汽车空调管路的设计FEMA(DFMEA)
DFMEA(设计FMEA)与 PFMEA(过程FMEA)简介
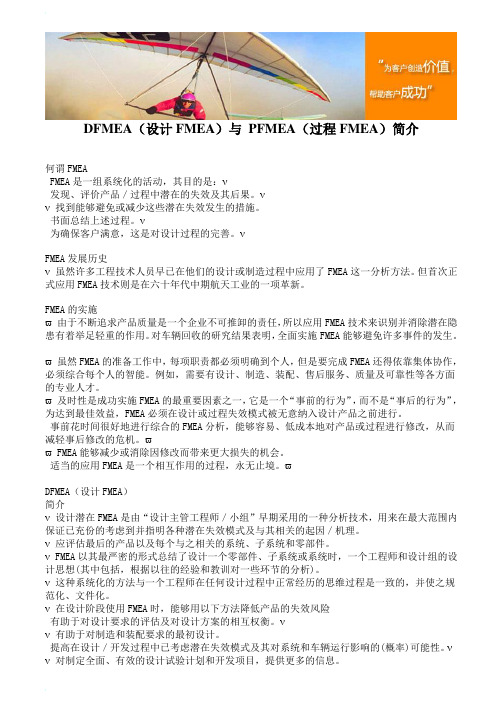
DFMEA(设计FMEA)与PFMEA(过程FMEA)简介何谓FMEAFMEA是一组系统化的活动,其目的是:ν发现、评价产品/过程中潜在的失效及其后果。
νν找到能够避免或减少这些潜在失效发生的措施。
书面总结上述过程。
ν为确保客户满意,这是对设计过程的完善。
νFMEA发展历史ν虽然许多工程技术人员早已在他们的设计或制造过程中应用了FMEA这一分析方法。
但首次正式应用FMEA技术则是在六十年代中期航天工业的一项革新。
FMEA的实施ϖ由于不断追求产品质量是一个企业不可推卸的责任,所以应用FMEA技术来识别并消除潜在隐患有着举足轻重的作用。
对车辆回收的研究结果表明,全面实施FMEA能够避免许多事件的发生。
ϖ虽然FMEA的准备工作中,每项职责都必须明确到个人,但是要完成FMEA还得依靠集体协作,必须综合每个人的智能。
例如,需要有设计、制造、装配、售后服务、质量及可靠性等各方面的专业人才。
ϖ及时性是成功实施FMEA的最重要因素之一,它是一个“事前的行为”,而不是“事后的行为”,为达到最佳效益,FMEA必须在设计或过程失效模式被无意纳入设计产品之前进行。
事前花时间很好地进行综合的FMEA分析,能够容易、低成本地对产品或过程进行修改,从而减轻事后修改的危机。
ϖϖ FMEA能够减少或消除因修改而带来更大损失的机会。
适当的应用FMEA是一个相互作用的过程,永无止境。
ϖDFMEA(设计FMEA)简介ν设计潜在FMEA是由“设计主管工程师/小组”早期采用的一种分析技术,用来在最大范围内保证已充份的考虑到并指明各种潜在失效模式及与其相关的起因/机理。
ν应评估最后的产品以及每个与之相关的系统、子系统和零部件。
ν FMEA以其最严密的形式总结了设计一个零部件、子系统或系统时,一个工程师和设计组的设计思想(其中包括,根据以往的经验和教训对一些环节的分析)。
ν这种系统化的方法与一个工程师在任何设计过程中正常经历的思维过程是一致的,并使之规范化、文件化。
DFMEA(设计FMEA)与 PFMEA(过程FMEA)简介范文

DFMEA(设计FMEA)与PFMEA(过程FMEA)简介何谓FMEAFMEA是一组系统化的活动,其目的是:ν发现、评价产品/过程中潜在的失效及其后果。
νν找到能够避免或减少这些潜在失效发生的措施。
书面总结上述过程。
ν为确保客户满意,这是对设计过程的完善。
νFMEA发展历史ν虽然许多工程技术人员早已在他们的设计或制造过程中应用了FMEA这一分析方法。
但首次正式应用FMEA技术则是在六十年代中期航天工业的一项革新。
FMEA的实施ϖ由于不断追求产品质量是一个企业不可推卸的责任,所以应用FMEA技术来识别并消除潜在隐患有着举足轻重的作用。
对车辆回收的研究结果表明,全面实施FMEA能够避免许多事件的发生。
ϖ虽然FMEA的准备工作中,每项职责都必须明确到个人,但是要完成FMEA还得依靠集体协作,必须综合每个人的智能。
例如,需要有设计、制造、装配、售后服务、质量及可靠性等各方面的专业人才。
ϖ及时性是成功实施FMEA的最重要因素之一,它是一个“事前的行为”,而不是“事后的行为”,为达到最佳效益,FMEA必须在设计或过程失效模式被无意纳入设计产品之前进行。
事前花时间很好地进行综合的FMEA分析,能够容易、低成本地对产品或过程进行修改,从而减轻事后修改的危机。
ϖϖ FMEA能够减少或消除因修改而带来更大损失的机会。
适当的应用FMEA是一个相互作用的过程,永无止境。
ϖDFMEA(设计FMEA)简介ν设计潜在FMEA是由“设计主管工程师/小组”早期采用的一种分析技术,用来在最大范围内保证已充份的考虑到并指明各种潜在失效模式及与其相关的起因/机理。
ν应评估最后的产品以及每个与之相关的系统、子系统和零部件。
ν FMEA以其最严密的形式总结了设计一个零部件、子系统或系统时,一个工程师和设计组的设计思想(其中包括,根据以往的经验和教训对一些环节的分析)。
ν这种系统化的方法与一个工程师在任何设计过程中正常经历的思维过程是一致的,并使之规范化、文件化。
