汽车制动器设计设计项目计划书
制动器总成项目方案

制动器总成项目方案一、项目背景和目标制动器是汽车中非常重要的安全部件之一,对汽车的制动效果和安全性能有直接影响。
本项目旨在开发一种高性能的制动器总成,提升汽车的制动效果和安全性能。
二、项目内容和范围1.项目名称:制动器总成项目2.项目范围:开发并生产制动器总成3.项目目标:提升汽车的制动效果和安全性能三、项目计划和时间安排1.项目启动:确定项目组成员,明确项目目标和计划2.市场调研:调研汽车市场需求,了解竞争对手产品3.技术研发:进行制动器总成的技术研发,包括制动系统、制动盘、制动片等关键技术4.检验测试:对制动器总成进行检验和测试,确保产品符合相关标准和要求5.生产准备:准备生产所需的设备、材料和人力资源6.生产组织:组织生产制动器总成7.市场推广:进行市场推广,推动制动器总成的销售四、项目组织和责任分工1.项目组长:负责项目的整体管理和协调工作2.技术人员:负责制动器总成的技术研发和测试工作3.生产人员:负责制动器总成的生产组织和生产准备工作4.市场人员:负责市场调研和推广工作5.财务人员:负责项目的财务管理和预算控制五、项目进度和风险管理1.项目进度:根据项目计划和时间安排,制定详细的里程碑和工作计划,及时跟踪项目进展情况并进行调整。
2.风险管理:对项目中的各种风险进行评估和管理,制定相应的应对措施,确保项目顺利进行。
六、项目投资和资金需求1.项目投资:确定项目的总投资额和资金计划2.资金需求:根据项目进度和需要,及时申请所需的资金,确保项目正常进行。
七、项目成果和效益评估1.项目成果:生产出高性能的制动器总成,并推向市场2.效益评估:根据市场销售情况和用户反馈,评估项目的效益和经济效果八、项目总结和展望1.项目总结:总结项目的经验和教训,总结项目成果和经济效果2.展望未来:为下一阶段的项目发展提出建议和展望,并规划下一阶段的发展目标和计划。
以上是制动器总成项目方案的基本内容,详细展开每个步骤,按时间顺序进行详细规划和具体安排,确保项目能够顺利进行并取得成功。
汽车磐石制动器设计项目计划书
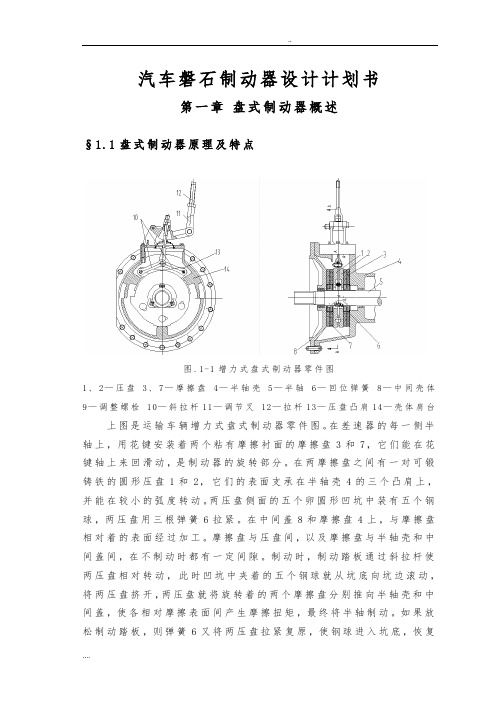
汽车磐石制动器设计计划书第一章盘式制动器概述§1.1盘式制动器原理及特点图.1-1增力式盘式制动器零件图1、2—压盘3、7—摩擦盘4—半轴壳5—半轴6—回位弹簧8—中间壳体9—调整螺栓 10—斜拉杆11—调节叉 12—拉杆13—压盘凸肩14—壳体肩台上图是运输车辆增力式盘式制动器零件图。
在差速器的每一侧半轴上,用花键安装着两个粘有摩擦衬面的摩擦盘3和7,它们能在花键轴上来回滑动,是制动器的旋转部分。
在两摩擦盘之间有一对可锻铸铁的圆形压盘1和2,它们的表面支承在半轴壳4的三个凸肩上,并能在较小的弧度转动。
两压盘侧面的五个卵圆形凹坑中装有五个钢球,两压盘用三根弹簧6拉紧。
在中间盖8和摩擦盘4上,与摩擦盘相对着的表面经过加工。
摩擦盘与压盘间,以及摩擦盘与半轴壳和中间盖间,在不制动时都有一定间隙。
