试论汽车铝合金压铸件质量的综合诊断和控制
压铸铝合金加工质量的控制分析

压铸铝合金加工质量的控制分析摘要:随着时代的持续发展,社会经济水平不断提高的同时,压铸铝合金的应用范围也越来越广泛。
因此,压铸铝合金类的铸件在性能、有点方面,是保障其应用质量的关键环节,有必要对压铸铝合金的加工技术进行了解,进而进一步对其展开研究。
对此,文章针对压铸铝合金加工质量的控制进行了分析,希望以此能够促进我国压铸铝合金加工质量的有效控制。
关键词:压铸;铝合金;加工质量;控制;分析引言:铝合金这种材料在实际使用中拥有众多优势,比如密度小、良好的耐蚀性、强度高等特点,当前阶段已经在各个领域都获得了广泛地应用。
而在进行铝合金零件成型的过程中,通常会以压铸方式作为主要加工工艺。
因此,要想使铝合金零件的加工质量得到保障,需要深入的对压铸工艺展开研究,及时针对压铸铝合金的发展现状,提出质量控制的策略。
1.压铸铝合金加工的主要类别虽然压铸铝合金属于苏联五十年代的合金系列,但是我国当前依然对其继续沿用,这种合金做成的刀具相比于其他金属材料做的道具更加具有优势,比如寿命更长、容易切削等。
我们日常生活中见到的压铸铝合金有很多种类别,比如Al-Mg、Al-Si、Al-Zn等铝合金,其中Al-Mg铝合金在实际使用中,体现出来的力学性能处于室温阶段的时候是最好的,处于此时阶段的合金在抗腐蚀性方面是最强的,但是其中存在的不足,就是相关压铸件很容易产生应力腐蚀裂纹,但是它自身具备的优点完全可以将它的一些缺点替代。
Al-Si铝合金在当前阶段属于应用最广泛的合金,它具有结晶温度间隔小的优势,主要是由于该合金内的硅的比热容、凝固潜热都比较大,促使其在线收缩系数方面较小,进而使得它在铸造性能方面极为良好。
此外,Al-Si铝合金的塑性也是极为良好的,所以使得获得了极为广泛的应用范围。
Al-Zn铝合金在压铸件方面,体现出的力学性能是比较高的,能够使锌的质量分数得到提升,进而使其强度得到增加。
但是,Al-Zn铝合金在耐蚀性方面是比较差的,如果压铸合金的时候硅与铁的含量较少,那么将会非常容易出现热裂现象。
铝合金压铸零件的质量缺陷及改善措施

铝合金压铸零件的质量缺陷及改善措施摘要:铸造铝合金是一种传统的金属材料,因其密度低、比强度高而广泛应用于航空、航天、汽车、机械等行业。
随着现代工业和铸造新技术的发展,对铸造铝合金零件的要求和质量越来越高。
压铸是现代金属加工技术中一种先进的少切削的特种铸造方法。
探讨了铝合金压铸件的质量缺陷及改进措施。
关键词:铝合金压铸零件;质量缺陷;改善措施引言压力铸造作为一种特殊的成形技术,已广泛应用于许多行业和领域,特别是汽车、摩托车、内燃机、电子、仪器和航天等行业。
一、铝合金压铸技术概述铝是地壳中分布最广、储量最大的金属元素。
纯铝为银白色,熔点低,导电性和导热性好,耐腐蚀。
铝合金密度低,比重小,比强度高,导热性好,耐腐蚀性好,价格低廉,易成型,适用于加工各种型材,工业用途仅次于钢材,是压铸行业中使用最多的有色金属结构材料。
铝合金具有熔点高、重量轻的特点,高熔点意味着它可以作为耐高温材料,广泛应用于各行各业,如发动机,等。
使用重量轻的优势可以应用在太空设备,中国已经建立了一个良好的登月车,绝大多数是由高强度铝合金引起,有很多这样的例子,也正因为如此,铝合金已成为汽车、航空航天等行业金属材料不可替代。
二、铝合金压铸零件的质量缺陷及改善措施2.1气孔气孔是指在压铸件内部或表面出现的孔洞和大小不等的孔洞,表面光滑,多为圆形。
气孔的形成会导致压铸件硬度不足,影响表面形貌。
2.1.1压铸箱螺栓孔周围出现气孔现象。
压铸铝合金箱体上有许多螺栓孔、油孔和各种安装孔,直接影响发动机的装配质量和使用性能。
2.1.2产生原因。
铝合金箱体压铸件由于充液腔速度快,模具腔内气体不易排出,容易滞留在铝液中。
铝液冷却凝固后,残余气体在铸件中形成小气泡,即气孔。
在铝合金压铸过程中,液态铝铸件的温度一般在660℃左右,但在铝液的温度包含大量的气体(主要是氢气),铝合金中氢的溶解度与温度密切相关,温度的气体含量0.69cm3/100克瓦斯含量大约是19到20倍正常,所以铝合金凝固后,气体的大量析出会导致铝合金铸件的气孔。
汽车铝合金缸盖铸件缺陷分析及控制
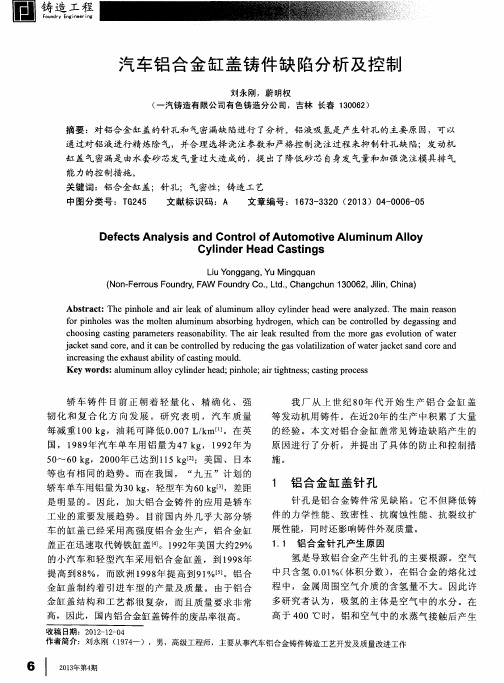
轿 车 铸 件 目前 正 朝 着 轻 量 化 、 精 确 化 、 强 韧 化 和 复 合 化 方 向 发 展 。研 究 表 明 , 汽 车 质 量 每减 重 1 O 0 k g , 油 耗 可 降低 0 . 0 0 7 L / k m[ 1 ] 。在 英 国,1 9 8 9 年汽 车单车用 铝量 为4 7 k g ,1 9 9 2 年 为 5 0 ~6 0 k g ,2 0 0 0 年 已达 到 1 1 5 k g [ 2 ] ;美 国 、 日本
件 的力 学 性 能 、致 密 性 、 抗 腐 蚀 性 能 、抗 裂 纹 扩
展 性 能 , 同 时还 影 响铸 件 外 观质 量 。
车 的缸 盖 已经 采 用 高 强 度 铝 合 金 生 产 ,铝 合 金 缸 盖 正 在 迅速 取 代 铸 铁 缸 盖 [ 4 ] 。1 9 9 2 年 美 国大 约2 9 % 的 小汽 车 和 轻 型 汽 车 采 用 铝 合 金 缸 盖 , 到 1 9 9 8 年 提 高到8 8 % ,而 欧 洲 1 9 9 8 年提 高到9 1 0 / 0 【 。铝 合
施。
轿车单车用铝量为3 0 k g ,轻 型 车 为6 0 k g [ 3 ] ,差 距 是 明 显 的 。 因此 , 加 大 铝 合 金 铸 件 的 应 用 是轿 车
工 业 的 重 要 发 展 趋 势 。 目前 国 内外 几 乎 大 部 分 轿
1 铝合金 缸盖针 孑 L
针 孔 是 铝 合 金 铸 件 常 见 缺 陷 。 它 不 但 降低 铸
缸盖 气密漏是 由水套砂 芯发 气量过 大造成 的,提 出了降低砂 芯 自身发 气量和加 强浇注模具排 气
能 力 的控 制措 施 。
关键词 :铝合金缸盖 ;针孔 ;气密性;铸造工艺
铝合金压铸件检验标准
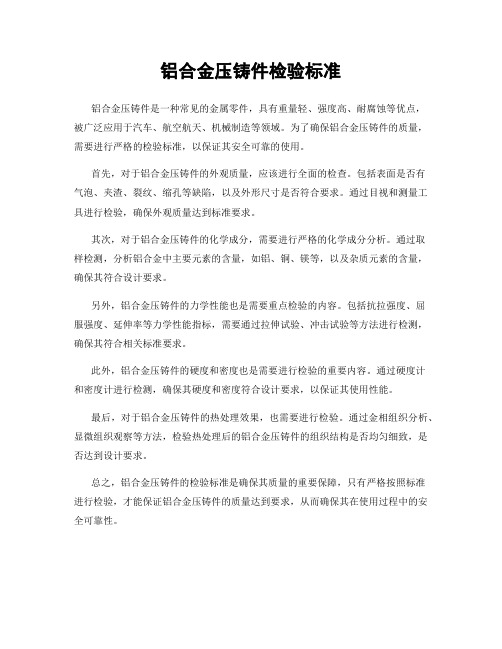
铝合金压铸件检验标准
铝合金压铸件是一种常见的金属零件,具有重量轻、强度高、耐腐蚀等优点,
