飞行器大型薄壁件制造的柔性工装技术
现代飞行器制造工艺学复习题简答及答案贾玉红何景武
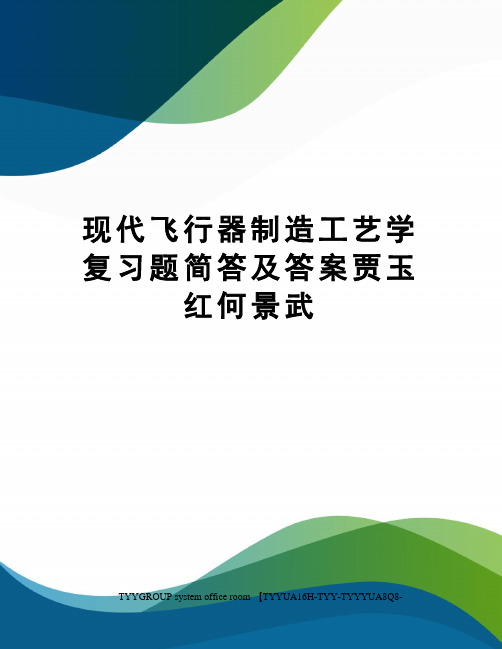
现代飞行器制造工艺学复习题简答及答案贾玉红何景武TYYGROUP system office room 【TYYUA16H-TYY-TYYYUA8Q8-1. 飞机产品的特点及其制造工艺的特点。
飞机产品的特点:1、零件数量大、品种多 2、外形复杂、精度要高 3、零件尺寸大、刚度小 4、材料品种多,新材料应用比例大 5、 结构不断改进,产量变化范围大制造工艺的特点:1、需采用新的保证互换性的方法-模线样板工作法; 2、 生产准备工作量大,需采用大量模具、夹具、型架等工艺装备,数字化制造技术;3、批量变化范围大,手工劳动量大,现在用柔性制造技术; 4、零件加工方法多种多样,装配劳动量比重大; 5、 生产协作能力强,推行并行工程。
2. 弯曲、拉伸、拉形、拉弯、落锤成形、液压成形、喷丸成形、旋压成形及胀形等典型成形工艺的成形原理、成形极限、容易出现的问题及解决方法。
弯曲:成型原理:弯曲是将平直板材或管材等型材的毛坯或半成品、用磨具或其他的工具弯成具有一定曲率和一定角度的零件的加工成型方法。
材料外层纤维受拉,内层纤维受压,中性层不变。
成形极限:当万区间相对弯曲半径小到一定程度时,会是万区间外表面纤维的拉伸应变超过材料所允许的极限而出现裂纹或折断,此时的变形记先成为成形极限。
相对弯曲半径r/t 达到材料即将破裂的极限是的min r问题:主要问题是回弹。
解决办法:补偿法、加压法,加热校形法及拉弯法。
拉伸原理:拉伸是在凸模作用下将平板毛坯变成开口空心零件的过程。
(凸缘切向收缩为筒壁,筒壁为传力区)成形极限:当壁筒要拉断时的拉伸系数为极限拉伸系数。
在筒壁将要拉断时的最小拉伸系数0/m d D容易出现的问题:凸缘起皱和筒壁拉裂。
解决办法:用压边圈防止外皱。
用带拉伸筋的凹模、反向拉伸法和正反向联合拉伸法防止内皱。
拉形原理:拉形时板料两端在拉形机夹钳夹紧的情况下,随着拉形模的上升,板材与拉形模接触产生不均匀的双向拉伸变形,是板料与拉形模逐渐贴合的成型方法。
航空薄壁零件变形控制方法的研究

寸稳 定性难 以控制 , 产 品一 次性合格率低 。这现 已成 为我国航 空 生产领 域 中的瓶颈 , 因此 薄壁结构件加 工变形控制技 术 己成
为 飞行 器 制 造 中 亟 待 解 决 的关 键 问 题之 一 。
限 元 模 拟 分 析 预 测 工件 在 铣 削 过 程 中 的变 形 趋 势 和 变 形 量 。 根
据预测 的变 形量将刀 具进 行偏摆 , 并将刀 具偏摆量录入 到数控 程序 中,使 得刀具在 实际切削加工 过程中偏 向工件 偏离方 向 , 从而克服让 刀带来的壁厚不均匀现象 , 实现加工误差 的补偿 。 薄壁结 构件 加工变形 由材料 内应 力所引起 , 选择应 力分布
应优化装 夹方式合 理消除装夹 力对 后 应 力 重 新 分布 , 达 到 新 的平 衡 状 态 , 最 终产 生 加 工 变 形 。由于 重新平衡而产 生塑性变形 , 薄壁 结构件在 加工过程 中材料 去除量 高 , 甚至 能达 到 9 0 %… , 因此残余应 力释 放所 引起 的加工变形尤 为显 著。 ( 2 ) 加工过程 中切 削力 的影 响。板框类薄壁 结构件 的加 工 主要采用铣 削方式 , 材料受铣 刀挤压作用 不断发生剪切 失效后 从材 料基体 上被去 除, 工件与铣 刀前 刀面 、 后 刀面之 间存 在变
好切 削力和零件局部刚度 的关系。降低切 削力和消除零件残余 应力是减小薄壁零件局部加 工变 形的主要途径 。 数控加工理 论 研究和实 际应用 表明高速切 削具有较小 的切 削力 , 从而在加 工
过 程 中产 生 的让 刀 变 形 效 应 较 小 , 同时, 由于切 削热大 部分 由
航空薄壁件加工技巧
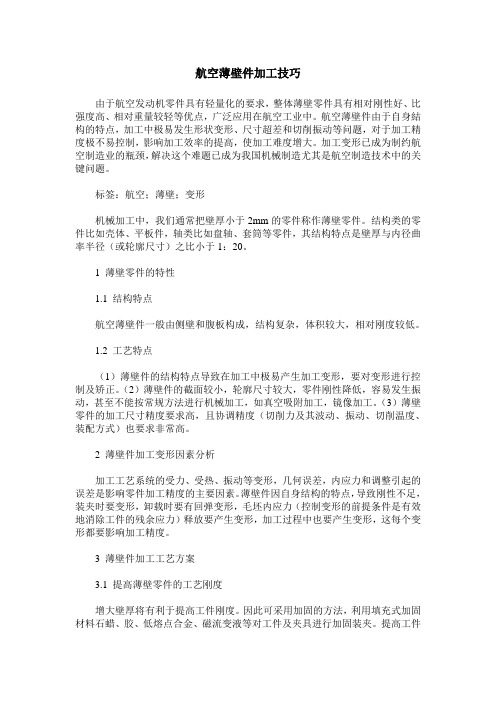
航空薄壁件加工技巧由于航空发动机零件具有轻量化的要求,整体薄壁零件具有相对刚性好、比强度高、相对重量较轻等优点,广泛应用在航空工业中。
航空薄壁件由于自身結构的特点,加工中极易发生形状变形、尺寸超差和切削振动等问题,对于加工精度极不易控制,影响加工效率的提高,使加工难度增大。
加工变形已成为制约航空制造业的瓶颈,解决这个难题已成为我国机械制造尤其是航空制造技术中的关键问题。
标签:航空;薄壁;变形机械加工中,我们通常把壁厚小于2mm的零件称作薄壁零件。
结构类的零件比如壳体、平板件,轴类比如盘轴、套筒等零件,其结构特点是壁厚与内径曲率半径(或轮廓尺寸)之比小于1:20。
1 薄壁零件的特性1.1 结构特点航空薄壁件一般由侧壁和腹板构成,结构复杂,体积较大,相对刚度较低。
1.2 工艺特点(1)薄壁件的结构特点导致在加工中极易产生加工变形,要对变形进行控制及矫正。
(2)薄壁件的截面较小,轮廓尺寸较大,零件刚性降低,容易发生振动,甚至不能按常规方法进行机械加工,如真空吸附加工,镜像加工。
(3)薄壁零件的加工尺寸精度要求高,且协调精度(切削力及其波动、振动、切削温度、装配方式)也要求非常高。
2 薄壁件加工变形因素分析加工工艺系统的受力、受热、振动等变形,几何误差,内应力和调整引起的误差是影响零件加工精度的主要因素。
薄壁件因自身结构的特点,导致刚性不足,装夹时要变形,卸载时要有回弹变形,毛坯内应力(控制变形的前提条件是有效地消除工件的残余应力)释放要产生变形,加工过程中也要产生变形,这每个变形都要影响加工精度。
3 薄壁件加工工艺方案3.1 提高薄壁零件的工艺刚度增大壁厚将有利于提高工件刚度。
因此可采用加固的方法,利用填充式加固材料石蜡、胶、低熔点合金、磁流变液等对工件及夹具进行加固装夹。
