焊管史话之二十二 高频焊接钢管生产工艺技术的成熟
高频焊管工艺流程
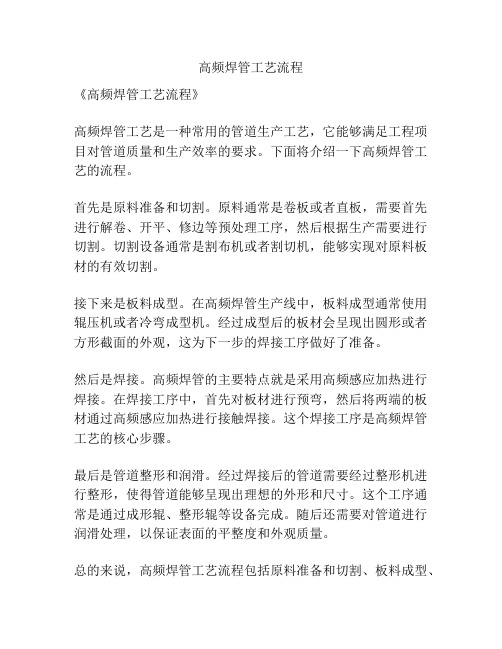
高频焊管工艺流程
《高频焊管工艺流程》
高频焊管工艺是一种常用的管道生产工艺,它能够满足工程项目对管道质量和生产效率的要求。
下面将介绍一下高频焊管工艺的流程。
首先是原料准备和切割。
原料通常是卷板或者直板,需要首先进行解卷、开平、修边等预处理工序,然后根据生产需要进行切割。
切割设备通常是割布机或者割切机,能够实现对原料板材的有效切割。
接下来是板料成型。
在高频焊管生产线中,板料成型通常使用辊压机或者冷弯成型机。
经过成型后的板材会呈现出圆形或者方形截面的外观,这为下一步的焊接工序做好了准备。
然后是焊接。
高频焊管的主要特点就是采用高频感应加热进行焊接。
在焊接工序中,首先对板材进行预弯,然后将两端的板材通过高频感应加热进行接触焊接。
这个焊接工序是高频焊管工艺的核心步骤。
最后是管道整形和润滑。
经过焊接后的管道需要经过整形机进行整形,使得管道能够呈现出理想的外形和尺寸。
这个工序通常是通过成形辊、整形辊等设备完成。
随后还需要对管道进行润滑处理,以保证表面的平整度和外观质量。
总的来说,高频焊管工艺流程包括原料准备和切割、板料成型、
焊接、管道整形和润滑等几个主要步骤。
每一步工序都需要进行严格的控制和管理,以保证最终产品的质量和性能。
随着科技的进步,高频焊管工艺也在不断创新和发展,为各种工程项目的管道生产提供了可靠的解决方案。
高频焊管成型技术的发展
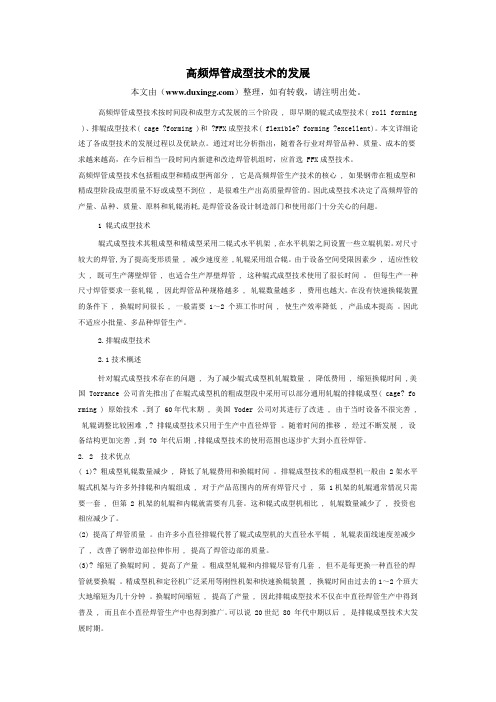
高频焊管成型技术的发展本文由()整理,如有转载,请注明出处。
高频焊管成型技术按时间段和成型方式发展的三个阶段 , 即早期的辊式成型技术( roll forming )、排辊成型技术( cage ?forming )和 ?FFX成型技术( flexible? forming ?excellent)。
本文详细论述了各成型技术的发展过程以及优缺点。
通过对比分析指出,随着各行业对焊管品种、质量、成本的要求越来越高,在今后相当一段时间内新建和改造焊管机组时,应首选 FFX成型技术。
高频焊管成型技术包括粗成型和精成型两部分 , 它是高频焊管生产技术的核心 , 如果钢带在粗成型和精成型阶段成型质量不好或成型不到位 , 是很难生产出高质量焊管的。
因此成型技术决定了高频焊管的产量、品种、质量、原料和轧辊消耗,是焊管设备设计制造部门和使用部门十分关心的问题。
1 辊式成型技术辊式成型技术其粗成型和精成型采用二辊式水平机架 ,在水平机架之间设置一些立辊机架。
对尺寸较大的焊管,为了提高变形质量 , 减少速度差 ,轧辊采用组合辊。
由于设备空间受限因素少 , 适应性较大 , 既可生产薄壁焊管 , 也适合生产厚壁焊管 , 这种辊式成型技术使用了很长时间。
但每生产一种尺寸焊管要求一套轧辊 , 因此焊管品种规格越多 , 轧辊数量越多 , 费用也越大。
在没有快速换辊装置的条件下 , 换辊时间很长 , 一般需要 1~2 个班工作时间 , 使生产效率降低 , 产品成本提高。
因此不适应小批量、多品种焊管生产。
2.排辊成型技术2.1技术概述针对辊式成型技术存在的问题 , 为了减少辊式成型机轧辊数量 , 降低费用 , 缩短换辊时间 ,美国 Torrance 公司首先推出了在辊式成型机的粗成型段中采用可以部分通用轧辊的排辊成型( cage? fo rming ) 原始技术。
到了 60年代末期 , 美国 Yoder 公司对其进行了改进 , 由于当时设备不很完善 ,轧辊调整比较困难 ,? 排辊成型技术只用于生产中直径焊管。
高频焊管的生产流程
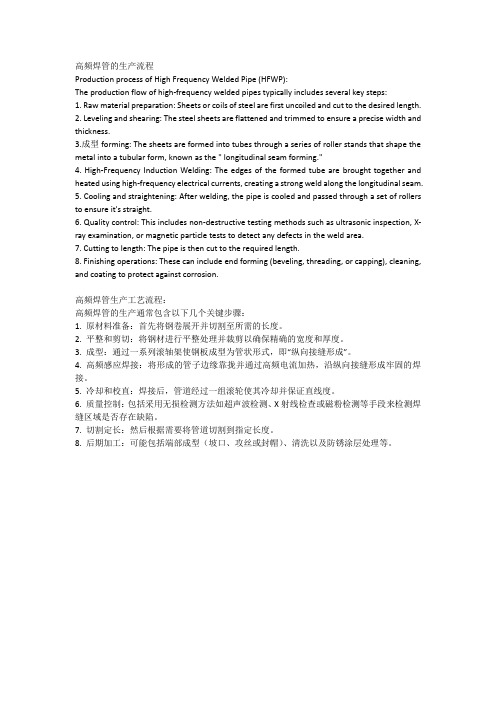
高频焊管的生产流程Production process of High Frequency Welded Pipe (HFWP):The production flow of high-frequency welded pipes typically includes several key steps:1. Raw material preparation: Sheets or coils of steel are first uncoiled and cut to the desired length.2. Leveling and shearing: The steel sheets are flattened and trimmed to ensure a precise width and thickness.3.