锰系磷化工艺流程
磷化工艺流程及磷化工艺
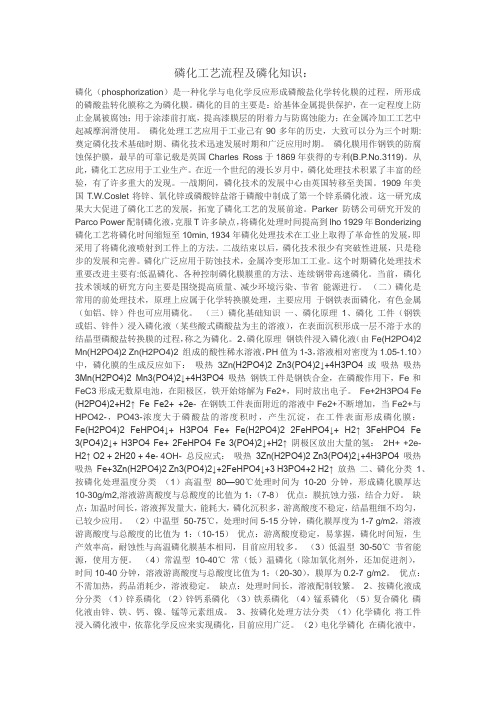
磷化工艺流程及磷化知识:磷化(phosphorization)是一种化学与电化学反应形成磷酸盐化学转化膜的过程,所形成的磷酸盐转化膜称之为磷化膜。
磷化的目的主要是:给基体金属提供保护,在一定程度上防止金属被腐蚀;用于涂漆前打底,提高漆膜层的附着力与防腐蚀能力;在金属冷加工工艺中起减摩润滑使用。
磷化处理工艺应用于工业己有90多年的历史,大致可以分为三个时期:奠定磷化技术基础时期、磷化技术迅速发展时期和广泛应用时期。
磷化膜用作钢铁的防腐蚀保护膜,最早的可靠记载是英国Charles Ross于1869年获得的专利(B.P.No.3119)。
从此,磷化工艺应用于工业生产。
在近一个世纪的漫长岁月中,磷化处理技术积累了丰富的经验,有了许多重大的发现。
一战期间,磷化技术的发展中心由英国转移至美国。
1909年美国T.W.Coslet将锌、氧化锌或磷酸锌盐溶于磷酸中制成了第一个锌系磷化液。
这一研究成果大大促进了磷化工艺的发展,拓宽了磷化工艺的发展前途。
Parker防锈公司研究开发的Parco Power配制磷化液,克服T许多缺点,将磷化处理时间提高到lho 1929年Bonderizing 磷化工艺将磷化时间缩短至10min, 1934年磷化处理技术在工业上取得了革命性的发展,即采用了将磷化液喷射到工件上的方法。
二战结束以后,磷化技术很少有突破性进展,只是稳步的发展和完善。
磷化广泛应用于防蚀技术,金属冷变形加工工业。
这个时期磷化处理技术重要改进主要有:低温磷化、各种控制磷化膜膜重的方法、连续钢带高速磷化。
当前,磷化技术领域的研究方向主要是围绕提高质量、减少环境污染、节省能源进行。
(二)磷化是常用的前处理技术,原理上应属于化学转换膜处理,主要应用于钢铁表面磷化,有色金属(如铝、锌)件也可应用磷化。
(三)磷化基础知识一、磷化原理1、磷化工件(钢铁或铝、锌件)浸入磷化液(某些酸式磷酸盐为主的溶液),在表面沉积形成一层不溶于水的结晶型磷酸盐转换膜的过程,称之为磷化。
磷化处理工艺操作规程
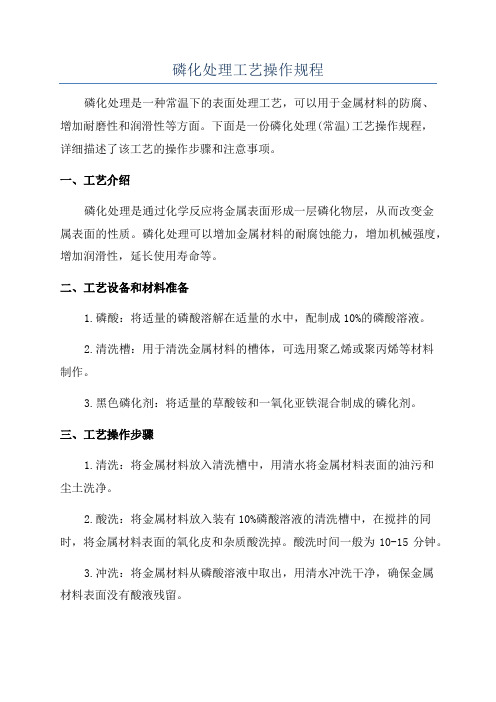
磷化处理工艺操作规程磷化处理是一种常温下的表面处理工艺,可以用于金属材料的防腐、增加耐磨性和润滑性等方面。
下面是一份磷化处理(常温)工艺操作规程,详细描述了该工艺的操作步骤和注意事项。
一、工艺介绍磷化处理是通过化学反应将金属表面形成一层磷化物层,从而改变金属表面的性质。
磷化处理可以增加金属材料的耐腐蚀能力,增加机械强度,增加润滑性,延长使用寿命等。
二、工艺设备和材料准备1.磷酸:将适量的磷酸溶解在适量的水中,配制成10%的磷酸溶液。
2.清洗槽:用于清洗金属材料的槽体,可选用聚乙烯或聚丙烯等材料制作。
3.黑色磷化剂:将适量的草酸铵和一氧化亚铁混合制成的磷化剂。
三、工艺操作步骤1.清洗:将金属材料放入清洗槽中,用清水将金属材料表面的油污和尘土洗净。
2.酸洗:将金属材料放入装有10%磷酸溶液的清洗槽中,在搅拌的同时,将金属材料表面的氧化皮和杂质酸洗掉。
酸洗时间一般为10-15分钟。
3.冲洗:将金属材料从磷酸溶液中取出,用清水冲洗干净,确保金属材料表面没有酸液残留。
4.磷化:将清洗干净的金属材料放入装有黑色磷化剂的磷化槽中,保持常温静置,时间根据材料的具体情况决定,一般为30-60分钟。
5.冲洗:将磷化完成的金属材料从磷化槽中取出,用清水冲洗干净,除去表面的磷化剂残留。
6.干燥:将冲洗干净的金属材料放入通风良好的地方,自然晾干。
四、注意事项1.操作时需佩戴防护手套和眼镜,以免酸液对皮肤和眼睛造成伤害。
2.操作过程中需注意防止酸液溅到周围环境或其他设备上,以免造成腐蚀。
3.磷化剂需按照一定比例混合制备,不得随意更改配方。
4.操作环境应通风良好,避免吸入磷化剂气体。
5.操作完成后,应及时清洁工作台和设备,避免磷化剂的残留。
