车间7S管理规范(新版)
生产车间7s标准

生产车间7s标准引言概述:生产车间7S标准是一种管理方法,旨在提高生产车间的效率和组织性。
它包括七个要素,即整理、整顿、清扫、清洁、标准化、素养和安全。
本文将详细阐述生产车间7S标准的内容和重要性。
正文内容:一、整理1.1 丢弃无用物品:清理生产车间中的废弃物品和无用物品,减少杂乱度。
1.2 分类整理:将生产车间的物品按照功能或用途进行分类整理,提高工作效率。
1.3 设置物品归位:为每个物品设定固定的存放位置,方便使用和管理。
二、整顿2.1 设定工作流程:明确生产车间的工作流程,确保每个工序的顺序和内容。
2.2 标识化管理:使用标识牌、标志和标识线等,标明物品和设备的位置和用途。
2.3 制定标准作业程序:对每个工序制定标准作业程序,确保操作的一致性和规范性。
三、清扫3.1 清除生产车间的垃圾和杂物:保持生产车间的整洁,减少污染和安全隐患。
3.2 定期清洁设备和工具:定期对生产设备和工具进行清洁,确保其正常运行和延长使用寿命。
3.3 建立清洁检查机制:制定清洁检查计划,定期检查清洁情况,及时发现问题并进行整改。
四、清洁4.1 清洁生产车间的地面和墙壁:保持地面和墙壁的清洁,减少灰尘和细菌的滋生。
4.2 清洁生产设备和工具:定期对生产设备和工具进行清洁,确保其正常运行和延长使用寿命。
4.3 清洁生产材料和产品:确保生产材料和产品的质量和卫生安全。
五、标准化5.1 制定工作标准:对每个工序制定工作标准,明确操作要求和质量标准。
5.2 实施标准化培训:对员工进行标准化培训,提高操作技能和质量意识。
5.3 建立标准化检查机制:制定标准化检查计划,定期检查操作和质量情况,及时发现问题并进行整改。
总结:生产车间7S标准对于提高生产车间的效率和组织性具有重要意义。
通过整理、整顿、清扫、清洁、标准化等七个要素的实施,可以减少杂乱度,提高工作效率,确保操作的一致性和规范性,保持生产车间的整洁和卫生,提高产品质量和安全性。
生产车间7s标准
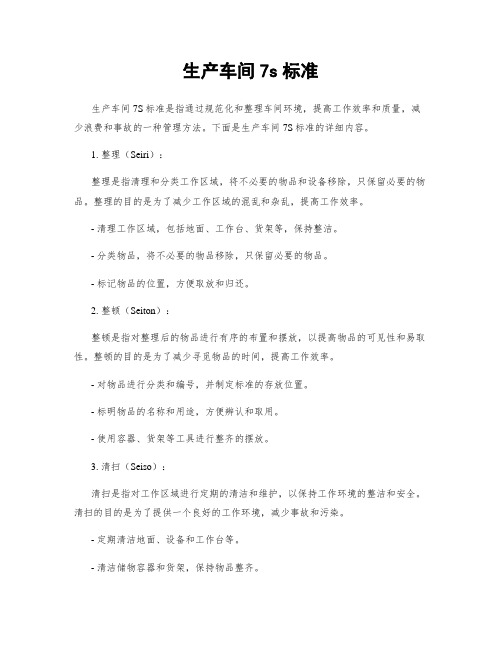
生产车间7s标准生产车间7S标准是指通过规范化和整理车间环境,提高工作效率和质量,减少浪费和事故的一种管理方法。
下面是生产车间7S标准的详细内容。
1. 整理(Seiri):整理是指清理和分类工作区域,将不必要的物品和设备移除,只保留必要的物品。
整理的目的是为了减少工作区域的混乱和杂乱,提高工作效率。
- 清理工作区域,包括地面、工作台、货架等,保持整洁。
- 分类物品,将不必要的物品移除,只保留必要的物品。
- 标记物品的位置,方便取放和归还。
2. 整顿(Seiton):整顿是指对整理后的物品进行有序的布置和摆放,以提高物品的可见性和易取性。
整顿的目的是为了减少寻觅物品的时间,提高工作效率。
- 对物品进行分类和编号,并制定标准的存放位置。
- 标明物品的名称和用途,方便辨认和取用。
- 使用容器、货架等工具进行整齐的摆放。
3. 清扫(Seiso):清扫是指对工作区域进行定期的清洁和维护,以保持工作环境的整洁和安全。
清扫的目的是为了提供一个良好的工作环境,减少事故和污染。
- 定期清洁地面、设备和工作台等。
- 清洁储物容器和货架,保持物品整齐。
- 检查并修复设备和工具的故障。
4. 清洁(Seiketsu):清洁是指对整个工作区域的定期检查和整理,以保持清洁和卫生的工作环境。
清洁的目的是为了提高工作效率和员工的工作满意度。
- 检查工作区域是否有杂物和污渍,及时清理。
- 定期检查设备和工具的状态,及时维修和更换。
- 培养员工的清洁习惯,定期进行培训和宣传。
5. 纪律(Shitsuke):纪律是指对员工的培训和管理,以保证7S标准的执行和持续改进。
纪律的目的是为了确保标准的执行和维护。
- 培训员工关于7S标准的知识和技能。
- 设立奖惩制度,激励员工积极参预。
- 定期检查和评估7S标准的执行情况,及时纠正和改进。
6. 安全(Safety):安全是指对工作环境和操作过程进行评估和管理,以保障员工的安全和健康。
安全的目的是为了减少事故和伤害。
生产车间7s标准

生产车间7s标准一、背景介绍生产车间是企业生产创造的重要场所,为了提高生产效率、优化工作环境、确保产品质量,采用7S管理方法是一种有效的管理手段。
本文将详细介绍生产车间7S标准的具体要求和实施步骤。
二、生产车间7S标准的具体要求1. 整理(Seiri)整理是指对生产车间内的物品进行分类、清理和整理,确保只保留必要的物品,清除无用、过期或者损坏的物品。
具体要求如下:- 对生产车间内的物品进行分类,按照功能和用途进行分组。
- 清理车间内的垃圾和废弃物,确保车间环境整洁。
- 整理物品摆放位置,确保物品摆放合理、便于取用。
2. 整顿(Seiton)整顿是指对生产车间内的物品进行有序的摆放和标识,确保物品易于找到和取用。
具体要求如下:- 对生产车间内的物品进行标识,使用标签、颜色等方式进行标记。
- 对物品进行编号,建立物品清单和库存管理系统。
- 确定物品的存放位置,采用标准化的摆放方式,确保物品摆放整齐、规范。
3. 清扫(Seiso)清扫是指对生产车间进行定期的清洁和维护,确保车间环境整洁、无尘、无杂物。
具体要求如下:- 制定清扫计划和清洁标准,明确清扫的频率和责任人。
- 清洁车间地面、墙壁、设备等,清除积尘和污渍。
- 定期检查设备和工具的使用状况,及时进行维护和保养。
4. 清洁(Seiketsu)清洁是指对生产车间进行标准化的清洁管理,确保车间环境整洁、无异味、无污染。
具体要求如下:- 制定清洁标准和操作规程,确保清洁工作按照标准进行。
- 建立清洁检查制度,定期检查车间的清洁情况。
- 培训员工清洁操作技能,提高清洁意识和责任心。
5. 纪律(Shitsuke)纪律是指对生产车间进行规范化管理,确保员工按照规定的要求进行工作。
具体要求如下:- 建立规章制度,明确员工的工作职责和行为规范。
- 培养员工的纪律意识,加强员工的培训和教育。
- 建立奖惩制度,激励员工遵守纪律和规定。
6. 安全(Anzen)安全是指对生产车间进行安全管理,确保员工的人身安全和设备的安全。
车间7S管理规定

