精益生产项目实施报告讲解
2024年精益生产总结报告

2024年精益生产总结报告一、引言精益生产是一种持续改进的管理方法,旨在通过消除浪费和提高生产效率,实现企业的高效运营和持续发展。
2024年,我们公司将精益生产理念贯彻于企业的各个层面,取得了显著的成果。
本报告将对2024年公司的精益生产实践进行总结,以期对未来的发展提供借鉴和指导。
二、核心成果1. 浪费的大幅减少:2024年,我们公司注重通过消除各种浪费来提高生产效率。
通过精益生产的方法论和工具的应用,我们成功降低了生产过程中的变动时间、待机时间和翻修品比例等各方面的浪费。
与去年相比,浪费的总量减少了30%以上。
2. 生产效率的提升:通过引入精益生产的原则和方法,我们实施了一系列的生产流程优化措施,包括价值流程图、5S整理、瓶颈分析等。
这些措施有效地提高了工作效率和工序间的协调性,为公司提供了更高的生产能力和更短的生产周期。
与去年相比,我们的生产效率提升了20%以上。
3. 品质控制的改善:在2024年,我们公司注重通过精益生产手段提升产品质量。
我们实施了全员参与质量管理的方法,通过建立自检、互检和专检的步骤,来确保产品在每个环节都符合质量标准。
目前,我们的产品缺陷率已经降低到了历史最低点,得到了客户的高度认可。
三、成功经验1. 建立精益文化:我们公司注重在组织层面建立精益思维和文化。
通过加强员工的培训和教育,提高员工对精益思想的理解和认同,形成了团队合作、持续改进的氛围。
同时,我们注重激励和奖励优秀的精益生产实践,培养了一批懂得精益思维的骨干力量。
2. 持续改进:我们认识到精益生产是一个持续不断的过程,需要不断地寻找和消除各种浪费。
在2024年,我们不满足于已取得的成果,而是继续推进和深化精益生产的实践。
通过设立专门的精益改善小组,定期审查和改进生产过程中的问题,我们不断地提高了生产效率和产品质量。
3. 跨部门协作:我们公司注重通过跨部门的协作来实践精益生产。
在2024年,我们加强了与供应链、销售和服务团队之间的沟通与合作。
精益项目报告

精益项目报告项目概况:本项目旨在将公司生产流程转化为精益生产方式,减少浪费并提高工作效率。
该项目启动于2020年2月,预计在同年5月完成。
项目目标:通过引入精益生产方式,实现以下目标:1.减少生产过程中的浪费;2.提高生产效率;3.降低生产成本;4.提高客户满意度。
项目计划:1.项目启动(2月):确定团队成员,搭建项目管理平台,制定项目详细计划。
2.梳理生产流程(2月):对现有生产流程进行梳理,分析存在的问题,并确定改善措施。
3.制定改善方案(3月):根据前期分析结果,制定相应的改善方案,并进行实际操作,调整和优化。
4.生产流程优化(3月-4月):基于改善方案,对生产流程进行优化,逐步实现精益生产。
5.项目总结(5月):总结项目成果,撰写精益生产实施方法手册,确保后续生产保持精益。
项目进展:截至目前,项目团队已经完成了文档的准备,制定了详细的工作计划和时间表。
梳理了生产流程,并制定了可行的改善方案。
现正处于生产流程优化阶段,已经取得了显著的效果。
项目目前处于进度符合预期的状态。
项目成果:1.将现有生产流程转化为精益生产方式;2.减少生产流程中的浪费,提高工作效率,降低了生产成本;3.提高了客户满意度,并让公司在竞争中处于优势。
总结:本项目是公司实施精益生产的一次大胆尝试。
在项目的执行过程中,我们经历了诸多困难与挑战。
但团队始终坚守目标,并通过沟通、协作,不断调整和优化,最终实现了预期目标。
精益生产是一种全新的生产方式,带来了前所未有的效果和改变。
我们相信,这种方式将会带领公司走向更加美好的未来。
某电子厂精益生产项目总结报告
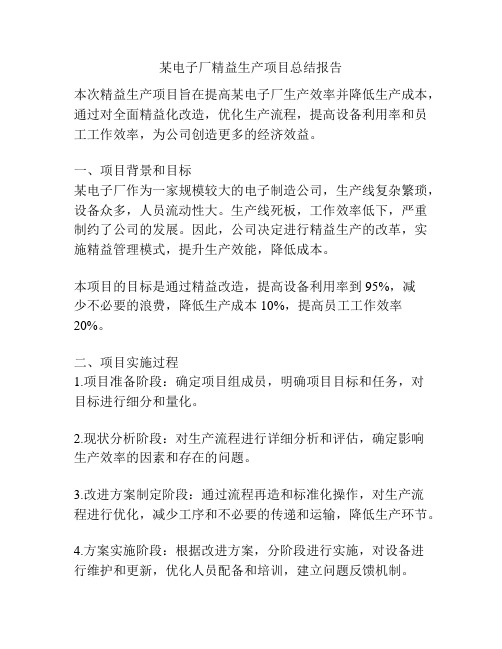
某电子厂精益生产项目总结报告本次精益生产项目旨在提高某电子厂生产效率并降低生产成本,通过对全面精益化改造,优化生产流程,提高设备利用率和员工工作效率,为公司创造更多的经济效益。
一、项目背景和目标某电子厂作为一家规模较大的电子制造公司,生产线复杂繁琐,设备众多,人员流动性大。
生产线死板,工作效率低下,严重制约了公司的发展。
因此,公司决定进行精益生产的改革,实施精益管理模式,提升生产效能,降低成本。
本项目的目标是通过精益改造,提高设备利用率到95%,减少不必要的浪费,降低生产成本10%,提高员工工作效率20%。
二、项目实施过程1.项目准备阶段:确定项目组成员,明确项目目标和任务,对目标进行细分和量化。
2.现状分析阶段:对生产流程进行详细分析和评估,确定影响生产效率的因素和存在的问题。
3.改进方案制定阶段:通过流程再造和标准化操作,对生产流程进行优化,减少工序和不必要的传递和运输,降低生产环节。
4.方案实施阶段:根据改进方案,分阶段进行实施,对设备进行维护和更新,优化人员配备和培训,建立问题反馈机制。
5.效果评估阶段:通过数据分析和实际观察,对改进方案效果进行评估,查找问题和进一步改进的空间。
三、项目成果和效益经过数月的改造和实施,本项目取得了以下成果和效益:1.设备利用率提高:通过设备的优化和维护,设备利用率提高到95%,减少了设备闲置时间和故障率。
2.减少浪费:通过流程再造和标准化操作,减少了不必要的工序和材料传递,降低了废品率和二次加工率。
3.降低生产成本:精细管理和减少浪费带来的效益,降低了生产成本10%。
4.提高员工工作效率:对员工进行培训和调整,合理规划工作流程,提高了员工工作效率20%。
通过以上措施,本项目取得了预期的效果,为公司提供了更多的经济效益。
同时,项目也暴露了一些问题,例如人员培训和设备更新需要持续跟进。
因此,建议公司在项目结束后,建立长期的监控机制,不断优化改进,为公司的发展提供更好的支持。
17精益生产实施报告