被广泛应用于汽车、航空航天、机械制造等领域。
为了确保铝合金压铸件的质量,需要进行严格的检验标准,以保证其安全可靠的使用。
首先,对于铝合金压铸件的外观质量,应该进行全面的检查。
包括表面是否有
气泡、夹渣、裂纹、缩孔等缺陷,以及外形尺寸是否符合要求。
通过目视和测量工具进行检验,确保外观质量达到标准要求。
其次,对于铝合金压铸件的化学成分,需要进行严格的化学成分分析。
通过取
样检测,分析铝合金中主要元素的含量,如铝、铜、镁等,以及杂质元素的含量,确保其符合设计要求。
另外,铝合金压铸件的力学性能也是需要重点检验的内容。
包括抗拉强度、屈
服强度、延伸率等力学性能指标,需要通过拉伸试验、冲击试验等方法进行检测,确保其符合相关标准要求。
此外,铝合金压铸件的硬度和密度也是需要进行检验的重要内容。
通过硬度计
和密度计进行检测,确保其硬度和密度符合设计要求,以保证其使用性能。
最后,对于铝合金压铸件的热处理效果,也需要进行检验。
通过金相组织分析、显微组织观察等方法,检验热处理后的铝合金压铸件的组织结构是否均匀细致,是否达到设计要求。
总之,铝合金压铸件的检验标准是确保其质量的重要保障,只有严格按照标准
进行检验,才能保证铝合金压铸件的质量达到要求,从而确保其在使用过程中的安全可靠性。
铝合金压铸件质量检验规范

铝合金压铸件质量检验规范铝合金压铸件是一种常见的金属制品,广泛应用于汽车、机械设备、电子产品等领域。
为了确保铝合金压铸件的质量,需要制定相应的质量检验规范。
下面是一份针对铝合金压铸件的质量检验规范,包括材料检验、尺寸检验、表面质量检验等方面的内容。
一、材料检验1.铝合金材料的检验应符合相关标准和技术要求;2.对材料的化学成分进行分析测试,确保合金成分符合要求;3.对材料的力学性能进行测试,如强度、硬度、延伸率等指标;4.检查材料的外观,包括气孔、夹杂物、裂纹等缺陷的情况;5.检验材料的金相组织,确保组织均匀、致密。
二、尺寸检验1.根据设计图纸,对铝合金压铸件的尺寸进行检验;2.检验件应符合设计要求的几何尺寸、公差和形位公差等要求;3.使用适当的测量工具进行尺寸检验,包括千分尺、卡尺、量具等;4.尺寸检验应包括外观尺寸、内孔尺寸、孔距等方面的检验。
三、表面质量检验1.对铝合金压铸件的表面进行检查,包括表面光洁度、光泽度等指标;2.检查表面是否有划痕、氧化、气孔、砂眼等缺陷;3.对表面的涂层进行检验,如喷漆、镀层等。
四、力学性能检验1.对铝合金压铸件的强度、硬度、延伸率等力学性能进行检验;2.根据相关标准和技术要求,进行相应的力学性能测试,如拉伸试验、冲击试验等。
五、工艺性能检验1.对铝合金压铸件的可焊性、可加工性等工艺性能进行检验;2.根据相关标准和技术要求,进行相应的工艺性能测试。
六、标识和包装1.对符合质量要求的铝合金压铸件进行标识,包括产品名称、型号、批次号、生产日期等;2.对铝合金压铸件进行适当的包装,确保其安全运输和质量保持。
七、检验记录和检验报告1.对铝合金压铸件的质量检验进行记录,包括检验日期、检验人员、检验结果等;2.编制相应的检验报告,归档保存,以备查阅。
以上是一份关于铝合金压铸件质量检验的规范,目的是确保铝合金压铸件的质量符合要求,以提供优质的产品给客户。
这份规范可以根据具体情况进行调整和完善,以适应不同厂家和产品的特点和需求。
汽车铝合金压铸件质量的综合诊断和控制
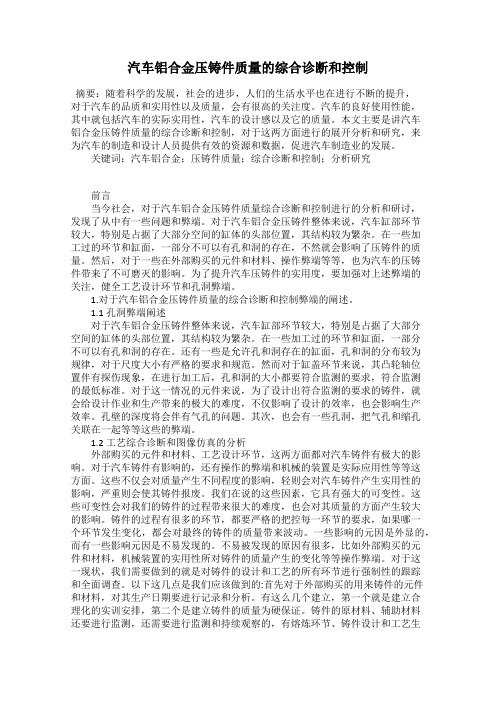
汽车铝合金压铸件质量的综合诊断和控制摘要:随着科学的发展,社会的进步,人们的生活水平也在进行不断的提升,对于汽车的品质和实用性以及质量,会有很高的关注度。
汽车的良好使用性能,其中就包括汽车的实际实用性,汽车的设计感以及它的质量。
本文主要是讲汽车铝合金压铸件质量的综合诊断和控制,对于这两方面进行的展开分析和研究,来为汽车的制造和设计人员提供有效的资源和数据,促进汽车制造业的发展。
关键词:汽车铝合金;压铸件质量;综合诊断和控制;分析研究前言当今社会,对于汽车铝合金压铸件质量综合诊断和控制进行的分析和研讨,发现了从中有一些问题和弊端。
对于汽车铝合金压铸件整体来说,汽车缸部环节较大,特别是占据了大部分空间的缸体的头部位置,其结构较为繁杂。
在一些加工过的环节和缸面,一部分不可以有孔和洞的存在,不然就会影响了压铸件的质量。
然后,对于一些在外部购买的元件和材料、操作弊端等等,也为汽车的压铸件带来了不可磨灭的影响。
为了提升汽车压铸件的实用度,要加强对上述弊端的关注,健全工艺设计环节和孔洞弊端。
1.对于汽车铝合金压铸件质量的综合诊断和控制弊端的阐述。
1.1孔洞弊端阐述对于汽车铝合金压铸件整体来说,汽车缸部环节较大,特别是占据了大部分空间的缸体的头部位置,其结构较为繁杂。
在一些加工过的环节和缸面,一部分不可以有孔和洞的存在。
还有一些是允许孔和洞存在的缸面,孔和洞的分布较为规律,对于尺度大小有严格的要求和规范。
然而对于缸盖环节来说,其凸轮轴位置伴有探伤现象,在进行加工后,孔和洞的大小都要符合监测的要求,符合监测的最低标准。
对于这一情况的元件来说,为了设计出符合监测的要求的铸件,就会给设计作业和生产带来的极大的难度,不仅影响了设计的效率,也会影响生产效率。
孔壁的深度将会伴有气孔的问题。
其次,也会有一些孔洞,把气孔和缩孔关联在一起等等这些的弊端。
1.2工艺综合诊断和图像仿真的分析外部购买的元件和材料、工艺设计环节,这两方面都对汽车铸件有极大的影响。
铝合金压铸件检验规范
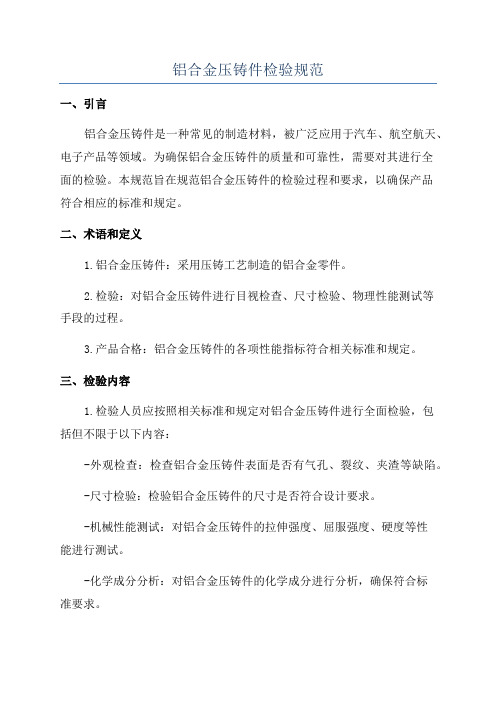
铝合金压铸件检验规范一、引言铝合金压铸件是一种常见的制造材料,被广泛应用于汽车、航空航天、电子产品等领域。
为确保铝合金压铸件的质量和可靠性,需要对其进行全面的检验。
本规范旨在规范铝合金压铸件的检验过程和要求,以确保产品符合相应的标准和规定。
二、术语和定义1.铝合金压铸件:采用压铸工艺制造的铝合金零件。
2.检验:对铝合金压铸件进行目视检查、尺寸检验、物理性能测试等手段的过程。
3.产品合格:铝合金压铸件的各项性能指标符合相关标准和规定。
三、检验内容1.检验人员应按照相关标准和规定对铝合金压铸件进行全面检验,包括但不限于以下内容:-外观检查:检查铝合金压铸件表面是否有气孔、裂纹、夹渣等缺陷。
