转炉一次除尘风机高压变频改造
关于炼钢厂一次除尘风机1800KW高压电机变频改造

4.3 除尘风机改造后变频运行预计功率 液偶调速器和变频调速器在效率上有很大的不同,变频调速器的效率要远 远高于液偶调速器的效率,一般在 96%以上。 出钢水时: 风机转速为 800r/min,液偶调速器的转速比为 i1 800/1488 0.5376 ,根据 液偶调速器的转差损耗公式得
P i12 i13 / ie3 P额 0.53762 0.53763 / 0.973 1800 263.49kW
1.引
言
某炼钢厂 1800kW 一次除尘风机原来满负荷运行,电机与风机之间通过液力 耦合器连接,根据工艺的需要通过液力耦合器来调节风机的转速。在炼一炉钢 的工艺流程中对风机转速的要求为:炼一炉钢的总时间为 40 分钟,前 15 分钟 风机转速为 1350r/min,然后 5 分钟为 800r/min,再 3 分钟为 1350r/min,再 17 分钟为 800r/min,然后依次循环。 此炼钢工艺中一次除尘风机在液力耦合器调速下转差损耗大、效率低、调 速精度低、转速随负载波动大,难以保证稳定除尘。如果使用高压变频器调速 的话,不但解决了上述问题,而且产生很大的节能效果。
功率单元
N
B1 C1
A1
A2
B2
C2
A3
B3
C3A4来自B4C4AC 10kV 电网
A5
B5
C5
A6
B6
C6
A7
B7
C7
A8
B8
C8
移相变压器 10kV电机
M
图 2 系统主功率拓扑框图 串联 H 桥多电平逆变器,每个功率单元的开关频率可以较低,但中高压变频 装置输出侧电压的等效开关频率却较高,大大减小了中高压变频装置输出的高 次谐波。 控制系统根据设计的载波 PWM 控制算法,适时控制各功率单元的逆变器输 出,得到频率和幅值均可调的交流输出电压,实现电动机的变频调速控制。 3 方案选型 3.1 电机参数: 电机型号:YB800S2-4 额定功率:1800kW 额定电压:10000V 额定电流:128.7A 额定转速:1488r/min 功率因数:0.85 电机接法:Y 负载:除尘风机 3.2 中高压变频装置选型 交流电动机采用变频调速时,必须使电机的定子反电势 E1 与电压频率 f1 之比 E1/f1 为常数,才能保持电机气隙磁通不变,使电机调速时有相同的输出 力矩。在变频调速下,由于其可以从零速起动,使起动电流远远小于电动机全 压下的起动电流。 针对此项目电机变频器选型为: ATMV-F2250-10/10。 其中 IGBT 选用德国英飞凌,电容器为 EPCOS,散热风机为 EMB,设备的主要元器件选用国 内外知名品牌。 3.3 改造方案的选定 如不考虑改造时间,此项目改造有三种改造方案:第一种,拆除液力耦合 器,电机前移对轴直接联接到除尘风机轴上,电机基座重新制作;第二种,不 拆除液力耦合器,把液力耦合器的转速比调到最大,高压变频器驱动电机拖动 液力耦合器;第三种,拆除液力耦合器,电机与除尘风机之间采用联轴器联接。 由于用户方计划改造时间短,因第一种方案改造工期长,成本高,首先被排除;
转炉一次除尘风机控制系统改造研究与应用
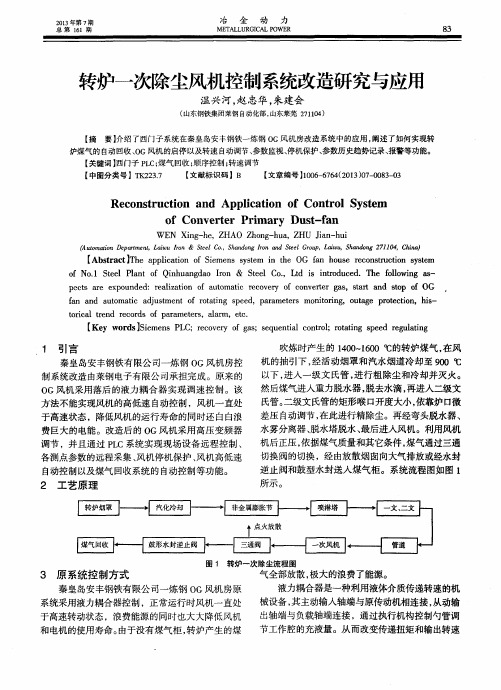
各测点参数的远程采集 、 风机停机保护 、 风机高低速 自动控制以及煤气 回收系统的 自动控制等功能。
2 工艺 原 理
图1 转 炉 一次 除 尘 流 程 图
3 原 系统控制方式
秦皇岛安丰钢铁有限公司一炼钢 O G风机房原 系统采用液力耦合器控制 ,正常运行时风机一直处 于高速转动状态 ,浪费能源的同时也大大降低风机 和电机的使用寿命。 由于没有煤气柜 , 转炉产生的煤
t o r i c a l t r e n d r e c o r d s o f p a r a me t e r s ,a l a r m,e t c .