五、工艺效果评估1.观察磷化处理后的金属材料表面是否呈现均匀的黑色。
2.通过化学测试,检测金属材料表面的磷化层厚度是否符合要求。
3.对磷化处理后的金属材料进行腐蚀试验,评估其耐腐蚀性能。
4.对磷化处理后的金属材料进行涂层附着力测试,评估其润滑性和耐磨性。
锰系磷化说明书

锰系磷化说明书 The manuscript was revised on the evening of 2021高温锰系黑色磷化液说明书一/本品能在钢铁上形成一种晶体状的锰系磷化膜,这层磷化膜能提高工件的耐磨性和耐腐蚀性能,磷化膜具有很强的吸附性,当浸泡了合适的油后具有高效的耐磨损效果,主要由磷酸铁和磷酸锰组成。
这种处理工艺能降低工件如活塞,活塞环,衬垫,凸轮轴,推杠,马达座及类似承载表面的磨损。
其他优点可归纳如下:锰系磷化处理使运动工件迅速跑合,防止承载表面之间金属与金属的直接接触,不会出现划伤或粘结。
由于磷化膜吸油,增加了处理过的表面的润滑作用。
消除了金属在机械加工中留下的刮痕。
延缓了腐蚀作用,因此也可以用作防腐底层。
可适用于汽车,摩托车,船舶,等高速运转零部件的减磨自润滑功能膜层处理。
以及工具,刀刃及较高标准要求标准件的耐摩,耐腐蚀处理。
二.产品特性1.高倍浓缩酸性液体。
2.用于钢铁表面的防腐耐摩处理。
3.也可以用于压铸件的处理。
4.在钢铁表面形成一层黑色的磷酸锰盐层。
5.符合甚至超过国标盐雾实验。
6..环保.安全,操作方便,废水处理简单/三.作业管理标准:管理项目管理标准1.皮膜建浴浓度:1比5(20%)2.全酸度(TA) :祥见本公司内部说明3.游离酸(FA):祥见本公司内部说明4.温度(Temp) 92-98℃.5.时间(Time) 8-20分钟6.限更新周期 12个月四.工艺流程:1.除油(XH-400)--水洗—除锈—水洗—表调(XH-28)--磷化(XH-575)---水洗—干燥或脱水防锈油(XH-300)?五.及添加方法:1.使用仪器及试剂:吸球、吸管、烧杯、 NaOH、酚酞(PP)、溴酚蓝(BPB)2.测量方法:(1)全酸度(TA):取槽处理10mL加酚酞(PP)指示剂3-5滴,再用 NaOH滴定,颜色由无色变至粉红5-10秒不褪色,即为其终点,此时所消耗 NaOH之毫升数,即为其全酸度之度数。
磷化处理工艺流程,表面处理黑色磷化工艺
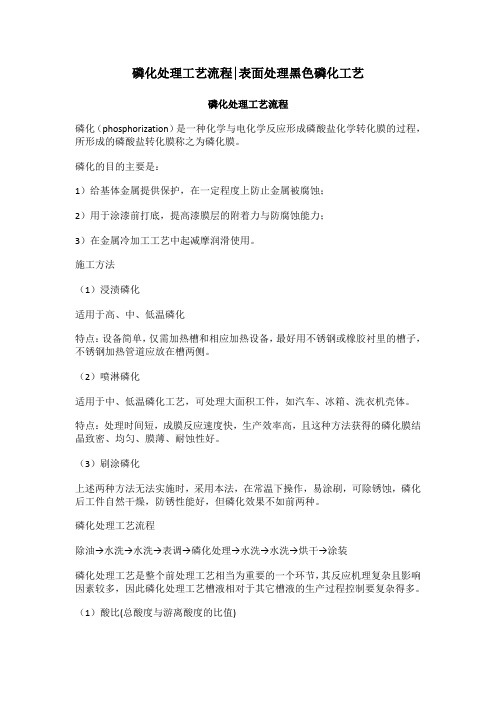
磷化处理工艺流程|表面处理黑色磷化工艺磷化处理工艺流程磷化(phosphorization)是一种化学与电化学反应形成磷酸盐化学转化膜的过程,所形成的磷酸盐转化膜称之为磷化膜。
磷化的目的主要是:1)给基体金属提供保护,在一定程度上防止金属被腐蚀;2)用于涂漆前打底,提高漆膜层的附着力与防腐蚀能力;3)在金属冷加工工艺中起减摩润滑使用。
施工方法(1)浸渍磷化适用于高、中、低温磷化特点:设备简单,仅需加热槽和相应加热设备,最好用不锈钢或橡胶衬里的槽子,不锈钢加热管道应放在槽两侧。
(2)喷淋磷化适用于中、低温磷化工艺,可处理大面积工件,如汽车、冰箱、洗衣机壳体。
特点:处理时间短,成膜反应速度快,生产效率高,且这种方法获得的磷化膜结晶致密、均匀、膜薄、耐蚀性好。
(3)刷涂磷化上述两种方法无法实施时,采用本法,在常温下操作,易涂刷,可除锈蚀,磷化后工件自然干燥,防锈性能好,但磷化效果不如前两种。
磷化处理工艺流程除油→水洗→水洗→表调→磷化处理→水洗→水洗→烘干→涂装磷化处理工艺是整个前处理工艺相当为重要的一个环节,其反应机理复杂且影响因素较多,因此磷化处理工艺槽液相对于其它槽液的生产过程控制要复杂得多。
(1)酸比(总酸度与游离酸度的比值)提高酸比可加快磷化处理工艺反应速度,使磷化处理工艺膜薄而细致,但酸比过高会使膜层过薄,易引起磷化处理工艺工件挂灰;酸比过低,磷化处理工艺反应速度缓慢,磷化处理工艺晶体粗大多孔,耐蚀性低,磷化处理工艺工件易生黄锈。
