钢中氮含量的控制
钢中氮含量的控制
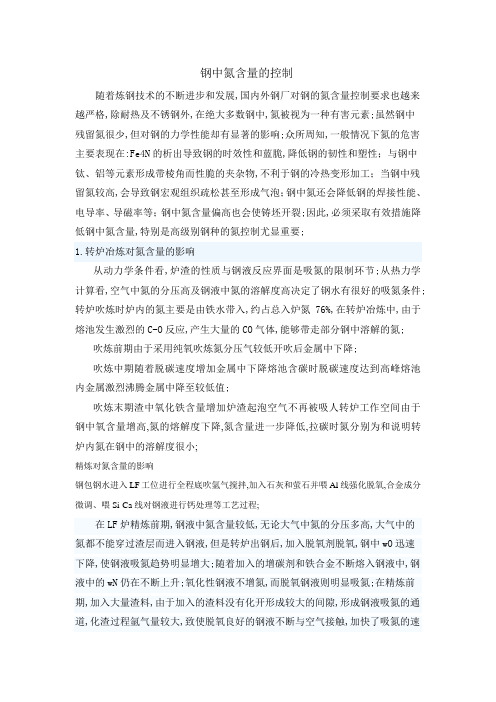
钢中氮含量的控制随着炼钢技术的不断进步和发展,国内外钢厂对钢的氮含量控制要求也越来越严格,除耐热及不锈钢外,在绝大多数钢中,氮被视为一种有害元素;虽然钢中残留氮很少,但对钢的力学性能却有显著的影响;众所周知,一般情况下氮的危害主要表现在:Fe4N的析出导致钢的时效性和蓝脆,降低钢的韧性和塑性;与钢中钛、铝等元素形成带棱角而性脆的夹杂物,不利于钢的冷热变形加工;当钢中残留氮较高,会导致钢宏观组织疏松甚至形成气泡;钢中氮还会降低钢的焊接性能、电导率、导磁率等;钢中氮含量偏高也会使铸坯开裂;因此,必须采取有效措施降低钢中氮含量,特别是高级别钢种的氮控制尤显重要;1.转炉冶炼对氮含量的影响从动力学条件看,炉渣的性质与钢液反应界面是吸氮的限制环节;从热力学计算看,空气中氮的分压高及钢液中氮的溶解度高决定了钢水有很好的吸氮条件;转炉吹炼时炉内的氮主要是由铁水带入,约占总入炉氮76%,在转炉冶炼中,由于熔池发生激烈的C-O反应,产生大量的CO气体,能够带走部分钢中溶解的氮;吹炼前期由于采用纯氧吹炼氮分压气较低开吹后金属中下降;吹炼中期随着脱碳速度增加金属中下降熔池含碳时脱碳速度达到高峰熔池内金属激烈沸腾金属中降至较低值;吹炼末期渣中氧化铁含量增加炉渣起泡空气不再被吸人转炉工作空间由于钢中氧含量增高,氮的熔解度下降,氮含量进一步降低,拉碳时氮分别为和说明转炉内氮在钢中的溶解度很小;精炼对氮含量的影响钢包钢水进入LF工位进行全程底吹氩气搅拌,加入石灰和萤石并喂Al线强化脱氧,合金成分微调、喂Si-Ca线对钢液进行钙处理等工艺过程;在LF炉精炼前期,钢液中氮含量较低,无论大气中氮的分压多高,大气中的氮都不能穿过渣层而进入钢液,但是转炉出钢后,加入脱氧剂脱氧,钢中wO迅速下降,使钢液吸氮趋势明显增大;随着加入的增碳剂和铁合金不断熔入钢液中,钢液中的wN仍在不断上升;氧化性钢液不增氮,而脱氧钢液则明显吸氮;在精炼前期,加入大量渣料,由于加入的渣料没有化开形成较大的间隙,形成钢液吸氮的通道,化渣过程氩气量较大,致使脱氧良好的钢液不断与空气接触,加快了吸氮的速度;另外在电极加热时,电弧最高温度可以达到6000℃;电弧作用到钢液上时,这部分钢液较其它部位的钢液温度高,超过2300℃;而当钢液温度超过2130℃时,发生如下反应:N2=2Ng 1Ng+Q=N 2在渣界面存在大量被电离的N,随着氧、硫在钢中的浓度急剧下降,吸氮趋势加强;被电离的N在裸露区域被钢液吸入,钢液中氮含量增加;渣料完全融化后,渣子覆盖在钢水表面;氩气压力降低,避免吹开渣层,这样隔绝了氮气跟钢水的接触,避免了N的吸入;精炼结束后,进行成分的微调和Ca处理过程中,会造成一定的增氮量,,喂线Ca-Si过程增氮,主要是由于Ca气化形成Ca气泡将钢液面吹开,造成裸露的钢液从空气中吸氮而产生的;Ca-Si线本身的增氮;如果渣层较厚线穿过渣层进人钢液而不把钢液面吹开,就有可能避免裸露钢液吸氮,这就是部分炉次喂线过程钢液没有增氮的原因;另外,LF炉渣碱度的控制也不容忽视,有研究表明:LF炉渣碱度不宜大于,否则渣的熔点升高,可能会有部分炉渣未完全熔化造成炉渣结构松散而存有空隙,使钢液吸氮的可能性增加;3.连铸浇铸对氮含量的影响连铸过程中为了防止钢包钢流和中间包钢流的二次氧化和吸氮,普遍采用保护浇注技术;连铸机连铸过程钢包到中间包之间的钢水保护采用大包长水口加氩气密封和中间包加覆盖剂保护钢液;中间包到结晶器的保护采用浸入式水口加连铸保护渣对钢液进行保护浇注,防止二次氧化和吸氮;由于该保护措施使得钢液与空气完全隔离,钢液从中间包到结晶器二次氧化和吸氮现象很弱,基本上不增氮;综上,连铸过程增氮主要发生在钢包到中间包之间的环节上,保护浇注系统的完善程度决定了,该阶段的保护工作是连铸段防止增氮的主要任务;连铸开浇时第一包钢水进入中间包开始阶段属于敞开浇铸,钢水会吸氮;连铸机长水口如密封不良,将会象一个抽气泵一样把空气从接缝处吸入;为防止在接缝处吸入空气,可以在接缝处通入Ar气,使长水口顶部形成正压区,基本可避免吸氮;综合分析以上因素,采取相应的措施,即可避免氮造成的皮下气泡等钢的质量问题;。