车间7S管理规定
标题:车间7S管理规定
引言概述:车间7S管理是一种有效的管理方法,通过规范化车间环境和流程,提高生产效率和产品质量。
本文将介绍车间7S管理的规定和要求。
一、整理(Seiri)
1.1 清理工作台和生产设备,保持工作区域整洁。
1.2 丢弃无用的物品,减少杂物堆积。
1.3 为每种物品设定固定的存放位置,方便取放。
二、整顿(Seiton)
2.1 将工具和物料分类整理,确保易于取用。
2.2 设立标识牌和标识,明确物品的存放位置。
2.3 定期检查和整理工具和设备,确保工作区域整洁。
三、清扫(Seiso)
3.1 每日清洁工作区域,保持地面和设备清洁。
3.2 定期进行深度清洁,清除积尘和杂物。
3.3 检查设备和管道,确保无漏水、漏油等情况。
四、清洁(Seiketsu)
4.1 建立清洁标准和程序,确保工作区域清洁。
4.2 培训员工正确的清洁方法和技巧。
4.3 定期检查和评估清洁情况,及时改进不足之处。
五、素养(Shitsuke)
5.1 培养员工良好的工作习惯和素养。
5.2 建立奖惩机制,激励员工遵守规定。
5.3 定期进行7S管理评估,持续改进管理水平。
结论:车间7S管理规定是一种有效的管理方法,可以提高生产效率和产品质量,同时也能改善工作环境,提升员工素养。
公司应该严格执行7S管理规定,不断完善和改进管理体系,实现持续发展。
生产车间7s标准

生产车间7s标准引言概述:生产车间7s标准是一种管理方法,旨在提高生产车间的效率和质量。
它包括七个方面的要求,分别是整理、整顿、清扫、清洁、素质、安全和自律。
本文将详细介绍生产车间7s标准的内容和实施方法。
一、整理1.1 工作区域整理:将工作区域内的杂物和不必要的物品清理出去,保持工作区域的整洁和有序。
1.2 工具和设备整理:将工具和设备按照规定的位置摆放,方便使用和管理,避免浪费时间和精力去寻觅。
1.3 文件和资料整理:将文件和资料按照一定的分类和命名规则整理好,方便查找和使用,提高工作效率。
二、整顿2.1 工作流程整顿:对工作流程进行分析和优化,消除不必要的环节和浪费,提高生产效率和质量。
2.2 工作规范整顿:明确工作规范和标准,确保每一个员工都按照规定的方法和要求进行工作,减少错误和质量问题。
2.3 设备维护整顿:建立设备维护计划,定期检查和保养设备,确保设备的正常运转和寿命。
三、清扫3.1 工作区域清扫:定期清扫工作区域,清除灰尘和杂物,保持工作环境的整洁和舒适。
3.2 设备清扫:定期清洗和保养设备,确保设备的正常运转和卫生,减少故障和事故的发生。
3.3 作业工具清扫:保持作业工具的清洁和整洁,减少污染和交叉感染的风险,提高产品的质量和安全性。
四、清洁4.1 产品清洁:对生产的产品进行清洁,确保产品的质量和卫生,满足客户的需求和期望。
4.2 设备清洁:定期清洗和保养设备,确保设备的正常运转和卫生,减少故障和事故的发生。
4.3 工作区域清洁:保持工作区域的清洁和整洁,减少污染和交叉感染的风险,提高工作效率和员工的工作积极性。
五、素质5.1 职业素质:培养员工的职业素质,包括工作态度、沟通能力、团队合作等方面,提高员工的综合素质和工作效率。
5.2 知识素质:提供员工的专业知识和技能培训,提高员工的专业素质和工作能力,推动技术进步和创新。
5.3 安全素质:加强员工的安全意识和安全知识培训,确保员工的人身安全和工作环境的安全,减少事故的发生。
生产车间7s标准

生产车间7s标准一、引言生产车间7S标准是指通过对生产车间进行整理、整顿、清扫、清洁、标准化、素质教育和自律等七个方面的管理,达到提高工作效率、优化工作环境、提升产品质量的目的。
本文将详细介绍生产车间7S标准的具体要求和实施方法。
二、整理(Seiri)整理是指对生产车间内的物品进行分类、清点和整理,保持工作区域的整洁和有序。
具体要求如下:1. 对生产车间内的物品进行分类,将必要的物品与非必要的物品分开。
2. 清点物品数量,确保库存数量与实际需求相符。
3. 整理物品摆放位置,保持工作区域的整洁和有序。
三、整顿(Seiton)整顿是指对生产车间内的物品进行合理摆放,使其易于取用和归还。
具体要求如下:1. 设定合理的物品存放位置,便于工人取用和归还。
2. 对物品进行标识和编号,以便于管理和追踪。
3. 根据物品的使用频率和重要性,合理安排物品的摆放位置。
四、清扫(Seiso)清扫是指对生产车间内的设备、工具和工作区域进行定期清洁,保持工作环境的整洁和卫生。
具体要求如下:1. 定期清洁设备和工具,确保其正常运行和安全使用。
2. 清扫工作区域,清除垃圾和杂物,保持地面干净整洁。
3. 清洗工作台和工作台面,保持产品的卫生和质量。
五、清洁(Seiketsu)清洁是指对生产车间内的空气、水源和环境进行清洁和净化,保持工作环境的清新和健康。
具体要求如下:1. 定期清洁空气过滤器和通风设备,确保空气质量达标。
2. 检查水源质量,保证生产过程中使用的水源符合卫生标准。
3. 定期消毒工作区域,预防细菌和病毒的传播。
六、标准化(Standardize)标准化是指通过制定工作标准和流程,确保生产车间的工作方式和质量达到统一的标准。
具体要求如下:1. 制定工作流程和操作规范,确保每个工作环节都按照标准进行。
2. 建立质量检查标准和流程,确保产品质量符合要求。
3. 建立绩效评估标准和流程,对员工的工作进行评估和奖惩。
七、素质教育和自律(Shitsuke)素质教育和自律是指通过培训和教育,提高员工的工作素质和自我管理能力。
车间7S管理规定

