炼钢中杂质去除或变形处理方法研究
钢铁冶炼中的废渣处理技术与研究
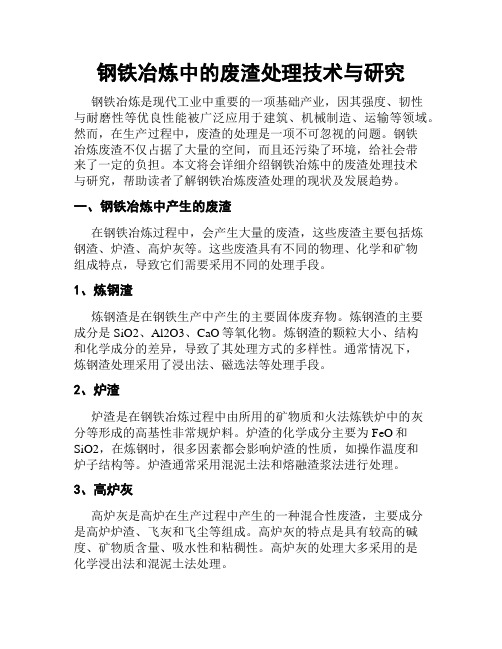
钢铁冶炼中的废渣处理技术与研究钢铁冶炼是现代工业中重要的一项基础产业,因其强度、韧性与耐磨性等优良性能被广泛应用于建筑、机械制造、运输等领域。
然而,在生产过程中,废渣的处理是一项不可忽视的问题。
钢铁冶炼废渣不仅占据了大量的空间,而且还污染了环境,给社会带来了一定的负担。
本文将会详细介绍钢铁冶炼中的废渣处理技术与研究,帮助读者了解钢铁冶炼废渣处理的现状及发展趋势。
一、钢铁冶炼中产生的废渣在钢铁冶炼过程中,会产生大量的废渣,这些废渣主要包括炼钢渣、炉渣、高炉灰等。
这些废渣具有不同的物理、化学和矿物组成特点,导致它们需要采用不同的处理手段。
1、炼钢渣炼钢渣是在钢铁生产中产生的主要固体废弃物。
炼钢渣的主要成分是SiO2、Al2O3、CaO等氧化物。
炼钢渣的颗粒大小、结构和化学成分的差异,导致了其处理方式的多样性。
通常情况下,炼钢渣处理采用了浸出法、磁选法等处理手段。
2、炉渣炉渣是在钢铁冶炼过程中由所用的矿物质和火法炼铁炉中的灰分等形成的高基性非常规炉料。
炉渣的化学成分主要为FeO和SiO2,在炼钢时,很多因素都会影响炉渣的性质,如操作温度和炉子结构等。
炉渣通常采用混泥土法和熔融渣浆法进行处理。
3、高炉灰高炉灰是高炉在生产过程中产生的一种混合性废渣,主要成分是高炉炉渣、飞灰和飞尘等组成。
高炉灰的特点是具有较高的碱度、矿物质含量、吸水性和粘稠性。
高炉灰的处理大多采用的是化学浸出法和混泥土法处理。
二、废渣处理技术废渣的处理方式是影响环境的一个重要因素。
废渣全部排放给公共环境会导致环境污染,所以对废渣进行处理显得十分重要。
1、浸出法浸出法是一种常用的废渣处理技术,适用于炼钢渣和高炉灰的处理。
其方式是采用化学方法将溶液与固体废渣进行接触反应,便可促进废渣中的物质溶解,最终从溶液中获得需求废渣处理物质。
浸出方法有多种,如浸出酸、浸出碱、浸出盐等,但需要根据废渣的具体物质组成选择不同的浸出介质。
2、磁选法磁选法是研究废渣处理的另一种方法,一般应用于炼钢渣的处理。
炼钢过程中的杂质控制技术
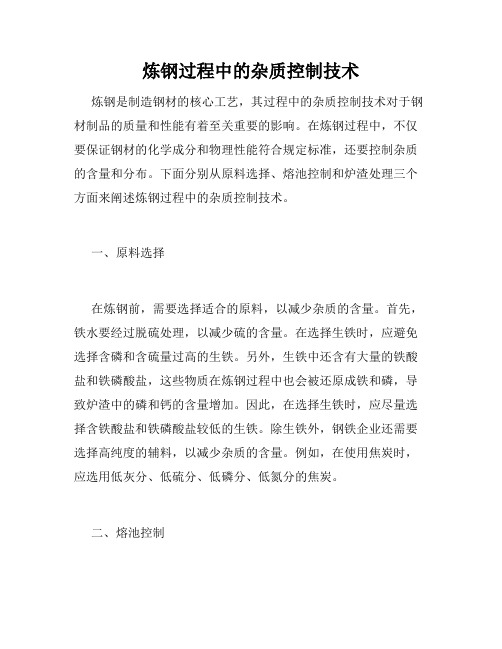
炼钢过程中的杂质控制技术炼钢是制造钢材的核心工艺,其过程中的杂质控制技术对于钢材制品的质量和性能有着至关重要的影响。
在炼钢过程中,不仅要保证钢材的化学成分和物理性能符合规定标准,还要控制杂质的含量和分布。
下面分别从原料选择、熔池控制和炉渣处理三个方面来阐述炼钢过程中的杂质控制技术。
一、原料选择在炼钢前,需要选择适合的原料,以减少杂质的含量。
首先,铁水要经过脱硫处理,以减少硫的含量。
在选择生铁时,应避免选择含磷和含硫量过高的生铁。
另外,生铁中还含有大量的铁酸盐和铁磷酸盐,这些物质在炼钢过程中也会被还原成铁和磷,导致炉渣中的磷和钙的含量增加。
因此,在选择生铁时,应尽量选择含铁酸盐和铁磷酸盐较低的生铁。
除生铁外,钢铁企业还需要选择高纯度的辅料,以减少杂质的含量。
例如,在使用焦炭时,应选用低灰分、低硫分、低磷分、低氮分的焦炭。
二、熔池控制炼钢时,由于各种原因,熔池中常常会产生一些杂质。
钢铁企业需要采取一系列措施,减少和控制这些杂质的生成和含量。
一方面,钢铁企业需要控制炉料的配比,以保证氧化还原反应的均衡。
当熔池中存在大量的氧化性杂质时,就需要加入还原剂(如生铁)来减少这些杂质的含量。
另一方面,钢铁企业需要采取一系列技术措施,以控制熔池的温度、氧化还原环境、氧分压等参数的变化。
当炉温升高时,氧化反应就会加剧,这时就需要加入还原剂来抵消氧化反应的影响。
在控制熔池中的杂质时,还需要对炉渣进行处理,以减少炉渣中的氧化性杂质。
三、炉渣处理炉渣是炼钢过程中产生的一种副产物,其中含有大量的杂质。
因此,在炼钢过程中,控制炉渣中的杂质含量和化学成分也是非常重要的。
一方面,钢铁企业需要采取一系列技术措施,来控制炉渣的生成和含量。
例如,可以选用低炉渣粘度的冶炼工艺,以减少炉渣的产生和减少炉渣中杂质的含量。
另一方面,钢铁企业还需要选择合适的炉渣处理工艺,以减少炉渣中的化学成分和杂质的含量。
目前,常用的炉渣处理工艺主要有电磁搅拌技术、氧气吹气技术、钢渣注入等。
钢中夹杂物的产生与去除途径
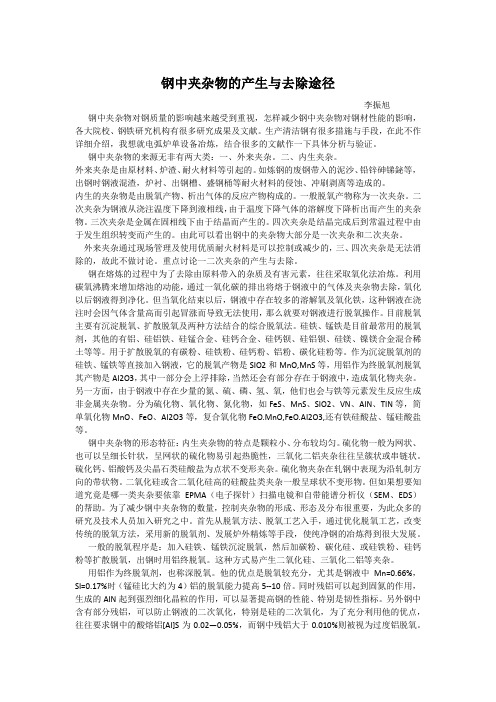
钢中夹杂物的产生与去除途径李振旭钢中夹杂物对钢质量的影响越来越受到重视,怎样减少钢中夹杂物对钢材性能的影响,各大院校、钢铁研究机构有很多研究成果及文献。
生产清洁钢有很多措施与手段,在此不作详细介绍,我想就电弧炉单设备冶炼,结合很多的文献作一下具体分析与验证。
