机械制造工艺基础全套课件
机械加工工艺基础(全套课件392P)
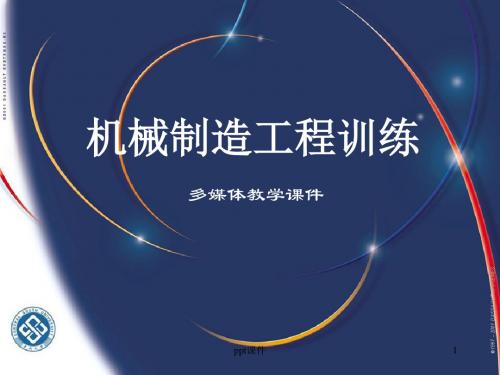
1.1.4第切一削运章动及切切削削要素加工基础知识
1.切削运动
要实现切削加工,刀具和工件之间必须具有 一定的相对运动,才能获得所需表面形状,这种 相对运动称为切削运动。
切削运动由机床提供。各种切削运动,都是 由一些简单的运动单元组合而成的。直线运动和 旋转运动是切削加工的两个基本运动单元。
第一章 切削加工基础知识
机械制造工程训练
多媒体教学课件
ppt课件
1Байду номын сангаас
材料成形工艺基础: 主要介绍机械零件毛坯成形方法的工
艺特点、工艺参数的选择、各类零件毛坯 的结构工艺性、零件的材料选择与成形方 法选择的基本原则。
机械加工工艺基础: 主要介绍机械加工的基本概念、切削
基本原理、切削机床与刀具、切削加工基 本工艺过程、选择切削加工方法的基本原 则,以及零件机械加工结构工艺性。
ppt课件
2
第一章 切削加工基础知识
1.1 切削加工概述 1.2 刀具及刀具切削过程 1.3 磨具及磨削过程 1.4 金属切削机床(自学、考试) 1.5 机床夹具及工件的装夹 1.6 机械加工质量 (不讲、不考) 1.7 材料的切削加工性 (不讲、不考) 1.8 切削液 (自学、考试)
第一章 切削加工基础知识
余的部分,使获得的零件具有符合图样要求的 尺寸精度、形状精度、位置精度及表面质量的 加工方法。 任何切削加工都必须具备三个基本条件:切削 工具、工件和切削运动。
第一章 切削加工基础知识
切削加工的实质是零件表面的形成过程,不同 类型表面所采用的成形方法是不相同的。
切削加工的对象是毛坯(或型材)。 切除的材料可以是金属也可以是非金属(如, 石材、木材、尼龙等)。
第一章 切削加工基础知识
2024版机械基础(全套课件487P)

机械基础(全套课件487P)contents •机械基础概述•机械设计基础知识•机械制造工艺与装备•液压与气压传动技术•机械工程材料及其选用•典型零部件设计计算与校核•现代设计方法在机械设计中的应用目录01机械基础概述机械定义与分类机械定义机械分类机械发展历史及现状发展历史机械的发展经历了古代机械、近代机械和现代机械三个阶段。
古代机械以简单工具和器械为主,近代机械开始引入蒸汽机和电动机等动力源,现代机械则向自动化、智能化方向发展。
现状当前,机械工业已经成为国民经济的重要支柱,涉及领域广泛,包括航空航天、汽车制造、能源化工等。
同时,随着科技的进步,现代机械设计制造水平不断提高,新材料、新工艺和新技术的应用推动了机械工业的发展。
本课程目标与要求课程目标课程要求02机械设计基础知识机械设计基本原则设计方法设计流程030201机械设计基本原则与方法连杆机构凸轮机构齿轮机构蜗杆传动机构常用机构及工作原理液压传动通过液体在密闭系统中的压力传递运动和动力,具有无级调速、易于实现自动化等优点。
利用蜗杆和蜗轮的啮合传递运动和动力,具有大传动比、结构紧凑等优点。
齿轮传动通过齿轮副的啮合传递运动和动力,具有传动效率高、结构紧凑等优点。
带传动通过带与带轮之间的摩擦传递运动和动力,具有结构简单、链传动传动装置类型与特点03机械制造工艺与装备铸造、锻造和焊接工艺铸造工艺锻造工艺焊接工艺切削加工方法及设备车削加工讲解车削的原理、特点及应用,包括车床的种类、结构、性能及选用。
