航空整体结构件高效高精度加工关键技术研究(上)
大型航空关键构件整体精密模锻成形技术研究进展

大型航空关键构件整体精密模锻成形技术研究进展
周杰;刘左发;屈志远;王航;张鹏;王周田
【期刊名称】《航空制造技术》
【年(卷),期】2023(66)5
【摘要】随着航空产业的快速发展,大型、整体、精密和高性能的模锻件在航空关键构件中的占比不断提高。
航空关键构件尺寸的增大、复杂程度的增加以及材料强度的提高,给大型航空关键构件的整体模锻成形带来了巨大挑战。
首先介绍了实现大型航空关键构件整体模锻成形面临的关键挑战以及解决途径,然后综述了整体精密模锻成形技术在典型大型航空关键构件如飞机承力框、起落架和发动机涡轮盘中的研究进展,最后对大型航空关键构件整体模锻成形技术的未来发展前景进行了展望。
【总页数】12页(P14-25)
【作者】周杰;刘左发;屈志远;王航;张鹏;王周田
【作者单位】重庆大学先进模具智能制造重庆市重点实验室;重庆大学材料科学与工程学院;中国第二重型机械集团德阳万航模锻有限责任公司
【正文语种】中文
【中图分类】TG3
【相关文献】
1.航空整体结构件加工变形控制与校正关键技术
2.航空整体结构件高效高精度加工关键技术研究(上)
3.航空整体结构件高效高精度加工关键技术研究(下)
4.航空航天复
杂曲面构件精密成形技术的研究进展5.应用于装备轻量化铝合金构件液态模锻成形技术的研究进展
因版权原因,仅展示原文概要,查看原文内容请购买。
基于MBD的飞机结构件数控加工方法

基于MBD的飞机结构件数控加工方法吕斌;王细洋;孙心宇【摘要】In order to improve the efficiency of the NC machining process decision of Aircraft structural parts, a process design is proposed based on MBD in this paper. The aircraft structural parts are marked with the CATIA by MBD. Geometry information and non-geometry information of the concerned machining features employing feature recognition are extracted before design the tool path. Finally, NC program are exported by post-processing and complete machining.%为解决飞机结构件数控加工工艺决策效率低下的问题,提出基于MBD的飞机结构件工艺设计方法。
该方法采用MBD技术,在CATIA环境下对飞机结构件进行标注,通过特征识别技术提取相关加工特征的几何信息和非几何信息并进行刀轨规划,经后置处理导出NC程序并完成加工。
【期刊名称】《机械工程师》【年(卷),期】2015(000)002【总页数】4页(P22-24,25)【关键词】飞机结构件;MBD;特征识别【作者】吕斌;王细洋;孙心宇【作者单位】南昌航空大学航空制造工程学院,南昌330063;南昌航空大学航空制造工程学院,南昌330063;南昌航空大学航空制造工程学院,南昌330063【正文语种】中文【中图分类】TP3910 引言飞机产品作为一种复杂的航空工业产品,逐渐趋向于数字化制造[1],数控技术集微电子、计算机、信息处理、自动检测及自动控制于一体。
航空零部件的金属增材制造光整加工技术研究进展
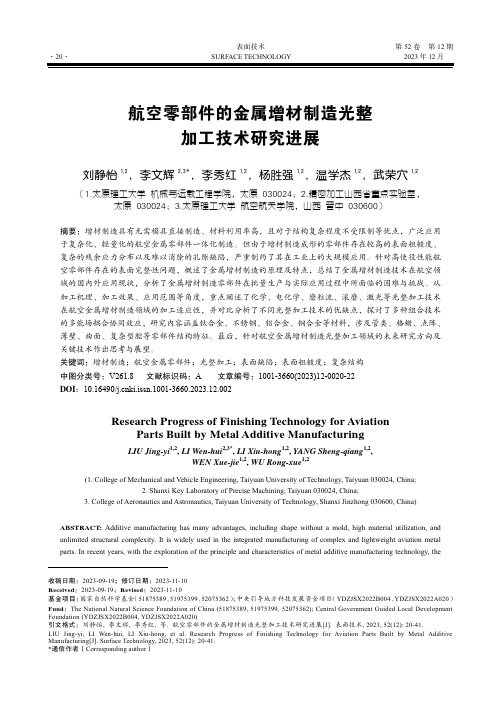
表面技术第52卷第12期航空零部件的金属增材制造光整加工技术研究进展刘静怡1,2,李文辉2,3*,李秀红1,2,杨胜强1,2,温学杰1,2,武荣穴1,2(1.太原理工大学 机械与运载工程学院,太原 030024;2.精密加工山西省重点实验室, 太原 030024;3.太原理工大学 航空航天学院,山西 晋中 030600)摘要:增材制造具有无需模具直接制造、材料利用率高,且对于结构复杂程度不受限制等优点,广泛应用于复杂化、轻量化的航空金属零部件一体化制造。
但由于增材制造成形的零部件存在较高的表面粗糙度、复杂的残余应力分布以及难以消除的孔隙缺陷,严重制约了其在工业上的大规模应用。
针对高使役性能航空零部件存在的表面完整性问题,概述了金属增材制造的原理及特点,总结了金属增材制造技术在航空领域的国内外应用现状,分析了金属增材制造零部件在批量生产与实际应用过程中所面临的困难与挑战。
从加工机理、加工效果、应用范围等角度,重点阐述了化学、电化学、磨粒流、滚磨、激光等光整加工技术在航空金属增材制造领域的加工适应性,并对比分析了不同光整加工技术的优缺点,探讨了多种组合技术的多能场耦合协同效应,研究内容涵盖钛合金、不锈钢、铝合金、铜合金等材料,涉及管类、格栅、点阵、薄壁、曲面、复杂型腔等零部件结构特征。
最后,针对航空金属增材制造光整加工领域的未来研究方向及关键技术作出思考与展望。
关键词:增材制造;航空金属零部件;光整加工;表面缺陷;表面粗糙度;复杂结构中图分类号:V261.8 文献标识码:A 文章编号:1001-3660(2023)12-0020-22DOI:10.16490/ki.issn.1001-3660.2023.12.002Research Progress of Finishing Technology for AviationParts Built by Metal Additive ManufacturingLIU Jing-yi1,2, LI Wen-hui2,3*, LI Xiu-hong1,2, YANG Sheng-qiang1,2,WEN Xue-jie1,2, WU Rong-xue1,2(1. College of Mechanical and Vehicle Engineering, Taiyuan University of Technology, Taiyuan 030024, China;2. Shanxi Key Laboratory of Precise Machining, Taiyuan 030024, China;3. College of Aeronautics and Astronautics, Taiyuan University of Technology, Shanxi Jinzhong 030600, China)ABSTRACT: Additive manufacturing has many advantages, including shape without a mold, high material utilization, and unlimited structural complexity. It is widely used in the integrated manufacturing of complex and lightweight aviation metal parts. In recent years, with the exploration of the principle and characteristics of metal additive manufacturing technology, the收稿日期:2023-09-19;修订日期:2023-11-10Received:2023-09-19;Revised:2023-11-10基金项目:国家自然科学基金(51875389、51975399、52075362);中央引导地方科技发展资金项目(YDZJSX2022B004、YDZJSX2022A020)Fund:The National Natural Science Foundation of China (51875389, 51975399, 52075362); Central Government Guided Local Development Foundation (YDZJSX2022B004, YDZJSX2022A020)引文格式:刘静怡, 李文辉, 李秀红, 等. 航空零部件的金属增材制造光整加工技术研究进展[J]. 