钢轨裂纹及断轨检测方法调研报告要点
关于铁路线路钢轨伤损的整治的调研报告

关于铁路线路钢轨伤损的整治的调研报告我于2009年12月至2010年1月份,在齐齐哈尔工务段齐线车间进行了关于铁路钢轨伤损整治的调查。
主要对象是铁路既有线路正线,站专线的线路。
通过这次调查活动我不仅掌握了很多铁路线路方面的资料和知识,而且咸受到了工作的辛苦,进一步了解了铁路线路养护任务,的好坏直接关系着维修投入与行车安全。
一、调查目的1 掌握钢轨及夹板伤损原因与整治。
2 掌握冬季钢轨三折分布及伤损原因3 加强冬季钢轨三折的检查与防护二、调查方法以现场实地检查的方法进行调查三、调研内容,过程及结论(一)概述齐齐哈尔工务段地处高寒地区,管内线桥设备陈旧老化、技术标准低,管辖的685.6km 嫩林正线,于1988年至1992年换轨大修,预应力钢筋混凝土枕代替了木枕,50kg25m轨取代了43kg25m轨,经过换轨大修,轨道结构强度大大增强,线路稳定性大幅度提高。
但随着运量的不断加大,列车速度的不断提高,运营十几年来,50kg钢轨及双头型夹板在冬季发生三折伤损较为严重,一旦发生,轻者将影响正常行车秩序,重者将导致机车脱轨造成车毁人亡。
因此分析线路设备在冬季发生三折伤损的原因,制定相应防范措施,延长使用寿命,提高设备质量,对确保行车安全有着重要意义。
(二)三折分布及伤损原因1 钢轨及夹板伤损部位和特点1.1 钢轨伤损部位和特点钢轨伤损包括核伤、横裂和垂裂,其部位均发生在钢轨头部和中央,就钢轨横裂和垂裂的横断面来看,均有5mm至20mm鱼鳞伤和剥落掉块的旧痕,绝大多数发生在钢轨顶部边缘,检查时容易发现。
而核伤多发生在钢轨内部,早期的小核伤因回波位移小,与干扰的回波混杂其中,而难以分辩,检查时不容易发现。
(1)特别是钢轨接头部位,如钢轨接头轨缝过大、错牙、折角破坏了轨道的连续性,改变了车轮瞬时转动中心,致使车轮产生了一个较大的瞬时加速度,从而增加了轨道的附加冲击力。
据计算,速度为100km/h的车辆,通过1.0mm迎轮错牙(P60钢轨),附加应力为608.8kN,通过轨缝为14mm接头时,附加应力为148.3kN,通过折角为0.025弧度的接头时,附加应力为380kN。
高速列车钢轨缺陷检测与预防技术研究

高速列车钢轨缺陷检测与预防技术研究摘要:高速列车的安全性对于铁路运输系统来说至关重要。
钢轨作为承载列车的主要结构之一,其质量和完整性对列车行驶的稳定性和安全性起着至关重要的作用。
因此,钢轨缺陷的检测与预防技术的研究成为提高高速列车系统安全性的关键。
1. 引言高速列车作为现代铁路交通系统的重要组成部分,在人们的日常生活中起着至关重要的作用。
随着铁路系统的发展和技术的进步,高速列车系统的速度和荷载都得到了大幅提升。
因此,高速列车行驶过程中的安全性成为人们关注的焦点。
2. 钢轨缺陷的类型和危害钢轨的缺陷种类繁多,包括疲劳裂纹、磨损、损伤、变形等。
这些缺陷会导致列车行驶时的不稳定性和安全隐患。
严重的缺陷可能导致钢轨断裂,造成严重的事故和人员伤亡。
3. 钢轨缺陷检测技术为了保证高速列车系统的安全性,钢轨缺陷的准确检测起着至关重要的作用。
传统的钢轨缺陷检测方法主要包括人工观察和机车运行检测。
然而,这些方法都存在许多缺点,如主观性高、效率低、依赖人力等。
因此,研究人员开发了一系列先进的钢轨缺陷检测技术,包括超声波检测、磁粉检测、激光检测等。
这些技术通过利用声波、磁力和光学原理,能够实时、准确地检测出钢轨的缺陷。
4. 钢轨缺陷预防技术除了及时检测钢轨缺陷外,预防钢轨缺陷的发生也是提高列车系统安全性的重要措施之一。
钢轨缺陷的主要原因之一是疲劳裂纹的产生,其主要是由于列车荷载和频繁的振动引起的。
因此,减小列车荷载和振动是预防钢轨缺陷的关键。
目前,研究人员已经提出了一些钢轨缺陷预防技术,如减轻列车荷载、改进钢轨设计和使用材料等。
这些技术能够减少钢轨的受力情况,提高钢轨的抗疲劳性能。
5. 高速列车钢轨缺陷检测与预防技术的应用高速列车的运行速度和损伤程度使得钢轨缺陷的检测与预防技术成为保证列车行驶安全的必备措施。
目前,我国的高速列车系统已经采用了一系列先进的钢轨缺陷检测与预防技术,如超声波检测技术和应力分析技术等。
这些技术能够对高速列车运行过程中的钢轨缺陷进行实时监测和预警,确保列车的行驶安全。
城轨检修调研报告

城轨检修调研报告城轨检修调研报告一、调研目的本次调研旨在了解当前城轨检修工作的现状和存在的问题,为城轨运行做出科学的调整和优化。
二、调研内容1. 检修工作流程:了解城轨检修的工作流程和各个环节的操作流程。
2. 检修设备和工具:调研城轨检修所需的设备和工具,包括仪器设备、维修工具等。
3. 人员配置和培训:了解城轨检修人员的配置情况,以及培训机制和培训内容。
4. 检修标准与要求:调研城轨检修的相关标准和要求,包括维修质量的评定标准等。
三、调研结果分析1. 检修工作流程:根据调研结果,发现目前城轨检修工作存在着流程不够规范、环节不够清晰的问题。
建议制定详细的检修工作流程,并加强对操作人员的培训和指导。
2. 检修设备和工具:通过调研发现,城轨检修设备和工具不够齐全,且部分工具存在老化和损坏的情况。
建议采购先进的检修设备和工具,并定期检修和更换。
3. 人员配置和培训:根据调研结果,城轨检修的人员配置合理,但部分操作人员缺乏相关技能和经验。
建议加强对检修人员的培训和考核机制,提高其专业水平。
4. 检修标准与要求:调研结果显示,城轨检修的标准和要求不够明确,导致维修质量无法保证。
建议制定详细的检修标准和要求,并建立完善的质量评估体系。
四、改进措施1. 完善检修工作流程:制定详细的检修工作流程,明确各个环节的操作流程和责任分工。
加强对操作人员的培训和指导,确保工作流程的规范和顺畅。
