焦炉煤气净化文章
焦炉煤气净化与焦化产品回收率提升探索应用
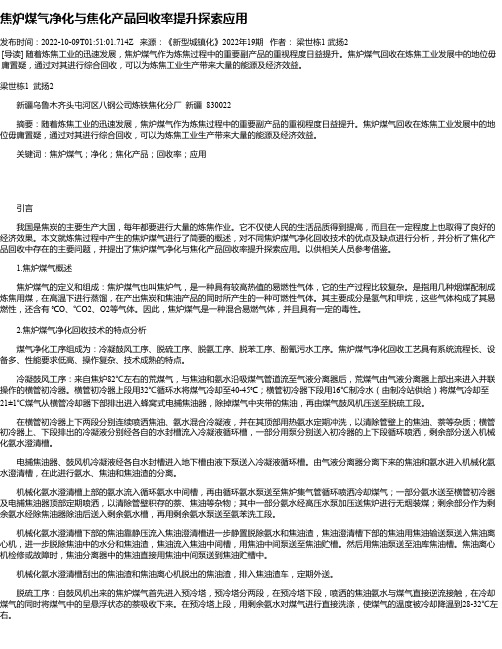
焦炉煤气净化与焦化产品回收率提升探索应用发布时间:2022-10-09T01:51:01.714Z 来源:《新型城镇化》2022年19期作者:梁世栋1 武扬2 [导读] 随着炼焦工业的迅速发展,焦炉煤气作为炼焦过程中的重要副产品的重视程度日益提升。
焦炉煤气回收在炼焦工业发展中的地位毋庸置疑,通过对其进行综合回收,可以为炼焦工业生产带来大量的能源及经济效益。
梁世栋1 武扬2新疆乌鲁木齐头屯河区八钢公司炼铁焦化分厂新疆 830022摘要:随着炼焦工业的迅速发展,焦炉煤气作为炼焦过程中的重要副产品的重视程度日益提升。
焦炉煤气回收在炼焦工业发展中的地位毋庸置疑,通过对其进行综合回收,可以为炼焦工业生产带来大量的能源及经济效益。
关键词:焦炉煤气;净化;焦化产品;回收率;应用引言我国是焦炭的主要生产大国,每年都要进行大量的炼焦作业。
它不仅使人民的生活品质得到提高,而且在一定程度上也取得了良好的经济效果。
本文就炼焦过程中产生的焦炉煤气进行了简要的概述,对不同焦炉煤气净化回收技术的优点及缺点进行分析,并分析了焦化产品回收中存在的主要问题,并提出了焦炉煤气净化与焦化产品回收率提升探索应用。
以供相关人员参考借鉴。
1.焦炉煤气概述焦炉煤气的定义和组成:焦炉煤气也叫焦炉气,是一种具有较高热值的易燃性气体,它的生产过程比较复杂。
是指用几种烟煤配制成炼焦用煤,在高温下进行蒸馏,在产出焦炭和焦油产品的同时所产生的一种可燃性气体。
其主要成分是氢气和甲烷,这些气体构成了其易燃性,还含有℃O、℃O2、O2等气体。
因此,焦炉煤气是一种混合易燃气体,并且具有一定的毒性。
2.焦炉煤气净化回收技术的特点分析煤气净化工序组成为:冷凝鼓风工序、脱硫工序、脱氨工序、脱苯工序、酚氰污水工序。
焦炉煤气净化回收工艺具有系统流程长、设备多、性能要求低高、操作复杂、技术成熟的特点。
冷凝鼓风工序:来自焦炉82℃左右的荒煤气,与焦油和氨水沿吸煤气管道流至气液分离器后,荒煤气由气液分离器上部出来进入并联操作的横管初冷器。
新型焦炉煤气净化工艺的开发及进展

新型焦炉煤气净化工艺的开发及进展随着环保意识的不断提高,对于大气污染物的排放要求也越来越严格。
作为高污染源之一的焦化行业,其排放的煤气含有大量的污染物,对环境污染严重。
煤气净化成为了焦化行业面临的重要任务之一。
在此情况下,新型焦炉煤气净化工艺的开发及进展成为了研究的热点之一。
一、传统焦炉煤气净化存在的问题传统的焦炉煤气净化工艺存在着诸多问题,主要包括以下几个方面:1.低净化效率:传统焦炉煤气净化工艺通常采用湿法净化,采用水洗等方式去除污染物。
但是由于浓度低、温度低等原因,致使净化效率不高,无法完全去除煤气中的污染物。
2.高能耗:传统的煤气净化工艺需要大量的水资源和能源,造成了较大的能源浪费,且处理过程中产生的废水也需要进一步处理,增加了处理成本。
3.废水处理难题:传统湿法净化工艺会产生大量含有有机物和化学物质的废水,对废水的处理和排放造成了一定的困难。
4.设备占地大:传统净化工艺需要大量的净化设备,占地面积大,增加了投资成本。
传统焦炉煤气净化工艺在净化效率、能耗和废水处理等方面存在着较大的问题,迫切需要新的工艺来解决这些问题。
二、新型焦炉煤气净化工艺的开发及进展随着焦化行业的发展和技术进步,一些新型的焦炉煤气净化工艺逐渐得到了关注和应用,取得了一定的进展。
主要包括以下几种工艺:2.活性炭吸附技术活性炭吸附技术是利用活性炭对煤气中的有机物质和颗粒物进行吸附,从而达到净化的目的。
该技术具有净化效率高、操作稳定等优点,且产生的废水较少,对环境影响小,逐渐成为焦炉煤气净化的重要技术之一。
3.等离子体净化技术等离子体净化技术是利用等离子体在高温和高频电场的作用下,对煤气中的有机物质和颗粒物进行分解和氧化的一种新型净化技术。
该技术对高浓度、高温、高湿度的煤气也具有良好的净化效果,且处理过程中不会产生废水,是一种环保型的净化工艺。
4.膜分离技术膜分离技术是利用高分子材料膜对煤气中的二氧化碳、氧气和氮气等进行分离,从而实现煤气的净化。
焦炉煤气净化与焦化产品回收率提升探索应用
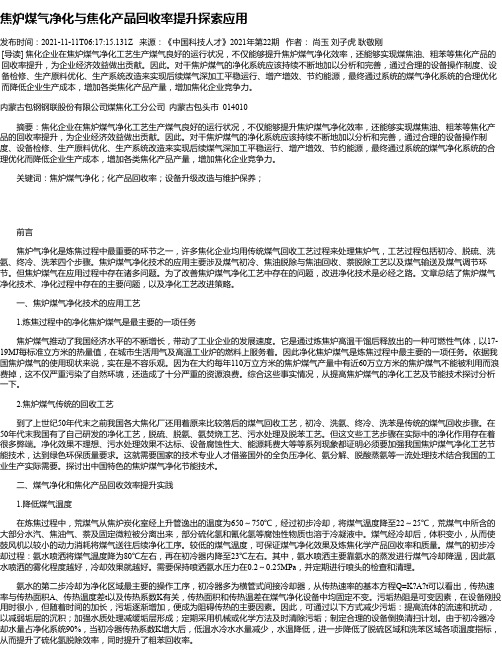
焦炉煤气净化与焦化产品回收率提升探索应用发布时间:2021-11-11T06:17:15.131Z 来源:《中国科技人才》2021年第22期作者:尚玉刘子虎耿敬刚[导读] 焦化企业在焦炉煤气净化工艺生产煤气良好的运行状况,不仅能够提升焦炉煤气净化效率,还能够实现煤焦油、粗苯等焦化产品的回收率提升,为企业经济效益做出贡献。
因此。
对干焦炉煤气的净化系统应该持续不断地加以分析和完善,通过合理的设备操作制度、设备检修、生产原料优化、生产系统改造来实现后续煤气深加工平稳运行、增产增效、节约能源,最终通过系统的煤气净化系统的合理优化而降低企业生产成本,增加各类焦化产品产量,增加焦化企业竞争力。
内蒙古包钢钢联股份有限公司煤焦化工分公司内蒙古包头市 014010摘要:焦化企业在焦炉煤气净化工艺生产煤气良好的运行状况,不仅能够提升焦炉煤气净化效率,还能够实现煤焦油、粗苯等焦化产品的回收率提升,为企业经济效益做出贡献。
因此。
对干焦炉煤气的净化系统应该持续不断地加以分析和完善,通过合理的设备操作制度、设备检修、生产原料优化、生产系统改造来实现后续煤气深加工平稳运行、增产增效、节约能源,最终通过系统的煤气净化系统的合理优化而降低企业生产成本,增加各类焦化产品产量,增加焦化企业竞争力。
关键词:焦炉煤气净化;化产品回收率;设备升级改造与维护保养;前言焦炉气净化是炼焦过程中最重要的环节之一,许多焦化企业均用传统煤气回收工艺过程来处理焦炉气,工艺过程包括初冷、脱硫、洗氨、终冷、洗苯四个步骤。
焦炉煤气净化技术的应用主要涉及煤气初冷、焦油脱除与焦油回收、萘脱除工艺以及煤气输送及煤气调节环节。
但焦炉煤气在应用过程中存在诸多问题。
为了改善焦炉煤气净化工艺中存在的问题,改进净化技术是必经之路。
文章总结了焦炉煤气净化技术、净化过程中存在的主要问题,以及净化工艺改进策略。
一、焦炉煤气净化技术的应用工艺1.炼焦过程中的净化焦炉煤气是最主要的一项任务焦炉煤气推动了我国经济水平的不断增长,带动了工业企业的发展速度。