提高工件的工艺刚度还可以从下面几个方面着手,一是提高工件与工装接触定位面的加工精度和表面光洁度,二是提高接触刚度(增强接触面硬度或采用高弹性模量材料)。
大型航空薄壁零件精确绿色制造技术研究

1. 2 飞机外形薄壁壁板数铣加工工艺分析
大型飞机外形壁板的传统工艺除了化铣之外,也 存在采用数铣和喷丸成形结合工艺、成形壁板采用型 面工装真空吸附装夹工艺、成形壁板强行压平数铣工 艺,具体工艺流程及面临的问题分析如下:
图 2 化铣与数铣相结合的工艺流程
化铣工艺及面临的问题分析[8]: ( 1) 化铣的保护膜刻线工艺繁杂: 采用手工刻线 工艺,需要设计制造立体化铣样板,按化铣样板在保护 膜上刻线。化铣样板设计制造流程长,精度底,且刻线 误差较大,效率底。而采用五坐标激光切割机配柔性 夹具能有效解决刻线工艺,实现零件的精确切边、开缺 口和制孔加工。但高昂的设备价格制约着刻线工艺的 推广。
图 3 精确绿色制造加工原理
飞机外形壁板精确绿色制造工艺流程如图 4 所 示 。 [11-12]
图 4 精确绿色制造工艺流程
大型飞机外形壁板的加工工艺流程设计为一次装 夹状态下,在一台设备上完成壁板壁厚减薄、切边、切
通窗、钻孔加工,等效于化铣与切边、钻孔和开通窗相 结合的制造工艺,是数铣替代化铣的最新制造技术,满 足精确制造和绿色制造的要求。
收稿日期: 2014 - 07 - 19; 修回日期: 2014 - 09 - 03 * 基金项目:“高 档 数 控 机 床 与 基 础 制 造 装 备”国 家 科 技 重 大 专 项“国 产 高 档 数 控 机 床 与 数 控 系 统 在 飞 机 筋 肋 梁 等 加 工 单 元 中 的 应 用”
( 2013ZX04001 - 021) 作者简介: 向兵飞( 1986—) ,男,土家族,湖北宜昌人,江西洪都航空工业股份有限公司工程师,硕士,从事航空制造数控加工工艺技术研究,( E -
适用于薄壁件加工的真空柔性夹具设计制造分析
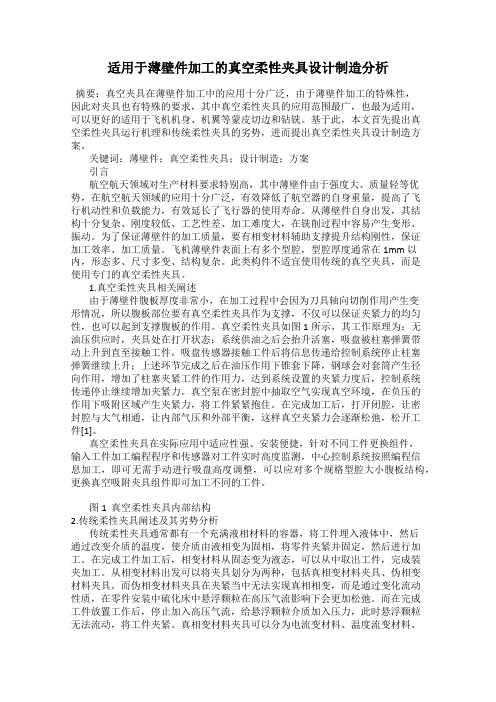
适用于薄壁件加工的真空柔性夹具设计制造分析摘要:真空夹具在薄壁件加工中的应用十分广泛,由于薄壁件加工的特殊性,因此对夹具也有特殊的要求,其中真空柔性夹具的应用范围最广,也最为适用,可以更好的适用于飞机机身、机翼等蒙皮切边和钻铣。
基于此,本文首先提出真空柔性夹具运行机理和传统柔性夹具的劣势,进而提出真空柔性夹具设计制造方案。
关键词:薄壁件;真空柔性夹具;设计制造;方案引言航空航天领域对生产材料要求特别高,其中薄壁件由于强度大、质量轻等优势,在航空航天领域的应用十分广泛,有效降低了航空器的自身重量,提高了飞行机动性和负载能力,有效延长了飞行器的使用寿命。
从薄壁件自身出发,其结构十分复杂、刚度较低、工艺性差、加工难度大,在铣削过程中容易产生变形、振动。
为了保证薄壁件的加工质量,要有相变材料辅助支撑提升结构刚性,保证加工效率、加工质量。
飞机薄壁件表面上有多个型腔,型腔厚度通常在1mm以内,形态多、尺寸多变、结构复杂。
此类构件不适宜使用传统的真空夹具,而是使用专门的真空柔性夹具。
1.真空柔性夹具相关阐述由于薄壁件腹板厚度非常小,在加工过程中会因为刀具轴向切削作用产生变形情况,所以腹板部位要有真空柔性夹具作为支撑,不仅可以保证夹紧力的均匀性,也可以起到支撑腹板的作用。
真空柔性夹具如图1所示,其工作原理为:无油压供应时,夹具处在打开状态;系统供油之后会抬升活塞,吸盘被柱塞弹簧带动上升到直至接触工件,吸盘传感器接触工件后将信息传递给控制系统停止柱塞弹簧继续上升;上述环节完成之后在油压作用下锥套下降,钢球会对套筒产生径向作用,增加了柱塞夹紧工件的作用力,达到系统设置的夹紧力度后,控制系统传递停止继续增加夹紧力。
真空泵在密封腔中抽取空气实现真空环境,在负压的作用下吸附区域产生夹紧力,将工件紧紧抱住。
在完成加工后,打开闭腔,让密封腔与大气相通,让内部气压和外部平衡,这样真空夹紧力会逐渐松弛,松开工件[1]。
真空柔性夹具在实际应用中适应性强、安装便捷,针对不同工件更换组件,输入工件加工编程程序和传感器对工件实时高度监测,中心控制系统按照编程信息加工,即可无需手动进行吸盘高度调整,可以应对多个规格型腔大小腹板结构,更换真空吸附夹具组件即可加工不同的工件。
【国家自然科学基金】_高效柔性制造_基金支持热词逐年推荐_【万方软件创新助手】_20140801
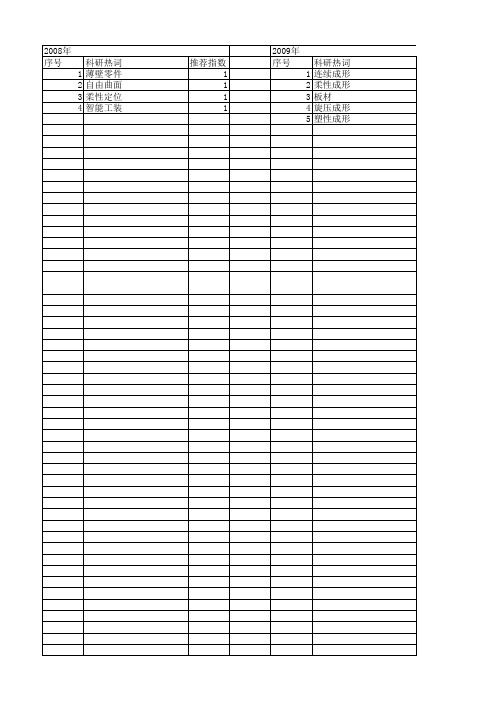
推荐指数 1 1 1 1 1 1 1 1 1 1 1 1 1 1 1 1 1 1 1 1 1 1 1
2013年 序号 1 2 3 4 5 6 7 8 9 10 11 12 13 14 15 16 17 18 19 20 21 22 23 24 25 26
科研热词 推荐指数 气压砂轮 2 高硬度模具表面 1 高效性 1 铣削加工 1 软固结磨粒群 1 软固结磨粒 1 让刀误差 1 纳米压印 1 纳米制造 1 突出预测 1 瓦斯涌出初速度 1 现场作业 1 焊接机器人 1 激光强化 1 滚对滚纳米压印 1 滚型纳米压印 1 测定装备 1 柔性 1 无导轨、刚性轨道、柔性轨道 1 应用 1 半导体激光 1 切削力预测 1 刀具挠度变形 1 再制造 1 修正的preston方程 1 preston方程 1
2008年 序号 1 3 4
科研热词 薄壁零件 自由曲面 柔性定位 智能工装
推荐指数 1 1 1 1
2009年 序号 1 2 3 4 5
科研热词 连续成形 柔性成形 板材 旋压成形 塑性成形
推荐指数 1 1 1 1 1
2010年 序号 1 2 3 4 5 6 7 8 9 10 11 12 13 14 15 16 17 18 19 20 21 22 23 24 25 26 27
