铸造缺陷(气孔与缩孔PPT课件
铸件缺陷分析PPT课件

铸件在凝固末期或刚凝固 后不久产生的裂纹。
03
铸件缺陷形成原因及机理分析
原材料因素
原材料质量
使用不合格或质量差的原材料, 如废钢、生铁等,其中含有的杂 质元素和气体可能导致铸件缺陷 。
原材料配比
原材料配比不合理,如碳、硅等 元素含量过高或过低,会影响铸 件的凝固过程和机械性能。
熔炼工艺因素
熔炼温度
介绍了常用的铸件缺陷检测与评估方法,如目视检查、无损检测、 金相分析等,以及各种方法的优缺点和适用范围。
缺陷预防与控制措施
重点讲解了铸件缺陷的预防和控制措施,包括优化铸造工艺、提高原 材料质量、加强过程监控等方面。
学员心得体会分享
知识收获
学员们表示通过本次课程,对铸件缺陷的类型、成因、检 测与评估方法有了更深入的了解,对铸件质量控制的重要 性有了更深刻的认识。
其他可能影响因素
生产环境
生产环境中的温度、湿度和清洁度等因素对铸件质量也有一 定影响。例如,湿度过高可能导致型砂粘结力下降,温度过 高则可能导致铁液冷却速度过快。
操作技能
操作工人的技能水平和经验对铸件质量也有重要影响。例如 ,合箱时定位不准确、浇注时铁液温度控制不当等都可能导 致铸件缺陷。
04
铸件缺陷预防措施与改进方法
控制熔炼温度
根据原材料成分和熔炼设备特点, 合理设置熔炼温度,避免过高或 过低的熔炼温度对铸件质量产生 不良影响。
调整化学成分
通过添加合金元素和调整废钢、生 铁等原材料的配比,控制铁水的化 学成分,提高铸件的力学性能和耐 蚀性。
减少熔炼杂质
采取过滤、除渣等措施,减少熔炼 过程中产生的氧化物、硫化物等杂 质,提高铁水的纯净度。
夹渣和夹杂物
01属夹杂物,夹杂 物则是金属或非金属杂质。
铸造缺陷组织缺陷PPT.

4、铁水的炉前处理 (1)、头部受伤后台有头晕、头痛、呕吐等症状,可能是脑震荡。这时应让病人安静平躺,头放平,头部冷敷,2~3小时内不给饮食
24
(四)防止对策: 1、适当降低碳当量; 2、合金化;均匀化。 3、孕育处理; 4、适当降低浇注温度; 5、改善铸件的温度场(如放冷铁)
25
六、魏氏石墨 (一)特征: 1、同共晶片状石墨是相互连接的; 2、石墨片延伸至珠光体基体中; 3、石墨片极薄,其厚度只有1800Å
(1.8×10-ቤተ መጻሕፍቲ ባይዱm) (二)危害:力学性能下降一半。 (三)形成原因:Pb、 H2、Al。 (四)防止对策:减少Pb、 H2、Al。
26
组织缺陷
2、说说有毒无毒蛇的区别:形态上,齿痕上。(放幻灯) 面试者需要了解空缺岗位与现有岗位之间的关联,它在整个单位结构中的位置,在现有团队工部门中的作用,新来的人将向谁汇报工 作,谁又向他汇报工作等。 二、 教学过程:
,在脑中整理出一套与客户交流的方案。 紧张,打哈欠等不良习惯具有感染性,所以有时通过观察应聘者的形体语言就可以知道你自己的形体语言如何。
2)铸型紧实度、吃砂量 大家都知道,车辆油漆的光洁度非常高,车门把手上面都是镀铬的,比较亮,只要手触摸到门把手或车身,马上会留下指纹。销售人
员在展厅里面工作的时候,随时随地要保持展车的规范清洁性。 我们要安全合理地使用体育器材。
石墨的形态: 5
1、分布特征 均匀无向性分布
2、形成条件 1)共晶成分(亚共 晶) 2)冷速较慢
3、对性能的影响 好
铸造缺陷及其对策.pptx

4、防止方法:
1、优化铸件结构设计,壁厚均匀,过渡平滑,肋板 厚度和分布的合理化; 2、优化浇注系统,控制浇温、浇速使铸件各部位冷 却速度趋于一致; 3、降低有害元素,合理控制合金元素添加量; 4、合理设定开箱时间。
5、补救措施:
1、开止裂孔后焊补; 2、采用工业修补剂; 3、如在重要面,报废重铸。
第16页/共28页
4、防止方法: 1、优化工艺设计,合理设置浇注系统; 2、考虑使用保温冒口、发热冒口; 3、优化铸件结构设计; 4、模拟分析(CAE); 5、调整成份; 6、控制炉料.
