课题数控铣削加工工艺浙江工业职业技术学院
数控车削加工工艺
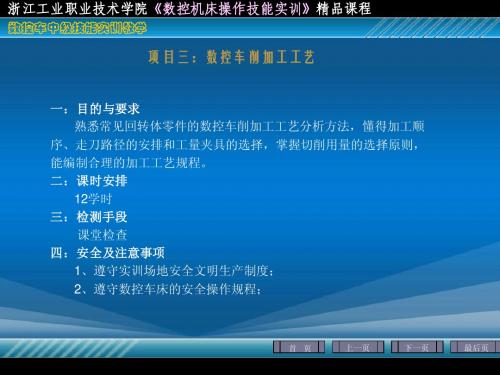
首 页
上一页
下一页
ห้องสมุดไป่ตู้最后页
浙江工业职业技术学院《数控机床操作技能实训》精品课程
数控车中级技能实训教学
一、数控车床加工工艺分析的主要内容 工艺分析是数控车削加工的前期准备工作。工艺制定的合理与否,对程序 编制、加工效率、加工精度等都有重要影响。因此,应遵循一般的工艺原则并 结合数控车床的特点,认真而详细的制定好零件的数控车削加工工艺。 数控车削加工工艺包括以下主要内容: 1、分析被加工零件的工艺性; 2、拟定加工工艺路线,包括划分工序、选择定位基准、安排加工顺序和组 合工序等; 3、设计加工工序,包括选择工装夹具与刀具、确定走刀路径、确定切削用 量等; 4、编制工艺文件。 二、数控车床加工零件的工艺性分析 适合数控车床加工的零件或工序内容选定后,首要工作是分析零件结构工 艺性、轮廓几何要素和技术要求。
首 页
上一页
下一页
最后页
浙江工业职业技术学院《数控机床操作技能实训》精品课程
数控车中级技能实训教学
1、循环切除余量 数控车削加工过程一般要经过循环切除余量、粗加工和精加工三道工序。应根 据毛坯类型和工件形状确定循环切除余量的方式,以达到减少循环走刀次数、 提高加工效率的目的。 (1)轴套类零件 轴套类零件安排走刀路线的原则是轴向走刀、径向进刀,循环切除余量的循环 终点在粗加工起点附近。这样可以减少走刀次数,避免不必要的空走刀,节省 加工时间。 (2)轮盘类零件 轮盘类零件安排走到路线的原则是径向走刀、轴向进刀,循环切除余量的循环 终点在粗加工起点附近。编制轮盘类零件的加工程序时,与轴套类零件相反, 是从大直径端开始顺序向前。 (3)铸锻件 铸锻件毛坯形状与加工后零件形状相似,为加工留有一定的余量。循环去除余 量的方式是刀具轨迹按工件轮廓线运动,逐渐逼近图纸尺寸。 2、确定退刀路线 数控机床加工过程中,为了提高加工效率,刀具从起始点或换刀点运动到接近 工件部位及加工后退回起始点或换刀点是以G00(快速点定位)方式运动的。 考虑退刀路线的原则是:第一、确保安全性,即在退刀过程中不与工件发生碰
数控铣床零件的加工工艺设计毕业设计

数控铣床零件的加工工艺设计毕业设计毕业论文题目数控铣床零件的加工工艺设计学生姓名沈金浩学号11020418 班级 110204专业数控技术专业分院工程技术分院指导教师孙增晖2013 年 9 月 14 日长春职业技术学院毕业论文专用纸目录摘要 ..................................................................... (1)第1章绪论 (1)1.1数控铣床的简介 ........................................................... 2 1.2本课题设计内容 ...........................................................2 第2章零件的数控铣削工艺分析 .............................................. 3 2.1零件图的绘制 ............................................................. 3 2.2零件图的分析 ............................................................. 3 2.3毛坯的选择 ............................................................... 4 2.4数控设备的选择 ........................................................... 4 2.5 零件定位基准及装夹方式的确定.............................................4 2.6加工路线的设计 ........................................................... 5 2.7刀具选择 .................................................................5 2.8切削用量的确定 ........................................................... 