热冲压关键技术
汽车热冲压成型工艺的技术解析

汽车热冲压成型工艺的技术解析热冲压技术热冲压成型(Hot stamping / Hot press forming)也称冲压硬化,是近年来出现的一项专门用于汽车高强度钢板冲压成型件的新技术,也是实现汽车轻量化生产的关键技术工艺之一。
那么,热冲压成型工艺的优势是什么?哪些是常见的汽车热冲压零件?热冲压生产线有几道工序?......汽车热冲压成形工艺3D动画常见的汽车热冲压零件采用热冲压成型技术制得的冲压件强度可高达1500MPa,且在高温下成型几乎没有回弹,具有成型精度高、成型性好等突出优点,因此引起业界的普遍关注并迅速成为汽车制造领域内的热门技术,广泛用于车门防撞梁、前后保险杠等安全件以及A柱、B柱、C柱、中通道等车体结构件的生产。
热冲压成型的五大工序•落料:是热冲压成型中的第一道工序,把板材冲压出所需外轮廓坯料。
•奥氏体化:包括加热和保温两个阶段。
这一工序的目的在于将钢板加热到一个合适的温度,使钢板完全奥氏体化,并且具有良好的塑性。
•转移:指的是将加热后的钢板从加热炉中取出放进热成型模具中去。
在这一道工序中,必须保证钢板被尽可能快地转移到模具中,一方面是为了防止高温下的钢板氧化,另一方面是为了确保钢板在成型时仍然处在较高的温度下,以具有良好的塑性。
•冲压和淬火:在将钢板放进模具之后,要立即对钢板进行冲压成型,以免温度下降过多影响钢板的成型性能。
成型以后模具要合模保压一段时间,一方面是为了控制零件的形状,另一方面是利用模具中设置的冷却装置对钢板进行淬火,使零件形成均匀的马氏体组织,获得良好的尺寸精度和机械性能。
•后续处理后续处理:在成型件从模具中取出以后,还需要对其进行一些后续的处理,如利用酸洗或喷丸的方式去除零件表面的氧化皮,以及对零件进行切边和钻孔。
热冲压件由于强度太高,不能用传统的手段对其进行切边及钻孔加工,而必须用激光技术来完成。
(来源:AI汽车制造业)。
热冲压工艺
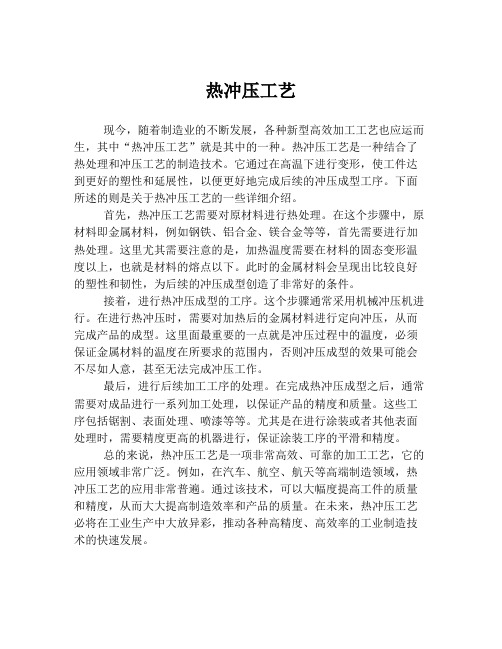
热冲压工艺现今,随着制造业的不断发展,各种新型高效加工工艺也应运而生,其中“热冲压工艺”就是其中的一种。
热冲压工艺是一种结合了热处理和冲压工艺的制造技术。
它通过在高温下进行变形,使工件达到更好的塑性和延展性,以便更好地完成后续的冲压成型工序。
下面所述的则是关于热冲压工艺的一些详细介绍。
首先,热冲压工艺需要对原材料进行热处理。
在这个步骤中,原材料即金属材料,例如钢铁、铝合金、镁合金等等,首先需要进行加热处理。
这里尤其需要注意的是,加热温度需要在材料的固态变形温度以上,也就是材料的熔点以下。
此时的金属材料会呈现出比较良好的塑性和韧性,为后续的冲压成型创造了非常好的条件。
接着,进行热冲压成型的工序。
这个步骤通常采用机械冲压机进行。
在进行热冲压时,需要对加热后的金属材料进行定向冲压,从而完成产品的成型。
这里面最重要的一点就是冲压过程中的温度,必须保证金属材料的温度在所要求的范围内,否则冲压成型的效果可能会不尽如人意,甚至无法完成冲压工作。
最后,进行后续加工工序的处理。
在完成热冲压成型之后,通常需要对成品进行一系列加工处理,以保证产品的精度和质量。
这些工序包括锯割、表面处理、喷漆等等。
尤其是在进行涂装或者其他表面处理时,需要精度更高的机器进行,保证涂装工序的平滑和精度。
总的来说,热冲压工艺是一项非常高效、可靠的加工工艺,它的应用领域非常广泛。
例如,在汽车、航空、航天等高端制造领域,热冲压工艺的应用非常普遍。
通过该技术,可以大幅度提高工件的质量和精度,从而大大提高制造效率和产品的质量。
在未来,热冲压工艺必将在工业生产中大放异彩,推动各种高精度、高效率的工业制造技术的快速发展。
热冲压工艺技术

热冲压工艺技术热冲压工艺技术是一种常用的金属加工方法,通常用于生产高精度、复杂形状的金属零件。
本文将介绍热冲压工艺技术的原理、应用领域,以及其优缺点。
热冲压是将金属板材加热至一定温度后,在冲床的作用下,通过模具将其冲压成所需形状的工艺。
由于加热后的金属板材具有良好的延展性和塑性,可以更容易地形成复杂的形状。
与传统的冷冲压相比,热冲压工艺技术具有以下几个优点:首先,热冲压可以改善金属板材的延展性。
在加热状态下,金属板材的结晶结构发生改变,晶格结构内的位错被激活,从而使金属板材具有更好的延展性,可以更容易地实现复杂形状的冲压。