表面技术, 2023, 52(12): 20-41.LIU Jing-yi, LI Wen-hui, LI Xiu-hong, et al. Research Progress of Finishing Technology for Aviation Parts Built by Metal Additive Manufacturing[J]. Surface Technology, 2023, 52(12): 20-41.*通信作者(Corresponding author)第52卷第12期刘静怡,等:航空零部件的金属增材制造光整加工技术研究进展·21·variety and quality of additive manufacturing parts have been fully developed. The application status of metal additive manufacturing technology in the aviation field at home and abroad is summarized, and the difficulties and challenges faced by metal additive manufacturing parts in mass production and practical application are analyzed. At present, the application of additive manufacturing technology in the aviation field is mature abroad. Compared with foreign countries, China has also made some progress in the surface quality and mechanical properties of additive manufacturing parts. However, there are still some gaps in post-processing.The defects of additive manufacturing parts include powder adhesion, step effect, balling effect, cracks, pores, and complex residual stress distribution. Poor surface integrity affects fatigue performance and seriously restricts the large-scale application of additive manufacturing in industry. To improve the surface integrity of aviation additive manufacturing parts, this article focuses on the processing adaptability of various finishing technologies such as chemistry, electrochemistry, abrasive flow, barrel, and laser in the aviation metal additive manufacturing field. The research involves surfaces created through additive manufacturing using different materials, including titanium alloy, stainless steel, aluminum alloy, copper alloy, etc., and the influence of structural features such as tubes, grids, lattices, thin walls, curved surfaces, complex cavities, and other parts on finishing behavior. Each finishing technology’s processing mechanism and appropriate processing parameters are reviewed to determine the optimal processing strategy. The processing effects of each technology on the surface of additive manufacturing are summarized from the perspectives of surface roughness, surface hardness, micromorphology, and so on. The advantages and disadvantages of different finishing technologies are compared and analyzed.Chemical finishing and electrochemical finishing have good accessibility and usually produce no residual stress during the process, which can be applied to complex structures such as grids and arrays. However, the processing of these two finishing technologies is not very environmentally friendly, and it is difficult to accurately control the accuracy of the parts. In contrast, barrel finishing and abrasive flow machining can control the machining process very well. They usually have a high material removal rate, which can respond quickly to rough surfaces. These two finishing technologies have a long processing time and are prone to edge effects. It is necessary to control the complex flow field. Laser finishing has a high degree of automation and can be integrated with additive manufacturing systems. However, its accessibility is limited, and the processing process may increase the generation of thermal residual stress. After that, combined with the advantages and disadvantages of each finishing technology, the multi-energy field coupling synergistic effect of different combination finishing processes such as chemical-electrochemistry, mechanical-chemistry, and mechanical-electrochemistry is introduced.In the future, research on the finishing technology of aviation metal additive manufacturing parts will focus on complex features, establish a more complete theoretical framework, and lead to more innovative finishing processes.KEY WORDS: additive manufacturing; aviation metal parts; finishing processing; surface defects; surface roughness; complex construction增材制造(Additive Manufacturing,AM),俗称3D打印,是一种自下而上的新型加工技术,主要基于离散-堆积原理,应用激光束[1-2]、电子束[3]、电弧[4]等能量源,以金属、陶瓷、高分子、新型材料等作为原材料,通过高温使材料熔融后逐层累积、快速成形。