钢中夹杂物的来源无非有两大类:一、外来夹杂。
二、内生夹杂。
外来夹杂是由原材料、炉渣、耐火材料等引起的。
如炼钢的废钢带入的泥沙、铅锌砷锑鉍等,出钢时钢液混渣,炉衬、出钢槽、盛钢桶等耐火材料的侵蚀、冲刷剥离等造成的。
内生的夹杂物是由脱氧产物、析出气体的反应产物构成的。
一般脱氧产物称为一次夹杂。
二次夹杂为钢液从浇注温度下降到液相线,由于温度下降气体的溶解度下降析出而产生的夹杂物。
三次夹杂是金属在固相线下由于结晶而产生的。
四次夹杂是结晶完成后到常温过程中由于发生组织转变而产生的。
由此可以看出钢中的夹杂物大部分是一次夹杂和二次夹杂。
外来夹杂通过现场管理及使用优质耐火材料是可以控制或减少的,三、四次夹杂是无法消除的,故此不做讨论。
重点讨论一二次夹杂的产生与去除。
钢在熔炼的过程中为了去除由原料带入的杂质及有害元素,往往采取氧化法冶炼。
利用碳氧沸腾来增加熔池的动能,通过一氧化碳的排出将熔于钢液中的气体及夹杂物去除,氧化以后钢液得到净化。
但当氧化结束以后,钢液中存在较多的溶解氧及氧化铁,这种钢液在浇注时会因气体含量高而引起冒涨而导致无法使用,那么就要对钢液进行脱氧操作。
目前脱氧主要有沉淀脱氧、扩散脱氧及两种方法结合的综合脱氧法。
硅铁、锰铁是目前最常用的脱氧剂,其他的有铝、硅铝铁、硅锰合金、硅钙合金、硅钙钡、硅铝钡、硅镁、镍镁合金混合稀土等等。
用于扩散脱氧的有碳粉、硅铁粉、硅钙粉、铝粉、碳化硅粉等。
作为沉淀脱氧剂的硅铁、锰铁等直接加入钢液,它的脱氧产物是SIO2和MnO,MnS等,用铝作为终脱氧剂脱氧其产物是AI2O3,其中一部分会上浮排除,当然还会有部分存在于钢液中,造成氧化物夹杂。
钢中夹杂物的去除方法

钢液中存在着夹杂物会严重影响着钢的性能,制约着钢材的使用,因此,必须采取有效措施,去除钢中夹杂物,改善钢的性能。
钢液中夹杂物的去除方法主要有钢液吹氩技术,结晶器电磁技术,中间包过滤技术。
1、吹氩技术吹氩搅拌是现代炼钢应用较为成熟的1种技术。
其原理是利用特殊装置将惰性气体均匀分散地吹入钢液中形成微小的气泡,气泡上浮时依靠界面张力将夹杂颗粒吸附在表面,上浮至液面除去。
在吹氩技术上又发展了1种技术,即中间包气幕挡墙,它是在包底埋入1排透气装置,通过向钢液内吹入微型气泡,形成1道气幕挡墙,夹杂物经过时与气泡发生碰撞,并吸附于气泡表面上浮,适合50-200μm夹杂物外墙岩棉复合板去除。
2、结晶器电磁技术结晶器电磁技术包括电磁搅拌和电磁制动,它们工作原理相似。
电磁搅拌是在结晶器内板坯后方设置直线运动式传感器,产生移动磁场,以驱动结晶器内弯月面附近的钢水沿着水平方向旋转流动,达到搅拌目的。
适合小于20μm夹杂物去除。
电磁制动是在结晶器的两个宽面处外加1对恒定的电磁场,使磁场方向垂直穿过结晶器的两个宽面。
钢液从水口侧孔流出后,高速垂直穿过磁场,因钢水导电,会产生感应电流,在电磁场作用下,钢液会受到和自身流动方向相反的电磁力,是钢液流动速度降低,达到制动的目的。
该技术最早由瑞典和日本联合开发,冶金效果良好。
3、中间包过滤技术中间包过滤技术是在挡墙挡坝的基础上增加过滤器装置,主要通过机械阻挡和表面吸附作用去除夹杂。
过滤器由带有微孔结构的耐火材料制成,它横跨在中间包的两个宽面上,将中间包完全隔开,钢水只能从微孔通过。
这样既延长了夹杂物在钢液中的停留时间,又保证了微型夹杂物在钢液中的停留时间,又保证了微型夹杂物有足够的时间吸附在过滤器上,达到去除夹杂物的目的。
适合大于20μm的所有夹杂颗粒。
应用中,现有的技术很难单独完成彻底去除夹杂的任务,所以应将多种技术结合起来,寻求更为合理可行的夹杂物去除方法和技术参数,做到“零夹杂”。
降低精炼钢钢中夹杂物的研究
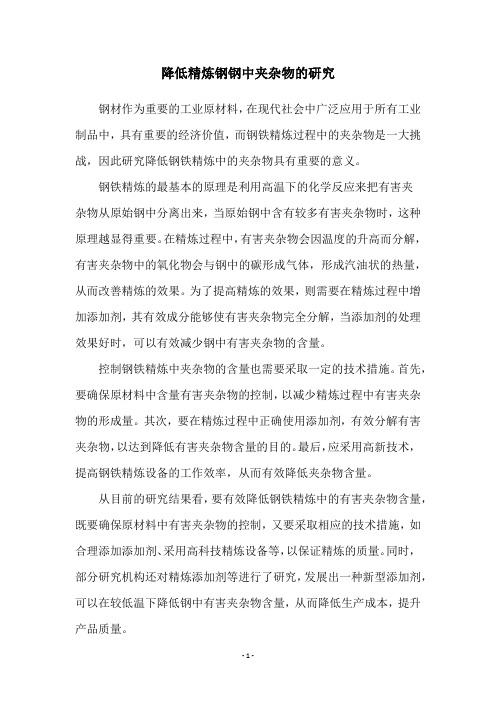
降低精炼钢钢中夹杂物的研究钢材作为重要的工业原材料,在现代社会中广泛应用于所有工业制品中,具有重要的经济价值,而钢铁精炼过程中的夹杂物是一大挑战,因此研究降低钢铁精炼中的夹杂物具有重要的意义。
钢铁精炼的最基本的原理是利用高温下的化学反应来把有害夹杂物从原始钢中分离出来,当原始钢中含有较多有害夹杂物时,这种原理越显得重要。
在精炼过程中,有害夹杂物会因温度的升高而分解,有害夹杂物中的氧化物会与钢中的碳形成气体,形成汽油状的热量,从而改善精炼的效果。
为了提高精炼的效果,则需要在精炼过程中增加添加剂,其有效成分能够使有害夹杂物完全分解,当添加剂的处理效果好时,可以有效减少钢中有害夹杂物的含量。
控制钢铁精炼中夹杂物的含量也需要采取一定的技术措施。
首先,要确保原材料中含量有害夹杂物的控制,以减少精炼过程中有害夹杂物的形成量。
其次,要在精炼过程中正确使用添加剂,有效分解有害夹杂物,以达到降低有害夹杂物含量的目的。