其次,热冲压可以提高冲压成形的精度和表面质量。
由于加热状态下的金属板材具有更好的塑性,可以更容易地填充模具中的形状,从而得到更精确的冲压成形。
同时,加热状态下的金属板材有更好的流动性,可以减少表面缺陷,提高表面质量。
再次,热冲压可以减少变形力和模具磨损。
在加热状态下,金属板材的延展性增强,冲压时所需的变形力较小,可以降低模具的磨损。
热冲压工艺技术在许多领域得到了广泛应用。
例如,汽车制造领域,热冲压可以用于生产汽车车身、座椅骨架等复杂形状的零件;电子设备制造领域,热冲压可以用于生产手机壳、电池罩等精密零件;航空航天领域,热冲压可以用于生产飞机的机身、发动机零件等。
然而,热冲压工艺技术也存在一些局限性和挑战。
首先,热冲压工艺需要对加热温度、加热时间等参数进行精确控制,否则容易导致冲压成形不良。
其次,由于金属在加热过程中容易发生氧化、变色等问题,需要采取相应的防护措施,增加生产成本。
此外,热冲压工艺还需要使用专门的设备和模具,投入成本较高。
综上所述,热冲压工艺技术是一种高效、精确的金属加工方法,具有广泛的应用前景。
随着科技的不断进步和工艺技术的不断改进,相信热冲压工艺技术将在未来的金属加工领域发挥更大的作用。
大型超高强钢热冲压成型装备关键技术及产业化应用
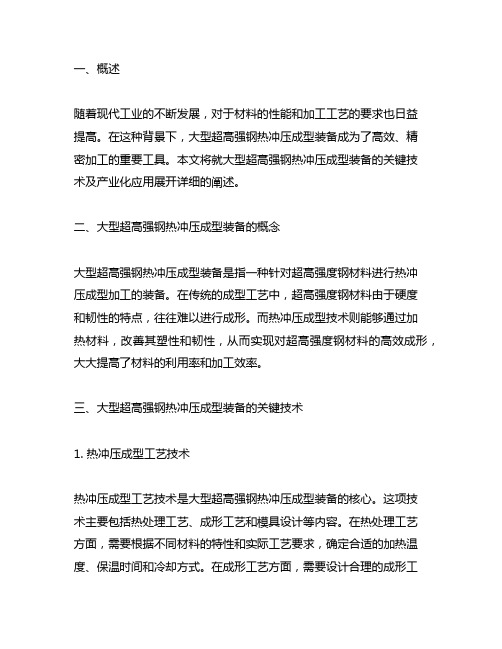
一、概述随着现代工业的不断发展,对于材料的性能和加工工艺的要求也日益提高。
在这种背景下,大型超高强钢热冲压成型装备成为了高效、精密加工的重要工具。
本文将就大型超高强钢热冲压成型装备的关键技术及产业化应用展开详细的阐述。
二、大型超高强钢热冲压成型装备的概念大型超高强钢热冲压成型装备是指一种针对超高强度钢材料进行热冲压成型加工的装备。
在传统的成型工艺中,超高强度钢材料由于硬度和韧性的特点,往往难以进行成形。
而热冲压成型技术则能够通过加热材料,改善其塑性和韧性,从而实现对超高强度钢材料的高效成形,大大提高了材料的利用率和加工效率。
三、大型超高强钢热冲压成型装备的关键技术1. 热冲压成型工艺技术热冲压成型工艺技术是大型超高强钢热冲压成型装备的核心。
这项技术主要包括热处理工艺、成形工艺和模具设计等内容。
在热处理工艺方面,需要根据不同材料的特性和实际工艺要求,确定合适的加热温度、保温时间和冷却方式。
在成形工艺方面,需要设计合理的成形工艺参数,包括压力、速度、温度等,从而确保成形过程的稳定性和高效性。
在模具设计方面,需要根据成形零件的形状和尺寸,设计合适的模具结构和加热方式,以实现对材料的精确成形。
2. 装备设计与制造技术大型超高强钢热冲压成型装备需要具备一定的加热、冷却和成形能力。
在装备设计方面,需要考虑材料的加热均匀性、成形的稳定性和模具的可靠性,从而确保整个成型过程的高效进行。
在装备制造技术方面,需要采用先进的加工工艺和材料技术,确保装备具备高强度、高稳定性和高耐用性,能够满足超高强度钢材料的加工需求。
3. 自动化控制技术自动化控制技术是大型超高强钢热冲压成型装备的重要保障。
通过自动化控制系统,可以实现对热处理、成形和模具等环节的精准控制,确保成型过程的稳定性和可靠性。
自动化控制系统还可以实现对装备运行状态的实时监测和故障诊断,提高了装备的运行效率和安全性。
四、大型超高强钢热冲压成型装备的产业化应用大型超高强钢热冲压成型装备的产业化应用已经在汽车、航空航天、轨道交通等领域得到广泛应用。
b柱热冲压
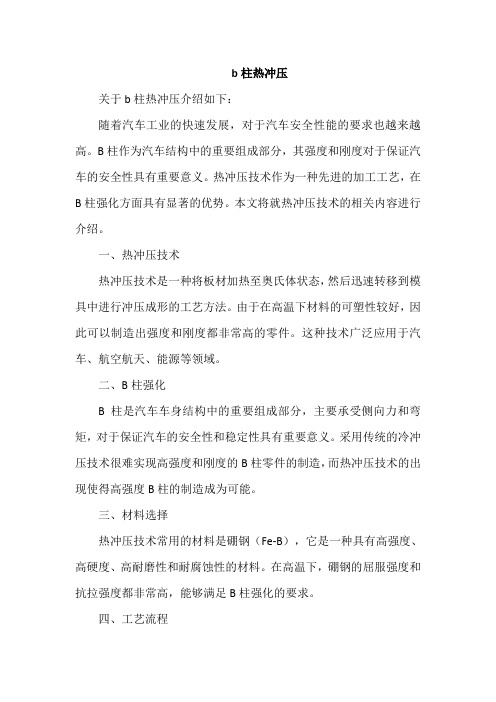
b柱热冲压关于b柱热冲压介绍如下:随着汽车工业的快速发展,对于汽车安全性能的要求也越来越高。
B柱作为汽车结构中的重要组成部分,其强度和刚度对于保证汽车的安全性具有重要意义。
热冲压技术作为一种先进的加工工艺,在B柱强化方面具有显著的优势。
本文将就热冲压技术的相关内容进行介绍。
一、热冲压技术热冲压技术是一种将板材加热至奥氏体状态,然后迅速转移到模具中进行冲压成形的工艺方法。
由于在高温下材料的可塑性较好,因此可以制造出强度和刚度都非常高的零件。
这种技术广泛应用于汽车、航空航天、能源等领域。
二、B柱强化B柱是汽车车身结构中的重要组成部分,主要承受侧向力和弯矩,对于保证汽车的安全性和稳定性具有重要意义。
