吸收稳定系统工艺流程讲义(ppt 24页)
催化裂化吸收稳定流程说明

催化裂化吸收稳定步骤说明一、工艺步骤叙述催化装置吸收稳定系统步骤模拟步骤图如图1 所表示。
由分馏塔顶油气分离器来富气经富气压缩机压缩到 1.6MPa(绝)。
压缩富气与解吸塔顶解吸气混合经气压机出口冷却器冷至55℃, 再与吸收塔底油混合, 经气压机出口后冷器冷至40℃, 进入平衡罐(D-301)分离出气相(富气)及液相(凝缩油)。
吸收塔(C-301)位于脱吸塔(C-302)上部, 压力1.4MPa(绝)。
由平衡罐来富气进入吸收塔下部, 自稳定塔返回补充吸收剂和分馏塔来粗汽油均进入吸收塔顶部, 与气体逆流接触。
吸收塔设有两个中段回流, 用以取走吸收过程所释放热量, 避免塔内温度上升过高。
中段回流自第14 层及第21 层用泵P3 及P4 抽出, 分别经水冷器(E-306, E-307)冷至40℃, 返塔第15 层及第22 层上方, 吸收塔底釜液饱和吸收油返回到上游与压缩富气混合。
吸收塔顶采出贫气, 进入再吸收塔(C-304)底部, 与轻柴油吸收剂逆流接触, 吸收贫气中汽油组分。
塔顶压力为1.3~1.4MPa(绝), 塔顶干气为装置副产品。
塔底富吸收油返回分馏塔。
D-301 底凝缩油经泵P1 加压, 与稳定汽油换热(E-304)至70℃进入解吸塔C-302 上部, 塔顶压力1.6MPa(绝)。
解吸塔底重沸器E-301 由分馏塔一中回流供热。
解吸塔顶气返回至E-305 前与压缩富气混合。
C-302 塔底脱乙烷汽油经稳定塔进料泵与稳定汽油换热(E-302)至165℃入稳定塔(C-303)。
C-303 塔顶压力1.17MPa(绝), 塔底重沸器E-303由分馏二中回流供热。
液化气组分由C-303 顶馏出, 经水冷器(E-308)冷却至40℃, 入回流罐(D-302)。
液化气经回流泵加压(P-304)后, 一部分作为顶回流, 另一部分出装置。
稳定塔釜液稳定汽油先与脱乙烷汽油换热(E-302)至161.4℃, 再与凝缩油换热(E-304)至130℃, 再经除盐水冷却器(E-309)冷至40℃, 一部分出装置, 一部分用泵P6 打入塔C-301 顶作补充吸收剂。
延迟焦化装置吸收稳定系统工艺与操作要点ppt
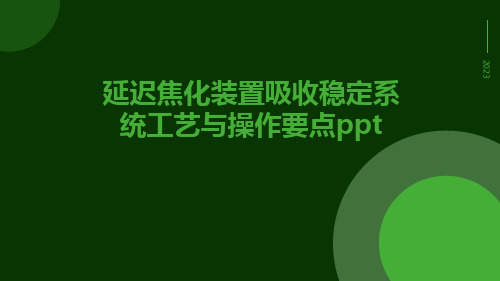
1 2
原料切割
将重油切割成小段,降低加热炉内的结焦倾向 。
加热和脱水
将原料加热到一定温度,并去除其中的水分和 轻质组分。
脱盐和脱硫
3
去除原料中的盐类和硫化物,防止腐蚀设备。
延迟焦化反应过程
加热炉加热
将原料加热到焦化反应所需温度。
焦化反应
原料在加热炉中发生裂解反应,生成气体、汽油 、柴油和重焦炭等产品。
对原料油的API、残碳、硫含量等性质进行严格把控,保 证进料质量。
原料加热
将原料加热到适当的温度,以便在焦化反应中达到最佳 效果。
进料方式选择
可选择连续进料或间歇进料方式,根据实际情况进行选 择。
反应条件优化
反应温度
01
通过控制加热炉出口温度,保证焦化反应在适宜的温度范围内
进行。
反应压力
02
通过控制分馏塔顶部压力,保证焦化反应在适宜的压力范围内
应用案例二:延迟焦化装置优化操作
优化背景
延迟焦化装置操作复杂,影响因素多,需要进行优化以提高装置的经济效益和环保性能。
优化内容
采用先进的在线监测和分析技术,对加热炉出口温度、压力,进料速度等关键参数进行实 时监测和调控。
优化效果
优化后装置运行更加稳定,产品质量和收率得到提高,同时降低了能耗和污染物排放。
2023
延迟焦化装置吸收稳定系 统工艺与操作要点ppt
目录
• 引言 • 延迟焦化装置工艺流程 • 操作要点 • 安全与环保 • 应用案例与效果展示
01
引言
目的和背景
介绍延迟焦化装置 吸收稳定系统的工 艺与操作要点
帮助企业优化生产 过程和提高经济效 益
为相关领域技术人 员提供操作指南
催化吸收稳定工艺流程及原理

催化吸收稳定工艺流程及原理英文回答:Catalytic absorption is a process used in various industries to remove pollutants from gas streams. It involves the use of a catalyst to enhance the absorption of the target pollutant by the solvent. This process is widely used in air pollution control, gas purification, and wastewater treatment.The basic principle behind catalytic absorption is the interaction between the catalyst and the pollutant. The catalyst provides a surface for the pollutant molecules to adsorb onto, which increases the contact area between the pollutant and the solvent. This leads to a higher rate of absorption and a more efficient removal of the pollutant from the gas stream.One example of catalytic absorption is the removal of sulfur dioxide (SO2) from flue gas in coal-fired powerplants. SO2 is a major contributor to acid rain and can have harmful effects on the environment and human