铸件形成理论重要知识点
超详细铸件形成理论重要知识点.

铸件形成理论告急知识点第一章液态金属得结构与性子1.金属得加热膨胀:原子间隔断将随温度得升髙而增长,即产生热膨胀:由于能量升沉,一些原子就大概越过势垒跑到原子之间得间隙中或金属外表,原子脱离点阵后,留下了自由点阵一空穴原子间距增大,空穴得产生为物体膨胀得缘故起因之一;2.金属得熔化:把金属加热;到熔点四周时,离位原子数大为增长;在外力得作用下,这些原子作定向运动,造成晶粒间得相对运动,称为品界粘滞运动:晶粒内部,也有相当数量得原子重复跳跃、离位,空穴数大为增长:靠近熔点时,晶界上得原子就大概脱离原晶粒外表,向相近晶粒跳跃,晶粒徐徐失去牢固形状:3. 理想金属得液态结构特点金属熔化后,以及在熔点以上不髙得温度领域内,液体状态得结构有以下特点:1、原子分列在较小隔断内仍具有肯定规律性,且其匀称原子间距增长不大:2、金属液体由许多原子团体所组成,在原子团体内保持固体得分列特性,而在原子团体之间得团结处就受到很大破坏(近程有序分列) :3、原子团体存在能量升沉与结构升沉:4、原子团体间距较大,比较疏松,犹如存在空穴:5、原子团体得匀称尺寸、游动速率都与温度有关,温度越髙,就原子团体得匀称尺寸越小,游动速率越快:归纳综合起去:靠近熔点得液态金属由许多游动得原子团体与空穴组成,原子团体中原子呈规就分列,结构与原固体相似,但存在能量升沉与结构升沉:4、实际金属得液态结构实际液态金属在微观上为由存在能星升沉、结构升沉与因素升沉得游动原子团体、空穴与许多固态、气态或液态得化合物组成得污浊液体:从化学键上看,除了基体金属与其合金元素组成得金属键之外,仍存在其他多种典范得化学键:(1)温度:温度不太髙时,T升髙,n值降落:温度很髙时,T升髙,n值升髙:(2)化学因素:外表活性元素使液体粘度低沉,非外表活性杂质得存在使粘度提髙:(3)非金属殽杂物:非金属殽杂物使粘度增长:6.粘度对铸坯质星得影响(1>对液态金属运动状态得影响:粘度对铸件外表得淸晰水平有影响,为降低液体得粘度应恰当进步过热度大概到场外表活性物质等:(2)对液态金属对流得影响:运动粘度越大,对流强度越小:铸坯得宏观偏析紧张受对流得影响:(3)对液态金属净化得影响:粘度越大,般杂物上浮速率越小,越容易滞留在铸坯中形成殽杂、气孔:7.影响外表张力得闲素1 )熔点:髙熔点得物质,其原子间结协力大,其外表张力也大:2)温度:大多数金属与合金,温度升髙,外表张力低沉:3)溶质:体系中到场削弱原子间结协力得组元,会使外表内能与外表张力低沉:8.外表张力对铸坯质量得影响1)界曲张力与润湿角:液态金属凝固时析出得固相与液相得界面能越小,形核率越卨;液态杂质与金属晶体之间得润湿性将影响杂质形态:2)外表张力引起得附加压力:附加压力进步金属液中气体析出得阻力,易产生气孔:影响金属液与铸型得相互作用:附加压力为正值时(不润湿),铸坯外表平滑,但充型本事较差,必须附加一个静压头:附加压力为负值时(润湿),金属液能很好地充满铸型型腔,但为容易与铸型粘结(粘砂),拦阻收缩,以致产生裂纹:9.看法能量升沉:金属晶体结构中每个原子得振动能量不为均等得,一些原子得能鼠髙出原子得匀称能量,有些原子得能量就远小于匀称能量,这种能量得不匀称性称为能量升沉”结构升沉:液态金属中得原子团体处于瞬息万变得状态,时而长大时而变小,时而产生时而消散,此起彼落,犹如在不绝顿地游动:这种结构得瞬息厘革称为结构升沉:近程有序分列:金属液体就由许多原子团体所组成,在原子团体内保持牢固得分列特性,而在原子团体之间得团结处就受到很大破坏:浓度升沉:差异原子间结协力存在差异,在金属液原子团簇之间存在着因素差异:这种因素得不匀称性称为浓度升沉:粘滞性:在流体力学中有两个看法,一个为动力粘度,另一个为运动粘度:外表张力:液态金属外表层得质点受到一个指向液体内部得力,物体倾向于减小其外表积,这相当于在液态金属外表有一个平行于外表且各向巨细相当得张力,这个张力就为外表张力:10.充型本事与运动性得接洽与区別:充型本事:液态金属充满铸型型腔,得到形状完备、外表淸晰得铸件得本事:即液态金属充填铸型得本事:运动性:液态金属本身运动得本事:运动性与金属得因素、温度、杂质含量及其物理性子有关:充型本事与运动性得干系:充型本事为外因(铸型性子、浇注条件、铸件结构)与内因(运动性)得共同效果:外因肯定时,运动性就为充型本事:充型本事弱,就大概产生浇缺乏、冷隔、砂眼、铁豆、抬箱,以及卷入性气孔、夹砂等缺陷:11.液态金属得克制运动机理纯金属、共晶合金、窄结品温度领域合金:型壁处凝固结壳,柱状品相打仗,通道中心归并,运动克制:合金得结晶温度领域越宽,枝晶就越旺盛,液流前端出现较少得固相量,通道壅闭,亦即在相对较短得时间内,液态金属便克制运动:纯金属、共晶合金或窄结品温度领域合金有良好得运动性,低沉了凝固成形中冷隔、热裂、缩松等缺陷得产生:反之,宽结晶温度领域合金由于运动性差,通常会有较多得缺陷产生:12.影响液态金属充型本事因素与进步步调:影响充型本事得因素为通过两个途径产生作用得:影响金属与铸型之间热交换条件,而改变金属液得运动时间:影响金属液在铸型中得水力学条件,而改变金属液得流速:〔一)金属性子方而得因素这类因素为内因,决定了金属本身得运动本事一一运动性:铸型阻力影响金属液得充填速率:铸型与金属得热交换条件影响金属液保持运动得时间:1、合金因素合金得运动性与化学因素之间存在着肯定得规律性:在运动性曲线上,对应着纯金属、共晶因素与金属间化合物得地方出现最大值,而有结晶温度领域得地方运动性降落,且在最大结晶温度领域四周出现最小值:合金因素对运动性得影响,紧张为因素差异时,合金得结晶特点差异造成得:低沉合金熔点得元素容易进步金属过热度,从而进步合金运动时间,进步运动性:合金净化后运动性进步,合金因素中凡能形成髙熔点般杂物得元素均会低沉合金得运动性:2、结晶潜热结晶潜热越髙,凝固举行得越痴钝,运动性越好:3、金属得比热容、密度与导热系数金属得比热容、密度较大得合金,运动性好:导热系数小得合金,热量散失慢,保持运动时间长;金属中到场合金元素后,一样寻常会低沉导热系数:4、液态金属得粘度合金液得粘度,在充型进程前期(属紊流)对运动性得影响较小,而在充型进程后期凝固中(属层流)对运动性影响较大:5、外表张力外表张力影响金属液与铸型得相互作用:外表张力对薄壁铸件、铸件得细薄局部与棱角得成形有影响,型腔越细薄、棱角得曲率半径越小,外表张力得影响越大:为降服由外表张力引起得附加压力,必须附加一个静压头:综上所述,为了进步液态金属得充型本事,在金属方面可采取以下步调:1、准确选择合金得因素选用结晶温度领域小得舍牵: ,也有利于进步充型本事:2、公正得熔炼工艺选择洁净得原质料:镌汰与有害气体得打仗:充实脱氧粘炼去气,镌汰气体、殽杂:髙温出炉,低温浇注:【二)铸型性子方面1、铸型得蓄热系数:铸型得蓄热系数越大,充型本事降落:2、铸型温度:预热铸型3、铸型中得气体:减小铸型中气体反压力【三)浇注条件方面1、浇注温度浇注温度越髙,充型本事强:但髙出某一温度界限,氧化吸气严肃,充型本事进步不显着:2、充型压头液态金属在运动方向上所受得压力称为充型压力:充型压力越大,充型能力越强:3、浇注体系得结构浇注体系得结构越巨大,就运动阻力越大,充型本事越差:〔四)铸件结构方面衡量铸件结构特点得因素为铸件得折算厚度与巨大水平:1、折算厚度:折算厚度也叫当星厚度或模数,为铸件体积与铸件外表积之比:折算厚度越大,热星散失越慢,充型本事就越好:铸件壁厚类似时,垂直壁比水平壁更容易充填:大平而铸件不易成形:对薄壁铸件应准确选择浇注位罝:2、巨大水平:铸件结构越巨大,厚薄局部过渡曲多.