2第八章聚酯切片及其干燥习题参考答案
合成纤维工艺习题

合成纤维工艺习题 Prepared on 22 November 2020纤维期末考试题:1、概念题1)、溶液纺丝 2)、线密度 3)、冷却长度L K 4)、溶胀度 5)、FDY 6)、空气变形纱 7)、极限氧指数 8)、湿法纺丝 9)、断裂伸长率 10)、浓缩凝固 11)、卷曲作用 12)、FOY 13)、缩醛度 14)、拉伸曲线的基本类型 15)、干法纺丝 16)、回潮率 17)、拉伸比 18)、假捻变形 19)、ZHENMOY 20)、复合纤维 21)、凝固的临界浓度再生纤维 23)短纤维24)长丝 25)零强温度 26)纤度 27)结晶速率常数(K) 28)动力学结晶能力(G) 29)连续冷却相变曲线(CCT) 30)熔体纺丝法 31)直接纺丝法32)切片纺丝法 33)牵切纤维 34)线密度 35)断裂长度36)打结强度37)钩接强度38)熔体纺丝39)湿法纺丝40)成纤聚合物41)断裂长度42)相对强度43)强度极限44)取向结晶45)双扩散46)POY 47)化学纤维48)含湿率49)天然纤维50)合成纤维2.填空题1.化学纤维的制造可以概括的分为____,____,____,____四个工序。
2.化学纤维按基本制造方法分_____,_____,_____三种。
3.化学纤维分为____,____,____。
4.纤维的染色性与_____,_____,_____三方面因素有关。
5.干法纺丝溶剂从纺丝线上除去三种机理_____,_____,_____。
6. 真空转鼓干燥机主要由_____,_____,_____三部分组成。
7.组合式干燥设备主要有_____,_____,_____三部分组成。
8.根据切片的结构变化把干燥划分为_____,_____,两个阶段。
9.喷丝板导孔形状有____,____,____,____四种。
10.熔体纺丝方法用于工业生产的有_____,_____,两种方法。
11.用于湿法纺丝的纺丝溶液浓度为_____,用于干法纺丝溶液浓度为_____。
2017年高分子材料加工工艺学I-复习题及答案

高分子材料加工工艺学复习题1、合成PET的原料(单体)是什么?写出直接酯化法合成聚对苯二甲酸乙二酯的主要化学反应式。
P11,P13 分子式自写答:(1)单体:对苯二甲酸双羟乙二酯(BHET)(2)直接酯化法即将对苯二甲酸(TPA)与乙二醇(EG)直接进行酯化反应,一步制得BHET。
BHET缩聚脱除EG生成PET。
反应式:2、聚酯切片干燥的目的是什么?其干燥机理是什么? P20 P20~21答:(1)目的 1)除去水分。
在纺丝温度下,切片中的水分存在使PET大分子的酯键水解,聚合度下降,纺丝困难、质量降低;少量水分汽化造成纺丝断头。
2)提高切片含水的均匀性,以保证纤维质量均匀。
3)提高结晶度及软化点,防止环结阻料。
(2)机理1)切片中的水分:PET大分子缺少亲水性基团,吸湿能力差,通常湿切片含水率<0.5%,其水分分为两部分:一部分是沾附在切片上表面的非结合水,另一部分是与PET大分子上的羰基及极少数的端羟基等以氢键结合的结合水。
2)切片的干燥曲线:切片干燥包括两个基本过程:加热介质传热给切片,使水分吸热并从切片表面蒸发,水分从切片内部迁移至切片表面,再进入干燥介质中。
这两个过程同时进行,因此切片的干燥实质是一个同时进行传质和传热的过程,并伴随高聚物的结晶度和软化点变化。
干燥曲线可知:①切片的含水率随干燥时间延长而逐步降低到平衡。
②干燥速度与T、t有关,T升高,V升高,140℃时最快。
③后期曲线平缓3)切片干燥过程的结晶:由于PET分子链的结构具有高度立构规整性,所有的芳环几乎处于同一平面上,因而具有紧密堆积的能力与结晶倾向。
结晶对切片干燥速度有很大影响。
通常情况下,结晶会使干燥速率迅速大幅度下降。
3、螺杆挤压机按几何分段可分哪三段?各段的作用是什么?P26、原理ⅡP262理解名词术语:螺杆的长径比、压缩比 P26~27答:(1)三段:进料段、压缩段和计量(均化)段。
(2)作用:①进料段:对物料进行输送和预热,使物料受压、受热前移;②压缩段:压实物料、使物料熔融,排除物料中的空气;③计量段:使熔体进一步塑化均匀,并将料流定量、定压地送入机头,使其在口模中成型。
2第八章聚酯切片及其干燥习题参考答案

涤纶长丝习题的参考答案第八章聚酯切片及其干燥1•长丝对切片质量有何要求?并说明理由。
[1] 特性粘数特性粘数是用来表示切片相对分子质量大小的一个指标。
相对分子质量的大小直接影响其加工性和纤维质量。
由于相对分子质量测量较麻烦,所以用特性粘数来表示。
相对分子质量低,则熔体粘度下降,纺丝易断头,纤维也经不起较高倍率的拉伸,所得成品强力下降,延伸度上升,耐热性、耐光性、耐化学稳定性差。
当相对分子质量小于8000〜100时,几乎不具可纺性。
要使产品既具有适当的物理机械性能,又能顺利纺丝,聚酯切片必须有适当的相对分子质量。
长丝切片的特性粘数,一般为0.660.02dL/g。
[2] 熔点(软化点)熔点是指高分子链能自由运动的温度。
熔点高低直接影响纺丝温度。
长丝生产要求切片的熔点260 C左右。
若波动大,会使生产波动,质量不稳定。
熔点升高或降低,均可能使染色性能下降。
[3] 二甘醇含量二甘醇是切片生产中的付产物,其含量的多少影响切片的熔点、色相和成品的染色,要求含量小于1.3%。
且分布均匀。
[4] 凝聚粒子聚酯切片中的凝聚粒子主要有聚合物的氧化凝胶物,二氧化钛凝聚物,催化剂沉淀物,以及反应釜壁上生成的高熔点物,碳化物等。