【 Ke y w o r d s 】 S i e me n s P L C ;r e c o v e r y o f g a s ; s e q u e n t i a l c o n t r o l ;r o t a t i n g s p e e d r e g u l a t i n g
2 0 1 3 年第 7 期
总第 1 6 1期
冶 金 动 力
ME TAL L URG I C AL P OW E R
转炉一次除尘风机控制 系统改造研 究与应用
温兴 河 , 赵 忠华 , 朱建会
( 山东钢铁集 团莱钢 自动化部 , 山东莱芜 2 7 1 1 0 4)
【 摘
要】 介绍 了西门子系统在秦皇 岛安 丰钢铁一 炼钢 O G风机房改造系统 中的应 用 , 阐述 了如何 实现转
炉煤气 的自动回收、 O G风机的启停 以及转 速 自动调节 、 参数监视 、 停机保护 、 参数历史趋 势记 录、 报警等功能。
【 关键词】 西门子 P L C ; 煤气回收; 顺序控制; 转速调节
高压变频器在100t转炉一次除尘主风机中的应用

式, 将 同一 相 的所 有功率 单元 串联在 一起 . 便 形成 了
5 9
www. c h i n a c a a a . c o m l 自动 化 应 用
变 频 节 能 及 软 起 动 系 统
一
个星型连接 的三相高压 电源 , 驱 动电动 机运行 。
变 频 器 通 过 MO D — B U S与 除 尘 主 P L C通 信 . 除 尘 P L C与 转 炉 氧 枪 倾 动 P L C之 间 通 过 以 太 网 实 现 数 据 交换和信 号采 集 . 通 过 对 转 炉 炉 况 的判 断 . 实 现 对 风 机 的 自动 调 速 控 制 。根据 炉前 冶炼 模式 ( 炼 钢 渣 ) 、 转 炉倾 动 角度 和 氧枪 高 度 。 来 建立 程 序 逻辑 关 系 在 上位
炼十余分钟后 . 操枪人员提枪 . 风机 自动进入 “ 提枪降
速” 档位 。 频率 以 3 0 H z 运行 : 如 果 点吹 。 程 序 判 断 抢
位. 会再 次升速至 3 5 H z “ 点吹升 速” 档位 . 点吹结 束提
枪 后 会 再 次 自动 降 速 至 “ 提枪 降速 ” 位: 当 转 炉 角 度
功 率 单 元 是 组 成 高 压 变 频 器 的最 小 单 位 。功 率 单 元 的基本拓 扑 为交一 直一 交 三 相 整 流/ 单 相 逆变 电路 . 功率 单元 串联后 得到 的是阶梯 正弦 的 P WM 波 形 , 波 形 正 弦度 好 . d u / d t 小. 可 以减 少 对 电机 和 电缆 的绝 缘 损 坏. 无需 输 出滤 波 器 就 可 以使 输 出 电 缆 长 度 很 长 , 电 动
荣信 R H V C高压变频器的主电路如 图 1 所示 具 有相 同标号 的 3组 副边绕组 . 分别 向 同一 功率柜 ( 同
除尘风机的高压变频节能改造

除尘风机的高压变频节能改造摘要:除尘风机在目前的生产实践中发挥着重要的作用,所以对除尘风机的具体应用进行分析和讨论有显著意义。
综合研究现阶段的除尘风机可知其在应用的过程中存在着几个方面的显著弊端,比如高能耗,该问题的存在降低了除尘风机在实践中的应用价值,所以要想显著提升除尘风机的应用效果,解决能耗问题势在必行。
通过变频控制的方式对除尘风机的运行状态进行控制,这对于其节能而言意义显著,所以在实践中,针对节能目标对其进行高压变频改造意义显著。
文章对除尘风机的高压变频节能改造进行分析,旨在为实践提供帮助。
关键词:除尘风机;高压变频;节能改造除尘风机在实践中的利用呈现出了显著价值,所以基于除尘风机的应用实践对其做综合研究,明确除尘风机应用过程中存在的问题并及时的进行问题改进,这样,除尘风机的现实利用效果会显著提升。
就目前掌握的资料来看,除尘风机在具体利用中存在的显著弊端是能耗高,该问题严重削弱了除尘风机的实际应用价值,使其应用效益大打折扣,所以出于除尘风机的高效利用,同时要配合目前的绿色和节能生产,对除尘风机进行节能改造有突出的现实价值。
1.除尘风机节能改造的必要性对现阶段的除尘风机节能改造进行具体分析可知其主要基于两方面的必要。
首先是除尘风机的节能改造出于企业生产成本控制的必要。
为了实现经济和环境的协调可持续发展,国家对生产制造的环境排放标准进行了严格制定,所以在生产实践中,不管是生产过程还是最后的废弃物排放均需要达到相应的标准。
除尘风机能够对生产过程进行净化,从而使生产环境的整体表现更加的突出。
在实践中,除尘风机的运行需要能量支撑,一般为电能。
在一般情况下,除尘风机的运行模式、功率是固定的,所以其运行不会受到除尘需要的具体影响,这种情况会导致两方面问题:1)除尘要求比较高的时候风机达不到预期的效果。
2)除尘要求比较低的时候风机存在着空转的问题。
这两种问题的存在均会导致企业自身的成本增加,所以在实践中,基于成本控制目标强调节能改造意义显著。
除尘风机的变频改造

除尘风机的变频改造一、冶金钢铁行业的基本情况冶金行业中电机应用主要是轧钢等机械的生产工艺传动和风机水泵的传动,设备量大,能源浪费极大。
随着冶金工业的产品结构调整和冶金生产的环保要求,冶金工业将建大量新建轧钢生产线,并大量应用除尘风机和冷却泵。
二、冶金行业电机系统运行现状及节能潜力钢铁生产流程的电机系统大体分两类:生产机械的动力驱动;供/排水泵、鼓风机及除尘风机1.生产机械的动力驱动:例如轧钢传动,恒转矩负载,工艺要求调速传动的,大都采用直流传动或交流调速传动。
如采用变频调速替代直流调速,不仅有可观的节电效果,还会因生产效率的提高,维修费用的降低等原因而带来很大的经济效益。
2.供/排水泵、鼓风机和除尘风机:它们在钢铁生产流程中大量采用,常规设计为不停机运行,流量过剩时采用流体循环或放空的耗能方法。
如果采用“ACI”变频节电器,不但节电效果达到30%以上,而且可采用闭环控制系统,进行自动跟踪、调速,无须人工操作,这样既节能又省工,并大大提高其设备之功效,增加经济效益。