-尺寸检验:检验铝合金压铸件的尺寸是否符合设计要求。
-机械性能测试:对铝合金压铸件的拉伸强度、屈服强度、硬度等性能进行测试。
-化学成分分析:对铝合金压铸件的化学成分进行分析,确保符合标准要求。
-金相组织检查:对铝合金压铸件的金相组织进行显微镜观察、显微硬度测试等。
-其他测试:根据需要可以进行疲劳强度测试、冲击试验等其他测试。
四、检验设备和工具1.显微镜:用于金相组织的观察。
2.数据采集仪器:用于机械性能测试时,实时采集铝合金压铸件的力、位移等数据。
3.尺子、千分尺、千分表等:用于尺寸检验。
4.电子秤、光谱仪等:用于化学成分分析。
5.硬度计:用于测量铝合金压铸件的硬度。
五、检验方法1.外观检查:按照标准要求进行目视检查,记录铝合金压铸件表面的缺陷,并标明数量和位置。
2.尺寸检验:使用合适的测量工具,按照设计图纸的要求测量铝合金压铸件的尺寸,将结果与设计要求进行对比。
3.机械性能测试:根据相关标准和规定进行测试,记录铝合金压铸件的拉伸强度、屈服强度、硬度等性能指标。
4.化学成分分析:通过光谱仪等设备进行化学成分分析,将结果与标准要求进行对比。
5.金相组织检查:制备金相试样,使用显微镜观察铝合金压铸件的金相组织,并进行显微硬度测试。
铝合金压铸零件的质量缺陷及改善措施

铝合金压铸零件的质量缺陷及改善措施压力铸造(简称压铸)是在高压作用下,使液态或半液态金属以较高的速度充填压铸模具型腔,并在压力下成型和凝固而獲得铸件的方法。
压铸是在高压高速下注入金属熔液,可制造形状复杂的薄壁件,获得的铸件晶粒细,组织致密,强度较高,且压铸的生产率高,因此压铸件广泛应用于汽车、仪器仪表、计算机、医疗器械等制造业,如发动机汽缸体、汽缸盖、仪表和照相机的壳体与支架、管接头、齿轮等零件。
用于压铸的材料主要有铝合金、锌合金、铜合金和镁合金等。
标签:铝合金;压铸;质量缺陷;改善措施1 气孔气孔是指在压铸件内部或表面出现的大小不等的孔眼、空穴,有光滑的表面,形状多为圆形。
气孔的产生会导致压铸件硬度不足和影响表面美观。
气孔的来源主要为压铸过程中卷入的气体或铝液析气。
1.1 压铸铝合金缸体螺栓孔周边的气孔现象压铸铝合金缸体上有很多螺栓孔、油孔以及各种安装孔,这些直接影响发动机的装配质量和使用性能,在压铸过程中需要严格控制其质量。
压铸生产后对缸体的主轴承螺栓孔和上下缸体螺栓孔区域进行剖切,发现铸造螺栓孔周围有小的气孔。
1.2 产生原因铝合金缸体压铸时由于液态金属充填型腔速度高,模具型腔内的气体不易排出,容易残留在铝液中,铝液冷却凝固后残留的气体在铸件内形成很小的气泡,即气孔,直径一般不大于1mm;压铸模具内型芯周围和壁厚变化较大的位置,铝液流动性不稳定,容易产生气孔,这也是铸件螺栓孔周围气孔较多的原因。
螺栓孔周围的气孔很小,小于螺纹长度1/3,且不在螺纹区域,对扭矩没有影响,不会影响其使用性能,可以不用解决该处的气孔问题。
2 缩孔缩孔是指压铸件厚截面处出现形状不规则的孔眼,孔的内壁粗糙。
缩孔的产生会导致压铸件内局部出现组织稀疏,有的甚至呈蜂窝状,影响铸件强度。
液态金属充满型腔后,在收缩过程中得不到足量补充,容易发生在厚薄不均的铸件上。
2.1 压铸铝合金缸体螺栓孔周边、水泵壳体附近的缩孔现象压铸生产后对缸体的主轴承螺栓孔和上下缸体螺栓孔区域进行剖切,发现预铸孔的底部有较大的气孔和缩孔(直径约1~5mm,或有长度超过10mm的细长隙)。
探讨汽车铝合金缸盖铸件缺陷及控制方法
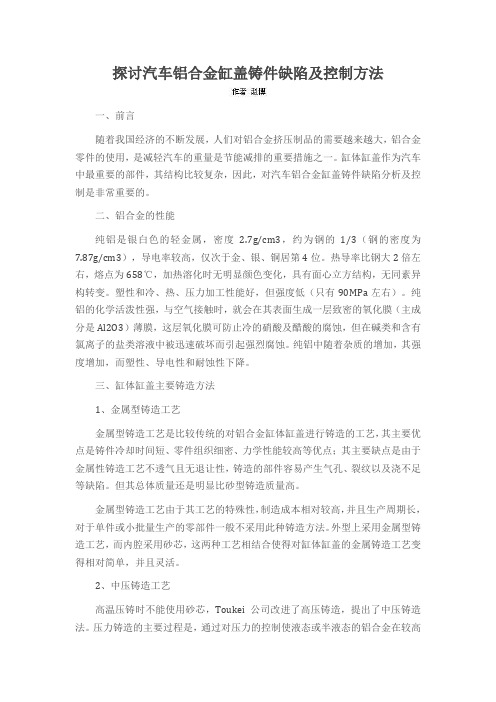
探讨汽车铝合金缸盖铸件缺陷及控制方法一、前言随着我国经济的不断发展,人们对铝合金挤压制品的需要越来越大,铝合金零件的使用,是减轻汽车的重量是节能减排的重要措施之一。
缸体缸盖作为汽车中最重要的部件,其结构比较复杂,因此,对汽车铝合金缸盖铸件缺陷分析及控制是非常重要的。
二、铝合金的性能纯铝是银白色的轻金属,密度 2.7g/cm3,约为钢的1/3(钢的密度为7.87g/cm3),导电率较高,仅次于金、银、铜居第4位。
热导率比钢大2倍左右,熔点为658℃,加热溶化时无明显颜色变化,具有面心立方结构,无同素异构转变。
塑性和冷、热、压力加工性能好,但强度低(只有90MPa左右)。
纯铝的化学活泼性强,与空气接触时,就会在其表面生成一层致密的氧化膜(主成分是Al2O3)薄膜,这层氧化膜可防止冷的硝酸及醋酸的腐蚀,但在碱类和含有氯离子的盐类溶液中被迅速破坏而引起强烈腐蚀。
纯铝中随着杂质的增加,其强度增加,而塑性、导电性和耐蚀性下降。
三、缸体缸盖主要铸造方法1、金属型铸造工艺金属型铸造工艺是比较传统的对铝合金缸体缸盖进行铸造的工艺,其主要优点是铸件冷却时间短、零件组织细密、力学性能较高等优点;其主要缺点是由于金属性铸造工艺不透气且无退让性,铸造的部件容易产生气孔、裂纹以及浇不足等缺陷。
但其总体质量还是明显比砂型铸造质量高。
金属型铸造工艺由于其工艺的特殊性,制造成本相对较高,并且生产周期长,对于单件或小批量生产的零部件一般不采用此种铸造方法。
外型上采用金属型铸造工艺,而内腔采用砂芯,这两种工艺相结合使得对缸体缸盖的金属铸造工艺变得相对简单,并且灵活。
2、中压铸造工艺高温压铸时不能使用砂芯,Toukei公司改进了高压铸造,提出了中压铸造法。
压力铸造的主要过程是,通过对压力的控制使液态或半液态的铝合金在较高的速度下填满压铸型型腔,增高压力即可改变速度,并在一定压力下是铸件凝固成型。
3、中压铸造工艺为满足日益提高的发动机功率,发动机缸体结构变得越来越复杂,而由于高温压铸时存在不能使用砂芯的缺点,Toukei公司改进了高压铸造,提出了中压铸造法。
汽车铝合金压铸件内部质量缺陷改善策略研究
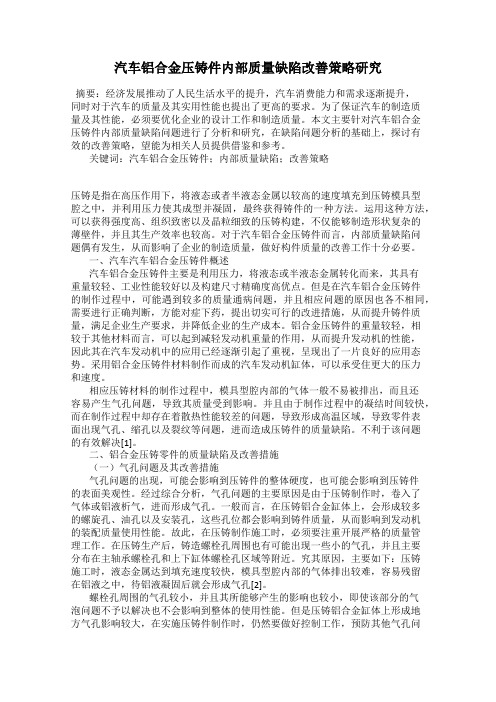
汽车铝合金压铸件内部质量缺陷改善策略研究摘要:经济发展推动了人民生活水平的提升,汽车消费能力和需求逐渐提升,同时对于汽车的质量及其实用性能也提出了更高的要求。
为了保证汽车的制造质量及其性能,必须要优化企业的设计工作和制造质量。
本文主要针对汽车铝合金压铸件内部质量缺陷问题进行了分析和研究,在缺陷问题分析的基础上,探讨有效的改善策略,望能为相关人员提供借鉴和参考。
