CSP轧机工作辊剥落原因及改进措施
热轧轧辊剥落或断裂的原因及预防方法探究

热轧轧辊剥落或断裂的原因及预防方法探究热轧轧辊在钢铁生产中起着至关重要的作用,是完成金属板材加工的重要设备之一。
在使用过程中,热轧轧辊剥落或断裂的现象时有发生,给生产带来了严重的影响。
针对这一问题,本文将从热轧轧辊剥落或断裂的原因及预防方法进行探究,以期为相关企业提供参考。
一、热轧轧辊剥落或断裂的原因1. 设备质量不达标热轧轧辊作为重要的设备之一,其质量必须达到相应的标准。
如果生产厂家在生产过程中使用了劣质的材料或者工艺不合格,就会导致轧辊的质量不达标,容易出现剥落或断裂的现象。
2. 设备磨损严重长时间的使用会造成轧辊表面的磨损,特别是在高温、高压力的环境下,磨损会更加严重。
一旦轧辊表面磨损过度,就会影响其正常的工作状态,进而产生剥落或断裂的风险。
3. 工艺参数设置不当热轧轧辊在使用过程中,需要根据所加工金属的性质和厚度等因素设置相应的工艺参数,如温度、压力等。
如果工艺参数设置不当,就会导致轧辊在工作过程中承受过大的压力或温度,从而容易出现剥落或断裂的情况。
4. 操作不当操作人员在使用热轧轧辊的过程中,如果操作不当,容易对设备造成损坏。
比如在装卸轧辊时使用不当的工具或方法,会导致轧辊受力不均,从而产生损坏的可能性。
5. 周期性检修不足热轧轧辊作为重要设备,需要定期进行检修和维护工作。
如果企业在这方面投入不足,就会导致轧辊出现各种问题,包括剥落或断裂现象。
二、预防方法探究1. 选购正规厂家生产的轧辊企业在选购热轧轧辊时,应该选择质量可靠的正规厂家生产的产品,避免使用劣质轧辊。
2. 定期维护检修企业应该对热轧轧辊进行定期的维护检修工作,包括表面磨损的修复、工艺参数的调整和润滑等工作,以确保轧辊处于最佳的工作状态。
3. 合理设置工艺参数在使用热轧轧辊时,企业应该合理设置工艺参数,根据加工的金属材料性质和厚度等因素进行调整,避免出现过大的压力或温度对轧辊造成损坏。
4. 加强操作培训企业应该加强对操作人员的培训,提高其对热轧轧辊设备的操作技能和安全意识,避免因为操作不当对轧辊造成损坏。
热轧轧辊剥落或断裂的原因及预防方法探究

热轧轧辊剥落或断裂的原因及预防方法探究热轧轧辊作为热轧设备中重要的组成部分,其质量直接影响到产品质量和生产效率。
在生产中,往往会出现轧辊剥落或断裂的情况,造成了生产效率低下和安全隐患,因此研究热轧轧辊剥落或断裂的原因及预防方法具有重要的实际意义。
1. 轧辊表面损伤导致轧辊剥落或断裂在轧辊使用过程中,出现轧辊表面损伤容易导致轧辊剥落或断裂。
这种损伤包括表面裂纹、划痕、磨损、腐蚀等,这些损伤会进一步扩大,最终导致轧辊剥落或断裂。
轧辊材质好坏直接影响到轧辊的使用寿命和质量。
如果轧辊的材质不够坚固耐用,那么在热轧过程中会出现轧辊变形、疲劳、裂纹等问题,将极大影响热轧产品质量。
热轧设备的操作不规范也容易导致轧辊剥落或断裂。
例如温度控制不当、轧辊调整不到位等等,都会在热轧过程中产生不同程度的影响,最终导致轧辊剥落或断裂。
热轧工艺参数是热轧过程中必须严格控制的参数,如果热轧工艺参数不合适将会直接影响到轧辊的寿命和使用效果。
例如,轧制过程中的拉伸率、轧制力、速度等参数不合适,都将导致轧辊剥落或断裂。
1. 轧辊材质的优化优化轧辊材质可以提高轧辊的抗拉、抗压、抗疲劳等性能。
特别是在硬度和韧性之间的平衡上,选择合适的轧辊材料可大大提高轧辊的使用寿命。
2. 加强对轧辊的检测热轧轧辊在使用过程中应每隔一些周期对轧辊进行检测,及时发现轧辊损伤和裂纹等问题并进行处理,避免因轧辊的损坏而影响到生产和产品质量。
3. 热轧设备的维护针对热轧设备操作不规范等问题,应加强设备维护,保持轧辊的良好状态。
定期做好轧辊的维护与更新,及时清理轧辊附着的物质,避免附着物进一步侵蚀轧辊表面。
4. 控制热轧工艺参数对于热轧工艺参数不合适问题,应严格控制热轧温度、轧制力、速度等参数。
调整工艺参数能够有效避免轧辊的剥落或断裂。
总之,对于热轧轧辊剥落或断裂问题,合理地选择轧辊材质,加强轧辊的检测和维护,规范热轧设备操作,严格控制热轧工艺参数,是预防轧辊剥落或断裂的有效方法。
热轧轧辊剥落或断裂的原因及预防方法探究
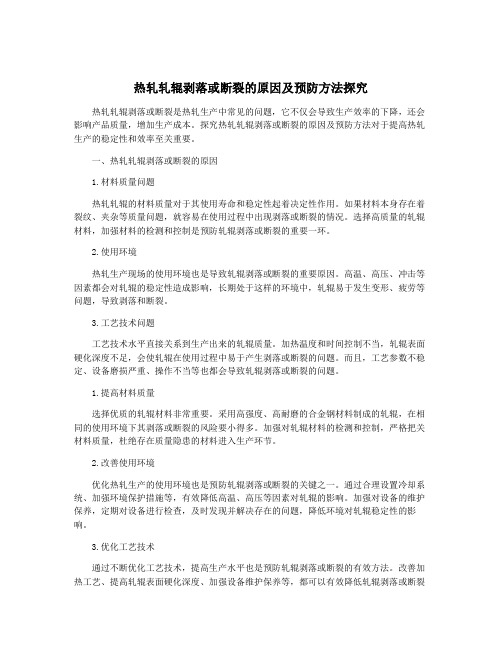
热轧轧辊剥落或断裂的原因及预防方法探究热轧轧辊剥落或断裂是热轧生产中常见的问题,它不仅会导致生产效率的下降,还会影响产品质量,增加生产成本。
探究热轧轧辊剥落或断裂的原因及预防方法对于提高热轧生产的稳定性和效率至关重要。
一、热轧轧辊剥落或断裂的原因1.材料质量问题热轧轧辊的材料质量对于其使用寿命和稳定性起着决定性作用。
如果材料本身存在着裂纹、夹杂等质量问题,就容易在使用过程中出现剥落或断裂的情况。
选择高质量的轧辊材料,加强材料的检测和控制是预防轧辊剥落或断裂的重要一环。
2.使用环境热轧生产现场的使用环境也是导致轧辊剥落或断裂的重要原因。
高温、高压、冲击等因素都会对轧辊的稳定性造成影响,长期处于这样的环境中,轧辊易于发生变形、疲劳等问题,导致剥落和断裂。
3.工艺技术问题工艺技术水平直接关系到生产出来的轧辊质量。
加热温度和时间控制不当,轧辊表面硬化深度不足,会使轧辊在使用过程中易于产生剥落或断裂的问题。
而且,工艺参数不稳定、设备磨损严重、操作不当等也都会导致轧辊剥落或断裂的问题。
1.提高材料质量选择优质的轧辊材料非常重要。
