19.型腔的数控加工
《数控特种加工技术》复习题集
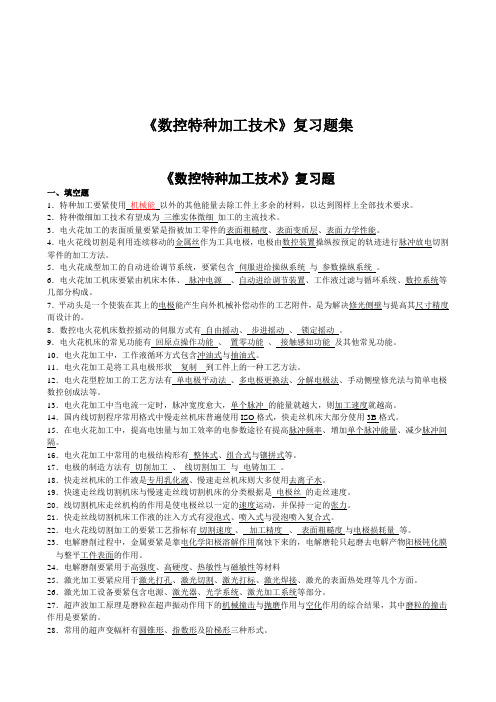
《数控特种加工技术》复习题集《数控特种加工技术》复习题一、填空题1.特种加工要紧使用机械能以外的其他能量去除工件上多余的材料,以达到图样上全部技术要求。
2.特种微细加工技术有望成为三维实体微细加工的主流技术。
3.电火花加工的表面质量要紧是指被加工零件的表面粗糙度、表面变质层、表面力学性能。
4.电火花线切割是利用连续移动的金属丝作为工具电极,电极由数控装置操纵按预定的轨迹进行脉冲放电切割零件的加工方法。
5.电火花成型加工的自动进给调节系统,要紧包含伺服进给操纵系统与参数操纵系统。
6.电火花加工机床要紧由机床本体、脉冲电源、自动进给调节装置、工作液过滤与循环系统、数控系统等几部分构成。
7.平动头是一个使装在其上的电极能产生向外机械补偿动作的工艺附件,是为解决修光侧壁与提高其尺寸精度而设计的。
8.数控电火花机床数控摇动的伺服方式有自由摇动、步进摇动、锁定摇动。
9.电火花机床的常见功能有回原点操作功能、置零功能、接触感知功能及其他常见功能。
10.电火花加工中,工作液循环方式包含冲油式与抽油式。
11.电火花加工是将工具电极形状复制到工件上的一种工艺方法。
12.电火花型腔加工的工艺方法有单电极平动法、多电极更换法、分解电极法、手动侧壁修光法与简单电极数控创成法等。
13.电火花加工中当电流一定时,脉冲宽度愈大,单个脉冲的能量就越大,则加工速度就越高。
14.国内线切割程序常用格式中慢走丝机床普遍使用ISO格式,快走丝机床大部分使用3B格式。
15.在电火花加工中,提高电蚀量与加工效率的电参数途径有提高脉冲频率、增加单个脉冲能量、减少脉冲间隔。
16.电火花加工中常用的电极结构形有整体式、组合式与镶拼式等。
17.电极的制造方法有切削加工、线切割加工与电铸加工。
18.快走丝机床的工作液是专用乳化液、慢速走丝机床则大多使用去离子水。
19.快速走丝线切割机床与慢速走丝线切割机床的分类根据是电极丝的走丝速度。
20.线切割机床走丝机构的作用是使电极丝以一定的速度运动,并保持一定的张力。
模具制造工艺课后答案

樓具制造工艺课后答案【篇 模具制造工艺 复习题(有答案 )】火花加工又 称为放电加工或 电蚀加工,是一种利用电热能量进行加工的方法。
2、在电火花加工过程中,电极和工件之间必须保持一定的距离以形 成放电 间隙。
7、 在常用电极材料中,损耗最大的是 黄铜 电极材料。
8、 电极的结构形式可分为整体式电极、镶拼式电极和组合式电极三 种,应 根据电极外形尺寸、复杂程度等因素来选取。
9、用电火花加工型孔时,电极的轮廓尺寸应比所加工的型孔尺寸均匀的缩 小一个放电间隙。
10、电规准是指电火花加工过程中的一组电参数,包括电流、电压、 脉冲宽度和脉冲间隔等。
11 、型孔的电火花加工工艺方法主要有单电极平动法、多电极更换法和 分解电极法三种方法。
12、 在电火花型孔加工中,有粗规准、中规准 和 精规准三种电 规准,根 据加工需要,每一种又分为几个档次。
13、 在电火花加工中,为了使脉冲放电能持续进行,必须靠 电极和 工件来 保证放电间隙。
14、 电火花加工与电火花线切割加工的加工原理是相同的,而加工 方式是 不同的。
15、 电火花加工采用的电极材料有石墨、紫铜和 铸铁(任写三种)。
16、 快走丝线切割的走丝速度一般为8-10m/s ,慢走丝线切割的走丝速度 —般为 3-12m/min 。
17、 电解加工时利用金属在电解液中产生阳极溶解的电化学反应,将工件 加工成形的一种方法。
18、 电解磨削是将 电解作用和机械磨削相结合的一种新的加工方法。
19、 型腔的冷挤压加工方式可以分为敞开式冷挤压 和 封闭式冷挤 压两 种。
3、 在电火花一次脉冲放电结束后,应间隔一段时间,使放电通道的 子复合成中性粒子,这个过程称为消电离。
4、 电火花加工时,工具电极的材料硬度不必比工件材料硬度高5、 在电火花加工过程中,工具电极和工件都受到电腐蚀的作用,但 速度却不一样,这种现象称为极性效应。
6、 在电火花加工冲裁模过程中,保证配合间隙的电火花加工方法有 合法、修配凸模法、混合法和二次电极法四种。
多工序数控机床操作调整工(高级)理论试卷(B)张家港市环宇职业培训学校职业技能等级鉴定复习资料
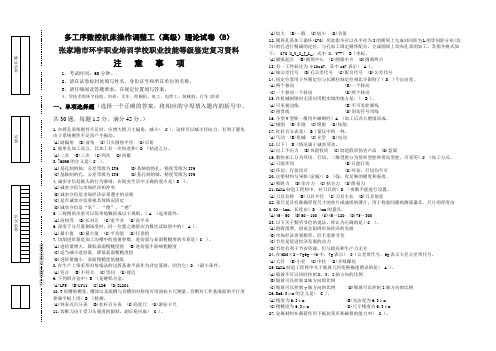
多工序数控机床操作调整工(高级)理论试卷(B ) 张家港市环宇职业培训学校职业技能等级鉴定复习资料注 意 事 项1、考试时间:60分钟。
2、请在试卷标封处填写姓名、身份证号和所在单位的名称。
3、请仔细阅读答题要求,在规定位置填写答案。
4、学技术到环宇技校,培训:叉车、挖掘机、电工、电焊工、装载机、行车\培训一、单项选择题(选择一个正确的答案,将相应的字母填入题内的括号中。
共30题,每题1.5分,满分45分。
)1.在镗孔系统刚性不足时,应增大镗刀主偏角,减小( C ),这样可以减小径向力,有利于避免由于系统刚性不足而产生振动。