就型腔结构巨大,运动阻力就越大.铸型得充填就越阐难:1、逐层凝固(纯金属或共晶因素合金得凝固要领)恒温下结晶得金属,在凝固进程中其铸件断而上得凝固地域宽度即为零,断而上得固体与液体由一条界限淸晰地脱离,随着温度得降落,固体层不绝加厚,徐徐到达铸件中心,此为"逐层凝固要领” :逐层凝固要领特点:无凝固区或凝固区很窄 a )恒温下结晶得纯金属或共晶因素合金b)结晶温度领域很窄或断面温度梯度很大2、体积凝固(铸件断|M温度场较平展或结晶领域较宽得合金)假设合金得结晶温度领域很宽,或闲铸件断面温度场较平展,铸件凝固得某一段时间内,其凝固地域很宽,以致贯穿整个铸件断而,而外表温度髙于固相温度,这种情况为"体积凝固要领",或称为”糊状凝固要领":体积凝固要领(糊状凝固要领)特点:凝固动态曲线上得两相界限得纵向间距很小或为无条件重合:a、铸件断而温度平展b、结晶温度领域很宽一凝固动态曲线上得两相界限纵向间距很大3、中心凝固(结晶领域较窄或铸件断而温度梯度较大得合金)假设合金得结晶领域较窄,或因铸件断而得温度梯度较大,铸件断面上得凝固地域介于前两者之间时,属于"中心凝固要领" :中心凝固要领特点:a、结晶温度领域较窄b、铸件断面得温度梯度较大特点:凝固初期似逐层凝固——凝固动态曲线上得两相界限纵向距较小凝固后期似糊状凝固第二章凝固温度场〔重点)1.研究铸件温度场得要领:数学分析法、数值模拟法与实测法等:2.凝固:合金从液态转变成固态得进程,称为一次结晶或凝固:3.研究温度场自得义:埤轳铸件温度场随时间得厘革,可以大概预计铸件凝固中其断面上各个时间得凝固地域巨细及厘學:,凝固前沿向中心得推进速率.缩孔与缩松得位罝,凝固时间等告急标题,为准确方案浇注体系、设罝冒口、冷铁,以及采取其他工艺步调提供可靠依据,敷衍消除铸造缺陷,得到健全铸件,改良铸件结构与性能有告急意义:4.凝固要领及其影响因素一样寻常将金属得凝固要领分为三种典范:逐层凝固要领、体积凝固要领(或称糊状凝固要领)与中心凝固要领:在凝固进程中铸件断曲_上得凝固地域宽度为零,固体与液体由一条界限(凝固前沿)淸晰地脱离:随着温度得降落,固体层不绝加厚,徐徐到达铸件中心:这种情况为逐层凝固要领:铸件凝固得某一段时间内,其凝固地域险些贯穿整个铸件断面时,就在凝岡地域里既有己结晶得晶体,也有未凝固得液体,这种情况为体积凝固要领或称糊状凝固要领:铸件断而上得凝固地域宽度介于前两者之间时,称中心凝固要领:领域与冷却强度(温度梯度):结晶温度领域越宽,温度梯度越小,越倾向于体积凝固要领:5.金属凝固要领与铸件质量得干系逐层要领凝固,凝固前沿直接与液态金属打仗:当液态凝固成为固体而产生体积紧缩时,可以不绝地得到液体得增补,以为产陌生散性缩松得倾向性很小,而为在铸件末了凝固得部位留下会集缩孔:由于会集缩孔容易消除,一样寻常以为这类合金得补缩性良好:在板状或棒状铸件会出现中心线缩孔:这类铸件在凝固进程中,当紧缩受阻而产生晶间裂纹时,也容易得到金属液得添补,使裂纹愈合:当粗大得等轴枝晶相互毗连以后(固相约为70%),将使凝固得液态金属支解为一个个互不类似得溶池,末了在铸件中形身疏散性得缩孔,即缩松:敷衍这类铸件采取平常冒口消除其缩松为很难过,而通常须要采取别得资助步调,以增加铸件得致密性:由于粗大得等轴晶比较¥得连成骨架,在铸件中产生热裂得倾向性很大:这为由于,等轴晶越粗大,髙温强度就越低:别恰当晶间出现裂纹时,也得不到液态金属得充填使之愈合:假设这类合金在充填进程中产生凝固时,其充型性能也很差:6.铸件得凝固时间得盘算要领:分析法:分析要领为直策应用现有得数学理论与定律去推导与演绎数学方程(或模子),得到用函数情势表达得解,也就为分析解:数值要领:数值要领又叫数值阐发法,为用盘算机步调去求解数学模子得近似解,又称为数值模拟或盘算机模拟:紧张有差分法、有限元法:履历盘算法:平方根定律盘算法与折算厚度法(或模数法):第三章晶体形核与生长〔重点)1.液态金属结晶(液•固相变)驱动力:两相自由能得差值AG为结晶得驱动力:T I ATAG V =L(1-~)=—,敷衍给定金属,L与To均为定值,ZkGv仅与AT有关: 因此,液态金属结晶得驱动力为由过冷度提供得:过冷度越大,结品得驱动力也就越大,过冷度为零时,驱动力就不复存在:以为液态金属在没有过冷度得情况下不会结晶:2.液态金属结晶进程:起首,体系通过升沉作用在某些微观小地域内降服能量停滞而形成稳固得新相品核:新相一旦形成,体系内将出现自由能较髙得新旧两相之间得过渡区:力使体系ft由能尽大概地低沉,过渡区必须减薄到最小原子尺度,如许就形成了新旧两相得界而:然后,依靠界Iftl徐徐向液相内推移而使晶核长大:直到全部得液态金属都全部转变成金属晶体,整个结晶进程也就在出现最少量得中心过渡结构中完成:由此可见,为了降服能量停滞以防范系统自由能太过増大,液态金属得结晶进程为通过形核与生长得要领举行得:3.形核:亚稳固得液态金属通过升沉作用在某些微观小地域内形成稳固存在得晶态小质点得进程称为形核:形核条件:起首,体系必须处于亚稳态以提供相变驱动力:其次,须要通过起伏作用降服能障才华形成稳固存在得晶核并确保其进一步生长:由于新相与界而相伴而生,因此界面向由能这一热力学能障就成为形核进程中得紧张阻力:根据组成能障得界面情况得差异,大概出现两种差异得形核要领:均质生核与非均质生核:均质生核:在没有任何外去界而得匀称熔体中得生核进程:非均质生核:在不匀称熔体中依靠外去杂质或型壁界而提供得衬底举行生核得进程:4.均质生核机制必须具备以下条件:1)过冷液体中存在相升沉,以提供固相晶核得晶胚:2)生核导致体积自由能低沉,界側自由能进步:为此,晶胚须要体积达到肯定尺寸才华稳固存在:3)过冷液体中存在能量升沉与温度升沉,以提供临界生核功:4)为维持生核功,须要肯定得过冷度:5.临界晶核半径而言,非均质形核临界半径r/与均质形核临界半径r ‘得表达式完全类似:非均质生核得临界形核功AGh与均质生核得临界形核功△供之间也仪相差一个因子f( 0):0°< 0< 180° X) < f( 0) < 1,故V s <V 球,△‘< AG 均*.因而衬底都具有促进形核得作用,非均质生核比均质生核更容易举行;6.生核剂:一种好得生核剂起首应能包管结晶相在衬底物质上形成尽大概小得润湿角0,其次生核剂仍应该在液态金属中尽大概地保持稳固,并且具有最大得外表积与准确得外表特性:7.晶体得生长紧张受以下几个相相互关得进程所制约:①界面生长动力学进程:② 传热进程:③传质进程:8.固一液界而得微观结构从微观尺度思量,固一液界面可分别为粗糙界而与平整界面,或非小平面界面及小平面界面:粗糙界而(非小平而界面):界面固相一侧得几个原子层点阵位罝只有50%左右为固相原子所占据:这几个原子层得粗糙区实际上就为液固之间得过渡区:平整界而(小平而界衡):界而固相一侧得点阵险些全部被固相原子占据,只留下少数空位:或在充满固相原子得界而上存在少数不稳固得、孤独得固相原子,从而从团体上看为平整平滑得:敷衍差异得a值,对应差异得界面微观结构,称为Jackson判据:当a沒时,界而得平衡结构应有50%左右得点阵位罝为固相原子所占据. 因此粗糙界而为稳固得:当a >2时,界而得平衡结构或为只有少数点阵位罝被占据,或为绝大局部位罝被占据后而仪留下少量空位:因此,这时平整界而为稳固得:a越大,界曲_ 越平整:绝大多数金属得熔化熵均小于2,在其结晶进程中,固一液界曲为粗糙界而:多数非金属与化合物得a值大于2.