车间7S管理规定引言概述:车间7S管理规定是指在生产车间中,通过对工作环境进行整理、整顿、清洁、清扫、安全、素养、自律等七个方面的管理,以提高生产效率、质量和员工工作积极性的一种管理方法。
本文将从七个方面详细阐述车间7S管理规定的内容。
一、整理(Sort)1.1 确定工作区域和物品的归类:根据工作内容和功能,将工作区域和物品进行分类,确保物品摆放有序,易于取用。
1.2 建立物品管理制度:制定物品使用和归还的规定,明确责任人,确保物品的归位和整理。
1.3 定期清理废弃物:定期检查工作区域,清理废弃物,保持工作环境整洁。
二、整顿(Set in order)2.1 制定工作区域标识:为每个工作区域设置标识,标明区域用途和工作内容,便于员工理解和使用。
2.2 规划工作流程:分析工作流程,优化工作顺序和布局,减少不必要的移动和等待时间,提高工作效率。
2.3 制定物品放置标准:为每种物品规定放置位置和方式,减少物品的丢失和混乱,提高工作效率。
三、清洁(Shine)3.1 制定清洁计划:制定清洁工作的时间表和内容,明确责任人,确保每个工作区域都能保持干净整洁的状态。
3.2 培养员工清洁意识:加强员工的清洁培训,提高他们对清洁工作的重视,使清洁成为每个员工的责任。
3.3 定期设立清洁检查:定期检查工作区域的清洁状况,及时发现问题并进行整改,确保工作环境的整洁度。
四、清扫(Standardize)4.1 制定清扫标准:制定清扫的具体标准和方法,明确清扫的频率和内容,确保清扫工作的质量和效果。
4.2 建立清扫记录:建立清扫记录表,记录每次清扫的时间、人员和内容,便于查阅和追溯。
4.3 培养员工清扫习惯:通过培训和激励机制,培养员工的清扫习惯,使其成为日常工作的一部分。
五、安全(Safety)5.1 制定安全操作规程:制定安全操作规程,明确员工在工作中应注意的安全事项,确保员工的人身安全。
5.2 定期进行安全培训:定期组织安全培训,提高员工的安全意识和技能,降低事故发生的概率。
生产车间7s标准

生产车间7s标准引言概述:生产车间7s标准是一种管理方法,旨在通过整理、整顿、清扫、清洁、安全、素养和遵守规章制度,实现生产车间的高效运作。
本文将详细介绍生产车间7s标准的五个部分,包括整理、整顿、清扫、清洁和安全。
一、整理:1.1 整理工作台:将工作台上的工具、文件和杂物归位,保持工作台整洁有序。
1.2 整理物料区:按照物料种类进行分类整理,确保物料摆放合理,易于取用。
1.3 整理设备区:将设备按照功能和使用频率进行整理,确保设备摆放合理,便于操作和维护。
二、整顿:2.1 整顿工作流程:对生产车间的工作流程进行分析和优化,消除不必要的环节和浪费,提高生产效率。
2.2 整顿工作规范:制定明确的工作规范,明确每个员工的职责和工作流程,确保工作有序进行。
2.3 整顿生产线布局:根据生产需求和工艺流程,对生产线进行布局调整,提高生产效率和质量。
三、清扫:3.1 清扫地面:定期清扫车间地面,清除杂物和灰尘,确保车间环境整洁。
3.2 清扫设备:定期对设备进行清洁和维护,确保设备正常运转,减少故障发生。
3.3 清扫工作区:每个员工在工作结束后,清扫自己的工作区域,保持工作环境整洁。
四、清洁:4.1 清洁工具和设备:定期对工具和设备进行清洁和消毒,确保使用安全和卫生。
4.2 清洁生产线:定期对生产线进行清洁,清除积尘和杂物,确保生产环境洁净。
4.3 清洁物料存放区:保持物料存放区干净整洁,避免杂物和灰尘对物料的污染。
五、安全:5.1 安全设施检查:定期检查安全设施的完好性,如灭火器、应急疏散通道等,确保安全设施可用。
5.2 安全培训和意识:定期进行安全培训,提高员工的安全意识,减少事故发生。
5.3 安全管理制度:建立完善的安全管理制度,明确责任和流程,确保安全工作的有效进行。
结论:通过遵守生产车间7s标准,可以有效提高生产车间的工作效率和质量,减少浪费和事故的发生。
每个部分的细节都需要重视和执行,只有全面贯彻整个标准,才能实现生产车间的高效运作。
生产车间7s标准

生产车间7s标准标题:生产车间7s标准引言概述:在现代生产车间管理中,7s标准是一种非常重要的管理方法,通过对车间环境、设备、人员等方面进行全面管理,提高生产效率和质量。
本文将详细介绍生产车间7s标准的内容和实施方法。
一、整理(Seiri)1.1 确定必需物品:首先要确定车间中必需的物品,将不必要的物品清理出去。
1.2 分类整理:对必需物品进行分类整理,确保物品摆放合理、易于取用。
1.3 标识物品:为每类物品设立明确的标识,方便工人快速找到需要的物品。
二、整顿(Seiton)2.1 设立标准化工位:为每一个工位设立标准化的工具和物品摆放位置。
2.2 保持整洁:定期清理工位,保持工位整洁,确保工作环境清爽。
2.3 制定清洁计划:制定清洁计划,明确责任人和清洁频率,保持工位整洁。
三、清扫(Seiso)3.1 定期清洁设备:定期对设备进行清洁和维护,确保设备正常运转。
3.2 清洁地面:保持地面干净整洁,减少地面污染对生产的影响。
3.3 清洁空气:保持车间空气流通,减少粉尘和异味对员工健康的影响。
四、清洁(Seiketsu)4.1 制定清洁标准:制定清洁标准,规范清洁作业流程,确保清洁工作质量。
4.2 培训员工:对员工进行清洁知识和技能培训,提高员工清洁意识。
4.3 定期检查:定期检查清洁工作执行情况,及时发现问题并改进。
五、素质(Shitsuke)5.1 培养良好习惯:培养员工良好的工作习惯,如按时上班、遵守规章制度等。
5.2 奖惩机制:建立奖惩机制,激励员工积极参预7s标准的执行。
5.3 持续改进:持续改进7s标准,不断完善管理方法,提高生产效率和质量。
结论:生产车间7s标准是一种全面管理方法,通过整理、整顿、清扫、清洁、素质五个方面的管理,可以提高生产效率和质量,营造良好的工作环境。
企业应该重视7s标准的执行,不断完善管理方法,实现持续改进。
生产车间7s标准