智能制造和高速高精加工技术——访中航工业北京航空制造工程研究所王焱研究员

王老师 说在整个 工艺流程 中切 削刀具 是支撑和促 进切 削加工技术进 步 的关 键 因素之 一 。近年来 ,高速 高精 数控机床 的广泛应用 促使现代 切削加 工技术发展 到 了一个新 的阶段 ,先进 高效刀具 的应用 是使 昂贵 的 数控机床 充分 发挥 其高速 高效加工 能力 的基本 前提之 一 , 也是先进工艺技术发挥效用 的重要保障 。
工艺装 备是实现 工艺方法 的基础 ,是工艺技术 实 施 的载 体 。由于航空产 品零部件越 来越 多地采用整 体 结 构 和 新 型 材 料 ,常 常 具 有 复 杂 曲面 外 形 、 复 杂 的 结 构形 式和装配 协调关 系等特殊要 求 ,高速 高精技术 成 为支撑航 空产 品制造的关键,航空制造业对高速 高精设 备 有 着 迫 切 的需 求 。工 艺技 术 研 究 除探 索 工 艺 方法 、确 定 工 艺 流程 外 ,经 常 要解 决 的就 是 新型 工 艺 设 备工 程 开 发 与 应 用 问题 。航 空 专 用工 艺 装 备 是 中航 工 业 北京 航 空 制造工程研究所主攻的另一个重要领域 ,从机床结构及 部 件 的设 计制 造 、配 置 安装 到 调 试 整个 过 程 都 形成 了独 有 的特 色 和 能力 , 以数 控机 床 为 例 ,经过 长 期 的 技术 研 究 和 实 际 工作 经 验 积 累 ,交 付 的数 控机 床 在 功 能 、性 能 和 可 靠 性 等方 面 都 达 到 了国 际或 国 内先进 水 平 ,完全 能 够 满足航空大型结构件的加工需要 。
切 削加 工 追 求 的 目标 是 高精 度 、 高效 率 、低 成 本 、 绿 色 环 保 。先 进 的 刀 具 技 术 是 促 进 切 削 技 术 发 展 的基础 和保证 ,刀具技术 的发展涉 及刀具材料 和刀具 结 构 的 发 展 , 刀 具 材 料 是 提 升 刀具 性 能 的基 础 , 刀 具 结 构是提高 工件加工精度 的关键 。随着高速 加工 、高 精 度 加 工 技 术 的 进 步 和 难 加 工 材 料 应 用 数 量 的 增 加 , 刀 具材料和 技术 的进展 也十分显 著 ,人们 在新型刀具 材料 的应用 、刀具涂层 技术 以及 新型刀具切 削性能方 面 进 行 了大 量 的 研 究 与 应 用 工 作 , 以适 应 高速 切 削 、 干式切 削、高精度加工 的基本 需求 。
航空整体结构件加工变形控制与校正关键技术分析

航空整体结构件加工变形控制与校正关键技术分析航空整体结构件加工变形控制与校正是航空制造中至关重要的关键技术之一。
航空整体结构件加工变形是指在航空零部件的加工过程中,由于各种原因引起的零件尺寸、形状或位置的偏差。
这些变形可能会对零部件的装配、运行和使用产生负面影响,甚至导致零部件的失效。
航空整体结构件加工变形的原因是多种多样的,主要包括材料性质的变化、加工工艺参数的变化、设备磨损和热变形等。
为了控制和校正这些变形,需要采取一系列的关键技术。
材料选择是影响加工变形控制与校正的关键因素之一。
不同材料具有不同的热胀冷缩系数和弯曲刚度,对加工变形的敏感度也不同。
合理选择材料可以减小加工变形的幅度。
设计优化是一种有效的加工变形控制与校正的方法。
通过在设计阶段考虑零部件的形状、结构和尺寸等因素,可以减小加工变形的影响。
在结构设计中使用加强件和支撑件,可以增加零部件的刚度和稳定性。
加工工艺参数的控制也是加工变形控制与校正的重要手段。
加工工艺参数包括切削速度、进给量、切削深度和刀具尺寸等。
通过合理选择和控制这些参数,可以减小加工变形的影响。
温度控制也是加工变形控制与校正的关键技术之一。
温度变化会导致材料的热胀冷缩和热变形,加剧加工变形的程度。
在加工过程中需要采取措施,如加工室温度控制、定期冷却等,以控制和减小温度对加工变形的影响。
加工方法的选择也是加工变形控制与校正的关键技术之一。
不同的加工方法具有不同的加工变形特点。
在高速切削中,由于切削温度的升高和材料的塑性变形,加工变形较大;而在慢速切削中,由于切削温度较低,加工变形较小。
航空整体结构件加工变形控制与校正是一个复杂而重要的问题,需要综合考虑材料选择、设计优化、加工工艺参数控制、温度控制和加工方法选择等关键技术。
只有掌握和应用这些技术,才能有效控制和校正加工变形,确保航空整体结构件的质量和性能。
航空材料精密成型技术

航空材料精密成型技术航空材料精密成型技术是指针对航空领域所用的各种材料,经过精密的成型加工,制成符合特定要求的零部件或结构件的技术。
精密成型技术,可以提高航空产品的品质,降低生产成本,延长使用寿命,减少故障率,并增强其适应能力和竞争力。
航空领域所用的材料种类繁多,包括合金钢、不锈钢、高温合金、镍基合金、钛合金等。
它们的物理、化学性能各不相同,生产加工难度大、成本高,因此要求精密成型技术必须能够承受高强度、高温、高压等压力的考验。
目前,航空材料精密成型技术的发展方向主要是针对高性能、高耐久性、高确度、高效率、高环保等特征,逐步发展出精密铸造、精密热加工、精密冷加工、精密电加工等多种技术。
一、高精度航空零部件的加工要求高精度,常常需要达到亚微米级别的品质标准。
此时,精密成型技术便是最佳选择。
通过采用先进的计算机数控技术和高精度的工艺设备,可以确保加工出来的零部件尺寸精准、形状不变形,形成封闭的加工过程,从而实现高品质的成型加工。
二、高效率航空零部件加工量大,生产效率成为生产制造的主要因素。
精密成型技术能够实现高效率的成型加工,因为精密成型技术采用了多个模具同时加工,从而节省了时间,同时保证高品质产品的生产率。
三、高质量精密成型技术具有最高的质量,这是因为该技术的每一步操作都采用精密加工设备,冷却系统、温度控制等设备都采用最新的先进技术,能够精确调节工艺参数,保证成品的材质、力学性能、加工精度等,从而提高产品品质和使用性能。
四、高应用性由于航空材料精密成型技术可以适应各种不同的材料,因此具有很高的应用性,能够产生不同种类的航空部件,可以满足不同种类航空飞行器部件的生产需求。
另外,精密成型技术还可以扩展到其他领域,如汽车制造、医疗器械等,可以提高这些行业产品的生产工艺和品质水平。
总的来说,航空材料精密成型技术是非常重要和必要的技术,它突破了在传统的制造工艺中的生产难题,并且成为了航空工业发展的重要基石。
飞行器制造工艺课件PPT 37页)
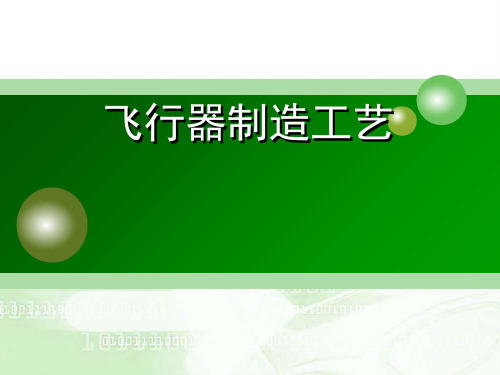
1.3 现代飞行器制造的先进技术及关键技术
整体结构件
1.3 现代飞行器制造的先进技术及关键技术
4. 数字化制造及装配技术
在飞行器的制造过程中,产品的制造实质上是一个产 品数据采集、建模、传递和加工处理的过程,整个过程离 不开数据的传递。
数字化装配技术的发展,使得现代飞行器装配技术发 生了重大变革,大幅缩短了装配周期,提高了装配质量。
整体结构件的加工成形技术13现代飞行器制造的先进技术及关键技术整体结构件13现代飞行器制造的先进技术及关键技术在飞行器的制造过程中产品的制造实质上是一个产品数据采集建模传递和加工处理的过程整个过程离不开数据的传递
飞行器制造工艺
第1章 绪论
第一节
1.1 飞行器研制的一般过程
第一节
飞行器
几个概念
指在大气层内或层外空间飞行的器械,包括 航空器、航天器、火箭和导弹。
1.2.1.飞机产品特点
1. 2. 3.
1.2 现代飞行器制造工艺的技术特点
1.2.1 飞机产品特点
5.
1.2 现代飞行器制造工艺的技术特点
1.2.2 飞行器制造工艺的技术特点
1. 2. 3.