2012年 序号 1 2 3 4 5 6 7 8 9 10 11 12 13 14 15 16 17 18 19 20 21 22 23
科研热词 高质高效 飞行器制造 飞机蒙皮 自动化 绿色制造系统 砂带 正交试验 柔性铰链 柔性制造 柔性 有限元 无模弯曲 数字化 抛光工艺 快速刀具伺服 微结构 平流式换热器 工装 工艺装备 工艺参数 大型薄壁件 发动机叶片 关键技术
推荐指数 1 1 1 1 1 1 1 1 1 1 1 1 1 1 1 1 1 1 1 1 1 1 1 1 1 1 1
关于飞机工装设计制造技术之研究
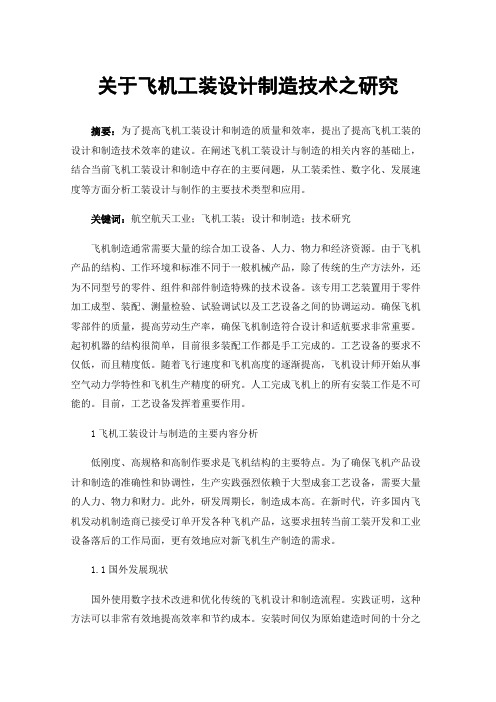
关于飞机工装设计制造技术之研究摘要:为了提高飞机工装设计和制造的质量和效率,提出了提高飞机工装的设计和制造技术效率的建议。
在阐述飞机工装设计与制造的相关内容的基础上,结合当前飞机工装设计和制造中存在的主要问题,从工装柔性、数字化、发展速度等方面分析工装设计与制作的主要技术类型和应用。
关键词:航空航天工业;飞机工装;设计和制造;技术研究飞机制造通常需要大量的综合加工设备、人力、物力和经济资源。
由于飞机产品的结构、工作环境和标准不同于一般机械产品,除了传统的生产方法外,还为不同型号的零件、组件和部件制造特殊的技术设备。
该专用工艺装置用于零件加工成型、装配、测量检验、试验调试以及工艺设备之间的协调运动。
确保飞机零部件的质量,提高劳动生产率,确保飞机制造符合设计和适航要求非常重要。
起初机器的结构很简单,目前很多装配工作都是手工完成的。
工艺设备的要求不仅低,而且精度低。
随着飞行速度和飞机高度的逐渐提高,飞机设计师开始从事空气动力学特性和飞机生产精度的研究。
人工完成飞机上的所有安装工作是不可能的。
目前,工艺设备发挥着重要作用。
1飞机工装设计与制造的主要内容分析低刚度、高规格和高制作要求是飞机结构的主要特点。
为了确保飞机产品设计和制造的准确性和协调性,生产实践强烈依赖于大型成套工艺设备,需要大量的人力、物力和财力。
此外,研发周期长,制造成本高。
在新时代,许多国内飞机发动机制造商已接受订单开发各种飞机产品,这要求扭转当前工装开发和工业设备落后的工作局面,更有效地应对新飞机生产制造的需求。
1.1国外发展现状国外使用数字技术改进和优化传统的飞机设计和制造流程。
实践证明,这种方法可以非常有效地提高效率和节约成本。
安装时间仅为原始建造时间的十分之一,飞机的生产和维护成本减半。
这表明,数字技术在促进飞机制造技术的发展和发展方面发挥着重要作用。
1.2国内发展现状为了顺应全球趋势和发展速度,中国飞机制造商积极采用国外数字化设计和制造技术。
柔性制造技术在航天制造业的应用
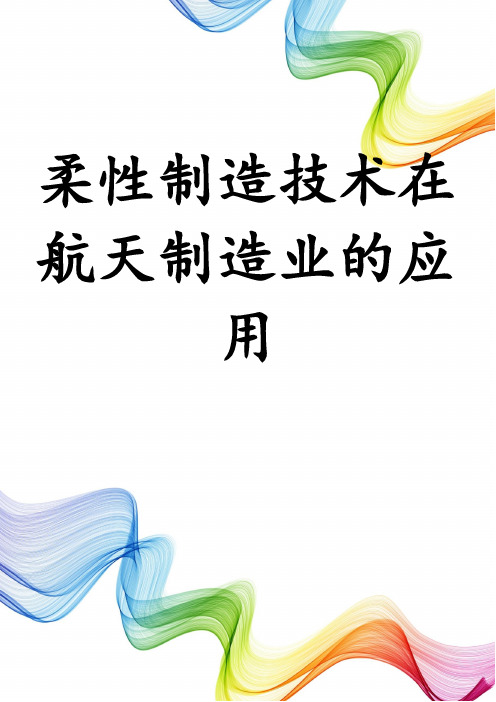
柔性制造技术在航天制造业的应用柔性制造技术在航天制造业的应用近年来,随着科技的不断进步和航天技术的快速发展,航天制造业对于更高效、更灵活的生产方式提出了更高的要求。
柔性制造技术应运而生,为航天制造业带来了许多创新和突破。
本文将以步骤思维的方式,探讨柔性制造技术在航天制造业中的应用。
第一步,柔性制造技术的定义与特点。
柔性制造技术是一种能够适应多品种、小批量和高变化的生产方式。
其特点包括生产设备的模块化、自动化程度高、生产线的可重构性等。
这些特点使得航天制造业能够更好地应对生产任务的变化和复杂性。
第二步,柔性制造技术在航天制造业的应用领域。
柔性制造技术在航天制造业的应用广泛,包括但不限于以下几个方面:1. 生产线的灵活性提升。
柔性制造技术可以使得航天制造企业能够根据市场需求快速调整生产线,实现不同产品的生产。
这种灵活性不仅能够提高生产效率,还能够减少生产线的闲置时间,降低生产成本。
2. 自动化生产的实现。
柔性制造技术可以实现航天制造业的自动化生产。
通过使用先进的机器人和自动化设备,航天制造企业可以实现生产过程的自动化,提高生产效率和产品质量。
3. 生产过程的优化。
柔性制造技术可以通过实时数据采集和分析,对生产过程进行优化。
航天制造企业可以通过监测生产过程中的关键参数,及时调整生产参数,提高产品的质量和一致性。
第三步,柔性制造技术在航天制造业中的应用案例。
柔性制造技术已经在航天制造业中得到了广泛应用,下面是一些典型案例:1. 柔性机器人应用。
柔性机器人可以根据不同的生产需求进行快速切换和调整,适应不同的制造任务。
在航天制造业中,柔性机器人可以在不同的工作站上完成不同的生产任务,提高生产效率和灵活性。
2. 自适应控制系统。
柔性制造技术可以通过自适应控制系统实现对生产过程的实时监控和调整。
航天制造企业可以通过监测生产过程中的关键参数,及时调整生产参数,提高产品的质量和一致性。
3. 3D打印技术的应用。
柔性制造技术可以与3D 打印技术相结合,实现航天部件的快速制造和定制生产。
大连理工大学科技成果——飞机发动机整机柔性安装系统研制
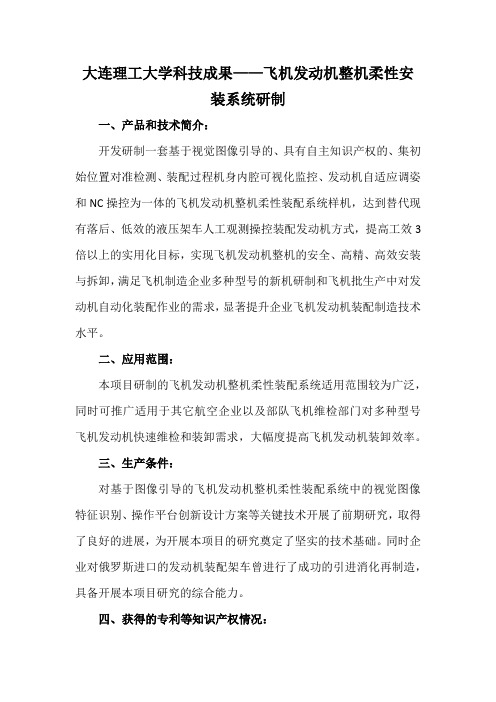
大连理工大学科技成果——飞机发动机整机柔性安装系统研制一、产品和技术简介:开发研制一套基于视觉图像引导的、具有自主知识产权的、集初始位置对准检测、装配过程机身内腔可视化监控、发动机自适应调姿和NC操控为一体的飞机发动机整机柔性装配系统样机,达到替代现有落后、低效的液压架车人工观测操控装配发动机方式,提高工效3倍以上的实用化目标,实现飞机发动机整机的安全、高精、高效安装与拆卸,满足飞机制造企业多种型号的新机研制和飞机批生产中对发动机自动化装配作业的需求,显著提升企业飞机发动机装配制造技术水平。
二、应用范围:本项目研制的飞机发动机整机柔性装配系统适用范围较为广泛,同时可推广适用于其它航空企业以及部队飞机维检部门对多种型号飞机发动机快速维检和装卸需求,大幅度提高飞机发动机装卸效率。