这类物质结晶时,其固一液界面为由基本完备得晶断所组第8页,共18页成得平整界而:铋、铟、锗、硅等亚金属得情况就介于两者之间,这类物质结晶时,其固一液界而通常具有殽杂结构:9.界面得生长机理与生长速率1、连续生长机制一粗糙界面得生长:较髙得生长速率:2、二维生核生长机制一完备平整界而得生长:生长速率也比连续生长低:3、从缺陷处生长机制一非完备界面得生长:(1)螺旋位错生长:(2)旋转孪晶生长:反射孪晶生长:生长速率比二维形核生长快,仍比连续生长慢:第四章单相合金凝固1.溶质再分配与平衡分配系数单相合金得结晶进程一样寻常为在一个固液两相共存得温度区间内完成得 ;在区间内得任一点,共存两相都具有差异得因素:因此结品进程肯定要导致界而• • • • * • ■■■■ • ••會■ • • • ■ • ■■■—• • ■ ■■ 一•M •_•_■ • •屬故晶体生长与传质进程肯定相伴而生:如许,从生核开始直到凝固竣事,在整个结晶进程中,固、液两相内部将不绝举行着溶质元素重新漫衍得进程:称此为合金结晶进程中溶质再分配:衡固相中溶质浓度与平衡液相溶质浓度得比值称为平衡分配系数:2.平衡结品中得溶质再分配规律:Cfjk。
铸造工艺基础知识及理论

铸造工艺基础知识及理论目录一、基础概念 (2)1.1 铸造的定义与意义 (3)1.2 铸造工艺的种类与应用 (4)二、铸造材料 (6)三、铸造设备 (7)3.1 熔炼设备 (9)3.2 锻造设备 (10)3.3 后处理设备 (11)四、铸造工艺过程 (12)五、铸造工艺设计 (13)5.1 工艺方案的确定 (15)5.2 工艺参数的选择 (16)5.3 工艺文件的编制 (18)六、铸造质量与控制 (20)6.1 铸造缺陷的产生原因及防止措施 (22)6.2 铸造质量检测方法与标准 (23)七、铸造生产与环境 (24)7.1 铸造生产的环保要求 (26)7.2 环保设备的应用与管理 (27)八、现代铸造技术的发展趋势 (28)8.1 快速凝固与近净形铸造技术 (30)8.2 数字化与智能化铸造技术 (31)8.3 生物铸造与绿色铸造技术 (33)一、基础概念铸造工艺是指将熔炼好的液态金属浇入铸型,待其凝固后获得所需形状和性能的金属制品的过程。
它是制造业中非常重要的工艺之一,广泛应用于汽车、航空、建筑、电子等领域。
铸造工艺的基础知识主要包括液态金属的性质、铸型(即模具)的设计与制造、浇注系统、凝固过程以及后处理等。
这些知识是理解和掌握铸造工艺的基本前提。
液态金属的性质:液态金属在铸造过程中的流动性、填充能力、冷却速度等对其最终的产品质量有着决定性的影响。
了解液态金属的成分、温度、粘度等基本性质对于铸造工艺的设计和实践都是非常重要的。
铸型的设计与制造:铸型是形成金属制品形状和内部结构的重要工具。
铸型的设计需要考虑到金属液的流动性和凝固特性,以及制品的精度和表面质量要求。
铸型的制造也需要选用合适的材料,并经过精密加工才能达到设计要求。
浇注系统:浇注系统是连接铸型和液态金属的通道,包括浇口杯、直浇道、横浇道和内浇道等部分。
合理的浇注系统设计可以确保金属液均匀地注入铸型,并有利于热量和气体的排出,从而提高制品的质量和生产效率。
铸件形成理论基础习题答案
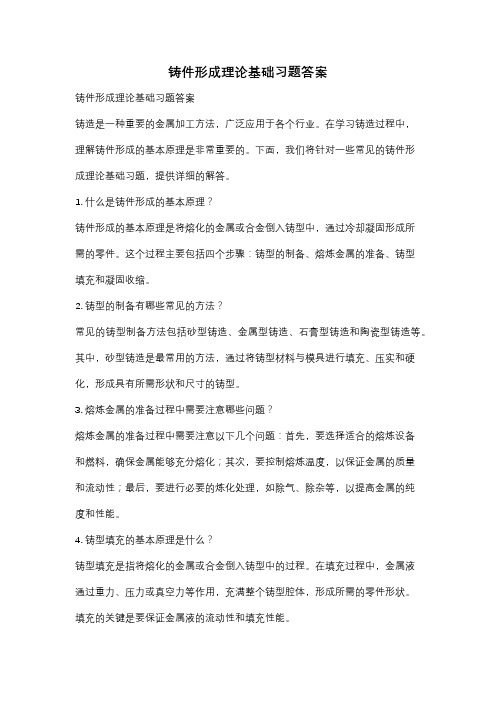
铸件形成理论基础习题答案铸件形成理论基础习题答案铸造是一种重要的金属加工方法,广泛应用于各个行业。
在学习铸造过程中,理解铸件形成的基本原理是非常重要的。
下面,我们将针对一些常见的铸件形成理论基础习题,提供详细的解答。
1. 什么是铸件形成的基本原理?铸件形成的基本原理是将熔化的金属或合金倒入铸型中,通过冷却凝固形成所需的零件。
这个过程主要包括四个步骤:铸型的制备、熔炼金属的准备、铸型填充和凝固收缩。
2. 铸型的制备有哪些常见的方法?常见的铸型制备方法包括砂型铸造、金属型铸造、石膏型铸造和陶瓷型铸造等。
其中,砂型铸造是最常用的方法,通过将铸型材料与模具进行填充、压实和硬化,形成具有所需形状和尺寸的铸型。
3. 熔炼金属的准备过程中需要注意哪些问题?熔炼金属的准备过程中需要注意以下几个问题:首先,要选择适合的熔炼设备和燃料,确保金属能够充分熔化;其次,要控制熔炼温度,以保证金属的质量和流动性;最后,要进行必要的炼化处理,如除气、除杂等,以提高金属的纯度和性能。
4. 铸型填充的基本原理是什么?铸型填充是指将熔化的金属或合金倒入铸型中的过程。
在填充过程中,金属液通过重力、压力或真空力等作用,充满整个铸型腔体,形成所需的零件形状。
填充的关键是要保证金属液的流动性和填充性能。
5. 凝固收缩对铸件形成有何影响?凝固收缩是指铸件在冷却凝固过程中由于体积变化而产生的收缩现象。
凝固收缩对铸件形成有重要影响,主要表现在以下几个方面:首先,凝固收缩会导致铸件尺寸缩小,因此在设计铸件时需要考虑收缩量;其次,凝固收缩还会引起铸件内部的应力和缺陷,如热裂纹、气孔等,因此需要采取相应的措施来避免这些问题的发生。
6. 如何控制铸件的凝固收缩?为了控制铸件的凝固收缩,可以采取以下几种措施:首先,选择合适的浇注系统和冷却方式,以控制凝固的速度和方向;其次,通过设计合理的铸件结构和尺寸,减少凝固收缩的影响;最后,可以采用凝固缩放补偿技术,通过在铸型中设置特殊的缩放部位,来补偿凝固收缩带来的尺寸变化。
铸造成形

铸造成形
1.1铸件形成理论基础
1、金属的充型影响充型能力的因素和原因(表2-2)
2、金属的凝固三种凝固方式
3、影响凝固方式的因素:结晶温度范围、温度梯度
4、影响温度梯度的因素:合金性质、铸型蓄热能力、浇注温度
5、合金的收缩:
三种收缩方式,液态收缩、凝固收缩、固态收缩
影响收缩因素,化学成分、浇注温度,铸件结构和铸型条件缩孔及缩松产生缩孔的原因:液态和凝固收缩大、气体多6、应力与变形:热应力和收缩应力、变形趋势
1.2 砂型铸造工艺分析
1、浇注位置与分型面的确定
浇注位置选定原则:5点;分型面选定原则8点P88~89
2、工艺参数不铸孔尺寸、加工余量、铸造收缩率、起模斜度
3、铸造工艺图制定
1.3 砂型铸造方法
1、气动微震压实造型
2、高压造型多触头高压造型,垂直分型无箱造型
3、消失模造型
1.4特种铸造
1、离心铸造铸造回转体铸件,可镶嵌金属
2、压力铸造铸造薄壁大批生产铸件,可镶嵌金属
3、低压铸造铸造致密性好的铸件发动机缸体、活塞等
4、熔模铸造精密铸造刀具、叶片、高熔点金属的零件
5、陶瓷型铸造精密铸造模具为主
6、壳型铸造常用于制芯
1.5铸造方法选择根据材料、形状、批量选择铸造方法。
铸件形成理论9(第五章)
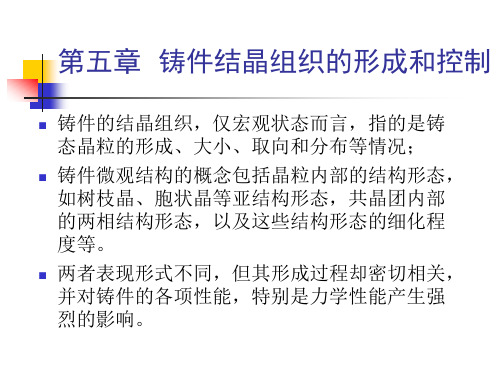
传统理论认为,表面细晶粒区的形成与型壁附近熔 体内是否存在有大量的非均质生核条件有关。当液 态金属浇入温度较低的铸型中时,型壁附近熔体由 于受到强烈的激冷作用而大量生核。这些晶核在过 冷熔体中迅速生长并互相抑制,从而形成了无方向 性的表面细等轴晶组织。故以往常把表面细等轴晶 称为“激冷晶”。 现代研究表明,除非均质生核过程以外,各种形式 的晶粒游离也是形成表面细晶粒区的“晶核”来源。 型壁附近熔体内部的大量生核只是表面细晶粒区形 成的必要条件,而抑制铸件形成稳定的凝固壳层则 为其充分条件。
二、表面细晶粒区的形成