三、案例分析1.控制对象:6000V、320KW电动机2.控制目的:根据工艺要求及特点,采用变频调速装置对电机调速,保证达到工艺的前提下,实现节能降耗的目的。
3.控制方案:要求根据烟尘量的大小,实现对电机转速大小的控制。
根据工艺要求的设计,控制系统采用可模拟输入输出的PLC与变频器的多步相结合,控制风机高速、中速、低速(或多步速)运行,并能实现风机在全范围内的调速、检测、监测、控制,变频器运行采用“闭环”和“开环”两种方式,并可互相切换。
4.控制特点:采用PLC控制与变频调节,可使系统满足调速方便,启动电流小,运行平稳,自动调节加料吹炼、出钢、倒渣、补炉等不同工艺时的电机转速。
这样,损耗减少,节能显著,工作安全、可靠。
5.控制要点:考虑到系统对于炼钢生产的特殊重要性,保留了原工频回路,与变频回路互锁控制,并加以完善,作为变频故障的应急措施,尽快恢复生产,实现“工频”“变频”两种运行状态的方便切换。
石家庄钢铁厂除尘系统高压变频改造节能分析与技术方案

石家庄钢铁厂除尘系统高压变频改造节能分析与技术方案首先,高压变频技术改造可以提高系统的运行效率。
传统的除尘系统中,除尘风机使用的是恒流输出方式,不能根据不同工况的需求来调节风量。
而高压变频技术可以实现风量的自动调节,根据炉排产生的烟尘和颗粒物的情况来调整风机的运转频率和转速,使其在适当的风速下运行,提高了除尘效率。
高压变频技术还可以通过改变风扇的工作频率来精确控制风量,使其与系统的需求匹配,避免能量的浪费。
其次,高压变频技术改造可以降低系统的能耗。
由于石家庄钢铁厂的除尘系统属于中压风机,风机的能耗通常较高。
采用高压变频技术可以实现风机的无级变速,避免了传统的多级调速方式,减少了能量的损耗。
高压变频技术还可以根据炉排产生的烟尘和颗粒物的情况实时调整风机的运行状态,避免了因为工况变化而导致的能耗增加。
最后,高压变频技术改造还可以提高系统的可靠性和稳定性。
传统的除尘系统中,由于恒流输出无法根据工况变化来调节风量,容易出现运行不稳定的情况。
而高压变频技术可以根据需求实时调整风机的运转频率和转速,使其保持恒定的风速,提高了系统的稳定性。
此外,高压变频技术还具有过载保护功能,可以避免因为外界因素导致的设备过载,提高了系统的可靠性。
针对石家庄钢铁厂的具体情况,推荐以下高压变频改造方案。
首先,需要选用适合的高压变频器来实现风机的变频调速。
建议选择具备较大功率范围和多种保护功能的高压变频器。
通过对风机的实时监测和数据分析,根据工况要求来调整风机的运行参数,实现风量的精确控制。
其次,需要对除尘系统的控制系统进行改造,增加高压变频器的控制模块。
通过与原有控制系统的数据交互和整合,实现对风机的远程监测和控制。
最后,应该对除尘系统的传感器和监测仪表进行升级。
选用高精度的传感器和监测仪表,对炉排产生的烟尘和颗粒物进行实时监测,反馈给控制系统,实现对风机运行状态的准确控制。
通过对石家庄钢铁厂除尘系统的高压变频改造,可以提高系统的运行效率,降低能耗,提高系统的可靠性和稳定性,实现节能减排的目标。
【技术前沿】高压变频器在转炉一次除尘风机上的研究与应用

【技术前沿】高压变频器在转炉一次除尘风机上的研究与应用高压变频器具有调速范围广、调速精度高、系统可靠性高等优点,在转炉一次除尘风机系统中得到了广泛的应用。
该文对高压变频器的组成、控制方式、性能及在转炉一次除尘风机中的应用情况进行了阐述。
1前言炼钢转炉一次除尘风机是烟气净化除尘及煤气回收的关键设备。
转炉吹炼过程中产生的烟气经汽化冷却烟道、溢流文氏管、可调喉口文氏管、重力除尘器、弯头脱水器,再由一次风机牵引从三通阀、水封逆止阀进入煤气柜实现煤气回收。
一旦除尘风机不能正常运行,不但影响生产造成巨大经济损失,还威胁现场人员安全,所以转炉一次除尘风机的正常运行显得尤为重要。
2除尘风机的工艺要求莱钢银前120t转炉一次除尘采用的是半干法除尘工艺(EC+OG),另有一套干法除尘器作为备用。
OG法一次除尘风机采用的是变频控制方式,除尘风机电动机型号为YB710-2,额定功率1600kW,额定电压3000V,额定电流366A,cosϕ=0.89,额定转速2985r/min。
变频器型号为ABBACS1000,额定功率为1800kW,输岀电压0-3300V,输岀电流0-417A,输出频率0-50Hz。
生产中风机控制分为两个阶段,首先是加废钢→测温取→样岀渣→出钢→溅渣→等待为风机低速阶段,此时风机转速为650r/min,频率为11Hz。
其次是降枪吹炼,转炉熔池反应剧烈,此时为风机高速阶段,转速为2500r/min,频率为42Hz。
利用转炉倾动的角度,来控制风机电动机自动升速和降速。
当转炉倾动角度在兑铁位时开始起高速,升速时间为60s,转速2500r/min,高速运行18min左右。
当转炉角度不在零位时,风机电动机自动降低转速,降速时间为60s,转速650r/min,低速运行22min左右。
同时利用转炉零位对其给定点进行复位。
转炉设置“手动/自动'切换功能,平时可根据生产情况实现手动高速运行,手动高速运行时频率为48Hz转速为2860r/min。
HIVERT高压变频器在一次除尘风机上的应用及维护
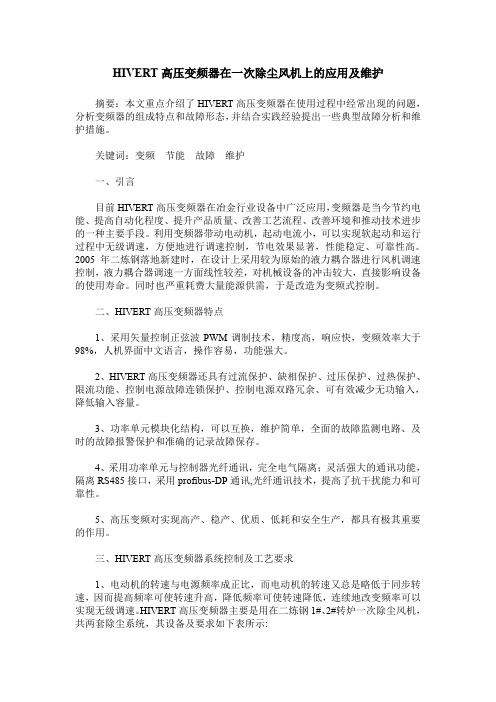
HIVERT高压变频器在一次除尘风机上的应用及维护摘要:本文重点介绍了HIVERT高压变频器在使用过程中经常出现的问题,分析变频器的组成特点和故障形态,并结合实践经验提出一些典型故障分析和维护措施。
关键词:变频节能故障维护一、引言目前HIVERT高压变频器在冶金行业设备中广泛应用,变频器是当今节约电能、提高自动化程度、提升产品质量、改善工艺流程、改善环境和推动技术进步的一种主要手段。
利用变频器带动电动机,起动电流小,可以实现软起动和运行过程中无级调速,方便地进行调速控制,节电效果显著,性能稳定、可靠性高。
