粉末喷涂工艺培训
粉末喷枪培训(二)2024

粉末喷枪培训(二)引言概述:粉末喷枪培训是针对使用粉末喷涂设备的操作人员而设计的专业培训课程。
本次培训是粉末喷枪培训的第二部分,旨在进一步了解和掌握粉末喷涂技术的操作和安全要点。
本文将围绕五个大点进行详细讲解,其中每个大点将包含五到九个小点,以便更好地理解和应用粉末喷枪培训的知识。
正文:一、粉末喷涂设备维护1.定期检查喷涂设备,确保其正常运行。
2.清洁喷枪喷嘴以保持喷涂质量。
3.检查粉末收集系统,确保其无堵塞。
4.调整压力和电流,以适应不同的喷涂工件。
5.正确存储粉末,防止潮湿和污染。
二、喷涂技术要点1.掌握正确的喷涂距离和喷射角度。
2.了解不同粉末的喷涂特性和适用范围。
3.喷涂前准备,如清理和准备工件表面。
4.粉末喷涂层的厚度控制和均匀性评估。
5.了解喷涂设备的操作要点,如开关控制和喷涂速度。
三、安全操作指南1.正确佩戴个人防护设备,如手套、眼镜和面具。
2.了解粉末喷涂设备的安全操作程序。
3.防止粉尘爆炸的措施和预防措施。
4.紧急情况下的应急处理和撤离程序。
5.合理使用喷枪的电能,确保电击和火灾的安全。
四、常见问题和解决方案1.喷涂质量不理想的常见原因和处理方法。
2.粉末堆积和堵塞的预防和解决方法。
3.喷涂过程中的意外情况应对措施。
4.粉末喷涂设备故障排除和维修要点。
5.相关规范和标准的参考资料和指导。
五、粉末喷涂技术的应用领域1.汽车工业中的粉末喷涂应用。
2.电子行业中的粉末喷涂应用。
3.家具制造业中的粉末喷涂应用。
4.建筑行业中的粉末喷涂应用。
5.其他行业中的粉末喷涂应用前景和发展趋势。
总结:通过学习本次粉末喷枪培训的内容,操作人员将能够更好地掌握粉末喷涂设备的维护和操作技巧。
同时,他们还将了解到粉末喷涂的应用领域以及相关的安全要点,以确保在工作中能够高效、安全地使用粉末喷枪。
希望本文对于粉末喷枪培训的学习和实践有所帮助。
喷粉车间培训教材

喷粉车间培训教材简介喷粉车间是一种常见的粉末涂装工艺,广泛应用于各种制造业中。
本教材将介绍喷粉车间的基本工作原理、操作流程、设备介绍、安全注意事项等内容,以帮助读者了解和掌握喷粉车间的相关知识。
基本工作原理喷粉车间通过将粉末涂料喷射到工件表面,使其在烤箱中进行固化,形成坚固的涂层。
这一过程包括以下几个步骤:1.准备工件:将需要涂装的工件进行清洁和预处理,以确保涂层能够牢固地附着在工件表面。
2.涂粉:将粉末涂料通过喷枪均匀地喷射到工件表面。
喷粉时需要注意喷枪与工件的距离和角度,以获得均匀的涂层。
3.固化:将喷粉后的工件放入烤箱,进行高温固化。
在固化过程中,涂料会熔化并流平,形成坚固的涂层。
4.检查和包装:将固化后的工件进行检查,确保涂层质量符合要求。
然后进行包装,以保护工件表面不受损。
操作流程以下是喷粉车间的常见操作流程:1.准备工件–清洁工件表面,去除油污和杂质。
–进行必要的表面预处理,如喷砂或磨砂。
2.准备涂粉设备–检查喷粉设备的工作状态,如压力和喷嘴是否正常。
–确保喷粉室内的环境清洁,避免杂质进入喷粉涂料。
3.涂粉操作–调整喷粉枪与工件的距离和角度,以获得均匀的喷粉效果。
–控制喷粉厚度,根据工件要求进行调整。
–涂粉完成后,清洁喷粉设备,以避免堵塞或交叉污染。
4.烤箱固化–将喷粉后的工件放入烤箱,按照涂粉涂料的要求设置适当的温度和时间。
–控制烤箱内的温度和时间,确保涂层能够完全固化。
5.检查和包装–对固化后的工件进行视觉检查,确保涂层质量符合要求。
–进行必要的修复和改善,以提高涂层质量。
–对涂粉完成的工件进行包装,以防止表面受损。
设备介绍喷粉车间常见的设备包括以下几类:1.喷粉枪:用于将粉末涂料喷射到工件表面。
根据不同的喷粉要求,喷粉枪的种类和型号有所不同。
2.烤箱:用于固化喷粉后的工件。
烤箱通常具有可调节的温度和时间控制功能,可以根据涂粉涂料的要求进行设置。
3.气动输送系统:将粉末涂料从储存容器输送到喷粉枪。
粉末喷涂工艺培训
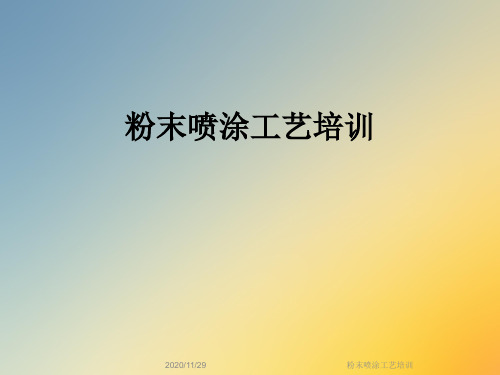
6.常见问题及解决办法
•6.1 缩孔 •产生原因
3.在制造粉末涂料 气中水分和油分离得 冷却辊太凉而凝结的
1.在制造粉末涂料过程中,流平剂、 4.,脱脂工序除油
消泡剂等助剂用量不够或者分散不均 表面比较粗糙的工件