2. 更新检修设备和工具:定期对检修设备和工具进行检修和更换,确保其正常使用。
同时加强对设备和工具的维护和保养,延长其使用寿命。
3. 加强人员培训和考核:加强对检修人员的技能培训和知识普及,提高其专业水平。
建立考核机制,对人员进行绩效评估,激励其积极主动参与检修工作。
4. 制定详细的检修标准和要求:制定明确的检修标准和要求,明确维修质量的评定标准。
建立质量评估体系,对检修工作进行监督和评估。
五、总结通过本次调研,我们了解到城轨检修工作存在的问题,并提出了相应的改进措施。
道岔钢轨的故障诊断与维修方法探讨

道岔钢轨的故障诊断与维修方法探讨道岔是铁路线路的重要部分,用于实现列车的转向和换线。
钢轨则是道岔的关键组件,承受着列车的重量和运行力。
然而,由于长时间的使用和环境的影响,道岔钢轨会出现各种故障,影响列车的正常运行。
本文将探讨道岔钢轨的故障诊断与维修方法,以提高铁路线路的安全和可靠性。
首先,对于道岔钢轨的故障诊断,我们可以采用以下几种方法。
首先,观察道岔钢轨的外观。
检查是否有明显的裂缝、变形或磨损等情况,这些都可能是道岔钢轨故障的表现。
其次,使用无损检测方法,如超声波、磁粉探伤等,对道岔钢轨进行全面的检测,以寻找隐藏的缺陷。
此外,还可以使用振动检测技术,通过检测道岔钢轨的振动特征来判断是否存在故障。
最后,可以利用红外热像仪等设备,检测道岔钢轨的温度分布情况,以发现异常情况。
一旦发现道岔钢轨存在故障,我们需要采取相应的维修方法来修复它。
首先,对于裂缝或变形等较小的故障,可以使用焊接或钢筋补强的方法进行修复。
这样可以使道岔钢轨恢复到正常的形状和强度。
如果裂缝较大或变形严重,则需要更换道岔钢轨。
在更换道岔钢轨时,需要注意对道岔其他部件的拆解和安装,以确保整个道岔系统的正常运行。
除了故障诊断和维修方法,我还想提到一些预防措施,以减少道岔钢轨的故障发生。
首先,定期检查和维护道岔钢轨,及时发现和修复潜在的故障。
其次,加强对道岔钢轨使用环境的管理,如控制草木的生长、防止泥土和石块进入轨道等。
此外,可以采用防腐、防锈等技术手段,延长道岔钢轨的使用寿命。
最后,使用先进的监测技术,如智能传感器和远程监控系统,实时监测道岔钢轨的运行状态,及时发现故障。
综上所述,道岔钢轨的故障诊断与维修是确保铁路线路安全和可靠的重要环节。
通过采用各种故障诊断方法,包括外观检查、无损检测、振动检测和红外热像仪等,我们可以及时发现道岔钢轨的故障。
对于不同类型的故障,可以采用焊接、钢筋补强或更换道岔钢轨的方法进行维修。
此外,预防措施也是至关重要的,包括定期检查和维护、环境管理、防腐和使用先进的监测技术等。
浅谈铁路线路钢轨设备伤损主要类型及检测方法

浅谈铁路线路钢轨设备伤损主要类型及检测方法铁路线路是现代交通运输的重要组成部分,它承担着连接城市与城市、地区与地区的重要任务。
而铁路线路的钢轨设备作为铁路运输的基础设施,其安全性和稳定性至关重要。
由于长期的使用和自然因素的影响,钢轨设备难免会出现损伤。
及时发现并修复钢轨设备的损伤对于保障铁路线路的安全和畅通具有重要意义。
本文将就铁路线路钢轨设备的损伤主要类型及检测方法进行探讨。
1. 疲劳裂纹疲劳裂纹是由于轮轨交会反复作用下引起的,通常出现在轨道的压应力和拉应力交替作用的地方,是铁路线路钢轨设备的常见损伤。
疲劳裂纹的存在会导致钢轨设备的强度下降,如果不及时修复会引发更严重的安全隐患。
2. 磨耗磨耗是指钢轨设备在使用过程中,由于轮轨间的摩擦作用,导致表面金属材料的逐渐流失。
磨耗会引起钢轨设备的几何形态发生变化,进而影响其使用寿命和安全性。
3. 变形变形是指钢轨设备在运行过程中由于受到外力作用或者自身质量和温度引起的形状改变。
变形会导致钢轨设备的受力状态发生变化,进而影响其安全性和稳定性。
4. 腐蚀腐蚀是指钢轨设备在使用过程中,由于大气、水分、化学物质等外界环境因素的影响,导致金属材料发生化学反应而引起的损伤。
腐蚀会导致钢轨设备的强度和稳定性下降,严重时甚至会影响使用寿命。
1. 目视检查目视检查是最基础的检测方法,通过铁路工作人员巡视铁路线路,发现可能存在的钢轨设备损伤。
目视检查通常是靠经验进行的,需要高度的警惕性和责任心。
目视检查存在局限性,不能发现微小和隐蔽的损伤。
2. 超声波检测超声波检测是一种非破坏性的检测方法,通过超声波技术对钢轨设备的内部进行检测。
超声波可以穿透金属材料,当遇到内部缺陷时会发生反射。
通过分析超声波的反射信号,可以确定钢轨设备的损伤情况和位置。
3. 磁粉检测磁粉检测是一种常用的表面缺陷检测方法,通过在钢轨设备表面喷洒磁粉,并施加磁场,当表面存在裂纹和其他缺陷时,磁粉会在这些缺陷处聚集形成磁束。
钢轨探伤漏检螺孔裂纹的原因分析和应对措施

钢轨探伤漏检螺孔裂纹的原因分析和应对措施摘要:在钢轨检测过程中,充分合理利用超声波进行检测,具有其自身的独特优势,主要是通过声学原理,避免在实质性上损坏钢轨,而且检测结果的准确性非常高。
据此,本文主要对钢轨超声波探伤漏检的原因进行了详细分析,并提出了一些有效的改进措施。
关键词:钢轨;超声波;探伤;漏检前言现阶段,利用超声波探伤技术在钢轨检测中的应用越来越深入和广泛,其主要原理是利用声学原理,对物体内部所具有的声学特征和性质对超声波传播带来影响作为检测的基础所在。
超声波检测技术不会对材料带来实质的破坏,可以在保证材料完整性的基础上对材料内部和表面的缺陷大小、形状和分布状况进行检测。
采用超声波检测可以有效确保设备材料的可靠性,以保证其品质。
目前,正是由于超声波探伤技术所具有的安全、可靠等一系列明显优势,使得其在国内外获得了非常广泛的应用。
目前使用的超声波探伤仪种类非常繁多,其中尤以脉冲反射式超声波探伤仪应用最为深入和广泛。