钢铁行业氮氧化物控制技术及对策
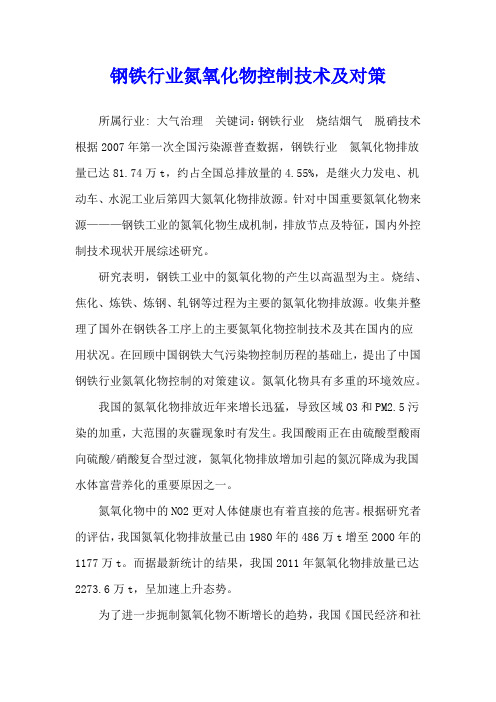
钢铁行业氮氧化物控制技术及对策所属行业: 大气治理关键词:钢铁行业烧结烟气脱硝技术根据2007年第一次全国污染源普查数据,钢铁行业氮氧化物排放量已达81.74万t,约占全国总排放量的4.55%,是继火力发电、机动车、水泥工业后第四大氮氧化物排放源。
针对中国重要氮氧化物来源———钢铁工业的氮氧化物生成机制,排放节点及特征,国内外控制技术现状开展综述研究。
研究表明,钢铁工业中的氮氧化物的产生以高温型为主。
烧结、焦化、炼铁、炼钢、轧钢等过程为主要的氮氧化物排放源。
收集并整理了国外在钢铁各工序上的主要氮氧化物控制技术及其在国内的应用状况。
在回顾中国钢铁大气污染物控制历程的基础上,提出了中国钢铁行业氮氧化物控制的对策建议。
氮氧化物具有多重的环境效应。
我国的氮氧化物排放近年来增长迅猛,导致区域O3和PM2.5污染的加重,大范围的灰霾现象时有发生。
我国酸雨正在由硫酸型酸雨向硫酸/硝酸复合型过渡,氮氧化物排放增加引起的氮沉降成为我国水体富营养化的重要原因之一。
氮氧化物中的NO2更对人体健康也有着直接的危害。
根据研究者的评估,我国氮氧化物排放量已由1980年的486万t增至2000年的1177万t。
而据最新统计的结果,我国2011年氮氧化物排放量已达2273.6万t,呈加速上升态势。
为了进一步扼制氮氧化物不断增长的趋势,我国《国民经济和社会发展十二五规划纲要》已明确在“十二五”期间将氮氧化物排放量减少10%作为主要目标之一。
本研究针对我国重要氮氧化物来源———钢铁工业的氮氧化物生成机制,排放节点及特征,国内外控制技术现状开展研究分析,并提出了我国钢铁行业氮氧化物控制的对策建议。
1 我国钢铁工业的发展及氮氧化物排放现状我国钢铁工业经历了不平凡的发展历程,改革开放以来取得了举世瞩目的成就。
建国初期,粗钢产量只有15.8万t,而到2011年粗钢产量已达6.955亿t,是建国初期的4400倍,占世界总产量的45.5%。
然而钢铁工业快速发展所引起的环境污染问题也不容忽视。
40CrB冶炼过程中氮含量的控制
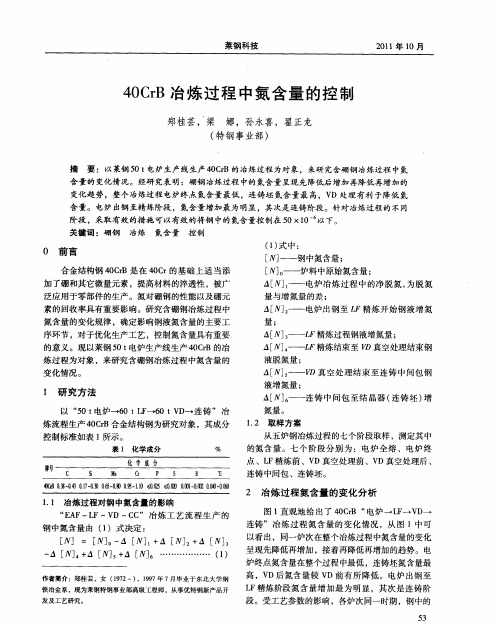
表 1 化学成分
— — — — — — — — — — — — 一
%
的氮含量。七 个阶段分别为 :电炉全熔 、电炉终
点 、L F精炼前 、V D真 空处 理前 、V D真 空处理 后 、 连 铸 中间包 、连 铸坯 。
4 Ⅻ U 8 U 3nl 【 X 3一 4 7 n揶 U6一 ; U 5 1】 ≤ 5 n{ 9一. U O u皿5 为工艺改进前 5炉 4 CB钢各 阶段氮 0r 含量的平均值与改进后新冶炼的 5炉 4 CB钢氮含 0r 量 平均 值 。
3 )针对冶炼过程 的不同阶段 ,采取有效的措 施可以有效将钢中的氮含量控制在 5 1 I以下。 0× 0 6
参 考 文献
[ ]祝真 祥 .转 炉冶 炼钢 中氮含 量 的控 制 [ ].本钢技 1 J
图 1 冶炼不 同时期氮含量 的变化
2 1 电炉 冶炼 过程 氮含量 变化 .