health. In this process, a catalyst, such as activated carbon or metal oxides, is used to enhance the absorption of SO2 by the solvent, typically an alkaline solution.The catalyst provides a surface for the SO2 molecules to react with the solvent, forming sulfite or sulfate ions. The reaction is typically exothermic, meaning it releases heat. This heat can be utilized to generate steam or to preheat the gas stream, increasing the overall energy efficiency of the process.Another example of catalytic absorption is the removal of volatile organic compounds (VOCs) from industrial exhaust gases. VOCs are a group of organic chemicals that can have harmful effects on the environment and human health. In this process, a catalyst, such as zeolites or activated carbon, is used to enhance the absorption of VOCs by a solvent, such as water or organic solvents.The catalyst provides a surface for the VOC moleculesto adsorb onto, increasing the contact area with the solvent. This leads to a higher rate of absorption and a more efficient removal of VOCs from the gas stream. The absorbed VOCs can then be recovered or treated further to minimize their environmental impact.Catalytic absorption offers several advantages overother gas cleaning processes. It can achieve high removal efficiencies, even for low concentration pollutants. It can also operate at lower temperatures and pressures, reducing energy consumption and equipment costs. Additionally, the catalyst can be regenerated and reused, further reducing operating costs.中文回答:催化吸收是一种用于各种行业中从气体流中去除污染物的工艺。
吸收稳定系统工艺流程描述
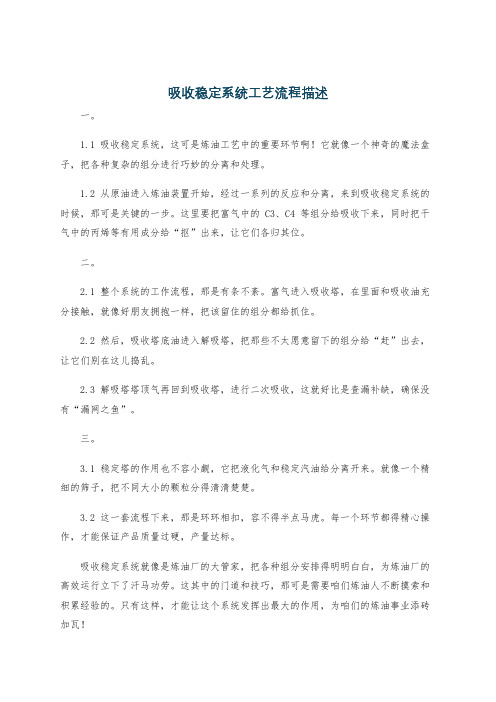
吸收稳定系统工艺流程描述
一。
1.1 吸收稳定系统,这可是炼油工艺中的重要环节啊!它就像一个神奇的魔法盒子,把各种复杂的组分进行巧妙的分离和处理。
1.2 从原油进入炼油装置开始,经过一系列的反应和分离,来到吸收稳定系统的时候,那可是关键的一步。
这里要把富气中的 C3、C4 等组分给吸收下来,同时把干气中的丙烯等有用成分给“抠”出来,让它们各归其位。
二。
2.1 整个系统的工作流程,那是有条不紊。
富气进入吸收塔,在里面和吸收油充分接触,就像好朋友拥抱一样,把该留住的组分都给抓住。
2.2 然后,吸收塔底油进入解吸塔,把那些不太愿意留下的组分给“赶”出去,让它们别在这儿捣乱。
2.3 解吸塔塔顶气再回到吸收塔,进行二次吸收,这就好比是查漏补缺,确保没有“漏网之鱼”。
三。
3.1 稳定塔的作用也不容小觑,它把液化气和稳定汽油给分离开来。
就像一个精细的筛子,把不同大小的颗粒分得清清楚楚。
3.2 这一套流程下来,那是环环相扣,容不得半点马虎。
每一个环节都得精心操作,才能保证产品质量过硬,产量达标。
吸收稳定系统就像是炼油厂的大管家,把各种组分安排得明明白白,为炼油厂的高效运行立下了汗马功劳。
这其中的门道和技巧,那可是需要咱们炼油人不断摸索和积累经验的。
只有这样,才能让这个系统发挥出最大的作用,为咱们的炼油事业添砖加瓦!。
延迟焦化装置吸收稳定系统工艺与操作资料ppt

THANKS
谢谢您的观看
吸收稳定系统的工艺流程
03
脱乙烷塔
主要作用是将吸收剂中的C2组分脱除,避免C2组分进入吸收塔影响吸收效果。
吸收稳定系统的主要设备
01
吸收塔
是吸收稳定系统的核心设备,主要作用是进行吸收操作,使混合碳四烃中的C4、C5轻组分被吸收剂吸收。
02
分馏塔
主要作用是将吸收剂中的C5以上组分分离成液化气和富气。
作用
通过吸收稳定系统,可以降低混合碳四烃中C4、C5轻组分和C6以上的重组分的含量,同时增加液化气中丙烷和丁烷的含量,从而满足液化气产品的质量要求。
吸收稳定系统的定义和作用
原料
进入吸收稳定系统的原料主要是来自延迟焦化装置的混合碳四烃。
工艺流程
混合碳四烃进入吸收塔,与脱乙烷塔来的贫油逆流接触,C4以下组分被吸收到油相中,从塔顶排出;C5以上组分从塔釜排出进入分馏塔,在分馏塔中切割成液化气和富气。
