试验数据,得到k(Mpa)的计算公式:k=(14-0.01t)[]8.9)(3.0)()(4.1⨯+++Cr Mn C ωωω(3.3)式中: t ——轧制温度,℃;ω(C)——碳的质量分数,%; ω(Mn)——锰的质量分数,%; ω(Cr)——铬的质量分数,%;把数据代入公式(3.3)中:k ≈81.222 2. 轧件粘度系数η(kg ·s/mm 2)按下式计算:η=0.01(14-0.01t)c (3.4)式中:c ——考虑轧制速度对η的影响系数,由文献[1]可知,其值如下:轧制速度v/(m ·s 1-) <6 6—10 10—15 15—20 系数c 1.0 0.8 0.65 0.60最大轧制速度nd max =110r/min=110πD/60 m/s=110⨯3.14⨯0.95/60 m/s ≈5.469m/s<6m/s取c=1.0由公式(3.4)计算得η=0.01⨯(14-0.01⨯1120) ⨯1.0=0.028 kg ·s/mm 23. 艾克隆德用(3.5)式计算变形速度:u 102h h R h v+∆≈(3.5)式中: v ——轧制速度,mm/s ;h 0,h 1——轧制前、后轧件的高度,mm ; R ——轧辊半径,mm 。