生产车间7s标准引言概述:生产车间7s标准是指通过对车间环境进行整理、清洁、整顿、清洁、标准化、素质、维护七个方面的管理,使生产车间达到高效、安全、整洁的工作状态。
遵循7s标准可以提高生产效率,减少浪费,提升员工工作积极性,是现代生产管理的重要手段。
一、整理 (Sort)1.1 清理无用物品:将车间内无用的工具、设备、杂物等清理出去,避免占用空间和干扰工作。
1.2 分类整理:将工具、设备按照类别进行整理,便于取用和管理。
1.3 设立标识:为每一个物品设立标识,清晰明了,方便员工识别和归纳。
二、清洁 (Sweep)2.1 定期清扫:每天对车间进行定期清扫,保持地面、设备、工作台面清洁。
2.2 清洁工具准备:准备好清洁工具,如扫帚、拖把、清洁剂等,方便员工使用。
2.3 垃圾分类:对车间产生的垃圾进行分类处理,有害垃圾、可回收垃圾等分开存放。
三、整顿 (Set in order)3.1 工作台整理:将工作台上的工具、文件整理归纳,确保工作台面整洁有序。
3.2 设立工作标准:为每项工作设立标准作业流程,明确员工工作内容和要求。
3.3 工具管理:对工具进行编号管理,确保每一个工具有固定的存放位置,方便取用和管理。
四、标准化 (Standardize)4.1 制定规范:制定生产车间的标准化管理规范,明确各项工作的标准和要求。
4.2 培训员工:对员工进行7s标准的培训,让每位员工都了解并遵守标准化管理规范。
4.3 持续改进:定期评估生产车间的7s标准执行情况,及时发现问题并进行改进。
五、素质 (Sustain)5.1 全员参预:要求所有员工都参预到7s标准的执行中,形成全员参预、全员负责的管理模式。
5.2 催促检查:设立专门的督查组织,定期检查车间的7s标准执行情况,发现问题及时解决。
5.3 持续改进:鼓励员工提出改进建议,不断完善生产车间的管理体系,提高生产效率和质量。
结语:生产车间7s标准是一种有效的管理方法,通过整理、清洁、整顿、清洁、标准化、素质、维护七个方面的管理,可以提高生产效率,减少浪费,提升员工工作积极性,为企业创造更大的价值。
车间7S管理规定
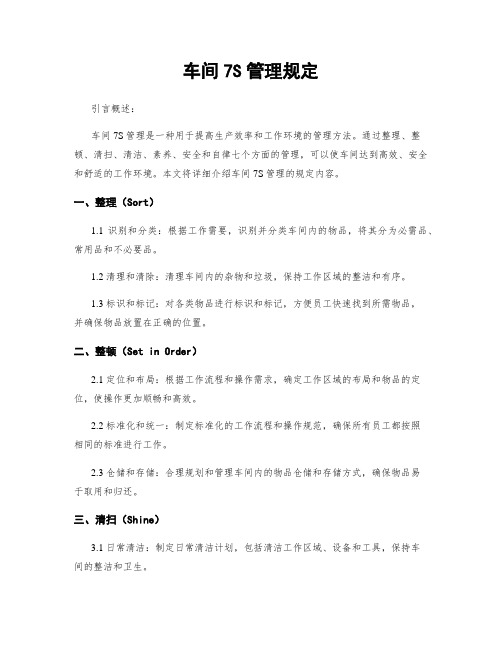
车间7S管理规定引言概述:车间7S管理是一种用于提高生产效率和工作环境的管理方法。
通过整理、整顿、清扫、清洁、素养、安全和自律七个方面的管理,可以使车间达到高效、安全和舒适的工作环境。
本文将详细介绍车间7S管理的规定内容。
一、整理(Sort)1.1 识别和分类:根据工作需要,识别并分类车间内的物品,将其分为必需品、常用品和不必要品。
1.2 清理和清除:清理车间内的杂物和垃圾,保持工作区域的整洁和有序。
1.3 标识和标记:对各类物品进行标识和标记,方便员工快速找到所需物品,并确保物品放置在正确的位置。
二、整顿(Set in Order)2.1 定位和布局:根据工作流程和操作需求,确定工作区域的布局和物品的定位,使操作更加顺畅和高效。
2.2 标准化和统一:制定标准化的工作流程和操作规范,确保所有员工都按照相同的标准进行工作。
2.3 仓储和存储:合理规划和管理车间内的物品仓储和存储方式,确保物品易于取用和归还。
三、清扫(Shine)3.1 日常清洁:制定日常清洁计划,包括清洁工作区域、设备和工具,保持车间的整洁和卫生。
3.2 定期保养:制定设备和工具的定期保养计划,确保其正常运行和延长使用寿命。
3.3 保持清洁:培养员工的清洁习惯,保持车间的整洁和清洁,提高工作效率和品质。
四、清洁(Standardize)4.1 工作标准:制定工作标准和操作规范,确保所有员工都按照相同的标准进行工作。
4.2 检查和评估:定期检查和评估车间的7S管理情况,及时发现问题并采取措施解决。
4.3 持续改进:根据检查和评估结果,不断改进和优化车间的7S管理,提高管理水平和效果。
五、素养(Self-discipline)5.1 培训和教育:对员工进行7S管理知识的培训和教育,提高员工的素养和意识。
5.2 自我管理:培养员工的自我管理能力,提高工作效率和自律性。
5.3 团队合作:鼓励员工之间的团队合作和互助,共同维护和改进车间的7S管理。
生产车间7s标准