(A)副偏角 (B)前角 (C)刀尖圆角半径 (D)后角2.就单孔加工而言,其加工有一次钻进和( D )钻进之分。
(A)二次 (B)三次 (C)四次 (D)间歇3.?60K9的含义是( C )。
(A)基孔制的轴,公差等级为IT9 (B)基轴制的孔,精度等级为IT9 (C)基轴制的孔,公差等级为IT9 (D)基孔制的轴,精度等级为IT9 4.诚实守信是做人的行为准则,在现实生活中正确的观点是( B )。
(A)诚实守信与市场经济相冲突(B)诚实守信是市场经济必须遵守的法则 (C)是否诚实守信要视具体情况而定 (D)诚实守信是“呆”、“傻”、“憨”5.三视图的关系可以简单地概括成以下规则,( A )选项除外。
(A)高相等 (B)长对正 (C)宽平齐 (D)高平齐6.深度千分尺量测深度时,同一位置之测值应为数次读取值中的( A )。
(A)最小值 (B)最大值 (C)平均值 (D)任意值7.切削进给量是加工沟槽中的重要参数.进给量与表面粗糙度的关系是( C )。
(A)进给量增大,降低表面粗糙度值 (B)进给量不影响粗糙度 (C)适当减小进给量,降低表面粗糙度值 (D)进给量越小,表面粗糙度值越低8.在生产上常采用对角线法的过渡基准平面作为评定基准,因为它( D )最小条件。
(A)符合 (B)不符合 (C)等同 (D)接近 9.下列铝合金中( B )是硬铝合金。
《数控加工工艺》习题与参考答案
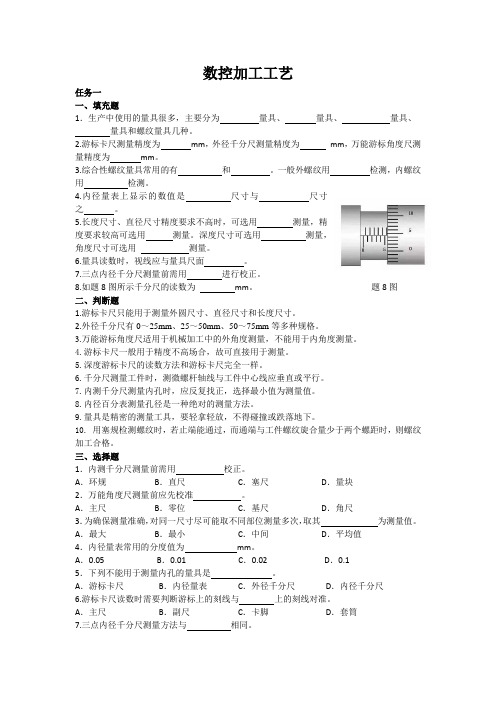
数控加工工艺任务一一、填充题1.生产中使用的量具很多,主要分为量具、量具、量具、量具和螺纹量具几种。
2.游标卡尺测量精度为mm,外径千分尺测量精度为mm,万能游标角度尺测量精度为mm。
3.综合性螺纹量具常用的有和。
一般外螺纹用检测,内螺纹用检测。
4.内径量表上显示的数值是尺寸与尺寸之。
5.长度尺寸、直径尺寸精度要求不高时,可选用测量,精度要求较高可选用测量。
深度尺寸可选用测量,角度尺寸可选用测量。
6.量具读数时,视线应与量具尺面。
7.三点内径千分尺测量前需用进行校正。
8.如题8图所示千分尺的读数为mm。
题8图二、判断题1.游标卡尺只能用于测量外圆尺寸、直径尺寸和长度尺寸。
2.外径千分尺有0~25mm、25~50mm、50~75mm等多种规格。
3.万能游标角度尺适用于机械加工中的外角度测量,不能用于内角度测量。
4.游标卡尺一般用于精度不高场合,故可直接用于测量。
5.深度游标卡尺的读数方法和游标卡尺完全一样。
6.千分尺测量工件时,测微螺杆轴线与工件中心线应垂直或平行。
7.内测千分尺测量内孔时,应反复找正,选择最小值为测量值。
8.内径百分表测量孔径是一种绝对的测量方法。
9.量具是精密的测量工具,要轻拿轻放,不得碰撞或跌落地下。
10. 用塞规检测螺纹时,若止端能通过,而通端与工件螺纹旋合量少于两个螺距时,则螺纹加工合格。
三、选择题1.内测千分尺测量前需用校正。
A.环规B.直尺C.塞尺D.量块2.万能角度尺测量前应先校准。
A.主尺B.零位C.基尺D.角尺3.为确保测量准确,对同一尺寸尽可能取不同部位测量多次,取其为测量值。
A.最大B.最小C.中间D.平均值4.内径量表常用的分度值为mm。
A.0.05 B.0.01 C.0.02D.0.15.下列不能用于测量内孔的量具是。
A.游标卡尺B.内径量表C.外径千分尺D.内径千分尺6.游标卡尺读数时需要判断游标上的刻线与上的刻线对准。
A.主尺B.副尺C.卡脚D.套筒7.三点内径千分尺测量方法与相同。
数控铣床加工中心加工工艺编程与操作轮廓型腔类零件加工

任务1 平面加工
(4)公英制转换指令
G21公制编程单位mm G20英制编程单位in(inch的缩写,1in=25.4mm)
任务1 平面加工
8、与插补有关的指令详解
(1)快速点定位G00(模态指令) 作用:控制刀具以点位控制方式从刀具所设在点快速移
动到指定点。
格式:G00 X-Y- Z-;
式中X、Y、Z的值是终点坐标。当使用增量编程时,为 目标的相对于起始点的增量坐标。
单向多次粗加工 单向多次精加工 双向多次粗加工 双向多次精加工
任务1 平面加工
7、程序初始化指令详解 (1)绝对尺寸指令G90和增量尺寸指令G91
1)绝对编程G90 (默认值)(模态指令)
坐标值以原点作为基准,表示刀具终点的绝对坐标。
2)增量编程G91 (模态指令)
坐标值以刀具起点作为基准,表示刀具终点相对于刀 具起点坐标值的增量值。
(2)刀心轨迹与工件边缘重合——刀齿冲击大,易蹦刃 (3)刀心轨迹在工件边缘外——冲击大,易破损或产生缺口 (4)刀心轨迹在工件边缘与中心线间——最合适
注意:刀心在工件内时铣刀直径选择要适当,避免全齿切削。
任务1 平面加工
5、平面铣削用量
粗加工:刚性、功率、效率
精加工:精度
6、大平面铣削时的走刀路线
任务1 平面加工
相关知识:
1、平面铣削的内容要求
分析平面铣削加工的内容应考虑:加工平 面区域大小,加工面相对基准面的位置;加工 平面的表面粗糙度要求,加工面相对基准面的 定 平面加工
