精益生产管理体系培训资料
精益生产培训管理资料

精益生产培训管理资料精益生产是一种追求生产效率、消除浪费的管理理念,通过持续改进和员工参与来实现高质量、低成本的生产。
为了帮助企业和员工更好地理解和应用精益生产,培训管理资料是必不可少的工具之一。
以下是一份关于精益生产培训管理资料的参考内容:一、精益生产概述1. 精益生产的定义和起源2. 精益生产的主要原则和特点3. 精益生产的优势和价值二、浪费与价值1. 浪费的概念和分类2. 价值流分析和价值流图的制作3. 识别与消除浪费的方法和工具(如6Sigma、5S、Kanban)三、连续改进1. 连续改进的重要性和目标2. PDCA循环和A3问题解决方法3. Kaizen活动的组织和实施四、员工参与与激励1. 员工参与的意义和价值2. 员工参与的具体方式:小组讨论、问题解决、改善提案等3. 员工激励的方法:奖励制度、培训机会、晋升等五、价值流管理与精细化生产1. 价值流管理的概念和原则2. TPS(丰田生产方式)的核心要素和实践3. 一体化生产和精细化生产的关键技术和方法六、精益生产的案例和实践1. 国内外企业成功应用精益生产的案例介绍2. 精益生产在本企业中的应用实践3. 成功实施精益生产需要的关键因素和注意事项七、精益生产的评估和提升1. 精益生产的评估标准和方法2. 评估结果的分析和改进方向的确定3. 持续改进和提升精益生产的方法和策略八、精益生产的管理与监控1. 精益生产的管理体系和方法2. 生产指标的设定和监控3. 精益生产的绩效评估和持续改进以上仅为一份精益生产培训管理资料的参考内容,具体的培训资料内容和形式可以根据企业的实际需求和情况进行调整和定制。
在培训过程中,还可以结合实例、案例分析和小组讨论等教学方法,以提高培训效果和参与度。
九、精益生产的沟通与协作1. 有效沟通的重要性和原则2. 沟通障碍及如何解决3. 跨部门协作与团队工作的重要性和技巧十、精益生产的文化建设1. 精益文化的特点和重要性2. 如何树立和培养精益文化3. 精益文化对企业发展的影响十一、精益生产的未来发展方向1. 数字化和智能化对精益生产的影响2. 全球化和供应链管控对精益生产的挑战与机遇3. 创新和研发对精益生产的持续改进与升级以上是一份关于精益生产培训管理资料的参考内容。
精益生产管理培训资料

KINSNA
精益生产的两大支柱
准时化:在必要的时候,生产必要数量的必要产品, 英文全称 “JUST IN TIME”, 简称“JIT”。
----均衡生产 ----单个流生产 ----标准化作业 ----拉动式 ----看板应用
KINSNA
精益生产的两大支柱
自动化:动字带人字旁的自动化,即是“机器被赋予 了人的智慧”,起到杜绝过量制造和生产不合格品这种
KINSNA
为何要实施精益生产
3.增加现金的周转 -原材料 -在制品 -成品
KINSNA
为何要实施精益生产
4.增加库存周转率 -测定库存轮流频率的财务数据 -对现有资金周转有直接影响 -对制造交货期有影响 库存周转率=销售标准成本/平均现有库存 原来周转率=35000/9000=3.8 精益生产后周转率=35000/3000=11.6
KINSNA
在越来越多的其他行业的企业中,精益管理的 生产组织方法、人员管理方法以及企业协作方法 都被广泛地吸收与推广 丰田公司开创精益生产的同时,日本独特的 文化氛围也促进精益生产的产生。强调集体与协 作的东方文化,为精益管理的人力管理提供了一 个全新的思维角度。符合这种追求集体与协调意 识的我国企业文化,更应用精益思想管理企业。 目前全球众多的发达国家都在采用精益生产 和六个西格玛的管理思想来降低成本,提高竞争能 力,满足顾客的要求.