生产车间7s标准引言概述:生产车间7s标准是一种用于提高生产效率和工作环境整洁度的管理方法。
它通过规范化和优化工作区域,达到提高工作效率、减少浪费和提升员工工作积极性的目的。
本文将从四个方面详细阐述生产车间7s标准的内容和实施方法。
一、整理(Sort)1.1 清理工作区域:将生产车间内的杂物、废弃物等进行清理,确保工作区域整洁有序。
1.2 标识物品:对生产车间内的物品进行标识,以便员工能够方便地找到所需物品,减少寻觅时间。
1.3 优化物品摆放位置:根据工作流程和使用频率,合理安排物品的摆放位置,减少员工挪移的时间和精力。
二、整顿(Set in Order)2.1 制定工具放置标准:对于常用的工具和设备,制定放置标准,确保每一个工具都有固定的位置,方便员工使用和归还。
2.2 制定物品归类标准:将生产车间内的物品按照类别进行归类,制定明确的归类标准,便于员工寻觅和管理。
2.3 制定工作区域布局:根据工作流程和工作要求,合理规划工作区域的布局,使得员工能够高效地完成工作任务。
三、清扫(Shine)3.1 定期清洁工作区域:制定清洁计划,定期对生产车间进行清洁,包括地面、设备、工作台等,保持整洁的工作环境。
3.2 培养员工清洁习惯:加强员工对清洁的重视,培养他们的清洁习惯,使得每一个员工都能够自觉地保持工作区域的整洁。
3.3 检查和维护设备:定期检查和维护生产设备,确保其正常运行,减少故障和停机时间。
四、标准化(Standardize)4.1 制定标准作业程序:对于各项工作任务,制定标准作业程序,明确每一个步骤的操作规范和要求,提高工作效率和质量。
4.2 建立绩效评估机制:建立绩效评估机制,对员工的工作表现进行评估和反馈,激励员工积极参预和遵守标准化操作。
4.3 建立持续改进机制:建立持续改进机制,定期评估和分析生产车间的工作效率和整洁度,寻觅改进的空间和机会,推动生产车间的不断进步。
通过实施生产车间7s标准,可以提高生产效率,减少浪费,提升员工工作积极性。
生产车间7s标准
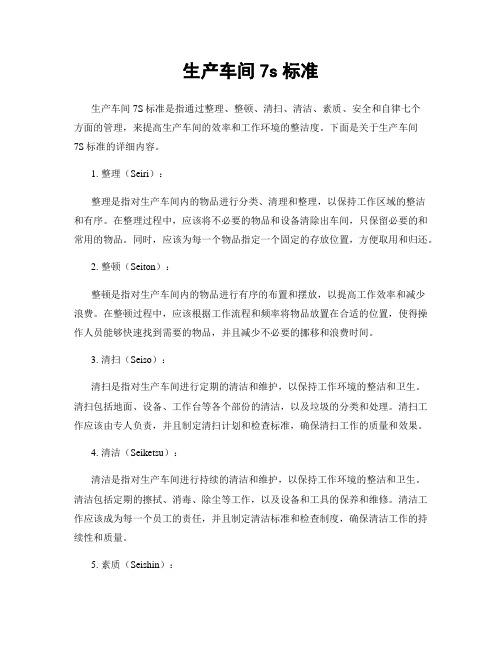
生产车间7s标准生产车间7S标准是指通过整理、整顿、清扫、清洁、素质、安全和自律七个方面的管理,来提高生产车间的效率和工作环境的整洁度。
下面是关于生产车间7S标准的详细内容。
1. 整理(Seiri):整理是指对生产车间内的物品进行分类、清理和整理,以保持工作区域的整洁和有序。
在整理过程中,应该将不必要的物品和设备清除出车间,只保留必要的和常用的物品。
同时,应该为每一个物品指定一个固定的存放位置,方便取用和归还。
2. 整顿(Seiton):整顿是指对生产车间内的物品进行有序的布置和摆放,以提高工作效率和减少浪费。
在整顿过程中,应该根据工作流程和频率将物品放置在合适的位置,使得操作人员能够快速找到需要的物品,并且减少不必要的挪移和浪费时间。
3. 清扫(Seiso):清扫是指对生产车间进行定期的清洁和维护,以保持工作环境的整洁和卫生。
清扫包括地面、设备、工作台等各个部份的清洁,以及垃圾的分类和处理。
清扫工作应该由专人负责,并且制定清扫计划和检查标准,确保清扫工作的质量和效果。
4. 清洁(Seiketsu):清洁是指对生产车间进行持续的清洁和维护,以保持工作环境的整洁和卫生。
清洁包括定期的擦拭、消毒、除尘等工作,以及设备和工具的保养和维修。
清洁工作应该成为每一个员工的责任,并且制定清洁标准和检查制度,确保清洁工作的持续性和质量。
5. 素质(Seishin):素质是指员工的素质和态度,包括对工作的热情、责任心、团队合作等方面。
在生产车间中,员工应该具备良好的职业道德和工作态度,积极参预工作,并且遵守规章制度和安全操作规程。
同时,应该加强培训和教育,提高员工的技能和素质,以提高生产车间的整体素质。
6. 安全(Seikatsu):安全是指对生产车间进行安全管理和风险控制,以确保员工的生命安全和工作环境的安全性。
在生产车间中,应该制定安全操作规程和应急预案,加强安全培训和教育,提高员工的安全意识和应对能力。
同时,应该定期进行安全检查和隐患排查,及时处理和纠正安全问题。
车间7S管理规定

车间7S管理规定一、背景介绍车间7S管理是指通过整理、整顿、清扫、清洁、标准化、素养和安全的七个方面的工作,来提高车间的生产效率和工作环境的整洁度。
本文将详细介绍车间7S管理的各项规定和要求,以确保车间的高效运作和员工的安全。
二、整理(Seiri)1. 要求每位员工每天开始工作前,对工作区域进行整理,清除多余的物品和杂物,保持工作区的整洁。
2. 严禁在车间内堆放无关物品,保持工作区域的空间整洁有序。
三、整顿(Seiton)1. 每位员工应按照工作需要,合理布置工作区域内的物品和设备,确保易于取用和归还。
2. 工作区域内的物品和设备应有明确的标识和编号,方便员工使用和管理。
四、清扫(Seiso)1. 每位员工每天结束工作后,要进行工作区域的清扫,包括地面、设备和工作台面等。
2. 清扫过程中,要注意安全,避免使用有损伤的清洁用具,确保清洁工作的质量。
五、清洁(Seiketsu)1. 车间内应保持干净、整洁的工作环境,确保工作区域的卫生。
2. 定期进行车间的大扫除,清洁工作应包括地面、墙壁、天花板、设备等各个部分。
六、标准化(Seiketsu)1. 制定并执行车间的标准化工作流程,确保工作的规范化和标准化。
2. 每位员工应按照规定的标准化流程进行工作,确保工作质量和效率。
七、素养(Shitsuke)1. 培养员工良好的工作习惯和素养,包括遵守工作纪律、保持良好的工作态度等。
2. 定期组织培训,提高员工的技能水平和工作素养。
八、安全管理1. 车间内应设置明显的安全警示标识,提醒员工注意安全。
2. 车间内的设备和机械应定期检修和维护,确保其安全可靠。
九、考核和改进1. 对车间7S管理进行定期考核,评估工作的执行情况和效果。
2. 根据考核结果,及时进行改进和调整,提高车间7S管理的水平。
综上所述,车间7S管理规定包括整理、整顿、清扫、清洁、标准化、素养和安全等七个方面的规定和要求。
通过严格执行这些规定,我们可以提高车间的生产效率,改善工作环境,确保员工的安全和健康。
车间7S管理规定

