热处理作业指导书
热处理作业指导书

热处理作业指导书引言概述:热处理是一种重要的金属加工工艺,通过控制金属的加热和冷却过程,改变其组织结构和性能。
本文将为您提供一份热处理作业指导书,详细介绍热处理的基本原理、常见的热处理方法、操作注意事项以及质量控制要点,匡助您正确进行热处理作业。
一、热处理基本原理1.1 金属组织变化原理:热处理过程中,金属的组织结构会发生变化。
通过加热使金属晶粒长大,晶界迁移,原子扩散,从而改变其力学性能和物理性质。
1.2 热处理影响因素:热处理效果受多种因素影响,包括温度、保温时间、冷却速度等。
不同金属和合金对热处理的响应也有所不同,需要根据具体材料进行调整。
1.3 热处理效果评估:通过金相显微镜观察和理化性能测试,可以评估热处理的效果。
常用的评估指标包括金属组织结构、硬度、韧性等。
二、常见的热处理方法2.1 淬火:淬火是将金属加热到临界温度,然后迅速冷却的过程。
通过淬火可以使金属获得高硬度和高强度,但韧性较差。
2.2 回火:回火是将淬火后的金属加热到较低温度,然后缓慢冷却。
回火可以减轻金属的脆性,提高其韧性和塑性。
2.3 等温淬火:等温淬火是将金属加热到临界温度,然后在恒温条件下保持一段时间,最后迅速冷却。
等温淬火可以获得细小的组织结构和高强度。
三、操作注意事项3.1 温度控制:热处理过程中,温度的控制非常关键。
应根据材料的热处理图谱和工艺要求,合理控制加热和保温温度,避免过热或者过低。
3.2 冷却介质选择:不同的金属和热处理方法需要选择合适的冷却介质。
常用的冷却介质包括水、油温和体等,根据具体情况进行选择。
3.3 保护措施:某些金属在高温下容易氧化和变质,需要采取适当的保护措施,如包覆剂、气氛控制等,以防止氧化和表面污染。
四、质量控制要点4.1 金相显微镜观察:通过金相显微镜观察金属的组织结构,判断热处理效果是否符合要求。
应注意观察区域的选择和标记方法,以确保准确的观察结果。
4.2 硬度测试:硬度测试是评估金属强度和硬度的重要方法。
热处理车间热处理作业指导书
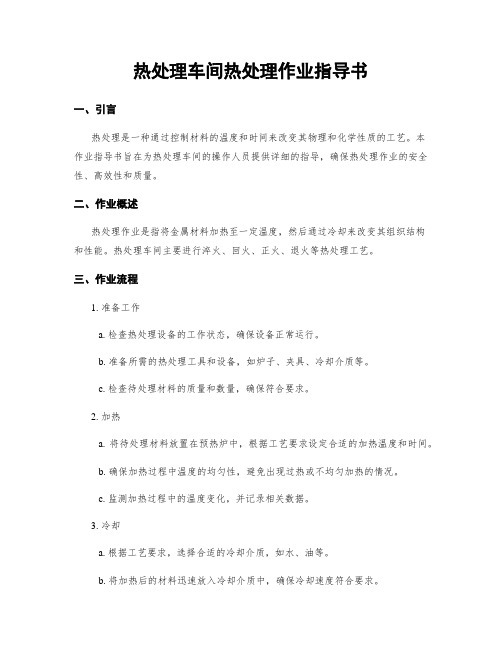
热处理车间热处理作业指导书一、引言热处理是一种通过控制材料的温度和时间来改变其物理和化学性质的工艺。
本作业指导书旨在为热处理车间的操作人员提供详细的指导,确保热处理作业的安全性、高效性和质量。
二、作业概述热处理作业是指将金属材料加热至一定温度,然后通过冷却来改变其组织结构和性能。
热处理车间主要进行淬火、回火、正火、退火等热处理工艺。
三、作业流程1. 准备工作a. 检查热处理设备的工作状态,确保设备正常运行。
b. 准备所需的热处理工具和设备,如炉子、夹具、冷却介质等。
c. 检查待处理材料的质量和数量,确保符合要求。
2. 加热a. 将待处理材料放置在预热炉中,根据工艺要求设定合适的加热温度和时间。
b. 确保加热过程中温度的均匀性,避免出现过热或不均匀加热的情况。
c. 监测加热过程中的温度变化,并记录相关数据。
3. 冷却a. 根据工艺要求,选择合适的冷却介质,如水、油等。
b. 将加热后的材料迅速放入冷却介质中,确保冷却速度符合要求。
c. 监测冷却过程中的温度变化,并记录相关数据。
4. 检验a. 完成热处理后,对处理后的材料进行外观检查,确保无明显变形、开裂等问题。
b. 进行金相组织检验,确认热处理效果是否符合要求。
c. 根据需要进行硬度测试、拉伸试验等其他性能检测。
5. 记录和报告a. 记录每次热处理作业的相关数据,包括加热温度、时间、冷却介质等。
b. 编制热处理作业报告,包括处理前后的材料性能变化、金相组织分析等内容。
四、安全注意事项1. 操作人员必须穿戴个人防护装备,包括防热手套、防护眼镜等。
2. 加热和冷却过程中,操作人员必须保持警惕,避免烫伤和其他安全事故的发生。
3. 确保热处理设备的正常运行,定期检查设备的安全性能。
4. 严禁在热处理车间吸烟或使用明火。
五、常见问题及解决方法1. 热处理过程中出现材料开裂问题:解决方法:检查加热温度和冷却速度是否符合要求,调整相应参数。
2. 热处理后材料硬度不符合要求:解决方法:检查加热温度和保温时间是否合适,根据需要进行回火或淬火处理。
热处理车间热处理作业指导书
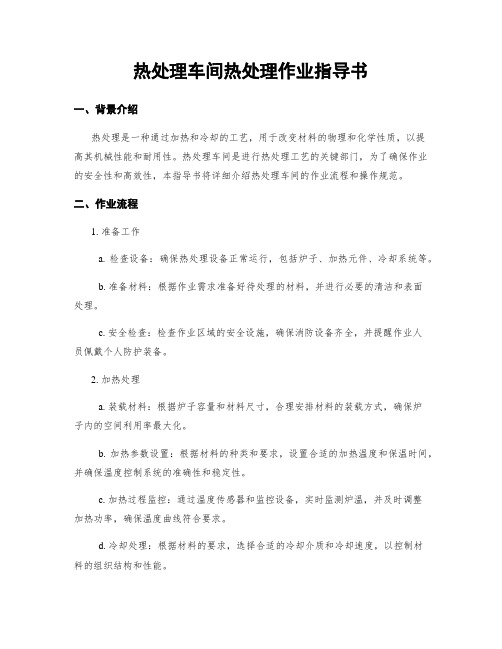
热处理车间热处理作业指导书一、背景介绍热处理是一种通过加热和冷却的工艺,用于改变材料的物理和化学性质,以提高其机械性能和耐用性。
热处理车间是进行热处理工艺的关键部门,为了确保作业的安全性和高效性,本指导书将详细介绍热处理车间的作业流程和操作规范。
二、作业流程1. 准备工作a. 检查设备:确保热处理设备正常运行,包括炉子、加热元件、冷却系统等。
b. 准备材料:根据作业需求准备好待处理的材料,并进行必要的清洁和表面处理。
c. 安全检查:检查作业区域的安全设施,确保消防设备齐全,并提醒作业人员佩戴个人防护装备。
2. 加热处理a. 装载材料:根据炉子容量和材料尺寸,合理安排材料的装载方式,确保炉子内的空间利用率最大化。
b. 加热参数设置:根据材料的种类和要求,设置合适的加热温度和保温时间,并确保温度控制系统的准确性和稳定性。
c. 加热过程监控:通过温度传感器和监控设备,实时监测炉温,并及时调整加热功率,确保温度曲线符合要求。
d. 冷却处理:根据材料的要求,选择合适的冷却介质和冷却速度,以控制材料的组织结构和性能。
3. 检验和质量控制a. 取样检测:在热处理完成后,从材料中取样进行物理和化学性能的检测,如硬度、拉伸强度、冲击韧性等。
b. 检验标准:根据产品的要求和相关标准,对检测结果进行评估和判定,确保产品的质量符合要求。
c. 记录和报告:将检验结果记录在热处理作业记录表中,并及时生成检验报告,以备后续的追溯和分析。
4. 设备维护和清洁a. 停机维护:在作业结束后,对热处理设备进行停机维护,包括清洁设备、更换耗损部件等。
b. 保养计划:制定设备保养计划,定期检查和维护热处理设备,以确保其长期稳定运行。
c. 作业区域清洁:定期清洁作业区域,清除杂物和油污,保持作业环境整洁。
三、操作规范1. 个人防护a. 穿戴个人防护装备:作业人员必须穿戴符合标准的个人防护装备,包括防护服、安全鞋、防护手套、护目镜等。
b. 防火安全:禁止在作业区域吸烟和使用明火,严禁携带易燃易爆物品进入作业区域。
热处理作业指导书

热处理作业指导书一、引言热处理是一种通过控制材料的温度和时间来改变其物理和化学性质的工艺。
