1 设计要求及工况分析
华龙一号一回路压力和温度运行限制曲线研究

华龙一号一回路压力和温度运行限制曲线研究摘要:一回路压力和温度运行限制曲线作为核电厂运行限值和条件的重要组成部分,对核电厂安全运行有重要作用。
文章给出了一回路压力和温度运行限制曲线的内容、绘制的流程和方法,并就华龙一号堆型给出了示例。
关键词:核电厂;一回路;温度;压力;运行限制;华龙一号1引言在核电厂初步设计阶段,总体设计的重点工作之一是确定核电厂设计安全原则和要求。
核能虽然是一种清洁、安全可靠的能源,但是一旦发生重大事故对人类和环境造成的危害要比其它工业项目造成的风险和危害来得严重,所以制定并落实核电厂安全原则和要求就非常必要。
本文就设计安全原则和要求之一的一回路压力和温度运行限制(以下简称大刀图)展开论述,给出其内涵和绘制方法,并以华龙一号堆型为例,就重要曲线给出示例。
2简介为保障电厂工作人员,群众和环境不致遭到超过国家规定限值的辐射照射和污染,并将辐射照射和污染减至可以合理达到的尽量低的水平,在核电厂设计过程中,要采取各种安全方法和设计措施,达到核电厂设计的安全原则要求。
为了确保核电厂安全运行,应从核电厂的厂址选择、设计、建造、运行等方面全面落实国家核安全局颁布的有关安全规定和导则。
有关安全准则和要求涉及到核电厂的纵深防御原则,辐射防护设计,可靠性设计,安全功能分级,对假想始发事件的分析和对策,设计限值,在役试验和检查,设备鉴定,质量保证,安全分析和评价等各方面的要求。
为保证核电厂安全运行,必须制定一组反映最终设计及对设备和人员要求的运行限值和条件。
并且在核电厂运行开始前报国家核安全当局批准。
制定核电厂的运行限值和条件是一项十分重要的设计工作,它是作为核电厂营运单位授权运行核电厂依据的一个重要部分。
它的作用是:⑴对核电厂在启动、功率运行、停堆过程及停堆状态,维修,试验和换料等各种正常运行方式和预计运行事件规定安全要求,防止核电厂发生可能导致事故工况的状态;⑵对保证所有安全系统,包括专设安全设施能在事故工况下执行功能的各种要求作出规定。
工程设计标准

工程设计标准
首先,工程设计标准的制定是为了保证工程质量。
在工程设计中,标准规范了
工程设计所应遵循的技术要求和工艺流程,从而确保了工程设计的科学性和合理性。
只有严格按照标准进行设计,才能保证工程的质量达到要求,减少工程质量问题和安全隐患的发生。
其次,工程设计标准的制定是为了提高工程效益。
通过制定合理的工程设计标准,可以有效地控制工程设计的成本,提高工程的经济效益。
标准化的设计流程和规范的设计要求,可以降低工程设计的成本,提高工程的效益,从而为工程的实施和运行提供保障。
另外,工程设计标准的制定是为了促进工程设计的科学化、规范化和标准化。
通过制定统一的工程设计标准,可以规范工程设计行为,提高工程设计的科学性和规范性。
标准化的设计流程和规范的设计要求,可以使工程设计更加规范和标准,提高工程设计的质量和效益。
总的来说,工程设计标准的制定和应用对于保证工程质量、提高工程效益、促
进工程设计的科学化、规范化和标准化具有重要的意义。
只有严格按照标准进行工程设计,才能确保工程的质量和安全,提高工程的效益,促进工程设计的科学化、规范化和标准化。
因此,工程设计标准的制定和应用是工程设计中不可或缺的重要环节。
设计规范-车桥1
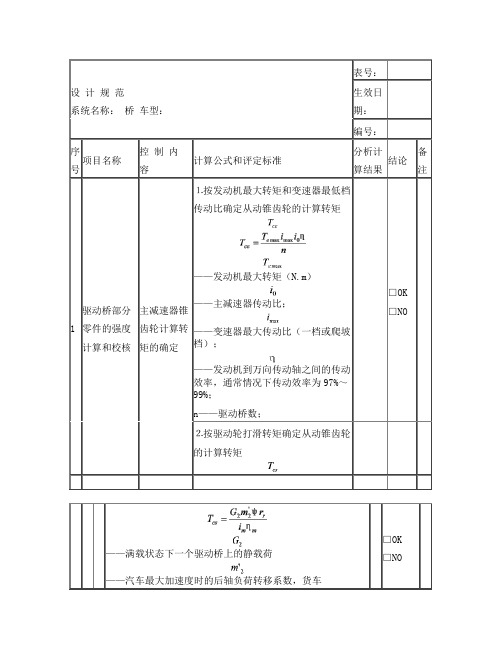
设计规范系统名称:桥车型:表号:生效日期:编号:序号项目名称控制内容计算公式和评定标准分析计算结果结论备注1驱动桥部分零件的强度计算和校核主减速器锥齿轮计算转矩的确定⒈按发动机最大转矩和变速器最低档传动比确定从动锥齿轮的计算转矩——发动机最大转矩(N.m)——主减速器传动比;——变速器最大传动比(一档或爬坡档);——发动机到万向传动轴之间的传动效率,通常情况下传动效率为97%~99%;n——驱动桥数;□OK□NO⒉按驱动轮打滑转矩确定从动锥齿轮的计算转矩——满载状态下一个驱动桥上的静载荷——汽车最大加速度时的后轴负荷转移系数,货车□OK□NO=1.1~1.2;——轮胎与路面间的附着系数,在良好的混凝土或沥青路面上,路面干燥时,值为0.7~0.8,路面潮湿时值为0.5~0.6,干燥的碎石路0.6~0.7,干燥的土路值为0.5~0.6,湿土路面时值为0.2~0.4;——车轮滚动半径(m)——主减速器传动比——主减速器从动齿轮到车轮之间的传动比;(双级减速的轮边减速比)——主减速器从动齿轮到车轮之间的传动比;(双级减速的轮边减速比)——主减速器主动齿轮到车轮之间的传动效率,对于双曲面齿轮副单级减速器,当>6时,取85%,当<6时,取90%,对于双曲面齿轮副双级减速器,取80%,⒊按汽车日常行驶平均转矩确定从动锥齿轮的计算转矩——汽车满载总重(N)——所牵引的挂车满载总重(N),但仅用于牵引车——道路滚动阻力系数,计算时轿车取0.010-0.015,载货汽车取0.015-0.020,越野汽车取0.020-0.035——汽车正常使用式的平均爬坡能力系数,轿车取0.08,载货汽车和城市公共汽车取0.05-0.09,长途公共汽车取0.06-0.10,越野汽车取0.09-0.30。
——汽车或汽车列车的性能参数当时,取当计算锥齿轮最大应力时,计算转矩取前两种的较小值,即=min[];当计算锥齿轮的疲劳寿命时,□OK □NO取。
脚手架工程方案的设计要求

脚手架工程方案的设计要求一、方案设计时要考虑的因素(一)工期在制定脚手架工程方案时,首先要考虑到工期的因素。
要根据施工的实际情况合理确定脚手架的搭建时间,确保工期能够满足工程的需要。
(二)施工环境施工环境是指脚手架搭建的地理环境、气象条件等外部因素。
要根据实际施工环境的情况,设计合理的脚手架工程方案,考虑到风速、地质条件等情况,确保脚手架的稳固性和安全性。
(三)荷载要求脚手架工程设计要满足实际的荷载要求,要考虑到人员、工具和材料的重量以及外部风载等因素,确保脚手架的承载能力满足工程需要。
(四)施工安全在脚手架工程方案设计中,施工安全是一个非常重要的因素。
要充分考虑到脚手架的稳定性、防护措施、安全通道等设计要求,确保施工过程中人员和设施的安全。
(五)脚手架材料选用在设计脚手架方案时,要考虑脚手架所需的材料,包括脚手架管、连接件、扣件、脚手板等等,要选用质量好、稳固可靠的材料,满足工程的需要。
二、方案设计的具体要求(一)结构设计脚手架的结构设计要求合理,要考虑到脚手架的承重、稳定性和使用安全等因素。
要根据不同的工程情况,确定脚手架的结构类型和高度,确保脚手架满足工程需要。
(二)安全防护脚手架工程方案设计要求充分考虑安全防护方面的要求,包括脚手架的围护、安全防护网、安全通道等设计要求,确保施工过程中的安全。