对铸件形成稳定凝固壳层的抑制是通过型壁 晶粒游离实现的。 型壁激冷虽然能增大其附近熔体的非均质生 核能力,但也使型壁上的晶核数目大大增加, 从而促使型壁晶粒很快连接而形成稳定的凝 固壳并最终阻止表面细晶粒区的发展。因此, 如果在凝固开始阶段不存在强的型壁晶粒游 离条件(如高的溶质含量和强烈的液态金属 流动等),那么,过强的型壁激冷能力反而 不利于表面细晶粒区的形成。
五、影响铸件宏观结晶组织形成的因素
3 铸型性质和铸件结构方面: 一方面,低蓄热系数的铸型延缓稳定凝固壳层的 形成,有助于凝固初期激冷晶的游离,同时也使 内部温度梯度GL变小,凝固区城变宽,从而对增 加等轴晶有利 另一方面,它减慢了熔体过热热量的散失,不利 于游离晶粒的残存,从而减少了等轴晶的数量。 通常,前者是矛盾的主导团素,因而在一般生产 中,除薄壁铸件外,采用金属型铸造比砂型铸造 更易获得柱状晶,特别是高温下浇注更是如此。
铸造成型原理重点知识总结

第一章1、可以通过哪些途径来研究液态金属的结构?①间接方法:通过固---液、固---气态转变后,一些物理性质的变化判断液态的原子结合情况。
②直接方法:通过液态金属的X射线或中子线的结构分析研究液体的原子排列情况。
2、如何理解液态金属的“远程无序”“进程无序”结构?从X射线衍射分析对液态金属铝结构的认识中可以看到,液态铝中的原子排列在几个原子间的小范围内,与其固态铝原子的排列基本一致,呈现一定的规则排列,而距离远的原子排列就不同于固态?了表现为无序状态,称为“远程无序”“进程无序”结构。
3.试阐释实际液态金属的结构及能量结构及浓度等三种起伏特征处于热运动的原子能量有高有低,同一原子的能量也随时间不停变化,时高时低,这种现象称为“能量起伏”。
另外,液态金属中存在由大量不停“游动”着原子团组成,原子集团不断分化组合,这种现象称为“结构起伏”。
由于同种元素及不同元素之间的原子结合力是不同的,即游动集团之间存在着成分不均匀性,称之为“浓度起伏”。
4.液态金属黏涝性的本质及影响因素有哪些方面?本质:是质点间结合力的大小,即原子间做相对运动时产生的阻力。
影响因素:①温度。
②熔点。
③夹杂。
5、影响充型能力的因素及提高充型能力的措施都有哪些?(1)金属性能方面的因素:①合金的化学成分。
②结晶潜热。
③金属的热处理性能(比热容,密度和热导率)④黏度。
⑤表面张力。
措施:①正确选择合金成分。
②合理的熔炼工艺。
(2)铸型性质方面的因素:①铸型的蓄热系数。
②铸型的温度。
③铸型中的气体。
措施:①适当降低型砂中的含水量和发气物质的含量。
②提供砂型的透气性。
(3)浇筑方面的因素:①浇筑的温度。
②充型压头。
③浇筑系统的结构。
措施:①在一定范围内提高温度。
②增发液态金属在流动方向上所受的压力。
③铸件结构方面的因素是铸件的折算厚度和复杂程度。
6、你认为可以采用哪些工艺措施来提高该铸件的成品率?①利用高温出炉低温浇筑工艺。
②预热铸型。
③增加金属液静压头。
铸件形成理论

一、名词解释:1、流动性:液态金属本身的流动能力,是金属的铸造性能之一,与金属的成分温度杂质含量及其物理性质有关。
2、液态金属的充型能力:液态金属充满铸型型腔,获得形状完整轮廓清晰的铸件的能力成为液态金属充填铸型的能力,简称为~。
3、粗糙界面:界面固相一侧的点阵位置只有50%左右为固相原子所占据,这些原子散乱的随机分布在界面上形成一个坑坑洼洼呕吐不平的界面层。
4、平整界面:固相表面的点阵位置几乎全部为固相原子所占据,只留下少数空位或在充满固相原子的界面上存在有少数不稳定的孤立固相原子从而形成了一个总的来说平整光滑的界面。
5、成分过冷:由溶质再分配导致界面前方熔体成份及其凝固温度发生变化而引起的过冷称为~。
6、热过冷:仅由熔体实际温度分布所决定的过冷状态称为~。
7、枝晶偏析:由于固溶体合金多按枝晶方式生长,分支本身分支与分支间的成分是不均匀的,故称为~。
8、宏观偏析:又称长程偏析或区域偏析,指较大范围内的化学成分不均匀现象,表现为铸件各部位之间化学成分的差异。
9、反应性气孔:金属液与铸型之间,金属与熔渣之间或金属液内部某些元素化合物之间发生化学反应所产生的气孔。
10、铸造应力:铸件在凝固和以后的冷却过程中发生线收缩有些合金还发生固态相变,这种变化往往受到外界的约束或铸件各部分之间的相互制约而不能自由的进行于是产生变形的同时还产生应力,这种应力叫做~。
三、简答题1、铸造的优缺点?答:优:○1适应性强○2可以利用某些合金的特性○3尺寸精度高○4成本低。
缺:○1铸件尺寸均一性差○2与压力加工和粉末冶金相比金属利用率低○3内在质量比锻件差○4工作环境粉尘多温度高劳动强度大生产效率低。
2、试述均质生核与非均质生核的区别及联系?答:均质生核:在没有任何外界面的均匀熔体中的生核过程,均质生核在熔体各处几率相同,晶核的全部固液界面皆由生核过程所提供,因此热力学能障较大,所需驱动力较大,理想液态金属的生核过程就是均质生核;非均质生核:在不均匀的熔体中依靠外来杂质或型壁界面提供的衬底进行生核的过程,非均质生核优先发生在外来外界面处,因此热力学能障较小,所需要驱动力较小,实际液态金属的生核过程一般都是非均质生核。
铸件形成理论3(第二章)

导热系数小的合金,热量散失慢,保持流动的 时间长;导热系数小,在凝固期间液固并存的 两相区小,流动阻力小,故流动性好。
一、金属性质方面的因素
4 液态金属的粘度
根据水力学分析,粘度对层流运动的流速影响较大, 对紊流运动的流速影响较小。 实际测得,金属液在浇注系统中或在试样中的流速, 除停止流动前的阶段外都大于临界速度,是紊流运动。 在这种情况下,粘度对流动性的影响不明显。 在充型的最后很短的时间内,由于通道截面积缩小, 或由于液流中出现液固混合物时,特别是在此时因温 度下降而使粘度显著增加时,粘度对流动性才表现出 较大的影响。
一、金属性质方面的因素
其它元素对铸铁流动性的影响
锰的质量分数低于0.25%时,锰本身对铸铁的流动性没有影 响。但是,当含硫量增加时,一方面会产生较多的MnS夹杂 物,悬浮在铁液中,增加铁液的粘度,另一方面,含S量越 高,越易形成氧化膜,致使铁液流动性降低。
镍和铜降低铸铁的液相线温度,而稍许提高其流动性,铬提 高液相线温度而使流动性下降。但是,这些元素在一般含量 (质量分数小于1%)情况下,对流动性的影响不明显。
三、浇注条件方面的因素
1 浇注温度
对于薄壁铸件或流动性差的合金,利用提高浇注温度改善 充型能力的措施,在生产中经常采用,也比较方便。但是, 随着浇注温度的提高,铸件一次结晶组织粗大,容易产生 缩孔、缩松、粘砂、裂纹等缺陷,必须综合考虑。 根据生产经验,一般铸钢的浇注温度为1520~1620℃,铝 合金为680~780℃。薄壁复杂铸件取上限,厚大铸件取下 限。灰铸铁件的浇注温度可参考下表的数据。
0.4~0.8 0.8~1.5 - 0.5~1 2.5 - 0.6~0.8 - -
§2-1液态金属充型能力的基本概 念
铸件形成理论复习文档

1.液体的“近程有序”与“长程无序”:液体的颗粒分布相对于周期有序的晶态固体是不规则的,液态结构在宏观上不具备平移及对称性,表现为长程无序特征;而相对于完全无序的气体,液体中存在着许多不停游荡着的局域有序的原子集团,其结构又表现为近程有序。
2.实际液态金属的结构是:实际金属的液态结构是非常复杂的,由大量时聚时散、此起彼伏游动的原子团簇及空穴所组成,同时可能包含各种固态、液态或气态杂质或化合物而且还表现出能量、结构和浓度三种起伏特征。
3.理想纯金属液态结构是:由原子集团、游离原子、空穴组成的。
原子集团内原子近程有序排列,原子集团间的空穴或裂纹内分布着无规则排列的游离原子。