成型forming: The sheets are formed into tubes through a series of roller stands that shape the metal into a tubular form, known as the " longitudinal seam forming."4. High-Frequency Induction Welding: The edges of the formed tube are brought together and heated using high-frequency electrical currents, creating a strong weld along the longitudinal seam.5. Cooling and straightening: After welding, the pipe is cooled and passed through a set of rollers to ensure it's straight.6. Quality control: This includes non-destructive testing methods such as ultrasonic inspection, X-ray examination, or magnetic particle tests to detect any defects in the weld area.7. Cutting to length: The pipe is then cut to the required length.8. Finishing operations: These can include end forming (beveling, threading, or capping), cleaning, and coating to protect against corrosion.高频焊管生产工艺流程:高频焊管的生产通常包含以下几个关键步骤:1. 原材料准备:首先将钢卷展开并切割至所需的长度。
高频焊接技术简介
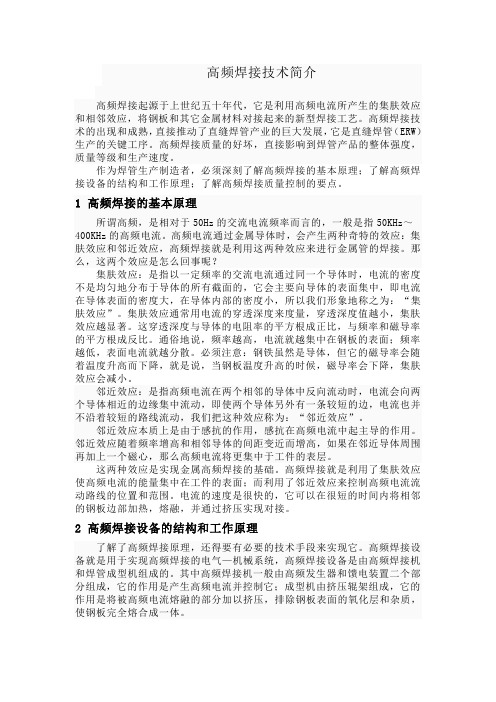
高频焊接技术简介高频焊接起源于上世纪五十年代,它是利用高频电流所产生的集肤效应和相邻效应,将钢板和其它金属材料对接起来的新型焊接工艺。
高频焊接技术的出现和成熟,直接推动了直缝焊管产业的巨大发展,它是直缝焊管(ERW)生产的关键工序。
高频焊接质量的好坏,直接影响到焊管产品的整体强度,质量等级和生产速度。
作为焊管生产制造者,必须深刻了解高频焊接的基本原理;了解高频焊接设备的结构和工作原理;了解高频焊接质量控制的要点。
1 高频焊接的基本原理所谓高频,是相对于50Hz的交流电流频率而言的,一般是指50KHz~400KHz的高频电流。
高频电流通过金属导体时,会产生两种奇特的效应:集肤效应和邻近效应,高频焊接就是利用这两种效应来进行金属管的焊接。
那么,这两个效应是怎么回事呢?集肤效应:是指以一定频率的交流电流通过同一个导体时,电流的密度不是均匀地分布于导体的所有截面的,它会主要向导体的表面集中,即电流在导体表面的密度大,在导体内部的密度小,所以我们形象地称之为:“集肤效应”。
集肤效应通常用电流的穿透深度来度量,穿透深度值越小,集肤效应越显著。
这穿透深度与导体的电阻率的平方根成正比,与频率和磁导率的平方根成反比。
通俗地说,频率越高,电流就越集中在钢板的表面;频率越低,表面电流就越分散。
必须注意:钢铁虽然是导体,但它的磁导率会随着温度升高而下降,就是说,当钢板温度升高的时候,磁导率会下降,集肤效应会减小。
邻近效应:是指高频电流在两个相邻的导体中反向流动时,电流会向两个导体相近的边缘集中流动,即使两个导体另外有一条较短的边,电流也并不沿着较短的路线流动,我们把这种效应称为:“邻近效应”。
邻近效应本质上是由于感抗的作用,感抗在高频电流中起主导的作用。
邻近效应随着频率增高和相邻导体的间距变近而增高,如果在邻近导体周围再加上一个磁心,那么高频电流将更集中于工件的表层。
这两种效应是实现金属高频焊接的基础。
高频焊接就是利用了集肤效应使高频电流的能量集中在工件的表面;而利用了邻近效应来控制高频电流流动路线的位置和范围。
焊接管的加工工艺流程

焊接管的加工工艺流程【焊接管的加工工艺流程】1. 焊接管的历史其实啊,焊接管的历史可以追溯到相当久远的时候。
在工业革命之前,人们就已经开始尝试用各种方法连接金属管材,但那时候的技术还非常原始和粗糙。
随着工业技术的不断发展,焊接管的工艺也逐渐变得成熟和完善。
早期的焊接管主要用于一些简单的结构和管道系统,比如早期的蒸汽机中的一些管道连接。
那时候的焊接质量和效率都比较低,而且成本也高。
但是随着时间的推移,焊接技术不断改进。