车间7S管理规定一、背景介绍车间7S管理是一种以改善工作环境和提高工作效率为目标的管理方法。
通过严格执行7S原则,即整理(Seiri)、整顿(Seiton)、清扫(Seiso)、清洁(Seiketsu)、素养(Shitsuke)、安全(Safety)、遵守(Standardization),可以改善车间的生产秩序、安全环境、工作效率和员工素质,进而提高产品质量和生产效益。
本文将详细介绍车间7S管理的具体要求和操作流程。
二、整理(Seiri)1. 工作内容:- 对车间内的物品进行分类,区分出必要和非必要的物品。
- 将非必要的物品进行处理,如清理、捐赠、报废等。
2. 操作流程:- 设定分类标准,如物品的使用频率、价值等。
- 对车间内的物品进行逐一检查,并按照分类标准进行分类。
- 对非必要的物品进行处理,并记录处理情况。
三、整顿(Seiton)1. 工作内容:- 对车间内的物品进行合理摆放,使其易于取用和归还。
- 设定物品摆放的标准和规范。
2. 操作流程:- 根据工作流程和使用频率,确定物品的摆放位置。
- 标识物品的摆放位置,如使用标识牌、标志等。
- 培训员工,使其了解物品摆放的标准和规范,并严格执行。
四、清扫(Seiso)1. 工作内容:- 对车间内的设备、工具、地面等进行定期清洁。
- 清除车间内的垃圾和杂物。
2. 操作流程:- 制定清扫计划,确定清扫的频率和责任人。
- 使用适当的清洁工具和清洁剂进行清扫。
- 检查清扫效果,并记录清扫情况。
五、清洁(Seiketsu)1. 工作内容:- 建立车间内的清洁标准和规范。
- 培养员工的清洁意识和习惯。
2. 操作流程:- 制定清洁标准和规范,包括车间内的清洁要求、频率等。
- 培训员工,使其了解清洁标准和规范,并严格执行。
- 定期检查清洁情况,并记录检查结果。
六、素养(Shitsuke)1. 工作内容:- 培养员工的自律、责任心和团队合作精神。
- 建立良好的工作习惯和行为规范。
车间7S管理规定
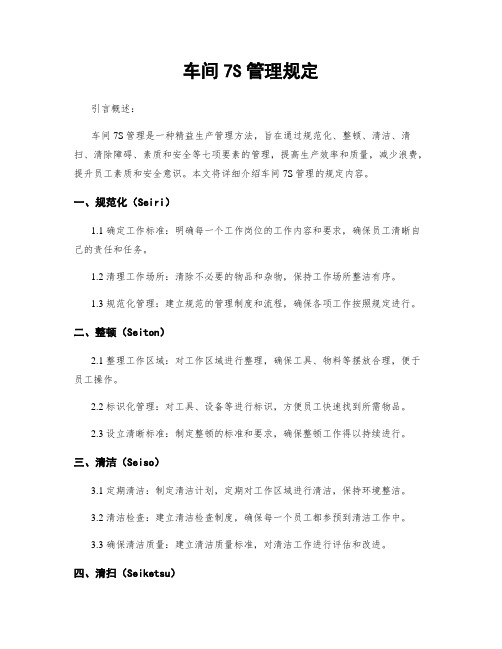
车间7S管理规定引言概述:车间7S管理是一种精益生产管理方法,旨在通过规范化、整顿、清洁、清扫、清除障碍、素质和安全等七项要素的管理,提高生产效率和质量,减少浪费,提升员工素质和安全意识。
本文将详细介绍车间7S管理的规定内容。
一、规范化(Seiri)1.1 确定工作标准:明确每一个工作岗位的工作内容和要求,确保员工清晰自己的责任和任务。
1.2 清理工作场所:清除不必要的物品和杂物,保持工作场所整洁有序。
1.3 规范化管理:建立规范的管理制度和流程,确保各项工作按照规定进行。
二、整顿(Seiton)2.1 整理工作区域:对工作区域进行整理,确保工具、物料等摆放合理,便于员工操作。
2.2 标识化管理:对工具、设备等进行标识,方便员工快速找到所需物品。
2.3 设立清晰标准:制定整顿的标准和要求,确保整顿工作得以持续进行。
三、清洁(Seiso)3.1 定期清洁:制定清洁计划,定期对工作区域进行清洁,保持环境整洁。
3.2 清洁检查:建立清洁检查制度,确保每一个员工都参预到清洁工作中。
3.3 确保清洁质量:建立清洁质量标准,对清洁工作进行评估和改进。
四、清扫(Seiketsu)4.1 制定清扫计划:建立清扫计划,确保每一个工作区域都得到定期清扫。
4.2 培训员工:对员工进行清扫技能培训,提高清扫效率和质量。
4.3 持续改进:定期评估清扫工作,找出问题并持续改进清扫管理。
五、清除障碍(Shitsuke)5.1 建立自律意识:培养员工的自律意识,确保员工自觉遵守7S管理规定。
5.2 奖惩机制:建立奖惩机制,激励员工遵守规定,惩罚违反规定的行为。
5.3 持续培训:定期对员工进行7S管理培训,提高员工对规定的理解和执行能力。
结语:车间7S管理规定是一种重要的管理方法,通过规范化、整顿、清洁、清扫、清除障碍、素质和安全等七项要素的管理,可以提高生产效率、质量和员工素质,降低浪费,确保生产安全。
企业应该严格执行7S管理规定,不断完善和改进管理制度,实现持续改进和提升。
工厂7S车间管理制度

工厂7S车间管理制度一、目的和范围为了改善工厂车间的管理效率和工作环境,提高员工的工作积极性和生产效率,特制定本车间管理制度。
二、七大管理要点1. 整理 (Seiri):整理车间,清理废弃物品和杂物,让工作场所保持整洁有序。
2. 整顿 (Seiton):将工作场所进行整顿,将设备、工具和物料按照一定的规定摆放,缩短工作路径,提高工作效率。
3. 清洁 (Seiso):经常清洗工作场所和设备,保持良好的工作环境。
4. 清楚 (Seiketsu):建立标准化工作程序,规范员工的工作行为,确保工作目标的达成。
5. 安全 (Anzen):确保工作场所安全,培养员工的安全意识,预防工伤事故的发生。
6. 节约 (Shitsuke):倡导节约使用资源和能源,提高生产效率。
7. 自律 (Shido):建立员工自律的意识,遵守各项规章制度,确保工作的顺利进行。
三、具体管理措施1.加强培训:对车间员工进行关于七S管理的培训,让他们了解七S管理的重要性和方法。
2.设立责任人:每个车间设立一名七S管理的责任人,负责车间的七S管理工作,定期检查并跟进改进措施。
3.制定工作标准:制定车间的工作标准,明确员工的工作职责和工作流程,确保工作的有条不紊进行。
4.创造奖惩机制:建立奖惩机制,对积极参与七S管理的员工进行奖励,对违反管理制度的员工进行惩罚。
5.开展定期检查:定期检查每个车间的七S管理情况,发现问题及时解决,并制定改进措施。
6.引入绩效指标:设立七S管理的绩效指标,用于衡量车间的管理水平和改进效果。
7.开展持续改进:定期开展七S管理的评估和改善活动,不断提高管理水平和工作效率。
四、管理制度落实1.全员参与:所有车间员工都应积极参与七S管理,遵守管理制度和要求。
2.持续改进:不断总结经验教训,改进管理制度,逐步提高管理水平。
3.管理评估:定期进行七S管理的评估,评估结果作为改进的基准和参考依据。
4.奖惩措施:对达到七S管理要求的车间和员工进行奖励,对未达到要求的进行惩罚或纠正。
车间7s管理制度范本