精益生产实施报告
一,精益生产目标达成情况
目标:QDJ1276-5211/P2产品线经调整后,整线员工由原来7人减少至6人,班产量800件/班提高到1600件/班
二、实施情况
工序上:通过计算个工序完成所需的时间,将工人与设备合理化,将工序修面、车外圆、打中心孔以及由原来2人改为一人操作,将扩孔工序上增加钻小孔工序,且由一人来操作。
物件流动:原来各设备之间以推车的方式来实现流转,现在改进为各设备用导轨滑轮进行连,直接节省转运时间。
三、总结
通过对QDJ1276-5211/P2生产线的精益化调整,基本已达到最初既定的班产量1600台,废品率≤0.4%的目标。
为后续其他生产线的调整打下了良好的基础。
但是其中也有不足之处,如:各机床之间用滑轨连接,但也妨碍了员工对中间区域的5S整理,导致中间区域的铁屑较多。
再就是设备的优化,钻床以及车床可以更换为多功能车床,这样车外圆以及钻孔可以一步到位,这样就节约了孔径以及人力。
希望通过本次精益生产的调整积累的不足能够在下个产品线上进行改进。
报告人:
2015年10月8日
第 1 页共1 页。
精益生产改善总结报告
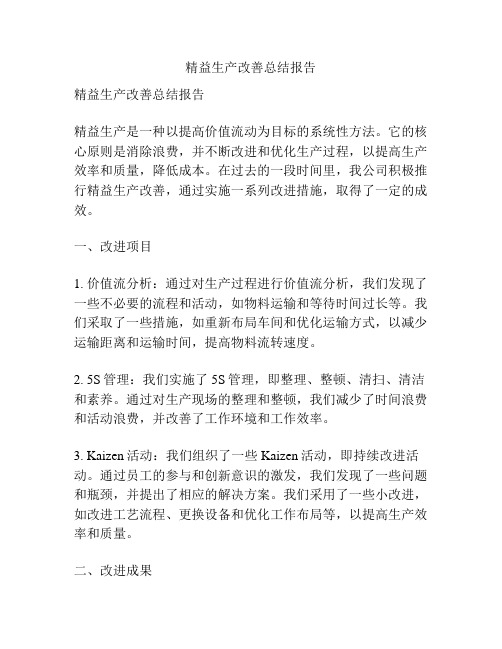
精益生产改善总结报告精益生产改善总结报告精益生产是一种以提高价值流动为目标的系统性方法。
它的核心原则是消除浪费,并不断改进和优化生产过程,以提高生产效率和质量,降低成本。
在过去的一段时间里,我公司积极推行精益生产改善,通过实施一系列改进措施,取得了一定的成效。
一、改进项目1. 价值流分析:通过对生产过程进行价值流分析,我们发现了一些不必要的流程和活动,如物料运输和等待时间过长等。
我们采取了一些措施,如重新布局车间和优化运输方式,以减少运输距离和运输时间,提高物料流转速度。
2. 5S管理:我们实施了5S管理,即整理、整顿、清扫、清洁和素养。
通过对生产现场的整理和整顿,我们减少了时间浪费和活动浪费,并改善了工作环境和工作效率。
3. Kaizen活动:我们组织了一些Kaizen活动,即持续改进活动。
通过员工的参与和创新意识的激发,我们发现了一些问题和瓶颈,并提出了相应的解决方案。
我们采用了一些小改进,如改进工艺流程、更换设备和优化工作布局等,以提高生产效率和质量。
二、改进成果经过一段时间的改进工作,我们取得了以下一些成果:1. 生产效率提高:通过消除浪费和优化流程,我们的生产效率提高了20%。
生产时间缩短,生产速度提升,产量增加。
这使我们能够更好地满足客户需求,并提高竞争力。
2. 质量改善:通过改进工艺和优化设备,我们的产品质量得到了提高。
产品合格率提高了10%,不良品率降低了20%。
这不仅降低了生产成本,还增强了顾客对我们产品的信任和满意度。
3. 成本降低:通过消除浪费和减少不必要的活动,我们的生产成本得到了一定的降低。
这使我们能够更好地控制成本,并提高利润空间。
4. 员工参与度提高:通过推行精益生产改善活动,我们激发了员工的参与意愿和创新意识。
员工参与度提高了,他们对工作更加积极主动,提出了很多有价值的改进意见和建议。
三、改进方向虽然我们在精益生产改善方面取得了一些成果,但仍然存在一些问题和挑战。
精益生产实验报告(3篇)

