转炉炼钢培训讲义
炼钢工艺及基础理论培训课件

炼钢工艺及基础理论培训课件一、转炉炼钢的基础理论1、氧气炼钢转炉中物理化学反应的基本条件和特点(1)、首先,在氧气炼钢转炉中要用氧气将铁水中的C、Si、Mn、P等元素快速氧化到吹炼终点的要求,在吹氧的全部时间内,熔池中始终进行着强烈的元素氧化反应,显然,在吹氧时间内,炉中具有很强的氧化特性。
只是在吹氧结束后的为时很短的脱氧和合金化时间内,熔池中的反应才主要是还原反应。
(2)、氧气转炉炼钢是在适当的高温下进行的,在吹炼过程中,将入炉的1250~1350℃的铁水加热到1660~1730℃。
这是现代优质、高产、低耗、低成本炼钢方法的必要条件。
吹炼的过程温度和终点温度都应当适当,不应过低或过高,过程温度过低,熔池中传质和传热速度缓慢,造渣困难,因而不利于熔池金属中杂质的去除和废钢等固体料的熔化,相反,过程温度过高,又对炉衬寿命有害,不利于某些不适于过高温度下进行反应的杂质的去除,钢中有害气体的含量也将提高。
此外,过高或过低的终点温度,都有会降低钢坯的质量,降低钢坯的合格率,降低设备的寿命,事故也增高。
(3)、氧气转炉炼钢过程中,同时而连续地进行着多种多相物理化学反应,通常在转炉中同时存在着金属和炉渣两相液相,CO、CO2、O2和炉气等几种气相,炉衬、固体成渣材料、废钢、铁合金和固体非金属夹杂物等多相固相,因此,必须应用多相系的物理化学规律研究炼钢熔池中的反应。
2、氧化反应化学反应进行的结果受两个因素制约;一个是热力学,即在给定的外界条件下,反应最终能达到的状态——平衡态;另一个是动力学,即反应向平衡态趋近的速率。
动力学因素比热力学复杂的多。
但幸运的是,化学反应随温度的升高而急剧增加,在炼钢主高温下,许多反应都可以达到或接近平衡。
因此,有关高温冶金反应平衡的知识对炼钢工作者是很有用的,炼钢过程中,有些反应没有完全达到,而是主要原因是由于反应物传输到反应地带的传质速率不够快造成的。
炼钢过程所涉及的物理变化和化学反应是复杂的,其中最主要的是[C]、[Si]、[Mn]、[P]组分的氧化。
氧气转炉炼钢培训
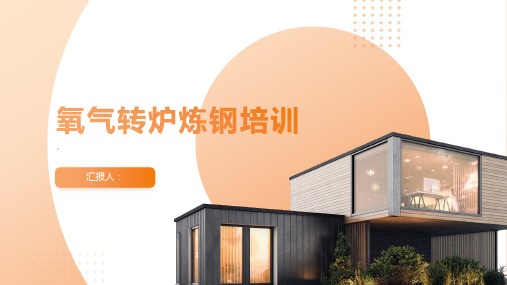
氧气转炉炼钢的原理:利用氧气与铁水中的碳、硅、锰等元素反应,去除杂质并提高钢的纯度。
氧气转炉炼钢的反应:在高温下,铁水中的碳与氧气发生氧化反应,生成二氧化碳气体,同时 释放出大量的热量。
氧气转炉炼钢的特点:通过控制氧气的流量和温度,实现对钢水成分和温度的精确控制,提高 钢的质量。
氧气转炉炼钢的应用:广泛应用于现代钢铁企业的生产中,是提高钢铁产品质量和降低能耗的 重要手段之一。
温度检测:使用热电 偶等温度检测设备, 监控钢水和炉渣的温 度,保证炼钢过程的 温度控制。
气体分析:通过分析 炼钢过程中产生的烟 气成分,推断炼钢过 程的反应程度和钢水 的纯净度。
质量问题:成分不均、夹杂物超标、表面质量差 解决方案:加强原材料控制、优化冶炼工艺、提高操作技能 检测方法:化学分析、金相检验、无损检测 质量控制:建立完善的质量管理体系、加强过程控制、提高员工素质
每日检查:对设备进行日常检查,确保设备正常运行 定期保养:按照规定进行定期保养,延长设备使用寿命 清洁工作:保持设备清洁,防止设备腐蚀和磨损 润滑工作:定期对设备进行润滑,减少设备磨损和摩擦
炉体漏水:检查密封圈和炉体连接处是否紧固,更换密封圈 炉内耐火材料脱落:检查耐火材料质量,定期更换 炉内结渣:调整吹氧量,控制炉温 炉底上涨:检查底渣排放是否畅通,调整底渣排放量
氧气转炉的结构:由炉体、炉帽、炉底和传动装置组成,炉体内有炉衬。
氧气转炉的工作原理:通过炉体的转动,使物料在高温下与氧气反应,实现炼钢过程。
氧气转炉的特点:具有高效率、低能耗、环保等优点,是目前应用最广泛的炼钢设备之 一。
氧气转炉的维护与保养:定期检查炉体、炉衬、传动装置等部位,及时更换损坏部件, 保持设备良好运行状态。
,
转炉炼钢培训材料2
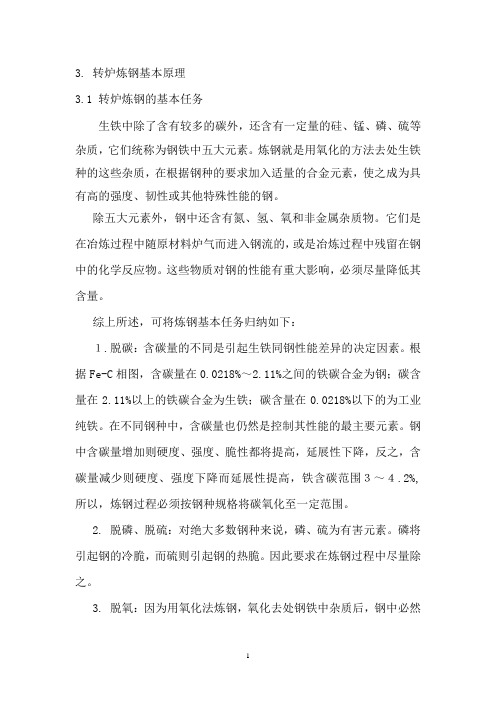
3. 转炉炼钢基本原理3.1 转炉炼钢的基本任务生铁中除了含有较多的碳外,还含有一定量的硅、锰、磷、硫等杂质,它们统称为钢铁中五大元素。
炼钢就是用氧化的方法去处生铁种的这些杂质,在根据钢种的要求加入适量的合金元素,使之成为具有高的强度、韧性或其他特殊性能的钢。