采用传统的冷冲压技术很难实现高强度和刚度的B柱零件的制造,而热冲压技术的出现使得高强度B柱的制造成为可能。
三、材料选择热冲压技术常用的材料是硼钢(Fe-B),它是一种具有高强度、高硬度、高耐磨性和耐腐蚀性的材料。
在高温下,硼钢的屈服强度和抗拉强度都非常高,能够满足B柱强化的要求。
四、工艺流程热冲压技术的工艺流程主要包括以下几个步骤:1. 板材加热:将板材加热至奥氏体状态,提高其可塑性;2. 快速转移:将加热后的板材迅速转移到模具中;3. 冲压成形:在模具中进行冲压成形;4. 冷却淬火:将成形后的零件进行淬火处理,使其从奥氏体状态转变为马氏体状态,提高其强度和硬度;5. 后处理:对零件进行矫形、切割等后处理操作,使其满足设计要求。
五、模具设计热冲压技术的模具设计需要充分考虑温度、压力、材料等因素的影响,以保证零件的成形精度和加工效率。
模具材料一般选用耐高温、耐磨损、耐腐蚀的材料,如硬质合金、陶瓷等。
同时,模具设计还需要考虑冷却系统的设置,以保证淬火过程的顺利进行。
六、冲压温度与时间冲压温度和时间是热冲压技术的关键参数,它们直接影响零件的成形质量和加工效率。
在加热过程中,温度不宜过高或过低,以避免材料发生氧化或变形。
新时期热冲压成形技术的构建探究

新时期热冲压成形技术的构建探究一、热冲压成形技术的发展历程热冲压成形技术是一种在高温条件下进行金属成形的新型技术,其发展历程可以追溯至20世纪60年代。
最初,热压成形技术主要用于高温合金、钢铁等金属材料的成形加工,其主要目的是提高材料的塑性变形能力和成形质量。
随着材料科学和加工技术的不断进步,热冲压成形技术逐渐应用于航空航天、汽车制造、机械制造等领域,成为一种重要的金属成形加工技术。
1. 高温条件下的成形加工:热冲压成形技术的最大特点就是在高温条件下进行成形加工。
高温条件下,金属材料的塑性变形能力大大提高,可以实现更复杂、更精密的金属成形加工。
2. 提高产品质量和精度:热冲压成形技术能够有效改善产品的表面光洁度和成形精度,减少材料的内部缺陷和裂纹,提高产品的强度和耐磨性。
3. 节能环保:热冲压成形技术可以减少金属材料的消耗,减少能源消耗,降低生产成本,减少对环境的污染,是一种高效节能、环保的加工工艺。
4. 多工序一体化:热冲压成形技术可以实现多工序一体化成形加工,简化生产工艺,提高生产效率,降低生产成本。
1. 材料和工艺的相容性:热冲压成形技术要求金属材料在高温条件下具有良好的塑性变形能力和抗热疲劳性能,这对材料的研发和工艺的设计提出了挑战。
2. 设备和工艺的集成化:热冲压成形技术需要结合高温加热设备、成形模具和润滑冷却系统,实现设备和工艺的高效集成化,提高生产效率和产品质量。
3. 数据化智能化:随着智能制造的发展,热冲压成形技术需要实现数据化采集和监控,建立智能化控制系统,提高生产过程的稳定性和可控性。
1. 多材料复合成形:随着新材料的不断涌现,热冲压成形技术将会发展成为一种多材料复合成形技术,实现金属与非金属材料的复合成形。
2. 精密微成形:随着微电子、光电子等领域的发展,热冲压成形技术将会发展成为一种精密微成形技术,实现微米级甚至纳米级的成形加工。
3. 智能制造:随着智能制造的发展,热冲压成形技术将会实现智能化生产,利用大数据、人工智能等技术实现设备和工艺的自适应控制。
新时期热冲压成形技术的构建探究
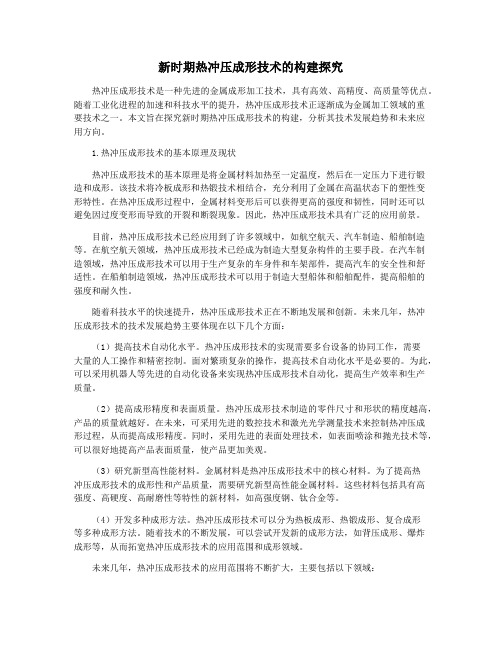
新时期热冲压成形技术的构建探究热冲压成形技术是一种先进的金属成形加工技术,具有高效、高精度、高质量等优点。
随着工业化进程的加速和科技水平的提升,热冲压成形技术正逐渐成为金属加工领域的重要技术之一。
本文旨在探究新时期热冲压成形技术的构建,分析其技术发展趋势和未来应用方向。
1.热冲压成形技术的基本原理及现状热冲压成形技术的基本原理是将金属材料加热至一定温度,然后在一定压力下进行锻造和成形。
该技术将冷板成形和热锻技术相结合,充分利用了金属在高温状态下的塑性变形特性。
在热冲压成形过程中,金属材料变形后可以获得更高的强度和韧性,同时还可以避免因过度变形而导致的开裂和断裂现象。
因此,热冲压成形技术具有广泛的应用前景。
目前,热冲压成形技术已经应用到了许多领域中,如航空航天、汽车制造、船舶制造等。
在航空航天领域,热冲压成形技术已经成为制造大型复杂构件的主要手段。