DFMEA-汽车空调 - 系统
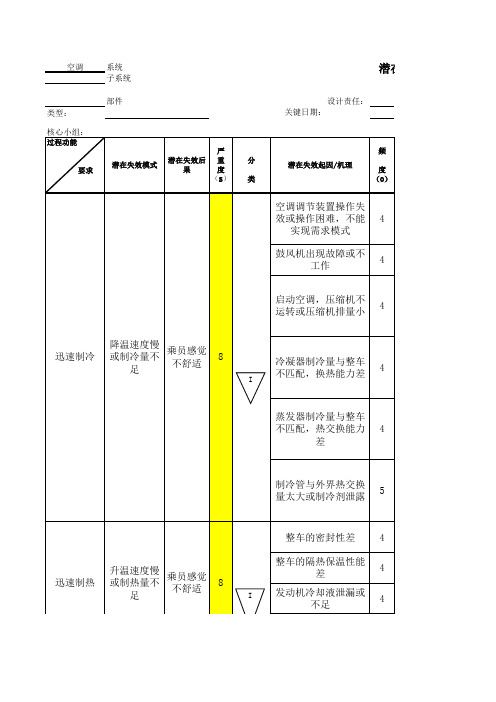
3
90
样件装车 试验验证
项目组
对安装结构和功 能部件进行优化
更换滤网
及时清理
4
72
FMEA编号: 页码: 第 页 编制人: FMEA日期(编制):
潜在失效模式及后果分析 (系统FMEA)
共
页
(修订)
现行设计控制
预防
探测
风 探 险 R 测 顺 P 度 序 N (D) 数
措施执行结果 建议措施 责任及目标完 成日期
采取的措施
要求厂家进行密封 加强出厂进行密 性实验,并出具相 封性试验 关报告
2
48
3D设计改进
CFD
2
32
3D设计改进
CFD
2
32
要求厂家进行相关 对鼓风机进行噪 实验,并出具报告 声试验
2
32
要求厂家进行相关 对压缩机进行噪 实验,并出具报告 声试验
2
32
3D设计改进
进行零部件性能 试验,检查接插 件安装情况
I
蒸发器芯体密封性差 冷凝器密封性能差 制冷剂循环不畅,连 接管路接头密封性能 差
4
由于风道结构造成噪 音大
4
噪音小
大于70dB(A)
不符合法
4
由于风道结构造成噪 音大
4
噪音小
大于70dB(A)
不符合法 规
4
N
鼓风机运转时噪音太 大
4
压缩机运行稳定性 差,噪音大
4
操纵方便
乘员操纵 空调装置操 不方便, 纵手感差或 产生抱怨 操纵失效 。
4
4
4
迅速制冷
8
I
冷凝器制冷量与整车 不匹配,换热能力差
FMEA、DFMEA、PFMEA学习资料
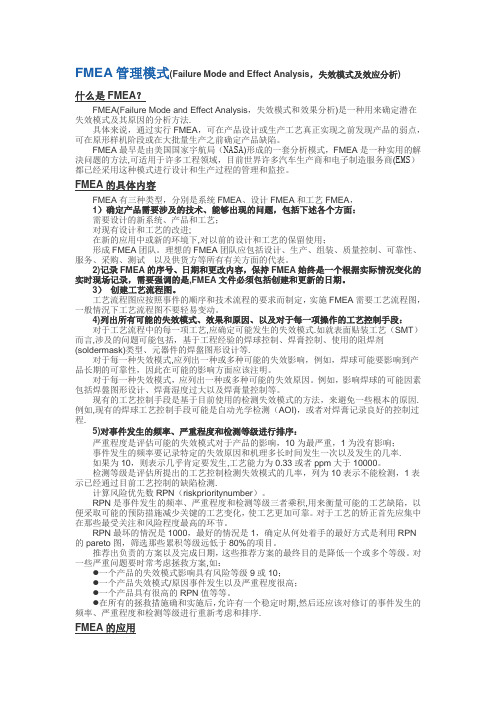
FMEA管理模式(Failure Mode and Effect Analysis,失效模式及效应分析)什么是FMEA?FMEA(Failure Mode and Effect Analysis,失效模式和效果分析)是一种用来确定潜在失效模式及其原因的分析方法.具体来说,通过实行FMEA,可在产品设计或生产工艺真正实现之前发现产品的弱点,可在原形样机阶段或在大批量生产之前确定产品缺陷。
FMEA最早是由美国国家宇航局(NASA)形成的一套分析模式,FMEA是一种实用的解決问题的方法,可适用于许多工程领域,目前世界许多汽车生产商和电子制造服务商(EMS)都已经采用这种模式进行设计和生产过程的管理和监控。
FMEA的具体内容FMEA有三种类型,分別是系统FMEA、设计FMEA和工艺FMEA,1)确定产品需要涉及的技术、能够出现的问题,包括下述各个方面:需要设计的新系统、产品和工艺;对现有设计和工艺的改进;在新的应用中或新的环境下,对以前的设计和工艺的保留使用;形成FMEA团队。
理想的FMEA团队应包括设计、生产、组装、质量控制、可靠性、服务、采购、测试以及供货方等所有有关方面的代表。
2)记录FMEA的序号、日期和更改内容,保持FMEA始终是一个根据实际情況变化的实时现场记录,需要强调的是,FMEA文件必须包括创建和更新的日期。
3)创建工艺流程图。
工艺流程图应按照事件的顺序和技术流程的要求而制定,实施FMEA需要工艺流程图,一般情況下工艺流程图不要轻易变动。
4)列出所有可能的失效模式、效果和原因、以及对于每一项操作的工艺控制手段:对于工艺流程中的每一项工艺,应确定可能发生的失效模式.如就表面贴装工艺(SMT)而言,涉及的问题可能包括,基于工程经验的焊球控制、焊膏控制、使用的阻焊剂(soldermask)类型、元器件的焊盤图形设计等.对于每一种失效模式,应列出一种或多种可能的失效影响,例如,焊球可能要影响到产品长期的可靠性,因此在可能的影响方面应该注明。
(完整版)DFMEA

第三版前言FMEA第三版(QS—9000)戴姆勒克莱斯勒、福特和通用汽车公司供方使用的参考手册,将其作为指南,在进行设计FMEA和过程FMEA开发中提供帮助。
本参考手册旨在澄清与FMEA开发相关的技术问题.本参考手册考手册与供方质量要求特别工作组的约定相一致,即将戴姆勒克莱斯勒、福特和通用汽车公司供方使用的参考手册、程序、报告格式及技术术语标准化.因此,FMEA第三版是为供方提供指南而编写的.手册中未规定要求,而是对覆盖设计阶段或过程分析阶段进行FMEA时通常出现的各种情形提供了通用性指南。