KINSNA
中国现将成为世界制造业的重心。面对资金雄厚、生 产条件先进且早已形成了自己一套管理体系的世界跨
国集团和国内同行业的佼佼者,我们如何应对?面对
竞争日益激烈的市场,困扰企业的种种不良现象,已 成为阻碍企业生存和发展的致命因素。但同样这些现 象也是使我们企业痛下决心,进行生产管理的过程控 制、提高制造系统的柔性、提升企业市场反应速度。
精益生产管理培训课件模板

中板在制品钢材 鄂城钢铁 0.8
棒线在制品钢材 河北敬业
在制品钢材合计 合计
0.1
6.2 10.0
2024年控制目标 一季度 二季度 三季度 四季度
1.0 3.0 3.0 1.0
2.5 2.4 2.4 2.5
2.5 2.6 2.6 2.5 6.0 8.0 8.0 6.0 1.7 1.5 1.5 1.7
宝钢股份 /
韶钢
100.0 99.0
100.0 100.0 100.0
100.0 100.0 100.0
93.9 93.6 93.5
宝钢股份 /
宝钢股份
98.0 98.0
100.0 100.0 100.0
依据产品盈利能力变化及时 调整生产流向,实现有效生 产资源最大效益化。充分发 挥绩效管理对计划值执行的 管控和引导作用,强化计划 值控制力度和执行效率评价。
6
计划值与交货期管理---总目标
计划值管理目标
聚焦计划管理专业化
目标:2024年计划值完成率100%
科学制定
按照上一年度最好4月平均 值制定工序产能能力,同时 结合“四有”原则,算账生 产,实现计划安排和企业效 益最大化的最佳组合。
调整评价
过程管控
产线
强化计划值过程管控,实现 计划的精细化管理,重点关 注铁钢轧瓶颈环节计划执行
查找计划值管理工作存在的 问题和短板,制定改善措施, 持续提高公司计划执行率。
冷轧产线
100.0
90.0
中板产线 计划值管10理0严.0 格执行 94.1
“月计划、周调整、日跟踪”,
全面提高生产计划执行率。
宝钢股份 鄂钢
98.0 97.0
100.0 100.0
精益生产管理体系培训课件

方法①、②都有被动的色彩!方法③ 才是主动的做法!
生产计划的编排两种思路
传统生产方式推进式(Push)生产计划
生产计划:既制定最终产品计划,也 制定产品各配套车间的零件生产计划。
D车间计划 A车间计划 D车间生产 A车间生产 D零件入库 A零件入库 出库 最终产品使用
推进式(Push)生产计划问题
精益生产的座右铭: “永远不变的是‘变化’” “永远存在更好的方法”
改善的着眼点: 从现场5S开始,由点到线,由线到面, 由面到链。
1、先从制造过程瓶颈点、问题点改善。 2、在不断积累对瓶颈、停滞、搬运、库存等点 的改善,所有的物、人被激活使之流动,变 成 “流水线” 3、以选定的样板产品纵向展开,完成了线的 改善之后,就让别的车间向这个车间看齐, 就变成“面的改善”。这一般称为“横向展开” 4、最终为链的改善:销售←生产→供应商
永续经营之根本
所谓管理,是指利用拥有的
的资源,建立过程控制,完成价
值增加的(或产生新的价值)过程。
IN
资源
OUT
过程控制 产品
产品价值≥资源+管理成本
三种经营思想
1、成本中心型 成本=售价-利润 成本上升要保持原有利润必须提高售价 2、售价中心型 售价=成本+利润 成本保持不变,用售价决定利润 3、利润中心型 利润=售价-成本 在充分竞争的市场上,一般工业产品终是越来越 便宜,为保持目标利润不变,追求成本越来越低同 时率先降价,以强占市场份额,保持领先地位。
第一部分: 认识工厂常见浪费现象案例
JIT诞 生背景
传统生产方式(消费旺盛,商品供应相对不足的时代)
少品种大批量生产
以批统生产方式问题点
传统生产方式: 1、品种大批量生产方式是粗放式管理,将 众多浪费问题藏匿在粗放生产中。 2、少品种同消费多层次需求不符。 JIT:粗放式 精益求精式。 有了浪费,立即暴露,彻底排除
精益生产篇(培训资料)
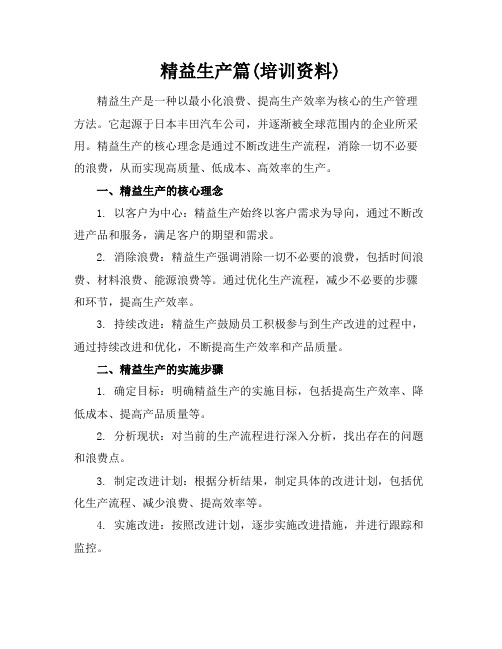
精益生产篇(培训资料)精益生产是一种以最小化浪费、提高生产效率为核心的生产管理方法。
它起源于日本丰田汽车公司,并逐渐被全球范围内的企业所采用。
精益生产的核心理念是通过不断改进生产流程,消除一切不必要的浪费,从而实现高质量、低成本、高效率的生产。