采用高强度、高耐磨的合金钢材料制成的轧辊,在相同的使用环境下其剥落或断裂的风险要小得多。
加强对轧辊材料的检测和控制,严格把关材料质量,杜绝存在质量隐患的材料进入生产环节。
2.改善使用环境优化热轧生产的使用环境也是预防轧辊剥落或断裂的关键之一。
通过合理设置冷却系统、加强环境保护措施等,有效降低高温、高压等因素对轧辊的影响。
加强对设备的维护保养,定期对设备进行检查,及时发现并解决存在的问题,降低环境对轧辊稳定性的影响。
3.优化工艺技术通过不断优化工艺技术,提高生产水平也是预防轧辊剥落或断裂的有效方法。
改善加热工艺、提高轧辊表面硬化深度、加强设备维护保养等,都可以有效降低轧辊剥落或断裂的风险。
培训操作人员,提高其技术水平,增强操作规范性,也是有效预防轧辊剥落或断裂的方法之一。
4.加强监控和管理加强对生产过程的监控和管理,及时发现并处理存在的问题也是预防轧辊剥落或断裂的关键。
关于辊皮剥落的原因分析

关于辊皮剥落的原因分析辊皮剥落是一个常见的问题,尤其是在金属制造和加工行业中。
其主要原因是材料的疲劳、制造和使用过程中的缺陷以及环境因素的作用。
下面将详细介绍这些原因。
首先,辊皮剥落的一个主要原因是材料的疲劳。
辊皮经受着重复的负荷和应力,长期以来会导致材料的疲劳。
当疲劳达到临界点时,材料就会出现疲劳裂纹,进而导致剥落。
其次,制造和使用过程中的缺陷也会导致辊皮剥落。
当制造过程中存在缺陷,如结构设计不合理、焊接不牢固、材料质量不过关等,都会导致辊皮的剥落。
在使用过程中,辊皮可能会因为磨损、冲击和振动等原因出现故障,从而引起剥落现象。
第三,环境因素也是导致辊皮剥落的重要原因之一、高温和腐蚀性气体是导致辊皮剥落的主要环境因素。
高温会导致辊皮热胀冷缩,从而导致裂纹和剥离。
腐蚀性气体可以腐蚀辊皮的金属材料,降低其强度和粘结力,导致剥离。
为了避免辊皮剥落,可以采取以下措施。
首先,需要加强材料的质量控制,确保辊皮的材料符合相关标准和要求。
制造过程中要严格按照工艺规程进行操作,避免因为制造缺陷导致辊皮剥落。
其次,应该对辊皮进行定期检测和维护。
定期进行超声波或磁粉探伤,查找潜在的裂纹和缺陷,并及时修复和加固。
此外,定期清洗和涂保护涂层,防止腐蚀。
此外,要控制辊皮的工作温度和应力,避免超过其负荷承受能力。
如果工作温度较高,可以采取冷却措施,如水冷或风冷等,降低辊皮的温度。
对于应力过大的情况,可以通过修改结构设计或增加支撑等方式进行调整和优化。
此外,定期进行辊皮的平衡检验,避免因为不平衡而导致辊皮振动和冲击,从而引起剥离。
总之,辊皮剥落是一个常见且影响生产安全和效率的问题。
对于辊皮剥落的原因进行分析,并采取相应的措施进行预防和修复,可以有效地提高生产效率和设备的使用寿命。
CSP轧机工作辊剥落原因初探

4 剥落原 因分析
轧辊剥落的类型有两种 , 一种是辊身剥 落, 另一种是辊边剥落 。辊身剥 落一般来说 起因于表面裂纹 的扩散 , 辊边剥 落一般是支 撑辊倒角和工作辊开压边部内浇 口所致。
4 1 轧 辊本 身 的分析 .
在轧制过程中, 轧辊 出现不 同程度 的磨 损。通过对现 场大量磨损 数据进行定 性分
析, 得到如下结论 : 上工作辊磨损量大于下工 作辊磨损量 。这主要是因各轧机问活套造成 带材对上辊面包角增 大, 增加了接触面积和 压力。另外 , 带钢氧化铁皮滞 留增加 了工作 辊的磨损。下支撑辊磨损量大于相应上支撑
从剥落部位取样进行轧辊成分和组织分 析, 随机在剥落断口取样 , 取样大小为 1 0 0× 20 m, 0 r 检查 出此轧辊的成分如表 1 a 。
维普资讯
C P轧 机工作辊剥 落原 因初探 S
热轧板厂 李 会 F 7下支撑辊有 凹坑现象。在剥落之前 , 轧制 了 2 块 S A— 4 0 m规格产品。该轧辊 4 P H、.m
1 前言
涟钢薄板 坯连铸 连轧生 产线属第 二代
“ 紧凑式 带钢生 产线 ( o pc S i Pou. C m at tp r c r d tn ” 技术及关键设 备从德 国西 马克 一德 i), o 马格( M D 财 团引进 , 中电气 控制部分 SS ) 其 由日本 T S IA— E公 司分包 , O HB G 辊底式均
响声, 当卷取卷了大约 l O吨左右, 带钢在 丌
工作辊剥落 , 多数为辊面裂纹所致。其 剥落 机理大致为 : 内部应力集中一产生热裂纹一热裂纹扩
散_ 粗糙的表面一剥落 +
轧破 , 操作人员拍 Q— T P 随后检查发现 丌 SO 。
热轧支承辊剥落问题根本原因分析及使用建议

热轧支承辊剥落问题根本原因分析及使用建议热轧支承辊剥落问题根本原因分析及使用建议■王维宁,赵学文我公司为客户热轧生产线提供的一只支承辊,辊身直径1461.02mm,客户反馈在某次轧钢时有异响,拉出后该辊的辊身发现有剥落。
通过现场勘察、支撑辊使用情况调查,对支承辊剥落问题进行根本原因分析,并根据分析结果为客户提供现场使用建议。
1. 现场勘察情况根据现场仔细勘察、测量,剥落处位于辊身中部至非字端(传动侧)辊身边部(见图1),范围约900mm(轴向)×800mm(周向),剥落断面中部有两个平滑的带状裂纹通道区域,均约100mm 宽。
①通道距辊身端部约500mm,②通道距辊身端部约300mm。
两条通道区域两侧有一个分界线,分界线及外侧较为粗糙,距辊面深度在25~30mm,条带上可以看到部分不太明显的疲劳扩展条纹,分布着比较经典的一圈一圈的“贝状纹(海滩样)”疲劳扩展条纹,这是每一阶段裂纹前沿轮廓留下的痕迹,贝状纹指示的两条裂纹通道的扩展方向均朝上,与支承辊在机旋转方向相反。