三、生产条件:对基于图像引导的飞机发动机整机柔性装配系统中的视觉图像特征识别、操作平台创新设计方案等关键技术开展了前期研究,取得了良好的进展,为开展本项目的研究奠定了坚实的技术基础。
同时企业对俄罗斯进口的发动机装配架车曾进行了成功的引进消化再制造,具备开展本项目研究的综合能力。
四、获得的专利等知识产权情况:申请发明专利2项1)一种飞机发动机安装作业用数控电动架车(专利申请号:201310097888.0)2)一种飞机发动机安装用多轴调姿平台(专利申请号:201310098161.4)五、成本估算:飞机发动机整机柔性安装系统因功能多样,结构复杂,自动化程度高,从前期项目筹备、方案设计到后期的加工、制造与调试需要较大的启动资金作支撑,初步估算制造成本至少400万元人民币。
六、规模与投资:据预测,研制的飞机发动机整机柔性装配系统因其良好的柔性化和通用化设计,使之不仅适用沈飞公司涉及的机型,以及其他飞机制造公司发动机装配,而且适合部队维检单位对飞机发动机的高效拆装,因而应用市场广阔,效益显著。
在成功研制原理样机之后,将逐步投资并生产数量更多,功能更全,可靠性更加优良的新型飞机发动机装配系统,以满足今后航天发动机安装作业的需求。
柔性制造系统在航空制造领域的应用研究

柔性制造系统在航空制造领域的应用研究摘要:在航空制造领域,充分发挥柔性制造系统功能,做好航空零部件生产加工制造作业,需要构建柔性生产线,量化柔性生产程序,编制相关程序,做好航空零部件加工测控工作,正确运用自动化加工工艺。
本文将简单分析柔性制造系统在航空制造领域的应用方案,希望能为航空机械零件加工作业提供参考与借鉴。
关键词:柔性制造系统;航空制造领域;应用方案;航空机械零件航空设备结构组合复杂,对零部件的精密性、安全性、牢固性、可靠性与轻量化的要求非常高,航空机械设备工作的环境也非常恶劣。
确保飞机的安全质量,做好航空机械零件加工生产作业,需要建立柔性制造系统。
本文将简单分析航空机械零部件的特征,并从建立柔性生产线,做好在线检测工作,启用自动化加工工艺,做好航空零部件加工测控工作等四个方面浅谈柔性制造系统在航空制造领域的应用方案。
一、航空机械零部件的特征从整体上分析,航空机械零部件有三大特征:第一,品种多,批量小。
航空设备组合有数万个不同类型的零部件,在壳体类、轴类与壁板类机械中均有安装应用。
随着中国航空事业的迅速发展,飞机的型号更新也很快,这样使得航空机械零部件的生产批量比较小,刚性生产线自然无法满足这些零部件的生产需求,因此,要启用灵活性良好的柔性生产线。
第二,机械零部件结构复杂,加工制造工作难度高。
飞机组合零部件构成复杂,对零部件的承力与轻量化性能的要求很高,所以会导致机械零部件加工作业的难度很大,在具体加工制造过程中,必须谨遵标准要求,严格选用刀具、机床和夹具[1]。
第三,机械零部件的尺寸精度要求极高。
确保航空安全,延长飞机使用寿命,优化飞机性能,必须严格做好组合零部件加工作业,充分确保机械零件的尺寸精度。
简而言之,航空机械零部件对尺寸精度的要求非常高,公差很小,在加工作业中,必须充分确保加工工艺的一致性与高精度。
二、柔性制造系统在航空制造领域的应用方案(一)建立柔性生产线发挥柔性制造系统在航空制造领域的应用价值,首先要建立可行的柔性生产线,将航空机械零部件加工流程纳入到自动柔性生产控制系统中,对柔性生产系统控制功能进行全面优化[2]。
航空宇航制造——柔性装配技术

航空制造工程概论报告题目:飞机柔性装配技术学院:机电学院班级:05010703学号:2007姓名:2010年04月27日【摘要】结合我国现阶段飞机装配背景,将国内外装配进行比较,探讨了飞机柔性装配技术的优势与发展前景。
对柔性装配工装,柔性制孔,虚拟装配等进行了分析与研究,报告目前国内外飞机柔性装配技术的现状,以及柔性装配技术在未来飞机制造业中的作用。
关键词:柔性装配技术;柔性装配工装;柔性制孔;虚拟装配。
1 背景飞机装配是飞机制造过程的主要环节。
飞机装配过程就是将大量的飞机零件按图纸、技术要求等进行组合、连接的过程,分为部装(零件→组合件→段件→部件)和总装(各部件→全机身)。
飞机的设计制造难度大,周期长,不仅表现在它的零件数控加工量大,而且表现在它的装配复杂性和难度。
飞机的装配工作量约占整个飞机制造劳动量的40%~50%(一般的机械制造只占20% 左右)。
飞机装配质量和效率取决于飞机机械连接技术,如自动钻铆、干涉连接、高质量紧密制孔、孔挤压强化、电磁铆接等,而装配件准确度受制于装配型架的制造和安装准确度。
迄今为止,装配技术已经历了从手工装配、半机械/ 半自动化装配、机械/自动化装配到柔性装配的发展历程。
飞机柔性装配技术的应用是当前国内外飞机制造业数字化制造的大趋势,能够克服飞机制造模线--样板法在模拟量协调体系下需要大量实物工装且应用单一、制造周期长、费用高等缺点,通过与自动化制孔设备、数控钻铆或自动电磁铆接设备等自动化装备的集成可组成自动化、数字化的柔性装配系统,缩短装配周期,提高和稳定装配质量。
柔性装配技术的范畴很广,涵盖了柔性装配工装、柔性制孔、装配系统、装配(含装配工艺)设计、虚拟装配、装配集成管理、数字化检测、面向柔性装配的设计等技术领域。
2 国内外研究现状目前,国内仍大量采用传统型架进行人工装配,装配的自动化和柔性化水平较低,数字量协调尚未贯穿飞机整个装配过程,面向装配的设计理念还未形成共识。
大型飞机柔性装配技术

⼤型飞机柔性装配技术⼤型飞机通常是指起飞总重量超过100t的运输类飞机,包括军⽤、民⽤⼤型运输机,也包括150座以上的⼲线客机。
与⼩型飞机相⽐,⼤型飞机在尺⼨、巡航速度、航载能⼒、可靠性等⼀些基本指标上均有更⾼的要求。
世界航空⼯业发展近百年来,各项技术取得了突飞猛进的发展,尤其在飞机装配与制造领域不断突破新的技术创新。