到了 19 世纪末和 20 世纪初,随着电力的广泛应用和焊接设备的不断更新,焊接管的生产开始大规模化。
说白了就是,焊接管从一开始的简单粗糙,逐渐变得越来越精细、高效和普及,成为了现代工业和建筑中不可或缺的一部分。
1.1 焊接管在不同时期的发展特点在早期,焊接管的生产主要依靠手工焊接,这就像是在做一件非常精细的手工活儿,速度慢不说,质量还不太稳定。
而且那时候能焊接的管材种类也很有限。
到了中期,半自动焊接设备开始出现,这就好比有了个小帮手,能提高一些效率,但还是需要人来时刻盯着。
而现在呢,自动化和智能化的焊接设备大行其道,不仅速度快得惊人,质量还特别稳定。
而且能够焊接各种材质、各种规格的管材,满足了各种各样的需求。
2. 焊接管的制作过程2.1 材料准备要制作焊接管,首先得准备好材料。
这就好比做饭,得先把食材准备齐全。
一般来说,常用的材料有钢带或者钢板。
这些材料的质量和性能可直接影响到最终焊接管的质量。
在选择材料时,要考虑到很多因素,比如强度、韧性、耐腐蚀性等等。
说白了就是,得根据焊接管的用途来选择合适的材料。
比如说,如果是要用于输送腐蚀性液体的管道,那就得选择耐腐蚀性强的材料;如果是用于承受高压力的场合,那就得选强度高的材料。
2.2 成型材料准备好后,接下来就是成型啦。
这个过程就像是把一张纸折成一个管子。
通过一系列的模具和设备,把钢带或钢板逐渐弯曲成管状。
在成型过程中,要保证管子的形状和尺寸准确无误。
高频焊管生产工艺

高频焊管生产工艺高频焊管生产工艺是利用高频电流将钢板加热到干燥状态后,经过钢板成型、焊接、内外焊接焊缝挤压、冷却、焊缝消除,通过修边、伸长、穿孔等工艺控制管道尺寸和形状,最后经过定径、直接焊接、挤压等工艺,制成具备一定强度和韧性的高频焊管。
下面将详细介绍高频焊管生产工艺的各个环节。
首先是钢板的预处理。
钢板进入生产线时,首先进行除锈、清洗和切割。
除锈主要是通过喷砂或化学清洗来去除钢板表面的氧化物和油渍,确保焊缝的质量;清洗则主要是去除表面的灰尘和杂质,保持焊管表面的干净;切割则是将整张大钢板进行裁剪,以便于后续的工艺。
接下来是钢板成型。
将已经预处理好的钢板送入成型机,通过辊轧将钢板弯曲成所需的形状,形成一个圆形管道。
成型机一般采用三辊辊轧机或四辊辊轧机,通过不同辊轧机的组合和控制,可以制备出不同直径和壁厚的管道。
然后是焊接。
将经过成型的钢板进行焊接,焊接方式主要有高频感应焊和高频阻抗焊。
高频感应焊是利用高频电流在钢板边缘产生热量,将两片钢板加热至一定温度后,施加压力将其焊接在一起;高频阻抗焊则是将两片钢板进行重叠,通过高频电流在接头位置产生电阻加热,使其达到熔点,然后施加压力焊接。
接下来是焊缝挤压。
通过焊缝挤压机,对焊接好的管道进行内外焊缝的挤压处理,将焊缝的金属挤入管道内部,使其形成一个平整的内外焊缝,提高焊缝的强度。
然后是冷却和焊缝消除。
焊接后的管道需要经过冷却处理,以降低焊缝温度和改善焊缝的组织结构,提高焊缝强度。
同时还需要进行焊缝消除处理,通过机械或热处理,去除焊缝附近的应力和变形,使管道的形状更加合理。
最后是修边、伸长和穿孔。
修边是将管道两端进行加工,使其边缘平整,以便于后续的工艺;伸长是通过拉伸机对管道进行拉伸,使其达到预设的长度和精度;穿孔则是通过穿孔机对管道进行钻孔,以便于后续的工艺。
最后还需要进行定径和直接焊接。
定径是通过定径机对管道进行调整,使其尺寸达到要求;直接焊接则是将两个管道进行焊接,以形成更长的管道。
高频焊管
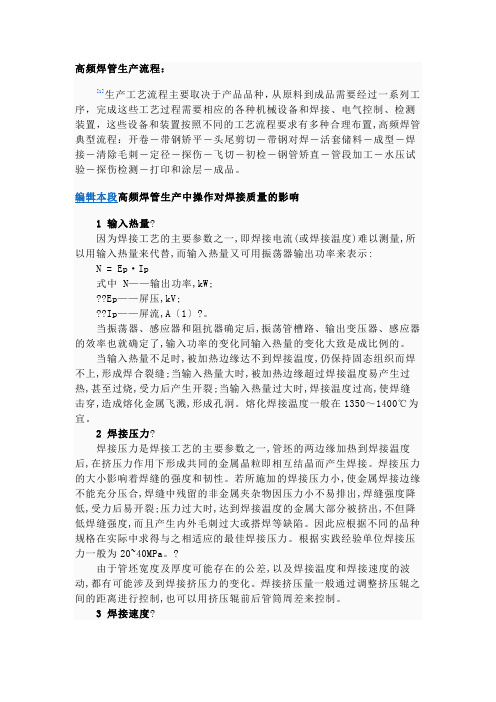
高频焊管生产流程:[1]生产工艺流程主要取决于产品品种,从原料到成品需要经过一系列工序,完成这些工艺过程需要相应的各种机械设备和焊接、电气控制、检测装置,这些设备和装置按照不同的工艺流程要求有多种合理布置,高频焊管典型流程:开卷―带钢矫平―头尾剪切―带钢对焊―活套储料―成型―焊接―清除毛刺―定径―探伤―飞切―初检―钢管矫直―管段加工―水压试验―探伤检测―打印和涂层―成品。
编辑本段高频焊管生产中操作对焊接质量的影响1 输入热量?因为焊接工艺的主要参数之一,即焊接电流(或焊接温度)难以测量,所以用输入热量来代替,而输入热量又可用振荡器输出功率来表示: N = Ep·Ip式中 N——输出功率,kW;??Ep——屏压,kV;??Ip——屏流,A〔1〕?。
当振荡器、感应器和阻抗器确定后,振荡管槽路、输出变压器、感应器的效率也就确定了,输入功率的变化同输入热量的变化大致是成比例的。
当输入热量不足时,被加热边缘达不到焊接温度,仍保持固态组织而焊不上,形成焊合裂缝;当输入热量大时,被加热边缘超过焊接温度易产生过热,甚至过烧,受力后产生开裂;当输入热量过大时,焊接温度过高,使焊缝击穿,造成熔化金属飞溅,形成孔洞。
熔化焊接温度一般在1350~1400℃为宜。
