石灰石及石灰石浆液的化学分析
石灰石化学分析方法
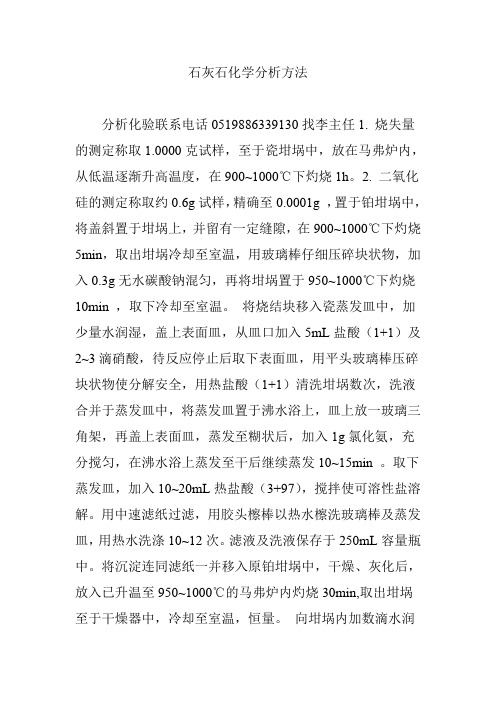
石灰石化学分析方法分析化验联系电话0519886339130找李主任1. 烧失量的测定称取1.0000克试样,至于瓷坩埚中,放在马弗炉内,从低温逐渐升高温度,在900~1000℃下灼烧1h。
2. 二氧化硅的测定称取约0.6g试样,精确至0.0001g ,置于铂坩埚中,将盖斜置于坩埚上,并留有一定缝隙,在900~1000℃下灼烧5min,取出坩埚冷却至室温,用玻璃棒仔细压碎块状物,加入0.3g无水碳酸钠混匀,再将坩埚置于950~1000℃下灼烧10min ,取下冷却至室温。
将烧结块移入瓷蒸发皿中,加少量水润湿,盖上表面皿,从皿口加入5mL盐酸(1+1)及2~3滴硝酸,待反应停止后取下表面皿,用平头玻璃棒压碎块状物使分解安全,用热盐酸(1+1)清洗坩埚数次,洗液合并于蒸发皿中,将蒸发皿置于沸水浴上,皿上放一玻璃三角架,再盖上表面皿,蒸发至糊状后,加入1g氯化氨,充分搅匀,在沸水浴上蒸发至干后继续蒸发10~15min 。
取下蒸发皿,加入10~20mL热盐酸(3+97),搅拌使可溶性盐溶解。
用中速滤纸过滤,用胶头檫棒以热水檫洗玻璃棒及蒸发皿,用热水洗涤10~12次。
滤液及洗液保存于250mL容量瓶中。
将沉淀连同滤纸一并移入原铂坩埚中,干燥、灰化后,放入已升温至950~1000℃的马弗炉内灼烧30min,取出坩埚至于干燥器中,冷却至室温,恒量。
向坩埚内加数滴水润湿沉淀,加3滴硫酸(1+4)和5mL氢氟酸,放入通风橱缓慢加热,蒸发至干,升高温度继续加热至三氧化硫白烟完全散尽。
将坩埚放入已升温至950~1000℃内灼烧30min,取出坩埚至于干燥器中,冷却至室温,恒量。
经氢氟酸处理后得到的残渣中加入1g焦硫酸钾,在500~600℃下熔融至透明,熔块用热水和数滴盐酸(1+1)溶解,溶液并入分离二氧化硅后得到的滤液和洗液中,用水稀释至标线,摇匀。
3. 氧化钙的测定吸取25mL于400mL烧杯中,加水稀释约200mL,加5mL三乙醇胺(1+2)及适量的CMP(1.000g钙黄绿素、1.000g甲基百里香酚蓝、0.200g酚酞、50g已在105℃烘干过的硝酸钾)混合指示剂,在搅拌下加入氢氧化钾(200g/L)至出现绿色荧光后再过量5~8mL ,以EDTA(0.015mol/L)滴定至绿色荧光消失并出现红色。
石灰石化学分析方法
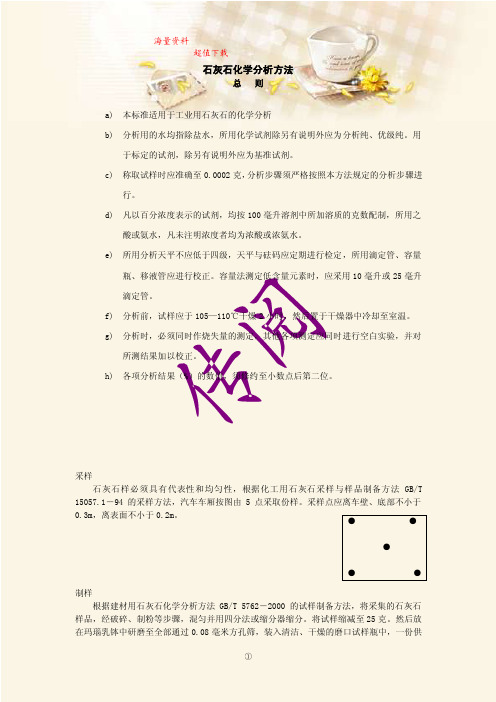
石灰石化学分析方法总 则a) 本标准适用于工业用石灰石的化学分析b) 分析用的水均指除盐水,所用化学试剂除另有说明外应为分析纯、优级纯。
用于标定的试剂,除另有说明外应为基准试剂。
c) 称取试样时应准确至0.0002克,分析步骤须严格按照本方法规定的分析步骤进行。
d) 凡以百分浓度表示的试剂,均按100毫升溶剂中所加溶质的克数配制,所用之酸或氨水,凡未注明浓度者均为浓酸或浓氨水。
e) 所用分析天平不应低于四级,天平与砝码应定期进行检定,所用滴定管、容量瓶、移液管应进行校正。
容量法测定低含量元素时,应采用10毫升或25毫升滴定管。
f) 分析前,试样应于105—110℃干燥2小时,然后置于干燥器中冷却至室温。
g) 分析时,必须同时作烧失量的测定,其他各项测定应同时进行空白实验,并对所测结果加以校正。
h) 各项分析结果(%)的数值,须修约至小数点后第二位。
采样石灰石样必须具有代表性和均匀性,根据化工用石灰石采样与样品制备方法 GB/T 15057.1―94 的采样方法,汽车车厢按图由5点采取份样。
采样点应离车壁、底部不小于0.3m ,离表面不小于0.2m 。
制样根据建材用石灰石化学分析方法 GB/T 5762―2000的试样制备方法,将采集的石灰石样品,经破碎、制粉等步骤,混匀并用四分法或缩分器缩分。
将试样缩减至25克。
然后放在玛瑙乳钵中研磨至全部通过0.08毫米方孔筛,装入清洁、干燥的磨口试样瓶中,一份供● ● ● ● ●试验分析使用,一份作为原样保存备用。
并注明生产单位名称、采样人员及采样日期。
样品保存期为个月。
一、石灰石试样溶液的制备1、方法提要:试样置于铂金坩埚中以碳酸钾—硼砂混合熔剂熔融,熔融物以硝酸加热浸取。
2、化验试剂:(1)碳酸钾—硼砂(1+1)混合熔剂:将1份重量的碳酸钾与一份重量的无水硼砂混匀研细,贮存于磨口瓶中。
(2)硝酸(1+6):将1体积的硝酸与6体积的水混合。
3、制备步骤:称取约0.5克试样于铂金坩埚中,加2克碳酸钾—硼砂混合熔剂混匀,再以少许熔剂清洗玻璃棒,并铺于试样的表面。
石灰石的化学分析方法

石灰石的化学分析方法⒈1试样的制备试样必须具有代表性和均匀性。
由大样缩分后的试样不得少于100g,试样通过0.08mm 方孔筛时的筛余不应超过15%。
再以四分法或缩分器减至约25g,然后研磨至全部通过孔径为0.008mm方孔筛。
充分混匀后,装入试样瓶中,供分析用。
其余作为原样保存备用。
⒈2烧失量的测定⒈⒉1方法提要试样中所含水分、碳酸盐极其他易挥发性物质,经高温灼烧即分解逸出,灼烧所失去的质量即为烧失量。
⒈⒉2分析步骤称取约1g试样(m),精确至0.0001g,置于已灼烧恒量的瓷坩锅中,将盖斜置于坩锅上,放入马弗炉内,从低温开始逐渐升温,在950~1000℃下灼烧1h,取出坩锅置于干燥器中,冷却至室温,称量。
反复灼烧,直至恒量。
⒈⒉3结果表示烧失量的质量百分数X LOI 按式(1.1)计算:m-m1X LOI =————×100 ......................(1.1)m式中: X LOI—烧失量的质量百分数,%;m—灼烧后试料的质量,g;1m—试料的质量,g。
⒈⒉4允许差同一实验室的允许差为:0.25%;不同实验室的允许差为:0.40%。