制动时,制动踏板通过斜拉杆使两压盘相对转动,此时凹坑中夹着的五个钢球就从坑底向坑边滚动,将两压盘挤开,两压盘就将旋转着的两个摩擦盘分别推向半轴壳和中间盖,使各相对摩擦表面间产生摩擦扭矩,最终将半轴制动。
如果放松制动踏板,则弹簧6又将两压盘拉紧复原,使钢球进入坑底,恢复了摩擦盘两侧的间隙。
盘式制动器在上述制动过程中有增力作用。
当摩擦盘顺时针旋转时;作用在压盘上的摩擦扭矩将使它们跟随旋转,但当压盘1由于其凸起13受到半轴壳上的凸肩14的限制而不能转动时,压盘2则在摩擦扭矩的作用下将相对于压盘1作顺时针转动,协助钢球继续将两压盘挤开,使操纵省力。
当摩擦盘反时针旋转时,和上述过程相似地起增力作用。
因此不管运输车辆前进还是倒退,制动时盘式制动器都有增力作用。
与带式和蹄式制动器相比,盘式制动器除了结构复杂外有一系列优点:如结构紧凑,操纵省力,制动效果好,衬面磨损较均匀,间隙不需调整,封闭性好不易进泥水,且散热容易,故使用寿命较长等。
这些特点使它得到越来越广泛的应用。
§1.2 盘式制动器的主要元件§1.2.1制动盘一、制动盘直径D制动盘直径D应尽可能取大些,这时制动盘的有效半径得到增加,可以降低制动钳的夹紧力,减少衬块的单位压力和工作温度。
制动系统项目规划方案设计

制动系统项目规划方案设计1. 项目背景制动系统是汽车关键的安全装置之一,对于汽车的刹车性能和稳定性起着重要作用。
随着汽车行业的快速发展,制动系统技术也在不断进步和创新,为了满足市场需求,开展本次制动系统项目。
2. 项目目标本项目的目标是设计一个高性能、稳定可靠的制动系统。
具体目标如下:1. 提高汽车刹车性能,实现更短的制动距离;2. 提高制动系统的可靠性,减少制动故障的发生概率;3. 降低制动系统的成本,提高制动系统的性价比;4. 增加制动系统的功能,满足用户的个性化需求。
3. 项目内容本项目主要包括以下工作内容:1. 系统需求分析:对制动系统的功能和性能进行详细的分析和描述,明确项目的需求目标;2. 技术研究和方案设计:通过对国内外相关技术和方案的研究,设计出适合本项目需求的制动系统解决方案;3. 软硬件开发:根据项目需求,进行软硬件的开发工作,包括电子控制单元(ECU)开发、传感器的设计和制造等;4. 系统集成和测试:对开发完成的软硬件进行集成,进行系统测试,验证系统的性能和可靠性;5. 项目管理和技术支持:进行项目进度管理,确保项目按计划进行,同时提供技术支持和服务,保证项目顺利实施。
4. 项目计划根据以上的项目内容,制定了如下的项目计划:项目阶段开始日期结束日期系统需求分析2022年10月1日2022年10月31日技术研究和方案设计2022年11月1日2022年12月31日软硬件开发2023年1月1日2023年3月31日系统集成和测试2023年4月1日2023年5月31日项目管理和技术支持2023年6月1日2023年12月31日5. 项目风险与控制在项目实施过程中,可能会面临以下风险:1. 技术风险:对于一些新的技术和方案,可能存在技术实施风险,需要进行充分的技术研究和风险评估;2. 人力资源风险:项目所需的人力资源可能存在不足或者能力不匹配的问题,需要进行合理的人员配备和培训;3. 进度风险:项目实施过程中,可能会受到各种因素的影响,导致项目进度延误,需要进行进度的及时控制和跟踪。