关键词:汽车铝合金压铸件;内部质量缺陷;改善策略压铸是指在高压作用下,将液态或者半液态金属以较高的速度填充到压铸模具型腔之中,并利用压力使其成型并凝固,最终获得铸件的一种方法。
运用这种方法,可以获得强度高、组织致密以及晶粒细致的压铸构建,不仅能够制造形状复杂的薄壁件,并且其生产效率也较高。
对于汽车铝合金压铸件而言,内部质量缺陷问题偶有发生,从而影响了企业的制造质量,做好构件质量的改善工作十分必要。
一、汽车汽车铝合金压铸件概述汽车铝合金压铸件主要是利用压力,将液态或半液态金属转化而来,其具有重量较轻、工业性能较好以及构建尺寸精确度高优点。
但是在汽车铝合金压铸件的制作过程中,可能遇到较多的质量通病问题,并且相应问题的原因也各不相同,需要进行正确判断,方能对症下药,提出切实可行的改进措施,从而提升铸件质量,满足企业生产要求,并降低企业的生产成本。
铝合金压铸件的重量较轻,相较于其他材料而言,可以起到减轻发动机重量的作用,从而提升发动机的性能,因此其在汽车发动机中的应用已经逐渐引起了重视,呈现出了一片良好的应用态势。
采用铝合金压铸件材料制作而成的汽车发动机缸体,可以承受住更大的压力和速度。
相应压铸材料的制作过程中,模具型腔内部的气体一般不易被排出,而且还容易产生气孔问题,导致其质量受到影响。
并且由于制作过程中的凝结时间较快,而在制作过程中却存在着散热性能较差的问题,导致形成高温区域,导致零件表面出现气孔、缩孔以及裂纹等问题,进而造成压铸件的质量缺陷。
《2024年低压铸造铝合金车轮主要缺陷分析与控制》范文
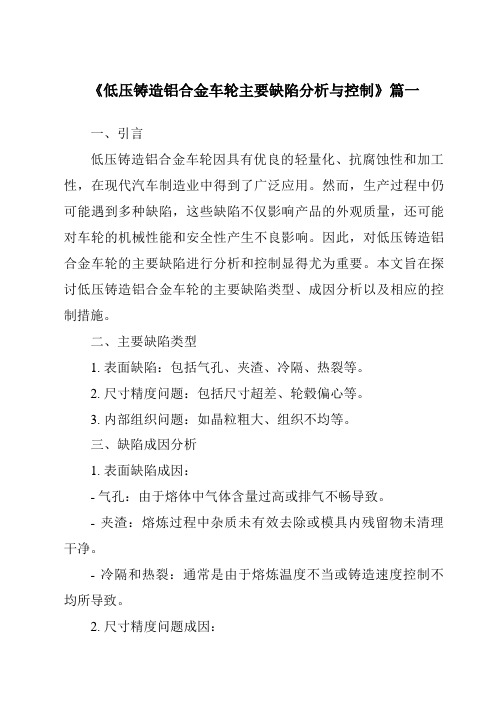
《低压铸造铝合金车轮主要缺陷分析与控制》篇一一、引言低压铸造铝合金车轮因具有优良的轻量化、抗腐蚀性和加工性,在现代汽车制造业中得到了广泛应用。
然而,生产过程中仍可能遇到多种缺陷,这些缺陷不仅影响产品的外观质量,还可能对车轮的机械性能和安全性产生不良影响。
因此,对低压铸造铝合金车轮的主要缺陷进行分析和控制显得尤为重要。
本文旨在探讨低压铸造铝合金车轮的主要缺陷类型、成因分析以及相应的控制措施。
二、主要缺陷类型1. 表面缺陷:包括气孔、夹渣、冷隔、热裂等。
2. 尺寸精度问题:包括尺寸超差、轮毂偏心等。
3. 内部组织问题:如晶粒粗大、组织不均等。
三、缺陷成因分析1. 表面缺陷成因:- 气孔:由于熔体中气体含量过高或排气不畅导致。
- 夹渣:熔炼过程中杂质未有效去除或模具内残留物未清理干净。
- 冷隔和热裂:通常是由于熔炼温度不当或铸造速度控制不均所导致。
2. 尺寸精度问题成因:- 模具设计不合理或加工精度不足。
- 铸造过程中压力控制不稳定。
- 材料收缩率估算不准确。
3. 内部组织问题成因:- 合金成分不均或合金元素含量超标。
- 铸造温度过高或保温时间过长导致晶粒长大。
四、控制措施1. 表面缺陷控制:- 控制熔体中的气体含量,采取真空除气技术。
- 严格清理模具,确保无杂质残留。
- 优化铸造工艺参数,如温度、压力和速度等。
2. 尺寸精度控制:- 提高模具设计及加工精度,确保尺寸稳定性。
- 采用先进的压力控制系统,确保铸造过程中压力稳定。
- 准确估算材料收缩率,合理设计模具补缩系统。
3. 内部组织控制:- 严格控制合金成分及含量,确保合金质量。
- 优化铸造温度和保温时间,避免晶粒长大。
- 采用合金化及热处理技术,改善内部组织结构。
五、结论低压铸造铝合金车轮的缺陷控制是保证产品质量和性能的关键环节。
通过对表面缺陷、尺寸精度问题和内部组织问题的成因分析,我们采取了相应的控制措施,如优化熔炼工艺、提高模具精度和优化合金成分等,从而有效地减少了产品缺陷的发生率,提高了产品的质量和性能。
汽车铝合金铸件质量的综合诊断和控制
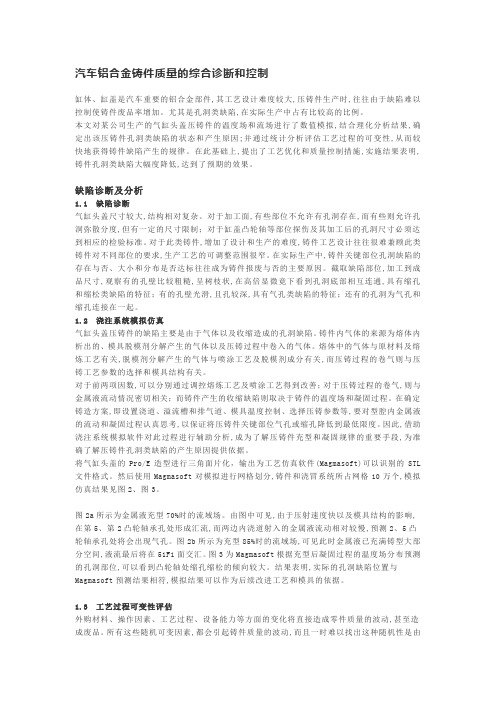
汽车铝合金铸件质量的综合诊断和控制缸体、缸盖是汽车重要的铝合金部件,其工艺设计难度较大,压铸件生产时,往往由于缺陷难以控制使铸件废品率增加。
尤其是孔洞类缺陷,在实际生产中占有比较高的比例。
本文对某公司生产的气缸头盖压铸件的温度场和流场进行了数值模拟,结合理化分析结果,确定出该压铸件孔洞类缺陷的状态和产生原因;并通过统计分析评估工艺过程的可变性,从而较快地获得铸件缺陷产生的规律。
在此基础上,提出了工艺优化和质量控制措施,实施结果表明,铸件孔洞类缺陷大幅度降低,达到了预期的效果。
缺陷诊断及分析1.1 缺陷诊断气缸头盖尺寸较大,结构相对复杂。
对于加工面,有些部位不允许有孔洞存在,而有些则允许孔洞弥散分度,但有一定的尺寸限制;对于缸盖凸轮轴等部位探伤及其加工后的孔洞尺寸必须达到相应的检验标准。
对于此类铸件,增加了设计和生产的难度,铸件工艺设计往往很难兼顾此类铸件对不同部位的要求,生产工艺的可调整范围很窄。
在实际生产中,铸件关键部位孔洞缺陷的存在与否、大小和分布是否达标往往成为铸件报废与否的主要原因。
截取缺陷部位,加工到成品尺寸,观察有的孔壁比较粗糙,呈树枝状,在高倍显微竟下看到孔洞底部相互连通,具有缩孔和缩松类缺陷的特征;有的孔壁光滑,且孔较深,具有气孔类缺陷的特征;还有的孔洞为气孔和缩孔连接在一起。
1.2 浇注系统模拟仿真气缸头盖压铸件的缺陷主要是由于气体以及收缩造成的孔洞缺陷。
铸件内气体的来源为熔体内析出的、模具脱模剂分解产生的气体以及压铸过程中卷入的气体。
熔体中的气体与原材料及熔炼工艺有关,脱模剂分解产生的气体与喷涂工艺及脱模剂成分有关,而压铸过程的卷气则与压铸工艺参数的选择和模具结构有关。
对于前两项因数,可以分别通过调控熔炼工艺及喷涂工艺得到改善;对于压铸过程的卷气,则与金属液流动情况密切相关;而铸件产生的收缩缺陷则取决于铸件的温度场和凝固过程。
在确定铸造方案,即设置浇道、溢流槽和排气道、模具温度控制、选择压铸参数等,要对型腔内金属液的流动和凝固过程认真思考,以保证将压铸件关键部位气孔或缩孔降低到最低限度。
汽车铝合金压铸件质量的综合诊断和控制
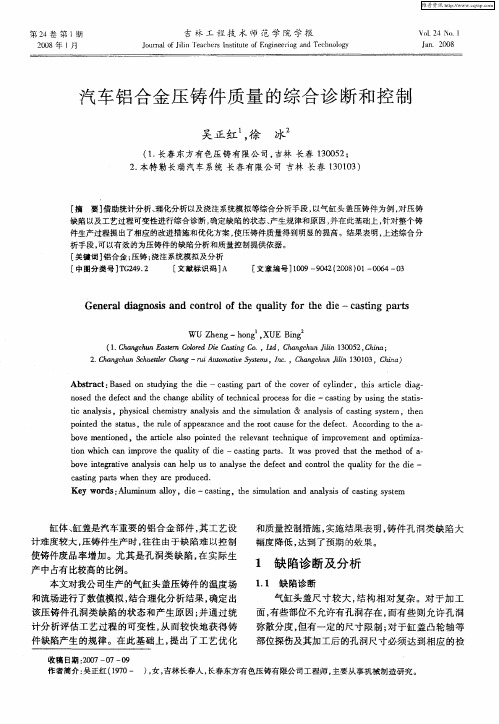
.65.