2005年二炼钢落地新建时,在设计上采用较为原始的液力耦合器进行风机调速控制,液力耦合器调速一方面线性较差,对机械设备的冲击较大,直接影响设备的使用寿命。
同时也严重耗费大量能源供需,于是改造为变频式控制。
二、HIVERT高压变频器特点1、采用矢量控制正弦波PWM调制技术,精度高,响应快,变频效率大于98%,人机界面中文语言,操作容易,功能强大。
2、HIVERT高压变频器还具有过流保护、缺相保护、过压保护、过热保护、限流功能、控制电源故障连锁保护、控制电源双路冗余、可有效减少无功输入,降低输入容量。
3、功率单元模块化结构,可以互换,维护简单,全面的故障监测电路、及时的故障报警保护和准确的记录故障保存。
4、采用功率单元与控制器光纤通讯,完全电气隔离;灵活强大的通讯功能,隔离RS485接口,采用profibus-DP通讯,光纤通讯技术,提高了抗干扰能力和可靠性。
5、高压变频对实现高产、稳产、优质、低耗和安全生产,都具有极其重要的作用。
三、HIVERT高压变频器系统控制及工艺要求1、电动机的转速与电源频率成正比,而电动机的转速又总是略低于同步转速,因而提高频率可使转速升高,降低频率可使转速降低,连续地改变频率可以实现无级调速。
HIVERT高压变频器主要是用在二炼钢1#、2#转炉一次除尘风机,共两套除尘系统,其设备及要求如下表所示:2、HIVERT高压变频器一般由主电路、功率单元和控制系统组成。
利用高压变频对转炉一次除尘风机实施节能改造

来调节输 出轴 的转 速 , 使输 出轴 的转速 得 以改 变 , 连
续改变勺 管 的位 置调节工 作腔 的充液量 ,输 出转速
原有的除尘风机一直是高速运行 。正常运行的无 级调 节 。风 机与 电机采 用液力偶合器 实现柔 性联结 ,采用 调速 型液力 偶合 器 , 速 为 30 mn 功 率 范 围为 50 10 W。 转 00r i, / 5 ~ 60k
c n e so r r s n e . Th u i g sae a h c n mi e e t fe e g a i g atr r — o v r in a e p e e t d e r nn n tt nd t e e o o c b n f so n ry s vn fe e i c n tu t n ae a a y e o r he i ey Th fe t r aif co y o sr ci r n lz d c mp e nsV l . e e fc sa e s t a t r . o s
GUO a d n Xio o g
(a gu hgn ru agn ei te C .Ld, i gu Hui 2 0 2 C i ) J n s aagGopHui gS c l el o t.J ns, aa 23 0 , hn i S a p aS , a n a
【 bt c】 h edcn o pi i e n nr v g r c l o h h oae r uny A s at T e pe ot l r c l adee y ai i i e f i l g f q ec r s r n p g s n p n p g v t e
一
为 :e 15 W, = 0 k ,= 3 . A, = 9 2 r 尸= 2 0 k 1 V, 19 n 2 8 / e 2 m n cs = .。 i ,o ̄ 09 工频运 行 。
炼钢厂一次风机节能改造浅析
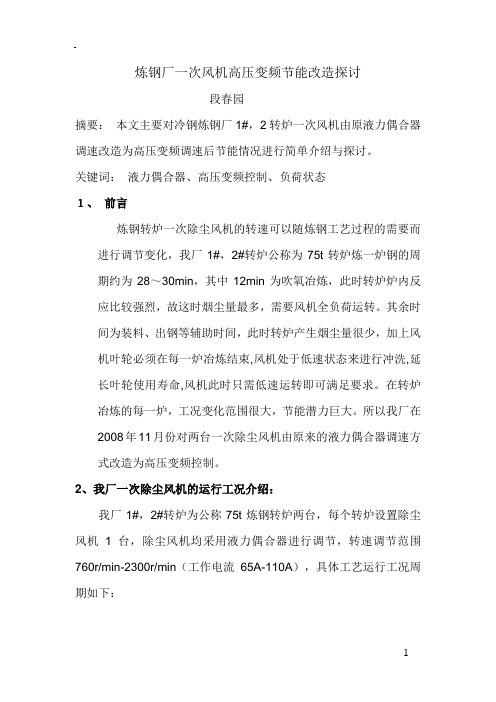
炼钢厂一次风机高压变频节能改造探讨段春园摘要:本文主要对冷钢炼钢厂1#,2转炉一次风机由原液力偶合器调速改造为高压变频调速后节能情况进行简单介绍与探讨。
关键词:液力偶合器、高压变频控制、负荷状态1、前言炼钢转炉一次除尘风机的转速可以随炼钢工艺过程的需要而进行调节变化,我厂1#,2#转炉公称为75t转炉炼一炉钢的周期约为28~30min,其中12min为吹氧冶炼,此时转炉炉内反应比较强烈,故这时烟尘量最多,需要风机全负荷运转。
其余时间为装料、出钢等辅助时间,此时转炉产生烟尘量很少,加上风机叶轮必须在每一炉冶炼结束,风机处于低速状态来进行冲洗,延长叶轮使用寿命,风机此时只需低速运转即可满足要求。
在转炉冶炼的每一炉,工况变化范围很大,节能潜力巨大。
所以我厂在2008年11月份对两台一次除尘风机由原来的液力偶合器调速方式改造为高压变频控制。
2、我厂一次除尘风机的运行工况介绍:我厂1#,2#转炉为公称75t炼钢转炉两台,每个转炉设置除尘风机1台,除尘风机均采用液力偶合器进行调节,转速调节范围760r/min-2300r/min(工作电流65A-110A),具体工艺运行工况周期如下:A到B为待料时间,电机低速运行;B到C为电机升速时间,时间可调(小于两分钟);C到D为吹氧时间,风机高速运行;D点风机开始降速,自然降速;D到E为出钢时间;E到F为溅渣时间;整个吹炼工艺周期约26~28分钟,其中高速时间(C到D)11~13分钟,风机高速为2300 r/min以上(可以调节);风机低速为800 r/min(可以调节)。
除尘风机具体参数如下:鼓风机:2118AB/745 风量:Q=33.33m3/h入口压力:P=26512pa 匹配功率:1250kw主轴转速:2880 r/min 出口介质密度:0.826 kg/m³配套电机:YB710S1-2 电压等级: 6kv额定功率: 1250kW 额定电流: 136.6A功率因数: 0.89 额定转速:2970r/min3 、原有的液力偶合器调速系统介绍:我厂的1#,2#转炉在2004年相继投产时,系统一次除尘风机,设计院设计的为调速型液力偶合器,对风机的工况进行调整。
一次风机高压变频改造

囝1 一次风机用电率
在 满 足扬 程 的情况 下 ,将系 统风 门挡 板 全开 ,通 过改
次风 管压 力维 持在 90 1.ka 围 内 ,通过 冷 、热 风 . ~ 30 P范 门开度 的调 整 ,实现进 入 磨煤 机 的一 次风温 控制 ,保 证 磨 煤 机运 行效 率 ; 由磨 入 口挡板 控制 一 次风量 ,从而 实现 磨