焦炉煤气净化技术研究
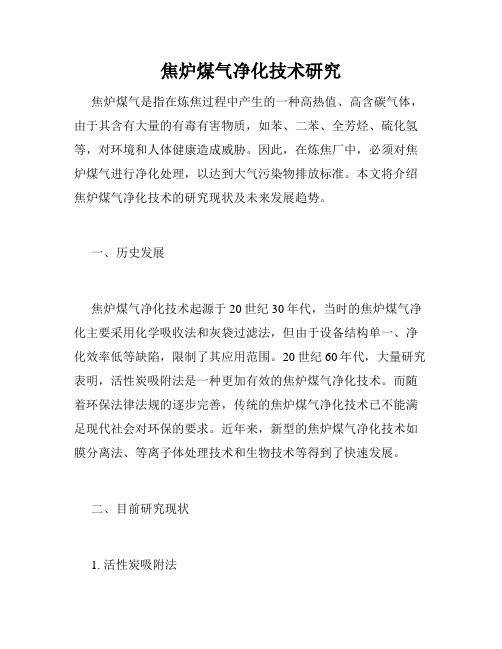
焦炉煤气净化技术研究焦炉煤气是指在炼焦过程中产生的一种高热值、高含碳气体,由于其含有大量的有毒有害物质,如苯、二苯、全芳烃、硫化氢等,对环境和人体健康造成威胁。
因此,在炼焦厂中,必须对焦炉煤气进行净化处理,以达到大气污染物排放标准。
本文将介绍焦炉煤气净化技术的研究现状及未来发展趋势。
一、历史发展焦炉煤气净化技术起源于20世纪30年代,当时的焦炉煤气净化主要采用化学吸收法和灰袋过滤法,但由于设备结构单一、净化效率低等缺陷,限制了其应用范围。
20世纪60年代,大量研究表明,活性炭吸附法是一种更加有效的焦炉煤气净化技术。
而随着环保法律法规的逐步完善,传统的焦炉煤气净化技术已不能满足现代社会对环保的要求。
近年来,新型的焦炉煤气净化技术如膜分离法、等离子体处理技术和生物技术等得到了快速发展。
二、目前研究现状1. 活性炭吸附法活性炭吸附法在焦化炉气体净化中得到广泛应用,其吸附剂具有强的吸附、选择性和再生性能,能够高效地去除苯、二苯、全芳烃等有害成分。
目前活性炭吸附法中存在着吸附剂失活、吸附速率慢等问题,研究人员正在通过改变吸附剂结构、增加吸附剂表面积等措施来提高活性炭吸附效率。
2. 膜分离法膜分离技术在气体分离领域具有广泛应用,可高效地分离和去除焦炉煤气中的有害成分。
与传统的吸附法相比,膜分离法具有操作简单、净化效率高等优点。
目前,膜分离技术研究仍处于实验室规模,尚未得到工业化应用。
3. 等离子体处理技术等离子体处理技术是一种新型的焦炉煤气净化技术,其原理是利用高能等离子体对有害物质进行氧化降解,将其转化为无害成分。
该技术具有能耗低、处理效率高等优点,在焦化炉气体净化方面存在广阔的应用前景。
4. 生物技术生物技术在焦化炉气体净化中应用也逐渐得到重视,其原理是利用微生物对有害成分进行降解,将其转化为无害物质。
与传统的焦炉煤气净化技术相比,生物技术有着对环境影响小、操作简单等优点,但目前该技术还存在处理效率低、微生物保存等问题,需要进一步完善。
焦炉煤气净化技术的应用现状与改进

直冷方式可冷却煤气,也可净化焦炉煤气。
而间接冷却方式在冷却焦炉煤气过程中,煤气不会直接与冷却水接触,而是借助于换热器来完成冷却过程。
间接冷却方式过程中由于冷却水不直接接触煤气,可不受煤气污染,因此,间接冷却方式所用冷却水可重复利用,适用于水资源紧缺的焦化企业。
基于直接冷却和间接冷却的优缺点,多数焦化企业选择使用直接、间接冷却结合式来完成煤气初冷过程。
焦炉企业煤气净化实践结果证明,煤气初冷后,其中所含萘气体量大大降低。
1.2 焦油脱除与焦油回收煤气初冷过程中,多数焦油也会随着煤气的冷却而冷却,小部分焦油则会进入焦油捕集装置,和氨水混合。
目前多数焦化企业均以氨水焦油分离设备来脱除焦油,此过程还可以有效去除渣尘。
一般而言,焦油脱除效果随着分离时间的延长而逐渐显著,但随着分离时间的延长,分离温度也会下降,使得焦油粘度大大增加,降低分离效果。
因此,焦油脱除过程还需要满足温度和时间两个因素。
1.3 萘脱除工艺粗煤气中含有约10g/m 3萘气体,经煤气初冷后,萘气体含量可降至2g/m 3左右,但冷却后的萘气体则处于过饱和状态。
焦炉煤气经管路输送至下道工序时,可能会在温度过低或流速过慢的制约下出现萘沉积现象,进而堵塞管路。
因此,将焦炉气体中的萘气体除去对焦化企业来说至关重要。
目前,萘脱除工艺主要有水洗工艺和油洗工艺两类。
其中,以油洗工艺来清洗焦炉煤气管路,可将其中萘气体含量降至1g/m 3以下,进而降低管路堵塞概率。
1.4 煤气输送及煤气调节常用的焦炉煤气输送设备主要是鼓风机,根据鼓风机结构的差异可将其分为两种:容积式鼓风机和离心式鼓风机。
其中,离心式鼓风机可进行调节,根据要求可进行循环调节、自动调节以及转速调节。
因此,国内多数焦化企业的煤气输送设备均选用离心式鼓风机。
2 焦炉煤气净化过程中存在的主要问题焦炉煤气在净化过程中存在诸多问题,主要分为以下几个方面。
第一,煤气初冷问题。
横管初冷器在设备运行期间容易出现故障,导致煤气在管路中堵塞。
焦炉煤气净化处理技术的相关分析

焦炉煤气净化处理技术的相关分析摘要:焦炉煤气是炼焦过程中产生的副产品,其成分复杂,含有多种杂质,必须进行净化处理,才能加以回收利用,以实现节能减排,提高资源利用效率。
焦炉煤气的净化处理,包含焦化厂的初步净化处理以及下游企业的精净化处理,本文重点对焦化厂对焦炉煤气初步净化处理的技术细节进行了分析,明确了其中的一些关键技术节点。
关键词:焦炉煤气;净化处理;技术细节在炼焦过程当中会产生一种副产品,即焦炉煤气,焦炉煤气是多种气体的混合产物,其主要成分为H2、CO、CO2、CH4、C2H6、N2等,其中H2、CO、CH4、C2H6为可燃气体。
同时含有多种杂质,主要有:焦油、笨、萘、无机硫、有机硫、氨、氰化氢等。
焦炉煤气的性质是一种高热值煤气,可作为燃料,也可作为化工产品的原料,但在使用前必须要净化,除去其中的杂质,满足生产要求和环保要求。
我们公司作为焦化厂的下游企业,是利用焦化厂多余的焦炉煤气制合成天然气。
焦化厂有自己的化产车间,对焦炉煤气进行了初步净化处理,脱除了焦炉煤气中大量的焦油、笨、无机硫、氨等。
焦炉煤气进入我们公司的装置后,再进行变温吸附脱焦油和萘、水洗脱氨、常温粗脱硫、加氢脱硫等精净化处理。
焦化厂对焦炉煤气初步净化处理技术的好坏,直接决定了出焦化厂的焦炉煤气杂质含量的高低,这是我们公司装置是否能够长周期稳定运行的重要因素,是我们公司是否能够产生较好经济效益的关键。
一、关于焦炉煤气净化处理焦炉煤气中含有大量对大气不友好的杂质,据不完全统计,焦炉煤气年均产量高达110万立方,在炼焦过程中正常消耗一部分,还有一部分大约60万立方的量,若不进行净化处理将直接排放至大气中,不仅浪费资源,更是对大气造成严重污染。
焦炉煤气中的H2、CO、CH4、C2H6,是可燃气体,使焦炉煤气可以作为炼焦过程的燃料气体,但还有一些杂质,比如焦油、笨、萘、无机硫、有机硫、氨、氰化氢等,会造成环境污染。
二、焦炉煤气初步净化处理工艺(一)焦炉煤气初步净化处理工艺的关键点焦炉煤气初步净化处理的工艺相对复杂,其中比较关键的几道工序包括,脱氨、脱苯和脱硫。
