125MN热模锻压力机拉杆测试研究
洛阳一拖参观实习报告(2012年——机械专业)

第一章前言“纸上得来终觉浅,绝知此事需躬行!”由于我们的专业实践性较强,所以生产实习是我们专业学习的重要组成部分。
此次,我们在老师的带领指导下去洛阳一拖进行生产实习,增长我们的见识,巩固课本知识,让我们了解工厂的一些基本运作过程,工艺流程以及机器设备的工作原理,这会突出我们的学习重点,为我们以后的工作奠定坚实的基础。
我校安排我们到洛阳中国一拖参观实习,开展生产实习历程,以及总结实习内容,实习感想。
通过我们自己的参观,产中相关技术人员的讲解和老师的指导,还查找各种图书资料以及到网上搜寻相关资料,使我们的的从实践中学得的知识得以巩固和完善,并能顺利完成本篇实习报告。
本次实习我们总共参观实习了五个隶属于一拖集团的分厂和农耕博物馆,下面具体谈谈本次实习的目的和历程。
一、实习目的生产实习是与今后工作生活最直接联系的,我们在生产实习过程中将完成学习到就业的过渡,作为我们材料专业,生产实习是我们知识结构中不可缺少的组成部分,并作为一个独立的项目列入专业教学计划中的。
通过生产实习,使我们学习和了解零件从原材料到成品批量生产的全过程以及生产组织管理等知识,培养学生树立理论联系实际的工作作风,以及生产现场中将科学的理论知识加以验证、深化、巩固和充实。
并培养学生进行调查、研究、分析和解决工程实际问题的能力,为后继专业课的学习、课程设计和毕业设计打下坚实的基础。
通过生产实习,拓宽我们的知识面,增加感性认识,把所学知识条理化系统化,学到从书本学不到的专业知识,并获得本专业国内、外科技发展现状的最新信息,激发学生向实践学习和探索的积极性,也是学生接触社会、了解产业状况、了解国情的一个重要途径,逐步实现由学生到社会的转变,培养我们初步担任技术工作的能力、初步了解企业管理的基本方法和技能;体验企业工作的内容和方法。
这些实际知识,为今后的学习和将从事的技术工作打下坚实的基础。
二、实习历程1、8月20日:上午一拖集团简介及安全教育下午一拖洛阳工程机械分公司2、8月21日:上午一拖股份有限公司锻造厂下午一拖股份有限公司热处理厂3、8月22日: 上午一拖股份有限公司齿轮厂下午一拖股份有限公司第一装配厂4、8月23日: 上午一拖股份有限公司农耕博物馆大学已过去四分之三,我们即将奔向社会,但是仅仅在书本学来的知识还不足以透彻的了解我们专业,。
热模锻压力机开发研究报告
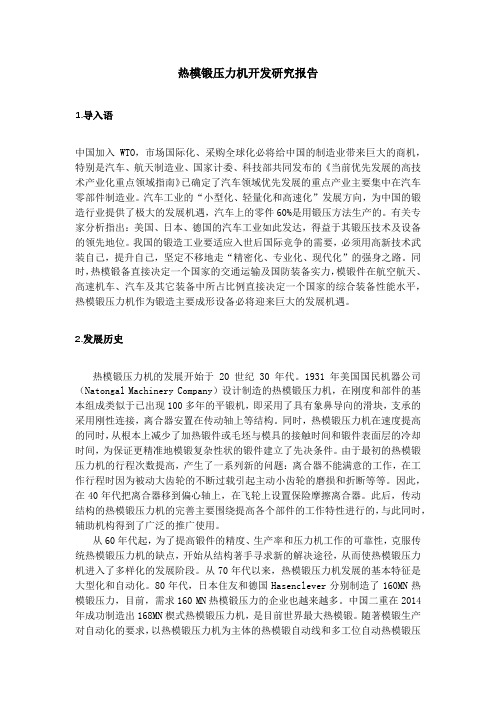
热模锻压力机开发研究报告1.导入语中国加入WTO,市场国际化、采购全球化必将给中国的制造业带来巨大的商机,特别是汽车、航天制造业、国家计委、科技部共同发布的《当前优先发展的高技术产业化重点领域指南》已确定了汽车领域优先发展的重点产业主要集中在汽车零部件制造业。
汽车工业的“小型化、轻量化和高速化”发展方向,为中国的锻造行业提供了极大的发展机遇,汽车上的零件60%是用锻压方法生产的。
有关专家分析指出:美国、日本、德国的汽车工业如此发达,得益于其锻压技术及设备的领先地位。
我国的锻造工业要适应入世后国际竞争的需要,必须用高新技术武装自己,提升自己,坚定不移地走“精密化、专业化、现代化”的强身之路。
同时,热模锻备直接决定一个国家的交通运输及国防装备实力,模锻件在航空航天、高速机车、汽车及其它装备中所占比例直接决定一个国家的综合装备性能水平,热模锻压力机作为锻造主要成形设备必将迎来巨大的发展机遇。
2.发展历史热模锻压力机的发展开始于20世纪30年代。
1931年美国国民机器公司(Natongal Machinery Company)设计制造的热模锻压力机,在刚度和部件的基本组成类似于已出现100多年的平锻机,即采用了具有象鼻导向的滑块,支承的采用刚性连接,离合器安置在传动轴上等结构。
同时,热模锻压力机在速度提高的同时,从根本上减少了加热锻件或毛坯与模具的接触时间和锻件表面层的冷却时间,为保证更精准地模锻复杂性状的锻件建立了先决条件。
由于最初的热模锻压力机的行程次数提高,产生了一系列新的问题:离合器不能满意的工作,在工作行程时因为被动大齿轮的不断过载引起主动小齿轮的磨损和折断等等。
因此,在40年代把离合器移到偏心轴上,在飞轮上设置保险摩擦离合器。
此后,传动结构的热模锻压力机的完善主要围绕提高各个部件的工作特性进行的,与此同时,辅助机构得到了广泛的推广使用。
从60年代起,为了提高锻件的精度、生产率和压力机工作的可靠性,克服传统热模锻压力机的缺点,开始从结构著手寻求新的解决途径,从而使热模锻压力机进入了多样化的发展阶段。
锻造液压机原理

天津大学2007届高职专科毕业设计论文题目:锻造液压机的原理姓名:年级:2007届院系:电气与自动化工程学院电气与自动化技术摘要液压机主机部分包括液压缸、横梁、立柱及充液装置等。
动力机构由油箱、高压泵、控制系统、电动机、压力阀、方向阀等组成。
液压机采用PLC控制系统,通过泵和油缸及各种液压阀实现能量的转换,调节和输送,完成各种工艺动作的循环。
该系列液压机具有独立的动力机构和电气系统,并采用按钮集中控制,可实现手动和自动两种操作方式。
该液压机结构紧凑,动作灵敏可靠,速度快,能耗小,噪音低,压力和行程可在规定的范围内任意调节,操作简单。
在本设计中,通过查阅大量文献资料,设计了液压缸的尺寸,拟定了液压原理图。
按压力和流量的大小选择了液压泵,电动机,控制阀,过滤器等液压元件和辅助元件。