制动器总成项目方案
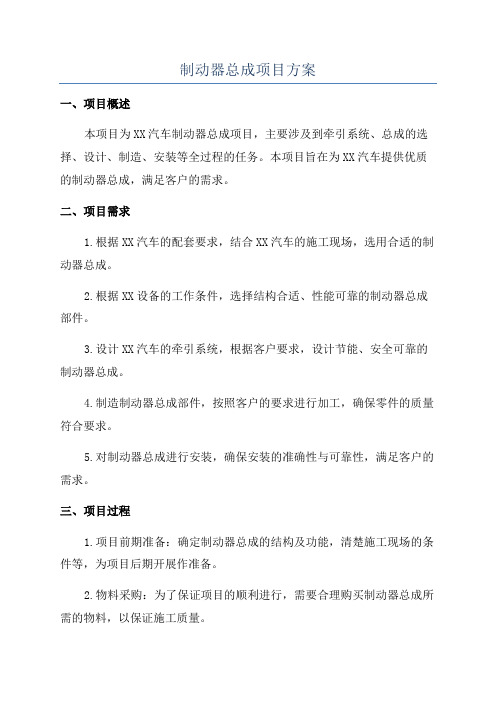
制动器总成项目方案
一、项目概述
本项目为XX汽车制动器总成项目,主要涉及到牵引系统、总成的选择、设计、制造、安装等全过程的任务。
本项目旨在为XX汽车提供优质的制动器总成,满足客户的需求。
二、项目需求
1.根据XX汽车的配套要求,结合XX汽车的施工现场,选用合适的制动器总成。
2.根据XX设备的工作条件,选择结构合适、性能可靠的制动器总成部件。
3.设计XX汽车的牵引系统,根据客户要求,设计节能、安全可靠的制动器总成。
4.制造制动器总成部件,按照客户的要求进行加工,确保零件的质量符合要求。
5.对制动器总成进行安装,确保安装的准确性与可靠性,满足客户的需求。
三、项目过程
1.项目前期准备:确定制动器总成的结构及功能,清楚施工现场的条件等,为项目后期开展作准备。
2.物料采购:为了保证项目的顺利进行,需要合理购买制动器总成所需的物料,以保证施工质量。
3.设计制动器总成:根据客户的需求,结合XX汽车的牵引系统,设计出优质、安全可靠的制动器总成部件。
4.制作制动器总成:按照客户的要求,优先采用机加工的方式,对零件进行精密加工,以保证零件的质量、安装准确性与可靠性。
汽车制动器设计设计项目计划书

汽车制动器设计设计项⽬计划书汽车制动器设计设计计划书⼀、设计任务书题⽬:已知条件:(1)假设地⾯的附着系数⾜够⼤;(2)车重2.2t(3)前后重量分配:40%,60%(4)蹄、盘正压⼒的分布状态可由⾃⾏假设(5)轮胎型号195/80R14(6)制动初速度100km/h(7)最⼤急刹车距离为18m(8)⼯作环境:设定为⾼温状态(9)制动摩擦系数取值围:0.25≤f≤0.55(10制动器具体结构可参考汽车实验室相关制动器结构,也⾃⾏设计。
前后轮重量分配⽰意图⼆、制动⽅案的拟定汽车制动系是⽤以强制⾏驶中的汽车减速或停车、使下坡⾏驶的汽车车速保持稳定以及使已停驶的汽车在原地(包括在斜坡上)驻留不动的。
随着⾼速公路的迅速发展和车速的提⾼以及车流密度的⽇益增⼤,为了保证⾏车安全,汽车制动系的⼯作可靠性显得⽇益重要。
也只有制动性能良好、制动系⼯作可靠的汽车,才能充分发挥其动⼒性能。
汽车制动系⾄少应有两套独⽴的制动装置,即⾏车制动装置和驻车制动装置;重型汽车或经常在⼭区⾏驶的汽车要增设应急制动装置及辅助制动装置;牵引汽车应有⾃动制动装置。
任何⼀套制动装置均由制动器和制动驱动两部分组成。
制动器有⿎式与盘式之分。
⾏车制动是⽤脚踩下制动踏板操纵车轮制动器来制动全部车轮,⽽驻车制动则多采⽤⼿制动杆操纵,且具有专门的中央制动器或利⽤车轮制动器进⾏制动。
中央制动器位于变速器之后的传动系中,⽤于制动变速器第⼆轴或传动轴。
⾏车制动和驻车制动这两套制动装置必须具有独⽴的制动驱动。