延迟焦化装置的操作
在操作过程中,需要控制加热炉出口温度、焦炭塔压力、分馏塔液面等参数,保证装置的稳定运行。
吸收稳定系统的操作
吸收稳定系统的操作主要包括吸收塔和稳定塔的操作。吸收塔主要通过控制吸收剂的流量和温度来吸收气体中的轻组分,而稳定塔则通过降低吸收塔顶部流出的富吸收油中的轻组分含量来达到操作要求。
xx年xx月xx日
延迟焦化装置吸收稳定系统工艺与操作资料
延迟焦化装置介绍吸收稳定系统介绍延迟焦化装置操作资料吸收稳定系统操作资料延迟焦化装置与吸收稳定系统的关系实际操作中的注意事项
contents
目录
01
延迟焦化装置介绍
延迟焦化是将重质烃类在高温高压下进行裂解和缩合反应,生成气体、汽油、柴油、蜡油等产品的过程。
催化吸收稳定工艺流程及原理

催化吸收稳定工艺流程及原理
催化吸收稳定工艺是一种在石油化工领域广泛采用的气体处理技术,主要用于炼油厂的气体回收和净化。
该工艺流程主要包括以下几个步骤:
1. 吸收过程:首先,从裂解装置或其他来源产生的富含烃类组分的工艺气(如催化裂化装置的干气),通过与富油吸收剂逆流接触,在吸收塔内将C3及以上烃类有效地溶解到吸收剂中。
2. 解吸过程:随后,含有被吸收烃类的富油进入解吸塔,在一定温度条件下,通过降低压力或加热,促使烃类从吸收剂中解析出来,得到富含C3、C4等轻烃的气体产品。
3. 稳定过程:对于含C5及更重组分的汽油组分,送入稳定塔进行进一步分离,通过精馏原理去除其中的C5+组分,以降低汽油蒸汽压,提高其储存和运输安全性。
整体而言,催化吸收稳定工艺通过连续的物理化学过程,实现了对裂解气和其他烃类混合气的有效分离和资源优化利用。
吸收稳定系统流程

吸收稳定系统流程下载温馨提示:该文档是我店铺精心编制而成,希望大家下载以后,能够帮助大家解决实际的问题。
文档下载后可定制随意修改,请根据实际需要进行相应的调整和使用,谢谢!并且,本店铺为大家提供各种各样类型的实用资料,如教育随笔、日记赏析、句子摘抄、古诗大全、经典美文、话题作文、工作总结、词语解析、文案摘录、其他资料等等,如想了解不同资料格式和写法,敬请关注!Download tips: This document is carefully compiled by theeditor. I hope that after you download them,they can help yousolve practical problems. The document can be customized andmodified after downloading,please adjust and use it according toactual needs, thank you!In addition, our shop provides you with various types ofpractical materials,such as educational essays, diaryappreciation,sentence excerpts,ancient poems,classic articles,topic composition,work summary,word parsing,copy excerpts,other materials and so on,want to know different data formats andwriting methods,please pay attention!吸收稳定系统流程一、准备工作阶段。
在进行吸收稳定系统的施工之前,需要进行充分的准备。
吸收稳定系统工艺流程研究

汇报人:
01
02
03
04
05
06
吸收稳定系统是炼油厂中重要的工艺流程之一
吸收稳定系统的主要作用是分离和回收混合气中的轻组分
吸收稳定系统主要包括吸收塔、解吸塔、再吸收塔和稳定塔等设备
吸收稳定系统的操作原理是通过利用混合气中各组分在吸收剂中的溶解度差异来实现分离和回 收
吸收塔:用于吸收混合气 体中的有害成分,提高气 体质量
再生塔:用于将吸收剂再 生,循环使用,提高吸收 效率
冷凝器:用于将吸收剂冷 凝成液体,便于储存和运 输
加热器:用于加热吸收剂, 提高吸收效率
循环泵:用于将吸收剂循 环使用,提高吸收效率
控制系统:用于控制整个 工艺流程的运行,确保稳 定运行
工艺流程概述: 简要介绍吸收稳 定系统的工艺流 程,包括主要设 备和操作步骤。
其他领域:除了以上几个领域,吸收稳定系统工艺流程还可应用于冶金、环保、食 品等行业,实现废气的净化处理和资源的回收利用。
石油化工领域:吸收稳定系统工艺流程在石油化工领域中广泛应用于烃类、烃类和非烃类混合 物等物质的分离和净化。
炼油领域:在炼油领域,吸收稳定系统工艺流程可用于对气体混合物进行分离和净化,提高产 品质量和生产效率。
拓展重点:加强与客户的沟通和合作,了解客户需求和反馈;加强与同行的交流和合作,共 同推动行业发展
拓展保障:建立完善的市场拓展计划和实施方案;加强团队建设和人才培养,提高执行力和 创新能力
行业政策对吸收稳定系统工 艺流程的影响
吸收稳定系统工艺流程的未 来发展趋势
吸收稳定系统工艺流程在环 保领域的应用前景
未来吸收稳定系统工艺流程 的技术创新方向
催化裂化吸收稳定系统优化PPT课件

补充吸收剂 流量20t/h 温度42℃ 压力1100 kPa
粗汽油
流量55t/h 温度40℃ 压力1100 kPa
轻柴油
流量32t/h 温度40℃ 压力1100 kPa
.
7
质量控制指标
液化气中C1+C2物质的量分数<0.3% 液化气中C5物质的量分数<3%
.
8
流程模拟建立
吸收稳定系统流程复杂,共有塔、容器、冷 换设备、混合器和泵等十几个单元模块,各 单元模块的进出物流相互密切联系,因此, 全流程工艺模拟要分多步完成。
.
3
压缩富气
粗汽油
流程简介
解吸气
干气
轻柴油
再
吸
收
塔
富吸油
吸
解
收
c析
塔
塔
液化气 稳 定 塔
补充吸收剂 稳定汽油
工艺流程图
.