匀 5.工件表面不平整,
2.由于粉碎机等设备清理不干净,而 麻坑
不同类型树脂粉末涂料之间相容性又
A、烘干的材料应为浅黄色到金黄色或略带彩红色,无挂粉、灰 无明显流痕;材料必须干燥、干净、无油污;
B、烘干后,材料应小心放在料车上,运至喷涂车间做后工序处 理,当天皮膜处理的型材当天喷涂,最长放置时间不许超过24 小时,且一定要用防尘布将其盖好。
C、前处理烘烤完成后到上架之前,皮膜处理的料不得用手直接 触摸,必须带干净手套后才能搬运。
• 5.7 吹料 • 5.8 喷粉 • 5.9 固化 • 5.10 下料 • 5.11 其他注意事项
粉末喷涂工艺培训
5. 静电粉末喷涂工艺规程
•5.1 生产工艺流程
粉末喷涂工艺培训
5. 静电粉末喷涂工艺规程
• 5.2 前处理工艺参数
槽名 槽液成分 处理温度 处理时间 液体浓度 检验项目
除油 水洗
AC除油 剂
自来水
常温 常温
4—5分 30—45g/L AC浓度
0.5—1分
/
/
皮膜处 理
皮膜剂 PH
20—30℃
2—3分
35—45 g/L 2.0—2.8
皮膜剂 PH
水洗 自来水 常温 0.5—1分
/
/
烘干
/
90±5℃ 10—20分
/
/
粉末喷涂工艺培训
5. 静电粉末喷涂工艺规程
粉末喷涂工艺培训教程PPT课件

硬度与耐磨性
采用硬度计对涂层硬度 进行检测,并通过磨损
试验评估耐磨性能。
耐腐蚀性能
通过盐雾试验、湿热试 验等手段检测涂层的耐
腐蚀性能。
05 粉末喷涂安全与环保
粉末喷涂安全操作规程
操作前检查
确保喷涂设备完好,无破损或泄露,检查电 源、气源是否正常。
保持工作区域整洁
定期清理工作区域,确保无杂物和灰尘,保 持工作环境的整洁和卫生。
对未附着在工件表面的粉末进 行回收,减少浪费并降低成本
。
固化与冷却流程
固化
通过加热或紫外线照射等 方法使涂层熔融并流平, 形成光滑、致密的涂层。
冷却
使涂层逐渐冷却并定型, 防止涂层出现裂纹或变形。
后处理
对固化后的工件进行质量 检查,对不合格的涂层进 行修复或重喷。
04 粉末喷涂质量控制
粉末喷涂膜厚控制
基材的附着力。
考虑粉末涂料的环保性能,优 先选择低挥发性有机化合物
(VOC)和低毒性的环保型粉 末涂料。
综合考虑粉末涂料的成本、涂 装效率以及涂层性能,以达到
最佳的性价比。
03 粉末喷涂工艺流程
前处理流程
01
02
03
表面清洁
去除工件表面的油污、锈 迹和杂质,确保工件表面 干净。
预处理
通过磷化、氧化或喷塑等 方法增强工件表面的附着 力,提高涂层与基材的结 合力。
的领域。
丙烯酸粉末
具有较好的耐候性和保色性, 适用于户外环境的装饰和保护
。
氟碳粉末
具有极佳的耐候性和抗污染性 ,常用于建筑外墙和玻璃制品
的装饰和保护。
粉末喷涂材料的选用原则
01
02
03
喷粉培训资料

喷粉作业的安全规范
喷粉作业前需检查设备及周边环境,确保安全无隐患 。
保持喷粉室内通风良好,防止粉末浓度过高。
针对不同材质和涂装要求,选择合适的粉末涂料和工 艺参数。
佩戴个人防护用品,如面罩、手套、脚套等。
静电喷粉的安全注意事项
确保电源稳定,防止静电喷粉设备因电压波动而产生 电火花。
定期清理静电喷粉设备的内部和外部,确保设备畅通 无阻。
经验二
选择合适的喷粉设备和涂 料
经验三
制定合理的喷粉工艺与流 程
喷粉技术的发展趋势与展望
技术一
高效、环保、节能的喷粉技术 成为主流
技术二
智能化、自动化喷粉设备越来越 受欢迎
技术三
粉末涂料向水性、无毒、高装饰性 方向发展
THANKS
感谢观看
影响喷粉质量的因素及控制措施
粉末质量
选用符合工艺要求的优质粉末,避 免使用过期、受潮或质量不稳定的 粉末。
喷粉设备
定期检查和维护喷粉设备,确保设 备正常运转,如更换磨损部件、清 洗喷枪等。
喷粉环境
保持喷粉环境清洁、干燥、无尘, 并控制环境温度和湿度,以减少对 喷粉质量的影响。
操作工艺
严格遵守喷粉操作工艺,控制喷粉 速度、气压、距离等参数,保持喷 枪移动速度均匀。
优化喷涂工艺和设备,提高粉末涂料的利用率,减少 浪费。
06
喷粉案例分析与实战经验
典型喷粉案例分析
01
02
03
案例一
某大型企业喷粉生产线调 试,产品品质不稳定
案例二
某小型企业喷粉设备选型 不当,生产效率低下
案例三
某出口型企业喷粉工艺改 进,符合国际标准
