材表面预处理、下料工艺守则
下料工艺处理制度与要求
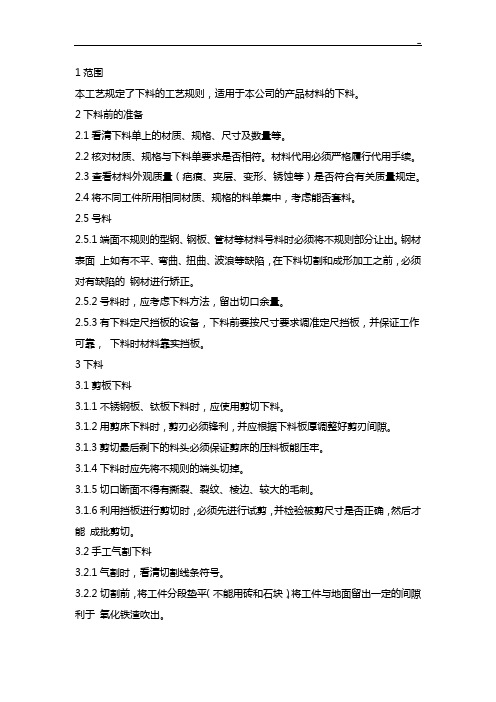
1范围本工艺规定了下料的工艺规则,适用于本公司的产品材料的下料。
2下料前的准备2.1看清下料单上的材质、规格、尺寸及数量等。
2.2核对材质、规格与下料单要求是否相符。
材料代用必须严格履行代用手续。
2.3查看材料外观质量(疤痕、夹层、变形、锈蚀等)是否符合有关质量规定。
2.4将不同工件所用相同材质、规格的料单集中,考虑能否套料。
2.5号料2.5.1端面不规则的型钢、钢板、管材等材料号料时必须将不规则部分让出。
钢材表面上如有不平、弯曲、扭曲、波浪等缺陷,在下料切割和成形加工之前,必须对有缺陷的钢材进行矫正。
2.5.2号料时,应考虑下料方法,留出切口余量。
2.5.3有下料定尺挡板的设备,下料前要按尺寸要求调准定尺挡板,并保证工作可靠,下料时材料靠实挡板。
3下料3.1剪板下料3.1.1不锈钢板、钛板下料时,应使用剪切下料。
3.1.2用剪床下料时,剪刃必须锋利,并应根据下料板厚调整好剪刃间隙。
3.1.3剪切最后剩下的料头必须保证剪床的压料板能压牢。
3.1.4下料时应先将不规则的端头切掉。
3.1.5切口断面不得有撕裂、裂纹、棱边、较大的毛刺。
3.1.6利用挡板进行剪切时,必须先进行试剪,并检验被剪尺寸是否正确,然后才能成批剪切。
3.2手工气割下料3.2.1气割时,看清切割线条符号。
3.2.2切割前,将工件分段垫平(不能用砖和石块),将工件与地面留出一定的间隙利于氧化铁渣吹出。
3.2.3将氧气调节到所需的压力。
对于射吸式割炬是否有射吸能力,如果割炬不正常时,应检查修理,否则禁止使用。
3.2.4预热火焰的长度应根据板材的厚度不同加以调整,火焰性质均应采用中性火焰,即打开切割氧时火焰不出现碳化焰。
3.2.5气割不同厚度的钢板时,要调节切割氧的压力,而同一把割炬的几个不同号码嘴头应尽量不经常调换。
3.2.6切割速度应适当。
速度适当时,熔渣和火花垂直向而去;速度太快时,产生较大的后拖量,不易切透,火花向后面,造成铁渣往上面,容易产生回火现象。
板材下料工艺守则

板材下料工艺守则编号XXXXXXXXX有限公司20XX.X1、适用范围1)本守则适用于我厂高低压配电装置所用各种黑色金属、有色金属、非金属直线边缘的板料毛坯的剪切及其他类似的下料。
2)被剪裁的材料厚度基本尺寸为0.35~16mm2、材料1)材料应符合技术条件要求。
2)对于卷板应予校平,不允许表面有严重擦伤、划痕、杂质、绣斑。
3)校平后的板材,按每平方米平面度不得大于3.5mm(用1米钢板尺检验),对于其他板材达不到平面度要求也需要校平。
3、设备及工艺装备、工具a、剪扳机;b、扳手、钳子、油壶、螺丝刀、手锤;c、游标卡尺、钢板尺、卷尺、直角尺、外径千分尺,划针。
4、工艺准备1)按所分配的任务领料并检查材料是否符合工艺卡片的要求,将合格的材料整齐的堆放在机床旁。
2)零件对材料有料纹要求的,应按其要求剪裁。
3)给剪扳机各油孔加油。
4)检查剪床刀片是否锋利及紧固可靠,并按板料厚度调好间隙(见表2)。
5、工艺过程1)首先用钢板尺量出刃口与挡料板之间的距离(按工艺卡片的规定),反复测量数次,直到所裁料的尺寸符合规定要求为止,然后进行纵挡板调整,使之与横挡板或刃口成90º,并紧牢。
2)开车试剪进料时应注意板料各边互相垂直,,首件检查符合工艺卡的规定后,方可进行生产,否则应重新调整纵横挡板。
3)辅助人员应该配合好,在加工过程中应随时检查尺寸、毛刺、角度,并及时与操作人员联系。
4)剪裁好的成品或半成品按不同规格应整齐摆放,不可随意乱放,以防止和其他规格板材混料及受压变形。
5)为了减少刃口磨损,钢板面及台面要保持清洁,剪板机床面上要严禁放置工具及其他材料。
6)剪切板料的宽度不得小于30mm。
6、工艺规范1)根据生产批量采用合理的套裁方法,先下大料,后下小料,尽量提高材料利用率,2)另件为弯曲件或有料纹要求的,应按其料纹、轧展方向进行裁剪,对于厚度大于3mm以上的钢板,更要注意以免产生折裂现象。
3)卷板经放直气割校平,剪切钢板时需先剪除毛边。
红木板材表面预处理工艺
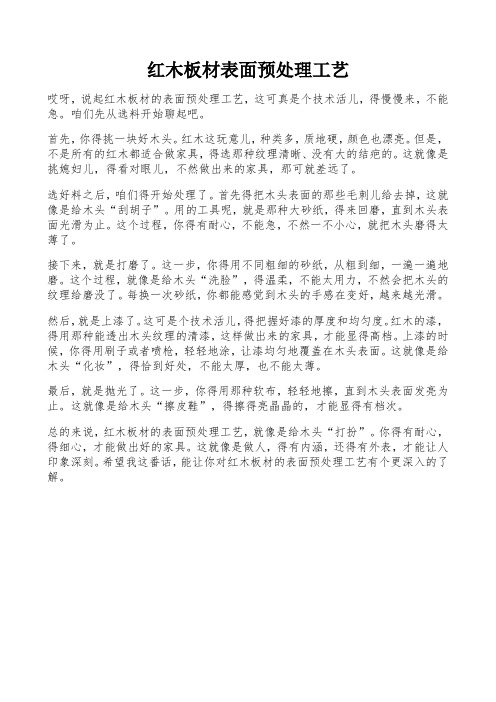
红木板材表面预处理工艺哎呀,说起红木板材的表面预处理工艺,这可真是个技术活儿,得慢慢来,不能急。
咱们先从选料开始聊起吧。
首先,你得挑一块好木头。
红木这玩意儿,种类多,质地硬,颜色也漂亮。
但是,不是所有的红木都适合做家具,得选那种纹理清晰、没有大的结疤的。
这就像是挑媳妇儿,得看对眼儿,不然做出来的家具,那可就差远了。
选好料之后,咱们得开始处理了。
首先得把木头表面的那些毛刺儿给去掉,这就像是给木头“刮胡子”。
用的工具呢,就是那种大砂纸,得来回磨,直到木头表面光滑为止。
这个过程,你得有耐心,不能急,不然一不小心,就把木头磨得太薄了。
接下来,就是打磨了。
这一步,你得用不同粗细的砂纸,从粗到细,一遍一遍地磨。
这个过程,就像是给木头“洗脸”,得温柔,不能太用力,不然会把木头的纹理给磨没了。
每换一次砂纸,你都能感觉到木头的手感在变好,越来越光滑。
然后,就是上漆了。
这可是个技术活儿,得把握好漆的厚度和均匀度。
红木的漆,得用那种能透出木头纹理的清漆,这样做出来的家具,才能显得高档。