本作业指导书旨在提供热处理作业的详细步骤和操作要求,以确保作业的安全性、高效性和质量。
二、作业准备1. 确定热处理的目的和要求,包括材料类型、硬度要求、工艺规范等。
2. 检查热处理设备和工具的状态,确保其正常工作和安全性。
3. 准备所需的材料和试样,确保其质量和数量满足要求。
三、作业步骤1. 清洁和预处理a. 将待处理的材料进行表面清洁,去除油污、灰尘等杂质。
b. 检查材料的尺寸和形状,确保其满足要求。
c. 对于需要预处理的材料,如去除氧化皮、切割等,按照相应的工艺要求进行处理。
2. 加热a. 将材料放置在热处理设备中,确保其与设备接触良好。
b. 根据热处理要求,设置加热温度和保温时间。
c. 启动加热设备,逐渐升温至设定温度,并保持一定时间。
d. 监测和记录加热过程中的温度变化,确保温度控制在规定范围内。
3. 冷却a. 加热结束后,立即将材料从加热设备中取出。
b. 根据热处理要求,选择合适的冷却方法,如水淬、油淬等。
c. 进行冷却过程中,注意安全防护措施,确保操作人员的安全。
d. 监测和记录冷却过程中的温度变化,确保冷却速度符合要求。
4. 淬火和回火(根据需要)a. 对于需要淬火的材料,将其迅速放入冷却介质中,以快速降低温度。
b. 对于需要回火的材料,将其放入回火炉中,按照工艺要求进行加热和冷却。
c. 监测和记录淬火和回火过程中的温度变化,确保控制在规定范围内。
5. 检验和评估a. 对热处理后的材料进行检验,包括硬度测试、显微组织观察等。
b. 根据检验结果,评估热处理的效果和质量,是否符合要求。
c. 记录检验和评估结果,作为质量控制的依据。
四、作业注意事项1. 在操作过程中,严格遵守安全操作规程,佩戴个人防护装备。
2. 确保热处理设备和工具的正常运行,及时进行维护和保养。
3. 控制加热和冷却过程中的温度,避免温度过高或过低导致材料性能不符合要求。
热处理作业指导书:
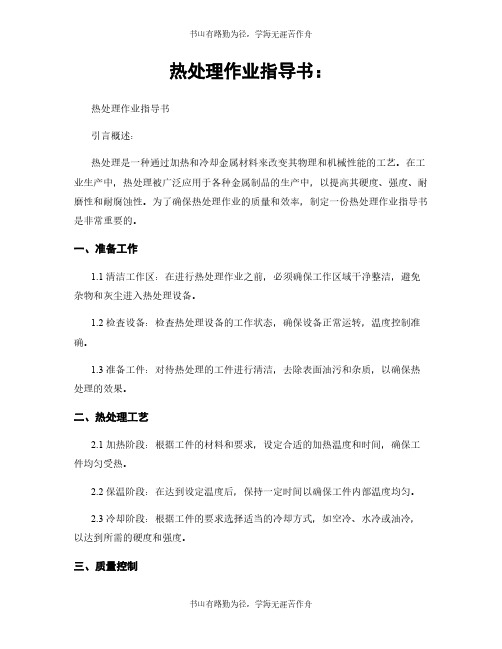
热处理作业指导书:热处理作业指导书引言概述:热处理是一种通过加热和冷却金属材料来改变其物理和机械性能的工艺。
在工业生产中,热处理被广泛应用于各种金属制品的生产中,以提高其硬度、强度、耐磨性和耐腐蚀性。
为了确保热处理作业的质量和效率,制定一份热处理作业指导书是非常重要的。
一、准备工作1.1 清洁工作区:在进行热处理作业之前,必须确保工作区域干净整洁,避免杂物和灰尘进入热处理设备。
1.2 检查设备:检查热处理设备的工作状态,确保设备正常运转,温度控制准确。
1.3 准备工件:对待热处理的工件进行清洁,去除表面油污和杂质,以确保热处理的效果。
二、热处理工艺2.1 加热阶段:根据工件的材料和要求,设定合适的加热温度和时间,确保工件均匀受热。
2.2 保温阶段:在达到设定温度后,保持一定时间以确保工件内部温度均匀。
2.3 冷却阶段:根据工件的要求选择适当的冷却方式,如空冷、水冷或油冷,以达到所需的硬度和强度。
三、质量控制3.1 温度控制:在整个热处理过程中,要时刻监控加热设备的温度,确保温度稳定。
3.2 工件质量检验:热处理后的工件需要进行质量检验,包括硬度测试、金相分析等,以确保达到设计要求。
3.3 记录数据:对每一次热处理作业进行记录,包括加热温度、保温时间、冷却方式等,以便追溯和分析。
四、安全注意事项4.1 佩戴防护装备:在进行热处理作业时,操作人员必须佩戴耐高温的防护服、手套和眼镜,确保人身安全。
4.2 防火防爆措施:热处理过程中易产生高温和火花,必须保持作业区域通风良好,避免火灾和爆炸事故。
4.3 避免中毒:某些热处理工艺可能产生有害气体,操作人员要注意防护,避免中毒。
五、设备维护5.1 定期检查:定期对热处理设备进行检查和维护,确保设备正常运转。
5.2 清洁保养:保持热处理设备的清洁,避免油污和杂质影响热处理效果。
5.3 更新升级:根据生产需求和技术发展,及时更新设备,提高热处理作业的效率和质量。
热处理作业指导书

热处理作业指导书一、引言热处理是一种通过加热和冷却金属材料来改变其物理和化学性质的工艺。
本指导书旨在提供热处理作业的详细指导,以确保作业过程的安全性、高效性和质量。
二、作业准备1. 确定热处理工艺:根据材料类型、要求性能和工艺规范,选择适当的热处理工艺,包括加热温度、保温时间和冷却方式等。
2. 材料准备:清洁材料表面,去除油污和其他污染物,以确保热处理效果。
3. 设备检查:检查热处理设备的运行状态,包括加热炉、冷却设备和控制系统等,确保其正常工作。
4. 工艺参数设定:根据工艺要求,设定加热温度、保温时间和冷却速率等参数。
三、作业流程1. 材料装夹:根据材料形状和尺寸,选择适当的装夹方法,确保材料在热处理过程中的稳定性和均匀性。
2. 加热过程:a. 将材料放入预热炉中,按照设定的温度曲线进行加热。
b. 控制加热速率,确保材料温度均匀上升,避免温度梯度过大引起应力集中。
c. 达到设定温度后,保持一定的保温时间,使材料达到所需的组织状态。
3. 冷却过程:a. 根据热处理工艺要求,选择适当的冷却方式,如水淬、油淬或空冷等。
b. 控制冷却速率,避免快速冷却引起材料的裂纹和变形。
4. 温度监控:在整个热处理过程中,通过温度传感器和控制系统实时监控和调节材料的温度,确保工艺参数的准确性和稳定性。
5. 作业记录:记录热处理过程中的关键参数,包括加热温度、保温时间、冷却方式和材料性能等,以备后续分析和追溯。
四、安全注意事项1. 确保作业场所通风良好,防止有害气体积聚。
2. 佩戴个人防护装备,如防护眼镜、耳塞、手套和防护服等。
3. 遵守操作规程,禁止在未经许可的情况下进行个人行为,如吸烟、饮食等。
4. 注意热处理设备和材料的温度,避免烫伤和热飞溅。
5. 使用合适的工具和设备进行作业,避免意外事故发生。
五、质量控制1. 检验方法:根据热处理工艺要求,选择适当的检验方法,包括金相显微镜、硬度计、拉伸试验机等,对热处理后的材料进行性能测试。
热处理作业指导书

热处理作业指导书引言概述:热处理是一种重要的金属加工工艺,通过控制材料的温度和时间来改变其结构和性能。
为了确保热处理作业的质量和效率,制定一份热处理作业指导书是非常必要的。
本文将详细介绍热处理作业指导书的内容和要点。
一、热处理前的准备工作1.1 清洁工作:在进行热处理之前,要确保工件表面干净无杂质,可以采用化学清洗或者机械清洗等方法。
1.2 检查工件:对工件进行外观检查和尺寸测量,确保工件符合要求。