铣削加工介绍铣削的原理、特点及应用,包括铣床的种类、结构、性能及选用。
磨削加工阐述磨削的原理、特点及应用,包括磨床的种类、结构、性能及选用。
介绍电火花加工的原理、特点及应用,包括电火花机床的种类、结构、性能及选用。
电火花加工激光加工超声加工水射流加工详述激光加工的原理、特点及应用,包括激光切割、激光焊接等。
阐述超声加工的原理、特点及应用,包括超声振动切削、超声磨削等。
机械制造技术基础(课程精完整版)ppt课件
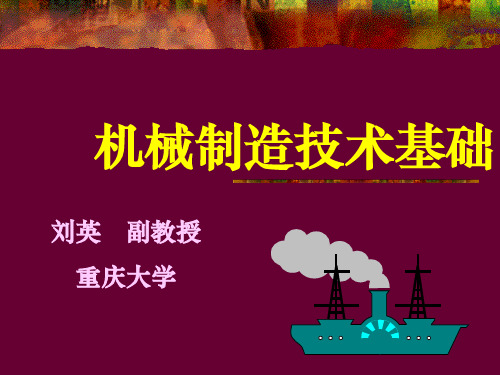
77
ppt精选版
一、对金属切削机床的基本要求
1. 机床的性能方面 (4)人机适应性
人机适应性的基本要求是可靠、 安全和舒适。
78
ppt精选版
一、对金属切削机床的基本要求
2. 机床的经济性方面
79
ppt精选版
一、对金属切削机床的基本要求
2. 机床的经济性方面 机床的经济性包括两方面: 机床制造厂的经济效益 机床使用厂的经济效益
切削用量三要素
背吃刀量asp、 进给量f 切削速度vc
50
ppt精选版
(6)合成切削运动
切削过程中,由主运动和进给运动合成 的运动称为合成切削运动。 合成切削运动方向:就是切削刃选定点相 对于工件的瞬时合成切削运动的方向;
合成切削速度ve:就是切削刃选定点相对
于工件的合成切削运动的瞬时速度。
51
2. 工件表面的形成
工件表面可以看成是一条线沿着另一条 线移动或旋转而形成的。并且我们把这两
条线叫着母线和导线,统称发生线。
14
ppt精选版
例、工件表面的形成
导线 母线
母线 导线
母线 导线 母线
导线 母线
导线 导线
导线
导线 母线
母线
图2-2 组成工件轮廓的几何表面
3.发生线的形成
1) 成型法——利用成形刀具来形成发生 线,对工件进行加工的方法。
二、金属切削机床的分类
(3)按机床的自动化程度分类
1)手动机床 2)机动机床 3)半自动机床 4)全自动机床
85
ppt精选版
二、金属切削机床的分类
(4)按机床的工作精度分类
1)普通精度机床 2)精密机床 3)高精度机床
机械制造工艺基础全套课件

5.数控工序与非数控工序间的衔接
有些工件的加工是由普通机床和数控机床共同完成 的,数控机床加工工序一般穿插在整个工艺过程之间, 应注意解决好数控工序与非数控工序间的衔接。如作为 定位基准的孔和面的精度是否满足要求,后道工序的加 工余量是否足够等。
第四节 选择毛坯和确定工序尺寸
一、毛坯选择
1.毛坯的种类
4.精基准的选择
基准重合原则 基准统一原则 互为基准原则 自为基准原则 基准不重合误
差最小条件
车床主轴箱工序简图 工艺尺寸链
基准不重合误差最小条件
5.辅助定位基准
涡轮叶片的辅助定位基准
第三节 工艺路线的拟定
一、表面加工方法的选择
选择加工方法一般根据工件的经济精度和表面粗糙度 来考虑。
有利于消除或减小变形对加工精度的影响。 可尽早发现毛坯的缺陷。 有利于合理地选择和使用设备。 有种于合理组织生产和工艺布置。
三、工序的集中与分散
工序集中——在一道工序中尽可能多地包含加工内 容,而使工艺过程中总的工序数目减少。集中到极限时, 工艺过程只有一道工序,这道工序就能把工件加工到图 样规定的要求。