验标准。对于此类铸件 ,增加了设计 和生产 的难度 , 铸件工艺设计往往很难兼顾此类铸件对不 同部位的 要求 ,生产工艺的可调整范 围很 窄。在实 际生产 中, 铸件关键部位孔洞缺陷的存在与否、大小和分布是 否达标往往成为铸件报废与否 的主要原 因。截取缺 陷部位,加工到成 品尺寸 ,观察有 的孔壁 比较粗糙 , 呈树枝 状 ,在高倍 显微竞 下 看到 孔 洞 底部 相 互 连通 , 具有缩孔和缩松类缺陷的特征 ;有的孔壁光滑 ,且孔 较深 ,具有 气孔类 缺 陷 的特 征 ;还有 的孔 洞为 气 孔 和 缩孔 连接 在一起 。
General diagnosis and control of the quality for the die——casting parts
W U Zheng— hong ,XUE Bing
(1.C ̄ chun Eastern Colored Die Casting Co.,l_td,Changchun Jilin 130052,China; 2.Changchun Schuettler Chang—mi Automotive sya.,a s ,Inc.,Ch a ngchun in 130103, )
Abstract:Based on studying the die — casting part of th e cover of cylinder, this article diag— nosed the defect and the chan ge ability of technical process for die—casting by usl’ng the statis— tic an alysis,physical chemistry an alysis an d the simulation & an alysis of casting system ,then pointed the status,the rule of appearan ce an d the root cause for the defect.According to the a— hove ment ioned,the article a lso pointed t he releva n t technique of improvement a n d optimiza— tion which Ca n impr ove t he q u alit y of die—cast ing parts.It Wa s proved t hat t he met hod of a— hove integrat ive a n a lysis can help US to a n a lyse t he defect a n d control t h e qualit y for t he die—— cas ting parts when th ey ar e produced. Key words:Aluminum au0y,die—casting,the simulation an d an alysis of casting system
《低压铸造铝合金车轮主要缺陷分析与控制》范文

《低压铸造铝合金车轮主要缺陷分析与控制》篇一一、引言低压铸造铝合金车轮以其优越的力学性能和外观品质在汽车行业中广泛应用。
然而,在生产过程中,由于多种因素的影响,可能会出现一些主要缺陷,这些缺陷不仅影响产品的性能,还可能对车辆的安全性和使用寿命产生不良影响。
因此,对低压铸造铝合金车轮的主要缺陷进行分析和控制显得尤为重要。
本文旨在探讨低压铸造铝合金车轮的主要缺陷及其控制措施,以提高产品质量和降低生产成本。
二、低压铸造铝合金车轮主要缺陷分析1. 气泡和气孔气泡和气孔是低压铸造铝合金车轮常见的缺陷之一。
这些缺陷主要是由于熔炼过程中气体未充分排出或熔体中含气量过高所导致。
气泡和气孔的存在会降低车轮的强度和耐腐蚀性,严重时可能导致车轮在使用过程中出现断裂等问题。
2. 轮毂与轮辐结合处不紧密轮毂与轮辐结合处不紧密是低压铸造铝合金车轮的另一个常见缺陷。
这主要是由于模具设计不合理、铸造工艺参数设置不当或铸件在凝固过程中受到外部振动等因素导致。
这一缺陷会影响车轮的整体性能,严重时可能导致轮毂与轮辐分离。
3. 表面质量差表面质量差主要表现在车轮表面出现砂眼、夹杂物、划痕等问题。
这主要是由于熔炼过程中杂质未充分去除、模具表面粗糙度不足或铸件在凝固过程中受到外力等因素导致。
表面质量差会严重影响车轮的外观品质,降低其市场竞争力。
三、低压铸造铝合金车轮缺陷控制措施1. 优化熔炼工艺为减少气泡和气孔等缺陷,应优化熔炼工艺。
具体措施包括控制熔体中的含气量、调整熔炼温度和速度、保持炉内气氛的稳定性等。
此外,还可以通过加入适当的合金元素和细化晶粒等方法提高熔体的流动性,从而减少气泡和气孔的产生。
2. 改进模具设计及制造工艺为解决轮毂与轮辐结合处不紧密的问题,需要改进模具设计及制造工艺。
首先,应确保模具设计合理、尺寸精确;其次,在制造过程中,应控制好模具的表面粗糙度、热处理工艺等;最后,应采取防震措施,减少铸件在凝固过程中受到的外部振动。
新能源汽车铝合金铸造件开发的质量管理
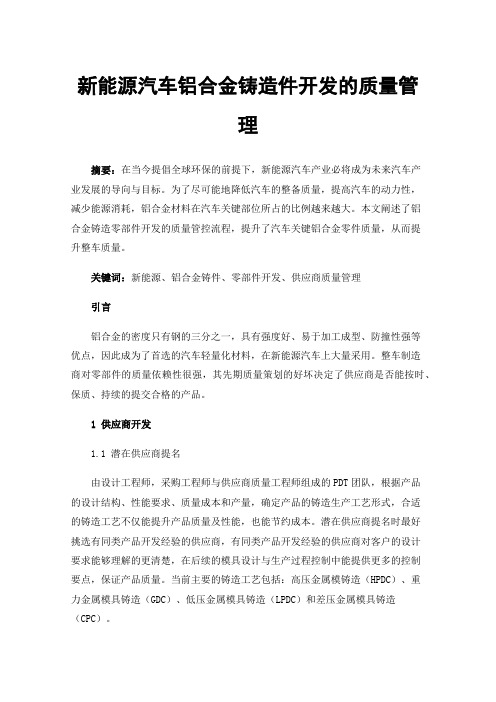
新能源汽车铝合金铸造件开发的质量管理摘要:在当今提倡全球环保的前提下,新能源汽车产业必将成为未来汽车产业发展的导向与目标。
为了尽可能地降低汽车的整备质量,提高汽车的动力性,减少能源消耗,铝合金材料在汽车关键部位所占的比例越来越大。
本文阐述了铝合金铸造零部件开发的质量管控流程,提升了汽车关键铝合金零件质量,从而提升整车质量。
关键词:新能源、铝合金铸件、零部件开发、供应商质量管理引言铝合金的密度只有钢的三分之一,具有强度好、易于加工成型、防撞性强等优点,因此成为了首选的汽车轻量化材料,在新能源汽车上大量采用。
整车制造商对零部件的质量依赖性很强,其先期质量策划的好坏决定了供应商是否能按时、保质、持续的提交合格的产品。
1供应商开发1.1 潜在供应商提名由设计工程师,采购工程师与供应商质量工程师组成的PDT团队,根据产品的设计结构、性能要求、质量成本和产量,确定产品的铸造生产工艺形式,合适的铸造工艺不仅能提升产品质量及性能,也能节约成本。
潜在供应商提名时最好挑选有同类产品开发经验的供应商,有同类产品开发经验的供应商对客户的设计要求能够理解的更清楚,在后续的模具设计与生产过程控制中能提供更多的控制要点,保证产品质量。