在汽车制造领域,热冲压成形技术可以用于生产复杂的车身件和车架部件,提高汽车的安全性和舒适性。
在船舶制造领域,热冲压成形技术可以用于制造大型船体和船舶配件,提高船舶的强度和耐久性。
随着科技水平的快速提升,热冲压成形技术正在不断地发展和创新。
未来几年,热冲压成形技术的技术发展趋势主要体现在以下几个方面:(1)提高技术自动化水平。
热冲压成形技术的实现需要多台设备的协同工作,需要大量的人工操作和精密控制。
面对繁琐复杂的操作,提高技术自动化水平是必要的。
为此,可以采用机器人等先进的自动化设备来实现热冲压成形技术自动化,提高生产效率和生产质量。
(2)提高成形精度和表面质量。
热冲压成形技术制造的零件尺寸和形状的精度越高,产品的质量就越好。
在未来,可采用先进的数控技术和激光光学测量技术来控制热冲压成形过程,从而提高成形精度。
同时,采用先进的表面处理技术,如表面喷涂和抛光技术等,可以很好地提高产品表面质量,使产品更加美观。
(3)研究新型高性能材料。
金属材料是热冲压成形技术中的核心材料。
热冲压设备介绍及与冷冲压的区别
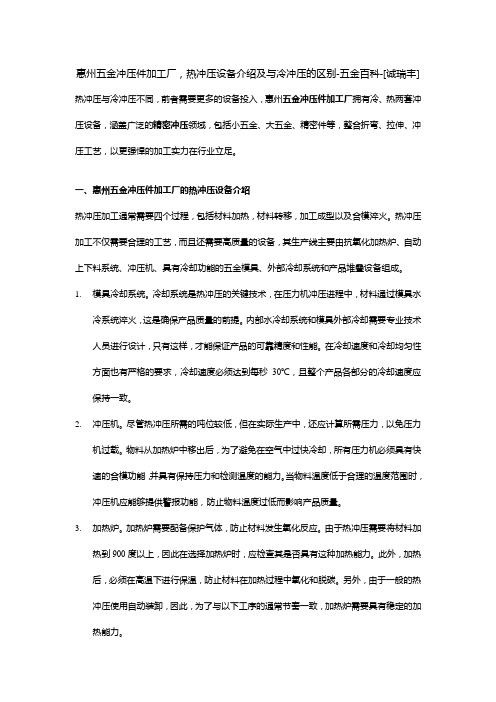
惠州五金冲压件加工厂,热冲压设备介绍及与冷冲压的区别-五金百科-[诚瑞丰]热冲压与冷冲压不同,前者需要更多的设备投入,惠州五金冲压件加工厂拥有冷、热两套冲压设备,涵盖广泛的精密冲压领域,包括小五金、大五金、精密件等,整合折弯、拉伸、冲压工艺,以更强悍的加工实力在行业立足。
一、惠州五金冲压件加工厂的热冲压设备介绍热冲压加工通常需要四个过程,包括材料加热,材料转移,加工成型以及合模淬火。
热冲压加工不仅需要合理的工艺,而且还需要高质量的设备,其生产线主要由抗氧化加热炉、自动上下料系统、冲压机、具有冷却功能的五金模具、外部冷却系统和产品堆叠设备组成。
1.模具冷却系统。
冷却系统是热冲压的关键技术,在压力机冲压进程中,材料通过模具水冷系统淬火,这是确保产品质量的前提。
内部水冷却系统和模具外部冷却需要专业技术人员进行设计,只有这样,才能保证产品的可靠精度和性能。
在冷却速度和冷却均匀性方面也有严格的要求,冷却速度必须达到每秒30℃,且整个产品各部分的冷却速度应保持一致。
2.冲压机。
尽管热冲压所需的吨位较低,但在实际生产中,还应计算所需压力,以免压力机过载。
物料从加热炉中移出后,为了避免在空气中过快冷却,所有压力机必须具有快速的合模功能,并具有保持压力和检测温度的能力。
当物料温度低于合理的温度范围时,冲压机应能够提供警报功能,防止物料温度过低而影响产品质量。
3.加热炉。
加热炉需要配备保护气体,防止材料发生氧化反应。
由于热冲压需要将材料加热到900度以上,因此在选择加热炉时,应检查其是否具有这种加热能力。
此外,加热后,必须在高温下进行保温,防止材料在加热过程中氧化和脱碳。
另外,由于一般的热冲压使用自动装卸,因此,为了与以下工序的通常节奏一致,加热炉需要具有稳定的加热能力。
二、惠州五金冲压件加工厂为您介绍热冲压与冷冲压的区别热冲压技术在冲压加工领域,特别是高强度钢板的冲压加工中的应用正变得越来越普遍。
热冲压具有许多优势,而冷冲压无法替代这些优势。
冲压新工艺(3篇)

第1篇随着我国制造业的快速发展,冲压工艺在汽车、家电、电子等行业中的应用越来越广泛。
传统的冲压工艺在满足产品性能和品质要求的同时,也存在一定的局限性,如能耗高、生产效率低、产品精度不足等。
为了推动制造业高质量发展,提升我国制造业的竞争力,冲压新工艺应运而生。
本文将从冲压新工艺的背景、关键技术、应用领域及发展趋势等方面进行探讨。
一、冲压新工艺的背景1. 传统冲压工艺的局限性传统冲压工艺主要依靠人力操作,设备较为简单,生产效率低,能耗高,且产品精度和一致性难以保证。
随着市场竞争的加剧,传统冲压工艺已无法满足现代制造业的需求。
2. 制造业高质量发展的需求为了提升我国制造业的竞争力,实现高质量发展,迫切需要提高生产效率、降低能耗、提高产品精度和一致性。
冲压新工艺的出现,为制造业提供了新的解决方案。
二、冲压新工艺的关键技术1. 智能化控制系统智能化控制系统是冲压新工艺的核心技术之一,通过引入PLC、工控机等智能设备,实现冲压过程的自动化、智能化。
智能化控制系统具有以下特点:(1)实时监控:对冲压过程中的各项参数进行实时监控,确保生产过程的稳定性和安全性。