1.3 现代飞行器制造的先进技术及关键技术
3D打印也叫增材制造技术或 激光快速成型(LRP),原理是将 计算机设计出的三维模型分解成 若干层平面切片,然后把打印材 料按切片图形逐层叠加,最终堆 积成完整的物体。
1.3 现代飞行器制造的先进技术及关键技术
3. 整体结构件的加工成形技术
飞机机体大量采用整体结构件后,对飞机的整个制造技术和 过程产生了重大影响。
整体结构的制造有利于全面采用先进的数字化技术进行设 计和生产。从而简化飞机的相互协调、工装的设计安装及飞机 装配工作。 飞机外形的协调和构件的互换将由原来主要依靠 模具和装配来保证,逐步过渡到主要依靠构件自身的加工准确 度和计算机辅助定位安装来实现。
精密焊接技术在航空航天的应用
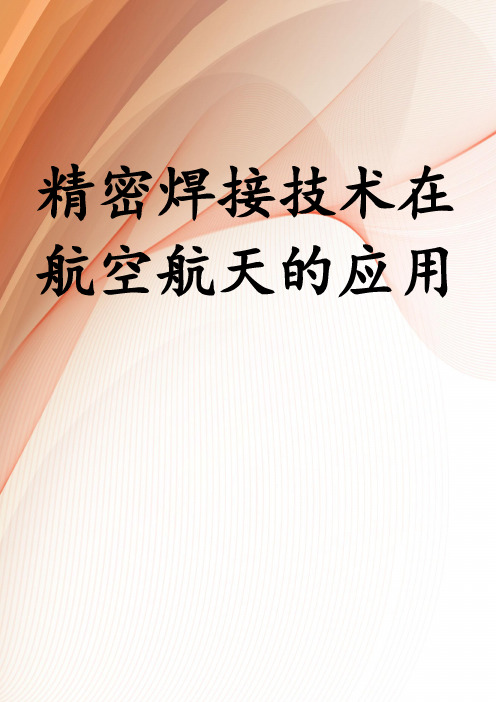
精密焊接技术在航空航天的应用精密焊接技术作为现代制造业中的一项关键技术,在众多高科技领域发挥着举足轻重的作用,尤其是在航空航天这样对材料性能、结构强度及可靠性要求极高的行业中,其应用显得尤为重要。
本文将从六个方面探讨精密焊接技术如何在航空航天领域中展现出独特的价值。
一、提高结构件的性能与安全性航空航天器在极端环境下的运行,如高速飞行、太空真空、剧烈温差等,对结构件的强度、耐腐蚀性和轻量化有着极高的要求。
精密焊接技术,尤其是激光焊接和电子束焊接,能实现极细小焊缝的精准控制,减小热影响区,保持材料的原有性能,显著提高结构件的整体强度和韧性,确保飞行器在复杂条件下的安全运行。
二、实现轻量化设计为了提高燃油效率和增加载荷能力,航空航天领域对轻量化材料的应用日益广泛,如钛合金、铝合金和复合材料等。
这些材料的传统连接方式往往难以满足轻量化和高强度的双重需求。
而精密焊接技术能有效解决这一问题,通过精确控制能量输入,最小化热变形和残余应力,使得轻质材料能够以更高效的方式连接,达到减轻整体重量的目的,进而提升飞行效率和续航能力。
三、提升制造精度与复杂度航空航天结构件通常具有复杂的几何形状和严格的尺寸公差要求。
精密焊接技术,特别是自动化和机器人焊接系统,能够实现高精度的三维空间轨迹控制,完成复杂结构的焊接,如发动机叶片、机身框架等。
这种技术的应用不仅提高了生产效率,还保证了零件的准确性和一致性,为航空航天器的高性能提供了基础。
四、延长使用寿命与维护周期航空航天器的维护成本高昂,频繁的维修和更换部件会大大增加运行成本。
精密焊接技术可以改善接头微观结构,减少焊接缺陷,如裂纹、气孔等,从而提高焊接部位的耐久性和疲劳寿命。
这意味着飞机和航天器可以在更长的时间内保持良好的运行状态,减少停机维护时间,降低总体拥有成本。
五、促进新材料的应用随着材料科学的进步,航空航天领域不断探索和应用新型材料,如陶瓷基复合材料、高温合金等,这些材料的加工和连接极具挑战。
飞机水平安定面整体复合材料结构装配关键技术研究

飞机水平安定面整体复合材料结构装配关键技术研究卜泳;肖庆东;黄春;韩洁【摘要】随着复合材料用量的不断扩大,我国民用客机的水平安定面复合材料整体化导致装配基准变化、对称度难以保证、大量盲区复合材料钻孔等问题.通过开展装配基准的选择、下壁板组件的精确定位、激光跟踪仪测量辅助定位、盲区精确协调钻孔等关键技术研究,顺利完成某型民用客机复合材料整体水平安定面的装配,气动外形、紧固件安装及装配质量均满足设计要求.【期刊名称】《航空制造技术》【年(卷),期】2015(000)021【总页数】4页(P93-95,99)【关键词】复合材料;水平安定面;整体结构;装配【作者】卜泳;肖庆东;黄春;韩洁【作者单位】中航工业北京航空制造工程研究所数字化制造技术航空科技重点实验室;中航工业北京航空制造工程研究所数字化制造技术航空科技重点实验室;中航工业北京航空制造工程研究所数字化制造技术航空科技重点实验室;中航工业北京航空制造工程研究所数字化制造技术航空科技重点实验室【正文语种】中文随着复合材料设计和制造技术的不断发展和成熟,先进复合材料在军、民用飞机上的用量不断扩大。
目前,复合材料和铝、钢、钛一起,已发展成为4大航空结构材料[1]。
在竞争激烈的民用客机市场,越来越突出强调安全性、经济性、舒适性和环保性,这些性能的高要求决定了对复合材料需求的迫切性和必然性,复合材料用量已是飞机先进性的一个重要标志[2]。
空客超大型客机A380复合材料用量达到25%,波音的B787飞机复合材料用量达到50%左右。
空客为应对B787的挑战,在研的A350复合材料用量达到52%[3]。
我国民用飞机结构上复合材料的应用与国际先进水平存在较大差距,最新研制的ARJ21-700支线客机复合材料用量不足2%[4]。
为此,某型支线客机水平安定面采用了与以往不同的结构设计,即结构复合材料整体化。
将原有铝合金材料的左、中、右3段分体式结构改为整体复合材料一段式结构,如图1所示。
现代化机械制造工艺及精密加工技术深入研究分析
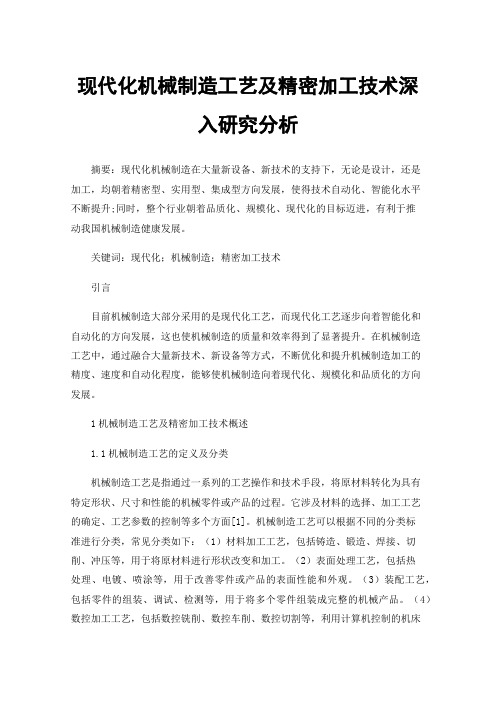
现代化机械制造工艺及精密加工技术深入研究分析摘要:现代化机械制造在大量新设备、新技术的支持下,无论是设计,还是加工,均朝着精密型、实用型、集成型方向发展,使得技术自动化、智能化水平不断提升;同时,整个行业朝着品质化、规模化、现代化的目标迈进,有利于推动我国机械制造健康发展。
关键词:现代化;机械制造;精密加工技术引言目前机械制造大部分采用的是现代化工艺,而现代化工艺逐步向着智能化和自动化的方向发展,这也使机械制造的质量和效率得到了显著提升。
在机械制造工艺中,通过融合大量新技术、新设备等方式,不断优化和提升机械制造加工的精度、速度和自动化程度,能够使机械制造向着现代化、规模化和品质化的方向发展。
1机械制造工艺及精密加工技术概述1.1机械制造工艺的定义及分类机械制造工艺是指通过一系列的工艺操作和技术手段,将原材料转化为具有特定形状、尺寸和性能的机械零件或产品的过程。
它涉及材料的选择、加工工艺的确定、工艺参数的控制等多个方面[1]。
机械制造工艺可以根据不同的分类标准进行分类,常见分类如下:(1)材料加工工艺,包括铸造、锻造、焊接、切削、冲压等,用于将原材料进行形状改变和加工。