除五大元素外,钢中还含有氮、氢、氧和非金属杂质物。
它们是在冶炼过程中随原材料炉气而进入钢流的,或是冶炼过程中残留在钢中的化学反应物。
这些物质对钢的性能有重大影响,必须尽量降低其含量。
综上所述,可将炼钢基本任务归纳如下:1.脱碳:含碳量的不同是引起生铁同钢性能差异的决定因素。
根据Fe-C相图,含碳量在0.0218%~2.11%之间的铁碳合金为钢;碳含量在2.11%以上的铁碳合金为生铁;碳含量在0.0218%以下的为工业纯铁。
在不同钢种中,含碳量也仍然是控制其性能的最主要元素。
钢中含碳量增加则硬度、强度、脆性都将提高,延展性下降,反之,含碳量减少则硬度、强度下降而延展性提高,铁含碳范围3~4.2%,所以,炼钢过程必须按钢种规格将碳氧化至一定范围。
2. 脱磷、脱硫:对绝大多数钢种来说,磷、硫为有害元素。
磷将引起钢的冷脆,而硫则引起钢的热脆。
因此要求在炼钢过程中尽量除之。
3. 脱氧:因为用氧化法炼钢,氧化去处钢铁中杂质后,钢中必然残留大量氧,还会给钢的性能带来危害,应当除去。
用人为地方法减少钢中含氧量的操作叫做脱氧。
一般是向钢流中加入比铁有更大亲氧力的元素(如Al、Si、Ca等合金)来完成。
4. 去除气体和非金属夹杂物:钢中期体主要指溶解在钢中的氢和氮。
非金属夹杂物包括氧化物、硫化物、氮化物、磷化物以及它们所形成的复杂化合物。
在转炉炼钢方法中,主要靠碳氧反应时生成的CO气泡的溢出所引起的熔池沸腾来降低钢中的气体和非金属夹杂物。
5. 升温与合金化:上述所有冶金过程均须在一定高温下才能完成,同时为保证钢水能浇成合格钢锭,也要求出钢时钢水有一定的温度。
因此,将钢水加热并控制在一定的温度范围内,是炼钢必须完成的任务。
炼钢工艺培训讲义

⒉废钢: 不得夹带泥沙、钢渣、废耐火材料、不得有封闭容器、橡胶冰块油类及爆炸 物不得夹带铜锌铅等有色金属。废钢块度要适当,不能太大(<300kg)会损坏 炉衬,也不能太长(<1000mm)会延长加料时间。必须干燥清洁,有条件的可采取 废钢预热,减少热损失和增加安全性。
对于高硫铁水可以采用双渣操作,或者锰铁脱硫等。
四、转炉炼钢原材料:
⒈铁水:
①硅是重要的发热元素之一。铁水Si含量增加0.10%,废钢加入量可提高1.31.5%。但转炉炼钢中硅几乎完全氧化,使铁水吹损加大,同时也使氧气消耗增加; 石灰消耗增大使渣量增大,引起渣中铁损增加;渣中SiO2增多加剧对炉衬的侵蚀, 并可能造成喷溅。
所以炉渣高碱度、高(FeO)及低温有利于去P,前期应早化渣形成高氧
化性炉渣,后期渣作粘及控制好(FeO)。
4、脱硫反应:
1) 气化脱硫 〔S〕+2〔O〕=SO2
占10%左右,高碱度降低硫的活度不利于脱硫
2)炉渣脱硫 〔FeS〕+(CaO)= (CaS) +(FeO)
主要以炉渣脱硫为主,高温、高碱度、大渣量及低(FeO)有利于脱硫。
2、脱碳反应:
〔C〕 +〔O〕=CO 〔C〕+2〔O〕=CO2
(主要以此为主)
(〔C〕<0.05%时才显著反应〉
熔池温度达到1368℃碳才开始氧化;直到熔池温度升到1480℃才剧烈氧化
在温度一定的情况下 〔C〕〔O〕=常数
当C-O反应中供氧与供碳处于平衡时,熔池中碳含量即是Cβ。
《转炉炼钢基础知识》课件

本课程将介绍转炉炼钢的基础知识,包括炼钢简介、原料与配料、炉渣的重 要性、过程控制、安全问题、工艺的发展趋势和结语。
1. 转炉炼钢简介
了解转炉炼钢的热态、工艺流程和炉内反应,为后续内容的学习奠定基础。
2. 原料与配料
探讨炼钢中使用的不同原料及其特性,以及铁水预处理和配料计算的关键步骤。
3. 炉渣的重要性
分析炼钢过程中炉渣的作用、组成及特性,以及炉渣处理技术的重要性。
4. 吹炼过程中的过程控制
介绍转炉炼钢中温度控制、化学反应控制以及氧吹量与流量控制的关键技术。
5. 转炉操作过程中的安全问题
探讨转炉炼钢的安全管理、典型事故案例分析以及针对安全问题的措施建议。
6. 转炉炼钢工艺的发展趋势
剖析技术进步对炼钢工艺的影响,绿色环保生产要求以及炼钢的重要性,强调学习该技术的意义,并展望转炉炼钢的未来发 展前景。
转炉炼钢工艺课件(PPT 54页)

1)硅(Si)
硅是重要的发热元素,铁水中含Si量高,炉内的化学热增加,铁水中Si量增加
0.10%,废钢的加入量可提高1.3%-1.5%。 铁水含Si量高,渣量增加,有利于脱磷、脱硫。 硅含量过高会使渣料和消耗增加,易引起喷溅,金属收得率降低,同时渣中
