制程检验作业流程图
制程检验作业规范
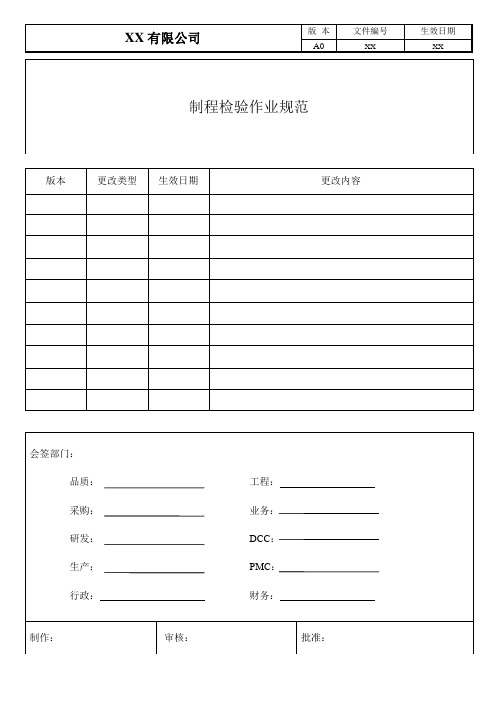
版本
更改类型
生效日期
更改内容
会签部门:
品质:工程:
采购:业务:
研发: DCC:
生产 :PMC:
行政:财务:
制作:
审核:
批准:
1.目的
规范制程检验作业方法,确保产品品质满足客户要求。
2.适用范围
制程检验作业流程。
3.定义
首件:指生产线量产前由生产制作样品的检查。
随机抽样:抽取的样品反映每一个生产时段产品品质。
6.4.3但制程巡检不良率超过3%,IPQC应填写“品质异常矫正单”、连同不良品给个责任部门进行原因分析,责任部门应制定纠正与预防措施,IPQC须加以追踪及效果确认。
6.4.4如产品缺陷无法判断,则应及时呈报班长。
6.4.5不合格品的处理具体依据“不合格品处理程序”作业,纠正与预防措依据“纠正与预防措施控制程序”作业。
品质检验:通过对产品质量进行观察和判断,适当时结合测量、试验进行的符合性评价。
巡检:按一定的时间间隔1H/1次,定期巡回检查:指定专人作在线管制项目定期检查。
抽样:是从要检验的一批产品中,随机抽取一部分产品检验,根据样品的质量,对产品批做出是否合格的判断。
4.作业方法
4.1岗位职责规定如下:
4.1.1工程师或其代理人负责首件确认,不良缺陷确认和判定,预防措施发出及跟进主管指定的其它工作。
8.作业流程图
4.2.4首件检查确认资料: 1) 制造通知单 2) 产品承认书
4.3定期巡回检查:由IPQC巡检人员依规定之点检频率进行抽样检查,巡回检查内容: 依产品管制计划内容检查.
1) 作业指导书是否正确?
2) 作业者是否依作业指导书作业?
3) 机械设备、治工具是否正确使用?
检验与试验管理程序(含流程图)
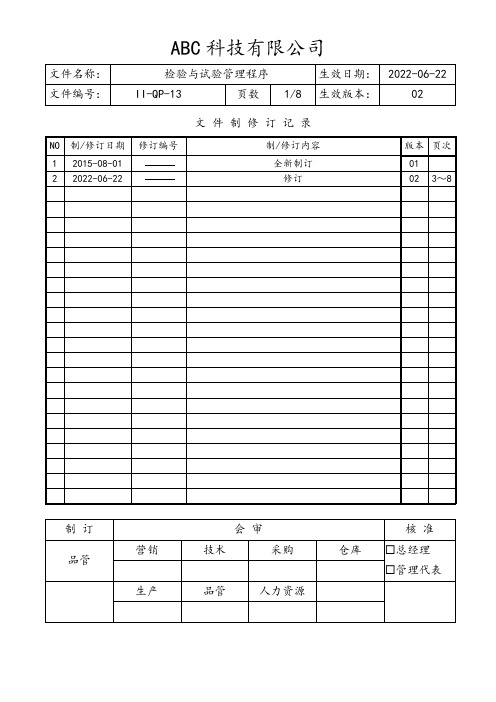
ABC科技有限公司
文件制修订记录
文件编号II-QP-13 页数2/8 生效版本02
1.目的:
规范检验流程及标准,使公司的生产、服务提供过程品质得到有效的控制,从而不流入不良品、不制造不良品,不流出不良品。
2.范围:
适用于本公司进料(包括客供料)、制程、成品检验工作和可靠性试验作业。
3.参考文件:
3.1产品防护与出货管理程序
3.2不合格品控制程序
3.3采购与供应商管理程序
4.定义:
4.1可靠性试验:对实现产品功能的保障能力的测试。
4.2首件:每个新订单生产前或生产过程中生产条件发生变化后(5M1E等)所生产的第一或前几件产品。
4.3首检:对首件产品进行检查及确认的过程。
5.责任:
5.1品管:负责来料、制程及成品的检验及标识、试验仪器操作及可靠性实验执行。
5.2生产:负责生产成品的送检,制程不合格情况的改善,将生产成品入库。
5.3仓库&采购:负责来料的送检,不合格品的处理,出货成品的送检;检测单位选定及管理。
5.4工程部:负责检验标准技术文档的提供。
6抽样方案:
文件编号II-QP-13 页数3/8 生效版本02
6.1特殊部件进行全检(例如摄像头等),电子料和线材按0.4抽样,壳料和包材按1.5抽样(若质量问题多则加严抽样)
7.相关记录:
7.1进料检验报告
7.2进料品质异常单
7.3制程巡检报表
7.4首件检验记录
7.5成品检验报告
7.6可靠性实验报告。
IQC--IPQC--FQC--OQC检验控制流程图
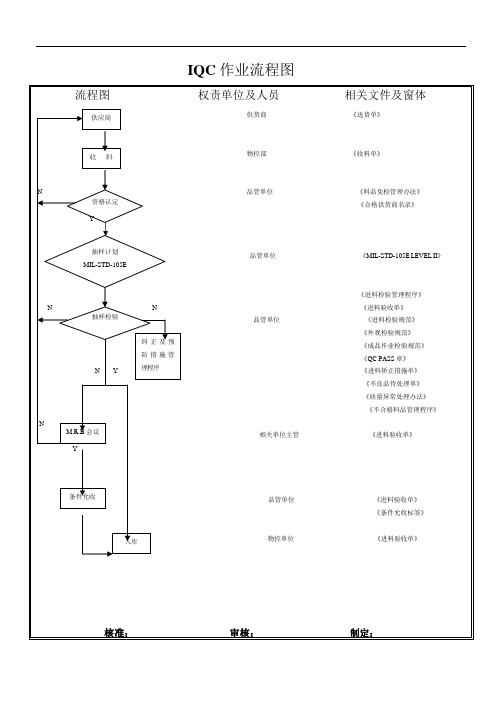
纠 正 及 预防 措 施 管
理程序
IQC 作业流程图
流程图
权责单位及人员
相关文件及窗体
供货商
《送货单》
物控部
《收料单》
N
品管单位
《料品免检管理办法》 资格认定
Y
《合格供货商名录》
抽样计划 MIL-STD-105E