上漆的时候,你得用刷子或者喷枪,轻轻地涂,让漆均匀地覆盖在木头表面。
这就像是给木头“化妆”,得恰到好处,不能太厚,也不能太薄。
最后,就是抛光了。
这一步,你得用那种软布,轻轻地擦,直到木头表面发亮为止。
这就像是给木头“擦皮鞋”,得擦得亮晶晶的,才能显得有档次。
总的来说,红木板材的表面预处理工艺,就像是给木头“打扮”。
你得有耐心,得细心,才能做出好的家具。
这就像是做人,得有内涵,还得有外表,才能让人印象深刻。
希望我这番话,能让你对红木板材的表面预处理工艺有个更深入的了解。
下料工艺守则
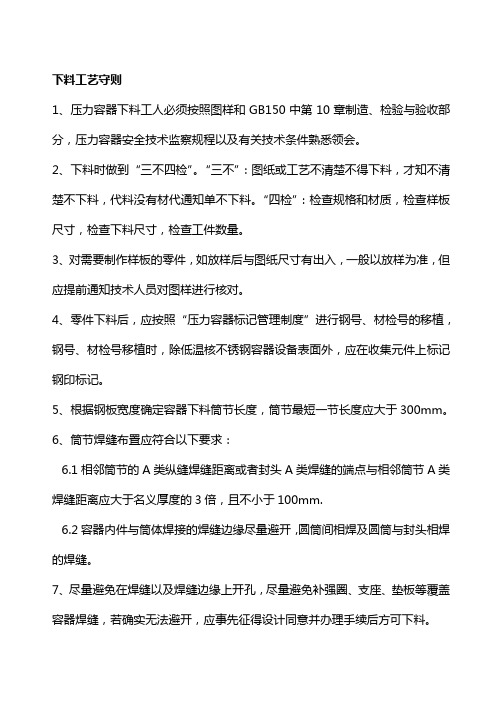
下料工艺守则1、压力容器下料工人必须按照图样和GB150中第10章制造、检验与验收部分,压力容器安全技术监察规程以及有关技术条件熟悉领会。
2、下料时做到“三不四检”。
“三不”:图纸或工艺不清楚不得下料,才知不清楚不下料,代料没有材代通知单不下料。
“四检”:检查规格和材质,检查样板尺寸,检查下料尺寸,检查工件数量。
3、对需要制作样板的零件,如放样后与图纸尺寸有出入,一般以放样为准,但应提前通知技术人员对图样进行核对。
4、零件下料后,应按照“压力容器标记管理制度”进行钢号、材检号的移植,钢号、材检号移植时,除低温核不锈钢容器设备表面外,应在收集元件上标记钢印标记。
5、根据钢板宽度确定容器下料筒节长度,筒节最短一节长度应大于300mm。
6、筒节焊缝布置应符合以下要求:6.1相邻筒节的A类纵缝焊缝距离或者封头A类焊缝的端点与相邻筒节A类焊缝距离应大于名义厚度的3倍,且不小于100mm.6.2容器内件与筒体焊接的焊缝边缘尽量避开,圆筒间相焊及圆筒与封头相焊的焊缝。
7、尽量避免在焊缝以及焊缝边缘上开孔,尽量避免补强圈、支座、垫板等覆盖容器焊缝,若确实无法避开,应事先征得设计同意并办理手续后方可下料。
8、钢板凡需进行超声波探伤者,探伤合格后再进行下料。
9、根据钢板实际宽度,确定好筒节长度,画出拼版图供装配、检查、加工,下料应考虑纵、环焊缝收缩量。
10、所下料的正面拥有其标歇工好(图号)、产品名称、下料尺寸、筒节数量、材质、坡扣型式等内容。
11、筒体剪板必须保证刨边(打磨)时有足够的余量,对不刨边(打磨)的板料,剪板时要特便注意找正。
12、刨边(打磨)坡口必须按检查线找正,刨边(打磨)的尺寸公差必须小于或等于划线的尺寸公差,对刨边(打磨)尺寸有特殊要求者,必须按照图样工艺要求,严格控制坡口型式及尺寸,并用坡口样板检查。
13、按图样和Q/LSJM.G.19-2005《压力容器焊接试板管理制度》下评定试板和产品试板。
下料工艺守则
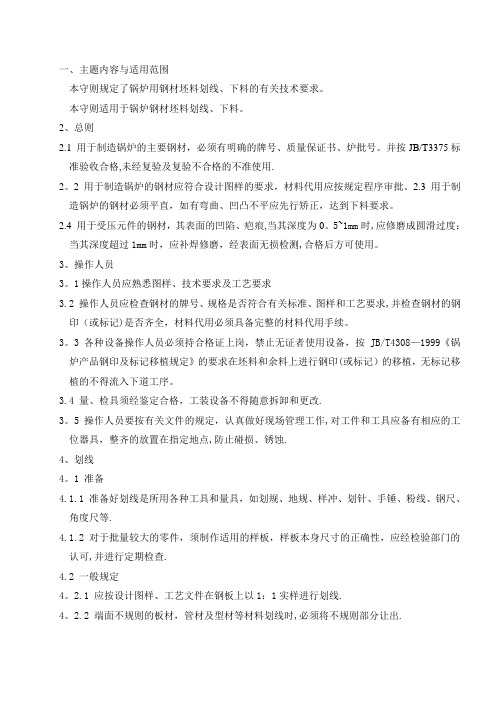
一、主题内容与适用范围本守则规定了锅炉用钢材坯料划线、下料的有关技术要求。
本守则适用于锅炉钢材坯料划线、下料。
2、总则2.1 用于制造锅炉的主要钢材,必须有明确的牌号、质量保证书、炉批号。
并按JB/T3375标准验收合格,未经复验及复验不合格的不准使用.2。
2 用于制造锅炉的钢材应符合设计图样的要求,材料代用应按规定程序审批。
2.3 用于制造锅炉的钢材必须平直,如有弯曲、凹凸不平应先行矫正,达到下料要求。
2.4 用于受压元件的钢材,其表面的凹陷、疤痕,当其深度为0。
5~1mm时,应修磨成圆滑过度;当其深度超过1mm时,应补焊修磨,经表面无损检测,合格后方可使用。
3、操作人员3。
1操作人员应熟悉图样、技术要求及工艺要求3.2 操作人员应检查钢材的牌号、规格是否符合有关标准、图样和工艺要求,并检查钢材的钢印(或标记)是否齐全,材料代用必须具备完整的材料代用手续。
3。
3 各种设备操作人员必须持合格证上岗,禁止无证者使用设备,按JB/T4308—1999《锅炉产品钢印及标记移植规定》的要求在坯料和余料上进行钢印(或标记)的移植,无标记移植的不得流入下道工序。
3.4 量、检具须经鉴定合格,工装设备不得随意拆卸和更改.3。
5 操作人员要按有关文件的规定,认真做好现场管理工作,对工件和工具应备有相应的工位器具,整齐的放置在指定地点,防止碰损、锈蚀.4、划线4。
1 准备4.1.1 准备好划线是所用各种工具和量具,如划规、地规、样冲、划针、手锤、粉线、钢尺、角度尺等.4.1.2 对于批量较大的零件,须制作适用的样板,样板本身尺寸的正确性,应经检验部门的认可,并进行定期检查.4.2 一般规定4。
2.1 应按设计图样、工艺文件在钢板上以1:1实样进行划线.4。
2.2 端面不规则的板材,管材及型材等材料划线时,必须将不规则部分让出.4.2.3 拼接并按有要求的零件下料应按有关标准及工艺进行。
4。
2.4 根据不同下料方法,划线时应留出适当的切割余量。
(完整版)下料工艺守则
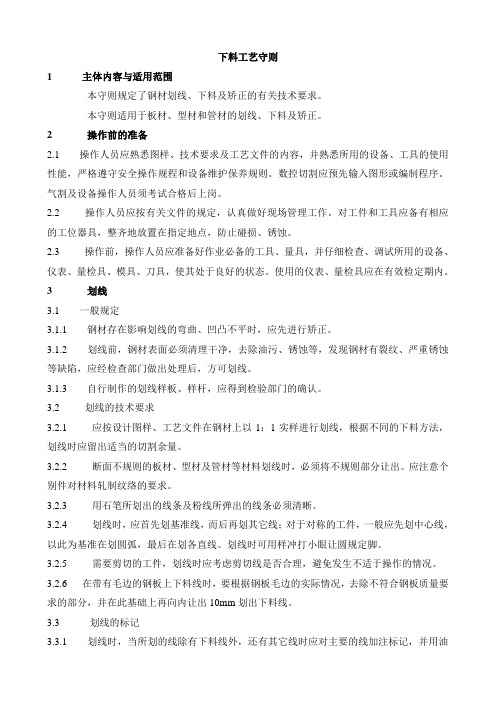
下料工艺守则1 主体内容与适用范围本守则规定了钢材划线、下料及矫正的有关技术要求。
本守则适用于板材、型材和管材的划线、下料及矫正。
2 操作前的准备2.1 操作人员应熟悉图样、技术要求及工艺文件的内容,并熟悉所用的设备、工具的使用性能,严格遵守安全操作规程和设备维护保养规则。
数控切割应预先输入图形或编制程序。
气割及设备操作人员须考试合格后上岗。
2.2 操作人员应按有关文件的规定,认真做好现场管理工作。