这些杂质的存在一方面加重了熔体预过滤器或组件过滤层的负荷,而且还极易导致毛丝和断头,要求凝聚粒子含量V0.4 个/mg (10 呵V直径V 20口)。
[5] 端羧基含量:端羧基含量高,说明相对分子质量分布宽,可纺性差。
一般要求其含量为30mmol/106mg。
[6] 二氧化钛含量:在聚酯切片中加入TiO2 的目的是为了使纤维消光,加入量为0.3% 〜0.5%。
在能取得较好消光效果的前提下,TiO2 的含量应尽量低,并且分布均匀,粒子细。
[7] 灰分:含量高,表明切片内杂多,切片的可纺性差。
一般要求<0.1%。
[8] 铁质:含铁量高,会使纤维发黄,色泽变差,要求其含量<3ppm。
[9] 色相:切片的色相不仅影响成品纤维的色相,而且影响切片的可纺性。
涤纶长丝加工工艺部分的习题

涤纶长丝加工工艺部分的习题第二篇涤纶长丝加工工艺部分的习题第七章概述1. 按产品的性能特点来分,涤纶长丝有哪些品种?各自的特点如何?2. 涤纶长丝的生产工艺路线有哪几种?3. 常规纺丝的三步法工艺路线是指的什么?高速纺丝有哪几种工艺路线?4. 涤纶长丝的生产特点有哪些?5. 涤纶长丝的品质指标主要有哪些?6. 涤纶长丝的外观指标主要有哪些?最重要的外观指标是什么?为什么?7. 条干不匀率是一种表示什么的指标?长丝条干不匀,在加工过程中容易产生什么现象?8. 断裂伸长率是反应纤维什么特性的指标?该指标有何意义?9. 涤纶长丝通过哪些物理变形方法可仿制哪些差别化纤维?10.涤纶长丝通过化学改性的方法,纺制的差别化纤维可获得哪些特殊性能?第八章聚酯切片及其干燥1.长丝生产对切片质量有何要求?并说明理由。
2.怎样在纺前对切片可纺性作出判断?3.试述切片可纺性的表现特征。
4.切片含水率对纺丝工艺有何影响?5.切片干燥的目的是什么?6.对切片干燥有何要求?7.试述切片干燥的原理。
8.切片干燥一般干燥进风温度不应超过多少度?切片温度不宜超过多少度?第九章常规纺丝1.写出常规纺丝的工艺流程。
2.试述纺丝的原理。
3.常规纺丝的工艺参数有哪些?其中熔体温度对纺丝过程及产品质量有何影响?常规纺丝时,为什么要上油给湿?4.什么叫预取向?取向度可用什么来表示?影响预取向的主要因素有哪些?5.卷绕丝具有何种特征?6.为什么要对UDY进行拉伸加工?对其有何要求?7.拉伸的工艺参数有哪些?为什么要先对UDY进行平衡?平衡条件对加工过程及产品质量有何影响?8.对UDY进行拉伸加工时,如何选择拉伸温度?9.对UDY进行拉伸时,拉伸倍数对成品丝的质量有何影响?10.拉伸过程中纤维的微观结构发生了很大的变化,主要表现在什么方面?11.结晶的生成需要什么条件?造成拉伸丝高结晶度的主要原因是什么?12.卷绕丝经拉伸后为什么要进行定型?13.试述假捻变形的原理。
纺丝工考试:纺丝工考试考试题及答案模拟考试练习

可编辑修改精选全文完整版纺丝工考试:纺丝工考试考试题及答案模拟考试练习 考试时间:120分钟 考试总分:100分遵守考场纪律,维护知识尊严,杜绝违纪行为,确保考试结果公正。
1、判断题 纺丝熔体计量泵在安装就位后,需要进行热紧固才能开启。
本题答案: 2、判断题 对于衣着用长丝,伸长愈大,手感愈柔软,后道加工毛丝、断头却较少。
本题答案: 3、单项选择题 油轮定期清洁是为了防止( )。
A.油轮磨损 B.油剂腐败,油藻增多,影响生产 C.轴承损坏 D.断头 本题答案: 4、判断题 增压泵出口压力不允许有波动。
本题答案: 5、判断题 液相热媒膨胀槽采用液位低报联锁保护。
本题答案: 姓名:________________ 班级:________________ 学号:________________---------密----------------------------------封 ----------------------------------------------线----------------------6、单项选择题聚酯切片分子量分布(),而且平均分子量()时,对纺丝有利。
A.宽,低B.宽,高C.窄,低D.窄,高本题答案:7、单项选择题空气处理系统新风经过表冷器主要是为了()。
A.增加新风湿度B.增加新风温度C.给新风脱湿D.过滤新风灰尘本题答案:8、判断题清洗炉内的三甘醇蒸汽是通过通入冷TEG的冷凝器来冷凝的。
本题答案:9、单项选择题联锁线路通常由输入部分,输出部分和()三部分组成的。
A.逻辑部分B.驱动部分C.控制盘D.选择开关本题答案:10、单项选择题增压泵出口压力升高,正确的处理方法是()。
A.手动降低增压泵的输出B.聚酯原料降负荷C.长丝停位降负荷D.拉断丝束放流本题答案:11、多项选择题FDY热辊温度的调整依据是()。
A.沸水收缩率B.染色性能C.卷绕张力D.条干不匀率本题答案:12、单项选择题三甘醇清洗喷丝板的温度控制正确的是()。
第2节聚酯切片的干燥(二)

第2节聚酯切片的干燥(二)一、聚酯切片干燥的必要性聚酯切片是聚酯生产过程中的一种重要中间产品,其主要成分为聚对苯二甲酸乙二醇酯(PET)。
在聚酯切片的生产过程中,由于聚合反应及后续处理过程中可能存在的水分、醇类等低分子物质,会对最终产品的性能产生不利影响。
因此,对聚酯切片进行干燥处理,去除其中的低分子物质,提高其纯度,对保证产品质量具有重要意义。
1. 提高聚酯切片的结晶速率和结晶度聚酯切片中的低分子物质会影响其结晶速率和结晶度,进而影响产品的性能。
通过干燥处理,可以去除这些低分子物质,提高聚酯切片的结晶速率和结晶度,从而提高产品的力学性能、热性能和透明度。
2. 降低聚酯切片的熔点低分子物质的存在会导致聚酯切片的熔点升高,影响其在后续加工过程中的熔融流动性。