b为 l ) 。则 风 机 由A 点移 至 B 点工 作 时 , 电机 节 省 功 耗 为A 点 、Q点 、0 、H 点和B 、Q 点 、0 、H 点面 积差 。若 0 点 0 点 1 点 I 能 采 用 调 速 手 段 改变 风 机转 速 ,那 么 当 流 量 从 Q减 小 至 0 Q 时 ,T 作 点将 由原 来 A 移 至 c ,风 机 运 行 也 更 趋 合 1 点 点 理 。挡板 全 开 ,没有 管 网阻力 情 况下 ,能 耗势 必 降低 。此 时 , 电机 节 省 功 耗 为A 、Q点 、O 、H 点 、和 C 、Q 点 0 点 0 点 1 点 、0 、H 点面 积差 :与挡 板控制 相 比更 为有 效合理 ,既 点 2 达 到 了改变 风 量 目的 ,又 明显改 善 了风机 运行 工况 ,设备 功耗 也随之 到大 大降低 。
新疆电力技术
20 0 年第4 总第 9 期 8 期 9
一
次风机 高压 变频改造
罗振 新
新疆华 电红雁池发 电 限责任公 司 ( 有 乌鲁木齐 804 ) 307
摘要 :火力发电厂 中各类大 型风机、水泵是最主要 的耗电 设备 。这 些设奋长期连 续运行 并常常处 于变 负荷运行状 态,节 能潜力 巨大。 为响应 国家节能减排号 召,降低厂 用电率,近期 隼 电红雁 池发 电公司对# 机组 一次风机进行 了高压变频改造, 2 采用北京动力潦科技股份有限公 司生产的HIV 6I 7 B N 一 /5 0 型高压 变频器 ,改造后 一次风机厂 用电率大 幅降低 ,节魄效果明显,
钢铁转炉除尘风机变频节能改造

目前转炉炼钢在 当代炼钢生产 中依然占据主 导地位 ,转炉的节能减排就显得尤为重要 ,越来
越多的钢铁企业 以 “ 负能炼 钢” 为 目标进行节 能技术改造 。转炉 “ 负能炼 钢”指 的是转炉炼 钢工序消耗 的总能量小于 回收的总能量 ,即转炉 炼 钢工 序 能 耗 小 于零 。转 炉 实 现 “ 能 炼 钢 ” 负 是衡 量 一个 现代 化炼 钢 厂生产 技术 水平 的重 要标 志 ,也是节能降耗、降低生产成本 、提高企业竞 争力 的主要 技 术措施 。
Qon ;Pon ;Jo, ; c z 7 c v l 式 中:N为风机轴功率 (W) Q为风机进 I容 k ; : 1
积流量 ( / n" 为 风 机进 口压 力 (P ) m mi) ;P ka ; J 7 v为风机 转速 (/ i) rmn 。
频率 ,控制电路本身能量消耗很小 , 变频器可以 在全转速范围内保持较高效率运行 ; ( )变频调速可 以实现 电机软启动 ,且在 2 很宽的转速范围内保持高功率因数运行;
s vn ae i p t 0 ,whc r v d a c r ig y ta h rq e c o v rin i h e u t g a ig rt s u o 4 % ih p o e c od n l t te f u n y c n eso n t e d d si h e n c mp e s r l b e e c a aie e e g a i g a d r d c n o s mpi n a d i c a ec n t n- o r s os wi e b n f ilt r l n r ys vn n u i g c n u t r s o sa t l i Oe z e o n ne
3 ri 0 n左右 。 a
一次风机高压变频改造工程施工组织设计
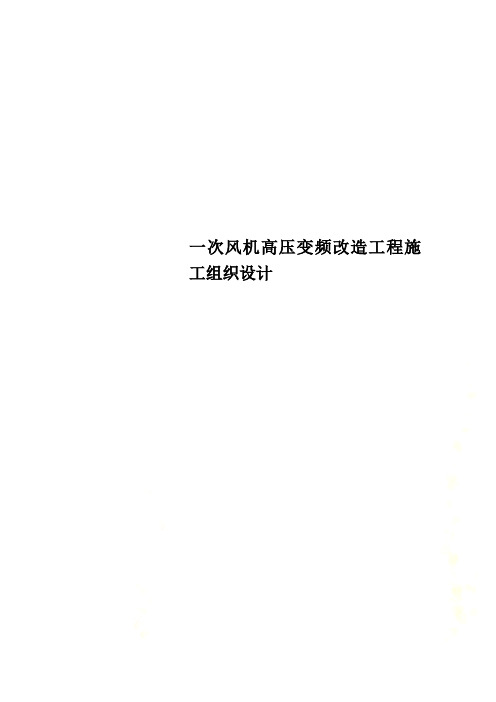
一次风机高压变频改造工程施工组织设计国电阳宗海发电有限公司3#、4#机组一次风机高压变频改造工程施工组织设计批准:_________________审核:_________________编制:_________________2010年月日目录1 编制说明 (1)2 工程概况 (1)3 机具、人员安排 (1)4 施工方案 (2)5 质量目标和保证措施 (15)6 安全保证措施 (16)7 文明施工保证措施 (17)8 附录 (17)一次风机高压变频改造工程施工组织设计1 编制说明1.1为使一次风机的变频装置顺利正确安装,确保安装质量达到设计要求和避免安装过程中不必要的重复工作,保证施工人员的安全,特编写此程序。
1.2施工组织设计的编制依据主要为:GB 50303-2002 《建筑电气工程施工质量验收规范》GB 7216-87 《继电器及继电保护装置基本试验方法》GB 14285-93 《继电保护和安全自动装置技术规程》GB 50171-92 《电气装置安装工程盘、柜及二次回路接线施工及验收规范》GB6450 《干式电力变压器》DL/T596—1996 《电力设备预防性试验规程》DL/T402—1999 《交流高压断路器订货技术条件》DL/T403—2000 《12kV~40.5kV高压真空断路器订货技术条件》DL/T404—1997 《户内交流高压开关柜订货技术条件》DL/T486—2000 《交流高压隔离开关和接地开关订货技术条件》DL/T615—1997 《交流高压断路器参数选用导则》DL401—1991《高压电缆选用导则》DL413—1991《35kV及以下电力电缆热缩型附件应用技术条件》DL/T572—1995 《电力变压器运行规程》变频器外形图、安装图、布置图及相关技术文件等2 工程概况#3、#4机组一次风机高压变频改造安装工作范围:#3、#4炉#1、#2号风机变频控制柜、模块柜、变压器柜、旁路柜、6千伏段至变频配电室、一次风机至高频间高压电缆采购及安装、控制电缆采购及安装敷设。
除尘风机节能高压变频技术改造
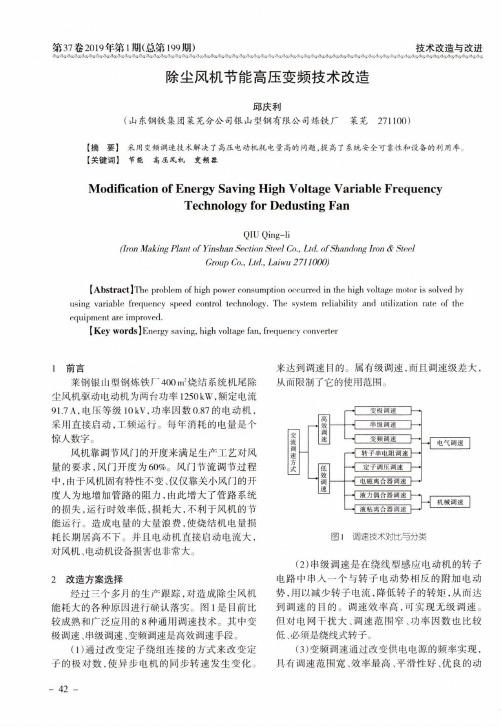
QIU Qing-li (Iron Making Plant of Yinshan Section Steel Co., Ltd. ofShandong Iron & Steel