新型焦炉煤气净化工艺的开发及进展

新型焦炉煤气净化工艺的开发及进展随着钢铁工业发展的不断壮大,焦炉生产的产生的煤气也成为重要的能源来源。
然而,煤气中含有大量的有害气体,如苯、甲醛、苯胺等有毒有害物质会对环境和人体健康造成严重危害。
因此,对焦炉煤气进行净化处理,是现代炼钢生产的重要组成部分。
近年来,新型焦炉煤气净化工艺的研发受到了越来越多的关注。
这些新技术的研发旨在减少环境污染,提高钢铁生产的质量和效率。
一、生物活性滤床技术生物活性滤床技术是一种目前广泛使用的焦炉煤气净化技术。
它利用特殊的生物质,如腐败菌、微生物等,将煤气中的有害有毒物质进行吸附、分解和氧化等一系列反应,进而净化煤气。
这种技术具有不需要额外能源、可根据需要进行扩展的优点。
但该技术的缺点是需要对过程参数进行严格控制。
二、离子液体技术离子液体技术也是一种新型的焦炉煤气净化技术。
该技术是利用具有溶解性、选择性和高能量的离子液体将难以分离的有害物质从煤气中去除。
离子液体具有非常高的溶解度,是传统有机溶剂的几十倍,可以有效地吸附和分离苯、加合苯、硫化氢等有害有毒气体。
但离子液体的成本很高,是一个制约其应用的主要因素。
三、催化氧化技术催化氧化技术是一种通过催化剂将有害有毒物质转化为无害物质的技术。
该技术主要是在高温和高压环境下利用氧气进行氧化反应,并通过催化剂的作用将反应速率提高。
目前,铜、钯、铬等元素被广泛地用作催化剂。
但此技术的问题是成本较高,对催化剂有着较高的要求。
总之,新型焦炉煤气净化工艺在各种技术上均呈现出不同程度的优点和不足,为解决当前钢铁工业的环境保护和健康保障问题提供了一个新思路和新方法。
在未来的研究中,希望能够开发出更加高效、经济、实用的焦炉煤气净化技术,提高钢铁工业的“绿色”程度,更好地保障环境和人类的健康。
大型钢铁企业焦炉煤气净化技术探讨
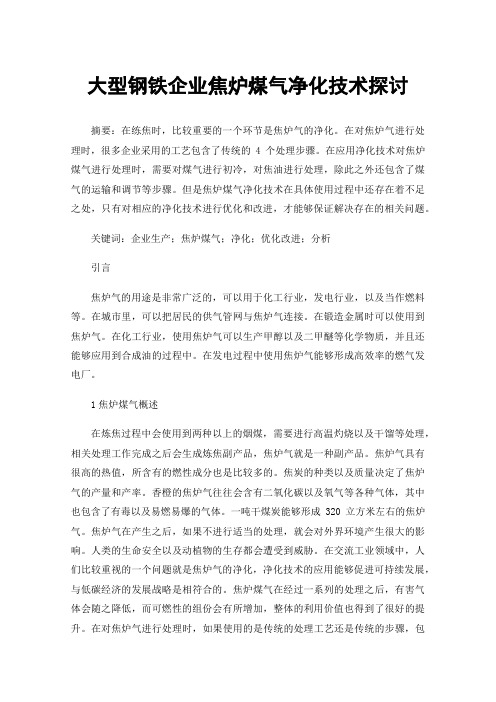
大型钢铁企业焦炉煤气净化技术探讨摘要:在练焦时,比较重要的一个环节是焦炉气的净化。
在对焦炉气进行处理时,很多企业采用的工艺包含了传统的4个处理步骤。
在应用净化技术对焦炉煤气进行处理时,需要对煤气进行初冷,对焦油进行处理,除此之外还包含了煤气的运输和调节等步骤。
但是焦炉煤气净化技术在具体使用过程中还存在着不足之处,只有对相应的净化技术进行优化和改进,才能够保证解决存在的相关问题。
关键词:企业生产;焦炉煤气;净化;优化改进;分析引言焦炉气的用途是非常广泛的,可以用于化工行业,发电行业,以及当作燃料等。
在城市里,可以把居民的供气管网与焦炉气连接。
在锻造金属时可以使用到焦炉气。
在化工行业,使用焦炉气可以生产甲醇以及二甲醚等化学物质,并且还能够应用到合成油的过程中。
在发电过程中使用焦炉气能够形成高效率的燃气发电厂。
1焦炉煤气概述在炼焦过程中会使用到两种以上的烟煤,需要进行高温灼烧以及干馏等处理,相关处理工作完成之后会生成炼焦副产品,焦炉气就是一种副产品。
焦炉气具有很高的热值,所含有的燃性成分也是比较多的。
焦炭的种类以及质量决定了焦炉气的产量和产率。
香橙的焦炉气往往会含有二氧化碳以及氧气等各种气体,其中也包含了有毒以及易燃易爆的气体。
一吨干煤炭能够形成320立方米左右的焦炉气。
焦炉气在产生之后,如果不进行适当的处理,就会对外界环境产生很大的影响。
人类的生命安全以及动植物的生存都会遭受到威胁。
在交流工业领域中,人们比较重视的一个问题就是焦炉气的净化,净化技术的应用能够促进可持续发展,与低碳经济的发展战略是相符合的。
焦炉煤气在经过一系列的处理之后,有害气体会随之降低,而可燃性的组份会有所增加,整体的利用价值也得到了很好的提升。
在对焦炉气进行处理时,如果使用的是传统的处理工艺还是传统的步骤,包含了中冷、洗苯、以及洗氨等。
焦化行业的专家在上世纪中期和末期,针对煤气的净化工艺进行了研发,所研发出的工艺能够很好的与58型号的焦炉匹配,包含了氨焚烧工业以及硫氨和氨水工艺等。
焦炉煤气净化工艺节能技术探讨
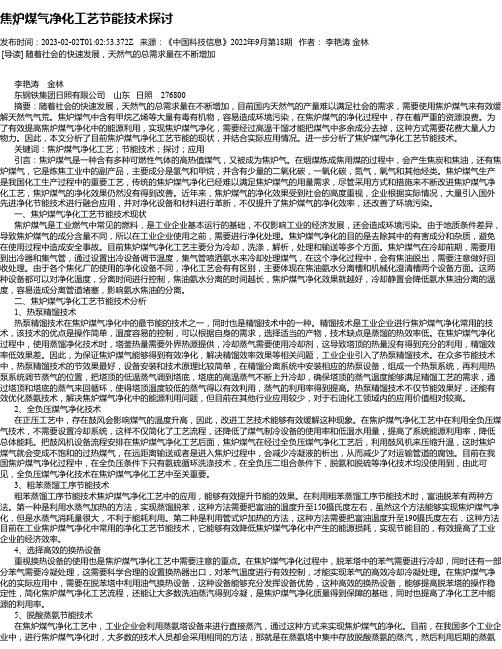
焦炉煤气净化工艺节能技术探讨发布时间:2023-02-02T01:02:53.372Z 来源:《中国科技信息》2022年9月第18期作者:李艳涛金林[导读] 随着社会的快速发展,天然气的总需求量在不断增加李艳涛金林东钢铁集团日照有限公司山东日照 276800摘要:随着社会的快速发展,天然气的总需求量在不断增加,目前国内天然气的产量难以满足社会的需求,需要使用焦炉煤气来有效缓解天然气气荒。
焦炉煤气中含有甲烷乙烯等大量有毒有机物,容易造成环境污染,在焦炉煤气的净化过程中,存在着严重的资源浪费。
为了有效提高焦炉煤气净化中的能源利用,实现焦炉煤气净化,需要经过高温干馏才能把煤气中多余成分去掉,这种方式需要花费大量人力物力。
因此,本文分析了目前焦炉煤气净化工艺节能的现状,并结合实际应用情况。
进一步分析了焦炉煤气净化工艺节能技术。
关键词:焦炉煤气净化工艺;节能技术;探讨;应用引言:焦炉煤气是一种含有多种可燃性气体的高热值煤气,又被成为焦炉气。
在烟煤炼成焦用煤的过程中,会产生焦炭和焦油,还有焦炉煤气,它是炼焦工业中的副产品,主要成分是氢气和甲烷,并含有少量的二氧化碳,一氧化碳,氮气,氧气和其他烃类。
焦炉煤气生产是我国化工生产过程中的重要工艺,传统的焦炉煤气净化已经难以满足焦炉煤气的用量需求,尽管采用方式和措施来不断改进焦炉煤气净化工艺,焦炉煤气的净化效果仍然没有得到改善。
近年来,焦炉煤气的净化效果受到社会的高度重视,企业根据实际情况,大量引入国外先进净化节能技术进行融合应用,并对净化设备和材料进行革新,不仅提升了焦炉煤气的净化效率,还改善了环境污染。
一、焦炉煤气净化工艺节能技术现状焦炉煤气是工业燃气中常见的燃料,是工业企业基本运行的基础,不仅影响工业的经济发展,还会造成环境污染。
由于地质条件差异,导致焦炉煤气的成分含量不同,所以在工业企业使用之前,需要进行净化处理。
焦炉煤气净化的目的是去除其中的有害成分和杂质,避免在使用过程中造成安全事故。
焦炉煤气脱硫净化的概述

焦炉煤气脱硫净化的概述摘要:在焦化厂生产中,焦炉煤气中所含的硫化氢及氰化氢是有害的杂质,它们腐蚀化产回收设备及煤气储存输送设施,还会污染厂区环境。