对工件和工具应备有相应的工位器具,整齐地放置在指定地点,防止碰损、锈蚀。
2.3 操作前,操作人员应准备好作业必备的工具、量具,并仔细检查、调试所用的设备、仪表、量检具、模具、刀具,使其处于良好的状态。
使用的仪表、量检具应在有效检定期内。
3 划线3.1 一般规定3.1.1 钢材存在影响划线的弯曲、凹凸不平时,应先进行矫正。
3.1.2 划线前,钢材表面必须清理干净,去除油污、锈蚀等,发现钢材有裂纹、严重锈蚀等缺陷,应经检查部门做出处理后,方可划线。
3.1.3 自行制作的划线样板、样杆,应得到检验部门的确认。
3.2 划线的技术要求3.2.1 应按设计图样、工艺文件在钢材上以1:1实样进行划线,根据不同的下料方法,划线时应留出适当的切割余量。
3.2.2 断面不规则的板材、型材及管材等材料划线时,必须将不规则部分让出。
应注意个别件对材料轧制纹络的要求。
3.2.3 用石笔所划出的线条及粉线所弹出的线条必须清晰。
3.2.4 划线时,应首先划基准线,而后再划其它线;对于对称的工件,一般应先划中心线,以此为基准在划圆弧,最后在划各直线。
划线时可用样冲打小眼让圆规定脚。
3.2.5 需要剪切的工件,划线时应考虑剪切线是否合理,避免发生不适于操作的情况。
3.2.6 在带有毛边的钢板上下料线时,要根据钢板毛边的实际情况,去除不符合钢板质量要求的部分,并在此基础上再向内让出10mm划出下料线。
3.3 划线的标记3.3.1 划线时,当所划的线除有下料线外,还有其它线时应对主要的线加注标记,并用油漆笔标出,以示区别。
1下料通用工艺守则(内容)

安徽四汇机械集团有限公司下料通用工艺守则编制:陆玲玲审核:游安军批准:梁永强2014-05-13发布2014-05-28实施1.总则1.1本守则适用于压力容器主要受压元件的下料,其他零部件下料可参照执行。
1.2下料人员必须严格执行产品图样和工艺文件的规定,当图样无特殊要求时,工艺人员在编制下料工艺文件时应遵照本守则的相应规定。
2基本要求2.1下料人员凭领料单办理领料手续。
2.2下料人员必须熟悉产品图样和工艺文件的要求。
2.3切割设备必须完好,现场有足够的下料场地,四周无有碍下料工作的堆积物。
计量器具能满足测量工作的基本要求,且在检定周期内。
2.4主要元件材料必须是经检验合格入库,且经监检确认的材料。
2.5材料上有清晰的出厂标记及入库检验标记,表面质量符合要求、牌号、规格必须与产品设计图样或工艺文件一致。
2.6筒体由若干个筒节拼焊而成时,筒节最小长度不得小于300mm。
2.7压力容器主要元件下料划线结束后应进行材质标记移植,并由专职检验人员进行检验确认,打上确认标记后方可切割下料。
2.8切割方法:碳素钢,低合金钢板材可选用剪板机或气割的方法;管材、棒材可以选用砂轮切割机。
2.9筒体下料尺寸的确定筒节展开长度,可按下式进行估算L=π(Di+δn)+2c式中:L:筒节展开长度Di:筒节内直径δn :壁厚C:边缘加工余量实际下料展开长度,还应以实际周长为准。
3.0划线3.1划线尺寸的依据是产品图样和工艺文件。
3.2划出工件毛坯尺寸线和切割线。
毛坯尺寸线和切割线之间的距离应保证工件切割后毛坯尺寸线不被破坏。
常用下料方法,毛坯尺寸线和切割线之间的距离可按表一推荐的数据选用。
表一mm材料厚度火焰切割等离子切割碳弧气刨剪板机手工自动、半自动手工自动、半自动手工≤10 3 2 9 6 8 010~30 4 3 11 8 10 032~50 5 4 14 10 14 052~65 6 4 16 12 18 03.3工件毛坯尺寸取工件展开尺寸和周边加工余量之和。
下料工艺守则
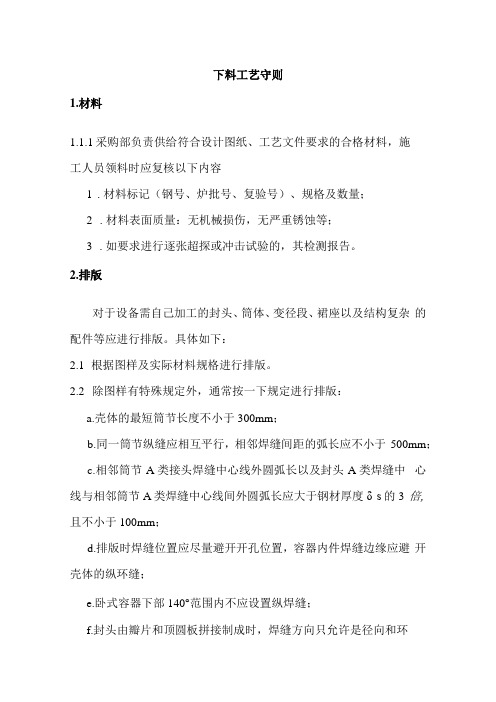
下料工艺守则1.材料1.1.1采购部负责供给符合设计图纸、工艺文件要求的合格材料,施工人员领料时应复核以下内容1.材料标记(钢号、炉批号、复验号)、规格及数量;2.材料表面质量:无机械损伤,无严重锈蚀等;3.如要求进行逐张超探或冲击试验的,其检测报告。
2.排版对于设备需自己加工的封头、筒体、变径段、裙座以及结构复杂的配件等应进行排版。
具体如下:2.1根据图样及实际材料规格进行排版。
2.2除图样有特殊规定外,通常按一下规定进行排版:a.壳体的最短筒节长度不小于300mm;b.同一筒节纵缝应相互平行,相邻焊缝间距的弧长应不小于500mm;c.相邻筒节A类接头焊缝中心线外圆弧长以及封头A类焊缝中心线与相邻筒节A类焊缝中心线间外圆弧长应大于钢材厚度δ s的3 倍,且不小于100mm;d.排版时焊缝位置应尽量避开开孔位置,容器内件焊缝边缘应避开壳体的纵环缝;e.卧式容器下部140°范围内不应设置纵焊缝;f.封头由瓣片和顶圆板拼接制成时,焊缝方向只允许是径向和环向的,封头各种不相交的拼缝中心线间距离至少应为钢材厚度δS的3倍,且不小于Ioomm,如图1-1:图ITh.球壳瓣片最小宽度不小于500mm;1.筒节展开周长按中径计算L= π (Di+δn) -∆L+HDi——圆筒的内直径;δn——钢板的名义厚度;——钢板的伸长量;H——焊缝收缩量。
J.材料切割前应先进行标记移植,移植时应有检验员的确认,确保标记移植的准确性。
k.排版图应包括:度数线、筒节中径展开长度、筒体总长、筒体件号、板规格、材质、筒节编号、筒节尺寸、焊缝编号、开孔编号、开孔中心标高及轴线的距离、收口缝位置、编制、审核、排版日期等内容。