1.3 准备热处理设备:检查热处理设备的工作状态,保证设备正常运行。
二、热处理工艺参数设定2.1 确定热处理工艺:根据工件材料和要求,选择合适的热处理工艺,包括加热温度、保温时间和冷却方式等。
2.2 设定热处理参数:根据热处理工艺要求,设定炉温、保温时间和冷却速度等参数。
2.3 监控热处理过程:在热处理过程中,要及时监控温度和时间,确保工艺参数的准确性。
三、热处理作业操作流程3.1 上料:将清洁的工件放入热处理炉中,注意罗列方式和间距。
3.2 加热保温:根据设定的工艺参数,进行加热保温处理,保证工件达到所需温度。
3.3 冷却处理:根据工艺要求选择合适的冷却方式,如空冷、水冷或者油冷等,确保工件的结构和性能。
四、热处理后的检验与评定4.1 金相检验:对热处理后的工件进行金相组织观察,评定组织结构是否符合要求。
4.2 硬度测试:进行硬度测试,检测工件的硬度值是否符合标准。
4.3 尺寸测量:对工件的尺寸进行测量,确保尺寸精度符合要求。
五、热处理作业记录与存档5.1 记录数据:对热处理过程中的关键数据进行记录,包括炉温、保温时间、冷却方式等。
5.2 制作报告:根据记录的数据,制作热处理作业报告,包括工艺参数、操作流程和检验结果等。
5.3 存档管理:将热处理作业报告进行存档管理,确保数据的完整性和可追溯性。
结语:热处理作业指导书是热处理作业的重要参考依据,通过严格遵守指导书的要求,可以确保热处理作业的质量和效率。
热处理作业指导书

热处理作业指导书一、引言热处理是一种通过控制材料的加热和冷却过程,改变其微观结构以达到改善材料性能的工艺。
本指导书旨在为热处理作业提供详细的指导,确保作业的安全性、高效性和质量。
二、作业准备1. 确认热处理工艺:根据材料种类和要求,确定适当的热处理工艺,包括加热温度、保温时间和冷却方式等。
2. 检查设备和工具:确保热处理设备完好无损,工具齐全,并进行必要的维护和检修。
3. 检查材料:仔细检查待处理材料的质量和数量,确保符合要求。
三、作业流程1. 材料准备a. 清洁材料:使用适当的清洁剂和工具,将待处理材料表面的污垢和油脂彻底清除。
b. 标记材料:在材料上进行清晰可见的标记,以便追踪和识别。
2. 加热处理a. 材料装夹:根据工艺要求,将材料进行适当的装夹,确保材料的稳定性和均匀加热。
b. 加热设定:根据工艺要求,将热处理设备设置到指定的加热温度,并确保温度的稳定性和均匀性。
c. 加热操作:将装夹好的材料放入热处理设备中,按照工艺要求进行加热操作,控制保温时间和温度。
d. 监控和记录:在加热过程中,对温度进行实时监控,并记录相关数据,以备后续分析和验证。
3. 冷却处理a. 冷却方式:根据工艺要求,选择适当的冷却方式,如水淬、油淬或空冷等。
b. 冷却操作:将加热处理后的材料放入冷却介质中,控制冷却速度和时间,确保材料的均匀冷却。
c. 监控和记录:在冷却过程中,对冷却介质的温度进行实时监控,并记录相关数据,以备后续分析和验证。
四、作业安全1. 人员防护:作业人员必须佩戴适当的个人防护装备,包括安全帽、防护眼镜、防护手套和防护鞋等。
2. 设备安全:确保热处理设备的安全性能,包括设备的接地、电气线路的绝缘和设备的稳定性等。
3. 灭火设备:在作业现场配备足够的灭火设备,并确保操作人员熟悉使用方法。
4. 废气排放:合理安排废气排放系统,确保废气排放达标,减少对环境的污染。
五、作业质量控制1. 温度控制:确保加热和冷却过程中的温度控制准确,避免温度过高或过低导致材料性能不稳定。
热处理作业指导书

热处理作业指导书一、引言热处理是一种通过加热和冷却材料来改变其物理和化学性质的工艺。
本指导书旨在提供热处理作业的详细步骤和操作要求,以确保作业的安全性、质量和效率。
二、作业准备1. 确定热处理的材料和要求,包括材料类型、尺寸、形状、硬度要求等。
2. 检查热处理设备的状态,确保其正常运行和安全可靠。
3. 准备所需的工具和设备,包括炉子、温度计、冷却介质等。
4. 确定热处理的工艺参数,包括加热温度、保温时间、冷却速率等。
三、热处理步骤1. 清洁材料:将待处理材料进行清洁,去除表面的污垢和氧化物。
2. 加热:将清洁后的材料放入预热炉中,逐渐升温至所需的加热温度。
确保加热速率适中,避免材料的过热或热应力。
3. 保温:在达到加热温度后,将材料保持在该温度下一定的时间,以确保热处理效果的达到。
4. 冷却:根据热处理要求,选择适当的冷却方法,如水淬、油淬或空冷。
确保冷却速率符合要求,避免材料的过冷或不均匀冷却。
5. 清理和检查:将热处理后的材料进行清理,去除表面的残留物。
进行必要的检查,如硬度测试、显微组织观察等,以评估热处理效果。
四、安全注意事项1. 操作人员必须熟悉热处理设备的操作规程和安全注意事项。
2. 在操作过程中,严禁接触加热设备和热处理材料,以免发生烫伤事故。
3. 加热和冷却过程中,要确保操作环境的通风良好,避免有害气体的积聚。
4. 在使用冷却介质时,要防止溅入眼睛和皮肤,必要时佩戴防护眼镜和手套。
5. 在热处理过程中,要随时观察材料的变化情况,如有异常应及时采取措施。
五、质量控制和记录1. 对于每次热处理作业,要制定相应的质量控制计划,包括对材料硬度、显微组织等进行检测和评估。
2. 在热处理过程中,要及时记录关键参数,如加热温度、保温时间、冷却方法等。
3. 对于热处理后的材料,要进行必要的质量检验,确保其符合规定的技术要求。
4. 所有的热处理作业记录和质量检验报告要进行归档保存,以备查阅和追溯。
天钢板厂热处理作业指导书-热处理岗位作业指导书(DOC13页)
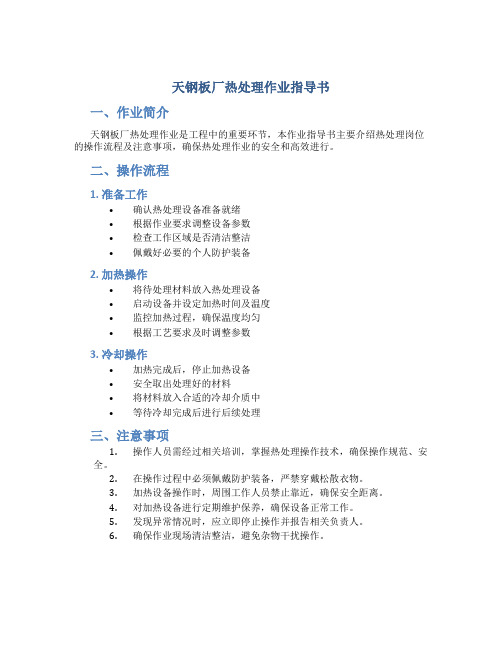
天钢板厂热处理作业指导书
一、作业简介
天钢板厂热处理作业是工程中的重要环节,本作业指导书主要介绍热处理岗位的操作流程及注意事项,确保热处理作业的安全和高效进行。
二、操作流程
1. 准备工作
•确认热处理设备准备就绪
•根据作业要求调整设备参数
•检查工作区域是否清洁整洁
•佩戴好必要的个人防护装备
2. 加热操作
•将待处理材料放入热处理设备
•启动设备并设定加热时间及温度
•监控加热过程,确保温度均匀
•根据工艺要求及时调整参数
3. 冷却操作
•加热完成后,停止加热设备
•安全取出处理好的材料
•将材料放入合适的冷却介质中
•等待冷却完成后进行后续处理
三、注意事项
1.操作人员需经过相关培训,掌握热处理操作技术,确保操作规范、安
全。