4
流程模拟
模拟计算热力学方程
气液平衡计算
修正PR方程
气液焓计算
Lee-Kesler关联式
.
5
基础数据
压缩富气流量12426.3Nm3/h,温度86℃,压力 1100kPa , 其组成见下表。
11
小结
从以上的数据可以看出,模拟计算值与取 样点标定数据基本上吻合,说明模拟系统 的计算和物性数据是可靠的。
.
12
流程模拟的优化
补充吸收剂温度 补充吸收剂流量 稳定塔回流比 解析塔进料温度 塔板数
.
吸收效果 系统能耗
13
系统能耗
总冷负荷:平衡罐前冷却器冷负荷,稳定塔塔 顶冷凝器冷负荷,稳定汽油冷却器负荷
C3H6
46.13
0.00
延迟焦化装置吸收稳定系统工艺与操作 ppt课件

正常调整:
影响因素 PC6605
调整方法 关小PC6605,稳定塔顶压力降低,反之上升
稳定塔顶回流 量
稳定塔底温度
提高稳定塔顶回流量,稳定塔顶压力升高,反之上 升
降低稳定塔底温度,稳定塔顶压力降低,反之上升
稳定塔进料量 降低稳定塔进料量,稳定塔顶压力降低,反之上升
延迟焦化装置吸收稳定系统工 艺与操作
稳定塔顶压力突然降低
A塔顶回流流量小 B稳定塔进料温度TI-6608低 C 稳定塔塔底温度TI-6613低 D塔顶水冷器E-204冷却过度
a增大塔顶回流 b提高塔低进料温度 c提高塔低重沸器温度 d关小开打E204冷却水
延迟焦化装置吸收稳定系统工 艺与操作
4.2再吸收塔压力控制 再吸收塔顶压力是再吸收塔操作的关键指标,压力控
油和液态烃质量的控制影响很大。
控制目标:稳定塔顶压力1.05MPa 控制范围:≯1.3 MPa 相关参数:稳定塔底温度、稳定塔进料量、稳定塔顶
回流量
控制方式:稳定塔顶压力由PC6605控制,当稳定 塔顶压力偏高时,关小PC6605,来实现稳定塔顶 压力的控制
延迟焦化装置吸收稳定系统工 艺与操作
延迟焦化装置吸收稳定系统工艺 与操作
2.5 将液化气(C3、C4组分)从脱乙烷汽油中
分离出来的操作过程是在稳定塔中进行的。 稳定操作是在一定压力下进行的精馏过程, 脱乙烷汽油由塔中部进入,塔底由重沸器提 供热量。塔顶由液化气作回流并控制塔顶温 度,进行精馏操作,最终在塔顶得到液化气 组分,塔底得到稳定汽油组分,达到液化气 与稳定汽油分离的目的。
a关小PC6604阀位开度 b联系仪表处理故障
延迟焦化装置吸收稳定系统工 艺与操作
4.3解吸塔底温度 解吸塔底温度是解吸塔操作的主要指标,温度控制偏
催化裂化吸收稳定岗讲解课件

设备维护与保养
定期检查
定期对设备进行检查,包 括阀门、管道、外表等, 确保其正常工作。
保养计划
制定保养计划,对设备进 行定期保养,如清洗、润 滑、更换磨损件等。
维修与更换
对破坏的设备进行维修或 更换,确保设备的正常运 行。
04
安全与环保
安全操作规程
操作人员资质要求
确保操作人员经过专业培训,熟悉操 作规程,具备必要的操作技能和安全 意识。
岗位培训计划
培训目标
确保催化裂化吸取稳定岗员工具备岗位 所需的专业知识和技能,提高工作效率
和安全意识。
培训方式
采用理论授课、实践操作、案例分析 等多种情势,重视员工实际操作能力
的培养。
培训内容
涵盖催化裂化原理、吸取稳定工艺流 程、设备操作与维护、应急处理等方 面的知识。
培训周期
根据员工岗位需求和技能水平,制定 个性化的培训计划,周期为3个月至1 年不等。
产。
03
催化裂化吸取稳定设备与 操作
主要设备介绍
01
02
03
04
吸取塔
用于吸取和稳定反应产物中的 气体,是催化裂化吸取稳定系
统的核心设备。
再沸器
用于加热吸取剂,使其到达所 需的温度,以便进行有效的吸
取操作。
再生塔
用于再生吸取剂,使其能够循 环使用。
紧缩机
用于提供吸取剂循环所需的压 力。
设备操作规程
启动前检查
确保所有设备处于良好的工作 状态,检查阀门、管道和外表
是否正常。
启动操作
按照规定的顺序启动设备,并 监控设备的运行状态,确保其 正常运行。
正常操作
根据生产需求调整设备的运行 参数,如温度、压力、流量等 ,以获得最佳的吸取效果。
刘为民分馏于与吸收稳定ppt