最后,应采用高新技术,提高钢铁精炼设备的工作效率,从而有效降低夹杂物含量。
从目前的研究结果看,要有效降低钢铁精炼中的有害夹杂物含量,既要确保原材料中有害夹杂物的控制,又要采取相应的技术措施,如合理添加添加剂、采用高科技精炼设备等,以保证精炼的质量。
同时,部分研究机构还对精炼添加剂等进行了研究,发展出一种新型添加剂,可以在较低温下降低钢中有害夹杂物含量,从而降低生产成本,提升产品质量。
以上就是关于降低精炼钢钢中夹杂物的研究的简要介绍。
钢铁精炼的夹杂物的控制对于钢的质量有着重要的作用,它不仅直接影响终端产品的质量,而且也会影响钢铁生产的费用。
因此,如何有效地降低钢铁精炼中夹杂物含量,在维护钢铁产品质量的方面显得尤为重要。
经过科学研究发现,精炼过程中以及原料夹杂物控制能够有效降低夹杂物含量,通过改进精炼设备以及优化添加剂,能够有效提升钢材的质量。
而且,添加剂也是重要的一环,不同的添加剂有不同的效果,应根据不同的情况来选择合适的添加剂,从而最大限度地降低钢铁精炼过程中夹杂物的含量。
夹杂物去除方法
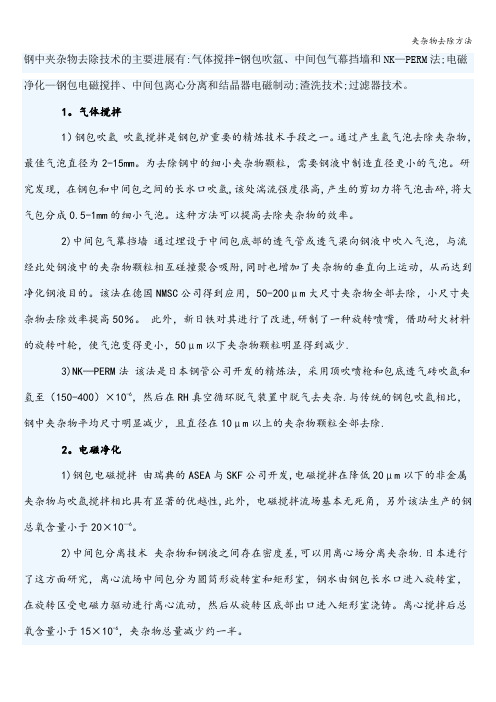
钢中夹杂物去除技术的主要进展有:气体搅拌-钢包吹氩、中间包气幕挡墙和NK—PERM法;电磁净化—钢包电磁搅拌、中间包离心分离和结晶器电磁制动;渣洗技术;过滤器技术。
1。
气体搅拌1)钢包吹氩吹氩搅拌是钢包炉重要的精炼技术手段之一。
通过产生氩气泡去除夹杂物,最佳气泡直径为2-15mm。
为去除钢中的细小夹杂物颗粒,需要钢液中制造直径更小的气泡。
研究发现,在钢包和中间包之间的长水口吹氩,该处湍流强度很高,产生的剪切力将气泡击碎,将大气包分成0.5-1mm的细小气泡。
这种方法可以提高去除夹杂物的效率。
2)中间包气幕挡墙通过埋设于中间包底部的透气管或透气梁向钢液中吹入气泡,与流经此处钢液中的夹杂物颗粒相互碰撞聚合吸附,同时也增加了夹杂物的垂直向上运动,从而达到净化钢液目的。
该法在德国NMSC公司得到应用,50-200μm大尺寸夹杂物全部去除,小尺寸夹杂物去除效率提高50%。
此外,新日铁对其进行了改进,研制了一种旋转喷嘴,借助耐火材料的旋转叶轮,使气泡变得更小,50μm以下夹杂物颗粒明显得到减少.3)NK—PERM法该法是日本钢管公司开发的精炼法,采用顶吹喷枪和包底透气砖吹氩和氢至(150-400)×10-6,然后在RH真空循环脱气装置中脱气去夹杂.与传统的钢包吹氩相比,钢中夹杂物平均尺寸明显减少,且直径在10μm以上的夹杂物颗粒全部去除.2。
电磁净化1)钢包电磁搅拌由瑞典的ASEA与SKF公司开发,电磁搅拌在降低20μm以下的非金属夹杂物与吹氩搅拌相比具有显著的优越性,此外,电磁搅拌流场基本无死角,另外该法生产的钢总氧含量小于20×10—6。
2)中间包分离技术夹杂物和钢液之间存在密度差,可以用离心场分离夹杂物.日本进行了这方面研究,离心流场中间包分为圆筒形旋转室和矩形室,钢水由钢包长水口进入旋转室,在旋转区受电磁力驱动进行离心流动,然后从旋转区底部出口进入矩形室浇铸。
离心搅拌后总氧含量小于15×10-6,夹杂物总量减少约一半。
炼钢废弃物中金属元素的回收和利用研究
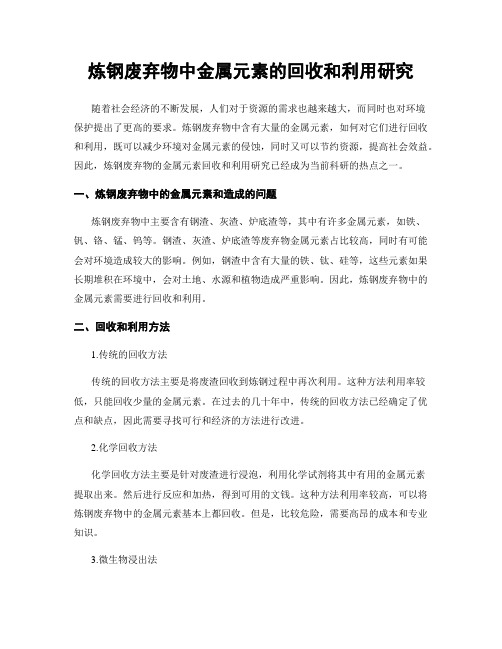
炼钢废弃物中金属元素的回收和利用研究随着社会经济的不断发展,人们对于资源的需求也越来越大,而同时也对环境保护提出了更高的要求。
炼钢废弃物中含有大量的金属元素,如何对它们进行回收和利用,既可以减少环境对金属元素的侵蚀,同时又可以节约资源,提高社会效益。
因此,炼钢废弃物的金属元素回收和利用研究已经成为当前科研的热点之一。
一、炼钢废弃物中的金属元素和造成的问题炼钢废弃物中主要含有钢渣、灰渣、炉底渣等,其中有许多金属元素,如铁、钒、铬、锰、钨等。
钢渣、灰渣、炉底渣等废弃物金属元素占比较高,同时有可能会对环境造成较大的影响。
例如,钢渣中含有大量的铁、钛、硅等,这些元素如果长期堆积在环境中,会对土地、水源和植物造成严重影响。
因此,炼钢废弃物中的金属元素需要进行回收和利用。
二、回收和利用方法1.传统的回收方法传统的回收方法主要是将废渣回收到炼钢过程中再次利用。
这种方法利用率较低,只能回收少量的金属元素。
在过去的几十年中,传统的回收方法已经确定了优点和缺点,因此需要寻找可行和经济的方法进行改进。
2.化学回收方法化学回收方法主要是针对废渣进行浸泡,利用化学试剂将其中有用的金属元素提取出来。
然后进行反应和加热,得到可用的文钱。
这种方法利用率较高,可以将炼钢废弃物中的金属元素基本上都回收。
但是,比较危险,需要高昂的成本和专业知识。
3.微生物浸出法微生物浸出法是一种通过微生物代谢作用将有用的金属元素从废弃物中提取出来的方法。