⒈3二氧化硅的测定(基准法)⒈⒊1方法提要试样以无水碳酸钠烧结,盐酸溶解,加固体氯化铵于沸水浴中加热蒸发,使硅酸凝聚,灼烧称量。
用氢氟酸处理后,失去的质量即为二氧化硅含量。
⒈⒊2分析步骤称取约0.6g试样(m2 ),精确至0.0001g,置于铂坩锅中,将盖斜置于坩锅上,在950~1000℃下灼烧5min,取出铂坩锅冷却至室温,用玻璃棒仔细压碎块状物,加入0.3g研细无水碳酸钠混匀。
再将坩锅置于950~1000℃下灼烧10min,取出冷却至室温。
将烧结物移入瓷蒸发皿中,加少量水润湿,盖上表面皿。
从皿口加入5mL盐酸(1+1)及2~3滴硝酸,待反应停止后取下表面皿,用平头玻璃棒压碎块状物使分解完全,用热盐酸(1+1)清洗坩锅数次,洗液合并于蒸发皿中。
火电厂脱硫系统化验数据解析与控制

火电厂脱硫系统化验数据解析与控制摘要:本文对脱硫系统石灰石(粉)、石灰石浆液、石膏、吸收塔浆液、工艺水的化学成份的解析及控制措施,从而实现导向脱硫系统的操作的目的.希望可以对其他电厂脱硫系统安全稳定运行和运行管理起到借鉴作用.关键词:火电厂;烟气脱硫;化验数据分析一、火电厂脱硫系统现状1.火电厂脱硫系统分类脱硫系统是火电厂重要的工艺设施,也是最基本、效率最高且最为关键的设备。
它不仅能够将烟气中所含的SO2进行回收利用,从而达到减少排放量和节约资源消耗目的,还可以提高能源使用效果。
根据不同类型脱除酸兰石化雾化二氧化钛气体来划分:酸性氧化塔为石灰石型结构;亚硫酸钠为硫酸盐型;硫化氯化铝、磷酸二氢钾等作为燃料的蒸汽锅炉。
其脱硫系统分为两个子厂房和三个子车间。
其中,酸性氧化塔为石灰石型结构。
亚硫酸钠、硫化氯化铝及硫化镁作为原料,经过水洗与除尘后再进行燃烧生成SO2等气体的过程称为酸兰石化雾化二氧化钛气净化装置(PDEM)。
燃煤电厂为烟粉锅炉,湿式炉渣为主要渣种,热力加热所产生的废气物即为脱硫塔中主要工艺。
2.脱硫工艺的安全结构脱硫工艺的安全结构主要是由以下几部分组成:①防火门和消防通道。
在火电厂中,有许多的设备,因此必须要做好防震措施。
首先是对其进行合理布局,比如设置防火门、消防车道以及相应数量出入口等;其次是将风管与水循环系统相连接或通过管道联通到锅炉房内来实现对整个燃烧过程的控制;最后是需要保证安全阀处于正常工作状态下才可以使用。
②锅炉房门。
对于火发电厂来说,在进行脱硫工艺过程中,需要保证其与电厂的安全阀、消防通道以及相应数量等都要保持一致。
比如说:对风管和消防水泵进行合理布局;同时还要注意防火管道与锅炉房之间的距离一定不要太大或者太小了,会影响烟气处理装置和燃烧设施之间是否能够顺利运行工作。
3.火力发电厂脱硫系统的运行特点与特性火电厂在脱硫系统的设计与运行中,主要有以下几个特点:①燃煤锅炉压力高,受热面面积大。
石灰石活性

石灰石/石膏湿法烟气脱硫系统石灰石活性研究脱硫系统一般要求CaCO3不低于90%,石灰石中往往含有少量的MgCO3,它通常以溶解形式或白云石形式存在。
在吸收塔中,白云石往往不溶解,而是随副产物离开系统。
因此含高浓度白云石的石灰石活性较低。
石灰石活性影响系统的脱硫性能及石膏的品质。
溶解石灰石为脱硫化学反应提供吸收SO2所需Ca2+及碱度,故要求活性越高越好。
1石灰石活性的研究概况石灰石/石膏湿法脱硫过程可以划分为5个阶段:(1)溶质SO2由气相主体扩散到气液两相界面气相的一侧;(2)SO2在相界面上的溶解,并转入液相;(3)SO2电离,同时剩余的SO2由液相界面扩散到液相主体;(4)石灰石的溶解、电离与扩散;(5)反应产物向液相主体的扩散及反应产物沉淀的生成。
5个阶段是同时进行的。
步骤2、3、5是快速离子反应,由化学动力学可知总化学反应速率由步骤1和4即气相中SO2的扩散(气相阻力,如式1~4所示)和石灰石固体的液相溶解(液相阻力,如式5~6所示)决定的。
降低液相阻力可以提高化学反应速率,进而提高整体系统性能,对于石灰石活性的研究都是从降低石灰石溶解的液相阻力入手的。
1.1国外石灰石活性研究情况1.1.1石灰石物理性质对活性的影响石灰石中主要有效成分是CaCO3,因此石灰石中CaCO3的含量对活性有重要影响。
石灰石中CaCO3含量越高,其活性越大。
由于白云石(MgCO3·CaCO3)比方解石(CaCO3)的溶解速率低3~l0倍,当石灰石纯度较低(CaCO3含量<85%wt)或者要求对石灰石要有较高的利用率时,白云石等杂质会大大降低石灰石的溶解。
MgCO3含量过高时,还容易产生大量可溶的MgSO3,减小SO2气相扩散的化学反应推动力,严重影响石灰石化学活性,因此设计时对石灰石中CaCO3含量一般要求高于90%。
石灰石粒径越小,比表面积越大,液固接触越充分,从而能有效降低液相阻力,故石灰石活性就越好,Chart和Rochelle1采用定pH值滴定法研究石灰石溶解特性,发现石灰石溶解速率是溶液组成、粒径分布的函数,与其表面粗糙度等无关。
浆液中毒

浆液中毒,有的同行称之为“盲区”,国外的文献上叫做“棕泥”现象。
;出现浆液中毒的原因是浆液中的氟离子和铝离子反应生成了氟化铝和其他物质的络合物,这种络合物呈粘性的絮凝状态,会封闭石灰石颗粒的表面,阻止石灰石颗粒的溶解,因此出现中毒时,加入石灰石吸收剂浆液的pH值不会升高,脱硫效率大大下降。
解决浆液中毒的办法是用新鲜浆液逐步替换已经中毒的浆液,另外也可以在中毒的浆液中加入NaOH来提高浆液的pH值。
要注意的一点是中毒浆液的恢复过程需要比较长的时间,根据国内电厂的经验,加入NaOH的时间要2-3天。
浆液中的氟离子的来源是烟气中的氟化氢、石灰石中的可溶性氟化物以及补给水中的氟离子;铝离子主要来自除尘器未脱除的飞灰中的Al2O3。
因此要避免中毒现象,首先要限制进入脱硫塔烟气中飞灰的浓度,其次要控制工艺水中的氟离子的含量。