(2)表面处理工艺,包括热处理、电镀、喷涂等,用于改善零件或产品的表面性能和外观。
(3)装配工艺,包括零件的组装、调试、检测等,用于将多个零件组装成完整的机械产品。
(4)数控加工工艺,包括数控铣削、数控车削、数控切割等,利用计算机控制的机床进行精密加工。
(5)先进制造工艺,包括激光加工、电子束加工、快速成型等,利用先进的技术手段进行高效、精密的制造。
1.2精密加工技术的定义及分类精密加工技术是指利用先进的加工设备和工艺,对工件进行高精度、高质量的加工和制造的技术。
它主要应用于制造高精度、高要求的零部件和产品,如航空航天、汽车、电子、光学等领域。
精密加工技术可以根据加工方式和加工对象的不同进行分类,常见的分类如下:(1)机械加工,包括车削、铣削、钻削、磨削等传统的机械加工方法,通过切削、磨削等方式对工件进行加工。
航空航天行业航天器部件精密制造方案
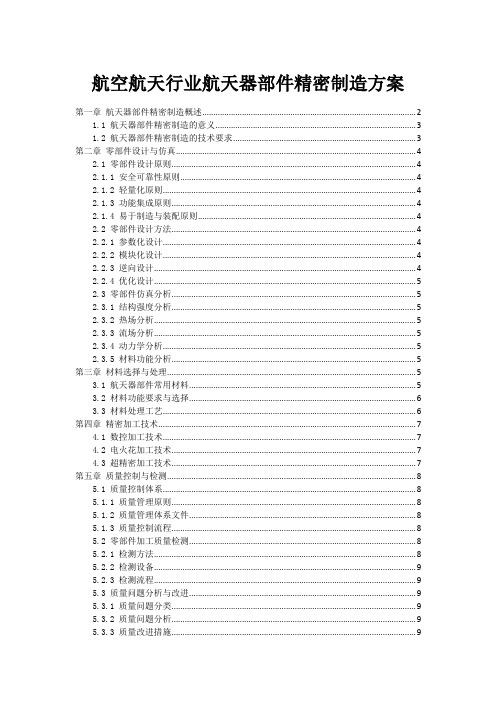
航空航天行业航天器部件精密制造方案第一章航天器部件精密制造概述 (2)1.1 航天器部件精密制造的意义 (3)1.2 航天器部件精密制造的技术要求 (3)第二章零部件设计与仿真 (4)2.1 零部件设计原则 (4)2.1.1 安全可靠性原则 (4)2.1.2 轻量化原则 (4)2.1.3 功能集成原则 (4)2.1.4 易于制造与装配原则 (4)2.2 零部件设计方法 (4)2.2.1 参数化设计 (4)2.2.2 模块化设计 (4)2.2.3 逆向设计 (4)2.2.4 优化设计 (5)2.3 零部件仿真分析 (5)2.3.1 结构强度分析 (5)2.3.2 热场分析 (5)2.3.3 流场分析 (5)2.3.4 动力学分析 (5)2.3.5 材料功能分析 (5)第三章材料选择与处理 (5)3.1 航天器部件常用材料 (5)3.2 材料功能要求与选择 (6)3.3 材料处理工艺 (6)第四章精密加工技术 (7)4.1 数控加工技术 (7)4.2 电火花加工技术 (7)4.3 超精密加工技术 (7)第五章质量控制与检测 (8)5.1 质量控制体系 (8)5.1.1 质量管理原则 (8)5.1.2 质量管理体系文件 (8)5.1.3 质量控制流程 (8)5.2 零部件加工质量检测 (8)5.2.1 检测方法 (8)5.2.2 检测设备 (9)5.2.3 检测流程 (9)5.3 质量问题分析与改进 (9)5.3.1 质量问题分类 (9)5.3.2 质量问题分析 (9)5.3.3 质量改进措施 (9)5.3.4 持续改进 (9)第六章零部件装配与调试 (9)6.1 装配工艺 (9)6.1.1 装配原则 (9)6.1.2 装配流程 (9)6.1.3 装配技术 (10)6.2 调试方法 (10)6.2.1 功能调试 (10)6.2.2 功能调试 (10)6.2.3 系统调试 (10)6.3 装配与调试质量控制 (10)6.3.1 质量保证体系 (10)6.3.2 质量问题处理 (11)6.3.3 持续改进 (11)第七章零部件可靠性分析 (11)7.1 可靠性评价指标 (11)7.2 可靠性分析方法 (11)7.3 可靠性改进措施 (12)第八章航天器部件精密制造信息化管理 (12)8.1 信息化管理平台构建 (12)8.2 数据采集与处理 (13)8.3 信息化管理应用 (13)第九章节能与环保 (14)9.1 节能措施 (14)9.1.1 设计优化 (14)9.1.2 生产过程控制 (14)9.1.3 能源回收与利用 (14)9.2 环保要求与措施 (14)9.2.1 原材料选用 (14)9.2.2 生产工艺改进 (14)9.2.3 环境保护设施 (15)9.3 节能与环保效果评价 (15)9.3.1 能源消耗评价 (15)9.3.2 环境污染评价 (15)9.3.3 节能与环保效益评价 (15)第十章航天器部件精密制造发展趋势与展望 (15)10.1 技术发展趋势 (15)10.2 市场前景与挑战 (16)10.3 产业政策与发展策略 (16)第一章航天器部件精密制造概述1.1 航天器部件精密制造的意义航天器部件是航天器系统的重要组成部分,其功能、精度和可靠性直接关系到航天器的整体功能和任务成功率。
航空航天工程师的航空航天工程关键技术攻关与创新
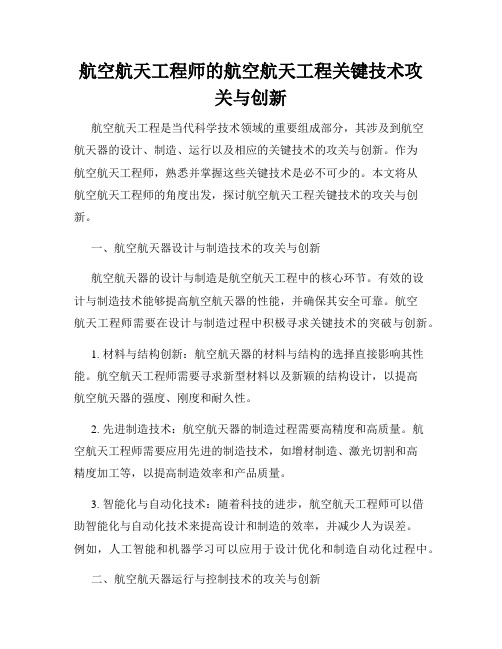
航空航天工程师的航空航天工程关键技术攻关与创新航空航天工程是当代科学技术领域的重要组成部分,其涉及到航空航天器的设计、制造、运行以及相应的关键技术的攻关与创新。
作为航空航天工程师,熟悉并掌握这些关键技术是必不可少的。
本文将从航空航天工程师的角度出发,探讨航空航天工程关键技术的攻关与创新。
一、航空航天器设计与制造技术的攻关与创新航空航天器的设计与制造是航空航天工程中的核心环节。
有效的设计与制造技术能够提高航空航天器的性能,并确保其安全可靠。
航空航天工程师需要在设计与制造过程中积极寻求关键技术的突破与创新。
1. 材料与结构创新:航空航天器的材料与结构的选择直接影响其性能。
航空航天工程师需要寻求新型材料以及新颖的结构设计,以提高航空航天器的强度、刚度和耐久性。
2. 先进制造技术:航空航天器的制造过程需要高精度和高质量。
航空航天工程师需要应用先进的制造技术,如增材制造、激光切割和高精度加工等,以提高制造效率和产品质量。
3. 智能化与自动化技术:随着科技的进步,航空航天工程师可以借助智能化与自动化技术来提高设计和制造的效率,并减少人为误差。
例如,人工智能和机器学习可以应用于设计优化和制造自动化过程中。
二、航空航天器运行与控制技术的攻关与创新航空航天器的运行与控制技术是保证航空航天器正常运行和飞行安全的关键。
航空航天工程师需要关注并不断攻关与创新这些技术,以确保航空航天器的高效运行。
1. 飞行控制系统:航空航天工程师需要研究与开发先进的飞行控制系统,如自动驾驶系统、导航系统和飞行模拟器等。
这些系统可以提高航空航天器的飞行控制精度和可靠性。
