钢中氢_氮_氧的来源及其控制对策
钢中氢的来源及控制

钢中氢的来源及控制对策
2.试验条件
2.1 试验工艺及主要设备参数 80tLD-CB(冶炼周期31min)→80tLF(冶炼周期35—55min)→240×1400mm断面弧形 板坯铸机(中包容量15t,浇注周期35min)。 2.2 试验方案 为了检测钢液中真实的氢含量,采用浸入式直读测氢仪(Multi—LabHydris System) 对“转炉炼钢+LF炉+连铸”各工位钢液在线测氢及对原辅料进行详细的水分分析,详 细的测试方案见表1。
表4 转炉吹炼过程辅料加入时机与钢水[H]含量的关系
项目 后吹过程加辅料
辅料水分含量 /%
3.0~5.5
试验炉次 30
辅料加入量/Kg 290
出钢后[H]含量/ppm 3.57
后吹过程未加辅料
/
28
0
2.5
钢中氢的来源及控制对策
4.1.2 耐材的影响 转炉补炉后耐材干燥程度对钢液[H]含量有直接影响,2008年因转炉补炉后耐 材未彻底干燥导致6炉钢[H]〉8.0ppm引发铸坯皮下气孔判废。 4.1.3 合金的影响 试验过程中发现,使用电解法生产的合金对钢液氢含量影响较大,在相同的生 产工艺条件下使用金属锰的炉次比未使用的炉次高1ppm,结果如表5。
897..64811~~~32243..4.18602 34544..6.31.9072546485
钢中氢的来源及控制对策
3.2 各工位钢液[H]测试 转炉炼钢+LF炉+连铸各工位各工位钢液[H]测试结果见表3,从表3可以看出: 转炉冶炼、LF精炼、浇注过程均存在钢液增[H]现象,转炉冶炼过程增[H]量 占 中 间 罐 总 量 的 66.4% 、 LF 占 25.95% 、 浇 注 过 程 占 7.57% 。 中 间 罐 [H]〉 5.0ppm的炉次占44.8%,个别炉次含量高达9.8ppm。
钢中的气体元素

•■测试与分析〜钢中的气体元素宋红艳(中车株洲电力机车有限公司,湖南株洲412001)摘要:介绍了钢中氮、氢、氧等气体的来源、存在形式和对钢材性能特别是力学性能的影响。
举例说明了氮、氢和氧元素在碳结构钢和不锈钢中的应用。
关键词:气体元素;钢;应用中图分类号:T G 115.3+3文献标志码文章编号:1008-1690(2021)01-0058-03Gaseous Elements in SteelsSONG Hongyan(Zliuzhou C R R C Power Loco Co ., Ltd ., Zhuzhou 412001, Hunan China )Abstract : Source , existence form of gaseous elements such as nitrogen , hydrogen and oxygen i n s teels and their e ffect on performances of s t e e l product , especially mechanical properties , were introduced . The applications of nitrogen,hydrogen and oxygen i n carbon structural steel and stainless s t e e l were explained with examples .Key words : gaseous element ; steel ; application1钢铁中气体的存在形式钢中气体仅包括氮、氢、氧三种,在钢铁中并非呈气体状态存在,主要是形成化合物或固溶于钢铁 组织中,仅少量以游离形式存在钢铁的缺陷中。
钢铁中的氮主要源于空气,在冶炼和浇注过程 中,空气与金属熔池或炉渣接触时,溶解于到钢液,与金属形成氮化物,也有以氮化锰和氮化铬等铁合 金作原材料加人的钢中氮主要形成氮化物,如 Fe 4N 、Fe 2N 、CriV 、V N 、TiN 、A l N 、Si 3N 4 等,还有部分 形成固溶体,只有极微量的氮以分子形式吸附于金 属表面或存在于金属空隙中,而且在钢中的溶解度 随着某些合金元素浓度的增加而增加,例如含铬合 金的含氮量较高。
降低钢中氢、氧、氮气体含量的措施
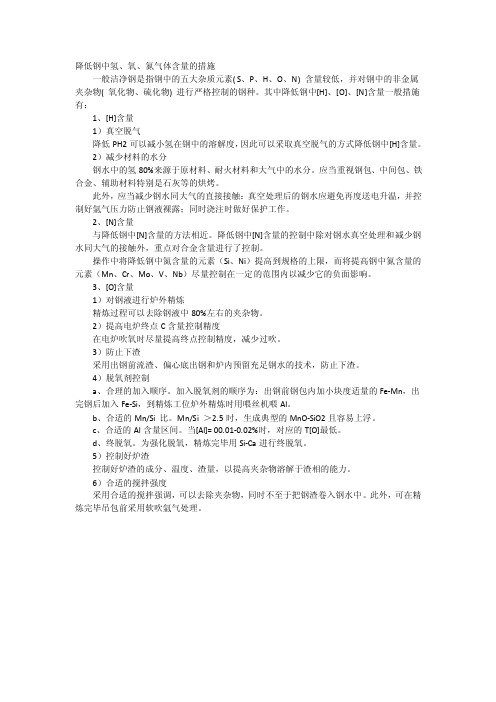
降低钢中氢、氧、氮气体含量的措施一般洁净钢是指钢中的五大杂质元素( S、P、H、O、N) 含量较低,并对钢中的非金属夹杂物( 氧化物、硫化物) 进行严格控制的钢种。
其中降低钢中[H]、[O]、[N]含量一般措施有:1、[H]含量1)真空脱气降低PH2可以减小氢在钢中的溶解度,因此可以采取真空脱气的方式降低钢中[H]含量。
2)减少材料的水分钢水中的氢80%来源于原材料、耐火材料和大气中的水分。
应当重视钢包、中间包、铁合金、辅助材料特别是石灰等的烘烤。
此外,应当减少钢水同大气的直接接触:真空处理后的钢水应避免再度送电升温,并控制好氩气压力防止钢液裸露;同时浇注时做好保护工作。
2、[N]含量与降低钢中[N]含量的方法相近。
