压铸件结构设计规范
2-3压铸件结构设计-53

表2-13 铸造圆角半径的设计计算 上一页 下一页 返回
4.压铸件的脱模斜度
为了保证压铸件能够从压铸模具中顺利脱出,在压铸件沿脱出方向上
的所有内表面都要有一定的斜度,该斜度称为脱模斜度。压铸件脱模 斜度的大小和压铸件的壁厚及合金种类有关。
压铸件壁厚↑,对型芯的抱紧力↑,脱模斜度↑;
收缩率及熔点↑,脱模斜度↑; 压铸件内表面或孔比外表面的脱模斜度要大。 在允许范围内,采用较大的脱模斜度,可减少推件力和抽芯力。
上一页 下一页 返回
表2-2 厚度尺寸公差(单位:mm)
表2-3 圆角半径尺寸的公差(单位:mm)
D4
表2-4 自由角度和自由锥度尺寸公差
表2-5 孔中心距尺寸公差(单位:mm)
2).表面形状和位置
压铸件的表面形状和位置主要由压铸模的成型表面决定,而压铸 模成型表面的形位公差精度较高,所以对压铸件的表面形位公差 一般不另行规定,其公差值包括在有关尺寸的公差范围内。对于 直接用于装配的表面,类似机械加工零件,在图中注明表面形状 和位置公差。
表2-9 压铸件机械加工余量(mm) 表2-10 压铸件铰孔加工余量
三、 压铸件结构设计
压铸件的结构设计是压铸生产中首先遇到的工作, 其设计的合理性和工艺适用性直接影响到后续工作
的顺利进行。设计压铸件除要满足使用要求外,同
时应该满足成型工艺要求,并且尽量做到模具结构 简单、生产成本低,达到设计的合理性、工艺性、 可制造性、经济性。
图2-4 改变凹区域方向消除抽芯受阻区域 图2-4 (a)形成区域A的活动型芯受到凸台K阻碍,无法抽出。 因此改变其方向,使区域A指向外侧,则可顺畅抽出,如图2-4 (b)所示。
(二)消除抽芯受阻区域
第4章 压铸件结构设计及压铸工艺

(一)从简化模具结构、延长模具使用寿命考虑
• 铸件的分型面上应尽量避免圆角; 如果将结构改为如图4-1b所示的结构,则分型面平整, 加工简便,避免了上述缺点。
(一)从简化模具结构、延长模具使用寿命考虑
• 避免模具局部过薄; 如下图a所示的压铸件,因孔边离凸缘距离过小,易使模 具镶块在a处断裂。若将压铸件改为如下图b所示的 a≥3mm的结构,则使镶快具有足够的强度,延长了模具 的使用寿命。
• 两壁连接时的圆角---交叉连接
β=90°,R=s; β=45°,R1=0.7s,R2=1.5s; β=30°,R1=0.5s,R2=2.5s
3.脱模斜度(铸造斜度) 作用: • 减少铸件与模型的摩擦,容易取出铸件; • 保证铸件表面不被拉伤; • 延长模型使用寿命。 压铸件上各部分所需要的斜度值是不相同的,应按金属收缩 的方向来确定。当金属的收缩受到的阻力大时,斜度应大些, 反之则取小些。
避免压铸件上互相交叉的不通孔
• 3)将型芯B分为两部分,从两侧抽出(见下图c)。
(一)从简化模具结构、延长模具使用寿命考虑
• 避免内侧凹 针对要求采取的措施有: 1)外形不加大,内部形状凸出至底部(见下图a)。
2)局部加厚,内形加至底部,外形加至分型面处,从而消 除侧凹(见下图b) 。
3)原凸台形状不改变,在零件底部开出通孔,模型成型镶 件可以从通孔处插入形成台阶(见下图c)。
三、压铸件的精度、表面粗糙度及加工余量
(一) 压铸件的精度、表面粗糙度及加工余量
◇压铸件的尺寸精度
压铸件的尺寸精度较高,基本上由压铸模的制造精度而定。
1.长度尺寸
压铸件线性尺寸公差及选用见表4-5。 尺寸公差带的位置如下: 1、不加工的配合尺寸,孔取正(+), 轴取负(-)。
汽车关于压铸件的要求标准

汽车关于压铸件的要求标准汽车压铸件是指通过压铸工艺制造的汽车零部件,这些部件通常由铝合金、镁合金等金属材料制成。
为确保汽车压铸件在安全、性能和质量方面达到要求,制定了一系列的标准和规范。
以下是关于汽车压铸件的要求标准的一般性内容:1. 材料要求1.1 金属合金规定压铸件所使用的金属合金的种类和成分要求,通常包括铝合金、镁合金等。
合金的选择直接影响到压铸件的强度、耐腐蚀性等性能。
1.2 材料性能测试对金属合金进行强度、硬度、延伸性等性能测试,确保所选材料符合相应的标准。
2. 设计要求2.1 几何设计规定压铸件的几何设计要求,包括尺寸、形状、壁厚等,确保压铸件可以正确嵌入汽车结构中。
2.2 壁厚均匀性要求压铸件的壁厚均匀,避免因过薄或过厚导致的性能问题。
2.3 结构设计对于需要承受特定载荷或作用的压铸件,规定其结构设计,以确保在正常使用情况下不发生断裂或变形。
3. 制造工艺要求3.1 压铸工艺规定压铸件的生产工艺,包括压铸机的选择、压射速度、温度控制等,以保证压铸件的成形质量。
3.2 熔炼和浇铸对金属合金的熔炼和浇铸过程进行要求,确保合金的纯度和均匀性。
3.3 热处理如果需要对压铸件进行热处理,规定热处理工艺,以提高压铸件的强度和硬度。
4. 表面处理要求4.1 防腐处理规定压铸件的防腐处理方法,确保其在汽车使用中具有足够的抗腐蚀性能。
4.2 涂装要求对于需要进行涂装的压铸件,规定涂装的种类、颜色、附着力要求等,以提高压铸件的外观和耐候性。
5. 检测和测试要求5.1 尺寸检测规定对压铸件尺寸的检测方法和标准,确保其符合设计要求。
5.2 材料性能测试对压铸件材料进行硬度、拉伸、冲击等性能测试,以验证其性能是否符合要求。
5.3 缺陷检测规定对压铸件进行缺陷检测的方法,如X射线检测、超声波检测等,以确保压铸件内部不存在瑕疵。
6. 标志和包装规定在压铸件上标明必要的标志,以便追溯生产信息。
同时规定适当的包装方式,确保在运输过程中不受损。