一、精益生产的核心理念1. 以客户为中心:精益生产始终以客户需求为导向,通过不断改进产品和服务,满足客户的期望和需求。
2. 消除浪费:精益生产强调消除一切不必要的浪费,包括时间浪费、材料浪费、能源浪费等。
通过优化生产流程,减少不必要的步骤和环节,提高生产效率。
3. 持续改进:精益生产鼓励员工积极参与到生产改进的过程中,通过持续改进和优化,不断提高生产效率和产品质量。
二、精益生产的实施步骤1. 确定目标:明确精益生产的实施目标,包括提高生产效率、降低成本、提高产品质量等。
2. 分析现状:对当前的生产流程进行深入分析,找出存在的问题和浪费点。
3. 制定改进计划:根据分析结果,制定具体的改进计划,包括优化生产流程、减少浪费、提高效率等。
4. 实施改进:按照改进计划,逐步实施改进措施,并进行跟踪和监控。
5. 持续改进:在实施改进的基础上,不断进行持续改进,提高生产效率和产品质量。
三、精益生产的工具和方法1. 5S管理:通过整理、整顿、清扫、清洁、素养五个步骤,提高生产现场的管理水平。
2. 单件流生产:通过优化生产流程,实现单件流生产,减少库存和浪费。
3. 拉动式生产:根据客户需求,实现按需生产,减少库存和浪费。
4. 标准化作业:制定标准化的作业流程,提高生产效率和产品质量。
5. 持续改进:通过PDCA循环,不断进行持续改进,提高生产效率和产品质量。
四、精益生产的挑战和应对策略1. 变革管理:精益生产需要企业进行全面的变革,包括管理理念、生产流程、员工培训等方面。
企业需要制定明确的变革计划和策略,确保变革的顺利进行。
2. 员工参与:精益生产的成功实施需要员工的积极参与和支持。
精益生产培训资料
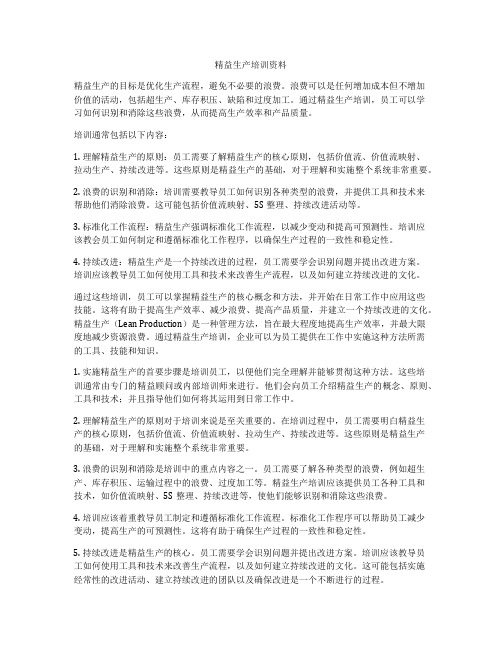
精益生产培训资料精益生产的目标是优化生产流程,避免不必要的浪费。
浪费可以是任何增加成本但不增加价值的活动,包括超生产、库存积压、缺陷和过度加工。
通过精益生产培训,员工可以学习如何识别和消除这些浪费,从而提高生产效率和产品质量。
培训通常包括以下内容:1. 理解精益生产的原则:员工需要了解精益生产的核心原则,包括价值流、价值流映射、拉动生产、持续改进等。
这些原则是精益生产的基础,对于理解和实施整个系统非常重要。
2. 浪费的识别和消除:培训需要教导员工如何识别各种类型的浪费,并提供工具和技术来帮助他们消除浪费。
这可能包括价值流映射、5S整理、持续改进活动等。
3. 标准化工作流程:精益生产强调标准化工作流程,以减少变动和提高可预测性。
培训应该教会员工如何制定和遵循标准化工作程序,以确保生产过程的一致性和稳定性。
4. 持续改进:精益生产是一个持续改进的过程,员工需要学会识别问题并提出改进方案。
培训应该教导员工如何使用工具和技术来改善生产流程,以及如何建立持续改进的文化。
通过这些培训,员工可以掌握精益生产的核心概念和方法,并开始在日常工作中应用这些技能。
这将有助于提高生产效率、减少浪费、提高产品质量,并建立一个持续改进的文化。
精益生产(Lean Production)是一种管理方法,旨在最大程度地提高生产效率,并最大限度地减少资源浪费。
通过精益生产培训,企业可以为员工提供在工作中实施这种方法所需的工具、技能和知识。
1. 实施精益生产的首要步骤是培训员工,以便他们完全理解并能够贯彻这种方法。
这些培训通常由专门的精益顾问或内部培训师来进行。
他们会向员工介绍精益生产的概念、原则、工具和技术;并且指导他们如何将其运用到日常工作中。
2. 理解精益生产的原则对于培训来说是至关重要的。
在培训过程中,员工需要明白精益生产的核心原则,包括价值流、价值流映射、拉动生产、持续改进等。
这些原则是精益生产的基础,对于理解和实施整个系统非常重要。
精益生产管理培训课件

1.1 精益生产方式概论
规MEASUREMENTS包括
➢ 收货准则(水平) ➢ 成本目标
➢ 规格书
➢ 效率目标
➢ 质量目标
➢ 其他目标
➢ 生产目标
➢ 收货依据
➢ 图纸
➢ 其他要求(如交货/
运送要求等) 17
1.1 精益生产方式概论
监MONITORING包括
➢ 检查/测量/测试指示
➢ 检查/测量/测试计划
的区别是什么?