现象:原烟气SO2总量不变时增加CaCO3浆液而PH值持续降低,脱硫率下降。
危害:脱硫率下降达不到预期脱硫效果,污染环境;pH值降低,加剧吸收塔内部腐蚀;过量的CaCO3浆液造成原材料浪费。
原因:1、FGD进口SO2浓度突变引起石灰石盲区;基本机理:由于烟气量或FGD进口原烟气SO2浓度突变,造成吸收塔内反应加剧,CaCO3含量减少,PH值下降,此时若石灰石供浆流量自动投入为保证脱硫效率则自动增加石灰石供浆量以提高吸收塔的PH值,但由于反应加剧吸收塔浆液中的CaSO3·1/2H2O含量大量增加,若此时不增加氧量使CaSO3·1/2H2O迅速反应成CaSO4·2H2O,则由于CaSO3·1/2H2O可溶解性强先溶于水中,而CaCO3溶解较慢,过饱和后形成固体沉积,这种现象称为“石灰石盲区”。
2、吸收塔浆液密度高没有及时外排,浆液中的CaSO4·2H2O饱和会抑制CaCO3溶解反应;3、电除尘后粉尘含量高或重金属成分高,在吸收塔浆液内形成一个稳定的化合物,附着在石灰石颗粒表面,影响石灰石颗粒的溶解反应,导致石灰石浆液对PH值的调解无效;4、氧化不充分引起亚硫酸盐致盲;(原理如1)5、工艺水水质差,系统中的氯离子浓度高,石灰石粉品质差,引起吸收塔浆液发生石灰石盲区。
田集电厂脱硫化验分析方法(20091012)

脱硫化学测试项目及其测试方法烟气脱硫化学测试是对脱硫系统运行中各主要参数的测试,根据测得的参数来判断系统目前的运行情况及应采取的措施,因此化学测试是在整个系统启动后进行的工作。
化学测试的内容主要包括:1、石灰石粉品质测定2、石灰石浆液的密度浓度测试3、吸收塔浆液的测试4、石膏品质的测试以上测试项目的具体测试内容及频次见下表:备注:●:1次/天▲:1次/3天╱:无此测试项石灰石粉末、石灰石浆液、吸收塔浆液、石膏的分析原理下面将做简要的介绍。
1、石灰石粉末。
石灰石粉末是烟气脱硫的吸收剂,对石灰石粉末的测试主要是对石灰石中的碳酸钙和碳酸镁以及细度、酸不溶物的测试。
碳酸钙、碳酸镁的分析方法依照《化工用石灰石的分析》的分析方法及数据处理。
酸不溶物的测试原理是称一定质量的石灰石粉末,以盐酸溶解,过滤,烘干不溶部分然后称量,根据不溶解部分的质量可计算出酸不溶物的含量。
2、石灰石浆液。
石灰石浆液的密度和浓度都是根据重量法而得出。
量取一定体积的浆液称其质量,根据质量与体积比可得出其密度。
浓度的测试原理是称取一定质量的浆液过滤,烘干不能通过滤膜的部分,称其质量,根据质量的比值即可知道其浓度。
3、吸收塔浆液。
以PH计测PH值。
密度的测量方法同石灰石浆液密度的测量。
亚硫酸盐以碘量法测量,在亚硫酸盐的吸收液(I2液)中加入样品,亚硫酸根离子被氧化,多余的I2用硫代硫酸钠溶液滴定。
根据消耗的硫代硫酸钠溶液的量可以计算出亚硫酸盐的含量。
碳酸盐测定采用滴定法,在盐酸的作用下二氧化碳被蒸发出以氢氧化钠吸收,过量的氢氧化钠用盐酸滴定,根据盐酸的消耗量可计算出碳酸盐含量。
酸不溶物的含量测试方法同石灰石粉末的测试。
氯离子是以硝酸汞为滴定液二苯偶氮碳铣肼-二甲苯蓝FF-溴酚蓝为指示剂进行滴定。
4、石膏。
石膏中水分含量采用重量法,在45度下烘干,根据其烘干前后质量差可计算出水分含量。
石膏中其它成分的测定方法见吸收塔中的分析方法。
其他项目的测量方法同石灰石粉末和吸收塔浆液的分析方法。
FGD脱硫系统化验分析规程最终版

FGD脱硫系统化验分析规程编制:审核:批准:北京国电清新环保技术股份有限公司托县运行分公司2011年11月目录第一章托克托电厂脱硫实验规程第二章实验方法石灰石部分一、石灰石中二氧化硅的含量%二、石灰石中氧化钙与氧化镁的含量%三、石灰粉的细度的测量%四、石灰石浆液密度的测量g/cm3五、石灰石粉反应速率的测定六、石灰石中盐酸不溶物含量的测定石膏部分一、石膏中碳酸钙的含量%二、石膏硫酸盐含量%三、石膏亚硫酸盐的测定%四、石膏浆液密度g/cm3五、石膏PH值六、测定石膏浆液中的氯离子mg/l七、脱水石膏氯离子含量的测定ppm八、脱水石膏附着水和结晶水的测定第三章标准溶液的配制化验室安全附密度和质量百分比关系第一章托克托电厂国电运行分公司脱硫试验规程1、范围本规程针对托电发电厂1 —8号机组的脱硫设备运行中各个阶段的化验监督,是脱硫试验人员在进行脱硫实验的标准和依据,必须严格执行操作中的有关规定,保证脱硫系统中各个阶段的化验工作的准确性。
2 概述烟气脱硫的方法很多,根据物理及化学的基本原理,大体上可分为吸收法、吸附法、催化法三种。
吸收法是净化烟气中SO的最重要的、应用最广泛的方法,吸收法通常是指应用液体吸收净化烟气中的SO,因此吸收法烟气脱硫也称为湿法烟气脱硫。
湿法烟气脱硫的优点是脱硫效率高,一般可达95%以上;我厂湿法烟气脱硫采用石灰石一石膏法。
2.1 FGD流程简述2.1.1石灰石贮存及浆液制备系统石灰石(粒径w 20mm卸入卸料斗,经石灰石给料机送入斗式提升机,然后由斗式提升机、皮带输送机送至石灰石贮仓内贮存。
石灰石由皮带称重给料机送到湿式球磨机内进行研磨,FGD补给水或滤液按与送入的石灰石成定比的量加入球磨机的入口。
石灰石在球磨机中被磨成粉末,浆液自流至浆液循环泵,然后再由浆液循环泵送至石灰石水力旋流器,底流返回至湿式球磨机继续研磨,从旋流器溢流出来的合格的石灰石浆液存贮于石灰石浆液箱中配置成30%勺浆液,经石灰石浆液给料机送至各吸收塔。
《石灰石化学分析方法 元素含量的测定 X射线荧光光谱法》

《石灰石化学分析方法 元素含量的测定 X 射线荧光光谱法》行业标准审定会会议纪要2013年9月24~27日,行业标准《石灰石化学分析方法 元素含量的测定 X 射线荧光光谱法》审定会在全国有色金属标准化技术委员会主持下在广西壮族自治区河池市巴马县召开,来自全国9个单位的21名代表和专家参加了会议。