(三)施工工艺要求在制定脚手架工程方案时,要考虑到脚手架的搭建、拆除工艺,包括搭设顺序、连接方式、检查验收等要求,确保脚手架的施工质量和进度。
(四)质量验收要求脚手架工程方案的设计要求中,质量验收是一个重要的环节。
要明确脚手架的质量验收标准、验收机构和验收流程,确保脚手架的质量合格。
(五)监理要求在脚手架工程设计要求中,要求由专业的监理机构进行监理,确保脚手架工程施工过程中的质量和安全。
综上所述,脚手架工程方案的设计要求是非常重要的,要考虑到工期、施工环境、荷载要求、施工安全、脚手架材料选用等各个方面的因素,设计合理的脚手架工程方案,确保工程的质量、安全和进度。
液压系统设计步骤与设计要求(一)
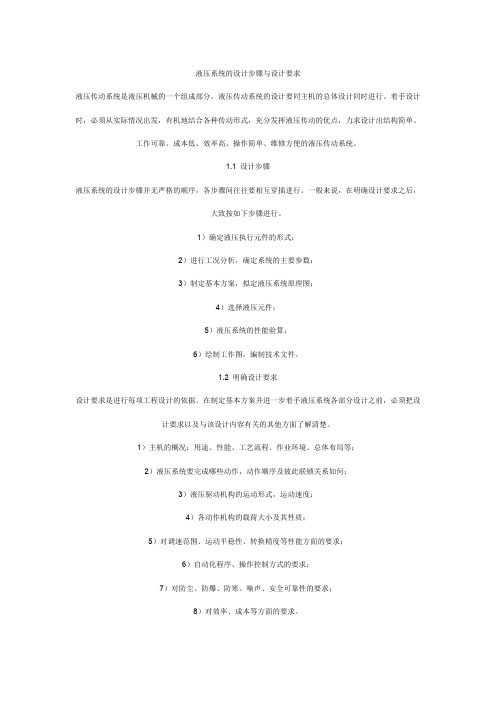
液压系统的设计步骤与设计要求液压传动系统是液压机械的一个组成部分,液压传动系统的设计要同主机的总体设计同时进行。
着手设计时,必须从实际情况出发,有机地结合各种传动形式,充分发挥液压传动的优点,力求设计出结构简单、工作可靠、成本低、效率高、操作简单、维修方便的液压传动系统。
1.1 设计步骤液压系统的设计步骤并无严格的顺序,各步骤间往往要相互穿插进行。
一般来说,在明确设计要求之后,大致按如下步骤进行。
1)确定液压执行元件的形式;2)进行工况分析,确定系统的主要参数;3)制定基本方案,拟定液压系统原理图;4)选择液压元件;5)液压系统的性能验算;6)绘制工作图,编制技术文件。
1.2 明确设计要求设计要求是进行每项工程设计的依据。
在制定基本方案并进一步着手液压系统各部分设计之前,必须把设计要求以及与该设计内容有关的其他方面了解清楚。
1)主机的概况:用途、性能、工艺流程、作业环境、总体布局等;2)液压系统要完成哪些动作,动作顺序及彼此联锁关系如何;3)液压驱动机构的运动形式,运动速度;4)各动作机构的载荷大小及其性质;5)对调速范围、运动平稳性、转换精度等性能方面的要求;6)自动化程序、操作控制方式的要求;7)对防尘、防爆、防寒、噪声、安全可靠性的要求;8)对效率、成本等方面的要求。
制定基本方案和绘制液压系统图3.1制定基本方案(1)制定调速方案液压执行元件确定之后,其运动方向和运动速度的控制是拟定液压回路的核心问题。
方向控制用换向阀或逻辑控制单元来实现。
对于一般中小流量的液压系统,大多通过换向阀的有机组合实现所要求的动作。
对高压大流量的液压系统,现多采用插装阀与先导控制阀的逻辑组合来实现。
速度控制通过改变液压执行元件输入或输出的流量或者利用密封空间的容积变化来实现。
相应的调整方式有节流调速、容积调速以及二者的结合——容积节流调速。
节流调速一般采用定量泵供油,用流量控制阀改变输入或输出液压执行元件的流量来调节速度。
毕业设计_液压缸试验台设计

第 4 页 共 39 页
6.4 供油泵出口处溢流阀的选择 ........................................28 6.5 补油泵出口处溢流阀的选择 ........................................28 6.6 单向阀的选择 ....................................................29 6.7 三位四通换向阀的选择 ............................................29 6.8 单向节流阀的选择 ................................................29 6.9 背压阀的选择 ....................................................29 6.10 管道的选择 .....................................................29 6.11 确定油箱容量 ...................................................30 6.12 滤油器的选择 ...................................................32 6.13 液压油的选择 ...................................................32 7.液压系统性能验算 .....................................................33 8.液压系统的安装、调试及使用与维护 .....................................34 8.1 液压系统调度前的准备工作 ........................................34 8.2 液压系统跳调度骤 ................................................34 8.2.1 调试前的检查 ..................................................34 8.2.2 启动液压泵 ....................................................34 8.2.3 系统排气 ......................................................34 8.2.4 系统耐压试验 ..................................................34 8.2.5 空载调试 ......................................................35 8.2.6 负载试车 ......................................................35 8.3 液压系统的验收 ..................................................35 8.4 液压系统的维护及检修 ............................................35 结语 ...................................................................36 致谢 ...................................................................38 参考文献................................................................39
(整理)sdfdsf.