关键词:锻造,液压系统,液压机, PLC目录目录 (Ⅰ)第1章国内外重型锻压设备的发展概况 (1)第2章锻造液压机系统 (4)2.1 锻造液压机的系统原理 (4)2.1.1液压系统工作原理 (4)2.2.液压系统分析 (5)第3章锻造液压机的改进设计方案及分析 (6)3.1 锻造液压机的该机方案 (6)3.2 液压机的改进方案分析 (7)第4章PLC在液压机控制系统改造中的应用 (7)4.1 工艺原理分析 (8)4.2 液压系统控制过程分析 (8)4.2.1 液压机执行部件动作过程分析 (8)4.3 PLC电控系统设计 (10)4.3.1 硬件设计与软件实现 (10)4.3.2 三地操作 (14)4.4 PLC可靠性保护措施 (15)4.4.1电动机组保护 (15)4.4.2机械设备的保护 (15)4.5 PLC程序设计 (16)第4章液压机电气控制系统 (18)4.1 液压机电气控制方案设计 (18)4.1.1液压机电气控制方案选择 (18)4.1.2电气控制要求与总体控制方案 (19)4.2 液压机电气控制电路设计 (20)4.2.1液压机主电路设计 (20)4.2.2液压机控制电路设计 (20)4.3 液压机电气控制系统分析 (22)参考文献 (23)附录 (24)致谢 (25)第一章绪论重型锻压设备是随着国民经济的发展,特别是随着汽车、航空、宇航、动力、造船、冶金、石油、化工、铁道、交通等工业部门对大型锻件、模锻件、冲压件日益增长的需要而迅速发展起来的。
21m长拉杆锻后热处理研究
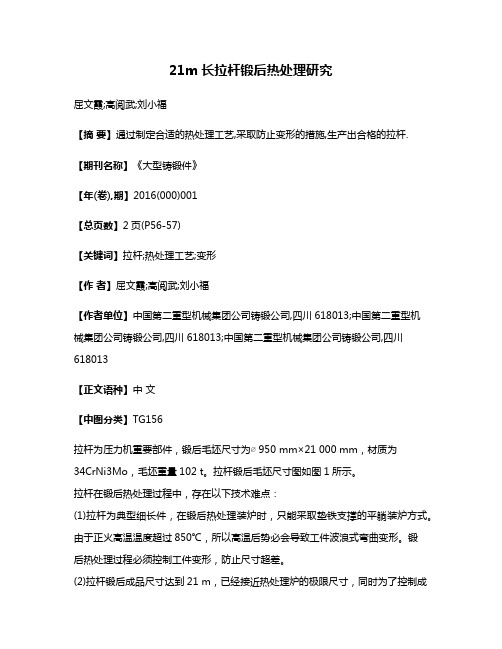
21m长拉杆锻后热处理研究屈文霞;高阅武;刘小福【摘要】通过制定合适的热处理工艺,采取防止变形的措施,生产出合格的拉杆.【期刊名称】《大型铸锻件》【年(卷),期】2016(000)001【总页数】2页(P56-57)【关键词】拉杆;热处理工艺;变形【作者】屈文霞;高阅武;刘小福【作者单位】中国第二重型机械集团公司铸锻公司,四川618013;中国第二重型机械集团公司铸锻公司,四川618013;中国第二重型机械集团公司铸锻公司,四川618013【正文语种】中文【中图分类】TG156拉杆为压力机重要部件,锻后毛坯尺寸为∅950 mm×21 000 mm,材质为34CrNi3Mo,毛坯重量102 t。
拉杆锻后毛坯尺寸图如图1所示。
拉杆在锻后热处理过程中,存在以下技术难点:(1)拉杆为典型细长件,在锻后热处理装炉时,只能采取垫铁支撑的平躺装炉方式。
由于正火高温温度超过850℃,所以高温后势必会导致工件波浪式弯曲变形。
锻后热处理过程必须控制工件变形,防止尺寸超差。
(2)拉杆锻后成品尺寸达到21 m,已经接近热处理炉的极限尺寸,同时为了控制成本,采取两件拉杆同炉处理,因此,锻后热处理过程中很难保证工件的均温效果,最终导致工件内部晶粒度不均匀,从而影响工件性能及UT可探性。
锻后热处理必须制定有效措施,保证工件的均匀性。
针对上述分析的技术难点,锻后热处理工艺采取了多项措施,主要措施如下:(1)工件变形措施拉杆装炉时,只能平躺在500 mm高的锥形垫铁上。
通常每5 m左右安置一根垫铁,考虑到拉杆属于细长件,应按每2 m~3 m安置一根垫铁,并且两端垫铁必须处于同一水平面,中部垫铁处于同一水平面,最终保证工件中心线与水平面平行。
装炉示意图(按比例)如图2所示。
减小垫铁间距,能有效控制工件在高温过程的扭曲变形,但并不能通过这唯一的措施控制拉杆的超差变形。
在锻后热处理过程中必须采取校直工序。
锻后热处理过程中,高温过程变形最大,所以有意在高温结束后,吊空冷过程中安排一次校直工序,目的是大大减小工件的高温变形。
热模锻压力机整机刚度估计与结构优化
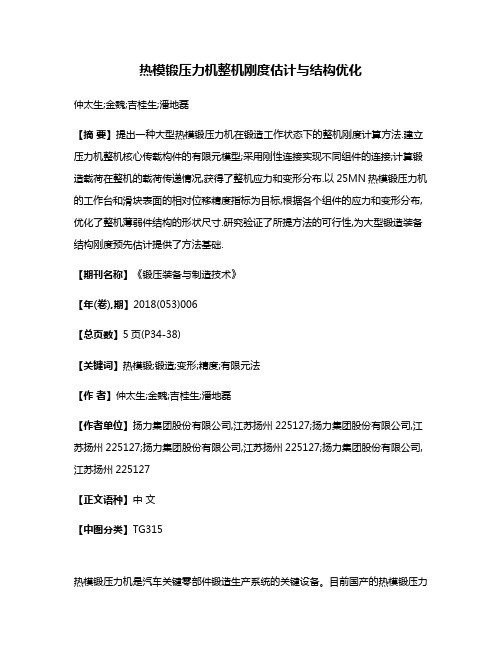
热模锻压力机整机刚度估计与结构优化仲太生;金魏;吉桂生;潘地磊【摘要】提出一种大型热模锻压力机在锻造工作状态下的整机刚度计算方法.建立压力机整机核心传载构件的有限元模型;采用刚性连接实现不同组件的连接;计算锻造载荷在整机的载荷传递情况,获得了整机应力和变形分布.以25MN热模锻压力机的工作台和滑块表面的相对位移精度指标为目标,根据各个组件的应力和变形分布,优化了整机薄弱件结构的形状尺寸.研究验证了所提方法的可行性,为大型锻造装备结构刚度预先估计提供了方法基础.【期刊名称】《锻压装备与制造技术》【年(卷),期】2018(053)006【总页数】5页(P34-38)【关键词】热模锻;锻造;变形;精度;有限元法【作者】仲太生;金魏;吉桂生;潘地磊【作者单位】扬力集团股份有限公司,江苏扬州225127;扬力集团股份有限公司,江苏扬州225127;扬力集团股份有限公司,江苏扬州225127;扬力集团股份有限公司,江苏扬州225127【正文语种】中文【中图分类】TG315热模锻压力机是汽车关键零部件锻造生产系统的关键设备。
目前国产的热模锻压力机基本沿用上世纪80年代引进的德国EUMUCO原有技术,很难满足汽车关键零件智能化精密锻造生产系统的需求。
压力机的整机刚度是沿压力机滑块方向工作载荷与主机在加载方向上变形量之比,是保证压力机锻造精度最重要的指标之一。
如果压力机的工作载荷一定,刚度越小,变形量也越大,对成形零件质量的影响也越大。
单纯从压力机抵抗弹性变形的能力来说,压力机的刚度参数应该越大越好,但压力机的制造成本也会越高。