2、平面铣削方法
端铣——立铣刀、端铣刀
周铣——圆柱铣刀 端铣优缺点: (1)平面度好 (2)刚性好,振动小 (3)齿数多,平稳 (4)主刃切削,副刃修光,铣刀使用寿命较长且Ra小 (5)台阶面铣削时效率高
数控加工工艺练习题

随堂考试-数控1、(2分)【单选题】3.尺寸链中,当其他尺寸确定后,新产生的一个环是( )。
A、A.增环B、B.减环C、C.增环或减环D、D.封闭环参考答案:D解析:无2、(2分)【单选题】外圆表面与内孔中心有较高同轴度要求时,常_______反复装夹外圆和内孔。
A、自为基准B、互为基准C、用外圆D、用内孔参考答案:B解析:无3、(2分)【单选题】车床上,刀尖圆弧只有在加工( ) 时才产生加工误差。
A、端面B、外圆柱面C、圆弧D、内圆孔面参考答案:C解析:无4、(2分)【单选题】5.一个工艺尺寸链中有( )个封闭环。
A、A.1B、B.2C、C.3D、D.多参考答案:A解析:无5、(2分)【单选题】薄壁工件在加工时应尽可能采取轴向夹紧的方法,以防止工件产生__A、切向位移B、弹性形变C、径向变形D、轴向变形参考答案:C6、(2分)【单选题】磨削加工中,大部分磨削热A、传给工件B、传给刀具C、传给机床D、被切屑所带走参考答案:D解析:无7、(2分)【单选题】单件小批生产,轴零件中心孔的加工方法为A、车床加工B、专用机床加工C、钳工划后铣床加工参考答案:A解析:无8、(2分)【单选题】工序尺寸的公差一般采用( )分布A、单向B、双向C、对称参考答案:A解析:无9、(2分)【单选题】成批量生产时通常确定加工余量的方法是A、分析计算法B、经验估算法C、查表修正法参考答案:C解析:无10、(2分)【单选题】加工套类零件的定位基准是A、端面B、外圆C、内孔D、外圆或内孔参考答案:D11、(2分)【单选题】35. ( )时,限制进给量的主要因素是加工精度和表面粗糙度。
A、A.端铣B、B.周铣C、C.粗铣D、D.精铣参考答案:D解析:无12、(2分)【单选题】不属于工艺基准的是()。
A、装配基准B、测量基准C、定位基准D、设计基准参考答案:D解析:无13、(2分)【单选题】加工高精度的有色金属外圆表面,常采用的加工路线是()。
复杂部件多轴数控加工智慧树知到期末考试章节课后题库2024年北京电子科技职业学院

复杂部件多轴数控加工智慧树知到期末考试答案章节题库2024年北京电子科技职业学院1.工件坐标系又称编程坐标系,它是用来确定工件几何形体上各要素的位置而设置的坐标系。
()答案:对2.创建几何体,主要是定义加工的几何对象,包括创建机床坐标系(MCS)、安全平面、指定部件几何体、毛坯几何体、切削区域、检查几何体等参数。
()答案:对3.在创建工序时,工序需要指定部件刀路的仿真加工操作,需要指定毛坯根据零件的特点掌握不同的指定方法。
预先指定的部件几何体,不能在多个工序中使用,也可以在创建工序时指定几何体。
()答案:错4.加工四轴零件时,通常将【安全设置选项】,选择圆柱,【指定点】为圆柱侧面的圆心,【指定矢量】选择圆柱的轴线方向。
()答案:对5.手工编程是编程人员直接编写输入数控程序到数控机床中去的方法,手工编程适合零件结构较为复杂,计算量较多的程序编制。
()答案:错6.UG NX是一款功能强大的CAD/ CAM/ CAE软件,涵盖了从概念设计、工业造型设计、三维模型设计、分析计算、动态模拟仿真和生产加工产品全过程。
()答案:对7.数控加工对卡具主要有两大要求:一是卡具应具有足够的精度和刚度,二是卡具应有可靠的定位基准。
对吗?()答案:对8.修改CAM软件中的机床坐标系,可以改变刀轨的深度位置。
()答案:对9.3D动态模拟能够以三维实体模式显示动态刀具,切除工件材料的过程,模拟过程非常直观,但播放时不允许用户在窗口中缩放、放大、旋转、移动等细节问题。
()答案:错10.真实的刀具轨迹是由直线和圆弧组成的线段合集近似地取代刀具的理想运动轨迹,实际刀具轨迹与理想轨迹之间不能存在误差。
()答案:错11.所谓多轴数控加工,就是在原有三轴加工的基础上,增加了旋转轴的加工。
对吗?()答案:对12.使用【检查边界】时,可以在指定【检查边界】对话框中设置每条边界的检查余量。
()答案:对13.车铣复合加工分类为{轴向车铣}和{正交车铣}。
CATIA型腔数控加工

第1章型腔的加工 1第1章型腔的加工本章将通过对如图1-1所示的零件进行加工,综合练习CATIA 2.5轴数控铣削加工的编程方法。
该零件是直壁零件,没有拔模角度,因此可以用2.5轴机床进行数控加工。
本例将用到的加工方法有:❑平面铣削❑粗加工❑轮廓铣削❑型腔铣削图1-11.1 设置加工参数打开附带光盘中的“Ch1/EX 1.CATPart”,零件如图1-1所示。
(1)选择Tools→Options命令,弹出Options对话框,选择Machining,选中复选框,如图1-2所示。
然后可以在进入数控加工模块后,同时生成一个用于存放辅助零件的文件夹,可以存放加工毛坯、辅助曲线/曲面等几何元素。