品管单位 《MIL-STD-105E LEVEL II 》
《进料检验管理程序》
N
N
《进料验收单》 抽样检验
品管单位
《进料检验规范》 《外观检验规范》 《成品作业检验规范》 《QC PASS 章》 N
Y
《进料矫正措施单》 《不良品待处理单》 《质量异常处理办法》 《不合格料品管理程序》
N
相关单位主管
《进料验收单》
Y
品管单位
《进料验收单》 《条件允收标签》
物控单位 《进料验收单》
核准: 审核: 制定:
供应商
收
料
入库
M.R.B 会议 条件允收
核准:审核:制定:。
IPQC制程检验流程(流程版)

生产部
品检组
业务
首五件产品量测记录表
异常联络单
IPQC巡回检验记录
作业流程
流程说明
权责
单位
产出
表单
6.5主管不定时地巡回检查,发现问题,要让检验人员清楚问题所在,查找原因,提出改善对策,同时要求IPQC记录于《IPQC巡回检验记录》,并指定跟催确认人回馈最终改善结果,必要时再到现场亲自查实。
5.5 确认成品首件时必须对打好钉的成品进行轮子检验:
5.5.1检验轮子三只脚/外八字:把装好轮子的成品放在一玻璃平面上,转动箱体(需正方向和反方向),观察四个轮子是否完全接触玻璃板,如有轮子未完全接触玻璃板(轮子与玻璃板有空隙或四脚未落地),则视为三只脚. 用手分别转动每个轮子,观察轮子转动是否顺畅,不卡顿,再把箱子放在玻璃板上,观察前后轮子是否在一直线上,观察方法:前左轮对后左轮,前右轮对后右轮,前左轮对前右轮,后左轮对后右轮,如有任意一个轮子不在一直线上,则视为八字脚。
3. 检验标准:
3.1顾客订单资料
3.2业务员(含)以上干部签名确认的样包或顾客提供的样包、原物料确认卡、订单通知与反馈单、顾客原始订单、工艺单,资料单。
3.3《QC工程表》。
4.标准核对步骤:
4.1IPQC根据业务所提供的工艺单逐步核对两者的物料名称、规格、颜色、配色是否正确,如两者无误时,以工艺单做为标准核对大货及样包。
一 范围:
产品试做、过程品质控制,成品首件检验、关注新产品上线成品品质,跟催确认品质改善。
二 参考文件:
2.1 QC工程总表PB-G-001
三术语和定义:
3.1检验标准:业务员(含)以上干部签名确认的样包或顾客提供的样包、原物料确认卡、订单通知与反馈单、顾客原始订单、工艺单,资料单。
OQC作业流程图
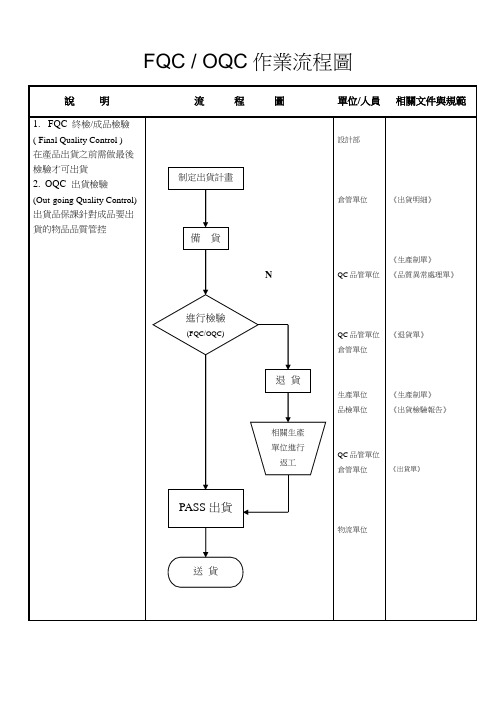
FQC / OQC作業流程圖製程巡檢作業辦法目的:落實品質意識在現場作業人員于制程過程中,實施檢驗或試驗以查證制程之合格性。
三〃範圍:凡本公司產品之各制程。
四、職責:生產部門:負責自製品自檢、送檢、重工、維修及入庫。
品保部門:負責自製品檢驗及記錄、標示。
五、內容:1、首件(產前樣/批版)、自主、巡迴檢驗:(1)品保部門IPQC人員在以下時段需做首件檢驗。
(1)每台機開始生產前開機需做首件檢驗。
(2)設計規格變更時需做首件檢驗。
(3)人員或材料更換時需做首件檢驗。
(2)生產部門作業人員應隨時注意生產產品品質狀況,並按照規定做好自主檢驗。
(3)品保部門IPQC人員應到現場做巡迴檢驗並做好記錄。
(4)品保部門檢驗管制程式,應按照規範和作業指導書之要求訂制(QC工程圖)。
(5)生產部門相關人員在制程中,發現不合格又無法矯正時,應及時停機報告主管,並通知品保部門,而品保部門應按照相關程式處理。
(6)品保部門IPQC人員按照實際檢驗情況記錄不合格品,並對制程式不良品作統計分析把結果回饋於相關部門,作糾正預防對策之依據。
(7)不合格品處理與標示(紅豆標&件投標):(1)、經判定為不合格品時,應在該批半成品貼上紅色圓點貼紙(故障貼紙)又稱紅豆,並加以區分,隨後將不合格批移至返工區或報廢區進行處理。