6 2.9拟定数控切削加工工序卡 ...................................................7 2.10工序设计 (8)2.11确定编程原点 ............................................................ 8 2.12编辑程序 ................................................................9 第3章操作步骤 ............................................................ 12 总结与致谢 .................................................................13 参考文献 ...................................................................141摘要毕业设计是培养我们实际工作能力的最后一个重要实践性学习环节,他不但是对我们三年来学习与实践的一个很好的总结与考验,也是为以后从事专业技术工作做个强而有力的铺垫。
zword06

浙江工业职业技术学院实习教案项目6 平面零件加工一、实训目的与要求(1) 掌握平面类零件的加工方法。
(2) 学习数控加工中的半径补偿功能。
(3) 学习数控加工编程中的数值计算方法。
(4) 掌握尺寸精度控制方法。
(5) 了解数控铣削加工的基本操作步骤。
二、实训设备及仪器(1)配备华中世纪星(HNC-21M)数控系统的立式铣床一台。
(2)相应的刀具系统及刀量具。
(3)硬铝合金或45#一块(100X100X20)。
三、相关知识讲解1、实训图纸(xx模具厂冲压模具)2、工艺分析该零件主要是简单外轮廓和内轮廓组成,几何轮廓比较简单,但轮廓尺寸精度要求比较高,为IT7-8级,需要粗、半精、精加工完成,并达到表面粗糙度要求。
为了能更好地保证加工精度,铣削方式采用顺铣方式。
同时采用平口钳来装夹工件,工件坐标系设置在工件对称中心轴上。
具体加工步骤如下:(1) 分析零件图,合理安排加工工艺;(2) 编制加工程序(程序学生自己编制,教师负责检查); (3) 安装夹毛坯,伸出平口虎钳钳口10mm 左右;(4) 安装寻边器(或铣刀),确定工件坐标系原点为毛坯上表面中心位置,并设定零点偏置;(5) 安装面铣刀,粗、精铣工件上表面,作为深度方向的测量基准; (6) 安装mm 16 立铣刀并对刀,设定相对应的工件坐标系原点偏置和刀具半径补偿值为8.5;(7)粗铣轮廓四方轮廓、八边形和圆内轮廓,单边余量为0.5mm ; (8)粗铣四方轮廓、八边形和圆内轮廓,调整相应的刀具半径补偿值为8.2; (9)半精加工轮廓凸台,单边余量为0.2mm ;(10)半精加工四方轮廓、八边形和圆内轮廓,调整相应的刀具半径补偿值为修整值;(11)精加工四方轮廓、八边形和圆内轮廓;(12)若外轮廓加工精度达不到加工要求,继续调整刀具半径补偿值,直到满足零件图纸的加工要求; 四、实训内容(1) 根据HNC-21M 数控系统的程序格式,编制图所示的加工程序。
数控铣削加工工艺PPT课件

定中心装夹 a) 用三爪自定心卡盘装夹 b) 用两顶尖装夹 c) 用自定心虎钳装夹
ห้องสมุดไป่ตู้、组合夹具
组合夹具的基本特点是满足标准化、 系列化、 通 用化的要求,具有组合性、 可调性、 柔性、 应急性和 经济性,使用寿命长,能适应产品加工中的周期短、 成本低等要求,比较适合在加工中心上应用。
数控夹具的调整 a) 平移式 b) 回转式 c) 复合式
1—定位支撑 2—钩形压板 3, 7—滚珠丝杠副 4—步进电动机 5, 6—齿轮 8—滑座 9—活动定位销
平移式自调数控夹具
数控夹具还有哪几种? 数控车床上有吗?
5. 专用夹具
l一夹具体 2一压板 3、7一螺母 4、5一垫圈 6一螺栓 8一弹簧 9一定位键 10一菱形销 11一圆柱销
双刃镗刀分类
结构特点不同
整体式(Ⅰ和Ⅱ) 模块式 (Ⅲ和Ⅳ)
工作特点不同 尺寸是否可调
浮动式(Ⅰ) 固定式(Ⅱ,Ⅲ,Ⅳ) 可调式(Ⅰ, Ⅲ,Ⅳ)
不可调式(Ⅱ)
可转位双刃镗刀的特点及适用场合见表4—3。
(2) 镗刀刀头 分为粗镗刀刀头和精镗刀刀头。
粗镗刀刀头
精镗刀刀头
将精镗刀刀头旋转一周,刀头在半径方向 上移动多少?镗孔直径变化多少?