终点 钢液 中 的氮含量 略低 于全 熔钢 液 中的氮 含 量 ,电炉 氮含 量低 于 4 0×1 ~。这 是 由于莱 钢 5 0 0t
电炉铁水 兑入量 比例 不低 于 3 % ,形成 熔池 早 , 5
氮严重 ;钢包在电炉 与 L 之 间停留时间越长 ,氩 F 气流量越大 ,吸氮越严重。钢包内加入的大量增碳
剂 ,也 会使 钢液 大量 增氮 。
保精炼炉埋弧操作 ,降低钢液吸氮量 ;精炼过程避
免大氩气流量搅 拌钢液 ;加入钛 固氮;通过优化 L 精炼炉的操作 ,降低入 V F D炉 时钢液 中的氧硫 含量 ;V D真 空处理 过 程 ,熔 渣 量越 少 越 有 利 于 钢 液中氮的脱除;在保证钢渣不溢出的情况下 ,增加
氮在钢水中的行为及工艺控制研究

山西冶金SHANXI METALLURGY Total 188No.6,2020DOI:10.16525/14-1167/tf.2020.06.17试(实)验研究总第188期2020年第6期氮在钢水中的行为及工艺控制研究晏武,付有彭,张忠福,王哲,任涛,孙海坤,李毅(日照钢铁控股集团有限公司,山东日照276800)摘要:氮元素在钢水中含量过高会导致钢材强度升高,降低钢材的韧性及塑性,严重时会影响钢材的时效性并引发“蓝脆”。
本文介绍了炼钢工序增氮及脱氮的机理,并制定了控氮措施,对转炉工序、精炼工序、RH 真空处理阶段做出了针对性的调整,钢水氮得到了有效控制。
关键词:炼钢增氮危害脱氮中图分类号:TF711文献标识码:A文章编号:1672-1152(2020)06-0041-04收稿日期:2020-07-22第一作者简介:晏武(1988—),男,硕士,毕业于安徽工业大学冶金工程专业,主要从事炼钢工艺技术相关工作。
钢中的氮是以氮化物的形式存在,它对钢质量的影响表现出双重性,氮含量高的钢种长时间放置将会变脆,这一现象称为“老化”或“时效”。
原因是钢中氮化物(Fe 4N )的析出速度很慢,逐渐改变着钢的性能。
钢中氮含量高时,会使钢发生第一类回火脆性,即在250~450℃温度范围内,其表面发蓝,钢的强度升高,冲击韧性降低,称为“蓝脆”。
氮的存在会使铸坯产生结疤和皮下气泡,在轧制过程中产生裂纹和发纹。
氮含量增加,钢的焊接性能变坏,造成焊接热影响区脆化,降低磁导率、电导率。
对于某些钢种氮的存在对其性能有一定的益处,氮可以起到细化晶粒的作用,但由于氮元素原子半径较大,即使在真空条件下扩散速率也不是很大[1],所以如何有效将钢水中氮去除仍是困扰炼钢工序的一个难题。
1氮对钢的影响在590℃时氮在α-Fe 中最高溶解度时约为0.1%,室温下降到0.001%以下。
对于游离氮含量高的钢,在高温下较快冷却时,铁素体将会被饱和,长时间放置,性能将变脆。
LF精炼过程钢中硫、磷、氮、氧含量控制

LF精炼过程钢中硫、磷、氮、氧含量控制作者:钱丹丹陈志月闫若璞来源:《中国科技博览》2016年第07期[摘要]将转炉、平炉或电炉中初炼过的钢液移到另一个容器中进行精炼的炼钢过程,也叫“二次炼钢”。
炼钢过程因此分为初炼和精炼两步进行。
初炼:炉料在氧化性气氛的炉内进行熔化、脱磷、脱碳和主合金化。
精炼:将初炼的钢液在真空、惰性气体或还原性气氛的容器中进行脱气、脱氧、脱硫,去除夹杂物和进行成分微调等。
这样将炼钢分两步进行,可提高钢的质量,缩短冶炼时间,简化工艺过程并降低生产成本。
[关键词]LF精炼脱硫脱磷氮、氧含量 s非金属夹杂物中图分类号:U231.92 文献标识码:A 文章编号:1009-914X(2016)07-0277-011.引言:钢材的质量及性能是根据需要而确定的,不同的需要,要有不同的元素含量。
硫;是钢中的有害杂物,含硫较高的钢在高温进行压力加工时,容易脆裂,通常叫做热脆性。
磷;能使钢的可塑性及韧性明显下降,特别的在低温下更为严重,这种现象叫做冷脆性。
通常情况下,氮被视为钢中的有害元素,而氧元素主要以氧化物系非金属夹杂物的形式存在于钢中。
减少LF 炉精炼工艺过程钢液增氧、去除钢中氢含量是生产优质钢的关键环节。
此外,控制钢中夹杂物是提高钢材使用性能的有效途径。
2.转炉LF精炼脱硫与脱磷2.1脱硫2.1.1脱硫方法硫是钢中的长存元素之一,它会使大多数钢种的加工性能和使用性能变坏,因此除了少数易切削钢种外,它是需要在冶炼中脱除的有害元素。
硫在钢中以[FeS]形式存在,常以[S]表示。
钢中含锰高时,还会有一定的[MnS]存在。
目前炼钢生产中能有效脱除钢中硫的方法有碱性氧化渣脱硫、碱性还原渣脱硫和钢中元素脱硫三种。
2.1.2 脱硫影响因素脱硫影响因素与碱性氧化渣脱硫不同,LF碱性还原渣脱硫反应方程式为:[FeS]+(CaO)=(CaS)+(FeO)(1) [MnS]+(CaO)=(CaS)+(MnO)(2)由于钢中的[S]大部分以[FeS]形式存在,因此脱硫反应主要以式(1)为主。
中碳含硼钢氮含量的控制
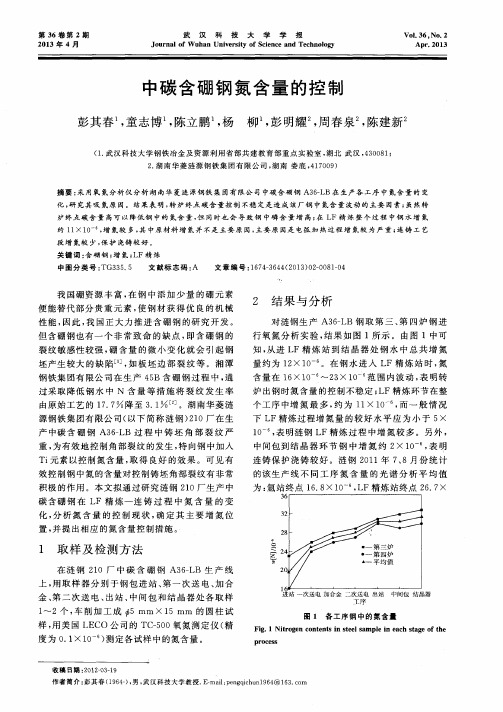
产 中碳 含 硼 钢 A3 6 一 L B过 程 中 铸 坯 角 部 裂 纹 严 重, 为有效 地控 制角 部裂 纹 的发生 , 特 向钢 中加入 Ti 元 素 以控制 氮含 量 , 取得 良好 的效果 。可见 有 效 控 制钢 中氮 的含量 对控 制铸 坯角 部裂 纹有 非常 积极 的作用 。本 文拟 通 过研究 涟钢 2 1 0厂生 产 中 碳含硼钢在 L F精 炼 一连 铸 过 程 中氮 含 量 的 变 化, 分 析 氮 含 量 的控 制 现 状 , 确 定 其 主 要 增 氮 位
度为 0 . 1 ×1 O ) 测 定各试 样 中的氮 含量 。
图 1 各 工 序 钢 中的 氮 含 量