车间7s管理制度范本车间 7S 管理制度范本一、目的为了创造一个整洁、有序、安全、高效的工作环境,提高员工的工作效率和质量,降低生产成本,提升企业形象,特制定本车间 7S 管理制度。
二、适用范围本制度适用于车间内所有区域和人员。
三、7S 定义及要求1、整理(Seiri)定义:区分要与不要的物品,现场只保留必需的物品。
要求:对工作场所进行全面检查,包括设备、工具、物料、文件等。
区分必需品和非必需品,将非必需品清理出工作场所。
制定必需品的清单,并明确其存放位置和数量。
2、整顿(Seiton)定义:将必需品依规定位置摆放整齐,并加以标识。
要求:对整理后留下的必需品进行分类、定位、定量摆放。
采用合适的容器、货架、抽屉等存放物品,使其易于查找和取用。
对物品进行标识,包括名称、规格、数量、责任人等。
3、清扫(Seiso)定义:清除工作场所内的脏污,并防止污染的发生。
要求:划分清扫责任区域,明确责任人。
定期对工作场所进行清扫,包括地面、墙壁、设备、工具等。
建立清扫标准和检查制度,确保清扫工作的质量。
4、清洁(Seiketsu)定义:将整理、整顿、清扫进行到底,并且制度化,经常保持环境处在美观的状态。
要求:制定7S 管理制度和标准,将整理、整顿、清扫工作纳入日常管理。
定期对 7S 工作进行检查和评估,发现问题及时整改。
加强员工的 7S 意识教育,使 7S 工作成为员工的自觉行为。
5、素养(Shitsuke)定义:每位成员养成良好的习惯,并遵守规则做事,培养积极主动的精神(也称习惯性)。
要求:制定员工行为规范和工作纪律,加强员工的培训和教育。
建立激励机制,对遵守 7S 规定的员工进行奖励,对违反规定的员工进行处罚。
营造良好的企业文化氛围,使员工自觉遵守 7S 规定。
6、安全(Safety)定义:消除隐患,排除险情,预防事故的发生。
要求:建立安全管理制度和操作规程,加强员工的安全培训和教育。
对工作场所进行安全风险评估,采取相应的安全措施。
车间7s管理制度十篇
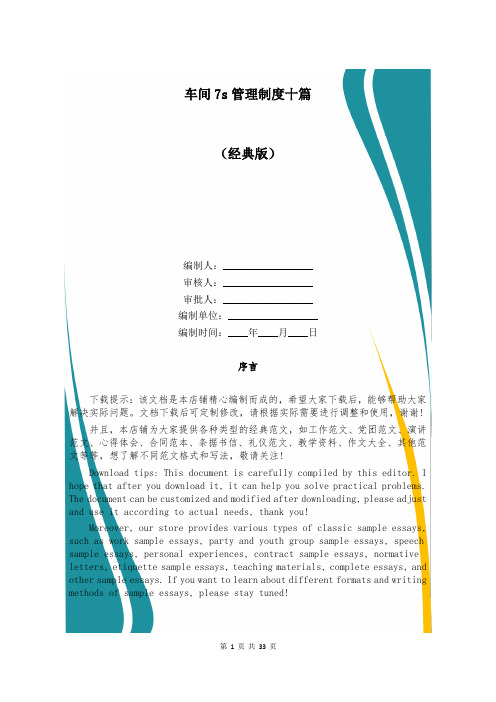
车间7s管理制度十篇(经典版)编制人:__________________审核人:__________________审批人:__________________编制单位:__________________编制时间:____年____月____日序言下载提示:该文档是本店铺精心编制而成的,希望大家下载后,能够帮助大家解决实际问题。
文档下载后可定制修改,请根据实际需要进行调整和使用,谢谢!并且,本店铺为大家提供各种类型的经典范文,如工作范文、党团范文、演讲范文、心得体会、合同范本、条据书信、礼仪范文、教学资料、作文大全、其他范文等等,想了解不同范文格式和写法,敬请关注!Download tips: This document is carefully compiled by this editor. I hope that after you download it, it can help you solve practical problems. The document can be customized and modified after downloading, please adjust and use it according to actual needs, thank you!Moreover, our store provides various types of classic sample essays, such as work sample essays, party and youth group sample essays, speech sample essays, personal experiences, contract sample essays, normative letters, etiquette sample essays, teaching materials, complete essays, and other sample essays. If you want to learn about different formats and writing methods of sample essays, please stay tuned!车间7s管理制度十篇车间7s管理制度篇11.目的为了给车间员工创造一个干净、整洁、舒适的工作场所和空间环境,营造公司特有的企业文化氛围,达到提高员工素养、公司整体形象和管理水平的目的,特制订本制度。
车间7S管理规范(新版)

