浅析组合动力镗的设计
组合机床车镗课程设计
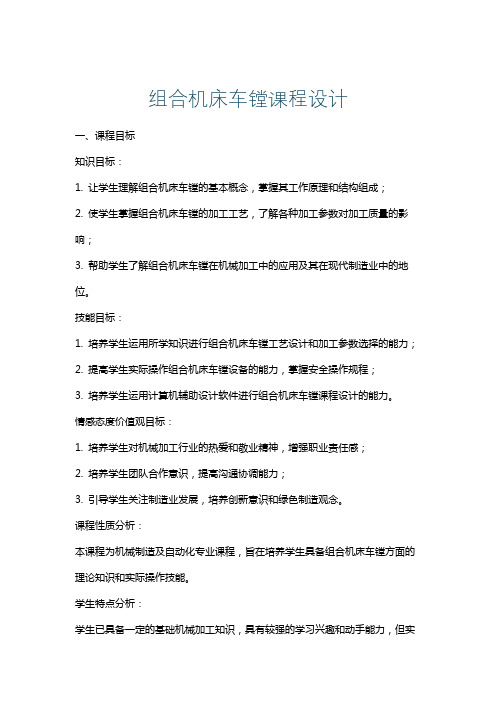
组合机床车镗课程设计一、课程目标知识目标:1. 让学生理解组合机床车镗的基本概念,掌握其工作原理和结构组成;2. 使学生掌握组合机床车镗的加工工艺,了解各种加工参数对加工质量的影响;3. 帮助学生了解组合机床车镗在机械加工中的应用及其在现代制造业中的地位。
技能目标:1. 培养学生运用所学知识进行组合机床车镗工艺设计和加工参数选择的能力;2. 提高学生实际操作组合机床车镗设备的能力,掌握安全操作规程;3. 培养学生运用计算机辅助设计软件进行组合机床车镗课程设计的能力。
情感态度价值观目标:1. 培养学生对机械加工行业的热爱和敬业精神,增强职业责任感;2. 培养学生团队合作意识,提高沟通协调能力;3. 引导学生关注制造业发展,培养创新意识和绿色制造观念。
课程性质分析:本课程为机械制造及自动化专业课程,旨在培养学生具备组合机床车镗方面的理论知识和实际操作技能。
学生特点分析:学生已具备一定的基础机械加工知识,具有较强的学习兴趣和动手能力,但实际操作经验不足。
教学要求:1. 结合课本内容,注重理论与实践相结合,提高学生的实际操作能力;2. 采用项目驱动教学法,激发学生学习兴趣,培养学生的创新能力和团队合作精神;3. 注重安全教育,提高学生的安全意识和自我保护能力。
二、教学内容1. 组合机床车镗基础知识:包括组合机床车镗的定义、分类及工作原理;机床结构及功能;常用刀具的类型及选用。
教材章节:第1章 组合机床概述,第2章 组合机床的构造与功能。
2. 组合机床车镗加工工艺:介绍车镗加工工艺流程,分析加工参数对加工质量的影响,探讨加工过程中常见问题及解决办法。
教材章节:第3章 车镗加工工艺,第4章 加工参数的选择与调整。
3. 组合机床车镗课程设计:讲解课程设计的基本要求,引导学生运用所学知识进行工艺设计和加工参数选择,完成课程设计任务。
教材章节:第5章 课程设计指导,第6章 课程设计实例。
4. 组合机床车镗操作与安全:介绍机床操作方法,强调安全操作规程,分析机床维护保养要点。
设计一台钻镗两用组合机床的液压系统方案

目录绪论1 1. 钻镗液压机床的设计 ........1.1 机床的设计要求 ............ 1.2 机床的设计参数 ............执行元件的选择 ............2.1 分析系统工况 ..............2.1.1 工作负载 ............. 2.1.2惯性负载 ............. 2.1.3阻力负载 ............. 2.2 负载循环图和速度循环图的绘制 2.3 主要参数的确定 ............ 2.3.1 初选液压缸工作压力 ... 2.3.2 确定液压缸主要尺寸 ... 2.3.3 计算最大流量需求 .....拟定液压系统原理图 ........速度控制回路的选择 ........ 换向和速度换接回路的选择 ... 油源的选择和能耗控制 ............ 压力控制回路的选择 ........3.13.23.33.4液压元件的选择 ............4.1 确定液压泵和电机规格 .......4.1.1 计算液压泵的最大工作压力 4.1.2 计算总流量 ............ 4.1.3 电机的选择 ............ 4.2 阀类元件和辅助元件的选择 ...4.2.1.阀类元件的选择 ...... 4.2.2 过滤器的选择 .......... 4.2.3 空气滤清器的选择 ...... 4.3 油管的选择 ................. 4.4 油箱的设计 ..................4.4.1 油箱长宽高的确定 ...... 4.4.2 隔板尺寸的确定 ......... 4.4.3 各种油管的尺寸 ..........2. 2.. 2..3..3.. .3. .3. .3. 3.. 5.. 5.. 6.. .7. 1..0.. 1...0. .1..0.. 1...1. 1...3.1..6.. 1...6. 1..6.. 1...6. 1...7. .1..7.. 1...7. 1..9.. 1...9. .2..0. .2..1. 2...1. .2..2.. .2..2..验算液压系统性能....5.1 验算系统压力损失...5.1.1 判断流动状态..5.1.2 计算系统压力损失5.2 验算系统发热与温升 . 设计总结............ 参考文献............ .2..3. .2..3..2..3..2...3.2...6. .2..8.. .2..9..绪论随着科学技术和工业生产的飞跃发展.国民经济各个部门迫切需要各种各样的质量优、性能好、能耗低、价格廉的液压机床产品。
数控加工中心用:超精密组合式精镗刀结构设计

数控加工中心用:超精密组合式精镗刀结构设计简介镗刀是镗削刀具的一种,一般是圆柄的,也有较大工件使用方形杆一般见于立车,最常用的场合就是里孔加工,现有技术中的精镗刀的调节行程只有直径6mm,范围比较小,且现有精镗刀的而重量较重,大大降低了转速,平衡能力差,制造成本比较高,亟待改进。
优点采用可替换式刀片座,能够扩大刀具的调节行程,重量较轻,转速得到大大的提高,增加了刀具的平衡性,本实用新型具有结构简单,设置合理,制作成本低等优点。
超精密组合式精镗刀结构设计本体1、活动轴2、延长刀座3、镗刀杆4、镗刀片5、刻度盘6、铜垫片7、紧固螺母8、侧固螺丝9、孔槽10、螺丝孔11、刀柄侧固螺丝12、链接刀柄13、一号齿条14、二号齿条15、一号通孔16、二号通孔17、三号通孔18、刀片19。
技术方案是:本体1、活动轴2、延长刀座3、刀片19、镗刀杆4、镗刀片5、侧固螺丝9;本体1的上、下两端和左、右两端分别设有一号通孔16和二号通孔17,且一号通孔16与二号通孔17中部连通设置;活动轴2穿设在本体1的二号通孔17内,且通过数个侧固螺丝9与本体1固定连接;活动轴2外侧壁中部设有三号通孔18,且三号通孔18与本体1上、下两端的一号通孔16连通设置;活动轴2的一端设有孔槽10,且孔槽10内设有螺纹,另一端设有对称的两个螺丝孔11,且螺丝孔11与三号通孔18连通设置;活动轴2另一端一体成型有一号齿条14;刻度盘6穿过铜垫片7后通过紧固螺母8与活动轴2的孔槽10旋接;延长刀座3的一端通过螺栓固定有刀片19,另一端一体成型有二号齿条15,二号齿条15与一号齿条14啮合;延长刀座3通过螺栓与活动轴2的螺丝孔11旋接固定;镗刀杆4穿过本体1底部后插设在活动轴2中部的三号通孔18内,且镗刀杆4顶部的凹面与三号通孔18的侧壁通过过盈配合卡接;镗刀杆4的底端通过螺栓固定有镗刀片5。
本体11上端通过刀柄侧固螺丝12插设固定在链接刀柄13的底端。
组合机床精镗孔的设计

组合机床精镗孔的设计作者指导教师摘要:组合机床是根据工件加工需要,以大量通用部件为基础,配以少量专用部件组成的一种高效专用机床。
其通用部件的选用根据零件的实际尺寸和加工工艺要求来选用,在此基础上,我们通过查找参考资料中的一系列标准件最终确定其结构、型号、规格及其配套关系。
通过对CW6132床头箱纵向孔的工艺分析,从而制定出几种加工工艺方案。
通过比较最终得到相对合理、经济、可靠的一种工艺方案。
再制定出机床的加工工艺过程卡,从中我们可以清晰的看出各道工序的加工顺序和和加工内容,确定加工余量与加工表面粗糙度值。
再通过机床的总体布局选出最合理的一种,并画出加工示意图、多轴箱装配图与机床联系尺寸图。