Fi g. 1 Ni t r o g e n c o nt e nt s i n s t e e l s a m pl e i n e a c h s t a g e of t he
源钢 铁集 团有 限公 司 ( 以下 简称 涟 钢 ) 2 1 0厂在 生
个 工序 中增 氮 最 多 , 约为 1 1 ×1 0 一, 而一 般 情 况 下L F精 炼 过程增 氮 量 的 较好 水 平 应 为小 于 5 ×
1 O ~, 表 明涟 钢 L F精炼 过 程 中增 氮 较 多 。另外 ,
2 . 湖 南 华 菱 涟 源钢 铁 集 团有 限公 司 , 湖南 娄底 , 4 1 7 O O 9 )
摘要 : 采 用 氧 氮 分 析 仪 分 析 湖 南华 菱 涟 源钢 铁 集 团有 限公 司 中碳 含 硼 钢 A 3 6 - L B在 生 产 各 工 序 中 氮含 量 的 变
化, 研 究 其 吸 氮 原 因 。结 果 表 明 , 转 炉 终 点碳 含 量控 制 不稳 定 是 造 成 该 厂钢 中氮 含 量 波 动 的 主要 因 素 ; 虽然 转
炼钢过程中钢水氮含量控制
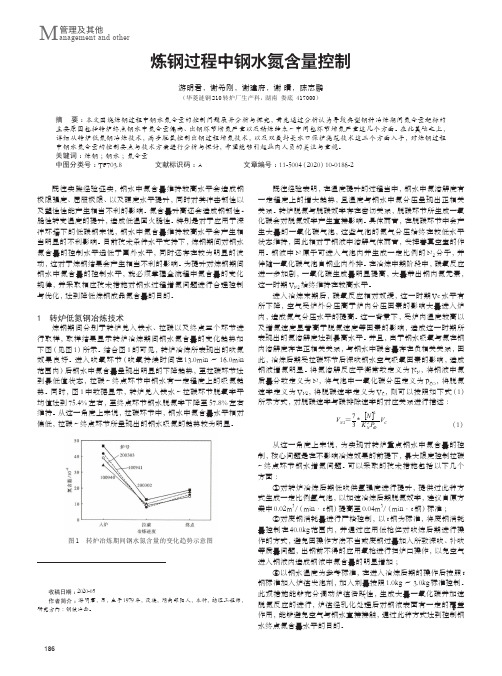
内,造成氮气分压水平的提高。这一背景下,受炉内温度较高以
及增氮速度显著高于脱氮速度等因素的影响,造成这一时期所
表现出的氮溶解度达到最高水平。并且,由于钢水吸氧与氮在钢
ቤተ መጻሕፍቲ ባይዱ
内溶解度存在正相关关系,与钢水中碳含量存在负相关关系,因
此,冶炼后期受拉碳环节后深吹钢水空气吸氧因素的影响,造成
钢液增氮明显。将氮溶解反应平衡常数定义为 KN,将钢液中氮 质量分数定义为 N,将气泡中一氧化碳分压定义为 PCO,将脱氮 速率定义为 VN2,将脱碳速率定义为 VC,则可以按照如下式(1) 所示方式,对脱碳速率与碳排除速率的对应关系进行描述 :
0.0*10-6 ~ 4.0*10-6
脱氧方式 不脱氧
11.0*10-6
3.0*10-6 ~ 22.0*10-6
12.0*10-6
5.0*10-6 ~ 22.0*10-6
铝铁脱氧
表 2 工艺优化前、后出钢环节增氮量示意表
平均值 11.3*10-6
应用前 区间
用。钢液中 N 原子可进入气泡内并生成一定比例的 N2 分子,并 伴随一氧化碳气泡自钢业内外排。在冶炼中期阶段中,碳氧反应
进一步加剧,一氧化碳生成量明显提高,大量带出钢内氮元素,
这一时期 VN2 始终维持在较高水平。 进入冶炼末期后,碳氧反应相对放缓,这一时期 Vc 水平有
所下降,空气受炉外分压高于炉内分压因素的影响大量进入炉
游明君,谢希刚,谢建府,谢 晴,陈志鹏
(华菱涟钢 210 转炉厂生产科,湖南 娄底 417000)
摘 要 :本文围绕炼钢过程中钢水氮含量的控制问题展开分析与探究,首先通过分析认为导致典型钢种冶炼期间氮含量超标的
主要原因包括转炉终点钢水中氮含量偏高、出钢环节增氮严重以及精炼结束 ~ 中间包环节增氮严重这几个方面。在此基础之上,
钢的纯净度评测及其控制

钢的纯净度估测及其控制<The Evaluation Methods and Control of Steel Cleanliness>1.引言随着社会发展和科技进步, 对钢质量, 尤其对它的纯净度(cleanliness)要求越来越高. 除了要降低钢中非金属氧化物夹杂物(non-metallic oxide inclusions)的含量, 控制其尺寸、形貌和成分外, 就洁净钢(clean steel)而言, 还要求控制其硫(S)、磷(P)、氢(H)、氮(N), 甚至碳(C), 并且要尽可能减少钢中金属杂质元素(metallic impurity elements), 诸如: 砷(AS)、锡(Sn) 、锑(Sb)、硒(Se)、铜(Cu)、锌(Zn)、铅(Pb)、镉(Cd)、碲(Te)、铋(Bi)等.不同钢种因其不同的应用场合和条件,对上述要求也各不相同。
例下表所示:表1 对不同钢种典型的纯净度要求(Typical steel cleanliness requirements for various steel grades)钢中的金属杂质元素(metallic impurity elements)通常被视为残余元素(trace elements).由于它们在炼钢和精炼过程很难去除,所以在钢中不断累积,成为废钢供应的一大问题。
鉴于钢中如存在超量的残余金属元素,会造成晶间偏析(intergranular segregation)、有害析出物和其它一些问题。
目前,在钢的生产过程中为了克服钢中残余元素造成的危害,尤其是电炉炼钢,通常采用严格控制废钢的种类和用量。
近年来世界各国普遍采用高炉铁水、直接还原铁、海绵铁、碳化铁或其它相对纯的铁来替代废钢,旨在降低钢中残余元素含量。
从钢中残余元素角度讨论钢纯净度问题近年来已有不少相关研究的报道和论文发表。
我们今天主要讨论钢厂普遍存在,大家又十分关注并想得到解决的问题:〈低碳铝镇静钢氧化物夹杂对其纯净度的影响〉。
钢水过程增氮分析与控制
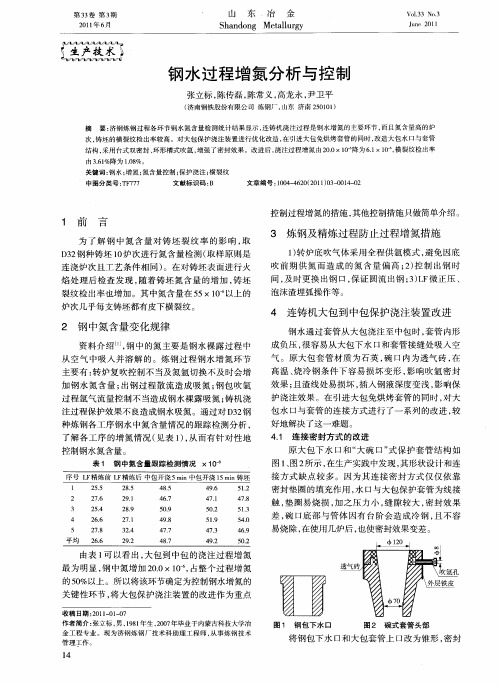
通 过专 门设 计 的石 棉垫 圈与 圆台 , 大包 水 口插 入套 管 后 , 其底 部 与 圆 台 紧密 结合 , 口 内径 与 套 水 管 内径成 直筒 形 , 注时不 易 结冷 钢 。 台式 套管 与 浇
因此 , 中氮含 量对 微合 金化 钢 种铸 坯横 裂纹 钢
产生有 明显影响 , 通过控制钢 中N 含量可有效降低
铸坯 横裂纹 检 出率 。
参考文献 :