当前主要的铸造工艺包括:高压金属模铸造(HPDC)、重力金属模具铸造(GDC)、低压金属模具铸造(LPDC)和差压金属模具铸造(CPC)。
通常而言,采购部门需要根据产品开发需求,提名至少三家符合PDT小组确定的产品生产铸造工艺要求的供应商,并取得提名潜在供应商的相关资料,提交的资料要求包含生产规模、财务状况、体系认证、质量管理、技术力量、主要产品、生产设备、测量设备等。
由于铸造行业属于高耗能产业,在当前环境保护要求比较严格的情况下,环境保护及应急计划是必须要考虑的重点问题。
1.2 潜在供应商审核潜在供应商提名后,由供应商质量工程师会同设计工程师、采购工程师对潜在供应商进行准入审核。
铝合金铸件由于生产工序多,过程变量多,设备要求高等特点,而被美国汽车工业行动集团(AIAG)定义为特殊工艺,并开发了《铸造评估过程CQI-27:Special Process:Casting System Assessment(CSA)》。
铝合金压铸件缺陷的产生与控制分析
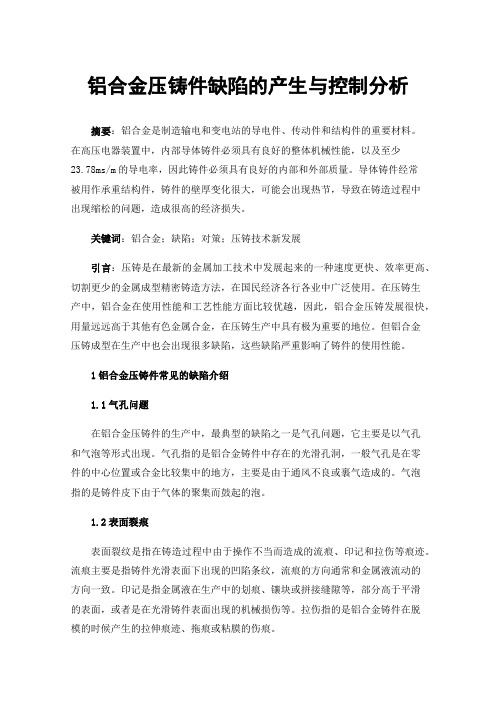
铝合金压铸件缺陷的产生与控制分析摘要:铝合金是制造输电和变电站的导电件、传动件和结构件的重要材料。
在高压电器装置中,内部导体铸件必须具有良好的整体机械性能,以及至少23.78ms/m的导电率,因此铸件必须具有良好的内部和外部质量。
导体铸件经常被用作承重结构件,铸件的壁厚变化很大,可能会出现热节,导致在铸造过程中出现缩松的问题,造成很高的经济损失。
关键词:铝合金;缺陷;对策;压铸技术新发展引言:压铸是在最新的金属加工技术中发展起来的一种速度更快、效率更高、切割更少的金属成型精密铸造方法,在国民经济各行各业中广泛使用。
在压铸生产中,铝合金在使用性能和工艺性能方面比较优越,因此,铝合金压铸发展很快,用量远远高于其他有色金属合金,在压铸生产中具有极为重要的地位。
但铝合金压铸成型在生产中也会出现很多缺陷,这些缺陷严重影响了铸件的使用性能。
1铝合金压铸件常见的缺陷介绍1.1气孔问题在铝合金压铸件的生产中,最典型的缺陷之一是气孔问题,它主要是以气孔和气泡等形式出现。
气孔指的是铝合金铸件中存在的光滑孔洞,一般气孔是在零件的中心位置或合金比较集中的地方,主要是由于通风不良或裹气造成的。
气泡指的是铸件皮下由于气体的聚集而鼓起的泡。
1.2表面裂痕表面裂纹是指在铸造过程中由于操作不当而造成的流痕、印记和拉伤等痕迹。
流痕主要是指铸件光滑表面下出现的凹陷条纹,流痕的方向通常和金属液流动的方向一致。
印记是指金属液在生产中的划痕、镶块或拼接缝隙等,部分高于平滑的表面,或者是在光滑铸件表面出现的机械损伤等。
拉伤指的是铝合金铸件在脱模的时候产生的拉伸痕迹、拖痕或粘膜的伤痕。
1.3缩孔缩孔指在铝合金铸件表层出现不均匀的粗糙孔洞。
通常来说,气孔也发生在收缩区。
1.4飞边飞边主要是指压铸铝合金铸件生产过程中出现铝料溢出从而产生薄片。
当铝合金铸件中出现飞边时,会严重影响零件的性能、外观和尺寸[1]。
2铝合金压铸件性能缺陷形成的原因与控制策略2.1气孔缺陷形成的原因与控制方法当铝合金在进行压铸时,由于液态金属内含有许多气体。
铝合金压铸件缺陷的产生与控制探讨
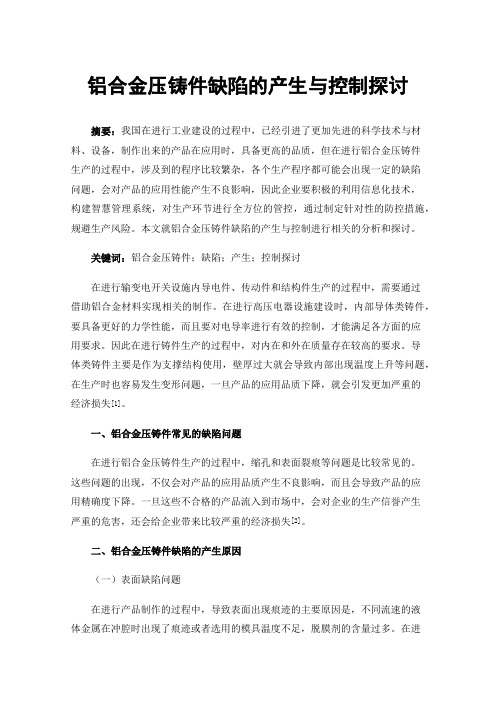
铝合金压铸件缺陷的产生与控制探讨摘要:我国在进行工业建设的过程中,已经引进了更加先进的科学技术与材料、设备,制作出来的产品在应用时,具备更高的品质,但在进行铝合金压铸件生产的过程中,涉及到的程序比较繁杂,各个生产程序都可能会出现一定的缺陷问题,会对产品的应用性能产生不良影响,因此企业要积极的利用信息化技术,构建智慧管理系统,对生产环节进行全方位的管控,通过制定针对性的防控措施,规避生产风险。
本文就铝合金压铸件缺陷的产生与控制进行相关的分析和探讨。
关键词:铝合金压铸件;缺陷;产生;控制探讨在进行输变电开关设施内导电件、传动件和结构件生产的过程中,需要通过借助铝合金材料实现相关的制作。
在进行高压电器设施建设时,内部导体类铸件,要具备更好的力学性能,而且要对电导率进行有效的控制,才能满足各方面的应用要求。
因此在进行铸件生产的过程中,对内在和外在质量存在较高的要求。
导体类铸件主要是作为支撑结构使用,壁厚过大就会导致内部出现温度上升等问题,在生产时也容易发生变形问题,一旦产品的应用品质下降,就会引发更加严重的经济损失[1]。
一、铝合金压铸件常见的缺陷问题在进行铝合金压铸件生产的过程中,缩孔和表面裂痕等问题是比较常见的。
这些问题的出现,不仅会对产品的应用品质产生不良影响,而且会导致产品的应用精确度下降。
一旦这些不合格的产品流入到市场中,会对企业的生产信誉产生严重的危害,还会给企业带来比较严重的经济损失[2]。
二、铝合金压铸件缺陷的产生原因(一)表面缺陷问题在进行产品制作的过程中,导致表面出现痕迹的主要原因是,不同流速的液体金属在冲腔时出现了痕迹或者选用的模具温度不足,脱膜剂的含量过多。
在进行生产的过程中,模具和铸件出现了比较严重的摩擦和碰撞等问题,也会引发表面缺陷。
在进行构件生产的过程中,表面可能会出现一定的擦伤问题,这是因为脱模的斜度不足,型腔的表面干燥度比较大,在进行处理时,作业速度过快引发的[3]。
(二)缩孔缺陷问题这项问题的出现是因为在进行冷凝处理时,构件内部的补偿不足引发的。
铝合金压铸件检验标准

铝合金压铸件检验标准铝合金压铸件是制造中常用的工业零件,广泛应用于汽车、电子、仪器仪表、电力设备等行业。
为了确保铝合金压铸件的质量,需要进行严格的检验。
铝合金压铸件的检验标准主要包括外观检验、尺寸检验、力学性能检验、化学成分检验和物理性能检验等方面。
首先,外观检验是铝合金压铸件检验中的重要环节。
主要包括铸件表面的缺陷、气孔、砂眼、夹渣、裂纹、毛边等的检查。
检查时可采用肉眼观察、放大镜观察和显微镜观察等方法,以判断铸件表面的质量是否符合要求。
其次,尺寸检验是铝合金压铸件检验中的另一个重要环节。
通过测量铸件的尺寸,检查其与设计图纸的偏差,以确定铸件的尺寸是否合格。
这包括铸件的长度、宽度、厚度、直径等方面的尺寸,可通过量具、千分尺、投影仪等设备进行测量。
第三,力学性能检验是评价铝合金压铸件材料强度和韧性的重要手段。