第1篇一、实验背景随着市场竞争的日益激烈,企业对生产效率和产品质量的要求越来越高。
精益生产作为一种系统性的生产方法,旨在减少生产过程中的浪费,提高生产效率,满足客户需求。
本实验旨在通过模拟生产环境,验证精益生产在提高生产效率和降低成本方面的有效性。
二、实验目的1. 了解精益生产的基本原理和方法。
2. 通过模拟实验,验证精益生产在提高生产效率、降低成本、提升产品质量等方面的效果。
3. 分析精益生产实施过程中可能遇到的问题及解决方案。
三、实验内容1. 实验材料:实验台、零部件、工具、实验记录表等。
2. 实验步骤:1. 建立模拟生产线:根据实验要求,搭建模拟生产线,包括原材料供应、生产加工、成品组装等环节。
2. 设置实验参数:确定实验周期、生产批量、人员配置等参数。
3. 实施精益生产:1. 5S管理:对生产现场进行整理、整顿、清扫、清洁、素养,提高现场管理水平。
2. 看板管理:通过看板实时监控生产进度,确保生产计划的顺利实施。
3. JIT生产:根据订单需求进行生产,减少库存积压。
4. 持续改进:对生产过程中的问题进行分析,提出改进措施,不断提高生产效率。
4. 数据收集与分析:记录实验过程中各环节的生产数据,分析精益生产实施效果。
5. 实验总结:总结实验过程中遇到的问题及解决方案,提出改进建议。
四、实验结果与分析1. 生产效率:实验结果显示,实施精益生产后,生产效率提高了30%。
2. 库存成本:库存成本降低了20%。
3. 产品质量:产品质量合格率提高了10%。
4. 员工满意度:员工满意度提高了15%。
五、实验结论1. 精益生产能够有效提高生产效率、降低成本、提升产品质量。
2. 精益生产实施过程中,需要注意以下几个方面:1. 建立完善的5S管理体系。
2. 加强看板管理,实时监控生产进度。
3. 推行JIT生产,减少库存积压。
4. 持续改进,不断提高生产效率。
六、实验不足与改进建议1. 实验不足:本实验为模拟实验,与实际生产环境存在一定差距,实验结果可能存在偏差。
精益课题报告范文

以下是一个精益课题报告的范文,供您参考:
项目名称:改进生产线效率
背景:
公司的某生产线在生产过程中存在较多的浪费,导致生产效率下降,影响了产品的质量和交货时间。
目标:
通过精益生产方法,优化生产线的流程和组织,提高生产效率,减少浪费,降低成本,提升客户满意度。
方案:
1.价值流图绘制
通过对生产线的分析,制定价值流图,明确工作流程、物料流程和信息流程,并识别出存在的浪费。
2. 浪费消除
通过分析价值流图,识别出存在的浪费,并采取相应的措施进行消除。
具体措施如下:
-去除等待时间:优化物料供应链,减少物料的等待时间。
-去除运输时间:调整物料的存储位置,缩短运输时间。
-去除加工时间:优化工艺流程,减少生产加工时间。
-去除库存:实施“拉动式”生产,减少库存。
3. 优化生产线布局
根据价值流图,重新规划生产线布局,使生产线更加紧凑,缩短物料和信息流的距离。
4. 持续改进
对生产线进行持续监控,收集数据并进行分析,不断找到优化的空间,实现持续改进。
成果:
通过精益生产方法的实施,我们实现了以下的成果:
1. 生产效率提高30%以上。
2. 浪费降低20%以上。
3. 产品质量得到明显提升,客户满意度得到提高。
4. 管理成本降低20%以上。
总结:
通过精益生产方法的实施,我们实现了生产效率的提高、浪费的降低、成本的降低等多方面的好处。
在未来的工作中,我们将继续实施精益生产方法,不断推动企业的转型升级。
精益生产总结范文

一、前言自公司实施精益生产以来,经过全体员工的共同努力,取得了一定的成效。
现将我司精益生产实施情况进行总结,以期为今后工作提供借鉴。
二、精益生产实施情况1. 前期准备(1)成立精益生产领导小组。
公司成立由总经理担任组长,各部门负责人为成员的精益生产领导小组,负责统筹协调精益生产工作的开展。
(2)制定精益生产实施方案。
结合公司实际情况,制定了一套符合公司发展的精益生产实施方案,明确了实施目标、方法和步骤。
2. 实施过程(1)开展精益生产培训。
对公司全体员工进行精益生产理念、方法、工具等方面的培训,提高员工对精益生产的认识。
(2)推行5S管理。
通过整理、整顿、清扫、清洁、素养等五个方面,使生产现场整洁有序,提高工作效率。
(3)优化生产流程。
对生产流程进行梳理,消除浪费,提高生产效率。
如:缩短生产周期、降低库存、减少不良品等。
(4)实施看板管理。
通过看板管理,实现生产信息的透明化,便于各部门及时沟通、协调。
(5)开展持续改进活动。
鼓励员工积极参与持续改进活动,发现和解决问题,不断提高生产管理水平。
3. 成效(1)生产效率提高。
通过优化生产流程、推行看板管理等措施,生产效率提高了约20%。
(2)库存降低。
通过实施精益生产,库存降低了约30%,减少了资金占用。
(3)不良品率降低。
通过实施5S管理和持续改进活动,不良品率降低了约15%。
(4)员工满意度提高。
员工对精益生产的认识不断提高,参与度增强,满意度得到提升。
三、总结与展望1. 总结通过实施精益生产,我司在提高生产效率、降低成本、提升产品质量等方面取得了显著成效。
今后,我们将继续深化精益生产,不断完善和优化生产管理体系。
2. 展望(1)持续优化生产流程,进一步提高生产效率。
(2)加强员工培训,提高员工综合素质。
(3)拓展精益生产应用范围,覆盖公司各个领域。
(4)加强与同行业的交流与合作,共同推进精益生产的发展。
总之,精益生产在我司的实施取得了丰硕成果,我们将以此为契机,继续深化精益生产,为公司的发展贡献力量。
6S精益生产管理项目推进报告