喷粉实战经验分享
经验一
粉末喷涂技能培训教材
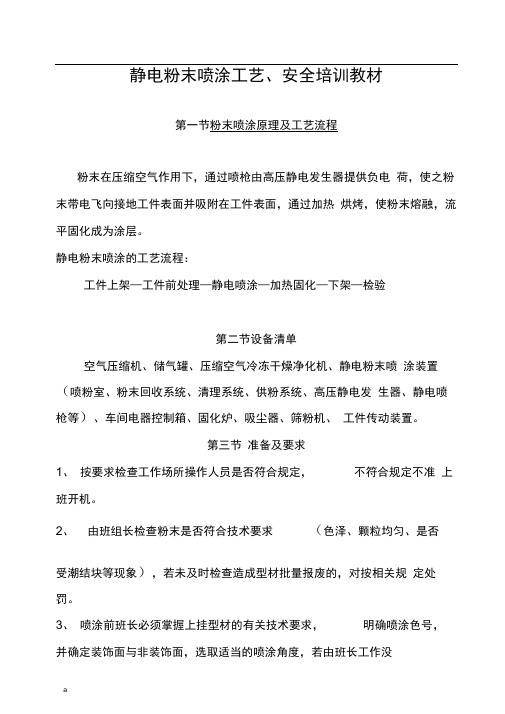
静电粉末喷涂工艺、安全培训教材第一节粉末喷涂原理及工艺流程粉末在压缩空气作用下,通过喷枪由高压静电发生器提供负电荷,使之粉末带电飞向接地工件表面并吸附在工件表面,通过加热烘烤,使粉末熔融,流平固化成为涂层。
静电粉末喷涂的工艺流程:工件上架—工件前处理—静电喷涂—加热固化—下架—检验第二节设备清单空气压缩机、储气罐、压缩空气冷冻干燥净化机、静电粉末喷涂装置(喷粉室、粉末回收系统、清理系统、供粉系统、高压静电发生器、静电喷枪等)、车间电器控制箱、固化炉、吸尘器、筛粉机、工件传动装置。
第三节准备及要求1、按要求检查工作场所操作人员是否符合规定,不符合规定不准上班开机。
2、由班组长检查粉末是否符合技术要求(色泽、颗粒均匀、是否受潮结块等现象),若未及时检查造成型材批量报废的,对按相关规定处罚。
3、喷涂前班长必须掌握上挂型材的有关技术要求,明确喷涂色号,并确定装饰面与非装饰面,选取适当的喷涂角度,若由班长工作没做到位造成喷涂面错误返喷的,将对班长予以50元/次的处罚。
4、检查整套设备是否正常,换粉前彻底清理喷粉室、输粉管、喷枪、一级回收器、振动筛、储粉筒等。
第四节工艺过程及技术要求1、工艺技术要求1.1按要求记录工艺参数,记录不全或造假者,对责任人按10元/次处罚,超过3次处罚车间主任100元/次。
1.2操作者每天对设备操作记录如实记录,如发现造假、漏记等,如造成生产事故的,量情节严重情况予以相应程度的处罚,对责任人按10〜20元/次处罚,超过3次处罚车间主任100元/次。
1.3 各工序员工对所在工序的工艺要求要能够全面理解、熟练掌握,发现问题及时汇报。
1.4粉房操作人员对回收粉的掺兑应做好记录,以便出现表面质量问题时查阅。
1.5车间班长应对返喷的型材做好详细的工艺记录并按周报工艺技术部,对隐瞒不报的量情节严重情况予以相应程度的处罚,对责任人按50元/次处罚,超过3次处罚车间主任100元/次。
1.6发现有员工不按工艺操作规程的行为对当事人以10元/次处罚,屡教不改的加倍处罚。
粉末喷涂工艺操作规程培训
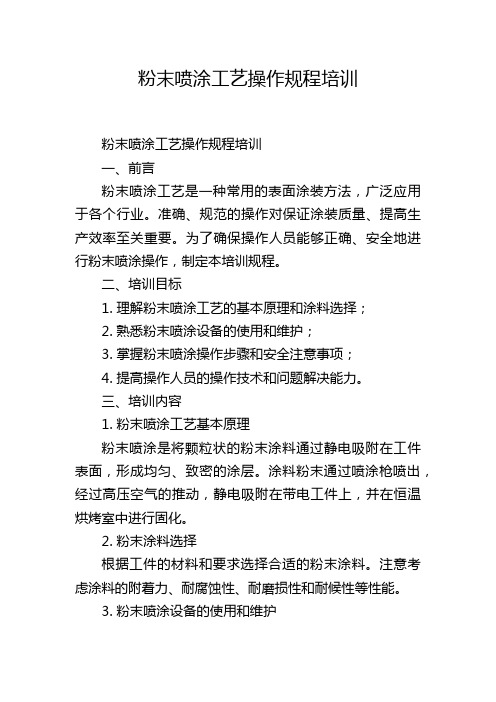
粉末喷涂工艺操作规程培训粉末喷涂工艺操作规程培训一、前言粉末喷涂工艺是一种常用的表面涂装方法,广泛应用于各个行业。
准确、规范的操作对保证涂装质量、提高生产效率至关重要。
为了确保操作人员能够正确、安全地进行粉末喷涂操作,制定本培训规程。
二、培训目标1. 理解粉末喷涂工艺的基本原理和涂料选择;2. 熟悉粉末喷涂设备的使用和维护;3. 掌握粉末喷涂操作步骤和安全注意事项;4. 提高操作人员的操作技术和问题解决能力。
三、培训内容1. 粉末喷涂工艺基本原理粉末喷涂是将颗粒状的粉末涂料通过静电吸附在工件表面,形成均匀、致密的涂层。
涂料粉末通过喷涂枪喷出,经过高压空气的推动,静电吸附在带电工件上,并在恒温烘烤室中进行固化。
2. 粉末涂料选择根据工件的材料和要求选择合适的粉末涂料。
注意考虑涂料的附着力、耐腐蚀性、耐磨损性和耐候性等性能。
3. 粉末喷涂设备的使用和维护- 了解粉末喷涂设备的组成和工作原理;- 熟悉设备的使用方法和注意事项;- 学会设备的保养和维护,确保设备的正常运行和寿命。
4. 粉末喷涂操作步骤- 工件准备:清理表面、研磨处理;- 喷涂前准备:调整喷枪参数、筛选粉末涂料;- 喷涂操作:保持一定的喷涂距离、使喷枪喷涂均匀;- 固化处理:将喷涂完毕的工件放入恒温烘烤室进行固化。
5. 安全注意事项- 装备各种必要的个人防护设备,如口罩、防护眼镜、防护手套等;- 喷涂操作时注意周围环境安全,防止火灾和爆炸;- 防止静电引起的危险,保持操作区域干燥,使用静电接地设备;- 注意操作时的人身安全,避免触电、碰撞等危险事故。
四、培训方式1. 理论培训:通过教材、PPT等方式进行基础知识的传授,理解粉末喷涂工艺的原理和涂料选择等内容。
2. 实践培训:在实际操作环境中进行操作演练,由专业人员进行指导和演示,提醒操作中的安全事项和注意事项。
3. 模拟练习:通过模拟器材进行练习,熟悉设备的使用方法和操作步骤,加深对工艺的理解和掌握度。
冷轧钢板粉末静电喷涂工艺培训教程