通过干燥处理,可以降低聚酯切片的熔点,提高其在加工过程中的流动性,有利于提高生产效率和降低能耗。
3. 减少聚酯切片在加工过程中的气泡和银纹低分子物质在聚酯切片加工过程中容易产生气泡和银纹,影响产品的外观和性能。
通过干燥处理,可以减少这些缺陷,提高产品的质量和市场竞争力。
4. 提高聚酯切片的稳定性干燥处理可以去除聚酯切片中的不稳定因素,提高其在储存和运输过程中的稳定性,降低产品的水解降解速率,延长产品的使用寿命。
二、聚酯切片干燥方法及设备聚酯切片的干燥方法主要有以下几种:热风干燥、真空干燥、红外干燥和微波干燥。
下面分别介绍这几种干燥方法及其设备。
1. 热风干燥热风干燥是利用热空气作为干燥介质,通过强制对流将热量传递给聚酯切片,使其中的水分和低分子物质蒸发的一种干燥方法。
(1)设备结构热风干燥设备主要包括:干燥室、热风炉、风机、物料输送装置和控制系统。
干燥室分为多层,每层设有输送带,用于放置聚酯切片。
热风炉产生的热空气通过风机送入干燥室,与聚酯切片进行热量交换。
(2)干燥原理热风干燥过程中,热空气与聚酯切片接触,热量传递给切片,使其中的水分和低分子物质蒸发。
5 干燥操作习题解析
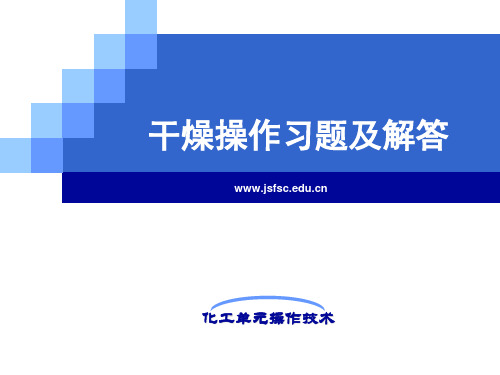
化工单元操作技术
江苏食品职业技术学院
选择题
6. 关于对流干燥过程的特点,以下哪种说法不正确( D )。 A、对流干燥过程是气固两相热、质同时传递的过程; B、对流干燥过程中气体传热给固体; C、对流干燥过程湿物料的水被汽化进入气相; D、对流干燥过程中湿物料表面温度始终恒定于空气的湿球温度 7. 在总压不变的条件下,将湿空气与不断降温的冷壁相接触,直至空气在光滑 的冷壁面上析出水雾,此时的冷壁温度称为( C )。 A、湿球温度; B、干球温度; C、露点; D、绝对饱和温度 8. 在总压 101.33 kPa , 温度 20 ℃ 下,某空气的湿度为 0.01 kg水 /kg干空气,现维持总压不变,将空气温度升高到 50 ℃,则相对湿度( B )。 A、增大; B、减小; C、不变; D、无法判断 9. 在总压 101.33 kPa , 温度 20 ℃ 下,某空气的湿度为 0.01 kg水 /kg干空气,现维持温度不变,将总压升高到 125 kPa,则相对湿度( A )。 A、增大; B、减小; C、不变; D、无法判断 10. 湿度表示湿空气中水汽含量的( B )。 A、相对值; B、绝对值; C、增加值; D、减少值
化工单元操作技术
江苏食品职业技术学院
简答题
1. 试分析: (1)湿空气的干球温度、湿球温度、露点在什么情况下相等?什么情况下 不等,大小关系如何? (2)湿空气在进入干燥器前,往往进行预热,这样做有什么好处? 答:(1)对于饱和空气(相对湿度=100%),干球温度=湿球温度=露 点温度;对于不饱和空气,干球温度>湿球温度>露点温度。 (2)温度升高,饱和蒸汽压变大,相对湿度变小,可增加空气的载湿能 力。同时温度升高,空气热焓量增加,增强了空气的载热能力。 2. 试简要说明湿物料在热空气流中的干燥过程? 答:干燥开始时,因物料表面被水分充分润湿,表面形成对应的饱和水气分 压>热空气主体的水汽分压,而表面温度<热空气温度,故物料表面的水汽 即通过气膜向热空气主体扩散,而需要的热量则由空气主体以对流方式通过 气膜传至物料表面,并导热方式传至内部。由于表面水汽扩散,使物料表面 与内部形成湿度差,这样物料内部的水分就会向表面扩散供给其汽化。随着 干燥的不断进行,物料中的水分就会不断的减少而达到产品的含水量。
涤纶长丝纺丝工艺与质量控制—聚酯切片的干燥

(二)、聚酯切片的干燥工艺参数 1、间隙式转鼓烘干工艺
项目
单位 参数
项目
单位
装料量
Kg
1750
转速
r/min
工作压力
Pa
40
升温时间 蒸汽压力150kpa
小时 0.5
蒸汽压力200Kpa 小时 1
蒸汽压力250Kpa 小时 1
蒸汽压力300Kpa 小时 1.5
蒸汽压力400Kpa 小时 1.5
保温时间 蒸汽压力500Kpa 小时 4 冷却时间 小时
进出料时间
-
小时 1.5
干燥温度 -
C
145-150 干切片含水 %
ห้องสมุดไป่ตู้
参数 2.9
1 <0.01
29
(二)、聚酯切片的干燥工艺参数
2、连续式烘干工艺 几种充填干燥工艺参数
流程图编号
3-10 3-11 3-12 3-13
结晶方式
机械搅拌 机械搅拌 机械搅拌 流态化
22
(一)、聚酯切片的干燥工艺流程
2、连续干燥工艺 (1)、预结晶 1.利用沸腾床等装置,将热空气从下往上吹向切片,使得切片呈现
沸腾状,切片粒子之间的位置一直处于快速波动之中,有效防止了切片 之间的粘结。一般将这种方式称为BM式。
2.利用搅拌装置,对处于预结晶过程中的切片不断搅拌,使得切片 粒子之间无法粘结或者粘结后随即被打散。一般将这种方式称为KF式 。 利用震动装置,使得处于预结晶过程中的切片高频震动,粒子之间的 位置快速变化,从而无法相互粘结。一般与BM式结合使用。
35
干燥后的切片由于产生结晶,切片也变得坚 硬,且熔程狭窄,熔体质量均匀,软化点得到提 高,可以防止切片进入螺杆挤压机后会很快软化 粘合,造成环结阻料。
原料化学分析试题及参考答案

原料化学分析试题及参考答案一、单选题(共46题,每题1分,共46分)1.下列物质的干燥条件中何者是错误的?( )A、邻苯二甲酸氢钾在105℃~110℃的电烘箱中B、Na2CO3在105℃~110℃电烘箱中C、CaCO3放在盛硅胶的干燥器中D、NaCl放在空的干燥器中正确答案:B2.下列物质不能作为干燥剂的有()。