(1)一般情况下,单件、小批量生产采用工序集中 原则,而大批量生产可采取工序集中原则,也可采取工 序分散原则。
(2)单件、小批量生产是在通用设备上主要使用通 用工具进行加工;大批、大量生产采则必须采用高效专 用设备,自动、半自动机床,组合机床等进行加工。
(3)应多采用工序集中原则来制定工艺过程和组织 生产。
除工艺需要的表面处理(如工件非渗碳表面的保护 性镀铜、非氮化表面的保护性镀锡和镀镍等)视工艺要 求而定以外,一般表面处理工序都安排在工艺过程的最 后。
4.检验工序的安排
(1)在下列情况下安排中间检验工序: 1)工件从一个车间转到另一车间前。 2)重要工件的关键工序加工后。 (2)特种检验主要指无损探伤,此外还有密封性检 验、流量检验、称重检验等。 (3)最终检验工序安排在零件表面全部加工完之后。
机械制造工艺基础知识培训课件

第二十六页,共66页。
机械加工工艺(gōngyì)规程的制订——基本概念
四、工艺规程 4、格式 技术文件JB/Z187.3—88《工艺规程格式》,
要求各机械(jīxiè)制造厂按统规定的格式填写。 属于机械(jīxiè)加工工艺规程的有: 1)机械(jīxiè)加工工艺过程卡片。 2)机械(jīxiè)加工工序卡片。 3)标准零件或典型零件工艺过程卡片。 4)单轴自动车床调整卡片。 5)多轴自动车床调整卡片。 6)机械(jīxiè)加工工序操作指导卡片。 7)检验卡片等。
第二十三页,共66页。
机械加工工艺规程(guīchéng)的制订——基本概 念四、工艺规程
1、定义 规定产品或零部件制造工艺过程和操作方法等的工艺
文件称为工艺规程。 其中,规定零件机械加工工艺过程和操作方法等的工
艺文件称为机械加工工艺规程。 它是在具体的生产条件下,最合理或较合理的工艺过
程和操作方法,并按规定的形式书写成工艺文件,经审批 (shěnpī)后用来指导生产的。
第十六页,共66页。
机械加工工艺规程(guīchéng)的制订——基本概念
三、生产纲领、生产类型及其工艺特征 2.生产类型
根据生产纲领的大小和产品品种的多少,机械制造企业的 生产可分为三种类型:单件生产、成批生产和大量生产。 (1)单件生产产品品种很多,同一(tóngyī)产品的产量很少,而且 很少重复生产,各工作地加工对象经常改变。如重型机械制造、 专用设备制造和新产品试制等均属单件生产。 (2)大量生产产品的产量很大,大多数工作地长期重复地进行某一 工件的某一工序的生产。如汽车、拖拉机、轴承和自行车等产 品制造多属大量生产。 (3)成批生产一年中分批轮流制造几种产品,工作地的加工对象周 期性地重复。如机床、机车、纺织机械等产品制造,多属成批 生产。
机械制造基础全套电子课件教案(完整版)ppt
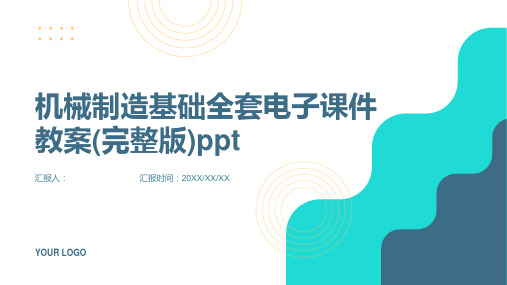
定义:新材料是指 最近发展或正在发 展的具有优异性能 和特殊功能的材料
分类:按照应用领 域分类,可分为电 子、航天、生物医 学等领域
发展趋势:高分子 材料、复合材料、 金属材料、无机非 金属材料等
重要性:新材料是 现代高新技术产业 的重要基础,对于 促进社会进步和经 济发展具有重要意 义
机械制造工艺
分类:自由锻、模锻
锻造工艺流程:下料、加热、锻 打、冷却、矫形
锻造设备:锻锤、液压机、机械 压力机等
焊接工艺
焊接定义:通过加 热或加压,或两者 并用,使两个分离 的物体产生原子间 结合。