用此种煤气炼钢、轧钢加热,会降低钢材产品的质量,腐蚀加热设备;用作城市燃气,硫化氢及燃烧生产的二氧化硫、氰化氢及其燃烧生成的氮氧化物均有毒,会严重影响环境卫生。
所以焦炉煤气中的硫化氢和氰化氢应予清除,本文介绍了利用焦炉副产品焦炉煤气,经过湿法脱硫成为硫化氢含量较低的净化煤气的工艺及特点,为两台燃气发电机组提供合格(H2S≤0.7ppm)的煤气,同时为甲醇、锅炉发电、焦化分厂提供合格(H2S≤13ppm)的煤气,并对此工艺进行了评价,提出了建议。
关键词:焦炉煤气;湿法脱硫;硫化氢焦炉煤气脱硫方法分为:干法脱硫和湿法脱硫,干法脱硫是一种古老的煤气脱硫方法。
这种方法的工艺和设备简单,操作和维修比较容易。
但该法为间歇操作,占地面积大,脱硫剂的更换和再生工作的劳动强度较大,现代化的大型焦化厂已不再采用。
焦化净化煤气脱硫一般采用湿法脱硫:湿法脱硫又分为吸收法和氧化法,氧化法脱硫是对吸收法脱硫的改进和完善,是脱硫工艺更流畅,脱硫效果进一步提高。
脱硫工序包含循环水站、煤气预处理、气柜、罗茨风机、湿法脱硫、熔硫釜、脱油塔、精脱硫塔、VOC设施。
主要负责煤气的脱油脱萘、储存、提压和脱除无机硫,使湿法脱硫出口煤气中H2S≤13ppm后,一部分煤气送往压缩工序,另一部分煤气送甲醇、锅炉发电、焦化分厂生产使用。
同时熔硫釜产出硫磺模块。
压缩工序由三台往复式焦炉气压缩机及附属设备组成。
其任务是将湿法脱硫后的煤气通过四级压缩加压到4.15MPa,然后经脱油塔脱除含油下液、精脱硫塔脱除煤气中H2S,经外管送往燃气发电机组。
焦炉煤气经过提压后进入湿法脱硫塔,与脱硫贫液逆向接触,在PDS脱硫催化剂的作用下,利用碱性水溶液中的碱性化合物Na2CO3与硫化物H2S、COS等进行反应生成不稳定的中间硫化物,再利用空气和生成的中间硫化物反应生成单质硫和碱性物,将单质硫进行分离,使脱硫液再生,从而达到脱除H2S等硫化物并使脱硫液再生循环使用目的。
新型焦炉煤气净化工艺的开发及进展

新型焦炉煤气净化工艺的开发及进展随着我国工业化进程加快,焦化行业作为重要的能源工业领域之一,其发展对于国民经济的发展具有重要的意义。
随之而来的环境问题也日益凸显,焦化厂所排放的废气中含有大量有害气体,对环境造成了严重的污染。
为了解决这一问题,我国在新型焦炉煤气净化工艺方面进行了大量的研究和实践,取得了显著的成果。
本文将对新型焦炉煤气净化工艺的开发及进展进行介绍。
一、新型焦炉煤气净化工艺的开发历程焦炉煤气是焦化过程中产生的一种气体,其中含有大量的有害物质,如苯、二苯、苯酚等有机物,同时还含有硫化氢、氰化氢等无机物质,对环境和人体健康造成严重威胁。
为了净化焦炉煤气,我国在20世纪90年代开始进行了相关研究工作。
首先是对焦炉煤气中有害成分进行了分析和确定,明确了净化的重点和难点。
随后,我国开展了一系列的实验和试验,探索了多种焦炉煤气净化工艺,包括干法净化、湿法净化、生物净化等多种方法,最终形成了比较成熟的工艺体系。
二、新型焦炉煤气净化工艺的技术特点1. 高效净化新型焦炉煤气净化工艺采用了多种净化方法的结合,能够高效地去除焦炉煤气中的有害成分,使排放气体的污染物浓度大大降低,净化效果显著。
2. 低能耗新型焦炉煤气净化工艺充分考虑了能源的利用和节约,采用了低能耗的净化设备和工艺方法,降低了生产成本,提高了经济效益。
3. 高适应性新型焦炉煤气净化工艺能够适应不同规模、不同工艺参数的焦化厂,具有较强的适应性和通用性,能够满足不同用户的需求。
4. 环保健康新型焦炉煤气净化工艺能够有效地减少焦化厂对环境的污染,降低了大气污染物排放量,保护了周边环境和居民的健康。
三、新型焦炉煤气净化工艺的发展前景随着我国环保意识的增强和环境保护政策的日益严格,新型焦炉煤气净化工艺将会得到更加广泛的应用和推广。
未来,新型焦炉煤气净化工艺将更加注重技术创新和工艺改进,提高净化效率,降低成本,实现节能减排。
新型焦炉煤气净化工艺还将结合信息化技术,实现自动化控制和智能化管理,进一步提高净化工艺的稳定性和可靠性。
焦化厂煤气回收净化过程中的问题与治理
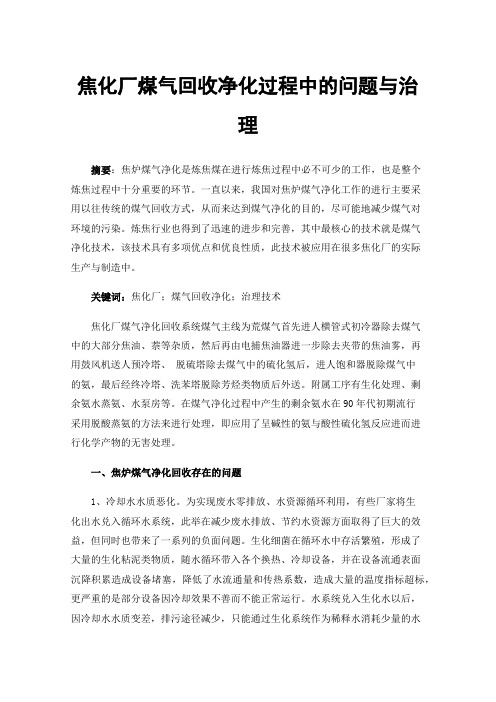
焦化厂煤气回收净化过程中的问题与治理摘要:焦炉煤气净化是炼焦煤在进行炼焦过程中必不可少的工作,也是整个炼焦过程中十分重要的环节。
一直以来,我国对焦炉煤气净化工作的进行主要采用以往传统的煤气回收方式,从而来达到煤气净化的目的,尽可能地减少煤气对环境的污染。
炼焦行业也得到了迅速的进步和完善,其中最核心的技术就是煤气净化技术,该技术具有多项优点和优良性质,此技术被应用在很多焦化厂的实际生产与制造中。
关键词:焦化厂;煤气回收净化;治理技术焦化厂煤气净化回收系统煤气主线为荒煤气首先进人横管式初冷器除去煤气中的大部分焦油、萘等杂质,然后再由电捕焦油器进一步除去夹带的焦油雾,再用鼓风机送人预冷塔、脱硫塔除去煤气中的硫化氢后,进人饱和器脱除煤气中的氨,最后经终冷塔、洗苯塔脱除芳烃类物质后外送。
附属工序有生化处理、剩余氨水蒸氨、水泵房等。
在煤气净化过程中产生的剩余氨水在90年代初期流行采用脱酸蒸氨的方法来进行处理,即应用了呈碱性的氨与酸性硫化氢反应进而进行化学产物的无害处理。
一、焦炉煤气净化回收存在的问题1、冷却水水质恶化。
为实现废水零排放、水资源循环利用,有些厂家将生化出水兑入循环水系统,此举在减少废水排放、节约水资源方面取得了巨大的效益,但同时也带来了一系列的负面问题。
生化细菌在循环水中存活繁殖,形成了大量的生化粘泥类物质,随水循环带入各个换热、冷却设备,并在设备流通表面沉降积累造成设备堵塞,降低了水流通量和传热系数,造成大量的温度指标超标,更严重的是部分设备因冷却效果不善而不能正常运行。
水系统兑入生化水以后,因冷却水水质变差,排污途径减少,只能通过生化系统作为稀释水消耗少量的水作为排污途径,长此以往,造成水质浓缩倍数超标,硬度和氯离子等指标超出国家标准,加速了设备的结垢和腐蚀。
2、螺旋板换热器堵塞,寿命减短。
许多厂家的脱硫预冷塔冷却器、终冷塔冷却器都是采用螺旋板换热器,由冷却水与循环液进行换热冷却,然而螺旋板换热器冷却水通道是侧进上出,在水质含悬浮物较多的情况下,容易因重力原因造成悬浮物沉降堵塞,而且无法通过反冲的方式进行清洗,久而久之,水流通道越来越小,最后因冷却效果导致工艺指标超标。
新型焦炉煤气净化工艺的开发及进展