Group Co., Ltd., Laiwu 2711000)
[Abstract ] The problem of high power consumption occurred in the high voltage motor is solved by using variable frequency speed control technology. The system reliability and utilization rate of the
10kV电源—10kV等级高压变频器—lOkV高 压电动机。
其中QF是用户高压开关柜的断路器;QS2, QS3 是变频器内部手动旁路隔离刀闸,供变频运行操 作;QS「是变频器内部手动旁路隔离刀闸,供工频 操作;且QS,与QS2, QS]互锁,安全可靠。
(2) 控制回路变更见图3,4。
3.2 高压柜控制回路改造 在原有高压柜端子基础上 ,保证原回路、功能
3具体实施方案 3.1改造流程(见表1)
表1现场改造流程
高压柜控制 设计、改造新 变频器与高压柜
回路改造
控制回路
实现联锁
1变频速度给定根据变频调速时间 以最低能耗,达
信号采集
确定,信号给定点 到最佳工作效果
2故障信号远传ห้องสมุดไป่ตู้
设立远程 操作监视
可远程起停设备 运行监视状态
3控制电源主 电源连接
重新敷设高圧 电缆、直流电源
位 .■7
隔
闸位置
离 刀一 闸 位
高压变频器在转炉一次除尘风机上的应用

1 引言
当前我国节能形势 日趋重要 , 钢材市场 日 趋激 烈 的竞争使企业成本压力增大 , 这为节能降耗提供 了有力的动力 , 新疆八一钢铁股份公 司( 简称八钢)
有挖潜的可能 , 原有的 6台高压风机全部采用液力 偶合器方式调速的 , 即电动机一直保持 5 z OH 频率
额定 功率 因数 :.8 08 ; 额定 转速 : 8 mi 290r n; / 润滑 方式 : 润滑 。 油
额定频率 :5 6 z 1 — OH ;
额定电流 :4 11 A;
( 可靠性高、 1 ) 维护简单 ( 只需紧固和清扫) 。 ( 绝缘温升等级高。 2 )
( 局部放 电量 / 通 常在 1P 3 ) b( 0 C以下 ) 可保 证 ,
长期安全运行 , 寿命可达 3 年 。 O ( 损耗低、 4 ) 效率高、 噪声小、 抗裂、 抗温度变化 。
一
高型, 电路结构为单元 串联结构 ,6 3 脉波整流 ,3 l
2 高压 电动机参数
选择 4 、 号和 6号三台 90k 高压风机进 号 5 0 W
电平输 出, 移相式 P WM, 缓冲电路 为电压源型 , 其原 理结构如图 1从图 1 , 可以看出, 高压变频器 由三部 分组成 : 移相变压器 、 功率单元及控制部分组成。 3 1 移相 变压 器 . 移相 变 压 器选 用 干 式 变 压 器 , 入 电压 6 输 . 3 V, 出为 60V, k 输 3 相位 角 间 隔 l。其 特点 有 : 0,
风机低速设定为 1 0 m n 对应 变频器频率 0r i, 0 / 为 l . z 高速设定 为 24 Orr n 对 应频 率 为 6 7H , O a , /i 通过 P C给定变频器频率信号控制变频器 的转速 。 L
转炉一次除尘风机控制系统改造研究与应用分析

转炉一次除尘风机控制系统改造研究与应用分析作者:李维花来源:《数字化用户》2013年第20期【摘要】本文以某公司为例,详细阐述了怎样让转炉一次除尘风机控制系统实现转速的自动调节、保护、参数记录以及转炉煤气的回收等。
并对转炉一次除尘风机控制系统的的改造进行了探索和研究。
【关键词】转炉除尘风机控制系统改造研究一、转炉一次除尘风机控制系统的工作流程某公司原来的除尘风机使用的是技术非常落后的液力耦合器对风机的速度进行调节。
对于这种液力耦合器而言,它并不能够让除尘风机对速度进行自我调节,因此当使用时,该除尘风机一直处于高速运转状态,如果这样长期运转下去,则会大大降低该除尘风机的使用寿命,同时还会导致大量电流的流失。
为了提升工作效率,尽可能节约更多的电能,便对该转炉一次除尘风机进行了系统改造。
当对该转炉一次除尘风机进行改造之后,使用的是高压变频器对其进行调节,并且通过可编程序控制器,实现了该转炉一次除尘风机的远程控制、自动控制和煤气回收系统等功能。
在吹炼过程中,会产生1500℃至1700℃的转炉煤气,当这些高温煤气在除尘风机的抽引下,会通过内部的汽水烟道以及活动烟罩,通过这两项装置之后,使最终的转炉煤气温度降低到700℃以下,当温度随之降低后,则会进入文氏管,在文氏管中进行灭火工作。
经过这道工序之后,转炉煤气的温度会持续降低,并且在重力脱水器中脱去水滴,接着便会进入二级文氏管。
在二级文氏管中,内部的矩形侯口会根据转炉的微差压进行自动调整,当达到最佳的状态时,便会对转炉煤气进行一个精准除尘。
当完成一系列工作之后,转炉煤气会经过脱水器(弯头)、分离器(水雾)、脱水塔脱水,当所有步骤一一完成后,最后才会进入除尘风机。
在除尘风机中,会对煤气的质量以及其它条件作出分析,并通过除尘风机对其正压,在内部的三通切换阀中,会对煤气进行切换,最后会通过烟囱向大气排放。
转炉一次除尘风机的工作原理如下图1:二、转炉一次除尘风机控制系统的改造和应用(一)除尘风机的控制条件当转炉的氧枪在吹炼位时,应该高速运转;而当转炉在停止工作或者没在吹炼的情况下,则应该低速运行;当转炉闲置或者尚未工作的情况下,便不能开氧。
转炉一次除尘3#风机高压变频改造
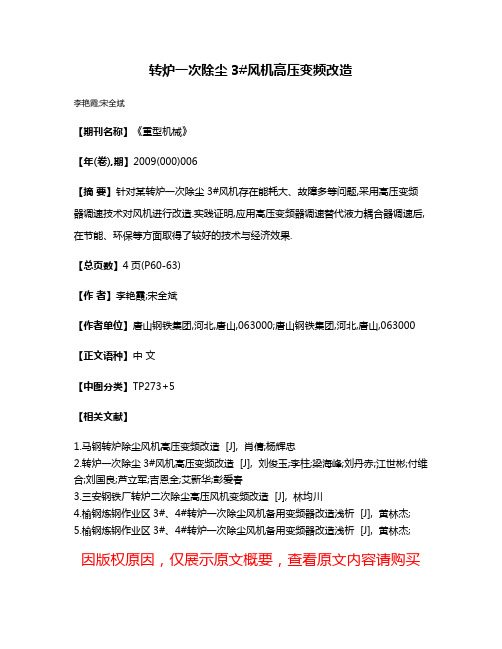
转炉一次除尘3#风机高压变频改造
李艳霞;宋全斌
【期刊名称】《重型机械》
【年(卷),期】2009(000)006
【摘要】针对某转炉一次除尘3#风机存在能耗大、故障多等问题,采用高压变频器调速技术对风机进行改造.实践证明,应用高压变频器调速替代液力耦合器调速后,在节能、环保等方面取得了较好的技术与经济效果.