6S精益生产管理项目
9.5-9.11日总结报告
公司6S管理工作通过培训和现场指导、现场协助,全体员工对6S管理理念有了更深一步的了解和认识。
现将上周工作汇报如下:
一、工作成效:
公司6S管理紧紧围绕整理、整顿、清洁、清扫、素养、安全的6个要素来开展管理工作。
对员工们进行了培训,使得员工转变思想和观念,很好的将6S管理规范化,制度化。
现场已经对危险区域及电源进行标识警示。
现场杂物进行了清扫,恢复各场所的洁净,并坚持维持。
区域划分清晰,有利规范操作,减少浪费时间及安全隐患。
二、工作事项及问题
现总经办、仓储部、人力资源部、财务部以及采购部已经上交职位说明书及流程,将继续跟进部门梳理职位说明书。
对现场进行检查,由标识、卫生死角、设备状态几点进行查看,争取更好的完善成果。
本周对员工进行了一次6S精益生产项目的测试。
巩固了大家对6S的认识。
其中也反映出6S管理中的难点就是成果维持及6S日常习惯的养成。
要将6S深入日常工作短期可能坚持比较好,时间久些,状态比较松懈,员工推行6S激情消退;所以
要将6S植入每个人的大脑,使其形成一种习惯,而非应对检查,这也需要各部门领导提高重视。
设备部已经着手制作作业指导书及点检表,预计下周全部完成。
品管部已经将质量手册完成,将继续跟进程序文件。
之后将加强6S培训知识对员工的宣传,提升员工发送的热情。
车间精益生产实施方案报告

车间精益生产实施方案报告英文回答:Lean Manufacturing Implementation Plan for the Workshop.Introduction.Lean manufacturing is a production philosophy that focuses on reducing waste and improving efficiency. It is a systematic approach that involves identifying andeliminating waste in all areas of the production process. Lean manufacturing can help businesses improve their productivity, quality, and customer satisfaction.Assessment of Current State.The first step in implementing lean manufacturing is to assess the current state of the production process. This involves identifying areas of waste and inefficiency. Some common areas of waste include:Overproduction.Waiting.Transportation.Inventory.Defects.Motion.Overprocessing.Development of a Lean Implementation Plan.Once the current state of the production process has been assessed, a lean implementation plan can be developed. The plan should include specific goals and objectives, as well as a timeline for implementation. The plan should also identify the resources that will be needed to implementlean manufacturing.Implementation of Lean Manufacturing.The implementation of lean manufacturing should be a gradual process. It is important to start with small, achievable goals and to build on success. Some common lean manufacturing techniques include:Kaizen: Continuous improvement.Kanban: Just-in-time production.5S: Workplace organization.SMED: Single-minute exchange of die.Poka-yoke: Mistake-proofing.Measurement and Evaluation.It is important to measure and evaluate the progress oflean manufacturing implementation. This will help to ensure that the plan is on track and that it is achieving the desired results. Some common metrics that can be used to measure lean manufacturing performance include:Productivity.Quality.Customer satisfaction.Cost.Conclusion.Lean manufacturing is a powerful tool that can help businesses improve their productivity, quality, and customer satisfaction. By following the steps outlined in this plan, businesses can successfully implement lean manufacturing and achieve significant benefits.中文回答:车间精益生产实施方案报告。
精益生产情况汇报