第一节 工件在数控铣床/ 加工中心上的装夹
一、 工件的夹紧
1. 夹紧装置应具备的基本要求
(1) 夹紧过程可靠,不改变工件定位后所占据的正确位置。 (2) 夹紧力的大小适当,既要保证工件在加工过程中其位置 稳定不变, 振动小,又要使工件不会产生过大的夹紧变形。 (3) 操作简单、 方便、 省力、 安全。 (4) 结构性好, 夹紧装置的结构力求简单、 紧凑,以便于制 造和维修。
曲轴的数控加工工艺
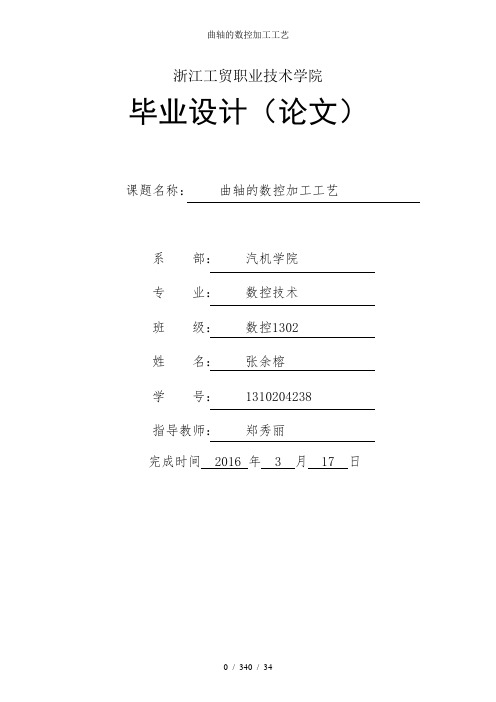
浙江工贸职业技术学院毕业设计(论文)课题名称:曲轴的数控加工工艺系部:汽机学院专业:数控技术班级:数控1302姓名:张余榕学号: 1310204238指导教师:郑秀丽完成时间 2016 年 3 月 17 日目录1、绪论 (1)1.1 引言 (1)1.2 设计内容 (2)2、零件的工艺分析 (2)2.1零件结构工艺性分析 (3)2.2零件技术条件分析 (3)2.3毛坯的选择 (3)2.3.1 毛坯种类选择 (3)2.3.2 毛坯制造方法的选择 (4)3.机加工工艺路线确定 (4)3.1加工方法分析确定 (4)3.2 加工顺序的安排 (4)3.3 定位基准选择 (4)3.4加工阶段的划分 (4)4. 工序的划分 (5)4.1工序的划分 (5)4.2 加工顺序的安排 (5)4.3 确定加工路线 (6)5.曲轴的机械加工工艺过程卡片 (7)6.拟定加工零件的工艺卡片 (10)6.1曲轴数控加工工艺 (10)7. 铣床加工曲轴表面程序 (16)8. 量具的选用 (16)8.1 游标卡尺 (19)8.2 千分尺 (19)总结 (30)参考文献 (31)曲轴的数控加工工艺张余榕汽车与机械工程学院班级:数控1302班摘要:曲轴是汽车发动机的关键零件之一,其性能好坏直接影响到汽车发动机的质量和寿命.曲轴在发动机中承担最大负荷和全部功率,承受着强大的方向不断变化的弯矩及扭矩,同时经受着长时间高速运转的磨损,因此要求曲轴材质具有较高的刚性、疲劳强度和良好的耐磨性能。
发动机曲轴的作用是将活塞的往复直线运动通过连杆转化为旋转运动,从而实现发动机由化学能转变为机械能的输出。
本课题是单拐曲轴的加工工艺的分析。
工艺路线的拟定是工艺规程制订中的关键阶段,是工艺规程制订的总体设计。
所撰写的工艺路线合理与否,不但影响加工质量和生产率,而且影响到工人、设备、工艺装备及生产场地等的合理利用,从而影响生产成本。
所以,本次设计是分析曲轴零件加工技术要求及加工精度后,合理确定毛坯类型,经过查阅相关参考书、手册、图表、标准等技术资料,确定各工序的定位基准、机械加工余量、工序尺寸及公差,最终制定出曲轴零件的加工工序卡片。
《数控铣削加工工艺》教学设计

《数控铣削加工工艺》教学设计摘要本文以数控技术应用专业“数控铣削加工工艺”这一章节的任务驱动法教学为例,以说课的方式,展示该课题的教学设计、教学实施过程、教学效果评价的环节,以及教师的角色变化,用以加深对任务驱动教学法的理解,促进在实际教学中的应用,有一定的理论和实践意义。
关键词工艺任务驱动法教学设计角色变化一、教材分析教材选取数控技术专业的核心课程《数控加工工艺》的第六章。
它采用传统教学理念编写,总体结构合理,但难度较大。
这一章的教学重点是:铣削加工工艺的分析。
难点是:一般零件的铣削加工工艺编制。
二、教学目标知识目标:掌握铣削工艺分析和编制的一般方法。
能力目标:培养学生分析工艺、编制工艺的能力;提高学生利用网络资源和收集整理资料的能力;培养学生与他人沟通协作的能力。
情感目标:通过问题的不断解决,增强他们克服困难的勇气,建立了自信心,树立了健康向上的人生态度。
同时,认识到自己的优势与不足,为今后工作中的自我定位打下了良好的基础。
三、教学理念叶圣陶先生曾经说过:“教任何一门课程,最终目的都在于达到不需要教。