铝合金压铸件的结构设计经验
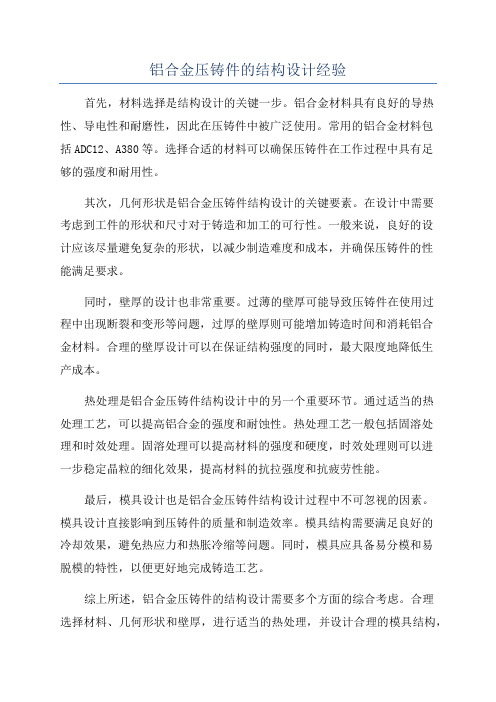
铝合金压铸件的结构设计经验首先,材料选择是结构设计的关键一步。
铝合金材料具有良好的导热性、导电性和耐磨性,因此在压铸件中被广泛使用。
常用的铝合金材料包括ADC12、A380等。
选择合适的材料可以确保压铸件在工作过程中具有足够的强度和耐用性。
其次,几何形状是铝合金压铸件结构设计的关键要素。
在设计中需要考虑到工件的形状和尺寸对于铸造和加工的可行性。
一般来说,良好的设计应该尽量避免复杂的形状,以减少制造难度和成本,并确保压铸件的性能满足要求。
同时,壁厚的设计也非常重要。
过薄的壁厚可能导致压铸件在使用过程中出现断裂和变形等问题,过厚的壁厚则可能增加铸造时间和消耗铝合金材料。
合理的壁厚设计可以在保证结构强度的同时,最大限度地降低生产成本。
热处理是铝合金压铸件结构设计中的另一个重要环节。
通过适当的热处理工艺,可以提高铝合金的强度和耐蚀性。
热处理工艺一般包括固溶处理和时效处理。
固溶处理可以提高材料的强度和硬度,时效处理则可以进一步稳定晶粒的细化效果,提高材料的抗拉强度和抗疲劳性能。
最后,模具设计也是铝合金压铸件结构设计过程中不可忽视的因素。
模具设计直接影响到压铸件的质量和制造效率。
模具结构需要满足良好的冷却效果,避免热应力和热胀冷缩等问题。
同时,模具应具备易分模和易脱模的特性,以便更好地完成铸造工艺。
综上所述,铝合金压铸件的结构设计需要多个方面的综合考虑。
合理选择材料、几何形状和壁厚,进行适当的热处理,并设计合理的模具结构,可以确保铝合金压铸件具有优良的性能和稳定的质量,满足不同工程领域的需求。
压铸件结构设计

h2≥0.8mm
a≤3°
压铸件加强筋的运用
3,作为散热加强;
4,作为装饰作用。
2,引导料流流向;
1,加强结构强度;
压铸件结构工艺性分析一
不好的案例
好的案例
说明
于型模中加工凹入文字较之加工凸出文字为困难﹒且模具寿命难以保证,使用后续刻加工﹐则与此相反。
1.5
0.014~0.020
6
0.056~0.084
2
0.018~0.026
7
0.066~0.100
2.5
0.022~0.032
8
0.076~0.116
3
0.028~0.040
9
0.088~0.138
3.5
0.034~0.050
10
0.100~0.160
4
0.040~0.060
合金浇注温度高时,填充时间可选长些。 模具温度高时,填充时间可选长些。 铸件厚壁部分离内浇口远时,填充时间可选长些。 熔化潜热和比热高的合金,填充时间可选长些。
好的案例
说明
陈学民
2021
2023
内容大纲
O1
产品的壁厚(模具成型的基础)
O2
产品的拔模(模具脱模的保障)
O3
产品的圆角(模具寿命的关键)
O4
加强筋的设计(结构优化的手段)
压铸件壁厚的设计
3.5
2.5
3.5
2.5
2.5
2.0
>500
3.0
1.8
3.0
1.8
2.2
1.5
>100~500
2.5
压铸产品结构设计的工艺要求

压铸类产品结构设计的工艺要求
压力铸造是将熔融状态或者(半)熔融状态合金浇入压铸机的压室,以极高的速度在高压的作用下充填在压铸模的型腔内,使熔融合金在高压下冷却凝固成型的方法。
常见的压铸材料包括:铝合金、锌合金、镁合金、铜合金等,铝合金又分为铝镁合金、铝铜合金、铝锌合金、铝硅合金等。
压铸类产品在结构设计时的工艺要求注意的几个方面。
①压铸件的厚度
压铸件产品的厚度一般指料厚,料的厚薄直接影响压铸的难易,一般情况下,压铸产品的料厚≥0.8mm,具体料厚根据产品设计。
压铸产品不会因为局部料厚产生缩水的现象,相反,在一些尖钢薄钢处要加料填充,避免模具强度低而损坏。
压铸产品的外观面局部最小料厚≥0.7mm,非外观面局部最小料厚度建议≥0.4mm,太薄会导致填充不良、无法成型,薄的区域面积也不能太大,否则无法成型。
②压铸件的拔模角
压铸件与塑胶件一样,内外表面都需要拔模角,压铸件外表面的
拔模角一般在1°~3°,内表面拔模角比外表面拔模角大一点,方便产品出模。
③压铸件的后续加工
压铸件有时达不到设计的要求,需要后续加工。
其中螺丝柱中的螺纹就是后续加工的,在设计产品时只需留出底孔就可以。
压铸件有深孔时,压铸件需要做出孔位置,再通过后续机械钻孔加工完成。
压铸件有些表面要求较高的精度,一般也需要后续加工,在设计时可在需要后续加工的地方留出加工余量,加工余量一般在0.5mm 左右。
④压铸件产品不能变形,一般是螺丝连接,在做扣位连接,连接的对应产品必须能变形,如塑胶产品等。
⑤压铸件产品加强筋不能太多,对于薄壁类零件,需适当设计加强筋,以增加产品的抗弯强度,防止产品变形损坏。
压铸件壁厚设计原则
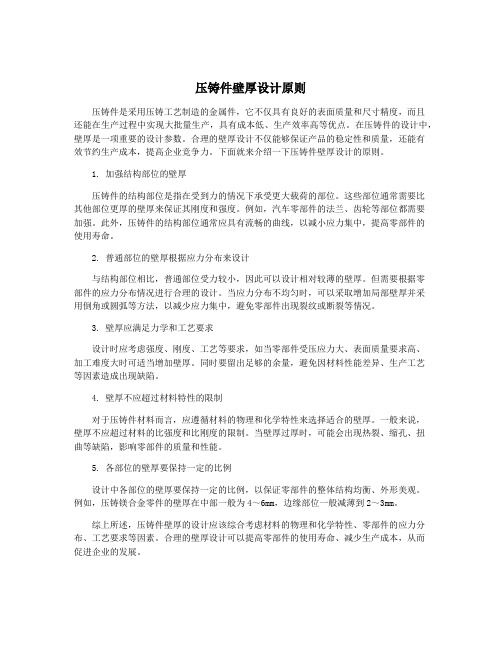
压铸件壁厚设计原则压铸件是采用压铸工艺制造的金属件,它不仅具有良好的表面质量和尺寸精度,而且还能在生产过程中实现大批量生产,具有成本低、生产效率高等优点。
在压铸件的设计中,壁厚是一项重要的设计参数。
合理的壁厚设计不仅能够保证产品的稳定性和质量,还能有效节约生产成本,提高企业竞争力。
下面就来介绍一下压铸件壁厚设计的原则。
1. 加强结构部位的壁厚压铸件的结构部位是指在受到力的情况下承受更大载荷的部位。
这些部位通常需要比其他部位更厚的壁厚来保证其刚度和强度。
例如,汽车零部件的法兰、齿轮等部位都需要加强。
此外,压铸件的结构部位通常应具有流畅的曲线,以减小应力集中,提高零部件的使用寿命。