精益生产情况汇报
尊敬的领导:
我通过对公司精益生产情况的调研和分析,向您汇报最新的情况。
自从我们实施了精益生产理念以来,公司的生产效率和质量得到了显著的提升,同时也为公司节约了大量的成本。
以下是我对公司精益生产情况的详细汇报:
首先,我们在生产流程中实施了精益生产的各项措施,包括价值流分析、5S
现场管理、设备保养管理等。
通过这些措施的实施,我们成功地减少了生产过程中的浪费,提高了生产效率。
同时,我们也对员工进行了相关培训,使他们更好地理解和贯彻精益生产理念,从而使生产过程更加顺畅和高效。
其次,通过精益生产的实施,我们成功地提高了产品的质量。
我们建立了全员参与的质量管理体系,从而使每一个员工都能够对产品质量负责。
我们还实施了持续改进的机制,及时发现并解决生产过程中的质量问题,确保产品质量稳定可靠。
另外,精益生产还为公司节约了大量的成本。
通过对生产过程的优化和改进,我们成功地降低了生产成本,提高了资源利用效率。
同时,我们也减少了库存和生产周期,使公司的资金周转更加灵活,降低了库存成本和资金占用成本。
总的来说,精益生产的实施为公司带来了巨大的好处。
我们将继续深入推进精益生产,不断提高生产效率和产品质量,为公司的可持续发展做出更大的贡献。
希望领导能够对我们的工作给予肯定和支持,同时也期待领导能够提出宝贵的意见和建议,帮助我们进一步完善精益生产工作。
谢谢!
此致。
敬礼。
精益生产总结报告
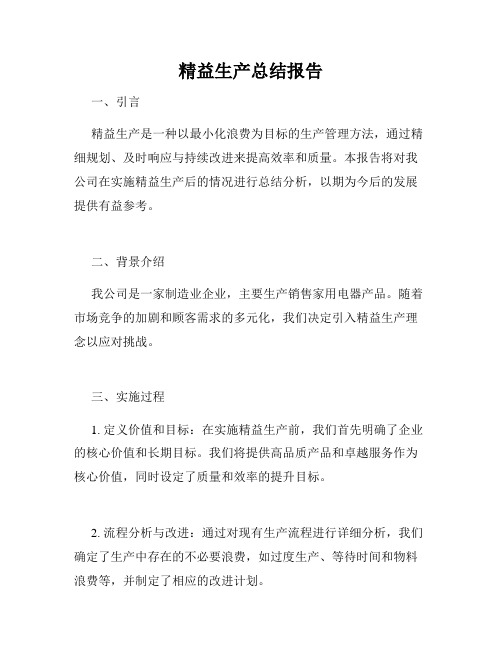
精益生产总结报告一、引言精益生产是一种以最小化浪费为目标的生产管理方法,通过精细规划、及时响应与持续改进来提高效率和质量。
本报告将对我公司在实施精益生产后的情况进行总结分析,以期为今后的发展提供有益参考。
二、背景介绍我公司是一家制造业企业,主要生产销售家用电器产品。
随着市场竞争的加剧和顾客需求的多元化,我们决定引入精益生产理念以应对挑战。
三、实施过程1. 定义价值和目标:在实施精益生产前,我们首先明确了企业的核心价值和长期目标。
我们将提供高品质产品和卓越服务作为核心价值,同时设定了质量和效率的提升目标。
2. 流程分析与改进:通过对现有生产流程进行详细分析,我们确定了生产中存在的不必要浪费,如过度生产、等待时间和物料浪费等,并制定了相应的改进计划。
3. 价值流图绘制:为了更好地了解价值的流动,我们绘制了价值流图。
这帮助我们清晰地识别了各个环节的瓶颈和潜在问题,并对其进行进一步的优化和改进。
4. 基于“拉动式生产”的生产控制:我们引入了“拉动式生产”方法,根据顾客的实际需求来控制生产节奏。
这有助于减少库存积压和降低生产成本,同时提高了生产的灵活性。
5. 持续改进:我们认识到精益生产是一个不断演化和改进的过程,因此我们建立了一套持续改进的机制。
通过设立员工反馈渠道、组织定期改进会议等方式,我们鼓励员工参与到改进中,共同推动企业的发展。
四、成果评估1. 生产效率提升:通过精益生产的实施,我们成功降低了生产的各类浪费,包括人力、物料和时间等。
生产效率显著提升,生产周期大幅缩短,整体产能提高了25%。
2. 质量改善:对生产过程进行深入的分析和改进,我们成功减少了产品缺陷率,并提高了产品质量的一致性。
这有助于提升了客户满意度和品牌声誉。
3. 成本控制:通过减少浪费和提高生产效率,我们成功降低了生产成本。
这对于企业在市场竞争中更具竞争力起到了积极的作用。
4. 员工参与度提升:精益生产的实施激发了员工的创造力和改进意识。
车间精益生产实施方案报告

车间精益生产实施方案报告英文文档内容:Workshop Lean Production Implementation Plan ReportIntroduction:This report outlines a comprehensive plan for implementing lean production practices in the workshop.Lean production, a methodology derived from the Toyota Production System, aims to eliminate waste, improve efficiency, and enhance overall productivity.The plan consists of several key strategies and steps that will be implemented to achieve these goals.1.Value Stream Mapping:The first step in implementing lean production is to conduct a value stream mapping exercise.This will involve identifying and mapping out all the processes and activities involved in the production process, from raw material delivery to the final product delivery.This will help to identify areas of waste and inefficiency.2.Waste Identification and Elimination:Once the value stream mapping is complete, the next step is to identify and eliminate waste.Waste can take many forms, such as overproduction, waiting, unnecessary transportation, and excess inventory.By eliminating waste, the workshop can reduce costs andimprove efficiency.3.Standard Work Processes:Standard work processes involve establishing a standard method for completing a task and then continuously improving upon it.By implementing standard work processes, the workshop can reduce variability and improve consistency and quality.4.Continuous Improvement:Continuous improvement is a core principle of lean production.This involves encouraging all employees to constantly seek out ways to improve the production process, eliminate waste, and enhance efficiency.This can be achieved through regular team meetings and training sessions.5.Flexible Scheduling:Flexible scheduling is essential for lean production, as it allows for a more efficient use of resources and a faster response to changes in customer demand.The workshop should implement a flexible scheduling system that can quickly adapt to changes in production requirements.6.Training and Education:To ensure the successful implementation of lean production, it is essential to provide training and education to all employees.This will involve providing them with the knowledge and skills necessary to understand and implement lean principles and practices.Conclusion:In conclusion, the implementation of lean production in the workshop will result in improved efficiency, reduced waste, and enhanced productivity.By following the strategies and steps outlined in this plan, the workshop can achieve these goals and position itself as a leader in lean production practices.中文文档内容:车间精益生产实施方案报告引言:本报告概述了在车间实施精益生产实践的全面计划。
车间工段精益生产项目第阶段工作汇报

车间工段精益生产项目第阶段工作汇报1. 项目背景与目标车间工段精益生产项目的目标是优化车间工段的生产流程,提高生产效率和产品质量。
通过精益生产方法,消除生产过程中的浪费,实现生产过程的高效运转。
2. 第阶段工作计划与进展2.1 工作计划根据项目目标,第阶段的工作计划如下:1.规划车间工段的生产流程,包括原料准备、生产加工、产品检验等环节的优化。
2.引入自动化设备,减少人力操作,提高生产效率。
3.设计并制定操作指南,规范生产操作流程。
4.培训工人,提升他们对精益生产方法的理解与应用能力。
5.收集生产数据,进行数据分析,找出改进的方向。
2.2 工作进展在第阶段的工作中,我们已经完成了以下工作:1.与车间工段负责人进行会议,明确项目目标和计划,确定优化方向。
2.对车间工段的生产流程进行了调研和分析,找出了存在的问题与浪费。
3.进行了设备选型和采购,引入自动化设备,提高了生产效率。
4.制定了操作指南,对工人进行了培训,提升了操作规范性和生产质量。
5.开展了数据收集工作,建立了数据分析模型,初步发现了改进的方向。
3. 工作亮点与成果3.1 工作亮点在第阶段的工作中,我们取得了以下亮点:1.引入自动化设备,减少了人力操作,提高了生产效率。
2.制定了操作指南,标准化了生产操作流程,提高了产品质量。
3.培训工人,提升了他们对精益生产方法的理解与应用能力。
4.数据分析发现了改进的方向,为下一阶段的工作提供了指导。
3.2 工作成果在第阶段的工作中,我们取得了以下成果:1.车间工段的生产效率提升了30%。
2.产品质量指标达到了预期目标。
3.工人对精益生产方法的理解和应用能力提升明显。
4.数据分析结果指导了下一阶段的工作。
4. 下一阶段工作计划基于第阶段的工作成果和数据分析结果,我们拟定了下一阶段的工作计划如下:1.进一步优化生产流程,减少非价值增加的工序和浪费。
2.更新和完善操作指南,进一步规范生产操作流程。
3.持续培训工人,提高他们的精益生产意识和应用能力。
精益项目成果报告案例