是指终点温度和成分的控制。
脱氧及合金化
•脱氧:向钢液加入某些脱氧元素,脱除其中多余氧的操作。
•合金化:加入一种或几种合金元素,使其在钢中的含量达到钢种规格 要求的操作。
•区别:合金元素的价格通常较高,希望尽量少氧化;脱氧元素则比较便 宜,先加入,让其充分脱氧以免后加入的合金元素氧化。
•联系:二者都是向钢液加入铁合金,同时加入钢液的脱氧剂必然会有 部分溶于钢液而起合金化的作用,如使用Fe-Si、Fe-Mn脱氧的同时调整 钢液的硅锰含量;加入钢液的合金元素,因其与氧的亲和力大于铁也势 必有一部分被氧化而起脱氧作用。转炉的脱氧与合金化的操作常常是同 时进行的。
1951年碱性空气侧吹转炉炼钢法首先 在我国唐山钢厂试验成功,并于1952年 投入工业生产。1954年开始厂小型氧气 顶吹转炉炼钢的试验研究工作,1962年 将首钢试验厂空气侧吹转炉改建成3t氧气 顶吹转炉,开始了工业性试验。在试验取 得成功的基础上,我国第1个氧气顶吹转 炉炼钢车间(2x30t)在首钢建成,于 1964 年12月26日投入生产。
转炉冶炼中,高碳钢种时,使用含杂质很少的 石油焦作为增碳剂。
3 、氧化剂
氧气是转炉炼钢的主要氧化剂,其纯度达到或超过 99.5%,氧气压力要稳定,并脱除水分。
氧化铁亦称铁磷,是钢坯加热,轧制和连铸过程中 产生的氧化壳层,铁量约占70%-75%。氧化铁皮 还有助于化渣和冷却作用,使用时应加热烘烤,保 持干燥。
转炉炼钢培训

采用合理的脱氧制度,使脱氧产物易于聚集上浮,从钢 液中排除。
应用钢包冶金如真空脱氧﹑吹Ar搅拌﹑喷粉处理等和中 间包冶金如采用堰、坝﹑导流板﹑过滤器﹑湍流控制器 等控流装置,去除钢水中的夹杂物。
沉淀脱氧
又叫直接脱氧。把块状脱氧剂加入到钢液 中,脱氧元素在钢液内部与钢中氧直接反 应,生成的脱氧产物上浮进入渣中的脱氧 方法称为沉淀脱氧。
出钢时向钢包中加入硅铁﹑锰铁﹑铝铁或 铝块脱氧就是沉淀脱氧。
2006.10.13/16:0 2:51
扩散脱氧
又叫间接脱氧。它是将粉状的脱氧剂如C粉 ﹑Fe-Si粉﹑CaSi粉﹑Al粉加到炉渣中,降 低炉渣中的氧含量,使钢液中的氧向炉渣中扩 散,从而达到降低钢液中氧含量的一种脱氧方 法。
3.3.7 脱硫反应
反应热力学
炉渣分子理论认为,脱硫反应为: [S]+(CaO)=(CaS)+[O]
分子理论解释不了纯FeO渣也能脱硫的现 象,故炉渣离子理论认为,脱硫反应属于 电化学反应: [S]+(O2-)=(S2-)+[O]
2006.10.13/16:0 2:51
炉渣脱硫原理
2006.10.13/16:0 2:51
气体的溶解反应为:
½ {H2}=[H] ½ {N2}=[N]
2006.10.13/16:0 2:51
降低钢中气体的措施
提高炼钢原材料质量。如使用含气体量低的废钢 和铁合金;对含水分的原材料进行烘烤干燥,采 用高纯度的氧气等。
尽量降低出钢温度,减小气体在钢中的溶解度。 在冶炼过程,应充分利用脱碳反应产生的溶池沸
在电炉炼钢的还原期和炉外精炼过程向渣中加 入粉状脱氧剂进行脱氧操作就是扩散脱氧。
转炉炼钢培训讲义

转炉炼钢培训讲义转炉炼钢培训讲义1、炼钢的基本任务炼钢就是在给定的原料条件下,根据钢种成分要求,冶炼出成分合格、有适当温度的钢水。
⑴脱碳,通常铁水含C量较高,要通过氧化反应将碳降到所炼钢种的规定范围。
⑵提温,为保证出钢后钢水能顺利地浇注,应通过金属氧化放出的热量(化学热)将钢液加热到所需要的温度⑶去除P、S等有害物质,P会使钢质产生冷脆现象,S会使钢质产生热脆现象⑷去除气体及杂质,钢中(H、O、N)以及非金属夹杂物(氧化物、硫化物、氮化物等)都直接影响钢的表面质量和内在质量,在钢成材后又影响其力学性能和金相组织⑸脱氧与合金化,在炼钢过程中因为脱碳反应的需要,要向钢液供氧,就不可避免的使钢含有较多的氧,氧无论是以气体形态还是以氧化物形态存在于钢中都会降低钢的质量2、炼钢的五大制度⑴装入制度:定量装入(大吨位转炉);分阶段定量装入中小转炉)⑵供氧制度:恒压变枪位(经常使用);恒枪位变压⑶造渣制度:单渣操作;双渣操作(对P较高的铁水);留渣操作⑷温度制度:合适的过程温度和终点温度⑸脱氧合金化:沉淀脱氧(加到钢水中);扩散脱氧(加到熔渣中);真空脱氧3、为什么铁液中各元素的氧化是有次序的?铁液中元素与氧的化学亲和力是不同的。