1.排版前应考虑焊缝收缩余量。
m.对于分段出厂的设备,排版图上应标注分段处位置。
分段的基本原则:(I)根据设备的形状特征、结构,分段线应尽量避开内件焊缝、塔壁不等厚处及材质不相同处。
(2)根据运输条件、起重能力及工艺装备的允许尺寸或合同确定分段。
门窗下料技术工艺守则

8、合格的半成品,按窗型下料单,立即将其各段做标记,按类分别放制输送车或输送带上,送入下道工序。
9、切割的型材,表面不允许粘有毛刺、污物、损伤,以保证良好的焊接质量。
描图
描校资料来源编制(签)(日期)底图号
装订号
编制部门
标记
处数
更改文件号
签字
日期
企业名称
门窗
下料技术工艺守则
共页
第2页
1、按照生产通知单和工艺技术要求选用双角锯。
2、按照工艺要求和图纸中标示的型材长度尺寸,调节好定尺夹具。
3、锯料前必须检查锯床的运转情况,待锯运转平稳后方可下料。
4、锯料时进刀要平稳、缓慢、匀速。
5、在锯第一根型材后,由检验人员检验合格后,方可成批生产。
6、在夹料、卸料时必须精心操作,防止型材损伤。
1型材下料工序守则
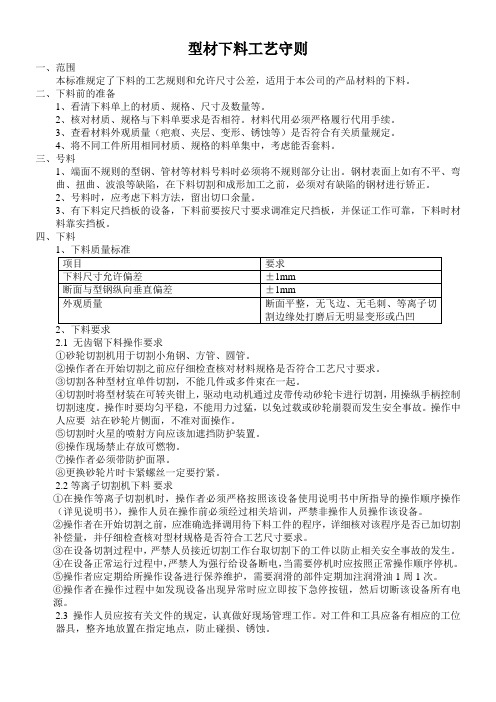
型材下料工艺守则一、范围本标准规定了下料的工艺规则和允许尺寸公差,适用于本公司的产品材料的下料。
二、下料前的准备1、看清下料单上的材质、规格、尺寸及数量等。
2、核对材质、规格与下料单要求是否相符。
材料代用必须严格履行代用手续。
3、查看材料外观质量(疤痕、夹层、变形、锈蚀等)是否符合有关质量规定。
4、将不同工件所用相同材质、规格的料单集中,考虑能否套料。
三、号料1、端面不规则的型钢、管材等材料号料时必须将不规则部分让出。
钢材表面上如有不平、弯曲、扭曲、波浪等缺陷,在下料切割和成形加工之前,必须对有缺陷的钢材进行矫正。
2、号料时,应考虑下料方法,留出切口余量。
3、有下料定尺挡板的设备,下料前要按尺寸要求调准定尺挡板,并保证工作可靠,下料时材料靠实挡板。
四、下料2.1 无齿锯下料操作要求①砂轮切割机用于切割小角钢、方管、圆管。
②操作者在开始切割之前应仔细检查核对材料规格是否符合工艺尺寸要求。
③切割各种型材宜单件切割,不能几件或多件束在一起。
④切割时将型材装在可转夹钳上,驱动电动机通过皮带传动砂轮卡进行切割,用操纵手柄控制切割速度。
操作时要均匀平稳,不能用力过猛,以免过载或砂轮崩裂而发生安全事故。
操作中人应要站在砂轮片侧面,不准对面操作。
⑤切割时火星的喷射方向应该加遮挡防护装置。
⑥操作现场禁止存放可燃物。
⑦操作者必须带防护面罩。
⑧更换砂轮片时卡紧螺丝一定要拧紧。
2.2等离子切割机下料要求①在操作等离子切割机时,操作者必须严格按照该设备使用说明书中所指导的操作顺序操作(详见说明书),操作人员在操作前必须经过相关培训,严禁非操作人员操作该设备。
②操作者在开始切割之前,应准确选择调用待下料工件的程序,详细核对该程序是否已加切割补偿量,并仔细检查核对型材规格是否符合工艺尺寸要求。
③在设备切割过程中,严禁人员接近切割工作台取切割下的工件以防止相关安全事故的发生。
④在设备正常运行过程中,严禁人为强行给设备断电,当需要停机时应按照正常操作顺序停机。
板料下料工艺守则模板

板料下料工艺守则Q/CD J3401-1适用范围本守则适用于我公司生产的各种开关柜、屏、箱的钢板的下料, 同时也适用于其它产品的板类材料的下料。
2使用设备和工具2.1剪板机2.2钢板尺2.3钢卷尺2.4直角尺2.5活搬手3工艺准备3.1熟悉图纸和下料清单, 查对生产任务单、工艺文件是否与其相符。
如有不符应找有关部门核对后方可工作。
3.2查对材料规格、型号及技术要求, 规格型号不符或质量低劣的材料不得使用。
3.3准备好所用的工量具。
3.4检查靠尺的垂直度和定位装置。
4工艺过程4.1根据材料厚度和设备性能选择剪板机, 按表1调节好刀口间隙。
表1剪板机刀片调整间隙( ㎜)4.2根据下料尺寸调整好定位。
4.3启动设备。
因启动负荷较大, 可点动, 直至机器转动稳定后再工作。
4.4用边角料试剪进行测量, 符合尺寸要求后再剪正式工件。
首剪件自检后交专检首检, 合格后方可批量生产。
首剪件必须有明显标记。
成批料加工时, 应经常抽检, 防止定位移动造成成批报废。
4.5剪料顺序先将不太整齐的一边剪去一刀( 落料尺寸不超过15㎜) , 然后根据几何形状剪切加工。
⑴剪正方形先剪a边, 再以a边为基准剪b、d边, 然后以b或d边为基准剪c边。
见图1。
⑵剪长方形先剪a、c两边( 必须用同一基准面剪切, 以保证a、c两边平行) , 然后以a或c作为基准剪b、d两边。
见图2。
图1 剪正方形图2 剪长方形4.6一种规格加工完毕后, 末件交检, 末件也必须有明显标记。
5工艺要求5.1各种零件的材料必须严格按工艺要求( 或图纸要求) 选用, 不得随意更改。
对代用材料必须由有关部门申请代用手续后方可使用。
5.2板面的平面度每米不大于1.5㎜, 否则应予校平。
5.3剪料尺寸公差参照表2、表3、图2、图3和图4规定:表2剪料尺寸公差( ㎜)表3用对角线测量法允许误差( ㎜)5.4 剪好的坯料应按不同零件进行堆放, 并根据图号进行编号, 转下工序。
板材、型材下料加工工艺守则

1.工艺准备1.1板材、型材下料加工必须选用合适的剪切和截料加工设备,操作者必须熟悉本机器的性能和遵守使用说明书的规定,并遵守设备使用的安全技术操作规程。