关键词:通用部件工艺方案机床尺寸Boring machine combination of fine designAbstract:Portfolio machine is based on the workpiece processing needs, to a large number based on common components, supported by a small number of dedicated components for a highly efficient machine. Common components of their choice based on the actual size and components of the processing requirements of choice, on the basis of this, we have to find reference materials in a series of standard parts ultimately determine its structure, models, specifications and supporting relationship. CW6132 me on the bedside through the vertical hole of the process, which would set out several processing technology programmes. By comparison finally be relatively reasonable, the economy, a reliable technology programmes. Further development of the processing machine to process card, from which we can clearly see that all the procedures and order processing and processing, and processing determine Jiagongyuliang surface roughness values. Through the machine to the overall layout of the most reasonable one and drawn diagram processing, multi-axle box assembly contact with the machine size map.Key words:General part craft plan Engine bed size前言需要的联系78290349随着科学技术和国民经济的飞速发展,组合机床近年来也得到快速普及和发展。
卧式钻镗组合机床的液压动力液压系统课程设计解读

卧式钻镗组合机床的液压动力液压系统课程设计
设计的目的和要求:
1工作循环:“快进—工进—死挡铁停留—快退—原位停止” 。
2工作参数轴向切削力 12000N ,移动部件总重 10000N ,快进行程 200mm,快进与快退速度 4.2m/min ,工进行程 30mm,工进速度 0.05m /min ,加、减速时间为 0.2s ,静摩擦系数 0.2,动摩擦系数 0.1,动力滑台可在中途停止。
要求动力部件可以手动调整,快进转工进平稳、可靠。
一、工况分析,确定液压缸推力
1.1 负载分析:
切削推力: tF=12000N
静摩擦力 : aF=afG=0.2×10000=2000N 动摩擦力 : dF=dfG=0.1×10000=1000N 启动惯性力: mF=t
vm
=
t
vgG =357.14N
1.2 液压缸的推力 (液压缸效率 9.0 启动推力:启F= aF/η= 222
2.22N 加速推力:加F=(dF+mF /η=1507.93N 快进推力:快F= dF/η=1111.11N 工进推力:工 F=(tF+ dF /η=14444.44N
反向启动过程作用力与 F 启、 F 加、 F 快大小相同,方向相反。
镗削动力头及其组件设计
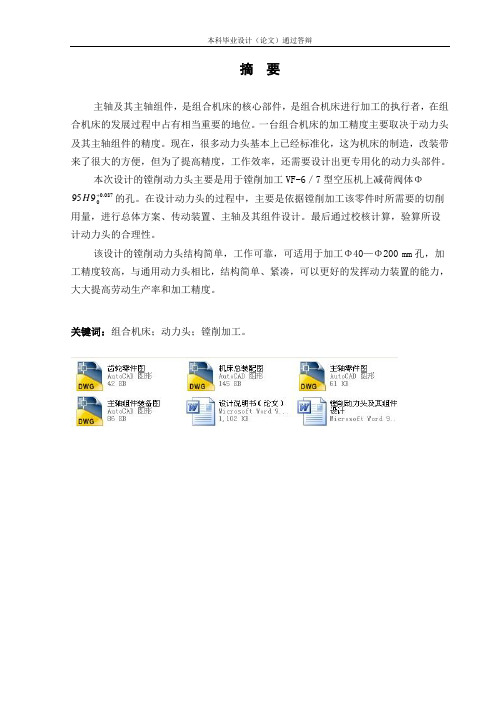
摘 要主轴及其主轴组件,是组合机床的核心部件,是组合机床进行加工的执行者,在组合机床的发展过程中占有相当重要的地位。
一台组合机床的加工精度主要取决于动力头及其主轴组件的精度。
现在,很多动力头基本上已经标准化,这为机床的制造,改装带来了很大的方便,但为了提高精度,工作效率,还需要设计出更专用化的动力头部件。
本次设计的镗削动力头主要是用于镗削加工VF-6/7型空压机上减荷阀体Φ087.00995 H 的孔。
在设计动力头的过程中,主要是依据镗削加工该零件时所需要的切削用量,进行总体方案、传动装置、主轴及其组件设计。
最后通过校核计算,验算所设计动力头的合理性。
该设计的镗削动力头结构简单,工作可靠,可适用于加工Φ40—Φ200 mm 孔,加工精度较高,与通用动力头相比,结构简单、紧凑,可以更好的发挥动力装置的能力,大大提高劳动生产率和加工精度。
关键词:组合机床;动力头;镗削加工。
ABSTACTThe main axle and its the main axle module, is the aggregatemachine-tool core part, is performer which the aggregate machine-toolcarries on the processing, holds the quite important status in theaggregate machine-tool developing process. A aggregate machine-toolprocessing precision mainly is decided by the power head and its themain axle module precision. Now, very many power heads basically already standardize, this for theengine bed manufacture, the reequipment has brought very bigconvenient, but in order to increase the precision, the workingefficiency, needed to design the special-purposer power head part.The design of Boring is the main driving force for the first Boring VF-6/7 aircompressor on a valve Φ087.00995 H by the hole. In the first design, dynamic process, which is mainly Boring processing required when cutting consumption, power sources, power transmission, Spindle assembly design. Finally, checking, checking dynamic design of the first reasonableThe first Boring power structure simple and reliable and can be applied to the processing of Φ40-200 mm hole, high precision machining, and General Dynamics compared to the first, simple and compact structure, we can better play the power plant capacity greatly improve labor productivity and accuracy.Keywords : portfolio machine; Dynamic head; Boring目录中文摘要 (Ⅰ)英文摘要 (Ⅱ)第一章绪论 (1)第二章动力头参数计算 (2)2.1零件分析 (2)2.2确定加工刀具材料 (2)2.3确定镗削时主轴最佳转速 (2)2.4运动参数 (3)2.4.1主运动速度范围 (3)2.4.2确定传动级数 (3)2.4.3确定主轴的标准转速 (3)2.5电动机的选择 (4)2.5.1计算电动机功率及各轴上的传递功率 (4)2.5.2选择电动机的型号 (5)2.6作转速图 (5)2.7动力头结构简图 (6)第三章主轴设计 (7)3.1主轴材料的选择 (7)3.2主轴轴承的选用 (7)3.3主轴热处理 (8)3.4确定主轴结构 (8)3.5主轴结构参数 (9)3.5.1确定主轴最小直径 (9)3.5.2确定主轴前轴颈 (9)3.5.3确定主轴后轴颈 (10)3.5.4确定主轴内孔 (10)3.5.5主轴前端尺寸的确定 (10)3.5.6主轴各具体尺寸的确定 (10)第四章齿轮设计 (12)4.2确定齿轮参数 (12)4.2.1确定齿轮的齿数 (12)4.2.2计算齿轮的宽度 (12)4.2.3计算齿轮的模数 (13)4.2.4分度圆直径 (14)4.3齿轮和主轴的联接 (14)第五章轴上零件设计 (15)5.1轴承的选取 (15)5.1.1前支承选取 (15)5.1.2后支承选取 (15)5.1.3主轴轴承精度的选择 (15)5.2定位元件设计 (15)5.2.1定位环 (16)5.2.2压块锁紧螺母 (16)5.2.3套筒 (16)5.2.4轴有弹性挡圈 (16)第六章主轴组件的检验校核 (18)6.1镗削切削力 (18)6.2主轴的校核 (19)6.2.1主轴刚度的验算 (19)6.2.2主轴强度的验算 (21)6.3滚动轴承额定寿命 (21)6.4主轴齿轮的校核 (22)6.4.1按接触疲劳强度校核 (25)6.4.2按齿根弯曲疲劳强度校核 (25)第七章主轴箱总体设计 (28)7.1箱体设计 (28)7.2密封装置设计 (28)7.3润滑设计 (29)第八章设计总结 (30)参考文献 (31)第一章绪论进入20世纪以来,机器是人类进行生产以减轻体力劳动和提高劳动生产率的主要工具,使用机器进行生产的水平是衡量一个国家的技术水平和现代化程度的重要标志。
毕业设计 组合镗床

摘要该篇论文是对粗镗CK-V型主轴箱Φ88.5、2-Φ68.5三孔双向卧式组合镗床SWT-5的设计。
本设计说明书主要包括组合机床总体设计和专题设计两个部分。
其中第一部分的内容有产品工序分析、组合机床总体布置以及“三图一卡”(被加工零件工序图、加工示意图,机床联系尺寸总图、机床生产效率计算卡)的设计;第二部分是主轴箱体的设计和传动系统的设计,并校核轴与齿轮的强度。
通过此次设计,真正了解镗床的内部结构,把所学的知识运用到生产实践中去。
关键字:组合机床、工序分析、三图一卡、主轴箱体、传动系统AbstractThis paper is to exactitude boring the CK-V headstockΦ88.5、2-Φ68.5 threebidirectional horizontal-type combinations boring lathe SWT- 5 design. This design instruction booklet mainlyincludes the aggregate machine-tool system design and the topicdesigns two parts. First part of content has the product workingprocedure analysis, the aggregate machine-tool general arrangement aswell as "a three charts card" (processes components working procedurechart, processing schematic drawing, engine bed relation size assemblydrawing, engine bed production efficiency computation card) thedesign; The second part is the headstock body design and thetransmission system design, and school epipolar axis and gearintensity. Through this design, truly understood the boring lathe the internalstructure, the knowledge which studies utilizes in the productionpractice.Essential character:Aggregate machine-tool working procedureanalysisa three charts card headstock body transmission system前言大学四年的学习生活即将结束,大学生活中的最后一个环节也是最重要的一个环节——毕业设计,是对所学知识和技能的综合运用和检验,也是我们完成学业走向工作岗位必不可少的一步。
「柴油机气缸体三面粗镗组合机床总体及镗模设计」
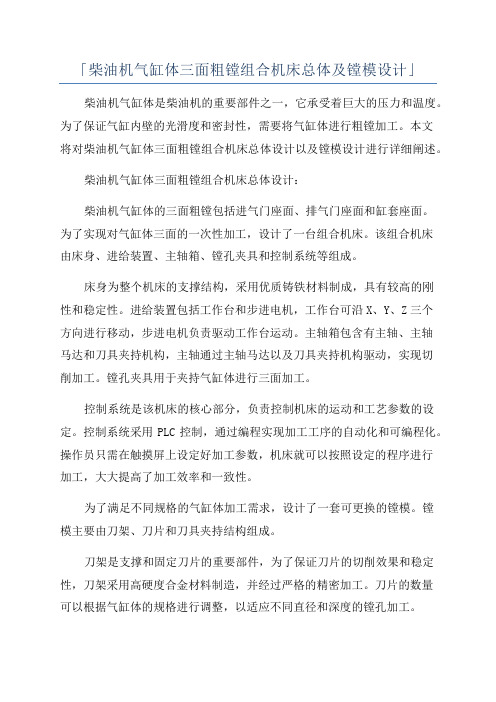
「柴油机气缸体三面粗镗组合机床总体及镗模设计」柴油机气缸体是柴油机的重要部件之一,它承受着巨大的压力和温度。
为了保证气缸内壁的光滑度和密封性,需要将气缸体进行粗镗加工。
本文将对柴油机气缸体三面粗镗组合机床总体设计以及镗模设计进行详细阐述。
柴油机气缸体三面粗镗组合机床总体设计:柴油机气缸体的三面粗镗包括进气门座面、排气门座面和缸套座面。
为了实现对气缸体三面的一次性加工,设计了一台组合机床。
该组合机床由床身、进给装置、主轴箱、镗孔夹具和控制系统等组成。
床身为整个机床的支撑结构,采用优质铸铁材料制成,具有较高的刚性和稳定性。
进给装置包括工作台和步进电机,工作台可沿X、Y、Z三个方向进行移动,步进电机负责驱动工作台运动。
主轴箱包含有主轴、主轴马达和刀具夹持机构,主轴通过主轴马达以及刀具夹持机构驱动,实现切削加工。
镗孔夹具用于夹持气缸体进行三面加工。
控制系统是该机床的核心部分,负责控制机床的运动和工艺参数的设定。
控制系统采用PLC控制,通过编程实现加工工序的自动化和可编程化。
操作员只需在触摸屏上设定好加工参数,机床就可以按照设定的程序进行加工,大大提高了加工效率和一致性。
为了满足不同规格的气缸体加工需求,设计了一套可更换的镗模。
镗模主要由刀架、刀片和刀具夹持结构组成。
刀架是支撑和固定刀片的重要部件,为了保证刀片的切削效果和稳定性,刀架采用高硬度合金材料制造,并经过严格的精密加工。
刀片的数量可以根据气缸体的规格进行调整,以适应不同直径和深度的镗孔加工。
刀片选择了高速钢材料制造,具有较高的硬度和耐磨性。
刀片的形状为圆弧形,可保证在镗削过程中产生较小的表面粗糙度和毛边。
刀具夹持结构用于夹持刀片,固定刀片到刀架上。
为了提高夹持的稳定性,刀具夹持结构采用了精密调节装置,可以根据刀片的尺寸进行微调,确保镗孔加工的精度和平行度。
总结:柴油机气缸体三面粗镗组合机床总体设计和镗模设计是为了满足柴油机气缸体粗加工的需求。
该机床结构紧凑、操作简单,通过合理的工艺参数和优质的镗模,可以实现高效、稳定、精确的气缸体粗镗加工,为柴油机的生产提供了可靠的设备保障。
镗主轴箱的6个轴孔的变速箱组合镗床设计

1.1组合机床及其特点
一个国家或地区经济发展的重要支柱是制造业,它的发展水平是该国家或地区的经济实力、科技水平、生活水准和国防实力的标志,而制造业的生产能力和制造水平主要取决于机械制造装备——金属切削机床的先进程度。组合机床作为金属切削机床的生力军,是以通用部件为基础配备,加上少量专用部件组成的一种专用高效自动化设备,它具有设计制造投资少、周期短、加工精度稳定、经济效益高、改装方便等优点。
以箱体零件同轴孔系为代表的长孔镗削,是金属切削加工中最重要的内容之一。尽管现在仍有采用镗模、导套、台式铣镗床后立柱支承长镗杆或人工找正工件回转180°等方法实施长孔镗削的实例,但近些年来,一方面由于数控铣镗床和加工中心的大量使用,使各类卧式铣镗床的坐标定位精度和工作台回转分度精度有了较大提高。从机床结构上使工作台回转180°自定位的调头镗孔,几乎是成为了在该种机床上镗削长孔的唯一方法。
The contents of product process analysis, combination of general layout of machine tool and boring spindle diagram.