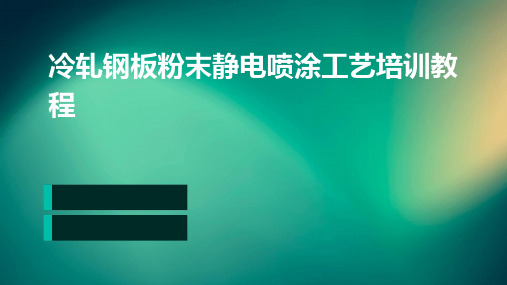
粒度分布
粉末的粒度应均匀,以保证良好的喷涂效果和涂层 质量。
流平性
粉末应具有良好的流平性,以形成平整光滑的涂 层。
固化温度和时间
粉末的固化温度和时间应与喷涂设备和工艺相匹配,以 确保涂层完全固化。
粉末配制方法与注意事项
配制方法
按照一定比例将环氧树脂、聚酯树脂、固化剂、颜料、填料 等原材料混合均匀,然后通过挤出、压片、破碎、筛分等工 序制成粉末。
冲击法
在涂层上粘贴一定规格的拉开试样,用拉 力试验机进行拉开试验,测量拉开试样时 所需的力来判断附着力。
用一定重量的重锤从一定高度自由落下冲击 涂层,观察涂层脱落情况来判断附着力。
07 安全生产与环保要求
安全生产规章制度遵守情况
严格遵守国家和地方 的安全生产法律法规, 确保生产过程中的安 全。
定期开展安全生产检 查和隐患排查,及时 发现和整改安全隐患。
厚度。
涂层附着力差
可能是由于基材与粉末不匹配、 固化温度过低或时间过短导致。 解决方案是更换合适的粉末、提
高固化温度或延长固化时间。
04 静电喷涂设备与系统
静电喷涂原理及设备组成
静电喷涂原理
利用高压静电场使粉末涂料带电,并吸附于接地工件表面,通过加热固化形成 涂层。
设备组成
主要包括喷枪、高压静电发生器、供粉装置、回收装置、控制系统等。
磷化过程控制
控制磷化液温度、浓度、 处理时间等参数,保证磷 化膜的质量和厚度。
磷化后处理
对磷化后的钢板进行清洗、 干燥等处理,防止磷化膜 受损。
表面粗糙度控制
粗糙度要求
根据涂层厚度和附着力要求,确 定钢板表面粗糙度的合理范围。
粗糙度测量
采用合适的测量工具和方法,对钢 板表面粗糙度进行测量和评估。
粉末喷涂工艺培训教程.ppt

1 提高后续涂层的表面质量 2 提高后续涂层的附着力 3 提高后续涂层的耐腐蚀能力 4 满足后续涂层的特殊性能要求
5
钢铁件前处理的主要工艺流程
工位
时间
温度
压力
1 热水喷淋
1-3分钟
40-45℃
0.07-0.12mpa
2 (喷淋)脱脂
1-3分钟
40-45℃
0.07-0.12mpa
3 脱脂
应将化学品储存在通风,干燥的室内,室内温度通常要求在 0-45℃
化学品应避免日光直射和雨淋,尤其是粉剂产品不得受潮 氧化,还原产品应远离酸性产品储存。例如:
Accelerator 131 所有化学品应独立堆放,并挂有识别标牌 搬运,使用化学品时要穿戴好必要的保护 用品。如:耐酸手 套, 围裙,雨靴,防护眼镜等 防止化学品与皮肤接触和飞溅,一旦接触应及时冲洗,若是 要害处,如眼睛或吸入口内,须及时到医务室就诊 一旦发生化学品泄漏,应及时阻止进一步泄漏,并根据化学 品 的特性,进行现场清洗。泄漏的化学品不得再用
23
出现问题时
检查操作人员的工作是否正确 检查磷化设备的喷嘴有无堵塞,是否调整,工件在工序间是 否保持湿润 检查线速度有无变化? 检查现场使用中的材料是否正确 检查是否坚持遵守了维修制度 检查槽液是否负载过度或比例失去平衡 检查工件种类是否变化,若是应重新设计夹具和设备调整
24
化学品的贮存条件和要求
主要辅助设施
除渣系统 升温系统 喷淋系统
15
Fe + 2H3PO4
(游离 酸)
3Zn(H2PO4)2
H2O
Fe + 2Zn(H2PO4)2
Fe(H2PO4)2 + H2 ------------------------------------------ (1) O(氧化剂
粉末喷涂工艺培训教材(PPT 105页)

围裙,雨靴,防护眼镜等 • 防止化学品与皮肤接触和飞溅,一旦接触应及时冲洗,若是
要害处,如眼睛或吸入口内,须及时到医务室就诊 • 一旦发生化学品泄漏,应及时阻止进一步泄漏,并根据化学品 的特性,进行现场清洗。泄漏的化学品不得再用
更新周期: 根据生产线具体情况确定,喷淋线一般每周一次(表调的使用寿命
与使用时间紧密相关)
表面调整的作用 -放大400倍磷化电镜照片有无表调对比
磷化定义
磷化原理:
工件(钢铁或铝,锌件)接触磷化液,通过化学反应 在金属表面形成一层不溶于水的具有一定耐腐蚀功能的 磷酸盐转化膜的过程,称之为磷化。
主要辅助设施
磷化的主要参数-总酸度
总酸度是指磷酸盐及其它无机酸的总和。总酸度一般以控制在规定范 围的上限为好,有利于加速磷化反应,使膜层晶粒细。总酸度低,反 应缓慢。
