丰田生产运营模式PPT图文.ppt
合集下载
丰田式生产方式(TPS)讲义PPT课件( 65页)

16
認識的含義
• 認識現場作業,不單單是漫不經心地到加工作 業現場走走看看,一知半解。而是要抓住全貌, 並掌握各部分的機能和作用。
• 認識的意思是非常嚴格的,是要積極地接近被 認識的對象,並抓住其本質的意思。
• 如果認為目前的作業方法較好、生產線的工作 效率比較高,廢品率也控制在不會形成問題的 較好的范圍內,因此從整體上來說就合格了。 那麼,進步就將立即停止,自身就把改進的幼 芽摧殘了。
・信息的确定(1个月前)
・材料的订购、各工序的人員、设备负荷、计划
③・日程计划
・平均化计划
・确定每天的生产量
・生产指示 ・指示每天的生产量、生产品种、生产順序
12
(2)・每天必要生产数量和节拍
・每天的必要数量= 1个月的必要数量 一个月运转天数
・节拍 =
每天的运转时间 × 运转率 每天的必要数量
・是决定用几分钟、几秒生产一个部件、或是1台份的时间长短值。
例:生產線上裝配所必需的零件,恰好在必要的時刻(不 早不晚),以必要的數量(不多不少),到達生產線的旁 邊。是一種理想的生產體系,能夠消除生產現場中的無效 勞動和浪費、生產不平準化的狀態以及管理不合理的現象, 從而提高效率。
① 提高生产效率性; ② 减少库存。
重點:不單純是做到按時,而是要非常準時,既不提前也 不拖遲,正是在需要的時刻就送到
18
作业的实际状态
实质作业
・部件安装 ・喷涂 ・切削 ・冲压 ・焊接、
不产生附加值的作业
・取部件、工具的行走 ・部件的开箱作业 ・部件的重新更换 ・按键按钮的操作 ・搬运作业
浪费
・等待 ・没有意义的搬运(临时放置) ・换手拿工具、部件 ・制造积压 ・部件的堆积 ・不合格品的修复
認識的含義
• 認識現場作業,不單單是漫不經心地到加工作 業現場走走看看,一知半解。而是要抓住全貌, 並掌握各部分的機能和作用。
• 認識的意思是非常嚴格的,是要積極地接近被 認識的對象,並抓住其本質的意思。
• 如果認為目前的作業方法較好、生產線的工作 效率比較高,廢品率也控制在不會形成問題的 較好的范圍內,因此從整體上來說就合格了。 那麼,進步就將立即停止,自身就把改進的幼 芽摧殘了。
・信息的确定(1个月前)
・材料的订购、各工序的人員、设备负荷、计划
③・日程计划
・平均化计划
・确定每天的生产量
・生产指示 ・指示每天的生产量、生产品种、生产順序
12
(2)・每天必要生产数量和节拍
・每天的必要数量= 1个月的必要数量 一个月运转天数
・节拍 =
每天的运转时间 × 运转率 每天的必要数量
・是决定用几分钟、几秒生产一个部件、或是1台份的时间长短值。
例:生產線上裝配所必需的零件,恰好在必要的時刻(不 早不晚),以必要的數量(不多不少),到達生產線的旁 邊。是一種理想的生產體系,能夠消除生產現場中的無效 勞動和浪費、生產不平準化的狀態以及管理不合理的現象, 從而提高效率。
① 提高生产效率性; ② 减少库存。
重點:不單純是做到按時,而是要非常準時,既不提前也 不拖遲,正是在需要的時刻就送到
18
作业的实际状态
实质作业
・部件安装 ・喷涂 ・切削 ・冲压 ・焊接、
不产生附加值的作业
・取部件、工具的行走 ・部件的开箱作业 ・部件的重新更换 ・按键按钮的操作 ・搬运作业