Key words:spindle box;combination machine;processing technology
This design instruction booklet mainly includes overall design process of machine tool, and discusses the aspects of design, process scheme for the overall design, component design.
Long hole boring to box part coaxial holes as the representative of the cut, is one of the most important content in the metal cutting. Although there are still using boring mode, guide sleeve, desktop milling and boring machine after the columns support the long boring bar or artificial alignment workpiece rotation of 180 DEG, examples of long hole boring. But in recent years, on the one hand because of the extensive use of CNC milling machine and machining center, precision of the coordinate positioning rotary precision and working table of horizontal boring and milling machine has been greatly improved. From the machine tool structure enable the rotary table 180 ° from the positioning of the turn-around boring, become almost the only method in the machine tool on the long hole boring.
变速箱工艺及组合镗床设计概述

1.1 组合镗床研究背景按照实际生产的要求,结合加工,一般来说,它是一个很常见的零件,加上一些小部分的特殊零件,从而形成有效的专用机床。
一个孔的加工和一个平面的加工都是应用的组合机床。
如今,仪器的生产,汽车行业,军工等等行都需要是用组合机床。
在不远的将来,我们需要更高的精度,更高的速度,复合化,高科技量并且更加环保的组合机床。
这时候有2 类样式制造出1 台满足加工要求的机床,第1 步是依据要求开展设计,许多工厂总用的则是这个。
第2 步,然而组合机床在机械加工领域里用的比较多,大部分人依照工作的经历,结合机床本身性能,研究出了加工特色,一些行业里来说,结构相似的组合机床,就设计成通用车床,这就是专门的组合机床。
允许运用组合机床不用经常展开加工,大批量的生产出来,根据被加工件的需要,把夹具和刀具配置在机床上,这样的机床就会有很高的效率。
最近的这些年,因为国家出台了较新的规定,使机床达到修理的简便,市场上能买到的零件是大家经常更换的。
1.2 组合机床的特点大家把我设计的机床和一般机床,以及特殊机床这三类机比对,其特色是:1、在上述中,很多工厂采用市场上容易买到的零件,由于价格比较便宜,零件易损坏,厂家花钱比较少,产值还算可观。
2 、大部分机床在制造期间需要刀库容量大,企业对他的性价比提出较高水平,使他加工速度大于常见机床,具有经济。
耐用。
又实惠。
3、一开始模块化机床的通用的部件设计非常谨慎,大部分零部件都能达到你想要的水平,另外某些大型企业是非常专业的生产厂家,其构造平稳,作业期间是比较稳定的,工作时十分便捷,后期进行维护时过程也很简单。
4、用这台机床操作一些零部件期间,必须用这台机器指定的其他零部件来加工,让其质量得到保证,这样对操作员工的技术要求降低很多。
1.3 本课题研究的目的及意义它可以在变速器轴和齿轮等零件以及别的零部件把他们相连其让他们融为一体,大部分零件的安装方位是准确的,还能确保上述零件安装的稳定性,齿轮箱铸铁有沙眼,影响他的使用寿命,让其性能不稳定,使其沙眼处易破损。
卧式钻镗组合机床的液压系统设计

卧式钻镗组合机床的液压系统设计卧式钻、镗组合机床是一种多功能的机床,广泛应用于金属加工行业。
其液压系统是该机床能正常运行的关键部分。
液压系统主要包括供油系统、动力系统、控制系统和液压元件等。
下面将详细介绍卧式钻、镗组合机床液压系统的设计。
首先是供油系统的设计。
供油系统主要包括供油泵、滤油器、储油箱等。
供油泵负责向液压元件提供工作液压油,因此需要选择合适的供油泵,确保其输出流量和压力能够满足机床的工作要求。
同时,滤油器的作用是过滤油液中的杂质,保护液压元件的正常工作,因此需要选择滤油器的类型和等级。
储油箱用于储存液压油,并起到平稳油液压力的作用,因此需要选择合适的储油箱容量。
其次是动力系统的设计。
动力系统主要包括电动机、液压缸、执行器等。
电动机主要负责提供动力,需要选择合适的电动机功率和转速,以满足机床的工作要求。
液压缸主要负责转换液压能为机械能,需要选择合适的液压缸类型和规格,以满足机床的工作要求。
执行器是液压系统中的关键元件,负责实现各种动作和运动,因此需要选择合适的执行器类型和规格,以满足机床的工作要求。
再次是控制系统的设计。
控制系统主要包括控制阀、油泵控制系统、安全保护装置等。
控制阀的作用是控制液压流量和压力,需要根据机床的工作要求选择合适的控制阀类型和规格。
油泵控制系统主要负责控制油泵的运行状态,需要选择合适的控制方式和系统结构。
安全保护装置是为了保障机床的安全运行,需要选择合适的安全保护装置类型和规格。
最后是液压元件的设计。
液压元件主要包括液压缸、控制阀、油泵等。
液压缸的设计需要根据机床的工作需求选择合适的液压缸类型和规格。
控制阀的设计需要根据机床的工作要求选择合适的控制阀类型和规格。
油泵的设计需要根据机床的工作要求选择合适的油泵类型和规格。
总之,卧式钻、镗组合机床的液压系统设计需要考虑供油系统、动力系统、控制系统和液压元件等多个方面的因素。
只有通过合理的设计,才能确保机床的正常运行和高效工作。
卧式钻、镗组合机床的液压系统设计
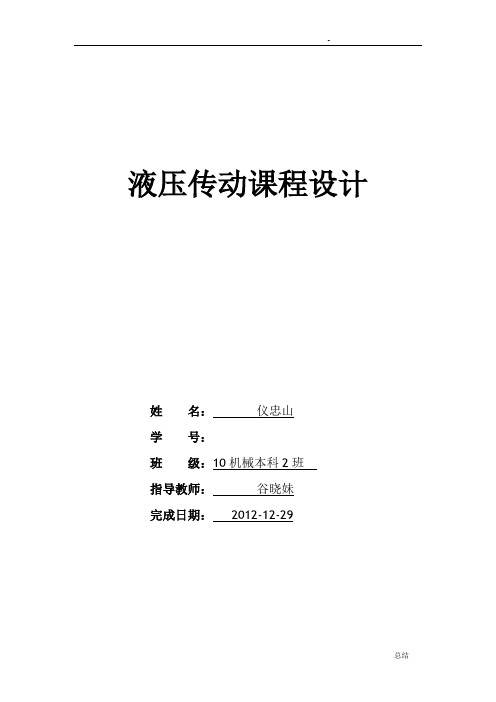