2.在操作过程中必须佩戴防护装备,严禁穿戴松散衣物。
3.加热设备操作时,周围工作人员禁止靠近,确保安全距离。
4.对加热设备进行定期维护保养,确保设备正常工作。
5.发现异常情况时,应立即停止操作并报告相关负责人。
6.确保作业现场清洁整洁,避免杂物干扰操作。
四、总结
热处理作业对于产品质量和性能具有重要影响,操作人员必须严格按照作业指导书要求进行操作,确保每一道工序都符合要求。
只有做好每一个细节,才能保证热处理作业的顺利进行,提高产品质量和生产效率。
以上为《天钢板厂热处理作业指导书》的内容摘要,希望每位操作人员能认真遵守操作规程,确保热处理作业顺利进行,谨防安全事故的发生。
作业指导书(热处理)

作业指导书(热处理)第一篇:作业指导书(热处理)热处理是金属加工中常见的一种工艺,通过加热和冷却金属材料,可以改变其组织结构和性能。
热处理可以分为多种类型,包括退火、淬火、回火等。
本篇文章将重点介绍热处理的基本原理和常见方法。
热处理的基本原理是通过控制金属材料的加热和冷却过程,使其产生期望的组织结构和性能变化。
热处理的过程可以分为三个阶段:加热、保温和冷却。
加热过程将金属材料加热到一定温度,使组织发生相变。
保温过程使金属材料的组织结构得到稳定,并使其达到均匀性。
冷却过程是将金属材料迅速冷却,使其组织结构固定下来。
热处理的常见方法之一是退火。
退火是通过将金属材料加热至适当温度,然后缓慢冷却的过程。
退火可以改善金属材料的塑性和韧性,并降低其硬度。
退火适用于处理冷加工后的金属材料,可以消除内部应力、改善金属的可加工性。
淬火是热处理的另一种常见方法。
淬火是通过将金属材料加热至适当温度,然后迅速冷却的过程。
淬火可以使金属材料产生马氏体组织,提高其硬度和强度。
淬火后的金属材料通常呈脆性,需要进一步进行回火来提高其韧性。
回火是淬火的后续处理步骤,通过将淬火后的金属材料加热至一定温度,然后缓慢冷却。
回火可以降低金属材料的硬度,提高其韧性和抗冲击性。
回火的温度和时间选择取决于金属的种类和期望的性能。
除了退火、淬火和回火,热处理还包括正火、间歇淬火、表面淬火等多种方法。
正火是将金属材料加热至适当温度,然后以较慢的速度冷却的过程。
正火可使金属材料的组织结构细化,提高其强度和韧性。
间歇淬火是将金属材料加热至适当温度,然后在空气中冷却。
表面淬火是将金属材料表面加热至适当温度,然后迅速冷却。
热处理在金属加工中起到了重要的作用。
通过热处理,可以改变金属材料的性能,使其更适合特定的应用。
然而,不同的金属材料对热处理的响应有所差异,因此在进行热处理之前,需要对材料进行详细的分析和实验,以确定最合适的处理方法。
总结起来,热处理是金属加工中常见的一种工艺,通过加热和冷却金属材料,可以改变其组织结构和性能。
热处理车间热处理作业指导书

热处理车间热处理作业指导书引言概述:热处理是一项重要的工艺,用于改善金属材料的性能。
为了确保热处理作业的准确性和安全性,制定一份热处理作业指导书是必要的。
本文将从五个大点来详细阐述热处理车间热处理作业指导书的内容和要求。
正文内容:1. 热处理作业前准备1.1 温度控制要求- 确定热处理温度和保温时间,根据材料类型和要求进行调整。
- 使用准确的温度计和热处理炉,确保温度控制的准确性。
- 监测炉内温度分布,避免温度梯度过大,导致不均匀的热处理效果。
1.2 材料准备- 清洁材料表面,去除杂质和氧化层,确保热处理效果。
- 检查材料尺寸和形状,确保符合要求。
- 根据材料特性和要求,选择适当的热处理工艺。
1.3 保护措施- 采取防护措施,确保操作人员的安全。
- 使用适当的个人防护装备,如耐高温手套、护目镜等。
- 确保热处理作业区域通风良好,排除有害气体。
2. 热处理作业流程2.1 加热阶段- 根据热处理工艺要求,将材料放入预热炉进行加热。
- 控制加热速度,避免材料过热或者温度变化过快。
- 监测材料温度,确保达到所需温度。
2.2 保温阶段- 将加热后的材料转移到保温炉,保持一定时间。
- 控制保温时间,确保材料达到所需的组织结构和性能。
- 监测保温过程中的温度变化,及时调整炉内温度。
2.3 冷却阶段- 将保温完成的材料转移到冷却装置中进行冷却。
- 选择适当的冷却介质和速度,控制冷却过程。
- 避免快速冷却引起的变形和裂纹。
3. 热处理作业质量控制3.1 温度控制- 使用准确的温度计和热处理设备,确保温度的准确性。
- 监测炉内温度分布,调整加热和保温时间,以达到均匀的温度分布。
3.2 时间控制- 根据热处理工艺要求,控制加热和保温时间。
- 监测保温时间,确保材料达到所需的组织结构和性能。
3.3 冷却控制- 选择适当的冷却介质和速度,控制冷却过程。
- 避免快速冷却引起的变形和裂纹。
4. 热处理作业安全控制4.1 作业人员安全- 提供必要的个人防护装备,确保作业人员的安全。
热处理作业指导书
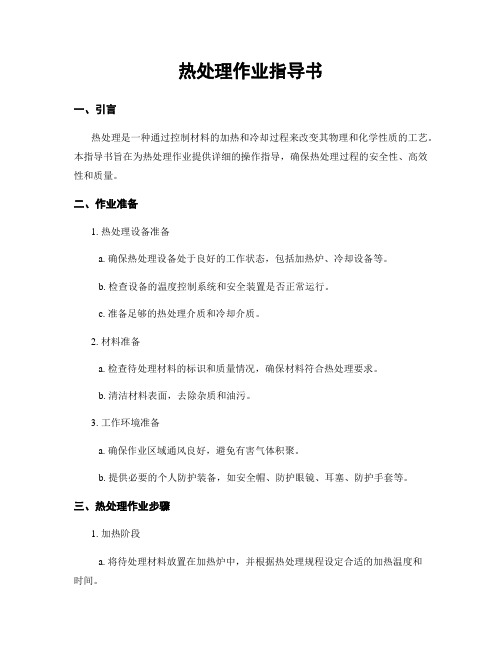
热处理作业指导书一、引言热处理是一种通过控制材料的加热和冷却过程来改变其物理和化学性质的工艺。
本指导书旨在为热处理作业提供详细的操作指导,确保热处理过程的安全性、高效性和质量。
二、作业准备1. 热处理设备准备a. 确保热处理设备处于良好的工作状态,包括加热炉、冷却设备等。
b. 检查设备的温度控制系统和安全装置是否正常运行。
c. 准备足够的热处理介质和冷却介质。
2. 材料准备a. 检查待处理材料的标识和质量情况,确保材料符合热处理要求。
b. 清洁材料表面,去除杂质和油污。
3. 工作环境准备a. 确保作业区域通风良好,避免有害气体积聚。
b. 提供必要的个人防护装备,如安全帽、防护眼镜、耳塞、防护手套等。
三、热处理作业步骤1. 加热阶段a. 将待处理材料放置在加热炉中,并根据热处理规程设定合适的加热温度和时间。
b. 监控加热过程中的温度变化,确保加热速率符合要求。
c. 在加热过程中,根据需要进行气氛控制,如氧化性、还原性等。
2. 保温阶段a. 达到设定的加热温度后,保持材料在该温度下一定时间,以确保热处理效果。
b. 根据材料的特性和热处理要求,确定保温时间。
3. 冷却阶段a. 根据热处理规程,选择合适的冷却介质和冷却速率。
b. 将材料迅速浸入冷却介质中,确保冷却均匀。
c. 监控冷却过程中的温度变化,确保冷却速率符合要求。
四、作业记录与质量控制1. 记录a. 在热处理过程中,及时记录加热温度、保温时间、冷却速率等关键参数。
b. 记录材料的标识、数量和热处理批次等信息。