第17页/共28页
5、补救措施: 1、轻者焊补或采用工业修补剂; 2、重者报废重铸.
第18页/共28页
2.夹砂
的不同大小、形状的 孔洞缺陷的总称
缩孔 缩松
形状不规则,孔壁粗糙,常伴有粗大 树枝晶.夹杂物.裂纹等缺陷;
是细小的分散缩孔,断口呈海绵状;
疏松(显微缩松) 不作严格区分;
第3页/共28页
气 孔
第4页/共28页
针孔
2、裂纹、冷隔类缺陷
定义
缺陷名 称
特征
宏观(肉眼、PT、R T、MT、UT)或微 观(显微镜)判断发现 有开裂状纹络
1、铸件内部裂纹可采用超声波探伤(UT)、 磁粉探伤(MT)或射线探伤法(RT)进行检验; 2、铸件表面的裂纹可采用染色探伤法(PT)来 帮助确定,大部份是肉眼可直接发现的。
第24页/共28页
3、形成原因:
1、铸件结构或浇注系统设计不合理壁厚相差悬殊, 过渡圆角小; 2、铸造合金中有害元素(P、S等)超标,珠光体 元素过量; 3、铸件开箱过早,冷却过快; 4、合金收缩率大; 5、肋板设计不合理。
铜合金铸件铸造缺陷及防止对策ppt课件

○
○
○
○ ○○
○
○○
○
○
○
○
○
○○○ ○
1 1 12
17 7 2
11 3 10
○ 65 3
表3续
2、艺术铸造铜合金的冶金特性
艺术铸造铜合金的独特要求:
①合金应满足艺术铸品的使用要求 ——耐蚀性、色泽、声学特性和机械性能
②合金应满足各种工艺要求 ——铸造成形性能、可焊接性能、可打磨加工 性能和表面着色性能
deabcde图1缩孔缩松缺陷示意图外缩孔内缩孔缩松图2铜合金铸件铸造缺陷分类及其主要原因主要原因铸造缺陷模型装置砂箱装置砂的性质的有机材料造型材料中制芯作业造型作业合箱金属液铸件设计浇冒口系统铸造工艺方案浇注温度浇注技术不注意1错箱2浇不到3冷隔4砂型压崩5胀箱6壁厚尺寸偏差7冲砂8夹砂表3铜合金铸件铸造缺陷分类及其主要原因续主要原因铸造缺陷模型装置砂箱装置砂的性质的有机材料造型材料中制芯作业造型作业合箱金属液铸件设计浇冒口系统铸造工艺方案浇注温度浇注技术不注意9表面气坑10烧结粘砂机械粘砂11内侧面包芯砂12表面不完整13虫眼表面14表面锈迹15锡汗铅汗16表面粗糙表3续铜合金铸件铸造缺陷分类及其主要原因续主要原因铸造缺陷模型装置砂箱装置砂的性质的有机材料造型材料中制芯作业造型作业合箱金属液铸件设计浇冒口系统铸造工艺方案浇注温度浇注技术不注意17表面麻点18褪色a1青铜19固体夹杂20缩孔21热裂22粗晶组织23气孔24铸件清理缺陷1112177211310653表3续2艺术铸造铜合金的冶金特性?艺术铸造铜合金的独特要求
砂 箱 装 置
砂 造的 制
的 性 质
型有 材机 料材 中料
芯 作 业
造 型 作 业
合 箱
铸造缺陷鉴别PPT精选文档

外形不圆正
孔壁粗糙不平,孔中无夹杂物 内表面为暗色 晶粒粗大
砂(渣)外形不规则 孔
孔壁不光滑
Байду номын сангаас
孔中全部或部 内表面为暗色
分充塞着型砂,
渣孔则全部或
部分充塞着渣
23
三、多肉类缺陷的鉴别
1、1 批缝:是铸件上 厚薄不均匀的薄片状 金属凸起物,长出现 在铸件分型面和芯头 部位
24
三、多肉类缺陷的鉴别
1、毛刺和脉纹:毛 刺是铸件表面上刺状 金属凸起物,常出现 在型和芯的裂缝处。
7-6、偏析 7-7、白口 7-8、反白口 7-9、球化不良 7-10、球化衰退
9
铸造缺陷名称及分类(8)