假如学生进入这一境界,能够自己去探索,自己去辨析,自己去历练,不就获得正确的知识和熟练的能力了吗?”所以,我从学生熟悉的生活案例入手,将一些不好理解的知识形象化,创建真实的教学环境,提出真实的任务,将教师传统式的“教”,转变为学生探究式的“学”,直到任务完成。
同时,为每一个学生的思考、探索、创新提供了开放的空间,使学生在不知不觉中构建起了属于自己的知识体系和经验体系。
四、教法、学法为了更好地体现以上教学理念,我以任务驱动法为主,设计了温故复习和提出任务(2学时)、讨论实施和综合评价(8学时)、课堂总结(2学时)这五个教学阶段,并将创设情境、案例分析、讨论参观、合作学习、作业练习等教法学法贯穿于整个教学过程中。
五、过程与评价首先,我根据学生课余时间复习不积极这一特点,用10分钟这一比较长的时间,通过学生对“妈妈和厨师都做西红柿炒鸡蛋,为什么会有差别?”“妈妈和厨师同时为你1个人做饭谁做得快呢?如果换成10人、100人甚至1000人呢?情况是否有变化?”“为什么给1000人做饭时妈妈会比厨师慢很多?”3个生活案例的回答帮助学生回忆复习了“什么是工艺?”“什么是生产纲领?”“工序划分原则有哪些?”。
课题数控铣削加工工艺浙江工业职业技术学院

浙江工业职业技术学院课题3 数控铣削加工工艺数控铣削加工工艺分析是数控铣削加工的一项重要工作,工艺分析的合理与否,直接影响到零件的加工质量,生产效率和加工成本。
在编制数控程序时,根据零件图纸要求首先应该考虑的几个问题:3.1 零件图样的工艺分析在数控工艺分析时,首先要对零件图样进行工艺分析,分析零件各加工部位的结构工艺性是否符合数控加工的特点,其主要内容包括:1)零件图样尺寸标注应符合编程的方便在数控加工图上,宜采用以同一基准引注尺寸或直接给出坐标尺寸。
这种标注方法,既便于编程,也便于协调设计基准、工艺基准、检测基准与编................程零点...的设置和计算。
2)零件轮廓结构的几何元素条件应充分在编程时要对构成零件轮廓的所有几何元素进行定义。
在分析零件图时,要分析各种几何元素的条件是否充分,如果不充分,则无法对被加工的零件进行编程或造型。
3)零件所要求的加工精度、尺寸公差应能否得到保证虽然数控机床加工精度很高,但对一些特殊情况,例如薄壁零件的加工,由于薄壁件的刚性较差,加工时产生的切削力及薄壁的弹性退让极易产生切削面的振动,使得薄壁厚度尺寸公差难以保证,其表面粗糙度也随之增大,根据实践经验,对于面积较大的薄壁,当其厚度小于3mm时,应在工艺上充分重视这一问题。
4)零件内轮廓和外形轮廓的几何类型和尺寸是否统一在数控编程,如果零件的内轮廓与外轮廓几何类型相同或相似,考虑是否可以编在同一个程序,尽可能减少刀具规格和换刀次数,以减少辅助时间,提高加工效率。
需要注意的是,刀具的直径常常受内轮廓圆弧半径R限制。
5)零件的工艺结构设计能否采用较大直径的刀具进行加工采用较大直径铣刀来加工,可以减少刀具的走刀次数,提高刀具的刚性系统,不但加工效率得到提高,而且工件表面和底面的加工质量也相应的得到提高。
6)零件铣削面的槽底圆角半径或底板与缘板相交处的圆角半径r不宜太大图(3-1)由于铣刀与铣削平面接触的最大直径d=D-2r,其中D为铣刀直径。
第二届数控技能竞赛数控铣(加工中心)理论试题

数控铣 / 加工中心理论竞赛试卷浙江工业职业技术学院注意事项1.请首先按要求在试卷的标封处填写你的姓名、学号和学校名称。
2.请仔细阅读各种题目的回答要求,在规定的位置填写你的答案。
3.不要在试卷上做任何标记,不要在标封区填写无关内容。
项目一二三四五六总分总分人得分得分评分人一、选择题:(以下四个备选答案中其中一个为正确答案,请将其代号填入括号内,每题1分,满分20分)1. 粗糙度的评定参数R a的名称是()。
(A)轮廓算术平均偏差(B)轮廓几何平均偏差(C)微观不平度十点平均高度(D)微观不平度五点平均高度2.容易引刀具积屑瘤的工件材料是()。
(A)低碳钢(B)中碳钢(C)高碳钢(D)铸铁3.金属表面渗碳后必须进行()才能起到改进材料性能的作用。