2. 质量控制a. 根据热处理规程,对热处理后的材料进行质量检验,包括硬度、组织结构等。
b. 根据质量检验结果,对热处理工艺进行调整和改进。
五、安全注意事项1. 操作人员必须熟悉热处理设备的操作规程和安全注意事项。
2. 在操作过程中,严禁使用损坏或不合格的设备和工具。
3. 加热炉周围必须保持清洁,防止杂物积聚引发安全事故。
4. 加热炉和冷却设备的电源必须可靠接地,以防止电击事故。
热处理作业指导书

热处理作业指导书一、引言热处理是一种通过控制材料的温度和时间来改变其物理和化学性质的工艺。
本作业指导书旨在提供详细的操作步骤和注意事项,以确保热处理过程的安全性和有效性。
二、作业准备1. 确保操作人员具备相关的热处理知识和技能,并已接受相关培训。
2. 检查热处理设备的运行状态,确保其正常工作。
3. 准备所需的热处理工具和材料,如炉子、保护气体、夹具等。
4. 检查待处理材料的质量和数量,确保其符合要求。
三、作业步骤1. 清洁和预处理a. 将待处理材料进行清洁,去除表面的污垢和氧化物。
b. 如果需要,进行预处理操作,如去应力退火、淬火或固溶处理等。
2. 加热a. 将待处理材料放入热处理炉中,确保其位置稳定。
b. 根据材料的特性和所需的热处理过程,设置合适的加热温度和保持时间。
c. 确保炉内的温度均匀分布,避免温度梯度过大。
3. 冷却a. 在加热完成后,将材料从炉中取出,放置在合适的冷却介质中,如水、油或空气等。
b. 控制冷却速率,以确保材料的组织和性能得到理想的调整。
4. 检验和测试a. 对热处理后的材料进行必要的检验和测试,如硬度测试、金相分析等。
b. 根据检验结果,评估热处理的效果,并记录相关数据。
5. 后处理a. 根据热处理结果,进行必要的后处理操作,如回火、淬火和时效处理等。
b. 确保后处理操作的参数和步骤符合要求,并记录相关数据。
四、安全注意事项1. 操作人员应穿戴适当的防护装备,如防火服、耳塞、眼镜等。
2. 在加热和冷却过程中,操作人员应保持距离热处理设备,避免烫伤或其他意外伤害。
3. 确保热处理设备的通风良好,避免有害气体的积聚。
4. 在操作过程中,严禁吸烟、使用明火等可能引起火灾的行为。
5. 定期检查热处理设备和工具的状态,及时修理或更换损坏的部件。
五、记录和报告1. 在每次热处理作业完成后,记录相关的操作参数和结果数据。
2. 将记录保存在适当的文档或数据库中,以备将来参考和分析。
3. 根据需要,编写热处理作业报告,包括作业过程、结果分析和改进建议等。
热处理作业指导书

热处理作业指导书引言概述:热处理是一种常见的金属材料加工方法,通过控制材料的加热和冷却过程,改变其组织结构和性能,以提高材料的力学性能、耐磨性和耐腐蚀性等。
本文将为您介绍热处理作业的指导书,包括热处理的基本原理、作业流程、注意事项和常见问题解答,以匡助您更好地进行热处理作业。
一、热处理的基本原理1.1 加热过程热处理的第一步是将材料加热到一定温度。
加热温度取决于材料的种类和要达到的性能要求。
常见的加热方法包括火焰加热、电阻加热和感应加热。
在加热过程中,需要注意以下几点:(1)控制加热速率:过快的加热速率可能导致材料内部应力过大,引起变形或者开裂。
因此,应根据材料的热导率和热膨胀系数,合理控制加热速率。
(2)保持均匀加热:确保材料在加热过程中均匀受热,避免浮现温度梯度过大的情况,以免引起组织不均匀或者应力集中。
1.2 保温过程在达到所需加热温度后,需要将材料保持在一定温度下,以使其组织发生相应的变化。
保温时间取决于材料的类型和要达到的性能要求。
在保温过程中,需要注意以下几点:(1)控制保温时间:过短的保温时间可能导致组织转变不彻底,影响材料的性能。
而过长的保温时间则可能导致材料的晶粒长大过大,影响材料的综合性能。
(2)保持稳定温度:保温过程中需要控制温度的稳定性,避免温度波动引起组织不均匀或者性能下降。
1.3 冷却过程在保温结束后,需要将材料迅速冷却,以固定其组织结构和性能。
冷却方法通常包括水淬、油淬和空冷等。
在冷却过程中,需要注意以下几点:(1)选择适当的冷却介质:根据材料的种类和要求的性能,选择合适的冷却介质。
不同的冷却介质会对材料的组织结构和性能产生不同的影响。
(2)控制冷却速率:过快或者过慢的冷却速率都可能导致材料的性能下降。
因此,需要根据材料的热导率和冷却介质的特性,合理控制冷却速率。
二、热处理作业流程2.1 准备工作(1)选择合适的材料:根据需要改善的性能要求,选择合适的材料进行热处理。
热处理作业指导书

热处理作业指导书一、概述热处理是一种通过控制材料的温度和时间来改变其物理和化学性质的工艺。
本指导书旨在提供热处理作业的详细流程和操作要求,以确保热处理过程的准确性和可靠性。
二、作业准备1. 材料准备:确保待处理的材料符合热处理要求,并进行必要的清洁和表面处理。
2. 设备准备:检查热处理设备的运行状态和温度控制系统的准确性。
3. 环境准备:确保作业现场的温度、湿度和通风等环境条件符合热处理要求。
三、作业流程1. 材料装夹:根据热处理要求,将待处理材料装夹到热处理设备中,并确保装夹稳固和安全。
2. 加热升温:根据材料的热处理规范,设定合适的加热速率和升温温度,启动热处理设备进行加热。
3. 保温保持:达到目标温度后,根据热处理要求设定保温时间,并确保温度的稳定性和均匀性。
4. 冷却控制:根据材料的冷却要求,选择合适的冷却介质和速率进行冷却,确保材料的组织和性能得到最佳调控。
5. 温度监控:在整个热处理过程中,持续监控和记录材料的温度变化,以确保热处理过程的准确性和可追溯性。
6. 试样取样:根据需要,取出合适数量的试样进行金相分析和性能测试,以评估热处理效果。
7. 清洁维护:作业结束后,对热处理设备进行清洁和维护,确保设备的正常运行和使用寿命。
四、安全注意事项1. 操作人员必须佩戴符合要求的个人防护装备,包括耐热手套、防护眼镜和防护服等。
2. 严禁在热处理设备周围堆放易燃物品,确保作业现场的安全和整洁。
3. 在进行加热和冷却过程中,严禁将手部或者其他身体部位挨近热处理设备,以防止烫伤事故的发生。
4. 确保热处理设备的电气系统和温度控制系统的正常运行,避免电气故障引起火灾或者其他安全事故。
5. 严格遵守热处理设备的操作规程和维护要求,定期进行设备的检查和保养,确保设备的安全和可靠性。
五、质量控制1. 根据热处理要求,制定合适的工艺参数和检验标准,确保热处理效果的稳定性和一致性。