【总页数】4页(P60-63)
【作者】李艳霞;宋全斌
【作者单位】唐山钢铁集团,河北,唐山,063000;唐山钢铁集团,河北,唐山,063000【正文语种】中文
【中图分类】TP273+5
【相关文献】
1.马钢转炉除尘风机高压变频改造 [J], 肖倩;杨辉忠
2.转炉一次除尘3#风机高压变频改造 [J], 刘俊玉;李柱;梁海峰;刘丹赤;江世彬;付维合;刘国良;芦立军;吉恩全;艾新华;彭爱春
3.三安钢铁厂转炉二次除尘高压风机变频改造 [J], 林均川
4.榆钢炼钢作业区3#、4#转炉一次除尘风机备用变频器改造浅析 [J], 黄林杰;
5.榆钢炼钢作业区3#、4#转炉一次除尘风机备用变频器改造浅析 [J], 黄林杰;因版权原因,仅展示原文概要,查看原文内容请购买。
- 1、下载文档前请自行甄别文档内容的完整性,平台不提供额外的编辑、内容补充、找答案等附加服务。
- 2、"仅部分预览"的文档,不可在线预览部分如存在完整性等问题,可反馈申请退款(可完整预览的文档不适用该条件!)。
- 3、如文档侵犯您的权益,请联系客服反馈,我们会尽快为您处理(人工客服工作时间:9:00-18:30)。
前言众所周知,钢铁工业是我国国民经济的支柱产业,也是资源、能源、资金、技术和劳动力密集行业和污染排放大户。
近年来,我国钢铁工业通过结构调整和技术进步,在节能降耗、减少污染物排放方面取得了显著成效。
及微量其它成分高温气体。
炼钢厂转炉吹炼过程中,会产生大量含有CO、少量CO2在气体中央带着大量氧化铁、金属铁和其他颗粒细小的固体烟尘即炉口观察到得棕红色浓烟这股高温含尘气流冲出炉口进入眼罩与净化系统,在气体流出炉口进入烟罩的同时,或多或少地吸入部分空气使CO燃烧。
转炉烟气的特点是温度高、气体多、含尘量大,气体具有毒性与爆炸性,必须对转炉烟气进行净化处理。
转炉一次除尘就担任了此项任务。
除尘风机是除尘系统的关键设备,一旦除尘风机不能正常工作,不仅耽误生产、影响质量,还有可能对现场工作人员的人身安全造成威胁。
现在除尘风机大多数采用液力耦合器控制,由于采用液力耦合器存在调速范围有限、调速精度低、线性度差、漏油严重、环境污染大等缺点。
而通过使用变频器控制风机后,不仅能解决使用液力耦合器时带来的缺点,而且改善了工艺过程,根据工艺需求自动调节风量,同时提高了生产工艺自动化程度,实现除尘风机自动调节,精简了控制程序,使操作更加方便,提高了生产效率,从而达到了节能降耗的目的。
其综合效益是特别明显的。
目录1、课题提出的目的以及意义 (1)2、转炉一次除尘系统简介 (1)2.1转炉一次除尘系统的目的 (1)2.2工艺参数 (1)2.3转炉一次除尘工艺结构图 (2)2.4转炉一次除尘系统结构 (2)2.5转炉一次除尘工艺概述 (3)2.6转炉一次除尘工艺流程图 (3)3、一次除尘电动机及风机设备主要参数 (3)3.1电动机 (3)3.2除尘风机 (4)4、转炉除尘风机的工艺要求 (5)4.1转炉工作一个工艺周期的工艺流程图及分析 (5)5、风机的控制方式主要有二种 (5)5.1通过液力耦合器控制风机 (5)5.2通过变频器控制风机 (6)6、风机控制的具体实现 (9)6.1电机和风机监控主要数据表 (9)6.2除尘风机控制系统图 (9)6.3除尘风机控制系统的分析 (9)7、节能 (10)7.1节能原理 (10)7.2节能分析 (11)总结 (12)主要参考文献 (13)附图 (14)1 课题提出的目的以及意义目前,在转炉除尘风机运行上大多采用液力耦合器进行调速控制,它比直接调整风门前进了一步,提高了负载的功率因数,改善了电机的启动冲击,传递功率大,操作维修简单。
但其滑差功率损失较大,调速范围相对较窄,速度变化跟随慢,节能效果较差。
随着国家对环境保护的日益加强,企业挖潜增效的日益深入,生产现场需要调速范围宽,生产效率高,节能效果显著,并能在原有设备基础上,方便地改造电气装置,优化除尘风机的控制。
变频调速装置可以方便地实现上述除尘风机的控制要求,变频器具备软启动、软停止、频繁启动不会对设备及电网产生冲击,速度跟随快,节能显著的功能。
故当转炉在非吹炼期间风机没有除尘任务时,可以减速运行,并利用减速过程的惯性再用高压水对叶轮进行冲洗。
在实际的工艺控制过程中,可根据实时检测烟道烟尘浓度或氧枪工作信号与调速系统构成闭环控制方式,实现风机自动调速控制运行。
2 转炉一次除尘系统简介2.1转炉一次除尘系统的目的及微量其它成分高温气体。
在气体转炉吹炼过程中,会产生大量含有CO、少量CO2中央带着大量氧化铁、金属铁、其他颗粒细小的固体烟尘。
即炉口观察到得棕红色浓烟。
这股高温含尘气流冲出炉口进入眼罩与净化系统,在气体流出炉口进入烟罩的同时,或多或少地吸入部分空气使CO燃烧。
转炉烟气的特点是温度高、气体多、含尘量大、气体具有毒性与爆炸性。
所以必须对转炉烟气进行净化处理。
一次除尘就是将烟气冷却、净化、由引风机将其排至烟筒放散或输送到煤气回收站备用。
2.2工艺参数转炉公称容量50t转炉座数 2座 2吹2铁水装入量最大44t冶炼周期 30min 其中吹氧时间16~18min脱碳速度最大0.5%/min表1 脱碳速度表表2 原始炉气温度和成分表名称温度CO CO2N2O2前烧期1450℃60% 30% 9% 1.0%中烧期1550℃86% 10% 3.5% 0.5%后烧起1600℃65% 25% 9% 1.0%表3 烟气净化后成分表CO CO2N2O264.3% 15.4% 16.3% 0.4%2.3转炉一次除尘工艺结构图图1 除尘工艺结构图2.4转炉一次除尘工艺结构:一级溢流文氏管(一文)、二级文氏管(二文)、除尘鼓风机、煤气柜、放散烟筒等构成。
一级文氏管(一文)作用:主要起消火、粗净化和降温的作用;二级文氏管(二文)作用:起精细净化作用;煤气柜:主要储存回收后的煤气;放散烟筒:主要用于排放烟气。