本手册在技术上等效于SAE J1739关于设计FMEA和过程FMEA的标准,但不包括设备FMEA的应用.对设备FMEA感兴趣者可以参考SAE J1739的有关示例.供方质量要求特别工作组感谢以下各位及其所在的公司。
在FMEA手册第三版或以前各版的编写过程中,他们倾注了大量的时间和精力。
第三版Kevin A。
Lange - 戴姆勒克莱斯勒Steven C. Leggett - 通用Beth Baker – AIAG以前各版Howard Riley - 戴姆勒克莱斯勒 Mark T。
Wrobbel —戴姆勒克莱斯勒George R。
Baumgartner —福特 Rebecca French - 通用Lawrence R。
Mccullen —通用 Mary Ann Raymond — Bosch Robert A。
May – Goodyear William Ireland –Kelsey-Hayes Tripp Martin – Peterson Spring此外,供方质量要求特别工作组还要感谢以下SAE J1739工作组的各位,他们在此版手册的技术变更和改进方面提供的大力支持。
William D。
Carlson —戴姆勒克莱斯勒Glen R. Vallance -福特Carl S。
Carlson —通用本手册的版权归戴姆勒克莱斯勒、福特和通用汽车公司所有。
DFMEA-汽车空调 - 空调控制器总成
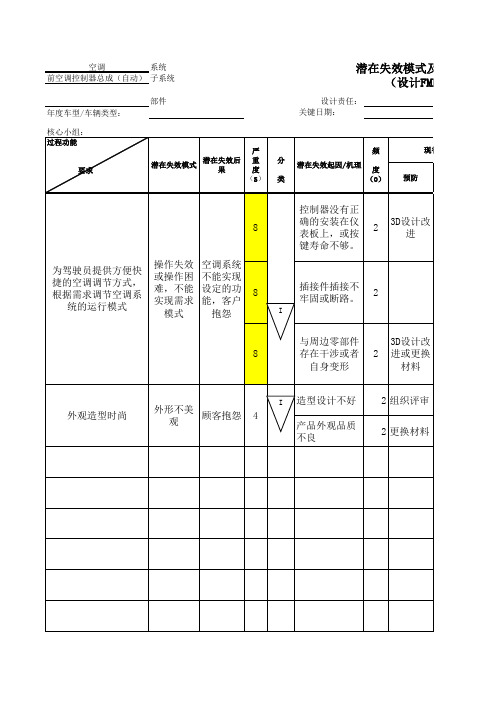
2
32
2
32
2
32
rp件验证
2 2
16 16
空调 系统 前空调控制器总成(自动) 子系统 部件 年度车型/车辆类型: 核心小组:
过程功能 潜在失效后 潜在失效模式 果 严 重 度 (S)
潜在失效模式及后果分析 (设计FMEA)
设计责任: 关键日期:
频 分 类 潜在失
要求
预防
8
控制器没有正 确的安装在仪 表板上,或按 键寿命不够。
外观造型时尚
外形不美 顾客抱怨 观
I
4
失效模式及后果分析 (设计FMEA)
编制人: FMEA日期(编制):
FMEA编号: 页码: 第 页
共
页
(修订)
现行设计控制
探测
风 探 险 R 测 顺 P 度 序 N (D) 数
措施执行结果 建议措施 责任及目标完 成日期
采取的措施
S
O
D
RPN
样件装车 验证,更 改相应结 构 检查插接 件及线束 的接通情 况
2
3D设计改 进
为驾驶员提供方便快 捷的空调调节方式, 根据需求调节空调系 统的运行模式
操作失效 或操作困 难,不能 实现需求 模式
空调系统 不能实现 设定的功 能,客户 抱怨
8
I
插接件插接不 牢固或断路。
2
8
与周边零部件 存在干涉或者 自身变形 造型设计不好 产品外观品质 不良
2
3D设计改 进或更换 材料 2 组织评审 2 更换材料
DFMEA-汽车空调 - 空调管路
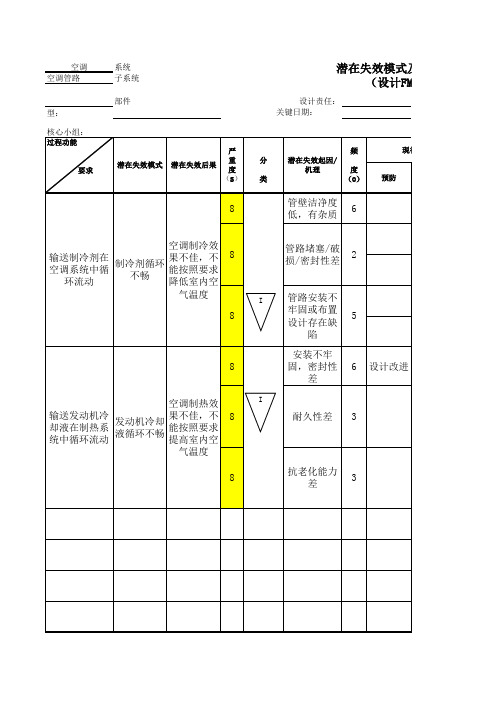
8
耐久性差
3
8
抗老化能力 差
3
失效模式及后果分析 (设计FMEA)
编制人: FMEA日期(编制):
FMEA编号: 页码: 第 页
共
页
(修订)
现行设计控制
探测
探 测 度 (D)
风 险 R 顺 P 序 N 数
措施执行结果 建议措施 责任及目标完 成日期
采取的措施
S
O
D
RPN
加强出厂 质检 加强出厂 质检 装配后检 验是否存 在隐患, 如干涉、 死弯等 样件装车 验证
空调制冷效 输送制冷剂在 果不佳,不 制冷剂循环 空调系统中循 能按照要求 不畅 环流动 降低室内空 气温度
8
2
I
8
管路安装不 牢固或布置 设计存在缺 陷 安装不牢 固,密封性 差
5
8
I
6
设计改进
空调制热效 输送发动机冷 果不佳,不 发动机冷却 却液在制热系 能按照要求 液循环不畅 统中循环流动 提高室内空 气温度
Hale Waihona Puke 空调 空调管路系统 子系统
潜在失效模式及后果分析 (设计FMEA)
设计责任: 关键日期:
部件 年度车型/车辆类型: 核心小组:
过程功能 潜在失效模式 严 重 潜在失效后果 度 (S)
频 分 类 潜在失效起因/ 机理 度 (O)
现行设计控制
要求
预防
8
管壁洁净度 低,有杂质 管路堵塞/破 损/密封性差