2. 进行金相分析和性能测试,评估热处理后材料的组织和性能是否符合要求。
热处理作业指导书

热处理作业指导书一、引言热处理是一种通过加热和冷却金属材料来改变其物理和化学性质的工艺。
本作业指导书旨在为热处理作业提供详细的操作指导,确保作业的安全性和效果。
二、作业准备1. 确定热处理工艺:根据材料类型、要求的物理性质和化学性质,选择合适的热处理工艺。
2. 准备设备和工具:确保热处理设备完好无损,并准备好所需的工具,如温度计、时钟等。
3. 确定作业区域:选择一个干燥、通风良好的作业区域,并确保有足够的空间进行操作。
4. 个人防护措施:佩戴适当的个人防护装备,如安全眼镜、耳塞、手套和防护服。
三、作业步骤1. 清洁材料:在进行热处理之前,必须确保材料表面干净,无油污和杂质。
可以使用溶剂或机械方法进行清洁。
2. 加热:根据选定的热处理工艺,将材料放入热处理设备中,并按照设备说明书设置合适的温度和时间。
确保材料均匀受热,避免过热或过冷。
3. 保温:在达到所需温度后,保持材料在设备中的一定时间,以确保热量充分传递和吸收,使材料达到所需的物理和化学性质。
4. 冷却:根据热处理工艺的要求,选择合适的冷却方法。
可以是自然冷却、水冷却或气体冷却。
确保冷却速度适当,以避免材料产生应力和变形。
5. 检测和评估:在完成热处理后,对材料进行检测和评估,以确保其达到所需的物理和化学性质。
可以使用金相显微镜、硬度计等设备进行检测。
四、安全注意事项1. 热处理设备和工具必须处于良好的工作状态,定期进行检查和维护。
2. 在进行热处理作业时,必须佩戴适当的个人防护装备,如安全眼镜、耳塞、手套和防护服。
3. 严禁在热处理区域内吸烟、使用明火等易引发火灾的行为。
4. 在进行热处理作业时,必须严格按照操作规程进行,避免操作失误和意外发生。
5. 在热处理过程中,应注意材料的温度和冷却速度,避免产生应力和变形。
五、常见问题及解决方法1. 材料表面出现氧化:可以使用酸洗或其他表面处理方法去除氧化层。
2. 材料硬度不符合要求:可以重新进行热处理,调整加热温度和时间,或者选择其他热处理工艺。
热处理作业指导书

热处理作业指导书一、引言热处理是一种通过控制材料的温度和时间来改变其物理和机械性质的工艺。
本作业指导书旨在提供热处理作业的详细步骤和操作要点,以确保热处理过程的安全性和有效性。
二、作业准备1. 确保热处理设备处于良好的工作状态,包括加热元件、温度控制系统和冷却装置等。
2. 检查材料的质量和数量,确保符合要求,并进行必要的标记和记录。
3. 准备必要的工具和设备,如热处理炉、夹具、传感器和测量工具等。
4. 确保作业场所通风良好,并配备必要的个人防护装备,如防护眼镜、耳塞、手套和防护服等。
三、作业步骤1. 根据热处理要求,将材料放置在热处理炉中,并确保夹具的稳固性和正确性。
2. 启动热处理炉,根据所需温度和时间设定合适的参数,并确保温度控制系统的准确性。
3. 监测热处理过程中的温度变化,并及时调整温度控制系统,确保温度在所需范围内稳定。
4. 在热处理过程中,根据需要进行必要的测量和记录,如温度、时间、压力温和氛等。
5. 确保热处理过程中的安全性,防止火灾和爆炸等事故,并及时采取应急措施。
6. 热处理结束后,关闭热处理炉,等待冷却到安全温度后,将材料取出并进行必要的检查和测试。
7. 根据热处理结果,对材料进行必要的记录和分类,以便后续使用和追溯。
四、作业注意事项1. 严格按照热处理要求进行操作,避免超过材料的最大温度和时间限制。
2. 在热处理过程中,注意炉内的温度均匀性,避免产生过渡热应力和变形等问题。
3. 在热处理过程中,避免与热处理炉内的加热元件和高温表面直接接触,以免造成烫伤和损坏。
4. 在热处理过程中,注意气氛控制,避免氧化和腐蚀等问题,可使用适当的保护气体和包装材料。
5. 在热处理过程中,遵守相关的安全操作规程,如穿戴个人防护装备、避免热处理炉内的烟尘吸入等。
6. 在热处理过程中,及时处理可能浮现的异常情况,如温度偏差、设备故障和材料损坏等,确保作业的连续性和准确性。
五、作业记录和追溯1. 对每次热处理作业进行详细的记录,包括材料的标识、热处理参数、测量数据和操作人员等信息。
热处理作业指导书
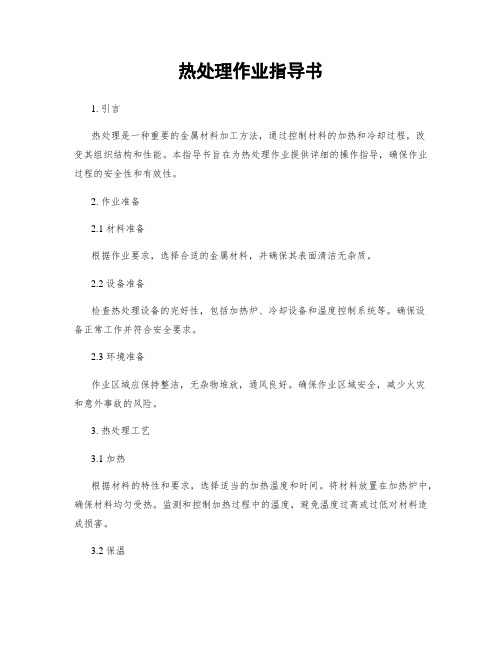
热处理作业指导书1. 引言热处理是一种重要的金属材料加工方法,通过控制材料的加热和冷却过程,改变其组织结构和性能。
本指导书旨在为热处理作业提供详细的操作指导,确保作业过程的安全性和有效性。
2. 作业准备2.1 材料准备根据作业要求,选择合适的金属材料,并确保其表面清洁无杂质。
2.2 设备准备检查热处理设备的完好性,包括加热炉、冷却设备和温度控制系统等。
确保设备正常工作并符合安全要求。
2.3 环境准备作业区域应保持整洁,无杂物堆放,通风良好。
确保作业区域安全,减少火灾和意外事故的风险。
3. 热处理工艺3.1 加热根据材料的特性和要求,选择适当的加热温度和时间。
将材料放置在加热炉中,确保材料均匀受热。
监测和控制加热过程中的温度,避免温度过高或过低对材料造成损害。
3.2 保温在达到加热温度后,保持材料在一定温度范围内保温一段时间,以确保材料的组织结构得到充分改变。
3.3 冷却根据热处理要求,选择适当的冷却方式。
常见的冷却方式包括空冷、水冷和油冷等。
确保冷却速率符合要求,避免材料因冷却过快或过慢而导致不良组织和性能。
3.4 淬火对于需要淬火的材料,将其迅速浸入冷却介质中,以快速冷却材料并形成所需的组织结构。
淬火介质的选择应根据材料的特性和要求进行合理选择。
4. 检测与评估热处理后的材料需要进行检测和评估,以确保其达到预期的性能要求。
4.1 金相组织观察通过金相显微镜观察材料的组织结构,检查是否符合要求。
观察晶粒大小、相比例和相分布等特征,并与标准进行对比评估。
4.2 硬度测试使用硬度测试仪对材料进行硬度测试,确定其硬度值是否符合要求。
常用的硬度测试方法包括布氏硬度和洛氏硬度等。
4.3 机械性能测试根据需要,对材料进行拉伸、弯曲、冲击等机械性能测试,评估其强度、韧性和冲击性能等。
5. 安全注意事项5.1 个人防护在进行热处理作业时,必须佩戴适当的个人防护装备,如防火服、防护手套和安全鞋等。
避免直接接触高温材料和冷却介质,以防止烫伤和化学伤害。
热处理作业指导书
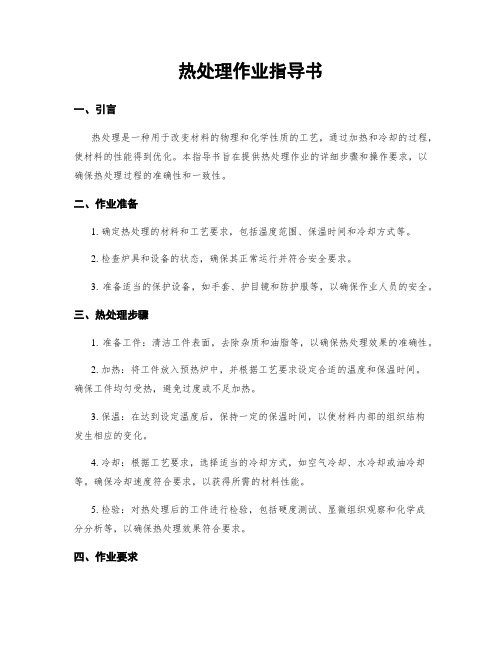