液压传动课程设计姓名:仪忠山学号:班级:10机械本科2班指导教师:谷晓妹完成日期:2012-12-29机电工程学院课程设计任务书目录第一章绪论41.1 开发背景及系统特点4第二章负载分析4第三章负载图和速度图的绘制5第四章液压缸主要参数的确定6第五章液压系统的拟定85.1 液压回路的选择85.2 液压回路的综合11第六章液压元件的选择116.1 液压泵116.2 阀类元件及辅助元件136.3 油管和油箱13第七章液压系统性能的验算147.1 验算系统压力损失并确定压力阀的调整值147.2 油液温升验算16第八章设计总结17参考文献17卧式钻、镗组合机床的液压系统设计说明书第一章 绪论 1.1 开发背景及系统特点本次课程设计将以组合机床动力滑台液压系统设计为例,介绍该组合机床液压系统的设计方法和设计步骤,其中包括组合机床动力滑台液压系统的工况分析、主要参数确定、液压系统原理图的拟定、液压元件的选择以及系统性能验算等。
组合机床是以通用部件为基础,配以按工件特定外形和加工工艺设计的专用部件和夹具而组成的半自动或自动专用机床。
组合机床一般采用多轴、多刀、多工序、多面或多工位同时加工的方式,生产效率比通用机床高几倍至几十倍。
组合机床兼有低成本和高效率的优点,在大批、大量生产中得到广泛应用,并可用以组成自动生产线。
组合机床通常采用多轴、多刀、多面、多工位同时加工的方式,能完成钻、扩、铰、镗孔、攻丝、车、铣、磨削及其他精加工工序,生产效率比通用机床高几倍至几十倍。
液压系统由于具有结构简单、动作灵活、操作方便、调速X 围大、可无级连读调节等优点,在组合机床中得到了广泛应用。
第二章 负载分析一、工作负载工作负载是在工作过程中由于机器特定的工作情况而产生的负载,即W F =12000N二、惯性负载最大惯性负载取决于移动部件的质量和最大加速度。
已知加、减速时间为0.2s ,工作台最大移动速度,即快进、快退速度为0.1m/s ,因此惯性负载为:N t v g G t v mF m 2.5102.08.91.010000=⨯⨯=∆∆•=∆∆=三、阻力负载阻力负载主要是工作台的机械摩擦阻力,分为静摩擦阻力和动摩擦阻力两部分。
卧式钻镗组合机床动力头设计(DOC)
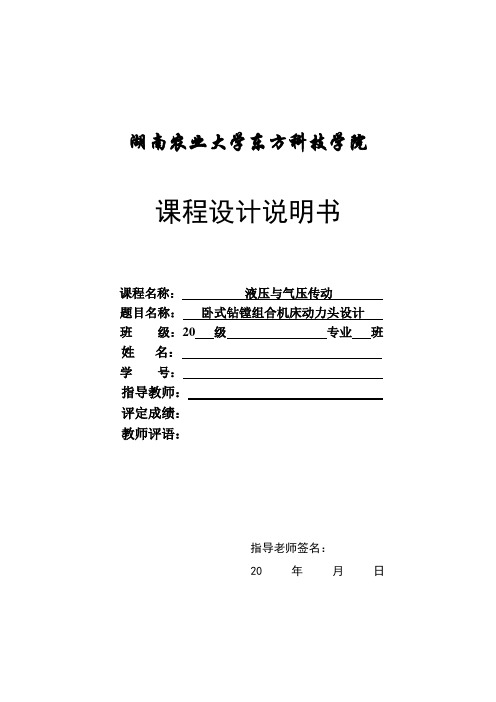
湖南农业大学东方科技学院课程设计说明书课程名称:液压与气压传动题目名称:卧式钻镗组合机床动力头设计班级:20 级专业班姓名:学号:指导教师:评定成绩:教师评语:指导老师签名:20 年月日一、设计任务 (1)二、设计数据分析计算 (1)1)确定液压缸的结构尺寸及工况图 (1)(1)负载图及速度图。
(1)(2)初选液压缸的结构尺寸。
(3)(3)液压缸工况图。
(3)2)拟定液压回路 (5)(1)选择液压回路。
(5)(2)组成液压系统图。
(7)3)计算和选择液压元件 (7)(1)确定液压泵的规格和电机功率。
(7)(2)液压阀的选择。
(8)(3)确定管道尺寸 (9)4)液压系统主要性能的估算 (9)(1)液压缸的速度 (9)(2)系统的效率 (10)(3)液压回路和液压系统的效率 (12)(4)液压系统发热与温升的验算 (12)一、设计任务设计一台卧式钻、镗组合机床液压系统。
该机床用于加工铸铁箱形零件的孔系,运动部件总重G=10000N ,液压缸机械效率为0.9,加工时最大切削力为12000N ,工作循环为:“快进——工进——死挡铁停留——快退——原位停止”。
快进行程长度为0.4m ,工进行程为0.1 m 。
快进和快退速度为0.1m /s ,工进速度范围为3×104-~5×103-m /s ,采用平导轨,启动时间为0.2s 。
要求动力部件可以手动调整,快进转工进平稳、可靠。
二、设计数据分析计算1)确定液压缸的结构尺寸及工况图 (1)负载图及速度图。
①负载分析。
a.切削力:L F =12000Nb.摩擦阻力:G s fs F f F ⋅==0.2×10000=2000NG d fd F f F ⋅==0.1×10000=1000Nc.惯性阻力tg F ma F G m ∆∆⋅==ν=2.01.081.910000⋅N=510N d.重力阻力因工作部件是卧式安置,故重力阻力为零。
组合镗床设计
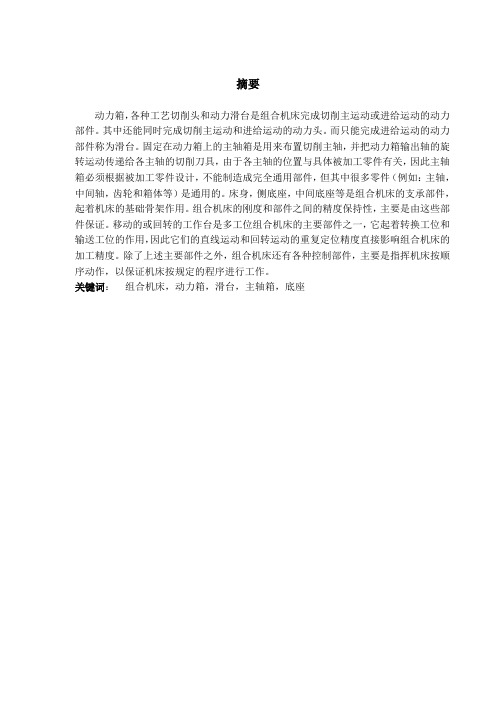
摘要动力箱,各种工艺切削头和动力滑台是组合机床完成切削主运动或进给运动的动力部件。
其中还能同时完成切削主运动和进给运动的动力头。
而只能完成进给运动的动力部件称为滑台。
固定在动力箱上的主轴箱是用来布置切削主轴,并把动力箱输出轴的旋转运动传递给各主轴的切削刀具,由于各主轴的位置与具体被加工零件有关,因此主轴箱必须根据被加工零件设计,不能制造成完全通用部件,但其中很多零件(例如:主轴,中间轴,齿轮和箱体等)是通用的。
床身,侧底座,中间底座等是组合机床的支承部件,起着机床的基础骨架作用。
组合机床的刚度和部件之间的精度保持性,主要是由这些部件保证。
移动的或回转的工作台是多工位组合机床的主要部件之一,它起着转换工位和输送工位的作用,因此它们的直线运动和回转运动的重复定位精度直接影响组合机床的加工精度。
除了上述主要部件之外,组合机床还有各种控制部件,主要是指挥机床按顺序动作,以保证机床按规定的程序进行工作。
关键词:组合机床,动力箱,滑台,主轴箱,底座AbstractThe power box, each kind of craft cutting head and the power slipway is the aggregate machine-tool completes cuts the host movement or enters for the movement power part. Also can simultaneously complete cuts the host movement and enters for the movement power head. But only can complete is called for the movement power part slipway. Fixes the headstock is uses for in the power box to arrange the cutting main axle, and transmits the power box output shaft rotary motion for various main axles cutting tool, because various main axles position with makes concrete is processed the components related, therefore