A、硅胶B、浓硫酸C、Ca(OH)2D、CaO正确答案:C3.仲裁检验是由公认的有权威的( )进行的检验。
A、第三方B、第一方C、第一方和第二方D、第二方正确答案:A4.有毒和刺激性气体放出的操作应在( )操作。
A、实验台上B、窗户外C、通风橱中正确答案:C5.读取滴定管读数时,下列操作中错误的是()。
A、读数时,应使滴定管保持垂直B、读数前要检查滴定管内壁是否挂水珠,管尖是否有气泡C、有色溶液与无色溶液的读数方法相同D、读取弯月面下缘最低点,并使视线与该点在一个水平面上正确答案:C6.准确量取20.5ml溶液,应选用:A、25ml滴定管B、50ml量筒C、100ml的容量瓶D、20ml移液管正确答案:A7.由计算器算得 2.236(×)1.1124/1.036(×)0.2000的结果为12.00471,按有效数字运算规则,应将结果修约为:( )。
A、12B、12.00C、12.0D、12.004正确答案:B8.大量的化学试剂应该怎样贮藏:( )。
A、贮藏在专用贮藏室内B、贮存在化验室操作间里C、堆积在化验室桌上正确答案:A9.氧化还原滴定法和酸碱滴定法基本相同之处是()。
A、分析操作B、方法原理C、反应速度D、反应历程正确答案:A10.计量标准主标准器及主要配套设备经检定和自检合格,应贴上的彩色标志是()。
A、绿色B、橙色C、蓝色D、红色正确答案:A11.化学物质溅入眼部的处理办法是()。
A、立即用大量清水冲洗B、用干净的布擦C、送去就医正确答案:A12.可用下法中哪种方法减小分析测定中的偶然误差?( )A、进行仪器检准B、进行空白试验C、进行对照试验D、增加平行试验的次数正确答案:D13.逆王水中,盐酸和硝酸的体积比是()。
高聚物生产技术练习题库(含参考答案)

高聚物生产技术练习题库(含参考答案)一、单选题(共90题,每题1分,共90分)1.聚酰胺纤维按加工方法可以分为初生丝、拉伸丝和( )A、单丝B、民用长丝C、变形丝D、复丝正确答案:C2.聚氯乙烯的英文缩写是( )A、PEB、PPC、CPD、PVC正确答案:D3.为防止单体聚合,在单体的储存和运输过程中通过加入少量的( )A、添加剂B、防老剂C、阻聚剂D、引发剂正确答案:C4.阳离子聚合最主要的链终止方式是( )A、向溶剂转移B、向反离子转移C、自发终止D、向单体转移正确答案:D5.聚酯生产过程中的工艺塔主要用来分离( )A、EG和PTAB、H2O和PETC、EG和H2OD、EG和PET正确答案:C6.下列选项中,可以反映出聚丙烯等塑料的平均的相对分子质量的是( )A、熔融指数B、挠曲模量C、拉伸强度D、等规度正确答案:C7.下列哪一项不是自由基型聚合反应特点( )A、快增长B、慢终止C、易转移D、慢引发正确答案:B8.掺和的目的是使( )A、产品质量均一稳定B、不同质量的产品分离C、外观颗粒一致D、颗粒表面光滑正确答案:A9.对压力容器用钢的基本要求是:良好的塑性、韧性,良好的焊接性,较高的( )和耐腐蚀性A、强度B、抗冲击力C、承受温差变化能力D、耐压性正确答案:A10.分子中的结构单元数称为( )A、DpB、XnC、MnD、M0正确答案:B11.如果r1·r2≈0,共聚时将得到( )共聚物。
A、接枝B、嵌段C、交替D、无规正确答案:C12.下列不属于离子型聚合反应的是( )A、逐步聚合B、阴离子聚合C、阳离子聚合D、配位聚合正确答案:A13.过氧化苯甲酰属于下列( )类型引发剂A、偶氮类B、有机过氧化物C、无机过氧化物D、氧化-还原体系正确答案:B14.通过调节( )来控制12-R01的液位,保证反应器內物料量的稳定A、泵的功率B、泵的转速C、入口阀D、泵的出口阀正确答案:B15.高分子合成材料的主要来源是( )A、煤B、石油C、天然气D、以上都是正确答案:D16.通常说的“白色污染”是指A、聚乙烯等塑料垃圾B、白色建筑废料C、冶炼厂的白色烟尘D、石灰窑的白色粉尘正确答案:A17.下面高聚物哪一个不是均聚物( )A、PVCB、PTFEC、ABS树脂D、PP正确答案:C18.预缩聚反应器15-R01下室压力进一步降低,为( )KPa-a左右,A、2.2B、2.0C、2.4D、1.2正确答案:D19.阴离子聚合链增长过程中,离子对的存在形式对下列哪一项没有影响( )A、产物结构B、聚合机理C、聚合速率D、产物聚合度正确答案:B20.下列引发剂进行阴离子聚合时活性最强的是( )A、RMgXB、LiRC、RONaD、H2O正确答案:B21.下列聚合物属于均聚物的是( )A、聚丙烯酸甲酯B、尼龙-66C、涤纶D、酚醛树脂正确答案:A22.自由基聚合反应中链增长的序列结构主要是( )种链节连接形式A、头-头连接B、都不是C、尾-尾连接D、头-尾连接正确答案:D23.聚对苯二甲酸乙二醇酯的简称是( )A、PECB、PCTC、PETD、PTC正确答案:C24.ABS树脂是由哪几个原料聚合而成的( )A、丙烯腈-丁二烯-氯乙烯B、丙烯腈-丁二烯-苯乙烯C、丙烯腈-氯乙烯-苯乙烯D、丁二烯-氯乙烯-苯乙烯正确答案:B25.聚酰胺聚合时,当温度升高时,不利于放热反应的进行,故反应向水解方向移动,使产物分子量( )。
服装材料学习题及答案

服装材料学习题及答案名词解释回潮率、主体长度、再蛋白质纤维、马海毛、结构相、抗熔孔性、克罗指、湿法纺丝、临界捻系数、电荷半衰期、相对强度、取向度、吸湿等温线、免烫性、初始模量、捻度、公定回潮率、结晶度、成熟度、异型纤维、品质长度、传热系数、熔体纺丝、冷感性、合成纤维、短绒率、开士米、复合纤维、品质支数、悬垂性、起拱变形、 CV%值、马克隆值、细绒棉、长绒棉、锯齿棉、皮辊棉、棉型纱线的英制支数、品质支数、公制支数、特数、旦数、极限氧指数名词解释答案1.回潮率:指纤维中所含水分的重量对纤维干重的百分率。