在本书的叙述中,默认选中该复选框。
(2)选择Start→Machining命令,进入数控加工的曲面加工模块。
首先进入这个模块是因为需要在这个模块中调用建立毛坯零件功能来建立毛坯。
进入加工模块后,特征树如图1-3所示。
特征树主要含有3个结点,加工过程结点包括加工零件设置、加工方法和刀路等;加工产品结点包括进行加工的目标零件、毛坯零件和辅助几何元素等;加工资源结点包括用于加工的数控机床和加工刀具等。
在图1-3中,方框处的结点就是选中复选框后所生成的辅助几何结点。
(3)在曲面加工模块中,单击“建立毛坯零件(Creates Rough Stock )”按钮,弹CATIA V5 数控加工应用实例 2出如图1-4所示的Rough Stock Creation对话框,选择目标零件,并在Z max数值框中设置毛坯零件的高度为55mm ,其他参数不变,单击按钮完成。
这样就建立了目标零件的毛坯零件,如图1-5所示,也就是将在毛坯零件的基础上进行加工而形成目标零件。
由此可见,毛坯零件是存放在辅助几何结点中,并由曲面构成的。
(4)选择Start→Machining →命令,进入2.5轴加工模块。
图1-2 图1-3图1-4(5)在特征树的加工过程结点中双击零件加工操作,弹出如图1-6所示的Part Operation对话框,其中可以设置数控加工机床、加工坐标系、加工的目标零件、毛坯零件和安全平面等内容。
数控铣理论题-4

2015年全国职业院校技能大赛(中职组)“数控铣加工技术”赛项理论知识竞赛题(4号)赛区:赛位号:注意事项1.理论知识竞赛总时间:90分钟。
2.请首先按要求在赛卷上填写您的赛位号。
3.请仔细阅读各题目,在规定的位置填写您的答案。
4.不要在试卷上乱写乱画,不要填写无关的内容。
0.1分,共4分)1.精铣平面时,宜选用的加工条件为()。
A、较大切削速度与较大进给速度B、较大切削速度与较小进给速度C、较小切削速度与较大进给速度D、较小切削速度与较小进给速度2.国家标准规定优先选用基孔制配合的原因是()。
A、因为孔比轴难加工B、因为从工艺上讲,应先加工孔,后加工轴C、为了减少定尺寸孔用刀具、量具的规格和数量D、为了减少孔和轴的公差带数量3.普通螺纹的配合精度取决于()。
A、公差等级与基本偏差B、基本偏差与旋合长度C、公差等级、基本偏差和旋合长度D、公差等级和旋合长度4.图纸中技术要求项中“热处理:C45”表示()。
A、淬火硬度HRC45B、退火硬度为HRB450C、正火硬度为HRC45D、调质硬度为HRC455.端铣刀()的主要作用是减小副切削刃与已加工表面的摩擦,其大小将影响副切削刃对已加工表面的修光作用。
A、前角B、后角C、主偏角D、副偏角6.麻花钻直径大于13mm时,刀柄一般做成()。
A、直柄B、两体C、莫氏锥柄D、直柄或锥柄7.通常依据后刀面的磨损尺寸来制定刀具允许磨损的( )A、最大限度B、最小限度C、标准限度D、时间8.刀具剧烈磨损阶段切削力( ) 。
A、缓慢下降B、不变C、急剧上升D、无法确定9.夹紧力通过工件传至( )造成工件变形和定位基准位移。
A、平面B、外平台C、内圆D、支承元件10.( )属于紧固件。
A、T形键和定位销B、螺栓C、定位盘和定位销D、平键和基础角铁11.主轴在转动时若有一定的径向圆跳动,则工件加工后会产生( )的误差。
A、垂直度B、同轴度C、斜度D、粗糙度12.在以下工序顺序安排中,()不是合理的安排。
教师招聘考试机械类(数控方向)试题(附答案)

机械类(数控方向)试题一、填空题(将适当的词语填入空格。
每空1.0分。
满分20分)12.在切削用量中对断屑影响最大的是。
3.球头铣刀的球半径通常 小于 (大于、小于、等于)加工曲面的曲率半径。
45.为了降低切削温度,目前采用的主要方法是切削时冲注切削液。
切削液的作用包括6.退火的目的是改善钢的组织,提高其强度,改善 切削加工性能 。
7.通常在命名或编程时,不论何种机床,都一律假定 工件 静止 刀具 移动。
8.FMS 是指 计算机集成制造系统 ,CIMS 是指 柔性制造系统,CAPP 是指计算机辅助工艺设计。
910.外圆车刀装得低于工件中心时,因切削力方向的变化,会使刀尖强度 降低 ,容易造成 崩刀 现象。
11.在切削平面内测量的车刀角度是 刃倾角 。
二、选择题(选择正确的答案填入题内的括号中。
每题1.0分。
满分25分) 1.标准公差分20级,其中等级最高的是( A )。
A 、IT01 B 、IT0 C 、IT1 D 、IT18 2.零件的机械加工精度主要包括( D )。
A 、机床精度、几何形状精度、相对位置精度 B 、尺寸精度、几何形状精度、装夹精度 C 、尺寸精度、定位精度、相对位置精度D 、尺寸精度、几何形状精度、相对位置精度3.主轴转速n (r/min )与切削速度v (m/min )的关系表达式为( C )。
A 、n = πvD/1000B 、n = 1000/VdC 、v = πnD/1000D 、v= 1000/n D4.刀具材料的硬度必须高于工件的硬度,一般应在60HRC 以上,下列几种常用刀具材料的硬度从低到高排列顺序正确的是( A )。