近10余年来,以波⾳777、波⾳787、A340、A380为代表的⼤飞机集中反映了飞机先进装配技术的现状和发展趋势。
采⽤基于单⼀产品数据源的数字量尺⼨协调体系,通过装配仿真和虚拟现实技术等虚拟制造技术和并⾏⼯程实现装配过程优化,应⽤柔性装配系统进⾏机体结构的⾃动化装配,实现了飞机结构⾼质量、⾼效率装配,以满⾜飞机长寿命、⾼可靠性、低成本和⾼效率制造的要求。
与国外先进的飞机装配技术相⽐,国内航空业仍采⽤⼿⼯装配、半机械化与机械化装配相结合的传统装配⽅式,应⽤⼤量较复杂的专⽤型架定位和夹紧的⾮精益化装配⽅法。
飞机柔性装配技术概述柔性装配技术是⼀种能适应快速研制和⽣产及低成本制造要求、模块化可重组的先进装配技术,它具有⾃动化、数字化、集成化的特点,是当代飞机装配技术发展的⼀个新领域。
传统飞机装配是刚性、固定、基于⼿⼯化的,⽽柔性装配则向⾃动化、可移动、数字化的⽅向转变。
表1 为飞机传统装配⽅法与柔性装配⽅法的⽐较。
国外发展现状1数字化装配设计技术数字化装配设计技术的发展历程始于波⾳公司,在研制波⾳777的过程中,第⼀次实现了“⽆纸设计”,全⾯采⽤数字化技术,实现了三维数字化定义、三维数字化预装配和并⾏⼯程,建⽴了全机的数字样机,取消了全尺⼨实物样机,使⼯程设计⽔平和飞机研制效率得到了很⼤的提⾼,制造成本降低了30%~40%,产品开发周期缩短了40%~60%,⽤户交货期从18个⽉缩短到12个⽉。
⾃此,数字化装配设计技术在国外发达国家的航空企业得到了⼴泛和深⼊的应⽤。
2⼤部件柔性装配技术世界航空发达国家的飞机部件柔性装配技术, 已向由⾃动化装配⼯装、模块化加⼯单元、数字化定位和检测系统、复杂多轴数控系统和离线编程与仿真软件等组成的⾃动化装配系统发展。
一种大型薄壁件的多点柔性定位工装与装夹优化技术
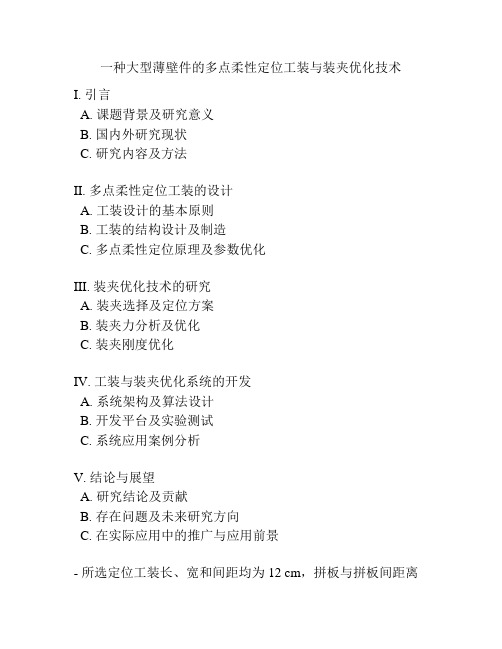
一种大型薄壁件的多点柔性定位工装与装夹优化技术I. 引言A. 课题背景及研究意义B. 国内外研究现状C. 研究内容及方法II. 多点柔性定位工装的设计A. 工装设计的基本原则B. 工装的结构设计及制造C. 多点柔性定位原理及参数优化III. 装夹优化技术的研究A. 装夹选择及定位方案B. 装夹力分析及优化C. 装夹刚度优化IV. 工装与装夹优化系统的开发A. 系统架构及算法设计B. 开发平台及实验测试C. 系统应用案例分析V. 结论与展望A. 研究结论及贡献B. 存在问题及未来研究方向C. 在实际应用中的推广与应用前景- 所选定位工装长、宽和间距均为12 cm,拼板与拼板间距离为1.2 cm,拼板与工装的间隙为0.1 cm,共计50个拼板单元。
拼板材料采用的是厚度为0.25 mm的不锈钢板,单元重量小于1.5 kg;- 多点柔性定位的原理是通过在薄壁件上设置多个靠板点,使得本体与工装形成一定的形位配合。
在具体应用过程中,需要优化工装的形位配合参数,包括靠板点数量、间距和位置等;- 完成装夹后,需要对装夹力进行分析和优化,尽量使得装夹力均匀,并防止出现过大或过小的情况;- 在系统的开发过程中,需要采用较为先进的算法和技术,如仿真技术、优化算法等,同时引入一些现代工具软件,如SOLIDWORKS、ANSYS等;- 未来需要进一步探索多点柔性定位工装的工艺应用,包括探索更多适用于该技术的材料和工艺方法。
同时,还要进一步改进现有的工装及装夹技术,提高生产效率和产品质量。
第一章:引言A. 课题背景及研究意义薄壁件在现代制造业中应用广泛,如汽车、航空等领域的车身、机身等大型薄壁件,需要在制造过程中实现高精度的定位和装夹,才能保证产品的质量和精度。
传统的定位工装和装夹技术存在局限性,无法满足高精度、高效率的工艺要求。
因此,研究一种适用于大型薄壁件的多点柔性定位工装与装夹优化技术具有重要的实践意义和应用价值。
B. 国内外研究现状在国内外,多点柔性定位技术和装夹优化技术的研究已经取得了一定的进展。
航空薄壁零件的加工工艺

航空薄壁零件的加工工艺航空薄壁零件的加工工艺是指将给定的材料通过一系列工艺处理和加工,使得最终成品符合航空行业中对零件质量、尺寸、精度要求,并适用于飞机等航空器件的装配和使用。
航空薄壁零件加工工艺通常包括以下几个步骤:1. 材料准备:航空薄壁零件通常使用高强度、轻质的材料,如铝合金、钛合金等。
在加工之前,首先需要对材料进行处理和准备,如材料的切割、热处理、表面清洁等。
材料的处理和准备对最终产品的质量和性能影响很大,因此必须严格控制每个步骤的工艺参数。
2. 零件加工:航空薄壁零件的加工通常采用数控机床进行,因为数控机床具有高精度、高效率和稳定性好等优点。
加工工艺通常包括车削、铣削、钻削、铆接、切割等。
在加工过程中,需根据零件的设计要求和工艺要求,合理选择刀具、工艺参数和加工路径,并严格控制加工过程中的加工质量和尺寸精度。
3. 表面处理:航空薄壁零件的表面处理对于提高零件的耐腐蚀性、耐磨性和表面光洁度非常重要。
常见的表面处理方法包括阳极氧化、电镀、喷涂、磷化等。
表面处理工艺需要根据零件材料的特性选择合适的方法,并控制处理参数和工艺流程,以保证表面处理效果和质量。
4. 检验与质量控制:航空薄壁零件的加工过程中需要进行严格的检验和质量控制,以确保产品的质量和性能满足航空行业的要求。
常见的检验方法有尺寸测量、外观检查、力学性能测试等。
质量控制包括对每个加工步骤和工艺参数进行监测和调整,以保证零件的尺寸精度、表面质量和机械性能。
在航空薄壁零件的加工过程中,还需要注意以下几个方面:1. 工艺规划和优化:在加工之前,需要对零件的结构和要求进行详细分析,从而制定合理的加工工艺流程和步骤,并对工艺进行持续优化,以提高加工效率和质量。
2. 设备与刀具选择:根据零件的特性和加工要求,需要选择合适的数控机床、刀具和夹具。