通常情况下,对于均匀的材料中,如果存在缺陷就会造成材料的不连续性,而该种不连续性又会造成声阻抗的不一致,根据反射定律,超声波在两种不同声阻抗的介质的交界面上将会发生反射,反射回来的能量的大小与交界面两边介质声阻抗的差异和交界面的取向、大小有关。
1钢轨使用过程中容易出现的缺陷钢轨容易出现损伤过程主要是钢轨制造以及安装焊接、列车车轮频繁的冲击力和载荷以及所处的环境因素等。
钢轨制造以及安装焊接采用的材料不恰当、焊接母材选取不合适、制造工艺以及焊接工艺不合理等,钢轨就容易出现微裂纹、灰板、焊接点脱落、鱼鳞纹以及掉块等损伤。
由于列车承重量大以及运输次数的频繁,钢轨可能发生擦伤、剥离掉块、变形以及滚动接触疲劳损伤等缺陷,在外界环境的影响下,雨水浸湿、氧化腐蚀钢轨。
总之,对于钢轨运作过程中,铁路相关部门应做好钢轨施工质量的监督和后续的检测以及保护,以避免因钢轨的伤损而发生安全事故。
2钢轨探伤技术的应用目前,钢轨无损探伤技术主要有超声波无损探伤、射线无损探伤、激光无损探伤、渗透无损探伤、目视无损探伤、涡流无损探伤等。
关于铁路工务钢轨探伤工作的探讨

关于铁路工务钢轨探伤工作的探讨摘要:铁路工务钢轨探伤是维护铁路安全的一项重要工作。
由于铁路工务钢轨长期受到列车的载荷和气候环境等因素的影响,容易发生裂纹、断裂和疲劳等问题,钢轨探伤工作能及时发现钢轨、道岔的损伤情况,并进行修复,是确保线路车辆正常运行和行车安全的重要保障。
若钢轨出现任何问题,都会对列车的行车安全造成极大影响。
本文将对铁路线路维修检测中钢轨探伤工作进行分析和讨论。
关键词:铁路公务;钢轨探伤;工作探讨引言:随着当前社会经济的进步,出行的次数、出行人数等运输量的大幅度增加,传统的钢轨探伤模式已无法满足铁路飞速发展的要求。
如何科学化、合理化、高效化提高钢轨探伤质量成为了当今社会迫在眉睫的话题。
目前在检修线路过程中,需要运用到更好更先进的检测技术。
而铁轨探伤拥有高灵敏度、低损伤等优点,在铁路检测中被广泛运用。
1铁路工务钢轨工作的探讨1.1 工务钢轨探伤的方法探伤方法主要有目测检查和无损检测两种。
目测检查主要是通过人工目测来判断钢轨表面是否有明显的损伤或者裂缝。
这种方法虽然简单易行,但耗时时间和精力,并且仅凭肉眼不能发现轨轮磨损等一些隐蔽的问题。
而无损检测方法则利用声波、磁力等物理原理,通过检测钢轨表面的声波振动和磁场分布,来发现钢轨内部的缺陷和损伤。
其中,声波探伤技术是一种较为常用的无损检测方法。
该方法是利用超声波在试件中传播的特性,探测和测量缺陷和材料性能的方法。
在声波探伤的过程中,先将超声波发射器放置在被检测的钢轨表面上,然后测量超声波的散射情况和信号强度等参数,以判断钢轨内部是否存在裂纹等损伤。
此外,还可以通过磁粉探伤、涡流探伤等方法来对钢轨进行无损检测。
对于铁路工务钢轨的探伤工作,不同的检测方式互相配合,可以更全面、更准确地发现钢轨中存在的问题,并做出及时的维修或更换。
1.2 轨底部位的探测1.2.1 探测和定位在对轨道底部进行损伤探测时,主要使用0°探头对钢轨出现的裂痕进行探测。
钢轨裂纹及断轨检测方法调研报告要点

钢轨裂纹及断轨检测方法调研报告在铁路运输系统中,钢轨起着支撑列车和引导车辆车轮前进的作用。
如果出现钢轨断裂将有可能造成列车出轨、倾覆等重大行车安全事故,造成人员伤亡和巨额财产损失。
因此钢轨伤损检测越来越受到人们的重视。
表1所示为近些年由于钢轨断裂造成的列车行车事故。
表1 近些年钢轨断裂造成的列车行车事故时间地点伤损情况2001年3月18日美国爱荷华州钢轨断裂引起列车脱轨,造成1人死亡96人受伤2007年10月17日伦敦钢轨断裂引发列车脱轨,造成4人死亡、70人受伤、4人重伤2009年4月7日河北野三坡钢轨断裂导致6节车厢脱轨同时,随着国家高速铁路和重载铁路的发展,钢轨受到挤压和冲击的程度越来越大,钢轨发生损伤的概率也在提高。
因此,为保证高速铁路和重在铁路的运营安全性,钢轨裂纹检测成为铁路运营部门十分重视的事情。
目前,钢轨的主要检测方式分为周期性探伤检测和实时断轨监测。
周期性钢轨探伤检测包括人工巡轨检测、大型钢轨探伤车、漏磁信号、涡流探伤、激光超声、图像处理等;实时断轨监测技术包括轨道电路实时断轨检测技术、牵引回流实时断轨检测技术、光纤实时断轨检测技术和超声波实时断轨监测技术等。
1 周期性检测技术周期性检测技术就是定期对钢轨进行检测,国内外都针对不同轨道、不同检测设备制定了检测周期和检测作业标准。
总体上说,周期性检测设备精确度高,能及时发现钢轨早期裂纹,以避免发生重大交通事故;但是它需要占用较多天窗时间。
1.1 探伤小车中国铁路广泛使用的是钢轨探伤小车,它将小型超声波钢轨探伤仪装在特制的手推车上,如图1所示。
通过人工手推进行钢轨损伤的检测,它耗费大量人力物力、检查结果主观性强、检查周期长、效率低下、速度慢,无法做到对钢轨伤损情况实时检测,不能适应于我国日益发展的高速铁路事业[1-2]。
近年来,随着钢轨裂纹导致脱轨事故的频发,为了加强钢轨安全监测,欧美也开始研发使用这种便携式钢轨探伤仪[3]。
由于超声波探伤技术比较成熟,成本比较低,且随着科技的发展,以前只有大型探伤车才具备的A/B超同屏显示、鱼鳞纹下核伤判别、探伤数据储存、探伤作业信息记录、探伤数据计算机管理等五大功能正移植到探伤小车身上,在各钢轨探伤仪器生产商当中,超声探伤小车倍受青睐。
钢轨特殊伤损检测研究

钢轨特殊伤损检测研究摘要:本文对钢轨特殊伤损检测进行了综合论述,包括常见伤损类型、检测技术以及优化措施。
在伤损类型方面,裂纹伤损、磨耗伤损和腐蚀伤损被详细讨论,强调了它们对铁路系统安全性的潜在威胁。
在检测技术方面,超声波检测、磁粉检测、热成像技术等五种方法被阐述,强调了它们的原理和应用。