在这种方法中,微生物首先选出对有用金属元素代谢作用较强的微生物,然后利用生物学中微生物的普遍特点,在不同的微生物体内预备分离有用的金属元素。
这种方法具有许多优点,如回收率高、成本低、有利于资源节约等。
三、发展现状炼钢废弃物金属元素的回收和利用研究是一个新兴的研究领域,目前涉及的学科非常广泛,如化学、材料学、生物技术等。
在这些学科的共同努力下,有了一些进展。
比如,在化学回收和微生物浸出法中,已经有一些具体的工业化应用实例,可以用于反循环造纸、金属开采等领域。
金属冶炼中的杂质控制与表面处理

,
汇报人:
目录 /目录
01
点击此处添加 目录标题
02
金属冶炼中的 杂质控制
03
金属表面处理 技术
04
金属表面处理 的应用
05
金属表面处理 的发展趋势与 挑战
01 添加章节标题
02 金属冶炼中的杂质控制
杂质来源与影响
杂质来源:矿石、 燃料、熔剂、耐火 材料等
影响:降低金属纯 度,影响金属性能
技术革新:开发新 型表面处理技术, 提高效率和性能
成本控制:降低表 面处理成本,提高 经济效益
法规政策:遵守相 关法规政策,确保 表面处理技术的合 法性和合规性
未来表面处理技术的发展方向
环保型表面处理技术:减少污染,降低能耗 纳米表面处理技术:提高表面性能,增强耐磨性、耐腐蚀性等 智能化表面处理技术:实现自动化、智能化生产,提高生产效率 复合表面处理技术:结合多种表面处理技术,提高表面性能和功能
化学分离法: 利用杂质与 金属的化学 性质差异进 行分离,如 酸洗、碱洗 等
电化学分离 法:利用电 化学原理进 行杂质分离, 如电解、电 镀等
真空冶金法: 利用真空环 境进行杂质 分离,如真 空熔炼、真 空蒸馏等
离子交换法: 利用离子交 换树脂进行 杂质分离, 如离子交换 树脂吸附、 离子交换树 脂再生等
航空航天:提高航天器零部件的耐高 温、耐腐蚀性和耐磨性
电子工业:提高电子元器件的导电性、 耐腐蚀性和美观性
建筑工业:提高建筑材料的耐腐蚀性 和美观性
医疗设备:提高医疗设备的耐腐蚀性 和生物相容性
食品工业:提高食品加工设备的耐腐 蚀性和卫生性
05
金属表面处理的发展趋 势与挑战
第三篇 洁净钢中杂质元素去除

C CO 2 g 2COg
G 144700 129.5T
2 log PCO / PCO2 a C 7558 / T 6.765
C O COg
G 2220 38.34T log PCO / a O a C 1160 / T 2.003
当钢中碳含量较高时,碳、氧活度是不可以忽略的。即
C O C log f C log f C log f C log f C 0.243%C
O C C log f O log f O log f O log f O 0.421%C
组合
log
%C %O log a C a O 0.243%C 0.42%C
Institute of Ferrous Metallurgy
d%C A / V K C %C %Ce dt
增大气-液相接触面积是 最有效也是最常用的增 加脱碳速率的方法。
图 RH精炼过程浸渍管径与脱碳速率的关系 Institute of Ferrous Metallurgy
C O COg
G 2220 38.34T log PCO / a O a C 1160 / T 2.003
当钢中C浓度较低时,fC、fO近似 等于1.0,可以表示成下式:
%C %O 1160 / T 2.003 log
PCO
当气氛中PCO近似等于1时,C-O 浓度积仅与温度有关:
C O C log f C log f C log f C log f C 0.243%C
O C C log f O log f O log f O log f O 0.421%C
活度系数
简述炼钢过程中产生夹杂物去除方法

简述炼钢过程中产生夹杂物去除方法原则上,炼钢过程中产生的夹杂物能够通过向钢液/气体、钢/渣或钢/耐火材料界面移动而得到去除。
然而,必须同时采取措施防止钢液二次氧化、卷渣和使夹杂物重新回到钢液中,避免夹杂物的去除速度小于夹杂物生成的速度的情况。
对于从钢液中去除到钢液/气体、钢/渣界面的夹杂物必须能够脱离钢液进入界面,然后再从界面上脱离。
只有当夹杂物和气泡的接触角为180°时,才能通过钢液/气体界面将夹杂物去除,因此这种几率很小。
然而,如果钢液表面有覆盖渣,覆盖渣就能够吸收夹杂物粒子,即使接触角较小也能够将夹杂物脱除。
总的来说,由于没有足够的上浮时间,钢包(或中间包、结晶器)中小颗粒的一次脱氧产物只有少部分得到了上浮去除,斯托克斯方程决定了上浮力的大小。
例如,直径为100 μm的三氧化二铝夹杂物从钢液表面下2.5 m上浮到钢液表面需要4.8 min,对于直径为20 μm 的夹杂物,上浮时间增加到119min,对于去除夹杂物来说显然上浮是效率很低的。