(2)、發生不合格品時,品保部門IPQC人員應填寫《IPQC服裝(巡廠)驗貨報告》加以記錄,並按照相關程序處理,並通知相關部門處理。
六〃使用表單:1、首件(制前樣/批版)吊卡2、特采申請單3、IPQC服裝(巡廠)驗貨報告4、返工\返修單5、報廢單6、制程異常備忘錄不合格品處理作業辦法一、目的:按照品質計畫及管制措施找出不合格品,採取各項管理及處理措施,並對不合格品進行分析,以防誤用。
二、範圍:供方之原材料、主輔料;廠內制程中之半成品、成品和庫存品;顧客之退貨品。
三、職責:生產、資材部門:負責不合格品標示、隔離及處理,必要時參與評審。
21制程检验管制程序
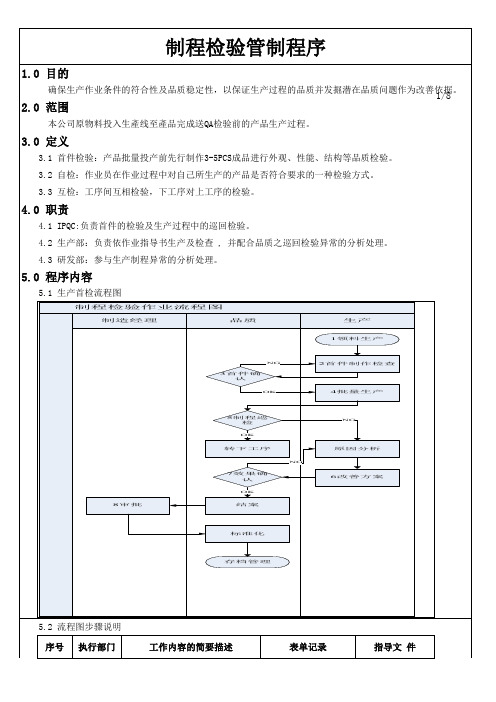
辅料的备料,并做好物料的标识和保管。
5.3.1.4 生产部主管依据工艺流程图和操作指导书等资料,就生产过程中的操作问题向各生产拉长
或作业员讲解说明和指导,以保证每个工序的作业人员清楚了解本岗位(工序)的作业要求。
5.3.1.5 生产拉长和IPQC第一时间对仓库配发物料进行检查核对,不合格则退回仓库,并标明不良
善方案
IPQC对改善方案予以效果确认,
07
品质
如改善方案无效时继续分析改 《纠正预防措施处理
善,OK后前期IPQC加严检验,稳
单》
定后转入正常检验,并予以结案
8
品质
将结案的《纠正预防措施处理单 》交制造经理审批后升成标准化
指导
《纠正预防措施处理 单》
5.3 制程检验内容说明
5.3.1 生产前召开产前会议并准备产前工作,如:(现场人员、物料、设备检查)。
做好的首件成品由拉长进行初步自检判定(检验项目: 外观、性能、结构),初步判
定OK后送给IPQC进行首检确认。
5.3.2.2.2 IPQC在接到生产送来的首件产品,必须在2小时内依成品检验标准进行首件检验 ,并
将结果记录在《首件检查记录表》上。
5.3.2.2.3 IPQC首件检验合格,经主管签名确认后知会生产。生产根据首件确认的结果,进行批
《首件检查记录表》
产线在生产过程中IPQC执行制程
05
品质 巡检,巡检正常填写检验记录转 《制程巡回检查表》
下工序生产
IPQC执行制程巡检NG时,IPQC填
写《纠正预防措施处理单》给主 《制程巡回检查表》/
06
生产 管审核后交产线PE并隔离标识NG 《纠正预防措施处理
产品,由生产PE进行分析拟定改
17.五金产品生产过程检验流程图2009.12.3

不合格品处理及纠正和预防措施实施
OK
入库
抽样检验记录
出货检验
OK
NG
不合格品处理及纠正和预防措施实施
出货
首件检验和制程检验
NG
不合格品处理及纠正和预防措施实施
OK
(后加工) 电镀/电泳漆/喷油/抹油试产
NG
首件确认
首件检验
OK
(后加工)电镀/电泳漆/ 喷油/抹油生产
首件确认、巡检报告、抽样检验记录
制程检验
NG
不合格品处理及纠正和预防措施实施
OK
包装
全检记录、巡检报告、抽样检验记录 、
全检/巡检/检验
NG
文件编号:EDI-WI-QA-17 生效日期:2009-12-03 文件版本:A.0 文件页数:共 2 页 第 1 页
生产过程检验流程图
支持性文件、记录
送货单、工段移转单
流程
材料接受
异常说明
检验标准、检验报告、抽样检验记 录
进料检验
NG
不合格品处理及纠正和预防措施实施
OK
作业指导书
调整机台、组织资源试产
a0材料接受送货单工段移转单进料检验ngok调整机台组织资源试产首件检验首件确认书初胚压铸生产制程检验ngok作业指导书ok首件检验和制程检验ng检验标准检验报告抽样检验记不合格品处理及纠正和预防措施实施okngokng巡检报告抽样检验记录不合格品处理及纠正和预防措施实施不合格品处理及纠正和预防措施实施前处理攻牙首件确认巡检报告抽样检验记录首件检验和制程检验不合格品处理及纠正和预防措施实施首件确认巡检报告抽样检验记录文件版本