焊接方法:电弧焊、 电阻焊、激光焊、 钎焊等。
焊接材料:焊条、 焊丝、焊剂等。
焊接应用:广泛应 用于机械制造、建 筑、化工等领域。
焊接电源 送丝机构 焊枪 控制系统
机械加工设备
车床:用于切削旋转零件, 分为卧式、立式和数控车 床等。
铣床:用于切削平面和沟 槽,包括数控铣床、加工 中心等。
钻床:用于在工件上钻孔, 包括摇臂钻床、数控钻床 等。
镗床:用于加工大型箱体 零件,可进行粗加工和精 加工。
磨床:用于磨削零件表面,具中, 冷却凝固后形成具有一定形状和 质量的金属零件的工艺方法
分类:砂型铸造、金属型铸造、 压力铸造等
优点:可以制造形状复杂的零件, 且成本相对较低
缺点:生产周期长,精度不高
锻造工艺
定义:将金属坯料放入模具中施 加压力,使其产生塑性变形,从 而获得所需形状和尺寸的零件
机械制造基础全套电子课件 教案(完整版)ppt
汇报人:
汇报时间:20XX/XX/XX
YOUR LOGO
目录
CONTENTS
1 机械制造概述 2 机械制造材料 3 机械制造工艺 4 机械制造设备 5 机械制造过程控制 6 机械制造的未来发展
机械制造工艺基础全套讲义51页PPT
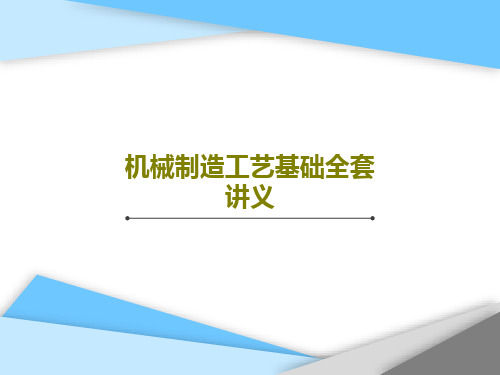
6、纪律是自由的第一条件。——黑格 尔 7、纪律是集体的面貌,集体的声音, 集体的 动作, 集体的 表情, 集体的 信念。 ——马 卡连柯
8、我们现在必须完全保持党的纪律, 否则一 切都会 陷入污 泥中。 ——马 克思 9、学校没有纪律真而不 幼稚, 勇敢而 鲁莽, 倔强而 有原则 ,热情 而不冲 动,乐 观而不 盲目。 ——马 克思
46、我们若已接受最坏的,就再没有什么损失。——卡耐基 47、书到用时方恨少、事非经过不知难。——陆游 48、书籍把我们引入最美好的社会,使我们认识各个时代的伟大智者。——史美尔斯 49、熟读唐诗三百首,不会作诗也会吟。——孙洙 50、谁和我一样用功,谁就会和我一样成功。——莫扎特
机械制造工艺基础全套通用课件

选择合适的装配方法、确定合理的装配顺序、采用有效的检测手段 等。
装配尺寸链与装配方法
装配尺寸链
在装配过程中,由相关零件的 尺寸和相对位置关系组成的封
闭图形。
装配尺寸链的建立
根据设计要求,确定封闭环、 组成环,并标注各环的尺寸和
偏差。
装配方法
根据零件的特性、精度要求、 生产批量等因素选择合适的装 配方法,如互换装配、选配装
零件的工艺分析
总结词
目的与内容
详细描述
工艺分析是对零件的结构、材料、精 度、批量等进行全面分析,确定加工 方法、加工设备和工艺装备等,以保 证零件的加工质量和生产效率。
毛坯的选择与确定
总结词
原则与依据
详细描述
毛坯的选择与确定是工艺规程制定的重要环节,应根据零件的材料、结构、尺寸、批量 、生产条件等综合考虑,选择合适的毛坯类型和制造方法,以满足零件的加工要求和提
工艺过程
机械制造工艺是将原材料转化为成品 的过程,包括零件的加工、装配和检 测等环节。
机械制造
机械制造是以各种机械加工方法和设 备,制造出各种机器、设备和零件的 过程。
生产类型与工艺特点
生产类型
根据生产批量、产品品种和生产组织方式的不同,机械制造可分为单件生产、 成批生产和大量生产等类型。
工艺特点