浪费
・等待 ・没有意义的搬运(临时放置) ・换手拿工具、部件 ・制造积压 ・部件的堆积 ・不合格品的修复
TPS丰田生产模式PPT课件

B易 于 暴 露 异 常 的 工 具
时间
800-9:00 9:00-10:00 10:00-11:00 11:00-12:00 13:00-14:00 14:00-15:00 15:00-16:00 16:00-17:00 17:00-18:00
合计
生产管理板
计划
60
实际数量
60
未进行原因
第47页/共48页
——经常为100%最理想
第9页/共48页
7
整体的生产效率比个体的生产效率 更为重要
赛艇
第10页/共48页
轴承厂的实例
B
D
d
内轮生产线(节拍快) 外轮生产线(节拍慢)
第11页/共48页
8 提高效率和强化劳动是不同的概念
提高效率
将动作“改善为有效劳动”(工作)
工
浪
动作
作
费
工
浪
作 动作 费
工
浪
作 动作费
缩短生产周期 简化生产流程
第29页/共48页
(3)按售出情况从事生产的概念较薄弱
a)由于生产的速度比售出的速度快,所以导致 生产过剩,出现停滞现象。
生产节拍
每天平均作业时间 每天所需数量
(例如)
每天平均作业时间 8小时 460分钟
每天所需数量
460件
生 产节 446 分 6 件 拍 00 钟 1分/钟 件
利润
售价
成本
利润
售价
成本
利润
售价
成本
利润
售价
成本
增加利润的方法:
1、提高售价
2、降低成本
需求>供应
需求≤供应
售价是顾客决定的
丰田生产与运作管理ppt

丰田全系
车到山前必有路,有路必有丰田车。 TOYOTA在汽车的销售量、销售额、知名度 方面均是世界一流公司之一。特别在汽车 轿车:crown皇冠、reiz瑞志、camry凯美瑞、 corolla花冠、prius普瑞斯、 vios威驰 Suv(越野车):land cruiser陆地巡洋舰、 prado普拉多、 rav4 Mvp(多功能车 ):previa普瑞维亚 商务:coaster科斯达、hiace
一大基础
“一大基础”是指改善(Improvement) : ①从局部到整体永远存在着改进与提高的余 地 ②消除一切浪费:不能提高附加价值的一切 工作都是浪费 ③连续改善:以消除浪费和改进提高的思想 为依托,不断地改善、巩固,改善、提高, 以求长期的积累,获得显著效果
两大支柱
“两大支柱”是准时化(JIT)与人员自觉 化 (1)以市场为龙头,以看板管理为基础,以 平准化(Leveling System)为条件在合适的时 间、生产合适的数量和高质量的产品。 (2)人员自主化是人员与机械设备的有机配 合行为
多技能作业员
多技能作业员(或称“多面手”)是指那些能够操 作多种机床的生产作业工人 U型生产单元内,由于多种机床紧凑地组合在一起, 便于“多面手”能够进行多种机床的操作,同时负 责多道工序的作业 一个多技能作业员按照标准作业组合表,依次操作 几种不同的机床 可以将各工序节省的零星工时集中起来,以便整数 削减多余的生产人员,从而有利于提高劳动生产率
设备的合理布置