⾏车制动装置的驱动,分液压和⽓压两种型式。
⽤液压传递操纵⼒时还应有制动主缸和制动轮缸以及管路;⽤⽓压操纵时还应有空⽓压缩机、⽓路管道、贮⽓筒、控制阀和制动⽓室等。
过去,⼤多数汽车的驻车制动和应急制动都使⽤中央制动器,其优点是制动位于主减速器之前的变速器第⼆轴或传动轴的制动⼒矩较⼩,容易满⾜操纵⼿⼒⼩的要求。
但在⽤作应急制动时,往往使传动轴超载。
现代汽车由于车速提⾼,对应急制动的可靠性要求更严,因此,在中、⾼级轿车和部分总质量在1.5t以下的载货汽车上,多在后轮制动器上附加⼿操纵的机械式驱动,使之兼起驻车制动和应急制动的作⽤,从⽽取消了中央制动器。
- 1、下载文档前请自行甄别文档内容的完整性,平台不提供额外的编辑、内容补充、找答案等附加服务。
- 2、"仅部分预览"的文档,不可在线预览部分如存在完整性等问题,可反馈申请退款(可完整预览的文档不适用该条件!)。
- 3、如文档侵犯您的权益,请联系客服反馈,我们会尽快为您处理(人工客服工作时间:9:00-18:30)。
汽车制动器设计设计计划书一、设计任务书题目:已知条件:(1)假设地面的附着系数足够大;(2)车重2.2t(3)前后重量分配:40%,60%(4)蹄、盘正压力的分布状态可由自行假设(5)轮胎型号195/80R14(6)制动初速度100km/h(7)最大急刹车距离为18m(8)工作环境:设定为高温状态(9)制动摩擦系数取值范围:0.25≤f≤0.55(10制动器具体结构可参考汽车实验室相关制动器结构,也自行设计。
前后轮重量分配示意图二、制动方案的拟定汽车制动系是用以强制行驶中的汽车减速或停车、使下坡行驶的汽车车速保持稳定以及使已停驶的汽车在原地(包括在斜坡上)驻留不动的机构。
随着高速公路的迅速发展和车速的提高以及车流密度的日益增大,为了保证行车安全,汽车制动系的工作可靠性显得日益重要。
也只有制动性能良好、制动系工作可靠的汽车,才能充分发挥其动力性能。
汽车制动系至少应有两套独立的制动装置,即行车制动装置和驻车制动装置;重型汽车或经常在山区行驶的汽车要增设应急制动装置及辅助制动装置;牵引汽车应有自动制动装置。
任何一套制动装置均由制动器和制动驱动机构两部分组成。
制动器有鼓式与盘式之分。
行车制动是用脚踩下制动踏板操纵车轮制动器来制动全部车轮,而驻车制动则多采用手制动杆操纵,且具有专门的中央制动器或利用车轮制动器进行制动。
中央制动器位于变速器之后的传动系中,用于制动变速器第二轴或传动轴。
行车制动和驻车制动这两套制动装置必须具有独立的制动驱动机构。
行车制动装置的驱动机构,分液压和气压两种型式。
用液压传递操纵力时还应有制动主缸和制动轮缸以及管路;用气压操纵时还应有空气压缩机、气路管道、贮气筒、控制阀和制动气室等。
过去,大多数汽车的驻车制动和应急制动都使用中央制动器,其优点是制动位于主减速器之前的变速器第二轴或传动轴的制动力矩较小,容易满足操纵手力小的要求。
但在用作应急制动时,往往使传动轴超载。