6
2
96
2
32
2
120
3D设计改 进
项目组
3D设计检查,装 车试验
8 2 2 32
3
汽车空调系统设计DFMEA案例分析

汽车空调系统设计DFMEA案例分析DFMEA简介DFMEA(Design Failure Mode and Effects Analysis,设计失效模式与影响分析)是一种常用的质量管理工具,用于在产品设计阶段识别并解决潜在的失效模式及其影响。
本文将以汽车空调系统设计为案例,探讨如何应用DFMEA来提高汽车空调系统设计的安全性和可靠性。
一、设计失效模式与影响分析(DFMEA)DFMEA是一种以系统化和有序方式对产品设计进行评估和分析的方法。
它的主要目的是识别可能的失效模式、评估其严重程度以及制定相应的纠正和预防措施。
下面我们将根据DFMEA的步骤,对汽车空调系统进行案例分析。
1. 制定DFMEA团队与范围首先,确定参与DFMEA的团队成员,包括汽车空调系统设计的工程师、质量控制专家、测试工程师等。
明确DFMEA的范围和目标,以汽车空调系统各个子系统为分析对象。
2. 识别失效模式对汽车空调系统设计进行全面的分析,列举可能的失效模式。
比如,制冷剂泄漏、温度控制失效、空调系统过热等。
3. 确定失效模式的可能原因针对每个失效模式,分析其潜在的原因,如设计不当、材料选择不当、制造工艺缺陷等。
以制冷剂泄漏为例,可能的原因包括密封件老化、接口松动等。
4. 评估失效的严重程度对每个失效模式进行严重程度评估,考虑其对汽车空调系统性能、安全性和可靠性的影响。
以温度控制失效为例,可能导致车内温度无法调节,对车内乘客的舒适度产生较大影响。
5. 确定控制措施针对每个失效模式确定相应的预防和纠正措施,以减少失效概率和降低失效的严重程度。
比如,在设计阶段增加密封件的检测和更换计划,严格控制安装过程中的接口紧固力矩。
6. 跟踪执行和评估效果实施控制措施后,跟踪其执行情况,并对效果进行评估。
通过实际数据的反馈,不断优化和改善汽车空调系统的设计。
二、汽车空调系统DFMEA案例分析以下是针对汽车空调系统的DFMEA案例分析,以帮助读者更好地理解DFMEA方法的应用。
空调系统及各部件共8个-SFMEA和DFMEA
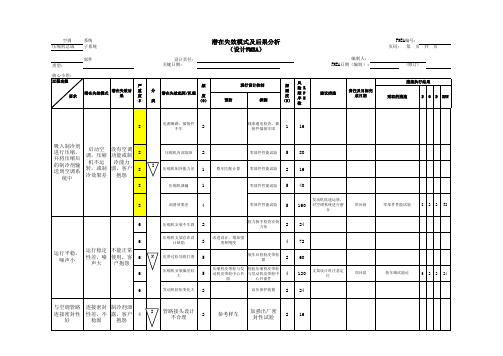
系统 子系统 设计责任: 关键日期:
潜在失效模式及后果分析 (设计FMEA)
编制人: FMEA日期(编制):
FMEA编号: 页码: 第 页
共
页
部件 年度车型/车辆类型: 核心小组:
过程功能 严 潜在失效后 重 潜在失效模式 果 度 (S )
(修订)
频 分 类 潜在失效起因/机理 度 (O)
N
压缩机安装不牢固
2 3 5 5 2
改进设计,增加强 度和刚度
扭力扳手检查安装 力矩
2 4
24 72 60 120 24
支架设计时注意定 位 项目组 装车路试验证 6 2 2 24
压缩机支架存在设 计缺陷
皮带过松导致打滑
装车后检验皮带松 紧 压缩机皮带轮与发 检验压缩机皮带轮 动机皮带轮中心共 与发动机皮带轮中 面 心共面性 高压保护装置
现行设计控制
要求(D)
风 险 R 顺 P 序 N 数
措施执行结果 建议措施 责任及目标完 成日期
采取的措施
S
O
D
RPN
8
电源断路,插接件 不牢
2
线束通电检查,插 接件插接牢固
1
16
吸入制冷剂 启动空 没有空调 进行压缩, 调,压缩 功能或制 并将压缩后 机不运 冷能力 的制冷剂输 转,或制 弱,客户 送到空调系 冷效果差 抱怨 统中
8 8 8
I
压缩机内部故障
2 1 1
整车匹配计算
零部件性能试验
5 2 5
80 16 40
发动机低速运转, 对空调系统进行磨 合
压缩机制冷能力差
零部件性能试验
压缩机泄漏
零部件性能试验
新版FMEA第五版2019版FMEA:设计DFMEA全解
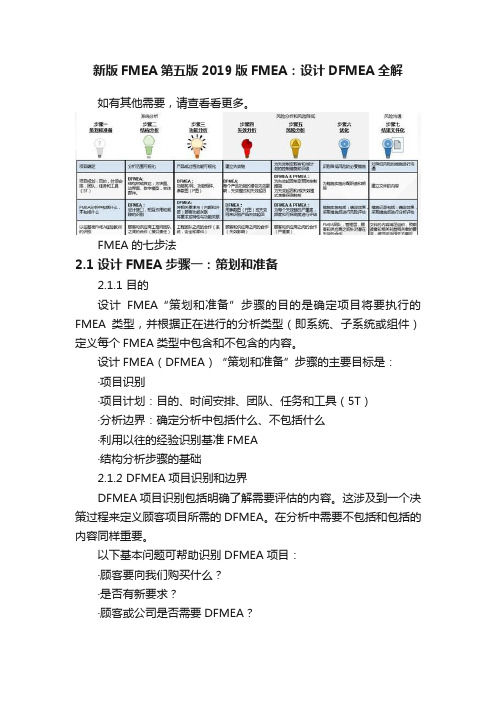
新版FMEA第五版2019版FMEA:设计DFMEA全解如有其他需要,请查看看更多。
FMEA的七步法2.1 设计FMEA步骤一:策划和准备2.1.1 目的设计FMEA“策划和准备”步骤的目的是确定项目将要执行的FMEA类型,并根据正在进行的分析类型(即系统、子系统或组件)定义每个FMEA类型中包含和不包含的内容。