降低钢中[N]含量的控制中除对钢水真空处理和减少钢水同大气的接触外,重点对合金含量进行了控制。
操作中将降低钢中氮含量的元素(Si、Ni)提高到规格的上限,而将提高钢中氮含量的元素(Mn、Cr、Mo、V、Nb)尽量控制在一定的范围内以减少它的负面影响。
3、[O]含量1)对钢液进行炉外精炼精炼过程可以去除钢液中80%左右的夹杂物。
2)提高电炉终点C含量控制精度在电炉吹氧时尽量提高终点控制精度,减少过吹。
3)防止下渣采用出钢前流渣、偏心底出钢和炉内预留充足钢水的技术,防止下渣。
4)脱氧剂控制a、合理的加入顺序。
加入脱氧剂的顺序为:出钢前钢包内加小块度适量的Fe-Mn,出完钢后加入Fe-Si,到精炼工位炉外精炼时用喂丝机喂Al。
b、合适的Mn/Si 比。
Mn/Si >2.5时,生成典型的MnO-SiO2且容易上浮。
c、合适的Al含量区间。
当[Al]= 00.01-0.02%时,对应的T[O]最低。
d、终脱氧。
为强化脱氧,精炼完毕用Si-Ca进行终脱氧。
5)控制好炉渣控制好炉渣的成分、温度、渣量,以提高夹杂物溶解于渣相的能力。
6)合适的搅拌强度采用合适的搅拌强调,可以去除夹杂物,同时不至于把钢渣卷入钢水中。
控制钢中氢含量的工艺措施
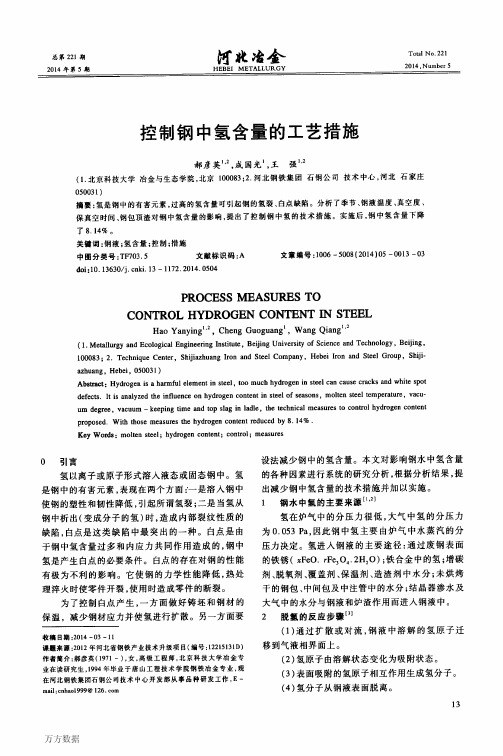
10‘4%;当真空度继续到100 Pa时,中包钢水[H]比 真空度50 Pa时增加了0.85
x
10“%。说明提高真
空度,有利于溶解在钢液中的自由氢原子从钢液中 排除,当真空度小于67 Pa时,脱氢效果不明显,考 虑成本问题,真空度为67 Pa合适。
3.4保持真空时间对钢中氢的影响
表1 不同季节VD炉真空
霹 * 苌 幂 面 导
处理前和破空软吹后钢液平均[H]×10“%
Tab.1
Average[H】in
molten steel
before Vacuum treating by VD
fIlmace强d after
seasons
真空厦/Pa
breaking—empty soft—blowing in different
总第221期 2014年第5期
HEBEI
河北冶全
METALLURGY
Total No.22l 2014.Number 5
控制钢中氢含量的工艺措施
郝彦英1’2,成国光1,王
0500311
强1’2
(1.北京科技大学冶金与生态学院,北京100083;2.河北钢铁集团石钢公司技术中心,河北石家庄 摘要:氢是钢中的有害元素,过高的氢含量可引起钢的氢裂、白点缺陷。分析了季节、钢液温度、真空度、 保真空时间、钢包顶渣对钢中氢含量的影响,提出了控制钢中氢的技术措施。实施后,钢中氢含量下降
Company,Hebei
STEEL
1一
Hao Yanying 1一,Cheng Guoguang
1,Wang Qiang
(1.Metallurgy and Ecological
Engineering
钢中氢、氮、氧的来源及其控制对策

钢中氢、氮、氧的来源及其控制对策高海潮摘要:比较了国内外钢中氢、氮、氧的水平,叙述了国外对纯净钢要求不断提高的过程,分析了钢中氢、氮、氧的来源,讨论了氢和氧的变化规律、吹氧过程中氮的变化以及碳和氧的关系,提出了减少钢污染的有效方法,总结出净化钢液的主要技术措施。
关键词:纯净钢来源钢污染控制措施Sources and Control Measures of Hydrogen,Nitrogen andOxygen in SteelGao Haichao(Ma Anshan Iron & Steel Co.Ltd.)Abstract:The contents of hydrogen, nitrogen and oxygen in steel produced in our country and other countries are compared in this paper. The requirements for clean steel are increased. The analysis on sources of H,N,O in steel have been carried out. The rule of changes in H and O contents, N change in oxygen-blowing process and the relationship between C and O have been discussed herein. The effective measures of decreasing steel pollution are put forward, and the main technology for mloten steel cleaning is then concluded.Keyworks:clean steel source steel pollution control measure1 前言1996年,我国的钢产量突破1亿 t,成为世界第一产钢大国。
钢中氢的来源及低成本控制对策