2.主体长度:纤维长度重量分布中,重量最重的纤维的长度。
4 .再蛋白质纤维:指用天然蛋白质制成的,组成成分仍为蛋白质的纤维。
5 .马海毛:安哥拉山羊毛。
6 .结构相:指机织物中经纬纱屈曲波高的比值。
7 .抗熔孔性:纤维接触火星时抵抗破坏的性能。
8 .克罗指:指热绝缘值( I clo )即传热系数的倒数。
9 .湿法纺丝:指将溶解制备的纺丝液喷丝后在溶液中固化成丝的方法。
10 .临界捻系数:指纱的强度达到最大时的捻系数。
11.电荷半衰期:指纺织材料上的静电衰减到原始数值一半所需的时间。
12.相对强度:指纤维或纱线单位细度上的强力。
13.取向度:指纤维内大分子链主轴与纤维轴平行的程度。
14.吸湿等温线:指温度一定时纤维回潮率与空气相对湿度的关系曲线。
15.免烫性:织物经洗涤后不经熨烫保持平整状态的性能。
16.初始模量:指纤维或纱线拉伸曲线上起始一段直线部分的应力应变的比值。
17 .捻度:指纱线单位长度内的捻回数。
18 .公定回潮率:权威部门对各种纺织材料根据其吸湿能力的强弱统一规定的回潮率。
19 .结晶度:在纤维中结晶部分占整根纤维的百分比。
20 .成熟度:指棉纤维胞壁的加厚程度。
21.异型纤维:指非圆形截面的纤维。
22.品质长度:又称右半部平均长度,即长度大于主体长度纤维的平均长度。
23 .传热系数:表示织物两表面温差为 1 ℃时 ,1s 内通过 1m 2 织物传递的热量。
环保型聚酯切片稳定剂的合成与应用考核试卷

A.提高反应温度
B.延长反应时间
C.使用环保型催化剂
D.增加原料的投量
10.下列哪种方法可以评价环保型聚酯切片稳定剂的性能?()
A.红外光谱法
B.热重分析法
C.差示扫描量热法
D.以上都是
11.环保型聚酯切片稳定剂在聚酯生产中的应用主要是为了()
B.反应温度
C.反应时间
D.催化剂的种类
14.下列哪种环保型聚酯切片稳定剂适用于聚酯纤维的生产?()
A.抗氧剂1010
B.抗氧剂1076
C.抗氧剂168
D.抗氧剂3114
15.环保型聚酯切片稳定剂合成过程中,以下哪个因素会影响产品的稳定性?()
A.反应压力
B.反应温度
C.催化剂的活性
D.原料的投料顺序
1.环保型聚酯切片稳定剂的主要作用是()
A.提高聚酯的熔点
B.改善聚酯的色泽
C.增加聚酯的抗氧化性
D.提高聚酯的结晶速度
2.下列哪种物质不属于环保型聚酯切片稳定剂?()
A.抗氧剂
B.光稳定剂
C.有机锡稳定剂
D.铅稳定剂
3.环保型聚酯切片稳定剂合成过程中,常用的绿色催化剂是()
A.钴化合物
B.铅化合物
3.合成方法包括直接酯化法、酯交换法等,工艺流程包括原料预处理、催化剂选择、反应条件控制等。确保环保性能应使用绿色催化剂,减少副产物和有害物质生成。
4.未来发展趋势将侧重于开发多功能一体化、高效环保的稳定剂,提高市场竞争力。技术方面需创新合成方法,市场方面需满足多样化需求,环保方面需符合可持续发展要求。
C.钠化合物
D.铜化合物
《化纤成型与加工》习题集
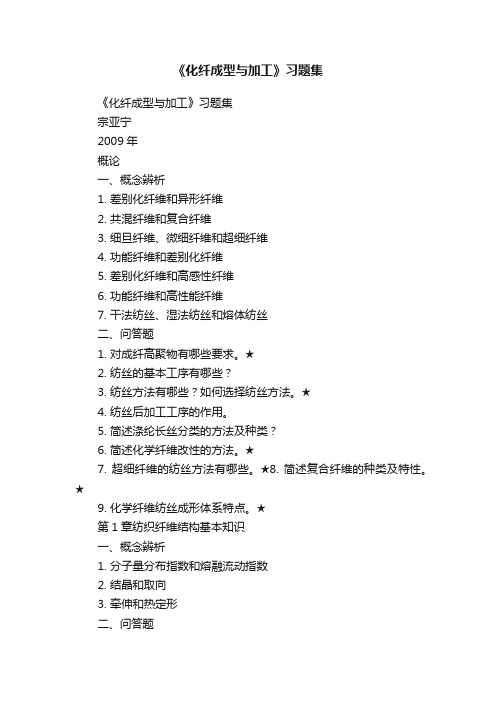
《化纤成型与加工》习题集《化纤成型与加工》习题集宗亚宁2009年概论一、概念辨析1. 差别化纤维和异形纤维2. 共混纤维和复合纤维3. 细旦纤维、微细纤维和超细纤维4. 功能纤维和差别化纤维5. 差别化纤维和高感性纤维6. 功能纤维和高性能纤维7. 干法纺丝、湿法纺丝和熔体纺丝二、问答题1. 对成纤高聚物有哪些要求。
★2. 纺丝的基本工序有哪些?3. 纺丝方法有哪些?如何选择纺丝方法。
★4. 纺丝后加工工序的作用。
5. 简述涤纶长丝分类的方法及种类?6. 简述化学纤维改性的方法。
★7. 超细纤维的纺丝方法有哪些。
★8. 简述复合纤维的种类及特性。
★9. 化学纤维纺丝成形体系特点。
★第1章纺织纤维结构基本知识一、概念辨析1. 分子量分布指数和熔融流动指数2. 结晶和取向3. 牵伸和热定形二、问答题1. 纺织纤维对纤维结构的要求★2. 高聚物晶态结构的类型及特点3. 影响高聚物结晶的因素★4. 高聚物取向的特点。
5. 如何使纤维有较高的强度和较好的伸长能力★6. 简述影响高分子长链柔顺性的因素。
7. 简述缨状微胞模型与缨状原纤模型的相异点。
. 温度对高分子结晶速度有哪些影响。
★9. 高分子整链取向和链段取向有什么不同。
如何在纺织纤维加工中利用这一特点。
★第2章纺丝原料制备一、概念辨析均相溶液聚合、非均相溶液聚合和水相聚合二、问答题1. 简述BHET制备方法及生产过程。
2. 聚对苯二甲酸乙二酯的生产方法及生产过程。
3. 聚酰胺纤维命名★4. 简述聚己内酰胺的制备过程5. 简述聚已二酰己二胺的制备过程6. 简述腈纶纤维采用共聚物纺丝的原因★第3章熔体纺丝纤维成型一、概念辨析1. 控制张力热定型、定长热定型、部分收缩热定型、自由收缩热定型2. 假捻变形纱、空气变形丝(A TY)、网络变形纱、BCF丝3. UDY、POY、FDY、DTY、FOY、HOY4. 高弹丝和低弹丝5. 结构一体化参数和沸水收缩率6. 纺粘法和熔喷法非织造布二、问答题1. 聚酯切片的干燥的目的(聚酯切片干燥后有哪些参数发生了改变)?2. 聚酯切片的干燥的过程和机理。
高分子材料加工工艺学习题答案
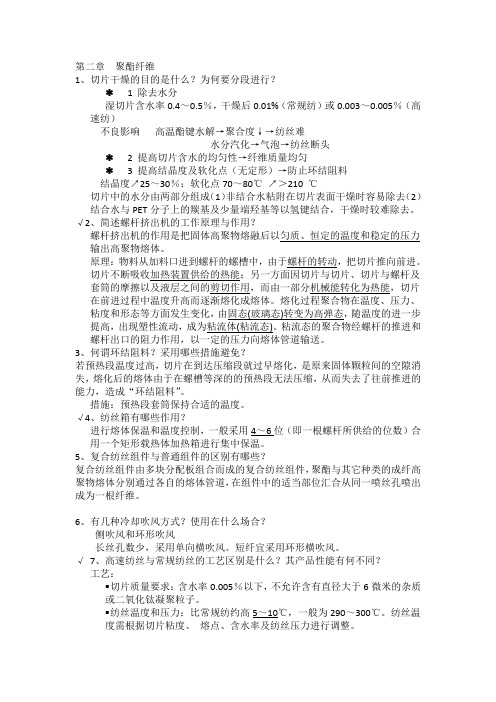