会议对中铝广西分公司、中铝河南分公司等单位提出的标准送审稿进行了认真、热烈的讨论,达成一致意见,形成会议纪要如下:1、标准名称与计划名称不一致,将《石灰石化学分析方法 第一部分:X 射线荧光光谱法测定元素含量》更正为《石灰石化学分析方法 元素含量的测定 X 射线荧光光谱法》,对其翻译部分进行修改,将标准号YS/T703-2009替换成YS/T703-201X 。
2、将熔片法和压片法整合成一个标准,确定熔片法由中铝广西分公司来完成,压片法由中铝河南分公司来完成。
3、前言部分应增加以下内容:3.1 本标准按照GB/T1.1-2009给出的规则修订。
3.2 本标准由全国有色金属标准化技术委员会(SAC/TC243)归口。
3.3 确定熔片法为方法1,压片法为方法2。
3.4 起草单位中补加“中国铝业股份有限公司河南分公司”。
3.5 补加“本标准所代替标准的历次版本情况如下:YS/T703-2009”。
4、测量范围中测量元素顺序按照“钙、镁、硅、铁、铝、钾”来绘制表1。
5、在规范性引用文件栏中删除“YS/T703-2009 X 射线荧光光谱法测定石灰石中CaO 、MgO 、SiO 2含量”。
6、熔剂的计算因子公式“F =/1100L m ⎛⎫- ⎪⎝⎭”更改为“F =100100L -”。
7、将高温炉温度控制“1000℃±10℃”更改为“1100℃±20℃”。
8、方法1与方法2中的试剂、仪器设备统一叙述。
9、步骤:按照方法1和方法2分别来叙述,序号格式按照下列要求编写:熔片法:7.1 方法1;压片法:7.2 方法2.10、两种方法中的分析结果的计算方法可以统一。
石灰石石膏法
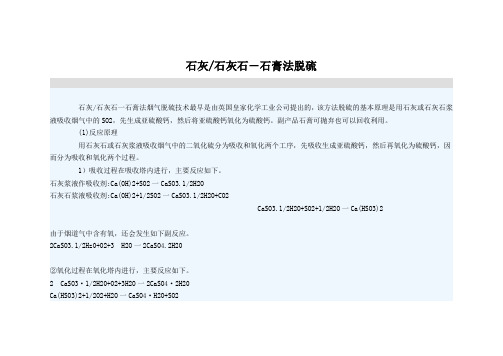
石灰/石灰石-石膏法脱硫石灰/石灰石一石膏法烟气脱硫技术最早是由英国皇家化学工业公司提出的,该方法脱硫的基本原理是用石灰或石灰石浆液吸收烟气中的SO2,先生成亚硫酸钙,然后将亚硫酸钙氧化为硫酸钙。
副产品石膏可抛弃也可以回收利用。
(1)反应原理用石灰石或石灰浆液吸收烟气中的二氧化硫分为吸收和氧化两个工序,先吸收生成亚硫酸钙,然后再氧化为硫酸钙,因而分为吸收和氧化两个过程。
1)吸收过程在吸收塔内进行,主要反应如下。
石灰浆液作吸收剂:Ca(OH)2+SO2一CaSO3.1/2H2O石灰石浆液吸收剂:Ca(OH)2+1/2SO2一CaSO3.1/2H2O+CO2CaSO3.1/2H2O+SO2+1/2H2O一Ca(HSO3)2由于烟道气中含有氧,还会发生如下副反应。
2CaSO3.1/2Hz0+O2+3 H2O一2CaSO4.2H20②氧化过程在氧化塔内进行,主要反应如下。
2 CaSO3·1/2H20+O2+3H2O一2CaSO4·2H20Ca(HSO3)2+1/2O2+H2O一CaSO4·H2O+SO2传统的石灰/石灰石一石膏法的工艺流程如图所示。
将配好的石灰浆液用泵送人吸收塔顶部,经过冷却塔冷却并除去90%以上的烟尘的含Sq烟气从塔底进人吸收塔,在吸收塔内部烟气与来自循环槽的浆液逆向流动,经洗涤净化后的烟气经过再加热装置通过烟囱排空。
石灰浆液在吸收so:后,成为含有亚硫酸钙和亚硫酸氢钙的棍合液,将此混合液在母液槽中用硫酸调整pH值至4左右,送人氧化塔,并向塔内送人490kPa的压缩空气进行氧化,生成的石膏经稠厚器使其沉积,上层清液返回循环槽,石膏浆经离心机分离得成品石膏。
现代石灰/石灰石一石膏法工艺流程主要有原料运输系统、石灰石浆液制备系统、烟气脱硫系统、石膏制备系统和污水处理系统。
①原料运输系统烟气脱硫所需的石灰石粉(粒度为250目,筛余量为5%),采用自卸封罐车运输,并卸人石灰石料仓。
《石灰石化学分析方法 元素含量的测定 X射线荧光光谱法》编制说明

《石灰石化学分析方法元素含量的测定 X射线荧光光谱法》行业标准(报批稿)编制说明一、工作情况1、任务来源根据工信厅科〔2013〕102号文件要求和全国有色金属标准化技术委员会2013年有色金属行业标准制修订项目计划, 中国铝业股份有限公司广西分公司和中国铝业股份有限公司河南分公司承担(YS/T 703-2009)行业标准的修订工作,项目计划编号:2013-0298T-YS,计划起始年为2013年,完成年限为2014年。
2、标准修订单位简介中国铝业股份有限公司广西分公司直属大型跨国上市公司中国铝业股份有限公司。
分公司下设12个部室和11个二级生产单位。
现有员工7000余人,其中高级职称169人,中级职称589人,各类专业技术人员1600多人,技术力量雄厚。
企业的主导产品目前已形成年生产能力砂状氧化铝252万吨、电解铝15万吨、阳极碳块8万吨、铁精矿22万吨,成为中国铝业的核心企业。
广西分公司在矿山开采、氧化铝及铝电解生产中大量采用了国际、国内先进的生产工艺,在生产过程中又相继自主开发,研制了以强化拜耳法生产氧化铝新工艺为代表的一大批拥有自主知识产权的新工艺、新设备,极大提高氧化铝拜耳法生产技术,并多次获得省部级各项科技进步奖,使分公司生产工艺水平、产量及产品质量有了大幅度提高,主要产品氧化铝质量指标达到砂状氧化铝要求,在行业中处于领先地位。
多年来积极参与标准的制定工作,主要负责起草了《砂状氧化铝物理性能测定》、《氧化铝化学分析方法和物理性能测定方法新亚铜灵光度法测定氧化铜含量》、《氧化铝化学分析方法和物理性能测定方法火焰原子吸收光谱法测定氧化镁含量》、《X射线荧光光谱法测定氢氧化铝中SiO2、Fe2O3、Na2O含量》、《X射线荧光法光谱法测定石灰石中CaO、MgO、SiO2含量》、《重熔用铝锭》、《铝土矿石化学分析方法第4部分:三氧化二铁含量的测定重铬酸钾滴定法》、《铝土矿石化学分析方法第13部分:锌含量的测定火焰原子吸收光谱法》、《岩溶堆积型铝土矿山复恳技术规范》等国家和行业标准,参与起草了《重熔用铝锭》、《电解铝企业单位产品能源消耗限额》等国家和行业标准。