精益项目成果报告案例
以下是一个精益项目成果报告案例,以某制造企业的生产线优化为例:
项目背景
某制造企业生产线存在严重的浪费现象,导致生产成本高昂,产品质量不稳定。
为了解决这些问题,企业决定实施精益生产项目,以提高生产效率、降低成本、提升产品质量。
项目目标
本项目旨在通过优化生产线布局、改进生产流程、减少生产浪费等方式,实现以下目标:
1. 提高生产效率,缩短生产周期;
2. 降低生产成本,提高盈利能力;
3. 提升产品质量,增强客户满意度。
项目实施
1. 生产线布局优化:通过对生产线布局进行重新设计,优化物料搬运路径,减少重复搬运和等待时间;
2. 生产流程改进:对生产流程进行梳理,消除不必要的环节和浪费,提高生产连续性;
3. 减少浪费:通过消除不良品、减少过度生产和减少库存等方式,减少生产浪费;
4. 员工培训:对生产线员工进行精益生产培训,提高员工的技能和意识。
项目成果
1. 生产效率提高:通过优化生产线布局和改进生产流程,生产效率提高了30%;
2. 生产成本降低:通过减少浪费和优化生产流程,生产成本降低了20%;
3. 产品质量提升:通过改进生产工艺和加强员工培训,产品质量合格率提高了10%;
4. 客户满意度提升:通过提高产品质量和缩短交货期,客户满意度提高了20%。
总结
本项目通过优化生产线布局、改进生产流程和减少浪费等方式,实现了提高生产效率、降低成本、提升产品质量和增强客户满意度的目标。
未来,企业将继续推广精益生产理念和方法,不断优化生产和业务流程,提高企业的竞争力和盈利能力。
精益生产项目实施报告

三、裸件配送实施的目标(优化仓库人员职能)
结构仓人员由14人减少至12人 电子仓人员由23人减少至20人,合计减少5人,缩减比例14%
人员组织配置表(仓库/品管)
现状
未来
NO.
仓库
部门
职位
配置人员
部门
职位
配置人员
1
结构仓
PMC
配料员(含组长)
4
搬运组
拆箱员
3
2
输单员
2
出库员
1
3
司机
2
入库员
1
4
司机
批量=1D
数量检查
缓存1天量
缓存1天量
时间=10-30min
批量=1D
数量检查
时间=60min
批量=1D
时间=360min
批量=1D
库存信息管理
5人
生管
周计划
车间
周计划
采购
C.T =520min-720min L/T=5.4D
一、未来价值流程图
30min
360min
10min
10min
10min
四、实施第一阶段(实施前后效率对比)
改善前小时产量
改善后小时产量
时间
3月19日
3月20日
3月21日
3月23日
3月24日
3月25日
3月26日
3月27日
3月28日
平均小时产量
264
262
274
278
308
305
291
305
302
平均小时产量
270
302
小时产量增长
32
小时产量增比
精益生产管理实施方案报告书

精益生产管理实施方案一、总体指导思想1.精益生产作为当今最为先进的制造管理方法,具有很强的实践性。
改善实施必须始终围绕精益生产管理体系的核心即消除浪费来开展各项工作,时时以精益生产思想作为工作指导的有力武器。
2.任何一项管理理论都不是一成不变的适用每一个企业。
在应用精益生产理论进行改善时,必须时刻结合企业所处的行业环境和企业本身的特殊性进行灵活应用,因地制宜。
只有这样,才一不至于在改善中生搬硬套,走错方向。
例如由于手机行业存在市场机会成本,战略要求不能完全做到“零库存”管理。
3一个拥有卓越企业文化和管理的企业,需要经过多年的实践积淀才能实现。
丰田公司自成立初期就开始不断探讨生产模式,历经四十年时间才一逐步形成了初步成型的丰田方式。
时至今日,丰田方式仍在不断改善进步中。
因此,没有那个企业的实现是一瞰而就的,需要一点一滴的积累。
卓越企业管理需要系统性的全面进行改善,但需要结合实际状况分步骤分门别类的逐步改善进而达成阶段目标并最终实现总目标。
4.改善不能脱离现场。
所有数据必须现场测量,所有问题必须现场观察,充分与一线员工交流并亲身实践才能得出结论。
脱离现场,脱离实际,脱离基层员工,任何改善都只是纸上谈兵。
5.改善成果必须实现标准化,没有标准化的改善不是完美的改善。
6.精益生产的改善需要以人为本,全员参与。
只有全员参与,充分发挥人的主动性和能动性,改善才能处处开花。
7.改善是一个持续创新不断发现问题不断进步的过程。
没有最好,只有更好,持续改善,不断进步,这是丰田方式的精髓。
只有深深理解这一精髓,并将其作为企业文化融入到员工心中,才能够在精益生产的实践应用中取得长久发展。
二、实施方案指导框架结合企业自身实际状况,借鉴国内外的精益生产理论指导和实践案例研究,研究将精益生产的各钟软硬件技术进行分类,提出了新的改善模型,作为公司推行精益生产管理的指导框架。
改善模型称为新“TPS”模型,T代表技术(Technology ),P代表人员(Person ),S代表系统(System,如图4-1所示。
精益生产管理实践报告(2篇)