2.5转炉一次除尘工艺概述转炉1500度的高温烟气经汽化冷却烟道冷却至800~1000度后,进入洗涤塔,其中设有一级溢流文氏管、二级文氏管、旋流脱水器等,使烟气在一级溢流文氏管经降温和粗除尘后,在脱水器(I)脱出污水,然后再二级文氏管中进一步净化,并经脱水器(II)脱水,进入鼓风机。
煤气经三通切换阀,水封逆止阀后进入煤气柜,供用户使用,不回收时烟气经三通切换阀和放散烟筒点燃放散。
一级文氏管除尘污水从脱水器(I)排入污水处理系统。
污水经粗粒分离池、辐射沉淀池澄清后,浊环水供二级文氏管喷淋,其排出的污水经水泵供给一文除尘用,实现串级供水。
经辐射沉淀池浓缩的泥浆送至中间罐,由泵打入板框压缩机进行脱水,脱水后含水率30%的泥饼通过汽车送往烧结厂利用。
条件允许时也可将辐射沉淀池的泥浆用泵直接送往烧结厂,经进一步浓缩后,供烧结厂混作原料配水使用。
2.6转炉一次除尘工艺流程图图2 除尘工艺流程图3 一次除尘电动机及风机设备主要参数3.1电动机:型号:YBKS560---2额定电压:10KV额定电流:110A功率:1250KW功率因数:0.89额定转速:2400r/min轴承报警温度和停机温度:80度、85度轴瓦报警温度和停机温度:75度、80度定子报警温度和停机温度:135度、140度3.2除尘风机除尘风机是除尘系统的关键设备,一旦除尘风机不能正常工作,不仅耽误生产、影响质量,还有可能对现场工作人员的人身安全造成威胁。
图3 除尘风机3.2.1风机各项参数型号:AII1300----1.124/0.787额定电压:10KV额定电流:107.5A进口流量:1300m /min出口压力:1.124×98KP轴承报警温度和停机温度:75度、80度轴瓦报警温度和停机温度:70度、75度3.2.2结构本产品结构:该风机为单级吸入、单极、双支承结构。
3.2.3工作原理离心鼓风机是把原动机(电动机)的机械能转变为气体压力能和速度能的一种机械。
气体经进气室均匀地进入叶轮,在叶轮片的作用下,随着叶轮高速旋转。
气体由于受到离心力的作用,以及在叶轮里的扩压流动,使气体通过叶轮后的压力和速度得到了提高。
由叶轮排出的高压、高速气体在流经扩压器后其流动速度逐渐减慢而压力进一步提高。
最后通过蜗壳将气体汇集起来(蜗壳也具有一定的减速扩压作用)。
由圆形出口排送到工艺流程中。
4 转炉除尘风机的工艺要求4.1转炉工作一个工艺周期的工艺流程图及分析在B点,工艺要求风机转速迅速升高,B→C点时间应为30s 。
在C点,风机达到高速运转,C→D的时间为12.5~14min ;在D点,工艺要求风速从高速降到中速;在E点,风速应从中速降到低速,B→C和D→E时间均应为30s ,这样就完成了一次炼钢周期。
从转炉工作情况看,转炉每个冶炼周期为30min左右,吹炼时间和装、出料的时间基本各占一半,风机在转炉吹炼时高速运行,在吹炼后期及补吹时中速运行,而在出钢和装料期间可将速度降低到额定转速的10%~15% ,低速运行,即可满足转炉冶炼工艺的除尘要求。
5 风机的控制方式主要有二种5.1 通过液力耦合器控制风机5.1.1液力耦合器的简要介绍(1)液力耦合器:液力耦合器是一种液力传动装置,又称液力联轴器。
(2)液力耦合器各项参数:型号:YOTGC450防爆调速型;输入转速:2900r/min;传递功率范围:900~1600kW;额定滑差率:1.5~3%;(3)基本结构:液力耦合器其结构主要由壳体、泵轮、涡轮三个部分组成。
(4)液力耦合器基本原理:电动机运行时带动液力耦合器的壳体和泵轮一同转动,泵轮叶片内的液压油在泵轮的带动下随之一同旋转,在离心力的作用下,液压油被甩向泵轮叶片外缘处,并在外缘处冲向涡轮叶片,使涡轮在受到液压油冲击力而旋转;冲向涡轮叶片的液压油沿涡轮叶片向内缘流动,返回到泵轮内缘,然后又被泵轮再次甩向外缘。
液压油就这样从泵轮流向涡轮,又从涡轮返回到泵轮而形成循环的液流。
液力耦合器中的循环液压油,在从泵轮叶片内缘流向外缘的过程中,泵轮对其作功,其速度和动能逐渐增大;而在从涡轮叶片外缘流向内缘的过程中,液压油对涡轮作功,其速度和动能逐渐减小。
液压油循环流动的产生,是泵轮和涡轮之间存在着转速差,使两轮叶片外缘处产生压力差。
液力耦合器工作时,电动机的动能通过泵轮传给液压油,液压油在循环流动的过程中又将动能传给涡轮输出。
液压油在循环流动的过程中,除受泵轮和涡轮之间的作用力之外,没有受到其他任何附加的外力。
根据作用力与反作用力相等的原理,液压油作用在涡轮上的扭矩应等于泵轮作用在液压油上的扭矩。
5.1.2采用液力耦合器控制风机存在的缺点(1)调速范围有限,约为50%~95%,转速不稳定,高速段减小了设备的出力能力,低速段影响节能效益的发挥;(2)调速越低时效率越低,低速时发热厉害;(3)调速精度低,线性度差,响应慢,不大适应自动控制要求;(4)电机虽然可以不带载启动,但仍然有5倍左右的冲击电流,影响电网稳定;(5)必须串入电机和机械负载的连接轴中,不适合于设备改造,液力耦合器故障时,没有工频旁路系统,负载机械将无法运转,必须停机检修;(6)漏油严重,对环境污染大,可靠性差,维修难度大,严重浪费人力及影响生产。
5.2通过变频器控制风机5.2.1通用变频器结构主要由整流(交流变直流)、滤波、再次整流(直流变交流)、制动单元、驱动单元、检测单元微处理单元等组成的。
5.2.2通用变频器基本原理(1)主电路是给异步电动机提供调压调频电源的电力变换部分,变频器的主电路大体上可分为两类:电压型是将电压源的直流变换为交流的变频器,直流回路的滤波是电容。
电流型是将电流源的直流变换为交流的变频器,其直流回路滤波是电感。
它由三部分构成,将工频电源变换为直流功率的“整流器”,吸收在变流器和逆变器产生的电压脉动的“平波回路”,以及将直流功率变换为交流功率的“逆变器”。
①整流器:最近大量使用的是二极管的变流器,它把工频电源变换为直流电源。