凡对氧亲和力大的元素,它夺取氧的能力就越强,就先开始氧化。
元素与氧的亲和力可用该元素氧化物的分解压力来确定。
不同温度下元素氧化物的分解压是不同的。
﹥1400℃,铁水中元素的氧化顺序AI、SI、Mn、Cr、P、C、Fe ﹥1530℃,铁水中元素的氧化顺序AI、C、SI、Mn、Cr、P、Fe4、硅、锰、碳氧化的特点各是什么?⑴硅氧化的特点:第一特点:硅与氧的亲和力是很强的,特别是在低温下,硅氧化物的分解压力很小,因此,硅在任何炼钢法中都是在熔炼的最初期被氧化第二特点:在碱性炉里,硅氧化的产物很快进入炉渣,完全被碱性氧化物结合,再也无法还原出来,因此硅的氧化是十分完全、彻底的,最后残留在钢液中的硅很少[SI]+{O2}=(SIO2)[SI]+2[O]=(SIO2)[SI]+2(FeO)=(SIO2)+[Fe](SIO2)+2(FeO)=(2FeO﹒SIO2)(2FeO﹒SIO2)+2(CaO)=(2CaO﹒SIO2)+2(FeO)第三特点:该反应是一个强放热反应,⑵锰的氧化第一特点:[Mn]+1/2{O2}=(MnO)[Mn]+[O]=(MnO)[Mn]+(FeO)=(MnO)+[Fe]第二特点:氧化不象硅那样彻底第三特点:由于(MnO)属弱碱性氧化物,在碱性渣条件下,它与渣中酸性氧化物结合的能力比较小,因此渣中大部分的(MnO)呈自由状态。
《顶底复吹转炉培训》课件
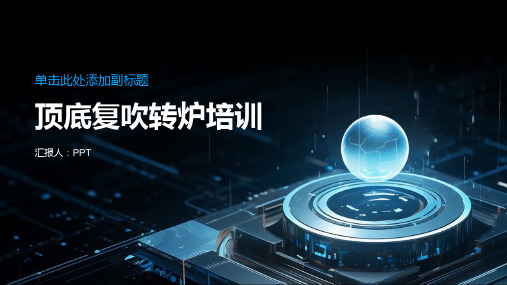
未来发展趋势与展望
顶底复吹转炉技术不断创新和完善 智能化、自动化水平不断提高 环保要求日益严格,绿色生产成为趋势 培训内容更加丰富和全面,提高员工素质
感谢观看
汇报人:PPT
维护记录:对每次检查和维修的情况进行记录,包括维修时间、维修内容、更换部件等 信息,方便后续管理和参考。
培训与指导:对操作人员进行培训和指导,提高其对顶底复吹转炉的维护保养意识和技 能水平,确保设备的正常运行和延长使用寿命。
故障排除与预防措施
常见故障及原因分析
故障排除方法与步骤
预防措施建议
维护保养注意事项
添加标题
添加标题
添加标题
添加标题
热量传递过程:炉顶和炉底的热 量通过辐射、对流和传导传递到 炉内熔池
热量传递影响因素:炉顶和炉底 的材质、结构以及操作参数等都 会影响热量传递效率
04
顶底复吹转炉操作规程
操作前准备
检查设备:确认转炉及其附属设备完好,无故障隐患 准备工具:准备好所需的工具和材料,如吹氧管、氮气等 确认安全:确认现场安全,无人员或其他障碍物影响操作 了解操作流程:熟悉顶底复吹转炉的操作流程和注意事项
添加项标题
顶底复吹转炉气体流动原理:炉内气体通过顶底复吹的方式进行 流动,实现金属的熔炼和氧化反应。
添加项标题
气体流动方向:炉内气体从炉顶进入,通过炉底排出,形成循环 流动。
添加项标题
气体成分:炉内气体主要由氧气、氮气、二氧化碳等组成,根据 不同的冶炼阶段,气体成分会有所变化。
添加项标题
气体流动速度:炉内气体流动速度与冶炼工艺、炉内温度等因素 有关,合理的控制气体流动速度可以提高冶炼效率。
转炉炼钢教材
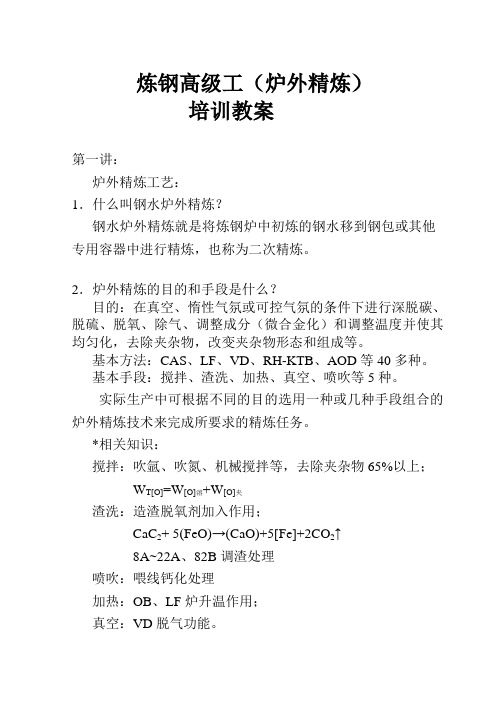
炼钢高级工(炉外精炼)培训教案第一讲:炉外精炼工艺:1.什么叫钢水炉外精炼?钢水炉外精炼就是将炼钢炉中初炼的钢水移到钢包或其他专用容器中进行精炼,也称为二次精炼。
2.炉外精炼的目的和手段是什么?目的:在真空、惰性气氛或可控气氛的条件下进行深脱碳、脱硫、脱氧、除气、调整成分(微合金化)和调整温度并使其均匀化,去除夹杂物,改变夹杂物形态和组成等。
基本方法:CAS、LF、VD、RH-KTB、AOD等40多种。
基本手段:搅拌、渣洗、加热、真空、喷吹等5种。
实际生产中可根据不同的目的选用一种或几种手段组合的炉外精炼技术来完成所要求的精炼任务。
*相关知识:搅拌:吹氩、吹氮、机械搅拌等,去除夹杂物65%以上;W T[O]=W[O]溶+W[O]夹渣洗:造渣脱氧剂加入作用;CaC2+ 5(FeO)→(CaO)+5[Fe]+2CO2↑8A~22A、82B调渣处理喷吹:喂线钙化处理加热:OB、LF炉升温作用;真空:VD脱气功能。
3、钢水精炼设备选择的依据是什么?钢水精炼设备的选择主要依据如下:(1)钢种的质量要求;(2)连铸机生产对钢水的质量要求;(3)转炉与连铸机生产的作业协调要求。