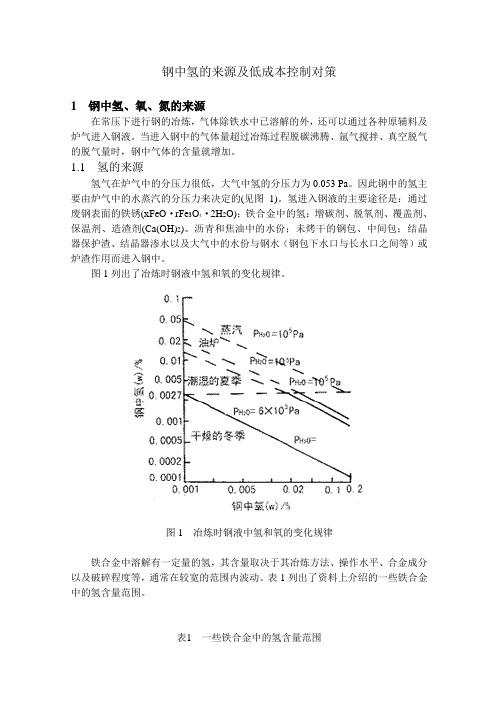
钢中氢的来源及低成本控制对策1钢中氢、氧、氮的来源在常压下进行钢的冶炼,气体除铁水中已溶解的外,还可以通过各种原辅料及炉气进入钢液。
当进入钢中的气体量超过冶炼过程脱碳沸腾、氩气搅拌、真空脱气的脱气量时,钢中气体的含量就增加。
1.1氢的来源氢气在炉气中的分压力很低,大气中氢的分压力为0.053 Pa。
因此钢中的氢主要由炉气中的水蒸汽的分压力来决定的(见图1)。
氢进入钢液的主要途径是:通过废钢表面的铁锈(xFeO·rFe3O4·2H2O);铁合金中的氢;增碳剂、脱氧剂、覆盖剂、保温剂、造渣剂(Ca(OH)2)、沥青和焦油中的水份;未烤干的钢包、中间包;结晶器保护渣、结晶器渗水以及大气中的水份与钢水(钢包下水口与长水口之间等)或炉渣作用而进入钢中。
图1列出了冶炼时钢液中氢和氧的变化规律。
图1冶炼时钢液中氢和氧的变化规律铁合金中溶解有一定量的氢,其含量取决于其冶炼方法、操作水平、合金成分以及破碎程度等,通常在较宽的范围内波动。
表1列出了资料上介绍的一些铁合金中的氢含量范围。
表1一些铁合金中的氢含量范围1.2氧的来源氧在各种炼钢炉冶炼终点时都以一定量存在于钢水中,氧是我们供给的这是不言而喻的。
因为炼钢过程首先是氧化过程,脱[P]、脱[S]、脱[Si]、脱[C]都需要向铁水供氧。
但随着炼钢过程的进行,尽管工艺操作千变万化,可是炼钢炉内熔池中钢液的[C]、[O]的关系却有着共同的规律性。
即随着[C]的逐步降低,[O]却在逐步增高,[C]和[O]有着相互对应的平衡关系。
1.3氮的来源氮气在炉气中的分压力很高,大气中氮的分压力大体保持在7.8×104 Pa。
因此钢中的氮主要是钢水裸露过程中吸入并溶解的。
电炉炼钢,包括二次精炼的电弧加热,加速了气体的解离,故[N]含量偏高;铁合金、废钢铁和渣料中的氮也会随炉料带入钢水。
2炼钢生产防止氢污染的主要技术措施(节源:基础工作)从管理上降低钢中原始氢含量,既是最经济的、符合降成本需要的,也是企业实现环境友好、资源节约的需要。
钢中氢的来源及控制对策 ppt课件

9
钢中氢的来源及控制对策
4.2.2 大吹氩时间与增氢量的关系 随大吹氩时间增加,炉气中的水分分解后进入钢液的氢量增加,结果如 图3,该阶段增[H]量占LF总增[H]量的16.66%。 4.2.3 LF加热时间对增氢的影响 在其它工艺一致的条件下,随加热时间的延长,钢液[H]增加。该阶段 增[H]的主要因素是炉气中的水被电弧电离后溶入钢水。 4.2.4 钙处理工艺与增氢量的关系 (1) 喂SiCa线速度与增氢量的关系 SiCa喂入量相同的前提下,增氢量随喂线速度增加有由大变小,再变大 的趋势,结果如图4所示。当喂线速度为180m/min左右时,增氢量最小。
表1 钢液测氢试验方案
名称
检测内容
转炉速补料
水分含量、用量、补炉后烘烤时间
转炉用辅料及合金
水分含量及用量、加入时机
出钢结束
钢液测氢
LF用辅料及合金
水分含量及用量
LF精炼过程
钢液测氢
连铸中间罐、结晶器覆盖剂
水分含量及用量
ቤተ መጻሕፍቲ ባይዱ
中间罐
钢液测氢
N2、O2、Ar气体
水分含量
钢中氢的来源及控制对策
3.试验结果
3.1 原辅料水分 炼钢过程辅料及合金水分含量分析结果见表2,从分析结果可以看出:转炉速补料、化 渣剂等部分材料水分较高,部分试样水分接近20%,部分石灰制品水分含量〉1.2%。
钢中氢的来源及控制对策
3.2 各工位钢液[H]测试 转炉炼钢+LF炉+连铸各工位各工位钢液[H]测试结果见表3,从表3可以看出: 转炉冶炼、LF精炼、浇注过程均存在钢液增[H]现象,转炉冶炼过程增[H]量 占 中 间 罐 总 量 的 66.4% 、 LF 占 25.95% 、 浇 注 过 程 占 7.57% 。 中 间 罐 [H]〉 5.0ppm的炉次占44.8%,个别炉次含量高达9.8ppm。
炼钢过程中气体和夹杂物的冶金控制
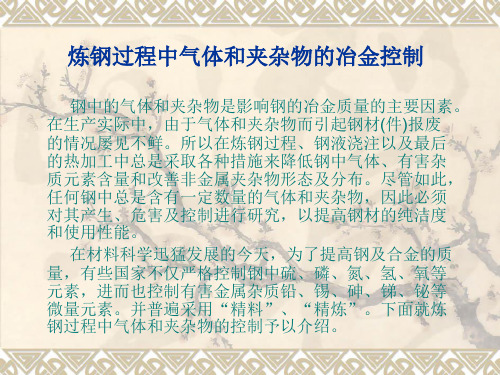
白点主要见于大中型锻件或钢坯。这 些钢件的尺寸愈大,对白点的敏感性也 愈大。把对白点敏感性大的钢锻轧成小 截面的型材及锻件时,很少发现白点。 例如在截面有效厚度小于50mm的钢中 一般不出现白点。 钢件在锻轧后的冷却速度对白点的产 生也起着重要的作用。对白点有敏感性 的钢锻轧后,以较快速度冷却则最易使 白点形成。
研究认为,钢的氢脆倾向除与形变速度、工 作温度及钢的强度水平有关外,还受下列因 素的影响: (1)钢中氢浓度 随着钢中氢浓度的增加,钢 的塑性降低或发生脆断所需时间减少。 (2)钢中微量有害元素 铁素体钢、马氏体钢 中的硫、磷在氢的共同作用下,使钢的脆 性更加明显。此外,Sb, Sn, As, Bi等有害微量 元素也会促进氢脆断裂。
2)采用钢包吹氢脱氢工艺对钢液进行 处理。
三、钢中氮的行为及去除 氮在钢中的作用并不像氢那样完全无 益,因为对于某些钢(例如奥氏体不锈钢) 来讲,氮可以作为合金元素提高钢在某 些方面的性能。尽管如此,由于氮是强 烈提高钢冷脆性的一个元素。所以对钢 中的氮也必须给予足够的重视。