切削用量选择是指在金属切削加工过程中,合理选择切削深度、切削宽度和切削速度等参数,以达到最佳的加工 效果。合理的切削用量选择可以提高加工效率,减少刀具磨损,降低生产成本。
PART 03
机械加工工艺规程制定
工艺规程的基本概念
总结词
定义与作用
详细描述
工艺规程是规定零件机械加工工艺过程和操作方法的工艺文件,是编制生产计划和在车间组织生产的 重要依据,它能够指导生产,提高生产效率。
- 1、下载文档前请自行甄别文档内容的完整性,平台不提供额外的编辑、内容补充、找答案等附加服务。
- 2、"仅部分预览"的文档,不可在线预览部分如存在完整性等问题,可反馈申请退款(可完整预览的文档不适用该条件!)。
- 3、如文档侵犯您的权益,请联系客服反馈,我们会尽快为您处理(人工客服工作时间:9:00-18:30)。
5.数控工序与非数控工序间的衔接
有些工件的加工是由普通机床和数控机床共同完成 的,数控机床加工工序一般穿插在整个工艺过程之间, 应注意解决好数控工序与非数控工序间的衔接。如作为 定位基准的孔和面的精度是否满足要求,后道工序的加 工余量是否足够等。
第四节 选择毛坯和确定工序尺寸
一、毛坯选择
1.毛坯的种类
(3)选择的定位基准,应使设计的夹具结构简单、工件 装卸和夹紧方便。
2.定位基准的分类
粗基准——在最初的切削工序中,只能使用毛 坯上未经加工的表面来定位,也称作毛基准 。
精基准——在后序的各工序中,采用已加工表 面作为定位基准表面。
3.粗基准的选择
(1)对于不需加工全部表面的零件,应采用始终不 加工的表面作为粗基准。
(5)进给
一次进给——在一个工步中,若所需切去的金属层 很厚,可以分几次切削,每一次切削称为一次进给。
3.生产过程与工艺过程
生产过程与工艺过程的关系
二、生产纲领和生产类型
1.生产纲领
工件的生产纲领主要是指包括备品与废品在内的年 产量。它根据市场需求量与本企业的生产能力来确定。
2.生产类型
生产类型——企业生产专业化程度 的分类。
选择不加工表面作粗基准
用相互位置精度要求高的不加工表面作粗基准
(2)选取加工余量要求均匀的表面作为粗基准。
(3)对于所有表面都 需要加工的零件,应选择 加工余量最小的表面作为 粗基准,这样可以避免因 加工余量不足而造成废品。
(4)选择毛坯制造中尺寸和位置可靠、稳定、平整、 光洁,面积足够大的表面作为粗基准,这样可以减小定 位误差和使工件装夹可靠稳定。
除工艺需要的表面处理(如工件非渗碳表面的保护 性镀铜、非氮化表面的保护性镀锡和镀镍等)视工艺要 求而定以外,一般表面处理工序都安排在工艺过程的最 后。
4.检验工序的安排
(1)在下列情况下安排中间检验工序: 1)工件从一个车间转到另一车间前。 2)重要工件的关键工序加工后。 (2)特种检验主要指无损探伤,此外还有密封性检 验、流量检验、称重检验等。 (3)最终检验工序安排在零件表面全部加工完之后。
第一节 机械加工工艺过程的组成和特征
一、生产过程与工艺过程
1.生产过程
生产过程——将原材料转变为成品的全过程。
2.工艺过程
工艺过程——在生产过程中,直接改变原材料(或毛坯) 形状、尺寸和性能,使之变为成品或半成品的过程。
Hale Waihona Puke (1)工序 工序——一个或一组工人,在一个工作地点对一个 或一组工件所连续完成的那部分工艺过程。 工序是工艺过程的基本组成部分。