②通道色泽相对发灰、发黑,表面有一薄层氧化腐蚀产物。
在剥落断面同侧的未剥落辊面上发现A、B两处表面裂纹区域,如图2、图3所示。
A区域位于剥落断面对面,距辊身端面385mm,范围100mm(轴向)×185mm(轴向),该区域内上方三处较小表面裂纹呈现“︿”形,“︿”形指向方向与裂纹通道扩展方向一致,下方有一条较长半弧形与轴向的竖直状组成的复合开口裂纹,根据裂纹交汇特点,竖直形裂纹为首先形成的主裂纹,该裂纹应为轧制事故造成的挤压裂纹。
B区域位于剥落断面上沿约400mm处,范围100mm (轴向)×185mm(轴向),距辊身端面100mm。
B区域有多处轴向小裂纹,裂纹密集处成带状,局部呈网状,此种裂纹为典型的热冲击裂纹。
根据着色显像,B区域下方较长的显像条带疑似为擦伤(硌痕),同时B区域下方有一小硌坑。
经超声波检测确定:外露①裂纹通道沿辊面下未剥离的裂纹通道与A区域相连,可确定A区域为①裂纹通道的起源,外露②裂纹通道沿辊面下未剥落暴露的裂纹通道与B区域相连,B区域为②裂纹通道的起源。
热轧轧辊剥落或断裂的原因及预防方法探究
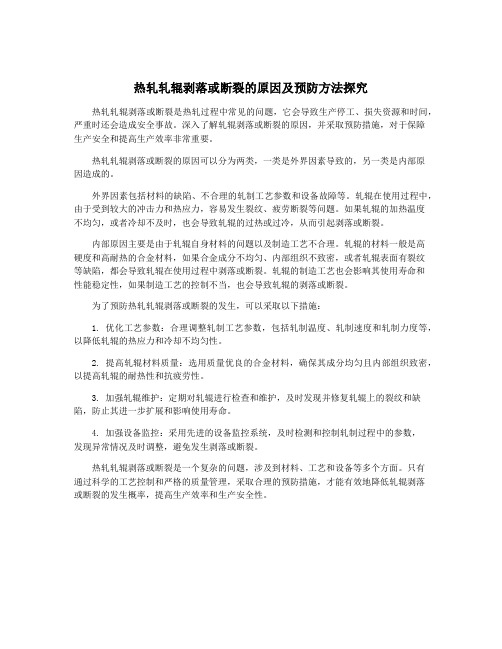
热轧轧辊剥落或断裂的原因及预防方法探究热轧轧辊剥落或断裂是热轧过程中常见的问题,它会导致生产停工、损失资源和时间,严重时还会造成安全事故。
深入了解轧辊剥落或断裂的原因,并采取预防措施,对于保障生产安全和提高生产效率非常重要。
热轧轧辊剥落或断裂的原因可以分为两类,一类是外界因素导致的,另一类是内部原因造成的。
外界因素包括材料的缺陷、不合理的轧制工艺参数和设备故障等。
轧辊在使用过程中,由于受到较大的冲击力和热应力,容易发生裂纹、疲劳断裂等问题。
如果轧辊的加热温度不均匀,或者冷却不及时,也会导致轧辊的过热或过冷,从而引起剥落或断裂。
内部原因主要是由于轧辊自身材料的问题以及制造工艺不合理。
轧辊的材料一般是高硬度和高耐热的合金材料,如果合金成分不均匀、内部组织不致密,或者轧辊表面有裂纹等缺陷,都会导致轧辊在使用过程中剥落或断裂。
轧辊的制造工艺也会影响其使用寿命和性能稳定性,如果制造工艺的控制不当,也会导致轧辊的剥落或断裂。
为了预防热轧轧辊剥落或断裂的发生,可以采取以下措施:1. 优化工艺参数:合理调整轧制工艺参数,包括轧制温度、轧制速度和轧制力度等,以降低轧辊的热应力和冷却不均匀性。
2. 提高轧辊材料质量:选用质量优良的合金材料,确保其成分均匀且内部组织致密,以提高轧辊的耐热性和抗疲劳性。
3. 加强轧辊维护:定期对轧辊进行检查和维护,及时发现并修复轧辊上的裂纹和缺陷,防止其进一步扩展和影响使用寿命。
4. 加强设备监控:采用先进的设备监控系统,及时检测和控制轧制过程中的参数,发现异常情况及时调整,避免发生剥落或断裂。
热轧轧辊剥落或断裂是一个复杂的问题,涉及到材料、工艺和设备等多个方面。
只有通过科学的工艺控制和严格的质量管理,采取合理的预防措施,才能有效地降低轧辊剥落或断裂的发生概率,提高生产效率和生产安全性。
CSP轧机工作辊剥落原因及改进措施

CSP轧机工作辊剥落原因及改进措施李会【摘要】涟钢CSP工作辊发生剥落的主要原因是板坯温度不均、轧辊冷却温度不均和轧制事故.通过严格操作规范和加强对轧辊的检测与维护,并选择适当的轧制参数及辊形,可使轧辊剥落事故发生频率降至最低.【期刊名称】《大型铸锻件》【年(卷),期】2006(000)004【总页数】3页(P37-39)【关键词】CSP轧机;轧辊;剥落【作者】李会【作者单位】湖南华菱涟钢热轧板厂,湖南,417009【正文语种】中文【中图分类】TG31 前言华菱涟钢薄板坯连铸连轧生产线属第二代紧凑式带钢生产线(Compact Strip Production)。
该生产线有7架精轧机组,所用轧辊分为三种类型:F1~F2为高铬钢轧辊,辊径范围为950 mm~820 mm;F3~F4为高铬铁轧辊,辊径范围为750 mm~660 mm;F5~F7为改进型高镍铬轧辊,辊径范围为620 mm~540 mm。
工作辊辊身长度为2 000 mm,轧辊辊型为CVC(plus)即连续可变凸度辊型。
每个机架的工作辊窜动量为±100 mm。
支承辊为平辊加倒角辊型,辊身长度为1 800 mm。
该生产线自投产以来,共发生了8次工作辊剥落事故。
F1~F2发生1次, F5~F7发生7次。
如果频繁发生轧辊剥落事故,不仅会严重影响生产的顺利进行,还会给企业造成较大的经济损失。
所以有必要对轧辊剥落的原因进行深入研究,并采取有利措施将该事故的发生频率降至最低。
2 轧辊剥落的产生机理剥落是轧辊常见缺陷之一,是指工作层或芯部结合层在热轧过程中脱落的现象。
剥落会给轧辊造成较大的损失,程度严重时还会导致轧辊的损坏。
根据工作辊剥落断口的形式可以判断剥落是由接触疲劳和热裂纹造成的,它同样存在裂纹产生和发展的过程。
生产中出现的工作辊剥落多数由辊面裂纹所致,其剥落机理大致为:内部应力集中→产生热裂纹→热裂纹扩散→粗糙的表面→剥落。
在生产过程中辊面产生裂纹的原因主要有以下两种:首先是因为冷却不均产生梯状热裂,并在辊体的环状带内出现径向平面弥漫的纵向裂纹。
热轧轧辊剥落或断裂的原因及预防方法探究
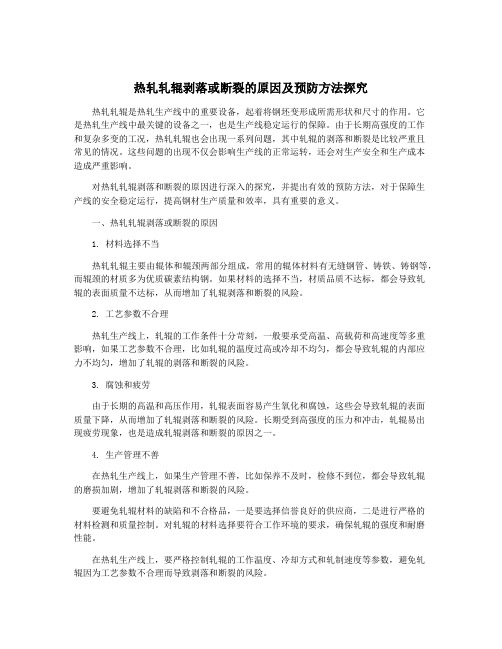