(A)退火(B)调质(C)淬火和回火(D)正火4.三相异步电机启动时的()。
(A) 电压较高 (B) 电流较大 (C) 电流较小 (D) 噪音较大5.内径大小为35的滚动轴承的内径代号为()。
(A)35 (B)3.5 (C)07 (D)0356.低压断路器通常用于(),又称自动空气开关。
(A)电机的启动和停止(B) 电机的过载保护(C) 进给运动的控制(D) 机床电源的引入7.同步带传动综合了()传动的优点。
(A)齿轮和链轮(B)链轮和凸轮(C)凸轮和三角带(D)三角带和齿轮8.当前数控铣床广泛使用性能优越的进给驱动电机类型为()电机。
(A)直流(B)交流伺服(C)交流变频(D)步进9.一般来说,容量在()千瓦以下的三相异步电机可以直接启动。
(A) 0.1 (B) 1 (C)10 (D)10010.钢板在外力作用下弯形时,凸面内层材料受到()。
(A)压缩(B)拉伸(C)延展(D)剪切11.数控机床刀具路径图形模拟页面功能键的英文缩写是()。
(A)ALARM (B) OFSET (C)RESET (D)GRAPH12.在程序中光标指定位置删除字符或数字的功能键的英文缩写是()。
《数控加工技术》教学大纲(数控铣削加工)
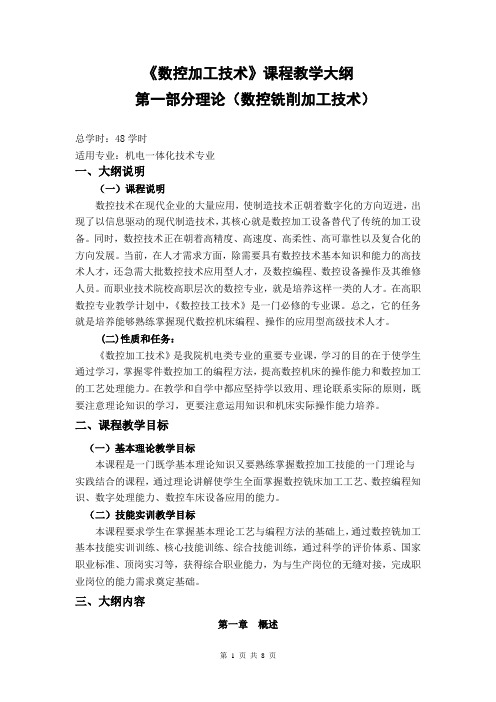
《数控加工技术》课程教学大纲第一部分理论(数控铣削加工技术)总学时:48学时适用专业:机电一体化技术专业一、大纲说明(一)课程说明数控技术在现代企业的大量应用,使制造技术正朝着数字化的方向迈进,出现了以信息驱动的现代制造技术,其核心就是数控加工设备替代了传统的加工设备。
同时,数控技术正在朝着高精度、高速度、高柔性、高可靠性以及复合化的方向发展。
当前,在人才需求方面,除需要具有数控技术基本知识和能力的高技术人才,还急需大批数控技术应用型人才,及数控编程、数控设备操作及其维修人员。
而职业技术院校高职层次的数控专业,就是培养这样一类的人才。
在高职数控专业教学计划中,《数控技工技术》是一门必修的专业课。
总之,它的任务就是培养能够熟练掌握现代数控机床编程、操作的应用型高级技术人才。
(二)性质和任务:《数控加工技术》是我院机电类专业的重要专业课,学习的目的在于使学生通过学习,掌握零件数控加工的编程方法,提高数控机床的操作能力和数控加工的工艺处理能力。
在教学和自学中都应坚持学以致用、理论联系实际的原则,既要注意理论知识的学习,更要注意运用知识和机床实际操作能力培养。
二、课程教学目标(一)基本理论教学目标本课程是一门既学基本理论知识又要熟练掌握数控加工技能的一门理论与实践结合的课程,通过理论讲解使学生全面掌握数控铣床加工工艺、数控编程知识、数字处理能力、数控车床设备应用的能力。
(二)技能实训教学目标本课程要求学生在掌握基本理论工艺与编程方法的基础上,通过数控铣加工基本技能实训训练、核心技能训练、综合技能训练,通过科学的评价体系、国家职业标准、顶岗实习等,获得综合职业能力,为与生产岗位的无缝对接,完成职业岗位的能力需求奠定基础。
三、大纲内容第一章概述教学目的:通过学习使学生了解数控机床的基本知识。
掌握数控机床的概念,掌握数控机床的组成及各部分的作用,掌握按伺服系统特点分类的方法,了解其它分类方法,了解数控机床的使用、加工特点。
数控铣削加工工艺及对刀操作PPT课件

进给速度的选择同样重要,过快或过 慢的进给速度都可能导致加工质量下 降或损坏刀具。
切削深度的选择
切削深度
根据工件材料、铣刀直径和加工要求等参数,合理选择切削深度,以确保切削 效率和加工质量。
总结
切削深度的选择对切削效率和加工质量均有影响,过大的切削深度可能导致刀 具损坏或加工质量下降。
刀具的选择与使用
05
数控铣削加工的未来发展与挑战
数控铣削加工技术的发展趋势
80%
智能化
随着人工智能和机器学习技术的 不断发展,数控铣削加工将更加 智能化,能够实现自适应加工和 智能优化。
100%
高效化
为了提高加工效率和降低成本, 数控铣削加工将不断优化切削参 数和加工路径,实现高效、高精 度的加工。