第1篇一、引言随着全球经济的快速发展,企业面临着日益激烈的市场竞争。
为了提高企业的核心竞争力,降低成本、提高效率,精益生产管理应运而生。
本文旨在通过对某企业精益生产管理实践的深入分析,探讨精益生产管理的实施效果及其对企业发展的促进作用。
二、企业背景某企业成立于20世纪90年代,主要从事电子产品研发、生产和销售。
经过多年的发展,企业规模不断扩大,员工人数超过1000人。
然而,在激烈的市场竞争中,企业面临着成本高、效率低、产品质量不稳定等问题。
为了解决这些问题,企业决定引入精益生产管理,以提高企业的整体竞争力。
三、精益生产管理实施过程1. 前期准备在实施精益生产管理之前,企业对全体员工进行了精益生产理念的培训,使员工充分认识到精益生产的重要性。
同时,企业成立了精益生产管理团队,负责整个项目的实施。
2. 现状分析通过对企业生产现场、流程、人员等方面的调查分析,发现以下问题:(1)生产流程复杂,存在冗余环节;(2)生产设备老化,维护保养不到位;(3)员工操作不规范,产品质量不稳定;(4)库存积压严重,资金占用大。
3. 精益生产管理实施(1)5S现场管理:对生产现场进行整理、整顿、清扫、清洁、素养,提高现场整洁度,降低安全隐患。
(2)价值流分析:对生产流程进行梳理,找出浪费环节,优化生产流程。
(3)看板管理:实施看板管理,实时监控生产进度,提高生产效率。
(4)设备管理:加强设备维护保养,提高设备利用率。
(5)人员培训:对员工进行技能培训,提高员工操作水平。
4. 持续改进企业将精益生产管理作为一项长期工作,不断对生产现场、流程、人员等方面进行改进,以实现持续提升。
四、精益生产管理实施效果1. 成本降低通过精益生产管理,企业生产效率提高,库存积压减少,生产成本降低20%。
2. 质量提升员工操作规范,产品质量得到有效保证,客户满意度提高。
3. 效率提高生产流程优化,看板管理实施,生产效率提高30%。
4. 员工满意度提升员工通过培训,技能水平得到提高,工作积极性增强,员工满意度提升。
精益生产实施与成效分析