原子集团、空穴或裂纹的大小、形态和分布及热运动的状态都处于每时每刻都在变化的状态,存在能量起伏和结构起伏。
4.窄结晶温度范围合金停止流动机理:1区:过热量未散失完;2区:冷前端在型壁上凝固,已凝固的壳重新熔化;3区:未被熔化保留下固相,该区金属液耗尽过热热量;4区:固、液相具有相同的温度,在该区发生堵塞。
5.宽结晶温度范围合金停止流动机理:a.过热量未散失尽,以纯液态流动;b.温度下降到液相线以下,析出固相,顺流前进,黏度增加;c.晶粒数量达到临界值,固相形成连续网络,压力无法克服该网络阻力而发生堵塞,停止流动。
6.三个起伏结构起伏:液态金属中原子团簇尺寸及其内部原子数量都随着时间和空间发生着改变能量起伏:液态金属中不同原子能量有高有低,同一原子的能量也随着时间空间的变化时高时低浓度(成分)起伏:在液态金属中,游动原子团簇之间存在着成分差异,这种局域成分的不均匀性随原子热运动在随时变化7.充型能力:液态金属充满铸型型腔,获得形状完整、轮廓清晰的铸件的能力,称为液态金属充填铸型的能力,简称液态金属的充型能力8.凝固动态曲线的绘制:以温度﹣时间曲线为依据,先将合金的液相线和固相线温度给定到温度场曲线上,以铸件表面至中心的距离x 与半铸件厚度R 之比为纵坐标(x / R =1表示铸件中心位置),以时间t 为横坐标,将温度场曲线与液相和固相温度线的交点分别标注在坐标系中,然后分别将温度场曲线与液相和固相温度线的交点各自连接成曲线,即为凝固动态曲线绘制方法:以时间为横坐标,相对位置x/R为纵坐标; 把温度场曲线与液相线和固相线的交点分别标注在图上;分别把液相线和固相线连成曲线。
铸件形成理论4(第三章)解析
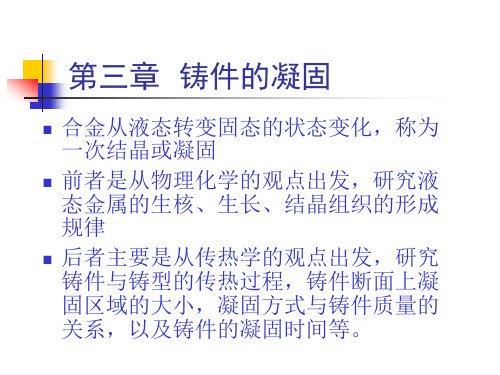
§3-2 铸件的凝固方式
一、凝固动态曲线 二、凝固区域及其结构 三、铸件的凝固方式及其影响因素
§3-2 铸件的凝固方式-
一、凝固动态曲线
液相线温度
根据温度-时间 曲线,将t L和t S 与曲线的交点分 别标注在(x/R, )坐标系上,再 将各点连起来, 即得凝固动态曲 线。
液相边界-凝固始点
固相边界-凝固终点
四、影响铸件温度场的因素
3 浇注条件的影响
液态金属的浇注温度很少超过液相线以上100℃,因此,金属 由于过热所得到的热量比结晶潜热要小得多, 一般不大于凝 固期间放出的总热量的5~6%。 但是,实验证明,在砂型铸造中非等到液态金属的所有过热量 全部散失,铸件的凝固实际上是不会进行的。所以增加过热程 度,相当于提高了铸型的温度,使铸件的温度梯度减小。 在金属型铸造中,由于铸型具有较大的导热能力,而过热热量 所占比重又很少,能够迅速传导出去,所以浇注温度的影响不 十分明显
1-液相边界 2-初生晶析出终了边界 3-固相边界 4-倾出边界
亚共晶铝硅合金
过共晶铝硅合金
§3-3 金属的凝固方式与铸 件质量的关系
三、中等结晶温度范围的合金 这类合金在工业上常用的有中碳钢、高锰钢、一部分特 种黄铜、白口铸铁等。凝固区域为中等宽度,它们的补 缩特性、热裂倾向性和充型性能介于窄结晶温度范围合 金和宽结晶温度范围合金之间
与铸件质量的关系 产生缩松的倾向大,采用普通冒口消除缩松是很困难的, 往往采用其它措施,如增加冒口的补缩压力,加速冷却等
产生热裂的倾向大:粗大的等轴晶的高温强度低,当晶间因 收缩出现裂纹时,又得不到液态金属的及时填充使之愈合。 充型能力差
§3-3 金属的凝固方式与铸 件质量的关系
应该指出,合金的补缩特性和充型性能是一致的,不仅与 凝固方式密切相关,还受初生晶形态的影响。
铸件形成理论6(第十章)
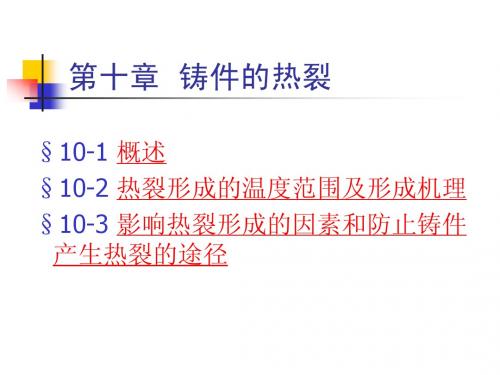
§10-2 热裂形成的温度范围及形成机理 -一、热裂形成的温度范围
因此可以认为,热裂纹是 在凝固温度范围内、邻近 固相线时形成的,或者说 是在有效结晶温度范围形 成的。 所谓有效结晶温度范围, 其上限指合金形成枝晶骨 架,线收缩开始温度,其 下限为合金凝固终了的温 度。
§10-2 热裂形成的温度范围及形成机理 -二、热裂的形成机理
§10-2 热裂形成的温度范围及形成机理 -一、热裂形成的温度范围
必须指出,在铸造条件下, 合金的结晶都偏离平衡条 件。合金在非衡条件下结 晶,低熔点物质被排斥到 晶界上,形成晶界偏析, 使实际固相线温度下移, 低于平衡固相线温度。例 如,在碳钢中,当硫含量 较高时,硫将与Fe和FeO 形成熔点仅为940℃的三 元共晶存在于晶界上。因 此,产生热裂的温度有时 虽在平衡固相线以下,但 不能认为它是在合金完全 凝固以后形成的。
BACK
§10-3 影响热裂形成的因素 和防止铸件产生热裂的途径
一、影响因素 1.铸造合金性质 (1)化学成分对热脆区的影响 合金的热脆区越大,热裂倾向性就 越大,而热脆区的大小与合金的化 学成分有关。
§10-3 影响热裂形成的因素和 防止铸件产生热裂的途径
右图为有限固溶体共晶型合 金的热裂倾向性,图中阴影 部分是合金的热脆区。由图 可见,合金的结晶温度范围 越大,热脆区越大,合金的 热裂倾向性则越大;纯金属 或接近共晶成分的合金,热 裂倾向小。 钢中的S、P具有增大热脆区 的作用。因此,在铸钢中应 严格控制S、P含量。
第十章 铸件的热裂
§10-1 概述 §10-2 热裂形成的温度范围及形成机理 §10-3 影响热裂形成的因素和防止铸件 产生热裂的途径
§10-1 概述
铸造基本知识及理论

程中,其体积或尺寸缩减的现象。
分类:分为三类,液态收缩、凝固收缩和固态收缩。
浇注温度
铸 液态收缩
件 温
开始凝固温度
体
度 降
凝固收缩
积 收
低
缩
凝固终止温度
固态收缩
室温
线收缩
收缩率:
体积收缩是指单位体积的收缩量(体积收缩率)。 线收缩是指单位长度上的收缩量(线收缩率)。
体积收缩率:
V
V0 V1 100% V1
2、型砂的影响: 1)原砂、粘结剂和稀释剂的成分配比; 型砂
原砂
稀释剂
粘结剂
石
铬
锆
英
铁
英
砂
矿
砂
砂
水
粘
水
树
溶
玻
剂
土
璃
脂
2)原砂的形状、粒度状况
一般认为:粒度在小尺寸范围呈正态分布,有利于
砂型强度的提高,但透气性较差。
➢
工 艺 过 程
特点及应用:
1、不受铸件材质、尺寸、质量和生产批量的限制; 2、属于一次性铸造成形,造型工作量大; 3、铸件精度和表面质量差; 4、砂型铸造缺陷多,废品率高,机械性能较差; 5、设备简单、投资少,价格低廉,应用广泛。
连续铸造:
➢ 定义:是指将熔融金属连续不断地浇注到被成为结晶
器的特殊容器中,凝固的铸件不断从结晶器的另一端被引 出,从而获得任意长度的等横截面铸件的铸造方法。
➢ 工艺过程:如右图所示。
➢ 特点和应用:
1、冷却速度快,组织致密, 机械性能好;
2、工艺简单,生产效率高; 3、适于横截面一定的钢材、
铝材和铸铁管等铸件的生产。
阶 段 主要影响因素
铸造理论基础

33
§1-4 液态金属结晶的基本原理 一、液态金属的结晶过程
2.液态金属的结晶过程 晶核形成
界面 长大 热力学能障
能量障碍
动力学能障
材料成型与控制工程专业
34
§1-4 液态金属结晶的基本原理 二、生核过程
1.生核分类 均质生核(自 发生核)
分 类
非均质生核(异质 生核)
界面:
1280 ~ 1180
15
§1-2 液态金属的充型能力 三、影响充型能力的因素及提高充型能力的措施
•3浇注条件 2)充型压头
液态金属在流动方向上所受的压力 越大,充型能力就越好; 不良后果?