8
1.1 精益生产方式概论
制造与生产在一般的理解是同义词,但其实有 不同之内涵.
首先一项生产过程是将输入变为输出(产品/服 务).
输入
生产过程
输出
9
1.1 精益生产方式概论
生产输入
人 MAN
机 MACHINES
料 MATERIAL
法 METHOD
规 MEASUREMENTS
但在导入的作业程序及方法上却比丰田生产体 系更为明确,更有条理.
5
1.1 精益生产方式概论
以企业价值流VALUE STREAM的了解与改善为管 理的立轴与起点.
引进各样的管理工具与技术. 管理工具包括目视管理/拉式生产系统/全面生
产性保养(TPM)等. 透过整合应用.
6
1.1 精益生产方式概论
的过程作出改良,减少(完全消灭)浪费.
33
1.1.3 品质控制的工具
有7种新/旧工具
7种旧工具
检查表 直方图 柏拉图 散布图
控制图 鱼骨图 层别图
34
1.1.3 品质控制的工具
检查表-描述次品及统计数量 直方图-描述某一项规格变化的分布情况
➢ 决定制造过程是否稳定 ➢ 决定有不合格的出现的机率 散布图-找出规格变化某一项生产参数的关系 柏拉图-对处理问题的先/后/急/缓作出排序
精益生产培训资料
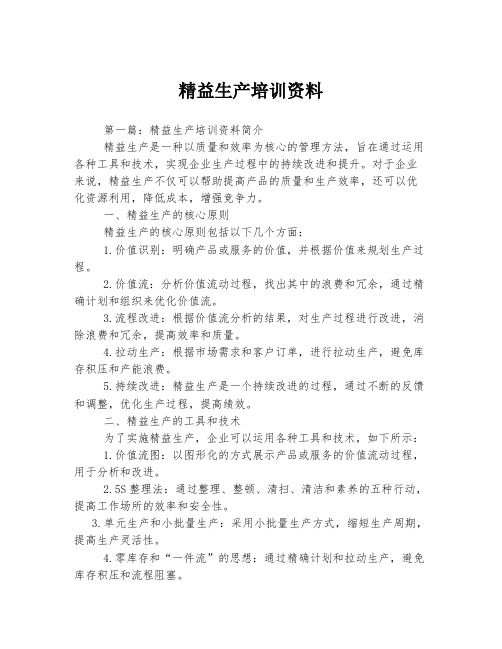
精益生产培训资料第一篇:精益生产培训资料简介精益生产是一种以质量和效率为核心的管理方法,旨在通过运用各种工具和技术,实现企业生产过程中的持续改进和提升。
对于企业来说,精益生产不仅可以帮助提高产品的质量和生产效率,还可以优化资源利用,降低成本,增强竞争力。
一、精益生产的核心原则精益生产的核心原则包括以下几个方面:1.价值识别:明确产品或服务的价值,并根据价值来规划生产过程。
2.价值流:分析价值流动过程,找出其中的浪费和冗余,通过精确计划和组织来优化价值流。
3.流程改进:根据价值流分析的结果,对生产过程进行改进,消除浪费和冗余,提高效率和质量。
4.拉动生产:根据市场需求和客户订单,进行拉动生产,避免库存积压和产能浪费。
5.持续改进:精益生产是一个持续改进的过程,通过不断的反馈和调整,优化生产过程,提高绩效。
二、精益生产的工具和技术为了实施精益生产,企业可以运用各种工具和技术,如下所示:1.价值流图:以图形化的方式展示产品或服务的价值流动过程,用于分析和改进。
2.5S整理法:通过整理、整顿、清扫、清洁和素养的五种行动,提高工作场所的效率和安全性。
3.单元生产和小批量生产:采用小批量生产方式,缩短生产周期,提高生产灵活性。
4.零库存和“一件流”的思想:通过精确计划和拉动生产,避免库存积压和流程阻塞。
5.持续改进的PDCA循环:通过实施计划、执行、检查和调整的循环,不断追求改进和创新。
6.故障模式和影响分析(FMEA):分析产品或服务中的潜在故障模式及其潜在影响,以预防和纠正故障。
三、精益生产培训的意义和目标精益生产培训的意义在于帮助企业了解和掌握精益生产的核心理念和实施方法,促进管理和员工的思维转变,并提供实用性的工具和技术,以实现企业的持续改进和提高。
精益生产培训的目标主要包括以下几个方面:1.增强质量意识:通过培训,提高员工对产品质量的重视和追求,减少缺陷和废品的产生。
2.优化生产流程:通过培训,让员工了解和应用各种工具和技术,优化生产过程,提高效率和质量。
精益生产管理培训
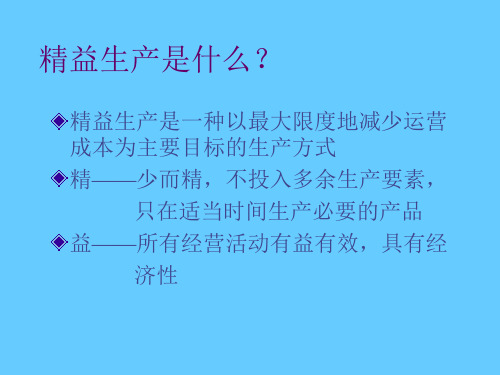
3.生产过程的在制品库存最低可减至1/10 4.工厂占用空间最低可减至1/2 5.成品库存最低可减至1/4
6.产品质量可大幅度提高30%
精益生产方式是彻底追求生产的合理性 和高效性,能灵活地生产适应各种需求 的高质量产品的生产技术
关注焦点:生产计划和控制,库存管理
LP在管理方法上的特点
•组织扁平化,减少非直接生产人员 •生产均衡化和同步化 •零库存和柔性生产 •全面质量管理(TQM),实现零缺陷 •减少任何浪费 •准时生产(JIT)
拉动式准时化生产(JIT)
以最终用户的需求为生产起点 强调物流平衡,追求零库存 看板生产 生产中的节拍可由人工干预,控制 采用拉动式生产,生产中的计划与调度 实际上由各个生产单元自己完成
精益生产是什么?