2. 飞行安全技术:在航空航天器的运行过程中,飞行安全至关重要。
航空航天工程师需要关注飞行安全技术的攻关与创新,如预测与避让系统、飞行器结构健康监测和航空管制系统的优化等。
3. 航空航天器维护与修复技术:航空航天工程师需要关注航空航天器的维护与修复技术,以确保航空航天器的正常运行。
航空发动机零部件精密制造技术

航空发动机零部件精密制造技术作者:贾丽郝军涛杜改梅来源:《科技创新与应用》2018年第30期摘要:航空发动机关键零部件的精密制造技术一直是我国高性能航空发动机研制的瓶颈。
文章深入分析了航空发动机关键零部件的典型制造技术,对精密制坯、高效切削、抗疲劳制造、特种加工以及复合材料构件加工技术进行了总结,并给出了其发展方向。
关键词:航空发动机;精密制坯;高效切削;抗疲劳制造中图分类号:V262.3 文献标志码:A 文章编号:2095-2945(2018)30-0157-04Abstract: The precision manufacturing technology of the key components of aero-engine has been the bottleneck of the development of high-performance aero-engine in our country. This paper analyzes the typical manufacturing technology of the key components of aero-engine, summarizes the technologies of precision billet making, high-efficiency cutting, anti-fatigue manufacturing,special machining and processing of composite components, and gives the development direction of these technologies.Keywords: aero-engine; precision blanking; high efficiency cutting; anti-fatigue manufacturing航空制造集聚了大量的高新制造技术,其制造过程对制造设备、工艺、执业人员素质等要求极高;航空发动机被誉为飞机的“心脏”,是研发制造难度最大最顶级的现代工业造物,其制造技术的进步对航空制造乃至整个制造业的发展起着决定性的作用。
飞机结构零件数控加工技术研讨

,$’’,.2"03’’;目前在高速设备上采用的参数为 !" ,$$$$% & ’(!, )*"$+,’’, ./"-14’’, .2"03’’。 前 者 (低速加工)切削速度为 #$0’ & ’(!;而后者 (高速
加工)切削速度为,$$$’ & ’(!。实际应用情况表明:采 用高速切 削 后 , 金 属 切 除 率 大 幅 提 高 , 约 是 低 速 切 削 的 A;1 倍,切削力大幅下降,仅是低速切削的 @<;A<D , 切削振动 减 少 , 零 件 表 面 质 量 及 尺 寸 精 度 提 高 , 在 常 规低速切 削 中 备 受 困 惑 的 一 系 列 亦 问 题 (如 加 工 变 形 等)得到了解决,加工效率和零件质量得到了提高。
图A
0+ 对于薄壁侧面的加工
在切削参数允许的范围内采用较大的径向分层和较 小的轴向分层加工;对于侧壁两面都需加工时候采取台 阶式来回铣削, 充分利用零件的整体刚性,可提高加 工效率(如下图C) 。
四、薄壁零件的加工工艺探讨
随着飞机性能要求的进一步提高,现代航空工业 中大量使 用 整 体 薄 壁 结 构 零 件 。 其 主 要 结 构 由 侧 壁 和 腹板组成 , 结 构 简 洁 、 尺 寸 较 大 、 加 工 余 量 大 、 相 对 刚度较低 (如 图 @) ,故加工工艺性差。在切削力、切 削热、切 削 振 颤 等 因 素 影 响 下 , 易 发 生 加 工 变 形 , 不 易控制加 工 精 度 和 提 高 加 工 效 率 。 加 工 变 形 和 加 工 效 率问题成为薄壁结构加工的重要约束。 加工薄壁零件的关键在于切削过程的稳定性。大 量的实验 工 作 证 明 , 随 着 零 件 壁 厚 的 降 低 , 零 件 的 刚 性减低, 加 工 变 形 增 大 , 容 易 发 生 切 削 振 颤 , 影 响 零 件的加工 质 量 和 加 工 效 率 。 以 下 是 我 厂 在 薄 壁 零 件 的
飞机结构件数控加工方案快速生成技术研究与开发

cekadotu o ah i l .o p e i t r t d,h cn u h ee v t e, hc n u t m i n pa C m a dwt o e h sti t h i e a s r a a a s i p c ng n f r h h m o e s e q s v a dn g l sc uh哪 s d d e entno m ci n pa dt f i t n cr e gnr i .nadtn it t a i dd i ahn g l a ef c n ad cu ee o I i ,t n a r z f i f i o  ̄ n n h e e a a o i t f t a n d i o
{其局限性基础上 , 出飞机结构件数控加 工方案快速生成技术。 _ 提 主要 内容 包, 建立其数据模型 , 完成加工方案规 范化定义;2 以方案规 范化定义为基础 , () 开展快速 生成技 t {术的研 究与开发 ;3介绍方案正确性检查及方案输 出等。 () 与现有加工方案生成技术相 比, 技术具有方案 ; t定义规范、 方案生成快速准确等特点, 此外 , 还体现 了加工方案知识表达与重用。 t
p a o a r l e s r c u e l n t i an tu t r p
S i g, HENG Gu -e RAO Yo - u , HU n — h n HI n Z J o 1i, u f C Ho g z e