车间7S管理规范(新版)车间7S管理规范(试行)1、目的本规范旨在规范生产现场管理,实现精益生产和精细化管理,达到“环境整洁、纪律严明、物流有序、设备完好、信息准确、安全生产”的目标。
2、适用范围本规范适用于___新能源108车间现场管理。
3、引用文件本规范引用GB 7231—2003《工业管道基本识别色》和GB 2894—2008《安全标志及其使用导则》。
4、相关职责各区域第一负责人负责本区域的环境、安全、设备维护保养。
5、生产现场7S管理内容与具体要求总要求为整理、整顿、清扫、清洁、素养、安全和节约。
5.1责任区划分5.1.1根据实际情况划分各责任区,设备归哪个部门,责任区就归哪个部门。
5.1.2追踪责任原则为“谁管理,谁负责”和“谁使用,谁负责”。
5.1.3区域负责人是本区域7S第一责任人,包括借给他人使用的区域。
5.1.4该区域的责任人有责任搞好本区域7S工作。
5.1.5 7S领导小组只问责责任区第一责任人,第一责任人对其下属责任人和借用区域负责。
5.1.6所有责任区都应责任到人,每天工作过程中和工作结束后都要对7S进行检查。
5.1.7每个区域必须有本区域的区域定置图。
5.2区域和通道划分5.2.1区域分为操作区、物料区和通道。
5.2.2有摆放物料的地方,就必须有通道。
5.2.3通道根据车间实际情况设置,车行通道宽度一般不得小于1.8米,人行通道不得小于1米。
5.3线条和画线要求5.3.1通道线为黄色实线,宽度为5厘米。
5.3.2区域线为黄黑色实线,宽度为5厘米。
5.3.3危险区域、不合格或废品区为红色实线,宽度为5厘米。
5.3.4线条不得出现缺失和破损,要保持颜色清晰。
5.4定置要求5.4.1能够移动的设备、工具、辅具等必须有定位线。
5.4.2存放物料的地方必须有物料区域定位线。
5.4.3采用宽度为5厘米的黄黑色实线画定位线,具体画定位线的方式有两种:密闭式和画定四角。
5.3.2 在定位线和被定位对象之间的距离应该适当,不应该过大或过小。
- 1、下载文档前请自行甄别文档内容的完整性,平台不提供额外的编辑、内容补充、找答案等附加服务。
- 2、"仅部分预览"的文档,不可在线预览部分如存在完整性等问题,可反馈申请退款(可完整预览的文档不适用该条件!)。
- 3、如文档侵犯您的权益,请联系客服反馈,我们会尽快为您处理(人工客服工作时间:9:00-18:30)。
文件名称:《车间7S管理规范(试行)》
车间7S管理规范(试行)
编号:
版本:
编制人/日期:
审核人/日期:
批准人/日期:
xxxxxxxxxxxxxxxxxxxxx 发布
车间7S管理规范(试行)
1、目的
为进一步规范生产现场管理,达到“环境整洁、纪律严明、物流有序、设备完好、信息准确、安全生产”,最终实现精益生产方式和精细化管理目标。
2、适用范围
本制度适用于永能新能源108车间现场管理。
3、引用文件
GB 7231—2003《工业管道基本识别色》
GB 2894—2008《安全标志及其使用导则》
4、相关职责
由各区域第一负责人负责本区域的环境、安全、设备维护保养。
5、生产现场7S管理内容与具体要求
总要求:整理、整顿、清扫、清洁、素养、安全和节约。
5.1责任区划分
5.1.1根据所实际情况划分各责任区。
(区域、实验室归属哪个部门,责任区就归哪个部门,设备归哪个部门,责任区就归哪个部门。
)
5.1.2根据“谁管理,谁负责”和“谁使用,谁负责”的原则追踪责任。
5.1.3区域负责人是本区域7S第一责任人,所谓本区域的范围也包括借给他人使用的区域。
5.1.4该区域的责任人有义务和责任搞好本区域7S工作。
5.1.5 7S领导小组只问责责任区第一责任人,第一责任人对其下属责任人和借用区域负责。
5.1.6所有责任区都应责任到人,每天工作过程中和工作结束后都要对7S进行检查。
5.1.7每个区域必须有本区域的区域定置图。
5.2区域和通道划分
5.2.1区域分为操作区、物料区和通道。
5.2.2有摆放物料的地方,就必须有通道。
5.2.3通道根据车间实际情况设置,车行通道宽度一般不得小于1.8米,人行通道不得小于1米。
5.3线条和画线要求
5.3.1通道线为黄色实线,实线宽度为5厘米。
5.3.2区域线为黄黑色实线,宽度为5厘米。
5.3.3危险区域、不合格或废品区为红色实线,宽度为5厘米。
5.3.4线条不得出现缺失和破损,要保持颜色清晰。
5.4定置要求
5.4.1能够移动的设备、工具、辅具等必须有定位线。
5.4.2存放物料的地方必须有物料区域定位线。
5.3画定位线方法
5.3.1采用宽度为5厘米的黄黑色实线。
具体画定位线的方式有两种:方式一为密闭式;方式二为画定四角。
5.3.2定位线与被定位对象之间的距离应适当,不可过大或过小。
5.5物料摆放要求
5.5.1单位包装重量超过10千克时高度不可超过1.5米。
5.5.2各类叠放摆放物料(单层不超过3千克)总高度不可超过2米。
5.5.3摆放物料时不可超出定位线划定的区域。
5.5.4区域标识标识牌必须面向通道方向,同一车间或厂房统一放置在定位线外右侧,易于识别。
5.5.5大型物料存放区必须有物料区域定置图。
5.6标识要求
5.6.1颜色
(1)不合格、报废、警示类区域标识:白底红字。
(2)生产区域:白底蓝字。
(3)合格区域:白底绿字。
(4)物料、原材料区域:白底黄字。
(5)安全警示类标识:按照GB 2894—2008设置
5.6.2标识高度
(1)区域标识牌高度:3米。
(2)安全警示类标识高度:1.8米。
5.6.3位置:面向通道方向。
5.6.4对象
(1)产品。
(2)物料。
(3)危险品。
(4)区域。
(5)工具。
5.6.5排版:一行优先,两行其次。
5.6.6挂法:固定优先,悬挂次之。
5.7颜色要求
5.7.1区域(1)黄黑色(虚线):一般为通道线、区域线、固定物品定位线。
(2)绿色:表示合格区。
(3)红色,表示不合格区、废品区和危险区。
(4)红色斑马线:表示不得放置、不得进入等。
(5)黄黑实线:表示警告、警示(如地面突起物、易碰撞处、坑道、台阶等)。
6、安全事项
6.1车间必须使用GB16179规定的安全标志,规格为A3(0.42米×0.3米)。
6.2在工作前,由各班组长组织班前会,对工作的安全事项进行说明,并强调要按规定穿戴好劳动防护用品。
6.3安全员随时进行巡查稽核,对作业中人的不安全行为、物的不安全状态、环境的不安全条件及时提出整改,由各区域整改完成后报安环请求复检,通过则合格。
6.4各区域随时检查安全标志,如果脱落要及时报告安环,并由安环安装新的标志。
7、节约要求
7.1各单位的负责人必须定期对员工进行低碳、节能的知识培训,使其养成环保节约的习惯。
7.2员工在完成作业后,将多余的物料、残料等集中起来,并放置到回收区域统一管理。
7.3实施作业时要严格按照安全操作规程及SOP进行,减少多余的作业或不必要的工序。
7.4将各种垃圾放到指定的垃圾区域,便于集中回收处理。
7.6下班后要及时关掉灯具和机器设备,检查水笼头等有无跑水漏水,养成节约用电用水习惯。
8、班后整理清扫
每天工作结束后,下班前10分钟,员工应对自己的工作范围进行整理、整顿、清扫。
(1)检查是否有物品掉在地上,将掉在地上的物品都捡起来,如零件、产品、废料等。
(2)重新放置那些放错位置的物品,确保所有工具、产品等物品都放在应该放置的地方。
(3)擦干净设备、机器的主要部位及工作台面等其他重要的地方。
(4)固定可能脱落的标签,将标识牌、标签等擦试干净,保持字迹清晰。
(5)处理所有不要物,扔掉废料和垃圾。
(6)清洁地面,擦干净溅落或渗漏的水、油或其他脏污。
(7)每周一为车间清洁日各区域负责人需带领本区域员工对本区域内进行大扫除,点检设备仪器查看是否存在跑冒滴漏等现象;清除本区域无用品;查看员工工装是否完好;地面及区域标识是否完好。
9、附件
《生产车间7S检查标准表》
10、其他
无
生产车间7S检查标准表。