2 焊接压力?焊接压力是焊接工艺的主要参数之一,管坯的两边缘加热到焊接温度后,在挤压力作用下形成共同的金属晶粒即相互结晶而产生焊接。
焊接压力的大小影响着焊缝的强度和韧性。
若所施加的焊接压力小,使金属焊接边缘不能充分压合,焊缝中残留的非金属夹杂物因压力小不易排出,焊缝强度降低,受力后易开裂;压力过大时,达到焊接温度的金属大部分被挤出,不但降低焊缝强度,而且产生内外毛刺过大或搭焊等缺陷。
因此应根据不同的品种规格在实际中求得与之相适应的最佳焊接压力。
根据实践经验单位焊接压力一般为20~40MPa。
?由于管坯宽度及厚度可能存在的公差,以及焊接温度和焊接速度的波动,都有可能涉及到焊接挤压力的变化。
高频焊管生产工艺
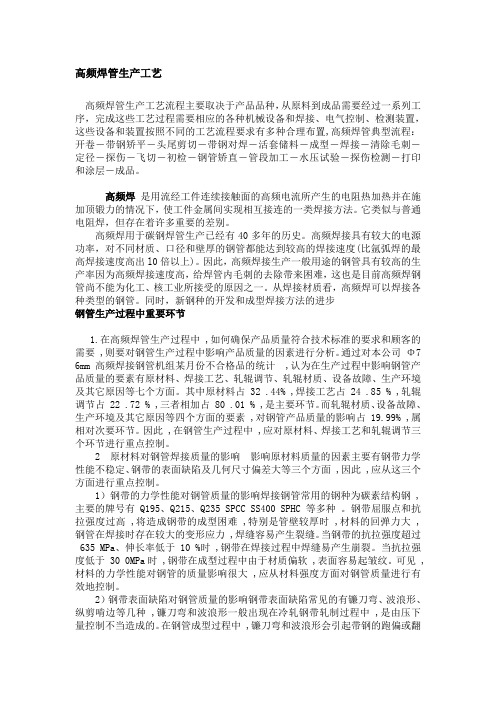
高频焊管生产工艺高频焊管生产工艺流程主要取决于产品品种,从原料到成品需要经过一系列工序,完成这些工艺过程需要相应的各种机械设备和焊接、电气控制、检测装置,这些设备和装置按照不同的工艺流程要求有多种合理布置,高频焊管典型流程:开卷―带钢矫平―头尾剪切―带钢对焊―活套储料―成型―焊接―清除毛刺―定径―探伤―飞切―初检―钢管矫直―管段加工―水压试验―探伤检测―打印和涂层―成品。
高频焊是用流经工件连续接触面的高频电流所产生的电阻热加热并在施加顶锻力的情况下,使工件金属间实现相互接连的一类焊接方法。
它类似与普通电阻焊,但存在着许多重要的差别。
高频焊用于碳钢焊管生产已经有40多年的历史。
高频焊接具有较大的电源功率,对不同材质、口径和壁厚的钢管都能达到较高的焊接速度(比氩弧焊的最高焊接速度高出l0倍以上)。
因此,高频焊接生产一般用途的钢管具有较高的生产率因为高频焊接速度高,给焊管内毛刺的去除带来困难,这也是目前高频焊钢管尚不能为化工、核工业所接受的原因之一。
从焊接材质看,高频焊可以焊接各种类型的钢管。
同时,新钢种的开发和成型焊接方法的进步钢管生产过程中重要环节1.在高频焊管生产过程中 ,如何确保产品质量符合技术标准的要求和顾客的需要 ,则要对钢管生产过程中影响产品质量的因素进行分析。
通过对本公司Φ7 6mm高频焊接钢管机组某月份不合格品的统计 ,认为在生产过程中影响钢管产品质量的要素有原材料、焊接工艺、轧辊调节、轧辊材质、设备故障、生产环境及其它原因等七个方面。
其中原材料占 32 .44% ,焊接工艺占 24 .85 % ,轧辊调节占 22 .72 % ,三者相加占 80 .01 % ,是主要环节。
而轧辊材质、设备故障、生产环境及其它原因等四个方面的要素 ,对钢管产品质量的影响占19.99% ,属相对次要环节。
因此 ,在钢管生产过程中 ,应对原材料、焊接工艺和轧辊调节三个环节进行重点控制。
2 原材料对钢管焊接质量的影响影响原材料质量的因素主要有钢带力学性能不稳定、钢带的表面缺陷及几何尺寸偏差大等三个方面 ,因此 ,应从这三个方面进行重点控制。
高频直缝焊管生产工艺规程
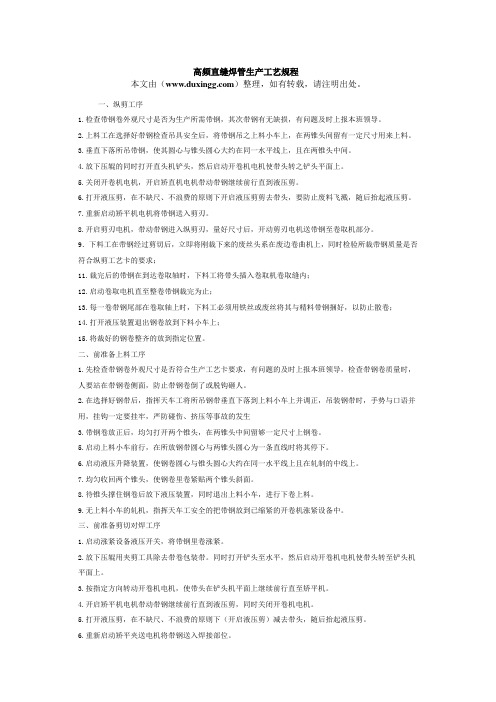
高频直缝焊管生产工艺规程本文由()整理,如有转载,请注明出处。
一、纵剪工序1.检查带钢卷外观尺寸是否为生产所需带钢,其次带钢有无缺损,有问题及时上报本班领导。
2.上料工在选择好带钢检查吊具安全后,将带钢吊之上料小车上,在两锥头间留有一定尺寸用来上料。
3.垂直下落所吊带钢,使其圆心与锥头圆心大约在同一水平线上,且在两锥头中间。
4.放下压辊的同时打开直头机铲头,然后启动开卷机电机使带头转之铲头平面上。
5.关闭开卷机电机,开启矫直机电机带动带钢继续前行直到液压剪。
6.打开液压剪,在不缺尺、不浪费的原则下开启液压剪剪去带头,要防止废料飞溅,随后抬起液压剪。
7.重新启动矫平机电机将带钢送入剪刃。
8.开启剪刃电机,带动带钢进入纵剪刃,量好尺寸后,开动剪刃电机送带钢至卷取机部分。
9.下料工在带钢经过剪切后,立即将刚裁下来的废丝头系在废边卷曲机上,同时检验所裁带钢质量是否符合纵剪工艺卡的要求;11.裁完后的带钢在到达卷取轴时,下料工将带头插入卷取机卷取缝内;12.启动卷取电机直至整卷带钢裁完为止;13.每一卷带钢尾部在卷取轴上时,下料工必须用铁丝或废丝将其与精料带钢捆好,以防止散卷;14.打开液压装置退出钢卷放到下料小车上;15.将裁好的钢卷整齐的放到指定位置。
二、前准备上料工序1.先检查带钢卷外观尺寸是否符合生产工艺卡要求,有问题的及时上报本班领导,检查带钢卷质量时,人要站在带钢卷侧面,防止带钢卷倒了或脱钩砸人。
2.在选择好钢带后,指挥天车工将所吊钢带垂直下落到上料小车上并调正,吊装钢带时,手势与口语并用,挂钩一定要挂牢,严防碰伤、挤压等事故的发生3.带钢卷放正后,均匀打开两个锥头,在两锥头中间留够一定尺寸上钢卷。