2. 普通部位的壁厚根据应力分布来设计与结构部位相比,普通部位受力较小,因此可以设计相对较薄的壁厚。
但需要根据零部件的应力分布情况进行合理的设计。
当应力分布不均匀时,可以采取增加局部壁厚并采用倒角或圆弧等方法,以减少应力集中,避免零部件出现裂纹或断裂等情况。
3. 壁厚应满足力学和工艺要求设计时应考虑强度、刚度、工艺等要求,如当零部件受压应力大、表面质量要求高、加工难度大时可适当增加壁厚。
同时要留出足够的余量,避免因材料性能差异、生产工艺等因素造成出现缺陷。
4. 壁厚不应超过材料特性的限制对于压铸件材料而言,应遵循材料的物理和化学特性来选择适合的壁厚。
一般来说,壁厚不应超过材料的比强度和比刚度的限制。
当壁厚过厚时,可能会出现热裂、缩孔、扭曲等缺陷,影响零部件的质量和性能。
5. 各部位的壁厚要保持一定的比例设计中各部位的壁厚要保持一定的比例,以保证零部件的整体结构均衡、外形美观。
例如,压铸镁合金零件的壁厚在中部一般为4~6mm,边缘部位一般减薄到2~3mm。
综上所述,压铸件壁厚的设计应该综合考虑材料的物理和化学特性、零部件的应力分布、工艺要求等因素。
合理的壁厚设计可以提高零部件的使用寿命、减少生产成本,从而促进企业的发展。
压铸件结构设计规范
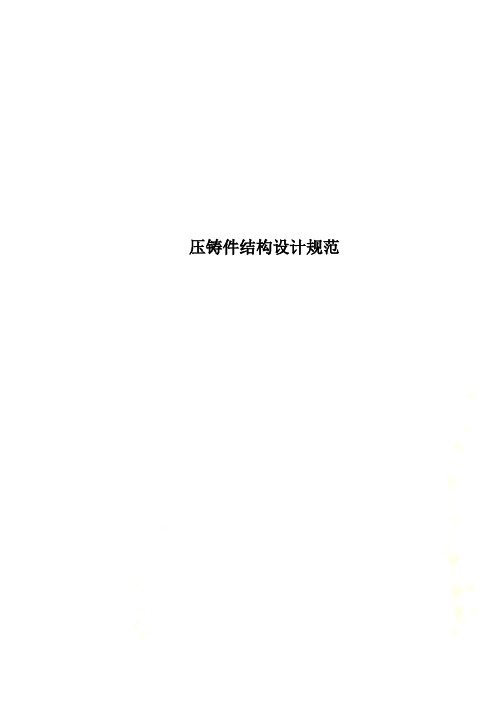
压铸件结构设计规范压铸件结构设计压铸件结构设计是压铸工作的第一步。
设计的合理性和工艺适应性将会影响到后续工作的顺利进行,如分型面选择、内浇口开设、推出机构布置、模具结构及制造难易、合金凝固收缩规律、铸件精度保证、缺陷的种类等,都会以压铸件本身工艺性的优劣为前提。
1、压铸件零件设计的注意事项⑴、压铸件的设计涉及四个方面的内容:a、即压力铸造对零件形状结构的要求;b、压铸件的工艺性能;c、压铸件的尺寸精度及表面要求;d、压铸件分型面的确定;压铸件的零件设计是压铸生产技术中的重要部分,设计时必须考虑以下问题:模具分型面的选择、浇口的开设、顶杆位置的选择、铸件的收缩、铸件的尺寸精度保证、铸件内部缺陷的防范、铸孔的有关要求、收缩变形的有关要求以及加工余量的大小等方面;⑵、压铸件的设计原则是:a、正确选择压铸件的材料;b、合理确定压铸件的尺寸精度;c、尽量使壁厚分布均匀;d、各转角处增加工艺园角,避免尖角。
⑶、压铸件分类按使用要求可分为两大类,一类承受较大载荷的零件或有较高相对运动速度的零件,检查的项目有尺寸、表面质量、化学成分、力学性能(抗拉强度、伸长率、硬度);另一类为其它零件,检查的项目有尺寸、表面质量及化学成分。
在设计压铸件时,还应该注意零件应满足压铸的工艺要求。
压铸的工艺性从分型面的位置、顶面推杆的位置、铸孔的有关要求、收缩变形的有关要求以及加工余量的大小等方面考虑。
合理确定压铸面的分型面,不但能简化压铸型的结构,还能保证铸件的质量。
⑷、压铸件结构的工艺性:1)尽量消除铸件内部侧凹,使模具结构简单。
2)尽量使铸件壁厚均匀,可利用筋减少壁厚,减少铸件气孔、缩孔、变形等缺陷。
3)尽量消除铸件上深孔、深腔。
因为细小型芯易弯曲、折断,深腔处充填和排气不良。
4)设计的铸件要便于脱模、抽芯。
5)肉厚的均一性是必要的。
6)避免尖角。
7)注意拔模角度。
8)注意产品之公差标注。
9)太厚太薄皆不宜。
10)避免死角倒角(能少则少)。
压铸件结构设计和压铸工艺
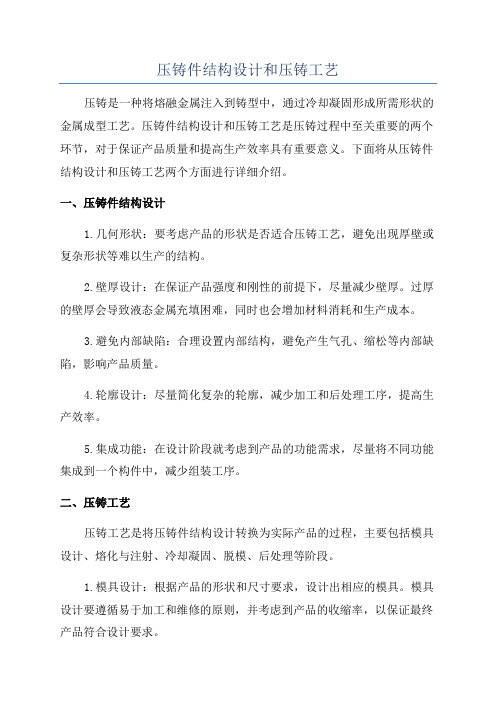
压铸件结构设计和压铸工艺压铸是一种将熔融金属注入到铸型中,通过冷却凝固形成所需形状的金属成型工艺。
压铸件结构设计和压铸工艺是压铸过程中至关重要的两个环节,对于保证产品质量和提高生产效率具有重要意义。
下面将从压铸件结构设计和压铸工艺两个方面进行详细介绍。
一、压铸件结构设计1.几何形状:要考虑产品的形状是否适合压铸工艺,避免出现厚壁或复杂形状等难以生产的结构。
2.壁厚设计:在保证产品强度和刚性的前提下,尽量减少壁厚。
过厚的壁厚会导致液态金属充填困难,同时也会增加材料消耗和生产成本。
3.避免内部缺陷:合理设置内部结构,避免产生气孔、缩松等内部缺陷,影响产品质量。
4.轮廓设计:尽量简化复杂的轮廓,减少加工和后处理工序,提高生产效率。
5.集成功能:在设计阶段就考虑到产品的功能需求,尽量将不同功能集成到一个构件中,减少组装工序。
二、压铸工艺压铸工艺是将压铸件结构设计转换为实际产品的过程,主要包括模具设计、熔化与注射、冷却凝固、脱模、后处理等阶段。
1.模具设计:根据产品的形状和尺寸要求,设计出相应的模具。
模具设计要遵循易于加工和维修的原则,并考虑到产品的收缩率,以保证最终产品符合设计要求。
2.熔化与注射:将所需的金属材料加热至液态,然后通过注射机将熔融金属注入到模具中。
注射过程需要控制注射速度和压力,保证金属充填完整且无气泡。
3.冷却凝固:在模具中进行冷却凝固,使注入的金属逐渐凝固。
冷却过程需要控制温度和时间,以保证产品的结晶组织均匀性和性能稳定性。
4.脱模:凝固后的产品从模具中取出,包括冷却水冲洗和振动脱模等工序。
脱模过程需要注意避免产品的变形和损坏。
5.后处理:包括修磨、去毛刺、清洗、表面处理等工序。
后处理旨在提高产品表面质量和机械性能,并满足特定的外观要求。
总结:压铸件结构设计和压铸工艺是相互关联的,一个合理的结构设计可以提高生产效率和产品质量,而一个良好的压铸工艺可以保证结构设计的实施效果。