文献[1]论述了热模锻压力机结构和载荷传递特点。
文献[2]从工程经验的角度指出了压力机刚度所需要的机身最大应力和静挠度值。
针对压力机结构刚度和振动问题,根据载荷传递特点,有限元法已用于多种吨位的压力机机身结构分析:竖直或水平分力被加载于机身有限元模型进行结构应力与变形计算[3]-[6];有限元模态分析揭示出了多种吨位压力机机身的振动特性[7][8]。
211165218_重型院研发的125MN预拉伸机组通过最终验收

马爱民,等:汽车前围内板铝合金冲压工艺设计工艺技术/信息报道Stamping process design of aluminum alloy for automobilefront inner panelMa Aimin,Xia Dewei,Duan Guangpo(Zhongwang Aluminum Co.,Ltd.,Beijing100020,China)Abstract:At present,the use of lightweight materials is an important way to realize the lightweight of automobile.Through the de⁃sign of stamping process program for the front inner panel of an all aluminum alloy automobile,the problems such as wrinkling,crack⁃ing,thinning and springback occurred in the stamping process of aluminum alloy automobile panel are discussed.By using the finite el⁃ement analysis software,the process plan of the front inner panel is simulated and analyzed.According to the analysis results,the pro⁃cess plan is optimized,and its feasibility is verified.The final processprogram is determined,which provides technical support and theo⁃retical basis for the development and trial production of aluminum alloy automobile panel.Key words:aluminum alloy;lightweight;front inner panel;stamping process重型院研发的125MN预拉伸机组通过最终验收125MN预拉伸机组作为宝武铝业年产600kt铝合金铸造及深加工项目(一期航天航空及汽车铝合金板项目)的核心设备,也是目前国内拉伸力最大的航空级铝合金板材拉伸机组,日前通过了最终考核验证。
洛阳一拖实习报告
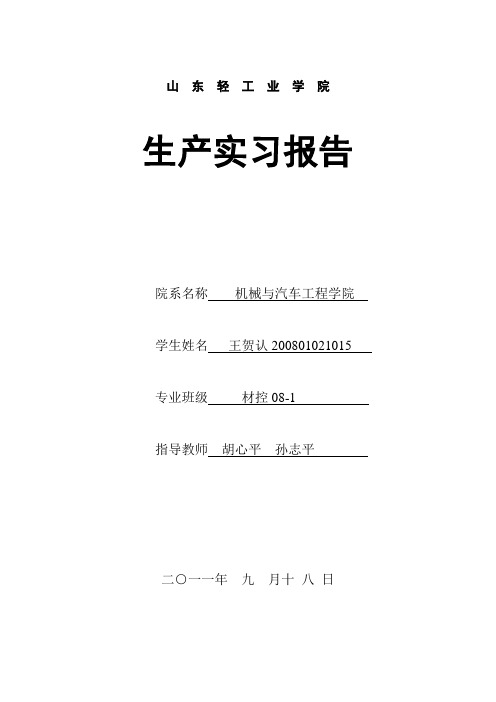
山东轻工业学院生产实习报告院系名称机械与汽车工程学院学生姓名王贺认200801021015 专业班级材控08-1指导教师胡心平孙志平二○一一年九月十八日实习情况一览表时间地点实习内容指导教师备注0830上午机电楼B125实习动员胡心平0831-0906山东轻工业学院实习预备知识学习0908上午一拖职教中心教室入厂安全教育以及一拖情况介绍0908下午一拖工程机械厂一拖热处理厂参观胡心平孙志平0909上午一拖锻造厂一拖齿轮厂参观胡心平孙志平0913-0915山东轻工业学院复习以及总结洛阳一拖实习报告2011年9月7日的早上我们山东轻工业学院材控专业的80多号人浩浩荡荡的向着洛阳出发,因为学校为我们安排了一周的实习,实习的地点就是洛阳一拖,因为这个是中国农机行业唯一的特大型企业,所以一拖的实习就成了我们的重中之重。
一、实习目的或研究目的(一)、安全教育我们是八号凌晨一点到达一拖的,然后上午工厂负责我们实习的老师给我们讲解了很重要的实习安全知识和一拖的发展历史,老师给我们看安全生产记录还有事故案例,一些注意事项加血淋淋的案例,这些血淋淋的案件给人们敲响了警钟。
老师给我们提了好多要求,我们都必须做到,毕竟事故发生了谁也负担不起。
厂内危害:1.机械性危害: 机械加工过程中(如机械转动时的刀削磨钻等)造成的伤害,居各类伤害之首。
2.化学物质危害: 如强酸、强碱、汞、铅、一氧化碳等使人中毒、窒息、烧伤等伤害。
3.燃烧爆炸危害:如钢水爆炸,化学物质爆炸等。
4.热危害:人与热件、热机直接接触 5.电器危害:灼伤、火灾等6.其他危害:如紫外线,辐射,低温等。
由于这些危害对人体的伤害很大,因此对我们着装要求然后第二天就开始了我们为期一周的实习。
(二)、一拖概况第一拖拉机股份有限公司是中国内地在香港上市的唯一农机制造与销售企业其前身第一拖拉机制造厂,创建于 1955年,是我国“一五”期间兴建的156个国家重点项目之一,是中国农机行业唯一的特大型企业,1990年被国务院企业管理委员会评为“国家一级企业”,1997年,中国一拖集团将与拖拉机相关的业务、资产、负债人员重组后进行股份制改造,依法设立了第一拖拉机股份有限公司。