石灰石-石膏湿法脱硫工艺的基本原理
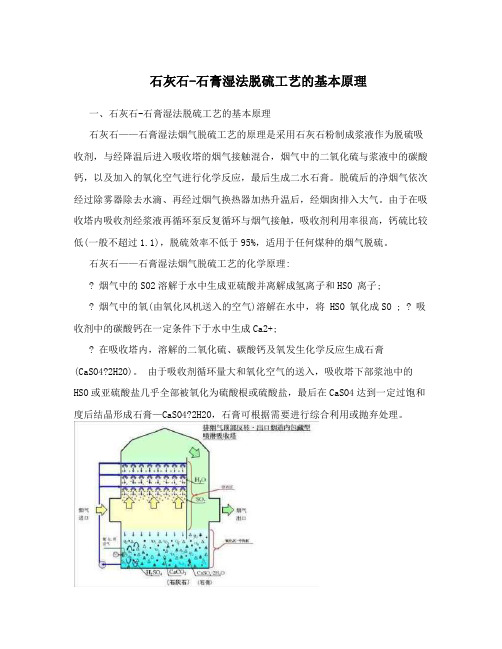
石灰石-石膏湿法脱硫工艺的基本原理一、石灰石-石膏湿法脱硫工艺的基本原理石灰石——石膏湿法烟气脱硫工艺的原理是采用石灰石粉制成浆液作为脱硫吸收剂,与经降温后进入吸收塔的烟气接触混合,烟气中的二氧化硫与浆液中的碳酸钙,以及加入的氧化空气进行化学反应,最后生成二水石膏。
脱硫后的净烟气依次经过除雾器除去水滴、再经过烟气换热器加热升温后,经烟囱排入大气。
由于在吸收塔内吸收剂经浆液再循环泵反复循环与烟气接触,吸收剂利用率很高,钙硫比较低(一般不超过1.1),脱硫效率不低于95%,适用于任何煤种的烟气脱硫。
石灰石——石膏湿法烟气脱硫工艺的化学原理:烟气中的SO2溶解于水中生成亚硫酸并离解成氢离子和HSO 离子;烟气中的氧(由氧化风机送入的空气)溶解在水中,将 HSO 氧化成SO ; ? 吸收剂中的碳酸钙在一定条件下于水中生成Ca2+;在吸收塔内,溶解的二氧化硫、碳酸钙及氧发生化学反应生成石膏(CaSO4?2H2O)。
由于吸收剂循环量大和氧化空气的送入,吸收塔下部浆池中的HSO或亚硫酸盐几乎全部被氧化为硫酸根或硫酸盐,最后在CaSO4达到一定过饱和度后结晶形成石膏—CaSO4?2H2O,石膏可根据需要进行综合利用或抛弃处理。
二、工艺流程及系统湿法脱硫工艺系统整套装置一般布置在锅炉引风机之后,主要的设备是吸收塔、烟气换热器、升压风机和浆液循环泵我公司采用高效脱除SO2的川崎湿法石灰石,石膏工艺。
该套烟气脱硫系统(FGD)处理烟气量为定洲发电厂,1和,2机组(2×600MW)100,的烟气量,定洲电厂的FGD系统由以下子系统组成:(1)吸收塔系统(2)烟气系统(包括烟气再热系统和增压风机)(3)石膏脱水系统(包括真空皮带脱水系统和石膏储仓系统)(4)石灰石制备系统(包括石灰石接收和储存系统、石灰石磨制系统、石灰石供浆系统) (5)公用系统(6)排放系统(7)废水处理系统1、吸收塔系统吸收塔采用川崎公司先进的逆流喷雾塔,烟气由侧面进气口进入吸收塔,并在上升区与雾状浆液逆流接触,处理后的烟气在吸收塔顶部翻转向下,从与吸收塔烟气入口同一水平位置的烟气出口排至烟气再热系统。
火电厂石灰石-石膏法脱硫浆液分析研究.doc

火电厂石灰石/石膏法脱硫浆液分析研究中国脱硫防腐网 2008-01-10 16:04:51 作者: 来源: 文字大小:[大][中][小]第(1)页第(2)页石灰石-石膏烟气湿法脱硫方法的有关反应方程式是?1)SO2 + H2O → H2SO3 吸收2)CaCO3 + H2SO3 → CaSO3 + CO2 + H2O 中和3)CaSO3 + 1/2 O2 → CaSO4 氧化4)CaSO3 + 1/2 H2O → CaSO3•1/2H2O 结晶5)CaSO4 + 2H2O → CaSO4 •2H2O 结晶6)Ca SO3 + H2SO3 → Ca(HSO3)2 pH 控制2008-12-09 | FGD系统化验测试项目及方法FGD系统化验测试项目及方法(草稿)1、目的为配合FGD系统调试,分析FGD系统运行状况,需要对FGD系统的烟气、石灰石原料、工艺水、石膏副产品和石膏浆液等项目进行化验分析测试,同时此分析测试也可为公司技术优化提供有力支持。
2、适用范围适用于FGD系统调试运行期间所需化验测试项目的实施。
3、职责3.1 研发部负责FGD系统调试运行期间所需化验测试项目的实施,并出具试验报告。
3.2 项目组、研发部、技术部和调试服务中心联合对试验报告进行讨论评审并进行备案。
4、需要化验测试的项目1、烟气参数和成分等2、石灰石品质3、吸收塔内石膏浆液的物性参数和成分4、石膏浆液旋流器顶流和底流的密度和含固量5、石灰石浆液旋流器溢流的密度和含固量6、脱水机出口的石膏副产品的含水率和成分7、脱硫排放的废水密度、含固量和惰性物质含量8、工艺水水质吸收塔浆液pH值、吸收塔浆液氯含量、吸收塔浆液CaCO3含量、吸收塔浆液CaSO3·1/2H2O含量、脱水石膏CaCO3含量、吸收塔浆液和水力旋流器底流的密度每天至少检查一次。
石灰石质量(化学和反应测试,颗粒尺寸)应每批检查一次或每三天检查一次。
当FGD出现非正常运行工况时,应适当加大相应项目的采样和测试频率。
石灰石石膏湿法脱硫化学分析

2.3.1 石灰石块粒度测试-筛分法
称取全部采集的样品,取出可能大于150mm粒度的 矿石,以任一角度放入150mm金属圆形筛孔内,称 量筛上物的量。大于150mm粒度的百分数计算公式
如下:
m1 X 100 m
2.3.2 石灰石粉细度(2种)
水筛法(附录B.2b) 方法原理
采用45 μm或63μm方孔筛,用筛上筛余物的质量分数来表 示石灰石浆液中石灰石的细度。 使用的称量瓶要保证恒重,在105 ~110 ℃下烘干30分钟 后,恒温恒重。 准确量取一定体积的石灰石浆液 ,倒入方孔筛内,调节水 龙头水压用水,筛内样品不能溅出。连续冲洗至筛底部出 水清晰透明为止。将石灰石粉自然凉干,用药匙和毛刷将 筛余物转移至称量瓶,在105-110℃烘干,冷却至室温称量。 反复烘干,直至二次重量相差不超过0.4mg,扣除称量瓶重 量即为筛余量。
DL/T943e-2005《烟气湿法脱硫用石灰石粉 反应速率的测定》 GB/T15057.2-1994《化工用石灰石中氧化钙和氧化镁含量的 测定》 GB/T15057.2-1994《化工用石灰石中氧化钙和氧化镁含量的 测定》
GB/T15057.3-1994《化工用石灰石中盐酸不溶物含量的测定》 GB/T15057.5-1994《化工用石灰石中二氧化硅含量的测定》
2、石灰石试验方法
2.1 使用标准