NG
不合格品处理及纠正和预防措施实施
编制:
审核/日期:
品质检验作业流程图
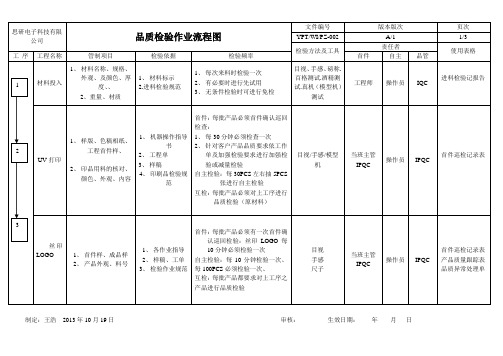
首件:每批产品必须有一次首件确认巡回检验:丝印LOGO每10分钟必须检验一次
自主检验:每10分钟检验一次、每100PCS必须检验一次、
互检:每批产品都要求对上工序之产品进行品质检验
目视
手感
尺子
当班主管
IPQC
操作员
IPQC
首件巡检记录表
产品质量跟踪表
品质异常处理单
制定:王浩2013年10月19日审核:生效日期:年月日
2、磨光胶、UV胶、白乳胶
3、糊边位置、产品料号、外观
1、作业指导书
2、粘盒检验规范
首检:每批产品必须有首件确认
巡回检验:每30分钟检验一次
自主检验:每200个抽检一次
互检:每批产品都要对上工序品质进行互检
目视
手感
直尺
制程主管
IPQC
操作者
IPQC
首件巡检记录表
产品质量跟踪表
不合格处理报告
品质异常处理单
思研电子科技有限公司
品质检验作业流程图
文件编号
版本版次
页次
YPT/WI/PZ-002
A/1
1/3
检验方法及工具
责任者
使用表格
工序
工程名称
管制项目
检验依据
检验频率
首件
自主
品管
材料投入
1、材料名称、规格、外观、及颜色、厚度、、
2、重量、材质
1、材料标示
2.进料检验规范
1、每次来料时检验一次
2、有必要时进行先试用
3、规格
4、外观
1、坑机作业指导书
2、纸板检验规范
首检:每批产品必须有首件确认
巡回检验:每30分钟检验一次
01检验流程图
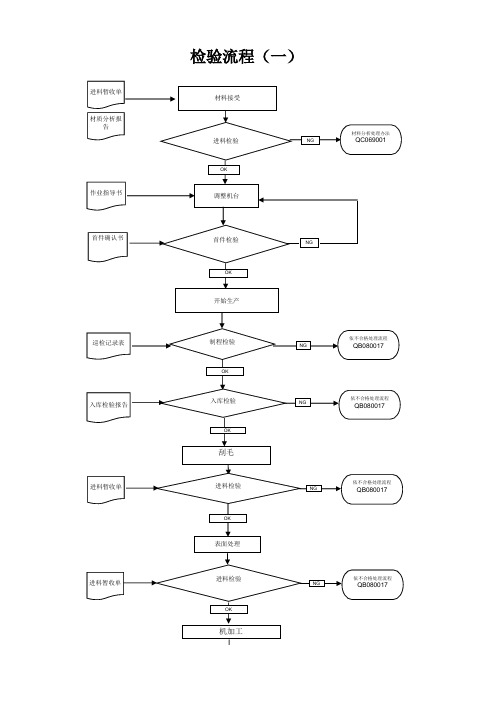
QB080017
OK
Surface 表面处理 Treatment
进料暂收单
进料检验
依不合格处理流程 NG
QB080017
OK
机加工
首件确认书
巡检记录表
首件检验 制程巡检
依不合格处理流程
NG
QB080017
OK
入库检验
入库检验报告
NG
依不合格处理流程
QB080017
OK
精加工
首件确认书
首件检验 制处理流程 NG
QB080017
入库检验报告
入库检验
NG
依不合格处理流程
QB080017
OK
烤漆
进料暂收单
进料检验
依不合格处理流程 NG
QB080017
OK
入库检验报 告
入库检验
依不合格处理流程 NG
QB080017
OK
包装
OQC出货检 验报告
出货检验
依不合格处理流程 NG
QB080017
检验流程(一)
进料暂收单
材料接受
材质分析报 告 进料检验
NG
材料分析处理办法
QC069001
OK
作业指导书
调整机台
首件确认书
首件检验
NG
OK
开始生产
巡检记录表
制程检验
依不合格处理流程 NG
QB080017
OK
入库检验报告
入库检验
NG
依不合格处理流程
QB080017
OK
刮毛
进料暂收单
进料检验
依不合格处理流程 NG
OK
仓库出货
FQC检验作业流程图
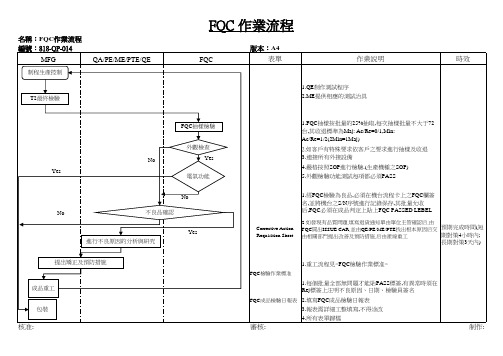
預期完成時間(短
由相關部門提出改善及預防措施,后由產線重工.
期對策4小時內;
長期對策3天內)
1.重工流程見<FQC檢驗作業標准>
FQC檢驗作業標准
1.每個批量全部無問題才能貼PASS標簽,有異常時須在 Rej標簽上注明不良原因、日期、檢驗員簽名
FQC成品檢驗日報表 2.填寫FQC成品檢驗日報表
3.報表需詳細工整填寫,不得涂改
提出矯正及預防措施
成品重工 包裝
核准:
1.FQC抽樣按批量的25%抽取,每次抽樣批量不大于72 台,其收退標準為Maj: Ac/Re=0/1,Min: Ac/Re=1/2(2Min=1Maj)