尺寸、形状和重量差错类缺陷
8-1尺寸和重量差错
8-2变形
8-3错型(错箱)
8-4 错芯
8-5偏芯
8-6舂移
10
二、孔洞类铸造缺陷的鉴别
1、气孔 在铸件内部、表面或
近于表面处有大小不 等的光滑孔眼。形状 有圆的,长的及不规 则的;有单个的,也 有集聚成片。颜色为 白色或带一点暗色, 有时覆有一层氧化皮。
网状或脉状分布的毛 刺称脉纹。
25
三、多肉类缺陷的鉴别
2、抬 箱(抬 型): 铸件在 分型面 部位高 度和宽 度增大
26
三、多肉类缺陷的鉴别
3、涨砂: 铸件内、 外表面局 部胀大, 形成不规 则的瘤状 金属凸起 物。
27
三、多肉类缺陷的鉴别
4、冲砂: 铸件表面 上有粗糙 不规则的 金属瘤状 物,常位 于浇口附 近。在铸 件其它部 位则往往 出现砂眼。
2
☆ 缺陷分类
一、常见铸件的缺陷分类
因此,分析铸件缺陷产生的原因时,要 从具体情况出发,根据具体条件—缺陷 的特点,位置,采用的工艺和所用材料 等因素,进行综合分析研究,才能正确 地得出产生缺陷的主要原因,采取相应 的技术和组织措施,有效地防止和消除 缺陷。
铸件质量检测PPT课件
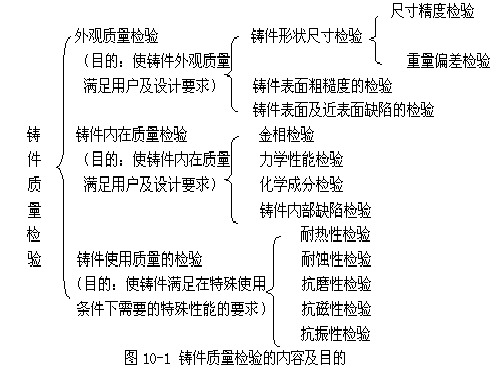
a) b) c) 图10-12 变形示意图 a) 模样变形 b)铸形变形 c)铸件变形
三、检验方法及结果 1. 铸件外形及几何尺寸的检测 2. 铸件重量偏差检验 3. 铸件化学成分检验 4. 铸件本体的金相检验 5. 球墨铸铁及活塞环的力学性能 6. 铸件的无损检测 7. 铸件缺陷分析
图10-25 灰铸铁B型抗拉试样 a) B1型 b) B2型
三、化学成分检验 四、铸件内部缺陷检验 第四节 铸件质量检验的工程应用实例 一、铸件简介 二、铸件质量检验项目 1.铸件外形及几何尺寸的检测,并由此测定铸造收缩率; 2.铸件重量偏差检验; 3.球墨铸铁化学成分分析; 4.铸件本体的合金检验; 5.球墨铸铁活塞环的力学性能; 6.无损检测(抽查); 7.铸件缺陷分析。
a) b) 图10-14 错芯示意图 图10-15 偏芯(漂芯)示意图 a)水平砂芯上浮 b) 凸出砂台断裂上浮 图10-16金属夹杂物示意图(下图)
a) b) 图10-20灰铸铁单试样铸坯示意图 图10-21 灰铸铁单附铸试块铸坯图
a) b) 图10-22 U形单铸试块和Y形单铸试块图 a)U形试块图 b)Y形试块图
第三节 铸件内在质量检验
铸件内在质量是通常是指其室温状态时的力学性能,金相组织及化学成分,内部缺陷等,对于特殊用途的铸件,还应包括如下一些特殊性能,如高(低)温力学性能、耐磨性、耐蚀性、减振性、承压密封性、电学、磁学性能等等。 一、金相检验 二、力学性能检验 1、拉伸试验及试样毛胚 2、冲击试验 3、硬度试验
a) b) 图10-5 冷裂示意图 图 10-4缩孔、缩松、疏松示意图 a)缩孔 b)缩松、疏松
第二节 铸件外观质量检验方法
一、常见铸造缺陷的特征及识别 图10-2 飞翅、毛刺示意图 a)飞翅 b)毛刺 c)脉纹
铸造培训PPT课件课件

态度,不断提升自己的专业技能和创新能力,以适应行业发展的需求。
02
关注行业动态与发展趋势
个人需要关注铸造行业的最新动态和发展趋势,了解新技术、新工艺和
新材料的应用情况,以便及时调整自己的职业规划和发展方向。
03
培养跨学科综合能力
未来铸造行业将更加注重跨学科综合能力的培养,个人需要注重学习机