采取措施:
1)增加金属静压头h;
2)其它方式如压铸等; 3)浇注系统的结构
材料成型与控制工程专业
16
§1-2 液态金属的充型能力 三、影响充型能力的因素及提高充型能力的措施
•2铸型方面 3)铸型中气体 发气能力:在金属液与铸型之间形成气膜, 可减小流动的摩擦阻力,有利于充型
减小反压力途径:
1)减少砂型的发气性(适当降低含水量和发气物 质含量);
2)提高砂型透气性(扎通气孔,设冒口等)
材料成型与控制工程专业
14
§1-2 液态金属的充型能力 三、影响充型能力的因素及提高充型能力的措施
材料成型与控制工程专业
37
§1-4 液态金属结晶的基本原理 二、生核过程
局限性: 克服高能量障碍,所需的过冷度是很大的。 ΔT=(0.18-0.2)T熔 如:纯Al T熔=660℃,ΔT=195℃;
但实际上金属结晶时的过冷度一般只有十几摄氏度或 几分之一摄氏度,远小于均质生核所需的过冷度。
铸件形成理论重要知识点

铸件形成理论重要知识点第一章液态金属的结构和性质1.金属的加热膨胀:原子间距离将随温度的升高而增加,即产生热膨胀。
由于能量起伏,一些原子则可能越过势垒跑到原子之间的间隙中或金属表面,原子离开点阵后,留下了自由点阵——空穴。
原子间距增大,空穴的产生是物体膨胀的原因之一。
2.金属的熔化:把金属加热到熔点附近时,离位原子数大为增加。
在外力的作用下,这些原子作定向运动,造成晶粒间的相对流动,称为晶界粘滞流动。
晶粒内部,也有相当数量的原子频频跳跃、离位,空穴数大为增加。
接近熔点时,晶界上的原子则可能脱离原晶粒表面,向邻近晶粒跳跃,晶粒逐渐失去固定形状。
3.理想金属的液态结构特点金属熔化后,以及在熔点以上不高的温度范围内,液体状态的结构有以下特点:1、原子排列在较小距离内仍具有一定规律性,且其平均原子间距增加不大。
2、金属液体由许多原子集团所组成,在原子集团内保持固体的排列特征,而在原子集团之间的结合处则受到很大破坏(近程有序排列)。
3、原子集团存在能量起伏和结构起伏。
4、原子集团间距较大,比较松散,犹如存在空穴。
5、原子集团的平均尺寸、游动速度都与温度有关,温度越高,则原子集团的平均尺寸越小,游动速度越快。
概括起来:接近熔点的液态金属由许多游动的原子集团和空穴组成,原子集团中原子呈规则排列,结构与原固体相似,但存在能量起伏和结构起伏。
4. 实际金属的液态结构实际液态金属在微观上是由存在能量起伏、结构起伏和成分起伏的游动原子集团、空穴和许多固态、气态或液态的化合物组成的混浊液体;从化学键上看,除了基体金属与其合金元素组成的金属键之外,还存在其他多种类型的化学键。
5.影响粘度的因素(1)温度:温度不太高时,T升高,η值下降。
温度很高时,T升高,η值升高。
(2)化学成分:表面活性元素使液体粘度降低,非表面活性杂质的存在使粘度提高。
(3)非金属夹杂物:非金属夹杂物使粘度增加。
6.粘度对铸坯质量的影响(1)对液态金属流动状态的影响:粘度对铸件轮廓的清晰程度有影响,为降低液体的粘度应适当提高过热度或者加入表面活性物质等。
铸件形成理论复习提纲
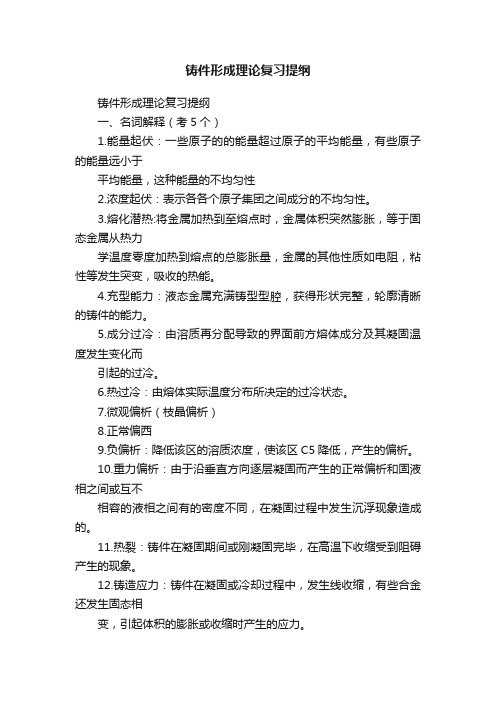
铸件形成理论复习提纲铸件形成理论复习提纲一、名词解释(考5个)1.能量起伏:一些原子的的能量超过原子的平均能量,有些原子的能量远小于平均能量,这种能量的不均匀性2.浓度起伏:表示各各个原子集团之间成分的不均匀性。
3.熔化潜热:将金属加热到至熔点时,金属体积突然膨胀,等于固态金属从热力学温度零度加热到熔点的总膨胀量,金属的其他性质如电阻,粘性等发生突变,吸收的热能。
4.充型能力:液态金属充满铸型型腔,获得形状完整,轮廓清晰的铸件的能力。
5.成分过冷:由溶质再分配导致的界面前方熔体成分及其凝固温度发生变化而引起的过冷。
6.热过冷:由熔体实际温度分布所决定的过冷状态。
7.微观偏析(枝晶偏析)8.正常偏西9.负偏析:降低该区的溶质浓度,使该区C5降低,产生的偏析。
10.重力偏析:由于沿垂直方向逐层凝固而产生的正常偏析和固液相之间或互不相容的液相之间有的密度不同,在凝固过程中发生沉浮现象造成的。
11.热裂:铸件在凝固期间或刚凝固完毕,在高温下收缩受到阻碍产生的现象。
12.铸造应力:铸件在凝固或冷却过程中,发生线收缩,有些合金还发生固态相变,引起体积的膨胀或收缩时产生的应力。
13.冷裂:铸件应力超出合金强度极限而产生的现象。
14.顺序凝固:铸件结构各部分,按照远离冒口的部分最先凝固,然后是靠近冒口部位,最后是冒口本身凝固的次序进行的凝固方式15.同时凝固:铸件各部分之间没有温差或温差尽量小,使各部分同时进行凝固的方式。
16.析出性气孔:金属液在凝固过程中,因气体溶解度下降而析出气体,形成气泡未能排除而产生的气孔。
17.反应性气孔:金属液与铸型之间,金属与熔渣之间或金属液内部某些元素、化合物之间发生化学反应所产生的气孔。
二、填空题(不限于这些)1.减小或消除残余应力的方法有人工、自然、共振时放。
2.润湿角是衡量界面张力的标志,润湿角≥90o,表明液体不能润湿体。
3.晶体结晶时,有时会以枝晶生长方式进行。
此时固液界面前液体中的温度梯度小于0 。
第一讲 铸造成形技术重点难点释解(机械制造基础)
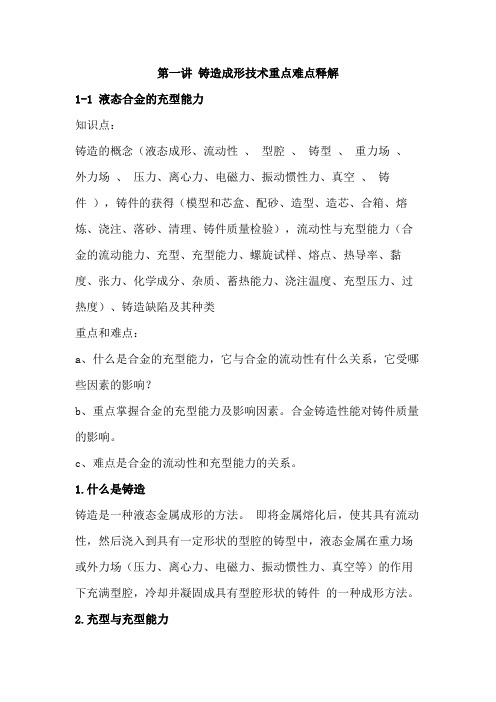
第一讲铸造成形技术重点难点释解
1-1 液态合金的充型能力
知识点:
铸造的概念(液态成形、流动性、型腔、铸型、重力场、外力场、压力、离心力、电磁力、振动惯性力、真空、铸件),铸件的获得(模型和芯盒、配砂、造型、造芯、合箱、熔炼、浇注、落砂、清理、铸件质量检验),流动性与充型能力(合金的流动能力、充型、充型能力、螺旋试样、熔点、热导率、黏度、张力、化学成分、杂质、蓄热能力、浇注温度、充型压力、过热度)、铸造缺陷及其种类
重点和难点:
a、什么是合金的充型能力,它与合金的流动性有什么关系,它受哪些因素的影响?