the headstock must act according to is processed the components design, cannot make creates the completely general part, but very many components (for example: The main axle, the intermediate shaft, the gear and the box body and so on) is general.The lathe bed, leans the foundation, the middle foundation and so on is the aggregate machine-tool supporting part, is playing the engine bed foundation skeleton role. Between the aggregate machine-tool rigidity and the part precision retentivity, mainly is guaranteed by these parts. Motion or the rotation work table is one of multiplex position aggregate machine-tool major components, it plays is transforming the location and transports the location the role, therefore their translation and gyroscopic motion repetition pointing accuracy direct influence aggregate machine-tool processing precision.Besides the above major component, the aggregate machine-tool also has each kind of control portion, mainly is directs the engine bed according to the smooth movement, guaranteed the engine bed carries on the work according to the stipulation procedure.Key word Aggregate machine-tool, power box, slipway, headstock, foundation目录第一章绪论 (1)1.1课题的来源及意义 (1)1.2课题应达到的要求 (1)1.3组合机床的组成及特点 (1)第二章组合镗床设计 (2)2.1 机床加工工艺分析 (2)2.1.1机床的工艺任务 (2)2.1.2加工方案分析 (2)2.2机床的总体方案设计 (3)2.2.1确定机床的布局形式 (3)2.2.2确定机床的传动方案 (3)2.2.3机床的总体方案设计 (3)2.2.4绘制加工示意图 (5)2.2.5绘制机床联系总图 (6)2.2.6编制机床生产率计算卡 (8)2.3 主要部件设计 (10)2.3.1绘制多轴箱原始依据图 (10)2.3.2主轴,齿轮的确定及动力计算 (11)2.3.3传动件设计 (12)2.4 机床专用夹具设计 (18)2.4.1主明确设计任务,收集分析原始资料 (18)2.4.2确定夹具的结构方案 (19)2.5 传动件设计 (20)2.5.1验算齿轮接触强度 (20)2.5.2验算主轴的扭转强度 (22)结论 (24)致谢 (25)参考文献 (26)错误!未定义书签。
卧式钻、镗组合机床的液压系统设计说明

卧式钻、镗组合机床的液压系统设计说明卧式钻、镗组合机床是一种用于金属加工的机床,它能够钻孔、镗孔和铰孔等多种加工操作。
其中,液压系统是这种机床的重要组成部分,通过控制液压元件的运动,实现机床的各项功能。
本文将从三个方面介绍卧式钻、镗组合机床的液压系统设计说明。
一、液压系统的组成卧式钻、镗组合机床的液压系统主要由油箱、油泵、流量控制阀、节流阀、液压缸、液压马达等组成。
首先是油箱,它是存储液压油的容器,通常位于机床的底部,可以提供稳定的液压油流,并冷却回收液压油。
其次是油泵,它是液压系统的主要动力来源,能够将油箱中的液压油压力提高,使得液压系统中的各种液压元件能够正常运行。
接下来是流量控制阀和节流阀,它们分别用于调节油液的流量和压力,以满足机床不同功能的操作需求。
液压缸和液压马达则是液压系统的输出部分,它们将液压能转化为机床的各种动力和运动形式,如夹持工件、钻孔、镗孔、铰孔等。
二、液压系统的设计方法设计液压系统需要考虑多个因素,包括机床类型、加工材料、加工过程、液压元件的选型等。
在设计时,应该做到以下几点:1.根据机床的功能需求确定系统的流量和压力等参数。
2.根据液压元件的性能和机床的使用情况,选择合适的液压元件。
3.配置流量控制阀和节流阀,根据机床的工作情况调整油液的流量和压力。
4.合理布局液压元件,使其保持恰当的距离,并在液压管路中添加过滤器,以确保液压油的清洁度。
5.配置压力表和温度计等仪表,监测液压系统的压力和温度等参数,及时调整机床的工作状态。
三、液压系统的维修和保养机床的液压系统需要定期检查和保养,以保证其良好的工作状态。
以下是液压系统的常见维修和保养措施:2.保持系统的清洁,及时清洗液压机床的液压管路、油泵和液压缸等液压元件,防止异物和腐蚀物污染液压油。
3.检查液压系统的各种液压元件,如密封件、油管、接头、泵阀等,及时更换磨损厉害的部件。
4.检查液压系统的压力和温度等参数,定期清洗压力表和温度计,保证其准确性。
卧式钻镗组合机床动力滑台液压系统设计
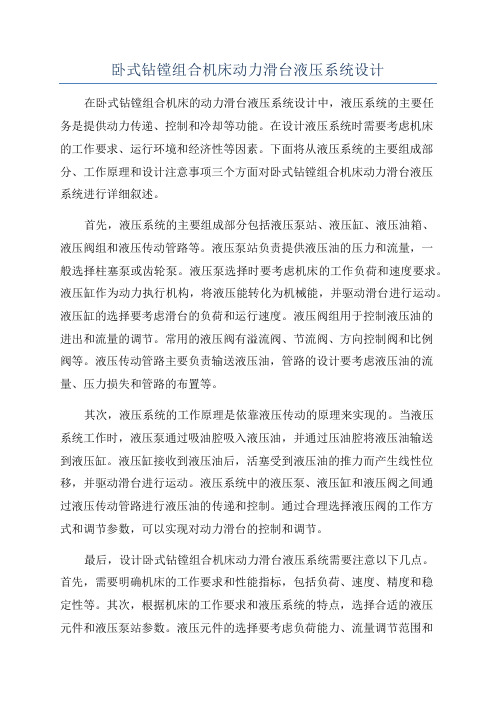
卧式钻镗组合机床动力滑台液压系统设计在卧式钻镗组合机床的动力滑台液压系统设计中,液压系统的主要任务是提供动力传递、控制和冷却等功能。
在设计液压系统时需要考虑机床的工作要求、运行环境和经济性等因素。
下面将从液压系统的主要组成部分、工作原理和设计注意事项三个方面对卧式钻镗组合机床动力滑台液压系统进行详细叙述。
首先,液压系统的主要组成部分包括液压泵站、液压缸、液压油箱、液压阀组和液压传动管路等。
液压泵站负责提供液压油的压力和流量,一般选择柱塞泵或齿轮泵。
液压泵选择时要考虑机床的工作负荷和速度要求。
液压缸作为动力执行机构,将液压能转化为机械能,并驱动滑台进行运动。
液压缸的选择要考虑滑台的负荷和运行速度。