第二章聚酯纤维1、切片干燥的目的是什么?为何要分段进行?← 1 除去水分湿切片含水率0.4~0.5%,干燥后0.01%(常规纺)或0.003~0.005%(高速纺)不良影响高温酯键水解→聚合度↓→纺丝难水分汽化→气泡→纺丝断头← 2 提高切片含水的均匀性→纤维质量均匀← 3 提高结晶度及软化点(无定形)→防止环结阻料结晶度↗25~30%;软化点70~80℃↗>210 ℃切片中的水分由两部分组成(1)非结合水粘附在切片表面干燥时容易除去(2)结合水与PET分子上的羰基及少量端羟基等以氢键结合,干燥时较难除去。
√2、简述螺杆挤出机的工作原理与作用?螺杆挤出机的作用是把固体高聚物熔融后以匀质、恒定的温度和稳定的压力输出高聚物熔体。
原理:物料从加料口进到螺杆的螺槽中,由于螺杆的转动,把切片推向前进。
切片不断吸收加热装置供给的热能;另一方面因切片与切片、切片与螺杆及套筒的摩擦以及液层之间的剪切作用,而由一部分机械能转化为热能,切片在前进过程中温度升高而逐渐熔化成熔体。
熔化过程聚合物在温度、压力、粘度和形态等方面发生变化,由固态(玻璃态)转变为高弹态,随温度的进一步提高,出现塑性流动,成为粘流体(粘流态)。
粘流态的聚合物经螺杆的推进和螺杆出口的阻力作用,以一定的压力向熔体管道输送。
3、何谓环结阻料?采用哪些措施避免?若预热段温度过高,切片在到达压缩段就过早熔化,是原来固体颗粒间的空隙消失,熔化后的熔体由于在螺槽等深的的预热段无法压缩,从而失去了往前推进的能力,造成“环结阻料”。
措施:预热段套筒保持合适的温度。
√4、纺丝箱有哪些作用?进行熔体保温和温度控制,一般采用4~6位(即一根螺杆所供给的位数)合用一个矩形载热体加热箱进行集中保温。
5、复合纺丝组件与普通组件的区别有哪些?复合纺丝组件由多块分配板组合而成的复合纺丝组件,聚酯与其它种类的成纤高聚物熔体分别通过各自的熔体管道,在组件中的适当部位汇合从同一喷丝孔喷出成为一根纤维。
干燥习题(附答案)
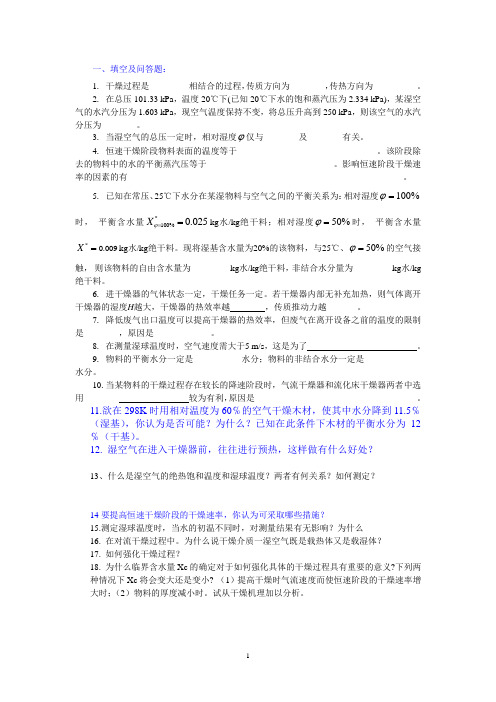
一、填空及问答题:1.干燥过程是_________相结合的过程,传质方向为________,传热方向为__________。
2.在总压101.33 kPa,温度20℃下(已知20℃下水的饱和蒸汽压为2.334 kPa),某湿空气的水汽分压为1.603 kPa,现空气温度保持不变,将总压升高到250 kPa,则该空气的水汽分压为________。
3. 当湿空气的总压一定时,相对湿度ϕ仅与________及________有关。
4.恒速干燥阶段物料表面的温度等于________________________________。
该阶段除去的物料中的水的平衡蒸汽压等于_____________________________。
影响恒速阶段干燥速率的因素的有_______________________________________________________________。
5.已知在常压、25℃下水分在某湿物料与空气之间的平衡关系为:相对湿度100%ϕ=时,平衡含水量*100%0.025X ϕ==kg水/kg绝干料;相对湿度50%ϕ=时,平衡含水量*0.009X=kg水/kg绝干料。
现将湿基含水量为20%的该物料,与25℃、50%ϕ=的空气接触,则该物料的自由含水量为_________kg水/kg绝干料,非结合水分量为_________kg水/kg 绝干料。
6.进干燥器的气体状态一定,干燥任务一定。
若干燥器内部无补充加热,则气体离开干燥器的湿度H越大,干燥器的热效率越,传质推动力越_______。
7.降低废气出口温度可以提高干燥器的热效率,但废气在离开设备之前的温度的限制是________,原因是_____________。
8.在测量湿球温度时,空气速度需大于5 m/s,这是为了。
9.物料的平衡水分一定是___________水分;物料的非结合水分一定是_____________水分。
10.当某物料的干燥过程存在较长的降速阶段时,气流干燥器和流化床干燥器两者中选用________ 较为有利,原因是_____________________________________。
2014年浙江理工大学高分子材料加工工艺学I_复习题_及答案(花花姐)

高分子材料加工工艺学复习题(张顺花)1、按纺丝速度的高低,聚酯纺丝技术路线可分成哪四个类型?P251)常规纺丝:纺丝速度1000~1500m/min,其卷绕丝为未拉伸丝,通称UDY(undrawn yarn)。
2)中速纺丝:纺丝速度1500~3000m/min,其卷绕丝具中等取向度,为中取向丝,通称MOY (medium oriented yarn)。
3)高速纺丝:纺丝速度3000~6000 m/min,纺丝速度4000 m/min以下的卷绕丝具有较高的取向度,为预取向丝,通称POY(pre-oriented yarn)。
若在纺丝过程中引入拉伸作用,可获得具有高取向度和中等结晶度的卷绕丝,为全拉伸丝,通称FDY(fully drawn yarn)。
4)超高速纺丝:纺丝速度6000~8000 m/min。
卷绕丝具有高取向度和中等结晶结构,为全取向丝,通称FOY(fully oriented yarn)。
2、合成PET的原料(单体)是什么?写出直接酯化法合成聚对苯二甲酸乙二酯的主要化学反应式。
P11,P13 分子式自写单体:对苯二甲酸双羟乙二酯(BHET)直接酯化法即将对苯二甲酸(TPA)与乙二醇(EG)直接进行酯化反应,一步制得BHET。
BHET 缩聚脱除EG生成PET。
反应式:3、聚酯切片干燥的目的是什么?其干燥机理是什么?P20 P20~21目的1)除去水分。