械、材料、计算机等相关学科知识,提高自己的综合素质和竞争力。
03
铸造工艺与操作
熔炼工艺与操作
01
02
03
04
熔炼设备选择
根据生产需求选择适当的熔炼 设备,如电弧炉、感应电炉等
。
熔炼材料准备
准备好所需金属原料、熔剂、 燃料等,并进行预处理。
熔炼过程控制
控制熔炼温度、时间、气氛等 参数,确保金属液质量。
熔炼安全操作
遵守安全操作规程,注意防火 、防爆、防烫伤等。
绿色环保与可持续发展
环保意识的提高将促使铸造行业朝着更加绿色环保的方向 发展,采用低污染、低能耗的生产工艺和材料,推动行业 可持续发展。
个性化定制与柔性生产
市场需求的多样化将促使铸造企业向个性化定制和柔性生 产方向转型,以满足客户多样化的需求。
对个人职业发展的建议和思考
01
持续学习与创新
随着技术的不断进步和市场需求的不断变化,个人需要保持持续学习的
铸造培训ppt课件
contents
目录
• 铸造基础知识 • 铸造设备与工具 • 铸造工艺与操作 • 铸造缺陷分析与防止措施 • 铸造安全与环保要求 • 总结与展望
01
铸造基础知识
铸造定义与分类
铸造定义
铸造是一种通过熔化金属或非金 属材料,并将其倒入模具中冷却 凝固,从而获得所需形状和性能 的工件的制造方法。
砂型铸造及其常见缺陷 PPT

变化容易形成孔洞、凹坑等现象 • 在铸造过程中因铸件的壁厚不均或散热方式、凝固条件不同而导致铸件的凝固顺序不
会同步进行,后凝固的迫使给先凝固的部分提供补缩,当浇铸终断后,最后凝固的部 分无补充来源由自身引起的收缩 • 在特殊情况下,凝固条件受到其它外界因素或客观条件的干涉而改变了凝固顺序所形 成的收缩(如气体、模具的局部温差等等 • 合金成分不良,导致流动性差,不能及时补缩 • 铸件含有厚实部位,收缩过程中得不到及时补缩
固化剂:常温呈碱性,中和树脂酸性,减缓树脂反应们延长混好砂的存放时间 添加剂:增加粘合强度 涂料:填补凹坑
制芯篇——制芯工艺1
一,砂芯配比
➢挂件砂:50kg砂+180ml固化剂+800ml树脂+30ml添加剂 ➢龙头砂:50kg砂+170ml固化剂+700ml树脂+30ml添加剂
二,混砂工艺 砂+固化剂
2、在铸造过程中,铸件凝固时体积变小则意味着往里面收缩,会产生向 内腔(砂芯)的作用力,而砂芯在高温作用下,体积会膨胀,同时向 铸件产生向外的作用力,在两种力的作用下,如果金属液处在浆状体 的那一瞬间就会产生裂纹(即金属液对砂芯的作用力小于砂芯对金属 液的作用力)
3、金属液自身晶体结构分布不均匀、合金组成成分不符合工艺需求,导 致凝固时组织不致密受力不均匀而产生裂纹(结构颗粒不均,大小不 一、分布无规律)
铸造篇——浇不满原因
➢ 原因分析: 1、铜水温度过低 2、浇铸工艺不当 4、铜材成份不良,导致流动性差 5、模具温度偏低、铸件壁厚太薄,铜液过早凝固
铸造篇——浇不满改善
解决办法:
铸造缺陷(气孔与缩孔)

铸造缺陷的分类
气孔
铸件内部或表面存在圆形或椭圆形的 孔洞,有时呈集群状分布,气孔的形 成与浇注时气体卷入和凝固时气体析 出有关。
缩孔
铸件在冷却过程中,由于体积收缩而 未能得到足够的金属补充,在铸件内 部形成的空洞或区域,缩孔通常出现 在铸件最后凝固的部位。
02
气孔的形成与控制
气孔的形成原因
材料因素
,导致形成空洞。
浇注系统设计不当,金属液流 动不均匀,局部区域金属液过
早凝固。