一般来说磷化处理工艺yao液体系或配方不同其酸比大小要求也不同。
(2)温度槽液温度适当提高,成膜速度加快,但温度过高,会影响酸比的变化,进而影响槽液的稳定性,同时膜层晶核粗大,槽液出渣量增大。
(3)沉渣量随着磷化处理工艺反应的不断进行,槽液内的沉渣量会逐渐增多,过量的沉渣会影响工件表面的界面反应,导致磷化处理工艺膜发花、挂灰严重,甚至不成膜,因此槽液必须根据处理的工件量和使用时间适时进行倒槽,进行清渣除淤。
磷化前的预处理和两种常用磷化工艺
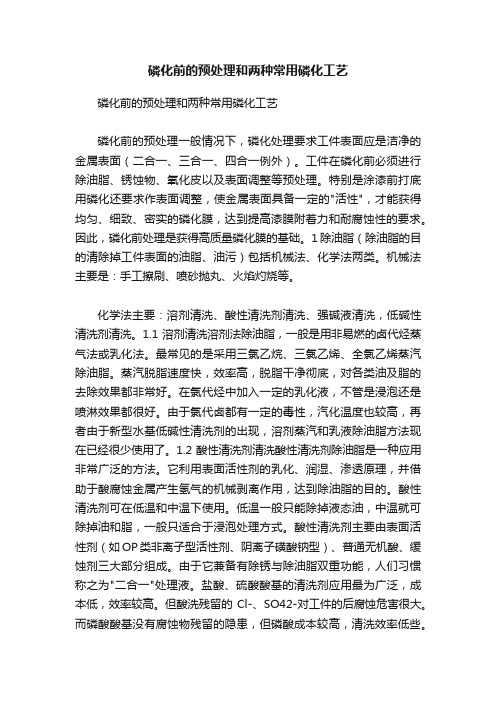
磷化前的预处理和两种常用磷化工艺磷化前的预处理和两种常用磷化工艺磷化前的预处理一般情况下,磷化处理要求工件表面应是洁净的金属表面(二合一、三合一、四合一例外)。
工件在磷化前必须进行除油脂、锈蚀物、氧化皮以及表面调整等预处理。
特别是涂漆前打底用磷化还要求作表面调整,使金属表面具备一定的"活性",才能获得均匀、细致、密实的磷化膜,达到提高漆膜附着力和耐腐蚀性的要求。
因此,磷化前处理是获得高质量磷化膜的基础。
1除油脂(除油脂的目的清除掉工件表面的油脂、油污)包括机械法、化学法两类。
机械法主要是:手工擦刷、喷砂抛丸、火焰灼烧等。
化学法主要:溶剂清洗、酸性清洗剂清洗、强碱液清洗,低碱性清洗剂清洗。
1.1溶剂清洗溶剂法除油脂,一般是用非易燃的卤代烃蒸气法或乳化法。
最常见的是采用三氯乙烷、三氯乙烯、全氯乙烯蒸汽除油脂。
蒸汽脱脂速度快,效率高,脱脂干净彻底,对各类油及脂的去除效果都非常好。
在氯代烃中加入一定的乳化液,不管是浸泡还是喷淋效果都很好。
由于氯代卤都有一定的毒性,汽化温度也较高,再者由于新型水基低碱性清洗剂的出现,溶剂蒸汽和乳液除油脂方法现在已经很少使用了。
1.2酸性清洗剂清洗酸性清洗剂除油脂是一种应用非常广泛的方法。
它利用表面活性剂的乳化、润湿、渗透原理,并借助于酸腐蚀金属产生氢气的机械剥离作用,达到除油脂的目的。
酸性清洗剂可在低温和中温下使用。
低温一般只能除掉液态油,中温就可除掉油和脂,一般只适合于浸泡处理方式。
酸性清洗剂主要由表面活性剂(如OP类非离子型活性剂、阴离子磺酸钠型)、普通无机酸、缓蚀剂三大部分组成。
由于它兼备有除锈与除油脂双重功能,人们习惯称之为"二合一"处理液。
盐酸、硫酸酸基的清洗剂应用最为广泛,成本低,效率较高。
但酸洗残留的Cl-、SO42-对工件的后腐蚀危害很大。
而磷酸酸基没有腐蚀物残留的隐患,但磷酸成本较高,清洗效率低些。
对于锌件,铝件一般不采用酸性清洗剂清洗,特别锌件在酸中的腐蚀极快。
磷化简介

磷化简介磷化是金属材料防腐蚀的重要方法之一,其目的在于给基体金属提供防腐蚀保护、用于喷漆前打底、提高覆膜层的附着力与防腐蚀能力及在金属加工中起减摩润滑作用等。
按用途可分为三类:1、涂装性磷化 2、冷挤压润滑磷化 3、装饰性磷化。
按所用的磷酸盐分类有:磷酸锌系、磷酸锌钙系、磷酸铁系、磷酸锌锰系、磷酸锰系。
根据磷化的温度分类有:高温(80 ℃以上)磷化、中温(50~70 ℃)磷化、低温磷化(40 ℃左右)和常温磷化( 10~30 ℃)。
一、磷化成膜机理磷化主要有以下过程:(1)金属的溶解过程即金属与磷化液中的游离酸发生反应:M+H3PO4 = M(H2PO4)2+H2↑(2)促进剂的加速过程为:M(H2PO4)2+Fe+[O]→M3(PO4)2+FePO由于氧化剂的氧化作用,加速了不溶性盐的逐步沉积,使金属基体与槽液隔离,会限制甚至停止酸蚀的进行。
(3)磷酸及盐的水解磷化液的基本成分是一种或多种重金属的酸式磷酸盐, 其分子式为Me(H2PO4)2,这些酸式磷酸盐溶于水,在一定浓度及pH值下发生水解,产生游离磷酸:Me(H2PO4)2=MeHPO4+H3PO43MeHPO4=Me3(PO4)2+H3PO4H3PO4=H2PO4-+H+= HPO2-4 + 2H+ =PO3-4 + 3H+由于金属工件表面的H+浓度急剧下降,导致磷酸根各级离解平衡向右移动,最终成为磷酸根。