[ ] 陆锦 祥 , 1 王忠英 , 陈水盛 , 1 0 B F L — H C 工艺 冶炼 等. t O — F R — C 0 结 构 钢 时 钢 中氮 的行 为及 控 制 [ ] 殊 钢 , 09 6 3 : J. 特 20 , ( )
Ab ta t T ets n ttsia e ut f h i o e o tn nmotnse li v r r c s tpo tema igc u s nJn nS el src: h e t dsaitc lrs l o ent g n c ne ti l te ne eyp o e sse fse l kn o rei ia te a s t r e
表 2 改进 后钢 中氮含量跟踪 检测情况 ×1 O
序号 L 精炼前 L 精炼后 中包开浇 5 i F F n中包 开浇 1 i m 5 n铸坯 m
式大 包套 管 , 型号 套管 与水 口之 间 的压 力集 中在 该 钢包 水 口底部 与套 管 台 阶上 , 不仅 解决 了套 管难 以
3 炼 钢及精炼 过程 防止 过程增氮 措施
1转 炉底 吹气体 采 用全 程供 氩模 式 , 免 因底 ) 避 吹 前 期 供 氮 而 造 成 的氮 含 量 偏 高 ; ) 制 出钢 时 2控 间 , 时 更换 出钢 口 , 及 保证 圆流 出钢 ; ) F 正 压 、 3L 微
降低钢中氮含量的措施

降低钢中氮含量的措施作者:达志鹏来源:《海峡科学》2008年第06期[摘要] 分析了钢液中氮的行为,采用强化碳氧反应,优化脱氧合金化,LF的精炼埋弧工艺,连铸采用全过程保护浇铸等综合控制手段,钢材中的氮含量控制在60ppm以内。
[关键词] 钢液氮保护浇铸1 前言福建省三明钢铁(集团)有限责任公司(以下简称“三钢”)使用100吨转炉—LF精炼炉—10m弧的连铸机生产工艺流程,在开发生产优质的硬线钢和金属制品用钢时,优化复吹模式,采用大流量底吹Ar形成强烈的气流场;LF采用大渣量埋弧操作并缩短加热时间;连铸采用保护浇铸,防止钢液在浇铸过程中吸入氮的技术方式,得到的钢种成品,钢的纯净度和质量均符合国标要求,其氮含量可控制在60ppm以内。
在开发优质硬线钢和金属制品用钢过程中,发现氮在钢中的存在会大大降低钢材的塑性和韧性,对钢种的力学性能和内在质量产生不利的影响。
针对氮在钢中的行为,经过细致的研究和摸索,开发出了低氮冶炼模式:即通过控制原材料和合金的质量,生产中减少各个工序氮的吸入,大大降低了成品中的氮含量,生产出了合格的钢材,也探索出了适合本公司生产工艺流程控制钢中含氮的方法。
2 钢中氮行为的分析2.1三钢冶炼生产工艺流程及要求铁水→铁水预处理→顶底复吹转炉→LF精炼炉→R10m连铸机。
在炼钢生产过程中,不可避免的会在一些工艺环节上增加钢中的含氮量,为了尽可能地降低钢中氮,必须研究生产中钢液增氮的机理,探索控制钢中氮的工艺模式。
2.2 氮在钢液中的溶解度氮在钢中的溶解度符合Sieverts定律,即: (1)公式中:[%N]:钢液中氮的重量百分浓度;KN:氮溶解的平衡常数;fN:钢液中氮的活度系数;:钢液中元素X对氮的相互作用系数;:钢液中元素X对氮的二阶相互作用系数;:氮气分压。
2.3 合金元素对氮含量的影响钢中主要合金元素为碳、硅、锰。
氮在钢液中的溶解度与其元素有关和温度有关,其关系为:……(2)[1]从式(2)可以看出,氮在钢中的溶解,随着温度的升高而增加。
2. 炼钢过程中氢和氮的控制

20
Solubility of nitrogen in liquid iron alloys at 1600 oC 氮在1600℃液态铁合金中的溶解度
21
Analytical tolerances (%) at AM IH #2 SP
Element Nitrogen Sulfur Range < 0.0050 < 0.005 0.005 - 0.007 0.007 - 0.010 0.010 - 0.020 < 0.050 0.05 - 0.40 .01 - .10 .10 - .20 .20 - .50 ARL Spectrometer ( 3 s ) 0.0015 ( LECO 0.0009 ) 0.0007 0.0010 0.0012 0.0018 0.0027 0.007 0.0052 0.009 0.015
6
0 2
4
6
8 10 12 14
Source of hydrogen 氢的来源
• Hydrogen 氢气 • Moisture 水分 Scrap 废钢 Lime 石灰 Ferroalloys 铁合金 Coal 煤 Gases – O2, N2, Ar 气体 - 氧气,氮气,氩气 Ladle and tundish fluxes and refractory 钢包和中间包保护渣和耐材 Mold powders 结晶器保护渣 Atmosphere 空气
Control of H in Steelmaking 煉钢过程中氫的控制
蔡焕堂
Hunan Valin Steel Company
0
Problems associated with H2 in steel
炼钢中与氢相关的问题
IF钢氮含量控制技术研究
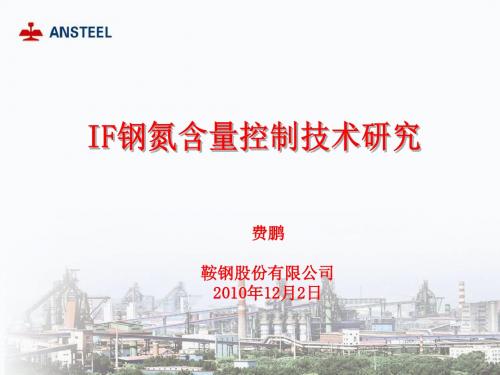
入生产,2002年10月及2006年9月LF炉和2号RH-TB相继投产。
至2006年末,经过大规模的技术改造,鞍钢股份有限公司第二炼钢厂北区主 体设备装备水平达到了国内先进水平。
(a) 复吹转炉设备状况
鞍钢二炼钢北区(原鞍钢三炼钢)1#转炉开始设备建设于1970年,至1984年完成“平改转”,后经扩 容 改造,建成3座180吨转炉,并相继引入德国TBM复吹、气动挡渣等先进技术装备。 表 1 复吹转炉主要设备参数