80%
柔性化
随着个性化需求的增加,数控铣 削加工将更加柔性化,能够快速 适应不同工件和加工需求的调整 。
数控铣削加工面临的挑战与问题
加工精度要求高
随着产品质量的不断提高,对 数控铣削加工的精度要求也越 来越高,如何保证高精度加工 是当前面临的重要问题。
切削参数优化
切削参数的优化是提高数控铣 削加工效率和加工质量的关键 ,但如何实现切削参数的合理 匹配和优化仍是一个挑战。
引入智能化技术
利用人工智能和机器学习技术,实现 加工过程的自适应控制和智能优化, 提高加工效率和精度。
THANK YOU
感谢聆听
详细描述
数控铣削加工是指利用数控机床进行铣削加工的一种技术,通过 计算机控制机床的运动和切削参数,实现高精度、高效率、高柔 性的加工。相比于传统铣削加工,数控铣削加工具有更高的加工 精度和更广泛的加工范围,能够满足各种复杂零件的加工需求。
- 1、下载文档前请自行甄别文档内容的完整性,平台不提供额外的编辑、内容补充、找答案等附加服务。
- 2、"仅部分预览"的文档,不可在线预览部分如存在完整性等问题,可反馈申请退款(可完整预览的文档不适用该条件!)。
- 3、如文档侵犯您的权益,请联系客服反馈,我们会尽快为您处理(人工客服工作时间:9:00-18:30)。
浙江工业职业技术学院课题3 数控铣削加工工艺数控铣削加工工艺分析是数控铣削加工的一项重要工作,工艺分析的合理与否,直接影响到零件的加工质量,生产效率和加工成本。
在编制数控程序时,根据零件图纸要求首先应该考虑的几个问题:3.1 零件图样的工艺分析在数控工艺分析时,首先要对零件图样进行工艺分析,分析零件各加工部位的结构工艺性是否符合数控加工的特点,其主要内容包括:1)零件图样尺寸标注应符合编程的方便在数控加工图上,宜采用以同一基准引注尺寸或直接给出坐标尺寸。
这种标注方法,既便于编程,也便于协调设计基准、工艺基准、检测基准与编................程零点...的设置和计算。
2)零件轮廓结构的几何元素条件应充分在编程时要对构成零件轮廓的所有几何元素进行定义。
在分析零件图时,要分析各种几何元素的条件是否充分,如果不充分,则无法对被加工的零件进行编程或造型。
3)零件所要求的加工精度、尺寸公差应能否得到保证虽然数控机床加工精度很高,但对一些特殊情况,例如薄壁零件的加工,由于薄壁件的刚性较差,加工时产生的切削力及薄壁的弹性退让极易产生切削面的振动,使得薄壁厚度尺寸公差难以保证,其表面粗糙度也随之增大,根据实践经验,对于面积较大的薄壁,当其厚度小于3mm时,应在工艺上充分重视这一问题。
4)零件内轮廓和外形轮廓的几何类型和尺寸是否统一在数控编程,如果零件的内轮廓与外轮廓几何类型相同或相似,考虑是否可以编在同一个程序,尽可能减少刀具规格和换刀次数,以减少辅助时间,提高加工效率。
需要注意的是,刀具的直径常常受内轮廓圆弧半径R限制。
5)零件的工艺结构设计能否采用较大直径的刀具进行加工采用较大直径铣刀来加工,可以减少刀具的走刀次数,提高刀具的刚性系统,不但加工效率得到提高,而且工件表面和底面的加工质量也相应的得到提高。
6)零件铣削面的槽底圆角半径或底板与缘板相交处的圆角半径r不宜太大图(3-1)由于铣刀与铣削平面接触的最大直径d=D-2r,其中D为铣刀直径。
当D 一定时,圆角半径r(如图(3-1)所示)越大,铣刀端刃铣削平面的能力越差,效率也就越低,工艺性也越差。
当r大到一定程度时甚至必须用球头铣刀加工,这是应当避免的。
当D越大而r越小,铣刀端刃铣削平面的面积就越大,加工平面的能力越强,铣削工艺性当然也越好。
有时,铣削的底面面积较大,底部圆弧r也较大时,可以用两把r不同的铣刀分两次进行切削。
5)保证基准统一原则若零件在铣削完一面后再重新安装铣削面的另一面,由于基准不统一,往往会因为零件重新安装而接不好刀,加工结束后正反两面上的轮廓位置及尺寸的不协调。