2.如客戶有特殊要求依客戶之要求進行抽樣及收退 3.連接所有外接設備 4.嚴格按照SOP進行檢驗.(生產機種之SOP) 5.外觀檢驗功能測試每項都必台流程卡上之FQC欄簽 名,並將機台之S/N序號進行記錄保存,其批量允收 后,FQC必須在成品判定上貼上FQC PASSED LEBEL
Corrective Action Requisition Sheet
2.如發現有品質問題,填寫退貨通知單由單位主管確認后,由 FQC開出ISSUE CAR,並由QE/PE/ME/PTE找出根本原因后交
FQC 作業流程
名稱:FQC作業流程 編號:818-QP-014
MFG
QA/PE/ME/PTE/QE
版本:A4
FQC
表單
作業說明
時效
制程生產控制
T2最終檢驗
1.QE制作測試程序 2.ME提供相應的測試治具
FQC抽樣檢驗
外觀檢查
No
Yes
Yes 電氣功能
No
No
不良品確認
检验和试验控制程序(含流程图)
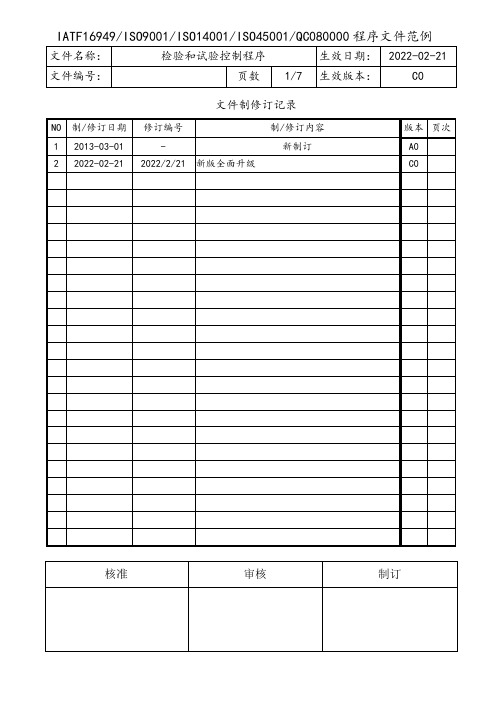
文件制修订记录1.0目的建立一个适合于对公司生产的所有产品(包括半成品与成品)及用于公司生产的所有原物料、辅料、零配件的检验与试验程序,规范公司的检验与试验作业,确保公司生产的产品质量/HSF达到客户所需的要求。
2.0范围:2.1适用于公司产品实现过程中所有物料包括原材料、半成品、成品的检验与试验。
2.2适用于公司制程管理值的验证作业。
3.0定义:3.1 IQC:Incoming Quality Control 指进料质量控制,即进料检验。
3.2 IPQC:In-process Quality Control 指生产过程中的质量控制,即制程检验,包含对产品以及生产过程中质量控制状态的检查与监视。
3.3 FQC:Final Quality Control制造过程最终检查验证,本公司指入库前的检验过程。
3.4 OQC:Outgoing Quality Control 指产品出货前由品质检验员对其进行的检验。
3.5 SQE:Supplier Quality Engineer 供应商质量工程师。
3.6 QE: Quality Engineer 质量工程师。
3.7自主检验:由操作员对本岗位材料、半成品、成品的检查,发现问题自己及时向直接上司汇报并作相应处理;同时也必须对过程质量(包括参数设定及是否按作业指导书要求作业等)的监控。
3.8首件检查:指生产者和技术员对生产调试阶段生产出来的产品(成品或半成品)进行确认并由品质检验员对其进行检验。
3.9巡检:指由品质检验员即IPQC人员对生产过程中的产品随机抽样检验或对制程过程状态(包括参数设置及是否按作业指导书要求作业等)的检查。
3.10抽检:指品质人员定期或定量对过程或项目进行抽样检查。
3.11半成品:指本公司还需要经下工序加工或装配后才能出货给客户的零组件。
3.12成品:指本公司可直接出货给客户的产品,对客户而言可能是半成品。
3.13原材料:指用于生产/加工成品的原料如塑胶粒、钢材等和组装产品用的零配件如螺丝、螺母、贴纸、辅料等,也包括包装产品用的包装材料如气泡袋、珍珠棉、PE袋、纸箱等。
OQC检验流程图

定期汇总和分析检验结果, 为产品质量改进提供依据
03 检验后处理
对不合格品进行标识和隔离
标识不合格品
对检验出的不合格品进行明确的标识,可以使用标签、印章或颜色 区分等方法,确保不合格品易于识别。
隔离不合格品
将标识好的不合格品与合格品进行物理隔离,防止在后续流程中混 淆或误用。
记录不合格品信息
详细记录不合格品的数量、批次、型号等信息,为后续处理提供依 据。
熟悉不良品的处理流程 和记录要求。
02 检验过程实施
接收待检产品
01 确认待检产品的数量、型号、规格等信息与送检 单一致
02 对待检产品进行初步的外观检查,确保无明显损 坏或缺陷