常用的力学性能检验项目包括抗拉强度、屈服强度、延伸率、缩颈率等。
这些检验项目能够客观地评价铝合金压铸件在正常使用条件下的受力性能。
化学成分检验是验证铝合金压铸件化学成分是否符合要求的关键环节。
常用的化学成分检验项目包括铝合金中各元素的含量、铝合金成分的比例、含铁、氧化物等杂质的含量。
这些检验项目能够判断铝合金的成分是否与设计要求相一致。
最后,物理性能检验是研究铝合金压铸件热处理、疲劳寿命、抗磨性等性能的重要环节。
物理性能检验项目包括热处理效果的测定、疲劳试验、硬度测试、摩擦磨损测试等。
这些检验项目能够评价铝合金压铸件在特定工况下的耐磨性、耐热性和疲劳寿命等重要性能。
总之,铝合金压铸件的检验标准涉及外观、尺寸、力学性能、化学成分和物理性能等多个方面。
通过严格的检验,可以确保铝合金压铸件符合要求,并保证其在使用中具有良好的性能和可靠性。
浅谈压铸汽车零件质量控制管理

浅谈压铸汽车零件质量控制管理摘要:本文阐述了压铸汽车零件质量控制的重要性,对压铸汽车零件存在的问题进行说明,做出压铸汽车零件质量控制措施的分析,希望对我国压铸汽车零件质量控制的发展有所帮助。
关键词:压铸汽车;零件;质量控制一、压铸汽车零件质量控制的重要性压铸属于铸造工艺的一种,是指将金属材料高温加热融化成为液态或者半液态,在压力而非重力作用下,以较高的速度快速填充至模具型腔,并在保压下成型凝固,最后脱模从而获得铸件的方法。
压铸工艺属于金属热加工成型技术,其技术较为先进,且生产效率高,材料利用率高,且一般来说废料可以循环使用,产品由于高压成型,精度高、强度高以及铸造缺陷均优于其它铸造工艺。
常用的有色金属压铸材料有很多,典型的有铝合金、锌合金、镁合金、铜合金,其中由于铝合金材料的优越性能、相对低廉的价格以及较为简单的切削加工性能,因此产量最大且应用最为广泛。
由于用这种方法生产产品具有生产效率高,工序简单,铸件公差等级较高,表面粗糙度好,机械强度大,可以省去大量的机械加工工序和设备,节约原材料等优点,所以现已成为我国铸造业中的一个重要组成部分。
压铸工艺是将压铸机、压铸模和合金三大要素有机地组合而加以综合运用的过程。
而压铸时金属按填充型腔的过程,是将压力、速度、温度以及时间等工艺因素得到统一的过程。
同时,这些工艺因素又相互影响,相互制约,并且相辅相成。
只有正确选择和调整这些因素,使之协调一致,才能获得预期的结果。
因此,在压铸过程中不仅要重视铸件结构的工艺性,压铸模的先进性,压铸机性能和结构优良性,压铸合金选用的适应性和熔炼工艺的规范性;更应重视压力、温度和时间等工艺参数对铸件质量的重要作用。
在压铸过程中应重视对这些参数进行有效的控制。
二、压铸汽车零件存在的问题压铸件缺陷按产生部位和性质分类可分为:表面缺陷、内部缺陷、形状和尺寸缺陷、成分和性能缺陷、基体不连贯缺陷。
1.表面缺陷。
指压铸件表面上存在的瑕疵,分类有表面流痕和花纹、网状毛刺及印痕、飞边、缩陷(凹陷)、粘模拉伤、划(碰)伤。
汽车铝合金缸盖铸件缺陷分析及控制

汽车铝合金缸盖铸件缺陷分析及控制汽车铝合金缸盖铸件是汽车发动机中不可或缺的部分,也是应用较多的铸件之一,它的质量对整个发动机的性能和寿命都有着至关重要的影响。
然而,在制造过程中难免会出现各种缺陷,如气孔、夹渣、疏松、细纹、裂纹等,这些缺陷的存在会直接影响铸件的质量,导致发动机性能不稳定,寿命缩短,生产成本和安全隐患增加,因此,汽车铝合金缸盖铸件缺陷的分析和控制非常重要。
1. 汽车铝合金缸盖铸件缺陷的分类及原因汽车铝合金缸盖铸件的主要缺陷包括气孔、夹渣、疏松、细纹、裂纹等。
其中,气孔是其中最常见的缺陷,它是由于铝液在冷却过程中所排放的气体未完全排出而形成的;夹渣是铝液在浇注过程中受到外界杂质的污染,造成的金属夹杂物;疏松是由于铝液凝固不充分,形成的孔洞和空隙;细纹是由于内应力过大,超过了材料的承受极限而造成的微裂纹;裂纹是铸件在使用或运输过程中因外力的作用而出现的断裂现象。
这些缺陷的产生原因,主要有以下几点:(1)铝液温度不均匀:铝液温度不均匀、过热或过冷都会导致铸件缺陷,因此,在铸造过程中必须保证铝液温度的均匀和稳定。
(2)铅模温度控制不当:铅模的温度对铸件质量影响很大,如果温度过高或过低,都会导致铸件出现缺陷,因此,在铸造过程中需要精确控制铅模的温度。
(3)浇注速度过快或过慢:浇注速度过快或过慢都会影响铸件的质量,因此,在铸造过程中需要合理控制浇注速度。
(4)浇注压力不足:浇注压力不足会使铝液中的气体不能完全排出,从而导致铸件出现气孔等缺陷。
2. 汽车铝合金缸盖铸件缺陷的控制方法为了减少和控制汽车铝合金缸盖铸件的缺陷,需要采取以下一些控制方法:(1)铸造工艺控制:必须确保铸造过程中铝液温度均匀和稳定,避免浇注速度过快或过慢,浇注压力不足等问题的出现,对每个生产环节都进行质量控制,避免形成气泡和夹杂物等物质缺陷。
(2)铅模温度控制:铅模的温度控制非常重要,必须保证温度稳定,避免过高或过低,以免出现疏松等缺陷。
- 1、下载文档前请自行甄别文档内容的完整性,平台不提供额外的编辑、内容补充、找答案等附加服务。
- 2、"仅部分预览"的文档,不可在线预览部分如存在完整性等问题,可反馈申请退款(可完整预览的文档不适用该条件!)。
- 3、如文档侵犯您的权益,请联系客服反馈,我们会尽快为您处理(人工客服工作时间:9:00-18:30)。
试论汽车铝合金压铸件质量的综合诊断和控制
随着竞技和科学技术的不断发展,人们生活水平的不断提高,对汽车的质量和实用性给予更高要求。
为了保证汽车的良好使用性能,保证汽车的实际应用性,提高汽车设计工艺和质量。
文章主要就试论汽车铝合金压铸件质量的综合诊断和控制展开分析和研究,来为汽车的制造和设计人员提供有效材料,促进汽车制造业的发展。
标签:汽车铝合金;压铸件质量;综合诊断和控制;分析研究
前言
对汽车铝合金压铸件质量的综合诊断和控制弊端进行分析和研究,发现其存在以下弊端和缺陷。
对于汽车铝合金压铸件汽车缸部环节较大,特别是缸体的头盖位置占据较大空间,结构较为繁琐。
其加工过的环节和缸面,一些部分不可以有孔和洞的存在,严重影响了压铸件的质量。
其次,由于外部购买的元件和材料、操作弊端等等,也为汽车压铸件带来质量影响。
为了提高汽车压铸件的质量,要增加对上述弊端的关注度,完善工艺设计环节和孔洞弊端。