在纺丝温度下,切片中的水分存在使PET大分子的酯键水解,聚合度下降,纺丝困难、质量降低;少量水分汽化造成纺丝断头。
2)提高切片含水的均匀性,以保证纤维质量均匀。
3)提高结晶度及软化点,防止环结阻料。
机理1)切片中的水分PET大分子缺少亲水性基团,吸湿能力差,通常湿切片含水率<0.5%,其水分分为两部分:一部分是沾附在切片上表面的非结合水,另一部分是与PET大分子上的羰基及极少数的端羟基等以氢键结合的结合水。
2)切片的干燥曲线切片干燥包括两个基本过程:加热介质传热给切片,使水分吸热并从切片表面蒸发,水分从切片内部迁移至切片表面,再进入干燥介质中。
干燥 考试题及答案

化工原理第八章考试题及答案一、填空题:1.(2分)难度中等干燥进行的必要条件是物料表面所产生的水汽(或其它蒸汽)压力__________________。
答案大于干燥介质中水汽(或其它蒸汽)的分压。
2.(2分)难度容易干燥这一单元操作,既属于传热过程,又属______________。
答案传质过程3.(2分)难度容易相对湿度ϕ值可以反映湿空气吸收水汽能力的大小,当ϕ值大时,表示该湿空气的吸收水汽的能力_________;当ϕ=0时。
表示该空气为___________。
答案小;绝干空气4.(4分)难度中等干燥速率曲线是在恒定干燥条件下测定的,其恒定干燥条件是指:_________________均恒定。
答案干燥介质(热空气)的温度、湿度、速度以及与物料接触的方式。
5.(2分)难度中等在一定温度下,物料中结合水分和非结合水分的划分是根据___________而定的;平衡水分和自由水分是根据__________而定的。
答案物料的性质;物料的性质和接触的空气状态6.(3分)难度中等在一定空气状态下干燥某物料,能用干燥方法除去的水分为__________;首先除去的水分为____________;不能用干燥方法除的水分为__________。
答案自由水分;非结合水分;平衡水分7.(4分)难度较难已知某物料含水量X=0.4kg水.kg量X=0.25kg水.kg X*=0.05kg 水.kg水分为__________,结合水分为__________,自由水分为___________,可除去的结合水分为________。
答案0.15、0.25、0.35、0.2(单位皆为:kg水.kg8.(2分)难度中等某物料含水量为0.5 kg水.kg绝干料,当与一定状态的空气接触时,测出平衡水分为0.1kg水.kg绝干料,则此物料的自由水分为_____________。
***答案***0.4 kg水.kg绝干料9.(2分)题号8009 第8章知识点 200 难度中等作为干燥介质的湿空气,其预热的目的_________________________________________________。
- 1、下载文档前请自行甄别文档内容的完整性,平台不提供额外的编辑、内容补充、找答案等附加服务。
- 2、"仅部分预览"的文档,不可在线预览部分如存在完整性等问题,可反馈申请退款(可完整预览的文档不适用该条件!)。
- 3、如文档侵犯您的权益,请联系客服反馈,我们会尽快为您处理(人工客服工作时间:9:00-18:30)。
涤纶长丝习题的参考答案
第八章聚酯切片及其干燥
1.长丝对切片质量有何要求?并说明理由。
[1] 特性粘数
特性粘数是用来表示切片相对分子质量大小的一个指标。
相对分子质量的大小直接影响其加工性和纤维质量。
由于相对分子质量测量较麻烦,所以用特性粘数来表示。
相对分子质量低,则熔体粘度下降,纺丝易断头,纤维也经不起较高倍率的拉伸,所得成品强力下降,延伸度上升,耐热性、耐光性、耐化学稳定性差。
当相对分子质量小于8000~10000时,几乎不具可纺性。
要使产品既具有适当的物理机械性能,又能顺利纺丝,聚酯切片必须有适当的相对分子质量。
长丝切片的特性粘数,一般为0.66 0.02dL/g。
[2] 熔点(软化点)
熔点是指高分子链能自由运动的温度。
熔点高低直接影响纺丝温度。
长丝生产要求切片的熔点260℃左右。
若波动大,会使生产波动,质量不稳定。
熔点升高或降低,均可能使染色性能下降。
[3] 二甘醇含量
二甘醇是切片生产中的付产物,其含量的多少影响切片的熔点、色相和成品的染色,要求含量小于1.3%。
且分布均匀。
[4] 凝聚粒子
聚酯切片中的凝聚粒子主要有聚合物的氧化凝胶物,二氧化钛凝聚物,催化剂沉淀物,以及反应釜壁上生成的高熔点物,碳化物等。
这些杂质的存在一方面加重了熔体预过滤器或组件过滤层的负荷,而且还极易导致毛丝和断头,要求凝聚粒子含量<0.4个/mg(10μm <直径<20μm)。
[5] 端羧基含量:
端羧基含量高,说明相对分子质量分布宽,可纺性差。
一般要求其含量为30mmol/106mg。
[6] 二氧化钛含量:
在聚酯切片中加入TiO2的目的是为了使纤维消光,加入量为0.3%~0.5%。
在能取得较好消光效果的前提下,TiO2的含量应尽量低,并且分布均匀,粒子细。
[7] 灰分:含量高,表明切片内杂多,切片的可纺性差。
一般要求<0.1%。
[8] 铁质:含铁量高,会使纤维发黄,色泽变差,要求其含量<3ppm。
[9] 色相:切片的色相不仅影响成品纤维的色相,而且影响切片的可纺性。
一般要求b<3。
[10] 粒子尺寸:要求切片粒子的尺寸均匀,超大粒子和粉末含量尽量少,粉末含量不超过0.02%,以防止切片在输送过程中的堵塞,且能减少成品纤维的原料消耗。
[11] 含水率:含水率高,不利于干燥,并增大切片消耗。
切片的标准含水率为0.4%。
2.怎样在纺前对切片可纺性作出判断?