800MN模锻压机用大拉杆热处理调质研究
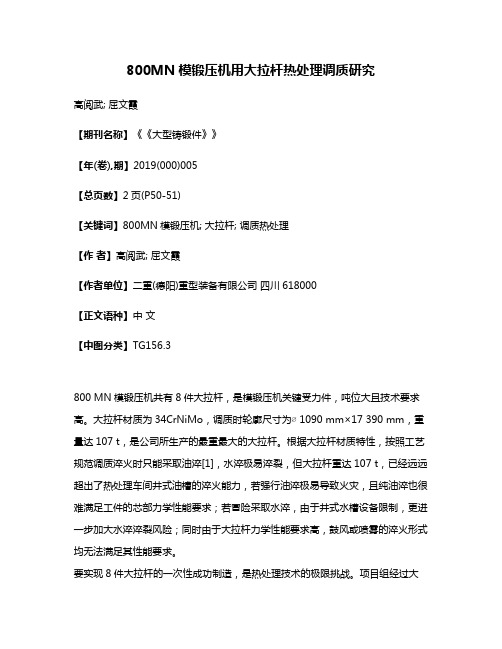
800MN模锻压机用大拉杆热处理调质研究高阅武; 屈文霞【期刊名称】《《大型铸锻件》》【年(卷),期】2019(000)005【总页数】2页(P50-51)【关键词】800MN模锻压机; 大拉杆; 调质热处理【作者】高阅武; 屈文霞【作者单位】二重(德阳)重型装备有限公司四川618000【正文语种】中文【中图分类】TG156.3800 MN模锻压机共有8件大拉杆,是模锻压机关键受力件,吨位大且技术要求高。
大拉杆材质为34CrNiMo,调质时轮廓尺寸为∅1090 mm×17 390 mm,重量达107 t,是公司所生产的最重最大的大拉杆。
根据大拉杆材质特性,按照工艺规范调质淬火时只能采取油淬[1],水淬极易淬裂,但大拉杆重达107 t,已经远远超出了热处理车间井式油槽的淬火能力,若强行油淬极易导致火灾,且纯油淬也很难满足工件的芯部力学性能要求;若冒险采取水淬,由于井式水槽设备限制,更进一步加大水淬淬裂风险;同时由于大拉杆力学性能要求高,鼓风或喷雾的淬火形式均无法满足其性能要求。
要实现8件大拉杆的一次性成功制造,是热处理技术的极限挑战。
项目组经过大量方案讨论,数据统计分析,在技术上进行大胆创新,在没增加任何设备、工装附具的情况下,利用现有设备,突破设备应用瓶颈,成功实现大拉杆的调质淬火,最终一次性成功制造,8件大拉杆的力学性能全部一次性满足技术要求。
1 大拉干调质前情况介绍1.1 化学成分要求大拉杆材质为34CrNiMo,化学成分要求如表1所示。
大拉杆长度达到17.39 m,冶炼过程中主要控制工件两端C偏析和合金聚集,同时将P、S含量控制在≤0.01%,提高钢水的纯净度,减少大拉杆后续的淬裂风险。
表1 34CrNiMo钢化学成分要求Table 1 Chemical composition requirements of 34CrNiMo steelCSiMnPSCrNiMo0.30~0.380.17~0.370.40~0.70≤0.035≤0.0351.40~1.70≤0.400.15~0.301.2 力学性能要求大拉杆力学性能要求为:Rm≥690 MPa,ReL≥490 MPa,A≥12%,Z≥32%,KU2≥31 J,根据制造技术规范JBT 5000.8—2007要求,大拉杆在工件两端的13半径处各套取一组试棒分别进行力学性能检验,两端力学性能均必须合格。
31.5MN热模锻压力机大修方案

31.5MN热模锻压力机大修方案31.5MN热模锻压力机安装投产于xxxx年。
由于是xx车间的顶级关键设备,投产使用以来,长期三班连续运转,设备机械方面相应磨损加快,各种故障频繁出现,维修频次增加,电气系统严重老化,就上述问题我公司与贵公司有关人员进行了探讨和研究并实地进行了考察。
一、设备存在的主要问题:1、主电机皮带轮磨损严重。
离合器、制动器磨损。
制动器中间盘有窜量,径向晃动。
制动器冷却效果不良。
2、滑块轻微变形,滑板磨损,造成间隙较大,已经影响制件质量。
3、滑块闭合高度传动部分,曲轴—连杆、连杆—滑块轴承磨损,滑块闭合高度传动部分重复精度不良。
4、封闭高度调整机构右后伞齿轮磨损,减速器齿轮磨损。
4、平衡缸有漏气现象。
5、工作台轨道变形,工作台走轮经常损坏,设备故障率极高。
液压系统漏油严重。
6、电气部分:PLC属基本淘汰产品,以及主电机调速装置等备件采购难且价格昂贵。
许多电线和电缆已老化和变性,尤其是床身和液压系统等处的电缆,因多年油浸、老化等原因,使得电缆绝缘外皮变硬、变脆。
设备各电器元件使用年限较长,存在不同的老化现象。
根据贵公司的意见和该设备的实际情况,制定以下大修改造方案。
二、大修改造技术方案(一)、机械部分:1、设备基础及机架部分1.1、检查设备地脚螺杆是否松动?1.2、检查设备二次浇灌层是否松动?1.3、测量框架与底座、底座与机架、机架与横梁接触面的间隙。
根据实际情况,与公司协商制定具体修理工艺。
根据GB50272-98<<锻压设备安装工程施工与验收规范》,与贵公司协商制定合理的修复工艺达标准要求。
2、主要部件的修复2.1、床身(即立柱)曲轴支承套底孔因磨损严重、孔径出大小头椭圆等情况,造成曲轴支承套定位不稳,需将两底孔按原设计精度要求(因无图纸提不出精度要求)以滑板导轨基面找正后,将底孔放大修复,并同时将两支承套的压紧螺钉底孔各8个换位重新加工好。
因该床身属特大型工件,修复需大型落地镗床或落地镗铣床。
公称力125MN曲柄式热模锻压力机的研制经验和建造更重机器的问题
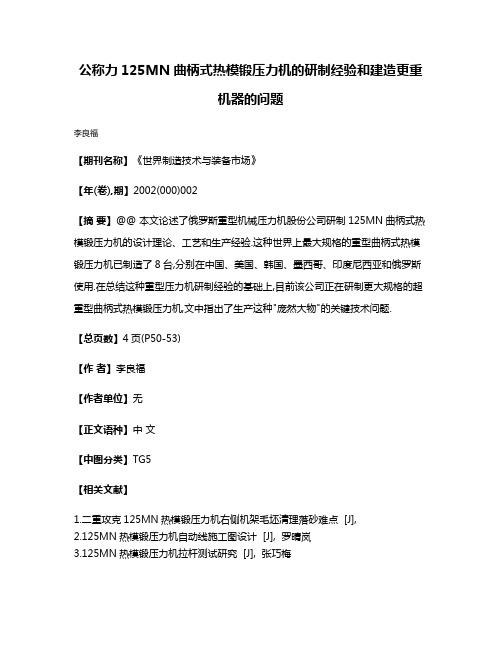
公称力125MN曲柄式热模锻压力机的研制经验和建造更重
机器的问题
李良福
【期刊名称】《世界制造技术与装备市场》
【年(卷),期】2002(000)002
【摘要】@@ 本文论述了俄罗斯重型机械压力机股份公司研制125MN曲柄式热模锻压力机的设计理论、工艺和生产经验.这种世界上最大规格的重型曲柄式热模锻压力机已制造了8台,分别在中国、美国、韩国、墨西哥、印度尼西亚和俄罗斯使用.在总结这种重型压力机研制经验的基础上,目前该公司正在研制更大规格的超重型曲柄式热模锻压力机,文中指出了生产这种"庞然大物"的关键技术问题.