精益生产是一种以最大限度地减少运营 成本为主要目标的生产方式 精——少而精,不投入多余生产要素,
只在适当时间生产必要的产品 益——所有经营活动有益有效,具有经
济性
特点
•消除一切浪费 •追求精益求精和不断改善 •去掉一切不增值的岗位
核心:精简
LP对大量生产方式的优越性
1.所需人力资源最多可降至1/2
120units / h
(取一个工作台,尚有生产能力剩余)
装配线2:
60m / h 60s / h 20units / h 180s / unit
80units / h 4 20units / h
(取4个工作台)
装配线1:
60m / h 60s / h 45units / h 80s / unit
消除零件不必要的移动
生产布局不合理是造成零件往返搬动的 根源,使得生产线长,生产周期长,占 用很多在制品库存,增加生产成本
精益生产的培训资料
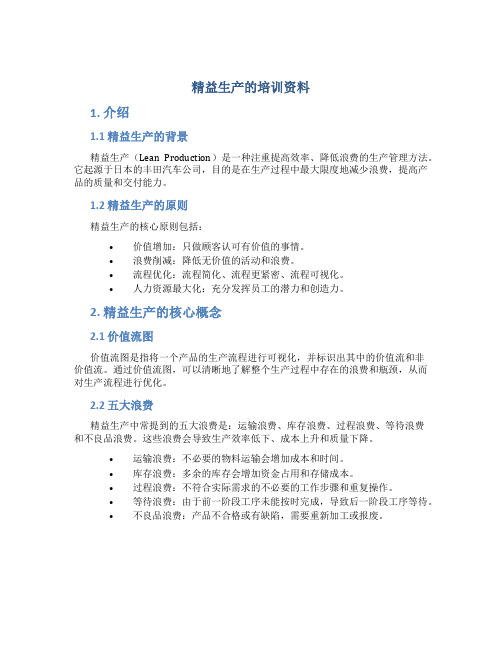
精益生产的培训资料1. 介绍1.1 精益生产的背景精益生产(Lean Production)是一种注重提高效率、降低浪费的生产管理方法。
它起源于日本的丰田汽车公司,目的是在生产过程中最大限度地减少浪费,提高产品的质量和交付能力。
1.2 精益生产的原则精益生产的核心原则包括:•价值增加:只做顾客认可有价值的事情。
•浪费削减:降低无价值的活动和浪费。
•流程优化:流程简化、流程更紧密、流程可视化。
•人力资源最大化:充分发挥员工的潜力和创造力。
2. 精益生产的核心概念2.1 价值流图价值流图是指将一个产品的生产流程进行可视化,并标识出其中的价值流和非价值流。
通过价值流图,可以清晰地了解整个生产过程中存在的浪费和瓶颈,从而对生产流程进行优化。
2.2 五大浪费精益生产中常提到的五大浪费是:运输浪费、库存浪费、过程浪费、等待浪费和不良品浪费。
这些浪费会导致生产效率低下、成本上升和质量下降。
•运输浪费:不必要的物料运输会增加成本和时间。
•库存浪费:多余的库存会增加资金占用和存储成本。
•过程浪费:不符合实际需求的不必要的工作步骤和重复操作。
•等待浪费:由于前一阶段工序未能按时完成,导致后一阶段工序等待。
•不良品浪费:产品不合格或有缺陷,需要重新加工或报废。
2.3 价值流分析通过对价值流进行分析,可以找到改善生产流程的机会。
分析包括识别价值和非价值流、测量价值流和非价值流的时间和成本,以及找出瓶颈和瓶颈的原因。
在分析的基础上,可以制定改进计划和实施措施。
3. 精益生产的实施步骤3.1 精益生产的基础准备在实施精益生产之前,需要进行一些基础准备工作,包括:•培训员工:让员工了解精益生产的基本原理和方法,以及其对企业的意义。
•设立团队:组建一个精益生产改善团队,负责推动和监督改进工作。
•确定目标:明确实施精益生产的目标,如提高产能、降低成本等。
•收集数据:对现有生产流程进行数据采集和分析,找出存在的问题和瓶颈。
3.2 精益生产的改进步骤根据实际情况,精益生产的改进步骤可以分为以下几个阶段:•价值流分析:通过价值流图和价值流分析,找出生产流程中的浪费和瓶颈。
精益化管理培训资料-文档资料
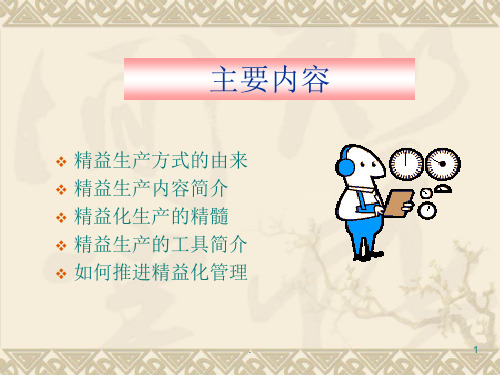
(3)价值流动:让价值增值环节无间断的流动起来;去掉 生产环节中一切无用的东西,每个工人及其岗位的安 排原则是必须增值,撤除一切不增值的岗位;精简产 品开发设计、生产、销售、管理中一切不产生附加值 的工作。
(4)需求拉动:让用户按需要拉动生产;
(5)尽善尽美:用尽善尽美的价值创造过程,为用户提供 尽善尽美的价值。追求精益求精和不断改善。
加工 维修 维护 停机 空转 转换
加工 搬运 停留 闲置 数检 质检
加工 搬运 等待 怠工 数检 质检
.
浪费
9
八大浪费
❖ 过剩生产的浪费 ❖ 过多在库的浪费 ❖ 等待的浪费 ❖ 搬运的浪费 ❖ 加工本身的浪费 ❖ 组装不良品的浪费 ❖ 动作的浪费 ❖ 员工智慧的浪费
.
10
(一)过量生产
产品生产超过需求,快过需求
考 4、要习惯性的从白纸的状态出发考虑
.
25
优化流程,提高效率
❖ 企业的生产流程包括:订单处理、物料计划、采购下单、
❖ 供应商备料、运输、来料检验、存储、搬运、加工、检验
❖ 和返工、过程等待、成品库存、发运、货款回收等环节
订 单 处 理
采 购 下 单
供 应 商 备 料
运 输
来 料 检 验
原 料 存 储
益,产生效益 所有经营活动都要 有益有效,并且具
有经济效益
.
4
精益生产