设计FMEA(DFMEA)“策划和准备”步骤的主要目标是:·项目识别·项目计划:目的、时间安排、团队、任务和工具(5T)·分析边界:确定分析中包括什么、不包括什么·利用以往的经验识别基准FMEA·结构分析步骤的基础2.1.2 DFMEA项目识别和边界DFMEA项目识别包括明确了解需要评估的内容。
这涉及到一个决策过程来定义顾客项目所需的DFMEA。
在分析中需要不包括和包括的内容同样重要。
以下基本问题可帮助识别DFMEA项目:·顾客要向我们购买什么?·是否有新要求?·顾客或公司是否需要DFMEA?·我们是否制造产品、并拥有设计控制权?·我们是否购买产品、并拥有设计控制权?·我们是否购买产品、但不拥有设计控制权?·谁负责接口设计?·我们是否需要系统、子系统、组件或其它层面的分析?对这些问题和公司定义的其他问题的回答有助于创建所需的设计FMEA项目清单,从而确保了方向、承诺和工作重点的一致性。
以下可有助于团队定义边界,适用于:·法律要求 / 技术要求·顾客需求/需要/期望(内部和外部顾客)·要求规范·类似项目图表(方块图/边界图)·示意图、图纸和/或3D模型·物料清单、风险评估·类似产品曾用的FMEA·防错要求、可制造性和可装配性设计(DFM/A)·质量功能展开(QFD)在界定FMEA范围时,如适用,以下方面可能被考虑:·技术新颖性/创新程度·质量/可靠性历史(内部、零公里、现场失效、类似产品的保修和保险索赔)·设计复杂性·人员和系统的安全·网络物理系统(包括网络安全)·法律合规性·目录和标准零件2.1.3 DFMEA项目计划确定设计FMEA项目后,应立即制定DFMEA的执行计划。
dfmea定义

D-FMEA定义1. 简介故障模式与效应分析(Design Failure Mode and Effects Analysis,简称D-FMEA)是一种旨在通过识别和评估可能的故障模式及其潜在影响,从而改进和增强产品、系统或过程的可靠性的方法。
它是一种高效的风险管理工具,可以在产品设计阶段早期识别和纠正潜在的设计问题,并制定相应的预防和纠正措施。
2. D-FMEA的目的D-FMEA的目的是通过系统性分析和评估潜在的故障模式及其可能的影响,以降低风险并提高产品的可靠性。
它的主要目标包括:•识别和分析潜在的故障模式,了解其可能的原因和影响;•评估故障的严重程度、概率和检测能力;•确定并实施预防和纠正措施,以减少故障的发生和影响;•提供参考资料,指导和改进设计、生产和服务过程;•增强团队成员之间的合作和沟通。
3. D-FMEA的步骤D-FMEA通常包含以下步骤:3.1 确定D-FMEA的范围确定D-FMEA的范围是指明分析的领域和具体对象。
这可以是一个产品、系统或过程。
准确定义范围是确保分析的有效性和准确性的关键步骤。
3.2 创建D-FMEA团队组建一个由专业人员组成的D-FMEA团队,该团队应包含具有相关专业知识和经验的成员。
团队成员应代表不同的领域,如设计、工程、质量控制等。
3.3 识别潜在的故障模式团队成员使用头脑风暴和其他适当的方法,识别可能的故障模式。
这包括产品功能的不正常失效或系统中的潜在问题等。
3.4 评估故障的严重程度、概率和检测能力团队对每个故障模式评估其严重程度、概率和检测能力。
严重程度指的是故障对产品或系统性能的影响程度,概率是指故障发生的可能性,检测能力是指故障是否可以被及早发现。
3.5 制定预防和纠正措施基于对潜在故障模式的评估,团队提出相应的预防和纠正措施。
预防措施旨在防止故障发生,而纠正措施旨在减少故障影响。
3.6 实施和跟踪措施团队将制定的预防和纠正措施纳入产品设计、开发和生产过程中,并跟踪实施的效果。
DFMEA是什么意思

DFMEA是什么意思
DFMEA是什么意思
在设计和制造产品时,FMEA是一种可靠性设计的重要方法。
它实际上是FMA(故障模式分析)和FEA(故障影响分析)的组合。
它对各种可能的风险进行评价、分析,以便在现有技术的基础上消除这些风险或将这些风险减小到可接受的水平。
及时性是成功实施FMEA的'最重要因素之一,它是一个“事前的行为”,而不是“事后的行为”。
为达到最佳效益,FMEA必须在故障模式被纳入产品之前进行.