(2)安装 安装——工件装卸一次所完成的那部分工作。应尽可 能减少工件装夹次数,以节省装卸工件的辅助时间。 (3)工位 工位——在一次安装中,工件在 机床或夹具占据的每个加工位置上所 完成的那一部分工艺工程。
多任务位加工
(4)工步 工步——在一个工序中,加工表面、刀具、转速和 进给量都不变时所完成的那部分工作。
(2)工序分散的特点 工序内容单一,可采用比较简单的机床设备和工艺
装备,调整容易。 对操作工人的技术水平要求低。 生产准备工作量小,变换产品容易。 机床设备数量多,工人数量多,生产面积大。 由于工序数目增多,工件在工艺过程中装卸次数
多,对保证工件表面之间较高的相对位置精度不利。
(3)测量基准
测量基准——测量时所采用的基准。测量基准是 据以测量已加工表面位置的点、线、面。
二、定位基准的选择
1.定位基准选择的基本原则
(1)应保证定位基准的稳定性和可靠性,以确保工件表 面之间相互位置的精度。
(2)力求与设计基准重合,也就是尽可能地从相互间有 直接位置精度要求的表面中选择定位基准,以避免因基准不 重合而引起的误差。
有利于消除或减小变形对加工精度的影响。 可尽早发现毛坯的缺陷。 有利于合理地选择和使用设备。 有种于合理组织生产和工艺布置。
三、工序的集中与分散
工序集中——在一道工序中尽可能多地包含加工内 容,而使工艺过程中总的工序数目减少。集中到极限时, 工艺过程只有一道工序,这道工序就能把工件加工到图 样规定的要求。
1.常见表面的加工方案
外圆表面加工方案 孔加工方案 平面加工方案
2.选择表面加工方法考虑要点
(1)确定加工方法及分几次加工。 (2)考虑被加工材料的性质。 (3)根据生产类型,考虑生产率和经济性等问题。 (4)根据本企业(或本车间)的现有设备情况和 技术水平,充分利用现有设备,挖掘企业潜力。
二、加工阶段的划分
铸件 锻件 型材 焊接件 冷冲压件 其他
2、选择毛坯应考虑的因素
工件的材料及其物理和力学性能。 工件的结构形状及其外形尺寸。 生产规模的大小。 工厂现场生产条件。
二、加工余量的确定
1.加工余量的基本概念
加工余量分工序余量和总余量。总余量等于该加 工表面各工序余量之总和。
主要设计基准
2.工艺基准
工艺基准——工艺过程中所采用的基准。
工序基准 定位基准 测量基准
(1)工序基准
工序基准——在工序图上用来确定本工序所加工表 面加工后的尺寸、形状、位置的基准。
(2)定位基准
定位基准——在加工中 用作定位的基准。定位基准 用来确定工件在机床上或夹 具中的正确位置。
单件生产 成批生产 大量生产
第二节 定位基准的选择
一、基准及其分类
基准——用来确定生产对象上几何要素间的几何关系 的那些点、线、面,是几何要素之间位置尺寸标注、计算 和测量的起点。
设计基准 工艺基准
1.设计基准
设计基准——设计图样上所采用的基准。
在设计图样上,以设 计基准为依据,标出一定 的尺寸或相互位置要求。
(2)毛坯尺寸公差按照毛坯制造方法或根据所选 型材的品种规格确定。
(3)中间工序的公差一般按照该工序加工方法的 经济加工精度确定。
第五节 生产工艺卡
一、机械加工工艺规程
机械加工工艺规程——规定工件机械加工工艺过程和 操作方法等的工艺文件。
工艺过程综合卡 机械加工工艺卡 机械加工工序卡
二、识读机械加工工艺规程
2.影响加工余量的因素