A 、工具钢、硬质合金、陶瓷、立方氮化硼(CBN )B 、工具钢、硬质合金、立方氮化硼(CBN )、陶瓷C 、硬质合金、工具钢、陶瓷、立方氮化硼(CBN )D 、陶瓷、立方氮化硼(CBN )、工具钢、硬质合金5.车削用量的选择原则是:粗车时,一般( A ),最后确定一个合适的切削速度。
数控技术考试试卷(附答案)

一、填空题(每空1分,共22分)1、按控制运动的方式分类,数控机床可分为点位控制数控机床、点位直线控制数控机床和轮廓控制数控机床等三种。
2、卡盘式数控车床适合车削(3)盘类,而顶尖式数控车床适合车削较长的轴类。
3、当数控装置的程序存储空间较小时,为实现程序的连续执行与加工,常采用(5)DNC或(6)通信输入程序输入方式。
4、数控加工时对刀点设置的原则为:便于数值计算和简化程序编制、(7)易于找正并在加工过程中便于检查、(8) 引起的加工误差小.5、在MC加工时,常用的高性能刀具材料有硬质合金刀具(涂层)、(9) 立方氮化硼刀具和(10)金刚石刀具等。
6、与数控电火花成形加工相比较,数控电火花线切割加工改善的主要两个方面为(11)不用成形电极和(12) 加工效率高(比电火花成形机床操作更方便.7、衡量数控机床可靠性的指标有(13)MTBF和(14)A。
8、数控机床的维修包含(15)日常性维护与保养和(16) 故障维修两方面内容。
9、数控机床的安装调试工作有(17) 准备工作、(18配合工作和(19)组织工作等。
10、数控程序的代码标准常用的有(20)ISO 和(21)EIA 两种,其中应用广泛的为 (22)ISO代码标准。
二、选择题:下列各题的选项中有一个或多个是正确的,请将其代号填入括号中。
(每题2分,共16分)1、在数控加工工序卡中,应包括()等内容。
A.编程原点与对刀点B.编程简要说明C.工艺过程安排D.数控切削用量2、数控车削螺纹时,为保证车出合格的螺纹,应()。
A.增加刀具引入距离 B.不需要刀具引入/引出距离C.增加螺纹长度 D.增加刀具引出距离3、当用于数控机床的调试及对刀时,其工作方式为( ).A.单段 B.手动 C.步进 D.手动攻丝4、对于高度较大且加工表面较多的箱体类零件,一般选用()。
A.立式MC B.卧式MC C.普通数控铣床5、对于中大型加工中心,其换刀方式一般采用()。
数控铣工国家试题库(附答案)
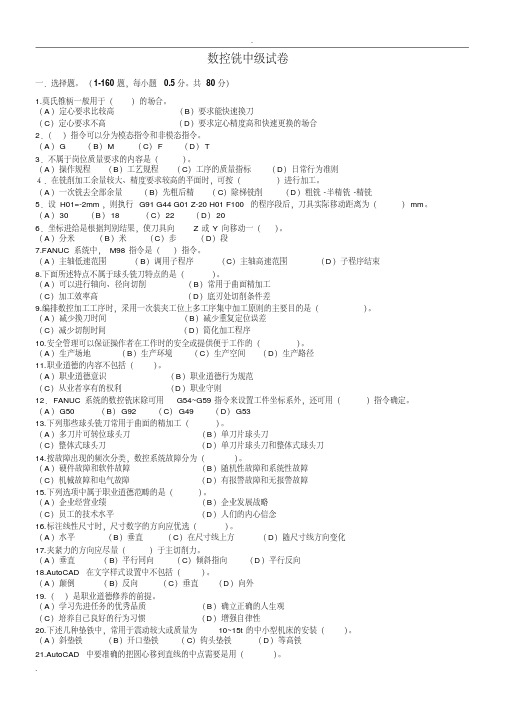
数控铣中级试卷一.选择题。
(1-160题,每小题0.5分。
共80分)1.莫氏锥柄一般用于()的场合。
(A)定心要求比较高(B)要求能快速换刀(C)定心要求不高(D)要求定心精度高和快速更换的场合2.()指令可以分为模态指令和非模态指令。
(A)G (B)M (C)F (D)T3.不属于岗位质量要求的内容是()。
(A)操作规程(B)工艺规程(C)工序的质量指标(D)日常行为准则4.在铣削加工余量较大、精度要求较高的平面时,可按()进行加工。
(A)一次铣去全部余量(B)先粗后精(C)除梯铣削(D)粗铣-半精铣-精铣5.设H01=-2mm,则执行G91 G44 G01 Z-20 H01 F100的程序段后,刀具实际移动距离为()mm。
(A)30 (B)18 (C)22 (D)206.坐标进给是根据判别结果,使刀具向Z或Y向移动一()。
(A)分米(B)米(C)步(D)段7.FANUC系统中,M98指令是()指令。
(A)主轴低速范围(B)调用子程序(C)主轴高速范围(D)子程序结束8.下面所述特点不属于球头铣刀特点的是()。
(A)可以进行轴向、径向切削(B)常用于曲面精加工(C)加工效率高(D)底刃处切削条件差9.编排数控加工工序时,采用一次装夹工位上多工序集中加工原则的主要目的是()。
(A)减少换刀时间(B)减少重复定位误差(C)减少切削时间(D)简化加工程序10.安全管理可以保证操作者在工作时的安全或提供便于工作的()。
(A)生产场地(B)生产环境(C)生产空间(D)生产路径11.职业道德的内容不包括()。
(A)职业道德意识(B)职业道德行为规范(C)从业者享有的权利(D)职业守则12.FANUC系统的数控铣床除可用G54~G59指令来设置工件坐标系外,还可用()指令确定。
(A)G50 (B)G92 (C)G49 (D)G5313.下列那些球头铣刀常用于曲面的精加工()。
(A)多刀片可转位球头刀(B)单刀片球头刀(C)整体式球头刀(D)单刀片球头刀和整体式球头刀14.按故障出现的频次分类,数控系统故障分为()。
模具制造工艺17.型腔的机械加工

5
.01
+0 0
R a 0. 8
8
R40 +00.0 25
25
16 12
4× M8
4
×φ
1
2+
0.0 0
18
Ra 0.8
Ra 0.8
Ra 0.4
18
0.0 0
4+
14
型腔的机械加工
仿形铣削
型
腔
的
铣
仿形靠模和 仿形销
削
加
工
①靠模的形状、尺寸、精度与型腔一至。 可用石膏、木材、塑料、铝合金、铸铁 或钢板等制成。