因此,在进行压铸件结构设计和压铸工艺选择时,需要综合考虑产品的功能要求、材料特性、生产成本等因素,以达到最佳的工艺效果。
压铸件结构设计及压铸工艺

压铸件结构设计及压铸工艺压铸件结构设计是指在满足产品功能和使用要求的前提下,通过合理地设计压铸件的结构,使得其具有较好的可靠性、经济性和工艺性。
压铸工艺是将熔化的金属经过高压注入模具中,经冷却固化后得到所需形状和尺寸的工艺过程。
1.功能需求:首先需要明确产品的功能需求,包括产品所需的力学性能、流体性能、电气性能等。
根据功能需求来确定结构形状和尺寸。
2.材料选择:根据产品使用环境和功能需求,选择合适的材料。
材料的选择会影响到压铸件的结构设计。
3.结构强度:压铸件在使用过程中需要承受一定的载荷,因此要考虑结构的强度和刚度问题。
通过合理的布局和加强设计,保证产品在正常使用情况下不会发生失效。
4.成本控制:在结构设计中要考虑到成本因素,通过优化设计和合理选择材料等方式,尽量降低制造成本。
5.工艺性:结构设计需要考虑到压铸工艺的要求。
例如,制造过程中是否需要加工孔、缝隙等,模具是否能够顺利铸造等。
要尽量避免设计上的复杂性,方便生产制造。
压铸工艺是将熔化的金属通过高压注入模具中,并在固化后得到所需形状和尺寸的工艺过程。
压铸工艺一般包括以下几个步骤:1.模具设计:根据压铸件的结构和尺寸要求,设计合适的模具。
模具需要具备良好的冷却性能和顺畅的金属流动性。
2.材料准备:根据产品要求选择合适的金属材料,并进行熔化和调质处理。
熔化后的金属要满足一定的温度和流动性要求。
3.注入模具:将熔化的金属注入到模具中,通过高压力使金属充填模具腔体,保证细节部位的填充。
4.冷却固化:金属在模具中冷却并固化,使其具备一定的力学性能和稳定性。
5.取出铸件:打开模具,将固化好的压铸件取出,并清理剩余的模具材料。
6.补充工艺:根据产品需求,可能需要进行后续的加工和处理工艺,比如热处理、表面处理、组装等。
压铸工艺的选择和优化对产品的质量和成本具有重要影响。
在工艺中需要考虑的因素有:1.注射参数:包括注射速度、注射压力、注射温度等。
这些参数会影响到铸件的成形和凝固过程。
压铸件结构设计规范
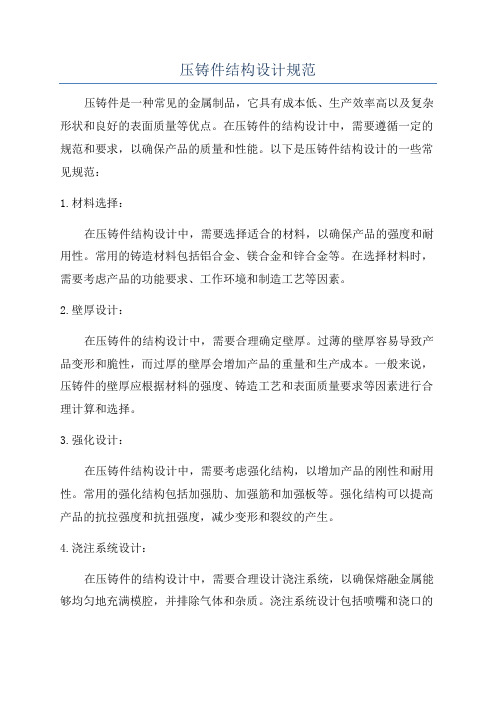
压铸件结构设计规范压铸件是一种常见的金属制品,它具有成本低、生产效率高以及复杂形状和良好的表面质量等优点。
在压铸件的结构设计中,需要遵循一定的规范和要求,以确保产品的质量和性能。
以下是压铸件结构设计的一些常见规范:1.材料选择:在压铸件结构设计中,需要选择适合的材料,以确保产品的强度和耐用性。
常用的铸造材料包括铝合金、镁合金和锌合金等。
在选择材料时,需要考虑产品的功能要求、工作环境和制造工艺等因素。
2.壁厚设计:在压铸件的结构设计中,需要合理确定壁厚。
过薄的壁厚容易导致产品变形和脆性,而过厚的壁厚会增加产品的重量和生产成本。
一般来说,压铸件的壁厚应根据材料的强度、铸造工艺和表面质量要求等因素进行合理计算和选择。
3.强化设计:在压铸件结构设计中,需要考虑强化结构,以增加产品的刚性和耐用性。
常用的强化结构包括加强肋、加强筋和加强板等。
强化结构可以提高产品的抗拉强度和抗扭强度,减少变形和裂纹的产生。
4.浇注系统设计:在压铸件的结构设计中,需要合理设计浇注系统,以确保熔融金属能够均匀地充满模腔,并排除气体和杂质。
浇注系统设计包括喷嘴和浇口的位置、大小和形状等因素。
合理的浇注系统设计可以提高产品的充型性能和表面质量。
5.模具设计:在压铸件结构设计中,需要合理设计模具,以确保产品的精度和一致性。
模具设计包括型腔结构、型芯结构和冷却系统等。
合理的模具设计可以减少缺陷和变形的产生,提高产品的尺寸精度和表面质量。
综上所述,压铸件的结构设计需要遵循一定的规范和要求,以确保产品的质量和性能。
这些规范包括材料选择、壁厚设计、强化设计、浇注系统设计和模具设计等。
通过合理设计和优化,可以提高产品的制造效率、降低成本,并满足不同应用领域的需求。
压铸件设计规范

压铸件设计规范相关知识压铸件设计规范相关知识一、壁厚压铸件的壁厚对铸件质量有很大的影响。
以铝合金为例,薄壁比厚壁具有更高的强度和良好的致密性。
因此,在保证铸件有足够的强度和刚性的条件下,应尽可能减少其壁厚,并保持壁厚均匀一致。
铸件壁太薄时,使金属熔接不好,影响铸件的强度,同时给成型带来困难;壁厚过大或严重不均匀则易产生缩瘪及裂纹。
随着壁厚的增加,铸件内部气孔、缩松等缺陷也随之增多,同样降低铸件的强度。
压铸件的壁厚一般以2.5~4mm为宜,壁厚超过6mm的零件不宜采用压铸。
推荐采用的最小壁厚和正常壁厚见表1。
表1 压铸件的最小壁厚和正常壁厚二、铸造圆角和脱模斜度1)铸造圆角压铸件各部分相交应有圆角(分型面处除外),使金属填充时流动平稳,气体容易排出,并可避免因锐角而产生裂纹。
对于需要进行电镀和涂饰的压铸件,圆角可以均匀镀层,防止尖角处涂料堆积。
压铸件的圆角半径R一般不宜小于1mm,最小圆角半径为0.5 mm,见表2。
铸造圆角半径的计算见表3。
表2 压铸件的最小圆角半径(mm)我司现采用的圆角一般取R1.5。
表3 铸造圆角半径的计算(mm)说明:①、对锌合金铸件,K=1/4;对铝、镁、合金铸件,K=1/2。
②、计算后的最小圆角应符合表2的要求。
2) 脱模斜度设计压铸件时,就应在结构上留有结构斜度,无结构斜度时,在需要之处,必须有脱模的工艺斜度。
斜度的方向,必须与铸件的脱模方向一致。
推荐的脱模斜度见表4。
表4 脱模斜度说明:①、由此斜度而引起的铸件尺寸偏差,不计入尺寸公差值内。