【总页数】4页(P50-53)
【作者】李良福
【作者单位】无
【正文语种】中文
【中图分类】TG5
【相关文献】
1.二重攻克125MN热模锻压力机右侧机架毛坯清理落砂难点 [J],
2.125MN热模锻压力机自动线施工图设计 [J], 罗晴岚
3.125MN热模锻压力机拉杆测试研究 [J], 张巧梅
4.国内首条全自动125MN热模锻压力机生产线投产 [J],
5.国内首条全自动125MN热模锻压力机生产线投产 [J],
因版权原因,仅展示原文概要,查看原文内容请购买。
140MN热模锻压力机上锻造大型曲轴用模具模架技术
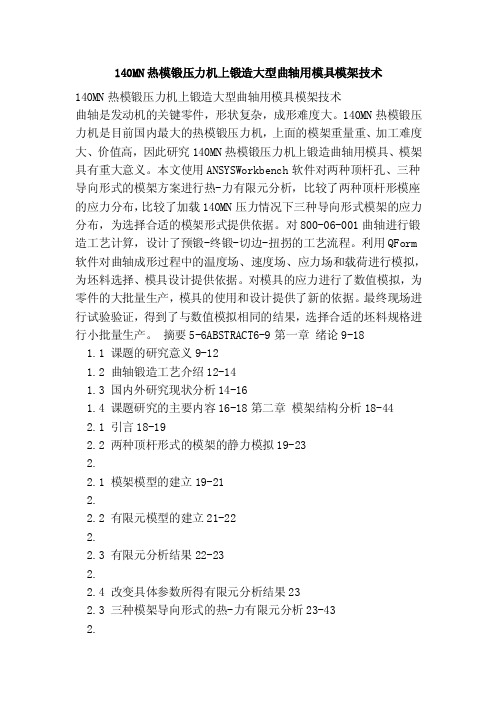
140MN热模锻压力机上锻造大型曲轴用模具模架技术140MN热模锻压力机上锻造大型曲轴用模具模架技术曲轴是发动机的关键零件,形状复杂,成形难度大。
140MN热模锻压力机是目前国内最大的热模锻压力机,上面的模架重量重、加工难度大、价值高,因此研究140MN热模锻压力机上锻造曲轴用模具、模架具有重大意义。
本文使用ANSYSWorkbench软件对两种顶杆孔、三种导向形式的模架方案进行热-力有限元分析,比较了两种顶杆形模座的应力分布,比较了加载140MN压力情况下三种导向形式模架的应力分布,为选择合适的模架形式提供依据。
对800-06-001曲轴进行锻造工艺计算,设计了预锻-终锻-切边-扭拐的工艺流程。
利用QForm 软件对曲轴成形过程中的温度场、速度场、应力场和载荷进行模拟,为坯料选择、模具设计提供依据。
对模具的应力进行了数值模拟,为零件的大批量生产,模具的使用和设计提供了新的依据。
最终现场进行试验验证,得到了与数值模拟相同的结果,选择合适的坯料规格进行小批量生产。
摘要5-6ABSTRACT6-9第一章绪论9-181.1 课题的研究意义9-121.2 曲轴锻造工艺介绍12-141.3 国内外研究现状分析14-161.4 课题研究的主要内容16-18第二章模架结构分析18-442.1 引言18-192.2 两种顶杆形式的模架的静力模拟19-232.2.1 模架模型的建立19-212.2.2 有限元模型的建立21-222.2.3 有限元分析结果22-232.2.4 改变具体参数所得有限元分析结果232.3 三种模架导向形式的热-力有限元分析23-432.3.1 模架模型的建立23-242.3.2 模架受热载荷有限元模型的建立24-252.3.3 模架热-力有限元分析25-432.4 本章小结43-44第三章 800-06-001 曲轴成形工艺研究44-543.1 引言443.2 800-060-001 曲轴工艺分析44-513.2.1 曲轴终锻件设计45-463.2.2 曲轴预锻件设计46-493.2.4 曲轴原材料规格选择49-513.3 模具设计研究51-533.3.1 辊锻模具设计513.3.2 终锻模设计51-523.3.3 预锻模设计52-533.4 本章小结53-54第四章成形过程的数值模拟54-704.1 引言54-554.2 800-06-001 曲轴成形工艺模拟参数55-564.3 辊锻过程数值模拟56-584.4 模锻过程数值模拟58-684.4.1 预锻过程数值模拟58-634.4.2 终锻过程数值模拟63-684.5 锻模应力分析684.6 本章小结68-70第五章试验验证70-755.1 引言705.2 生产准备70-715.3 试验验证71-725.4 试验结果及分析72-735.5 本章小结73-75第六章结论与展望75-776.1 总结756.2 研究展望75-77参考文献77-80致谢80-81在学期间发表的学术论文和参加科研情况81。
125MN自由锻造水压机立柱应力测试分析
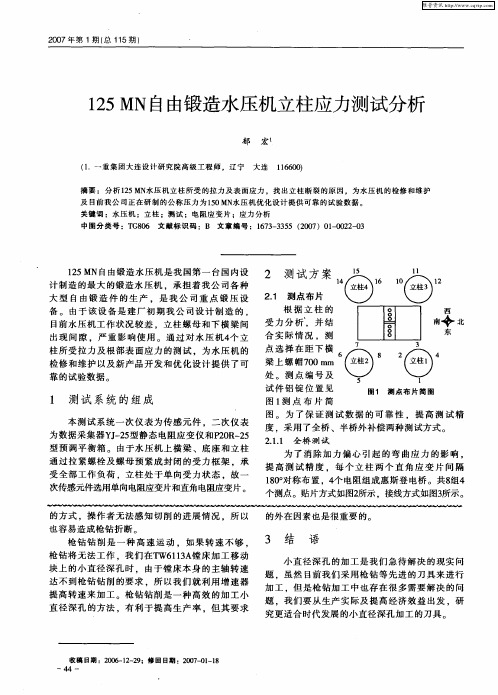
2 11 全 桥 测 试 ..
图 1 点 布 片 简 测 图 。为 了保 证 测 试 数 据 的可 靠 性 。 提 高 测 试 精
通过 拉 紧螺 栓 及 螺母 预 紧成 封 闭的 受力 框 架 ,承
受全 部 工作 负 荷 ,立 柱 处 于单 向受 力状 态 ,故一
为 了 消 除 加 力偏 心 引 起 的 弯 曲应 力 的影 响 , 提 高 测 试 精 度 , 每 个 立 柱 两 个 直 角 应 变 片 间 隔
10 对称 布置 ,4 电阻 组成 惠斯 登 电桥 。共8 8。 个 组4 个测点 。贴片方式如图2 所示 ,接线方式如 图3 所示 。 的外 在 因素也是 很重 要 的。
15MN自由锻 造水 压 机 是我 国第 一 台国 内设 2
2 测试方案 , 。
l‘ .