最后,针对伤损检测的优化措施还待进一步展开研究。
通过本文的综合论述,有望为铁路系统的安全性和可靠性提供更有效的伤损检测和维护策略。
关键词:钢轨;伤损检测;裂纹伤损;磨耗伤损;腐蚀伤损;超声波检测;磁粉检测;热成像技术引言钢轨作为铁路系统的基础组成部分,承受着列车的巨大重量和运行速度,因此容易受到各种伤损的影响。
这些伤损类型包括裂纹、磨耗和腐蚀,它们可能对铁路系统的安全性和性能构成潜在威胁。
因此,及时的伤损检测和维护至关重要。
本文将首先对钢轨常见伤损类型进行详细探讨,然后介绍多种伤损检测技术,包括超声波检测、磁粉检测、热成像技术等。
最后,将探讨如何优化伤损检测措施,以提高铁路系统的安全性和可靠性。
1钢轨常见伤损类型1.1裂纹伤损裂纹伤损是钢轨常见的伤损类型之一,具有潜在的安全风险。
这种类型的伤损通常源于多种复杂原因。
首先,裂纹的形成与应力集中密切相关。
在铁路系统中,列车的重量和速度在轨道上产生巨大的应力,而这些应力往往会在轨道的特定部位积聚,如轨道接头或材料存在缺陷的地方。
这种应力集中可能导致裂纹的初始形成。
其次,材料疲劳也是裂纹伤损的重要原因之一。
由于列车的不断往返运行,轨道材料可能会逐渐疲劳,导致微小裂纹的逐渐扩展。
这些微小裂纹可能会随着时间的推移而变得更加严重,最终引发裂纹伤损。
此外,制造过程中的缺陷也可能在使用中导致裂纹伤损。
如果在轨道材料的制造过程中存在材料缺陷或工艺问题,这些问题可能会在使用中逐渐演化成裂纹。
因此,裂纹伤损的检测和监测对于铁路系统的安全至关重要。
非破坏性检测技术如超声波检测和磁粉检测被广泛用于检测裂纹伤损,以便及时发现并采取维护措施,以防止进一步的损坏和潜在的事故发生。
钢轨损伤检测方法及数据分析技术研究

钢轨损伤检测方法及数据分析技术研究随着铁路运输的发展和扩大,铁路运输设备的安全问题越来越受到重视。
其中,钢轨作为铁路上的重要运输设备,其损坏情况对铁路运输的安全和稳定性产生了重要影响。
因此,如何及时、准确地检测和分析钢轨的损伤情况,成为当前研究和实践的热点问题。
钢轨损伤检测方法主要有目视检查、物理检测、无损检测等。
目视检查是传统的钢轨损伤检测方法,在铁路检测中应用广泛。
物理检测方法包括冲击测试法、振动测试法、声音检测法等。
无损检测方法是一种非接触式检测方法,包括超声波检测、磁粉检测、涡流检测等多种技术。
从方法本身来看,无损检测技术是当前钢轨损伤检测的主流技术之一。
其原理是基于电磁感应、超声波、磁力线等物理原理实现对钢轨内部和表面缺陷的自动检测。
与目视检查、物理检测等传统重复劳动方法相比,无损检测技术具有检测快速、准确性高、自动化程度高等显著优点。
钢轨损伤检测的数据分析技术是无损检测技术的重要组成部分,其目的是通过对检测数据的分析和处理,确定钢轨的损伤位置、类型和严重程度,以便进行钢轨维修和更换,提高铁路运输设备的安全性和稳定性。
一般来说,数据分析技术包括信号处理、特征提取和分类识别三个主要步骤。
信号处理是对检测数据进行预处理、去噪等处理,以获得更好的信号质量。
特征提取是对处理后的数据进行特征量计算和模型建立,以便于找到钢轨损伤的具体位置和类型。
分类识别是对特征量进行分类,以确定钢轨损伤的严重程度和质量。
钢轨损伤检测方法和数据分析技术的研究已在国际上发展了几十年,不断涌现了一大批优秀的研究成果。
但目前国内对于钢轨损伤检测技术和数据分析技术还不够重视和深入。
未来,我国需要进一步加强基础研究和科技攻关,探索和开发更加高效、精准的钢轨损伤检测方法和数据分析技术。
此外,需要加快推广和应用,提高铁路运输安全保障的水平,推进国家经济和社会的可持续发展。
综上所述,钢轨损伤检测方法和数据分析技术是铁路运输安全保障的重要组成部分。
钢轨轨头裂纹分析

道岔钢轨轨头裂纹缺陷分析+送样单位:一、来样情况材质为YH20的道岔钢钢轨使用一段时间后,在轨头踏面两侧距边缘约5毫米处,分布着两条纵向线状裂缝(图1、2)。
图1、道岔钢轨轨头裂纹整体形貌图2、道岔钢轨轨头局部裂纹形貌二、缺陷分析在裂纹处取横向金相试样,经磨制、抛光、显微镜下观察后发现:裂纹开口较大,其中尾段分叉,尾部尖细并向基体内部延伸;深度约为0.64毫米(图3、4)。
缺陷处无大型非金属夹杂物、无高温氧化现象;基体的非金属夹杂物级别为A:0,0.5;B:0,0;C:0,0;D:0.5,1.0,钢质纯净度好。
图3、裂纹整体形貌(12.5×)图4、裂纹中尾段形貌(50×)经4%的硝酸酒精水溶液腐蚀后,显示裂纹旁侧的金相组织为回火屈氏体+面积百分比约3%的回火贝氏体;基体金相组织为回火屈氏体+部分回火贝氏体,其中距表面约5毫米处金相组织中回火贝氏体的面积百分比约为18%。
随着与表面距离的增加,基体金相组织中回火贝氏体的面积百分比也相应增加。
裂纹旁侧与基体之间无明显的成分偏析。
裂纹旁侧与基体金相组织中回火贝氏体含量的差别缘于其热处理淬火冷速的不同。
在裂纹旁侧未发现明显脱碳现象(图5-8)。
图5、裂纹周围的金相组织(100×)图6、裂纹旁侧的金相组织(500×)回火贝氏体图7、基体金相组织(100×)图8、基体金相组织(500×)经饱和苦味酸水溶液腐蚀后,显示该试样的原奥氏体晶粒度为7.0-7.5级(图9)。
图9、试样的原奥氏体晶粒度(100×)三、分析讨论1、缺陷处无大型非金属夹杂物,钢质纯净度好。
说明该裂纹的产生与非金属夹杂物无关。
2、缺陷处无高温氧化现象,未发现明显脱碳现象,说明该裂纹非锻造裂纹所致。
3、缺陷形态呈非锯齿状、裂纹处未发现明显氧化现象,说明该裂纹非淬火裂纹所致。
综上所述,该道岔钢轨裂纹是在使用过程中所形成的钢轨轨头滚动接触疲劳裂纹。
钢轨出厂检验报告
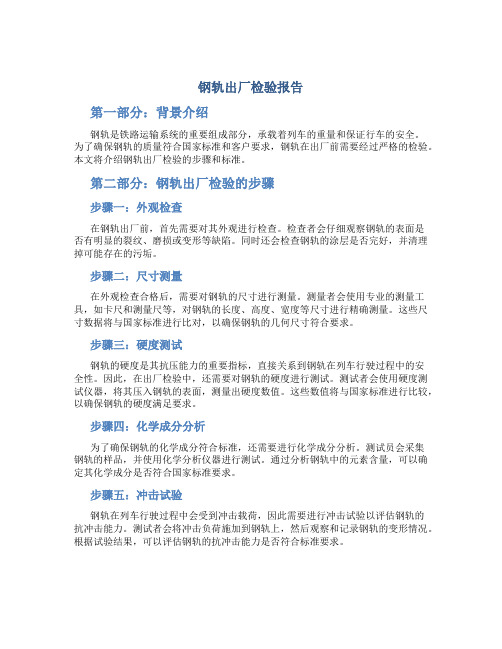