现代汽车由于车速提高,对应急制动的可靠性要求更严,因此,在中、高级轿车和部分总质量在1.5t以下的载货汽车上,多在后轮制动器上附加手操纵的机械式驱动机构,使之兼起驻车制动和应急制动的作用,从而取消了中央制动器。
汽车制动系设计的程序1. 设计的前提条件(1)汽车的参数汽车的满载质量、自重以及满载和空载时的前、后轴负荷及重心高度,还有轴和轮胎尺寸。
(2)法规适合性决定制动系统、构造和参数的最低要求是适合指定的法规。
根据上述两项最基本的前提条件,再加上市场的需求、使用条件、竞争性及本司现生产情况确定设计方向。
2. 制动操纵方式和制动系统的确定(1)研究、确定制动控制采用气压方式还是液压(真空助力、真空增压或油气混合)方式(2)研究、确定制动系统的构成①行车制动系统所采用双回路或多回路,应由那些部件构成,这些部件是现有的还是需要选购或新设计,设计制动系统示意图。
②驻车制动采用中央制动器还是作用后轮(机械操纵还是弹簧制动缸)。
③应急制动的操纵是与行车制动或驻车制动结合,还是独立操纵。
④是否需要有辅助制动,采用排气制动、液力缓速器或电涡流缓速器(3)汽车必需制动力及其前后分配的确定前提条件一经确定,与前项的系统的研究、确定的同时,研究汽车必需的制动力并把它们适当地分配到前后轴上,确定每个车轮制动器必需的制动力。
此外,还应研究、确定汽车必需的驻车制动力和应急制动力。
(4)确定制动器制动力、摩擦片寿命及构造、参数制动器必需制动力求出后,考虑摩擦片寿命和由轮胎尺寸等所限制的空间,选定制动器的型式、构造和参数,绘制布置图,进行制动力制动力矩计算、摩擦磨损计算。
(5)制动器零件设计零件设计、材料、强度、耐久性及装配性等的研究确定,进行工作图设计。
(6)制动操纵系统设计制动系操纵部件(阀类、加力器、制动气室等)的研究、选定或设计,操纵机构设计;注意性能(操纵力和行程、制动系统静特性和动特性)、强度、耐久性及车辆装配性等。
(7)管路设计管路布置、设计。
三、各种形式制动器现状比较汽车制动器按其在汽车上的位置分为车轮制动器和中央制动器,前者是安装在车轮处,后者则安装在传动系的某轴上,例如变速器第二轴的后端或传动轴的前端。
摩擦式制动器按其旋转元件的形状又可分为鼓式和盘式两大类。
鼓式制动器又分为内张型鼓式制动器和外束型鼓式制动器。
内张型鼓式制动器的固定摩擦元件是一对带有摩擦蹄片的制动蹄,后者又安装在制动底板上,而制动底板则又紧固于前梁或后桥壳的突缘上(对车轮制动器)或变速器壳或与其相固定的支架上(对中央制动器);其旋转摩擦元件为固定在轮毂上或变速器第二轴后端的制动鼓,并利用制动鼓的圆柱内表面与制动蹄摩擦片的外表面作为一对摩擦表面在制动鼓上产生摩擦力矩,故又称为蹄式制动器。
外束型鼓式制动器的固定摩擦元件是带有摩擦片且刚度较小的制动带;其旋转摩擦元件为制动鼓,并利用制动鼓的外圆柱表面和制动带摩擦片的内圆弧面作为一对摩擦表面,产生摩擦力矩作用于制动鼓,故又称为带式制动器。
在汽车制动系中,带式制动器曾仅用作某些汽车的中央制动器,现代汽车已很少采用。