总酸度过高,产渣量大,消耗升高,可加水稀释。
总酸度过低,膜层薄,易反锈,可加磷化液添加剂调整。
总酸度的滴定: 10毫升槽液+酚酞指示剂 用0.1当量的氢氧化钠标准溶 液滴定至粉红色时所消耗的标准溶液毫升数即为槽液的总酸点数
磷化膜外观要求
合格的磷化膜外观均匀完整细密、无金属亮 点、无白灰; 磷化膜表面有光泽斑点,是裸露金属表面, 说明磷化很不完全,空隙率大;若有色斑, 说明磷化膜不均匀,颜色浅的区域膜薄; 工件表面是否形成磷化膜可以用指甲划工件 是否出现划痕判断。
水洗的作用
清洗掉工件表面残留的化学品,避免对后道工序的处理效果产生影响 降低脱脂后工件的温度,避免氧化 在工件表面形成一层水膜,避免工件与空气中的氧气接触发生氧化 最后的纯水洗是为了降低工件携带的水的电导率,避免对后续的涂层的 表面状态或性能产生影响
粉末喷涂工艺培训教材PPT(共 105张)

)
FePO4+H3PO4+1/2H2O -------------------------------(3)
(磷化渣)
Zn3(PO4)2.4 H2O + 4 H3PO4------------------------ (4)
(磷化膜
H.H2oOpeite) Zn2Fe(PO4)2.4H2O+2 H3PO4 --------------------(5)
表调的定义
n 目的:
n
膜。
调整金属表面活性,以便通过磷化反应获得均匀致密的磷化
n 作用机理:
n
细化磷化结晶晶核; 提高磷化反应速度;降低磷化温度。
n 组成:
n
主要是胶体磷酸钛
n 主要参数:
n
温度--- <30度,否则会引起槽液老化
n
PH---保证表调效果及槽液的稳定
n 表调对水质的要求:
n
配槽及补加水电导不大于100us/cm ,电导对表调寿命影响较大。
n 主要辅助设施
n 除渣系统 升温系统 喷淋系统
15
Fe + 2H3PO4
(游离 酸)
3Zn(H2PO4)2
H2O
Fe + 2Zn(H2PO4)2
Fe(H2PO4)2 + H2 ------------------------------------------ (1) O(氧化剂
O(氧化剂
) 2OH -------------------------------(2)
有机成分
消泡剂 控制泡沫的产生
缓蚀剂 避免工件发生腐蚀
络合剂 对硬水进行软化
表面活性剂 促进油脂乳化,增加油脂水溶性
粉末喷塑工艺培训课件

粉末喷塑工艺培训课件粉末喷塑工艺培训课件粉末喷塑工艺是一种广泛应用于工业生产中的表面涂装技术。
它通过将粉末状的涂料喷射到待涂物体表面,并在高温下烘烤使其熔化、流平和固化,形成坚固、耐用的涂层。
这种工艺具有高效、环保、经济等优势,因此在汽车、家具、建筑等领域得到了广泛的应用。
一、粉末喷塑工艺的基本原理粉末喷塑工艺的基本原理是将粉末状的涂料通过喷枪喷射到待涂物体表面。
涂料粉末在喷射过程中会带有静电电荷,这使得粉末能够均匀地附着在待涂物体表面上。
然后,待涂物体会进入一个高温烘烤室,通过加热使涂料粉末熔化、流平和固化,最终形成坚固的涂层。
二、粉末喷枪的使用技巧粉末喷枪是粉末喷塑工艺中最核心的工具之一。
使用粉末喷枪需要掌握一些技巧,以确保喷涂效果的质量和稳定性。
1. 喷枪的选择:根据涂料的特性和喷涂的需求,选择合适的喷枪。
一般来说,有压力式和电静电式两种喷枪可供选择。
2. 喷涂距离的掌握:喷涂距离的掌握对喷涂效果至关重要。
过近会导致涂层厚度不均匀,过远则会导致喷涂效果不理想。
根据涂料的要求,掌握合适的喷涂距离。
3. 喷涂角度的选择:喷涂角度也会影响喷涂效果。
一般来说,垂直喷涂可以获得均匀的涂层厚度,而水平喷涂则可以获得平滑的涂层表面。
4. 喷涂速度的控制:喷涂速度的控制也是关键。
过快的喷涂速度会导致涂层厚度不均匀,过慢则会导致涂层流挂。
根据涂料的要求,掌握合适的喷涂速度。
三、粉末喷塑工艺的优点粉末喷塑工艺相比传统的涂装工艺具有许多优点。
1. 环保:粉末喷塑工艺不含溶剂,不会产生有害气体和废水,对环境友好。
2. 经济:粉末喷塑工艺节约涂料和能源,降低了生产成本。
3. 耐久性:粉末喷塑形成的涂层具有良好的耐久性,能够抵抗腐蚀和磨损。
4. 多样性:粉末喷塑工艺可以实现各种颜色和效果的涂装,满足不同需求。
四、粉末喷塑工艺的应用领域粉末喷塑工艺在许多领域得到了广泛的应用。