5.启动上料小车前行,在所放钢带圆心与两锥头圆心为一条直线时将其停下。
6.启动液压升降装置,使钢卷圆心与锥头圆心大约在同一水平线上且在轧制的中线上。
7.均匀收回两个锥头,使钢卷里卷紧贴两个锥头斜面。
高频焊管生产工艺
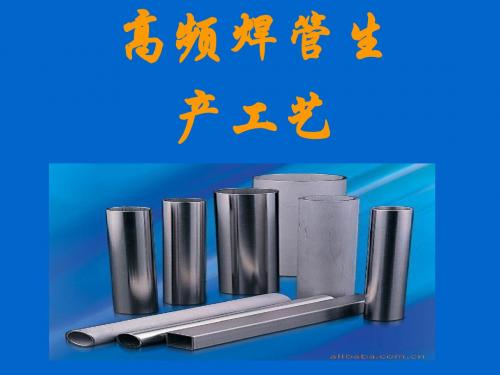
3)钢带几何尺寸对钢管质量的影响当钢带的宽度小
于允许偏差时,焊接钢管时的挤压力减小,使得钢管焊缝处 焊接不牢固,出现裂缝或是开口管;当钢带的宽度大于允许 偏差时,焊接钢管时的挤压力增加,在钢管焊缝处出现尖嘴、 搭焊或毛刺等焊接缺陷。所以,钢带宽度的波动,不但影响 了钢管外径的精度,而且严重影响了钢管的表面质量。对 要求同一断面壁厚差不超过规定值的钢管,即要求壁厚均 匀程度高的钢管,钢带厚度的波动,会将同一卷钢带厚度差 超出的允许值转移到成品钢管的壁厚差,使大批钢管厚度 超出允许偏差而判废。厚度的波动不仅影响成品钢管的厚 度精度,同时,由于钢带的厚薄不一,使钢管在焊接时,挤压 力和焊接温度不稳定,造成了钢管焊接时焊缝质量不稳定。 此外,由于钢材内部存在着夹层、杂质、沙眼等材料缺陷, 也是影响钢管质量的一个重要因素。因此,在钢带焊接前, 要检查每卷钢带的表面质量和几何尺寸,对钢带质量不符
五 高频焊管的技术要求与质量检验
根据GB3092《低压流体输送用焊接钢管》 标准的规定,焊管的公称直径为6~150mm, 公称壁厚为2.0~6.0mm,焊管的长度通常为 4~10米,可按定尺或倍尺长度出厂。钢管 表面质量应光滑,不允许有折叠、裂缝、 分层、搭焊等缺陷存在。钢管表面允许有 不超过壁厚负偏差的划道、刮伤、焊缝错 位、烧伤和结疤等轻微缺陷存在。允许焊 缝处壁厚增厚和内缝焊筋存在。
三、钢管生产过程中的重要环节(续)
2)钢带表面缺陷对钢管质量的影响钢带表面缺 陷常见的有镰刀弯、波浪形、纵剪啃边等几种,镰 刀弯和波浪形一般出现在冷轧钢带轧制过程中,是 由压下量控制不当造成的。在钢管成型过程中,镰 刀弯和波浪形会引起带钢的跑偏或翻转,容易使钢 管焊缝产生搭焊,影响钢管的质量。钢带的啃边(即 钢带边缘呈现锯齿状凹凸不平的现象 ) ,一般出现 在纵剪带上 ,产生原因是纵剪机圆盘刀刃磨钝或不 锋利造成的。由于钢带的啃边,时时出现局部缺肉 , 使钢带在焊接时易产生裂纹、裂缝而影响焊缝质量 的稳定性。
焊接钢管的成型工艺大全.pdf

焊接钢管的成型工艺大全Via 常州精密钢管博客焊接钢管的成型工艺大全钢管生产技术的发展开始于自行车制造业的兴起,19世纪初期石油的开发,两次世界大战期间舰船、锅炉、飞机的制造,第二次世界大战后火电锅炉的制造,化学工业的发展以及石油天然气的钻采和运输等,都有力地推动着钢管工业在品种、产量和质量上的发展。
通常钢管按照生产方法,分为无缝钢管和焊接钢管两种类型,这次主要给大家介绍焊接钢管。
焊接钢管即有缝钢管,其生产是将管坯(钢板和钢带)用各种成型方法弯卷成要求的横断面形状和尺寸的管筒,再用不同的焊接方法将焊缝焊合而得到钢管的过程。
相比于无缝钢管,焊管具有产品精度高,尤其是壁厚精度、主设备简单,占地小、生产上可以连续化作业、生产灵活、机组的产品范围宽等特点。
而焊管要从生产工艺上来分,又分为:螺旋埋弧焊管SSAW(Spirally Submerged Arc Welding);直缝双面埋弧焊管LSAW(LongitudinallySubmerged Arc Welding);电阻焊管ERW(Electric Resistance Welding)三种。
一螺旋钢管生产工艺大致如下 ● 螺旋钢管原材料即带钢卷、焊丝、焊剂。
● 成型前带钢经过矫平、剪边、刨边,表面清理输送和予弯边处理。
● 采用焊缝间隙控制装置来保证焊缝间隙满足焊接要求,管径、错边量和焊缝间隙都得到严格的控制。
● 切成单根钢管后,每批钢管头三根要进行严格的首检制度,检查焊缝的力学性能,化学成份,溶合状况,钢管表面质量以及经过无损探伤检验,确保制管工艺合格后,才能正式投入生产。
二直缝埋弧焊管而直缝埋弧焊管(LSAW)一般是以钢板为原料,经过不同的成型工艺,采用双面埋弧焊接和焊后扩径等工序形成焊管。
主要设备有铣边机、预弯机、成型机、预焊机、扩径机等。
同时直缝埋弧焊管的成型型方式有UO(UOE)、RB(RBE)、JCO(JCOE)等多种。
将钢板在成型模内先压成U形,再压成O形,然后进行内外埋弧焊,焊后通常在端部或全长范围扩径(Expanding)称为UOE焊管,不扩径的称为UO焊管。
焊管制造工艺
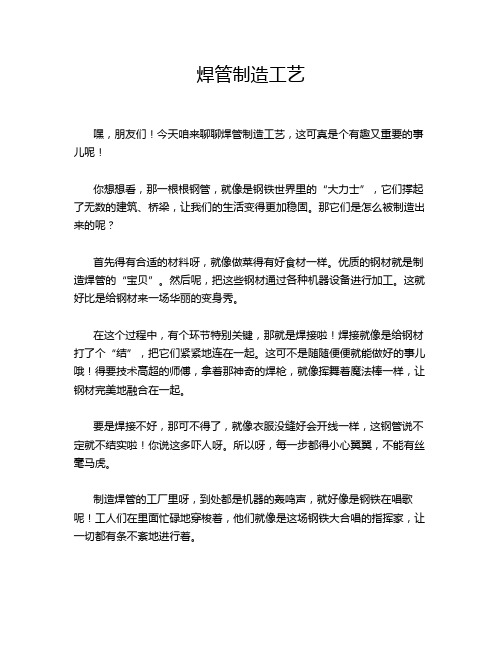
焊管制造工艺嘿,朋友们!今天咱来聊聊焊管制造工艺,这可真是个有趣又重要的事儿呢!你想想看,那一根根钢管,就像是钢铁世界里的“大力士”,它们撑起了无数的建筑、桥梁,让我们的生活变得更加稳固。