液压阀组用于控制液压油的进出和流量的调节。
常用的液压阀有溢流阀、节流阀、方向控制阀和比例阀等。
液压传动管路主要负责输送液压油,管路的设计要考虑液压油的流量、压力损失和管路的布置等。
其次,液压系统的工作原理是依靠液压传动的原理来实现的。
当液压系统工作时,液压泵通过吸油腔吸入液压油,并通过压油腔将液压油输送到液压缸。
液压缸接收到液压油后,活塞受到液压油的推力而产生线性位移,并驱动滑台进行运动。
液压系统中的液压泵、液压缸和液压阀之间通过液压传动管路进行液压油的传递和控制。
通过合理选择液压阀的工作方式和调节参数,可以实现对动力滑台的控制和调节。
最后,设计卧式钻镗组合机床动力滑台液压系统需要注意以下几点。
首先,需要明确机床的工作要求和性能指标,包括负荷、速度、精度和稳定性等。
其次,根据机床的工作要求和液压系统的特点,选择合适的液压元件和液压泵站参数。
液压元件的选择要考虑负荷能力、流量调节范围和控制精度等因素。
液压泵站的选择要考虑泵的压力和流量特性,以及泵的安装方式和传动机构等。
最后,需要注意液压系统的传动管路的布局和液压油的冷却方式。
合理的管路布局可以减小压力损失和能耗,提高系统的效率和可靠性。
液压油的冷却方式可以选择冷却器或油冷却器等。
数控加工刀具技术:多功能组合镗刀杆结构设计

数控加工刀具技术:多功能组合镗刀杆结构设计简介传统的 12V 机体主油道孔的加工,TPX6113 等普通镗床设备一直是生产上的瓶颈工序。
工序繁琐,丝堵完工步骤如下:第一步,先装钻头钻掉机体内的部分钢管。
第二步,换镗杆粗镗¢63 底孔。
第三步,换装止口镗杆,加工¢ 74 的丝堵止口。
第四步,装夹倒角刀。
第五步,装顶尖镗杆校正。
第六步,攻丝器攻丝完成。
单台机体有 3 个丝堵,过去完工一台就需要操作者装卸沉重的镗杆18 次以上,按照传统加工方法存在如下缺点或不足:1) 原镗杆粗老笨重,操作者劳动强度大,搬上搬下,经常造成操作人员腰部损伤;2) 此方法镗杆装卸频繁,丝堵加工尺寸精度变化参差不齐,难以达到高质量要求;3) 受设备限制和人员体力影响,如大批量生产,加工能力难以满足出产要求。
多功能组合镗刀杆结构设计机床主轴1、紧固螺钉2、攻丝器、划线顶尖 10、定位锥面 11、划线刀槽 12、粗镗刀槽 13、精镗刀槽 3、刀杆锥柄 4、粗镗刀 16、精镗刀 17、倒角刀 14、划线刀 15。
刀杆锥柄 4 和攻丝器顺次安装连接于机床主轴 1 上,所述攻丝器包括与刀杆锥柄 15 相连接的攻丝器体7、紧固螺钉5、攻丝刀8,刀杆锥柄15 上顺次安设有划线刀槽12、粗镗刀槽 13、精镗刀槽 3,粗镗刀槽 13、精镗刀槽 3 上分别与粗镗刀 16、精镗刀 17 相安装,划线刀槽 12 上与倒角刀 14 或划线刀15 相安装。
刀杆锥柄 4 的前端为定位锥面 11,顶端为划线顶尖 10。
刀杆锥柄 4 的圆柱体上设有一紧固面 6,将攻丝器体 7 由紧固螺钉 5 固定于紧固面 6 上。
攻丝器体 7 由紧固螺钉 5 固定于刀杆锥柄 4 上的紧固面 6 上,攻丝刀 8 安装于攻丝器体 7 中,攻丝刀 8 的内端部与刀杆锥柄 4 的定位锥面 11 相接触。
攻丝器体 7 的前端设有定位方槽端9。
使用时,通过定位装置找正后,先用粗镗刀镗削¢63 油道底孔,接着后面的精镗刀,加工¢74 止口。
钻镗两用组合机床动力滑台的课程设计分析
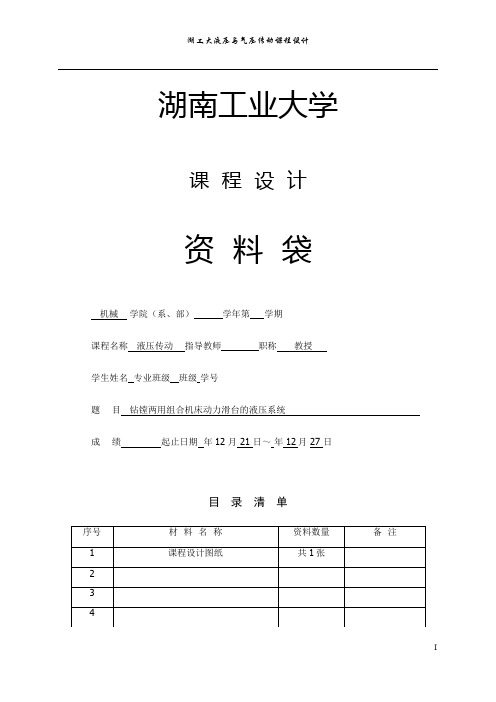
湖南工业大学课程设计资料袋机械学院(系、部)学年第学期课程名称液压传动指导教师职称教授学生姓名专业班级班级学号题目钻镗两用组合机床动力滑台的液压系统成绩起止日期年12 月 21 日~年 12月 27 日目录清单序号材料名称资料数量备注1 课程设计图纸共1张23456目录绪论 (1)1 钻镗液压机床的基本情况 (1)1.1机床的设计要求 (2)1.2 机床的相关设计参数 (2)2工况分析及液压缸的选择 (3)2.1分析系统工况 (3)2.1.1工作负载计算 (3)2.1.2惯性负载计算 (3)2.1.3阻力负载计算 (3)2.2负载循环图和速度循环图的绘制 (4)2.3主要参数的确定 (5)2.3.1 液压缸工作压力 (5)2.3.2 液压缸主要尺寸 (6)2.3.3 最大流量需求的计算 (7)3 液压系统原理图的绘制 (9)3.1 速度控制回路的选择 (9)3.2 换向和速度换接回路的选择 (10)3.3 油源的选择和能耗控制 (11)3.4 压力控制回路的选择 (12)4液压系统性能的验算 (15)4.1系统压力损失 (15)4.1.1判断流动状态 (15)4.1.2系统压力损失的计算 (15)4.2系统发热与温升的验算 (18)5 设计总结 (19)6 参考文献 (20)绪论设计目的为进一步加深学生对所学液压传动理论知识的理解,培养学生运用理论知识独立解决有关本课程实际问题的能力,使学生对液压系统工作原理图的设计有一完整和系统的概念;同时通过课程设计,培养学生计算,使用技术资料及绘制液压原理图的工程设计能力。
设计步骤首先对液压系统进行工况分析,通过分析计算,绘制速度、负载循环图,初步选定液压缸工作压力,并计算加紧液压缸和工作缸尺寸以及各阶段流经液压缸的流量;其次根据液压系统供油方式、调速方式、速度换接方式以及加紧回路的选择拟定液压系统图,并且对系统工作状态分析;最后通过对压力损失和系统升温的验算,对液压系统进行性能分析。
- 1、下载文档前请自行甄别文档内容的完整性,平台不提供额外的编辑、内容补充、找答案等附加服务。
- 2、"仅部分预览"的文档,不可在线预览部分如存在完整性等问题,可反馈申请退款(可完整预览的文档不适用该条件!)。
- 3、如文档侵犯您的权益,请联系客服反馈,我们会尽快为您处理(人工客服工作时间:9:00-18:30)。
座 、电气部分组成 。X 0 D1A铣削头安装在机械滑 台上 带动镗 杆套上 的刀杆进行切 削加工 ,固定镗杆后的把手 ,镗杆 里的
求十分严格 ,其同轴度要 求小于 0 2m . m,一些 企业 内部没 0
刀杆向前运动进行加工轴承座孔及其端面。
进行冬期施工 ,若采取的措施 不当,会给施工的工程带来不利的影响 ,极易给 量事故 ;正确选择施工方法 ,可以保证 工程质量取得较好的经济效益。 【 关键词 】冬期施工 ;平均气温 ;混凝土 ;施 工过程 【 中图分类号 ]T 7 58 U 5. [ 文献标识码 ]B [ 文章编号】1 . 6 / IS 09 04 . 1 . . 3 0 9 9 N 10 — 122 0 0 3 JS 017 2
的刀套连接镗杆 ,使镗杆 带动刀杆 进行加工 ,刀杆横 向进给 量是靠铣削头下面的机械滑 台来实现 。如 图 1 所示 。
堕
.