一、设计的目的和要求:㈠设计的目的液压传动课程设计是本课程的一个综合实践性教学环节,通过该教学环节,要求达到以下目的:1.巩固和深化已学知识,掌握液压系统设计计算的一般方法和步骤,培养学生工程设计能力和综合分析问题、解决问题能力;2.正确合理地确定执行机构,选用标准液压元件;能熟练地运用液压基本回路、组合成满足基本性能要求的液压系统;3.熟悉并会运用有关的国家标准、部颁标准、设计手册和产品样本等技术资料。
对学生在计算、制图、运用设计资料以及经验估算、考虑技术决策、CAD技术等方面的基本技能进行一次训练,以提高这些技能的水平。
㈡设计的要求1.设计时必须从实际出发,综合考虑实用性、经济性、先进性及操作维修方便。
如果可以用简单的回路实现系统的要求,就不必过分强调先进性。
并非是越先进越好。
同样,在安全性、方便性要求较高的地方,应不惜多用一些元件或采用性能较好的元件,不能单独考虑简单、经济;2.独立完成设计。
设计时可以收集、参考同类机械的资料,但必须深入理解,消化后再借鉴。
不能简单地抄袭;3.在课程设计的过程中,要随时复习液压元件的工作原理、基本回路及典型系统的组成,积极思考。
不能直接向老师索取答案。
4.液压传动课程设计的题目均为中等复杂程度液压设备的液压传动装置设计。
具体题目由指导老师分配,题目附后;5.液压传动课程设计一般要求学生完成以下工作:⑴设计计算说明书一份;⑵液压传动系统原理图一张(3号图纸,包括工作循环图和电磁铁动作顺序表)。
二、设计的内容及步骤㈠设计内容1. 液压系统的工况分析,绘制负载和速度循环图;2. 进行方案设计和拟定液压系统原理图;3. 计算和选择液压元件;4. 验算液压系统性能;5. 绘制正式工作图,编制设计计算说明书。
设计步骤以一般常规设计为例,课程设计可分为以下几个阶段进行。
1.明确设计要求⑴阅读和研究设计任务书,明确设计任务与要求;分析设计题目,了解原始数据和工作条件。
⑵参阅本书有关内容,明确并拟订设计过程和进度计划。
排气阀qb1设计标准
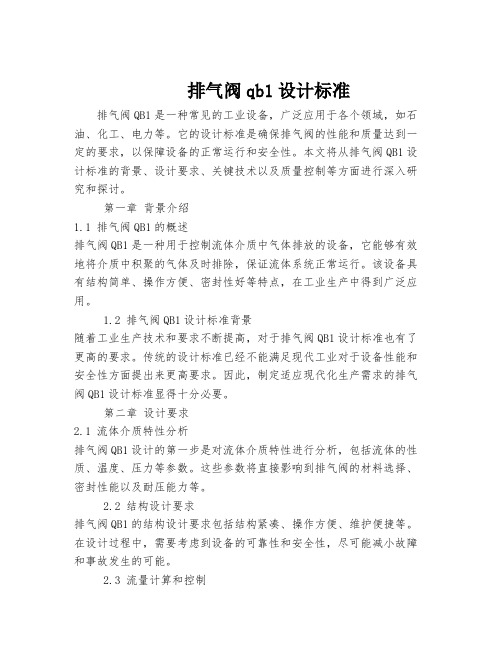
排气阀qb1设计标准排气阀QB1是一种常见的工业设备,广泛应用于各个领域,如石油、化工、电力等。
它的设计标准是确保排气阀的性能和质量达到一定的要求,以保障设备的正常运行和安全性。
本文将从排气阀QB1设计标准的背景、设计要求、关键技术以及质量控制等方面进行深入研究和探讨。
第一章背景介绍1.1 排气阀QB1的概述排气阀QB1是一种用于控制流体介质中气体排放的设备,它能够有效地将介质中积聚的气体及时排除,保证流体系统正常运行。
该设备具有结构简单、操作方便、密封性好等特点,在工业生产中得到广泛应用。
1.2 排气阀QB1设计标准背景随着工业生产技术和要求不断提高,对于排气阀QB1设计标准也有了更高的要求。
传统的设计标准已经不能满足现代工业对于设备性能和安全性方面提出来更高要求。
因此,制定适应现代化生产需求的排气阀QB1设计标准显得十分必要。
第二章设计要求2.1 流体介质特性分析排气阀QB1设计的第一步是对流体介质特性进行分析,包括流体的性质、温度、压力等参数。
这些参数将直接影响到排气阀的材料选择、密封性能以及耐压能力等。
2.2 结构设计要求排气阀QB1的结构设计要求包括结构紧凑、操作方便、维护便捷等。
在设计过程中,需要考虑到设备的可靠性和安全性,尽可能减小故障和事故发生的可能。
2.3 流量计算和控制在排气阀QB1的设计中,需要进行流量计算和控制。
通过对介质流动特性进行分析,确定合理的流量计算方法,并选择合适的控制方式和参数,以确保设备在不同工况下都能够正常工作。
第三章关键技术3.1 材料选择与耐压能力材料选择是影响排气阀QB1耐压能力和使用寿命的重要因素。
常见材料有不锈钢、铜合金等,在选择材料时需要考虑介质的腐蚀性、温度、压力等因素。
3.2 密封性能设计排气阀QB1的密封性能设计是确保设备正常运行的关键。
通过合理的密封结构设计和密封材料选择,保证介质不会泄漏,防止气体逆流和介质污染等问题。
3.3 结构强度分析排气阀QB1在工作过程中需要承受不同程度的压力和温度,因此结构强度分析是必不可少的。
《中国汽车行驶工况》国家标准第1部分轻型汽车

表 1-2 主要技术会议及研究活动
时间
会议活动
主要工作
17 年 1 月 17 年 1 月 17 年 2 月 17 年 3 月 17 年 5 月
准备会议 启动会 汽车工况标准讨论会 第一次会议
前期技术调查总结 确定工作形式、工作内容及任务安排
欧美日汽车工况标准讨论 讨论曲线构成 提出标准草案
3
17 年 5 月
1.2. 前期研究及任务来源
马凯副总理高度重视新能源汽车工况研究与开发,2014 年 9 月和 2015 年 5 月, 两次指示要求加快我国电动汽车典型工况标准制定。
《汽车产业中长期发展规划》规定到 2020 年,新车平均燃料消耗量乘用车降到 5.0 升/百公里,到 2025 年,新车平均燃料消耗量乘用车降到 4.0 升/百公里,新能源汽 车能耗处于国际领先水平。
欧洲在多年的实践中也发现 NEDC 工况的诸多不足,转而采用世界轻型车测试循 环(WLTC),但该工况的怠速比例和平均速度这两个最主要的工况特征与我国实际工 况的差异更大。作为车辆开发、评价的最为基础的依据,开展深入研究,制定反映我 国实际道路行驶状况的测试工况,显得越来越重要,行业呼吁开发中国工况。
《中国汽车行驶工况》国家标准 第 1 部分:轻型汽车 征求意见稿 编制说明
1. 工作简况 1.1. 背景
进入 21 世纪,我国汽车工业实现了井喷式发展。自 2009 年开始,我国汽车产销 量已经连续八年保持世界第一。保持汽车产业健康、持续发展,从汽车大国到汽车强 国,成为汽车人乃至全社会的梦想。2016 年中国原油对外依存度升至 65.5%,其中汽 车耗油约占整个石油消费量的 1/3 以上,预计到 2020 年这个比例将上升到 57%。节 约化石能源、降低汽车尾气排放,是汽车行业必须面对和解决的问题。
机械设计基础课程设计一级圆柱齿轮减速器设计说明书、零件图和装配图

机械设计基础课程设计一级圆柱齿轮减速器设计说明书、零件图和装配图机械设计基础课程设计一级圆柱齿轮减速器设计说明书一、设计要求1:减速比:根据实际需求确定减速比。
2:安装空间:根据实际使用场景,为齿轮减速器设计合适的安装空间。
3:轴向和径向载荷:根据实际工作负载,计算并确定减速器所能承受的轴向和径向载荷。
4:传动效率:设计具有高传动效率的减速器。
5:噪音和振动:减速器在运转时应尽量减少噪音和振动的产生。
二、设计步骤及详细说明1:确定减速比:根据实际需求确定减速比,考虑到工作负载和转速要求。
2:确定齿轮数目和模数:根据减速比和齿轮模数的关系,计算所需齿轮数目和模数。
3:计算齿轮参数:根据设计公式,计算齿轮齿数、齿宽、齿向系数等参数。
4:绘制齿轮零件图:根据计算结果,绘制齿轮零件的图纸,包括齿轮齿数、齿宽、法向压力角等。
5:绘制齿轮装配图:根据齿轮零件图,绘制齿轮减速器的装配图,标注零件之间的配合关系和装配顺序。
6:分析齿轮传动系统:利用仿真软件对齿轮传动系统进行分析,验证齿轮的传动效率和载荷承受能力。
7:选取材料并计算强度:根据齿轮传动系统的设计参数,选取合适的材料,并进行强度计算,保证齿轮的可靠性和使用寿命。
8:考虑润滑和冷却:根据实际工况和齿轮传动系统的特点,设计合适的润滑和冷却装置。
9:进行产品优化:对设计的减速器进行优化,考虑减少重量、减小尺寸和提高传动效率等方面。
10:绘制装配顺序图:绘制减速器的装配顺序图,指导实际生产过程。