热轧轧辊剥落或断裂的原因及预防方法探究热轧轧辊是热轧生产线中的重要设备,起着将钢坯变形成所需形状和尺寸的作用。
它是热轧生产线中最关键的设备之一,也是生产线稳定运行的保障。
由于长期高强度的工作和复杂多变的工况,热轧轧辊也会出现一系列问题,其中轧辊的剥落和断裂是比较严重且常见的情况。
这些问题的出现不仅会影响生产线的正常运转,还会对生产安全和生产成本造成严重影响。
对热轧轧辊剥落和断裂的原因进行深入的探究,并提出有效的预防方法,对于保障生产线的安全稳定运行,提高钢材生产质量和效率,具有重要的意义。
一、热轧轧辊剥落或断裂的原因1. 材料选择不当热轧轧辊主要由辊体和辊颈两部分组成,常用的辊体材料有无缝钢管、铸铁、铸钢等,而辊颈的材质多为优质碳素结构钢。
如果材料的选择不当,材质品质不达标,都会导致轧辊的表面质量不达标,从而增加了轧辊剥落和断裂的风险。
2. 工艺参数不合理热轧生产线上,轧辊的工作条件十分苛刻,一般要承受高温、高载荷和高速度等多重影响,如果工艺参数不合理,比如轧辊的温度过高或冷却不均匀,都会导致轧辊的内部应力不均匀,增加了轧辊的剥落和断裂的风险。
3. 腐蚀和疲劳由于长期的高温和高压作用,轧辊表面容易产生氧化和腐蚀,这些会导致轧辊的表面质量下降,从而增加了轧辊剥落和断裂的风险。
长期受到高强度的压力和冲击,轧辊易出现疲劳现象,也是造成轧辊剥落和断裂的原因之一。
4. 生产管理不善在热轧生产线上,如果生产管理不善,比如保养不及时,检修不到位,都会导致轧辊的磨损加剧,增加了轧辊剥落和断裂的风险。
要避免轧辊材料的缺陷和不合格品,一是要选择信誉良好的供应商,二是进行严格的材料检测和质量控制。
对轧辊的材料选择要符合工作环境的要求,确保轧辊的强度和耐磨性能。
在热轧生产线上,要严格控制轧辊的工作温度、冷却方式和轧制速度等参数,避免轧辊因为工艺参数不合理而导致剥落和断裂的风险。
要对轧辊的表面进行防腐处理,避免氧化和腐蚀的发生;并对轧辊进行定期的疲劳检测和预防性维护,延长轧辊的使用寿命。
热轧轧辊剥落或断裂的原因及预防方法探究
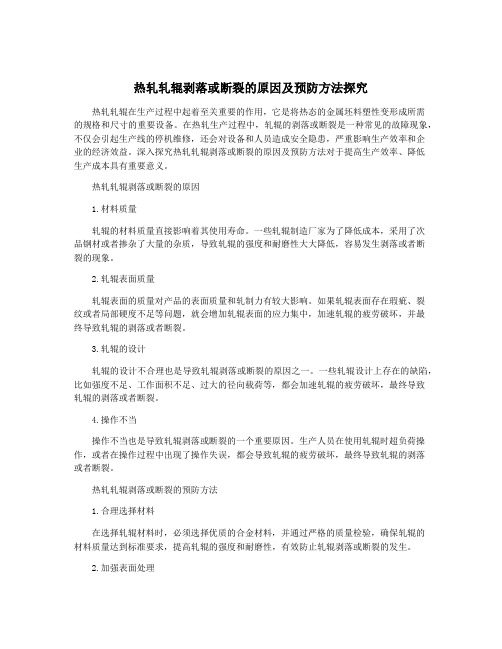
热轧轧辊剥落或断裂的原因及预防方法探究热轧轧辊在生产过程中起着至关重要的作用,它是将热态的金属坯料塑性变形成所需的规格和尺寸的重要设备。
在热轧生产过程中,轧辊的剥落或断裂是一种常见的故障现象,不仅会引起生产线的停机维修,还会对设备和人员造成安全隐患,严重影响生产效率和企业的经济效益。
深入探究热轧轧辊剥落或断裂的原因及预防方法对于提高生产效率、降低生产成本具有重要意义。
热轧轧辊剥落或断裂的原因1.材料质量轧辊的材料质量直接影响着其使用寿命。
一些轧辊制造厂家为了降低成本,采用了次品钢材或者掺杂了大量的杂质,导致轧辊的强度和耐磨性大大降低,容易发生剥落或者断裂的现象。
2.轧辊表面质量轧辊表面的质量对产品的表面质量和轧制力有较大影响。
如果轧辊表面存在瑕疵、裂纹或者局部硬度不足等问题,就会增加轧辊表面的应力集中,加速轧辊的疲劳破坏,并最终导致轧辊的剥落或者断裂。
3.轧辊的设计轧辊的设计不合理也是导致轧辊剥落或断裂的原因之一。
一些轧辊设计上存在的缺陷,比如强度不足、工作面积不足、过大的径向载荷等,都会加速轧辊的疲劳破坏,最终导致轧辊的剥落或者断裂。
4.操作不当操作不当也是导致轧辊剥落或断裂的一个重要原因。
生产人员在使用轧辊时超负荷操作,或者在操作过程中出现了操作失误,都会导致轧辊的疲劳破坏,最终导致轧辊的剥落或者断裂。
热轧轧辊剥落或断裂的预防方法1.合理选择材料在选择轧辊材料时,必须选择优质的合金材料,并通过严格的质量检验,确保轧辊的材料质量达到标准要求,提高轧辊的强度和耐磨性,有效防止轧辊剥落或断裂的发生。
2.加强表面处理对轧辊表面进行加强处理,提高轧辊的表面质量和强度,有效减少轧辊表面的裂纹和瑕疵,降低轧辊的疲劳破坏,延长轧辊的使用寿命,减少剥落或断裂的发生。
3.改善轧辊设计改善轧辊的设计,提高轧辊的强度和刚性,增加轧辊工作面积,合理分配径向载荷,减小轧辊的应力集中,降低轧辊的疲劳损伤,有效预防轧辊剥落或断裂。
探究冷轧支撑辊和工作辊剥落机理及有效预防措施(全文)

探究冷轧支撑辊和工作辊剥落机理及有效预防措施引言轧辊是轧钢生产的重要工具,价格非常昂贵,尤其是冷轧板带用的锻钢支撑辊及工作辊。
近年来,各轧钢厂为提高产量和减少换辊周期, 广泛使用价格更贵、硬度更高及淬硬层更深的高合金辊。
因此,减少轧辊的早期失效及降低生产成本显得日益重要。
在冷轧板带生产过程中,轧辊处于复杂且不断变化的应力状态。
轧制负荷引起的支撑辊与工作辊间的接触应力、带钢跑偏断带以及肋浪粘钢造成的机械及热冲击容易使轧辊损坏。
轧辊损坏的形式主要为剥落,因此,探究轧辊剥落机理以便早期发现裂纹和预防剥落是延长轧辊使用寿命的有效途径。
1、冷轧技术概述钢材是国民经济的各个领域中的十分重要的材料,它被广泛应用于机械工程、电机工程、建筑、金属制品、汽车、运输、家用器具等各个行业。
20XX年以来,全球对钢材的需求量除了在经受金融危机时出现负增长以外均保持持续增长状态。
20XX年全球范围内粗钢产量11.65亿吨,ZG达到5.68吨,ZG在全球钢材市场上的产量及消费量表现出强劲的态势。
冷轧是指金属进行礼制变形时的温度在再结晶温度以下,实际一般是指带钢在室温下进行轧制加工而不加热。