②、表中数值仅适用型腔深度或型芯高度≤50mm,表面粗糙度在Ra0.1,大端与小端尺寸的单面差的最小值为0.03mm。
当深度或高度>50mm,或表面粗糙度超过Ra0.1时,则脱模斜度可适当增加。
我司现采用的脱模斜度一般取1.5°。
一般采用的加强筋的尺寸按图1选取:t1=2 t /3~t;t2=3 t /4~t;R≥t/2~t;h≤5t;r≤0.5mm(t—压铸件壁厚,最大不超过6~8mm)。
简述压铸件的结构工艺性及工艺设计

简述压铸件的结构工艺性及工艺设计1.压铸件的结构工艺性合理的铸件结构外形,应使压铸型结构简化,加工制造便利,不易形成铸造缺陷,有利于保证铸件质量。
压铸件外形和结构上应使铸件能顺当从压铸型中取出,影响取出铸件的障碍,应改进其结构加以消退。
压铸生产中,几乎全部压铸工艺参数都与铸件壁厚有关。
壁厚过厚,易产生气孔、缩孔及缩松等缺陷;若壁厚过薄,易产生表面缺陷,甚至浇不足。
允许最小的壁厚依合金种类及铸件单面表面积的大小而定。
2.压铸件的工艺设计压铸件工艺设计是压铸型设计前必需做的工作,其内容许多,除制订工艺方案外,还要确定一系列的工艺参数和详细细节。
1)压铸件分型面的选择分型面的确定对于压铸型的简单程度和加工制度是否便利,以及铸件质量(尤其是尺寸精度)都有很大影响。
因此,对分型面的选择有如下要求:分型面应取在铸件的最大截面上,且在开型时,应使铸件留在动型内;浇注系统和排气系统能够得到合理的分布;尺寸精度要求高的部分尽可能位于同一半型内,使压铸型尽可能简化。
对某一详细铸件而言,设计者应在全面考虑、权衡轻重后选择铸件的分型面。
2)压铸件浇注系统的设计浇注系统一般由直浇道、内浇口和横浇道等组成。
依据压铸机的类型及引入液体金属的方式不同,浇注系统的形式也有所不同。
图5-52示出了同一铸件在不同类型压铸机上的浇注系统结构。
(1)直浇道的设计。
典型的立式冷压室压铸机上的铸件直浇道由喷嘴、浇口套和定型上的相应孔洞形成。
每台压铸机上常有几种内孔直径的喷嚏,而形成直浇道金属喷喷入口处的直径依据压铸件金属的种类和经喷嘴被压射金属的质量进行选择。
太粗的直浇道会铺张金属液,还会引起铸型局部过热。
太细的直浇道会提高压铸时金属液在浇道中的流速,有可能冲刷下在浇口套壁上初凝的金属层进入型腔堵塞内浇口使金属液充型不畅。
(2)内浇口的设计。
一般在大多数压铸型中,内浇口都设在分型面上,应尽可能削减金属液充型过程中可能遇到的障碍,在压铸螺纹时,应使浇口顺着螺纹方向,对圆环形铸件采纳切向浇口,设置内浇口位置时应留意使金属流的方向与型腔捧气方向全都,且不应引起铸件变形。
详解压铸零件结构设计-精

压铸件设计规范目录铸圆脱铸缘压铸压铸内压铸压铸级压铸压铸一、壁厚1、压铸件的壁厚对铸件质量有很大的影响。
以铝合金为例,薄壁比厚壁具有更高的强度和良好的致密性。
因此,在保证铸件有足够的强度和刚性的条件下,应尽可能减少其壁厚,并保持壁厚均匀一致。
2、铸件壁太薄时,使金属熔接不好,影响铸件的强度,同时给成型带来困难;壁厚过大或严重不均匀则易产生缩瘪及裂纹。
厚壁压铸件,其壁中心层的晶粒粗大,易产生缩孔、缩松等缺陷,同样降低铸件的强度。
3、压铸件的壁厚一般以2.5~4mm为宜,同一压铸件内昀大壁厚与昀小壁厚之比不要大于3∶1,壁厚超过6mm的零件不宜采用压铸。
推荐值见表1。
我司的铝压铸件,按如下要求选取壁厚:散热齿一般取2.0~2.5mm,(自然散热)间距取10~12mm,(强迫风冷)间距取8~10mm.其余壁厚取4.5~5.0mm;螺纹孔为M3的PCB支撑柱,直径取6.5~7.5mm;接地螺纹孔处的壁厚取:M4 9.5~10.5mm, M5 10.5~11mm。
表1 压铸件的最小壁厚和正常壁厚二、铸造圆角和脱模斜度1、铸造圆角压铸件各部分相交应有圆角(分型面处除外),使金属填充时流动平稳,气体容易排出,并可避免因锐角而产生裂纹。
对于需要进行电镀和涂饰的压铸件,圆角可以均匀镀层,防止尖角处涂料堆积。
压铸件的圆角半径R一般不宜小于1mm,最小圆角半径为0.5 mm,见表2。
铸造圆角半径的计算见表3。
我司铝压铸件的圆角一般取R1.0mm,无配合处最小取R3.0mm(有外观要求的除外)。
表2 压铸件的最小圆角半径(mm)①、对锌合金铸件,K=1/4;对铝、镁合金铸件, K=1/2。
②、计算后的最小圆角应符合表2的要求。
表3 铸造圆角半径的计算(mm)2、脱模斜度设计压铸件时,就应在结构上留有脱模斜度,无脱模斜度时,在需要之处,必须有脱模的工艺斜度。
斜度的方向,必须与铸件的脱模方向一致。
推荐的脱模斜度见表4。
我司现采用的脱模斜度一般取前模1.5°,后模1.0°。
压铸件结构设计规范方案

压铸件结构设计规范方案压铸件是一种常见的金属制品,广泛应用于汽车、电子、航空航天、军工等领域。
在压铸件的结构设计中,需要考虑安全性、可靠性、质量控制和经济性等多个方面的要求。
下面是一些压铸件结构设计的规范方案:1.结构设计原则:设计师应遵循结构设计的基本原则,包括坚固性、合理性和安全性。
压铸件在使用过程中需经受各种力的作用,因此结构需要具有足够的强度和刚度,同时保持合理的重量和尺寸,以确保产品的性能和可靠性。
2.材料选择:压铸件一般使用铝合金、镁合金和锌合金制造,根据具体使用条件和要求选择适合的材料。
在材料选择过程中,需要考虑材料的特性、成本、可塑性以及耐磨性等因素。
3.壁厚设计:压铸件的壁厚对于产品的强度和质量至关重要。