设备的选型和使用对加工质量和效率具有重要影响。
3. 清洁与防护:在加工过程中,需要保持加工设备和工作环境的清洁和整洁,防止杂质和污染物对零件质量的影响。
基于PLC的飞机翼类结构件柔性夹具设计
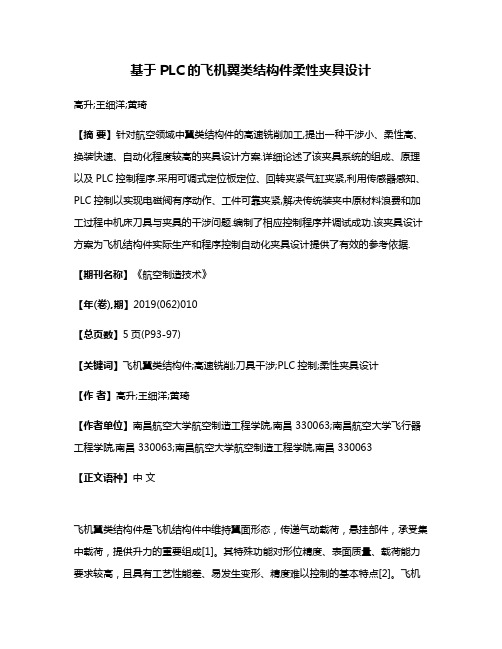
基于PLC的飞机翼类结构件柔性夹具设计高升;王细洋;黄琦【摘要】针对航空领域中翼类结构件的高速铣削加工,提出一种干涉小、柔性高、换装快速、自动化程度较高的夹具设计方案.详细论述了该夹具系统的组成、原理以及PLC控制程序.采用可调式定位板定位、回转夹紧气缸夹紧,利用传感器感知、PLC控制以实现电磁阀有序动作、工件可靠夹紧,解决传统装夹中原材料浪费和加工过程中机床刀具与夹具的干涉问题.编制了相应控制程序并调试成功.该夹具设计方案为飞机结构件实际生产和程序控制自动化夹具设计提供了有效的参考依据.【期刊名称】《航空制造技术》【年(卷),期】2019(062)010【总页数】5页(P93-97)【关键词】飞机翼类结构件;高速铣削;刀具干涉;PLC控制;柔性夹具设计【作者】高升;王细洋;黄琦【作者单位】南昌航空大学航空制造工程学院,南昌 330063;南昌航空大学飞行器工程学院,南昌 330063;南昌航空大学航空制造工程学院,南昌 330063【正文语种】中文飞机翼类结构件是飞机结构件中维持翼面形态,传递气动载荷,悬挂部件,承受集中载荷,提供升力的重要组成[1]。
其特殊功能对形位精度、表面质量、载荷能力要求较高,且具有工艺性能差、易发生变形、精度难以控制的基本特点[2]。
飞机翼类结构件的夹具设计对其制造精度、使用性能影响很大。
传统的飞机翼类结构件夹具设计中,常采用位置固定的定位元件定位,螺钉压板进行夹紧。
对于刚度差的薄壁件常用预留工艺凸台的办法进行加工。
由于柔性低,精度差,材料浪费大,加工过程存在干涉,组合夹具和专用夹具的设计使用逐步将其取代。
组合夹具柔性高,可以对多种工件进行装夹,可循环使用,但成本巨大,且多次使用后组合夹具本身精度降低,累计误差加大[3]。
专用夹具能有效提高结构件加工质量,然而也会产生夹具数量过多、适用面窄、难以管理等问题[4]。
目前,“中国制造2025”逐步推进,更高水平的自动化技术和自动化装备大范围投入到实际生产过程中。
现代飞行器制造工艺学复习题简答及答案贾玉红何景武新

1.飞机产品的特点及其制造工艺的特点。
飞机产品的特点:1、零件数量大、品种多2、外形复杂、精度要高3、零件尺寸大、刚度小4、材料品种多,新材料应用比例大5、结构不断改进,产量变化范围大制造工艺的特点:1、需采用新的保证互换性的方法-模线样板工作法;2、生产准备工作量大,需采用大量模具、夹具、型架等工艺装备,数字化制造技术;3、批量变化范围大,手工劳动量大,现在用柔性制造技术;4、零件加工方法多种多样,装配劳动量比重大;5、生产协作能力强,推行并行工程。
2.弯曲、拉伸、拉形、拉弯、落锤成形、液压成形、喷丸成形、旋压成形及胀形等典型成形工艺的成形原理、成形极限、容易出现的问题及解决方法。
弯曲:成型原理:弯曲是将平直板材或管材等型材的毛坯或半成品、用磨具或其他的工具弯成具有一定曲率和一定角度的零件的加工成型方法。
材料外层纤维受拉,内层纤维受压,中性层不变。
成形极限:当万区间相对弯曲半径小到一定程度时,会是万区间外表面纤维的拉伸应变超过材料所允许的极限而出现裂纹或折断,此时的变形记先成为成形极限。
相对弯曲半径r/t 达到材料即将破裂的极限是的min r问题:主要问题是回弹。
解决办法:补偿法、加压法,加热校形法及拉弯法。
拉伸原理:拉伸是在凸模作用下将平板毛坯变成开口空心零件的过程。
(凸缘切向收缩为筒壁,筒壁为传力区)成形极限:当壁筒要拉断时的拉伸系数为极限拉伸系数。
在筒壁将要拉断时的最小拉伸系数0/m d D容易出现的问题:凸缘起皱和筒壁拉裂。
解决办法:用压边圈防止外皱。
用带拉伸筋的凹模、反向拉伸法和正反向联合拉伸法防止内皱。
拉形原理:拉形时板料两端在拉形机夹钳夹紧的情况下,随着拉形模的上升,板材与拉形模接触产生不均匀的双向拉伸变形,是板料与拉形模逐渐贴合的成型方法。
成形极限:在拉形时,挡板料濒于出现不允许的缺陷时的拉形系数max 0/l l 。
容易出现的问题:拉裂、起皱。
解决办法:防止拉裂的主要方法是控制一次拉形变量;防止起皱可使夹头钳口取现金量符合模具两端对应曲面的剖面形状,在操作中正确配合夹头拉伸和台面上顶的动作。
飞行器大型薄壁件制造的柔性工装技术
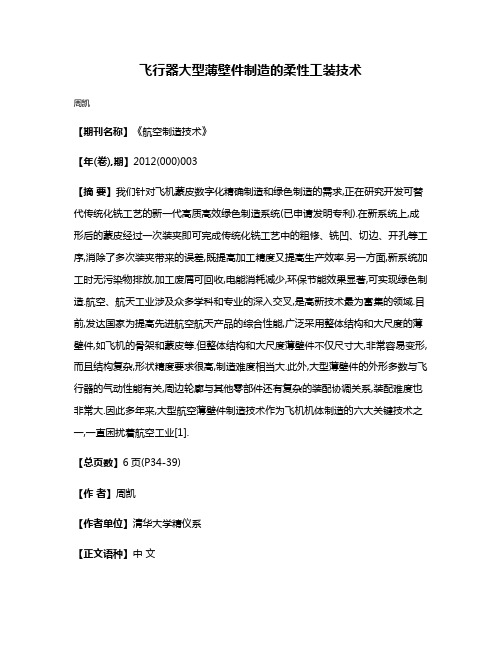
飞行器大型薄壁件制造的柔性工装技术
周凯
【期刊名称】《航空制造技术》
【年(卷),期】2012(000)003
【摘要】我们针对飞机蒙皮数字化精确制造和绿色制造的需求,正在研究开发可替代传统化铣工艺的新一代高质高效绿色制造系统(已申请发明专利).在新系统上,成形后的蒙皮经过一次装夹即可完成传统化铣工艺中的粗修、铣凹、切边、开孔等工序,消除了多次装夹带来的误差,既提高加工精度又提高生产效率.另一方面,新系统加工时无污染物排放,加工废屑可回收,电能消耗减少,环保节能效果显著,可实现绿色制造.航空、航天工业涉及众多学科和专业的深入交叉,是高新技术最为富集的领域.目前,发达国家为提高先进航空航天产品的综合性能,广泛采用整体结构和大尺度的薄壁件,如飞机的骨架和蒙皮等.但整体结构和大尺度薄壁件不仅尺寸大,非常容易变形,而且结构复杂,形状精度要求很高,制造难度相当大.此外,大型薄壁件的外形多数与飞行器的气动性能有关,周边轮廓与其他零部件还有复杂的装配协调关系,装配难度也非常大.因此多年来,大型航空薄壁件制造技术作为飞机机体制造的六大关键技术之一,一直困扰着航空工业[1].
【总页数】6页(P34-39)