热处理作业指导书一、引言热处理是一种用于改变材料的物理和化学性质的工艺,通过加热和冷却的过程,使材料的性能得到优化。
本指导书旨在提供热处理作业的详细步骤和操作要求,以确保热处理过程的准确性和一致性。
二、作业准备1. 确定热处理的材料和工艺要求,包括温度范围、保温时间和冷却方式等。
2. 检查炉具和设备的状态,确保其正常运行并符合安全要求。
3. 准备适当的保护设备,如手套、护目镜和防护服等,以确保作业人员的安全。
三、热处理步骤1. 准备工件:清洁工件表面,去除杂质和油脂等,以确保热处理效果的准确性。
2. 加热:将工件放入预热炉中,并根据工艺要求设定合适的温度和保温时间。
确保工件均匀受热,避免过度或不足加热。
3. 保温:在达到设定温度后,保持一定的保温时间,以使材料内部的组织结构发生相应的变化。
4. 冷却:根据工艺要求,选择适当的冷却方式,如空气冷却、水冷却或油冷却等。
确保冷却速度符合要求,以获得所需的材料性能。
5. 检验:对热处理后的工件进行检验,包括硬度测试、显微组织观察和化学成分分析等,以确保热处理效果符合要求。
四、作业要求1. 操作人员应具备热处理工艺的基本知识和技能,了解不同材料的热处理要求。
2. 操作人员应严格按照工艺要求进行操作,确保加热温度、保温时间和冷却方式的准确性。
3. 操作人员应正确使用个人防护设备,保证自身安全。
4. 操作人员应定期检查和维护炉具和设备,确保其正常运行。
5. 操作人员应及时记录热处理过程中的关键参数和结果,以便后续分析和追溯。
五、安全注意事项1. 操作人员应熟悉炉具和设备的操作手册,并按照要求进行操作。
2. 确保热处理区域通风良好,避免有害气体积聚。
3. 确保炉具和设备的电气安全,避免火灾和电击等危险。
4. 确保炉具和设备的机械安全,避免意外事故发生。
5. 在操作过程中,严禁随意更改工艺参数,以免影响热处理效果和材料性能。
六、总结本指导书详细介绍了热处理作业的步骤和要求,包括作业准备、热处理步骤、作业要求和安全注意事项等。
- 1、下载文档前请自行甄别文档内容的完整性,平台不提供额外的编辑、内容补充、找答案等附加服务。
- 2、"仅部分预览"的文档,不可在线预览部分如存在完整性等问题,可反馈申请退款(可完整预览的文档不适用该条件!)。
- 3、如文档侵犯您的权益,请联系客服反馈,我们会尽快为您处理(人工客服工作时间:9:00-18:30)。
1. 项目工程概况及工程量本作业指导书适用于辽宁盘山新城热力有限公司热电项目安装工程的钢制焊件的热处理工作。
本工程的热处理工作主要包括对委托单位委托的钢制焊件进行的焊前预热、后热和焊后热处理。
1.1 编制依据1.1.1 《中国人民共和国安全生产法》主席令第13 号1.1.2 《中华人民共和国特种设备安全法》主席令第4 号1.1.3 《特种设备安全监察条例》国务院令第549 号1.1.4 火力发电厂焊接热处理技术规程》DL/T 819-20101.1.5 《火力发电厂焊接技术规程》DL/T 869-2012 。
1.1.6 《火力发电厂异种钢焊接技术规程》DL/T 752-2010 。
1.1.7 DL5009.1-2014《电力建设安全工作规程第一部分:火力发电》2. 项目作业进度的安排热处理工作的进度要求是满足现场热处理工作的需要,不影响下道工序的正常进行。
3. 作业准备工作及条件3.1 作业人员的质量3.1.1 热处理人员必须经过专业培训考核并取得资格证书后方可上岗。
3.1.2 热处理人员必须经过安全考试合格后方可工作。
3.1.3 热处理人员必须认真学习《火力发电厂焊接技术规程》DL/T 869-2012 ;《火力发电厂焊接热处理技术规程》DL/T 819-2010 等标准规范;熟练掌握常用钢材的热处理工艺参数。
3.1.4 熟练掌握控温设备、焊炬、测温仪等的使用与维护。
3.2 作业机械、工具、仪器、仪表的要求3.2.1 热处理控温柜、焊炬等的使用性能必须能满足工艺要求,安全、可靠。
3.2.2 温度记录仪、热电偶等计量器具必须经过计量检定合格,并在有效期内。
3.2.3 控温柜、测温仪等要由专人负责保养、使用和维护,使其处于良好的运行状态。
3.2.4 配备钳子、扳手、验电笔等工具。
3.2.5 准备相应数量、规格、性能符合标准要求的柔性陶瓷电阻加热器、硅酸铝保温材料、K分度的铠装热电偶、焊炬、氧气、乙炔、细铁丝、绝缘胶布等。
4. 作业程序及作业方法4.1 热处理作业流程图(见图1)4.2 加热方法的选择本工程采用的加热方法主要有柔性陶瓷电阻加热法和火焰(氧-乙炔)加热法两种。
柔性陶瓷电阻加热法适用于焊前预热、后热和焊后热处理。
采用热电偶进行温度测量,并用自动控温设备进行温度监控和记录。
火焰加热法适用于难以使用柔性陶瓷电阻加热法的场合,适用于焊件的焊前预热和后热。
如需采用火焰加热进行焊后热处理时,应详细的编制施工方案,以保证加热均匀,并有有效的温度控制措施。
对高合金焊件不宜采用火焰加热进行焊后热处理。
火焰加热时采用远红外测温仪进行温度监测。
签发热处理资料、审核、存档热处理作业流程图4.3焊前预热4.3.1通常采用柔性陶瓷电阻炉或火焰(氧-乙炔)进行局部加热。
4.3.2常用钢材的焊前预热温度见表1。
表1 常用钢材的焊前预热温度注1:上表中的温度为根据壁厚确定的最低预热温度,当采用乌极氩弧焊打底时,可按下限温度降低50 预热。
注2:环境温度低于允许进行焊接操作的规定值时,应在原预热温度的基础上提高30 C〜50C;对于待焊接部件厚度小于表中规定板材、管材需预热的厚度时,应按表中规定的温度进行预热。
注3:承压件与非承压件进行预热,接管与主管焊接时,应按主管进行预热。
注4:表中预热温度上限值亦可以理解为焊接层间温度上限。
4.3.3 当加热器在待焊接焊缝两侧分别布置或全覆盖布置时,加热宽度自待焊接焊缝边缘始计算。
若采用柔性陶瓷电阻加热,预热宽度每侧不少于4 倍的焊件厚度;火焰加热,每侧加热宽度不少于焊件厚度的3倍,且不小于100mm当待焊接区为类似点状时,加热范围是以焊接中心为圆心,以焊缝最大深度尺寸的9 倍为半径的近园形区域。
4.3.4对于管径》219mm或壁厚》20mn t勺管子,宜采用柔性陶瓷电阻炉加热。
4.3.5 异种钢焊接时预热温度应按:一侧为奥氏体型钢时,可以只对非奥氏体型钢单侧进行预热,应选择较低的预热温度:焊接时层间温度不宜超过150C。
两侧均为非奥氏体型钢时,应按母材预热温度较高的选择,层间温度不低于预热温度的下限。
4.3.6 接管座与主管焊接时,应以主管规定的预热温度为准。