传统“机群式”布置方式:即把功能相同的机器设 备集中布置在一起 零件制品的流经路线长、流动速度慢、在制品量多、 用人多,而且不便于小批量运输 丰田“U”型单元式布置方式 :按零件的加工工艺要 求,把功能不同的机器设备集中布置在一起组成一 个一个小的加工单元。 简化物流路线,加快物流速度,减少工序之间不必 要的在制品储量,减少运输成本
丰田精益生产方式PPT课件
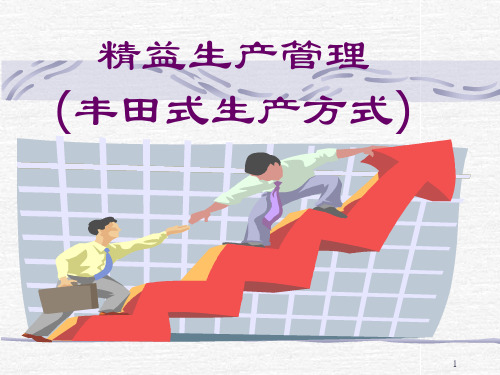
箱内数量:100 看板编号:2/5
使用工序 总装1-3 入口位置
POS.12-8
9
•七大浪费 1.生产过量的浪费
2.等工造成的浪费
•改善措施
1.单件流动: 避免 以批量为单位加工 ,应逐个完成相关 工序加工 2.按工序排列设备 布置流水线
•七大浪费 3.搬运上的浪费
4.加工本身的浪费
•改善措施
3.按节拍进行生产 ,按看板和用户需 求适时、适量、适 物连续流动 4.站立式走动作业
什么是浪费? 不增加价值的(生产过程改变零件尺寸、 形状或功能,非价格) 活动是浪费 尽管是增加价值的活动,但所用资源超 过了绝对最少的界限,也是浪费
精益生产目的就是取消那些不增加产品价 值的工作,即降低成本
3
到处都存在浪费 – 7种表现
生产过量的浪费 等工造成的浪费 搬运上的浪费 加工本身的浪费 库存的浪费 操作作业的浪费 生产废品、次品的浪费
精益生产管理 (丰田式生产方式)
1
何为精益生产
精益生产方式70年代起源于丰田汽 车公司 丰田生产方式最终目标就是提高全 公司的利润,为实现目标,大野耐 一把消除浪费、降低成本就成为最 基本目标 精益生产( Lean Production)是美国 麻省工学院给丰田生产方式的名称
2
减少浪费 --降低成本的主要手段
17
谢谢!
18
祝各位身体健康、工作顺利、家 庭幸福。
•19
•七大浪费
5.库存的浪费
6.操作作业的浪 费 7.生产废品、次 品的浪费
•改善措施
5.培养多能工,一 人多机(工序)操作 6.设备小型化,排 列U、L、三角形等 7.作业标准化
均衡化同步同节拍生产
同步化节拍生产是按照生产工艺规定和 物流顺序确定生产提前期条件下和产品 总装配线保持同步地进行生产
使用工序 总装1-3 入口位置
POS.12-8
9
•七大浪费 1.生产过量的浪费
2.等工造成的浪费
•改善措施
1.单件流动: 避免 以批量为单位加工 ,应逐个完成相关 工序加工 2.按工序排列设备 布置流水线
•七大浪费 3.搬运上的浪费
4.加工本身的浪费
•改善措施
3.按节拍进行生产 ,按看板和用户需 求适时、适量、适 物连续流动 4.站立式走动作业
什么是浪费? 不增加价值的(生产过程改变零件尺寸、 形状或功能,非价格) 活动是浪费 尽管是增加价值的活动,但所用资源超 过了绝对最少的界限,也是浪费
精益生产目的就是取消那些不增加产品价 值的工作,即降低成本
3
到处都存在浪费 – 7种表现
生产过量的浪费 等工造成的浪费 搬运上的浪费 加工本身的浪费 库存的浪费 操作作业的浪费 生产废品、次品的浪费
精益生产管理 (丰田式生产方式)
1
何为精益生产
精益生产方式70年代起源于丰田汽 车公司 丰田生产方式最终目标就是提高全 公司的利润,为实现目标,大野耐 一把消除浪费、降低成本就成为最 基本目标 精益生产( Lean Production)是美国 麻省工学院给丰田生产方式的名称
2
减少浪费 --降低成本的主要手段
17
谢谢!