过厚的壁厚会增加材料的用量和制造成本,同时也会降低产品的制造精度和性能;而过薄的壁厚会导致产品强度不足,容易发生变形和破裂。
因此,壁厚的设计需要综合考虑产品的用途和要求,确保最佳的壁厚。
4.结构设计和冷却系统设计:压铸件在制造过程中需要通过冷却系统进行冷却,以确保产品的质量和性能。
合理的结构设计和冷却系统设计可以提高产品的制造精度和表面质量,减少材料的收缩和变形,同时也可以确保冷却介质的循环流动,提高冷却效果。
5.模具设计:压铸件的形状和尺寸需要通过模具来实现。
模具设计需要考虑产品的尺寸、形状、结构和材料特性等多个因素,确保产品可以准确复制并保持良好的质量。
同时,模具设计也需要考虑到产品的成本和制造工艺的可行性。
6.表面处理和热处理:压铸件在制造完成后需要进行表面处理,以提高产品的表面质量和耐腐蚀性。
表面处理可以选择镀铬、喷涂、阳极氧化等方式,根据产品的具体要求进行选择。
另外,部分压铸件还需要进行热处理,以改善材料的性能和强度。
7.质量控制:压铸件的质量控制是确保产品质量和性能的重要环节。
在生产过程中,需要对原材料、模具和工艺进行严格的检验和控制,以确保产品的符合设计要求。
同时,还需要建立完善的质量管理体系和检验机制,对成品进行检验和测试,以确保产品的质量和可靠性。
铝合金压铸件产品结构设计要点

铝合金压铸件的结构设计要点简介为了提升铝合金铸件产品研发的合格率,在结构设计、开发时应注意以下几方面的内容:铸件壁厚相差不能过大,厚度的差距过大会对填充带来影响,且一般浇口部分的肉厚要大于零件的平均肉厚,目的是减少多铝液的压力损失;脱模问题,这点在压铸过程中非常重要,现实中脱模往往容易出现问题,这比注塑脱模麻烦多了,所以拔模斜度的设置和动定模脱模力的计算要注意些,一般拔模斜度为1°~3°,通常考虑到脱模的顺利性,外拔模要比内拔模的斜度要小些,外拔模1°,而内拔模要2°~3°左右。
设计时考虑到模具设计的问题,如果有多个位置的抽芯位,尽量放两边,最好不要放在下位抽芯,这样时间长了下抽芯会容易出问题;有些压铸件外观可能会有特殊的要求,如喷油、喷粉等,这时就要使结构上避开重要外观位置,便于设置浇口溢流槽;在结构上尽量的避免出现导致模具结构复杂的情况出现,如不得不使用多个抽芯或螺旋抽芯等。
对于需进行表面加工的零件,在零件设计时给适合的加工留量,不能太多,会把里面的气孔都暴露出来的;不能太少,否则粗精定位一加工,黑皮还没加工掉,你就等再在模具上打火花了,留量最好不要大于0.8mm,这样加工出来的面基本看不到气孔的,因为有硬质层的保护。
选料应注意选用ADC12还是A380等,但同时也要看具体的要求——销往法国的铝压铸件,如果有FDA的要求,就不能用ADC-12,须用ADC-3T代替;铝合金没有弹性,要做扣位只有和塑料配合。
一般不能做深孔,在开模具时只做点孔,然后在后加工;如果是薄壁件,不能太薄,而且一定要用加强肋,增加抗弯能力。
由于铝铸件的温度要在800摄氏度左右,模具寿命一般比较短,如电机外壳一般只有80K左右;压铸件的设计与塑胶件的设计比较相似,塑胶件的一些设计常规也适用于压铸件,压铸模具一般是不允许靠破的。
对于铝合金,模具所受温度和压力比塑胶的大很多,对设计的正确性要求特严,即使很好的模具材料,一旦有焊接,模具就几乎无寿命可言,锌合金跟塑胶差不多,模具寿命较好;不能有凹的尖角,避免模具崩角。
压铸件设计指南(两篇)2024
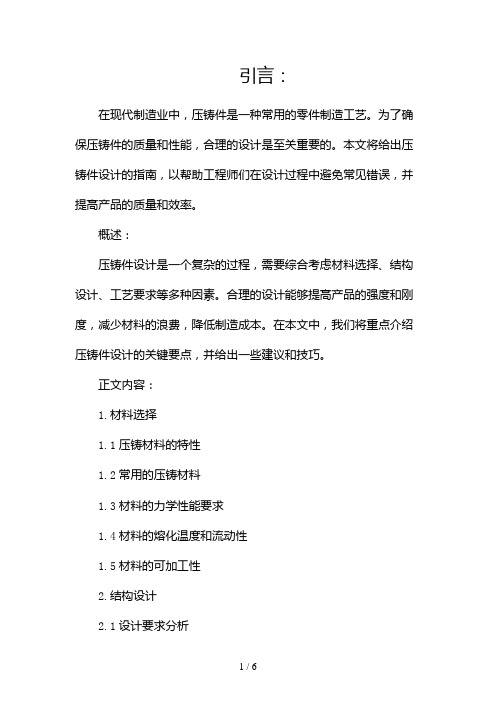
引言:在现代制造业中,压铸件是一种常用的零件制造工艺。
为了确保压铸件的质量和性能,合理的设计是至关重要的。
本文将给出压铸件设计的指南,以帮助工程师们在设计过程中避免常见错误,并提高产品的质量和效率。
概述:压铸件设计是一个复杂的过程,需要综合考虑材料选择、结构设计、工艺要求等多种因素。
合理的设计能够提高产品的强度和刚度,减少材料的浪费,降低制造成本。
在本文中,我们将重点介绍压铸件设计的关键要点,并给出一些建议和技巧。
正文内容:1.材料选择1.1压铸材料的特性1.2常用的压铸材料1.3材料的力学性能要求1.4材料的熔化温度和流动性1.5材料的可加工性2.结构设计2.1设计要求分析2.2模具结构设计2.3壁厚和浇注系统设计2.4冷却系统设计2.5零件的尺寸和公差控制3.工艺要求3.1压铸工艺流程3.2压铸机选择和设置3.3涂料和涂层选择3.4表面处理要求3.5检测和检验标准4.模具设计4.1模具材料选择4.2模具结构设计4.3模具加工和装配4.4模具寿命和维护4.5模具的修复和更换5.产品质量控制5.1压铸件的缺陷和问题5.2检测和排除缺陷5.3压铸件的可靠性分析5.4数据分析和改进措施5.5持续改进和质量管理总结:压铸件设计是一个综合性的工程,需要工程师充分了解材料特性、结构设计、工艺要求等方面的知识。
通过本文所介绍的指南,希望能够帮助工程师们在设计过程中避免常见错误,并提高产品的质量和效率。
压铸件设计的关键在于合理选材、结构良好,并满足工艺要求,从而确保产品的可靠性和持久性。
引言概述压铸件是一种常用于生产各种复杂形状金属零件的工艺,具有精度高、成本低、效率高等优点。
在进行压铸件设计时,需要考虑多个因素,包括材料选择、模具设计、压力与温度控制等。
本文将详细介绍压铸件设计的指南,包括结构设计、形状设计、材料选择、模具设计和工艺控制。
正文内容1. 结构设计a. 了解产品要求:在进行结构设计前,需要全面了解产品的功能需求、强度要求、装配要求等,以确保压铸件的结构设计符合实际需求。