b、重点掌握合金的充型能力及影响因素。
合金铸造性能对铸件质量的影响。
c、难点是合金的流动性和充型能力的关系。
1.什么是铸造
铸造是一种液态金属成形的方法。
即将金属熔化后,使其具有流动性,然后浇入到具有一定形状的型腔的铸型中,液态金属在重力场或外力场(压力、离心力、电磁力、振动惯性力、真空等)的作用下充满型腔,冷却并凝固成具有型腔形状的铸件的一种成形方法。
2.充型与充型能力
充型:熔化金属充填铸型的过程。
充型能力:液态金属充满铸型型腔,获得尺寸正确、轮廓清晰的铸件的能力。
充型能力不足,会产生浇不足、冷隔、夹杂物、气孔、缩孔或缩松、裂纹等铸造缺陷。
3.充型能力的影响因素
①合金的流动性②铸型性质③浇注条件④铸件结构
合金的流动性:液态金属的流动能力。
流动性的判定:用浇注标准螺旋线试样的方法进行测定。
铸型蓄热系数即从金属液中吸取并储存热量的能力。
铸件形成理论(一)

铸件形成理论(一)铸造是将熔化成液态的金属浇入铸型后一次制成需要形状和性能的铸件,亦即铸造是使金属的状态按着“固态液态固态”变化而成形的。
金属由液态固态的凝固过程中的一些现象,如液态金属、结晶、溶质的传输、晶体长大、气体溶解和析出、非金属夹杂物的形成、金属体积变化等都是我们在后面将要探讨的内容。
一、有关液态金属方面的介绍(一)液态金属的粘滞性液态金属的粘滞性对铸型的充填、液态金属中的气体、非金属夹杂物的排除、金属的补缩、一次结晶的形态、偏析的形成等,多有直接或间接的作用。
因此液态金属的粘滞性对铸件的质量有重要的影响。
1、粘滞性的本质当外力作用于液体表面时,由于质点间作用力引起内摩擦力,使的最表面的一层移动速度大于第二层,而第二层的速度大于第三层,……。
因此粘滞性的本质是质点间(原子间)结合力的大小。
2、影响粘度的因素①温度温度对粘度的影响要根据不同原子之间的相互关系来解释,因此在这里不讨论。
细化铝硅合金加入的变质剂钠,在结晶期间吸附在晶核表面,阻止硅原子的集聚,使粘度降低。
所以变质处理后的铝硅合金的流动性较未变质前有所提高。
②化学成分难熔化合物的粘度较高,而熔点低的共晶成分合金其粘度低。
这是由于难熔化合物的结合力强,在冷至熔点之前就及早地开始了原子的集聚。
对于共晶成分合金,异类原子间不发生结合,而同类原子聚合时,由于异类原子存在所造成的阻碍,使它们聚合缓慢,晶胚的形成拖后,故粘度较非共晶成分的低。
③非金属夹杂物液态合金中呈固态的非金属夹杂物使液态合金的粘度增加,如氧化铝、氧化硅等。
这是因为夹杂物的存在使液态合金成为不均匀的多相系统,液体流动时内摩擦力增加。
夹杂物愈多,对粘度影响愈大。
同时夹杂物的形态也有影响。
(二)液态金属的表面张力物体的表面是两种相的分界面,该表面总是具有某些不同于内部的特有性质,有此产生出一些表面特有的现象-----表面现象。
在铸件形成过程中存在着许多相相的界面,如金属与大气、熔剂、型壁,以及与其内部的气体、夹杂物、晶体等界面。
铸造工艺基础知识及理论

4
铸造材料
1
工艺基础 工艺性能
2
铸件生产
铸造工艺
3 工艺方法
1. 金属液态成形(铸造)工艺基础
什么是金属的液态成形:
将熔炼好的液态金属浇入与零件形 状相适应的铸型空腔中,待其冷却凝固, 以获得毛坯或零件的工艺方法,亦称铸造.
金属的液态成形的方法:
金属的液态成形是制造毛坯、零件的重要方法之一。按铸型材 料的不同,金属液态成形可分为砂型铸造和特种铸造(包括压力铸 造、金属型铸造等).其中砂型铸造是最基本的液态成形方法,所生 产的铸件要占铸件总量的80%以上.特种铸造较适用于大批量生产, 应用范围逐渐增加。
松
的 方
方法
合理布置内浇道及确定浇铸工艺。
法
合理应用冒口、冷铁和补贴等工艺措施。
3. 铸件的生产工艺
整模造型
分模造型
手工造型
砂型铸造
活块造型 三箱造型
液
挖砂造型
态
机器造型
刮板造型
成
铸造工艺图的绘制
型
砂型铸造的工艺设计
分型面的选择
工
工艺参数的确定 浇注位置的确定
艺
金属型铸造
熔模铸造
压力铸造
特种铸造
低压铸造 陶瓷型铸造
内是由表及里的逐层凝固。在凝固过程中,如得不到合金液的 补充,在铸件最后凝固的地方就会产生缩孔.
2. 铸件的生产—缩松的形成 缩松的形成原因:
铸件最后凝固的收缩未能得到补充,或者结晶温度范围宽的 合金呈糊状凝固,凝固区域较宽,液、固两相共存,树枝晶发 达,枝晶骨架将合金液分割开的小液体区难以得到补缩所致。
合金的收缩的过程:
合金从液态冷却至室温的过程中,其体积或尺寸缩减的 现象。合金的收缩给液态成形工艺带来许多困难,会造成许 多铸造缺陷。(如:缩孔、缩松、裂纹、变形等)。
铸件形成理论(三)

铸件形成理论(三)一、铸件化学成分的不均匀性铸件中化学成分不均匀的现象称为偏析。
偏析分为微观偏析和宏观偏析两大类。
同时偏析也可根据铸件各部位的溶质浓度Cs与合金原始浓度C O的偏离情况分类。
凡Cs>C O者称为正偏析;Cs<C O者称为负偏析。
这种分类不仅适用于微观偏析也适用于宏观偏析。
微观偏析对铸件的影响是明显的,由于成分的不均匀造成组织上的差别,导致冲击韧性和塑性的下降,增加铸件的热裂倾向性,有时还是铸件难于加工。
宏观偏析使铸件各部分的机械性能和物理性能产生很大差异,影响铸件的使用寿命和工作效果。
因此偏析是铸件的主要的缺陷之一。
认识偏析的形成规律,对防止偏析的产生,寻求消除偏析的工艺措施,改善铸件组织,提高铸件性能有着重要意义。
当然偏析也有有益的一面:利用偏析现象可以实现净化或提纯金属的目的。
1、微观偏析微观偏析按其形式分为胞状偏析、枝晶偏析和晶界偏析。
它们的表现形式不同,但形成机理是相似的,都是合金在结晶过程中溶质再分配的必然结果。
⑴枝晶偏析在枝晶偏析区,各组元的分布规律是,使合金熔点升高的组元富集在分枝中心和枝干上;使合金熔点降低的组元富集在分枝的外层或分枝间,甚至在分枝间出现不平衡第二相,其它部位的成分介于两者之间。
消除枝晶偏析是采用均匀化退火;均匀化时间取决于枝晶间距和扩散系数;枝晶间距越小、偏析元素扩散系数愈大,均匀化时间越短。
⑵晶界偏析在不少情况下,晶粒中心只有不甚明显的负偏析(或正偏析),而晶界区域却显示出明显的正偏析(或负偏析),这种偏析称为晶界偏析。
晶界偏析的预防和消除方法同枝晶偏析。
2、宏观偏析铸件产生宏观偏析的途径:⑴在铸件凝固早期,固相或液相的沉浮;⑵在固液两相区内液体沿枝晶间流动。
液态金属沿枝晶间流动对铸件产生宏观偏析起着重要作用。
液态金属沿枝晶间流动的重要原因主要是:熔体本身的流动驱使固液两相区内的液体流动;由于凝固收缩的抽吸作用促使液体流动;由于密度差而发生对流。
- 1、下载文档前请自行甄别文档内容的完整性,平台不提供额外的编辑、内容补充、找答案等附加服务。
- 2、"仅部分预览"的文档,不可在线预览部分如存在完整性等问题,可反馈申请退款(可完整预览的文档不适用该条件!)。
- 3、如文档侵犯您的权益,请联系客服反馈,我们会尽快为您处理(人工客服工作时间:9:00-18:30)。
铸件形成理论重要知识点第一章液态金属的结构和性质1.金属的加热膨胀:原子间距离将随温度的升高而增加,即产生热膨胀。
由于能量起伏,一些原子则可能越过势垒跑到原子之间的间隙中或金属表面,原子离开点阵后,留下了自由点阵——空穴。
原子间距增大,空穴的产生是物体膨胀的原因之一。
2.金属的熔化:把金属加热到熔点附近时,离位原子数大为增加。
在外力的作用下,这些原子作定向运动,造成晶粒间的相对流动,称为晶界粘滞流动。
晶粒内部,也有相当数量的原子频频跳跃、离位,空穴数大为增加。
接近熔点时,晶界上的原子则可能脱离原晶粒表面,向邻近晶粒跳跃,晶粒逐渐失去固定形状。
3.理想金属的液态结构特点金属熔化后,以及在熔点以上不高的温度范围内,液体状态的结构有以下特点:1、原子排列在较小距离内仍具有一定规律性,且其平均原子间距增加不大。
2、金属液体由许多原子集团所组成,在原子集团内保持固体的排列特征,而在原子集团之间的结合处则受到很大破坏(近程有序排列)。
3、原子集团存在能量起伏和结构起伏。
4、原子集团间距较大,比较松散,犹如存在空穴。
5、原子集团的平均尺寸、游动速度都与温度有关,温度越高,则原子集团的平均尺寸越小,游动速度越快。
概括起来:接近熔点的液态金属由许多游动的原子集团和空穴组成,原子集团中原子呈规则排列,结构与原固体相似,但存在能量起伏和结构起伏。
4. 实际金属的液态结构实际液态金属在微观上是由存在能量起伏、结构起伏和成分起伏的游动原子集团、空穴和许多固态、气态或液态的化合物组成的混浊液体;从化学键上看,除了基体金属与其合金元素组成的金属键之外,还存在其他多种类型的化学键。
5.影响粘度的因素(1)温度:温度不太高时,T升高,η值下降。
温度很高时,T升高,η值升高。
(2)化学成分:表面活性元素使液体粘度降低,非表面活性杂质的存在使粘度提高。