(一)钢中氮的来源 钢中的氮主要来源于炼钢过程中的炉气和金 属原料(如含Cr, V, Al, Ti较高的废钢和铁合金)。 目前主要采用的炼钢方法中,以氧气转炉炼钢 法生产的钢材氮的质量分数最低,所以使用的 氧气越纯净,钢液中氮就越少。例如要使钢中 氮的质量分数小于0.003%,则氧气纯度必须大 于99%。而电沪冶炼的钢材一般含氮都较高, 因为高温电弧不但使炉气和原料中的氮分子易 于分解,而且也容易被熔池吸附。
从上式中可看出,当炉气中水的蒸汽压 PH2O增大时,ωH必定增大;而当ωO高时,不利 于水蒸气的分解。因此,在炼钢末期和电弧炉 炼钢的还原期,钢液最易于从炉气中吸氢。 此外,钢中含氢量与钢的冶炼方法、钢种成分 也有关系。在三种主要炼钢方法(碱性平炉、碱 性电弧炉、氧气顶吹转炉)中,电弧炉钢中的氢 含量最高,这主要是因为电弧区的高温(高于 3000℃ )使炉气中的水蒸气易于分解且被钢液 吸收。而氧气顶吹转炉使用工业纯氧进行吹炼, 炉气中水蒸气分压低,加之其熔池脱碳反应激 烈,故使钢中氢含量最低。
2. 炼钢过程中氢和氮的控制

20
Solubility of nitrogen in liquid iron alloys at 1600 oC 氮在1600℃液态铁合金中的溶解度
21
Analytical tolerances (%) at AM IH #2 SP
Element Nitrogen Sulfur Range < 0.0050 < 0.005 0.005 - 0.007 0.007 - 0.010 0.010 - 0.020 < 0.050 0.05 - 0.40 .01 - .10 .10 - .20 .20 - .50 ARL Spectrometer ( 3 s ) 0.0015 ( LECO 0.0009 ) 0.0007 0.0010 0.0012 0.0018 0.0027 0.007 0.0052 0.009 0.015
6
0 2
4
6
8 10 12 14
Source of hydrogen 氢的来源
• Hydrogen 氢气 • Moisture 水分 Scrap 废钢 Lime 石灰 Ferroalloys 铁合金 Coal 煤 Gases – O2, N2, Ar 气体 - 氧气,氮气,氩气 Ladle and tundish fluxes and refractory 钢包和中间包保护渣和耐材 Mold powders 结晶器保护渣 Atmosphere 空气
Control of H in Steelmaking 煉钢过程中氫的控制
蔡焕堂
Hunan Valin Steel Company
0
Problems associated with H2 in steel
炼钢中与氢相关的问题
2. 炼钢过程中氢和氮的控制

3
Hydris – Direct measurement of hydrogen Hydris – 直接测量氢
Schematic of the measuring system showing the gas flow through the pneumatic unit and the immersion probe. 测量系统展示气体流经气动单元 和浸没探头简图
脱氢处理才实现。
1
Hydrogen sampling methods 氢的取样
• Silica tube 石英管
• Hydris
2
Loss of hydrogen in pin sample 针样品中氢的损失
Hydrogen diffuses out of the sample unless it is kept in very low temperature. 氢会从样品中扩散出去,除非 它能保持在非常低的温度下。
Low hydrogen steels e.g. Line pipe grades for severe weather applications require a hydrogen level of less than 3ppm, which can only be achieved via a tank or RH degasser. 低氢钢 ,例如某些气候下应用的管线钢要求氢含量低于3ppm, 只能通过真空罐或RH
23
Nitrogen control in steelmaking 炼钢过程中氮的控制
• • • • • • • Hot metal nitrogen content 铁水中氮含量 Hot metal ratio 铁水比 Partial pressure of N2 in blowing oxygen 氧气中的氮含量 BOF lining life 转炉炉衬寿命 BOF blowing practice 转炉吹炼工艺 Ore consumption 铁矿石消耗 Scrap melting 废钢熔化情况
钢铁行业氮氧化物控制技术及对策
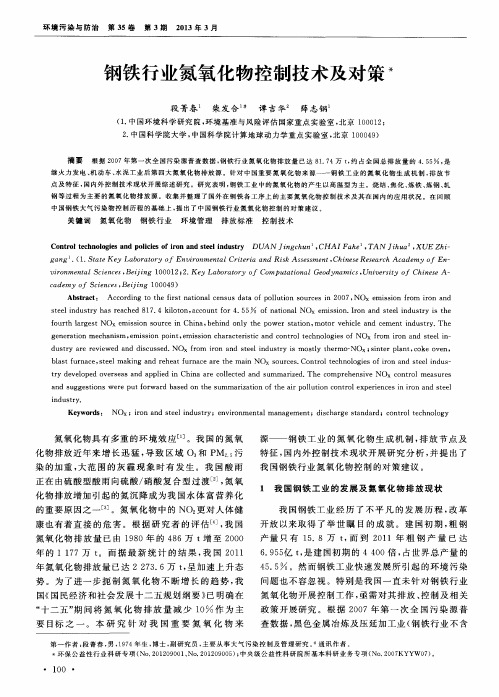