11:进行减速器的试制和测试:根据设计图纸,进行减速器的试制和测试,验证设计的减速器性能。
附:齿轮减速器设计相关附件本文所涉及的法律名词及注释:1:减速比:指减速器输出轴的转速与输入轴的转速之比。
2:轴向载荷:作用在减速器轴承上的力,与轴线平行。
3:径向载荷:作用在减速器轴承上的力,与轴线垂直。
设计一台卧式单面多轴钻孔组合机床动力滑台的液压系统

负载分析中�暂不考虑回油腔的背压力�液压缸的密封装置产生的摩擦阻力 在机械效率中加以考虑。因工作部件是卧式放置�重力的水平分力为零�这样需 要考虑的力有�夹紧力�导轨摩擦力�惯性力。
在对液压系统进行工况分析时�本设计实例只考虑组合机床动力滑台所受到 的工作负载、惯性负载和机械摩擦阻力负载�其他负载可忽略。
防止油液温升过高。
从工况图中可以清楚地看到�在这个液压系统的工作循环内�液压要求油源
交替地提供低压大流量和高压小流量的油液。而快进快退所需的时间 t1 和工进所 需的时间 t 2 分别为
工进时液压缸的推力计算公式为
F / �m � A1 p1 � A2 p2 � A1 p1 � ( A1 / 2) p2 �
根据已知参数�液压缸无杆腔的有效作用面积可计算为
F
A1 �
�m
p1 �
p2 2
16333 .33 �10 6
�
0.8
3�
2
� 0.006282 m 2
液压缸缸筒直径为
D � 4 A1 � � 89 .46 mm mm
5
工进过程中�当孔被钻通时�由于负载突然消失�液压缸有可能会发生前 冲的现象�因此液压缸的回油腔应设置一定的背压(通过设置背压阀的方式)�选 取此背压值为 p2=0.8MPa。
快进时液压缸虽然作差动连接,但连接管路中不可避免地存在着压降 �p �且 有杆腔的压力必须大于无杆腔�估算取 �p � 0.5MPa。快退时回油腔中也是有背 压的�这时选取被压值 p2 =0.6MPa。
3
Fm
� m�
�v �t
�
20000 9.81
7 �
60 � 0.15
N
对ASME_1管壳式换热器设计的介绍

#5# 2004年第6期1沿革关于管壳式换热器管板、管子和壳体的设计,美国在过去一直以T EM A(T ubuler Exchan g er M anu-facturer's Association)标准为主要依据。
ASM EØ-11983年版,首次以附录AA的方式列入了U形管式换热器2种比较简单结构类型的管板设计; 1992年版又增加了固定管板式换热器3种结构类型的管板设计;并在以后的各版中对此二者陆续增添类型并修改、完善,还补充了计算实例。
在2002年的增补(2002A)又增加了浮动式换热器6种类型静止端管板、4种类型固定端管板的管板设计。
至2003年增补(2003A),则把以前各版列在附录AA的管板设计规则和列在UW-20的管子对管板焊缝统一列入新编的UH X篇,并重新命名为对管壳式换热器的规则。
这些规则,基本上都按照ASMEØ-2的应力分析设计概念,对由不同载荷在不同结构处引起的应力进行分类,分别采用不同的限制条件。
至今,ASM EØ-1的UH X篇对U形管式换热器的管板已列入6种结构类型(见图1),对固定管板式换热器的管板已列入4种结构类型(见图2),对浮动式换热器的静止端管板已列入6种(见图1)、对浮动端管板已列入4种管板结构类型(见图3),连同管子对管板的焊缝结构和计算,以及计算实例等,构成了完整的管壳式换热器管板、管子和壳体设计体系。
2简单介绍和分析虽然T EMA标准也采用弹性基础圆平板理论,但是它把影响管板、管束、壳体(必要时包括膨胀节)变形的各项复杂因素都归纳在有效设计压力P中,所列出的管板、管束和壳体的设计公式形式上甚为简单,而对各类换热器、特别是固定管板式换热器有效压力P的确定却甚为繁复,所列出的有关公式也较难分析各相关元件对管板、管束和壳体应力的影响,而且各类换热器管板的结构类型也不如现行ASM EØ-1所列的齐全。
和国内外各有关管板设计的标准相比,ASMEØ-1对管板设计也采用开孔圆平板(如U形管式)或弹性基础上开孔圆平板(如固定管板式和浮动管板式)理论,即不计或计及管束对管板变形的弹性支承作用。
GB50497-2009建筑基坑工程监测技术规范[1]
![GB50497-2009建筑基坑工程监测技术规范[1]](https://img.taocdn.com/s3/m/0fcc0f0584254b35effd3493.png)
GB50497-2009建筑基坑工程监测技术规范[1]中华人民共和国国家标准P GB50497-2009建筑基坑工程监测技术规范Technical Code for Monitoring of Building ExcavationEngineering2009—04—29发布 2009—09—01实施中华人民共和国建设部联合发布国家质量监督检验检疫总局中华人民共和国国家标准建筑基坑工程监测技术规范Technical Code for Monitoring of BuildingExcavation EngineeringGB 50497—2009主编部门:山东省建设厅批准部门:中华人民共和国住房和城乡建设部施行日期:2009年09月01日中国建筑工业出版社2009 北京前言本规范是根据建设部《关于印发“2006年工程建设标准规范制定、修订计划(第一批)”的通知》(建标[2006]77号文)的要求,由济南大学会同9个单位共同编制完成。
本规范共有9章及7个附录,内容包括总则、术语、基本规定、监测项目、监测点布置、监测方法及精度要求、监测频率、监测报警、数据处理与信息反馈等。
本规范是我国首次编制的建筑基坑工程监测技术规范。
在编制过程中编制组调查总结了近年来我国建筑基坑工程监测的实践经验,吸收了国内外相关科技成果,开展了多项专题研究并形成了专题研究报告,通过各种方式在全国范围内广泛征求了意见。
本规范的初稿、征求意见稿经多次编制工作会议的讨论、反复修改后,形成送审稿并通过了审查。
本规范以黑体字标志的条文为强制性条文,必须严格执行。
本规范由住房和城乡建设部负责管理和对强制性条文进行解释,由主编单位负责具体技术内容的解释。
为了提高本规范的质量,敬请各单位在执行本标准的过程中,注意总结经验,积累资料,随时将有关意见和建议反馈给济南大学国家标准《建筑基坑工程监测技术规范》管理组(济南市济微路106号,邮编250022),以供今后修订时参考。
设计一台钻镗两用组合机床地液压系统
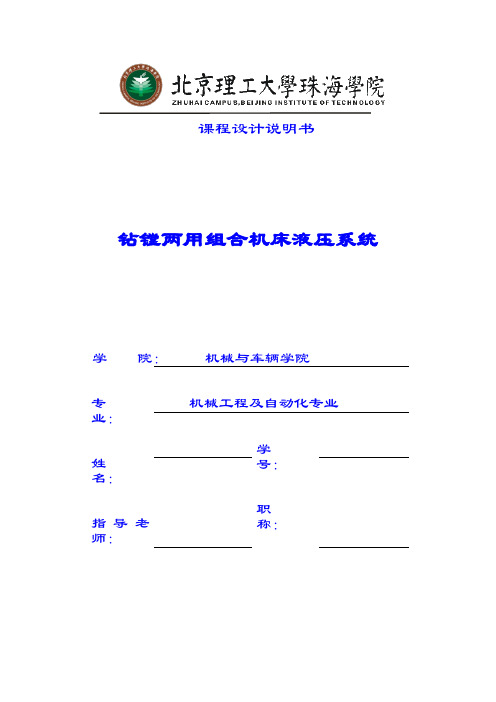
课程设计说明书钻镗两用组合机床液压系统学院:机械与车辆学院专业:姓名:指导老师:机械工程及自动化专业学号:职称:中国·珠海二○一二年五月北京理工大学珠海学院课程设计任务书学生姓名:专业班级:机械工程及自动化指导教师:工作部门:机械与车辆学院一、课程设计题目设计一台钻、镗两用组合机床的液压系统,要求液压系统完成“快进→工进→快退→停止”的工作循环及工件的定位与夹紧。
已知:最大切削力为12000N,运动部件自重为18000N,工作台快进行程为200mm,工进行程为200mm,快进、快退速度为5m/min,工进速度为20—100mm/min,加、减速时间为0.2s,导轨为平导轨,静摩擦系数为0.2,动摩擦系数为0.1。
工件所需夹紧力不得超过6000N,最小不低于3330N,由松开到夹紧的时间为1s,夹紧缸的行程为40mm。
二、课程设计内容液压传动课程设计一般包括以下内容:(1) 明确设计要求进行工况分析;(2) 确定液压系统主要参数;(3) 拟定液压系统原理图;(4) 计算和选择液压元件;(5) 验算液压系统性能;(6) 结构设计及绘制零部件工作图;(7) 编制技术文件。