②考虑受力变形,实际仿形销的尺寸应 稍大于铣刀尺寸。仿形销端头的圆弧半 径应小于靠模型槽的最小圆角半径,仿 形销的斜角应小于靠模型槽的最小斜角。 仿形销要尽可能轻,一般用硬铝、黄铜、 塑料或木材等材料制成。
45钢 两块310mm×210 mm×70 mm锻件( 或钢板)
分型面及垂直侧面
见下表
12
型腔的机械加工
有关计算
型
腔
①计算R14 mm圆心到中心线的距离30.5 mm; ②计算两R14 mm圆心的距离61mm; ③ R14 mm 到R26mm中心的距离60.78mm; ④ 两R40mm圆心的距离36mm;
铣
削
加 仿形铣削特点
工 和应用
仿形销贴靠在靠模表面作进给运动,使铣刀作 同步的仿形运动,加工出与靠模形状和尺寸相 同的曲面.
①各运动; ②随动系统;靠模销始终与靠模表面接触,靠模 使靠模销产生轴线运动,信号通过放大器7驱动 刀具相应的运动.
加工效率高,特别适用于型腔的粗加工。但难 以加工深窄型腔和内清角,对淬硬型腔,一般 淬火前先仿形粗加工,留1~2mm加工余量,淬 火后 削 铣削过程 加 工
数控机床考试试题(附答案)

数控机床技术测试试卷A卷 <附答案)一、填空题 <每空1分,共30分)1、数控机床按伺服系统的控制方式可分为、、。
2、较常见的CNC 软件结构形式有软件结构和软件结构。
3、数控技术中常用的插补算法可归纳为插补法和插补法,前者用于数控系统,后者用于数控系统。
4、数控机床上导轨型式主要有滑动导轨、导轨和导轨。
5、数控铣削加工需要增加一个回转坐标或准确分度时,可以使用配备或使用。
6、电火花加工一次放电后,在工件和电极表面各形成一个小凹坑,其过程可分为电离、、热膨胀、和消电离等几个连续阶段。
7、影响材料放电腐蚀的主要因素是、、。
8、影响电火花加工精度的主要因素是、、。
9、电火花成形加工极性的选择主要靠经验和实验确定,当采用短脉冲时,一般应选用极性加工。
10、数控车床X 轴方向上的脉冲当量为Z 方向上的脉冲当量的。
11、数控机床的日常维护与保养主要包括、、等三个方面内容。
12、 3B 格式的数控系统没有功能,确定切割路线时,必须先根据工件轮廓划出电极丝中心线轨迹,再按编程。
13、旋转变压器和感应同步器根据励磁绕组供电方式的不同,可分为工作方式和工作方式。
二、判断题 <每题1分,共10分,正确打√错误打×)1、更换电池一定要在数控系统通电的情况下进行。
否则存储器中的数据就会丢失,造成数控系统的瘫痪。
<)2、数控机床几何精度的检测验收必须在机床精调后一次完成,不允许调整一项检测一项。
<)3、数控铣削螺纹加工,要求数控系统必须具有螺旋线插补功能。
<)4、电火花成形加工在粗加工时一般选择煤油加机油作为工作液。
<)5、当脉冲放电能量相同时,热导率愈小的金属,电蚀量会降低。
<)6、开环数控机床,进给速度受到很大限制,其主要原因是步进电机的转速慢。
<)7、当数控机床具有刀具半径补偿功能时,其程序编制与刀具半径补偿值无关。
<)8、只有加工中心机床能实现自动换刀,其它数控机床都不具备这一功能。
《数控铣床编程与操作项目教程》期未试卷一附答案

班级: 姓名: 学号: 考试号: 密封线内禁止答题 密封线内禁止答题学校期终考试试卷(一) 级 班《数控铣床编程与操作》试卷适用班级:________ 出卷教师: 审核人: 考试时间: 90 分钟1.企业中常用铣刀刀柄型号有 、 。
2.立式铣床圆弧插补平面为 平面。
3.法那克系统子程序结束指令为 ,西门子系统子程序结束指令有 。
4.西门子系统米制尺寸输入设定指令是 ,英制尺寸输入设定指令是 。
5.铣平面应选用 铣刀。
6. 西门子系统倒圆指令格式G01 X Z RND=;其中RND 表示 。
7. 刀具半径补偿过程中运动轨迹可分为 、 、 等三个步骤。
8.法那克系统G28指令表示 ,G29指令表示 。
9.加工内轮廓的进给路线有 、 、 三种,轮廓精加工应采用 才能获得较好表面质量。
10. 当加工内、外轮廓 的薄壁件时,可采用同一个程序,通过设置刀具半径值来分别进行内外轮廓的加工。
11.加工凹槽时铣刀半径应 凹槽拐角圆弧半径。
12. 西门子系统 凹槽循环指令加工凹槽,法那克系统 凹槽循环指令。
(填“有”或“没有”)13.法那克系统坐标系偏转是围绕 点进行偏转,西门子系统坐标系偏转是围绕 点进行偏转。
14.执行镜像功能后,G02与G03,G41与G42指令将被 。
15.每 程序中刀具工作的那一个坐标系通常又称为当前坐标系。
16.法那克系统中以子程序形式存储并带有 的程序称为用户宏程序。
17.西门子系统矩形型腔或圆形型腔循环中,铣刀半径应 矩形腔转角半径或圆形腔半径。
18. 在极坐标系中 运行G00、G01、G02、G03等指令。
(填“能”或“不能”) 19.寻边器装夹在 上,常用于 、 轴对刀。
20.Z 轴设定器一般放置在 上,用于 坐标轴的对刀。
21.机外对刀仪主要用于测量刀具的 、 、 等尺寸。
22.大部分数控机床可通过 、 等方法将程序传入数控机床。