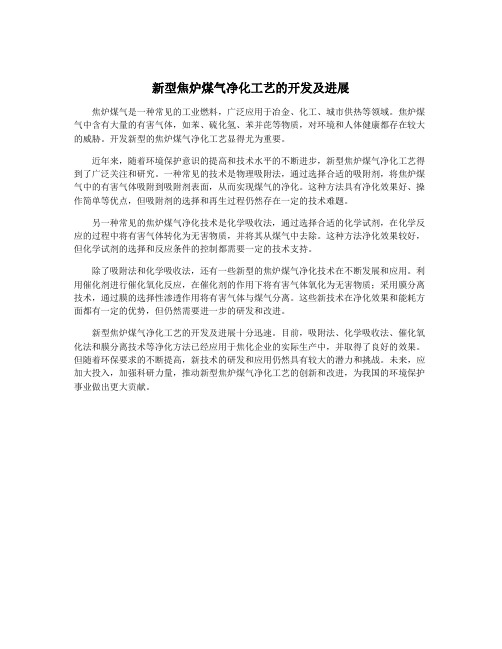
新型焦炉煤气净化工艺的开发及进展
焦炉煤气是一种常见的工业燃料,广泛应用于冶金、化工、城市供热等领域。
焦炉煤气中含有大量的有害气体,如苯、硫化氢、苯并芘等物质,对环境和人体健康都存在较大的威胁。
开发新型的焦炉煤气净化工艺显得尤为重要。
近年来,随着环境保护意识的提高和技术水平的不断进步,新型焦炉煤气净化工艺得到了广泛关注和研究。
一种常见的技术是物理吸附法,通过选择合适的吸附剂,将焦炉煤气中的有害气体吸附到吸附剂表面,从而实现煤气的净化。
这种方法具有净化效果好、操作简单等优点,但吸附剂的选择和再生过程仍然存在一定的技术难题。
另一种常见的焦炉煤气净化技术是化学吸收法,通过选择合适的化学试剂,在化学反应的过程中将有害气体转化为无害物质,并将其从煤气中去除。
这种方法净化效果较好,但化学试剂的选择和反应条件的控制都需要一定的技术支持。
除了吸附法和化学吸收法,还有一些新型的焦炉煤气净化技术在不断发展和应用。
利用催化剂进行催化氧化反应,在催化剂的作用下将有害气体氧化为无害物质;采用膜分离技术,通过膜的选择性渗透作用将有害气体与煤气分离。
这些新技术在净化效果和能耗方面都有一定的优势,但仍然需要进一步的研发和改进。
新型焦炉煤气净化工艺的开发及进展十分迅速。
目前,吸附法、化学吸收法、催化氧化法和膜分离技术等净化方法已经应用于焦化企业的实际生产中,并取得了良好的效果。
但随着环保要求的不断提高,新技术的研发和应用仍然具有较大的潜力和挑战。
未来,应加大投入,加强科研力量,推动新型焦炉煤气净化工艺的创新和改进,为我国的环境保护事业做出更大贡献。
焦炉煤气污染物净化技术研究

焦炉煤气污染物净化技术研究随着工业化进程的不断加快,燃煤产生的废气污染成为了当今社会所面临的重要环境问题之一。
焦化厂作为一个典型的燃煤重点行业,其煤气污染物净化技术一直备受关注。
本文将重点探讨焦炉煤气污染物净化技术的现状和发展。
煤气污染物主要包括二氧化硫(SO2)、氮氧化物(NOx)、可吸入颗粒物(PM),以及挥发性有机物(VOCs)等。
这些污染物对人体健康和环境造成严重威胁,且其中一些污染物还具有温室气体的特点,加速了全球变暖的进程。
因此,寻找焦炉煤气污染物净化技术显得尤为重要。
目前,焦炉煤气污染物净化技术主要分为物理吸收、化学吸收、脱硫脱硝一体化、吸附技术等几种。
物理吸收主要通过将煤气经过填料层使其与吸收剂接触,从而达到净化的目的。
化学吸收则是在物理吸收的基础上,通过添加化学吸收剂以提高净化效果。
脱硫脱硝一体化技术是将脱硫和脱硝的过程进行整合,提高处理效率的同时减少能耗。
而吸附技术则是通过吸附剂对污染物进行捕捉和分离。
在众多的焦炉煤气污染物净化技术中,脱硫脱硝一体化技术备受关注。
该技术具有高效、节能的特点,同时能够同时去除煤气中的硫氧化物和氮氧化物。
脱硫脱硝一体化技术通常分为湿法和干法两种方法,湿法的优点在于对污染物的去除效率较高,而干法则主要应用于对氮氧化物的净化。
然而,无论采用哪种方法,脱硫脱硝一体化技术都面临着高能耗和废水处理问题,因此,如何进一步提高处理效率和降低能耗成为了研究的重点。
此外,吸附技术也是一种常见的焦炉煤气污染物净化技术。
该技术通常使用活性碳、沸石等为吸附剂,对煤气中的污染物进行捕捉和分离。
吸附技术具有操作灵活、效果稳定的特点,且可以适用于各种污染物。
然而,吸附剂的选择和再生问题仍然需要进一步研究和改进。
此外,随着技术的不断发展,生物技术也逐渐应用于焦炉煤气污染物净化领域。
生物技术通过利用微生物菌群进行脱硫和脱硝,具有不产生二次污染物、能耗低的特点。
然而,生物技术的应用仍存在着菌种选择、稳定性和操作成本等问题,需要进一步加强研究。
煤气净化论文
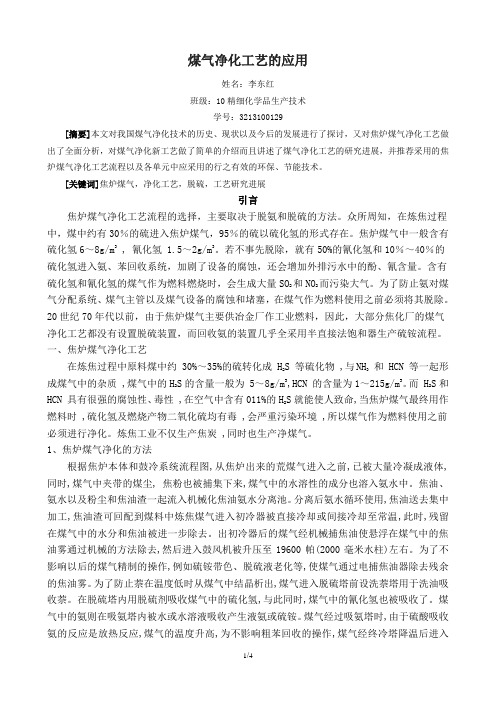
煤气净化工艺的应用姓名:李东红班级:10精细化学品生产技术学号:3213100129[摘要]本文对我国煤气净化技术的历史、现状以及今后的发展进行了探讨,又对焦炉煤气净化工艺做出了全面分析,对煤气净化新工艺做了简单的介绍而且讲述了煤气净化工艺的研究进展,并推荐采用的焦炉煤气净化工艺流程以及各单元中应采用的行之有效的环保、节能技术。
[关键词]焦炉煤气,净化工艺,脱硫,工艺研究进展引言焦炉煤气净化工艺流程的选择,主要取决于脱氨和脱硫的方法。
众所周知,在炼焦过程中,煤中约有30%的硫进入焦炉煤气,95%的硫以硫化氢的形式存在。
焦炉煤气中一般含有硫化氢6~8g/m 3 , 氰化氢 1.5~2g/m 3。
若不事先脱除,就有50%的氰化氢和10%~40%的硫化氢进入氨、苯回收系统,加剧了设备的腐蚀,还会增加外排污水中的酚、氰含量。
含有硫化氢和氰化氢的煤气作为燃料燃烧时,会生成大量SO 2和NO 2而污染大气。
为了防止氨对煤气分配系统、煤气主管以及煤气设备的腐蚀和堵塞,在煤气作为燃料使用之前必须将其脱除。
20世纪70年代以前,由于焦炉煤气主要供冶金厂作工业燃料,因此,大部分焦化厂的煤气净化工艺都没有设置脱硫装置,而回收氨的装置几乎全采用半直接法饱和器生产硫铵流程。
一、焦炉煤气净化工艺在炼焦过程中原料煤中约 30%~35%的硫转化成 H 2S 等硫化物 ,与NH 3 和 HCN 等一起形成煤气中的杂质 ,煤气中的H 2S 的含量一般为 5~8g/m 3,HCN 的含量为1~215g/m 3。
而 H 2S 和 HCN 具有很强的腐蚀性、毒性 ,在空气中含有011%的H 2S 就能使人致命,当焦炉煤气最终用作燃料时 ,硫化氢及燃烧产物二氧化硫均有毒 ,会严重污染环境 ,所以煤气作为燃料使用之前必须进行净化。
炼焦工业不仅生产焦炭 ,同时也生产净煤气。
1、焦炉煤气净化的方法根据焦炉本体和鼓冷系统流程图,从焦炉出来的荒煤气进入之前,已被大量冷凝成液体,同时,煤气中夹带的煤尘, 焦粉也被捕集下来,煤气中的水溶性的成分也溶入氨水中。
煤气净化资料
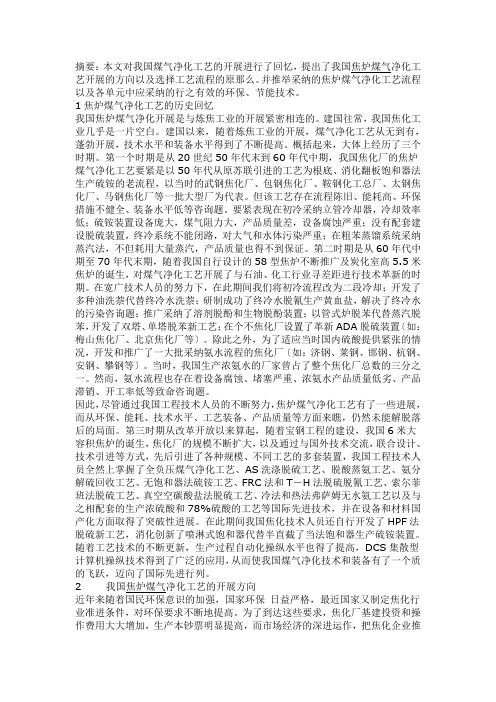
摘要:本文对我国煤气净化工艺的开展进行了回忆,提出了我国焦炉煤气净化工艺开展的方向以及选择工艺流程的原那么。
并推举采纳的焦炉煤气净化工艺流程以及各单元中应采纳的行之有效的环保、节能技术。