答:未曾使用过的切片,除要看切片的质量指标,还需从以下几个方面分析、判断其可纺性。
[1] 切片的外观形状和包装:
外观形状为切口光滑的园柱形,大小适中,破碎粒子和粉末含量少的切片,容易筛选干燥,在干燥过程中产生的粉末少,螺杆进料顺畅,压力波动小,不影响可纺性。
切片的包装应在贮运过程中不易污染和积存灰尘、泥砂等物。
若有在投料前应予以清除,
否则易造成纺丝组件升压过快。
[2] 切片的色泽:
色泽均一、晶亮的切片可纺性好,若色泽暗淡或明亮不一,或发黄和有夹心碳化粒子,则可纺性较差。
[3] 批间质量差异:
批内或批间质量指标差异小,可纺性好,否则易造成生产不稳定。
[4] 相对分子质量分布指数:
一般用凝胶色谱柱测得α值小于2.0时,可纺性较好。
[5] 差热分析:
熔融结晶温度高,峰形分布窄或峰形极尖锐的切片可纺性差,熔融温度低,峰形分布宽,且平坦的切片可纺性好。
[6] 耐热性:耐热性差,可纺性差。
3.试述切片可纺性的表现特征。
答:切片可纺性的表现特征为:
[1] 预过滤器或纺丝组件的升压速率
日升压速率,高速纺丝应小于10%,常规纺丝应小于6%,否则,易出现染色不匀和毛丝、断头等问题。
升压速率过快,还会影响预过滤器和纺丝组件的使用寿命。
[2] 卷绕筒子满卷率:可纺性好的切片,断头少,满卷率高,大于95%。
[3] 拉伸断头率和绕辊率:可纺性好的切片,拉伸时断头率和绕辊率均较低。
[4] 假捻变形断头率:在变形或拉伸变形张力下,可纺性差的切片其断头率高。
[5] 成品的物理性能:切片的可纺性差,成品的强度低、伸长度小,不匀率大,从外观上看筒子的毛丝也较多。
4.切片含水率对纺丝工艺有何影响?
答: [1] 切片中的水分使聚酯分子在纺丝时产生剧烈水解,相对分子质量降低,从而使丝的质量下降甚至无法纺丝。
[2] 水分的存在使单丝中夹带水蒸汽,形成“气泡丝”,引起毛丝和断头。
[3] 含水量的差异,使成品染色不匀。
[4] 含水切片软化点低,易在螺杆挤出机的进料口受热而软化粘连,造成“环结”堵塞。
5.切片干燥的目的是什么?
[1] 除去水分;[2] 提高切片含水的均匀性;[3] 提高结晶度及软化点。
6.对切片干燥有何要求?
答:切片干燥的要求:
[1]干燥切片的含水率对不同纺丝工艺要求不同,速度愈高、单丝线密度愈小,要求含水率愈低。
常规纺丝:含水率≤80ppm,高速纺丝:含水率≤50ppm,最好≤30ppm。
[2]尽量除去切片在预结晶、干燥过程中因摩擦、撞击而产生的粉末。
[3]干燥过程中不能产生粘连粒子和结块。
否则易堵塞管道,并使螺杆进料不畅,造成压力波动。
[4]切片干燥后,要求特性粘数的变化<0.01。
[5]要求干切片不再度吸湿回潮,干燥均匀性要好。
干燥设备运转费用低,操作维修方便。
7.试述切片干燥的原理
[1] 水分的脱除:
切片的含水量包括自由含水量(F’)和平衡含水量(F*)。
自由含水是可以脱除的水分,平衡含水则是与一定的干燥条件相平衡的,不能被完全脱除的水分,降低平衡水分关系到切片的最终含水量能否符合纺丝要求。
因此,切片干燥的关键是减少平衡含水量。
根据享利定律:F*=KP (1)式中:K——平衡常数P——水汽分压
由式(1)可知,若要降低平衡含水量,必须降低平衡条件的水汽分压,可采用抽真空、空气脱湿、提高温度等均可降低水汽分压。
水分脱除的速率取决于干燥介质温湿度和水分与切片结合的形式。
根据水分子与切片结合形式可将切片中的水分为表面吸附水和内部结合水。
自由水分基本属于表面吸附水,存在于切片表面或孔隙中,较容易去除;平衡水分基本属于分子间水分,其中部分水分子与聚酯大分子形成氢键,很难去除。
只有当切片内部与表面存在水汽分压差时,内部结合水由于温度升高而加剧运动,才能扩散到切片表面,进而蒸发,被干燥介质带出。
切片内的水分扩散到表面较困难,必须有足够的时间才能达到平衡。
水分的平衡是切片内部与表面的平衡,又是切片表面与干燥介质的平衡。
[2] 结晶
当切片温度超过T g时,无定形区开始结晶,结晶需一定的的温度和时间。
结晶在预结晶和干燥两个阶段完成,预结晶可以防止切片在干燥时接触高温产生粘连。
8.干燥时,切片的温度最好不要超过多少度?干燥风的温度最好不要超过多少度?
一般切片温度不宜超过165℃,干燥进风温度不应超过190℃。