通过气体或电磁搅拌钢液,增加夹杂物之间的碰撞能够使周态夹杂物聚集,液态夹杂物聚合为大颗粒夹杂物,从而提高夹杂物去除速率。
因此搅拌钢液是生产洁净钢的一个重要操作。
当通过吹氩搅拌钢液时,气体吹入点要尽可能地在钢包底部从而获得最大的搅拌能和搅拌区域,使气泡捕获更多的夹杂物。
固态夹杂物例如Al20、S102和Mg0等能够通过粘附到小气泡上,再上浮到钢渣界面。
夹杂物的直径越大,气泡越小,接触角越小,钢液表面张力越小,夹杂物去除的效率就越高。
普通液态夹杂物也是通过粘附到上浮的气泡去除的。
大多数的粘附方式为夹杂物成球形粘附到气泡内部。
有效去除夹杂物的最佳气泡直径为2—15 mm。
但是由于气泡在钢液中上浮过程迅速膨胀,因此很难达到最佳尺寸。
夹杂物可以随气泡尾流中上浮去除,尤其是小气泡,例如20 mm。
然而通过观察发现:到达钢/渣界面并破裂的气泡一般都明显大于这个尺寸,因此降低了辅助夹杂物上浮去除的能力。
金属冶炼中的杂质控制与去除

利用电解过程将溶液中的金属离子还原成金属并沉积在阴极上,通过控制电位和电流密 度,使杂质元素不被还原或以较小量被还原,从而实现杂质的分析
案例一:不锈钢冶炼中的杂质控制与去除
不锈钢中的杂质元素
不锈钢中的杂质元素如碳、氮、氧、硫等会影响其耐腐蚀性和机 械性能。
金属冶炼中的杂质控制与去 除
目录
• 金属冶炼概述 • 金属冶炼中的杂质控制技术 • 金属冶炼中的杂质去除技术 • 金属冶炼中的杂质控制与去除案
例分析 • 金属冶炼中的杂质控制与去除发
展趋势与展望
01
金属冶炼概述
金属冶炼的定义与目的
定义
金属冶炼是指通过一系列化学和 物理过程,将矿石或废旧金属中 的目标金属提取出来,并与其他 杂质分离的过程。
在铝的熔炼和精炼过程中,采用电解沉积和区域熔炼等方法进
一步去除杂质元素,提高铝的纯度。
05
金属冶炼中的杂质控制与去 除发展趋势与展望
新型杂质控制与去除技术的研发与应用
新型熔融还原技术
利用直接还原法将铁矿石熔融成铁水,减少传统炼铁工艺中的杂 质引入,提高金属纯度。
真空蒸馏法
在真空条件下,利用不同金属或其化合物的蒸气压差异,实现杂 质的分离和去除。
磁选法
利用杂质元素与主金属在 磁性上的差异,通过磁场 将磁性杂质与主金属分离 。
筛分法
通过不同规格的筛网将主 金属与杂质进行粒度分级 ,从而将杂质去除。
电解法去除杂质
电解精炼
利用杂质元素在电解过程中的电化学性质与主金属的差异,通过阴极析出或阳极溶解将 杂质去除。
电解提取
通过电解溶融盐类溶液,使杂质元素在阳极上氧化溶解,而主金属则在阴极上还原析出 ,达到杂质去除的目的。
炼铁过程中的炉身杂质清理技术

清理炉身杂质的 方法:机械清理、 化学清理、电化 学清理等
实践案例分析: 某钢铁公司采用 机械清理方法, 成功清理炉身杂 质,提高了生产 效率
实践经验总结: 根据炉身杂质的 类型和程度,选 择合适的清理方 法,确保清理效 果和生产效率。
提高生产效率:清理技术 可以减少炉身杂质,提高 炼铁效率,从而降低生产
案例背景:某钢铁公司炉身杂 质清理项目
技术应用:采用先进的炉身杂 质清理技术
效果评估:杂质清理效果显著, 提高了生产效率
成本节约:降低了生产成本, 提高了经济效益
环保效益:减少了废气、废水 排放,符合环保要求
案例启示:采用先进的炉 身杂质清理技术,可以提 高生产效率,降低生产成
本,符合环保要求。
清理炉身杂质的 重要性:提高炉 身寿命,减少停 炉时间,提高生 产效率
ቤተ መጻሕፍቲ ባይዱ
自动化技术的应用:提高清 理效率,降低人工成本
环保技术的应用:减少环境 污染,提高清洁生产水平
新材料的应用:提高清理效 果,延长设备使用寿命
智能化技术的应用:实现远 程监控和故障诊断,提高设
备运行稳定性
清理方法:机械清理、化学清理、电化学清理等
清理效果:提高炉身使用寿命,降低生产成本 案例分析:某钢铁公司采用机械清理方法,成功清除炉身杂质,提高生产效 率 实践经验:定期清理炉身杂质,确保生产安全与产品质量
影响炉身寿命:杂质可能导致炉身磨损,缩短使用寿命 影响铁水质量:杂质可能导致铁水质量下降,影响产品质量 影响生产效率:杂质可能导致生产过程不稳定,影响生产效率 影响环境污染:杂质可能导致废气、废水等污染物排放增加,影响环境污染
提高炉身寿命:清除杂质可以减少 炉身的磨损,提高使用寿命。
钢中夹杂物的去除方法

钢中夹杂物的去除方法
钢中夹杂物的去除方法可以根据夹杂物的性质和形状来选择适当的方法。
以下是一些常用的方法:
1. 磁性夹杂物的去除:如果夹杂物是磁性的,可以使用磁铁或电磁铁来吸附和清除夹杂物。
将磁铁或电磁铁放在钢材附近,使用磁力将夹杂物吸附在磁铁上,然后将磁铁与夹杂物一起移除。