03 将待检产品放置在指定的检验区域,并做好标识 和记录
按流程进行检验
01
根据产品的检验标准和流程,对待检产品进行相应的
OQC检验流程图
汇报人:XX
2024-01-27
• 检验前准备 • 检验过程实施 • 检验后处理 • 流程图详解 • OQC检验流程与其他流程的关系 • 检验流程中常见问题及解决方案
01 检验前准备
了解检验要求
01
仔细阅读产品检验规范,了解检验项目、标准和方法。
02
确认检验批次、数量、包装等要求。
对不合格品进行跟踪处理
原因分析
组织相关部门对不合格品进行原 因分析,找出问题根源,制定改 进措施。
措施实施与验证
根据分析结果,实施相应的纠正 措施或预防措施,并对措施的有 效性进行验证。
跟踪记录
对不合格品的处理过程进行详细 跟踪记录,包括处理时间、处理 人员、处理结果等信息,确保问 题得到妥善解决。
检验工具不足问题及解决方案
IPQC检验作业流程管理规定

包装 组装
重工
QE IPQC QA
巡
检
NG
不 合 格 品 处 理
成品入库
苏州市冯氏钣金有限公司
SUZHOU FENGSHI SHEET METAL CO.,LTD
文件编号 版 页 次 次
FS/QC-05-07
A0 第4 页 共4 页
作 业 文 件
7.0 修改记录 版号/改次 页
标 题: IPQC 检验作业流程管理规定
拟制 拟制日期
审核 审核日期
核准 核准日期
苏州市冯氏钣金有限公司
SUZHOU FENGSHI SHEET METAL CO.,LTD
文件编号 版 页 次 次
FS/QC-05-07
A0 第2页 共4页
作 业 文 件
标 题: IPQC 检验作业流程管理规定
3.9 量产后,IPQC 将严格按照《制程检验和实验管理规定》的内容对产品做尺寸和外 观巡检(巡检时外观以客户要求为准,以签单样品为参考;尺寸以图纸或 SIP 和 SOP 的尺寸及公差作管控,以签单样品为参考)。 3.10IPQC 巡检时,需监督操作工对加工出来的产品做好标识与防护;同时监督首件样 品直到当批生产完之前必须保留于现场;还需注意操作工的作业方法是否妥当,若 影响产品的品质(如包装方式不当,产品摆放不当等),必须即时给予指正或汇报于 相应上司。 3.11 巡检完毕,须将检验结果记录在《制程检验记录表》上。 3.12 若巡检结果为“NG”,同时须在《编排产品生产及维修记录》或《编排产品包装 记录》上标注“NG”,并通知调校师傅重新调校并送检。IPQC 必须按照 S-1 AQL1.0 的抽样水准追溯已生产的产品是否合格。若不合格,则用“待处理标识牌”将已经 生产的产品作好标识和隔离,并开出《不合格品处理报告》交 QE 处理。 3.13 若该工序即将完成生产,IPQC 需根据操作工提供的样品做好末件确认。确认 OK, 须在当批产品的《产品标识牌》上盖上 QC 小章,以表示该批产品可转包装或委外 加工。若确认 NG,则按 3.12 执行。 3.14 若处理结果为可使用,IPQC 应即时将 “待处理标识牌” 取掉,以方便制造进行下工 序生产。 3.15 若处理结果为选别或重工,IPQC 须同操作工一起完成选别或重工,以确保选别/重 工后的品质。 3.16 若处理结果为报废,IPQC 须即时开出 《产品报废申请单》 于相关人员签字确认后, 将不良品丢于废料池内。 4.0 相关文件 4.1《制程检验和实验管理规定》 4.2《工序检验作业指导书》 5.0 相关记录 5.1《编排产品生产及维修记录》 5.2《制程检验记录表》 5.3《不合格品处理报告》 5.4《产品报废申请单》 5.5《编排产品包装记录》
制程检验控制程序2-013(非常详细-附有流程图)

5.1首件确认时机
新产品生产、产品间断性生产、换材料、换人、机器故障、更换机台.