18
祝各位身体健康、工作顺利、家 庭幸福。
•19
•七大浪费
5.库存的浪费
6.操作作业的浪 费 7.生产废品、次 品的浪费
•改善措施
5.培养多能工,一 人多机(工序)操作 6.设备小型化,排 列U、L、三角形等 7.作业标准化
均衡化同步同节拍生产
同步化节拍生产是按照生产工艺规定和 物流顺序确定生产提前期条件下和产品 总装配线保持同步地进行生产
丰田生产模式、班组长优秀品质

3) 发展人员以增加企业价值 (People)
4)持续解决问题以驱动企业 学习(Problem Solving)
品质 服务 互动 繁荣
原则1:管理决策以长期理念为基础,即使因此 牺牲短期财务目标也在所不惜。
◆丰田长期一致的理念与使命: 做有益于公司、公司员工、客户
及整个社会的事。 ◆力奴经营理念:
新技术引进目的是为了支持员工提高工作效率和优化流程
直线型生产线
U型生产线 品质 服务 互动 繁荣
原则9:把彻底了解并拥护公司理念的员工培养成为 领导者,使他们能教导其他员工。
丰田人才培养模式: 丰田的领导者是组织内部
自行育成。
品质 服务 互动 繁荣
原则10:培养与发展信奉公司理念的杰出人才与团队。
原则5:建立立即暂停以解决问题、从一开 始就重视品质管理的文化。
力奴精益“三色牌”:
提问:
为我们带来的好处?
品质 服务 互动 繁荣
原则6:工作的标准化是持续改进与授权员工的基础
工作的标准化是丰田目视流程的基础之一 工作标准必须够明确,才能作为对员工有效的指引
思考:
力奴的工作标准?
品质 服务 互动 繁荣
即各工序只有一个工件在流动,使工序从原材料到成品的加工过程始终 处于不停滞、不堆积、不超越的流动状态,是一种工序间在制品向零挑战的 生产管理方式。
品质 服务 互动 繁荣
原则2:建立无间断的操作流程以使问题浮现
◆思考:
下图所示某车间产品制成工序流程,你该如何精益规划?
传统模式
丰田“一个流”模式 品质 服务 互动 繁荣
一、丰田模式的14项原则
品质 服务 互动 繁荣
品质 服务 互动 繁荣
丰田模式的14项原则由4P组成
精益生产(TPS丰田生产方式)ppt课件

1950年 3月日本全厂罢工, 1950年 4 .11- 6.10 TOYOTA自动车劳动争议
- 因日銀나고야支店的经济条件充足得到的资金
① 把销售公司从TOYOTA自动车工业里分离独立起来.- 销售部门分离
② TOYOTA自动车只生产销售公司能销售出的台数.- 在月1,500台里4吨BM型卡车扩散减少到940 台.
精选课件
23
1. TOYOTA的成本MIND
Ⅱ. 得出利益的生产方式
销售额 = 成本 + 利益 : 只有成本主义的话是不能生存下去的.
利益 = 销售值 – 成本 : 这思考方式是基本. 一定,客户决定
为了挣钱(为了扩大利益) 只有节减成本的方法.
为了这个有必要彻底排除浪费
以下3种方法中哪方法最有现实性?
Ⅰ. TPS的概要
文书化的技能 • 确保跟继承一样的方针的连续性 • 仅TOYOTA所有的经营思想的连续性,强调给营业员的构造 • 公式规则体制的,得意的保存方法
精选课件
11
Ⅰ. TPS的概要
TOYOTA Soichiro的遗传子
减少
TOYOTA Eiji的遗传子
减少
TOYOTA 退三的遗传子
改定•制定 统治
1938年在擧母工厂的准公式上TOYOTA喜一郞强调 “JUST IN TIME”
生产方式是 “每日需要的 在需要时 只制作需要的那么量”
投入TOYOTA式的流水作业
精选课件
6
Ⅰ. TPS的概要
什么是TPS (Toyota Production System)
- TOYOTA的生产SYSTEM是,把生产能力效率性的活动的生产SYSTEM. - TOYOTA生产SYSTEM是将人力和设备等的生产能力,按需要的量维持也把效率极大化的把