那它们是怎么被制造出来的呢?首先得有合适的材料呀,就像做菜得有好食材一样。
优质的钢材就是制造焊管的“宝贝”。
然后呢,把这些钢材通过各种机器设备进行加工。
这就好比是给钢材来一场华丽的变身秀。
在这个过程中,有个环节特别关键,那就是焊接啦!焊接就像是给钢材打了个“结”,把它们紧紧地连在一起。
这可不是随随便便就能做好的事儿哦!得要技术高超的师傅,拿着那神奇的焊枪,就像挥舞着魔法棒一样,让钢材完美地融合在一起。
要是焊接不好,那可不得了,就像衣服没缝好会开线一样,这钢管说不定就不结实啦!你说这多吓人呀。
所以呀,每一步都得小心翼翼,不能有丝毫马虎。
制造焊管的工厂里呀,到处都是机器的轰鸣声,就好像是钢铁在唱歌呢!工人们在里面忙碌地穿梭着,他们就像是这场钢铁大合唱的指挥家,让一切都有条不紊地进行着。
你知道吗,焊管的种类也有很多呢!有大的、小的、粗的、细的,各种各样的形状和尺寸,就像是一个庞大的钢铁家族。
它们各自有着不同的用途,在不同的地方发挥着重要的作用。
有时候我就想啊,这焊管制造工艺不就跟我们做人一样嘛!都得一步一个脚印,踏踏实实地做好每一件事。
不能偷工减料,不能马马虎虎。
只有这样,才能做出好的产品,才能成为一个可靠的人。
制造一根好的焊管不容易呀,需要很多人的努力和付出。
从原材料的选择到最后的成品,每一个环节都凝聚着大家的心血。
这让我想起了我们生活中的很多事情,不也是这样吗?只有大家齐心协力,才能把事情做好。
总之呢,焊管制造工艺可真是一门大学问!它看似简单,实则蕴含着无数的智慧和技巧。
我们可不能小瞧了它哦!希望大家以后看到那些钢管的时候,能想起它们背后的故事,想起那些默默付出的人们。
让我们一起为焊管制造工艺点赞,为那些勤劳的工人们点赞!。
审核员培训教程
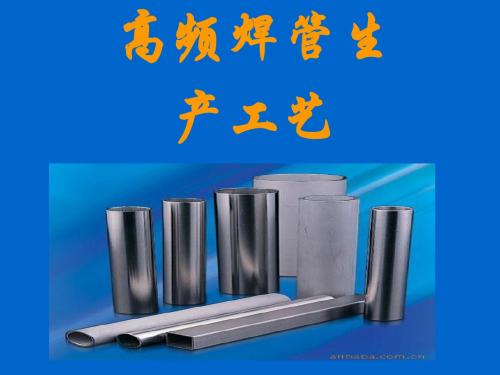
第一章概述
第一节 第二节 第三节 第四节 第五节 验
我国焊管的产生和发展 焊管的生产方法 焊管的用途
低压流体输送管的生产工艺流程
高频焊管的技术要求与质量检
1.1 我国焊管产生的发展
解放前我国只有少数几台链式炉焊管机 组.
1958年天津轧钢一厂从苏联进口φ60机 组;首钢焊管厂从苏联进口φ102机组;宝 鸡钢管厂从苏联进口φ650螺旋焊管机组; 上海钢管厂测绘仿制了φ60机组。 1960年以后高频焊代替了低频焊。
影响焊缝的焊接质量。
2)高频感应圈位置的调控
感应圈应放置在与钢管同一中心线上 ,感 应圈前端距挤压辊中心线的距离 ,在不烧损 挤压辊的前提下 ,应视钢管的规格而尽量接 近。若感应圈距挤压辊较远时 ,有效加热时 间较长 ,热影响区宽 ,使得钢管焊缝的强度 下降或未焊透 ;反之感应圈易烧毁挤压辊。
3) 阻抗器位置的调控
4)高频焊接工艺参数——输入热量的控制高频电源输 入给钢管焊缝部位的热量称为输入热量。将电能转换成热 能时 ,其输入热量的公式为 :Q=KI2 Rt (1)
式中Q—输入管坯的热量 ;K—能量转换效率 ;I—焊接电
流;R—回路阻抗 ;t—加热时间。
加热时间:t=Lv (2)
式中L—感应圈或电极头前端至挤压辊的中心距;v—焊接速度。
三、钢管生产过程中的重要环节(续)
2)钢带表面缺陷对钢管质量的影响钢带表面缺 陷常见的有镰刀弯、波浪形、纵剪啃边等几种,镰 刀弯和波浪形一般出现在冷轧钢带轧制过程中,是 由压下量控制不当造成的。在钢管成型过程中,镰 刀弯和波浪形会引起带钢的跑偏或翻转,容易使钢 管焊缝产生搭焊,影响钢管的质量。钢带的啃边(即 钢带边缘呈现锯齿状凹凸不平的现象 ) ,一般出现 在纵剪带上 ,产生原因是纵剪机圆盘刀刃磨钝或不 锋利造成的。由于钢带的啃边,时时出现局部缺肉 , 使钢带在焊接时易产生裂纹、裂缝而影响焊缝质量 的稳定性。
高频焊管技术交流
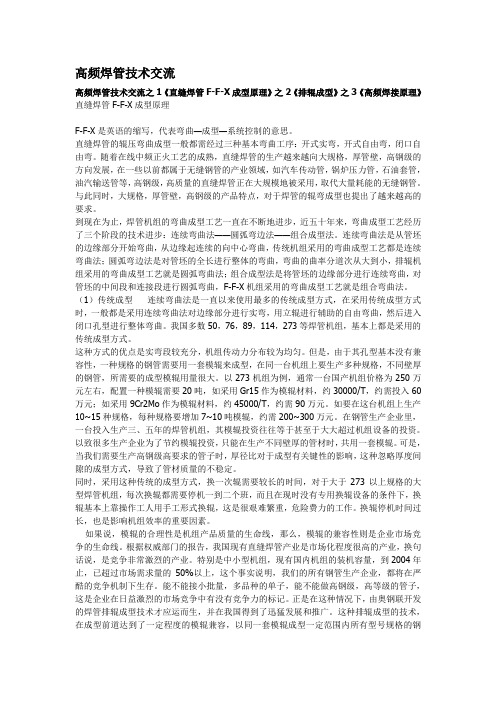
高频焊管技术交流高频焊管技术交流之1《直缝焊管F-F-X成型原理》之2《排辊成型》之3《高频焊接原理》直缝焊管F-F-X成型原理F-F-X是英语的缩写,代表弯曲—成型—系统控制的意思。
直缝焊管的辊压弯曲成型一般都需经过三种基本弯曲工序:开式实弯,开式自由弯,闭口自由弯。
随着在线中频正火工艺的成熟,直缝焊管的生产越来越向大规格,厚管壁,高钢级的方向发展,在一些以前都属于无缝钢管的产业领域,如汽车传动管,锅炉压力管,石油套管,油汽输送管等,高钢级,高质量的直缝焊管正在大规模地被采用,取代大量耗能的无缝钢管。
与此同时,大规格,厚管壁,高钢级的产品特点,对于焊管的辊弯成型也提出了越来越高的要求。
到现在为止,焊管机组的弯曲成型工艺一直在不断地进步,近五十年来,弯曲成型工艺经历了三个阶段的技术进步:连续弯曲法——圆弧弯边法——组合成型法。