三、进度安排四、基本要求(1) 液压传动课程设计是一项全面的设计训练,它不仅可以巩固所学的理论知识,也可以为以后的设计工作打好基础。
在设计过程中必须严肃认真,刻苦钻研,一丝不苟,精益求精。
(2) 液压传动课程设计应在教师指导下独立完成。
教师的指导作用是指明设计思路,启发学生独立思考,解答疑难问题,按设计进度进行阶段审查,学生必须发挥主观能动性,积极思考问题,而不应被动地依赖教师查资料、给数据、定方案。
(3) 设计中要正确处理参考已有资料与创新的关系。
任何设计都不能凭空想象出来,利用已有资料可以避免许多重复工作,加快设计进程,同时也是提高设计质量的保证。
另外任何新的设计任务又总有其特定的设计要求和具体工作条件,因而不能盲目地抄袭资料,必须具体分析,创造性地设计。
工程方案设计要求

工程方案设计要求1. 项目背景及目的1.1 项目背景本项目是针对某公司生产车间的空气质量问题进行改善的工程项目。
由于生产过程中产生的废气和粉尘对员工的健康造成了一定的影响,因此需要对空气质量进行改善,保障员工健康。
1.2 项目目的通过本工程方案设计,改善车间的空气质量,减少对员工的健康影响,提高生产效率和产品质量。
2. 工程范围2.1 地点本项目针对某公司的生产车间进行改善。
2.2 内容改善车间的空气质量,包括废气排放控制、通风系统改善、粉尘处理等。
3. 设计要求3.1 空气质量监测必须对车间的空气质量进行详细监测,包括废气成分、粉尘浓度、温湿度等指标,以了解现状。
3.2 废气排放控制分析车间内废气来源和成分,设计相应的废气排放控制方案,保证废气排放符合相关标准,降低对员工的影响。
3.3 通风系统改善对车间的通风系统进行改善,确保空气流通畅通,减少空气污染物浓度,提高空气质量。
3.4 粉尘处理对车间内产生的粉尘进行收集和处理,减少粉尘对空气质量的影响。
3.5 设备选型选用符合国家标准的通风设备和粉尘处理设备,以确保系统运行稳定、耐用。
3.6 安全性设计方案必须充分考虑安全性,保证设备运行安全可靠,减少事故风险。
4. 施工要求4.1 施工单位施工单位必须具有相关的施工资质和经验,具备相关工程施工能力。
4.2 施工进度施工单位必须按照设计方案的要求,严格控制施工进度,确保工程按时完工。
4.3 施工质量施工单位必须按照国家标准和设计要求,保证工程质量,杜绝质量问题。
4.4 安全管理施工单位必须严格执行安全管理要求,保障施工人员的安全。
5. 质量验收5.1 质量验收标准施工单位在完成工程后,需按照设计要求进行质量验收,确保工程符合相关标准。
5.2 质量验收单位质量验收由相关部门或第三方进行,对工程质量进行严格把关。
6. 工程验收6.1 工程验收标准工程验收按照设计要求进行,确保工程质量符合标准。
6.2 工程验收单位工程验收由相关部门或第三方进行,对工程的各项指标进行验收。
机械设计课程设计说明书一用于带式运输机上的两级圆柱齿轮减速器
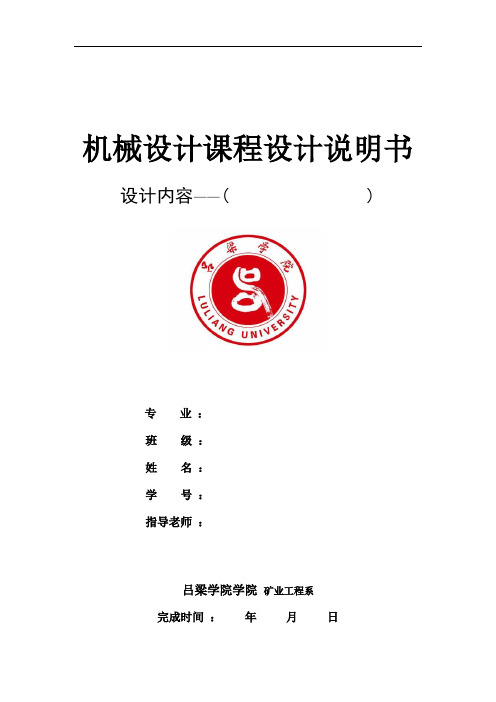
机械设计课程设计说明书设计内容——( )专业:班级:姓名:学号:指导老师:吕梁学院学院矿业工程系完成时间:年月日2013 级机械设计制造及其自动化专业《机械设计课程设计》任务书学生姓名:班级:学号:一、设计题目:设计一用于带式运输机上的两级圆柱齿轮减速器二、给定数据及要求已知条件:运输带工作拉力F= 12000 N;运输带工作速度v= m/s(允许运输带速度误差为±5%);滚筒直径D= 450 mm,滚筒长度L=800mm;两班制,连续单向运转,载荷轻微冲击;工作年限5年;环境最高温度350C;小批量生产。
三、应完成的工作1.减速器装配图1张;2.零件工作图2—4张(从动轴、齿轮);3.设计说明书1份。
系主任:教研室负责人:指导教师:发题日期完成日期目录任务书.............................................................................................................................. 第一章机械传动装置的总体设计................................................................................1.1 选择电动机........................................................................................................1.1.1 电动机类型的选择..................................................................................1.1.2 电动机容量的选择..................................................................................1.1.3 电动机转速的选择..................................................................................1.2 传动比的分配....................................................................................................1.3传动系统的运动和动力参数计算.....................................................................1各轴的转速、功率和扭矩计算.....................................................................1.3.2各轴的运动参数表................................................................................... 第二章V带传动的设计..............................................................................................2.1 V带的参数设计.................................................................................................2.2 V带的主要参数表............................................................................................. 第三章齿轮的设计........................................................................................................3.1齿轮传动设计.....................................................................................................3齿轮参数设计.................................................................................................3.1.2齿轮的主要参数表................................................................................... 