1.2操作者应认真看清图纸及工艺文件,了解技术要求,在加工过程中不得随意更改。
1.3按加工工艺要求,准备好所需的工具。
1.4操作者应对加工设备按规定定期润滑保持设备良好的润滑状态。
1.5工作前检查机器各部分是否正常,空转试行,看机器是否运行平稳,无异常杂音,方可正式工作。
1.6机器在工作期间,操作者不得擅离工作岗位,工作场地应保持清洁,工作坯料摆放整齐。
2.工艺要求2.1板材下料厚度和宽度不得超过机器的规定容许厚度和宽度。
使用2500剪切机,其规格为2500×6剪切最大宽度不超过2500毫米,最大厚度为6毫米。
2.2下料前的毛坯应该是经过校正的板材或型材,不允许剪切凹凸不平或带有凸缘,焊巴的毛胚件,以免损伤刀口。
2.3保持剪切设备的切刀平整、锋利、无缺陷,剪切后的工作要求平整、无毛刺、其不直角平行度、剪切误差应在规定范围内。
2.4对不同厚度、不同材料的板料,应根据实际情况,调整好设备切刀间隙,直至下料后毛刺、弯曲等现象。
并符合要求,才准生产。
2.5板机剪切不同厚度板料时,应调整刀片刀口间隙,间隙值的大小接下图选用。
54320.10 0.15 0.20 0.25 0.302.6间隙的调整:用手动点动,使上刀架至下死点,再将工作台紧固螺栓松开,根据确定的间隙值,用塞尺在刀口的全长上加以测量,在测量时用手动点动,使上刀架上下运动几次,用支拉螺栓调节切口之间隙达到要求为止,然后拧紧工作台的紧固螺栓,再进行一次间隙的复核,如无误,即可进行剪切下料。
根据剪切板的尺寸,调整档料装置。
2.7剪切板料的精度要求:直线度0.5‰,平行度0.3‰,剪切误差±0.5mm。
2.8剪材下料根据工艺卡片要求选用设备,对较大型材下料选用弓锯床,较小型材采切断机。
钢板预处理工艺规程

xx大桥拓宽工程钢结构钢板预处理工艺规程
编制:
校对:
审核:
目录
1.表面预处理包括如下工序 (1)
2.预处理工艺流程 (1)
3.施工要求 (1)
4.质量要求 (1)
xx 大桥拓宽工程钢结构钢板预处理工艺规程
1
本工程所有板材及型钢在下料前都应进行钢板校平、表面清洁、抛丸除锈、喷涂车间底漆的工序;对于不能直接在自动预处理线上进行处理的特殊型材,需要进行手工喷砂除锈、喷涂车间底漆的工序。
1.表面预处理包括如下工序
(1)钢板校平处理。
(2)表面清理:清除油污及其它污染物。
(3)预处理线使用的抛丸磨料为钢丸,其规格为S280;钢板在预处理线上走行速度为2.0~3.5m/min 。
(4)抛丸/喷砂除锈:清洁度Sa2.5级,粗糙度Rz40~75μm 。
(5)喷涂车间底漆:喷涂醇溶性无机硅酸锌车间底漆1道,干漆膜厚度为20~30μm 。
2.预处理工艺流程
3.施工要求
(1)施工条件:喷漆时钢材应清洁干燥,温度宜在5~38℃之间,相对湿度低于80%(含80%),钢材表面温度必须高于露点3℃,以免水汽凝结。
(2)抛丸或喷砂除锈前先用有机溶剂清除钢板表面油污,并清除其它污染物。
(3)钢板表面预处理施工须在预处理生产线上进行。
4.质量要求
(1)外观质量:漆膜均匀平整,无漏涂、脱落、裂纹、流挂等缺陷。
(2)厚度要求:涂层干膜厚度达到20~30μm 。
角钢下料工艺守则

角钢下料工艺守则1. 适用范围本工艺守则适用于角钢的下料。
2. 设备及工具a)根据角钢规格使用的冲床及工装;b)角钢校直机;c)V型切断模具;d)活动搬手、钢板尺、划针、宽座角尺、钢卷尺、手锤。
3. 准备工作3.1按分配的任务熟悉图纸和有关工艺文件,弄懂图纸和工艺文件规定另件几何形状,各部分尺寸。
3.2不同规格的角钢应分别放置,整齐堆放、防止堆放变形。
3.3根据施工批量进行套裁,先下长料,后下短料,充分提高材料利用率。
3.4所用角钢材料1米内直线度超过5毫米时,均需经过校直,方可下料。
4.工艺过程4.1根据零件图纸尺寸或下料明细的展开尺寸调下模具定位装置,角钢端头紧靠定位板,先冲试样,进行首件检查尺寸偏差是否在规定范围,如符合图纸或本守则公差,才能正式加工,若不符合图纸尺寸,应调正定位板,必要时可调正模具。
4.2角钢下料加工时应将原料角钢首端和末端变形部份切除。
4.3需要进行冲孔、切角等延序的在制品件应分别堆放,便于搬运,防止混料。
4.4加工完的角钢在制品或半成品件,应分清规格、型号经检查合格后转下道工序或半成品库。
5.工艺要求1.1下料长度允许偏差见下表单位: mm5.2切角斜度 mm注:不等边角钢以长边尺寸为准。
6.质量检查:在操作中应经常检查工件是否合格,成批的零件,每加工30~40件检查一次,如发现不合格,立即停止施工,进行调整。
7.技术安全及注意事项7.1班前要检查机床是否正常,空运转2~3分钟,加注润滑油,保持设备技术性能良好。
7.2操作过程中要经常检查下料冲模是否松动,若发现松动、错位应立即停车校正,经常检查定位器是否移动,发现移动应立即校正。
7.3调节模具的闭合高度,校正冲模或调整定位器时应先切断电源。
7.4搞好车间文明生产,搬动长角钢件时应注意安全,防止人身设备事故。
剪板机下料工艺守则1. 适用范围1.1本守则适用于各种黑色金属的直线边缘的材料毛坯的剪切及其他类似的下料。
1.2被剪切的材料厚基本尺寸为0.5~6毫米,最大宽度为2500毫米。
下料工艺守则