【作者】周凯
【作者单位】清华大学精仪系
【正文语种】中文
【相关文献】
1.浅谈飞行器大型薄壁件制造的柔性工装技术 [J], 刘东帅
2.飞行器大型薄壁件制造的柔性工装技术 [J], 李栋;张伟林;刘丁荣
3.飞行器大型薄壁件制造的柔性工装技术研究 [J], 何守志
4.飞行器大型薄壁件制造的柔性工装技术 [J], 李志楠; 高刚毅
5.飞行器大型薄壁件制造的柔性工装技术 [J], 李志楠; 高刚毅
因版权原因,仅展示原文概要,查看原文内容请购买。
- 1、下载文档前请自行甄别文档内容的完整性,平台不提供额外的编辑、内容补充、找答案等附加服务。
- 2、"仅部分预览"的文档,不可在线预览部分如存在完整性等问题,可反馈申请退款(可完整预览的文档不适用该条件!)。
- 3、如文档侵犯您的权益,请联系客服反馈,我们会尽快为您处理(人工客服工作时间:9:00-18:30)。
飞行器大型薄壁件制造的柔性工装技术我们针对飞机蒙皮数字化精确制造和绿色制造的需求,正在研究开发可替代传统化铣工艺的新一代高质高效绿色制造系统(已申请发明专利)。
在新系统上,成形后的蒙皮经过一次装夹即可完成传统化铣工艺中的粗修、铣凹、切边、开孔等工序,消除了多次装夹带来的误差,既提高加工精度又提高生产效率。
另一方面,新系统加工时无污染物排放,加工废屑可回收,电能消耗减少,环保节能效果显著,可实现绿色制造。
航空、航天工业涉及众多学科和专业的深入交叉,是高新技术最为富集的领域。
目前,发达国家为提高先进航空航天产品的综合性能,广泛采用整体结构和大尺度的薄壁件,如飞机的骨架和蒙皮等。
但整体结构和大尺度薄壁件不仅尺寸大,非常容易变形,而且结构复杂,形状精度要求很高,制造难度相当大。
此外,大型薄壁件的外形多数与飞行器的气动性能有关,周边轮廓与其他零部件还有复杂的装配协调关系,装配难度也非常大。
因此多年来,大型航空薄壁件制造技术作为飞机机体制造的六大关键技术之一,一直困扰着航空工业[1]。
另一方面,飞行器制造,特别是大型飞机的制造,属于典型的多品种小批量制造,因此对制造过程的柔性有特别突出的要求。
传统和柔性制造系统(FMS)虽然可实现常规刚性零件的柔性制造,但却难以实现飞行器大型薄壁件的柔性制造。
主要原因是,传统工艺装备无法实现易变形薄壁件的柔性定位、柔性装夹、柔性输送和柔性存储,因此仅靠数控机床本身的柔性和常规自动化物流系统无法实现对这类特殊零件实施高柔性制造,更无法实现系统化的柔性制造(从柔性成型、柔性加工到柔性装配的全过程柔性制造)。
以上两方面问题的叠加和交错影响,使得飞行器大型薄壁件的柔性制造变得非常复杂,已成为航空、航天制造中的重大难题。
业界认为,解决此问题的关键是大型易变形薄壁件的柔性工艺装备技术。
只有高柔性抗变形的新型工艺装备与先进数控机床相配合,才能真正有效解决这一难题。
因此,对柔性工艺装备的理论、方法和实现技术进行深入系统研究,在此基础上加速发展柔性工装产品并加强在实际中推广应用,对解决飞行器制造中的上述关键问题,对促进我国航空、航天工业的发展,具有重要实际意义。
国外研究和应用现状通过新的工艺技术和柔性工艺装备解决大型薄壁件加工中的变形问题,美、法、德、日等工业发达国家都非常重视,均投入相当人力物力进行研究[2-4]。
但所取得的成果,均作为涉及国防的关键技术,对外秘而不宣[5]。
目前,国外公开发表的文献多以常规零件为研究对象,主要进行切削力模型、变形分析、误差预测等方面的理论研究[6-12]。
在实际工装系统开发方面,企业进行了大量工作,推出许多实用产品,并在行业得到应用。
例如,美国的Rohr Industries公司开发了柔性工作单元,用于机身部件的装配[13]。
德国Horst Witte Geratebau公司制作了基于框架结构的模块工装系统[14]。
美国CAN制造系统公司研发了基于POGO单元的柔性工装系统[15]。
美国Wisconsin-Madison大学开发了快速可组装装配工装。
Northrop Grumman公司开发出龙门式可重组工装[16]。
英国Electroimpact公司为空客飞机机翼的制造开发了大型柔性工装系统[17]。
西班牙MTorres公司开发了飞机板类零部件制造的柔性工装TORRESTOOL[18]。
法国Dufieux Industrie公司开发了新型镜像铣系统(Mirror Milling System,MMS),主要用于蒙皮类零件的铣切加工[19]。
综上所述,用于飞行器制造的柔性工装系统大体分为3类,第一类基于框架及机器人技术,第二类基于柔性多点支承技术[20],第三类为新发展起来的镜像铣技术。
其中,基于前两类技术的柔性工装系统,已经在戴姆勒- 奔驰、波音、麦道、格鲁门、英宇航、CASA、EADS、空客、庞巴迪宇航等飞行器制造企业中得到了广泛应用[3]。
基于第三类技术的柔性工装和加工系统也开始在空客等公司进行应用,有望取得良好效益。
下面以TORRESTOO系统和MM系统为例,对柔性工装系统的技术特点作简要介绍。
TORRESTOOL柔性工装系统是一种用于支承板类零部件的柔性多点固定装置。
它采用模块化结构,包括一定数量的可以沿X坐标运动的排架,排架上装配有一定数量的可沿Y坐标和Z坐标运动的支承杆,每个支承杆上装配有真空吸盘,用以固定工件。
这样,每一个支承杆都可以在计算机的控制下,沿X、Y、Z坐标移动(同一排架上支承杆的X坐标相同),并可被锁定,如图1所示。
系统的主要性能参数如表1所示。
TORRESTOOL系统在X方向上,两个相邻排架之间的最小距离是500mm,在Y方向上,两个相邻鞍座之间的最小距离是228mm ;独立轴总数为195,支承单元总数为90。
整个系统从一种工件的配置到完全不同的另外一种工件的配置,最多耗时不超过2min[21]。