铸件结构复杂,厚薄差异大, 导致金属液冷却速度不一致。
浇注时金属液面过低,补缩能 力不足。
缩孔对铸件的影响
缩孔会导致铸件局部厚度减小,降低承载能力。 缩孔会降低铸件的致密度和气密性,影响性能。
缩孔部位容易引起应力集中,降低铸件疲劳强度。 缩孔影响铸件外观质量,可能导致产品不合格。
通过目视或低倍放大镜观察铸件表面,寻找是否 存在气孔和缩孔的迹象。
无损检测
利用射线、超声波、磁粉等无损检测技术对铸件 内部进行检测,确定缺陷的位置和大小。
力学性能测试
对铸件进行拉伸、冲击等力学性能测试,分析其 机械性能是否符合要求。
识别技巧
01
观察表面特征
气孔通常表现为圆形或椭圆形的凸起,而缩孔则表现为不规则的凹陷。
铸造缺陷(气孔与缩孔)
• 引言 • 气孔的形成与控制 • 缩孔的形成与控制 • 气孔与缩孔的检测与识别 • 案例分析
01
引言
铸造缺陷的定义
01
铸造缺陷是指在铸造过程中,由 于各种原因导致铸件内部或表面 出现的不符合技术要求或使铸件 性能下降的区域或点。
02
铸造缺陷的产生与铸造工艺、模 具设计、原材料、操作环境等多 种因素有关。
铸造缺陷气孔与缩孔ppt课件

易吸气的合金时,合金液 在铸型内合理设施排气塞和溢流
大量吸气,造成铸件成批 槽,必要时可采用真空吸铸、真
报废。
空压铸、吹氧压铸和在惰性气体
8、树脂砂的树脂和固化 保护下浇注等方法防止铸件产生
剂加入量过多,树脂含氟 气孔。
量过高,原砂和再生砂的 6、熔模铸造、消失模铸造、壳型
角形系数过高、粒度过 铸造等可与真空吸铸相结合,以
1、气孔超出验收标 准时应报废 2、单独的大气孔可 进行焊补 3、成群分散的小气 孔可采取侵渗处理 方法进行填补,质 量要求高的铸件可 采用热等静压处理 法消除气孔
面反应,形成表面针孔与
皮下气孔
2
(1)卷入气孔:金属液在 充型过程中因卷入气体而 在铸件内形成气孔,多呈 孤立存在的圆形或椭圆形 大气孔,位置不固定,一 般偏铸件中上部 (2)侵入气孔:由型、芯 、涂料、芯撑、冷铁产生 的气孔侵入铸件表层而形 成气孔,多呈梨形或椭圆 形,尺寸较大,孔壁光 滑,表面多呈氧化色 (3)反应气孔:由金属液 内部某些成分之间或金属 液与型、芯在界面上发生 化学反应而形成群分布的 气孔。位于铸件表层的针 头形或腰圆形反应气孔称 为表面针空与皮下气孔, 由金属液与型、芯涂料发 生界面反应所至;分散或 成群分布在铸件整个断面 上或某个局部区域的针头 反应气孔通常称为针孔, 由金属液内某些成分之间 发生化学反应所引起,位 于铸件上部的反应气孔常 拌有夹渣 (4)析出气孔:溶解在金 属液中的气体在铸件成型 过程中析出而形成的气孔 呈细圆形、椭圆形或针头 形,成群分布在铸件整个 断面上或某个局部区域 内,空壁光亮,铝合金铸 件析出的气孔通常称为针 孔,在热节与厚截面处较 严重
2、缩孔、缩松 、疏松(显微缩
松)
(1)、缩孔:铸件在凝 固过程中因补缩不良而在 热节或最后凝固部位形成 的宏观孔洞,缩孔形状不 规则,孔壁粗糙,常伴有 粗大树枝品、夹杂物、气 孔、裂纹、偏析等缺陷, 缩孔上方或附近的铸件表 面有时会出现凹陷,缩孔 按分布特征可分为集中缩
铸件常见缺陷及分析方法PPT课件

3. 黏砂与夹砂 (1)黏砂 铸件表面或内腔黏附着一层难以清除的砂粒称为黏砂。根据砂粒与铸件连 接情况的不同,一般分为机械黏砂和化学黏砂。