精益生产Lean Production :是一种能以最快的市场 响应速度,以最低的成本和最优的品质,设计和
制造市场所需产品的生产管理技术。
.
5
精益生产的5个理念
(1)价值:以客户的观点定义价值,而且通过对各个环节 中采用的杜绝一切浪费(人力、物力、时间、空间) 的方法与手段满足顾客对价格的要求。
精益生产管理5S培训课件

整顿(Seiton)
总结词
将必需品按照规定的位置进行摆放, 并保持整齐有序。
详细描述
整顿是在整理的基础上,对必需品进 行合理摆放,使其整齐有序。这需要 制定明确的标识和规定的位置,以便 员工能够快速找到所需物品,提高工 作效率。
清扫(Seiso)
总结词
清除工作场所内的脏污和垃圾,保持 环境整洁。
展望
未来5S将成为企业生产管理的必 备工具,将有更多的企业加入到 5S的实施中来
建议
企业应持续推进5S的实施,不断 完善和优化管理体系,提高生产 效率和产品质量
THANKS
感谢观看
同时,5S管理还有助于企业文化的建设,培养员工的团队精神和创新意识,促进企 业的可持续发展。
02
5S的实施方法
整理(Seiri)
总结词
将工作场所的物品进行分类,区分必需品和非必需品。
详细描述
整理是5S中的第一步,要求将工作场所内的物品进行分类,区分出必需品和非 必需品。对于非必需品,应考虑是否可以丢弃、回收或修理。对于必需品,应 明确其存放位置,以便在需要时能够快速找到。
问题一
员工对5S的实施不理解, 缺乏积极性
问题二
现场管理混乱,难以推行 5S
问题三
实施过程中遇到资源和技 术瓶颈
解决方案
加强培训和宣传,提高员 工对5S的认识和认同感
解决方案
建立标准化作业流程,明 确责任分工,加强监督和
考核
解决方案
寻求外部支持和资源整合 ,加强技术培训和交流
对未来实施5S的展望和建议
检查和评估
对5S实施效果进行检查和评估
通过各种指标和方法,对5S实施效果进行检查和评估,发现问题及时改进。
精益生产管理培训

精益生产管理培训精益生产管理是一种效率型的管理方法,旨在通过减少浪费和提高价值创造活动的效率,从而提升企业的生产效益。
为了推广和应用精益生产管理,许多企业会组织培训课程,以帮助员工和管理者掌握相关知识和技能。
精益生产管理培训通常包括以下内容:1. 精益生产管理概述:介绍精益生产管理的起源、发展和基本原理,让学员对精益理念有一个整体的了解。
2. 浪费识别与分析:介绍各种类型的生产浪费,例如等待时间、库存过剩、不必要的运输等,并教授如何识别和分析浪费的方法。
3. 价值流分析:教授如何通过价值流图分析整个生产过程中的价值与非价值活动,并确定改进的重点。
4. 拉动式制造原则:介绍拉动式制造的概念和实施方法,以实现供需平衡和减少库存。
5. 5S方法:详细介绍5S(整理、整顿、清扫、清洁、素养)方法,培养学员良好的工作环境整理和维护的意识。
6. 持续改进和团队合作:强调持续改进和团队合作的重要性,教授相关的方法和工具,如PDCA循环和Kaizen活动。
7. 精益生产管理案例分析:通过实际案例分析,让学员了解如何应用精益生产管理解决实际问题和取得实质性的改善效果。
在精益生产管理培训中,通常会通过讲解、案例分析、小组讨论和实践演练等形式进行教学。
培训的目的是让学员明白精益生产管理的理论与实践之间的关系,并能够根据企业实际情况进行具体应用和改进。
通过精益生产管理培训,员工和管理者不仅可以学习到先进的管理思想和方法,还能够提升解决问题的能力和团队合作能力。
这将有助于提高企业的生产效率、产品质量和竞争力,为企业的可持续发展奠定坚实的基础。
除了上述提到的培训内容,精益生产管理培训还可以涵盖以下相关的内容,以帮助学员全面理解和应用精益生产管理的方法和原则:8. 价值流映射(Value Stream Mapping):介绍如何通过价值流映射方法来绘制出整个生产过程中的价值流,并分析出其中存在的浪费和瓶颈,从而制定相应的改进措施。
- 1、下载文档前请自行甄别文档内容的完整性,平台不提供额外的编辑、内容补充、找答案等附加服务。
- 2、"仅部分预览"的文档,不可在线预览部分如存在完整性等问题,可反馈申请退款(可完整预览的文档不适用该条件!)。
- 3、如文档侵犯您的权益,请联系客服反馈,我们会尽快为您处理(人工客服工作时间:9:00-18:30)。
消除运输浪费
• 更加靠近供应基地 • 构成运输网络
– 预先确定运输日程 – 预先确定集货时间 – 明确的卸货时间 – 材料处理标准作业
• 采用标准的、可回收包装,运输装备空间利用率最大化 • RFID和定位技术