前工序(或毛坯)表面的加工痕迹和缺陷层。 前工序的尺寸公差。 前工序的相互位置公差。 本工序加工时的安装误差。 热处理变形量。 工序的特殊要求。
3.确定加工余量的方法
分析计算法 查表修正法 经验估算法
二、工序尺寸及其公差的确定
1.工序尺寸的确定
4.精基准的选择
基准重合原则 基准统一原则 互为基准原则 自为基准原则 基准不重合误
差最小条件
车床主轴箱工序简图 工艺尺寸链
基准不重合误差最小条件
5.辅助定位基准
涡轮叶片的辅助定位基准
第三节 工艺路线的拟定
一、表面加工方法的选择
选择加工方法一般根据工件的经济精度和表面粗糙度 来考虑。
2.工序集中与分散的选择
(1)一般情况下,单件、小批量生产采用工序集中 原则,而大批量生产可采取工序集中原则,也可采取工 序分散原则。
(2)单件、小批量生产是在通用设备上主要使用通 用工具进行加工;大批、大量生产采则必须采用高效专 用设备,自动、半自动机床,组合机床等进行加工。
(3)应多采用工序集中原则来制定工艺过程和组织 生产。
工序分散——使整个工艺过程的工序数目增多,而 每道工序的加工内容尽可能减少。分散到极限时,一道 工序中只包含一个简单工步的内容。
1.工序集中与工序分散的特点
(1)工序集中的特点
减少了工序数目、简化了工艺路线,缩短了生 产周期。
减少了机床设备、操作工人和生产面积。 容易保证有关工件表面之间的相互位置精度。 大大提高劳动生产率。 对调试、维修工人的技术水平要求高。
粗加工阶段:切除工件各加工表面的大部分余量。在 粗加工阶段,主要的问题是如何提高生产率。
半精加工阶段:达到一定的准确度要求,完成次要表 面的最终加工,并为主要表面的精加工作好准备。
精加工阶段:完成各主要表面的最终加工,使工件的 加工精度和加工表面质量达到图样规定的要求。
2.划分加工阶段的作用
1.识读机械加工工艺卡
识读表头。 识读毛坯信息。 识读加工工艺过程。 各表面加工方案。 机床和工艺装备。 工时定额。
传动齿轮的机械加工工艺卡
传动齿轮
2.识读机械加工工序卡
识读表头。 识读工序简图。 识读工步内容和要求。 识读设备和工艺装备。 识读工艺参数。
机械加工工序卡
工序余量——某表面在一道工序中所切除的材料 层厚度。工序余量也就是同一表面相邻的前后工序尺 寸之差。
基本余量——按照基本尺寸计算出的工序余量。
外表面:z = a-b
内表面:z = b-a
计算工序余量,有外表面和内表面之分。
工序余量要注意单面余量与双面余量之分。
回转表面的工序基本余量 a)轴加工 b)孔加工
(1)被加工表面的最终工序的工序尺寸及公差, 在一般情形下可直接按工件图样规定的尺寸和公差确定。
(2)中间各工序的工序尺寸,由工件图样规定的 尺寸,根据工序余量的大小采用“由后向前”推算的方 法确定,一直推算到毛坯尺寸。
2.工序尺寸公差的确定
(1)最终工序的公差,当工序基准与设计基准重 合时,一般就是工件图样规定的尺寸公差。
四、加工顺序的确定
1.机械加工顺序的安排
先粗后精 先基面后其他表面 先主后次
2.热处理工序的安排
取决于工件的材料和热处理的目的及要求。 目的:提高材料的力学性能(强度、硬度等),改 善材料的切削加工性,消除内应力以及为后继热处理作 组织准备等。
3.表面处理工序的安排
主要目的和作用:提高工件的抗蚀能力,提高工件 的耐磨性,增加工件的导电率和作为一些工序的准备工 序。