*相关知识:(1)、连铸对钢水质量要求:合适的钢水成份、温度;钢水可浇性;钢水洁净度。
(2)、洁净钢概念:[P]+[S]+[O]+[N]+[H]≤100ppm。
区别ppm与%、个4.钢包吹氩搅拌的作用是什么?钢包吹氩搅拌是最基本也是最普通的炉外处理工艺。
钢包吹氩搅拌的作用是:(1)均匀钢水温度。
包衬温度较低,中心区域温度较高,钢包上、下部钢水温度较低,中间温度较高。
(2)均匀钢水成分。
全程吹氩搅拌。
(3)促使夹杂物上浮。
渣中的(FeO)↓,吹氩搅拌夹杂物去除↑。
5.钢包吹氩搅拌通常有哪几种形式?1)底吹氩。
包括全程吹氩自动、手动控制;事故底吹氩;2)顶吹氩。
事故吹氩,搅拌效果不如底吹氩。
6.在什么情况下采用强搅拌,什么情况下采用弱搅拌?预吹氩、加废钢调温或调合金时采用强搅拌,以加速废钢、合金熔化,保证钢水成分、温度均匀。
转炉培训讲义
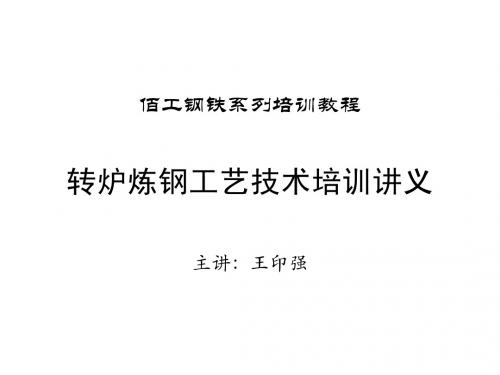
第二讲 转炉炼钢用原材料
三、冷却剂 1. 种类 废钢、铁块、铁皮、矿石、烧结矿、球团矿、渣钢等。 2. 冷却效应 物料 冷却效应 废钢 1 石灰 1 铁块 0.5-0.7 渣钢 1.2 铁皮、矿石、返矿 3
○废钢、铁块既是冷却剂,又是金属料。
四、氧化剂 ○氧气:要求纯度不小于99.5%,总管压力不低于12kg/cm2。 ○铁皮、圹石、返矿、球团矿等既是冷却剂,又是氧化剂。
○要有足够的渣量。(低硅铁水要进行配硅处理)
第三讲 转炉炼钢基本工艺制度
(三、造渣制度) 2. 造渣模式简介 (1) 单渣法 ○吹炼过程不进行倒渣操作。○是一种常规的操作方法。
第二讲 转炉炼钢用原材料
一、金属料 1. 铁水 (1) 铁水温度 ○炼钢用铁水的温度一般要求在1250℃以上。 (2) 铁水成分 ○Si:0.40-0.80%;Mn:0.20-0.40%;P≤0.150%;S≤0.070%。 ○铁水含硅量每增加0.10%,可增加废钢比1.3~1.5%。 ○转炉的脱磷率一般在85-90%。 ○转炉的脱硫率一般在40%左右。 2. 废钢 ○块度适中。 ○清洁干燥。 ○不得有封闭器皿和爆炸物。 ○不得混有有色金属和橡胶类杂物。
第一讲 转炉炼钢基础知识
(三、炼钢的基本原理) 4. 转炉炉渣 (2) 炉渣的组成 CaO、MgO、MnO、FeO、SiO2、P2O5、Al2O3等。 注:对炉渣性质有决定性影响的是CaO、 SiO2 和FeO 。 (3) 炉渣的作用 ○去除S、P等有害杂质。 ○在吹炼过程中间接传氧。 (4) 炉渣的性质 ○碱度:经典的观点 R=3 左右为宜,现在要求更低一些。 ○氧化还原性:取决于FeO,转炉为氧化渣,电炉为还原渣。 ○粘度和流动性:CaO、MgO高则粘度大,FeO高则流动性好。
转炉炼钢技术培训-文档资料

在氧气炼钢中,金属中一少部分碳可以受到直接氧化。
[C] + {O2} = {CO}
+136000J
该反应放出大量的热,是转炉炼钢的重要热源。在氧
射流的冲击区及电炉炼钢采用吹氧管插入钢液吹氧脱碳时,
氧气流股直接作用于钢液,均会发生此类反应。脱碳示意
图分别如图1示。
12
二、炼钢基本原理
流股中的气体氧与钢液中的碳原子直接接触,反应 生成气体产物一氧化碳,脱碳速度受供氧强度的直接影 响,供氧强度越大,脱碳速度越快。
(1)加速了熔池内各种物理化学反应的进行; (2)强化了传热过程;
11
二、炼钢基本原理
(3)CO气泡的上浮有利于钢中气体[H]、[N]和非金
属夹杂物的去除;
(4)促进了钢液和熔渣温度和成分的均匀,并大大加
速成渣过程;
(5)大量的CO气泡通过渣层,有利于形成泡沫渣。
4.5.1 氧气流股与金属液间的C—O反应
良好的物理化学反应条件。供氧制度的内容包括确定合 理的喷头结构、供氧强度、氧压和枪位。
供氧强度是指单位时间内每吨金属的供氧量,目前 多数转炉控制在2.5~4.0m3/(t·min),少数转炉控 制在4.0m3/(t·min)以上。供氧操作多采用恒压变枪 位操作。
20
二、炼钢基本原理
6.3 造渣制度 造渣制度就是确定合适造渣方法、渣料的加入数量和
17
二、炼钢基本原理
6.1装入制度 装入制度是指确定转炉合理的装入量和合适的铁水废钢
比。 装入量是指铁水和废钢的装入数量。它是决定转炉产量、