l’
/ 丛 /一 一
,
厂
H h
I
图 1 组 合动 力镗 床 结 构 简 示 意
工 作 进 给 速 度 范 围 1. 4 5r n 45 0 mi /
快 速行程 电动机
Y 0 - 9 14
镗杆里采用三组 圆锥齿轮 ,两组渐 开线圆柱齿轮以及丝 杠 、丝母等实现了镗杆 、刀杆 的旋 转 ,两刀杆在同一镗杆轴
[ 收稿 日期 ]2 1- 6 2 0 10 — 0
上的伸缩以及前后进给的功能 ,解决 了同轴度 要求高 ( 小于
4 9
辽 宁 建 材 2 1 年 第 7 期 01
浅谈冬期施工中应注意的问题
赵会德 (灯塔 市 工程 质量监 督站 ,辽 宁 辽 阳 13 0 1 0 1)
【 摘 要 】 健 筑工程冬期施 工技术规程》 ( J0- )规范规定 ,当室外 日平均气温连续 5 J 14- G  ̄7 天稳 定低于 5 ℃即进 入冬期施工 , 工程建设施工过程 中,受自然气候的影响 ,加之工程建设的进 度需 要 , 时不可避免的要 在 有
鄂式破 碎机 所取 代 ,这 样 给加 工鄂 式破 碎机 的机体 带 来难 机 用现有 设备 " 1 1 2或 T 2 6镗 床加 工 ,其主 轴直 径 q 6 7 6 61  ̄0 1
m m ,
功率
转速
1 W .k 5
1 0 mi 0r n 5 /
快速移动速度 镗杆直径 手柄转动一圈刀杆前进
◎ 研 究 与 应 用
浅析 组合动 镗 的设 计 力
李 永 军 ,刘 春英
(朝 阳重 型机 器有 限公 a,辽 宁 朝 阳 120 20 0)
[ 摘 要 ]本文主要介绍组合动力镗 的设 计 ,此设备可加] 大规 格 、大跨距轴 承座里孔设 备 ,结构简单 ,使用方便 , : 是一种加 工轴承座孔 间距大及轴承孔 同轴度要 球 高的专用设备 。 较
围 内的各种 工件 的轴承座里孔及端面 。
旋转的同时 前后进给功能, 在工作时铣削 头带动镗杆及刀杆
在旋转 同时前后进给 功能 ,镗杆又通过传动装置使刀杆进 行 旋转和前后进给运动。 主轴 转动是 由 X 0 D1A铣 削头来 实现 。由电动机 经过 皮
带轮传递给铣 削头 ,铣削头由 8组交换齿轮可实现不 同的主
率非常低. 后采用活镗杆 ,镗杆里采用三组圆锥齿轮 ,两组渐 开线 圆柱齿 轮 ,以及丝杠 、丝母等部件实现 了镗杆及 刀杆 在
2 用途
该组合 动力镗 用于轴 承里孔 直径 大于 20m 0 m,轴承 孔 两挡距小 于 22 0m 的备种破 碎机 ,也可适 用于镗 适合 范 0 m
有满足它的设备 , 用镗床镗 里孔主轴伸缩量不够 ,只能掉个 找正加工 ,很难保证两轴孔在 同一条直线上 ,满 足不 了鄂式
破 碎机 的设 计 要 求 ,针对 这 种 情 况 设计 了组 合 动 力 镗 床 T0—。 G 5 9
最初设计 时 , 轴承 座镗杆里面加一个 固定刀杆 , 具 在 刀 进给需要 人工一 次次 上刀 ,费时费力 ,劳动强度高 ,生产 效
电机转速 主轴滑 套直径
H 4 A机械滑台 T0 滑台面宽 滑 台 面 长 最 大行程
工 作进 给 电 动机 功率
9 0r n 7 mi / 2 0m 2 m
4 0m 0 m 1 0 m 0m 0 6 0ln 3 l n
Y 0 — 824 07 W . k 5
两刀杆之间的距离
64m m n . / i 20 mm 0 O3 m -m
1 0 n I 0 IT 4 l
度, 是机体上两轴承座之间的跨距比 原因 较大, 规格 小 破碎 3 构 成
主轴镗杆 行程 在 1 0 a n 间。 0r 之 2 i
中小企 业 生产 较大 一些 的 鄂式 破碎 机 ,轴 承孔 距 在 1 5 0 20 0m 0 — 0 m之间 ,而鄂式破 碎机 机体 轴承 座里 孔的精度要
规格号 陧 : 能
X IA铣削头 DO 主轴电机 功率 Y10 6 6 M一 75 k . W
轴转速 , 同零件 的加 工选用不同的交换齿轮 。企业生产 的 不
鄂式破碎机 机体 ,交换齿 轮一般选择 ,主轴转速 7 转/ i, mn l 交换齿 轮为 2 /3 ( 动比为 2 /3 ,通过一 个锥度 为 72 94 传 9 ) 4 :4
[ 关键词 ]机体 ;同轴度 ;动 力镗 ;铣 削 ;齿轮 ;轴承座
[ 中图分类号 ]T 5 9 G 3 [ 文献标识 码 ]B [ 文章编号] 1.9 9 S 0 9 0 4 . 1 . .2 03 6 / I N 10 — 122 0 0 2 JS 017
1 前 言
由于近年来矿 山 、冶金 、水泥行业的迅猛发展 。鄂式破 碎机的应用范 围越来越广 泛 ,销量越来越大 。各 种小 规格的 鄂式破碎机 已经满足不 了社 会发展的需要 ,逐渐被大 规格的