5.2首件品生产
5.2.1生产部门在生产首件品时,至少提前半小时完成首件品的生产并认真对首件品进行自检,确认OK后,再填写《IPQC首件检查项目表》.最将《IPQC首件检查项目表》和首件确认品交IPQC进行品质确认,
1.0目的
对整个制程中产品质量进行有效控制,确保生产顺利进行和确保产品质量符合客户的要求。
2.0范围
适用于本公司制程品质检验作业.
3.0职责
3.1 IPQC:首件确认、制程巡检、品质判定、作业指导、异常分析及反馈与跟踪、检验结果记录.
3.2 FQC: 对产线完成品进行全检作业.
3.3 Q E:制定或修订产品检验标准、制程品质异常分析、异常跟踪及作业指导。
5.3.2因部分产品需做特性测试,试验时间较长而影响生产, IPQC需及时向部门领导反映,征得同意后方可通知生产部门量产,若试验结果NG,IPQC应及时要求生产部门停止生产并对已生产的产品标识隔离.
5.3.3确认项目:材料/加工工艺/ 尺寸/外观/特性/包装等方面进行品质确认,及时发现问题,避免在量产时造成批量性的不良.
5.7制程异常的追踪确认
针对在巡检中所发现的不良品或不良批次,IPQC除标识隔离外,还需对不良品的流向及处理方式进行追踪确认,对责任单位回复的《制程品质异常报告》进行确认,(如原因分析是否正确,改善对策制定是否合理等),若回复不符要求则退回责任单位重新分析,责任单位在改善过程中IPQC应进行全程跟踪验证.
5.10制程中发现原材料不良之处理方式
上线前若生产部门发现材料不良情形,生产部应及时反馈给制程IPQC确认,在生产过程中生产单位及时发现原材料不良问题,应及时通知现场IPQC确认,此时IPQC需对已做好的半制品或成品进行标识隔离,同时品保部需发出《制程品质异常报告》给生产单位,同时品质部需及时通知IQC对此款材料的库存进行品质再确认,经确认在库材料不良,需标识隔离,同时品质部需及时开出《制程品质异常报告》知会相关单位和通知供应商改善。
- 1、下载文档前请自行甄别文档内容的完整性,平台不提供额外的编辑、内容补充、找答案等附加服务。
- 2、"仅部分预览"的文档,不可在线预览部分如存在完整性等问题,可反馈申请退款(可完整预览的文档不适用该条件!)。
- 3、如文档侵犯您的权益,请联系客服反馈,我们会尽快为您处理(人工客服工作时间:9:00-18:30)。
制程检验作业流程
流程图
1.0目的
为保证产品在生产制程中得到有效检验作业,控制制程品质,降低制程返工、报废,提升产品合格率,提高不良出来的时效性,特制定本作业流程。
2.0 范围
适用于(备料车间、白身车间、油漆车间、包装车间)生产过程中的检验与控制及不良品处理。
3.0 职责
3.1 PMC部:计划课负责生产指令的下达,参与生产异常处理;仓务课负责完成
不良品的回仓分类保管、标识确认及不良品退料的督促工作。
3.2 各生产车间:负责制程产品材料确认,首件产品品质确认及生产过程中的自
检、互检工作。
反馈、参与生产异常处理;
3.3品管部:首件产品确认及生产过程中的巡检、完工后检验,反馈、主导或参
与品质异常处理工作,并对数据记录保存、统计、分析、改善,持续改善;
3.4 相关部门:主导或参与品质异常处理及异常分析工作。
4.0 作业程序
4.1 PMC部下发《生产日计划》给各生产车间主管,各生产车间主管根据《生产日
计划》,组织安排操作工做好生产前的准备工作;
4.2 各车间组长、技术员准备工装夹具、测量量具、签样等,按样品或
产品工程作业标准书等准备物料进行生产。
备料、白身、总装车间:工装夹具、测量量具、签样、作业指导书、图纸、模具等。
油漆车间:色板、签样、作业指导书、图纸等。
包装车间: 签样、作业指导书、图纸、产品包装示意图、模具等。
4.3组长、技术员对首件先自检,合格报制程检验员对首件进行检验,详细参考
《首件检验控制卡》。
4.4制程检验员全检或按规定频次(正常情况下每天不少于6次)及工艺图纸等要
求巡检各工序制程品质状况,巡检要有相关侧重点,填写巡检记录,若不符
图纸和工艺要求,则知会操作员异常状况;当生产操作工自检发现不良现象
时及时隔离和标识;当产生不良品超标时,发现人即时通知本组组长
到现场确认,组长到现场确认后,按《生产异常提报控制卡》进行操
作,必要时组长填写《品质异常报告和处理单》交责任单位处理(来
料引起的不良交品管部处理;制程引起的不良交本部车间主管处
理)。
现场品质组长监督执行情况和跟进结果。