(4 ) 磷化膜的形成当金属表面离解出的PO3-4与磷化槽液中的金属离子Zn2+、Mn2+、Fe2+达到饱和时,即结晶沉积在金属工件表面,晶粒持续增长,直到在金属工件表面生成连续不溶于水的牢固的磷化膜:3M2 + + 2PO3 -4 + 4H2O = M3 ( PO4 ) 2·4H2O ↓2 M2 + + Fe2 + + 2PO3 -4 + 4H2O= M2 Fe ( PO4 ) 2· 4H2O金属工件溶解出的Fe2+一部分作为磷化膜的组成部分被消耗掉,而残留在磷化槽液中的Fe2+则氧化成Fe3+,生成FePO4沉淀,即磷化沉渣的主要成分之一。
磷化处理工艺

磷化处理工艺关于磷化处理工艺1 防锈磷化工艺磷化工艺的早期应用是防锈,钢铁件经磷化处理形成一层磷化膜,起到防锈作用。
经过磷化防锈处理的工件防锈期可达几个月甚至几年(对涂油工件而言),广泛用于工序间、运输、包装贮存及使用过程中的防锈,防锈磷化主要有铁系磷化、锌系磷化、锰系磷化三大品种。
铁系磷化的主体槽液成分是磷酸亚铁溶液,不含氧化类促进剂,并且有高游离酸度。
这种铁系磷化处理温度高于9 5℃,处理时间长达30min以上,磷化膜重大于10g/m2,并且有除锈和磷化双重功能。
这种高温铁系磷化由于磷化速度太慢,现在应用很少。
锰系磷化用作防锈磷化具有最佳性能,磷化膜微观结构呈颗粒密堆集状,是应用最为广泛的防锈磷化。
加与不加促进剂均可,如果加入硝酸盐或硝基胍促进剂可加快磷化成膜速度。
通常处理温度80~100℃,处理时间10~20min,膜重在7.5克/m2以上。
锌系磷化也是广泛应用的一种防锈磷化,通常采用硝酸盐作为促进剂,处理温度80~90℃,处理时间10~15min,磷化膜重大于7.5g/m2,磷化膜微观结构一般是针片紧密堆集型。
防锈磷化一般工艺流程:除油除锈——水清洗——表面调整活化——磷化——水清洗——铬酸盐处理——烘干——涂油脂或染色处理通过强碱强酸处理过的工件会导致磷化膜粗化现象,采用表面调整活化可细化晶粒。
锌系磷化可采用草酸、胶体钛表调。
锰系磷化可采用不溶性磷酸锰悬浮液活化。
铁系磷化一般不需要调整活化处理。
磷化后的工件经铬酸盐封闭可大幅度提高防锈性,如再经过涂油或染色处理可将防锈性提高几位甚至几十倍,见表1。
表1 磷化膜与涂油复合对耐蚀性的影响出现锈蚀时间(h)(盐雾你发的这个词被禁止发行B117-64)材料 出现锈蚀时间(0.5 裸钢 0.5 15.0 钢+涂油 15.0 4.0 钢+16g/m2锌磷化 4.0 550.0 钢+锌磷化+涂油 550.0 摘自Freeman D B.Phosphating and Metal Pretreatment Woodhead-Faukner,1986. 2 耐磨减摩润滑磷化工艺对于发动机活塞环、齿轮、制冷压缩机一类工件,它不仅承受一次载荷,而且还有运动摩擦,要求工件能减摩、耐摩。
锰盐磷化工艺控制

锰盐磷化工艺控制
魏全明 , 罗
1
庆 , 谢春英 , 程红霞
2
2
2
(1 . 西北工业大学材料学院 , 陕西 西安 2 . 成都飞机工业集团制造工程部 , 四川 成都 [摘 要]
1 试
验
1. 1 工艺流程 工件表面准备→溶剂清洗→吹砂→装挂→碱 清洗→冷水洗→热水洗→锰盐磷化→冷水洗→封 闭→干燥→除氢→涂油。 1. 2 锰盐磷化液配方和工艺参数 PL 复合磷化液 Fe
2+
,
145 g /L 1. 5~ 3. 0 g /L 50~ 75 点 ( 10 3) 点 90~ 98 12~ 15 m in
测量
, 延长磷化时
间并使磷化膜粗糙多孔、 附着力差, 甚至会使零件 表面得不到完整的磷化 膜层, 同时 使槽液沉淀增 多。当槽液中的游离酸过多时 , 可以在磷化槽中加 入中和剂 Neutra lizer 200( Parker& Am chem 公司生 产的磷化液专用中和剂 ) 来调节酸度, 试验表明每 升磷化液中加 0 . 3 g Neu tra lizer 200 可以降低游离 酸度 5 点。游离酸度过低时 , 磷化膜薄, 甚至磷化 不上。因此需严格控制游离酸度范围为 7~ 13 点 较为合适。 ( 3) F e