计 制 造 的最 大 的锻 造水 压 机 ,承担 着 我 公 司各 种 . 大 型 自由锻 造 件 的 生 产 ,是 我 公 司 重 点 锻 压 设 21 测 点布 片 根 据 立 柱 的 备 。 由于 该 设 备 是 建 厂初 期 我 公 司设 计 制 造 的 . 受 力 分 析’ .并 结 目前 水 压机 工 作状 况 较差 ,立 柱螺 母 和 下 横梁 间
及 目前 我公 司正 在 研 制 的 公 称 压 力 为 10MN 压 机 优 化设 计提 供 可 靠 的试 验 数 据 。 5 水 关 键词 :水 压机 ;立 柱 ;测 试 ;电 阻 应 变 片 ;应力 分析 中 图 分 类 号 :T 8 6 文 献标 识 码 :B 文章 编 号 : 17 — 3 5 (0 7 10 2 — 3 G 0 6 3 35 2 0 )0 — 0 2 0
基于Deform的刮板锻造工艺及模具设计研究
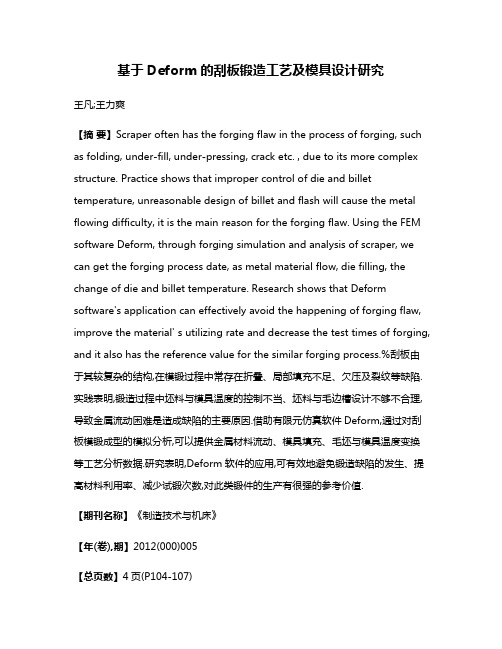
基于Deform的刮板锻造工艺及模具设计研究王凡;王力爽【摘要】Scraper often has the forging flaw in the process of forging, such as folding, under-fill, under-pressing, crack etc. , due to its more complex structure. Practice shows that improper control of die and billet temperature, unreasonable design of billet and flash will cause the metal flowing difficulty, it is the main reason for the forging flaw. Using the FEM software Deform, through forging simulation and analysis of scraper, we can get the forging process date, as metal material flow, die filling, the change of die and billet temperature. Research shows that Deform software's application can effectively avoid the happening of forging flaw, improve the material' s utilizing rate and decrease the test times of forging, and it also has the reference value for the similar forging process.%刮板由于其较复杂的结构,在模锻过程中常存在折叠、局部填充不足、欠压及裂纹等缺陷.实践表明,锻造过程中坯料与模具温度的控制不当、坯料与毛边槽设计不够不合理,导致金属流动困难是造成缺陷的主要原因.借助有限元仿真软件Deform,通过对刮板模锻成型的模拟分析,可以提供金属材料流动、模具填充、毛坯与模具温度变换等工艺分析数据.研究表明,Deform软件的应用,可有效地避免锻造缺陷的发生、提高材料利用率、减少试锻次数,对此类锻件的生产有很强的参考价值.【期刊名称】《制造技术与机床》【年(卷),期】2012(000)005【总页数】4页(P104-107)【关键词】刮板;模锻;Deform【作者】王凡;王力爽【作者单位】沈阳理工大学机械工程学院,辽宁沈阳110168;沈阳理工大学机械工程学院,辽宁沈阳110168【正文语种】中文【中图分类】TG316.3煤机刮板是矿用刮板传送机广泛使用的关键配件之一,其机械性能和产品质量直接影响到煤炭业的安全生产和企业的效益。
125MN挤压机活动部件中心偏移检测系统软件设计与应用研究的开题报告

125MN挤压机活动部件中心偏移检测系统软件设计与应用研究的开题报告一、研究背景和意义挤压工艺是制造金属材料和非金属材料的重要方法之一。
挤压机作为挤压工艺生产的核心设备,其性能和准确度对挤压工艺的成形质量和生产效率具有关键影响。
挤压机的运动系统中存在着一些活动部件,如液压缸、导柱、活塞等,其中液压缸表现出偏移、倾斜等不良运动状态会导致挤压工艺中产生材料废品、产品寿命缩短以及生产效率低下等问题。
因此,对挤压机活动部件中心偏移进行检测和控制就显得尤为重要。
目前,国内外研究出现了一些针对挤压机运动系统的检测和控制方案。
例如,利用激光干涉仪和位移传感器等检测技术测量液压缸偏心度,实现挤压机液压缸的精确定位。
但是,这些解决方案存在着复杂、昂贵、操作难度大等问题,不太适合应用于生产线上。
因此,为解决挤压机液压缸中心偏移问题,严格控制生产线上的品质和效率,本文提出了开发挤压机活动部件中心偏移检测系统软件的研究。
挤压机活动部件中心偏移检测系统通过相机拍摄活动部件运动状态的图像,通过图像处理和模式识别技术,实时检测液压缸中心偏移,并根据检测结果控制液压缸的运动。
该研究可以为挤压工艺的自动化和制造领域的智能化提供技术支持,具有理论和实践意义。
二、研究内容和方法本文研究内容主要包括挤压机活动部件中心偏移检测系统软件的设计和应用研究两个方面。
1.挤压机活动部件中心偏移检测系统软件的设计本文将该系统软件设计为一个PC端软件,主要包括相机采集、图像处理、模式识别和控制系统四大模块。
其中相机采集模块使用高速相机拍摄液压缸运动状态的图像,图像处理和模式识别模块使用MATLAB和OpenCV等工具建立液压缸中心偏移检测算法,控制系统模块实现根据检测结果实时控制液压缸的运动状态。
2.挤压机活动部件中心偏移检测系统软件的应用研究为验证本文提出的挤压机活动部件中心偏移检测系统软件的有效性和可靠性,本文将设计成的系统软件应用于挤压机灰铸铁制造过程中,对液压缸中心偏移进行检测,根据检测结果实时控制液压缸的运动状态,监控生产线的工艺质量和效率。
公称力125MN曲柄式热模锻压力机的研制经验和建造更重机器的问题

维普资 与技 术
Po ut rd c s& Tc nl y ★ eh o g o
俄 罗斯机 械 制 造 业专 栏
Th p r e c fDe e o ng H o e Ex e i n e o v l pi t— f r i a e s 、 h pa iy o 2 M N o m ng Cr nk Pr s t Ca c t f 1 5 a d o l m s i a uf c u i a ir M a hi e n Pr b e n M n a t r ng He v e c n