( c ol f c a ia E gn eiga dA t t n B in nv r t o eo at s n s o a t s h o o h ncl n ier n uo i , e igU i s y f rnui dA t n ui , S Me n ma o j e i A ca r c
面向大型航空构件的国产高档数控机床和专用装备

面向大型航空构件的国产高档数控机床和专用装备王增新;王卫朝【期刊名称】《航空制造技术》【年(卷),期】2015(000)016【总页数】6页(P48-53)【作者】王增新;王卫朝【作者单位】中航工业北京航空制造工程研究所;中航工业北京航空制造工程研究所【正文语种】中文飞机性能的提高取决于机体结构效率和发动机推重比的提高,机体结构效率和发动机推重比的提高取决于高性能材料和先进结构的采用,而高性能材料和先进结构的获得则取决于先进的制造技术。
数控制造技术是航空工业发展先进制造技术的重要组成部分。
数控技术应用的广度和水平是衡量航空工业综合技术水平和企业现代化水平的重要指标之一。
航空制造业既是高端制造业技术水平的标志,又是一个国家高档数控机床创新与发展的策源地。
各国数控机床厂商正紧密围绕航空制造技术不断发展的需求进行设备研制。
航空结构件是构成飞机机体骨架和气动外形的主要组成部分,现代飞机为满足隐身、超声速巡航、超常规机动、高信息感知能力、长寿命、结构轻量化等方面的性能要求,大量采用新技术、新结构、新材料,其结构件主要向整体化、大型化、复杂化、精确化和材料多元化方向发展。
随着技术的发展,现代大型飞机在材料选择方面呈现出新的特点和趋势,现代飞机材料已经从以前的铝合金独霸天下变成了铝合金、钛合金、复合材料三分天下的局面,而且复合材料、钛合金还有进一步扩大的趋势[1]。
航空结构件制造中,不同的材料特性和工艺方法对相应的数控装备提出了不同要求,主要表现为:(1)铝合金零件数控加工机床的设计轻量化和运行高速化;(2)钛合金和高强度结构钢零件数控加工机床的大扭矩和高刚性;(3)复合材料零件制造设备的自动化和数控化。
中航工业北京航空制造工程研究所航空专用装备工程中心是国内最早开发数控机床的单位之一,作为航空专用工艺装备的配套研制单位,经过数十年的发展,逐步形成了多种型号规格的针对铝合金、钛合金和复合材料高效加工的系列产品。
提高数控加工效率与潜能的关键技术应用研究(上)
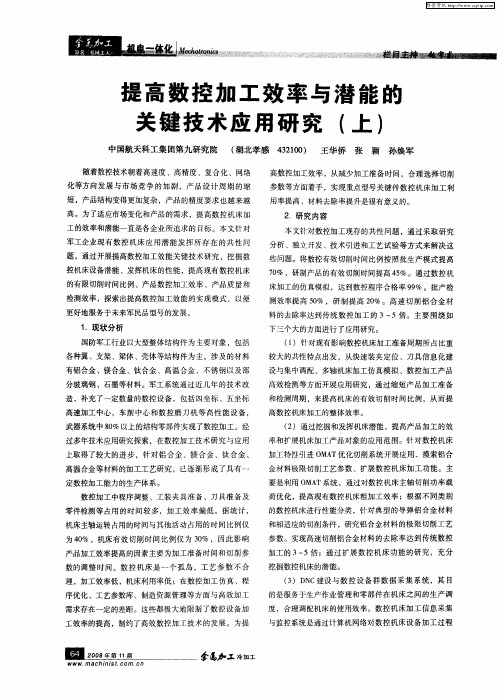
高速加工 中心 ,车削 中心和数 控磨 刀机等 高性 能设 备 , 武器 系统 中 8% 以上 的结构零部件实现了数 控加工 。经 0 过多年技术 应用研究探索 ,在数控加 工技 术研究 与应用 上取得 了较大 的进步 ,针对 铝 合金 、镁 合金 、钛 合金 、
加工特性 引进 O A 优化切削系统 开展 应用 、摸索铝合 M T
( )D c建设 与数 控设 备群 数 据采 集 系统 ,其 目 3 N
零件检测等 占用 的时间较 多 ,加工 效率 偏低 。据 统计 ,
机床主轴运转占用的时间与其他活动占用的时间比例仅 为4% , 0 机床有效切削时间比例仅为 3%,因此影响 0
产 品加工效率提高 的因素主要为加工准备 时间和切 削参 数的调 整 时 间。数 控 机床 是 一个 孤 岛,工艺 参数 不 合 理, 加工效率低 ,机床利用率低 ;在 数控加工仿 真 、程 序优化 、工艺参数库 、制造 资源管理等方 面与高效加 工 需求存在一定 的差距。这些都极大地限制 了数控设备 加
夹定位夹具 的结构简 图。该夹具 具有适应性 广 ,既可 以 在加工 中心上使用 ,也可 以在 车床上使用 。该夹具 的设
计 ,符合标准化 、通用化 的设计 要求 ,切实 提升 了夹 具 的设计能力 ,填补 了 目前市场上 还没有大直 径 自定心 卡
盘的空白。
间、机床停机状态及机床报警等生 产信息 和机 床信息 进 行数据采集和监控 。在 以上信息 的帮助下 ,生 产管理 者
参磊 工冷 工 加
维普资讯
一
一
搿 冁 麓
囊嚣 露一控 ,对数控设备运行 的全 过程进行 信息采集 ,包
括机 床空 载 、有 效切 削 、产 品加工 数 量 、产 品加 工 时
航空整体结构件加工变形校正技术研究

straightening parameters
对于同样变形工件,不同的校正载荷施加方式 对校正效果有一定影响。采用集中校正载荷与分布 校正载荷,对于尺寸精度影响是不一样的。对于同 样的变形工件,校正支点位置不同,校正效果也会有 差别。支点位置选择不合理,会引起工件的附加变 形,达不到预期校正效果甚至造成工件报废。由于 航空结构件存在着框、筋板等,选择支点位置及载荷
2. 1 校正载荷施加方式影响 支点位置及校正载荷施加位置,如图 4 所示。
支点位置选取为 B 处,为了对比不同载荷施加方式 对尺寸精度的影响,在 A 处施加集中校正载荷,C 处 施加分布载荷进行校正过程分析。
图 4 载荷施加位置及类型 Fig. 4 Sketch of constrain and loading
1 变形校正的关键技术
1. 1 三维质量模型重构及协同仿真集成环境 本文将包含有加工残余应力信息的初始变形几
何模型称之为三维质量模型,一方面是三维几何模 型的重构,另一方面是对内部残余应力的信息模型 进行重构,为校形量的正确计算及安全校正提供基 础和保障。建立如图 1 所示的集成协同仿真环境, 将加工变形仿真—校正过程综合起来进行研究。主 要包含 3 个过程: 1) 加工过程的仿真,以获得加工 变形后的模型及残余应力分布状态。由于残余应力 是引起加工变形的主要原因,在加工仿真过程中,忽 略铣削力的影响,假定残余应力沿层深方向有规律 分布[10]。2) 进行加工变形结果分析,用 ANSYS 中 的 APDL 语言编制相应的接口程序,提取加工变形 后的有限元模型及最终的残余应力场数据。3) 变 形校正仿真,将第 2 个过程提取得到的加工变形模 型作为初始校正模型,即几何模型的重构。再将加 工变形后的残余应力场添加进来,完成残余应力信 息的重构,形成变形校正三维质量模型。 1. 2 校正参数的计算及校正载荷作用方式