钢轨出厂检验报告第一部分:背景介绍钢轨是铁路运输系统的重要组成部分,承载着列车的重量和保证行车的安全。
为了确保钢轨的质量符合国家标准和客户要求,钢轨在出厂前需要经过严格的检验。
本文将介绍钢轨出厂检验的步骤和标准。
第二部分:钢轨出厂检验的步骤步骤一:外观检查在钢轨出厂前,首先需要对其外观进行检查。
检查者会仔细观察钢轨的表面是否有明显的裂纹、磨损或变形等缺陷。
同时还会检查钢轨的涂层是否完好,并清理掉可能存在的污垢。
步骤二:尺寸测量在外观检查合格后,需要对钢轨的尺寸进行测量。
测量者会使用专业的测量工具,如卡尺和测量尺等,对钢轨的长度、高度、宽度等尺寸进行精确测量。
这些尺寸数据将与国家标准进行比对,以确保钢轨的几何尺寸符合要求。
步骤三:硬度测试钢轨的硬度是其抗压能力的重要指标,直接关系到钢轨在列车行驶过程中的安全性。
因此,在出厂检验中,还需要对钢轨的硬度进行测试。
测试者会使用硬度测试仪器,将其压入钢轨的表面,测量出硬度数值。
这些数值将与国家标准进行比较,以确保钢轨的硬度满足要求。
步骤四:化学成分分析为了确保钢轨的化学成分符合标准,还需要进行化学成分分析。
测试员会采集钢轨的样品,并使用化学分析仪器进行测试。
通过分析钢轨中的元素含量,可以确定其化学成分是否符合国家标准要求。
步骤五:冲击试验钢轨在列车行驶过程中会受到冲击载荷,因此需要进行冲击试验以评估钢轨的抗冲击能力。
测试者会将冲击负荷施加到钢轨上,然后观察和记录钢轨的变形情况。
根据试验结果,可以评估钢轨的抗冲击能力是否符合标准要求。
第三部分:钢轨出厂检验的标准外观标准钢轨的外观应该没有明显的裂纹、磨损、变形等缺陷。
涂层应该完好,表面应该清洁。
尺寸标准钢轨的长度、高度、宽度等尺寸应该符合国家标准要求。
硬度标准钢轨的硬度应该在一定的范围内,以保证其抗压能力。
化学成分标准钢轨的化学成分应符合国家标准要求,其中碳含量、硅含量、锰含量等元素的含量应在一定的范围内。
冲击试验标准钢轨在冲击试验中应具有一定的变形能力,但不能发生严重的破坏。
U75V钢轨疲劳裂纹扩展行为研究的开题报告

U75V钢轨疲劳裂纹扩展行为研究的开题报告
一、课题背景:
U75V钢轨作为铁路线路上的重要构件,其安全性问题一直备受关注。
钢轨在使用过程中会受到多种因素的影响,如运输载荷、温度变化、车
辆频率等,这些因素都会影响钢轨的耐久性能。
钢轨裂纹是钢轨疲劳失
效的主要形式之一,其对铁路行车安全和铁路建设的长期稳定运营都会
产生严重影响,因此开展U75V钢轨疲劳裂纹扩展行为研究具有重要意义。
二、研究内容:
本课题拟从U75V钢轨材料组织性能、载荷条件、磨损情况等多个
方面入手,研究U75V钢轨疲劳裂纹扩展行为的规律。
1、采用扫描电镜等方法对U75V钢轨的组织结构进行观察和分析,探究组织结构与钢轨裂纹扩展行为的相关性。
2、在实验室条件下,通过疲劳试验进行疲劳应力历程加载,研究
U75V钢轨在实际运行条件下的疲劳裂纹扩展行为规律。
3、采用数值仿真方法对U75V钢轨的应力分布及应力集中区域进行模拟分析,得出U75V钢轨在载荷条件下的裂纹扩展规律。
4、结合实验数据和数值仿真结果,综合分析U75V钢轨疲劳裂纹扩展行为的影响因素,探究影响因素之间的相互关系及作用机理。
三、研究意义:
通过本课题的研究,深入了解U75V钢轨疲劳裂纹扩展行为的规律,为提高U75V钢轨的使用寿命和安全性能,优化铁路线路运行和维护管理提供科学依据。
同时,本课题的研究方法和分析手段也具有良好的推广
价值,可为其他材料的疲劳裂纹扩展行为研究提供参考。
浅谈铁路线路钢轨设备伤损主要类型及检测方法
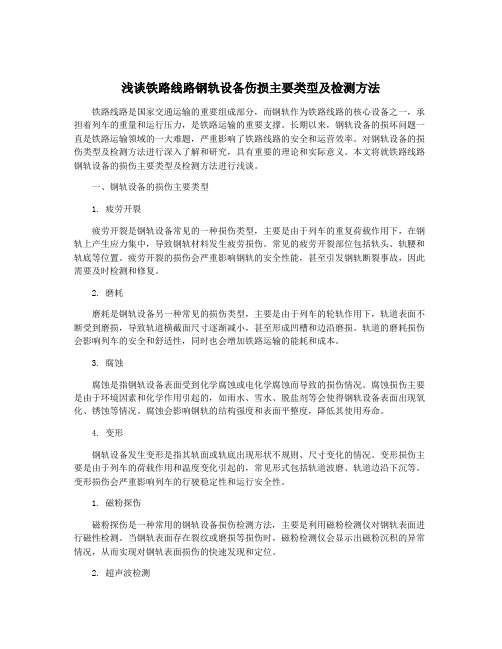
浅谈铁路线路钢轨设备伤损主要类型及检测方法铁路线路是国家交通运输的重要组成部分,而钢轨作为铁路线路的核心设备之一,承担着列车的重量和运行压力,是铁路运输的重要支撑。
长期以来,钢轨设备的损坏问题一直是铁路运输领域的一大难题,严重影响了铁路线路的安全和运营效率。
对钢轨设备的损伤类型及检测方法进行深入了解和研究,具有重要的理论和实际意义。
本文将就铁路线路钢轨设备的损伤主要类型及检测方法进行浅谈。
一、钢轨设备的损伤主要类型1. 疲劳开裂疲劳开裂是钢轨设备常见的一种损伤类型,主要是由于列车的重复荷载作用下,在钢轨上产生应力集中,导致钢轨材料发生疲劳损伤。
常见的疲劳开裂部位包括轨头、轨腰和轨底等位置。
疲劳开裂的损伤会严重影响钢轨的安全性能,甚至引发钢轨断裂事故,因此需要及时检测和修复。
2. 磨耗磨耗是钢轨设备另一种常见的损伤类型,主要是由于列车的轮轨作用下,轨道表面不断受到磨损,导致轨道横截面尺寸逐渐减小,甚至形成凹槽和边沿磨损。
轨道的磨耗损伤会影响列车的安全和舒适性,同时也会增加铁路运输的能耗和成本。
3. 腐蚀腐蚀是指钢轨设备表面受到化学腐蚀或电化学腐蚀而导致的损伤情况。
腐蚀损伤主要是由于环境因素和化学作用引起的,如雨水、雪水、脱盐剂等会使得钢轨设备表面出现氧化、锈蚀等情况。
腐蚀会影响钢轨的结构强度和表面平整度,降低其使用寿命。
4. 变形钢轨设备发生变形是指其轨面或轨底出现形状不规则、尺寸变化的情况。
变形损伤主要是由于列车的荷载作用和温度变化引起的,常见形式包括轨道波磨、轨道边沿下沉等。
变形损伤会严重影响列车的行驶稳定性和运行安全性。
1. 磁粉探伤磁粉探伤是一种常用的钢轨设备损伤检测方法,主要是利用磁粉检测仪对钢轨表面进行磁性检测。
当钢轨表面存在裂纹或磨损等损伤时,磁粉检测仪会显示出磁粉沉积的异常情况,从而实现对钢轨表面损伤的快速发现和定位。
2. 超声波检测超声波检测是一种通过超声波对钢轨内部进行检测的方法,可以有效发现钢轨内部的裂纹、变形等损伤情况。