(2)故障诊断:对设备故障进行实时诊断,提高设备运行效率。
(3)工艺优化:根据实际生产情况,优化工艺参数,提高产品精度和一致性。
2. 高精度模具技术高精度模具是冲压新工艺的关键,通过采用CNC加工、电火花加工等先进加工技术,实现模具的高精度制造。
高精度模具具有以下特点:(1)精度高:满足产品尺寸精度和形状精度要求。
(2)耐磨性:延长模具使用寿命。
(3)一致性:提高产品的一致性。
3. 精密检测技术精密检测技术在冲压新工艺中扮演着重要角色,通过引入高精度测量设备,如三坐标测量机、光学投影仪等,对产品进行全方位检测,确保产品质量。
精密检测技术具有以下特点:(1)高精度:满足产品精度要求。
(2)高效:提高检测效率。
(3)自动化:实现检测过程的自动化。
4. 绿色环保技术绿色环保技术是冲压新工艺的重要组成部分,通过优化工艺流程、降低能耗、减少废弃物排放,实现生产过程的绿色环保。
热冲压成形中的先进加热技术及设备

热冲压成形中的先进加热技术及设备摘要:热冲压成形技术是汽车工业中常用的零部件加工技术,通过热冲压制造的成形件具有强度高、质量轻等特点。
由此可见,热冲压成形技术可以很好的满足新时期汽车工业对材料轻量化、高强度的技术要求,具有非常广阔的应用前景。
关键词:热冲压成形;加热技术;设备前言热冲压成形技术是一种常见的零件加工方式,尤其在汽车工业中应用最为普遍。
将材料先加热至奥氏体化状态,该状态下钢板材料的塑性较好,强度低,并且具有一定的韧性,然后使用冲压机在模具中进行冲压并淬火,获得相应形状的高强度金属零件。
通过热冲压成形技术获取高强度的冲压件来代替传统的厚钢板,不但可以有效降低零部件自身的重量,而且能大幅度地提升抗拉强度。
1热冲压技术原理热冲压技术是一种将钢板材料加热至奥氏体形态下,快速进行冲压成形,并且通过模具对零件进行淬火冷却,获得强度为1500MPa左右的马氏体成形件。
可以说热冲压技术是将钢板材料由奥氏体向马氏体转化的过程。
奥氏体(Austenite)是钢铁的一种层片状的显微组织,该状态下的钢板材料ɣ-Fe中固溶少量碳的无磁性固溶体,因此也称为沃斯田铁或者ɣ-Fe。
马氏体(Martensite)是黑色金属材料的一种组织名称,是碳在α-Fe中的过饱和固溶体。
马氏体和奥氏体的不同在于,马氏体是体心正方结构,奥氏体是面心立方结构。
奥氏体向马氏体转变仅需很少的能量,因为这种转变是无扩散位移型的,仅仅是迅速和微小的原子重排。
马氏体的密度低于奥氏体,所以转变后体积会膨胀。
相对于转变带来的体积改变,这种变化引起的切应力、拉应力更需要重视。
热冲压成形技术可以分直接冲压和间接冲压两种形式,其中直接冲压是将钢板材料加热至奥氏体后,直接传送至模具上冲压,模具表面有冷却通道,可以在钢板材料冲压的过程中进行淬火冷却,获得马氏体成形件。
间接冲压则是钢板材料先进行冷冲压,然后再加热成奥氏体进行淬火和校准,确保成形材料强度达到1500MPa的马氏体。
钢板热冲压新技术介绍

钢板热冲压新技术介绍一、本文概述随着汽车工业的快速发展,对汽车零部件的性能要求日益提高,特别是在安全性、轻量化和节能减排方面。
钢板热冲压技术作为一种先进的金属成形工艺,以其独特的优势在这些领域发挥着重要作用。
本文旨在全面介绍钢板热冲压新技术,包括其基本原理、工艺流程、设备配置、材料选择以及应用领域等方面的内容。
通过深入了解钢板热冲压新技术,可以为汽车工业及其他相关领域的技术进步和创新发展提供有益的参考和借鉴。
二、传统钢板热冲压技术概述传统钢板热冲压技术,也被称为热成形或热压成形,是一种广泛应用于汽车制造业的金属成形工艺。
该技术主要利用高温下金属材料的良好塑性,通过在红热状态下对钢板进行冲压,以实现复杂形状和高强度构件的制造。
在传统的钢板热冲压过程中,钢板首先被加热到奥氏体相变温度以上,使其具备足够的塑性。
随后,在高温条件下,钢板被迅速转移到冲压模具中,利用模具的压力和形状,使钢板发生塑性变形,从而得到所需的形状和尺寸。
完成冲压后,零件通过淬火和回火等热处理工艺,获得高强度和高硬度的马氏体组织。
传统钢板热冲压技术的优点在于能够制造出高强度、高刚度的复杂形状零件,这些零件在汽车工业中广泛应用于车身结构、底盘部件以及安全系统等关键部位。
该技术还能够实现零件的轻量化,降低整车的能耗和排放。
然而,传统钢板热冲压技术也存在一些局限性。