[ 3 ] [ 4 ] [ 5 ]
2+
参
考
文
献
]
顾国成 , 吴文森 . 钢铁材 料的防 蚀涂层 [M ]. 北京 : 科学出版社 , 1987: 337. 王章中 , 蔡 55. ASTM B 117, 盐雾试验 [ S]. I GC 04. 24. 116, 脆性 - 应力致脆试验 [ S] . 成都市科学技术交流站表面处理 研究会 . 电镀技术 [M ] . 成都 : 四川人民出版社 , 1982: 515 . [ 编辑 : 魏兆军 ] 璐 . 磷化膜后 处理与润 滑状况 对其摩 擦学特性的影响 [ J]. 材料保 护 , 2003, 36 ( 1) : 54 ~
锰系磷化作用和用途
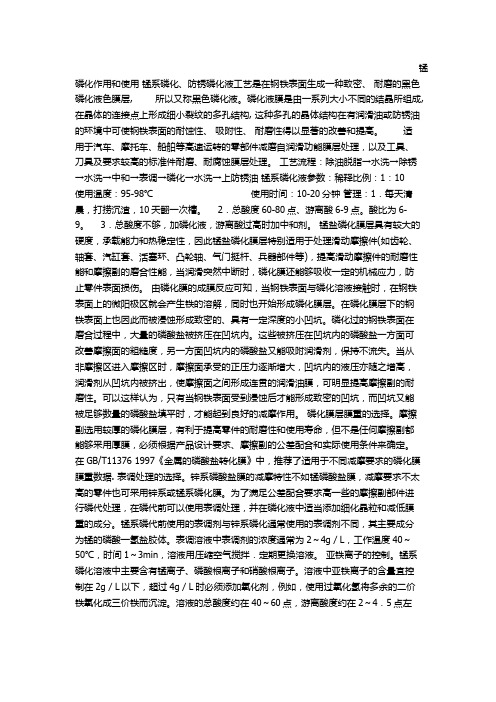
锰磷化作用和使用锰系磷化、防锈磷化液工艺是在钢铁表面生成一种致密、耐磨的黑色磷化液色膜层, 所以又称黑色磷化液。
磷化液膜是由一系列大小不同的结晶所组成,在晶体的连接点上形成细小裂纹的多孔结构, 这种多孔的晶体结构在有润滑油或防锈油的环境中可使钢铁表面的耐蚀性、吸附性、耐磨性得以显著的改善和提高。
适用于汽车、摩托车、船舶等高速运转的零部件减磨自润滑功能膜层处理,以及工具、刀具及要求较高的标准件耐磨、耐腐蚀膜层处理。
工艺流程:除油脱脂→水洗→除锈→水洗→中和→表调→磷化→水洗→上防锈油锰系磷化液参数:稀释比例:1:10 使用温度:95-98℃使用时间:10-20分钟管理:1.每天清晨,打捞沉渣,10天翻一次槽。
2.总酸度60-80点、游离酸6-9点。
酸比为6-9。
3.总酸度不够,加磷化液,游离酸过高时加中和剂。
锰盐磷化膜层具有较大的硬度,承载能力和热稳定性,因此锰盐磷化膜层特别适用于处理滑动摩擦件(如齿轮、轴套、汽缸套、活塞环、凸轮轴、气门挺杆、兵器部件等),提高滑动摩擦件的耐磨性能和摩擦副的磨合性能,当润滑突然中断时,磷化膜还能够吸收一定的机械应力,防止零件表面损伤。
由磷化膜的成膜反应可知,当钢铁表面与磷化溶液接触时,在钢铁表面上的微阳极区就会产生铁的溶解,同时也开始形成磷化膜层。
在磷化膜层下的钢铁表面上也因此而被浸蚀形成致密的、具有一定深度的小凹坑。
磷化过的钢铁表面在磨合过程中,大量的磷酸盐被挤压在凹坑内。
这些被挤压在凹坑内的磷酸盐一方面可改善摩擦面的粗糙度,另一方面凹坑内的磷酸盐又能吸附润滑剂,保持不流失。
当从非摩擦区进入摩擦区时,摩擦面承受的正压力逐渐增大,凹坑内的液压亦随之增高,润滑剂从凹坑内被挤出,使摩擦面之间形成连贯的润滑油膜,可明显提高摩擦副的耐磨性。
可以这样认为,只有当钢铁表面受到浸蚀后才能形成致密的凹坑,而凹坑又能被足够数量的磷酸盐填平时,才能起到良好的减摩作用。
磷化膜层膜重的选择。
低合金钢的锰磷化处理
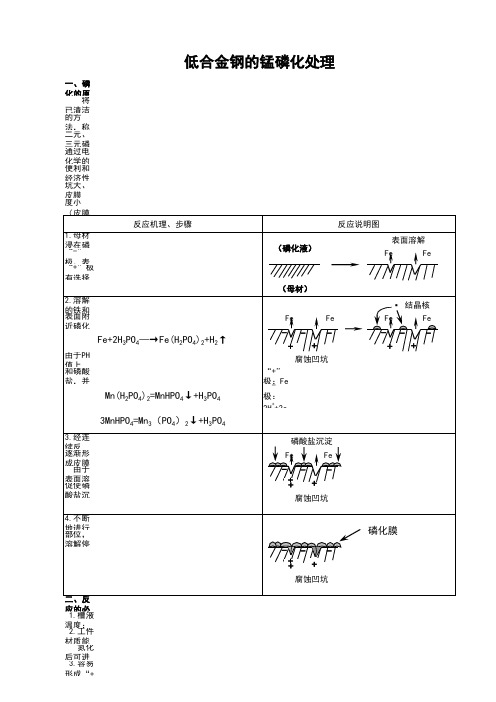
Fe
Fe
-- ++ +
腐蚀凹坑
4.不断 地部进 位行, 溶解停
-- ++ +
腐蚀凹坑
磷化膜
二、反 应1.的槽必液 温2.度工:件 材质氮能化 后3.可容进易 形成“+
4.工件 表三面 、清磷 化粗糙
项目 1.表面 形状
2.槽液 条反件 应平 衡
3.其他 条件
四、低
合★ 金依钢
1据.总下酸文 度 锰磷 化在3槽0~液 6总0点之的, 必须根
低合金钢的锰磷化处理
一、磷 化的原
将 已清洁 的方 法,称 二元、 三元磷 通过电 化学的 便利和 经济性 坑大、 皮膜 度小 (皮膜
1.母材 浸“-在”磷 极“+,”表极 有选择
反应机理、步骤
2.溶解 的表铁 面和附 近磷化
Fe+2H3PO4—→Fe(H2PO4)2+H2↑
由于PH 值和上 磷酸 盐,并
[Fe](%) 0.4 0.3 0.2 0.1 0