第一作者 : 段菁 春, 男, 1 9 7 4年 生 , 博士 , 副研 究 员 , 主 要 从 事 大 气 污 染 控制 及 管 理 研 究 。 通讯作者。 *环 保 公 益 性行 业 科 研 专 项 ( No . 2 0 1 2 0 9 0 0 1 、 No . 2 0 1 2 0 9 0 0 5 ) ; 中 央 级公 益 性 科 研 院 所 基 本科 研 业 务 专 项 ( No . 2 0 0 7 K YYW0 7 ) 。
昌
用, 从 源头 限制 污染物 排放量 和减 少 固体 燃料 消耗 。
曼
赠
其循 环废 气 量 大 约 为 4 o ~4 5 %, 相 应 含 氧 气 为
1 4 ~ 1 5 , 能够 减 少 废 气 排放 量 大 约 4 5 ~ 5 O 。E O S能够起 到 多污 染物 减 排 的效 果 , 对 氮 氧 化 物减 排 的效 果是 3 O ~4 5 。
s t e el i ndu s t r y h as r e ac he d 81 7. 4 ki l ot on, a c c oun t f or 4.5 5 o f n a t i ona l N Ox e mi s s i o n. I r o n a nd s t e e l i nd us t r y i s t h e
的重要 原 因之一口 ] 。氮 氧化物 中的 NO 更对 人体 健 康也有 着直 接 的危 害 。根 据 研 究 者 的 评估 ] , 我 国
氮氧化 物 排 放量 已 由 1 9 8 0年 的 4 8 6万 t 增至 2 0 0 0
我 国钢铁 工业 经 历 了不 平 凡 的 发 展历 程 , 改革
采样位置: 烧 结 床 长 度
钢中氢气体知识问答(3)
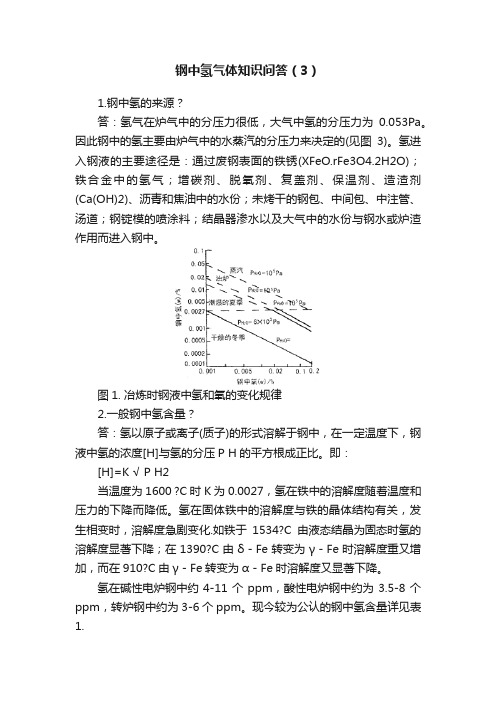
钢中氢气体知识问答(3)1.钢中氢的来源?答:氢气在炉气中的分压力很低,大气中氢的分压力为0.053Pa。
因此钢中的氢主要由炉气中的水蒸汽的分压力来决定的(见图3)。
氢进入钢液的主要途径是:通过废钢表面的铁锈(XFeO.rFe3O4.2H2O);铁合金中的氢气;增碳剂、脱氧剂、复盖剂、保温剂、造渣剂(Ca(OH)2)、沥青和焦油中的水份;未烤干的钢包、中间包、中注管、汤道;钢锭模的喷涂料;结晶器渗水以及大气中的水份与钢水或炉渣作用而进入钢中。
图1. 冶炼时钢液中氢和氧的变化规律2.一般钢中氢含量?答:氢以原子或离子(质子)的形式溶解于钢中,在一定温度下,钢液中氢的浓度[H]与氢的分压P H的平方根成正比。
即:[H]=K √ P H2当温度为1600 ?C时K为0.0027,氢在铁中的溶解度随着温度和压力的下降而降低。
氢在固体铁中的溶解度与铁的晶体结构有关,发生相变时,溶解度急剧变化.如铁于1534?C由液态结晶为固态时氢的溶解度显著下降;在1390?C由δ-Fe转变为γ-Fe时溶解度重又增加,而在910?C由γ-Fe转变为α-Fe时溶解度又显著下降。
氢在碱性电炉钢中约4-11个ppm,酸性电炉钢中约为3.5-8个ppm,转炉钢中约为3-6个ppm。
现今较为公认的钢中氢含量详见表1.表1. 一般钢中氢含量3.钢中氢对钢性能的危害?答:氢溶入钢中会降低钢的塑性和韧性。
研究表明,氢含量高不仅会导致钢的伸长率和面缩率急剧降低,还易产生氢致裂纹缺陷。
钢在冷却放置过程中,氢呈过饱和固溶体状态,由于其具有极强的扩散能力,很可能聚集在某些部位,使钢产品的局部压力增高,产生白点,形成内裂,进一步诱发高碳钢的疲劳损伤,严重影响其使用性能。
另一方面,冷却放置时,氢也能扩散到大气中,从而降低钢中的氢含量,减弱其危害。
4. 如何降低钢中氢?答:溶解在钢中的氢和氮以原子状态存在,其溶解反应为:{}[]H H =2%21在一定温度下达到平衡时: []212%H H P H K =[]2%H H P K H ?=上式说明氢在钢中的溶解度与作用在钢液面上的氢的分压的平方根成正比,即称西华特定律。
转炉钢中h n o 的含量

转炉钢中H、N、O的含量一、引言转炉钢是指通过转炉炼钢法生产的钢种,具有低碳、低硫、低磷等优点,广泛应用于建筑、机械、汽车、船舶等领域。
在转炉钢的生产过程中,氢(H)、氮(N)和氧(O)是重要的杂质元素,对钢的性能产生重要影响。
本文将对转炉钢中H、N、O的含量及其影响因素进行深入探讨,旨在为控制转炉钢的质量提供理论支持。
二、H、N、O在转炉钢中的存在形式在转炉钢中,H、N、O主要以溶解状态存在,形成如NH₃、OH⁻、H₂等化合物,另外还有一些以固态氧化物形式存在的杂质。
这些杂质元素在钢中的存在形式和含量受到炼钢原料、冶炼工艺和操作条件等因素的影响。
三、转炉钢中H、N、O的含量及影响因素1.氢(H)的含量及影响因素:转炉钢中的氢含量一般在0.001%~0.005%之间。
氢的主要来源是炼钢原料中的水分和空气中水蒸气的冷凝。
此外,钢铁料中的含碳物质也是氢的来源之一。
为降低转炉钢中的氢含量,应严格控制炼钢原料的水分,并加强炉气氛围的保护,避免空气中的水分进入炉内。
2.氮(N)的含量及影响因素:转炉钢中的氮含量一般在0.002%~0.01%之间。