3、催化分馏塔特点视为三塔:重油塔(3#板—塔底)柴油塔(3#板—17#板)汽油塔(17#—塔顶)高温过热油气(含催化剂颗粒)进料设脱过热段(洗涤段)全抽出塔盘4、控制指标:粗汽油干点轻柴油凝点、闪点5、塔底液面控制塔底抽出流量控制露点温度控制: 塔底液相温度(FCC)一层板下温度(RFCC) 6、防止油浆系统结焦:塔底温度≯350 ℃塔底油浆停留时间≯5 min油浆管线速度≮1.2 m/s使用阻垢剂7,分馏系统原则流程图两流程比较常规流程:塔顶出汽油与气体;重循环油(回炼油)与轻循环油(轻柴油)抽出均设全抽出塔板,用回流返塔控制板下气相温度控制产品质量;原料油进料温度用油浆换热最终控制;循环油浆与原料油换热后去发生蒸汽新流程:塔顶出汽油与气体,塔上部(一线)抽出重石石脑油;设双塔汽提,轻循环油与轻柴油;重循环油与回炼油均在同一抽出口(半抽出塔板)抽出,用产品抽出量控制产品质量,回流返塔温度不做严格控制;原料油尽可能与产品及回流换热,原料油进料温度用重循环油换热最终控制;循环油浆全去去发生蒸汽二、吸收稳定1、任务控制汽油蒸汽压、回收LPG和干气2、名词●富气—未经吸收的油气,C3+ >150g/m3组成:干气3~4%m/feedLPG14~18%m/feed汽油10~15%m/feed烟气1.0~1.2Nm3/t循环cat气压机工艺参数的确定?●贫气—经过一次吸收的油气,C3+ 100-150g/m3●干气—经过两次吸收的油气,<C3+100g/m3吸收C3 C4解吸C1C2使汽油蒸汽压合格LCO 含有汽油组分回收汽油组分吸收剂补充吸收剂4、控制指标:汽油蒸汽压:冬季≯88kpa夏季≯74 kpa LPG 中:C5+ ≯3%v (C1+C2≯1%v )+ ≯3%v干气中:C3高压瓦斯压力:0.5~0.6MPa(表)欢迎指正谢谢大家。
延迟焦化装置吸收稳定系统工艺与操作课件
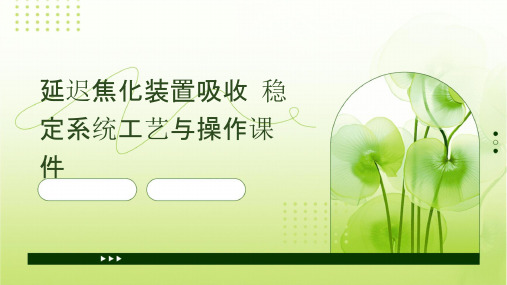
按照停工计划逐步停止吸收稳定系统的运行,关闭相关 阀门和仪表。
对停工过程中出现的问题和情况进行记录和分析,及时 处理并采取预防措施。
PART 04
吸收稳定系统常见问题及 解决方案
吸收效果差
总结词
吸收效果差可能是由于吸收剂选择不当、吸收塔结构不合理、操作条件不合适等原因引起的。
详细描述
吸收剂应具备高溶解度、高选择性、低挥发性等特性,否则可能造成吸收效果不理想。吸收塔应具备适宜的填料 和喷淋系统,以保证良好的气液接触和均匀的温度分布。操作条件如温度、压力、流量等也需要根据工艺要求进 行合理设置。
塔盘改造
针对现有塔盘存在的问题 进行改造,以提高吸收效果。
增加再沸器
在吸收塔底部增加再沸器, 提高塔内温度,增强吸收 效果。
优化操作条件
操作压力
通过调整系统压力,改善吸收效果。
操作温度
合理设置操作温度,以提高吸收剂 的活性。
液气比
优化液气比,使吸收剂与气体充分 接触,提高吸收效率。
PART 06
气体泄漏可能是由于设备密封不良、管 道破裂、阀门故障等原因引起的。
VS
详细描述
应定期检查设备的密封性能,及时更换损 坏的密封件。同时,对管道和阀门进行定 期检修和维护,以确保其正常运转。在生 产过程中,应密切关注工艺参数的变化, 发现异常及时处理。
PART 05
吸收稳定系统优化与改进 建议
提高吸收剂性能
01
02
03
吸收剂的选择
针对延迟焦化装置的特定 工况,选择适合的吸收剂, 以提高吸收效果。
吸收剂的纯化
确保吸收剂的纯度,以降 低杂质对吸收系统的影响。
吸收剂的再生
采用有效的再生方法,使 吸收剂在循环使用过程中 保持较高的性能。
(完整word版)催化吸收稳定系统工艺流程
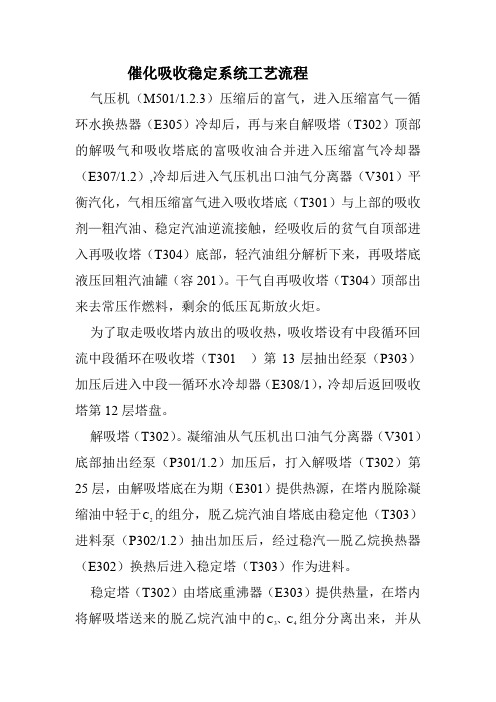
催化吸收稳定系统工艺流程气压机(M501/1.2.3)压缩后的富气,进入压缩富气—循环水换热器(E305)冷却后,再与来自解吸塔(T302)顶部的解吸气和吸收塔底的富吸收油合并进入压缩富气冷却器(E307/1.2),冷却后进入气压机出口油气分离器(V301)平衡汽化,气相压缩富气进入吸收塔底(T301)与上部的吸收剂—粗汽油、稳定汽油逆流接触,经吸收后的贫气自顶部进入再吸收塔(T304)底部,轻汽油组分解析下来,再吸塔底液压回粗汽油罐(容201)。
干气自再吸收塔(T304)顶部出来去常压作燃料,剩余的低压瓦斯放火炬。
为了取走吸收塔内放出的吸收热,吸收塔设有中段循环回流中段循环在吸收塔(T301 )第13层抽出经泵(P303)加压后进入中段—循环水冷却器(E308/1),冷却后返回吸收塔第12层塔盘。
解吸塔(T302)。
凝缩油从气压机出口油气分离器(V301)底部抽出经泵(P301/1.2)加压后,打入解吸塔(T302)第25层,由解吸塔底在为期(E301)提供热源,在塔内脱除凝缩油中轻于2C 的组分,脱乙烷汽油自塔底由稳定他(T303)进料泵(P302/1.2)抽出加压后,经过稳汽—脱乙烷换热器(E302)换热后进入稳定塔(T303)作为进料。
稳定塔(T302)由塔底重沸器(E303)提供热量,在塔内将解吸塔送来的脱乙烷汽油中的43C C 、组分分离出来,并从塔顶蒸出,经稳定塔(T303)顶空冷器(E309/1.2)和塔顶冷却器(E310)后,进入稳定塔顶回流罐(V302)平衡汽化,液相—液化石油气自底部经泵(P304/1.2)加压后一部分作为塔顶回流返回稳定塔顶,另一部分作为产品出装置,气相—不凝气经压控送至装置瓦斯管网。