利用冷轧技术生产的带材和钢板精确度高,而且性能优良,其主要特点为轧制温度低,可以获得精确的尺寸和均匀的厚度,可以获得很薄的带材,这是热轧技术无法做到的;冷轧产品具有很好的力学性能和工艺性能,可以获得优越的表面质量,可以幸免热轧生产的带钢具有的缺陷,并且可以操纵带钢的表面粗糙度,以满足不同的用户需求,也可以满足下一道工序的加工需求;并且可实现高速轧制,具有很高的生产效率。
2、冷轧支撑辊轴承的力学分析2.1、轴承的失效形式轴承的常火效形式命内的疲破坏命期外的失效,其中寿命内的疲劳点蚀、剥落、塑性变形、磨损与胶合。
轴承的非常失效形式发生在寿命期内,可能会出现在滚子、内圈、外圈滚道或保持架上具体表现形式为破裂、取性变形或烧独等。
(此处需要修改,语句不顺)2.2、轴承的失效机理图1 轴承的运动及受力从运动学原理上分析,轴承的失效可能源于内倒随捉轴的高速旋转,或滚子高速自转和公转。
关于辊皮剥落的原因分析

关于辊皮剥落的原因分析辊皮剥落可能有以下原因1,堆焊质量堆焊质量方面看剥落的基础均为本次堆焊的基础面。
有理由怀疑堆焊时,基础面未清理干净。
部分磨辊存在堆焊层较厚的问题。
堆焊层越厚,脱焊的几率越大。
建议适度控制磨辊的磨损深度。
对磨损过深的磨辊报废掉。
从前期堆焊情况看,磨辊磨盘堆焊经常出现超堆的问题。
堆焊辊槽辊面形状偏离原始尺寸。
磨盘中间平台堆焊较高。
从三线4#磨辊部分脱落层看。
堆焊内部应力较大。
裂纹较密。
估计焊接时表面温度偏高。
2,物料性质近期所使用的尾矿里含有少量的小块铁矿石,石碌铁矿的矿石为硬质赤铁矿,伴有石英岩。
此两种相比方解石均为硬度较大矿物。
需加强对块状铁质原料的去除。
3,操作调整状况磨机拉杆调整问题,从剥落前看,部分磨机拉杆均存在波动幅度较大,波动频率高,料层不稳定。
有些磨机振动跳停次数偏多。
在目前石灰石粒度降低的情况下,可根据情况适当考虑降低磨机研磨压力。
控制在130-135左右。
从磨辊磨损情况看,部分磨机外侧磨辊存在较大的磨损坑,磨损不均匀,降低了磨辊的使用时间,不利于磨辊的继续堆焊使用。
4,除铁器问题以供料二车间圆堆两个除铁器为例,安装过高基本没吸到铁。
生产三短皮带除铁器从未投入过。
(电控柜缺失)。
供料一长堆A18除铁器电控柜在长堆里面,开停清理要去长堆里面操作,存在安装缺陷。
经常存在开机不开除铁器。
除铁器吸到的铁质物料直接排到调配站。
上游车间检修割下的螺栓,轴承,等硬质铁件检修完未清理出来。
5, 生产车间管理懈怠部分车间出磨除铁器清理不干净,或者基本不清理。
除铁器不开,或者缺失。
致使一些铸造的铁磁性较差的铁件在磨内循环碾压。
车间检修日常管理松懈。
6,上游车间对下游车间的漠视上游车间对于除铁的漠视,从磨内捡到的油桶和上游车间的除铁器安装均可看出。
只要我的皮带没事。
你的磨辊破是你的事。
上游车间只对本车间设备负责。
一线4#辊三线4#辊二线4#辊四线1#磨4#辊。
热轧轧辊剥落或断裂的原因及预防方法探究

热轧轧辊剥落或断裂的原因及预防方法探究【摘要】热轧轧辊剥落或断裂是热轧生产中常见的问题,严重影响生产效率和产品质量。
本文从热轧轧辊剥落或断裂现象引起注意和研究目的和意义两个方面展开,然后深入探讨了造成这一问题的原因,包括金属材料的质量问题、外部环境因素和工艺参数设置不当等。
针对这些原因,提出了一些有效的预防方法,如加强材料检验、保持良好的生产环境和合理设置工艺参数。
在研究成果总结和未来研究展望两个方面进行总结,指出今后需要深入研究轧辊剥落或断裂的原因及预防方法,以提高热轧生产的效率和质量。
通过本文的研究,有望为解决热轧轧辊剥落或断裂问题提供一定的参考和借鉴。
【关键词】热轧轧辊、剥落、断裂、金属材料、质量问题、外部环境、工艺参数、预防方法、研究成果、展望。
1. 引言1.1 热轧轧辊剥落或断裂现象引起注意热轧轧辊剥落或断裂是热轧生产中常见的问题,一旦发生会给生产带来严重的影响。
轧辊是热轧生产中不可或缺的重要设备之一,承担着对金属带材进行塑性加工的重要任务。
由于受到多种因素的影响,轧辊往往会出现剥落或断裂的现象,如果不及时处理和预防,将导致生产事故的发生,影响生产效率和产品质量。
热轧轧辊剥落或断裂现象需要引起注意,因为其主要危害包括:一是轧辊剥落或断裂会导致生产线停机,给企业带来直接的经济损失;二是剥落或断裂的轧辊会造成产品表面质量不达标,影响产品的销售和企业的声誉;三是轧辊剥落或断裂会增加生产中的安全隐患,可能导致事故发生,影响员工的生命安全。
对热轧轧辊剥落或断裂现象引起足够的重视,研究其发生的原因以及预防方法,对于提高生产效率、保证产品质量和保障人员安全具有重要意义。
本文旨在探究热轧轧辊剥落或断裂的原因及预防方法,为热轧生产提供一定的参考和指导。
1.2 研究目的和意义研究的目的在于深入探究热轧轧辊剥落或断裂的原因,分析其中可能存在的金属材料质量问题、外部环境因素以及工艺参数设置不当等方面的因素。
通过研究分析,可以为预防热轧轧辊剥落或断裂提供理论依据和技术支持,提高轧辊的使用寿命和生产效率。
热轧轧辊剥落或断裂的原因及预防方法探究

热轧轧辊剥落或断裂的原因及预防方法探究热轧轧辊在钢铁生产中扮演着非常重要的角色,它直接影响到板材的成型质量和生产效率。
在实际生产中,经常会发生热轧轧辊剥落或断裂的情况,给生产带来严重的影响。
探究热轧轧辊剥落或断裂的原因及预防方法对于提高生产效率,降低生产成本具有非常重要的意义。
一、热轧轧辊剥落或断裂的原因1. 轧辊质量问题热轧轧辊的质量直接关系到其使用寿命和稳定性。
如果轧辊材料的硬度和强度不达标,就容易在生产过程中发生剥落或断裂的问题。