- 1、下载文档前请自行甄别文档内容的完整性,平台不提供额外的编辑、内容补充、找答案等附加服务。
- 2、"仅部分预览"的文档,不可在线预览部分如存在完整性等问题,可反馈申请退款(可完整预览的文档不适用该条件!)。
- 3、如文档侵犯您的权益,请联系客服反馈,我们会尽快为您处理(人工客服工作时间:9:00-18:30)。
压铸件结构设计压铸件结构设计是压铸工作的第一步。
设计的合理性和工艺适应性将会影响到后续工作的顺利进行,如分型面选择、内浇口开设、推出机构布置、模具结构及制造难易、合金凝固收缩规律、铸件精度保证、缺陷的种类等,都会以压铸件本身工艺性的优劣为前提。
1、压铸件零件设计的注意事项⑴、压铸件的设计涉及四个方面的内容:a、即压力铸造对零件形状结构的要求;b、压铸件的工艺性能;c、压铸件的尺寸精度及表面要求;d、压铸件分型面的确定;压铸件的零件设计是压铸生产技术中的重要部分,设计时必须考虑以下问题:模具分型面的选择、浇口的开设、顶杆位置的选择、铸件的收缩、铸件的尺寸精度保证、铸件内部缺陷的防范、铸孔的有关要求、收缩变形的有关要求以及加工余量的大小等方面;⑵、压铸件的设计原则是:a、正确选择压铸件的材料;b、合理确定压铸件的尺寸精度;c、尽量使壁厚分布均匀;d、各转角处增加工艺园角,避免尖角。
⑶、压铸件分类按使用要求可分为两大类,一类承受较大载荷的零件或有较高相对运动速度的零件,检查的项目有尺寸、表面质量、化学成分、力学性能(抗拉强度、伸长率、硬度);另一类为其它零件,检查的项目有尺寸、表面质量及化学成分。
在设计压铸件时,还应该注意零件应满足压铸的工艺要求。
压铸的工艺性从分型面的位置、顶面推杆的位置、铸孔的有关要求、收缩变形的有关要求以及加工余量的大小等方面考虑。
合理确定压铸面的分型面,不但能简化压铸型的结构,还能保证铸件的质量。
⑷、压铸件结构的工艺性:1)尽量消除铸件内部侧凹,使模具结构简单。
2)尽量使铸件壁厚均匀,可利用筋减少壁厚,减少铸件气孔、缩孔、变形等缺陷。
3)尽量消除铸件上深孔、深腔。
因为细小型芯易弯曲、折断,深腔处充填和排气不良。
4)设计的铸件要便于脱模、抽芯。
5)肉厚的均一性是必要的。
6)避免尖角。
7)注意拔模角度。
8)注意产品之公差标注。
9)太厚太薄皆不宜。
10)避免死角倒角(能少则少)。
11)考虑后加工的难易度。
12)尽量减少产品内空洞。
13)避免有半岛式的局部太弱的形状。
14)太长的成形孔,或太长的成形柱皆不宜。
2、压铸件零件设计⑴、压铸件的形状结构a、消除内部侧凹;b、避免或减少抽芯部位;c、避免型芯交叉;合理的压铸件结构不仅能简化压铸型的结构,降低制造成本,同时也改善铸件质量。
⑵、壁厚压铸件的壁厚对铸件质量有很大的影响。
以铝合金为例,薄壁比厚壁具有更高的强度和良好的致密性。
因此,在保证铸件有足够的强度和刚性的条件下,应尽可能减少其壁厚,并保持壁厚均匀一致。
铸件壁太薄时,使金属熔接不好,影响铸件的强度,同时给成型带来困难;壁厚过大或严重不均匀则易产生缩瘪及裂纹。
随着壁厚的增加,铸件内部气孔、缩松等缺陷也随之增多,同样降低铸件的强度。
压铸件的壁厚一般以2.5~4mm为宜,壁厚超过6mm的零件不宜采用压铸。
推荐采用的最小壁厚和正常壁厚见表1。
压铸件壁厚度(通常称壁厚)是压铸工艺中一个具有特殊意义的因素,壁厚与整个工艺规范有着密切关系,如填充时间的计算、内浇口速度的选择、凝固时间的计算、模具温度梯度的分析、压力(最终比压)的作用、留模时间的长短、铸件顶出温度的高低及操作效率;a、零件壁厚偏厚会使压铸件的力学性能明显下降,薄壁铸件致密性好,相对提高了铸件强度及耐压性;b、铸件壁厚不能太薄,太薄会造成铝液填充不良,成型困难,使铝合金熔接不好,铸件表面易产生冷隔等缺陷,并给压铸工艺带来困难;压铸件随壁厚的增加,其内部气孔、缩孔等缺陷增加,故在保证铸件有足够强度和刚度的前提下,应尽量减小铸件壁厚并保持截面的厚薄均匀一致,为了避免缩松等缺陷,对铸件的厚壁处应减厚(减料),增加筋;对于大面积的平板类厚壁铸件,设置筋以减少铸件壁厚。
1)压铸件壁厚与性能有关。
2)压铸件壁厚影响金属液填充型腔状态,最终影响铸件表面质量。
3)压铸件壁厚影响金属料消耗及成本。
在设计压铸件时,往往为保证强度和刚度的可靠性,以为壁越厚性能越好;实际上对于压铸件来说,随着壁厚增加,力学性能明显下降。
原因是在压铸过程中,当金属液以高压、高速的状态进入型腔,与型腔表面接触后很快冷却凝固。
受到激冷的压铸件表面形成一层细晶粒组织。
这层致密的细晶粒组织的厚度约为0.3m左右,因此薄壁压铸件具有更高的机械性能。
相反,厚壁压铸件中心层的晶粒较大,易产生内部缩孔、气孔,外表面凹陷等缺陷,使压铸件的机械性能随着壁厚的增加而降低。
随着壁厚的增加,金属料消耗多,成本也增加。
但如果单从结构性计算出最小壁厚,而忽略了铸件的复杂程度时,也会造成液态金属充填型腔状态不理想,产生缺陷。
在满足产品使用功能要求前提下,综合考虑各后工序过程的影响,以最低的金属消耗取得良好的成型性和工艺性,以采取正常、均匀的壁厚为佳。
⑶、铸造圆角压铸件各部分相交应有圆角(分型面处除外),使金属填充时流动平稳,气体容易排出,并可避免因锐角而产生裂纹。
对于需要进行电镀和涂饰的压铸件,圆角可以均匀镀层,防止尖角处涂料堆积。
压铸件的圆角半径R一般不宜小于1mm,最小圆角半径为0.5 mm,见表2。
铸造圆角半径的计算见表3。
缺陷。
特别是压铸件需要电镀处理时,圆角对于保证其良好的电镀效果是十分必要的。