的趋势 。
例 如 ,在 16 9 0年 , 克 拉 马托 尔 机器 制造 厂 按 利 佩 新 茨 克拖 拉 机 厂 的 订 货 ,曾制 造 公称 力 8 MN的 曲 柄 式 热 0
模 锻压 力 机 , 是 其工 作 可靠 性 不 高 : 但 在每 批 行程 后 必 须
拉 紧所有 连 接件 ,且需 重 新 调 整 。考 虑 到那 时 引起 困难 的原 因 , 不仅 是 具体 的设计 解 决 办 法 和生 产 水平 , 且 是 而 类 似 型号 的压 力机 原 则上 不 可 能提 高 公称 力 。这 点 已被 后来 压力 机 制 造 的实 际 所证 实 。 从 7 代 中期 开 始 ,大 型锻 件 的 品种 不 断 迅 速 扩 0年 大 为 制造 这 些锻 件 , 求 采 用公 称 力 8 MN以上 的 曲柄 要 0 式 热 模锻 压 力 机 。在 这 些锻 件 的品种 中包括 载 重 汽 车 的 曲轴 和前 轴 梁 、 型齿 轮 和 管法 兰 、 旋 桨 发动 机 的 涡轮 大 螺 叶 片和 桨 叶 、 多其 它 重型 锻 件 。 许 研 究表 明 , 在成批 和大 批 生 产 条件 下 , 在锻 锤 线上 制 造 重量 为 6 k 以上 的锻 件 是 不合 理 的 ,因这 时不 能 保证 09 所需 的生 产率 。 已确定 ,当大 型锻 件从 锻 锤上 转 到 曲 柄 式 热模 锻 压力 机 上 生产 时 , 过 减 小余 量 、 通 模锻 斜 度 和 毛 边 金 属废 料 可节 约 金 属达 2 %以上 。例如 ,在 曲柄 式 热 0 模 锻 压力 机 上模 锻 重 量 为 8 k 以上 的 曲轴 时 , 量 可 减 09 余 小 1 % ~5 % , 锻 斜 度可 减 小 4 % 。在 比较分 析 蒸 汽 7 0 模 7
国产热模锻压力机的创新研究及应用选型
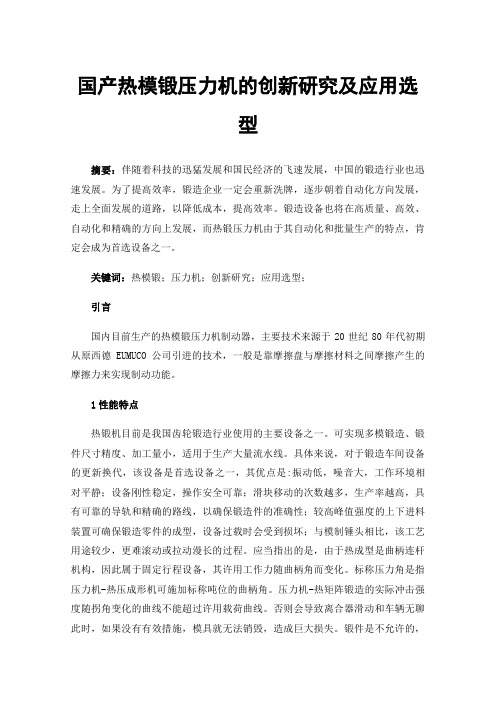
国产热模锻压力机的创新研究及应用选型摘要:伴随着科技的迅猛发展和国民经济的飞速发展,中国的锻造行业也迅速发展。
为了提高效率,锻造企业一定会重新洗牌,逐步朝着自动化方向发展,走上全面发展的道路,以降低成本,提高效率。
锻造设备也将在高质量、高效、自动化和精确的方向上发展,而热锻压力机由于其自动化和批量生产的特点,肯定会成为首选设备之一。
关键词:热模锻;压力机;创新研究;应用选型;引言国内目前生产的热模锻压力机制动器,主要技术来源于20世纪80年代初期从原西德EUMUCO公司引进的技术,一般是靠摩擦盘与摩擦材料之间摩擦产生的摩擦力来实现制动功能。
1性能特点热锻机目前是我国齿轮锻造行业使用的主要设备之一。
可实现多模锻造、锻件尺寸精度、加工量小,适用于生产大量流水线。
具体来说,对于锻造车间设备的更新换代,该设备是首选设备之一,其优点是:振动低,噪音大,工作环境相对平静;设备刚性稳定,操作安全可靠;滑块移动的次数越多,生产率越高,具有可靠的导轨和精确的路线,以确保锻造件的准确性;较高峰值强度的上下进料装置可确保锻造零件的成型,设备过载时会受到损坏;与模制锤头相比,该工艺用途较少,更难滚动或拉动漫长的过程。
应当指出的是,由于热成型是曲柄连杆机构,因此属于固定行程设备,其许用工作力随曲柄角而变化。
标称压力角是指压力机-热压成形机可施加标称吨位的曲柄角。
压力机-热矩阵锻造的实际冲击强度随拐角变化的曲线不能超过许用载荷曲线。
否则会导致离合器滑动和车辆无聊此时,如果没有有效措施,模具就无法销毁,造成巨大损失。
锻件是不允许的,温度低,操作错误可能导致汽车无聊,停产。
为了避免过载和确保锻造零件的尺寸,需要多次调整闭合高度,模具调整相对较重,使热锻机适合批量生产,效率和质量稳定。
2工艺用途及其选择2.1热模锻压力机使用选择使用热锻压力机的选择包括确定压力机的额定压力,以及压力机工作平面和滑块底部的尺寸、行程、闭合高度和调整量等参数,并确保用于锻造模具的能量小于或等于压力机所能提供的最大能量使用热锻压机时,工件加热温度过低,在锻造过程中冷却加热工件,工件体积公差和压机闭合高度调整不当,可能会导致锻造力大幅增加因此,正确选择热锻压机的额定力仍然是保证热锻压机正常可靠运行的重要手段。
168MN热模锻压力机的结构分析
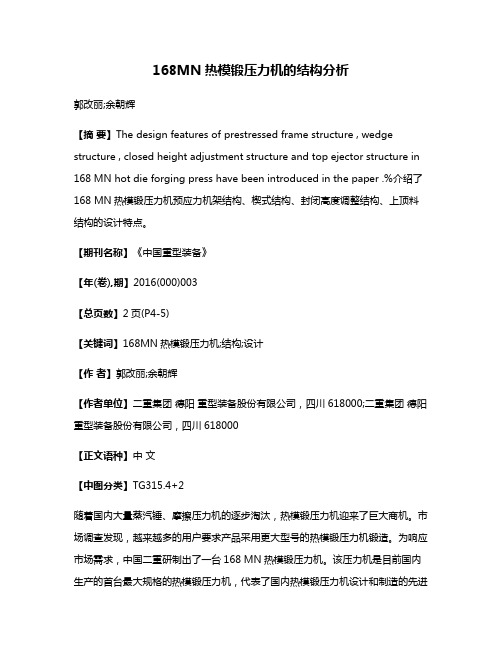
168MN热模锻压力机的结构分析郭改丽;余朝辉【摘要】The design features of prestressed frame structure , wedge structure , closed height adjustment structure and top ejector structure in 168 MN hot die forging press have been introduced in the paper .%介绍了168 MN热模锻压力机预应力机架结构、楔式结构、封闭高度调整结构、上顶料结构的设计特点。
【期刊名称】《中国重型装备》【年(卷),期】2016(000)003【总页数】2页(P4-5)【关键词】168MN热模锻压力机;结构;设计【作者】郭改丽;余朝辉【作者单位】二重集团德阳重型装备股份有限公司,四川618000;二重集团德阳重型装备股份有限公司,四川618000【正文语种】中文【中图分类】TG315.4+2随着国内大量蒸汽锤、摩擦压力机的逐步淘汰,热模锻压力机迎来了巨大商机。
市场调查发现,越来越多的用户要求产品采用更大型号的热模锻压力机锻造。
为响应市场需求,中国二重研制出了一台168 MN热模锻压力机。
该压力机是目前国内生产的首台最大规格的热模锻压力机,代表了国内热模锻压力机设计和制造的先进水平。
168 MN热模锻压力机是在125 MN压机的基础上,结合锻压设备自动化、智能化的发展趋势,采用了一系列科学合理的创新设计技术,不仅保证了压力机的使用性能,而且为实现自动化连线垫定了坚实基础。
本文分析了该压机的结构设计。
热模锻压力机机架是连接和安装热模锻压力机所有功能机构的基础,承受模锻产生的力和力矩。
因此,机身的合理设计对减轻压力机质量、提高压力机刚度以及减少制造工时都具有直接的影响[1]。
如图1所示,为满足机架刚度要求,168 MN热模锻压力机不仅采用上梁、左右侧机架、下机架组成的铸钢机架,而且采用四个拉杆将机架预紧,还在机架左右布置了三个横向拉杆,使得机架在锻造之前就具有一定的预应力。