序 号 1 2 3 4 5 6 7 8 试验项目 方法名称 试验方法 GB/T 15057.11-1994a《化工用石灰石粒度的测定》 附录B.2b GB/T 1345-2005c《水泥细度检验方法 负压筛析法》 GB/T 2565d-1998《煤的可磨性指数测定方法》 石灰石块粒度 筛分法 石灰石粉细度 可磨性指数 活性 氧化钙 氧化镁 盐酸不溶物 二氧化硅 水筛法 负压筛析法 哈德格罗夫法 盐酸滴定法 EDTA滴定法 EDTA滴定法 重量法 钼蓝分光光度 法
石灰石-石膏湿法脱硫化学分析
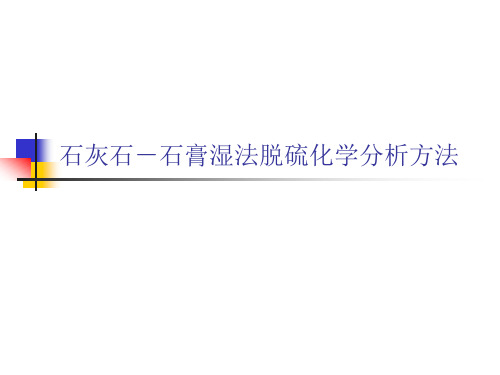
试样的烘干条件
石灰石 105~110℃下烘2小时 石膏和石膏浆液40~45 ℃下干燥
2、石灰石
2.1 CaO含量分析
方法参考GB/T 5762-2000 第14页氧化钙的测定(代用法) 原理:在酸性溶液中,加氟化钾,消除硅酸的干扰后, 在pH13以上的强碱中,以三乙醇胺为掩蔽剂,CMP为 指示剂,用EDTA溶液滴定。 注意点:1.指示剂的用量 2.终点的判断 3.计算公式
(3)影响沉淀溶解度的因素
影响沉淀平衡的因素很多,如同离子效应、盐效应,酸效应、 配位效应等。
同离子效应
当沉淀反应达到平衡后,若向溶液中加入含某一构晶离子的试剂 或溶液,则沉淀的溶解度减小,这一效应称为同离子效应。
盐效应
在难溶电解质的饱和溶液中,由于加入了强电解质而增大沉淀溶 解度的现象.称为盐效应。例如用Na2SO4作沉淀剂测定Pb2+时, 生成PbSO4。当PbSO4沉淀后,继续加入Na2SO4,就同时存在同离 子效应和盐效应。
EDTA滴定法 重量法(GB/T5484-2000)
重量法测三氧化硫含量
方法提要: 方法提要:在 酸 性 溶液中,用氯化钡溶液沉淀硫酸盐,经过滤灼 烧后,以硫酸钡形式称量,测定结果以三氧化硫计。 分析过程: 分析过程: 1.试样的分解 试样的分解。称 取 约 0.2 g 试样,置于300mL烧杯中,加人 试样的分解 30~40m L水使其分散。加10 mL盐酸(1+1),将溶液加热微沸5 min。用中速滤纸过滤,用热水洗涤10~12次。 2.沉淀。调整滤液体积至200 mL煮沸,在搅拌下滴加15 mL氯化 钡溶液,继续煮沸数分钟,然后移至温热处静置4h或过夜(此时溶 液的体积应保持在200 mL )。用慢速滤纸过滤,用温水洗涤,直 至检验无氯离子为止。 3.灰化、灼烧、称量。将沉淀及滤纸一并移人已灼烧恒量的瓷柑 祸中,灰化后在800 C的马弗炉内灼烧30 min,取出琳涡置于干 燥器中冷却至室温,称量。反复灼烧,直至恒量。
石灰石石灰法湿法烟气脱硫技术

化学成分,如氯化物。在酸性环境中,它们对金属(包括 不锈钢)的腐蚀性相当强。目前广泛应用的吸收塔材料是 合金C-276,其价格是常规不锈钢的15倍,为延长设备的 使用寿命,溶液中氯离子的浓度不能太高。为保证氯离子 不发生浓缩,有效地方法是在脱硫系统中根据物料平衡排 出适量的废水,以清水补充。
1.反应原理
用石灰石或者石灰浆液吸收烟气中的SO2,首先生成亚 硫酸钙:
石灰石:CaCO3+ SO2+0.5H2O→CaSO3•0.5H2O+CO↑ 石灰:CaO+ SO2+0.5H2O→CaSO3•0.5H2O
然后亚硫酸钙再被氧化为硫酸钙。
石灰石石灰法湿法烟气脱硫反应机 理比较表格
石灰石系统和石灰系统的主要区别
②结要原因,特别是硫酸钙结构坚硬、 板结,一旦结垢难以去除,影响到所有与脱硫液接触的阀 门、水泵、控制仪器和管道等。硫酸钙结垢的原因是SO42和Ca2+的离子积在局部达到过饱和。为此,在吸收塔中要 保持亚硫酸盐的氧化率在20%以下。亚硫酸盐的氧化需要 在脱硫液循环池中完成,可通过鼓氧或空气等方式进行, 形成的硫酸钙发生沉淀。从循环池返回吸收塔的脱硫液中, 还因为含有足量的硫酸钙晶体,起到了晶种的作用,因此 在后续的吸收过程中,可防止固体直接沉积在吸收塔设备
③除雾器堵塞:在吸收塔中,雾化喷嘴并不能产生尺 寸完全均一的雾滴,雾滴的大小存在尺寸分布。较小的雾 滴会被气流所夹带,如果不进行除雾,雾滴将进入烟道, 造成烟道腐蚀和堵塞。除雾器必须保持清洁,目前使用的 除雾器有多种形式(如折流板型等),通常用高速喷嘴每 小时数次喷清水进行冲洗。
④脱硫剂的利用率:脱硫产物亚硫酸盐和硫酸盐可沉 积在脱硫剂颗粒表面,从而堵塞了这些颗粒的溶解通道。 这会造成石灰石或石灰脱硫剂来不及溶解和反应就随产物 排除,增加了脱硫剂和脱硫产物的处理费用。因此脱硫液 再循环池中的停留时间一般要达到5~10min。实际的停留 时间设计与石灰石的反应性能有关,反应性能越差,为使 之完全溶解,要求它在池内的停留时间越长。
石灰石浆液成分

石灰石浆液成分石灰石浆液是一种常用的建筑材料,广泛应用于建筑、工程、冶金和环境保护等领域。
石灰石浆液的成分主要包括石灰石、水和其他辅助材料。
下面将对石灰石浆液的成分进行详细介绍。
1. 石灰石:石灰石是石灰石浆液的主要原料,其主要成分为碳酸钙(CaCO3)。
石灰石的颗粒大小可以根据具体的应用需求进行调整,通常使用的石灰石颗粒大小在数毫米到几厘米之间。
石灰石的质量、纯度和颗粒大小对石灰石浆液的性能有重要影响。
2. 水:水是石灰石浆液中的溶剂,起到溶解石灰石和调节浆液浓度的作用。
水的纯度和含量对石灰石浆液的性能和稳定性起到重要影响。
通常情况下,使用纯净水或经过处理的水作为石灰石浆液的溶剂。
3. 辅助材料:石灰石浆液中还可以添加一些辅助材料,用于改善其性能和加工工艺。
常见的辅助材料有以下几种:a. 分散剂:分散剂可以改善石灰石颗粒的分散性和稳定性,提高浆液的流动性和可加工性。
常用的分散剂有聚酸盐类、有机酸类和聚合物类等。
b. 粘结剂:粘结剂可以增加石灰石颗粒的粘结力和附着力,提高浆液的粘结性和强度。
常用的粘结剂有胶凝材料、胶体矿物和有机胶粘剂等。