由于外束型鼓式制动器通常简称为带式制动器,而且在汽车上已很少采用,所以内张型鼓式制动器通常简称为鼓式制动器,而通常所说的鼓式制动器即是指这种内张型鼓式结构。
盘式制动器的旋转元件是一个垂直安放且以两侧表面为工作面的制动盘,其固定摩擦元件一般是位于制动盘两侧并带有摩擦片的制动块。
制动时,当制动盘被两侧的制动块夹紧时,摩擦表面便产生作用与制动盘上的摩擦力矩。
盘式制动器常用作轿车的车轮制动器,也可用作各种汽车的中央制动器。
按摩擦副中的固定摩擦元件的结构来分析,盘式制动器可分为钳盘式和全盘式制动器两大类,本次课程设计为定钳盘式制动器。
定钳盘式制动器的制动钳固定安装在轿车上,既不能旋转,也不能沿制动盘轴线方向移动,因而其中必须在制动盘两侧都装设制动快触动装置(例如相当于制动轮缸的油缸),以便分别将两侧的制动快压向制动盘。
四、整个传动系统运动和动力参数的选择与计算鼓式制动器主要参数的确定1.制动鼓内径D输入离F0一定时,制动鼓内径越大,制动力矩越大,且散热能力越强。
但D的增大(图1-1)受轮辋内径的限制。
制动鼓与轮辋之间应保持足够大的间隙,通常要求该间隙不小于20mm,否则不仅制动鼓散热条件差,而且轮辋受热后可能粘住内胎或烤坏气门嘴。
制动鼓应有足够的壁厚,用来保证有较大的刚度和热容量,以减少制动时的升温,制动鼓的直径小,刚度就大,并有利于保证制动鼓的加工精度。
制动鼓的直径与轮辋直径之比D/D r的范围如下:乘用车 D/D r = 0.64 ~ 0.74商用车 D/D r = 0.70 ~ 0.83制动鼓内径尺寸应参照专业标准QC/T309—1999《制动鼓工作直径及制动蹄片宽度尺寸系列》选取。
本次规定的轮胎型号为195/80R14,轮辋直径为355.6mm,所以根据QC/T309—1999《制动鼓工作直径及制动蹄片宽度尺寸系列》选取制动鼓直径为125mm蹄片宽度B为60mm2.摩擦衬片宽度b和包角β摩擦衬片宽度尺寸b的选取对摩擦衬片的使用寿命有影响。
衬片的宽度尺寸取窄些,则磨损速度快,衬片寿命短;若衬片宽度尺寸取宽些,则质量大不易加工,且增加了成本。
制动鼓半径R确定后,衬片的摩擦面积为A p = Rβb。
制动器各蹄衬片总的摩擦面积ΣA p越大,制动时所受单位面积的正压力和能量负荷越小,从而磨损特性越好。
根据国外统计资料分析,单个车轮鼓式制动器的衬片面积随汽车总质量的增大而增大,具体数据见表1-1。
试验表明,摩擦衬片包角β=90°~ 100°时,磨损最小,制动鼓温度最低,且制动效能最高。
β角减小虽然有利于散热,但单位压力过高将加速磨损。
实际上包角两端处的单位压力最小,因此过分延伸衬片两端以加大包角对减小压力的作用不大,而且将使制动作用不平顺,容易使制动器发生自锁。
因此包角一般不宜大于120°。
考虑到磨损以及合适的摩擦片面积选用的摩擦衬片的包角β= 90°;摩擦衬片宽度为60mm。
3.摩擦衬片起始角β0一般将衬片不知在制动蹄的中央,即令β0= 90°-β/2。
有时为了适应单位压力的分布情况,将衬片相对于最大压力点对称布置,以改善磨损均匀性与制动效能。
因为β= 90°所以β0 = 45°。