设计FMEA(也记为d-FMEA ,Design Failure Mode and Effects Analysis )应在一个设计概念形成之时或之前开始,并且在产品开发各阶段中,当设计有变化或得到其他信息时及时不断地修改,并在图样加工完成之前结束。
其评价与分析的对象是最终的产品以及每个与之相关的系统、子系统和零部件。
需要注意的是,d-FMEA在体现设计意图的同时还应保证制造或装配能够实现设计意图。
因此,虽然d-FMEA不是靠过程控制来克服设计中的缺陷,但其可以考虑制造/装配过程中技术的/客观的限制,从而为过程控制提供了良好的基础。
【DFMEA是什么意思】。
汽车空调控制面板DFMEA
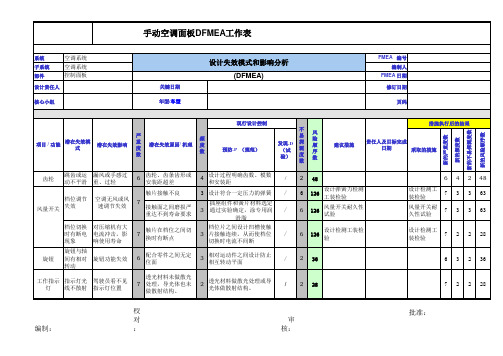
频 潜在失效原因/ 机理 度
数
现行设计控制 预防-P (规范)
不 易 发现-D 探 (试 测 验) 度 数
风 险 顺 序 数
措施执行后的结果
建议措施
责任人及目标完成
日期
采取的措施
齿轮
跳齿或运 漏风或手感过 动不平滑 重、过轻
齿轮、齿条齿形或 6 安装距超差
4
设计过程明确齿数、模数 和安装距
/
触片接触不良
6
126
风量开关耐久性 试验
6
126
设计检测工装检 验
2 36
2 28
6 4 2 48
设计检测工 装检验
7
3
3
63
风量开关耐 久性试验
7
3
3
63
设计检测工 装检验
7
2
2
28
6 3 2 36
7 2 2 28
校
对
编制:
:
审 核:
批准:
手动空调面板DFMEA工作表
系统 子系统 部件
空调系统 空调系统 控制面板
设计责任人
核心小组
关键日期 年型/车型
设计失效模式和影响分析 (DFMEA)
FMEA 编号 编制人
FMEA 日期 修订日期
页码
新的严重度数 新的频度数 新的不易探测度数 新的风险顺序数
项目 / 功能
潜在失效模 式
潜在失效影响
严 重 度 数
切换时电流不间断
/
旋钮
旋钮与轴 间有相对 旋钮功能失效 转动
6
配合零件之间无定 位面
3
相对运动件之间设计防止 相互转动平面
/
工作指示 指示灯光 驾驶员看不见 灯 线不散射 指示灯位置
DFMEA和PFMEA评分原则

很高
没有前期历史的新技术/新设计
≥100/1000
≥1/10
10
高
在工作循环/操作条件内,对于新设计、新应用或变更,失效是不可避免的
50/1000
1/20
9
在工作循环/操作条件内,对于新设计、新应用或变更,失效是可能的
20/1000
1/50
8
在工作循环/操作条件内,对于新设计、新应用或变更,失效是不确定的
4
中等偏高
在来源处探测问题
通过自动控制探测不规范的零件,自动封锁零件,防止零件进入下一步流程,在本岗位上实施失效模式的探测
3
高
错误探测和/或问题预防
通过自动控制防止不规范零件的生产,在岗位上实施错误(原因)的探测
2
很高
探测不适用;错误预防
有预防错误(原因)的夹具设计,机械设计或零件设计。由于过程/产品的防错设计,不规范零件无法生产
一部分产品必须废弃。偏离基本过程,包括降低生产线速度或增人力
7
中等中断
100%的产品必须离线返工后再被接受
6
一部分产品必须离线返工后被接受
5
中等中断
100%的产品在处理前,必须在线返工
4
一部分产品在处理前,必须在线返工
3
微小中断
对过程,操作或操作员造成轻微的不便
2
没有影响
没有可识别的影响
1
表5 PFMEA发生度(O)评价标准
1
几乎可以确定
表4 PFMEA严重度数(S)评价标准
影响/后果
对产品的影响严重性
(对制造/装配的影响)
严重度
不符合安全性或者法规要求
会使操作员身处危险(机械或装配),失效发生时无预警
DFMEA讲解
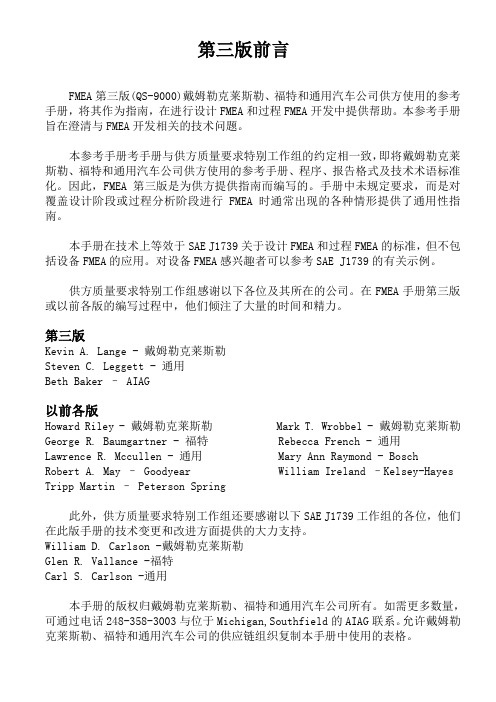
第三版前言FMEA第三版(QS-9000)戴姆勒克莱斯勒、福特和通用汽车公司供方使用的参考手册,将其作为指南,在进行设计FMEA和过程FMEA开发中提供帮助。
本参考手册旨在澄清与FMEA开发相关的技术问题。
本参考手册考手册与供方质量要求特别工作组的约定相一致,即将戴姆勒克莱斯勒、福特和通用汽车公司供方使用的参考手册、程序、报告格式及技术术语标准化。
因此,FMEA第三版是为供方提供指南而编写的。
手册中未规定要求,而是对覆盖设计阶段或过程分析阶段进行FMEA时通常出现的各种情形提供了通用性指南。
本手册在技术上等效于SAE J1739关于设计FMEA和过程FMEA的标准,但不包括设备FMEA的应用。
对设备FMEA感兴趣者可以参考SAE J1739的有关示例。
供方质量要求特别工作组感谢以下各位及其所在的公司。
在FMEA手册第三版或以前各版的编写过程中,他们倾注了大量的时间和精力。