高温操作对设备和模具的材料要求较高,增加了制造成本。
热冲压过程中需要精确控制加热温度、冲压速度和冷却速率等参数,以确保零件的质量和性能。
由于热冲压过程中金属材料的流动性和成形性受温度影响较大,因此对于一些形状复杂或尺寸精度要求较高的零件,制造难度较大。
随着科技的不断进步和汽车工业的发展,传统钢板热冲压技术也在不断创新和完善。
目前,研究人员正致力于探索新型加热方式、优化冲压工艺参数以及开发高性能的模具材料等方面的工作,以期进一步提高热冲压技术的成形精度、生产效率和经济效益。
三、钢板热冲压新技术介绍随着现代工业的快速发展,钢板热冲压技术作为一种先进的金属成型工艺,正日益受到业界的广泛关注和应用。
钢板热冲压新技术关键装备和核心技术

世 界 钢 铁2009年第2期轧钢钢板热冲压新技术关键装备和核心技术徐伟力1,管曙荣2,艾 健1,罗爱辉1(1.宝山钢铁股份有限公司,上海 201900;2.宝钢金属有限公司,上海 200120)摘要:钢板热冲压是一种将先进高强度钢板加热到奥氏体温度后快速冲压,在保压阶段通过模具实现淬火并达到所需冷却速度,从而得到组织为马氏体,强度在1500MPa左右的超高强度零件的新型成形技术。
对钢板热冲压新技术的关键装备、核心技术和优缺点做了系统介绍,并指出了其使用现状和前景。
关键词:热冲压;冷却;淬火0 前言随着国家汽车正碰、侧碰、排放等强制法规的相继推出,汽车车身钢铁用材正面临日益严峻的挑战,采用先进高强钢,如DP钢、T R I P钢、高扩孔钢等也无可争议地成为汽车用材的主流趋势。
通过车身零件减薄和高强的合理匹配,不仅可以有效减轻车身重量,降低油耗,而且可以确保和提高车型的安全性和舒适性。
但对冲压成形工艺而言,减薄和高强是恶化成形性的双重因素,不仅使得车身零件在成形过程中容易开裂,而且容易产生过量回弹,影响车身后续的装配。
另外,减薄和高强对车身零件本身的使用性能,特别是刚度特性会产生不利影响。
对于强度超过1000MPa的高强钢,传统冲压工艺往往是束手无策。
一种新型的成形工艺,特殊高强度钢板的热冲压技术应运而生。
钢板热冲压是另一种获得超高强度冲压件的有效途径,是最近二十多年发展和应用起来的一种新技术。
这种新技术最先由瑞典的Hard Tech公司于20世纪80年代提出,经过二十多年的发展,成功实现产业化批量应用。
这种钢板热冲压新技术和传统意义上的热冲压技术的本质区别在于其不是通过空冷,而是通过布置冷却回路,并通冷却水的模具对零件实现快速淬火冷却,然后得到1500MPa左右甚至更高强度的冲压件。
这种超高强度的冲压件,无论是冷冲压工艺,还是传统意义上的热冲压工艺,都无法实现。
在传统热冲压领域,无论是装备还是核心技术方面,公开发表的文章相对较多,国内也有较多文献报道[1-3]。
热冲压成形零件生产工艺与控制

热冲压成形零件生产工艺与控制摘要:高强度、超高强度钢的应用是制造业节能减排的有效手段。
高强度钢的应用带来模具磨损、工件回弹、成形困难等诸多问题。
热冲压成形应运而生。
热冲压成形是获得高性能安全件的一个有效的工艺技术。
关键词:热冲压成形零件;生产工艺控制;前言:热冲压成形(HotForming)是将初始硬度为500~600MPa 的硼钢板加热至奥氏体化状态,快速转移至模具中高速冲压成形,在保证一定压力情况下,制件在模具本体中以大于27℃/s 的冷却速度进行淬火处理,保压淬火一段时间,以获得具有均匀马氏体组织的超高强度钢零件的成形方法。
热冲压成形技术可以得到超高强度的车身零件,改善冲压成形性,提高零件尺寸精度等优点。
一、热冲压成形工艺特性在成形工序上,热冲压同冷冲压并无较大差别,但由于温度、相变和接触等的影响,材料又具有区别于冷冲压的特征。
( 1) 高温板料( 600 ~850 ℃) 变形抗力低,流动性能好,塑性变形能力大幅提升。
( 2) 板料经历塑性变形的同时发生马氏体相变强化。
室温下为铁素体/珠光体混合组织,抗拉强度400 ~600 MPa; 热冲压后,其组织转变为完全马氏体,抗拉强度提升到1500 MPa 左右。
( 3) 摩擦系数增大。
热变形条件下,受温度的影响,硼钢板的强度、硬度降低,且板料与模具接触表面之间分子吸附能力增强; 同时,高温时润滑剂的性能变坏,因而摩擦系数增大,并高达0. 5。
( 4) 接触条件对成形的影响作用显著提升。