如果轧辊的表面光洁度不够,也容易导致板材表面出现瑕疵,甚至剥落。
2. 过热或过冷的板坯温度在热轧生产过程中,如果板坯的温度不稳定,容易导致热轧轧辊受到过大的冲击力,从而加速其磨损和断裂的过程。
特别是过冷的板坯容易导致轧辊的温度骤然下降,从而造成轧辊的变形和断裂。
3. 辊缝调整不当热轧轧辊的辊缝调整不当也是导致剥落或断裂的重要原因之一。
如果辊缝太小,就容易造成辊缝夹板,从而导致轧辊的断裂;如果辊缝太大,就会导致轧辊的挤压能力下降,磨损加剧,最终也会导致轧辊的剥落或断裂。
4. 轧辊表面磨损随着生产的不断进行,轧辊表面会发生磨损,磨损过多会导致轧辊的表面粗糙,从而造成板材表面质量的下降。
轧辊表面的磨损也会加速轧辊的断裂。
5. 运行参数不合理一些运行参数不合理也是导致热轧轧辊剥落或断裂的原因之一。
轧辊的进给速度过快,就容易导致轧辊受到过大的冲击力,从而加速其磨损和断裂;轧辊的冷却水量不足,也会导致轧辊温度过高,从而破坏轧辊的结构。
1. 选择优质的轧辊材料为了防止热轧轧辊的剥落或断裂,首先要选择优质的轧辊材料。
要选择具有高硬度和高强度的轧辊材料,以及表面光洁度好、抗磨损性能好的轧辊材料。
2. 严格控制板坯温度在热轧生产过程中,要严格控制板坯的温度,确保其稳定在适宜的温度范围内。
尤其是在板坯的预热和送入轧机的过程中,要确保板坯温度的稳定性。
为了防止轧辊的剥落或断裂,辊缝的调整非常重要。
热轧轧辊剥落或断裂的原因及预防方法探究
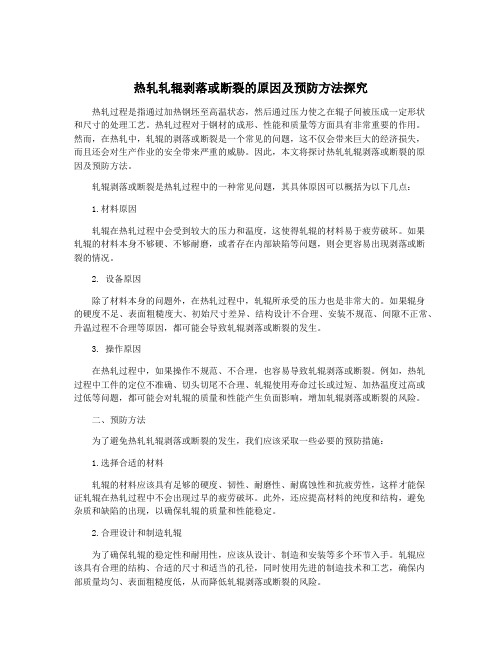
热轧轧辊剥落或断裂的原因及预防方法探究热轧过程是指通过加热钢坯至高温状态,然后通过压力使之在辊子间被压成一定形状和尺寸的处理工艺。
热轧过程对于钢材的成形、性能和质量等方面具有非常重要的作用。
然而,在热轧中,轧辊的剥落或断裂是一个常见的问题,这不仅会带来巨大的经济损失,而且还会对生产作业的安全带来严重的威胁。
因此,本文将探讨热轧轧辊剥落或断裂的原因及预防方法。
轧辊剥落或断裂是热轧过程中的一种常见问题,其具体原因可以概括为以下几点:1.材料原因轧辊在热轧过程中会受到较大的压力和温度,这使得轧辊的材料易于疲劳破坏。
如果轧辊的材料本身不够硬、不够耐磨,或者存在内部缺陷等问题,则会更容易出现剥落或断裂的情况。
2. 设备原因除了材料本身的问题外,在热轧过程中,轧辊所承受的压力也是非常大的。
如果辊身的硬度不足、表面粗糙度大、初始尺寸差异、结构设计不合理、安装不规范、间隙不正常、升温过程不合理等原因,都可能会导致轧辊剥落或断裂的发生。
3. 操作原因在热轧过程中,如果操作不规范、不合理,也容易导致轧辊剥落或断裂。
例如,热轧过程中工件的定位不准确、切头切尾不合理、轧辊使用寿命过长或过短、加热温度过高或过低等问题,都可能会对轧辊的质量和性能产生负面影响,增加轧辊剥落或断裂的风险。
二、预防方法为了避免热轧轧辊剥落或断裂的发生,我们应该采取一些必要的预防措施:1.选择合适的材料轧辊的材料应该具有足够的硬度、韧性、耐磨性、耐腐蚀性和抗疲劳性,这样才能保证轧辊在热轧过程中不会出现过早的疲劳破坏。
此外,还应提高材料的纯度和结构,避免杂质和缺陷的出现,以确保轧辊的质量和性能稳定。
2.合理设计和制造轧辊为了确保轧辊的稳定性和耐用性,应该从设计、制造和安装等多个环节入手。
轧辊应该具有合理的结构、合适的尺寸和适当的孔径,同时使用先进的制造技术和工艺,确保内部质量均匀、表面粗糙度低,从而降低轧辊剥落或断裂的风险。
3.规范操作和维护在热轧过程中,必须确保操作规范严谨。
轧辊失效的原因及防治措施

轧辑失效的原因及防治措施轧辐的损坏形式多种多样,典型形式及失效原因如下:1、轧辑磨损分三类:机械磨损是由轧辐表面与轧件摩擦引起的;热磨损是由高温作用使其表层软化、熔化或蒸发引起的;腐蚀磨损是由轧辐表面水分的化学作用、电化学作用、氧化作用等引起表面材料损失和迁移。
2、轧辐裂纹轧制中发生堆钢、卡钢、追尾等事故,致使其局部温度急剧升高,产生的热应力和组织应力超过极限,形成热裂纹;轧制延伸形成舌头,其温度低于中部轧件,会产生热应力以及轧制应力突变,形成冲击裂纹;轧制中,由于氧化铁皮叠轧,导卫划痕等原因也会形成裂纹。
3、轧辐剥落裂纹的形成和扩展加快,到达一定长度和深度后,会导致剥落。
4、轧辑断裂1)辐轴铸造缺陷轧辐离心铸造中,因离心震动产生成分和组织层状偏析,形成裂纹迅速扩展,造成轧辐断裂。
2)轧辐组织缺陷化学成分不合格、冷却速度不当会导致成分偏析、渗碳体过高等缺陷,只是机械性能下降,最终导致断裂。
3)加工工艺轧辐在锻造时压力过小或变形不合理造成轧辐芯部未锻透,形成穿晶裂纹。
其防治措施为:1、轧辐选用耐磨又抗热裂纹的材质,采取相应的热处理及物流化学处理措施,使组织均化,表面耐磨性增加。
2、轧辑在上轧机前进行硬度、超声波等综合检验,确保其无裂纹等缺陷。
3、轧辐车削时,将残留氧化层及裂纹彻底清除,以减少轧辐表面裂纹及剥落产生。
4、合理安排换辐周期,选配轧辐,制定详细的轧辐车修方案,将车修量控制在要求范围内。
5、合理布置冷却水喷射范围和控制冷却水量,确保轧辐冷却温度控制在正常范围内。
6、加强设备点检,预防轧钢设备事故,减少导致卡钢、堆钢、追尾等事故发生。
严格控制轧制温度,杜绝低温钢通过轧机,避免轧制力过载。
轧辊氧化膜剥落的原因

轧辊氧化膜剥落的原因轧辊氧化膜剥落,这事儿就像房子的墙皮突然掉了一块似的,让人挺头疼的。
那为啥会出现这种情况呢?咱们先说说这轧辊本身的质量吧。