1)机械黏砂 影响机械黏砂的主要因素如下: ① 砂型表面孔隙的大小。 ② 金属液的静压力对机械黏砂影响较大。 ③ 浇注温度越高,则金属液在铸型表面保持液态的时间就越长。 ④ 铸型表面材料的导热性能大小,影响铸件的黏砂程度。
2) 侵入性气孔缺陷的预防措施 ① 降低铸型和型芯的发气量。 ② 增加铸型(芯)的透气性。 ③ 采用合理的浇注工艺。 ④ 采用合理的浇注系统。 2. 缩孔与缩松 液态金属注入型腔后,随着温度的下降,发生凝固,在此期间发生液态 收缩和凝固收缩。在铸件最后凝固的部位,往往会出现由于补缩不良而产生 的孔洞,称为缩孔。
(2)反应性气孔 金属液与铸型(芯)或在金属液内部某些成分之间,因 发生化学反应产生的气体来不及排出所产生的气孔,称 为反应性气孔。 反应性气孔一般都位于铸件表面以下,呈分散分布的 小孔。其又分为金属液与铸型间反应性气孔和金属液内 部反应性气孔,反应性气孔类型、特征、产生原因及预 防方法等见表11-8。
(3)侵入性气孔 气体从金属液外部侵入金属液后造成的气孔称为侵入 性气孔。 侵入性气孔的特征是: 气孔出现在铸件的个别地方, 数量较少、体积(尺寸)较大、孔壁光滑、表面有光泽或 轻微的氧化色。形状多成椭圆形,一般位于铸件浇注位 置的中上部或上部。
1)造成侵入性气孔的因素 ① 浇注时,气体由浇注系统、型腔混入金属液, 导致气孔的产生。 ② 金属液和冷铁、芯撑相互作用而产生气体。 ③ 砂型或砂芯中的水分或附加物(黏结剂),在金 属液的热作用下气化、分解或燃烧产生的气体,侵入 金属液形成气孔。
(2)砂眼 砂眼是指铸件内部或表面带有砂粒的孔洞。多产度太低,或造型、合型等工序不够细致所 造成的,具体表现如下:
铸造缺陷特征、原因及预防措施(图文并茂)

缺陷名称特征产生的主要原因预防措施实例照片气孔在铸件内部或表面有大小不等的光滑孔洞①炉料不干或含氧化物、杂质多;②浇注工具或炉前添加剂未烘干;③型砂含水过多或起模和修型时刷水过多;④型芯烘干不充分或型芯通气孔被堵塞;⑤春砂过紧,型砂透气性差;⑥浇注温度过低或浇注速度太快等①降低熔炼时金属的吸气量,减少砂型在浇注过程中的发气量②改进铸件结构,提高砂型和型芯的透气性,使型内气体能顺利排出缩孔与缩松缩孔多分布在铸件厚断面处,形状不规则,孔内粗糙①铸件结构设计不合理,如壁厚相差过大,厚壁处未放冒口或冷铁;②浇注系统和冒口的位置不对;③浇注温度太高;④合金化学成分不合格,收缩率过大,冒口太小或太少①壁厚小且均匀的铸件要采用同时凝固②壁厚大且不均匀的铸件采用由薄向厚的顺序凝固③合理放置冒口的冷铁编辑版word砂眼在铸件内部或表面有型砂充塞的孔眼①型砂强度太低或砂型和型芯的紧实度不够,故型砂被金属液冲入型腔;②合箱时砂型局部损坏;③浇注系统不合理,内浇口方向不对,金属液冲坏了砂型;④合箱时型腔或浇口内散砂未清理干净①严格控制型砂性能和造型操作②合型前注意打扫型腔③改进浇注系统粘砂铸件表面粗糙,粘有一层砂粒①原砂耐火度低或颗粒度太大;②型砂含泥量过高,耐火度下降;③浇注温度太高;④湿型铸造时型砂中煤粉含量太少;⑤干型铸造时铸型未刷涂斜或涂料太薄①适当降低金属的浇注温度②提高型砂、芯砂的耐火度夹砂铸件表面产生的金属片状突起物,在金属片状突起物与铸件之间夹有一层型砂①型砂热湿拉强度低,型腔表面受热烘烤而膨胀开裂;②砂型局部紧实度过高,水分过多,水分烘干后型腔表面开裂;③浇注位置选择不当,型腔表面长时间受高温铁水烘烤而膨胀开裂;④浇注温度过高,浇注速度太慢①严格控制型砂、芯砂性能②改善浇注系统,使金属液流动平稳③大平面铸件要倾斜浇注④适当调整浇注温度和浇注速度编辑版word错型铸件沿分型面有相对位置错移①模样的上半模和下半模未对准;②合箱时,上下砂箱错位;③上下砂箱未夹紧或上箱未加足够压铁,浇注时产生错箱④砂箱或模板定位不准确,或定位销松动①定期检查砂箱、模板的定位销及销孔、并合理地安装;②定期对套箱整形,脱箱后的铸型在搬运时要小心。