板料与模具的接触时序和接触状态差异将导致板料温度梯度的产生,不仅影响其淬火相变,还会引起流动性能变化。
( 5) 裸板在高温下成形,与空气接触后产生氧化,零件表面质量不佳; 镀层板在拉应力作用下则会产生镀层开裂,防氧化能力降低。
二、热冲压成形零件生产工艺与控制1.热冲压件翻边工艺设计。
冲压热成形零件设计中,应该尽量避免圆角翻边造型,目前的热冲压工艺中,进行圆孔翻边比较难以达到技术要求的产品精度,并且,很难将坯料优化到可以翻孔的位置,并且翻边后难以做激光切割。
浅谈热冲压成形技术
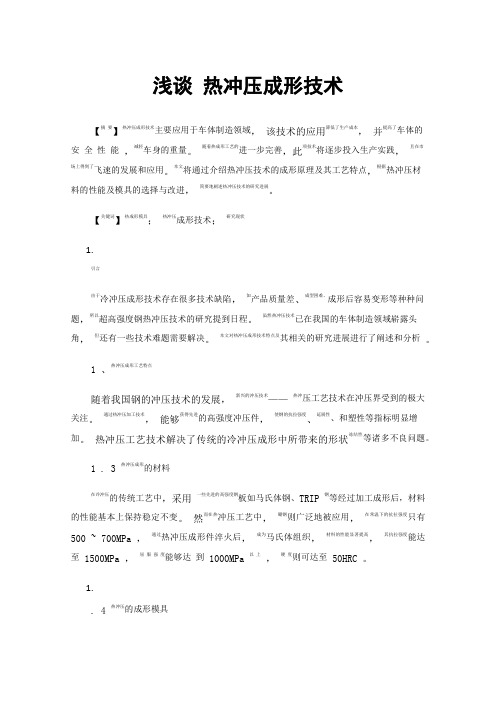
浅谈热冲压成形技术【摘要】热冲压成形技术主要应用于车体制造领域,该技术的应用降低了生产成本,并提高了车体的安全性能,减轻车身的重量。
随着热成形工艺的进一步完善,此项技术将逐步投入生产实践,且在市场上得到了飞速的发展和应用。
本文将通过介绍热冲压技术的成形原理及其工艺特点,根据热冲压材料的性能及模具的选择与改进,简要地阐述热冲压技术的研究进展。
【关键词】热成形模具;热冲压成形技术;研究现状1.引言由于冷冲压成形技术存在很多技术缺陷,如产品质量差、成型困难、成形后容易变形等种种问题,所以超高强度钢热冲压技术的研究提到日程。
虽然热冲压技术已在我国的车体制造领域崭露头角,但还有一些技术难题需要解决。
本文对热冲压成形技术特点及其相关的研究进展进行了阐述和分析。
1 、热冲压成形工艺特点随着我国钢的冲压技术的发展,新兴的冲压技术——热冲压工艺技术在冲压界受到的极大关注。
通过热冲压加工技术,能够获得先进的高强度冲压件,使钢的抗拉强度、延展性、和塑性等指标明显增加。
热冲压工艺技术解决了传统的冷冲压成形中所带来的形状冻结性等诸多不良问题。
1 . 3 热冲压成形的材料在冷冲压的传统工艺中,采用一些先进的高强度钢板如马氏体钢、TRIP 钢等经过加工成形后,材料的性能基本上保持稳定不变。
然而在热冲压工艺中,硼钢则广泛地被应用,在常温下的抗拉强度只有500 ~ 700MPa ,通过热冲压成形件淬火后,成为马氏体组织,材料的性能显著提高,其抗拉强度能达至 1500MPa ,屈服强度能够达到 1000MPa 以上,硬度则可达至 50HRC 。
1.. 4 热冲压的成形模具在传统的冷冲压成形技术中,模具只是用于零件的成形,冲压前后的机械强度不会发生显著差别。
但在热冲压的工艺中,模具需要成形、淬火等技术工艺,工序复杂,零件的强度高,综合性能很好。
热冲压模具的材料在成形和冷却淬火的技术中需要实现快速且均匀冷却还要有快速传热、冷却的功能。
汽车钣金热冲压技术详解

内容
1. 热冲压工艺流程及其典型应用 2. 热冲压钢板 3. 热冲压设备 4. 热冲压钢板加热方式 5. 热冲压优缺点分析 6. 热冲压零件的检测技术 7. 热冲压技术成本分析
2、热冲压钢板
从成分分为:
Mn-B系
宝钢热冲压用钢
Mn-Mo-B系 北美、欧洲等的热冲压用钢
Mn-Cr-B系 高淬透性的热冲压用钢
Roof-bows
Bumper Armatures Front & Rear
A Pillar Reinforcements
2 Piece A Pillar Reinforcements Side Impact Beams and Waste Reinforcements
钢管热冲压 典型应用
1.2 钢管热冲压
快速移到压机
快速合模、成形,保压冷 却到100-2000C。组织全 部为马氏体
抗拉强度为400 -600Mpa左右 的BORON钢板
随室温冷却, 激光(模具) 切边、冲孔
得到抗拉强度为 1500Mpa左右的零件
若采用裸板则进行喷丸处 理以去除零件表面氧化皮
1、热冲压工艺流程及其典型应用
Time in the tool
2、热冲压钢板
镀层钢板热冲压:
➢ 加热、冲压过程中无氧化皮 ➢ 无需喷丸处理 ➢ 成本高 ➢ 零件储存过程不生锈 ➢ 零件耐腐蚀性能好 ➢ 加热过程中镀层易和陶瓷辊粘结
非镀层钢板热冲压:
➢ 加热、冲压过程中有氧化皮 ➢ 需喷丸处理 ➢ 成本低 ➢ 零件储存过程易生锈 ➢ 零件耐腐蚀性能稍差 ➢ 焊接性好
USIBOR1500介绍:
2、热冲压钢板
Aluminium (90%) and Silicon铝(90%)和硅
热冲压关键技术
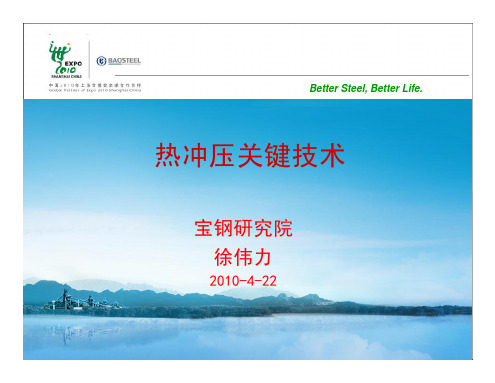