1. 汽车工业:粉末喷塑工艺可以用于汽车车身、零部件和轮毂等的涂装,提高产品的外观和耐久性。
粉末喷涂工艺培训教程ppt

粉末堵塞及解决方案
粉末堵塞
在粉末喷涂过程中,如果供粉系统或喷枪出现堵塞,会导致 粉末无法正常喷出,影响涂装效果。
解决方案
定期检查供粉系统,确保管道和喷枪畅通;对喷枪进行定期 的清洗和维护,防止粉末在枪口处堆积。
工件表面粗糙及解决方案
工件表面粗糙
由于粉末颗粒大小不均、温度不当等原因,可能会导致工件表面出现粗糙、 桔皮等现象。
粉末喷涂工艺培训教程ppt
xx年xx月xx日
目录
• 粉末喷涂工艺简介 • 粉末喷涂工艺流程 • 粉末喷涂设备与材料 • 粉末喷涂工艺中的问题及解决方案 • 粉末喷涂工艺的应用实例 • 粉末喷涂工艺的发展趋势与展望
01
粉末喷涂工艺简介
粉末喷涂工艺的定义
粉末喷涂工艺是一种表面处理技术,它通过将粉末涂料均匀 地喷涂到工件表面,形成一层致密的保护膜,从而达到防腐 、耐磨、美观等目的。
将粉末均匀地喷涂到工件表面,控制喷涂厚度 和均匀性。
粉末固化
加热固化
将喷涂后的工件加热到指定温度,使粉末熔融并流平,形成光滑表面。
冷却降温
降温后,粉末固化形成一层紧密附着的涂层。
成品检验
外观检测
检查涂层外观是否符合要求, 如颜色、光泽度等。
厚度检测
检测涂层厚度是否符合要求,以 保证涂层性能。
附着力检测
通过划格试验、拉拔试验等方法检 测涂层与工件之间的附着力是否符 合要求。
03
粉末喷涂设备与材料
粉末喷涂设备
静电粉末喷枪
静电粉末喷枪是粉末喷涂的主要设备之一,其作用是将粉末涂料均匀地喷涂到工件表面。 静电粉末喷枪分为内混式和外混式两种,根据不同的需求进行选择。
供粉系统
供粉系统是粉末喷涂的供料装置,包括储粉罐、输粉管、粉泵等部件,确保粉末涂料的连 续供应。
喷粉操作手培训教材

喷粉培训教材
原理:粉末涂料在高压直流-50~-90KV电场中带上负电荷,利用高压静电电晕电场原理,在静电场及气流的作用下飞向被涂物的表面,经过加热融熔固化形成均匀,连续,平整,光滑的涂膜。
喷涂过程:*带电的粉末在静电场中沿着电场线飞向工件并均匀的吸附于工件表面;
*工件对于粉末的吸引力大于粉末之间的相互排斥力,粉末密集堆积形成一定厚度的涂膜;
*随着粉末沉积层厚度的增加,粉层对于飞来粉粒的排斥力增大,当工件对粉末的吸引力和对粉末的排斥力相等时,继续飞来的粉末不再被工件吸附。
因此静电粉末喷涂能够得到厚度均匀的涂膜。
通过上图,可以看出喷粉较合理的电压40~70KV,(设备不一样,粉末品牌不一样也有轻微区别,
依据工艺卡片要求设置)
我们可能会有个误区,会认为粉末在粉桶中翻腾得越厉害越好,但是正确的流化应该是表面轻微沸腾,用手在粉桶里面抓,抓不成团为最佳。
(流化压力一般设置在0。
1~0.15MPA为佳)
电荷过多就会产生反电离作用,轮毂产品夹角不容易上粉就是法拉利静电效应(反电离作用)
岗位工作流程
枪距15~25厘米
安全意识
静电喷涂常见的异常情况
常见问题以及原因分析。
- 1、下载文档前请自行甄别文档内容的完整性,平台不提供额外的编辑、内容补充、找答案等附加服务。
- 2、"仅部分预览"的文档,不可在线预览部分如存在完整性等问题,可反馈申请退款(可完整预览的文档不适用该条件!)。
- 3、如文档侵犯您的权益,请联系客服反馈,我们会尽快为您处理(人工客服工作时间:9:00-18:30)。
槽名 槽液成分 处理温度 处理时间 液体浓度 检验项目
除油 水洗
AC除油 剂
自来水
常温 常温
4—5分 30—45g/L AC浓度
0.5—1分
/
/
皮膜处 理
皮膜剂 PH
20—30℃
2—3分
35—45 g/L 2.0—2.8
皮膜剂 PH
水洗 自来水 常温 0.5—1分
/
/
烘干
/
90±5℃ 10—20分
/
5.7 吹料 5.8 喷粉 5.9 固化 5.10 下料 5.11 其他注意事项
5.1 生产工艺流程
预处理
挤压坯料 → 检验 → 上架 → 脱脂 → 水洗
↓
下架 ← 沥干烘干 ← 水洗 ← 水洗 ← 成膜 ← 水洗
移交 ↓
上架 → 表面清渣 → 喷粉 → 固化 → 下架 → 检验→
喷涂
5.2 前处理工艺参数
2.5——3.0m/min
5.4 生产前的准备工作