连续弯曲法是从管坯的边缘部分开始弯曲,从边缘起连续的向中心弯曲,传统机组采用的弯曲成型工艺都是连续弯曲法;圆弧弯边法是对管坯的全长进行整体的弯曲,弯曲的曲率分道次从大到小,排辊机组采用的弯曲成型工艺就是圆弧弯曲法;组合成型法是将管坯的边缘部分进行连续弯曲,对管坯的中间段和连接段进行圆弧弯曲,F-F-X机组采用的弯曲成型工艺就是组合弯曲法。
(1)传统成型连续弯曲法是一直以来使用最多的传统成型方式,在采用传统成型方式时,一般都是采用连续弯曲法对边缘部分进行实弯,用立辊进行辅助的自由弯曲,然后进入闭口孔型进行整体弯曲。
我国多数50,76,89,114,273等焊管机组,基本上都是采用的传统成型方式。
这种方式的优点是实弯段较充分,机组传动力分布较为均匀。
但是,由于其孔型基本没有兼容性,一种规格的钢管需要用一套模辊来成型,在同一台机组上要生产多种规格,不同壁厚的钢管,所需要的成型模辊用量很大。
以273机组为例,通常一台国产机组价格为250万元左右,配置一种模辊需要20吨,如采用Gr15作为模辊材料,约30000/T,约需投入60万元;如采用9Cr2Mo作为模辊材料,约45000/T,约需90万元。
高频焊管制造技术的进步
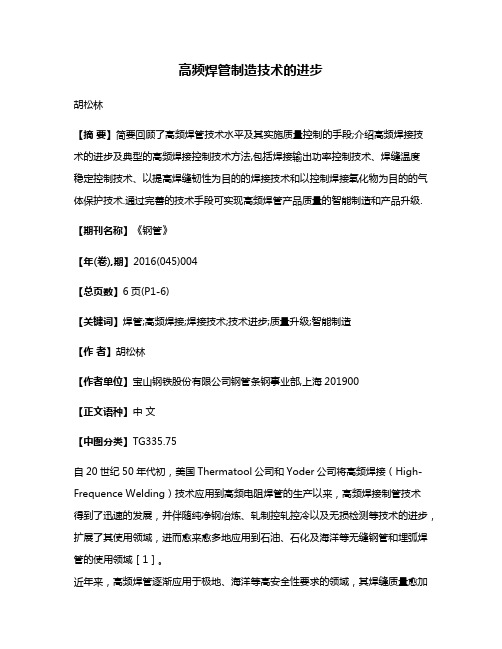
高频焊管制造技术的进步胡松林【摘要】简要回顾了高频焊管技术水平及其实施质量控制的手段;介绍高频焊接技术的进步及典型的高频焊接控制技术方法,包括焊接输出功率控制技术、焊缝温度稳定控制技术、以提高焊缝韧性为目的的焊接技术和以控制焊接氧化物为目的的气体保护技术.通过完善的技术手段可实现高频焊管产品质量的智能制造和产品升级.【期刊名称】《钢管》【年(卷),期】2016(045)004【总页数】6页(P1-6)【关键词】焊管;高频焊接;焊接技术;技术进步;质量升级;智能制造【作者】胡松林【作者单位】宝山钢铁股份有限公司钢管条钢事业部,上海201900【正文语种】中文【中图分类】TG335.75自20世纪50年代初,美国Thermatool公司和Yoder公司将高频焊接(High-Frequence Welding)技术应用到高频电阻焊管的生产以来,高频焊接制管技术得到了迅速的发展,并伴随纯净钢冶炼、轧制控轧控冷以及无损检测等技术的进步,扩展了其使用领域,进而愈来愈多地应用到石油、石化及海洋等无缝钢管和埋弧焊管的使用领域[1]。
近年来,高频焊管逐渐应用于极地、海洋等高安全性要求的领域,其焊缝质量愈加引起行业的重视,也使得高频焊接技术研究和质量控制手段的应用得以重视。
目前,国内高频焊管制造从规格和数量上都具备较强的生产能力,但在高频焊接技术研究及焊缝质量完整性控制技术方面尚有较大空缺。
了解掌握高频焊接控制技术,对提升高频焊管产品质量、拓宽产品应用具有积极的借鉴作用[2-3]。
1.1 高频焊管技术高频焊接制管是将带钢进行连续冷弯成型,然后在两边缘形成V形会合区域,通过施加高频感应电流来加热带钢边部到熔化状态,同时施加挤压力实现锻焊的一种焊管生产工艺过程。
高频焊接的质量受焊接装置、阻抗装置、冷却装置及现场操作等诸多因素的综合影响,对焊接过程单一要因的分析已难以实现现场质量的有效控制。
目前,在生产实际中,多凭借现场经验进行干预,结合在线检测和检(试)验来实现过程质量控制。
- 1、下载文档前请自行甄别文档内容的完整性,平台不提供额外的编辑、内容补充、找答案等附加服务。
- 2、"仅部分预览"的文档,不可在线预览部分如存在完整性等问题,可反馈申请退款(可完整预览的文档不适用该条件!)。
- 3、如文档侵犯您的权益,请联系客服反馈,我们会尽快为您处理(人工客服工作时间:9:00-18:30)。
焊机 功 率提 高到 7 0 0 k W ,提 高 了焊 接 速度 ,并 实现 了厚 壁 管 的焊接 。 而焊接 输 入 功率 自动 控 制 技 术 的 出现 ,提 高 了焊 缝质 量及 其稳 定性 。开始工 业性 生产低 合金 焊 管 。 高频焊 管诞 生之 初 ,焊接 质 量的检 查 和评 定一 直 由 肉眼人 工检 查 。进入 2 0世 纪 6 O年代 , 出现 了 各 种焊 缝无 损检 测技 术 和装 置 .诸 如 旋转 超声探 伤 、焊缝 跟踪 超 声探伤 、 涡流探 伤 、 电磁探 伤 等 。配 置 了这些焊 缝 无损检 测 装置 的生 产线 可 以更好 地保证 焊 管质 量的 可靠性 。 内毛 刺去 除技 术也 得 到 了完 善 .毛 刺去 除后 钢 管 内表 面质量 可 以通过 无损检 测 ,进 一步 增加 了焊 管 附加 值 。 多级 频 率 ( 1 8 O H z / 3 6 0 Hz ) 焊接 取 代 低 频 焊接 ( 6 0 H z ) 后 ,焊接 速 度 提 高到 了 4 0 ~ 6 0 m / m i n 。 