4.3.7 非承压件与承压件焊接时,预热温度应按承压件选择。
4.3.8 当监测焊件坡口外热电偶达到预热温度时,应保持一定时间,使坡口待焊接部位的温度达到要求。
4.3.9对于SA-335P91钢,焊前预热还应做到:a)采用电加热,加热器布置在坡口两侧。
加热器边缘与坡口间的距离,以不影响焊接为原则。
测温点布置在加热区以内。
b)用远红外测温仪测量坡口处温度,达到要求时开始焊接。
焊接过程中,伴随加热跟踪监测层间温度。
4.3.10 重新预热a)焊接中断后,应在重新焊接前重新预热。
b)重新预热的工艺应与原预热工艺一致。
4.4 后热处理4.4.1对有冷裂纹倾向的焊件,焊后应立即进行热处理,否则应作后热处理。
其温度以300E〜400r为宜,恒温时间2h〜4h,其加热宽度与热处理要求相同。
4.4.2 对于SA-335P91 等马氏体型热强钢焊接接头不宜采用后热。
当被迫后热时,应在焊后焊件处于80C〜100C,保温1h〜2h后进行。
后热工艺为:温度300E〜350E为宜,恒温时间2h。
4.4.3 后热时的加热宽度应不小于预热时的加热宽度。
4.5 焊后热处理焊件的焊后热处理方式通常为高温回火。
应按DL/T869、DL/T752 的规定,或其他规程、工艺文件的要求对焊件进行焊后热处理。
对Cr含量为9%-12%勺马氏体钢,应在其完成马氏体转变后立即进行焊后热处理,否则应按4.4 的要求进行后热。
4.5.1 加热器功率及数量勺确定a)加热器功率(KV)数二管子直径X管子壁厚十625。
b)加热器的数量二加热器功率(KV y数十每块加热器的功率。
c)设备的总电流(A)=加热器功率(KV y数十电源电压(V)X 1000。
4.5.2 升、降温速度a)按V=6250/ S (单位为计算C / h,其中S为焊件厚度,单位mr)且不大于300E / h 升、降温过程中,温度在300C以下可不控制,但降温时必须在保温层内缓冷至室温;当壁厚大于100mm寸,升、降温速度按60r/ h进行控制。
b) SA-213T91及SA-335P91钢升、降温速度按V= 250 X(25/壁厚)C / h计算,且小于等于150r /h 进行。
c)当管子外径不大于108mn或厚度不大于10mm寸,若采用火焰加热时,可不控制加热速度。
d)对管座或返修焊件,应按主管的壁厚计算焊接热处理的升降温速度。
4.5.3常用钢材的焊后热处理温度与恒温时间见表2; 9〜12%Cr马氏体型耐热钢的焊后热处理温度与恒温时间见表3。
表2 常用钢材的焊后热处理温度与恒温时间表①管座或返修焊件,其恒温时间按焊件的名义厚度替代焊件厚度来确定,但应不少于30min。
②对于SA-335P91钢焊缝,焊后应在马氏体转变结束后立即进行热处理。
表3 9 〜12%Cr马氏体型耐热钢的焊后热处理温度与恒温时间表4.5.4异种钢焊接接头的焊后热处理,应按照两侧钢材及所用焊条(焊丝)综合考虑。
4.5.5焊后热处理温度的选择原则:a)不能超过焊接材料融敷金属及两侧母材中最低的下转变温度(A ci),一般以低于Ai以下30 Cb)对调质结构钢焊接接头,应低于调质处理时的回火温度。
c)对异种钢焊接接头,按照DL/T 752-2010的相关规定执行。
(两侧均为非奥氏体型钢时,其焊后热处理温度应按加热温度要求较低侧的加热温度上限来确定)4.5.6焊后热处理恒温时间的确定方法:a)焊后热处理恒温时间应根据材料类别、加热方法和焊件厚度综合确定。
b)一般按照焊件厚度确定恒温时间。
对中低合金钢,恒温时间按2min/m叶3min/mm计算,最少30min;对高合金钢,恒温时间按4min/mm-5min/mm计算,最少60min。
采用柔性陶瓷电阻加热时,取值偏于计算的上限。
c)管径不小于76mm采用SMAW填充盖面的9〜12%Cr马氏体型耐热钢焊接接头,焊后热处理的恒温时间应不小于2小时。
d)返修件及非熔透型管座,其恒温时间按焊件的名义厚度S'替代焊件厚度S来确定,但应不少于30min。
焊件的名义厚度S'可根据具体的焊缝结构计算:返修件及非熔透型管座:h v 5mn fl寸S'= 3h+5mmh=5mm 〜10mn寸寸S' =2h+10mmS' =h+20mm其他厚度情况可参照DL/T819-2010中643进行计算。
4.5.7下列焊接接头焊后应进行热处理壁厚>30mm 的碳素钢管子与管件;壁厚>32mnm 勺碳素钢容器;壁厚>28mm 的普通低合金 钢容器(A- U 类钢);壁厚大于20mm 勺普通低合金钢容器(A- m 类钢);耐热钢管子与管件和 壁厚大于20mm 勺普通低合金钢管道;经焊接工艺评定需作热处理的焊件。
4.5.8凡采用氩弧焊或低氢型焊条,焊前预热和焊后适当缓冷的下列部件可免作焊后热处理:壁厚小于等于10mm 管径小于等于108mm 的15CrMo 12CrMo 钢管子;壁厚小于等于 8mm 管径小于等于108mm 的12Cr1MoV 钢管子;壁厚小于等于 6mm 管径小于等于 63mm 的12Cr2MoWVTi 钢管子。
4.6温度测量4.6.1对于可以采用火焰加热进行热处理的焊接接头,用远红外测温仪进行温度检测。
4.6.2采用柔性陶瓷电阻加热器进行热处理的焊接接头,宜选用K 分度的防水型铠装热电偶 进行测温,仪表自动记录温度。
4.6.3用热电偶测温按以下要求进行:a ) 热电偶的安装位置与数量,应以保证测温和控温准确可靠、有代表性为原则。
b ) 预热时,控温热电偶应布置在加热区以内,监测热电偶应尽可能靠近待焊坡口,必要时,应使用其他测温方法检测待焊坡口的温度,见下图:图2 预热时加热宽度与测温点布置示意图c )一般情况下,焊缝后热、焊后热处理时,对管子外径不大于273mm 的管道,可以使用1支热电偶布置于焊缝中心;否则,应使用不少于 2支热电偶,并沿圆周均匀布置 于焊缝中心,测温点应按圆周对称布置,且不少于两点;水平管道的热电偶应上下对 称布置,其他热电偶布置于焊缝边缘 1倍壁厚处,且不超过50mm 并用焊缝处的热电偶控制温度,见下图:h>10mm 加热宽度监测热电偶控温热电偶< 50mm2号热电偶2号温区保温宽度图3 后热、焊后热处理分区控温与热电偶布置示意图d)应注意工件位置不同可能导致的加热区温度不均匀,对于管子外径不小于273mm勺管道,如果此种影响明显,则应该采取与分区加热相应的测温/控温方式安装热电偶。
e)异形结构焊件(如有焊缝的三通、管座等),后热、焊后热处理时,应注意采取措施使得焊件实际被加热的最高温度位于被热处理的焊缝上。