炉龄及其它技术经济指标的重要因素之一。若装入量过小 时,产量下降,同时因熔池过浅,容易使炉底受冲击损坏。 反之,会使熔池搅拌不好,成渣慢而且喷溅严重,延长冶 炼时间。
转炉炼钢操作工艺培训
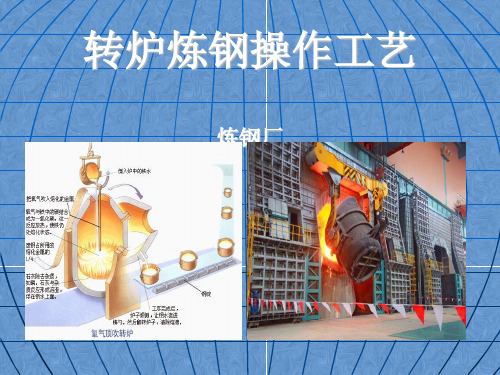
铁水入炉温度保持1280—1350℃,并保持相对稳定,有 利于迅速造渣,易于操作,C-O反应平稳,避免喷溅。
对铁水带渣量的要求:
高炉渣中含硫、SiO2、和Al2O3量较高,过多的高炉渣 进入转炉内会导致转炉钢渣量大,石灰消耗增加,造成喷 溅,降低炉衬寿命,因此,进入转炉的铁水要求带渣量不 得超过0.5%。 作业:高炉渣成分
1.2 废钢
氧气顶吹转炉用废钢量一般是总装入量的10—30%。废 钢的质量对炼钢的技术经济指标影响很大,而废钢的来源往 往很复杂,因此废钢的加工和管理工作非常重要。
废钢按来源分为厂内自产废钢和外购废钢。
对于主要从厂外购入的废钢铁有以下几方面要求:
少锈。 锈的主要成分是Fe(OH)2,在炉内分解后会增 加钢中的氢含量。
无泥砂和油污。 前者会增大渣量,后者会增加钢中的氢 含量。
不含各种有色金属。 有色金属中Cu、Sn会降低成品钢的 机械性能;Pb的熔点低而比重大,且不溶于钢中,能够损 坏炉底,甚至造成漏钢事故。
不含有爆炸物或封闭的容器。
硫和磷的含量低。
废钢的块度合适,应小于炉口直径的1/2。单重过大,熔 化慢,会出现终点不化,另外对炉衬的冲击大,影响炉衬 寿命;轻型废钢体积大,影响装入量,会造成点火困难。
[P]<0.020%的钢种时,一般需采用双渣脱磷工艺。
[S] 硫是钢中有害元素。氧气顶吹转炉中采用单渣法,脱硫效 果最高只可达到40%,采用双渣法或双渣留渣法可以达 到60%,但石灰消耗量大,生产率低。
对于铁水成分除关注Si、Mn、P、S元素外,其他元素的 异常也应重视。
[As]
As是一种非常容易偏析的元素,它会导致钢材的塑性变 差和钢板表面的微裂纹。这种情况会带来连铸或轧制过程 钢材的内部和表面质量问题,最终会危害产品的质量和性 能。 奥钢联从一个方坯连铸机工程项目发现在As+Sn=0.1% 时,方坯完全失去了塑性,导致了严重的裂纹甚至在矫直 过程中方坯出现了漏钢
- 1、下载文档前请自行甄别文档内容的完整性,平台不提供额外的编辑、内容补充、找答案等附加服务。
- 2、"仅部分预览"的文档,不可在线预览部分如存在完整性等问题,可反馈申请退款(可完整预览的文档不适用该条件!)。
- 3、如文档侵犯您的权益,请联系客服反馈,我们会尽快为您处理(人工客服工作时间:9:00-18:30)。
转炉炼钢培训讲义1、炼钢的基本任务炼钢就是在给定的原料条件下,根据钢种成分要求,冶炼出成分合格、有适当温度的钢水。
⑴脱碳,通常铁水含C量较高,要通过氧化反应将碳降到所炼钢种的规定范围。
⑵提温,为保证出钢后钢水能顺利地浇注,应通过金属氧化放出的热量(化学热)将钢液加热到所需要的温度⑶去除P、S等有害物质,P会使钢质产生冷脆现象,S会使钢质产生热脆现象⑷去除气体及杂质,钢中(H、O、N)以及非金属夹杂物(氧化物、硫化物、氮化物等)都直接影响钢的表面质量和内在质量,在钢成材后又影响其力学性能和金相组织⑸脱氧与合金化,在炼钢过程中因为脱碳反应的需要,要向钢液供氧,就不可避免的使钢含有较多的氧,氧无论是以气体形态还是以氧化物形态存在于钢中都会降低钢的质量2、炼钢的五大制度⑴装入制度:定量装入(大吨位转炉);分阶段定量装入中小转炉)⑵供氧制度:恒压变枪位(经常使用);恒枪位变压⑶造渣制度:单渣操作;双渣操作(对P较高的铁水);留渣操作⑷温度制度:合适的过程温度和终点温度⑸脱氧合金化:沉淀脱氧(加到钢水中);扩散脱氧(加到熔渣中);真空脱氧3、为什么铁液中各元素的氧化是有次序的?铁液中元素与氧的化学亲和力是不同的。
凡对氧亲和力大的元素,它夺取氧的能力就越强,就先开始氧化。
元素与氧的亲和力可用该元素氧化物的分解压力来确定。
不同温度下元素氧化物的分解压是不同的。