氮的主要来源是炼钢原料中的含氮物质和空气中的氮气。
氮在高温下易溶于钢液中,难以去除。
为降低转炉钢中的氮含量,应选用低氮原料,如低氮生铁、低氮废钢等。
同时,加强炉气氛围的保护,减少空气中的氮气进入炉内也是重要的措施。
3.氧(O)的含量及影响因素:转炉钢中的氧含量一般在0.001%~0.01%之间。
氧的主要来源是炼钢过程中空气中的氧气和水蒸气与钢液反应产生的氧化物。
为降低转炉钢中的氧含量,应加强炉气氛围的保护,减少空气中的氧气和水蒸气进入炉内。
同时,采用合适的造渣工艺和脱氧合金化工艺也是重要的措施。
四、H、N、O对转炉钢性能的影响H、N、O等杂质元素对转炉钢的性能产生重要影响,主要表现在以下几个方面:1.力学性能:H、N、O等杂质元素会降低转炉钢的强度和韧性,特别是对于高强度级别钢材的影响更为显著。
炼钢过程钢中氧的控制
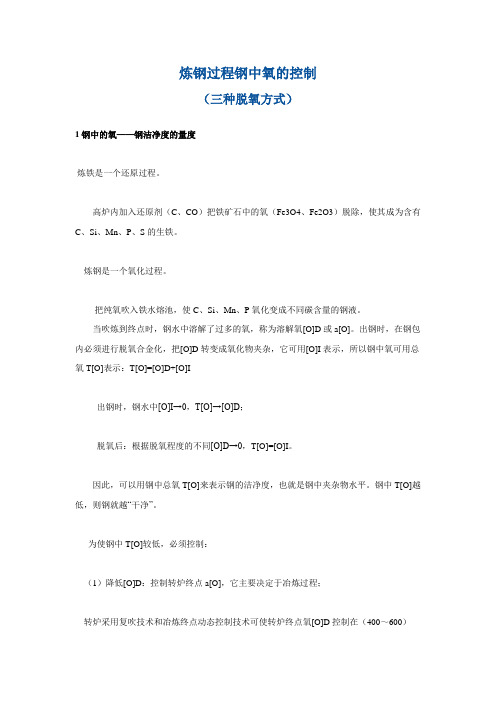
炼钢过程钢中氧的控制(三种脱氧方式)1 钢中的氧——钢洁净度的量度炼铁是一个还原过程。
高炉内加入还原剂(C、CO)把铁矿石中的氧(Fe3O4、Fe2O3)脱除,使其成为含有C、Si、Mn、P、S的生铁。
炼钢是一个氧化过程。
把纯氧吹入铁水熔池,使C、Si、Mn、P氧化变成不同碳含量的钢液。
当吹炼到终点时,钢水中溶解了过多的氧,称为溶解氧[O]D或a[O]。
出钢时,在钢包内必须进行脱氧合金化,把[O]D转变成氧化物夹杂,它可用[O]I表示,所以钢中氧可用总氧T[O]表示:T[O]=[O]D+[O]I出钢时,钢水中[O]I→0,T[O]→[O]D;脱氧后:根据脱氧程度的不同[O]D→0,T[O]=[O]I。
因此,可以用钢中总氧T[O]来表示钢的洁净度,也就是钢中夹杂物水平。
钢中T[O]越低,则钢就越“干净”。
为使钢中T[O]较低,必须控制:(1)降低[O]D:控制转炉终点a[O],它主要决定于冶炼过程;转炉采用复吹技术和冶炼终点动态控制技术可使转炉终点氧[O]D控制在(400~600)×10-6范围。
(2)降低夹杂物的[O]I:控制脱氧、夹杂物形成及夹杂物上浮去除——夹杂物工程概念(Inclusion Engineering)。
随着炉外精炼技术的发展,钢中的总氧含量不断减低,夹杂物越来越少,钢水越来越“干净”,甚至追求“零夹杂物”,钢材性能不断改善。
1970~2000年钢中T[O]演变,由于引入炉外精炼,对于硅镇静钢,T[O]可达(15~20)×10-6,对于铝镇静钢,T[O]可达到<10×10-6。
(3)连铸过程:一是防止经炉外精炼的“干净”的钢水不再污染,二是要进一步净化钢液,使连铸坯中的T[O]达到更低的水平。
钢中T[O]量与产品质量关系举例如下:(1)轴承钢T[O]由30×10-6降到5×10-6,疲劳寿命提高100倍。
(2)钢中T[O]与冷轧板表面质量存在明显的对应关系。
钢中氧的控制及氧化物冶金

钢中氧的控制及氧化物冶金钢铁工业是世界上最重要的基础产业之一,钢铁产品广泛应用于建筑、交通、机械、电力、航空航天等领域。
在钢铁生产过程中,氧气是一个重要的助燃剂和氧化剂,但过多的氧气会影响钢的质量和性能,因此需要控制钢中氧含量。
本文将介绍钢中氧的控制方法及氧化物冶金的应用。
一、钢中氧的来源和影响钢中氧的来源主要有两个:一是钢水中的氧气,二是钢水和钢渣之间的氧化反应产生的氧化物。
在钢水中,氧气的含量越高,钢中氧的含量就越高,同时也会影响钢的成分和组织。
过多的氧气会使钢中杂质含量增加,同时也会使钢中的碳、硫等元素含量降低,从而影响钢的强度和韧性。
此外,钢中氧的含量还会影响钢的表面质量和机械性能,如表面氧化、裂纹、脆性等。
二、钢中氧的控制方法1. 氧气吹炼法:氧气吹炼法是一种常用的钢中氧控制方法,通过向钢水中吹入氧气,使钢水中氧气与钢中的杂质发生反应,从而将杂质氧化掉。
这种方法可以有效地降低钢中氧含量,提高钢的质量和性能。
但是,过多的氧气吹入会引起钢水温度升高,从而影响钢的成分和组织,因此需要控制氧气的吹入量和时间。
2. 氮气保护法:氮气保护法是一种较为先进的钢中氧控制方法,通过向钢水中吹入氮气,形成氮气保护层,防止氧气与钢水发生反应,从而降低钢中氧含量。
这种方法不仅能够控制钢中氧含量,还能够保护钢水不受空气污染,提高钢的纯度和质量。
3. 真空处理法:真空处理法是一种高端的钢中氧控制方法,通过将钢水置于真空状态下,使钢水中的氧气和气体得以排出,从而降低钢中氧含量。
这种方法不仅能够控制钢中氧含量,还能够提高钢的纯度和质量,但是成本较高,适用范围较窄。
三、氧化物冶金的应用氧化物冶金是一种利用氧化物进行冶金反应的技术,它能够有效地控制钢中氧含量,提高钢的质量和性能。
氧化物冶金主要有以下几种应用:1. 氧化物还原法:氧化物还原法是一种利用氧化物进行还原反应的技术,通过向钢水中添加氧化物,使氧化物与钢中的杂质发生反应,从而将杂质还原掉。
钢中氮的来源及控制
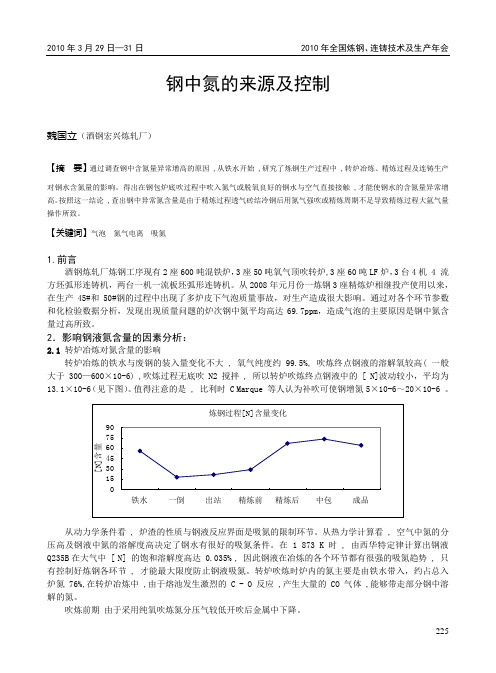
钢中氮的来源及控制魏国立(酒钢宏兴炼轧厂)【摘要】通过调查钢中含氮量异常增高的原因 ,从铁水开始 ,研究了炼钢生产过程中 ,转炉冶炼、精炼过程及连铸生产对钢水含氮量的影响。