c. 稳定剂:稳定剂可以防止石灰石颗粒的沉积和结块,提高浆液的稳定性和保存性。
常用的稳定剂有缓冲剂、防腐剂和抑制剂等。
d. 调节剂:调节剂可以调整石灰石浆液的性能和特性,满足不同应用领域的需求。
常用的调节剂有pH调节剂、温度调节剂和流变调节剂等。
以上就是石灰石浆液的主要成分介绍。
石灰石浆液的成分对其性能、稳定性和加工工艺都有重要影响,合理选择和控制石灰石、水和辅助材料的成分,可以提高石灰石浆液的品质和使用效果。
在实际应用中,还需要根据具体的工程要求和使用环境进行配方设计和工艺优化,以确保石灰石浆液达到预期的效果。
- 1、下载文档前请自行甄别文档内容的完整性,平台不提供额外的编辑、内容补充、找答案等附加服务。
- 2、"仅部分预览"的文档,不可在线预览部分如存在完整性等问题,可反馈申请退款(可完整预览的文档不适用该条件!)。
- 3、如文档侵犯您的权益,请联系客服反馈,我们会尽快为您处理(人工客服工作时间:9:00-18:30)。
石灰石及石灰石浆液的化学分析1 总则1.1 本方法适用于石灰石法烟气脱硫系统(简称FGD)石灰石(粉)及石灰石浆液的化学分析。
1.2 根据实际情况选用本方法。
1.3 分析用的水系指去离子水,所用化学试剂除另有说明外应为分析纯、优级纯。
用于标定的试剂,除另有说明外应为基准试剂。
1.4 称取试样时应准确至0.0002克,分析步骤须严格按照本方法规定的分析步骤进行。
1.5 凡以百分浓度表示的试剂,均按100毫升溶剂中所加溶质的克数配制(重/容)。
所用之酸或氨水,凡未注明浓度者均为浓酸或浓氨水。
1.6 所用分析天平不应低于四级,天平与砝码应定期进行检定。
所用滴定管、容量瓶、移液管应进行校正。
容量法测定低含量元素时,应采用10毫升或25毫升滴定管。
1.7 分析前,试样应于105—110℃干燥2小时,然后置于干燥器中冷却至室温。
1.8 分析时,必须同时作烧失量的测定。
其他各项测定应同时进行空白试验,并对所测结果加以校正。
1.9 各项分析结果(%)的数值,须修约至小数点后第二位。
2 试样2.1试样必须具有代表性和均匀性。
2.2采样时注意采样的部位和深度。
采集样品应进行缩分,由大样缩分后的试样不得少于100克,再以四分法或缩分器将试样缩减至约25克。
2.3送到化验室的粉末试样必须充分混匀,并应以磁铁吸除破碎石灰石时可能带入的铁屑。
2.4分析后剩余样品用密封袋装好后贴上标签作为原样保存备查。
将注明指标化验结果及化验时间的标签放入样袋内封存,样品保存一月。
3 分析3.1 试样溶液的制备原理:试样于铂坩埚中以碳酸钾-硼砂混合熔剂熔融,熔融物以硝酸加热浸取。
试剂:a.碳酸钾-硼砂(1+1)混合熔剂:将1份重量的碳酸钾与1份重量的无水硼砂混匀研细,贮存于磨口瓶中。
b.硝酸(1+6):将1体积的硝酸与6体积的水混合。
仪器:铂坩埚、玻璃棒、马弗炉、烧杯、天平、坩埚钳、量筒、容量瓶、洗瓶、铂坩埚三角架步骤:称取约0.5克试样置于铂坩埚中,加2克碳酸钾-硼砂混合熔剂,混匀,再以少许熔剂擦洗玻璃棒,并铺于试样表面。
盖上坩埚盖,从低温开始逐渐升高温度至气泡停止发生后,在950—1000℃下继续熔融3—5分钟。
然后用坩埚钳夹持坩埚旋转,使熔融物均匀地附着于坩埚内壁。
冷却至室温后将坩埚及盖一并放入已加热至微沸的盛有100毫升硝酸的300毫升烧杯中,并继续保持微沸状态,直至熔融物完全分解。
用水洗净坩埚及盖,然后将溶液冷却至室温,移入250毫升容量瓶中,加水稀释至标线,摇匀,供测定用。
3.2 氧化钙:原理:在pH大于13的强碱性溶液中,以氟化钾(2%)掩蔽硅酸,三乙醇胺掩蔽铁、铝,以CMP(钙黄绿素—甲基百里香酚蓝—酚酞混合指示剂)为指示剂,用EDTA二钠标准溶液直接滴定钙。
钙离子与钙黄绿素生成的络合物为绿色荧光,钙黄绿素指示剂本身为桔红色,因此滴定至终点时溶液绿色荧光消失,而呈现桔红色。
试剂 :盐酸(1+1)、2%氟化钾溶液(20g/L)、三乙醇胺(1+2)、 CMP混合指示剂、氢氧化钾溶液(200g/L)、 0.015M EDTA二钠标准溶液仪器:锥形瓶、酸式滴定管、移液管、烧杯、磁力搅拌器步骤:试样的溶解:称取0.5g石灰石试样,用25ml(1:1)的盐酸分解后,移至250ml容量瓶中。
准确吸取试样溶液25毫升,放入400毫升烧杯中,加5毫升盐酸及5毫升氟化钾溶液(20g/l),搅拌并放置2分钟以上,然后用水稀释至约200毫升。
加5毫升三乙醇胺(1+2)及适量的CMP混合指示剂,以200g/L氢氧化钾溶液调节溶液出现绿色荧光后再过量7—8毫升(此时溶液pH大于13),用0.015M EDTA二钠标准溶液滴定至溶液绿色荧光消失呈现红色。
计算:氧化钙质量百分含量(X)按公式(15)计算:T CaO×V×10X Cao=─────────── ×100 (15)G×1000式中:X Cao—氧化钙的质量百分数,%;T CaO─每毫升EDTA二钠标准溶液相当于氧化钙的毫克数;T CaO=C EDTA×56.08=0.015×56.08=0.8412mg/mLC EDTA——EDTA的浓度,0.015moL/L56.08——CaO的摩尔质量,g/molV──滴定时消耗EDTA二钠标准溶液的体积,毫升;G──试样重量,克;10──试样溶液的总体积与所分取试样溶液的体积之比。
3.3 氧化镁的测定原理:在pH10的溶液中,以三乙醇胺、酒石酸钾钠掩蔽铁、铝,以酸性铬蓝K-萘酚绿B为指示剂,用EDTA二钠标准溶液滴定钙镁合量。
减去按3.2测得的钙量后,求得氧化镁含量。
试剂:氟化钾溶液(20g/L)、三乙醇胺(1+2)、氨水(1+1)、 10%酒石酸钾钠溶液、氨水-氯化铵缓冲溶液(pH10.5) 、0.015M EDTA二钠标准溶液精密试纸:pH9.5—13.0。