2. 熔炼剂的去除:对于含有氧化物或硫化物夹杂物的钢材,可以使用熔炼剂来与夹杂物反应形成渣滓,并将其从钢中分离出来。
熔炼剂可根据夹杂物的成分和特性选择不同的化学物质。
3. 精炼处理:通过加热和冷却的方式,利用夹杂物与钢的差异性,使夹杂物凝固或浮于钢液表面,然后进行分离。
精炼处理包括真空精炼、气体精炼和浸渣精炼等方法。
4. 超声波清洗:通过将钢材浸泡在特殊的清洗液中,利用超声波震荡,使夹杂物从钢材表面或内部脱离,并被清洗液带走。
5. 机械加工:对于较大的夹杂物或粗大的颗粒夹杂物,可以通过机械加工(如切割、磨削、铣削等)的方法将其从钢材中去除。
以上是一些常用的去除钢中夹杂物的方法,具体的方法选择应根据材料的要求和夹杂物的性质进行决定。
在进行夹杂物去除时,需遵循相关的操作规程和安全操作要求。
精炼过程中夹杂物的控制

精炼过程中夹杂物的控制发布时间:2009-04-02 14:34:54研究表明精炼过程可以去除钢液中80%左右的夹杂物。
1 真空吹氩气搅拌去除夹杂物真空可以进一步脱氧去除夹杂物。
钢包吹氩的精炼原理是:氩气泡的清洗作用;氩气泡上浮带动的钢水流动。
其作用主要有:使包中钢液成分均匀;使包中钢液温度均匀,便于正确掌握铸温;搅动的钢液增加了钢中非金属夹杂碰撞、聚集长大的机会,使上浮的氩气泡把钢液中的非金属夹杂物和气体一起带到钢液表面,并被渣层所吸收。
2 加入粉剂进一步去除钢中的杂质元素特别是在RH精炼过程中深脱硫,在RH精炼时以气粉两相流喷入石灰(CaO)、石灰(Ca0)/萤石(CaF2)+硅钙粉(CaSi)、石灰(Ca0),萤石(CaF2)、Ca、Mg等粉剂,这些粉剂在钢液循环流动的过程中可以作为吸附夹杂物的载体,将很快弥散于钢液内部,并与钢液中的硫在钢液与粉剂颗粒界面处发生脱硫反应。
正是由于RH精炼过程中钢液独特的流动和混合特性,使其具有一些显著的冶金效果:可使钢液的氧位降得更低,从而保证有效地脱硫;在脱硫的同时还可有效地脱气;可最大限度地消除顶渣对脱硫的影响;能为脱硫提供更好的动力学条件。
3 钢液中夹杂物的改性对钢中夹杂物MnS和A1203改性的原理是:钙与硫、氧均有很强的亲和力,其脱硫产物CaS和脱氧产物CaO易与钢中的A1203反应化合,形成低熔点的钙铝酸盐(mCaO·nA1203)复合夹杂物,这种夹杂物易于上浮,排出钢液进入顶渣,起到进一步净化钢水和对A1203夹杂物改性的作用。
当有A1203存在的条件下形成钙铝酸盐,它具有较高的硫容量,可以吸收脱硫后钢中剩余的硫。
随着钢液的冷却,硫在钙铝酸盐中溶解度的降低,硫化物以硫化钙的形式析出,抑制钢水在此过程中MnS的总量和聚集程度,并将MnS部分或全部改性为CaS,导致最后形成内部含钙铝酸盐、外壳包围着硫化钙层的复合夹杂物,或是CaS与Mn 的复合相,从而改善钢的各向异性,起到了钙作为硫的变性剂作用。
炼钢过程中钢水中杂质的分离技术

炼钢过程中钢水中杂质的分离技术
钢是一种非常重要的材料,广泛应用于现代的建筑、交通、机械制造等领域。
而钢的质量往往直接影响到其使用效果和使用寿命,因此在生产过程中必须对钢的质量进行严格的控制。
钢水中的杂质是影响钢的质量的重要因素之一,如何去除钢水中的杂质成为了炼钢过程中需要解决的难点之一。
现在,有许多分离技术可以有效地去除钢水中的杂质,例如溶剂抽提、过滤、离心分离等。
本文将介绍几种常见的炼钢过程中钢水中杂质的分离技术。
一、溶剂抽提
溶剂抽提是一种高效的分离技术,适用于分离钢水中的铁、铬、锰、镉等金属离子,该技术可将钢水中的杂质离子与有机溶剂组成络合离子,以达到去除杂质的目的。
将有机溶剂与钢水混合搅拌后,静置一段时间,溶剂中的络合离子便可以溶解出来从而实现分离。
二、过滤
过滤是一种最简单直接的分离技术。
过滤器通常由设有细
小孔隙的过滤网制成,对于大颗粒杂质和固体微粒有很好的分离效果。
在炼钢中,通过在钢水流动的管道中设置过滤器,可以将较大的杂质分离出来,从而降低钢水中的杂质含量。
三、离心分离
离心分离是一种重力分离的方法,该方法适用于钢水中的
浮游细颗粒和稠密颗粒的分离。
在离心分离过程中,由于工作管道中的钢水在离心力的作用下分离出较轻的杂质颗粒和较重的金属颗粒,从而得到较纯净的钢水。
总之,在炼钢过程中,钢水中的杂质分离技术可以对钢的质量产生重要影响。
鉴于各种分离技术的适用范围和工艺要求不同,需要根据情况选择最合适的分离技术,以确保钢水成分的纯净度,从而提高钢的质量和使用寿命。
减少钢中夹杂的途径及其变形处理

S I E HIF R TO E E O M N C— C O MA IND V L P E T&E O O Y T N C NM
20 年 06
第 1卷 6
第 1 期 1
收稿 日 20 — 1 1 期:0 6 0 — 3