得出在钢包炉底吹过程中吹入氮气或脱氧良好的钢水与空气直接接触 ,才能使钢水的含氮量异常增高。
按照这一结论 ,查出钢中异常氮含量是由于精炼过程透气砖结冷钢后用氮气强吹或精炼周期不足导致精炼过程大氩气量操作所致。
【关键词】气泡氮气电离吸氮1.前言酒钢炼轧厂炼钢工序现有2座600吨混铁炉,3座50吨氧气顶吹转炉,3座60吨LF炉,3台4机 4 流方坯弧形连铸机,两台一机一流板坯弧形连铸机。
从2008年元月份一炼钢3座精炼炉相继投产使用以来,在生产45#和50#钢的过程中出现了多炉皮下气泡质量事故,对生产造成很大影响。
通过对各个环节参数和化检验数据分析,发现出现质量问题的炉次钢中氮平均高达69.7ppm,造成气泡的主要原因是钢中氮含量过高所致。
2.影响钢液氮含量的因素分析:2.1转炉冶炼对氮含量的影响转炉冶炼的铁水与废钢的装入量变化不大 , 氧气纯度约 99.5%, 吹炼终点钢液的溶解氧较高( 一般大于 300—600×10-6) ,吹炼过程无底吹 N2 搅拌 , 所以转炉吹炼终点钢液中的 [ N]波动较小,平均为13.1×10-6(见下图)。
值得注意的是 , 比利时 C Marque 等人认为补吹可使钢增氮5×10-6~20×10-6 。
从动力学条件看 , 炉渣的性质与钢液反应界面是吸氮的限制环节。
从热力学计算看 , 空气中氮的分压高及钢液中氮的溶解度高决定了钢水有很好的吸氮条件。
在 1 873 K 时 , 由西华特定律计算出钢液Q235B在大气中 [ N] 的饱和溶解度高达 0.035% , 因此钢液在冶炼的各个环节都有很强的吸氮趋势 , 只有控制好炼钢各环节 , 才能最大限度防止钢液吸氮。
- 1、下载文档前请自行甄别文档内容的完整性,平台不提供额外的编辑、内容补充、找答案等附加服务。
- 2、"仅部分预览"的文档,不可在线预览部分如存在完整性等问题,可反馈申请退款(可完整预览的文档不适用该条件!)。
- 3、如文档侵犯您的权益,请联系客服反馈,我们会尽快为您处理(人工客服工作时间:9:00-18:30)。
造还原渣 < 100 ( C = 0. 10 %) 300~500
4. 1. 1 氢的来源
氢气在炉气中的分压力很低 , 大气中氢的分 压力为 0. 053 Pa 。因此钢中的氢主要由炉气中的 水蒸汽的分压力来决定的 ( 见图 3) 。氢进入钢液 的主 要 途 径 是 : 通 过 废 钢 表 面 的 铁 锈 ( XFeO ・ rFe3O4・ 2H2O) ; 铁合金中的氢气 ; 增碳剂 、 脱氧剂 、 沥青和焦油 复盖剂 、 保温剂 、 造渣剂 ( Ca ( OH) 2 ) 、 中的水份 ; 未烤干的钢包 、 中间包 、 中注管 、 汤道 ; 钢锭模的喷涂料 ; 结晶器渗水以及大气中的水份 与钢水或炉渣作用而进入钢中 。
80 × 10 - 6 以外 , 到目前为止 , 根据已有的资料 , 还
没有见到将钢中氢 、 氮、 氧作为有害元素控制的新 标准发布或颁布 。 我国有炉外精炼装置 , 经真空处理的钢不足
联系人 : 高海潮 ,高级工程师 ,安徽省马鞍山市 (243000) 马鞍山钢铁股份有限公司第一炼钢厂
© 1994-2007 China Academic Journal Electronic Publishing House. All rights reserved.
1 前 言
1996 年 ,我国的钢产量突破 1 亿 t ,成为世界
在分析钢的缺陷时已形成了共识 。20 世纪 50 年 代后 ,人们着手深入研究对钢的脱氢 、 脱氮 、 脱氧 。 到目前为止从某种意 义上讲 ,对氢 、 氮、 氧的控制 和要求 ,即反映出整条工艺路线的综合水平又反映 出一个工厂所能生产高附加值产品档次的高低。
表3 三种炼钢炉终点钢水中 [ H] 、 [N ] 、 [O ] 的含量 (w) × 10 - 6 冶炼方法 平炉 电炉 转炉
[ H] 3~8 4~7 3~5 [N ] 40~60 70~140 20~40 [O ] ( C = 0. 10 %) 400~600
图4 全程吹氧时钢中含氮量的变化
1. 氮流量 0. 25Nm3/ min・ t 终点 w(C) - 0. 065 % ; 2. 氮流量 0. 2Nm3/ min・ t 终点 w(C) - 0. 037 % ; 3. 氮流量 0. 19Nm3/ min・ t 终点 w(C) - 0. 048 % ; 4. 氮流量 0. 13Nm3/ min・ t 终点 w(C) - 0. 032 % ; 5. 氮流量 0. 09Nm3/ min・ t 终点 w(C) - 0. 079 % ;
的飞跃 。通常这种钢是指 [ S ] 、 [ P]、 [ H] 、 [N] 、 T - 6 [O ] 含量 (w) 总和 ≯ 100 × 10 。当然还有一种观
© 1994-2007 China Academic Journal Electronic Publishing House. All rights reserved.