• 不增值活动 – 点数 – 搬运 – 检查 – 运输 – 移动
过程浪费
– 延迟 – 保管 – 返工 – 催促和干预 – 多重签署
• Therefore, 5 days of safety stock cover is neede •
– If CTI is 10 days and cycle time is 5 days, an order can always be expedited forward by 5 days
–
• Again, 5 days of safety stock cover is needed
消除过量生产
• 要求从根本上转变观念(可能与直觉相反)
– 只要能够满足市场需求,资源不一定需要完全利用,获得更高的成 本-效益
• 观察作为“顾客”的后工序的生产活动
– 仅生产“顾客”所要求的“量” – 用“需求拉动”(Kanban)代替“计划推动”(预测/MPS/MRP)
等待造成的浪费
• 时间陷阱的罪状 – 流程拥堵 – 刚性的工序安排,不具备“多技能” – 机器或者生产线停机,进行外部换装( External setup );例如:
= Cycle Time
工程准备时间 + 排队(延迟)时间 + 安装调试时间 + 生产运行时间 + 检验时间 + 返工 + 移动 + 接收
= 周期
材料采购周期计算
Order Placement Time
+ Supplier’s Manufacturing Cycle Time
+ Supplier’s Fulfillment Cycle Time
产品缺陷的浪费
• 不仅仅是不合格品本身造成浪费,还包括:
– 增加了后续流程的等待时间 – 返工 – 增加劳动力以找出缺陷产品、拆卸、重新组装 – 修复所增加的材料消耗 – 报废零件的材料和工时浪费
• 更加严重的情况是,客户发现缺陷带来的损失
• 实施6西格玛 • 关键概念
– Define – Measure – Analyze – Improve – Control
精益生产致力于在客户关系、产品设计、供应网络和工厂管理等 各个方面全面消除浪费。
其目标是以最少的人员、最低的库存、最短的时间,高效、经济 地生产出高质量的产品,对顾客需求做出最迅速的响应。
Source: MIT Production System Design Laboratory
精益生产已经成为更多制造商的策略
消除缺陷损失
定义 测量 分析 改进 控制
议程
1 精益(Lean)的概念 2 面临的挑战 3 转变成为精益企业
8种关键衡量指标
• Coefficient of Variation • Cycle Time • On-Time-In-Full (OTIF) • Days of Inventory Cover • Process Efficiency • Strategic Job Coverage Ratio • Line Balance Ratio • Overall Equipment Effectiveness (OEE)
触发点
}预期接收 现有库存
供应商B 立体库 中转库
制造产品的周期计算
Engineering & Configuration Time + Queue (Delay) Time + Setup Time + Production Running Time + Inspection Time + Rework Time + Moving Time + Receiving Time
+ Shipping Time
定单处理时间
+ Transport Time + Receiving Time + Inspection Time + Moving Time
+ 供应商制造周期 + 供应商交付周期 + 发运时间 + 运输时间 + 接收时间
+ 检验时间
= Cycle Time
+ 转移时间
离散系数/变异系数 周期 准时完全交付率 库存周转天数 过程效率 资源需求满足率 动态生产均衡率 设备综合效能
战略缓冲[看板]计算
Average Cycle Time Average Demand + Cycle Time Interval Average Demand + Safety Stock + Seasonality
库存浪费
• 与过量生产的浪费类似。主要问 •
题:
– 进程不同步
– 生产线不均衡
– 突然停机
– 冗长的换装
– 质量问题
– 缺勤
– 长途运输提前期
– 内部管理
– 供应商交货时间过长
– 信息问题
消除库存浪费
• 尽快处理废旧材料 • 仅生产后续流程需要的数量