- 1、下载文档前请自行甄别文档内容的完整性,平台不提供额外的编辑、内容补充、找答案等附加服务。
- 2、"仅部分预览"的文档,不可在线预览部分如存在完整性等问题,可反馈申请退款(可完整预览的文档不适用该条件!)。
- 3、如文档侵犯您的权益,请联系客服反馈,我们会尽快为您处理(人工客服工作时间:9:00-18:30)。
细,灼减量和微粉含量过 防止铸件产生侵入气孔和卷入气
高,使型砂的发气量过 孔。
高,透气性过低
7、修改浇注系统设计,保证金属
液连续平稳地充型。
8、降低树脂砂的树脂和固化剂加
入量,采用低氟或无氟树脂及粒
型圆整、粒度适中,灼减量和微
粉含量低的原砂和再生砂,以降
低树脂砂的发气量,提高树脂砂
的透气性。
SUCCESS
1、非铁合金熔炼时,炉料、溶剂 、工具和浇包要充分预热和烘 干,去锈去油污,多次重熔炉料 的加入量要适当限制 2、防止金属液在熔炼过程中过度 氧化和吸气,加以脱氧、除气和 除渣,在浇包内的金属熔池表面 加覆盖溶剂,防止金属二次氧化 、吸气和有害杂质返回熔池。用 铝对铸钢、铸铁脱氧时,应严格 控制残留含铝量,吸气倾向严重 的钢液,应尽量避免用铝脱氧, 可采用AVD、VOD、多孔塞吹惰性 气体、喷粉法等对钢液进行炉外 精练,脱除钢液中的气体与有害 杂质;对球墨铸铁,应加强脱 硫,降低原汤的含流量,在保证 球化的前提下,尽量减少球化剂 的加入量,降低铸铁的残留含镁 量并加孕育剂处理;熔炼易氧化 吸气的非铁合金时,采用真空熔 炼、吹惰性气体或高效精炼剂等 加强对合金液的净化处理 3、浇注时金属液不得断流,冲型 速度不易过高,铸件浇注位置和 浇注系统的设置应保证金属液平 稳的充满型腔,并利于型腔内的 气体能畅通的排出,易氧化和吸 气的合金,可采用真空浇注或在 控制气氛下浇注
铸造缺陷
2006年9月12日
名称与简图
定义与特征
检验与鉴别
形成原因
防止方法
补救措施
1、由于炉料潮湿、锈蚀
1、气孔、针孔
气孔是出现在铸件内和 或表层,截面呈圆形、椭 圆形、腰圆形、梨形与针 头状,孤立存在或成群分 布的孔洞,大气孔常孤立 存在,小气孔常成群或分 散分布,暴露在铸件表面 的气孔称为表面气孔;位 于铸件表皮下的腰圆形分 散的气孔称为皮下气孔; 分散分布在铸件内部、状 如针头的气孔称为针孔; 成群分布在铸件表层、状 如针头的气孔称为表面针 孔、气孔壁一般较光滑, 气孔常与夹渣与缩孔并 存,气孔按形成原因分 为:卷入气孔、侵入气孔 、反映气孔和析出/30
1、改进铸型工艺设计,合理设置
4、型腔铸造时,应保证型和芯内
应开排气通道,合型时要填补芯
头间隙,以免钻入金属液阻塞通
气道;型腔最高处及易窝气的部
位应设置出气冒口;大平面铸件
可倾斜浇注,并在型腔最高处设
置出气冒口,芯撑和冷铁应干燥
6、浇注温度过低,金属 、无锈、无油污;砂型要扎足够
型温度过低,金属液除渣 多的出气孔;型腔中不得混入铁