⑷、拔模斜度设计压铸件时,就应在结构上留有结构斜度,无结构斜度时,在需要之处,必须有脱模的工艺斜度。
斜度的方向,必须与铸件的脱模方向一致。
推荐的脱模斜度见表4。
②、表中数值仅适用型腔深度或型芯高度≤50mm,表面粗糙度在Ra0.1,大端与小端尺寸的单面差的最小值为0.03mm。
当深度或高度>50mm,或表面粗糙度超过Ra0.1时,则脱模斜度可适当增加。
斜度作用是减少铸件与模具型腔的摩擦,容易取出铸件;保证铸件表面不拉伤;延长压铸模使用寿命,为了顺利脱模,减少推出力、抽芯力,减少模具损耗,在设计压铸件时,应在结构上有尽可能大的斜度。
从而减少压铸件与模具的摩擦,容易取出铸件,也使铸件表面不被拉伤,保证表面光洁。
⑸、加强筋加强筋的设置可以增加零件的强度和刚性,同时改善了压铸的工艺性。
但须注意:① 分布要均匀对称;② 与铸件连接的根部要有圆角; ③ 避免多筋交叉;④ 筋宽不应超过其相连的壁的厚度。
当壁厚小于 1.5mm 时,不宜采用加强筋; ⑤ 加强筋的脱模斜度应大于铸件内腔所允许的铸造斜度。
图1大于或等于设计原则:1、受力大,减小壁厚,改善强度。
2、对称布置,壁厚均匀,避免缩孔气孔。
3、与料流方向一致,避免乱流。
4、避免在肋上设置任何零部件。
筋的作用是壁厚改薄后,用以提高零件的强度和刚性,防止减少铸件收缩变形,以及避免工件从模具内顶出时发生变形,填充时用以作用辅助回路(金属流动的通路),压铸件筋的厚度应小于所在壁的厚度,一般取该处的厚度的2/3~3/4。
压铸件倾向采用均匀的薄壁,为了提高其强度和刚性,防止变形,不应单纯用增加壁厚的方法,而应采用适当的薄壁加强筋达此目的。
加强筋应对称布置,厚度均匀,避免新的金属堆聚。
为减少脱模时的阻力,加强筋应有铸造斜度。
⑹、压铸孔和孔到边缘的最小距离1)铸孔压铸件的孔径和孔深,对要求不高的孔可以直接压出,按表5。
表②、对于较大的孔径,精度要求不高时,孔的深度亦可超出上述范围。
铸件的孔应尽量铸出,这不仅可使壁厚均匀,减少热节,节约金属,而且可节省机加工工时。
压铸件可压铸出的孔的最小尺寸和深度,受到形成孔的型芯在型腔中的分布位置的制约。
细型芯在抽出时易弯曲或折断,因此孔的最小尺寸和深度受到一定限制。
其深度应带有一定斜度,以便于抽芯。
对于压铸件自攻螺钉用的底孔,推荐采用的底孔直径见表6。
表6 自攻螺钉用底孔直径(mm )2) 为了保证铸件有良好的成型条件,2。
图2b ≥(1/4~1/3)t当t <4.5时,b ≥1.5mm 3) 长方形孔和槽压铸件上的长方形孔和槽的设计推荐按表7 采用。
⑺、文字、标志、图案1)用压铸铸出,应采用凸纹。
凸纹高度大于0.3m ,以适应模具制造的特点。
2)采用目前开始流行的新技术:“转移彩膜”,可将彩色的文字、标志、图案彩膜转印到压铸件表面。
3)压铸出铸件后,用激光在铸件表面打出文字、标志、图案,可以打出非常细微的文字。
例:平行纹(直纹)高0.7MM ﹐间距1MM ﹐角度60.5。
外径Φ34.5mm 共104牙。
⑻、收缩率收缩率通常称为缩水。
它是指合金由液态凝固为固态,并冷却至室温时尺寸缩小的百分数,可用下式表示:K=(L 模-L 件)/L 件式中:L 模为模腔尺寸,L 件为铸件尺寸。
收缩率的大小与压铸件的结构特点、壁厚、合金的化学成分和工艺因素等有关。
锌合金的线收缩率一般为:自由收缩时取0.6%~0.8%,受阻收缩时取0.3%~0.6%。
表5为有型芯的锌合金压铸件不同壁厚时的线收缩率参考值。
⑼、螺纹1)外螺纹可以铸出,由于铸件或模具结构的需要,采用两半分型的螺纹型环时,需留有0.2~0.3mm加工余量。
可铸出的最小螺距为0.75mm,最小螺纹外径6mm,最大螺纹长为螺距的8倍。
2)内螺纹虽然可以铸出,但要通过使用机械装置转动压铸模中的型芯,使模具结构更复杂,而增加成本。
所以一般先铸出底孔,再由机械加工成内螺纹。
合金最小螺距(P)最小螺纹外径最大螺纹长度锌0.75外内外内6 10 8P 5P铝 1 10 20 6P 4P ⑽、齿轮齿轮可以铸出,锌合金压铸齿轮最小模数m为0.3。
对要求高的齿轮齿面应留有0.2~0.3mm的加工余量。
⑾、表皮铸态零件其外表面有致密的激冷表皮层比铸件其它部分有较高的力学性能。
因此设计者应避免机械加工去掉铸件表皮致密层,尤其是对要求耐磨的铸件。
⑿、嵌件压铸件内采用嵌件的目的:①改善和提高铸件上局部的工艺性能,如强度、硬度、耐磨性等;②铸件的某些部分过于复杂,如孔深、内侧凹等无法脱出型芯而采用嵌件;③可以将几个部件铸成一体。
设计带嵌件的压铸件的注意事项:①嵌件与压铸件的连接必须牢固,要求在嵌件上开槽、凸起、滚花等;②嵌件必须避免有尖角,以利安放并防止铸件应力集中;③必须考虑嵌件在模具上定位的稳固性,满足模具内配合要求;④外包嵌件的金属层不应小于1.5~2mm;⑤铸件上的嵌件数量不宜太多;⑥铸件和嵌件之间如有严重的电化腐蚀作用,则嵌件表面需要镀层保护;⑦有嵌件的铸件应避免热处理,以免因两种金属的相变而引起体积变化,使嵌件松动。
当设计要求将不同材料的零件组合成一个部件时,可采用插入件压铸,先把嵌件装放到压铸模型腔内,然后在嵌件周围压铸成形锌合金部件。
⒀、功能组合在进行产品设计中,降低成本最有效的方法是将几个零件组合成一个压铸件。
图4是一个设计典范,原设计的部件由一个钢冲压件和两个带螺纹的机加工钢件组成。
新设计是一个压铸件。
⒁、压铸件的加工余量压铸件由于尺寸精度或形位公差达不到产品图纸要求时,应首先考虑采用精整加工方法,如校正、拉光、挤压、整形等。