﹥1400℃,铁水中元素的氧化顺序AI、SI、Mn、Cr、P、C、Fe﹥1530℃,铁水中元素的氧化顺序AI、C、SI、Mn、Cr、P、Fe4、硅、锰、碳氧化的特点各是什么?⑴硅氧化的特点:第一特点:硅与氧的亲和力是很强的,特别是在低温下,硅氧化物的分解压力很小,因此,硅在任何炼钢法中都是在熔炼的最初期被氧化第二特点:在碱性炉里,硅氧化的产物很快进入炉渣,完全被碱性氧化物结合,再也无法还原出来,因此硅的氧化是十分完全、彻底的,最后残留在钢液中的硅很少[SI]+{O2}=(SIO2)[SI]+2[O]=(SIO2)[SI]+2(FeO)=(SIO2)+[Fe](SIO2)+2(FeO)=(2FeO﹒SIO2)(2FeO﹒SIO2)+2(CaO)=(2CaO﹒SIO2)+2(FeO)第三特点:该反应是一个强放热反应,⑵锰的氧化第一特点:[Mn]+1/2{O2}=(MnO)[Mn]+[O]=(MnO)[Mn]+(FeO)=(MnO)+[Fe]第二特点:氧化不象硅那样彻底第三特点:由于(MnO)属弱碱性氧化物,在碱性渣条件下,它与渣中酸性氧化物结合的能力比较小,因此渣中大部分的(MnO)呈自由状态。
在强脱碳期,可使部分(MnO)还原,钢中的Mn有所升高,最后,随着脱碳反应的减弱,[Mn]又有所下将。
⑶碳的氧化第一特点:>1400℃时,开始有少量的碳氧化>1523℃时,碳开始大量被氧化第二特点:直接供氧条件下2[C]+{O2}=2{CO}(放热)[C]+[O]={CO}(放热)间接供氧条件下2/3Fe2O3(固)+2[C]=4/3Fe(液)+2CO(吸热)第三特点:碳氧反应主要在气泡与金属的界面上发生5、控制钢水终点含碳量的方法有哪些?⑴拉碳法:也就是当熔池金属中的含碳量达到要求时停吹⑵高拉补吹法:冶炼中高碳钢时采用⑶后吹增碳法:在冶炼中高碳钢时,可先将碳吹得较低,然后再增碳6、什么叫炉渣“返干”,炉渣“返干”与脱碳有什么关系?在氧气顶吹转炉吹炼的中期,冶炼温度已足够高,碳氧反应激烈,此时枪位比较低,已形成的炉渣的流动性往往会突然降低,甚至会造成结块,这就叫炉渣“返干”。
当(FeO)较高时,炉渣是一个均匀的液体在转炉吹炼的中后期,碳氧反应速度很快,炉渣中的FeO大量地减少。
当(FeO)<16%时,炉渣体系进入多相区,沉淀出2CaO·SIO2、3CaO·SIO2及CaO等固相颗粒,炉渣黏度加大,造成不同程度的“返干”。
7、什么叫“硬吹”、“软吹”?所谓硬吹、软吹是指氧气射流对熔池冲击力的大小,从而引起不同的熔池作用而区分的。
氧气射流对熔池的作用,主要是冲击深度、冲击面积、搅拌强度以及对钢、渣的击碎等。
硬吹就是指枪位较低,对熔池的冲击深度较深,冲击面积较小,搅拌作用及对金属液的击碎较强,反应速度快,适用脱碳,渣中氧化铁少。
软吹则是指枪位较高,射流对熔池的冲击深度浅,冲击面积较大,搅拌作用及对金属液的击碎较弱,反应速度慢,渣中氧化铁高,适用化渣。
8、脱磷的基本条件是什么?脱磷反应是钢渣间的氧化反应4(CaO)+2[P]+5(FeO)=(4CaO·P2O5)+5Fe⑴较高的碱度⑵较高的(FeO)⑶较低的温度⑷较大的渣量9、脱硫的基本条件是什么?主要是炉渣脱硫,是钢渣间的置换反应[FeS]+(CaO)=(CaS)+(FeO)一部分为气化脱硫[S]+{O2}={SO2}⑴较高的碱度⑵较低的(FeO)⑶较高的温度⑷较大的渣量10、什么叫活性石灰?活性石灰也叫轻烧石灰,是一种含SIO2及S量较低、粒度较小、反应能力强、冶炼时容易溶解的石灰。
其物理特性是体积密度小(1.5-1.7g/cm3),比表面积大(1.5-2.0m2/kg),气孔率高(50%),活性度﹥300ml4NHCL(10分钟)。
11、什么叫供氧强度?它对冶炼有什么影响?供氧强度是衡量吹炼强度的一个指标,它是指单位时间内每吨金属料由喷枪供给的氧气量,单位是m3/t﹒min。
供氧强度对冶炼过程有重大影响,供氧强度过小,冶炼时间长,对化渣不利。
供氧强度过大,由于熔池反应不能“吸收”大量的氧气,会造成严重的喷溅。
因此,供氧强度的选择原则是,在不造成严重喷溅的条件下,尽可能采用较大的供氧强度。
宁波建龙180t转炉的氧枪设计为五孔拉瓦尔型,供氧强度为3.65 m3/t﹒min。
12、什么叫“拉碳”?“拉碳”是我国转炉炼钢工人常用的一个通俗的技术术语,是指吹炼过程进行到熔池钢液中含碳量达到出钢的要求时,停止吹氧并摇炉这个过程。
所以,拉碳就是根据钢水含碳量控制终点的操作。
13、如何确定氧枪的枪位高度?喷枪枪位高度是吹炼工艺的一个重要参数,确定枪位主要考虑两个因数:一是使流股有一定的冲击面积,二是要使流股有一定的冲击深度。
要确定流股的冲击面积,则枪位要高,但过高将使流股的冲击深度减小,熔池搅拌减弱,熔池表面铁的氧化加剧,吹炼时间延长。