20
15
10 75 80 85 铁水比,% 90 95 100
(a)提高铁水比 入炉铁水比越高,吹炼终点氮含量越低。所以提高铁水比,减少大尺寸废钢的使 用量,使熔池形成早,钢液能尽早的被熔渣覆盖,能够有效减少熔炼过程钢液滴的 吸氮。鞍钢二炼钢冶炼IF钢铁水比控制目标为90%以上。
(b) 保证化好渣,避免炉渣返干 复吹转炉的脱氮机理基于两方面的原因。其一,在一次反应区元素的氧化 产生了极高的温度(2600℃左右),这使得表面活性元素氧、硫对氮的影响消失, 碳氧化产生的CO气泡降低了界面的氮分压,同时乳化的渣相和CO气泡共同为脱 氮反应提供了足够大的反应界面积,这使得钢液中的氮能够在界面上得以析出脱 除。其二,在一次反应区以外的区域,持续的供氧使钢渣界面保持较高的氧势, 富集在界面上的氧作为表面活性元素的阻碍作用并没有消失,同时乳化的炉渣和 大量CO气泡的微真空室作用都阻碍着钢液从气相中吸氮,这两方面的原因使得 转炉冶炼过程是强脱氮过程。 因此控制良好的乳化渣与CO气泡的真空作用可以使富集在反应区之外界面 上的氧作为表面活性元素阻碍氮气溶解,即阻碍着钢液从气相中吸氮。鞍钢二炼 钢生产IF钢时,采用轻烧白云石和活性白灰造渣,熔炼过程可加入铁矾土、铁皮 球等化渣剂促进化渣,能够将熔炼过程炉渣控制在活跃的状态。
转炉冶炼钢中氮含量的控制
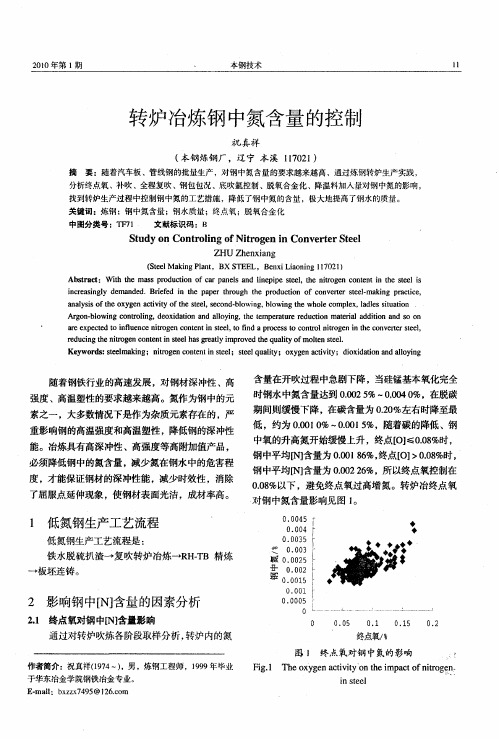
了屈服点延伸现象 ,使钢材表面光洁 ,成材率高。
08 . %以下 ,避免终点氧过高增氮。转炉冶终点氧 0
对钢中氮含量影响见图 l 。
1 低氮钢生产工艺流程
低 氮钢生 产工艺 流程是 :
‘
dp
\
铁水脱硫扒渣 复吹转炉冶炼一R .B 精炼 HT
21 0 0年第 1 期
本钢技术
转炉冶炼钢 中氮含量 的控制
祝 真祥 ( 本钢 炼钢厂 ,辽 宁 本 溪 l7 2 ) 10 1
摘 要:随着汽车板 、管线钢 的批量生产 ,对钢 中氮含量 的要求越来越高 ,通过炼钢转炉生产实践 , 分析终点氧 、补吹 、全程复吹 、钢包包况、底吹氩控制 、脱 氧合金化 、降温料加入量对钢 中氮的影 响 , 找到转炉生产过程 中控制钢中氮的工艺措施 ,降 低了钢中氮的含量 ,极大地提高了钢水的质挝 。 关键词 :炼钢 ;钢 中氮含量 ;钢水质量 ;终点氧 ;脱氧合金化
a ay i o e o y e c i i ft e se l s c n - l wi g b o n h o ec mp e , a l sst ai n 、 n lss f h x g n a t t o t e, e o d b o n , l wi g t e wh l o lx ld e i t t vy h u o
随着钢铁行业 的高速发展 ,对钢材深冲性 、 高 强度、高温塑性的要求越来越高。氮作为钢中的元
素之一 , 大多数情况下是作为杂质元素存在的, 严
含量在开吹过程中急剧下降 , 当硅锰基本氧化完全 时钢水中氮含量达到 0 0 . 2 %~ , 4 %, 0 5 0 0 0 0 在脱碳
钢中氮含量标准

钢中氮含量标准全文共四篇示例,供读者参考第一篇示例:钢中氮含量标准是指钢材中氮元素的含量限制范围和要求,氮是一种常见的非金属元素,在钢材中存在的形式可以是游离态的氮、固溶态的氮、化合态的氮等。
氮对钢材的性能和性质具有重要影响,过高或过低的氮含量都会影响钢材的机械性能、加工性能、耐蚀性能等。
在钢材生产中,通常会控制钢中氮含量的范围,以确保钢材的质量和性能符合要求。
一般来说,碳钢中的氮含量在0.009%~0.015%之间,合金钢中的氮含量则会更高一些,可以达到0.02%~0.06%。
钢中氮含量的标准不仅是为了保证钢材的质量,也是为了满足特定的使用要求。
根据不同的工程要求和使用环境,钢材的氮含量会有不同的标准要求。
首先,钢中氮含量的标准与钢材的用途密切相关。
在一些高强度、耐磨性和耐蚀性要求较高的领域,如航空航天、汽车制造、石油化工等领域,通常要求钢材中的氮含量较高,以提高钢材的硬度、强度和耐磨性。
而在一些精密仪器、医疗器械等领域,则对钢材中的氮含量要求较低,以避免氮在加工过程中对材料性能的影响。
其次,钢中氮含量的标准与钢材的生产工艺和原材料有关。
在钢材生产过程中,氮元素往往会从原料、燃料、气氛等多个方面进入钢水中,因此在生产过程中需要对这些来源进行控制,以确保最终钢材的氮含量符合标准要求。
此外,在生产设备、工艺参数等方面也需要进行调整和控制,以提高氮的转化率和提取率。
最后,钢中氮含量的标准也受到国家标准和行业标准的影响。
钢材作为一种重要的工业材料,在国家标准和行业标准中通常都有相关的氮含量标准要求。
国家标准通常是全国统一的规范,适用于所有领域和行业;而行业标准则是针对特定行业或特定用途的规范,通常更为严格和具体。
总的来说,钢中氮含量标准的制定不仅是为了保证钢材的质量和性能,也是为了确保钢材能够满足不同领域和不同用途的特定要求。
在钢材生产和使用过程中,需要严格遵守和执行这些标准,以确保钢材的质量可靠、性能稳定。
转炉冶炼风电钢过程氮含量的控制

Q N Jn XU in y g X A GH a I u , EX a- i , I N u n
( n f t ig M n g m n e a m n , a irn Sel o,a s e G o p Ma ua u n a a e e t p r e tB y I & te C . ot l ru ) cr D t o B e
售
^
^. / \ . √V 八 厂 V 入
.
,
3 改进 措 施
31 降低 生铁 用量 的实践 .