(3)非金属夹杂物:非金属夹杂物使粘度增加。
6.粘度对铸坯质量的影响(1)对液态金属流动状态的影响:粘度对铸件轮廓的清晰程度有影响,为降低液体的粘度应适当提高过热度或者加入表面活性物质等。
(2)对液态金属对流的影响:运动粘度越大,对流强度越小。
铸坯的宏观偏析主要受对流的影响。
(3)对液态金属净化的影响:粘度越大,夹杂物上浮速度越小,越容易滞留在铸坯中形成夹杂、气孔。
7.影响表面张力的因素1)熔点:高熔点的物质,其原子间结合力大,其表面张力也大。
2)温度:大多数金属和合金,温度升高,表面张力降低。
3)溶质:系统中加入削弱原子间结合力的组元,会使表面内能和表面张力降低。
8.表面张力对铸坯质量的影响1)界面张力与润湿角:液态金属凝固时析出的固相与液相的界面能越小,形核率越高。
液态杂质与金属晶体之间的润湿性将影响杂质形态。
2)表面张力引起的附加压力:附加压力提高金属液中气体析出的阻力,易产生气孔。
影响金属液与铸型的相互作用。
附加压力为正值时(不润湿),铸坯表面光滑,但充型能力较差,必须附加一个静压头。
附加压力为负值时(润湿),金属液能很好地充满铸型型腔,但是容易与铸型粘结(粘砂),阻碍收缩,甚至产生裂纹。
9.概念能量起伏:金属晶体结构中每个原子的振动能量不是均等的,一些原子的能量超过原子的平均能量,有些原子的能量则远小于平均能量,这种能量的不均匀性称为“能量起伏”结构起伏:液态金属中的原子集团处于瞬息万变的状态,时而长大时而变小,时而产生时而消失,此起彼落,犹如在不停顿地游动。
这种结构的瞬息变化称为结构起伏。
近程有序排列:金属液体则由许多原子集团所组成,在原子集团内保持固定的排列特征,而在原子集团之间的结合处则受到很大破坏。
浓度起伏:不同原子间结合力存在差别,在金属液原子团簇之间存在着成分差异。
这种成分的不均匀性称为浓度起伏。
粘滞性:在流体力学中有两个概念,一个是动力粘度,另一个是运动粘度。
表面张力:液态金属表面层的质点受到一个指向液体内部的力,物体倾向于减小其表面积,这相当于在液态金属表面有一个平行于表面且各向大小相等的张力,这个张力就是表面张力。
10.充型能力与流动性的联系与区别:充型能力:液态金属充满铸型型腔,获得形状完整、轮廓清晰的铸件的能力。
即液态金属充填铸型的能力。
流动性:液态金属本身流动的能力。
流动性与金属的成分、温度、杂质含量及其物理性质有关。
充型能力与流动性的关系:充型能力是外因(铸型性质、浇注条件、铸件结构)和内因(流动性)的共同结果。
外因一定时,流动性就是充型能力。
充型能力弱,则可能产生浇不足、冷隔、砂眼、铁豆、抬箱,以及卷入性气孔、夹砂等缺陷。
11.液态金属的停止流动机理纯金属、共晶合金、窄结晶温度范围合金:型壁处凝固结壳,柱状晶相接触,通道中心合并,流动停止。
合金的结晶温度范围越宽,枝晶就越发达,液流前端出现较少的固相量,通道阻塞,亦即在相对较短的时间内,液态金属便停止流动。
纯金属、共晶合金或窄结晶温度范围合金有良好的流动性,降低了凝固成形中冷隔、热裂、缩松等缺陷的产生。
反之,宽结晶温度范围合金由于流动性差,往往会有较多的缺陷产生。
12.影响液态金属充型能力因素和提高措施:影响充型能力的因素是通过两个途径发生作用的:影响金属与铸型之间热交换条件,而改变金属液的流动时间;影响金属液在铸型中的水力学条件,而改变金属液的流速。
(一)金属性质方面的因素这类因素是内因,决定了金属本身的流动能力——流动性。
铸型阻力影响金属液的充填速度;铸型与金属的热交换条件影响金属液保持流动的时间。
1、合金成分合金的流动性与化学成分之间存在着一定的规律性。
在流动性曲线上,对应着纯金属、共晶成分和金属间化合物的地方出现最大值,而有结晶温度范围的地方流动性下降,且在最大结晶温度范围附近出现最小值。
合金成分对流动性的影响,主要是成分不同时,合金的结晶特点不同造成的。
降低合金熔点的元素容易提高金属过热度,从而提高合金流动时间,提高流动性。
合金净化后流动性提高,合金成分中凡能形成高熔点夹杂物的元素均会降低合金的流动性。
2、结晶潜热结晶潜热越高,凝固进行得越缓慢,流动性越好。
3、金属的比热容、密度和导热系数金属的比热容、密度较大的合金,流动性好。
导热系数小的合金,热量散失慢,保持流动时间长。
金属中加入合金元素后,一般会降低导热系数。
4、液态金属的粘度合金液的粘度,在充型过程前期(属紊流)对流动性的影响较小,而在充型过程后期凝固中(属层流)对流动性影响较大。
5、表面张力表面张力影响金属液与铸型的相互作用。
表面张力对薄壁铸件、铸件的细薄部分和棱角的成形有影响,型腔越细薄、棱角的曲率半径越小,表面张力的影响越大。
为克服由表面张力引起的附加压力,必须附加一个静压头。
综上所述,为了提高液态金属的充型能力,在金属方面可采取以下措施:1、正确选择合金的成分选用结晶温度范围小的合金。
对某些合金进行变质处理使晶粒细化,也有利于提高充型能力。
2、合理的熔炼工艺选择清洁的原材料;减少与有害气体的接触;充分脱氧精炼去气,减少气体、夹杂。
高温出炉,低温浇注。
(二)铸型性质方面1、铸型的蓄热系数:铸型的蓄热系数越大,充型能力下降。
2、铸型温度:预热铸型3、铸型中的气体:减小铸型中气体反压力(三)浇注条件方面1、浇注温度浇注温度越高,充型能力强。
但超过某一温度界限,氧化吸气严重,充型能力提高不明显。
2、充型压头液态金属在流动方向上所受的压力称为充型压力。
充型压力越大, 充型能力越强。
3、浇注系统的结构浇注系统的结构越复杂,则流动阻力越大,充型能力越差。
(四)铸件结构方面衡量铸件结构特点的因素是铸件的折算厚度和复杂程度。
1、折算厚度:折算厚度也叫当量厚度或模数,是铸件体积与铸件表面积之比。
折算厚度越大,热量散失越慢,充型能力就越好。
铸件壁厚相同时,垂直壁比水平壁更容易充填;大平面铸件不易成形。
对薄壁铸件应正确选择浇注位置。
2、复杂程度:铸件结构越复杂,厚薄部分过渡面多,则型腔结构复杂,流动阻力就越大,铸型的充填就越困难。
1、逐层凝固(纯金属或共晶成分合金的凝固方式)恒温下结晶的金属,在凝固过程中其铸件断面上的凝固区域宽度等于零,断面上的固体和液体由一条界线清晰地分开,随着温度的下降,固体层不断加厚,逐步到达铸件中心,此为“逐层凝固方式”。
逐层凝固方式特点:无凝固区或凝固区很窄 a )恒温下结晶的纯金属或共晶成分合金 b)结晶温度范围很窄或断面温度梯度很大2、体积凝固(铸件断面温度场较平坦或结晶范围较宽的合金)如果合金的结晶温度范围很宽,或因铸件断面温度场较平坦,铸件凝固的某一段时间内,其凝固区域很宽,甚至贯穿整个铸件断面,而表面温度高于固相温度,这种情况为“体积凝固方式”,或称为“糊状凝固方式”。
体积凝固方式(糊状凝固方式)特点:凝固动态曲线上的两相边界的纵向间距很小或是无条件重合。
a、铸件断面温度平坦b、结晶温度范围很宽——凝固动态曲线上的两相边界纵向间距很大3、中间凝固(结晶范围较窄或铸件断面温度梯度较大的合金)如果合金的结晶范围较窄,或因铸件断面的温度梯度较大,铸件断面上的凝固区域介于前两者之间时,属于“中间凝固方式”。
中间凝固方式特点:a、结晶温度范围较窄b、铸件断面的温度梯度较大特点:凝固初期似逐层凝固——凝固动态曲线上的两相边界纵向距较小凝固后期似糊状凝固第二章凝固温度场(重点)1.研究铸件温度场的方法:数学解析法、数值模拟法和实测法等。
2.凝固:合金从液态转变成固态的过程,称为一次结晶或凝固。
3.研究温度场的意义:根据铸件温度场随时间的变化,能够预计铸件凝固过程中其断面上各个时刻的凝固区域大小及变化,凝固前沿向中心的推进速度,缩孔和缩松的位置,凝固时间等重要问题,为正确设计浇注系统、设置冒口、冷铁,以及采取其他工艺措施提供可靠依据,对于消除铸造缺陷,获得健全铸件,改善铸件组织和性能有重要意义。
4.凝固方式及其影响因素一般将金属的凝固方式分为三种类型:逐层凝固方式、体积凝固方式(或称糊状凝固方式)和中间凝固方式。
在凝固过程中铸件断面上的凝固区域宽度为零,固体和液体由一条界线(凝固前沿)清楚地分开。
随着温度的下降,固体层不断加厚,逐步达到铸件中心。
这种情况为逐层凝固方式。
铸件凝固的某一段时间内,其凝固区域几乎贯穿整个铸件断面时,则在凝固区域里既有已结晶的晶体,也有未凝固的液体,这种情况为体积凝固方式或称糊状凝固方式。
铸件断面上的凝固区域宽度介于前两者之间时,称中间凝固方式。
凝固方式取决于凝固区域的宽度,而凝固区域的宽度取决于合金的结晶温度范围和冷却强度(温度梯度)。
结晶温度范围越宽,温度梯度越小,越倾向于体积凝固方式。
5.金属凝固方式与铸件质量的关系逐层方式凝固,凝固前沿直接与液态金属接触。
当液态凝固成为固体而发生体积收缩时,可以不断地得到液体的补充,所以产生分散性缩松的倾向性很小,而是在铸件最后凝固的部位留下集中缩孔。