图1 日本商业生产纯净钢 [ C] 、 [ P] 、 [ S] 的计划
表 1、 表 2 是我们收集到的资料 ,以及对国内 外产品的检验报告 ,经整理列出的一些代表钢种 , 仅供参考 。
3 结净钢或纯净钢的出现及发展
中国的钢铁市场是国际市场的一部分 。中国 钢铁企业不能生产的或实物质量上尚存不足的产 品 ,还得从国外大量进口 , 这个量每年仍有 1 000 ~1 500 万 t 。要实现从量变到质变 , 值得一提的 ( Clean - steel ) 或 是国外生产的所谓 “洁净钢” “纯
炼 钢 2000 年第 2 期 ・40 ・ 当进入钢中的气体量超过冶炼过程脱碳沸腾的脱 气量时 ,钢中气体的含量就增加 [4 ] 。各种不同的 炼钢炉 ,终点钢水中都含有一定量的氢 、 氮、 氧 ,实 测和统计情况见表 3 。
2 我国钢中氢 、 氮、 氧的控制与外国先进
水平的现状
对钢中氢 、 氮 、 氧要求 ,我国已有一些部门和 行业标准 ,也包括企业内控标准 ,在一些特殊用途 的钢上做出了规定 。如马钢快速客车轮钢中含氢 (w) ≤ 3. 5 × 2× 10 - 6 ,重载货车轮钢中含氢 (w) ≤ - 6 10 ;特钢企业生产的轴承钢对全氧提出明确的 要求 。但在我国的国家标准 ( G B ) 中 , 除了众所周 知的对优质碳素结构钢提出过钢中含氮的 (w) ≯
[ H] [N ] 30~40 30~40 10~40 T[O ]
≤ 2 ≤ 2 ≤ 1. 6
≤ 40
40~60
≤ 15 < 20 ≤ 30 10~30
(D ≤ μ 40 m) 20~30 (D ≤ μ 20 m)
< 1. 5 <2
≤ 25 ≤ 40 10~20 ≤ 35 ≤ 35
≤ 20 ≤ 10 ≤ 30 < 30
含量 ( 见图 4) ; 铁合金 、 废钢铁和渣料中的氮也会 随炉料带入钢水 。
4. 1. 3 氧的来源
氧在各种炼钢炉冶炼终点时都以一定量存在 于钢水中 ,氧是我们供给的这是不言而喻的 。因 为炼钢过程首先是氧化过程 , 脱 [ P ] 、 脱 [ S] 、 脱 [ Si ] 、 脱 [ C] 都需要向铁水供氧 。但随着炼钢过程 的进行 ,尽管工艺操作千变万化 ,可是炼钢炉内熔 池中钢液的 [ C ] 、 [ O ] 的关系却有着共同的规律 性 。即随着 [ C ] 的逐步降低 , [ O ] 却在逐步增高 , [ C] 和 [O ] 有着相互对应的平衡关系 。( 见图 5) 。
Sources and Control Measures of Hydrogen , Nitrogen and Oxygen in Steel
Gao Haichao (Ma Anshan Iron & Steel Co. Ltd. ) Abstract The contents of hydrogen , nitrogen and oxygen in steel produced in our country and other countries are compared in this paper. The requirements for clean steel are increased. The analysis on sources of H ,N ,O in steel have been carried out . The rule of changes in H and O con2 tents , N change in oxygen - blowing process and the relationship between C and O have been dis2 cussed herein. The effective measures of decreasing steel pollution are put forward , and the main ogy for mloten steel cleaning is then concluded. Keyworks clean steel source steel pollution control measure
2000 年 4月 炼 钢 Apr. 2000 Steelmaking Vol . 16 No. 2 ・38 ・ 第 16 卷 第 2 期
钢中氢 、 氮、 氧的来源及其控制对策
高海潮
( 马鞍山钢铁股份有限公司)
摘 要 比较了国内外钢中氢 、 氮、 氧的水平 ,叙述了国外对纯净钢要求不断提高的过程 ,分析了钢 中氢 、 氮、 氧的来源 ,讨论了氢和氧的变化规律 、 吹氧过程中氮的变化以及碳和氧的关系 ,提出了减少钢 污染的有效方法 ,总结出净化钢液的主要技术措施 。 关键词 纯净钢 来源 钢污染 控制 措施
[N ] ≤ 14 、 T[ O ] ≤ 5、 [ H] ≤ 0. 5 , 总含量 ≤ 51. 5 × - 6 ( ) 10 见图 1 、 图2 。
≤ 2 1. 5~3. 3 1. 5~3. 5
≤ 25 25~55 40~50
表2 国外钢中氢 、 氮、 氧控制的先进水平及现状 (w) × 10 - 6 品 种 车轮轮箍 重轨 耐蚀结构钢 超低碳薄板 优硬线材 汽车钢板 中厚钢板 合金钢棒材 管线钢 冷墩钢
第一产钢大国 。但与世界主要发达产钢国家相 比 ,在品种结构 、 产量质量 、 技术装备 、 能源消耗 、 生产成本等方面还有不少的差距 ,因此 ,我们还没 有成为世界钢铁强国 [1 ] 。 世界上发达的钢铁工业国家都经历了同样的 发展历程 。即先是粗钢在量上按年份绝对增长 , 到达一定高峰后调整结构 , 转而追求品种质量 。 当品种质量占据市场的绝对份额后 , 由于激烈的 竞争 ,相继在高附加值的精品上下功夫 。人们在 20 世纪 50 年代前 ,主要致力于脱磷 、 脱硫 、 脱氧 。 ( 脱磷 、 随现代铁水预处理技术的发展 “三脱” , 脱 [2 ] 硫、 脱硅) 在生产上已实现了最经济成本 。人们 可以把普通钢的硫磷比一般标准 ≯ 0. 040 %再降 至更低的水平 。这样磷 、 硫的危害在下降的同时 , 氢、 氮、 氧对钢的危害则愈加显露出来 。钢中氢的 致裂 , 氮的发脆 , 全氧与钢中夹杂物的紧密关系 ,
( Purity - steel) ,在对钢的纯净度上出现了质 净钢”
图2 日本商业生产纯净钢 [ H] 、 [N ] 、 [O ] 的计划
4 影响钢中氢 、 氮、 氧的因素与其控制 4. 1 钢中氢 、 氮、 氧的来源
在常压下进行钢的冶炼 , 气体除铁水中已溶 解的外 ,还可以通过各种原辅料及炉气进入钢液 。
高海潮 : 钢中氢 、 氮、 氧的来源及其控制对策 钢产量的 1/ 10 。以 4 大钢铁企业为例 。由于各家 产品不同 , 工艺不同 , 精炼装置的不同 , 氢 、 氮、 氧 波动幅度较大 。即便以我国先进的拥有真空处理 装备的炼钢厂与国外相比 , 在这方面仍有较大差 距 ( 见表 1 、 表 2) 。