要是轧辊在制造的时候就有一些小毛病,就像一个人生下来就带着点小缺陷一样。
比如说材料里有杂质,这就好比一锅好粥里混进了几颗沙子。
在轧辊工作的时候,这些杂质周围的应力就会不均匀。
这应力不均匀可不得了,就像拔河的时候两边力量不一样,很容易就把氧化膜给撕扯开了,然后就剥落了。
再讲讲工作环境的事儿。
轧辊工作的地方那可是个挺复杂的环境。
温度忽高忽低的,这就像人一会儿在大夏天晒太阳,一会儿又被扔到冰窖里。
氧化膜在这种环境下,热胀冷缩得厉害。
时间长了,就像一根皮筋老是被拉来拉去的,它的结构就变得脆弱了。
一旦脆弱到一定程度,可不就剥落了嘛。
还有那润滑条件也很关键啊。
要是润滑不好,就像人走路的时候鞋里有沙子,每走一步都咯得慌。
轧辊之间的摩擦力就会增大,这摩擦力就像一只无形的手,在不断地搓揉氧化膜,搓着搓着,氧化膜就受不了了,就从轧辊上掉下来了。
操作人员的操作习惯也会影响轧辊氧化膜剥落。
有些操作人员可能不太细心,就像一个粗心的厨师做菜的时候乱放调料一样。
比如说在轧制过程中,加载的压力不均匀。
这就好比给轧辊的压力一会儿大得像座山,一会儿又小得像片羽毛。
这种不稳定的压力会让轧辊表面的应力发生变化,氧化膜在这种不断变化的应力下,就像风中的树叶一样,摇摇欲坠,最后就剥落了。
还有啊,这轧制工艺也有讲究。
如果轧制的速度不合理,太快或者太慢都不行。
太快了呢,就像一辆车在马路上狂飙,轧辊和材料之间的相互作用就会变得很激烈,氧化膜就容易被破坏。
太慢了呢,又像乌龟慢慢爬,一些化学反应或者物理过程就会变得不正常,也会影响氧化膜的稳定性。
就像一群人走路,速度不协调就容易乱套,这氧化膜的稳定性一乱套,就容易剥落。
轧辊氧化膜剥落是多种因素共同作用的结果。
轧辊自身质量不过关,工作环境的折腾,操作人员的粗心大意,轧制工艺的不合理,就像一群调皮捣蛋的小鬼,一起把氧化膜给折腾得剥落了。
热轧轧辊剥落或断裂的原因及预防方法探究
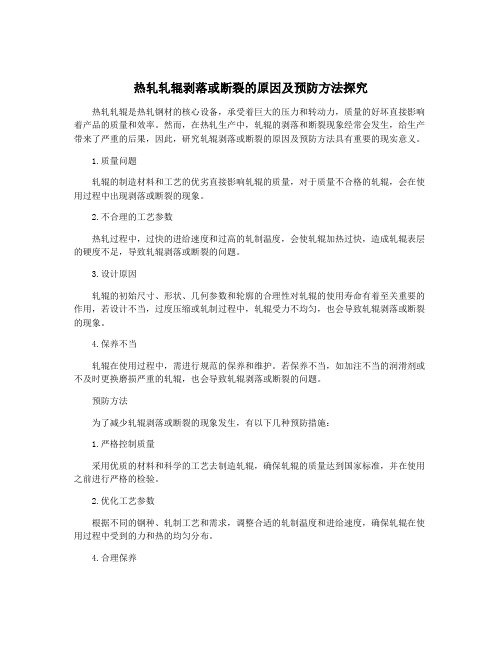
热轧轧辊剥落或断裂的原因及预防方法探究热轧轧辊是热轧钢材的核心设备,承受着巨大的压力和转动力,质量的好坏直接影响着产品的质量和效率。
然而,在热轧生产中,轧辊的剥落和断裂现象经常会发生,给生产带来了严重的后果,因此,研究轧辊剥落或断裂的原因及预防方法具有重要的现实意义。
1.质量问题轧辊的制造材料和工艺的优劣直接影响轧辊的质量,对于质量不合格的轧辊,会在使用过程中出现剥落或断裂的现象。
2.不合理的工艺参数热轧过程中,过快的进给速度和过高的轧制温度,会使轧辊加热过快,造成轧辊表层的硬度不足,导致轧辊剥落或断裂的问题。
3.设计原因轧辊的初始尺寸、形状、几何参数和轮廓的合理性对轧辊的使用寿命有着至关重要的作用,若设计不当,过度压缩或轧制过程中,轧辊受力不均匀,也会导致轧辊剥落或断裂的现象。
4.保养不当轧辊在使用过程中,需进行规范的保养和维护。
若保养不当,如加注不当的润滑剂或不及时更换磨损严重的轧辊,也会导致轧辊剥落或断裂的问题。
预防方法为了减少轧辊剥落或断裂的现象发生,有以下几种预防措施:1.严格控制质量采用优质的材料和科学的工艺去制造轧辊,确保轧辊的质量达到国家标准,并在使用之前进行严格的检验。
2.优化工艺参数根据不同的钢种、轧制工艺和需求,调整合适的轧制温度和进给速度,确保轧辊在使用过程中受到的力和热的均匀分布。
4.合理保养轧辊在使用过程中,应定期进行润滑和维护,并根据实际情况进行轧辊更换和修理,以保证轧辊使用寿命的延长。
总之,热轧轧辊的剥落或断裂问题的解决需要多方面的努力,除了以上预防措施之外,还需要提高工作人员的素质,严格执行操作规程,保证生产环境安全、清洁、整洁,以及进行适当的科技创新和技术改进,以确保轧辊质量及生产效率的提高。
- 1、下载文档前请自行甄别文档内容的完整性,平台不提供额外的编辑、内容补充、找答案等附加服务。
- 2、"仅部分预览"的文档,不可在线预览部分如存在完整性等问题,可反馈申请退款(可完整预览的文档不适用该条件!)。
- 3、如文档侵犯您的权益,请联系客服反馈,我们会尽快为您处理(人工客服工作时间:9:00-18:30)。
关键词 :CSP 轧机 ;轧辊 ;剥落 中图分类号 : T G333. 7 + 2 文献标识码 :B
The Reaso n of t he Wo rk Roll Flaking in t he CSP Mill and It s Imp rovement
Li Hui
Abstract :The main reasons of CSP work roll flaking in Lianyuan Steel are t he uneven slab temperat ure , un2 even roll cooling temperat ure and t he rolling accident . By means of t he st rict normative operation and t he well maintenance and detecting of t he rolls ,as well as by selecting t he p roper rolling parameter and roll p rofile , t he roll flaking incident can be reduced to t he min. limitation.