1焦炉煤气净化工艺的历史回忆我国焦炉煤气净化开展是与炼焦工业的开展紧密相连的。
建国往常,我国焦化工业几乎是一片空白。
建国以来,随着炼焦工业的开展,煤气净化工艺从无到有,蓬勃开展,技术水平和装备水平得到了不断提高。
概括起来,大体上经历了三个时期。
第一个时期是从20世纪50年代末到60年代中期,我国焦化厂的焦炉煤气净化工艺要紧是以50年代从原苏联引进的工艺为根底、消化翻板饱和器法生产硫铵的老流程,以当时的武钢焦化厂、包钢焦化厂、鞍钢化工总厂、太钢焦化厂、马钢焦化厂等一批大型厂为代表。
但该工艺存在流程陈旧、能耗高、环保措施不健全、装备水平低等咨询题。
要紧表现在初冷采纳立管冷却器,冷却效率低;硫铵装置设备庞大,煤气阻力大,产品质量差,设备腐蚀严重;没有配套建设脱硫装置,终冷系统不能闭路,对大气和水体污染严重;在粗苯蒸馏系统采纳蒸汽法,不但耗用大量蒸汽,产品质量也得不到保证。
第二时期是从60年代中期至70年代末期,随着我国自行设计的58型焦炉不断推广及炭化室高5.5米焦炉的诞生,对煤气净化工艺开展了与石油、化工行业寻差距进行技术革新的时期。
在宽广技术人员的努力下,在此期间我们将初冷流程改为二段冷却;开发了多种油洗萘代替终冷水洗萘;研制成功了终冷水脱氰生产黄血盐,解决了终冷水的污染咨询题;推广采纳了溶剂脱酚和生物脱酚装置;以管式炉脱苯代替蒸汽脱苯,开发了双塔、单塔脱苯新工艺;在个不焦化厂设置了革新ADA脱硫装置〔如:梅山焦化厂、北京焦化厂等〕。
除此之外,为了适应当时国内硫酸提供紧张的情况,开发和推广了一大批采纳氨水流程的焦化厂〔如:济钢、莱钢、邯钢、杭钢、安钢、攀钢等〕。
当时,我国生产浓氨水的厂家曾占了整个焦化厂总数的三分之一。
包头钢铁集团有限责任公司焦炉煤气的净化和提氢技术
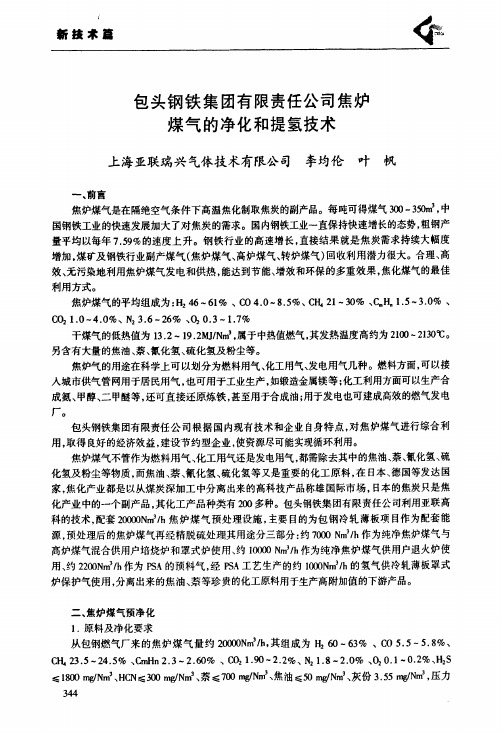
具体过程依次如下: A.吸附:预处理后气体从底部进入吸附塔下部,在吸附压力下,杂质被吸附,粗氢气从塔顶 流出进氢气缓冲罐。 B.均压降压过程 在吸附过程结束后,顺着吸附方向将塔内的较高压力的氢气放人其它已完成再生的较低压 力吸附塔的过程,这一过程不仅是降压过程,更是回收床层死空间氢气的过程,本流程共包括了 三次连续的均压降压过程,以保证氢气的充分回收。 C.顺放过程 在均压回收氢气过程结束后,继续顺着吸附方向进行减压,顺放出来的氢气放入顺放罐中 混合并储存起来,用作吸附塔冲洗的冲洗气源。 D.逆放过程 在顺放结束后,逆着吸附方向将吸附塔压力降至接近常压,此时被吸附的杂质开始从吸附 剂中大量解吸出来,逆放气送至再生气缓冲罐用作预处理系统的再生气源。 E。冲洗过程 逆放结束后,为使吸附剂得到彻底的再生,用顺放罐中储存的氢气逆着吸附方向冲洗吸附 床层,进一步降低杂质组分的分压,并将杂质冲洗出来。冲洗再生气也送至再生气缓冲罐用作 预处理系统的再生气源。 F.均压升压过程 在冲洗再生过程完成后,用来自其它吸附塔的较高压力氢气依次对该吸附塔进行升压,这 一过程与均压降压过程相对应,不仅是升压过程,而且也是回收其它塔的床层死空间氢气的过 程,本流程共包括了连续三次均压升压过程。 G.产品气升压过程 在三次均压升压过程完成后,为了使吸附塔可以平稳地切换至下一次吸附并保证产品纯度 在这一过程中不发生波动,需要通过升压调节阀缓慢而平稳地用产品氢气将吸附塔压力升至吸 附压力。 经这一过程后吸附塔便完成了一个“吸附一再生”循环,为下一次吸附做好了准备。 ②变压吸附提氢装置可靠性的控制手段 A故障塔切除 在变压吸附装置运行过程中,如因阀门、控制线路、电磁阀等问题,使某塔不能正常工作时, 就需要切掉一个塔,让其余的塔正常运行,保证生产不问断,以此类推可切除多个塔,系统仍能 正常运行,这是提高变压吸附装置可靠性的一个关键,也是变压吸附控制技术的一个核心。本 系统可作从五塔到三塔的任意切换运行。切塔过程如下:
新型焦炉煤气净化工艺的开发及进展
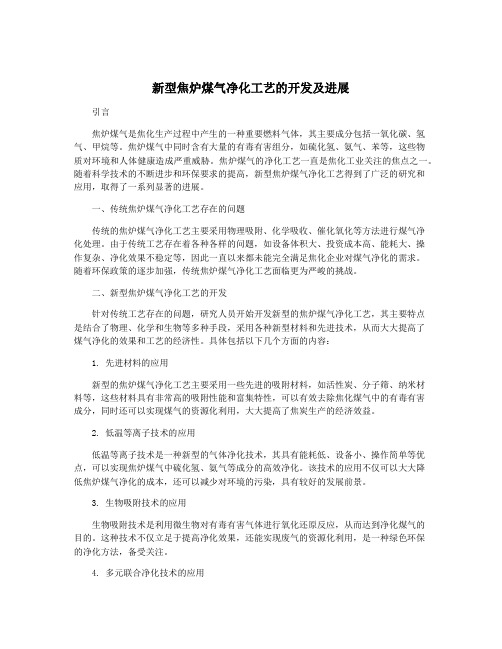
新型焦炉煤气净化工艺的开发及进展引言焦炉煤气是焦化生产过程中产生的一种重要燃料气体,其主要成分包括一氧化碳、氢气、甲烷等。
焦炉煤气中同时含有大量的有毒有害组分,如硫化氢、氨气、苯等,这些物质对环境和人体健康造成严重威胁。
焦炉煤气的净化工艺一直是焦化工业关注的焦点之一。
随着科学技术的不断进步和环保要求的提高,新型焦炉煤气净化工艺得到了广泛的研究和应用,取得了一系列显著的进展。
一、传统焦炉煤气净化工艺存在的问题传统的焦炉煤气净化工艺主要采用物理吸附、化学吸收、催化氧化等方法进行煤气净化处理。
由于传统工艺存在着各种各样的问题,如设备体积大、投资成本高、能耗大、操作复杂、净化效果不稳定等,因此一直以来都未能完全满足焦化企业对煤气净化的需求。
随着环保政策的逐步加强,传统焦炉煤气净化工艺面临更为严峻的挑战。
二、新型焦炉煤气净化工艺的开发针对传统工艺存在的问题,研究人员开始开发新型的焦炉煤气净化工艺,其主要特点是结合了物理、化学和生物等多种手段,采用各种新型材料和先进技术,从而大大提高了煤气净化的效果和工艺的经济性。
具体包括以下几个方面的内容:1. 先进材料的应用新型的焦炉煤气净化工艺主要采用一些先进的吸附材料,如活性炭、分子筛、纳米材料等,这些材料具有非常高的吸附性能和富集特性,可以有效去除焦化煤气中的有毒有害成分,同时还可以实现煤气的资源化利用,大大提高了焦炭生产的经济效益。
2. 低温等离子技术的应用低温等离子技术是一种新型的气体净化技术,其具有能耗低、设备小、操作简单等优点,可以实现焦炉煤气中硫化氢、氨气等成分的高效净化。
该技术的应用不仅可以大大降低焦炉煤气净化的成本,还可以减少对环境的污染,具有较好的发展前景。
3. 生物吸附技术的应用生物吸附技术是利用微生物对有毒有害气体进行氧化还原反应,从而达到净化煤气的目的。
这种技术不仅立足于提高净化效果,还能实现废气的资源化利用,是一种绿色环保的净化方法,备受关注。
焦炉煤气的净化和有效利用途径

焦炉煤气的净化和有效利用途径摘要:随着我国钢铁工业的发展,焦化行业进入到一个大发展时期。
大量焦炉煤气的产生,为焦炉煤气的合理开发利用提出了新的课题。
焦炉煤气的有效利用可产生巨大的经济效益,并且可避免环境污染和二次能源的浪费。