4.制动器中心到张开力F0作用线的距离e在保证轮缸或制动凸轮能够布置于制动鼓内的条件下,应使距离e(图1-1)尽可能增大以提高制动效能。
初步设计时可暂定e = 0.8R左右。
5.制动蹄支撑点位置坐标a和c应在保证两蹄支撑端毛面不致相互干涉的条件下,使a尽可能大而c尽可能小(图1-1)。
初步设计时也可暂定a = 0.8R左右。
根据设计要求,设定e = 0.8R,a = 0.8R,c = 0.3R鼓式制动器的设计计算根据此次设计要求,需要设计的是一个车重2.2t,后重量分配为40%、60%轮胎型号为195/80R14,当时速为100km/h时,最大紧急刹车距离为18m。
所以根据公式2as = v2- u2算得汽车的最大加速度为21.5m/s2。
而其中一个前轮分配到的重量为440kg(不计人的重量)。
所以要想制动,根据F = ma摩擦衬片施加在制动鼓上的摩擦力为9460N。
而摩擦因数f为0.35,所以施加在摩擦片上的法向合力为27028N。
由表1-1得,选取A=200 cm 2设P=2XP=⎰⎰=xxxdx pdx 002 又P.S=N ⇒X 2.S=N X=S N /=11.62pa所以Pmax=2X=23.24paNmax=Pmax.S=4648N因为摩擦片压强范围为40~90Pa⇒取50Pa⇒Pmax 1=50paNmax 1= Pmax 1.S=10000N1m ax m ax N N < ∴摩擦片可用衬片磨损特性的计算摩擦衬片(衬块)的磨损,与摩擦副的材质、表面加工情况、温度、压力以及相对滑磨速度等多种因素有关,因此在理论上要精确计算磨损性能是困难的。
但试验表明,摩擦表面的温度、压力、摩擦系数和表面状态等是影响磨损的重要因素。
汽车的制动过程是将其机械能(动能、势能)的一部分转变为热量而耗散的过程。
在制动强度很大的紧急制动过程中,制动器几乎承担了耗散汽车全部动力的任务。
此时由于在短时间内热量来不及逸散到大气中,致使制动器温度升高。
此即所谓制动器的能量负荷。
能量负荷愈大,则衬片(衬块)的磨损愈严重。
制动器的能量负荷常以其比能量耗散率作为评价指标。
比能量耗散率又称为单位功负荷或能量负荷,它表示单位摩擦面积在单位时间内耗散的能量,其单位为W /mm 2。
双轴汽车的单个前轮制动器和单个后轮制动器的比能量耗散率分别为βδ1222112)(21tA v v m e a -= )1(2)(21222212βδ--=tA v v m e a(1-13)jv v t 21-=式中 δ——汽车回转质量换算系数;a m ——汽车总质量;1v ,2v ——汽车制动初速度与终速度,m /s ;计算时轿车取1001=v km/h(27.8m/s);总质量3.5t 以下的货车取1v =80km/h(22.2m/s);总质量3.5t 以上的 货车取1v =65km /h(18m /s);j ——制动减速度,m /s 2,计算时取j=0.6g ;t ——制动时间,s ;A l ,A 2——前、后制动器衬片(衬块)的摩擦面积;β——制动力分配系数。