4 改进措施
根据以上分析可知 ,涟钢 CSP 工作辊发生剥 落的主要原因是板坯温度不均 、轧辊冷却温度不 均和轧制事故 。针对这些问题应采取以下措施加 以改进 :
(1) 严格控制轧辊进货质量 。必须逐项检查 轧辊的几何尺寸和硬度 ,并对轧辊内部质量进行 探伤检测 。对不符合图纸及技术协议要求的轧辊 向厂家提出异议 。
另外 ,导致轧制力分布不均匀的还有板坯形 状及板坯温度等因素 。板坯形状只要不出现楔形 和鼓肚现象 ,则对轧制力的影响比较小 。而轧制 过程中板坯温度不均匀 ,尤其是轧制强度比较高 的钢种时 ,如果在某个区域冷却不均匀 ,则辊间受 力是不均匀的 ,会引起轧辊应力的不均 。当热应 力和组织应力的综合作用超过了材料的强度极限 时 ,就会产生热冲击裂纹 。
该工作辊的金相组织检测结果为贝氏体 + 25 %的碳化物 ,其化学成分检验结果见表 1 。
表 1 工作辊的金相组织和化学成分( 质量分数 , %) Table. 1 The metallurgical structure and
chemical composition of the
work roll ( mass fraction %)
37
No . 4 November 2006
《大型铸锻件》 H EAV Y CASTIN G AND FOR GIN G
角和工作辊开压边部内浇口所致 。
3 涟钢 CSP 工作辊发生剥落的原因
涟钢薄板坯连铸连轧生产线在轧制钢卷时 , 其 F7 机架上的下工作辊发生了严重剥落 ,并造 成 F7 下支承辊有凹坑现象 。该轧辊进厂后共使 用 23 次 ,总轧制长度为 1 051 km ,总轧制量为 41 024 t ,总 生 产 时 间 为 190 h , 平 均 轧 制 量 为 1 784 t/ 46 km 。
(2) 轧辊冷却的不均匀 轧辊冷却情况不但要影响轧制模型的计算精 度 ,还会影响轧辊的表面质量 。轧辊冷却分前后 和上下布置 。进口只有两排喷嘴 ,出口有三排喷 嘴 ,都是交叉布置 。喷嘴喷射的角度是固定的 ,但 是出口喷嘴型号每排不一样 。后机架的喷嘴比前 机架的小 ,堵塞的现象也较严重 。只要某部位喷 嘴堵塞 ,在这个部位的轧辊温度相对较高 ,在局部 就会产生相应的热裂 。同时 ,如果喷嘴没有完全 堵塞 ,就会出现喷射的角度交叉不到位 ,会在交叉 部位产生热裂 。冷却水的纯净度不高或者过滤器
总之 ,CVC 精轧机组轧辊磨损规律与一般轧 辊磨损基本相同 ,只是 CVC 辊型引起支承辊与 工作辊磨损的箱形底部有一端抬高现象 。这主要 是由于 CVC 辊型引起的辊间压力分布不均和各 点相对滑动量不同造成的 。这种压力分布的不均 匀会导致轧辊与轧件接触时 ,轧辊内部产生应力 不均 。
因此 ,随着轧制量的增加 ,轧辊磨损会越来越 严重 。在这种情况下 ,轧辊与所轧物表面的硬的 氧化物或轧辊本身的硬的碳化物产生摩擦都会使 轧辊表面发生更加严重的变化 ,如表面粗糙等 ,从 而导致表面氧化膜的破裂 。这样不但会影响产品 质量 ,还会在轧辊表面产生热疲劳 。轧辊疲劳后 , 辊身各处应力不均 ,在表面非常容易产生表面裂 纹 。随着轧辊的继续使用 ,表面裂纹会沿着轧辊 圆周向芯部扩散 ,最终导致轧辊剥落 。
38
下支承辊磨损量大于相应上支承辊磨损量 。这主 要是因为带钢下表面氧化铁皮掉入下支承辊面以 及下支承辊恶劣的运行环境造成的 。另外 ,工作 辊和支承辊的磨损形状近似于箱形 ,且磨损曲线 的箱形底部基本平坦 。有时磨损曲线的箱形底部 会出现一端或两端的突起情况 ,这主要是由于辊 间压力分布不均和各点相对滑动量不同造成的 。 通过分析还知道 ,磨损量的大小与轧辊周期内所 轧带钢长度 、温度 、钢种以及金属前滑 、后滑 、横向 流动等因素有关 。
在生产过程中辊面产生裂纹的原因主要有以 下两种 :首先是因为冷却不均产生梯状热裂 ,并在 辊体的环状带内出现径向平面弥漫的纵向裂纹 。 根据金属的热传递 ,这种温度的不均蔓延至轧辊 内部 ,出现明显的热渗进 。如果这些裂纹在局部 区域内受到机械撞击 (诸如冲击碰痕 、带钢粘结 、 带钢边部或尾部重叠等) ,并且和热应力相结合超 过了轧辊辊身的屈服强度 ,就会在随后的冷却过 程中扩大并发生剥落 。
《大型铸锻件》 H EAV Y CASTIN G AND FOR GIN G
No . 4 November 2006
CSP 轧机工作辊剥落原因及改进措施
李 会
(湖南华菱涟钢热轧板厂 ,湖南 417009)
摘要 :涟钢 CSP 工作辊发生剥落的主要原因是板坯温度不均 、轧辊冷却温度不均和轧制事故 。通过严格 操作规范和加强对轧辊的检测与维护 ,并选择适当的轧制参数及辊形 ,可使轧辊剥落事故发生频率降至最低 。
另外 ,在轧机停机时 (比如堆钢) 产生裂纹的 可能性也非常大 。因为带钢可能会与工作辊有一 段时间的接触 ,接触区域的轧辊表面温度会快速 上升 。当带钢移开 ,轧辊提起时 ,轧辊表面迅速冷 却 ,此时极易产生裂纹 。裂纹的严重程度取决于 接触时间和冷却速度 。
轧辊剥落的类型有两种 ,一种是辊身剥落 ,另 一种是辊边剥落 。辊身剥落一般来说起因于表面 裂纹的扩散 ,而辊边剥落一般来说是由支承辊倒
《大型铸锻件》 H EAV Y CASTIN G AND FOR GIN G
No . 4 November 2006
没有及时清洗等 ,都会引起喷嘴堵塞 。 (3) 轧制事故的影响 轧机事故往往是产生热裂的主要祸根 ,不管
是堆钢还是甩尾 ,都会使轧辊产生致命的冲击或 热烫伤 。每次堆钢后都会在轧机内留下氧化铁 皮 ,氧化铁皮会在事故后进入机架 ,给轧辊造成一 定的影响 。同时堆钢后 ,在轧辊局部产生大量热 流 ,这种热流一直渗入到轧辊内部 ,在轧机恢复轧 制时 ,因轧辊散热的不均 ,同样会在轧辊表面产生 热裂纹 。甩尾会对轧辊局部产生很大的冲击 ,给 轧辊造成大的损伤 。
(1) 轧辊表面的变化 在轧制过程中 ,轧辊出现不同程度的磨损 。 通过对现场大量的磨损数据进行定性分析 ,得到 如下结论 :首先 ,上工作辊磨损量大于下工作辊磨 损量 。这主要是因各轧机间活套造成带材对上辊 面包角增大 ,增加了接触面积和压力 。另外 ,带钢 氧化铁皮的滞留也增加了工作辊的磨损 。其次 ,
C Mn Si
S
P
Cr Ni Mo
3. 32 0. 86 1. 03 0. 011 0. 025 1. 81 4. 38 0. 5
由检测结果可知 ,工作辊的化学成分和金相 组织均符合轧辊材质的技术要求 ,不是导致发生 剥落的主要原因 。对剥落的断口形状及剥落部位 进行仔细观察 ,发现有裂纹扩散的纹路 。裂纹行 走的路线是围绕轧辊辊身蔓延 ,并向内扩散 。这 种剥落的开始阶段 ,通常是在接近轧辊辊身的表 面处 ,有一个或多个压裂在局部超载处形成 。这 种裂纹总是与轧辊轴向平行 ,但以非径向方向弥 漫 。接下来 ,这种带状疲劳裂纹逐渐沿着大致平 行于轧辊表面的方向呈环形方向发展 ,弥漫方向 对应于轧辊的旋转方向 。弥漫向轧辊工作层内部 发展 ,逐渐加深 、加宽 ,随后是覆盖辊身表面的大 面积剥落 。此剥落的起因是在轧制强度比较高的 SPA2H 钢种时 ,长期高负荷运转加速了轧辊工作 层材料的剪力强度 。同时工作辊和支承辊经过较 长的断面磨损 ,把高负荷限定在某一区域 ,产生了 不正确的 CVC 曲线 。轧机事故和轧制异体会导 致形成初始裂纹 ,随后的轧制使材料疲劳 ,裂纹开 始弥漫直到大块自然剥落发生 。因此找出初始裂 纹产生的原因就可能避免轧辊剥落的发生 。我们 从以下几方面进行了分析研究 。
2 轧辊剥落的产生机理
剥落是轧辊常见缺陷之一 ,是指工作层或芯 部结合层在热轧过程中脱落的现象 。剥落会给轧
收稿日期 :2006 —06 —12
辊造成较大的损失 ,程度严重时还会导致轧辊的 损坏 。
根据工作辊剥落断口的形式可以判断剥落是 由接触疲劳和热裂纹造成的 ,它同样存在裂纹产 生和发展的过程 。生产中出现的工作辊剥落多数 由辊面裂纹所致 ,其剥落机理大致为 :内部应力集 中 →产生热裂纹 →热裂纹扩散 →粗糙的表面 →剥 落。