稳定汽油由稳定塔(T303)底重沸器(E303)自流出,经稳汽—脱乙烷汽油换热器(E302)进入稳汽—凝缩油换热器(E304),再进入稳汽与采暖水换热,空冷器(E311/1.2)后,经循环水冷却后,一路经泵(P305/1.2)加压冷却后到吸收塔(T301)顶作吸收剂,另一路去碱洗出装置。
吸收稳定部分

吸收稳定部分从两个分馏塔顶油气分离器(V1203、V1204)来的混合富气进入气压机(C-1301)压缩,压缩富气与解吸塔顶气及来自酸性水罐的富气洗涤水混合,经气压机出口干式空冷器(E1301A-D)冷却,然后与吸收塔底油混合后经压缩富气冷凝冷却器(E1302A-D)冷却至40℃,进入气压机出口油气分离器(V1302)进行气、液、水三相分离,分离后的气体进入吸收塔(T1301)进行吸收,吸收过程放出的热量由吸收塔一、二中段冷却器(E1303AB、E1304AB)取走。
吸收塔顶(T1301)贫气至再吸收塔(T1303),经贫吸收油进一步吸收后,干气经干气分液罐(V1304)送出装置,贫吸收油经轻柴油-富吸收油换热器加热后返回主分馏塔。
V1302分离的酸性水返回酸性水罐。
凝缩油从气压机出口油气分离器(V1302)经解吸塔进料泵(P1303AB)抽出后进入解吸塔(T1302)。
解吸塔设中间重沸器(E1306)和两台塔底重沸器(E1305AB),其中解吸塔中间重沸器(E1306)用稳定汽油加热,一台塔底重沸器(E1305A)以副分馏塔中段循环回流油做主热源,另一台解吸塔底重沸器(E1305B)用低压蒸汽做补充热源。
脱乙烷汽油由解吸塔(T1302)底经稳定塔进料泵(P1307AB)加压后经稳定塔进料换热器(E1307),与稳定汽油换热后进入稳定塔(T1304)中部。
稳定塔底重沸器(E1313)由主分馏塔一中循环回流油提供热量。
稳定塔顶馏出物经干式空冷器(E1311A-F)和冷凝冷却器(E1312A-F)冷却至40℃后进入稳定塔顶回流油罐(V1303),液化气经稳定塔顶回流泵(P1308AB)抽出后一部分作稳定塔顶回流,其余作为液化石油气产品送出装置。
稳定汽油从稳定塔(T1304)底流出,先后经稳定塔进料换热器(E1307)、解吸塔中间重沸器(E1306)、稳定汽油-除盐水换热器(E1308AB)及稳定汽油冷却器(E1309AB)冷却至40℃,一部分经稳定汽油泵(P1309AB)升压送至吸收塔(T1301)作补充吸收剂,其余部分送出装置。
吸收稳定系统工艺流程讲义

两种流程能耗费和经济效益表
销售收入 水 电 蒸汽 总能耗费 总经济效益
新流程 149983 202 80 1187 1469
148514
双塔流程 149277 272 102 1686 2060
147217
相对值
706
-70 -22 -499 -591
1297
单位:万元/年
新工艺流程的主要特点
取消了双塔流程中的两股返回物料 采用复杂蒸馏塔代替原有的吸收塔和脱 吸塔 换热网络的合理匹配(稳定塔取消进料预 热器) 分离汽油馏分的能力提高 新流程设备费用较双塔流程节省
0 10.213
0 69.2% 40.3%
(MKcal/hr) 双塔流程 17.485 17.212 17.485 5.375 12.110 7.417 19.527 -1.489 21.016 7.417 0 13.735 0.136 69.2% 35.1%
结论
新的省能的吸收稳定系统工艺流程,在比较基 准相同、进出口条件一致的情况下,对于120万 吨的年生产能力的催化裂化装置,比典型的双 塔流程年总经济效益高出1297万元。 新流程采用复杂蒸馏塔—油吸收脱乙烷塔来取 代原有的吸收塔和脱吸塔,不仅具有较高的塔 板效率,而且提高了分离汽油馏分的能力。
万元年销售收入蒸汽总能耗费总经济效益新流程1499832028011871469148514双塔流程14927727210216862060147217相对值70670224995911297新流程双塔流程12328174851211217212021617485直接损失能38015375有效供能852712110回收循环能69047417工艺总用能1543119527热力学能耗16861489待回收能1711721016回收循环能69047417回收输出能回收排弃能1021313735不平衡项0136转换效率692692回收效率403351新的省能的吸收稳定系统工艺流程在比较基准相同进出口条件一致的情况下对于120万吨的年生产能力的催化裂化装置比典型的双塔流程年总经济效益高出1297万元
- 1、下载文档前请自行甄别文档内容的完整性,平台不提供额外的编辑、内容补充、找答案等附加服务。