TA=35± 5点 [Fe]=0. 15~
20
40Biblioteka 60 TAMn(H2PO4)2=MnHPO4↓+H3PO4
3.经连 续逐反 渐形 成由皮于膜 表促面 使溶磷 酸盐沉
3MnHPO4=Mn3(PO4)2↓+H3PO4
(磷化液)
反应说明图
表面溶解
Fe
Fe
(母材)
Fe
Fe
-- -
++
腐蚀凹坑
“+” 极“:-”Fe 极: 2H++2e
· 结晶核
Fe
Fe
磷化工艺流程
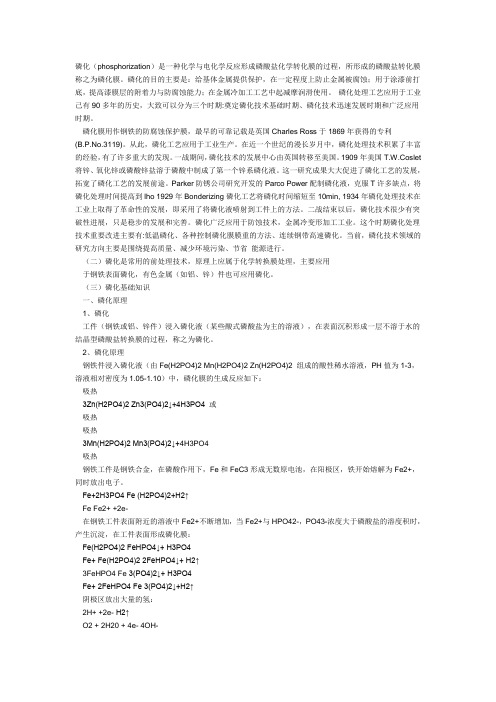
磷化(phosphorization)是一种化学与电化学反应形成磷酸盐化学转化膜的过程,所形成的磷酸盐转化膜称之为磷化膜。
磷化的目的主要是:给基体金属提供保护,在一定程度上防止金属被腐蚀;用于涂漆前打底,提高漆膜层的附着力与防腐蚀能力;在金属冷加工工艺中起减摩润滑使用。
磷化处理工艺应用于工业己有90多年的历史,大致可以分为三个时期:奠定磷化技术基础时期、磷化技术迅速发展时期和广泛应用时期。
磷化膜用作钢铁的防腐蚀保护膜,最早的可靠记载是英国Charles Ross于1869年获得的专利(B.P.No.3119)。
从此,磷化工艺应用于工业生产。
在近一个世纪的漫长岁月中,磷化处理技术积累了丰富的经验,有了许多重大的发现。
一战期间,磷化技术的发展中心由英国转移至美国。
1909年美国T.W.Coslet 将锌、氧化锌或磷酸锌盐溶于磷酸中制成了第一个锌系磷化液。
这一研究成果大大促进了磷化工艺的发展,拓宽了磷化工艺的发展前途。
Parker防锈公司研究开发的Parco Power配制磷化液,克服T许多缺点,将磷化处理时间提高到lho 1929年Bonderizing磷化工艺将磷化时间缩短至10min, 1934年磷化处理技术在工业上取得了革命性的发展,即采用了将磷化液喷射到工件上的方法。
二战结束以后,磷化技术很少有突破性进展,只是稳步的发展和完善。
磷化广泛应用于防蚀技术,金属冷变形加工工业。
这个时期磷化处理技术重要改进主要有:低温磷化、各种控制磷化膜膜重的方法、连续钢带高速磷化。
当前,磷化技术领域的研究方向主要是围绕提高质量、减少环境污染、节省能源进行。
(二)磷化是常用的前处理技术,原理上应属于化学转换膜处理,主要应用于钢铁表面磷化,有色金属(如铝、锌)件也可应用磷化。
(三)磷化基础知识一、磷化原理1、磷化工件(钢铁或铝、锌件)浸入磷化液(某些酸式磷酸盐为主的溶液),在表面沉积形成一层不溶于水的结晶型磷酸盐转换膜的过程,称之为磷化。
磷化工艺流程图
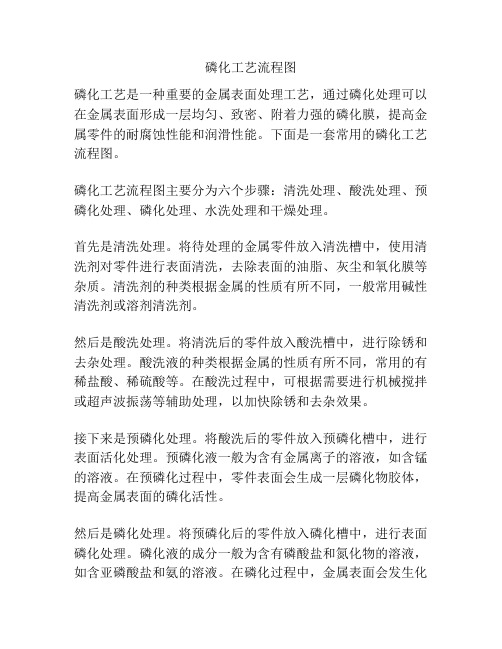
磷化工艺流程图磷化工艺是一种重要的金属表面处理工艺,通过磷化处理可以在金属表面形成一层均匀、致密、附着力强的磷化膜,提高金属零件的耐腐蚀性能和润滑性能。
下面是一套常用的磷化工艺流程图。
磷化工艺流程图主要分为六个步骤:清洗处理、酸洗处理、预磷化处理、磷化处理、水洗处理和干燥处理。
首先是清洗处理。
将待处理的金属零件放入清洗槽中,使用清洗剂对零件进行表面清洗,去除表面的油脂、灰尘和氧化膜等杂质。
清洗剂的种类根据金属的性质有所不同,一般常用碱性清洗剂或溶剂清洗剂。
然后是酸洗处理。
将清洗后的零件放入酸洗槽中,进行除锈和去杂处理。
酸洗液的种类根据金属的性质有所不同,常用的有稀盐酸、稀硫酸等。
在酸洗过程中,可根据需要进行机械搅拌或超声波振荡等辅助处理,以加快除锈和去杂效果。
接下来是预磷化处理。
将酸洗后的零件放入预磷化槽中,进行表面活化处理。
预磷化液一般为含有金属离子的溶液,如含锰的溶液。
在预磷化过程中,零件表面会生成一层磷化物胶体,提高金属表面的磷化活性。
然后是磷化处理。
将预磷化后的零件放入磷化槽中,进行表面磷化处理。
磷化液的成分一般为含有磷酸盐和氮化物的溶液,如含亚磷酸盐和氨的溶液。
在磷化过程中,金属表面会发生化学反应,生成一层致密的磷化膜。