因此,尽量利用零件本身具有的合适的孔或以零件轮廓的基准边或专门设置工艺孔(如在毛坯上增加工艺凸台或在后续工序要去除余量上设置基准孔)等作为定位基准,保证两次装夹加工后相对位置的准确性。
6)考虑零件的变形情况当零件在数控铣削过程中有变形情况时,不但影响零件的加工质量,有时,还会出现蹦刀的现象。
这时就应该考虑铣削的加工工艺问题,尽可能把粗、精加工分开或采用对称去余量的方法。
当然也可以采用热处理的方法来解决。
3.2 加工方法选择及加工方案的确定1)加工方法选择根据零件的种类和加工内容选择合适的数控机床和加工方法。
(1)机床的选择平面轮廓零件的轮廓多由直线、圆弧和曲线组成,一般在两坐标联动的数控铣床上加工;具有三维曲面轮廓的零件,多采用三坐标或三坐标以上联动的数控铣床。
(2)粗、精加工的选择经粗铣的平面,尺寸精度可达IT11~IT13级(指两平面之间的尺寸),表面粗糙度(或Ra值)可达6.3μm~25μm。
经粗、精铣的平面,尺寸精度可达IT8~IT10级,表面粗糙度Ra值可达1.6μm~6.3μm。
(3)孔的加工方法选择在数控机床上孔加工的方法一般有钻削、扩削、铰削和镗削等。
孔加工方案的确定,应根据加工孔的加工要求,尺寸、具体的生产条件,批量的大小以及毛坯上有无预加孔合理选用。
1)加工精度为IT9级,当孔径小于10mm时,可采用钻→铰加工方案;当孔径小于30mm时,可采用钻→扩加工方案;当孔径大于30mm时,可采用钻→镗加工方案。
工件材料为淬火钢以外的金属。
2)加工精度为IT8级,当孔径小于20mm时,可采用钻→铰加工方案;当孔径小于20mm时,可采用钻→扩→铰加工方案,同时也可以采用最终工序为精镗的方案。
此方案适用于加工除工件材料为淬火钢以外的金属,3)加工精度为IT7级,当孔径小于12mm时,可采用钻→粗铰→精铰加工方案;当孔径在12mm至60mm之间时,可采用钻→扩→粗铰→精铰加工方案。
对于加工毛坯己铸出或锻出毛坯孔的孔加工,一般采用粗镗→半精镗→孔口倒角一精镗加工方案。
4)孔精度要求较低且孔径较大时,可采用立铣刀粗铣→精铣加工方案。
有空刀槽时可用锯片铣刀在半精镗之后、精镗之前铣削完成,也可用镗刀进行单刃螳削,但单刃镗削效率低。
5)有同轴度要求的小孔,须采用饶平端面→打中心孔→钻→半精镗→孔口倒角→精镗(或铰)加工方案。
为提高孔的位置精度,在钻孔工步前须安排锪平端面和打中心孔工步。
孔口倒角安排在半精加工之后、精加工之前,以防孔内产生毛刺。
(4)螺纹的加工螺纹的加工根据孔径大小而定,一般情况下,直径在M5mm~M20mm之间的螺纹,通常采用攻螺纹的方法加工。
直径在M6mm以下的螺纹,在数控机床上完成底孔加工后,通过其他手段来完成攻螺纹。
因为在数控机床上攻螺纹不能随机控制加工状态,小直径丝锥容易拆断。
直径在M25mm以上的螺纹,可采用镗刀片镗削加工或采用圆弧插补(G02或G03)指令来完成。
加上方法的选择原则:在保证加工表面精度和表面粗糙度要求的前提下,尽可能提高加工效率。
由于获得同一级精度及表面粗糙度的加工方法一般有许多,因而在实际选择时,要结合零件的形状、尺寸和热处理要求全面考虑。
此外,还应考虑生产率和经济性的要求,以及工厂的生产设备等实际情况。
2)加工方案确定确定加工方案时,首先应根据主要表面的尺寸精度和表面粗糙度的要求,初步确定为达到这些要求所需要的加工方法,即精加工的方法,再确定从毛坯到最终成形的加工方案。
在加工过程中,工件按表面轮廓可分为平面类和曲面类零件,其中平面类零件中的斜面轮廓又分为有固定斜角和变斜角的外形轮廓面。
外形轮廓面的加工,若单纯从技术上考虑,最好的加工方案是采用多坐标联动的数控机床,这样不但生产效率高,而且加工质量好。
但由于一般中小企业无力购买这种价格昂贵、生产费用高的机床,因此应考虑采用2.5轴控制和3轴控制机床加工。
2.5轴控制和3轴控制机床上加工外形轮廓面,通常采用球头铣刀,轮廓面的加工精度主要通过控制走刀步长和加工带宽度来保证。
加工精度越高,走刀步长和加工带宽度越小,编程效率和加工效率越低。