第四章轴的设计(输入轴)........................................................................................4.1高速轴(输入轴)的设计.................................................................................4.材料的选择和热处理.....................................................................................4..........................................................................................................................4.轴的结构设计并绘制结构草图.....................................................................4.2低速轴(输出轴)的设计.................................................................................4.材料的选择和热处理.....................................................................................4..........................................................................................................................4.轴的结构设计并绘制结构草图.....................................................................4.4低速轴(输出轴)的校核.................................................................................4..........................................................................................................................4.......................................................................................................................... 第五章联轴器的选择....................................................................................................5.1.联轴器的选择和参数......................................................................................... 第六章键联接的选择和计算........................................................................................6.1 键的选择和参数................................................................................................ 第七章滚动轴承的选择................................................................................................7.1轴承的选择......................................................................................................... 第八章箱体结构尺寸....................................................................................................8.1 箱体的结构尺寸................................................................................................ 设计小结.......................................................................................................................... 参考文献.......................................................................................................................... 附表.................................................................................................................................. 附图..................................................................................................................................min参考文献[1] —[2] —附表1 第一章各轴的运动参数表附表2 第二章V带传动的主要参数表附表3第三章齿轮的主要参数表附表4 第八章箱体的结构尺寸表附录16。
0-机械设计基础课程大作业-要求 (1)(1)

课程大作业学生须完成2个课程大作业:机器方案及传动设计、支承轴系部件装置设计。
课程大作业的设计工况条件、设计参数与所选课程设计题目和参数一致,并与后续学期课程教学内容并行实施(温馨提醒:望保留计算数据,备后续第三学期课程设计再次使用),按规定时间节点提交。
大作业成绩计入平时成绩。
1) 根据课程设计任务书,每位同学一组设计参数和工作条件,技术参数和工作条件应交叉组合,不得重复。
2) 课程大作业学生须独立完成。
课程大作业具体内容要求如下:(1) 课程大作业 1:机器方案及传动设计本课程大作业按自行选定的课程设计题目和设计参数进行设计。
1) 机器传动方案给出2-3种方案,进行评价,优选一种方案。
2) 机器结构方案设计包括装配方案、结构布局、支承方案、连接方案。
给出2-3种方案,进行评价,优选一种方案。
3) 驱动方案设计根据设计要求选定电动机类型及型号。