铁路铁轨裂纹检测技术的研究与应用

铁路铁轨裂纹检测技术的研究与应用铁路铁轨作为重要的交通基础设施,在运行过程中裂纹的产生对运输安全和运行效率都会带来严重影响。
因此,铁路铁轨裂纹检测技术的研究和应用显得尤为重要。
本文将从裂纹检测技术的意义、常见的铁路铁轨裂纹检测方法以及新兴的无损检测技术等方面进行论述。
1. 裂纹检测技术的意义铁路铁轨上的裂纹问题一直以来都是一个非常严重的技术难题。
裂纹的产生可能来自多种因素,如材料的疲劳、应力过大等。
裂纹可能会导致铁轨的损坏,进而引发事故的发生。
因此,建立有效的裂纹检测技术,可以及早发现裂纹并采取相应的修复措施,保障铁路运输的安全和畅通。
2. 常见的铁路铁轨裂纹检测方法2.1 目视检测目视检测是最为传统和简单的裂纹检测方法,它主要通过人工观察铁轨表面是否存在裂纹来进行判断。
然而,这种方式存在主观性较强以及工作效率低下的问题。
2.2 磁粉探伤磁粉探伤是一种常用的有接触式检测技术。
通过将铁轨表面涂抹上磁粉,然后通过磁场引入裂纹,通过观察磁粉沉积的情况来判断是否存在裂纹。
这种方法依然需要人工参与,且对设备和技术要求较高,操作也较为复杂。
2.3 超声波检测超声波检测是一种非接触式的无损检测技术,通过发送超声波信号,并接收其回波来检测材料内部的裂纹情况。
这种方法具有高效、精确的特点,并且能够自动化进行,因此被广泛应用于铁路铁轨裂纹检测中。
3. 新兴的无损检测技术近年来,随着科技的不断进步,越来越多的新兴无损检测技术应用于铁路铁轨裂纹检测中。
3.1 热红外检测技术热红外检测技术基于物体的热辐射特性,通过对铁轨表面温度的监测,可以检测出表面存在的裂纹。
它具有高效、迅速的特点,并且能够在运营状态下进行检测,极大地提高了检测的效率。
3.2 激光光纤传感技术激光光纤传感技术通过在铁轨表面安装激光光纤传感器,通过光纤的变形来判断铁轨表面是否存在裂纹。
这种技术具有高灵敏度、高精度的特点,并且可以实时监测裂纹的扩展情况。
4. 综合应用与发展趋势目前,针对铁路铁轨裂纹检测技术,一般采用多种方法的综合应用。
铁路钢轨调研报告

铁路钢轨调研报告铁路钢轨调研报告一、调研目的本次调研旨在了解铁路钢轨的使用情况和存在的问题,以及相关的技术发展和应用情况,为今后的研究和改进提供参考依据。
二、调研内容1. 铁路钢轨的基本情况通过调研,在中国的铁路系统中,普遍采用的钢轨材质为50Mn和60Si2Mn,两者性能稳定,适应不同的工况要求。
而在铁路的建设过程中,合适的轨道质量也是至关重要的。
2. 钢轨的检查与维护钢轨在使用过程中受到重压和动载荷的作用,会导致轨道受力不均匀而产生疲劳裂纹、损伤和变形等问题。
因此,其检查与维护工作很重要。
目前,通过超声波探伤和轨道检测技术,可以提前发现并处理钢轨的问题,保证铁路安全运行。
3. 钢轨材质的研发与改进目前,随着科技的进步,一些新材料的应用也逐渐出现在铁路钢轨领域。
比如,使用先进的高强度低合金轨帮助减少轨道变形和延长使用寿命。
此外,还有一些新型复合材料也被应用在一些特殊工况下。
4. 高速铁路钢轨的技术要求在高速铁路领域,钢轨的质量要求更高,需要具备良好的耐疲劳性、抗变形能力和承载能力。
因此,高速铁路钢轨的生产技术也在不断改进,以满足安全运行的要求。
三、存在的问题1. 钢轨使用寿命短由于高铁运营强度大,现有钢轨的寿命相对较短,需要更加耐磨和耐久的新材料来替代。
2. 高铁速度限制当前中国高铁运行速度已达到350公里/小时,但由于钢轨材料和技术存在局限性,速度的进一步提升受到限制,研究改进钢轨的材料和制造技术具有重要意义。
四、建议和展望1. 加强钢轨的检查与维护工作,提高轨道质量,确保铁路的安全运行。
2. 针对高速铁路的需求,加大钢轨材料的研究和开发力度,生产更加耐磨和耐久的高速铁路钢轨。
3. 提高钢轨的生产技术水平,加强与科研机构的合作,积极引进并应用新的材料和技术。
4. 加强国际交流与合作,在全球范围内分享钢轨技术的发展和应用经验,共同推动铁路交通的发展。
总结:铁路钢轨作为铁路运输的重要基础设施之一,其质量和技术水平直接影响着铁路运输的安全和效率。
城市轨道交通钢轨的断裂失效分析与预防
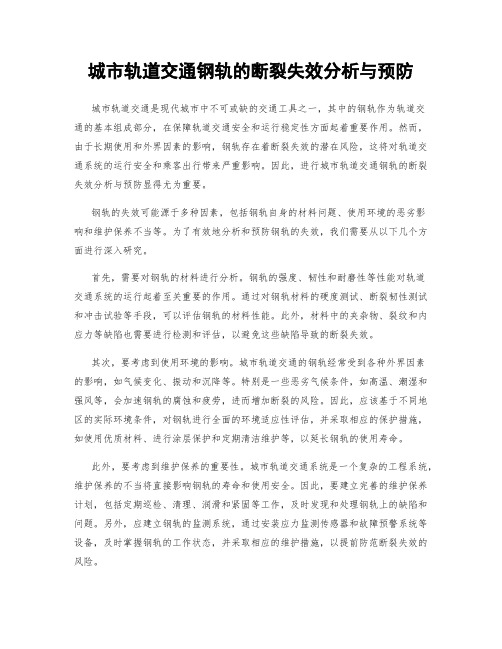
城市轨道交通钢轨的断裂失效分析与预防城市轨道交通是现代城市中不可或缺的交通工具之一,其中的钢轨作为轨道交通的基本组成部分,在保障轨道交通安全和运行稳定性方面起着重要作用。
然而,由于长期使用和外界因素的影响,钢轨存在着断裂失效的潜在风险,这将对轨道交通系统的运行安全和乘客出行带来严重影响。
因此,进行城市轨道交通钢轨的断裂失效分析与预防显得尤为重要。
钢轨的失效可能源于多种因素,包括钢轨自身的材料问题、使用环境的恶劣影响和维护保养不当等。
为了有效地分析和预防钢轨的失效,我们需要从以下几个方面进行深入研究。
首先,需要对钢轨的材料进行分析。
钢轨的强度、韧性和耐磨性等性能对轨道交通系统的运行起着至关重要的作用。
通过对钢轨材料的硬度测试、断裂韧性测试和冲击试验等手段,可以评估钢轨的材料性能。
此外,材料中的夹杂物、裂纹和内应力等缺陷也需要进行检测和评估,以避免这些缺陷导致的断裂失效。
其次,要考虑到使用环境的影响。
城市轨道交通的钢轨经常受到各种外界因素的影响,如气候变化、振动和沉降等。
特别是一些恶劣气候条件,如高温、潮湿和强风等,会加速钢轨的腐蚀和疲劳,进而增加断裂的风险。
因此,应该基于不同地区的实际环境条件,对钢轨进行全面的环境适应性评估,并采取相应的保护措施,如使用优质材料、进行涂层保护和定期清洁维护等,以延长钢轨的使用寿命。
此外,要考虑到维护保养的重要性。