关键词:液化天然气;液化石油气;焦炉煤气;甲醇;还原铁根据“世界能源数据提要”2002年底的数据,全世界已探明的煤炭储量为9844亿吨,其中炼焦煤储量为1752亿吨,占全部煤炭储量的17.8%。
我国的炼焦煤(指气煤、肥煤、焦煤、瘦煤)资源主要分布于山西、山东、贵州、安徽、河南、河北、陕西、新疆、黑龙江等省。
截止2001年底探明的储量约为588.25亿吨,约占世界炼焦煤总储量的34%。
1.我国焦炉煤气的生产和使用概况我国是个产煤、焦炭大国,以吨煤产气320m3计算,2005年我国产焦炭2.5412亿吨,用煤达3亿余吨,可产气1000余亿m3。
2006年焦炭产量略高于2005年。
保守计算以40%焦炉自用,尚余600亿m3可外供。
相当于西气东输工程的4倍多(西气东输工程设计年供气量120亿m3)。
由此可见,焦炉煤气每年产量十分可观。
据有关统计,2005年全国有焦化厂1300余家,其中焦炭生产能力超过100万吨以上的企业达43家,总产量为85297万吨,占全国总产量的35.1%。
全国年产焦炭产能近3亿吨,日产焦炉煤气将近3亿m3。
2005年我国新建焦炉61座,新增产能约2736万吨。
筹划将于2007-2008年建设的焦炉约61座,总计产能将达到3970万吨。
其产生的煤气除工厂自用约40%外,约40%作为城市煤气,其余作为它用。
目前将焦炉煤气充分利用及进行深加工的企业为数不多,有的甚至直接放空,造成二次能源的极大浪费及环境污染。
2.焦炉煤气的利用2.1焦炉煤气的净化与石油资源相比,我国的煤炭储量十分丰富,结合当前焦炭市场需求旺盛的局面,必将会产生大量的焦炉煤气。
焦炉煤气与天然气相比,无论热值、燃烧产物,还是洁净度,都不如天然气。
- 1、下载文档前请自行甄别文档内容的完整性,平台不提供额外的编辑、内容补充、找答案等附加服务。
- 2、"仅部分预览"的文档,不可在线预览部分如存在完整性等问题,可反馈申请退款(可完整预览的文档不适用该条件!)。
- 3、如文档侵犯您的权益,请联系客服反馈,我们会尽快为您处理(人工客服工作时间:9:00-18:30)。
焦炉煤气净化文章1. 焦炉煤气净化技术现状及探讨1.1. 焦炉煤气净化的作用焦炭是冶金工业炼铁的主要原料。
全国共有焦化企业200余家,其中约10%生产能力超过100万t/a ,总生产能力超过亿t/a ,中国焦炭产量居世界第一位,焦化产品百余种。
炼焦用煤在复杂的地质状况下含有上百种成分,在焦炉中成焦时,其中多种成分随煤气一起进入随后的工序。
在炼焦过程中原料煤中约30%~35%的硫转化成H S 等含量一般为5g ~8g/m ,HCN 的含量为1g/m ~2.5g/m 。
而H S 和HCN 具有很强的腐蚀性、毒性,在空气中含有.1%的S 就能使人毒,会严重污染环境,所以煤气作为燃料使用之前必须进行净化。
1792年苏格兰人发明用铁罐干馏烟煤以来,煤气制造技术发展较快。
法国、德国、英国、荷兰先后建立起能够回收化学产品的焦炉,并以奥托——霍夫曼型焦炉最为著名,从此炼焦工业不仅生产焦炭,同时也生产净煤气。
硫化物,与N H 和HCN 等一起形成煤气中的杂质,煤气中的H S 的/m 0H 致命,当焦炉煤气最终用作燃料时,硫化氢及燃烧产物二氧化硫均有1.2.煤气净化的内容及技术现状煤气净化主要是脱除煤气中有害成分,具体包括冷却和输送出炉H H煤气、脱除煤气中S,HCN等酸性气体和N 类碱性气体、脱除及回收煤气中焦油类、苯类等物质以及萘等。
因此一般的净化工艺包括鼓冷、洗涤、解析、后处理等主要工序内容。
1.2.1煤气的初冷煤气的初冷是指出炉煤气通过集气管喷洒氨水和设置初冷器将出炉煤气由650~800℃降至25℃左右的处理过程。
初冷器冷却方法通常有间接式、直接式、间直结合式3种。
冷却设备有直冷式喷淋塔、立管式初冷器和横管式初冷器。
间接式煤气冷却过程冷却水不与煤气接触,通过换热器完成两相传热。
由于冷却介质——水没有受到煤气中有害介质的污染,循环使用次数多。
间冷式适用于大多数缺水地区的焦化厂。
由于煤气初冷时有大量萘的结晶析出,所以采用立管式初冷器的工艺要求初冷器后集合温度不低于25℃,以防冷凝液管堵塞。
而在采用横管多级喷洒洗萘初冷器的工艺中,由于喷洒液对萘的吸收而大大降低了萘结晶堵塞管道。
直冷煤气设备通常采用塔,由煤气与冷介质的逆相直接接触,完成热量和物质传递,因此煤气直接冷却,不但冷却了煤气,而且具有净化的效果。
据测定,在直冷过程中可有效除去煤气中90%以上的焦油、80%左右的氨、60%的萘、80%的H S 等。
鉴于间、直冷各自优点,多数厂家采用间——直冷结合方式,即煤气先在间接初冷器中冷却至45℃后,再进入直接冷却器进一步冷却至25℃~30℃,冷却后煤气含萘降至1g/m 以下。
1.2.2 煤气中焦油的脱除及回收煤气中大部分焦油在喷洒过程中随氨水冷却下来,其余部分随着煤气的初冷及焦油捕集装置混合在氨水中。
目前各厂家采用的氨水焦油分离装置主要是依靠氨水、焦油两相比重不同而分层分离,在分离过程中也有效去除了渣尘。
根据设备的不同,可分为机械化澄清槽和焦油氨水分离槽两种形式。
操作要点主要是温度及分离时间。
相对来说,分离时间越长则分离效果越好,而分离温度却由于静置冷却作用而变低(温度高时焦油粘度小有利于分离)。
一般焦油氨水分离槽有保温系统,能够同时满足温度和分离时间两个因素的要求。
氮转化成以氨为代表的含氮化合物,因此粗煤气中含有6g/m ~9g/m 的氨。
由于氨的腐蚀特性,作为有害成分必须从煤气中除去。
目前采用的脱氨方法主要有3类。
(3)磷酸吸氨法,包括磷酸氢二铵法和弗萨姆法、半直接饱和器吸收器后含氨可控制在0.03g/m 以下,水洗氨和氨分解联合流程,目前塔后含氨在 以下。
1.2.3 煤气中氨类的脱除煤在干馏时,其中大部分(1)水洗法,包括浓氨水法、间接法制 NH SO 、联碱法制N H Cl 、氨分解法等。
(2)硫酸吸氨法生产 NH SO ,有饱和器法和酸洗塔法。
法。
0.05g/m1.2.4来并溶于焦油中,含量约为2g/m 的萘处于过饱和状态,初冷后的煤气沿管道流向后序净化设备时,一旦流速缓慢或温度进一塞,因此煤气进一步脱萘是必要的。
目前脱萘主要有两种方式,水洗法和油洗法。
所谓水洗法是利用终冷塔中冷水与热煤气的逆向接触,吸收其中的萘,而从洗油中分离萘可以同富油脱苯同时进行,该法较水洗法效率高,一般可将煤气含萘降至0.5g/m 以下。