接下来是水洗处理。
将磷化后的零件放入水洗槽中,进行表面的中和和去除残留的磷化液。
水洗处理可以采用流水冲洗或浸泡冲洗。
水洗的时间和次数可以根据需要进行调整,以确保洗净效果。
最后是干燥处理。
将水洗后的零件放入干燥槽中,进行表面干燥处理。
干燥处理一般采用自然干燥或热风干燥,以去除零件表面的水分和残留的溶剂。
以上就是一套常用的磷化工艺流程图。
在实际应用中,还需要根据具体的情况进行工艺参数的调整和工艺步骤的优化,以达到最佳的磷化效果。
磷化处理工艺流程
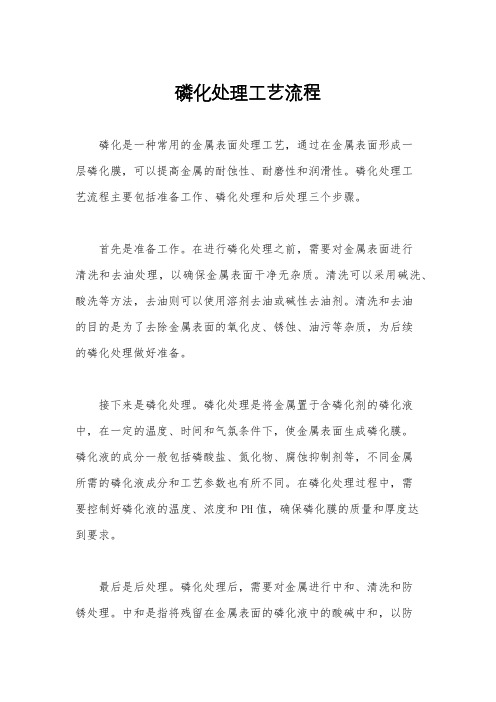
磷化处理工艺流程磷化是一种常用的金属表面处理工艺,通过在金属表面形成一层磷化膜,可以提高金属的耐蚀性、耐磨性和润滑性。
磷化处理工艺流程主要包括准备工作、磷化处理和后处理三个步骤。
首先是准备工作。
在进行磷化处理之前,需要对金属表面进行清洗和去油处理,以确保金属表面干净无杂质。
清洗可以采用碱洗、酸洗等方法,去油则可以使用溶剂去油或碱性去油剂。
清洗和去油的目的是为了去除金属表面的氧化皮、锈蚀、油污等杂质,为后续的磷化处理做好准备。
接下来是磷化处理。
磷化处理是将金属置于含磷化剂的磷化液中,在一定的温度、时间和气氛条件下,使金属表面生成磷化膜。
磷化液的成分一般包括磷酸盐、氮化物、腐蚀抑制剂等,不同金属所需的磷化液成分和工艺参数也有所不同。
在磷化处理过程中,需要控制好磷化液的温度、浓度和PH值,确保磷化膜的质量和厚度达到要求。
最后是后处理。
磷化处理后,需要对金属进行中和、清洗和防锈处理。
中和是指将残留在金属表面的磷化液中的酸碱中和,以防止对环境和设备的腐蚀。
清洗是指用清水或稀碱溶液清洗金属表面,去除残留的磷化液和杂质。
防锈处理则是为了增强磷化膜的耐蚀性能,可以采用油封、涂漆等方法进行防锈处理。
总的来说,磷化处理工艺流程包括准备工作、磷化处理和后处理三个步骤。
在实际操作中,需要严格控制每个步骤的工艺参数,确保磷化膜的质量和性能达到要求。
同时,也需要注意环保和安全,合理处理废液和废气,确保生产过程安全环保。
希望以上内容能够对磷化处理工艺有所帮助。
高温锰系磷化液配方

高温锰系磷化液配方高温锰系磷化液配方:随着科技进步和社会发展,高温锰系磷化成为了一道非常重要的加工工艺。
而磷化液的配方可谓关乎制品质量,更是制约着生产效益的一大关键。
一、高温锰系磷化液配方的重要性高温锰系磷化工艺具有涂层厚度均匀度、硬度及耐腐蚀性三大优点,广泛应用于钢铁、铜材、铝材等基材的防腐、增韧等领域,应用价值与未来前景广阔。
磷化液的配方关系到磷化液能否在现代工业领域中得到广泛应用,这点可谓非常重要。
二、高温锰系磷化液配方的组成高温锰系磷化液的主要组成物如下:1. 锰盐在高温锰系磷化液策略中扮演着重要角色,其主要作用是增加液体的氧化还原电势和调节液体的pH值,有利于磷化产物的生成。
2. 氟化物氟化物的存在有助于在磷化过程中去除杂质,增加涂层密度,有利于涂层的质量。
3. 氯化物氯化物的作用在于增加磷化液的酸度,同时对于磷化过程中的金属离子有着清除作用,保证磷化液中金属离子的稳定性和可测性。
4. 硝酸盐硝酸盐的主要作用是提高磷化液中的氧化还原电势,对于电解质的稳定和溶解有着显著促进作用。
5. 磷酸盐磷酸盐的存在有助于在磷化液中形成多种磷酸盐离子,对于磷化液中的阴离子有着很大的作用,能够促进磷化液的pH值的稳定性和涂层的质量。
三、高温锰系磷化液配方的优化通过对配方的优化调整可以提高生产效益,使产品质量更上一层楼。
举个例子,增加硝酸盐和氟化物的配比能够显著提高涂层的质量,相应的,控制磷酸盐的含量可以提高磷化液的反应性,进而提高涂层的质量。
四、高温锰系磷化液的涂层质量检测离不开对涂层质量的检测。
检测方法有酸度测定、涂层质量检测、表面硬度检测三种。
酸度测定主要是检测磷化液中pH值的稳定性和涂层的厚度,涂层质量检测主要是检测涂层表面的平整性和涂层结晶度,表面硬度检测则是检测涂层的硬度,保证涂层的质量和性能表现。