第三版Kevin A. Lange - 戴姆勒克莱斯勒Steven C. Leggett - 通用Beth Baker – AIAG以前各版Howard Riley - 戴姆勒克莱斯勒 Mark T. Wrobbel - 戴姆勒克莱斯勒George R. Baumgartner - 福特 Rebecca French - 通用Lawrence R. Mccullen - 通用 Mary Ann Raymond - BoschRobert A. May – Goodyear William Ireland –Kelsey-Hayes Tripp Martin – Peterson Spring此外,供方质量要求特别工作组还要感谢以下SAE J1739工作组的各位,他们在此版手册的技术变更和改进方面提供的大力支持。
William D. Carlson -戴姆勒克莱斯勒Glen R. Vallance -福特Carl S. Carlson -通用本手册的版权归戴姆勒克莱斯勒、福特和通用汽车公司所有。
汽车DFMEA管理程序
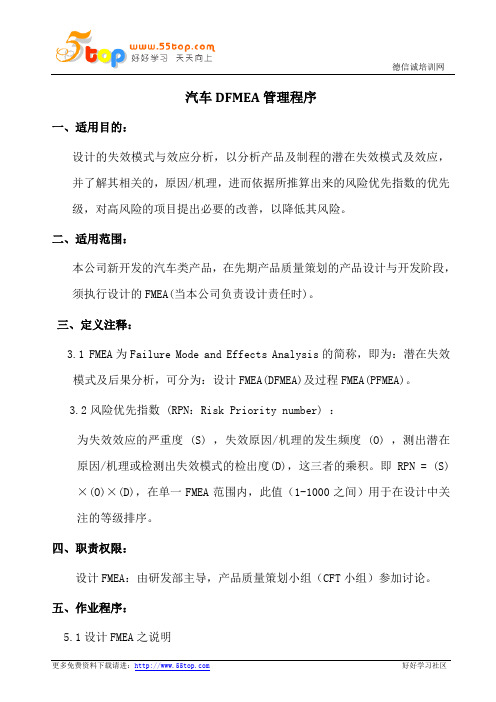
汽车DFMEA管理程序一、适用目的:设计的失效模式与效应分析,以分析产品及制程的潜在失效模式及效应,并了解其相关的,原因/机理,进而依据所推算出来的风险优先指数的优先级,对高风险的项目提出必要的改善,以降低其风险。
二、适用范围:本公司新开发的汽车类产品,在先期产品质量策划的产品设计与开发阶段,须执行设计的FMEA(当本公司负责设计责任时)。
三、定义注释:3.1 FMEA为Failure Mode and Effects Analysis的简称,即为:潜在失效模式及后果分析,可分为:设计FMEA(DFMEA)及过程FMEA(PFMEA)。
3.2风险优先指数 (RPN:Risk Priority number) :为失效效应的严重度 (S) ,失效原因/机理的发生频度 (O) ,测出潜在原因/机理或检测出失效模式的检出度(D),这三者的乘积。
即RPN = (S)×(O)×(D),在单一FMEA范围内,此值(1-1000之间)用于在设计中关注的等级排序。
四、职责权限:设计FMEA:由研发部主导,产品质量策划小组(CFT小组)参加讨论。
五、作业程序:5.1设计FMEA之说明5.1.1设计的FMEA是一种分析技术,主要是由负责设计的工程师/团队来使用,他们把DFMEA当做“在可能的范围内,确保潜在失效模式及其相关的原因/机理都已经被考虑及强调”的一种方法。
5.1.2最终完成品,连同其每一个相关系统、子系统及物料,皆应被评估。
5.1.3设计FMEA是工程师/团队针对零件、子系统或系统设计的所有意见之摘要 (包含依据经验及过去所关心的事项,来分析出产品设计风险,潜在失效及后果分析)。
5.2设计FMEA的使用时机在先期产品质量策划(APQP)之构想阶段(第一阶段),先将客户的期望转换成需求,再将产品设计与开发阶段(第二阶段)导入设计FMEA。
5.3设计FMEA:5.3.1设计FMEA过程的开始,是要先发展出一份清单,内容描述设计预期做什么 (即:列出该产品应有之功能、客户想要的或需要的),以及什么是不希望发生的(即:不希望发生的现象、可包含过去的客户抱怨、异常现象…等经验)。
设计FMEA(DFMEA)

三、DFMEA是一項活頁文件,在設計階段應完成制訂,並且在生產階段時持續修訂,DFMEA要考慮易製性和易裝性,因此必須靠製程管製法找出設計弱點。
四、DFMEA首先要利用QFD,將顧客需求轉成設計規格,使用功能方塊圖,利用流程方式,將各另組件間的功能關係(輸出、輸入)連貫起來,接著再使用結構樹,將另件層、組件層與系統層依序劃分,作為DFMEA制訂之依據。
2.潛在效應分析
失效模式產生後對功能之影響性,效應分析必須從另件失效後一直探討至產品之影響性,必須要 有整體性,故是一項term work。 嚴重度:失效模式發生後,對本身、上一層組件或顧客之影響程度。要降低嚴重度,唯有透過設計變更。
3.潛在失效原因
失效原因是一項設計弱點的指標,設計弱點的結果就是失效模式。 發生度:失效原因發生之可能機率。透過設計變更,可以降低發生度。
3.在設計發展階段,增加失效模式和系統效應分析的次數。
4.提供另一項分析方法,幫助設計者進行有效的驗證規劃。
5.根據對顧客需求的影響性,列出失效模式的排序,並按序改善。
6.提供一項改善方案,可以減少矯正與追查的活動。
7.提供更好的參考資料,協助現場解決問題,評估設計變更和發展進一步的設計。
6.嚴重度在9分及10分者,不論RPN之分數,應優 先改進,接著依RPN之高低逐項改善,改進步驟依降低嚴重度,發生度與難檢度之順利進行。
難檢度:失效模式及失效原因被偵測出之能力(在另組件生產之前)。為降低難檢度,適當的設計管制措施必須加以改進。
5.RPN
6.矯正措施
j增加設計驗證或確認,可以降低難檢度。
设计潜在失效模式及影响(DFMEA)的分析理解与应用
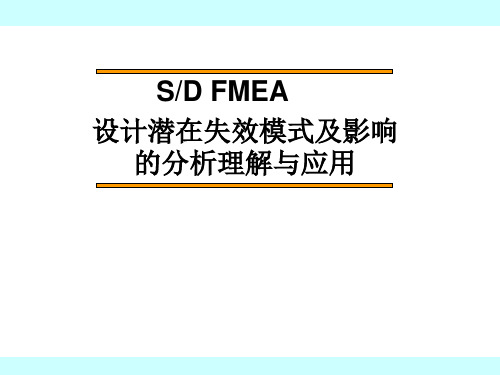
课程回顾
一.FMEA背景知识 二.实施FMEA的原因 三.实施FMEA的步骤
谢 谢!
1.FMEA基本知识—常规的设计思路
当前是怎么设计的 ? 可能会发生哪些问题 ? 这些问题会导致什么后果 ? 当前采用什么办法控制 ?
效果如何 ? 还需要做什么 ?
过去发生过 什么问题? 还会发生什 么问题? 经验积累
设计实准际则上 这设就计是经F验MEA !