23.将数控程序传入数控系统,法那克系统程序头为 。
- 1、下载文档前请自行甄别文档内容的完整性,平台不提供额外的编辑、内容补充、找答案等附加服务。
- 2、"仅部分预览"的文档,不可在线预览部分如存在完整性等问题,可反馈申请退款(可完整预览的文档不适用该条件!)。
- 3、如文档侵犯您的权益,请联系客服反馈,我们会尽快为您处理(人工客服工作时间:9:00-18:30)。
数 控 铣 削 加 工
刀 具 的 选 择
17
型腔的数控加工
数 控 铣 削 加 工
1.铣削用量的选择
铣 削 用 量 的 选 择 (1)背吃刀量ap (端铣)或侧吃刀量ae(圆周铣) (2)进给速度 (3)切削速度 切削速度与刀具耐用度T、每齿进给量fz、 背吃刀量ap、侧吃刀量ae以及铣刀齿数z成反比,而与铣刀 直径d成正比。 2.钻削用量的选择
存放于刀具库内,需要时再通过换刀指令,由ATC自动换刀。
数控镗铣床和加工中心都能够进行铣削、钻削、镗削及攻螺纹 等加工。 常有: (1)三坐标数控铣床与加工中心 (2)四坐标数控铣床与加工中心 (3)五坐标数控铣床与加工中心
10
型腔的数控加工
1.零件结构工艺性分析 (1)零件图样尺寸的正确标注 (2)获得要求的加工精度 如过薄的底板与助 板,因加工时弹性退让极易产生切削面的振动, 薄板厚度尺寸公差难以保证。 (3)如图① R尽量统一;②R与 H的关系;③r 与铣刀端刃铣削平面的能力的关系。 (4)保证基准统一 :采用统一基准定位加工各 要素。 (5)分析零件的变形情况: ①热处理方法解决; ②粗、精加工分开;③对称去余量 。 2.零件毛坯的工艺性分析 (1)分析毛坯的装夹适应性定位和夹紧的可靠 性与方便性 ;增加装夹余量或工艺凸台、工艺 凸耳等辅助基准。 (2)分析毛坯余量的大小及均匀性
型腔的数控加工
数 控 车 削 加 工
1.数控加工的最大特征有两点: 一是可以极大地提高精度; 二是可以提高加工质量的重复精度,稳 定加工质量,保持加工零件质量的一致。 2.数控加工及特点 (P142) 3.数控机床在模具加工中应用(P142)
1
型腔的数控加工
1.模具数控加工工艺设计是对模具 零 模 具 数 控 车 削 加 工 工 艺 的 制 订 件进行数控加工前的准备工作,无论是手 工编程还是自动编程,在编程前都要对所 加工的模具零件进行工艺设计。
23
型腔的数控加工
数 控 车 削 加 工
对以上三种切削进给路线,经 分析和判断后可知矩形循环进 给路线的进给长度总和最短。
24
型腔的数控加工
数 控 车 削 加 工
各种焊接式车刀 1一切断刀 2—90º 左偏刀 4—弯头车刀 5一直头车刀 7一宽刃精车刀 8一外螺纹车刀 10一内螺纹车刀 11一内槽车刀 13一盲孔车刀
11
数 控 铣 削 加 工
零件 图的 工艺 性分 析
型腔的数控加工
1.二维轮廓加工 (1)二维外轮廓加工 二维轮廓多由直线和圆 弧或各种曲线构成。通常采用三坐标数控铣床进 行两轴半坐标加工。 (2)二维型腔加工 (3)固定斜角平面加工 ①斜垫铁垫平后加工 ②行切法 ③将机床主轴偏转适当的角度④专用 的角度成形铣刀加工 (4)曲面轮廓加工 ①曲率变化不大和精度要求 不高的曲面的粗加工 常用两轴半坐标的行切法 加工。 ②曲率变化较大和精度要求较高的曲面 的精加工 常用x、y、z三坐标联动插补的行切 法加工。③形状复杂零件的精加工 常用五坐标 联动加工 。
8
型腔的数控加工
毛坯为已粗车过的¢34mm×80mm棒料,材料为Cr12, 要求在数控车床上车削。 1.零件工艺分析 坯件左端应加长用作夹持部位
数 控 车 削 加 工
2.确定装夹方案 左端三爪卡盘,右端用活顶针一次 装夹完成粗、精加工。
3 .确定数控加工顺序及进给路线 ①车端面;②粗 加工外轮廓;③精加工外轮廓;④割断四个工步完成。
6
型腔的数控加工
与传统的车削方法相比,数控车削对刀具的 要求更高。不仅要求精度高、刚度好、耐用度高、 而且要求尺寸稳定、安装调整方便。 l.焊接式车刀
数 控 车 削 加 工
(1)概念:将硬质合金刀片用焊接的方法固定在刀 体上称为焊接式车刀 . 刀具的选择
(2)优、缺点:优点是结构简单,制造方便,刚 性较好:缺点是由于存在焊接应力,使刀具材料 的使用性能受到影响,甚至出现裂纹。刀杆不能 重复使用,硬质合金刀片不能充分回收利用 (3)应用 2 .机夹式可转位车刀:
19
型腔的数控加工
数 控 车 削 加 工
按标注的尺寸画出来,圆 弧和斜线不相切
12+14+5=32 不等于32 ¢ 12和SR5不相切
20
型腔的数控加工
加工所用 坯料为 Ф32棒料, 批量生产
数 控 车 削 加 工
第一道工序 车 出Ф12mm和 Ф20mm两圆柱 面及圆锥面,换 刀后切断。
第二道工序 车 削包络SR7mm 球面的30°圆锥 面,换精车刀精 车圆弧表面。
数控车削加工时应尽量采用机夹式可转位车刀。
7
型腔的数控加工
数控车床加工中的切削用量包括:背吃刀量、主轴转速 或切削速度(用于恒线速切削)、进结速度或进给量。