城市轨道交通系统是一个复杂的工程系统,维护保养的不当将直接影响钢轨的寿命和使用安全。
因此,要建立完善的维护保养计划,包括定期巡检、清理、润滑和紧固等工作,及时发现和处理钢轨上的缺陷和问题。
另外,应建立钢轨的监测系统,通过安装应力监测传感器和故障预警系统等设备,及时掌握钢轨的工作状态,并采取相应的维护措施,以提前防范断裂失效的风险。
最后,钢轨的设计和安装也需要考虑断裂失效的预防。
在钢轨的设计中,应合理确定钢轨的几何形状、尺寸和支撑结构,以确保钢轨在重载和高速运行条件下的稳定性和安全性。
- 1、下载文档前请自行甄别文档内容的完整性,平台不提供额外的编辑、内容补充、找答案等附加服务。
- 2、"仅部分预览"的文档,不可在线预览部分如存在完整性等问题,可反馈申请退款(可完整预览的文档不适用该条件!)。
- 3、如文档侵犯您的权益,请联系客服反馈,我们会尽快为您处理(人工客服工作时间:9:00-18:30)。
钢轨裂纹及断轨检测方法调研报告在铁路运输系统中,钢轨起着支撑列车和引导车辆车轮前进的作用。
如果出现钢轨断裂将有可能造成列车出轨、倾覆等重大行车安全事故,造成人员伤亡和巨额财产损失。
因此钢轨伤损检测越来越受到人们的重视。
表1所示为近些年由于钢轨断裂造成的列车行车事故。
表1 近些年钢轨断裂造成的列车行车事故时间地点伤损情况2001年3月18日美国爱荷华州钢轨断裂引起列车脱轨,造成1人死亡96人受伤2007年10月17日伦敦钢轨断裂引发列车脱轨,造成4人死亡、70人受伤、4人重伤2009年4月7日河北野三坡钢轨断裂导致6节车厢脱轨同时,随着国家高速铁路和重载铁路的发展,钢轨受到挤压和冲击的程度越来越大,钢轨发生损伤的概率也在提高。
因此,为保证高速铁路和重在铁路的运营安全性,钢轨裂纹检测成为铁路运营部门十分重视的事情。
目前,钢轨的主要检测方式分为周期性探伤检测和实时断轨监测。
周期性钢轨探伤检测包括人工巡轨检测、大型钢轨探伤车、漏磁信号、涡流探伤、激光超声、图像处理等;实时断轨监测技术包括轨道电路实时断轨检测技术、牵引回流实时断轨检测技术、光纤实时断轨检测技术和超声波实时断轨监测技术等。
1 周期性检测技术周期性检测技术就是定期对钢轨进行检测,国内外都针对不同轨道、不同检测设备制定了检测周期和检测作业标准。
总体上说,周期性检测设备精确度高,能及时发现钢轨早期裂纹,以避免发生重大交通事故;但是它需要占用较多天窗时间。
1.1 探伤小车中国铁路广泛使用的是钢轨探伤小车,它将小型超声波钢轨探伤仪装在特制的手推车上,如图1所示。
通过人工手推进行钢轨损伤的检测,它耗费大量人力物力、检查结果主观性强、检查周期长、效率低下、速度慢,无法做到对钢轨伤损情况实时检测,不能适应于我国日益发展的高速铁路事业[1-2]。
近年来,随着钢轨裂纹导致脱轨事故的频发,为了加强钢轨安全监测,欧美也开始研发使用这种便携式钢轨探伤仪[3]。
由于超声波探伤技术比较成熟,成本比较低,且随着科技的发展,以前只有大型探伤车才具备的A/B超同屏显示、鱼鳞纹下核伤判别、探伤数据储存、探伤作业信息记录、探伤数据计算机管理等五大功能正移植到探伤小车身上,在各钢轨探伤仪器生产商当中,超声探伤小车倍受青睐。
图1 手推式钢轨探伤车结构示意图1.2 大型钢轨探伤车大型钢轨探伤车系统由高速轮探头,超声发生装置,探头自动对中伺服装置,以及伤损信号处理等系统组成。
其原理是,装有超声探头组的高速探轮在钢轨上滚动,超声发生接收器组合探头向钢轨发出连续超声脉冲波束,连续波束通过耦合液及探轮橡胶轮壁到达钢轨内,如无损伤存在,波束到达钢轨底面后依原路返回探头,得到底波;如有损伤,则底波前出现一个伤损波,底波降低或消失[4]。
我国铁道部门为了提高钢轨伤损的检出率,推动钢轨维护设备的进步,从1989年开始从美国引进大型钢轨探伤车,并由宝鸡工程机械厂实现国产化制造。
经过20余年的集成创新研究,发展了GJ-3,GJ-4,GJ-5三种类型;其中,GJ-4、GJ-5型检测设备已成为我国既有线路轨道状态监控的主要手段,最高检测速度达到200 km/h,其自动分辨为:钢轨头部横向疲劳裂纹(核伤),不小于直径5 mm平底孔当量;螺栓孔裂纹及腰部斜裂纹,长度不小于10 mm;钢轨纵向水平裂纹,长度不小于10 mm;探轮自动对中精度小于1 mm[2,5]。
图2 大型钢轨探伤车该技术对检测钢轨疲劳裂纹和其它内部缺陷具有灵敏度高、检测速度快、定位准确等优点[6]。
但是常规的超声波钢轨检测使用的是压电传感器。
压电传感器与轨顶连接,同时将超声轮或滑板注满水或其他耦合液。
此种方法的最大缺点是,浅表面裂缝(剥落)可能会遮掩钢轨内部存在的横向缺陷[7]。
而且造价过高、维护要求较高,数量有限,检测时受轨面平整度和清洁度影响较大,其为离线式轨道检测设备。
上海铁路局龚佩毅等人在专利(CN 102445495A)“双轨白动探伤系统”中提出了一种基础超声波的成本比较低的双轨自动探伤系统[8]。
其特点是超声波探轮可三维运动,可实现钢轨的超声波自动探伤和定位,特别适用于检测钢轨头部横向疲劳裂纹(核伤)、螺栓孔裂纹、腰部斜裂纹和钢轨纵向水平裂纹等损伤。
南车洛阳机车有限公司的袁其刚等人在专利(CN 201882114U)“用于检测城市轻轨钢轨的探伤车”中设计了一种用于检测城市轻轨钢轨的探伤车[9]。
其特点是车体通过二系悬挂落座于前后转向架上,用以保证车辆有较高的运行性能,并在其中一台转向架上设置有用于对钢轨进行检测的探伤系统,探伤轮通过下降和上升的液压系统控制,提高了钢轨探伤的效率,增加了轻轨车辆运行的安全性。
1.3 基于漏磁信号的钢轨检测技术该技术是通过励磁装置给钢轨施加一个磁场,当钢轨完好时,磁场能顺利的通过钢轨,基本不产生漏磁;当钢轨出现裂纹时,裂纹会阻碍磁场的顺利通过,产生漏磁。