4) 运动与动力参数计算各级传动的运动参数和动力参数:总传动比和各级传动比、转速、功率、转矩等。
5) 传动性能设计根据传动方案,进行相应传动零部件设计,如带轮传动、链传动、齿轮传动、蜗杆传动或螺旋传动等性能设计与校核。
6)传动件结构设计根据传动方案,传动性能设计,进行相应传动件结构设计。
具体要求:1) 画出方案简图并进行评价,方案简图与评价结果均汇总于设计报告中。
2) 按规定模板撰写设计报告。
3) 方案图(要表述清楚,利于不同设计者理解本人设计表达)。
4) 传动零件零件图绘制(零件图采用CAD软件绘制)(2) 课程大作业 2:支承轴系部件装置设计本课程大作业按本课程前期自行选定的课程设计题目和设计参数进行设计(为课程大作业1的局部结构的详细结构设计,属于部件装配图)。
1)完成轴系支承方案设计给出2-3种支承方案,进行评价,优选一种方案。
2)支承轴系部件装置结构设计完成设计方案传动轴系装置结构设计。
3)轴的性能分析4)轴承的性能分析5)键/销性能分析具体要求:1)画出轴系支承结构图(A2或A3图幅,按适当比例绘制)2)按模板撰写设计报告。
高级培训-105 应用CFD仿真分析优化某SUV车型的机舱流场1

应用CFD仿真分析优化某SUV车型的机舱流场1前言SUV的全称是Sport Utility Vehicle,中文意思是运动型多用途汽车。
现在的SUV一般指那些以轿车平台为基础、在一定程度上既具有轿车的舒适性,又具有一定越野性的车型通俗说就是能在城市中开的越野车[1]。
国内SUV市场正处于从优质走向成熟的阶段。
按照SUV的功能性,通常分为城市型SUV与越野车,前者代表有景逸x3、奇瑞瑞虎、宝马X1、奥迪Q3、现代ix35、雪佛兰创酷等;后者代表有奔驰G500、悍马H2、丰田普拉多、铃木吉姆尼、路虎卫士等。
,SUV的特点是动力强、越野性、宽敞舒适及良好的载物和载客功能。
良好的通过性是SVU车型的一大亮点,SUV车的机舱结构特点与轿车基本相同,但是它的离地间隙、接近角和离去角比普通的轿车要好。
从以上SUV车的功能和结构特点可以看出,为了保证它具有良好的热管理性能,设计阶段的SUV车型的机舱优化更加重要。
在当前的整车开发过程中,需要通过大量的仿真分析和试验来平衡动力总成冷却需求、空气动力学特性、环境控制、造型风格、整车结构以及成本之间的关系。
前端的设计在整车开发过程中非常重要,比如发动机的冷却和环境需求要求有足够的空气进入机舱,但是这会增加整车的冷却阻力。
机舱内安装导流板可以增加前端开口的利用率并有效防止机舱热回流进入冷凝器和散热器,但这同时也增加了成本。
采用CFD分析技术可以快速有效地解决这一问题,实现不同性能需求间的平衡[9-12]。
本文针对中心开发的一款红旗品牌SUV车型,在设计阶段开展机舱流场分析,确定导风板方案提高冷却风的有效利用、优化风扇布置提高散热器入口冷却空气速度分布均匀性,同时优化发动机进气口设计,保证发动机的进气需求。
2仿真分析模型与计算方法2.1仿真分析模型为了准确反映机舱内的流动情况,机舱流动CFD分析的整车模型是实际整车结构的全尺寸三维模型,仅去掉螺栓等小的特征,对于关键部件如动力总成、格栅、前端冷却模块等则按照实际几何保留尺寸,格栅及机舱布置如图1所示。
对IEC 61400-1(第四版)中风电机组载荷计算部分的解读与分析
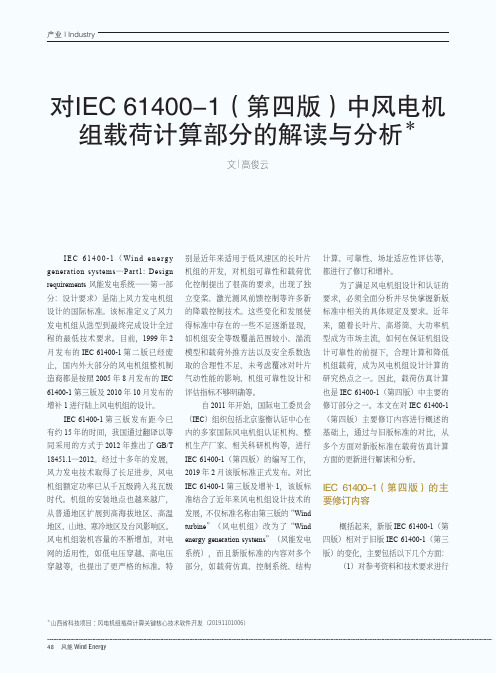
对IEC 61400-1(第四版)中风电机组载荷计算部分的解读与分析*文|高俊云I E C61400-1(Wi n d e n e r g y generation systems―Part1: Design requirements 风能发电系统⸺分:设计要求)是陆上风力发电机组设计的国际标准。
该标准定义了风力发电机组从选型到最终完成设计全过程的最低技术要求。
目前,1999年2月发布的IEC 61400-1第二版已经废止,国内外大部分的风电机组整机制造商都是按照2005年8月发布的IEC 61400-1第三版及2010年10月发布的增补1进行陆上风电机组的设计。
IEC 61400-1第三版发布距今已有约15年的时间,我国通过翻译以等同采用的方式于2012年推出了GB/T 18451.1―2012。
经过十多年的发展,风力发电技术取得了长足进步,风电机组额定功率已从千瓦级跨入兆瓦级时代。
机组的安装地点也越来越广,从普通地区扩展到高海拔地区、高温地区、山地、寒冷地区及台风影响区。
风电机组装机容量的不断增加,对电网的适用性,如低电压穿越、高电压穿越等,也提出了更严格的标准。
特别是近年来适用于低风速区的长叶片机组的开发,对机组可靠性和载荷优化控制提出了很高的要求,出现了独立变桨、激光测风前馈控制等许多新的降载控制技术。
这些变化和发展使得标准中存在的一些不足逐渐显现,如机组安全等级覆盖范围较小、湍流模型和载荷外推方法以及安全系数选取的合理性不足、未考虑覆冰对叶片气动性能的影响、机组可靠性设计和评估指标不够明确等。
自2011年开始,国际电工委员会(IEC)组织包括北京鉴衡认证中心在内的多家国际风电机组认证机构、整机生产厂家、相关科研机构等,进行IEC 61400-1(第四版)的编写工作,2019年2月该版标准正式发布。
对比IEC 61400-1第三版及增补1,该版标准结合了近年来风电机组设计技术的发展,不仅标准名称由第三版的“Windturbine”(风电机组)改为了“Windenergy generation systems”(风能发电系统),而且新版标准的内容对多个部分,如载荷仿真、控制系统、结构计算、可靠性、场址适应性评估等,都进行了修订和增补。
- 1、下载文档前请自行甄别文档内容的完整性,平台不提供额外的编辑、内容补充、找答案等附加服务。
- 2、"仅部分预览"的文档,不可在线预览部分如存在完整性等问题,可反馈申请退款(可完整预览的文档不适用该条件!)。
- 3、如文档侵犯您的权益,请联系客服反馈,我们会尽快为您处理(人工客服工作时间:9:00-18:30)。
1 设计要求及工况分析
1.1 设计要求
一卧式钻镗组合机床动力头要完成快进→工进→快退→原位停止的工作循环,最大轴向切削力为F=30000N,动力头自重FG=19600N,工作进给要求能在0.02~0.12m/min范围内无级调速,快进、快退速度为6m/min,工进行程为200mm,快进行程为200mm,导轨型·设计该液压系统。
2.2 负载与运动分析
假定主轴转速n=360r/min,s=0.147mm/r
(1)工作负载Ft30000N
G v6 (2)惯性负载Fm()()19600 999N (1-1)g
t600.2
(3)摩擦负载因为采用的动力滑台是平导轨,因此作用在其上的正压力N=G=19600N。
静摩擦阻力 Ffs fsN0.2196003920N (1-2)动摩擦阻力 Ffd fdN0.1196001960N (1-3)取液压缸的机械效率m0.90,得出的液压缸在各个工作阶段的负载值如下表1-1所示。
根据液压缸上述各阶段的负载可绘制负载循环图F-l。
速度图按已知数值v1v3=6m/min,快进行程长度为l1200mm,工进行程长度为l2200mm,快退行程长度l3l1l2400mm和工进速度v2等绘图,其中v2由主轴转速及每转进给量求出。
即:
v2ns53mm/min (1-4)
2 主要参数的确定
2.1 初选液压缸的工作压力
所设计的动力头在工进时的负载最大,在其他工况负载都不太高,由课本表9-2和9-3初选液压缸工作压力p1=4MPa
2.2 计算液压缸主要尺寸