酸性铬蓝K-萘酚绿B(1+2.5)混合指示剂仪器:锥形瓶、酸式滴定管、移液管、烧杯、磁力搅拌器、量筒步骤:准确吸取25毫升试样溶液放入400毫升烧杯中,加5毫升20g/L氟化钾溶液,然后用水稀释至约200毫升。
加入1毫升10%酒石酸钾钠溶液,5毫升三乙醇胺(1+2),以氨水(1+1)调节溶液pH至约10(用精密试纸检验),加入25毫升氨水-氯化铵缓冲溶液(pH10)及适量的酸性铬蓝K-萘酚绿B混合指示剂,以0.015M EDTA二钠标准溶液滴定,近终点时应缓慢滴定至纯蓝色。
计算:氧化镁的质量百分含量(X)按公式(16)计算:T MgO×(V2-V1)×10X MgO=────────────×100 (16)G×1000式中:X MgO—氧化镁的质量百分数,%T MgO──每毫升0.015M EDTA二钠标准溶液相当于氧化镁的毫克数;T MgO =C EDTA×40.3044=0.015×40.3044=0.6046mg/mLC EDTA——EDTA的浓度,0.015moL/L40.3044——MgO的摩尔质量,g/molV1──滴定钙时消耗EDTA二钠标准溶液的体积,毫升;V2──滴定钙、镁合量消耗EDTA二钠标准溶液的体积,毫升;G──试样重量,克;10──试样溶液的总体积与所分取试样溶液的体积之比。
3.4 石灰石中酸不溶物的测定同石膏中酸不溶物的测定3.5 烧失量的测定原理:试样中所含碳酸盐、有机物,及其他易挥发性物质,经高温灼烧即分解逸出,灼烧所损失的重量即为烧失量。
仪器:天平、瓷坩埚、马弗炉、干燥器、坩埚钳、步骤:称取约1克试样,精确至约0.0001克,置于已灼烧恒重的瓷坩埚中,将盖斜置于坩埚上,放在马弗炉内从低温开始逐渐升高温度,在950—1000℃下灼烧1小时,取出坩埚,置于干燥器中冷至室温,称量。
如此反复灼烧直至恒重。
计算:烧失量的质量百分含量(X)按公式(17)计算:G-G1X=─────×100 (17)G式中:G──灼烧前试样质量,克;G1──灼烧后试样质量,克。
3.6 二氧化硅的测定方法提要试样于铂坩埚中以碳酸钾-硼砂混合熔剂熔融,熔融物以硝酸加热浸取。
试剂碳酸钾-硼砂(1+1)混合熔剂、.硝酸(1+6)制备步骤1、称取约0.5 克试样置于铂坩埚中,加2 克碳酸钾-硼砂混合熔剂,混匀,再以少许熔剂擦洗玻璃棒,并铺于试样表面。
盖上坩埚盖,从低温开始逐渐升高温度至气泡停止发生后,在950~1000℃下继续熔融3~5分钟。
然后用坩埚钳夹持坩埚旋转,使熔融物均匀地附着于坩埚内壁。
冷却至室温后将坩埚及盖一并放入已加热至微沸的盛有100 毫升硝酸的300 毫升烧杯中,并继续保持微沸状态,直至熔融物完全分解。
用水洗净坩埚及盖,然后将溶液冷却至室温,移入250 毫升容量瓶中,加水稀释至标线,摇匀,供测定用。
2、硅钼蓝比色法[注]注:二氧化硅含量小于7%时可采用比色法。
2.1方法提要在微酸性(0.035~0.40N)溶液中单硅酸和钼酸铵生成硅钼酸络离子(钼黄),然后以抗坏血酸使钼黄还原为硅钼蓝。
用分光光度计于660纳米处测定吸光度。
2.2 试剂与仪器.无水碳酸钠、.盐酸(1+11)、盐酸(1+1) 、95%乙醇、5%钼酸铵溶液、0.5%抗坏血酸溶液、.二氧化硅标准溶液:(准确称取0.1000克二氧化硅(光谱纯,已于950℃灼烧30分钟) 置于铂坩埚中,加入1克碳酸钠搅拌均匀后,于高温下熔融3~5分钟。
冷却后用热水将熔块浸出于盛有约300 毫升热水的烧杯中,待全部溶解后,移入1 升容量瓶中,冷至室温,加水稀释至标线,摇匀,移入塑料瓶中保存。
此标准溶液每毫升含有0.1 毫克二氧化硅。
)分光光度计:721型或类似性能的仪器。
2.3 工作曲线的绘制准确量取0.00,1.00,2.00,3.00,4.00毫升二氧化硅标准溶液(分别相当于0.00,0.10,0.20,0.30,0.40毫克二氧化硅),分别放入100毫升容量瓶中,用水稀释至约40毫升。
加入5毫升盐酸(1+11),8毫升95%乙醇,6毫升5%钼酸铵溶液,按下述不同温度,放置不同的时间:温度(℃) 放置时间(分)10 ~20 3020 ~30 10 ~2030 ~35 5 ~20沸水浴振摇30秒钟立即以自来水冷却然后加20毫升盐酸(1+1),5毫升0.5%抗坏血酸溶液,用水衡释至标线,摇匀。
放置1小时后,用分光光度计以水作参比,使用10毫米比色皿,在波长660纳米处测定溶液的吸光度。
同时按上述操作进行空白试验。
然后,以测得的吸光度为纵坐标,比色溶液的浓度为横坐标,绘制工作曲线。
2.4 分析步骤准确吸取一定体积试样溶液(视二氧化硅含量而定),放入100 毫升容量瓶中,用水稀释至约40毫升,加入2~3毫升盐酸(1+11)。
以下操作同3.2.1.3。
2.5 结果计算二氧化硅的百分含量(X1)按公式(18)计算:C·nX1=────×100 (18)G×1000式中:C──在工作曲线上查得每100毫升被测定溶液中二氧化硅的含量,毫克;G──试样重量,克;n──试样溶液的总体积与所分取试样溶液的体积之比。
3.7 三氧化二铁的测定原理:EDTA络合滴定法:以磺基水杨酸钠为指示剂,在溶液酸度为pH1.5—2.0,温度为60—70℃时以EDTA滴定。
磺基水杨酸与Fe3+络合生成紫红色络合物后能为EDTA所取代,终点时溶液由紫红色变为亮黄色,如三氧化二铁含量低,则紫红色很浅,终点几乎为无色。
以HIn-代表磺基水杨酸根离子,以H2Y2-代表EDTA离子,络合滴定Fe3+的反应如下:指示剂反应:Fe3++ HIn- = FeIn++ H+(无色) (紫红色)滴定反应:Fe3++ H2Y2-= FeY-+ 2H+终点时指示剂变色反应:H2Y2-+FeIn+ = FeY- + HIn-+ H+(紫红色) (黄色) (无色)试剂:a. 氨水(1+1):将氨水与等体积水混合。