高频 焊 接技 术应 用后 .在 很 多情 况 下焊接 速度 已经 不 再是 生产 速度 的瓶 颈 ,生产 速度 主 要 受 制 于其 他 因 素 。这 又 大大促 进 了 自动开卷 、 自动切 头对焊 、 自动化 活套 和 高速 飞锯技 术的发 展 ,呈 现 了高频 焊 管 生产技 术 的快速 发展 期 ,形成 了现代 焊管机 组 的基 本设备 组 成 。在 此相 互促 进 下 , 高频 焊 管生 产速 度 得 到迅速 提 高 ,小直 径机 组 生产速 度甚 至 高达 2 0 0 m / mi n 。 以活套技 术为例 。可以看到这 一 高频焊 管生产技 术快速发展 期 的轨 迹 。在 低频 焊接 年代 ,焊接速度 不 高 ,钢 管壁厚偏 薄 , 中小直径机 组 多采用地 坑式或 笼式活套 ,大 中直径机 组 经常没有 活套 。1 9 6 9年 , 美国A r m c o钢 铁公 司首 次开发 出了立 式螺 旋 活套 .后 K e n t 公 司购 买 了专利 授 权 ,经技 术改进 推 广 到 了全世界 。之 后 美国和 欧洲其 他公 司也 开发 出 了类似 活套 ,使得 螺 旋 活套成 为 了中小直 径 高频焊 管机 组 的标 准配 置 。直到 今 天 ,虽然 主要 采 用 水平螺 旋 活套 ,并 出现 了不 同的技 术 风格 ,但储 存 钢 带的基 本 原理 与 当时 的立式 活套 并无 差异 。 美 国为 高频 焊 管 生产 技 术 的 最初 发展 做 出 了重大 贡献 ,其 中著 名 的 公 司有 Y o d e r 公 司 、T h e r ma — t o o l 公 司、Ma c K a y公 司、A b b e y A e t n a公 司 以及 K e n t 公 司等 。 同期 或略微 滞 后 一些 ,欧 洲一 些 国 家也 在 完善 高频 管 生产 工 艺 、开发 生 产装 备 方 面取得 了业绩 ,如德 国著 名的 ME E R公 司于 1 9 6 1 年 完成 了 其 首条 高频 焊 管生产 线 的建设 。 日本在 从 美 国和 欧 洲 引进 高频 焊 管技 术 的基 础上 ,通过 消化 引进 和 自 主创 新 。到 7 0年代 后 一跃 成 为 高频 焊 管 生产大 国和技 术领 先 国家,其 经验 值得 我们 借鉴 。 2 0世 纪 6 O年代 末 、7 O年 代初 ,高频焊 管 生产 工艺基 本定 型 ,形成 了现 代 工 艺 : 自动 开卷一 自动 切 头对 焊一 螺旋 活套一 成 型一 焊接一 去 除 内外毛 刺一 焊缝探 伤一 定 径一 定尺 飞锯 切 断。尽 管后 来在成 型技 术 、飞锯 、探 伤技 术 等方 面均 有 突破性 进 步 .但 基本 的 工艺原 理 沿用至今 。 2 大 直径 高频 焊 管生产 技 术的 发展
焊管 史 话 之 二 十 二 高频 焊 接钢 管 生产 工 艺技 术 的成 熟
高频 焊接技 术起 始 于 2 0世 纪 5 0年代 ,成 熟 于 6 O 一7 0年代 ,历 经 1 0多年 的发 展 ,形 成 了完善 的
生产 工 艺 ,奠 定 了现 代 高频 焊 管 生产技 术 的基 础 。 自7 0年代 后 至 今 ,在 成 型 、焊接 、探 伤 等 多方 面 的技 术 虽均有发 展 和 突破 .但 高频焊 管 生产基 本 工艺并 无 大的 变化 。 1 高 频焊 管 生产工 艺技 术 的发展 历经 1 0多年发展 ,直到 2 0世 纪 ’ 6 0年代 末、7 0年代初 ,高频 焊管 生产技 术奠 定 了现代 工 艺基础 。 首先成 型技 术得 到 显著 改进 ,产 品 范 围向厚 壁 管和 薄壁 管均有 扩展 ,形成 了定 型 的 中小直径 焊 管
ME E R公 司于 1 9 6 0年 首 次提 供 一条 2 0 i n ( 5 0 8 m m) 机 组设 备 。 最早 的 大 中直径 电 阻焊管 成 型法诞 生于 美 国的笼 式成 型 ( 也称 为排 辊 成型 ) 技 术 ,首先 由 T o r r a n c e 机 械 工程 公 司开发 应 用 , 同期 Yo d e r 公 司也推 出 了类似 的笼 式成 型技 术 。该 成型技 术 采 用一 系列 密布
大直径 电阻焊 管机 组指 2 0 i n ( 5 0 8 mm) 以上机 组 。2 0世 纪 5 0年 代 末 、6 0年 代初 ,在 美国 、欧 洲
和 日本 .改造 扩建 或新 建 了一批 大 直径机 组 。Y o d e r 公 司 当时是 大 直径 高频 焊 管机 组 的先行 者 和 领先 设 备 供 应 商 ,后 Ma c K a y公 司和 A b b e y A e t n a公 司也 加入 了其行 列 ,均有 大机 组 的供 货 业绩 。德 国的