– 实施需求拉动系统
• 仅采购需要的原材料数量
安全储备(Safety Stock)
• 预期OTIF >99.5% (3σ) ,针对供应和需求的主要变化,提供的库存 缓冲
• 安全储备
– 平均需求乘以CTI或者周期二者之中的较小者
• 离散系数
– 标准偏差/平均数 – 计算需求和供应
安全储备计算
3 MIN(CTI, Average Cycle Time) demand ([(supply supply)2 + (demand demand)2] 2)½ = Safety Stock
例如: 2分钟/台 25秒/台
例如: 180台/小时
精益生产对 “节拍”的定
义
过去习惯的 “节拍”定
义
目标是使Run Rate与 Takt Time处于平衡状态
什么是周期
• 周期是一个测量值,不是一个计算值
– 现场测量:生产1件产品实际花费的时间 – 测量两个时间:1)每个操作者的TCT(从开始到结束花费多长时
• 开展TPM – 跟踪设备OEE – 利用合适的流程消除故障 – 集中于消除5分钟故障 – 预防性维护
• 消除不增值的签字确认/批准
什么是“节拍”
• Takt是一个德语单词-“指挥棒”,管理音乐家的演奏节奏
– 在制造业术语中,通过顾客需求计算出来 – 满足需求必需的零件生产速度(节奏) – 任何精益系统的“心跳” – 目标:节拍必须达到满足需求的水平
• 为什么要实施精益生产?
– 更加激烈的竞争 – 越来越薄的利润 – 更多的按单生产 – 消除浪费 – 法规符合性审核
Seven Deadly Wastes 七种浪费
• Waste of Overproduction • Waste of Waiting Time • Transportation Waste • Processing Waste • Inventory Waste • Waste of Motion • Waste from Product Defects
• 找材料 • 找工单 • 找工具
– 额外调试 – 计划外停机 – 计划停机 – 签字确认/批准延迟
消除过度等待
• 复杂产品的生产同步 – 触发部件组装,满足下游产 品要求
• 动态重排 – 节拍和周期平衡 – 工人进行“多技能”培训
• 交叉排程和休息 • 开展4步快速换装
– 区分内部/外部换装 – 将外部换装 转换为内部换装 – 使内部换装简化并高效 – 消除调试
= Maximum Strategic Buffer
平均周期 平均需求 + 周期间隔 平均需求 + 安全储备 + 季节调整
= 最大战略缓冲
战略缓冲和触发点的作用机制
季节增减
周期间隔内 的平均需求
动态战略缓冲信息,最大限度降低总体库存
最大战略缓冲
}触发点 平均周期内 的平均需求
}安全库存
生产过程不断 消耗战略缓冲 消耗至触发点时,触发补料信息(拉)
• Example:
– 确定日需求(定单)值.
215件/日
– 确定一天内的工作时间(分钟). 10分钟休息
430分钟:8小时,30分钟午餐,2次
– 节拍=430/215=2 每2分钟必须生产1件
正确理解“节拍”
• Takt Time –节拍 是完成订单所需要的生产节奏,即 每件需要XX分钟。
• Run Rate 是资源(例如生产线、工作中心、 人员)可以供应的能力。
Operational Excellence from the Bottom Out
全有文档
Lean Production 精益生产
议程
1 精益生产概述 2 面临的挑战 3 转变成为精益企业
精益生产的定义
Lean production is aimed at the elimination of waste in every area of production including customer relations, product design, supplier networks and factory management. Its goal is to incorporate less human effort, less inventory, less time to develop products, and less space to become highly responsive to customer demand while producing top quality products in the most efficient and economical manner possible.