精益生产实施与成效分析前言随着工业化和全球市场的竞争日益激烈,企业为了提高生产效率和降低成本,开始寻求更有效的生产方法。
在这种背景下,精益生产作为一种管理理念和实践方法逐渐流行起来。
本文将介绍精益生产的实施过程和成效分析,帮助读者了解并应用这一方法。
精益生产的基本原则精益生产是一种追求高效率和高质量的生产方式,旨在通过消除浪费和提高价值流程来实现这一目标。
其基本原则包括:价值定义和流程映射精益生产强调以客户为导向,明确产品或服务的价值以及实现该价值的流程。
通过细致分析各个环节的价值和非价值活动,可以识别并消除浪费。
流程改进和精益化精益生产通过优化生产流程,降低生产过程中的时间、质量和成本等资源消耗。
这包括设立清晰的标准工作流程、减少库存、优化设备运行和制定高效的工作计划等。
所有员工参与和持续改进精益生产强调所有员工都是价值创造和浪费消除的主要参与者。
通过培训和激励机制,使员工能够积极参与到整个生产过程中,并不断寻找改进的机会。
精益生产实施的步骤实施精益生产可以分为以下步骤:了解和培训:组织需要了解精益生产的基本原理和方法。
为此,培训是必不可少的,可以通过专家指导、内部培训等方式进行。
价值流分析:确定产品或服务的价值流,通过价值流图等工具分析其中的流程和活动。
识别出不必要的浪费,并寻找改进的机会。
流程优化:对流程中的非价值活动进行改进和简化。
通过优化布局、优化设备使用、优化工作步骤等方式,减少不必要的浪费和时间消耗。
持续改进:精益生产是一个持续不断的过程,需要不断寻找改进的机会并落实到实际操作中。
建立改进措施评估和反馈机制,确保持续改进的进行。
精益生产的成效分析精益生产的实施可以带来多方面的成效,包括:提高生产效率:通过消除浪费、优化流程和改进设备使用等措施,可以提高生产效率,减少生产时间和资源消耗。
提高产品质量:精益生产强调优化流程和标准化操作,可以有效降低产品缺陷率,提高产品质量和客户满意度。
- 1、下载文档前请自行甄别文档内容的完整性,平台不提供额外的编辑、内容补充、找答案等附加服务。
- 2、"仅部分预览"的文档,不可在线预览部分如存在完整性等问题,可反馈申请退款(可完整预览的文档不适用该条件!)。
- 3、如文档侵犯您的权益,请联系客服反馈,我们会尽快为您处理(人工客服工作时间:9:00-18:30)。
一.人员工作分工单一化,改纵向分工为横向分工 (2)
一.人员工作分工单一化,改纵向分工为横向 分工(3)
一.人员工作分工单一化,改纵向分工为横向 分工(4)
二.推行自动化,低减人工作业成本;
三.制作,设计简易工装,精化生产;
• 制做炉后手动搅拌刀,及 锡膏,擦试纸的存放夹具 ,避免绞拌刀裸露,粘粘 灰尘及其它杂物导致混入 锡膏;如图:
一.人员工作分工单一化,改纵向分工为横向分工( 1);
• SMT原线体员工分工为单线体纵向分工: 印刷机操作员1+贴片机操作员1+AOI操作1人+炉后目检1人
高速线体共6条,人员配置为: 4人/条线*6条线+3(组长1人+助拉2人)+1(维修1人)=28 人 精益生产导入整合线体横向分工,具体人员分工为: 印刷操作员+接料员+贴片机操作员+AOI操作员 高速线体共6条,人员配置为: 印刷机操作员3人/6条线+接料员6人/6条线+贴片机操作员2 人/6条线+AOI 6人/6条线+3(组长1人+助拉2人)+1(维修1 人)=21人
1 • SMT精益职能分离项目汇报 2 • 大数据(集控中心 )项目进度汇报 3 • 裸件配送项目汇报 4 • 齐套上线项目汇报
SMT精益生产报告
随着市场竞争越来越激烈,对于产品的生产制造成本控 制要求也越来越高,自2015年1月份公司开始推行精益生产 ,整体减员增效,在公司高层领导的积极推动下,公司上下 全员参与,现将推行以来,SMT的推行进度及相关的工作状 态,做简单的汇报,SMT主要推行以下事项: 一.人员工作分工单一化,改纵向分工为横向分工; 二.推行自动化,低减人工作业成本; 三.制作,设计简易工装,精化生产; 四.生产讯息管理系统建设;
PD与PM系统状况
• (二).关于生产文件变更讯息集控中心流程设定及规划; • 目的: • 1.规划技术齐套资料,规范程序自动上传,提醒功能减少人工传递遗漏; • 2.技术齐套讯息提前采集讯息,并系统性收集,反馈,做到技术资料讯息系统化确认; • 3.满足计划部门准确掌握,技术齐套讯息,快速,准确,高效排产; • 系统过程设定规划: • 1.针对工程变更,及新机型相关资料,由研发中心人员拟定后,上传至公司PDM系统; • 2.相关工程需求文件及相关程序,工冶具准备工作,根据上层集中通过PDM系统派发至相关责任人,由系统设定各
• (一) 关于SMT程序信息集控中心的相关功能要求 • 1.将SMT程序编辑,及设备实时生产讯息相关数据进行整合,建立服
务器平台,做到讯息共享,生产数据实时可视化; • 2.程序员分工优化,分离职能,1人负责程序的编辑,模拟,一人负责
程序的优化,提高作业效率,同时杜绝出错率,确保生产程序的合理 化; • 3.生产设备内,确保生产程序唯一,当产线转线,服务器上传生产程 序设备自动开起生产界面,当技术员在生产过程中在线优化程需,设 备可自动采集优化后程序,并回传至服务器,自动保存; • 4.生产相关数据能在线,实时上传,及时反馈生产讯息;
批量=1D
批量=1D
30min
30-120min 30-120min 10-30min
60min
360min
3D
1D
0.5D
0.5D
0.2D
0.002D
采购
生管
周计划
车间
周计划
入库信息
出库信息 使用进度
C.T =422min L/T=4.6D
待检区
检验/转箱 3人
入库 1人
备料出库 1人
线边仓 1人
配送到岗位 助拉
时间=30min 时间=360min 时间=10min 时间=10min
时系统自动弹出技术相关讯息齐套确认资料至各部门; • 需查讯技术齐套部门收到信息后,可直接跟据以上讯息,做下步工作!
五.综合职能分离,精简人员编制
• 在产线未导入相关自动化,将岗位合并,分工单一化,同时对各岗位职能最 大限度化的做职能分离,生产自主产品,人员编制计划由原来编制的155人, 计划精简至127人;
• 后期如导入相应的自动化设备,及对原材料做好相关的要求,改善来料品质 ,优化岗位职能分离,在人员的合理利用上,还有可调整空间;
1 • SMT精益职能分离项目汇报 2 • 大数据(集控中心 )项目进度汇报 3 • 裸件配送项目汇报 4 • 齐套配送项目汇报
采购
生管
周计划
车间周Biblioteka 划抽检库存信息管理
二,建立设备程序讯息集控中心 ;
1)将车间设备建立局域集团网,设立服务器功能 ,所有程序等资源共享,杜绝设备间外置U盘资 料COPY,减少设备病毒; 2)购置贴片设备辅助软件,PD,PM系统,取消 人员程序传递,服务器自动传递程序,并下载新 程序,回传,减少了人员备份程序; 3)设备运行相关数据实时反馈,实现看板管理功 能,可以及时的收集相关生产数据,实时监控产 线生产情况;
5人
C.T =520min-720min L/T=5.4D
5人
入库
发货
领料
缓存1天量
暂放区
缓存1天量
线边
拆箱
时间=30min
4人
8人
人
数量 检查
数量 检查
时间=30-120min时间=30-120min 时间=10-30min
人
时间=60min
64人
时间=360min
批量=不定
批量=1D
批量=1D
批量=1D
收件责任人,并回传收条,同时设定完成时间提醒功能; • 3.由集控中心负责人,通过PDM系统工具,分别指派各部负责人,确认相关程序及文件,工冶具; • 4.各部门责任人收到需确认文件,制定固定确认表单,分发至各责任工程师确认,确认完成后,交由部门负责人再
次确认,确认无问题回传系统; • 5.集控中心负责人,收到各部回传文件后,整体核对,无问题,则关闭系统,更改,添加功能,设定只读模式,同
• 制作印刷机后端接驳台, 屏蔽罩,避免印刷完成品 ,在运送过程中出现焊盘 粘杂物及灰尘,导致炉后 虚焊!
四.生产讯息管理系统建设;
一,评估研发物料上料系统;
1)可以对应减少人工上料手动比对,及手动做上 料记录的工作时间,分离接料人员的岗位职能, 提升人员工作效率; 2)上料系统,可自动比对物料相关讯息,做系统 比对,减少上料的出错率,同时可以上传相关物 料讯息,可追溯物料的使用讯息; 3)现阶段,软件研发进度基本完成,已进行到测 试阶段;