煤气中苯类脱除理论上可以通过冷冻、吸附、洗涤3种方式完成。
工业上主要采用油洗涤方式,根据使用洗油的来源及组份差别,分为焦油洗油洗苯和石油洗油洗苯。
有粗焦油加工系统的大型焦化厂均采洗触,要具备足够的吸收面积、吸收时间、吸收推动力(温度、塔内压力、贫油含苯)、洗油分子量及喷淋量等,洗涤后煤气中苯可由25g/m ~38g/m 降至2g 煤气中萘的脱除工艺粗煤气中含萘约10g/m ,其中大部分在集气管初冷器中冷凝下经过初冷后,步下降,萘就会沉积析出并造成堵降低煤气温度使萘析出,再利用热焦油吸收水中的萘而实现冷水循环洗萘。
油洗萘是利用洗油洗涤煤气并1.2.5 煤气中苯类的脱除及回收用自产焦油洗油洗涤方式。
在洗涤塔中煤气与油逆向接/m 以下。
洗苯后的富油经蒸馏解析后返回洗涤,轻苯和重苯送后续系统进一步加工。
1.2.6 煤气中H S 的脱除直接从焦炉中出来的煤气约含5g/m ~8g/m 的硫化氢和m 1g/ ~2.5g/m 的氰化氢。
目前国内外关于H S 和HCN 的脱除方式主要有3类:(1)干式氧化工艺(3)湿式吸收工艺国应用,是19世纪40年代随着城市煤气工业的诞生而产生的。
干法脱硫工艺度厂。
干法脱硫工艺及功能的局限性,制约了其在焦化生脱硫脱氰的湿式氧化法工艺技术经历了长期的落后的砷减法、对苯二酚法等,到现代的日本斯法)、FRC 法(苦味酸法)等。
其中关于氨水(2)湿式氧化工艺干式氧化工艺常见的是氧化铁箱法。
氧化铁脱硫最早在德简单、净化程高。
但仅适用于那些煤气须在高压下净化,符合城市煤气质量的工产中的应用。
焦炉煤气发展过程,从早期比较研制的TH 法(塔卡哈克湿式氧化脱硫,国外进行了大量的研究。
早在1972年,德国就“氨水湿式氧化法脱硫和废液加入炼焦煤”的工艺申请了专利。
日本大胶公司发明了FUMLKS——RHODACSCOMPACKS(FRC)法脱硫脱氰技术。
在湿式氧化工艺中,Stretford 法也是一种较为广泛采用的工艺流程。
英国的霍姆公司、法国的瑟雷芒日焦化厂、加拿大、意大利等国的焦化厂大多采用这种工艺。
焦炉煤气脱硫脱氰的湿式吸收法有VacuumCarbonate(真空碳酸盐)法、朋循环洗涤法、Sud—fiban 法(索尔菲班法)等。
真空碳酸盐法脱硫系统的操作是基于吸收—解析的原理,焦炉煤气与碳酸钠混合物接触,只有酸性气体被溶液吸收,吸收了H S ,HCN 和C O 的溶液循环到再生塔,调节塔内的温度和压力,把酸性气体从溶液中赶出来。
此法在原苏联乌克兰大多数的焦化厂采用,美国、德国等国家焦化厂也采用此法。
以氨为碱源的湿式吸收法目前在国外应用最为广泛,其中最但由于单乙醇胺昂贵,转中有损耗,因此,该法操作费用大。
鼓风机是煤气输送装置,按结构分为容积式和离心式两种。
离心式鼓风机按动力源又分为电动式和透平式。
在离心式鼓风机使用厂家中,按机前、机后压力调节方式可分为循环煤气调节、自动调节机调节和改变鼓风机转速法调节。
大型焦化厂多数采用离心式鼓风机。
现有焦炉煤气净化技术存在的问题随着世界范围内环保法规的日趋严格以及环保意识的不断增强,传统的煤气净化技术己不能满足需要,染等缺陷。
尤其是氨和苯多未回收或回收率低,高热值煤气未合理利用,因而经济效益差。
焦炉煤气中H S ,HCN 及其燃烧产物对大气环境的污染问题日益突出,严重影响了焦化工业的可持续发展,改造现有焦炉煤气净化工艺技术刻不容缓。
典型的工艺为AS 循环洗涤法。
Sulfiban 法是一种高效的脱硫脱氰工艺,脱硫效率在98%以上,脱氰率也高于90%,同时还能脱除焦炉煤气中的有机硫。
素尔菲班法与其它脱硫法相比,工艺设备简单、操作弹性大、材质要求低、投资费用小,且运1.2.7 煤气的输送及调节日益显示出资源浪费和环境污(1)消除焦炉加热煤气管道的堵塞、腐蚀等问题,改善焦炉加热条件,同时使合理利用焦炉煤气,促进焦炉生产正常化。
(2)确保氨、苯烃及焦炉煤气等资源的合理利用,节能降耗,降低焦炭生产成本,提高企业经济效益。
(3)降低中小型焦化厂生产过程中废水、废气、烟尘和有毒物1.3. 焦炉煤气净化新技术探讨质的排放量,保护环境。
在更新改造传统的煤气净化技术的同时,应研发新型节能的焦炉煤气净化技术。
将烟气冷凝净化法移植应用于焦炉煤气净化系统,通过分阶段冷却和除尘替代传统焦化系统中直接用氨水喷淋荒煤气的湿法熄焦,是非常有发展前景的焦炉煤气净化新技术。
焦炉煤气净化新工艺流程统中的温度分布。
从焦炉出口的煤气(约800℃~850℃)首先经过热回收器,通过热交换后煤气被冷却到500℃左右,同时从热回收器出来的热空气是一种很好的热源。
而后煤气进入旋风除尘器,除去煤气中的粗粉尘,再由底部进入陶瓷除尘塔,经过塔内陶瓷球的过滤吸附,除去高温煤气中直径在50μm 左右的细粉尘颗粒。
当陶瓷球达到饱和状态,启动陶瓷球连续再生装置,的干净煤气进入焦油冷却分离器,煤气温度控制在400℃左右,由于焦炉煤气在1.3.1 工艺流程与原理该技术关键是准确控制整个系清掉陶瓷球表面的灰尘,再生循环使用。
从陶瓷塔顶出来400℃以下会产生焦油凝集,必须及时分离冷凝的焦油,防止其冷凝在换热管管壁上,堵塞煤气通道。
因此冷却分离器整体倾斜放置以利于焦油的流动。
并且,分离器底部分段设置引流槽,对不同温度段冷凝出来的焦油分段引出。
出焦油冷却分离器的煤气温度控制在85℃~100℃,进入初冷塔脱萘,最后煤气进入深冷室,冷冻温度15℃~20℃,分离纯化煤气中的H S,S O ,HCN等。
深冷部分采用自行设计的热制冷系统。
1.3.2工艺特点(1)粉尘去除率高。
经过旋风除尘和高温陶瓷除尘,煤气中的粉尘去除率很高。
(2)热回收利用率高。
用分阶段冷却和除尘替代传统焦化系统中直接用氨水喷淋荒煤气,可回收利用大量的焦炭显热(据统计,焦炉耗热量中焦炭的显热占40%,干熄焦设备可回收焦炭显热的80%),是焦化厂最大节能和环保项目,系统中热制冷的热源就是焦油冷却分离器的冷却介质油。
(3)减轻了焦化废水的处理难度。
采用物理方法来回收荒煤气中的焦油,就避免了由氨水喷淋所引起的化学反应而产生的多余杂质成分和N比进入焦炉煤气,有利于后阶段的煤气净化,也大大减少了焦化废水的排放量,降低了焦化废水的处理难度,为焦化污染治理提供了新技术、新思路。
1.4.结束语概述了目前国内外关于煤气净化技术方面的几种常见工艺选择,初步探讨了煤气净化新技术。