1.背吃刀量的确定
数 控 车 削 加 工
粗车余量应尽可能大,精车余量一般比普通车削时所留余 量少,常取0.1-0. 5mm。
切 削 用 量 的 选 择
车削工艺制 订的实例
4.选择刀具和确定切削用量 选用硬质合金90º 粗车 刀,硬质合金90º 精车刀和高速钢割断刀。 (1) 背吃刀量 粗车循环时,取背吃刀量ap=3mm,精 车时ap=0.25mm。 (2) 主轴转速 查表取粗车vc=60 m/min,精车 vc=90m/min,既粗车时,主轴转速n=600r/min 精 车时,主轴转速n=850r/min (3) 进给速度 粗车时,f=0.3mm/r,精加工时, f=0.1mm/r。计算得:粗车vf=180mm/min,精车 vf=85mm/min。
4
型腔的数控加工
进给路线泛指刀具从对刀点(或机床固定原 点)开始运动起,直至返回该点并结束加工程序 所经过的路径,包括切削加工的路径及刀具切入、 切出等非切削空行程。 进给路线的 确定 主要在于确定粗加工及空行程的进给路线 1.最短的空行程路线
数 控 车 削 加 工
(1)合理利用起刀点
(2)合理设置换(转)刀点 (3) 合理安排“回零”路线
数 控 铣 削 加 工
装夹 方案 的确 定
15
型腔的数控加工
1.铣削外轮廓的进给路线 应避免沿零件外轮廓的法向切入,以避在切入 处产生刀痕,而应沿切削起始点延伸线或切线方 向逐渐切入工件,保证零件曲线的平滑过渡。 2.铣削内轮廓的进给路线 刀具可以沿一过渡圆弧切入和切出工件轮廓 R1 >R2 (过渡圆弧半径 ) 3.铣削二维型腔的进给路线 第一步切内腔,第二步切轮廓。切削内腔区域 时,主要采用环切和行切两种走刀路线 4.铣削曲面的进给路线 在保证零件加工精度 和表面粗糙度的条件下,尽量缩短进给路线,以 提高生产率。 5.孔加工进给路线 (l)确定xy平面内的进给路线 ①定位要迅速 ②定位要准确 (2)确定Z向的进给路线和工作进给距离计算
16
数 控 铣 削 加 工
进给 路线 的确 定
型腔的数控加工
1.对在数控铣削刀具的基本要求: 一是刚性要好;二是耐用度要高。 2.常用铣刀的种类和特点 (1)面铣刀 主要用于面积较大的平面铣削和较平 坦的立体轮廓的多坐标加工。 (2)立铣刀 立铣刀的圆柱表面和端面上都有切 削刃,它们可同时进行切削,也可单独进行切削。其 端面中心处无切削刃,所以立铣刀不能轴向进给。 (3)模具铣刀 主要用于模具型腔的铣削加工。 (4)键槽铣刀 键槽铣刀端面刃延至中心,既象立 铣刀,又像钻头。加工时能轴向进给。 (5) 鼓形铣刀 控制刀具上下位置,相应改变刀刃 的切削部位,可以切出从负到正的不同斜角。 (6)成形铣刀 为特定的加工专门设计制造的铣刀。
2.最短的切削进给路线
3.完工轮廓的连续切削进给路线
5
型腔的数控加工
夹具的精度和结构应该和数控机床的高速度、 高精度和自动化相适应,除使用通用三爪自定心 卡盘、四爪卡盘、液压、电动及气动夹具外,还 常用
数 控 车 削 加 工
夹具的选择
(1) 用于轴类工件的夹具:自动夹紧拨动卡盘、 拔齿顶尖、三爪拨动卡盘和快速可调万能卡盘等。 (2)用于盘类工件的夹具 这类夹具适用在无尾座的卡盘式数控车床上。 主要有可调卡爪式卡盘和快速可调卡盘。
数 控 铣 削 加 工
模具 常用 数控 加工 方法 及选 用
12
型腔的数控加工
(5)孔系的加工 在一次安装中可以完成零 件的铣削、孔系的钻削、镗削、铰销及攻螺纹等。 ①直径大于¢30mm的已铸出毛坯孔的孔加工, 用粗镗→半精镗→孔口倒角→精镗的加工方案, 孔径较大的可采用立铣刀粗铣→精铣加工方案。 ②对于直径小于¢30mm无底孔的孔加工,用 锪平端面→打中心孔→钻→扩→孔口倒角→铰加 工方案,对有同轴度要求的小孔,用锪平端面→ 打中心孔→钻→半精镗→孔口倒角→精镗(或铰) 加工方案。 ③内螺纹的加工 ,M6~M20机攻螺纹 M6以 下 手攻螺纹 M20以上用铣削(或镗削)
21
型腔的数控加工
数 控 车 削 加 工
先粗后精
先近后远
22
型腔的数控加工
数 控 车 削 加 工
第一刀 A→B→C→D→A; 第二刀 A→E→F→G→A; 第三刀 A→H→I→J→A 。
第一刀 B→C→D→E→B; 第二刀 B→F→G→H→B; 第三刀 B→I→J→K→B。 起刀点与对刀点分离, 并设于图示B点位置处 进给路线短
数 控 车 削 加 工
零件图的 工艺分析
3
型腔的数控加工
工序的确定
数控加工应按工序集中的原则划分工序,在 一次安装中尽可能完成大部分甚至全部表面的加 工。 (1)按零件加工表面划分 (2)按粗、精加工划分 (1)先粗后精
数 控 车 削 加 工
加工(工步) 顺序的确定
(2)先近后远:在一般情况的刚性。 (3)内外交叉
数 控 车 削 加 工
2.制订数控车削工艺在遵循一般工艺原
则的基础上结合数控车削的特点来进行。 其主要内容有: (1)分析零件图纸; (2)确定安装方式; (3)确定各表面的加工顺序和进给路线; (4)选择刀具、夹具和切削用量等。