下料工艺守则德信诚培训网下料工艺守则1 范围本标准规定了下料应遵守的基本规则,适用于各企业的下料。
下料还应遵守JB/T 9168.1的规定。
2 引用标准下列标准所包含的条文,通过在本标准中引用而构成为本标准的条文。
本标准出版时,所示版本均为有效。
所有标准都会被修订,使用本标准的各方应探讨使用下列标准最新版本的可能性。
JB/T 9168.1-1998 切削加工通用工艺守则总则 3 下料前的准备3.1 看清下料单上的材质、规格、尺寸及数量等。
3.2 核对材料、规格与下料单要求是否相符。
材料代用必须严格履行代用手续。
3.3 查看材料外观质量(疤痕、夹层、变形、锈蚀等)是否符合有关质量规定。
3.4 将不同工件所用相同材质、规格的料单集中,考虑能否套料。
3.5 号料3.5.1 端面不规则的型钢、钢板、管材等材料号料时,必须讲不规则部分让出。
3.5.2 号料时应考虑下料方法,留出切口余量。
3.6 有下料定尺挡板的设备,下料前要按尺寸要求调准定尺挡板,并保证工作可靠,下料时材料一定靠实挡板。
好好学习社区德信诚培训网4 下料 4.1 剪切下料4.1.1 钢板、扁钢下料时,应优先使用剪切下料。
4.1.2 用剪床下料时剪刃必须锋利,并应根据下料板后调整好剪刃间隙,其值参见附录A。
4.1.3 剪切最后剩下的料头必须保证剪床的压料板能压牢。
4.1.4 下料时应先将不规则的端头切掉。
4.1.5 切口断面不得有撕裂、裂纹、棱边。
4.2 气割下料4.2.1 气割前应根据被切割板材厚度换好切割嘴 [ 参见附录B] ,调整好表压,点火试验合格后方可切割。
4.2.2 气割下料时,毛坯每边应留适当加工余量,手工气割下料毛坯加工余量参见附录C。
4.2.3 气割下料后,应将气割边的挂渣、氧化物等打磨干净。
4.3 锯削下料4.3.1 用锯削下料时,应根据材料的牌号和规格选好锯条或锯片。
4.3.2 锯削下料时工艺留量应适当,常用各种型材的锯削下料工艺留量参见附录D。
下料通用工艺守则最新
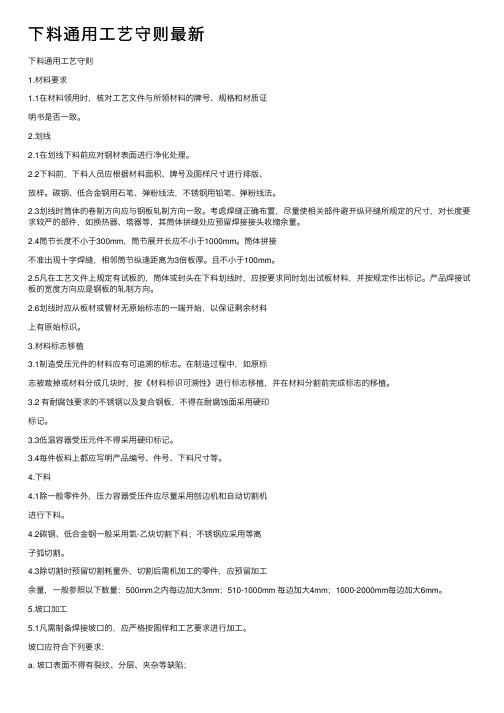
下料通⽤⼯艺守则最新下料通⽤⼯艺守则1.材料要求1.1在材料领⽤时,核对⼯艺⽂件与所领材料的牌号、规格和材质证明书是否⼀致。
2.划线2.1在划线下料前应对钢材表⾯进⾏净化处理。
2.2下料前,下料⼈员应根据材料⾯积、牌号及图样尺⼨进⾏排版、放样。
碳钢、低合⾦钢⽤⽯笔、弹粉线法,不锈钢⽤铅笔、弹粉线法。
2.3划线时筒体的卷制⽅向应与钢板轧制⽅向⼀致。
考虑焊缝正确布置,尽量使相关部件避开纵环缝所规定的尺⼨,对长度要求较严的部件,如换热器、塔器等,其筒体拼缝处应预留焊接接头收缩余量。
2.4筒节长度不⼩于300mm,筒节展开长应不⼩于1000mm。
筒体拼接不准出现⼗字焊缝,相邻筒节纵逢距离为3倍板厚。
且不⼩于100mm。
2.5凡在⼯艺⽂件上规定有试板的,筒体或封头在下料划线时,应按要求同时划出试板材料,并按规定作出标记。
产品焊接试板的宽度⽅向应是钢板的轧制⽅向。
2.6划线时应从板材或管材⽆原始标志的⼀端开始,以保证剩余材料上有原始标识。
3.材料标志移植3.1制造受压元件的材料应有可追溯的标志。
在制造过程中,如原标志被裁掉或材料分成⼏块时,按《材料标识可溯性》进⾏标志移植,并在材料分割前完成标志的移植。
3.2 有耐腐蚀要求的不锈钢以及复合钢板,不得在耐腐蚀⾯采⽤硬印标记。
3.3低温容器受压元件不得采⽤硬印标记。
3.4每件板料上都应写明产品编号、件号、下料尺⼨等。
4.下料4.1除⼀般零件外,压⼒容器受压件应尽量采⽤刨边机和⾃动切割机进⾏下料。
4.2碳钢、低合⾦钢⼀般采⽤氧-⼄炔切割下料;不锈钢应采⽤等离⼦弧切割。
4.3除切割时预留切割耗量外,切割后需机加⼯的零件,应预留加⼯余量,⼀般参照以下数量:500mm之内每边加⼤3mm;510-1000mm 每边加⼤4mm;1000-2000mm每边加⼤6mm。
5.坡⼝加⼯5.1凡需制备焊接坡⼝的,应严格按图样和⼯艺要求进⾏加⼯。
坡⼝应符合下列要求:a. 坡⼝表⾯不得有裂纹、分层、夹杂等缺陷;b. 标准抗拉强度下限值R m≥540MPa的低合⾦钢材及Cr-Mo低合⾦钢材经热切割的坡⼝表⾯,加⼯完成后应按JB/T4730.4进⾏磁粉检测,I级合格;c. 施焊前,应清除坡⼝及两侧材表⾯⾄少20mm范围内(以离坡⼝边缘的距离计)的氧化⽪、油污、溶渣及其他有害杂质。
木工作业中的材料预处理与拼接要求
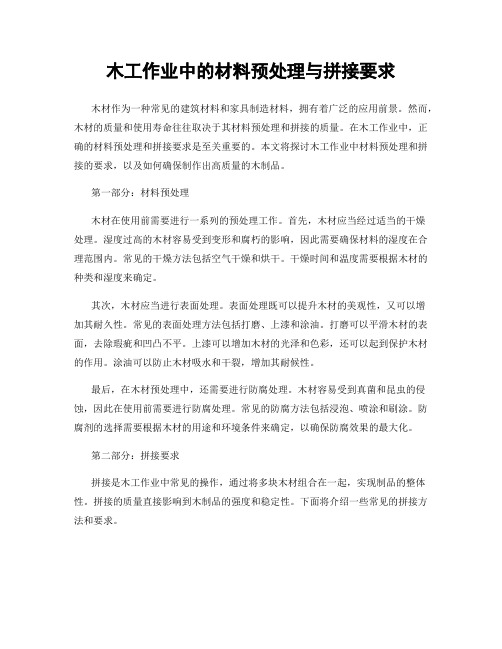
木工作业中的材料预处理与拼接要求木材作为一种常见的建筑材料和家具制造材料,拥有着广泛的应用前景。
然而,木材的质量和使用寿命往往取决于其材料预处理和拼接的质量。
在木工作业中,正确的材料预处理和拼接要求是至关重要的。
本文将探讨木工作业中材料预处理和拼接的要求,以及如何确保制作出高质量的木制品。
第一部分:材料预处理木材在使用前需要进行一系列的预处理工作。
首先,木材应当经过适当的干燥处理。
湿度过高的木材容易受到变形和腐朽的影响,因此需要确保材料的湿度在合理范围内。
常见的干燥方法包括空气干燥和烘干。
干燥时间和温度需要根据木材的种类和湿度来确定。
其次,木材应当进行表面处理。
表面处理既可以提升木材的美观性,又可以增加其耐久性。
常见的表面处理方法包括打磨、上漆和涂油。
打磨可以平滑木材的表面,去除瑕疵和凹凸不平。