由于裂纹大的大小形状不同,其产生漏磁的强度也不同,根据漏磁信号的变化来判断裂纹信息,如图3所示。
该技术的缺点是检测范围有限,仅能检测钢轨轨头表面和近表面的横向裂纹缺陷,而对于夹杂、剥离以及轨头内部深处的缺陷无法进行有效的检测。
(a)无裂纹(b)有裂纹图3 基于漏磁信号的钢轨检测原理南京航空航天大学陈智军等人[10,11]通过有限元软件Ansoft仿真研究了钢轨斜裂纹的识别原理及方法,包括理论分析、模型建立、斜裂纹与矩形裂纹的漏磁信号差异、斜裂纹深度与宽度的识别以及连续多个斜裂纹的识别等。
它可以识别斜裂纹的方向及宽度,但是不能识别小间隔多裂纹的数量。
1.4 涡流探伤技术该技术的传感器由一个U形激励线圈和一个I型检测线圈组成,如图4所示。
两线圈的相对位置为正交取向,检测线圈放置在U型激励线圈的开口中点处。
工作时,在激励线圈上通以一定频率的正弦波,当传感器沿着试件表面移动时,试件表面在交变磁场作用下会产生一定分布和大小的涡流,此涡流产生一个反磁场。
当无裂纹时,没有反磁场磁力线通过检测线圈,没有电信号输出;有裂纹时,反磁场发生变化,磁力线通过检测线圈,输出电信号,从而反映缺陷的情况。
该方法结构简单、操作方便、具有非接触的优点,但其检测范围也仅局限于钢轨表面的缺陷。
1.激励 2.激励线圈 3.U型磁心 4.测量线圈 5.磁心图4 传感器结构示意图长安大学马旺宇等人在专利(CN 101576533A)“一种用于钢轨检测的便携式涡流探伤仪”中提出一种便携式探伤仪[12],如图5所示,该探伤仪所使用了专利(CN 201429587Y)“一种用于钢轨检测的新型传感器”中所设计的传感器[13],其测量线圈的线圈匣数、直径以及激励线圈和测量线圈间的问距H为通过正交试验设计法确定的最佳参数组合。
所述激励线圈和一个测量线圈安装在一能倒扣在钢轨上的外部壳体内,所述外部壳体下部设置有与钢轨的上部结构相对应的凹槽。
采集到的信号再由后台放大器放大,并在显示器上同步显示裂纹缺陷的相对大小,且相应驱动蜂鸣器报警,实现了防患于未然的目的。
其结构简单紧凑、体积小、重量轻、便于携带,并配备有独立电源。
经过测试,其测量精度能达到0.2 mm [14]。
图5 一种用于钢轨检测的便携式涡流探伤仪庄鑫等人申请的专利(CN 201965116U)“钢轨裂纹检测仪”如图6所示[15],由检测头、检测主机、推拉支架、滚轮、连接管、固定环组成,其特征在于推拉支架下端两侧分别通过连接管前后固定连接两个检测头,每个检测头两侧部分别固定有滚轮,推拉支架中间的上连管上通过两个固定环连接有检测主机,检测头与检测主机电连接。
该仪器采用手推车式,可实现双规同时检测,每条钢轨前后设有两个检测头,检测速率相对较高,漏检率低。
图6 钢轨裂纹检测仪专利(US 6,768,298B2)“Transverse crack detection in rail head using low frequency eddy currents”设计了一种低频涡流探测轨头横向裂纹的装置[16],如图7所示。
其特点是该专利采用环形的直流饱和磁体,通过钢轨上方的低频涡流探针探测钢轨轨头横向裂纹。
并且探针上装有防护材料,以防止探针受损。
图7 低频涡流探测轨头横向裂纹装置示意图1.5 图像处理探伤技术该技术通过安装在机车下方随机车型走的摄像机拍摄钢轨照片,当钢轨有缺陷时,这些缺陷便被摄相机拍了下来,在通过对图片的处理和分析,可以将其中的缺陷提取出来,进行模式识别,完成钢轨损伤检测。
其缺点是无法实现轨头内部缺陷的检测[17]。
西南交通大学的官鑫等人[18]对这一技术做了理论分析,他采用图像处理、模式识别及机器视觉等理论,对现役钢轨缺陷进行检测和分类。
完成自动提取缺陷图像和最小化缺陷图像,以减少处理量并降低存储空间需求,自动判断缺陷类别。
文章对采集到的缺陷图像进行处理,实验结果证明该方法能够正确实现检测轨道表面缺陷检测,并具有一定的适用性。
此方法可以克服人工检测方法的许多弊端,提高检测速度和精度。
Liu Ze等人[19]用此技术分析了轨头剥离和钢轨表面裂纹的图片,并得到了钢轨的磨损程度和裂纹宽度。
Chen Limin等人[20]也做了这方面的理论研究。
他研究了图像采集,图像处理,提取特征,缺陷识别的钢轨表面缺陷识别过程,并基于裂纹形态学,通过动态模版去检测连续裂纹边界,以此来估算裂纹长度。
北京交通大学李清勇等人在专利(CN 101893580A)“基于数字图像的钢轨表面缺陷检测方法”中提出了一种基于数字图像的钢轨表面缺陷检测方法[21]。
该方法从对钢轨拍摄的图像中提取钢轨区域,并模拟人类视觉机制,将灰度图转换为对比度图,从而对可疑缺陷区域进行定位及判定。
北京交通大学刘泽等人在专利(CN 101699273A)“一种在线钢轨探伤的图像处理辅助检测装置及方法”中利用工业CCD线阵摄像机采集钢轨表面的图像信息。
其过程是在列车在线运行过程中,嵌入式控制系统控制光源激励控制器使两个辅助光源照射钢轨表面,工业CCD线阵摄像机通过数字线阵图像采集接口的控制采集钢轨表面的图像信息,将信息传输到嵌入式系统,嵌入式系统使用图像处理技术对采集到的钢轨图像进行处理;从处理后的钢轨图像中统计钢轨表面的损伤信息及固有结构信息;再将所获得的钢轨表面损伤信息进行分类和损伤程度计算。
最后将结果融合到钢轨损伤探测装置,以减少表面损伤对探测钢轨内部伤损的干扰[22],其总体结构图如图8所示。
106.钢轨107.控制机箱206.工业CCD 线阵摄像机207,208.辅助光源图8 在线钢轨探伤的图像处理辅助检测装置的总体结构图1.6 激光超声探伤技术该技术用脉冲激光器发出的高能脉冲激光轰击钢轨表面,钢轨表面被照射区域吸收其能量并将之转化为热能,引起钢轨表面迅速升温膨胀,从而构成超声声源。