减少钢 中夹杂的途径及 其变形处理
陈 聪
( 山西工程职业技术学 院, 山西太原 ,3 0 9 000 ) 摘 要 : 了解 夹杂物 对钢性能影响 的基础 上, 在 首先应力求降低 夹杂物的含量 , 对不可
夹杂物是钢 中非金属元素( ,,, ,) O sPN c 的化 合物 , 是 O及 s 特别 的 化合物 最重要 , 对钢性能的影 响也最大 。 它们是 非金属特性 的组成物 , 来 源于炼 钢的原材料 , 产生于冶炼 及凝固过程 中 。 在随后的热 、 并 冷加工过 程中发 生形态 的变化 , 对钢材的性能有较大的影响。 夹 杂物与基体金属 的物性及 机械性能 , 弹性 、 如 塑性及热膨胀 系数 均有较大差别 , 在受力 过程中 , 夹杂物不能随金属相应 变形 。 变形大的铁 就会在 变形小 的夹杂物的周 围产生塑性流动。 它们 的连接处应力的分布 不均 匀 , 出现 了应力集 中 , 急剧地升 高, 井 导致微 裂纹 的产生 , 为材 料的 破坏提供 了受力的薄弱区 , 了塑性破裂的过程。 加速 因而导致钢的范性 、 韧性及疲劳强度降低 , 向性加强及加卫 陛能变坏等。 方
夹杂物往往作 为显微裂纹的起点 起着重要作用 。 因此夹杂物对金属材料 与断裂过程有 关联的性能指标如延伸率 、 断面收缩率等影响很大。就夹 杂物对 塑性 的影响来说 。在断面收缩率上 比在延伸率上表现得更显著 。 条带状 塑性夹杂物和点链状脆性 夹杂物使钢材 性能带有方向性 , 使钢的 横向塑性低 于纵向塑性。
降低炼钢中的d类夹杂物的方法

降低炼钢中的d类夹杂物的方法我折腾了好久降低炼钢中的d类夹杂物的方法,总算找到点门道。
说实话,刚开始我真的是瞎摸索。
我知道d类夹杂物主要是一些小颗粒的氧化物、硫化物啥的,要把它们减少可不容易。
我先试的是调整炉内的温度,我就寻思着温度合适了,说不定那些杂质就不容易形成了。
我试着把温度升高一点,结果发现有时候会让钢水变得更不稳定,夹杂物反倒没减少还增加了。
我一下就愣了,这跟我想的不一样啊。
后来我才明白,炉内的反应很复杂,不是光温度高就行。
然后我又想,原料是不是有影响呢。
我就特别仔细地检查我用的原料,就好比咱做饭,食材要是不好,做出来的饭肯定不行,炼钢的原料就像咱做饭的食材。
结果发现有些原料里本身就带着不少微小的杂质,这肯定不行啊。
我开始严格筛选原料,那些杂质多的我都淘汰掉。
这一步真的还挺有效的,我发现d类夹杂物的量开始有减少的趋势了。
还有一个我尝试的方法,就是调整炼钢过程中加入的脱氧剂的量。
脱氧剂这东西就像是清洁员,能把钢水里的氧清理一下,可加少了氧太多会有夹杂物,加多了也可能产生别的问题。
我就一点点试这个量。
有一回我加多了,钢水的流动性都变差了,就像粥太稠了搅不动。
我就知道加多了不行,后来慢慢调整,就找到一个比较合适的数值,这样又能减少一些d 类夹杂物。
另外呢,我觉得炉内的搅拌也很重要。
好的搅拌就像是把钢水彻底搅匀,让各种成分充分反应。
我尝试了不同的搅拌速度和时间,有的时候搅拌太猛了,就像你用筷子在碗里使劲搅汤一样,弄得乱七八糟的,钢水也会乱套。
我不断调整,发现找到一个合适的搅拌参数,对减少夹杂物也是好办法。
我现在也还在摸索,但是按照目前这些方法去做,d类夹杂物的量确实能有比较明显的降低。
如果你们也在搞这个,不妨试试从原料、温度、脱氧剂、搅拌这几个方面入手,不过真的要很细心很耐心,千万不能着急。
我就是因为着急,还试错过好几回呢。
比如刚才我提到的那些加多了或者用猛了的情况,都是着急犯错的结果。
- 1、下载文档前请自行甄别文档内容的完整性,平台不提供额外的编辑、内容补充、找答案等附加服务。
- 2、"仅部分预览"的文档,不可在线预览部分如存在完整性等问题,可反馈申请退款(可完整预览的文档不适用该条件!)。
- 3、如文档侵犯您的权益,请联系客服反馈,我们会尽快为您处理(人工客服工作时间:9:00-18:30)。
炼钢中杂质去除或变形处理方法研究
徐茂钧 重庆钢铁研 究所有限公 司,重庆4 0 0 0 8 4
摘 要 通 过 分析 杂质 对钢铁 性 能 的影响 ,有 针 对性 的降低 杂质 的含 量 。对 于 无法去 除 并残 留于 钢铁 中的 杂质 ,借 助 变形处 理 ,使这 类 杂质 发 生 形 态 改 变,从 而 降低 对 钢材 性 能 的损
钢 材 的加 工 性 能 是 以 钢 材 发 生 破 坏 时 的 扭 转数 来 表 示 。S 化 物 对钢 材 的加 工 性 能 影 响 巨大 。提 高 钢 材 中的m(Mn )/ m(S ) 比值 ,可时 部分 Mn S 取代 F e S ,从而 改 善 钢 材 的 加 工 性 能 。然 而 ,过 量 的 Mn S,将 降 低钢 材的 热加 工性 能 。