鉴于动力头要求快进、快退速度相等,液压缸可选单杠式的并在快进时作差动连接。
此时液压缸无杆腔工作面积A1应为有杆腔A2的两倍,即活塞杆外径d与液压缸内径D有d=0.707D的关系。
在钻孔加工时,液压缸回油路上必须有背压p2,以防被钻通时滑台突然前冲。
可取p2=0.8MPa。
快进时液压缸虽然作差动连接,但是由于p存在,有杆腔的压力必须大于无杆腔,估算时可取p约为0.5MPa估算。
由工进时的推力计算液压缸的面积
A
A1F A1p1A2p2A1p1(1)p2 (2-1)
m所以A1(
F
m
)/(p1p2)35511/(4
0.8
)0.0099m299cm2 2
D4A1/11.23cm (2-2)
d0.707D7.94cm (2-3)
当按GB 2348-1980将这些直径圆整成接近标准值时得
D=11cm,d=8cm。
由此求得液压缸两腔实际的有效面积为:A1D2/495.03cm2 (2-4) A2A(D2d2)/444.77cm2 (2-5)经检查,活塞杆的强度和稳定性均符合要求。
根据上述D与d的值,可以估算液压缸在不同工作阶段的压力、流量和功率,如表2-1.并据此绘出液压工况图,如图2.,其中虚线、细实线和双点划线分别表示P、q、p。
表2-1 液压缸在不同工作阶段的压力、流量和功率值
3 液压系统图的拟定
3.1 选择基本回路
(1)选择调速回路
由功率曲线得知,这台机床液压系统的功率小,动力头运动速度低,工作负载变化小,可采用进口节流的调速形式。
由于要求不高,考虑经济性,使用节流阀来进行进口节流调速。
由于液压系统选用了节流调速的方式,系统中液压油的循环必须是开式的。
从工况图系统的工作循环内,液压缸交替地要求油源提供低
压大流量和高压小流量的液压油。
最大流量和最小流量之比约为60,而快进、快退所需的时间t1和工进所需时间t2分别为
t1=(l1/v1)+(l3/v3)=(60x200)/(6x1000)+(60x400)/(6x1000)=6s (3-1)
t2=l2/v2=(60x200)/53=226.4s (3-2)
即t2/t1=38。
因此从提高系统效率、节约能量的角度来看,采用单个定量泵作为油源是不合适的,应选用双联式定量叶片泵。
(2)选择快速运动和换向回路
系统在节流调速回路后,不管采用什么油源形式,都必须有单独的油路直接通向液压缸两腔,以实现快速运动。
考虑快进速度与快退速度相等,因此在本系统中采用了单杆液压缸作差动连接,来实现液压缸的快进快退换向回路。
在油路设计一个行程阀来控制快进与工进的转换。
(3)选择速度换接回路
由工况图得当动力头从快进转向工进时输入的液压缸的流量由
30.16L/min降到0.504L/min,动力头速度变化很大,应该选用行程阀来控制速度的换接,以减少液压冲击。
当动力头由工进转向快退时,回路中通过的流量大,为了保证换向平稳,可采用电液换向阀式换接回路。
(4)选择调压回路和卸荷回路
系统的压力变化由工况图可知变化与流量变化相反,系统调压主要由高压小流量泵来调节供应,流量变化由另一个低压大流量泵来调节。
两个泵互相作用一起调节油路的压力和流量供应。
为了防止系统出现一些故障,导致系统压力在短时间内急剧上升,在泵的出口设计一个溢流阀与泵并联。
当系统压力急剧上升,为了不让系统元件遭到破坏,也为了避免高压油从管道接口处爆出,溢流阀就会自动为系统卸荷,通向油箱,保护设备。
(5)顺序动作
通过以上的各个回路的设计以及组装,目的就是能够通过系统的开关得以能实现动力头的循环动作,并符合要求。
动力头的顺序动作通过开关的通断来实现的,具体通断情况细节如下表:
表3-1电磁铁和行程阀的动作顺序
4 液压元件的计算与选择
液压元件的计算主要是计算各个元件在工作中承受的压力和流量。
根据计算得结果来选择元件的规格、型号,此外还要计算原动机的功率和油箱的容量,尽量选用标准元件,比较具有经济性。
4.1 动力元件的选择
液压缸整个工作循环中的最高工作压力为7.506Mpa,如果进油路上的压力损失为0.8Mpa,则高压小流量泵的最高的压力应为
pp1=7.506+0.8=8.306Mpa。
(5)顺序动作
通过以上的各个回路的设计以及组装,目的就是能够通过系统的开关得以能实现动力头的循环动作,并符合要求。
动力头的顺序动作通过开关的通断来实现的,具体通断情况细节如下表:
表3-1电磁铁和行程阀的动作顺序
4 液压元件的计算与选择
液压元件的计算主要是计算各个元件在工作中承受的压力和流量。
根据计算得结果来选择元件的规格、型号,此外还要计算原动机的功率和油箱的容量,尽量选用标准元件,比较具有经济性。
4.1 动力元件的选择
液压缸整个工作循环中的最高工作压力为7.506Mpa,如果进油路上的压力损失为0.8Mpa,则高压小流量泵的最高的压力应为
pp1=7.506+0.8=8.306Mpa。
低压大流量是在快速运动时才向液压缸供油,快退时液压缸中的工作压力比快进时大,如果取进油路的压力损失为0.5Mpa,则低压大流量泵的最高压力为
pp2=1.55+0.5=2.05Mpa。
两个液压泵向液压缸提供的最大流量为30.16L/min,若回路中的泄漏按液压
q
缸输入流量的10%估算,则两泵总流量应为
p=1.1x30.16=33.18L/min。
而溢流阀的最小稳定流量为3L/min,工进时输入液压缸的流量为0.5L/min,所以低压小流量的流量规格最小应为3.5L/min。
根据以上的压力和流量的数值查得,最后选择PV2R12型双联叶片泵。
由于液压缸在快退时输入功率最大,这相当于液压泵输出压力2.05Mpa,流量为30L/min p=0.75,则液压泵的驱动原动机所需的功率为:
P=ppqp/p=2.0530/60103)/(0.75103)=1.4kW (4-1)根据此数据查得,选择J02-32-6型电动机,其额定功率为2.2kw。
4.2 确定控制元件和辅助元件
根据液压系统的工作压力和通过各个控制阀类元件和辅助元件的实际流量,可选用这些元件的规格和型号,见下表:
4.3 确定油管
各元件间管道的规格按元件接口处的尺寸确定,液压缸进、出油管按输入的最大流量计算。
由于液压泵具体选定后液压缸在各个阶段的进、出流量已经与原定数据不同,所以要重新计算。
当液压油的流速取3m/min时,可得到液压缸有杆腔和无杆腔相连的油管内径为: d=2x(62.7106)/(310360)=21.1mm (4-2) d=2x(32106)/(310360)=15.05mm (4-3) 为标准化,本系统所有的油管均为内径18mm,外径25mm的10号冷拔钢管。
4.4 确定油箱
油箱的容积V按是V=aqv估算,当经验系数取6时,V=aqv=6x30=180L 按国标规定,取靠近的值V=200L。
5 回路压力损失验算
压力损失包括管道内的沿程损失和局部损失以及阀类元件处的局部损失三项。
阀类元件的局部压力损失则查出,当通过阀类元件的实际流量q不是公称流量qn p pn 之间有以下近似关系:p=pn(q2) (4-5) qn
5.1 热温升验算
工进在整个工作循环过程中所占用的时间达96%,所以系统的发热和液压油温升主要计算工进时的。
工进液压缸的有效功率为
p0=p2xq2=Fv=35511x0.053/60x1000=0.0314kW 泵的总输出功率为:
pi=pp1qp1pp2qp2=0.74kW (4-6)
则液压系统的发热量为
HI=pi-p0=0.74-0.0314=0.7086kw 求液压油的温升的近似值T=HI/2103=21 C
温升没有超出允许的范围,系统不需要设置冷却器。
10
4-7)(4-8)(。