上漆可以增加木材的光泽和色彩,还可以起到保护木材的作用。
涂油可以防止木材吸水和干裂,增加其耐候性。
最后,在木材预处理中,还需要进行防腐处理。
木材容易受到真菌和昆虫的侵蚀,因此在使用前需要进行防腐处理。
常见的防腐方法包括浸泡、喷涂和刷涂。
防腐剂的选择需要根据木材的用途和环境条件来确定,以确保防腐效果的最大化。
第二部分:拼接要求拼接是木工作业中常见的操作,通过将多块木材组合在一起,实现制品的整体性。
拼接的质量直接影响到木制品的强度和稳定性。
下面将介绍一些常见的拼接方法和要求。
首先,常见的拼接方法包括榫卯接、榫头接、卯榫接、卡榫接等。
不同的拼接方法在使用时需要注意的要点不同,但有一个共同点就是确保拼接面的贴合度。
拼接面应当平整、无毛刺,并且紧密贴合,以确保拼接的强度。
其次,要求拼接的木材之间应当具有较好的协调性。
无论是颜色、纹理还是细微的尺寸差异,都应当尽量减少,以确保拼接后的制品整体看起来自然而流畅。
在材料选择时,可以选择具有颜色相近或相容的木材,或者使用染色剂进行染色处理,以达到更好的协调效果。
最后,拼接要求还包括拼接面的质量和胶水的选择。
[资料]钢板下料工艺守则
![[资料]钢板下料工艺守则](https://img.taocdn.com/s3/m/1b806736dc36a32d7375a417866fb84ae45cc306.png)
钢板下料工艺守则本标准规定了下料应遵守的基本原则,适用于我厂结构件加工材料和切削加工所用材料的下料。
1.下料前的准备:1.1接到下料定单后,首先要检查所需的产品图样,工艺规程和有关技术资料是否齐全.1.2要看懂、看清工艺规程、产品图样及其技术要求。
1. 3看清下料工艺过程卡片的材质、规格、尺寸及数量等,发现问题应找有关技术人员及时解决。
1. 4核对材质、规格与下料工艺过程卡片上的要求是否相符,材料代用必须严格履行代用手续。
1. 5查看材料外观质量(疤痕、夹层、变形、锈蚀等)是否符合有关质量规定.1. 6号料1.6.1相同材质、相同规格、相同下料方法的工件为了充分利用材料,应考虑集中排料号料.1.6.2端面不规则的型钢、钢板、管材等材料号料时,必须将不规则的部位让出.1.6.3号料时,应将样板贴实在材料上,划线时不得移动.1.6.4号线时应清晰,必要时作上标记.1.6.5根据下料方法,号料时留出切口余量.1.6.6在所号的材料上分别注明零件的图号,1.6.7号料完毕,样板应妥善保管,以备再用.2.下料:2.1剪切下料:2.1.1检查号线是否清晰、正确,发现问题应及时找有关人员解决.2.1.2剪切下料时,剪床的剪刀必须锋利,并根据剪切厚度调整好剪刀间隙,其值参见附录A.2.1.3根据下料尺寸要求,调准定尺挡板,并保证工作可靠,剪切时材料一定靠实挡板.2.1.4按号线剪切,剪切时剪刃必须对准号线.2.1.5剪切时应先将不规则的料边剪掉.2.1.6切口断面不得有撕裂、裂纹、棱边.2.1.7剪切最后剩下的料头,必须保证剪床的压料板能压牢,否则必须加辅助压料板.附录A剪切钢板时剪刃间隙与板厚的关系2.2气割下料:2.2.1检查号线是否正确、清晰.数控切割机应复核切割图样和数控程序是否正确,发现问题应及时找有关人员解决.2.2.2检查仿形切割靠模板是否正确,对变形的靠模板应修复后再用.2.2.3气割前应根据被切割板材厚度换好切割嘴(参见附录A)2.2.4气割型材时应根据具体情况选用切割嘴.2.2.5气割前应调整好表压,点火试验合格后方可切割.2.2.6机动气割时,应不间断地使用冷却水.2.2.7气割过程中,应注意观察切割情况,发现异常情况,应立即停止切割.2.2.8气割下料后,应清渣、除去氧化皮、必要时采用工具打磨干净.附录A气割下料时割嘴规格号的选择2.3锯削下料:2.3.1锯削下料时,应根据材料的牌号和规格选用锯条或锯片.2.3.2根据下料尺寸要求调准定尺挡杆,并保证工作可靠,锯削时材料一定靠实挡杆.2.3.3锯削时应先将不规则的料头锯掉.2.3.4锯床的夹料装置应能可靠地夹紧材料,在锯削过程中不得有松动现象.2.3.5装夹后的材料应与锯床的工作台面相平行.2.3.6在锯削过程中应不间断地使用冷却液.2.3.7锯切最后剩下的料头必须保证锯床的夹料装置能夹牢.。
- 1、下载文档前请自行甄别文档内容的完整性,平台不提供额外的编辑、内容补充、找答案等附加服务。
- 2、"仅部分预览"的文档,不可在线预览部分如存在完整性等问题,可反馈申请退款(可完整预览的文档不适用该条件!)。
- 3、如文档侵犯您的权益,请联系客服反馈,我们会尽快为您处理(人工客服工作时间:9:00-18:30)。
钢材表面预处理、下料工艺守则
1 适用范围
本标准适用于焊接结构产品所用钢材的表面预处理,下料工艺。
本标准未规定的要求,应符合有关标准或专业技术要求。
本标准属通用工艺,若与产品图纸要求不一致时,应以产品图纸为准。
2 钢材的技术要求
焊接结构件钢材的牌号、规格、尺寸、质量指标和订货要求,应符合图样和相关技术标准的规定,
采购的钢材应有制造商合格证明书,无合格证书或证明不全的都必须补做检验,合格后才能入库和使用,代用钢材应有签署完整的代用单。
采用新品种钢材,必须先做试验,性能合格才能入库和使用。
钢材上有较严重的锈蚀、麻坑时不得用于重要承载构件和影响外观的结构件。
3 钢材的表面预处理 预处理的依据:
3.1.1按合同和技术协议要求。
3.1.2按产品工作环境要求。
(沿海、出口、有化学腐蚀气体的环境等)。
预处理的范围:规定预处理的产品,其结构件的板材和型材全部进行预处理。
钢材表面的锈蚀等级和除锈等级除按下面文字叙述外,必要时可按《GB8923-88涂装前钢材表面锈
蚀等级和除锈等级》中的照片对比判定。
钢材表面的四个锈蚀等级分别以A 、B 、C 、D 表示。
A 全面地复盖着氧化皮而几乎没有铁锈的钢材表面。
B 已发生锈蚀,并且部分氧化皮已经剥落的钢材表面。
C 氧化皮已因锈蚀而剥落,或者已刮除,并且有少量点蚀的钢材表面。
D 氧化皮已因锈蚀而全面剥离,并且已普遍发生点蚀的钢材表面。
钢材表面的除锈等级以代表所采用的除锈方法的字母“Sa ”、“St ”、或“FI ”表示,字母后阿拉伯数字表
示清除氧化皮、铁锈和油漆层等附着物的程度等级。
3. 6 喷射或抛射除锈 代号:Sa,分为四个等级。
(注:喷射是指喷砂或喷丸,抛射是指抛砂或抛丸) Sa1级 轻度的喷射或抛射除锈。
钢材表面无可见的油脂和污垢,并且氧化皮、铁锈和油漆层等附着物已基本清除。
其残留物应
是牢固附着的。
Sa2
2
1
级非常彻底的喷射或抛射除锈。
钢材表面无可见的油脂、污垢、氧化皮、铁锈和油漆层等附着物,任何残留的痕迹应仅是点状
或条纹状的轻微斑。
Sa3级 洁净的喷射或抛射除锈。
钢材表面无可见的油脂、污垢、氧化皮、铁锈和油漆层等附着物,该表面应显示均匀的金属光
泽。
手工和动力工具除锈 代号:St 分为二个等级 St2级 彻底的手工和动力工具除锈。
钢材表面无可见的油脂和污垢,并且没有附着不牢的氧化皮、铁锈和油漆层等附着物。
St3级 非常彻底的手工和动力工具除锈。
钢材表面无可见的油脂和污垢,并且没有附着不牢的氧化皮、铁锈和油漆层等附着物,除锈应
比St2级更为彻底,底材显露部分的表面应具有金属光泽。
火焰除锈 代号:FI 一个等级。
钢材表面无氧化皮、铁锈和油漆层等附着物,任何残留的痕迹应仅为表面变色。
结构件用钢材在焊接前应优先采用表面预处理,重要构件的表面预处理后应达到Sa2
2
1
级(抛丸和喷丸),其余构件应达到Sa2级或St2级(手工除锈)特殊情况下对结构件施焊后再进行表面处理。
喷射或抛射除锈后的钢材或部件,应立即喷底漆或采取防护措施,防止由各种因素而引起生锈, 对已生锈的表面,应重新进行喷射或抛射除锈。
钢板表面除锈并涂防锈底漆后,材料牌号(含质量等级)应移植(用油笔写字)到材料的端部适当位置。
4 钢材的矫正
各种钢材在下料前翘曲的形状偏差,超过下列数值时应进行矫正。
a)钢板用1米平尺检查翘曲时,超过允许偏差2毫米时;
b)型钢用1米平尺检查局部平面度,其偏差大于1毫米时;
c)零件下料后,翘曲不平超过设计图纸要求时。
钢材矫正可用机械矫正、手工矫正、火焰矫正。
手工矫正钢板时应加垫板,其锤痕深度不大于0.5mm。
火焰矫正温度应控制在大约550~900°C之间,(暗褐色至樱红色),防止加热到900~1200°C的过热温度(桔红和黄色)
5 钢材的弯曲
钢板与型钢需要成型弯曲时,如果符合下述条件则可冷弯。
钢板:R25δ(非重要构件可为R≥10δ)
R为弯曲半径δ为钢板厚度
型钢:R≥25H(B)(随弯曲方向而定)
型钢的截面尺寸如下图
钢板与型钢不符合冷弯条件时则应用热弯,热弯时温度为900~1100°C,弯曲完成时的温度不得低于700°C
6 钢材的下料
号料结构件的放样、号料和样板制作,应考虑结构中的装配间隙、焊接收缩量、割口宽度和加工余量等因素,其样板应经过检查合格后才投入使用。
起重机主梁、端梁、门腿的腹板、盖板等大型零件,应先对接,后划线,号料,对于先号料后拼接的零件,号料后应提供对接图。
主梁的拼接参照《主梁作业指导书》。
重要件用板材的划线和号料应使轧制方向与所受的最大应力方向一致。
号料完毕的零件应用快干漆注明产品的代号,剩余的材料应注明材质。
(尤其特殊材料和厚度较大的板材)。
一般下料偏差的规定
. 使用说明
a)内部筋板等被包容零件同一组、腹板同一组对应点尺寸相差均不大于4mm。
b)本规定不包括焊接工艺余量。
剪切下料偏差单位:mm
自动气割下料偏差单位:mm
半自动、手工气割下料偏差单位:mm
对于板钩内口尺寸,切割后的尺寸应比图示小于3毫米左右。
(弥补与内衬板的贴合间隙)
套料切割时,应注意零件的变形,切割顺序应按先窄边、后宽边的原则,特别易变形的零件,要编制专用工艺。
套料切割时,应注意提高材料利用率,切割零件之间的套料间距可参考下表
套料间距尺寸表mm
下料后需要加工外露的过渡坡口,可用半自动气割割出,坡度按图纸要求,图纸未注明的坡度按1:4 坡口宽度差应小于3毫米。
坡口面上有~毫米沟槽时应修光,大于毫米时应焊补修光。
重要件焊接坡口也要用半自动气割割出,尺寸按《桥、门式起重机用焊接工艺规程》的有关规定执行。
各种气割的规范,应根据工件的厚度和设备特点,选用不同的割嘴、氧气压力,具体数据参考下表
气-气炔射吸式割炬及割嘴规格和性能
气割下料后应把割渣、飞边等清理干净,成品件外露割口面上有~毫米沟槽时应修光,大于毫米时应焊补修光。
气割下料时,钢材的下平面与地面或另一工件平面应有100毫米左右的空位。
下料的首件产品必须经过检查,合格后才能批量生产,尤其是重要零件和数控切割的零件。
下料时,应严格按照所用设备的操作规程认真操作,确保安全和质量。