高温锰系磷化液配方的优化和涂层质量检测的标准化,相信会使这项工艺走得更稳健,更有前途。
黑色锰系磷化工艺文件
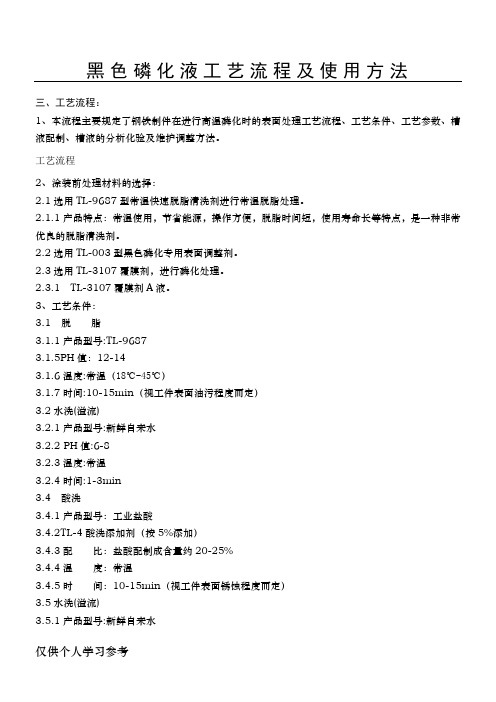
黑色磷化液工艺流程及使用方法三、工艺流程:1、本流程主要规定了钢铁制件在进行高温磷化时的表面处理工艺流程、工艺条件、工艺参数、槽液配制、槽液的分析化验及维护调整方法。
工艺流程2、涂装前处理材料的选择:2.1选用TL-9687型常温快速脱脂清洗剂进行常温脱脂处理。
2.1.1产品特点:常温使用,节省能源,操作方便,脱脂时间短,使用寿命长等特点,是一种非常优良的脱脂清洗剂。
2.2选用TL-003型黑色磷化专用表面调整剂。
2.3选用TL-3107覆膜剂,进行磷化处理。
2.3.1 TL-3107覆膜剂A液。
3、工艺条件:3.1 脱脂3.1.1产品型号:TL-96873.1.5PH值:12-143.1.6温度:常温(18℃-45℃)3.1.7时间:10-15min(视工件表面油污程度而定)3.2水洗(溢流)3.2.1产品型号:新鲜自来水3.2.2 PH值:6-83.2.3温度:常温3.2.4时间:1-3min3.4 酸洗3.4.1产品型号:工业盐酸3.4.2TL-4酸洗添加剂(按5%添加)3.4.3配比:盐酸配制成含量约20-25%3.4.4温度:常温3.4.5时间:10-15min(视工件表面锈蚀程度而定)3.5水洗(溢流)3.5.1产品型号:新鲜自来水3.5.2 PH值:6-83.5.3温度:常温3.5.4时间:1-3min3.6水洗(溢流)3.6.1产品型号:新鲜自来水3.6.2 PH值:6-83.6.3温度:常温3.6.4时间:1-3min3.7 表调3.7.1产品型号:TL-003表面调整剂3.7.2配比:4‰-6‰3.7.3PH值:8.5-93.7.4温度:常温3.7.5时间:30秒-1分钟3.8磷化3.8.1产品型号:TL-3107A液3.8.2配比:14-16%3.8.6时间:15-20min3.9水洗(溢流)3.9.1产品型号:新鲜自来水3.9.2 PH值:6-83.9.3温度:常温3.9.4时间:1-3min5、槽液配制方法5.1脱脂槽:(按1000升计)5.1.1在脱脂槽中加水至配槽液总量的1/4体积刻度线。
- 1、下载文档前请自行甄别文档内容的完整性,平台不提供额外的编辑、内容补充、找答案等附加服务。
- 2、"仅部分预览"的文档,不可在线预览部分如存在完整性等问题,可反馈申请退款(可完整预览的文档不适用该条件!)。
- 3、如文档侵犯您的权益,请联系客服反馈,我们会尽快为您处理(人工客服工作时间:9:00-18:30)。
锰系磷化工艺流程
锰系磷化工艺是一种常用的表面处理方法,可在金属表面生成一
层具有防腐、减摩、润滑等多种功能的膜层。
下面我们一起来了解一
下锰系磷化工艺流程:
1. 表面清洗:首先,需要将待处理的金属表面进行清洗,以去
除其表面的油脂、灰尘、氧化层等杂质,保证后续处理的质量。
2. 预处理:将待处理的金属表面进行预处理,使其表面形成一
层基础的锰氧化物膜。
预处理的方法有多种,如酸洗、电化学处理等。
3. 磷化处理:接下来进行磷化处理,即将待处理金属表面浸泡
在含有磷化剂的溶液中,通过化学反应在表面生成一层富含磷的复合
膜层。
4. 旋转:磷化完成后,需要将金属件进行旋转,以保证涂层的
均匀性。
旋转的速度和时间应该根据具体情况进行调整。
5. 清洗:磷化处理后,需要对金属表面进行清洗,去除残留的
磷化剂等。
6. 封闭层:最后加入封闭层,在磷化膜层表面生成一层防锈、
防腐、润滑等功能性封闭层。
通过以上的几个步骤,即可顺利完成锰系磷化工艺流程。
需要注
意的是,不同金属的磷化工艺可能会略有差异,在具体操作时需要注
意遵循材料科学的原则。
同时,工艺的成功还要依赖于厂商的设备及
技术的优势,保证质量的稳定性和批量生产的效率。