在 热加 工 过 程 中 ,这 类 夹 杂 一 般 不 会 出现 形变 。同时 ,因 为稀 土 元素 ( R e ) 对O元素 具 有较 强 的亲 和 力 ;因而 将稀 土元 素 ( Re ) 添加 进钢 液 中后 ,最 先形 成 稀土 元 素 ( Re ) 的0 化 物 。只有 当m( s ) / m( Re ) <l / 3 时 ,才 有可 能形 成 稀土 元 素 ( R e ) 的S 化 物 ,使得 Mn S 夹 杂 彻底 清 除 。因而 ,钢 液 中 ,所 形成 的 稀土 元素( Re ) 夹杂 类 型 ,与 钢液 中 的m( S ) 、m( 0) 的含 量密 切相 关 。然而 ,稀 土 元素 ( R e ) 夹 杂 密度 较大 (5 . 1 g / c m ~6 . 1 g / c m ) ,难 以 上 浮 ,常在 钢锭 底部 出现 偏析 。因而 稀土 元 素( Re ) 添加 量需 合理 控制 。
3 . 3 铝酸 盐夹 杂处 理
1钢中夹杂物
般 地 ,钢 内非 金 属元 素 ( 包 括 :s , 0, N, P, C等 ) 的 化 合 物 , 即 钢 的 夹 杂 物 ,对 钢性 能具 有较 大 的 负面 影 响 。其 中 影 响 最 大 的 为S 及 0的化 合 物 。 它们 组 成 了 钢 的非 金属 特 性 。这些 化合 物 由炼钢 原材 料 带 人 ,并 在钢 的 冶 炼 与 凝 固 冷 却 过 程 中产 生 ,其 形态 变 化发 生于 钢 的冷 ,热加 工过 程 中 ,最 终极 大 的影 响钢 材性 能 。 由于钢 中夹 杂 物 的机 械 性 能和 物 性 ( 包 括 :塑 性 、 热膨 胀 系 数 和 弹性 ) 和 钢 基 体 金 属 的相 差较 大 , 因此夹 杂物 在受 力变 形过 程 中 ,不 能与 基体 金 属发 生相 应 的变形 。 由于 铁 的变 形较 大 ,夹 杂物 变形 较小 ,所 以铁 将 在 夹杂 物 周 围发 生 塑性 变 形 。铁 与夹 杂 物 的连 接处 将 产生 较大 的应 力集 中。随着 塑 性 变形 的 进一 步加 大 ,铁 与夹 杂物 的连 接处 应 力集 中将 急 剧升 高 ,产生 微 裂纹 ,使得 材 料 产生 了受力 薄弱 区 ,塑性 破 裂的过 程加 速 。 从而 使得 钢 的疲 劳 强度 、范性 和韧 性 降低 , 加 工性 能 变化 和 方 向性 变 强等 。
伤。
关键 词
杂质 ; 变形 处理 ;钢 铁性 能
:a . 表面缺 口;b . 材料 内部 杂质 ;c . 第 二相 质点 ;d . 微 裂纹 等 。 研 究 发 现 ,不 同的 杂 质 对 钢 材 的 疲 劳 寿 命 的影 响程 度存 在一 定的 差 异 ,按照 其影 响程 度 ,由 强到 弱排 序 为 :1 )刚 玉 、球 状 不 变形 夹杂 物 ;2 )半 塑性 硅酸盐 ;3 )塑性 硅 酸盐 ;4 )硫 化物 。 2 . 3 杂 质对钢 材 的加 工性能 的 影响
一
3减少钢 中夹杂的措施与变形处理
3 . 1减 少钢 中夹 杂 的措施 股 情 况 下 ,钢 材 中 的夹 杂 将 降低 其 某种性 能 ,因为夹 杂含 量 需严 格控 制 。常规 的解决 措 施为 :合 理控 制 金属 的冶 炼 、浇注 工 艺 ,从 而 实 现 降 低 钢 材 中杂 质 含 量 的 目 的 ,其 作 用有 一定 的局 限性 。随 着科 学技 术 的不断 进 步 ,一些 先进 的精 炼技 术被 引入 到 金 属பைடு நூலகம்的 冶炼 过 程 中 ,用 于 降 低 夹 杂 含 量 , 如 :a . 真空 技 术 ;b. 渣 洗 技术 ;c . 惰 性 气体 净 化 ;d . 电渣重 熔等 。
一
采 用 铝 脱 氧 的镇 静 钢 材 内 部 ,会 形 成 A 1 O 等 固相 ,其 熔 点较 高 J ;出 了少部 分 上 浮 之外 ,绝 大 多数均 残 留于钢 液之 中。在 轧 制过 程 中 ,枝 晶易于 破裂 ,从 而生 产 串状 的 夹杂 ,提 高 了钢 的异 向性 。 将 钙 合 金 脱氧 喷 入到 钢 液 中 ,可 有 效 降 低0元 素 的 质量 百 分 比 ( < 0 . 0 0 0 1 % ) , 从 而 得 到 熔 点较 低 ( 1 4 2 0 ℃) 的 液 态 铝 酸 钙 ( C1 2 A 7 、1 2 C a O・ 7 A1 2 O3 ) 。 C1 5 A 7 、 l 2 Ca O ・7 Al 2 O 3 容 易 上 浮 , 溢 出 ; 即 使残 留于钢液 中的极 少量的 C l A 、 1 2 C a O・ 7 A1 2 O 3 等 夹 杂 ,不 会 像 Al 2 0 3 那 样 ,呈 串状分 布 ,从而 解决 了钢 材异 向性 问