1检查前处理各工艺槽的槽液成分是否与表一相符,如果不符应及时进行调整。 2 检查各工艺槽的液面高度符合工艺要求,并清除槽液中的污物和液面漂浮物。 3 检查溢流水压力是否正常,水量是否足够。 4 检查行车、升降机、转移车、烘干炉等设备是否正常。如有异常应及时排除,严禁带 病运行。 5 查固化炉烘道内部有否异常和吊具是否牢靠,保持烘道畅通。 6 开启输送链控制系统,检查输送链运行是否正常。 7 开启固化炉热风循环系统,打开热风循环风机的冷却水,检查热风循环系统是否正常。 8 开启空气压缩机,检查储气罐压力和干燥度是否符合要求。
8根据粉末的颜色使用粉管,深色的粉末应使用深色的粉管,浅色 的粉末应使用浅色的粉管,一定不能混用粉管避免出现混色的不 良品。
5.8喷粉
9 在更换不同颜色的粉末时,喷粉系统和回收系统一 定要完全清理干净后才能喷涂另一个颜色。
10 随时保持喷房的环境和设备的清洁,不能有粉 末和垃圾。
11 经喷涂后、固化前的制品禁止用手摸及其它物品 相碰,以防表面粉末局部脱落。
6.1 缩孔 产生原因
3.在制造粉末涂料时所用的压缩空 气中水分和油分离得不干净或者压片 冷却辊太凉而凝结的露滴带进水分
1.在制造粉末涂料过程中,流平剂、 4.,脱脂工序除油不干净,特别是
消泡剂等助剂用量不够或者分散不均 表面比较粗糙的工件上的油污
匀 5.工件表面不平整,而且有一些显微
2.由于粉碎机等设备清理不干净,而 麻坑
6.1 缩孔
解决办法
1.严格供应商质量管理和原材料进厂 检验 2.脱脂工序除油要彻底
5.换粉时 喷房和输送粉末的管道要彻 底清理干净
6.压缩空气要除油和除水彻底,定期 排放气罐里的水
7.严格按要求存放粉末,防止粉末受 潮
3.加强挤压坯料的表面质量控制
4.严格控制前处理烘干时间和烘干温 度
8.输送链上的润滑油要适当,防止跑 冒滴漏
6补喷或自动喷涂粉末时要特别注意积粉、露底、膜厚超高、针 孔等不良品.所以在喷涂砂纹粉末和金属粉末时,静电电压要调低 点,电压大约在45Kv-55Kv之间;平光、高光、哑光的粉末静 电电压相对要调高一点,电压大约在60Kv-70Kv之间。
7喷涂过程中,要不断观察表面情况,如果出现异常情况时,应及时 处理。
主讲:谢恩
1. 培训纪律 2. 静电粉末喷涂原理 3. 影响静电粉末喷涂的主要因素 4. 静电粉末涂装的主要设备 5. 静电粉末喷涂工艺规程 6. 常见问题及解决办法
1. 按时签到; 2. 不迟到、不早退、无特殊情况不得请假; 3. 中途不擅自离场,特殊情况例外; 4. 手机设置为震动或关机,紧急电话去培训室外接 听; 5. 保持安静,不得抽烟,不做与培训无关的事; 6. 注意力集中,做好应控制在5—9万伏之间。
3.4 喷涂距离
喷涂距离控制在150-300mm之间。
3.5 供气压力
在喷涂时应尽量把气压和粉末
输 送空气量保持在所需的最小要求量。
4.1 高压静电喷枪 4.2 粉末回收装置 4.3 供粉装置 4.4 喷粉室 4.5 自动喷枪往复机
5.1 生产工艺流程 5.2 前处理工艺参数 5.3 喷涂工艺参数 5.4 生产前的准备工作 5.5 前处理操作要求 5.6 上架
/
5.3 喷涂工艺参数
项目 静电压 供粉气压 雾化气压 流化气压 粉末粒度 粉末电阻率 工件与喷嘴间距
工作温度、湿度
链速
工艺参数 30——100KV 0.2——0.4MPa 0.01——0.1MPa 0.01——0.1MPa 过180目筛 1010——1014Ω•m 150——300mm 温度 0——40℃ 相对湿度 <85%
第三阶段:随着涂层厚度的不断增加,排斥力亦将增大,当增大到 与静电电场力相同时,粉末便不再被工件吸附,这时涂层厚度不再 增加,喷出的粉末完全不被吸附,全部掉下来。因此,静电粉末涂 层的厚度有一定的限制。
3.1 粉末导电率 一般在1010—1014Ω.cm。
3.2 粉末粒度
粉末粒径分布在30—50um范围内。
4定期检查喷枪的高压线,发现有线管老化或线路出现裂纹的 立即更换,以免发生意外事故。
➢ 6.1 缩孔 ➢ 6.2 物理性能不合格 ➢ 6.3 不容易上粉 ➢ 6.4 涂膜厚度不合格 ➢ 6.5 颗粒 ➢ 6.6 失光和泛黄 ➢ 6.7 色差
➢ 6.8 涂膜遮盖力不好 ➢ 6.9 凹膜、针孔 ➢ 6.10 气泡 ➢ 6.11 流挂 ➢ 6.12 橘纹、橘皮 ➢ 6.13 耐化学性能不好