易吸气的合金时,合金液 在铸型内合理设施排气塞和溢流
大量吸气,造成铸件成批 槽,必要时可采用真空吸铸、真
报废。
空压铸、吹氧压铸和在惰性气体
8、树脂砂的树脂和固化 保护下浇注等方法防止铸件产生
剂加入量过多,树脂含氟 气孔。
量过高,原砂和再生砂的 6、熔模铸造、消失模铸造、壳型
角形系数过高、粒度过 铸造等可与真空吸铸相结合,以
的类别和成因
、油污、气候的潮湿,熔 练工具和浇包未烘干,金 属液成分不当,合金液为 精炼与精炼不足,使金属 液中含有大量气体或气体 物质,导致在铸件中析出 气孔或反应气孔。 2、型、芯未充分烘干, 透气性差,通气不良,含水 分和发气物质过多,涂料 未烘干或含发气成分过 多,冷铁、芯撑有锈斑、 油污或未烘干,金属型排 气不良,在铸件中形成侵 入气孔。 3、浇注系统不合理,浇 注和充型速度过快,金属 型排气不良,使金属液在 浇注和充型过程中产生紊 流、涡流或断流而卷入气 体,在铸件中形成卷入气 孔。 4、合金液易吸气,在熔 炼和浇注过程中未采取有 效的精练保护和净化措 施,使金属液中含有大量 夹渣、气体和产气成分, 在充型和凝固过程中形成 析出气孔和反应气孔。 5 、型砂、芯砂和涂料成 分不当,与金属液发生界
(1)卷入气孔 (2)侵入气孔 (3)反应气孔 (4)析出气孔
铸件内部的气孔采用超 声波检验与射线检验, 铸件表层的气孔采用渗 透液或磁粉检验各类气 孔的鉴别,除应根据它 的形状、大小与分布特 征外,有时还须根据他 们的形成原因,辅以测 定合金的化学成分及溶 解在金属液内的各种气 体和杂质的含量,型、 芯、涂料的成分、水分 和发气性,以及检查和 分析铸型的浇注系统与 排气条件,方能确定, 必要时,还应进行金相 、扫描电镜和透射电镜 检验,以及X射线分析 等,才能准确鉴定气孔
不良,粘度过高,使在浇 豆、煤粒、粘土等杂物,并控制
注和充型过程中卷入的气 水分及碳质材料的含量,减少粘
体及由金属液中析出的气 土的含量,提高型腔的透气性;
体来不及排出铸型或上浮 涂料要烘干并不含易发气的物质
到冒口或出气口中去
5、金属型铸造和压力铸造时,
7、在气候潮湿季节熔炼 适当提高浇注温度和铸型温度,
1、气孔超出验收标 准时应报废 2、单独的大气孔可 进行焊补 3、成群分散的小气 孔可采取侵渗处理 方法进行填补,质 量要求高的铸件可 采用热等静压处理 法消除气孔
面反应,形成表面针孔与
皮下气孔
(1)卷入气孔:金属液在 充型过程中因卷入气体而 在铸件内形成气孔,多呈 孤立存在的圆形或椭圆形 大气孔,位置不固定,一 般偏铸件中上部 (2)侵入气孔:由型、芯 、涂料、芯撑、冷铁产生 的气孔侵入铸件表层而形 成气孔,多呈梨形或椭圆 形,尺寸较大,孔壁光 滑,表面多呈氧化色 (3)反应气孔:由金属液 内部某些成分之间或金属 液与型、芯在界面上发生 化学反应而形成群分布的 气孔。位于铸件表层的针 头形或腰圆形反应气孔称 为表面针空与皮下气孔, 由金属液与型、芯涂料发 生界面反应所至;分散或 成群分布在铸件整个断面 上或某个局部区域的针头 反应气孔通常称为针孔, 由金属液内某些成分之间 发生化学反应所引起,位 于铸件上部的反应气孔常 拌有夹渣 (4)析出气孔:溶解在金 属液中的气体在铸件成型 过程中析出而形成的气孔 呈细圆形、椭圆形或针头 形,成群分布在铸件整个 断面上或某个局部区域 内,空壁光亮,铝合金铸 件析出的气孔通常称为针 孔,在热节与厚截面处较 严重