航空航天行业先进制造技术与研发管理方案
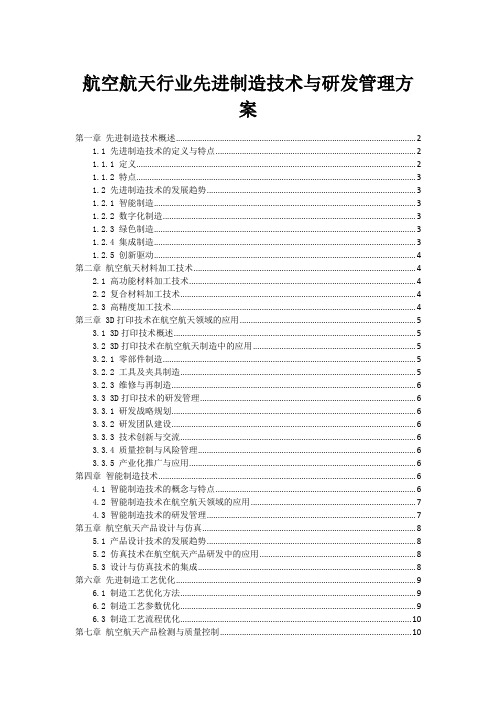
航空航天行业先进制造技术与研发管理方案第一章先进制造技术概述 (2)1.1 先进制造技术的定义与特点 (2)1.1.1 定义 (2)1.1.2 特点 (3)1.2 先进制造技术的发展趋势 (3)1.2.1 智能制造 (3)1.2.2 数字化制造 (3)1.2.3 绿色制造 (3)1.2.4 集成制造 (3)1.2.5 创新驱动 (4)第二章航空航天材料加工技术 (4)2.1 高功能材料加工技术 (4)2.2 复合材料加工技术 (4)2.3 高精度加工技术 (4)第三章 3D打印技术在航空航天领域的应用 (5)3.1 3D打印技术概述 (5)3.2 3D打印技术在航空航天制造中的应用 (5)3.2.1 零部件制造 (5)3.2.2 工具及夹具制造 (5)3.2.3 维修与再制造 (6)3.3 3D打印技术的研发管理 (6)3.3.1 研发战略规划 (6)3.3.2 研发团队建设 (6)3.3.3 技术创新与交流 (6)3.3.4 质量控制与风险管理 (6)3.3.5 产业化推广与应用 (6)第四章智能制造技术 (6)4.1 智能制造技术的概念与特点 (6)4.2 智能制造技术在航空航天领域的应用 (7)4.3 智能制造技术的研发管理 (7)第五章航空航天产品设计与仿真 (8)5.1 产品设计技术的发展趋势 (8)5.2 仿真技术在航空航天产品研发中的应用 (8)5.3 设计与仿真技术的集成 (8)第六章先进制造工艺优化 (9)6.1 制造工艺优化方法 (9)6.2 制造工艺参数优化 (9)6.3 制造工艺流程优化 (10)第七章航空航天产品检测与质量控制 (10)7.1 检测技术的发展趋势 (10)7.1.1 检测技术概述 (10)7.1.2 发展趋势 (11)7.2 质量控制方法与标准 (11)7.2.1 质量控制方法 (11)7.2.2 质量控制标准 (11)7.3 检测与质量控制技术的集成 (11)第八章航空航天研发项目管理 (12)8.1 研发项目管理体系 (12)8.1.1 管理体系概述 (12)8.1.2 项目管理组织结构 (12)8.1.3 项目管理流程 (12)8.2 研发项目进度与成本控制 (12)8.2.1 进度控制 (13)8.2.2 成本控制 (13)8.3 研发项目风险管理 (13)8.3.1 风险识别 (13)8.3.2 风险评估 (13)8.3.3 风险应对 (13)第九章航空航天研发团队建设与管理 (14)9.1 研发团队组织结构 (14)9.1.1 领导层 (14)9.1.2 研发部门 (14)9.1.3 支持部门 (14)9.2 团队成员能力培养与激励 (14)9.2.1 能力培养 (14)9.2.2 激励措施 (14)9.3 团队协作与沟通 (15)9.3.1 建立有效沟通机制 (15)9.3.2 强化团队协作意识 (15)9.3.3 提高沟通效率 (15)第十章航空航天先进制造技术创新与发展 (15)10.1 技术创新策略与方法 (15)10.2 先进制造技术发展趋势 (15)10.3 航空航天先进制造技术发展路径与规划 (16)第一章先进制造技术概述1.1 先进制造技术的定义与特点1.1.1 定义先进制造技术是指在现代工业生产中,融合了信息技术、自动化技术、新材料技术、绿色制造技术等多种高新技术,以提高生产效率、降低成本、提高产品质量和创新能力为核心的一类制造技术。
飞机用钛合金结构件高效精密加工技术
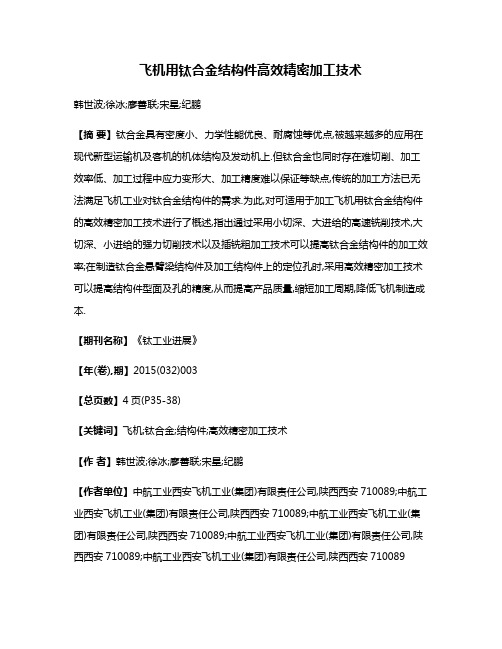
飞机用钛合金结构件高效精密加工技术韩世波;徐冰;廖善联;宋星;纪鹏【摘要】钛合金具有密度小、力学性能优良、耐腐蚀等优点,被越来越多的应用在现代新型运输机及客机的机体结构及发动机上.但钛合金也同时存在难切削、加工效率低、加工过程中应力变形大、加工精度难以保证等缺点,传统的加工方法已无法满足飞机工业对钛合金结构件的需求.为此,对可适用于加工飞机用钛合金结构件的高效精密加工技术进行了概述,指出通过采用小切深、大进给的高速铣削技术,大切深、小进给的强力切削技术以及插铣粗加工技术可以提高钛合金结构件的加工效率;在制造钛合金悬臂梁结构件及加工结构件上的定位孔时,采用高效精密加工技术可以提高结构件型面及孔的精度,从而提高产品质量,缩短加工周期,降低飞机制造成本.【期刊名称】《钛工业进展》【年(卷),期】2015(032)003【总页数】4页(P35-38)【关键词】飞机;钛合金;结构件;高效精密加工技术【作者】韩世波;徐冰;廖善联;宋星;纪鹏【作者单位】中航工业西安飞机工业(集团)有限责任公司,陕西西安710089;中航工业西安飞机工业(集团)有限责任公司,陕西西安710089;中航工业西安飞机工业(集团)有限责任公司,陕西西安710089;中航工业西安飞机工业(集团)有限责任公司,陕西西安710089;中航工业西安飞机工业(集团)有限责任公司,陕西西安710089【正文语种】中文钛合金材料是一种轻质的高强度结构材料,在航空航天、车辆工程、生物医学等领域具有非常重要的应用价值及广阔的应用前景[1]。
尤其是在现代航空制造领域中,钛合金材料因其良好的机械性能、耐腐蚀性能及密度小等优点,已逐步取代钢和铝合金,得到越来越广泛的应用。
然而,在实际加工中,一方面由于钛合金本身抗塑性变形能力很强,使得所需切削力很大,而且在加工过程中存在“表面硬化”现象,已加工过的结构件表面硬度很高,达到加工前的300% ~600%,所以切削钛合金时所需要的切削力需进一步增大,导致单位时间的金属去除率很低,制约了加工效率;另一方面由于钛合金材料加工过程中刀具每齿进给量很小,刀具与结构件材料间反复摩擦会产生大量的切削热,而钛合金的热导率约为 21 ~25 W/(m · K),是45#钢的1/3 ~1/4[2],使得切削区的温度很高,会加剧刀具的磨损,并限制进给速度。