4.5操作工确认品质没有异常的,通知制程检验员进行全检或抽检.制程检验员
按照图纸上要求及抽样标准进行全检或抽检,检验合格正常转入下一工序,并贴上合格标贴同时在交接单上签名承认.若不符规格要求,则要求生产操作者返工,暂停转序,即时通知本组组长到现场确认,组长到现场确认后,按《生产异常提报控制卡》进行操作,必要时组长填写《品质异常报告和处理单》交责任单位处理(来料引起的不良交品管部处理;制程引起的不良交本部车间主管处理)。
现场品质组长监督执行情况和跟进结果。
4.6相关人员收到异常提报的通知后10分钟内赶到现场处理,收到现场组长或
品管填写的《品质异常报告和处理单》后需在规定时间内完成(来料引起的不良交品管部处理;制程引起的不良交本部车间主管处理)。
现场品质组长和生产主管监督执行情况并结果跟进。
4.7品管部对相应检验记录表与《品质异常报告和处理单》作相应的归类保存,
作出周/月/年统计,并组织召开品质会议。
4.8 不良品处理:
各车间主管、组长根据品质检验标准判定不良现象是否属实,不能判定时可联络品管部协同判定,判定后进行标识并放置在指定的不良区域。
生产组长安排把不良品按上工序不良,来料不良,本制程不良进行分类,分类后填写《产品交接单或退料单》并由品管开具不合格品标识单;生产组长或物料员提交《产品交接单或退料单》给QC组长,QC组长根据《产品不良品交接单》填写的内容进行与实物验证(抽查),属实签名确认,不符退生产单位重新分类;来料不良引起的不良需IQC确认并由品管部主管审核后,再由IQC通知采购部联络供应商确认后做出最终处理(更换良品或索赔(供商要在收到信息或报告72小时给结果,超时未告知结果的本司默认供商已知或同意本司做出处理方案。
下工序不良退上工序处理;制程导致的不良品由生产经理主导处理。
4.9计划课负责完成不良品的回仓分类保管、标识确认及不良品退料的督促。
5.0异常处理规定
5.1处理流程
(1)由发现异常之单位(一般为制造单位或品管)提出《品质异常报告和处理单》,并先用口头、电话方式向发生单位与责任单位告知。
(2)由制造单位或品管部提出临时对策。
(3)由责任单位提出改善对策。
(4)由品管部负责对策效果追溯、评估。
(5)由品管部负责对品质异常进行统计、存档和其他管理。
5.2品质异常报告和处理单内容:
(1)产品(配件)名称、。
(2)加工单位。
(3)发生时间(日期)。
(4)不良问题点。
(5)不良率(不良数和生产数量)。
(6)责任单位。
(7)检验员。
(8)检验日期。
5.3品质异常处理时效
(1)责任单位应在接获异常反馈单后,于半小时内提出对策,并回馈至发现异常单位及品管部。
(2)确因原因复杂未能于上述期限内完成时,应事先向发现异常单位及品管部说明。
5.4异常原因分类及责任单位有下
(1)技术原因,由生产部、工程技术部研究对策。
(2)原材料原因,由品管部、采购部、生产部研究对策。
(3)上工序原因,由品管部、上工序制造单位研究对策。
(4)设备原因,由生产部研究对策。
(5)作业原因,由生产单位研究对策。
(6)其他原因,由相关责任单位研究对策。
5.5措施原则
5.5.1临时措施------以尽快恢复生产,在确保品质的情形下降低损失为原则。
5.5.2纠正和预防措施------以彻底纠正不良,具有巩固和预防再发生之功效为原则。
6.0 相关表单
6.1《品质标识单》
6.2《生产日计划》
6.3《品质异常报告与处理单》
6.4《QC不良品记录日报表>
6.5《制程交接单》或《退料单》
6.6工程作业标准书
6.7生产异常提报控制卡
6.8首检确认控制卡
6.9物料交接控制卡
6.10物料退还控制卡
7.0管理规定
7.1生产人员、制程检验员未按规定时间处理待检物料的,违规责任人需捐款5
元/次,
7.2制程检验员未对按照要求进行首检、巡检和终检的,违规责任人需捐款10
元/次,
7.3制程检验员发现品质异常后未通知上司处理的,违规责任人需捐款10元/
次,
7.4出现品质异常时品管部及生产部未召集改善会议的,违规责任人需捐款5元
/次,
7.5 会议讨论的执行责任人未按照会议决议完成工作又未提前申请的,违规责
任人需捐款10元/次,
7.6《供商不良品退料》其制约是执行时退料单位、品管部、采购部、PMC部相
互进行横向制约,稽核中心定期抽查;责任每违反一次(一项)乐捐10元。
7.7其它违规按相关的控制卡进行处罚。
7.8附件:《不良品处理流程》
不良品处理流程。