- 1、下载文档前请自行甄别文档内容的完整性,平台不提供额外的编辑、内容补充、找答案等附加服务。
- 2、"仅部分预览"的文档,不可在线预览部分如存在完整性等问题,可反馈申请退款(可完整预览的文档不适用该条件!)。
- 3、如文档侵犯您的权益,请联系客服反馈,我们会尽快为您处理(人工客服工作时间:9:00-18:30)。
125MN热模锻压力机拉杆测试研究摘要论述125mn热模锻压力机的检测方法和结果,并就实测数据和影响因数进行了分析。
125mn热模锻压力机是由左、右侧机架、上梁、下机架通过四根拉杆组合而成一个坚实的铸钢机架,拉杆的拉力是保证主体设备正常运行关键参数。
拉杆通过加热方法使其伸长并拧紧螺母,降温后拉杆收缩产生拉应力,本次测试主要测试拉杆加热预紧后的应变值,并以此计算拉杆预紧力。
关键词应力;应变;预紧力;检测
中图分类号th2 文献标识码a 文章编号
1674-6708(2012)64-0145-02
1 测量设备、元器件及计算公式
1.1 测量设备及元器件
1.1.1 测量设备
本次测试选定了主要的测量设备为江苏东华测试技术有限公司制造的dh3815静态应变测试系统。
1.1.2 测量元器件及主要参数
拉杆应变测量主要测量元件为应变片,采用中航工业电测仪器股份有限公司公司制造的高温应变片bb350-4bb。
该型号应变片电阻值350ω,灵敏系数:k=2.04,使用温度<250℃。
1.1.3 应变片传感器的工艺要求
在测试中应变片的粘贴要符合作为传感器的粘贴工艺。
为此,
选用北京化工厂生产的r-1型502高温胶作为粘胶,按照应变片传感器的标准工艺要求进行布置。
1.2 计算公式
1.2.1 应变仪读数到测试应变的换算
本次拉杆应变片采用半桥接法引入应变仪。
应变仪读数和测试应变的换算如下:
对半桥接法:
其中:为测试应变,i为应变仪读数,为材料泊松比。
1.2.2 应变到应力以及预紧力的计算
对于125mn模锻压机,拉杆为单向应力状态。
根据虎克定律,应力由测试应变表示为:式中,e为弹性模量(),为测试应变。
由于拉杆主要段为等截面杆,根据测试得到的应力,可计算出拉杆预紧力为:
式中:f0预紧力,为轴向应力,a为横截面积(a前=3 138cm2,a后=2 533cm2)。
2 拉杆应变测试及计算分析
2.1测点布置
此次应力测试我们采用了静态应变测量技术,选用二片应变片组成的应变花(90度角),根据设计要求,拉杆应力测点是在四根拉杆中部距二次灌浆面4 300mm处布置一组应变片组成半桥,每测点布二组接至静态应变仪。
如下图所示。
2.2测试过程
125mn热模锻压力机由左、右侧机架、上梁、下机架通过四根拉杆加热预紧组合而成一个坚实的铸钢机架,四根拉杆的预紧力参数测试尤为重要。
根据现场装配过程包含了拉杆的加热-降温过程。
在整个过程中对拉杆应变进行监控测试,应变值由应变测试系统自动记录。
现场通过加热方式使拉杆达到设计要求的伸长量,拧紧螺母后自然降温,利用拉杆收缩施加预紧力。
拉杆测点布置图
2.3 补偿及预置平衡
2.3.1 补偿
应变的测试主要考虑温度的补偿。
但对于拉杆应变片用半桥接法,拉杆应变片采用轴向和径向成90度的应变花接法,实现温度应变自补偿,温度应变不影响电桥平衡。
2.3.2 预置平衡与修正的考虑
根据安装工艺要求,为了消除接触面初始间隙,对拉杆螺母施加了一定的初始拧紧力矩,装配测试时以此作为测试初始状态,各测点可能有一定初始应变,所有测点预调平衡,应变仪读数归零。
2.4 测试结果及计算分析
为消除接触面间隙,在预紧前先给各螺母施加了初始力矩,该过程从11月15日开始,对四根拉杆同时加热(持续时间超过了14
个小时),伸长量达到要求后,拧紧螺母,自然冷却到常温,实现拉杆的预紧。
根据降温较稳定状态下的测点应变读数(取稳定时的值),应变实测数据见下表:
2.4.1 取值分析
从上表所测数据中,1号拉杆上的测点1与测点9,2号拉杆上的测点2与测点10的数据差距较大,3号拉杆上的测点3已损坏,4号拉杆上的测点4与测点12的数据相差较小,原因如下:由于本次加热的加热杆总功率不够、放置不均匀(偏心)和通风状态不好等,拉杆热量为此分布严重不均,造成出沙孔贴片处300mm直径范围内不同位置处温度差异很大,以致于有些位置温度过高造成应变片失效或部分失效,从而使得两组数据的差异也较大。
在测试当天晚上,测试人员经过通宵监测,用测温器测试,发现当加热快结束时,已加热14小时,在1号拉杆上的测点1的表面温度79℃,而测点9的温度就达到103℃;2号拉杆上的测点2的表面温度87℃,而测点10的温度就已达到105℃;3号拉杆上的测点3点处温度高达120℃,应变片已经失效,而测点11的温度是92℃;4号拉杆上的测点4点处温度71度,测点12的温度是78℃,这组数据就比较接近。
经过观察,在各高温区的应变片有的部分失效,有的已经损坏,而温度较低处的应变片是完全正常的。
故取采集数据为:1号拉杆测点1;2号拉杆测点2;3号拉杆测点11;4
号拉杆测点4。
2.4.2 测试数据及计算数据如下表所示
3主要测试结论及建议
1)前后拉杆预紧力最大分别为4 502t、3 324t。
根据前后拉杆预紧力要求分别为5 000t和3 900t,结合现场实际情况,根据计算结果,得知预紧力未达到设计要求。
2)按照拉杆加热预紧测试所采用的静态应变测试法的要求,拉杆预紧时贴片处表面温度不应超过80℃,加热预紧所需的加热棒功率应达到360kw,加热温度控制在450℃~470℃,加热时间应在9h左右即可达到要求的伸长量。
一般此类测试在每根拉杆上只需贴一组应变片,而为确保能采集到有效数据及通过两组数据进行相互验证,现场测试人员加贴了一组应变片;本次测试贴片严格按规范操作。
但本次加热总功率虽经技术人员的改进,也只有228kw,为达到加热预紧要求的伸长量,加热温度后来达到550℃~570℃,加热时间达14.5h,既没有满足加热温度控制在450℃,也没有满足加热时间这两个指标。
因此两组应变片中,有的完全失效,有的部分失效。
3)对于实测数据与设计要求偏小约10%~15%的情况,分析如下:根据现场安装情况,原定应在规定期间完成的预紧,由于加热杆等原因,经过多次加热,加热时去掉了热电偶,没有进行温度控制,致使加热棒在加热过程中就已经熔化,拉杆内部局部温度相当高,后两次加热温度也在550℃以上,多次超过450℃的高温加热,不排除可能造成拉杆组织
相变,使内应力发生变化,可能是造成预紧力偏小的主要原因。
参考文献
[1]吴宗岱,陶宝祺主编.应变电测试原理及技术.
[2]邵明亮,李文望主编.机械工程测试技术.
[3]刘鸿文主编.材料力学.。