兰
娃
鉴于 生铁 的热容 比较 大 , 导热性 不好 , 含量 较 氮
高 的现状 , 在冶 炼风 电钢 时采 全废 钢配 料 , 不使 用 生铁 。 与原 来 的装入 制度进 行 了对 比, 据近 2 0炉 根 6 的试 验数 据 ( 见表 5 , 用 此工 艺 冶炼 的炉 次 , 炉 )采 转
主要 因素是炉气增氮。 转炉补吹过程中, 由于此时熔 池 内的碳含量一般低于 0 %, . 即所谓的临界碳含量 6
范 围 ,脱 碳反 应 的开始 取决 于熔池 碳 向钢渣 界 面 的
段属于熔池的硅锰氧化期 , 炉渣没有熔化好 , 氧气射 流携裹炉气射人熔池 , 加上转炉的底吹气体为氮气 , 二者的作用促使熔池急剧增氮 , 增氮现象随着熔池 温度的升高而升高, 脱碳反应开始以后 , 脱碳反应的 C O气泡有效实现脱氮作用使得转炉熔池 内的氮含 量迅速降低 ,冶炼接近终点 ,转炉熔池的氮含量为 ( 4 5 ×1 1 4 ) 0 。
表 2 风 电钢 各 工 序 氮 含 量
表 3 转炉各种原料的氮含量化验分析
表 4 风 电钢 原 转 炉 装 入 量 制度
转炉钢中h n o 的含量

转炉钢中H、N、O的含量一、引言转炉钢是指通过转炉炼钢法生产的钢种,具有低碳、低硫、低磷等优点,广泛应用于建筑、机械、汽车、船舶等领域。
在转炉钢的生产过程中,氢(H)、氮(N)和氧(O)是重要的杂质元素,对钢的性能产生重要影响。
本文将对转炉钢中H、N、O的含量及其影响因素进行深入探讨,旨在为控制转炉钢的质量提供理论支持。
二、H、N、O在转炉钢中的存在形式在转炉钢中,H、N、O主要以溶解状态存在,形成如NH₃、OH⁻、H₂等化合物,另外还有一些以固态氧化物形式存在的杂质。
这些杂质元素在钢中的存在形式和含量受到炼钢原料、冶炼工艺和操作条件等因素的影响。
三、转炉钢中H、N、O的含量及影响因素1.氢(H)的含量及影响因素:转炉钢中的氢含量一般在0.001%~0.005%之间。
氢的主要来源是炼钢原料中的水分和空气中水蒸气的冷凝。
此外,钢铁料中的含碳物质也是氢的来源之一。
为降低转炉钢中的氢含量,应严格控制炼钢原料的水分,并加强炉气氛围的保护,避免空气中的水分进入炉内。
2.氮(N)的含量及影响因素:转炉钢中的氮含量一般在0.002%~0.01%之间。
氮的主要来源是炼钢原料中的含氮物质和空气中的氮气。
氮在高温下易溶于钢液中,难以去除。
为降低转炉钢中的氮含量,应选用低氮原料,如低氮生铁、低氮废钢等。
同时,加强炉气氛围的保护,减少空气中的氮气进入炉内也是重要的措施。
3.氧(O)的含量及影响因素:转炉钢中的氧含量一般在0.001%~0.01%之间。
氧的主要来源是炼钢过程中空气中的氧气和水蒸气与钢液反应产生的氧化物。
为降低转炉钢中的氧含量,应加强炉气氛围的保护,减少空气中的氧气和水蒸气进入炉内。
同时,采用合适的造渣工艺和脱氧合金化工艺也是重要的措施。
四、H、N、O对转炉钢性能的影响H、N、O等杂质元素对转炉钢的性能产生重要影响,主要表现在以下几个方面:1.力学性能:H、N、O等杂质元素会降低转炉钢的强度和韧性,特别是对于高强度级别钢材的影响更为显著。
碳钢中n的有害作用

碳钢中n的有害作用
碳钢中的氮(N)可能会对材料的性能产生一些有害作用。
首先,氮可以在碳钢中形成氮化物,这些氮化物会降低钢的塑性和韧性。
此外,氮也可能导致碳钢的脆性增加,从而降低其抗冲击性能。
另外,氮还可能导致碳钢的焊接性能下降,因为氮会在热影响区形成
氮化物和氮化铁,从而引起脆性断裂。
此外,氮还可能对碳钢的耐
蚀性能产生负面影响,因为氮会促进晶间腐蚀的发生。
因此,在一
些特定的应用中,需要控制碳钢中氮的含量,以避免这些有害作用
的发生。
需要注意的是,氮对碳钢的影响也与其他合金元素的含量
和加工工艺有关,因此在具体的应用中需要综合考虑各种因素。
转炉冶炼耐磨钢过程氮含量的控制
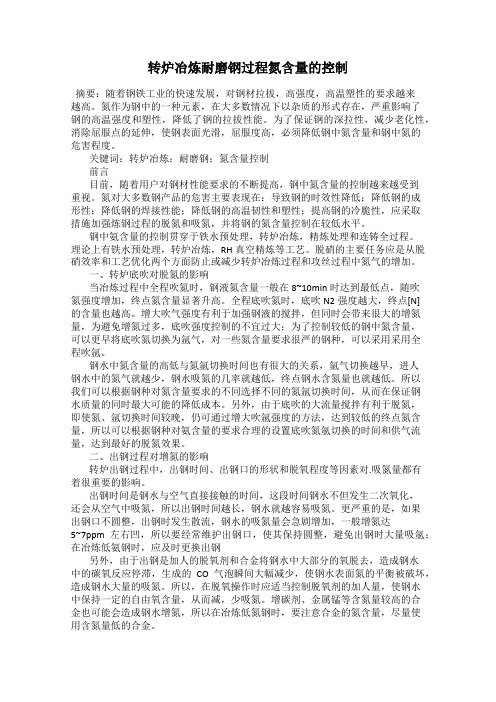
转炉吹炼完后,从精炼到连铸都为钢水增氮过程,因此如何防止钢液增氮成为控制钢水氮含量的重要手段。精炼过程中氮主要来源于与钢水接触的大气、加入的合金及熔剂等。
(一)脱氧对钢液吸氮的影响
钢液经铝脱氧后,钢液平均溶解氧质量分数控制在小于20x10-6的水平,随着精炼时间延长,钢液吸氮现象越来越严重。在精炼中随着氧、硫含量的降低,由于氧、硫的表面活性作用而阻碍钢液吸氮的作用基本消失,只要钢液裸露就有可能吸氮。将精炼过程分为钢水到LF炉精炼前、精炼渣料加热、合金微调及喂丝后4个时段,分别取氮样,考察每个时段的增氮量,结果见图1。
五、结语
降低炼钢过程中的氮含量应从源头抓起,精选原材料,尽可能控制转炉终点的[N]含量在较低的范围;严格控制钢水从LF(VD)-CCM全过程的吸氮量,减少钢液与大气接触,且严格执行上述分析讨论的各项技术措施。因此,在生产过程中可以对各影响因素进行控制来减少钢水中的氮含量。
1)顶底复吹转炉中合理切换底吹氮气、氩气时间的工艺可以满足多数钢种对氮含量的要求,同时会降低底吹成本。