冗余设计 工程计算 试验确认
进一步分 析试验确 认设计修 改
E D
B A
G
C
H
F
实施实例——活塞DFMEA
• 活塞组的边界图
3)接 口 矩 阵
• 接口矩阵是用适当的方法表示系统接口相关 性的工具。用以显示接口所表示的组件、零 部件之间的关系是正相关的还是负相关的。
实施实例——活塞DFMEA
• 活塞组的接口矩阵
4)P 图
• P图是用于确定和描述噪声控制因素和错误状 态的健壮性工具。
干扰因子
输入信号
系统描述 控制因子
理想功能 错误状态
实施实例——活塞组DFMEA
2.FMEA 实施流程
确定分析对象
鉴别故障模式
故障影响
鉴别故障原因
严重度
频度
风险顺序数 接下页
预先控制措施 探测度
2.FMEA 实施流程
接上页
是否要 纠正?
是
确定纠正措施
确定责任人和完 成日期
纠正措施效果判 定
是否满
S/D FMEA
设计潜在失效模式及影响 的分析理解与应用
主要内容
一.FMEA背景知识 二.为什么要实施FMEA? 三.如何实施FMEA?
- 1、下载文档前请自行甄别文档内容的完整性,平台不提供额外的编辑、内容补充、找答案等附加服务。
- 2、"仅部分预览"的文档,不可在线预览部分如存在完整性等问题,可反馈申请退款(可完整预览的文档不适用该条件!)。
- 3、如文档侵犯您的权益,请联系客服反馈,我们会尽快为您处理(人工客服工作时间:9:00-18:30)。
7
▲
设计人员对车体连 接结构运用不合理
2
3
42
扣压角度
扣压角度设计不合 理 1、海绵管位置不合 理 2、海绵管尺寸应用 不合理
车体装车干涉
6
设计人员绘制图纸 时出错 设计人员对整体车 体装配结构考虑不 全面
2
3
36
套海绵护套结构设 计
装夹位置不合理
6
2
3
36
第 1 页,共 2 页
D FMEA
供应商名称 零部件编号 发行等级 设计通知番号 工程机能 作业内容 A 供应商工厂 零部件名称 发行日 图面等级 严 重 级 度 别 H 潜在的故障原因/机 理 1、技术人员在制作 过程中没有认真校 对 2、焊接温度及焊接 时间没有选择恰当 1、使用一定周期未 定时更换 2、作业人员组装时 损坏 管路未清洗,清洗 液使用时间过期; 组装工艺不良,零 部件未保持整洁 流道设计不合理, 存在瓶颈现象 发 生 度 检 出 度 R. P. N. 对策/处理结果 严 发 重 生 度 度 检 出 度 R. P. N. 驾驶室-压缩机管路 供应商代码 项目 再发行的理由 新开发
潜在的故障模式
潜在的故障影响
现行工程管理
建议措施
责任单位
对策实施
焊接
1、焊接角度不正确 1、焊接工装制作失 2、焊缝处有沙眼, 误 管路泄露 2、工人焊接过程中 焊缝有沙眼 密封处O型圈损坏 管路泄露 外观不符合图纸要 求
7
▲
3
1、安排质检人员对工装 制作的跟踪校验 2、加强对技术员的岗位 培训 1、依规定使用寿命更换 2、防呆措施,制作操作 指导书 依照正确顺序作业
3
27
压板的设计
影响产品的装配, 导致管路泄露
7
▲
2
加强对操作人员的技能培 训,增加现场巡检的次数 对不同的密封结构整理专 门的标准图纸,产品加工 时检测实际尺寸是否与产 品图纸吻合 设计人员在设计时利用三 维软件电脑演示装配结构 1、对不同的密封结构及 连接结构整理专门的标准 图纸 2、产品加工时通过对方 部品检验连接性能是否合 理,利用气密实验检验密 封性能 设计人员在设计时利用三 维软件电脑演示装配结构 设计人员在设计时利用三 维软件电脑演示装配结构
3
63
焊接部分泄漏
生产部
加强对焊接的检查
3
3
4
36
O型圈
7
3
2
42
清洁度
管路及零件表面有 污渍
6
2 设计评审DOE
2
24
制冷剂流阻
流阻偏大
蒸发器制冷性能下 降, 达不到顾客要求 管路连接性不好,达 不到空调作用
7
2 1、新产品开发部门整理 出不同的连接方式,以便 选用合适的连接 2、 生产时通过对方部品检验 连接性是否可行
2
28
管路与空调其他管 路连接结构,采用螺 纹连接
管路连接性不好
6
设计人员对连接性 能考虑不全面
2
3
36
-
第 2 页,共 2 页
D FMEA
供应商名称 零部件编号 发行等级 设计通知番号 工程机能 作业内容 A 供应商工厂 零部件名称 发行日 图面等级 严 重 级 度 别 H 潜在的故障原因/机 理 进货检验过程中存 在疏忽或者所选铝 管的尺寸有不符合 要求 1、扣压机压力故障 2、进货检验疏忽 1、设计人员绘制图 纸出错 2、机加工过程中操 作人员失误 设计人员绘制图纸 时出错 发 生 度 2 检 出 度 3 R. P. N. 18 对策/处理结果 严 发 重 生 度 度 检 出 度 R. P. N. 驾驶室-压缩机管路 供应商代码 项目 再发行的理由 新开发
4
56
影响后期装配
生产部
检查图纸,督促自 检巡检
4
4
3
48
端末(凸台旋压)
密封部尺寸设计不 合格
车体装车时密封性 不好
▲ 7
2
3
42
管体走向
弯管形状设计不合 理
车体装车干涉
6
▲
设计人员对整体车 体装配结构考虑不 全面
2
3
36
接头形状及尺寸
1、接头形状设计 不合理 2、接头尺寸设计 不合理
车体装车连接性不 合理,密封性能不 好
潜在的故障模式
潜在的故障影响 折弯后圆弧变形过 大,影响管路的外 观及强度要求
现行工程管理
建议措施
责任单位
对策实施
铝管管路变形
铝管壁厚不均,材 质偏软
3
加强进货检验,提高设计 人员的技能水平
耐爆破
1、管路扣压部紧 2、铝管材质不符 装配尺寸设计不合 格,外观不符合技 术要求
影响管路使用寿命
3
3
1、设备定期维护检查 2、加强进货检验