5.4 生产前的准备工作
9 按喷涂设备操作规程的相关规定启动设备空载运行并巡回检查,确认喷涂设备运转正常。 10 确认一切正常,将烘干炉和固化炉升温到工艺规定温度。 11前处理工按生产部下达的生产指令领用和吊运坯料,并核对型材的长度、数量、壁厚是 否和生产指令单相符,确定无误后才能生产。 12相关岗位人员检查以下工具是否齐备和符合使用要求: a)挂具:导电良好,无空缺、无变形; b)小车:能正常推动。 13相关操作人员去库房领取生产所需的粉末涂料、熔剂和砂纸等。 14准备好当班生产必须的记录表格、文件、量具及色板等。
B、烘干后,材料应小心放在料车上,运至喷涂车间做后工序处理, 当天皮膜处理的型材当天喷涂,最长放置时间不许超过24小时,且一 定要用防尘布将其盖好。
C、前处理烘烤完成后到上架之前,皮膜处理的料不得用手直接触摸, 必须带干净手套后才能搬运。
5.6上架
1上挂前所有上挂和相关的工作人员,必须佩戴干净的沙布手套,才 能搬料和挂料。
5.5前处理操作要求
(1) 脱脂:温度为常温,脱脂时间以脱脂后铝件表面挂水均匀为准。 材料吊起过槽时,要尽量倾斜,倾斜度控制在10°左右,并吊起控水 0.5—1分钟。
(2) 水洗:两次用自来水洗,时间为1-3分钟,倾斜度控制在10°左 右,并吊起控水0.5—1分钟。要求水洗槽有溢流换水。
(3) 皮膜处理:皮膜处理温度为常温,材料过槽时,要尽量倾斜, 倾斜度控制在10°左右,并吊起控水1分钟,保证皮膜颜色为从浅黄到 金黄或略带彩虹色且颜色均匀。
12 合理搭配新旧粉末,回收粉要按规定过筛。
5.9固化
1固化炉内应保持清洁无尘,以防止灰尘附着于型材表面。
2按工艺规程合理控制固化炉温度,防止温度过高或过低。 经常用炉温测试仪检查温度曲线是否符合生产工艺。
3根据烘道长度合理调整输送链速度,使有效固化时间控制 在10——20分钟之间。
4经常检查型材固化流平是否符合要求,不符合要求及时调 整工艺参数,使产品符合要求。
不同类型树脂粉末涂料之间相容性又
不好,或者不同流平剂粉末涂料之间 6. 前处理干燥温度和时间不充分,工
相容性不好而产生互相污染
件表面上残留着水分
6.1 缩孔 产生原因 7. 粉末涂装设备系统在更换涂料品种时,喷枪、供粉 箱、送粉管道、回收系统和喷粉室清扫不彻底 8. 压缩空气中含有的水分和油分离不干净 9. 粉末涂料受潮严重时,也容易使涂膜产生缩孔 10.挂链上的油污等掉进喷粉室或烘炉中也会污染型材
2.2 粉末吸附于工件表面的过程
第一阶段:粉末在静电电场力的作用下均匀吸附于工件表面上,形 成一层稀薄的连续覆盖层,这一阶段的粉末基本上被工件吸附。
第二阶段:粉末在静电电场作用下继续飞向工件表面,由于已覆盖 上的粉末与新的粉末所带电荷相同而产生排斥作用,但静电电场力 比排斥力强大,因而粉末将继续吸附,涂层将不断增厚,但有部分 粉末不能吸附于工件表面而掉下来。
5.6上架
5上挂的型材(双面挂和单面挂)头尾都要整齐,前后不能超出30mm。 6挂料时要用尽挂料的高度空间,不然会影响生产的产量,增加生产成本。 7上挂工件的装饰面应正对喷枪,以获得较均匀的漆膜;上料吊具与工件的装 饰面应尽量避免接触。 8相邻两支料间的距离不得小于50mm。 9小断面型材,中间可能碰到在一起的型材,中间应加辅助挂点。 10隔条要用车子装好,下班前把挂具整理好并放整齐。 11多余的料及待检料放在推车上,废料应及时处理,不能混淆。
2.1 静电粉末喷涂原理
静电粉末喷涂是利用高压静电电晕电场原理。喷枪头上的金属导流环接 上高压负极,被涂工件接地形成正极,在喷枪和工件之间便形成较强的静 电场。当运送载体(压缩空气)将粉末涂料从供粉桶经输送管送至喷枪的 导流环时,由于导流环接上高压负极产生电晕放电,其周围便产生密集的 电荷而使粉末带上负电荷。在静电力和压缩空气这两个动力的共同作用下, 粉末从喷枪口飞向工件并均匀地吸附在工件表面,经过加热,粉末熔融并 流平固化成均匀、连续、平整、光滑的涂层。
2根据生产计划单的要求,将同一种颜色的型材从前处理领入。要经 常检查型材表面有无水分,前处理状况是否良好,否则不能上架。
3根据铝型材的形状,选择合适的挂具和挂钩。选定挂具后必须保证 挂具无变形,接触点无涂料覆盖,导电性能良好。如有接触不良的挂 具要及时修理,以免影响喷涂质量。