另外,由于出钢是加人的脱氧剂和合金将钢水中大部分的氧脱去,造成钢水中的碳氧反应停滞,生成的CO气泡瞬间大幅减少,使钢水表面氮的平衡被破坏,造成钢水大量的吸氮。所以,在脱氧操作时应适当控制脱氧剂的加人量,使钢水中保持一定的自由氧含量,从而减,少吸氮。增碳剂、金属锰等含氮量较高的合金也可能会造成钢水增氮,所以在冶炼低氮钢时,要注意合金的氮含量,尽量使用含氮量低的合金。
关键词:转炉冶炼;耐磨钢;氮含量控制
前言
目前,随着用户对钢材性能要求的不断提高,钢中氮含量的控制越来越受到重视。氮对大多数钢产品的危害主要表现在:导致钢的时效性降低;降低钢的成形性;降低钢的焊接性能;降低钢的高温韧性和塑性;提高钢的冷脆性,应采取措施加强炼钢过程的脱氮和吸氮,并将钢的氮含量控制在较低水平。
- 1、下载文档前请自行甄别文档内容的完整性,平台不提供额外的编辑、内容补充、找答案等附加服务。
- 2、"仅部分预览"的文档,不可在线预览部分如存在完整性等问题,可反馈申请退款(可完整预览的文档不适用该条件!)。
- 3、如文档侵犯您的权益,请联系客服反馈,我们会尽快为您处理(人工客服工作时间:9:00-18:30)。
钢中氮含量的控制
随着炼钢技术的不断进步和发展,国内外钢厂对钢的氮含量控制要求也越来越严格,除耐热及不锈钢外,在绝大多数钢中,氮被视为一种有害元素。
虽然钢中残留氮很少,但对钢的力学性能却有显著的影响。
众所周知,一般情况下氮的危害主要表现在:Fe4N的析出导致钢的时效性和蓝脆,降低钢的韧性和塑性;与钢中钛、铝等元素形成带棱角而性脆的夹杂物,不利于钢的冷热变形加工;当钢中残留氮较高,会导致钢宏观组织疏松甚至形成气泡;钢中氮还会降低钢的焊接性能、电导率、导磁率等;钢中氮含量偏高也会使铸坯开裂。
因此,必须采取有效措施降低钢中氮含量,特别是高级别钢种的氮控制尤显重要。
1.转炉冶炼对氮含量的影响
从动力学条件看,炉渣的性质与钢液反应界面是吸氮的限制环节。
从热力学计算看,空气中氮的分压高及钢液中氮的溶解度高决定了钢水有很好的吸氮条件。
转炉吹炼时炉内的氮主要是由铁水带入,约占总入炉氮76%,在转炉冶炼中,由于熔池发生激烈的C-O反应,产生大量的CO气体,能够带走部分钢中溶解的氮。
吹炼前期由于采用纯氧吹炼氮分压气较低开吹后金属中下降。
吹炼中期随着脱碳速度增加金属中下降熔池含碳时脱碳速度达到高峰熔池内金属激烈沸腾金属中降至较低值。
吹炼末期渣中氧化铁含量增加炉渣起泡空气不再被吸人转炉工作空间由于钢中氧含量增高,氮的熔解度下降,氮含量进一步降低,拉碳时氮分别为和说明转炉内氮在钢中的溶解度很小。
2.LF精炼对氮含量的影响
钢包钢水进入LF工位进行全程底吹氩气搅拌,加入石灰和萤石并喂Al线强化脱氧,合金成分微调、喂Si-Ca线对钢液进行钙处理等工艺过程。
在LF炉精炼前期,钢液中氮含量较低,无论大气中氮的分压多高,大气中的氮都不能穿过渣层而进入钢液,但是转炉出钢后,加入脱氧剂脱氧,钢中w(O)迅速下降,使钢液吸氮趋势明显增大。
随着加入的增碳剂和铁合金不断熔入钢液中,钢液中的w(N)仍在不断上升。
氧化性钢液不增氮,而脱氧钢液则明显吸氮。
在精炼前期,加入大量渣料,由于加入的渣料没有化开形成较大的间隙,形成钢
液吸氮的通道,化渣过程氩气量较大,致使脱氧良好的钢液不断与空气接触,加快了吸氮的速度;另外在电极加热时,电弧最高温度可以达到6000℃。
电弧作用到钢液上时,这部分钢液较其它部位的钢液温度高,超过2300℃。
而当钢液温度超过2130℃时,发生如下反应:
N2=2N(g) (1)
N(g)+Q=[N] (2)
在渣界面存在大量被电离的[N],随着氧、硫在钢中的浓度急剧下降,吸氮趋势加强。
被电离的[N]在裸露区域被钢液吸入,钢液中氮含量增加。
渣料完全融化后,渣子覆盖在钢水表面;氩气压力降低,避免吹开渣层,这样隔绝了氮气跟钢水的接触,避免了[N]的吸入。
精炼结束后,进行成分的微调和Ca处理过程中,会造成一定的增氮量,,喂线Ca-Si过程增氮,主要是由于Ca气化形成Ca气泡将钢液面吹开,造成裸露的钢液从空气中吸氮而产生的;Ca-Si线本身的增氮。
如果渣层较厚线穿过渣层进人钢液而不把钢液面吹开,就有可能避免裸露钢液吸氮,这就是部分炉次喂线过程钢液没有增氮的原因。
另外,LF炉渣碱度的控制也不容忽视,有研究表明:LF炉渣碱度不宜大于1.9,否则渣的熔点升高,可能会有部分炉渣未完全熔化造成炉渣结构松散而存有空隙,使钢液吸氮的可能性增加。
3.连铸浇铸对氮含量的影响
连铸过程中为了防止钢包钢流和中间包钢流的二次氧化和吸氮,普遍采用保护浇注技术。
连铸机连铸过程钢包到中间包之间的钢水保护采用大包长水口加氩气密封和中间包加覆盖剂保护钢液。
中间包到结晶器的保护采用浸入式水口加连铸保护渣对钢液进行保护浇注,防止二次氧化和吸氮。
由于该保护措施使得钢液与空气完全隔离,钢液从中间包到结晶器二次氧化和吸氮现象很弱,基本上不增氮。
综上,连铸过程增氮主要发生在钢包到中间包之间的环节上,保护浇注系统的完善程度决定了,该阶段的保护工作是连铸段防止增氮的主要任务。
连铸开浇时第一包钢水进入中间包开始阶段属于敞开浇铸,钢水会吸氮。
连铸机长水口如密封不良,将会象一个抽气泵一样把空气从接缝处吸入。
为防止在
接缝处吸入空气,可以在接缝处通入Ar气,使长水口顶部形成正压区,基本可避免吸氮。
综合分析以上因素,采取相应的措施,即可避免氮造成的皮下气泡等钢的质量问题。