- 2、"仅部分预览"的文档,不可在线预览部分如存在完整性等问题,可反馈申请退款(可完整预览的文档不适用该条件!)。
- 3、如文档侵犯您的权益,请联系客服反馈,我们会尽快为您处理(人工客服工作时间:9:00-18:30)。
产品规格表
干气中C3 浓度
3%
液化气中C2 含量
1%
液化气中 C5 以上组分含量
2%
稳定汽油中C4 含量
1%
产品产量一览表
产品产量 ( t/h ) 干气 液化气 稳定汽油
新工艺流程 13.752 23.535 70.781
双塔流程 14.099 23.511 70.266
过程系统的经济活动[16,39]可以描述如下: B+T = S-M-(Oe+Od+Oc)
新工艺流程流程图(PFD)
12.8Kg/cm2 的压缩富气进入汽液平衡罐进行汽液分离。气相直接进入油吸收 脱乙烷塔的第 20 块理论板,液相用泵打入第 25 块理论板。
粗汽油作为吸收剂直接进入油吸收脱乙烷塔塔顶,稳定汽油作为补充吸收剂 用泵打入油吸收脱乙烷塔塔顶。塔顶气体经塔顶冷凝器冷凝后,进入一平衡罐。 贫气直接进入再吸收塔底部,液相用泵打回油吸收脱乙烷塔顶。为取走吸收过 程中放出的热量,在油吸收脱乙烷塔第 15 块板采用一个中段回流来冷却。为有 效地利用能量,在塔的底部设一中间再沸器。
来自分馏塔系统的轻柴油作为再吸收剂,由再吸收塔顶部打入,以回收贫气 带出的汽油组分。再吸收塔底部富吸收柴油返回分馏塔系统。塔顶干气至气体 脱硫系统或排入燃料气管网。
脱乙烷汽油由油吸收脱乙烷塔底部用泵抽出,直接进入稳定塔,以分离液化 气馏分和汽油馏分。 液化气自稳定塔塔顶分出,一部分作为塔顶回流,其余部分送去脱硫或直接作 为产品出装置。稳定汽油从重沸器底部出来先做油吸收脱乙烷塔塔底再沸器热 源,然后加热油吸收脱乙烷塔中间再沸器,再经冷却水冷却后,分为两路:一 路用泵送至吸收塔塔顶作为补充吸收剂,另一路作为产品出装置。
– 采用华贲教授创立的三环节分解协调优化 方法,综合集成,整体优化,设计新流程。
– 在相同的进出口条件下,对新流程和双塔 流程进行分析比较。
化工流程模拟技术
化工流程模拟技术的发展 化工流程模拟技术的特点 – 在炼油和石化领域,取代了实验室实验.。 –不受压力、温度、物料、设备和仪表等等
条件的限制,节省了费用和时间。 –较高的准确性和可靠性 –国外很多炼油、石化企业已将国际著名的
图1 吸收脱吸单塔流程简图 图2 吸收脱吸双塔流程简图
双塔流程的严重缺陷
脱吸塔顶气相、吸收塔釜液返回系统的 最开始处,相当于进料量的大量返回物 料在系统中循环,必然造成能量的浪费。 单独的吸收塔、脱吸塔效率都比较低下, 这又造成了能量的损失。
单塔流程的控制问题
吸收和脱吸属于多级多组分分离的范畴, 必须遵循蒸馏分离过程的基本原理。 在石化领域,同一塔内,塔顶、塔釜对 分离要求均有严格规定的蒸馏塔比比皆 是,而且长期以来操作良好。 过程控制的进步和发展,特别是先进控 制技术的蓬勃发展,使得控制更不成为 问题。
化工模拟软件,如ASPEN PLUS和ቤተ መጻሕፍቲ ባይዱRO/II等 作为企业标准。
热力学方法
热力学方法研究的进展已经可以准确的应用状态方程计算石油 馏份和烃类的热力学性质。如广泛采用的 PR 状态方程,是 PengRobinson 于 1976 年提出的半经验半理论方程,通过数万点的实 验数据回归了方程中的各项系数,其准确性已获普遍承认。大多 数情况下混合物相平衡常数的计算,平均误差小于 5%,这已是十 分高的准确度。该方法的准确性不仅为实验数据所证实,也为如 乙烯、常减压、气分和吸收稳定等装置的生产数据所肯定。如乙 烯装置中的乙烯塔塔顶基本为纯乙烯(浓度为 99.96%),丙烯塔 塔顶为纯丙烯(99.6%);由 PR 方程所算的温度和实验值(纯组 分实验值比较容易获得)相差小于 1C,和生产装置的实测值也 十分吻合。准确的热力学性质计算为流程模拟计算的准确性提供 了保证。
富气
压力 Kg/cm2
12.5 9.5
12.8
温度 流量
恩氏曲线或组成
C t/h HK 5% 10% 30% 50% 70% 90% 95% KK
40 39.9 40 54 68 99 124 150 186
212
40 30.0 193.5 220 229.5 248 269. 295 324 340 347
新流程的开发思路
取消双塔流程中的两股返回物料 采用复杂蒸馏塔取代原有的吸收塔 和脱吸塔 换热网络的合理匹配
双塔流程的选定
取自某大型炼油厂的催化裂化装置 进料数据、产品规格等参数来自现场的 实测标定数据和有关规定 模拟结果与生产数据符合较好 与新流程有相同的比较基准
进料条件和原料组成
物料 粗汽油 贫吸收油