1 汽车铝合金压铸件质量的综合诊断和控制弊端阐述
1.1 诊断缺陷阐述
对于汽车铝合金压铸件整体来说,其汽车缸部环节较大,特别是缸体的头盖位置占据较大空间,结构较为繁琐。
其加工过的环节和缸面,一些部分不可以由孔和洞的存在。
对于那些允许孔和洞存在的缸面,孔和洞的分布较为扩散,对于尺度大小具有严格规范和要求。
对于缸盖环节来说,其凸轮轴位置伴有探伤现象,在进行加工后其孔洞的大小要满足监测的要求,符合监测的最低标准。
对于这一形式的元件来说,为设计作业和生产工作带来极大难度,严重影响了设计效率和生产效率。
铸件的技术和工艺无法全面顾及到整个铸件的不同环节和部位,对于生产环节和工艺设计环节的可调和性较小。
一些孔壁伴有光滑特征,孔壁的深度较大,伴有气孔问题产生。
其次,也有一些孔洞把气孔与缩孔关联在一起等等弊端[1]。
1.2 工艺综合诊断和分析和图像仿真分析
外部购买的元件和材料、操作弊端、工艺设计缓解、机械装置是实际应用性等等,都和汽车铸件的安全性具有极大影响,带来质量的变化,严重者会带来铸件的报废。
上述这些因素都具有可变性特点,进而为铸件带来的质量影响较大,任何一个环节发生变化,都会给铸件质量带来波动。
对于外部购买的元件和材料、操作弊端、工艺设计缓解、机械装置是实际应用性等等带来的铸件质量的变化,不易发现其主要影响原因。
面对这一形势,需要增加对铸件设计和工艺环节进行持续性的跟踪和调查。
首先要对不同铸件的生产日期进行观察和分析,建立合理
化的时序安排,建立铸件的质量为导向目标,对下述几个缓解进行监测和持续观察。
包括对铸件的原材料、辅佐材料、熔炼环节、铸件的设计和工艺生产参數、铸件的监测质量等等环节进行综合监测和跟踪[2]。
对于图像仿真分析时铸件其主要缺陷体现在齿轮室中,对于这一缺陷的影响因素主要是气体变化和收缩带来的影响,为孔洞带来极大缺陷。
对于铸件来说,其气体的产生主要是从溶体内部获得,从脱模剂中获取的气体。
从铸件过程中意外得到的气体。
在溶体种产生的气体与铸件的材料种类和性质具有紧密联系,和铸件的熔炼技术具有紧密联系[3]。
2 优化完善举措
2.1 图像仿真管理和完善
对于铸件来说,其气体的产生主要是从溶体内部获得,从脱模剂中获取的气体。
从铸件过程中意外得到的气体。
在溶体种产生的气體与铸件的材料种类和性质具有紧密联系,和铸件的熔炼技术具有紧密联系[4]。
脱模剂产生的气体,和铸件工艺设计环节和铸件的压制环节模型的选择具有紧密联系。
对于这一铸件发展弊端,可以对利用对于铸件熔炼技术的调整,利用对喷涂技术的调整,来进行完善和优化。
对于铸件在压制环节带来的气体弊端面和金属液体的运作形式具有紧密联系。
对于铸件的伸缩弊端,和铸件的温度高低和凝固环节具有紧密。
在明确好铸件的设计方案后,便可以展开浇道的设计和配置、对排气线路和溢流设备机进行设置、对铸件模具的温度高低进行设置、对压件的系数进行设置。
在对压件的系数和参数进行设计和配置时,要考虑到铸件体内的金属液体流动形式,考虑液体的凝固化,保证缩孔数值最小化,保证其限度最小化。
进而,在这一环节可以利用图像仿真来进行分析。
图像仿真这一方法是当下对铸件进行规律分析和了解其充形的主要方法,为铸件的孔洞弊端形成的原由给予科学依据。
把正时此轮模型进行变化,把其展现为三角化形式,进而给出其技术工艺的仿真系统,对STL文件进行格式辨别。
在进行辨别后,利用Msgmasoft软件,来对网络展开划分作业。
把铸件与浇冒体系给予其十万个网络节点。
在经过对Msgmasoft软件进行深入研究和分析,对其展开实际应用后,发现利用Msgmasoft软件具备实际应用性,可以为铸件工艺模具进行改革和创新,为铸件的模具和工艺的设计奠定理论基础。
2.2 增加对溶体气体的管理
正时齿轮其在进行熔炼作业时,齿轮室的炉料的走出包括百分之五十的铝淀与百分之三十九的回炉。
因为其在回炉作业时,水分和一些其它物质会不断增加,进而会增加气体的含量,进而在材料放入炉中前期,要把其及时进行处理和管理,减少熔体元素含量,为其加除气液体,曾增加对气体含量的监测和观察,与此同时,也要对工艺进行改变和优化,完善喷吹技术,对喷吹线路进行调整,保证除气作业高效进行,提高除气效率。
保证一百克的铝物质中,其气体的含量在0.2ml 上下。
2.3 增加工艺参数的合理性,优化铸件条件
对于工艺参数的合理性,首先,要依据监测的结果,把铸件可以带来影响的工艺参数和质量关系进行分析和研究,在不改变铸件条件基础上,来增加铸件的质量。
为了确保工艺参数的合理性,可以在以压射环节,增加铸件的紧实度,环节其充型卷气压力等等方法,来增加铸件工艺的合理性。
其次,也要增加对铸件条件的关注度,保证其工艺的合理性运作,增加对孔洞的关注度,对浇道大小进行调整,在液体交汇环节增设排气管道。
在铸件的实际生产和设计活动中,要增加对铸件孔洞的观察,看其是否存在缺陷和弊端,观察其大小和扩散范围。
对铸件进行这一观察,主要是监测铸件的实际应用性,看其是否需要被报废和更新。
对铸件的缺陷环节进行截取,把其缺陷部位进行再次加工,保证其达到标准铸件要求,增加其实际应用性。
对加工完毕的铸件也要注意对其进行孔壁的观察,看其孔壁是否粗糙,对于较为粗糙的孔壁,其主要呈现为树枝性质,在利用显微镜进行观察和分析时,可以发其底部连贯性较好,伴有孔洞的缩小和松动现象。
3 结束语
对汽车铝合金压铸件质量弊端进行管理,首先要增加对溶体气体的管理,对工艺进行改变和优化,增加工艺参数的合理性,优化铸件条件,对铸件进行监测和观察,看其是否需要被报废和更新。
把其缺陷部位进行再次加工,保证其达到标准铸件要求。
对于图像仿真分析正时性质的铸件其主要缺陷,可以利用对于铸件熔炼技术的调整,利用对喷涂技术的调整。
参考文献
[1]吴正红,徐冰.汽车铝合金压铸件质量的综合诊断和控制[J].吉林工程技术师范学院学报,2008,01:64-66.
[2]黄晓锋,田载友,朱凯,等.压铸铝合金及压铸技术的研究进展[J].热加工工艺,2008,17:137-141.
[3]姜银方,徐金成,朱元右,等.镁合金压铸技术的几个主要问题及其应用前景[J].中国铸造装备与技术,2004,01:7-11.
[4]吴殿杰.国外八十年代汽车铸造技术发展状况及九十年代趋势[J].铸造设备研究,1994,06:1-11.。