如图(3-2)所示,球头刀半径为R ,零件曲面上曲率半径为ρ,行距为S,加工后曲面表面残留高度为H。
则有:ρρ±•-=R H R H S )2(2式中,当被加工零件的曲面在ab 段内是凸的时候取“+”号,是凹的时候取“-”号。
图(3-2 )行距的计算图3.3 工艺设计1)工序的划分在数控机床上加工零件,工序应尽量集中,一次装夹....应尽可能完成大部分工序。
数控加工工序的划分有下列方法:(1)按先面后孔的原则划分工序在加工有面和孔的零件时,为提高孔的加工精度,应先加工面,后加工孔这一原则。
一方面可以用加工过的平面作为基准;另一方面可以提高孔的加工精度。
(2)按所用刀具划分工序在数控机床上,为了减少换刀次数,缩短辅助时间,经常按集中工序的原则加工零件,即用同一把刀加工完相应的零件的全部加工余量后,再用另一把刀加工其他部位的余量。
(3)按粗、精加工划分工序对于精度要求较高且易发生加工变形的零件,应将粗、精加工分开,这样可以使粗加工引起的各种变形得到恢复,同时充分发挥粗加工的效率。
2)加工余量的选择加工余量指毛坯实体尺寸与零件(图纸)尺寸之差。
加工余量的大小对零件的加工质量和制造的经济性有较大的影响。
余量过大会浪费原材料及机械加工工时,增加机床、刀具及能源的消耗;余量过小则不能消除上道工序留下的各种误差、表面缺陷和本工序的装夹误差,容易造成废品。
因此,应根据影响余量的因素合理地确定加工余量。
零件加工通常要经过粗加工、半精加工、精加工才能达到最终要求。
因此,零件总的加工余量等于中间工序加工余量之和。
(1)工序间加工余量的选择原则采用最小加工余量原则,以求缩短加工时间,降低零件的加工费用。
应有充分的加工余量,特别是最后的工序。
(2)在选择加工余量时,还应考虑的情况由于零件的大小不同,切削力、内应力引起的变形也会有差异,工件大,变形增加,加工余量相应地应大一些。
零件热处理时引起变形,应适当增大加工余量。
加工方法、装夹方式和工艺装备的刚性可能引起的零件变形,过大的加工余量会由于切削力增大引起零件的变形。
(3)确定加工余量的方法查表法:这种方法是根据各工厂的生产实践和实验研究积累的数据,先制成各种表格,再汇集成手册。
确定加工余量时查阅这些手册,再结合工厂的实际情况进行适当修改后确定。
目前我国各工厂普遍采用查表法。
经验估算法:这种方法是根据工艺编制人员的实际经验确定加工余量。
一般情况下,为了防止因余量过小而产生废品,经验估算法的数值总是偏大。
经验估算法常用于单件小批量生产。
分析计算法:这种方法是根据一定的试验资料数据和加工余量计算公式,分析影响加工余量的各项因素,并计算确定加工余量。
这种方法比较合理,但必须有比较全面和可靠的试验资料数据。
目前,只在材料十分贵重,以及少数大量生产的工厂采用。
3)进给路线的确定在数控加工中,刀具刀位点相对于工件运动的轨迹称为加工路线,它是编程的依据,直接影响加工质量和效率。
在确定加工路线时要考虑下面几点:(1)证零件的加工精度和表面质量,且效率要高。
(2)尽可能加工路线最短,减少空行程时间和换刀次数,提高生产率。
(3) 减少零件的变形;(4)尽量使数值点计算方便,缩短编程工作时间。
(5)合理选择铣削方式,以提高零件的加工质量。
(6)合理选取刀具的起刀点、切入和切出点及刀具的切入和切出方式,保证刀具切入和切出的平稳性。
(7)位置精度要求高的孔系零件的加工应避免机床反向间隙的带入而影响孔的位置精度;(8)复杂曲面零件的加工应根据零件的实际形状、精度要求、加工效率等多种因素来确定是行切还是环切,是等距切削还是等高切削的加工路线等。
(9)保证加工过程的安全性,避免刀具与非加工面的干涉。
3.4 零件安装与夹具选择1)尽量选择通用夹具、组合夹具,能使零件一次装夹中完成全部加工面的加工,并尽可能使零件的定位基准与设计基准重合,以减少定位误差。
一般在模具加工中采用平口虎钳或压板为多。
2)装夹迅速方便及定位准确,以减少辅助时间。