贫气由吸收塔顶部排出,进入再吸收塔底部。来自分馏塔系统的轻 柴油作为再吸收剂,由再吸收塔顶部打入,以回收贫气带出的汽油组 分。再吸收塔底部富吸收柴油返回主分馏塔。塔顶干气至气体脱硫系 统或排入燃料气管网。
进入脱吸塔塔顶的凝缩油,脱去 C2 以下的轻组分,脱乙烷汽油由 脱吸塔底部用泵抽出,与稳定汽油换热后,进入稳定塔,以分离液化 气馏分和汽油馏分。 液化气自稳定塔塔顶分出,一部分作为塔顶回流,其余部分送去脱硫 或直接作为产品出装置。稳定汽油从重沸器底部出来先后加热脱乙烷 汽油与凝缩油,再经冷却水冷却后,分为两路:一路用泵送至吸收塔 塔顶作为补充吸收剂,另一路作为产品出装置。
催化裂化装置简介
催化裂化装置是我国主要的原油加工装置之一。 它是将重质油轻质化,生产液化气、汽油和柴油的 重要装置。根据1998年的统计,全国催化裂化装置 的生产能力已达7200万吨/年。而吸收稳定系统是催 化裂化装置中的后处理系统,它将催化裂化反应产 物分离成干气、液化气和稳定汽油产品。本催化裂 化装置与一般的催化装置工艺流程基本相同,即由 三个部分组成:反应-再生系统、分馏系统和吸收稳 定系统。因而吸收稳定系统的产品收率和能耗对整 个装置的经济效益有着十分重要的作用。因此,即 使我国催化裂化生产能力的一半改造为新流程,每 年的总计经济效益也有上亿元。
式中:B—纯利润;T—税收;S—销售收入;M—物耗 Oe—能耗;Od—设备费;Oc—其它费用
研究目的主要在于比较两种流程经济效益的优劣。因而 经济效益比较的函数简化为:
总经济效益 P = 销售收入 S - 能耗费 Oe 有关价格分别如下:冷却水—0.25 元/吨,中压蒸汽— 80 元/吨,电—0.4 元/度,干气—600 元/吨,液化气—1450 元/吨,稳定汽油——2050 元/吨。
新流程取消了双塔流程中的两股返回物料,较 大程度地降低了能耗。
新流程的换热网络经优化匹配,其用能更为合 理,进一步减小了能耗。
谢谢光临指导!
系统能量平衡汇总表
项目
总供入能 蒸汽 电 直接损失能 有效供能 回收循环能 工艺总用能 热力学能耗 待回收能 回收循环能 回收输出能 回收排弃能 不平衡项 转换效率 回收效率
能量 新流程 12.328 12.112 0.216 3.801 8.527 6.904 15.431 -1.686 17.117 6.904
两种流程能耗费和经济效益表
销售收入 水 电 蒸汽 总能耗费 总经济效益
新流程 149983 202 80 1187 1469
148514
双塔流程 149277 272 102 1686 2060
147217
相对值
706
-70 -22 -499 -591
1297
单位:万元/年
新工艺流程的主要特点
取消了双塔流程中的两股返回物料 采用复杂蒸馏塔代替原有的吸收塔和脱 吸塔 换热网络的合理匹配(稳定塔取消进料预 热器) 分离汽油馏分的能力提高 新流程设备费用较双塔流程节省
0 10.213
0 69.2% 40.3%
(MKcal/hr) 双塔流程 17.485 17.212 17.485 5.375 12.110 7.417 19.527 -1.489 21.016 7.417 0 13.735 0.136 69.2% 35.1%
结论
新的省能的吸收稳定系统工艺流程,在比较基 准相同、进出口条件一致的情况下,对于120万 吨的年生产能力的催化裂化装置,比典型的双 塔流程年总经济效益高出1297万元。 新流程采用复杂蒸馏塔—油吸收脱乙烷塔来取 代原有的吸收塔和脱吸塔,不仅具有较高的塔 板效率,而且提高了分离汽油馏分的能力。
吸收稳定系统工艺流程研究
制作人: 贾小平 曾敏刚 指导老师:钱 宇 陆恩锡
目录
绪论 吸收稳定系统工艺流程的沿革 新工艺流程开发研究 两种流程能耗与经济效益的比较 新工艺流程的主要特点 结论
项目来源和主要研究内容
项目来源 项目来源于石化企业吸收稳定装置的优化改造。 主要研究内容
– 以系统分析和过程模拟技术为基础,对吸 收稳定系统进行新的省能的工艺流程研究。
5
N2 5.2 CO2 1.23 CO 0.54 O2 1.3 H2 12.0 40 27.0 C1 15.34 C2 7.4 C2= 8.92 C30 4.12 C3= 15.82
IC40 5.14 NC40 1.20 BUT1 4.85 IBTE 2.2 BTT2 3.97 BTC2 1.53 NC5 10.98
双塔流程图(PFD)
12.8Kg/cm2 的压缩富气与吸收塔塔底的富吸收油及脱吸塔顶部的脱 吸气混合后,冷凝冷却,然后进平衡罐进行气液分离。液相称作凝缩 油,被稳定汽油加热至 70C 后用泵打入脱吸塔塔顶,气相直接进入吸 收塔底部。
粗汽油作为吸收剂直接进入吸收塔顶部,稳定汽油作为补充吸收剂 用泵打入吸收塔顶。为取走吸收过程中放出的热量,吸收塔采用两个 中段回流来冷却。