TORRESTOOL柔性工装系统可与TORRESMILL五坐标钻配套使用,对飞机整流罩、平尾和垂尾的前缘、壁板、梁等工件进行铣削、切割、钻孔、忽窝等加工。
该系统不但可适用于板类零件的加工,还可用于大部件的装配,已经被应用在波音、空客系列民用飞机以及军用飞机的生产组装中。
镜像铣系统(MMS)是一种用于蒙皮铣切加工的新型柔性加工系统。
该系统与传统多点系统不同,它采用立式夹持框架从周边对被加工蒙皮进行固定,并通过随动支承头对工件被加工部位进行支承。
支承头和位于被加工工件两侧,成镜像布局。
支承头采用无划痕设计,可在计算机控制下保持与工件曲面接触并随刀具运动,其位置和姿态与刀具位置姿态时刻成镜像关系,从而实现对工件加工部位的高刚度支承,有效抑制颤振,保证加工顺利进行。
虽然国外的柔性工装系统技术上已经比较成熟,但市场售价仍然很高,一般一套系统的价格高达数千万元人民币。
因此,国外系统并不完全符合我国国情,难以在我国的飞行器制造企业中广泛推广应用。
国内研究和应用现状在通过新工艺技术和新工艺装备解决薄壁件柔性加工方面,国内许多单位也进行了大量的探索,提出了一些实用的方法[22-25]。
特别是一些高校和研究单位针对生产实际问题,对柔性工装系统进行了系统研究,并开发出多种应用系统。
下面从成形和切削加工2个方面进行简要介绍。
在成形方面,吉林大学对板材多点成形的柔性工装技术开展了大量研究工作[26],开发出多种规格的多点成形设备[27-30]。
在算法方面,提出了一种在多点成形中计算各冲头与板材接触点的快速算法[31-32],并研究了三维板类件的多点闭环成形方法[33]。
北京航空航天大学开展了基于可重构柔性多点的蒙皮数字化拉形工艺技术研究[34],突破了飞机蒙皮CAD数模工艺补充面的自动生成技术,实现了调形数据的自动生成,解决了大量密集冲头的实时、并行控制等关键技术,并开展了基于弹性垫层、复合垫层的蒙皮拉形工艺研究,建立了基于可重构柔性多点模具的飞机蒙皮数字化拉形试验系统[35]。
在大型薄壁件切削加工方面,北京航空制造工程研究所、成都飞机公司、清华大学等单位开展了较深入的研究和开发工作,取得较多成果。
北京航空制造工程研究所针对飞机薄壁件制造的需求,对柔性工装的关键技术进行了研究[36],并开发出用于飞机蒙皮和壁板切割加工的柔性工装系统。
清华大学对用于飞行器大型薄壁件切削加工和装配的智能柔性工装系统进行了研究,并与成都飞机公司合作,深入研究了以柔性途径实现“先成型后加工”工艺的有关方法和实现技术,开发出用于飞行器大型薄壁件切削加工的智能柔性工装系统(见图2)。
通过多年结合生产实际的研究工作,攻克了柔性工装系统涉及的关键技术,取得系列研究成果[37-51]。
图2 用于大型薄壁件切削加工的智能柔性工装系统柔性工装技术的发展趋势根据对有关信息的分析可以看到,在飞行器柔性工装技术的研究和应用方面,其发展呈以下趋势:1机床工装集成与机床工装互动技术通过网络和信息技术实现机床与工装集成可形成新的集成加工系统,其意义如同机床与刀库集成构成一样,将使制造装备和制造系统产生新的变革。
此新体系带来的好处之一是,机床与工装可进行互动和互操作,从而提高薄壁件制造的综合效益。
典型案例:(1)机床与工装进行信息交流,实现刀具运动轨迹校正。
具体方法是,通过多点柔性工装中的传感器阵列感知工件受力和受热分布情况,计算机根据传感信息和数学模型求解工件变形量,然后发出控制信息对刀具运动轨迹进行校正,从而提高加工精度。
(2)机床与工装进行操作交互,实现对工装定位/支撑阵列布局的自动调整,从而抑制工件变形。
实现方案是,在五轴数控机床主轴上装上操作手,通过计算机对操作手进行五自由度控制,实现仿机器人运动,从而完成对柔性工艺装备的自动调整,将定位/支撑单元阵列的布局调整到使加工变形最小的最佳状态。
2基于智能预测的闭环成形技术回弹是大型薄壁件成形工艺中一大难题。
基于智能预测的闭环成形技术是解决此问题的一个有效途径。
该技术基于闭环控制原理,采用数学模型与人工智能相结合的方法,对回弹量进行精确预测,并基于预测信息对成形过程进行闭环精确控制,从而有效抑制回弹的影响,提高成形精度,保证制造质量。
3成形、加工一体化技术目前,大型曲面薄壁件制造采用成形与加工相分离的工艺方案,由此产生一严重问题:由于成形固有的回弹特性,无法在成型产生的半成品工件上建立后续加工所需的精确基准(即使打上定位孔,误差也较大),使得后续加工时难以进行准确定位,由此造成较大的加工误差,影响飞行器总体制造质量。
成形加工一体化为解决上述问题提供了新的技术途径。
其思想是基于同一基准进行成形与加工作业,从而消除由于基准不重合而产生的多次定位误差,有效提高大型薄壁件的制造质量和效率。
4可替代化铣的绿色制造技术与工艺装备技术长期以来,飞机蒙皮加工中一直普遍采用化铣工艺。
这种工艺虽然可以较好解决复杂凹腔、凹面、凸台等的加工问题,但其存在的化学污染、生产周期长、消耗铝材无法回收等固有弊端,却一直困扰着航空工业,成为世界性难题。
行业内一直在寻求可替代化铣的新工艺和新装备。
尤其在当前环保和可持续发展要求日益迫切的国际环境下,取代化铣实现蒙皮类零件的高质高效绿色制造,已成为全球航空工业都在追求的目标。
波音、空客等航空巨头已计划在数年内取消化铣。
在我国,取代化铣的要求也越来越迫切。
因此,以新的绿色制造技术取代污染严重的化铣技术已成为不可逆转的大趋势。
面对这一趋势,我国一些单位也积极开展了可替代化铣的新工艺技术和新装备技术的研究开发,这些具有广泛应用范围和巨大实用价值的前沿新技术,对推动我国航空制造技术的发展具有重要的实际意义。
5与柔性工装融为一体的原位检测与质量控制技术飞行器大型薄壁件由于刚度极差,当加工完从机床上卸下送往测量机室时将产生很大的变形,而重新安装到检测工装上后又难以精确定位,由此造成再好的测量机也无法检测出实际的加工误差。