但枪位过低,冲击面积过小,冲击深度过大,熔池铁的氧化减小,不易化渣,且易损坏炉底。
因此,应有一个合适的喷枪高度,一般是由经验确定一个控制范围,根据吹炼中的炉况加以调整。
14、什么是炉渣的碱度?对冶炼有什么影响?炼钢生产中,炉渣中CaO与SiO2含量的比值称为碱度(R),即R=%CaO/%SiO2。
碱度值反应了渣中CaO除去与SiO2结合后,剩余自由CaO的多少,脱磷及脱硫反应都要求渣中有足够量的自由CaO,才能有效进行。
所以,碱度是炉渣脱磷脱硫能力的重要标志。
但并不是碱度越高越好。
例如,吹炼前期,炉温较低,此时如果炉渣碱度过高,渣子发粘,脱磷反应不能有效进行,一般应将碱度控制在R=1.5左右。
吹炼后期,炉温高,可以造碱度较高的炉渣(R=2.5-3.0),但如果碱度过高,不仅增加石灰消耗和热损耗,而且,炉渣的脱磷、脱硫能力提高不多,甚至因为炉渣发粘,反而影响了脱磷、脱硫的效率。
终渣碱度不能过小,否则,不仅影响磷、硫的去除,低碱度炉渣将加剧对炉衬的侵蚀。
15、什么是炉渣的氧化性?对冶炼有什么影响?炉渣氧化性是表示炉渣对C、Si、Mn、P等元素氧化能力的一种重要性质,生产上,常以炉渣中的∑FeO含量来表示其氧化性,∑FeO高,则称氧化性强,∑FeO低,则称氧化性弱,∑FeO是渣中FeO及Fe2O3含量经换算后之和,常采用两种换算方法。
全氧法:(∑FeO)%=(FeO)%+1.35(Fe2O3)%全铁法:(∑FeO)%=(FeO)%+0.9(Fe2O3)%炉渣氧化性对冶炼过程有很大的影响⑴影响脱磷及脱硫氧化性强的炉渣,有利于脱磷,不利于脱硫。
⑵影响石灰的溶解(即化渣)速度在炼钢过程中炉渣碱度较高时,FeO是降低炉渣熔点,促进石灰溶解的重要且是持续性的因素。
⑶影响钢液中残余含锰量氧化性强时,钢中残余锰就低,反之则高。
⑷影响钢液终点时的含氧量炉渣氧化性强,钢液含氧量就高,反之则低。
⑸影响金属及铁合金的收得率氧化性强,收得率则低,反之则高。
⑹影响泡沫渣的生成与喷溅的发生渣中含有一定数量的FeO,才能形成转炉炼钢所需要的泡沫渣,但是FeO过高,则会发生大量喷溅。
⑺影响转炉炉衬寿命 FeO对炉衬的侵蚀能力甚强,炉渣氧化性过高,将大大地降低炉衬使用寿命。
由上可见,控制炉渣氧化性,有着重大的意义。
16、炉料中加萤石有什么作用?萤石的主要成分是CaF2,其它还含有少量的SiO2、AI2O3、Fe2O3等化合物,萤石的熔点较低(930℃左右)。
加入炉内后,能使CaO和2CaO·SiO2的熔点降低,生成低熔点的化合物3CaO·CaF2·2SiO2(熔点1362℃)也可以与MgO生成低熔点化合物(1350℃),从而使石灰迅速地溶解改善碱性炉渣的流动性,适应转炉炼钢快速成渣的要求。
萤石化渣作用虽快,但持续时间短,大量使用萤石会增加喷溅,加速炉衬的侵蚀,应控制使用。
17、吹炼过程中的喷溅是怎样造成的?喷溅是转炉炼钢过程中常见的现象,由于氧气流股对熔池的冲击,以及脱碳反应产生大量CO气体逸出,造成炉渣及金属液的飞溅是不可避免的,在正常情况下,这种飞溅的高度一般不会超出炉口,不形成喷溅。
但在脱碳反应突然加剧,例如,当脱碳速度达到0.40-0.60%/min 时(正常情况是0.20-0.25%/min),短时内产生大量的CO,每秒钟向炉口排出其体积为钢液体积3-4倍的CO气体,具有较大的动能,可将炉渣及金属液喷出炉外,所以,熔池脱碳反应的不均匀性而产生的突发性脱碳,是发生喷溅的根本原因。
熔池温度的突然变化及炉渣中FeO的大量聚集,又是发生突然性脱碳反应的导因。
炉渣严重发泡时,泡沫渣充满了炉膛,在这种情况下,脱碳速度稍有增加,即可将炉渣喷出炉外。
18、怎样预防喷溅的发生?预防喷溅关键在于吹炼操作,避免导致喷溅的因素产生,主要有⑴控制好熔池温度。
前期温度不过低,中期温度不过高,防止熔池温度突然降低,保证脱碳反应能均衡进行,消除爆发性脱碳发应。
⑵控制好渣中∑FeO,不使渣中氧化铁过高。
当炉渣已化时,一定要降枪,减少渣中氧化铁。
⑶吹炼中途加料,尽量采用小批量多批次的办法,以避免熔池温度明显降低,而使渣中氧化铁增高。
⑷炉渣不化,提枪化渣时,不要长时间在高枪位吹氧,否则,氧化铁大量增加,炉渣一化,便引起喷溅。
一旦发生喷溅,不能立即降枪,若此时降枪,脱碳反应更加激烈,反会加剧喷溅。