② 加热炉
3、热冲压装备技术
② 加热炉
3、热冲压装备技术
② 加热炉
3、热冲压装备技术
② 加热炉
3、热冲压装备技术
② 加热炉
3、热冲压装备技术
② 加热炉
3、热冲压装备技术
② 加热炉
3、热冲压装备技术
② 加热炉
3、热冲压装备技术
② 加热炉
3、热冲压装备技术
② 加热炉
3、热冲压装备技术
2、热冲压零件检测技术
便携式三坐标测量仪
测量范围3700mm,测量精度0.073mm
METROCON精密台式三坐标测量仪
范围2500*800*900
拉伸试验机
硬度计
高速拉伸试验机
2、热冲压零件检测技术
热冲压零件的实物性能检测
2、热冲压零件检测技术
2、热冲压零件检测技术
内容
1. 2. 3. 4. 5. 6. 7. 热冲压零件/小总成协同设计 热冲压零件检测技术 热冲压装备技术 热冲压样模制作及样件试制 热冲压模具设计 热冲压模具制造和调试 热冲压零件的激光切割、喷丸及防锈处理
5、热冲压模具设计
8. 热冲压零件焊接工艺参数的优化 9. 尚需攻克的技术难点
3、热冲压装备技术
① ② ③ ④ ⑤ ⑥ ⑦ ⑧
拆跺系统&打标站 加热炉 上料自动化设备 压机(高温测量仪) 下料自动化设备 零件堆跺系统 外部冷却系统 整线控制
3、热冲压装备技术
① 拆跺系统&打标站
3、热冲压装备技术
① 拆跺系统&打标站
CAE仿真分析、成形性评估和外形改进
热冲压CAE分析与试冲结果对比
零件外形优化
1、热冲压零件/小总成协同设计
热冲压工艺流程注意点
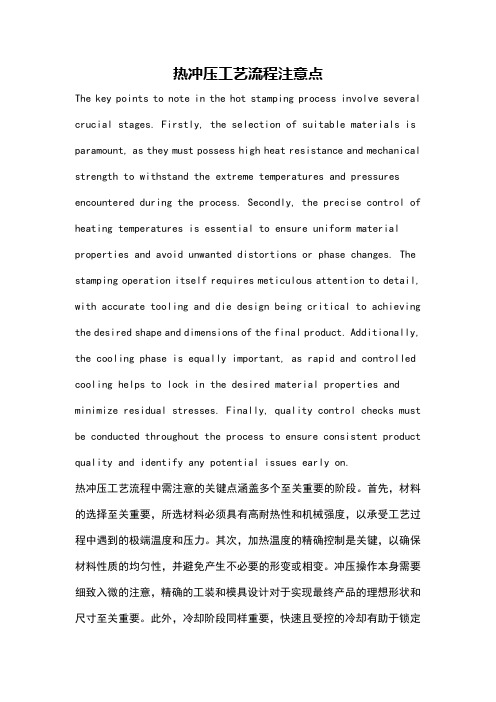
热冲压工艺流程注意点The key points to note in the hot stamping process involve several crucial stages. Firstly, the selection of suitable materials is paramount, as they must possess high heat resistance and mechanical strength to withstand the extreme temperatures and pressures encountered during the process. Secondly, the precise control of heating temperatures is essential to ensure uniform material properties and avoid unwanted distortions or phase changes. The stamping operation itself requires meticulous attention to detail, with accurate tooling and die design being critical to achieving the desired shape and dimensions of the final product. Additionally, the cooling phase is equally important, as rapid and controlled cooling helps to lock in the desired material properties and minimize residual stresses. Finally, quality control checks must be conducted throughout the process to ensure consistent product quality and identify any potential issues early on.热冲压工艺流程中需注意的关键点涵盖多个至关重要的阶段。
热冲压生产线关键技术探讨

热冲压生产线关键技术探讨
林平
【期刊名称】《金属加工:热加工》
【年(卷),期】2015(0)15
【摘要】热冲压生产线的关键技术,是围绕如何提升热冲压成形零件的生产效率和降低制造成本,从而提高企业的竞争力来展开,这些技术是相互支持和相互促进的,缺一不可。
大部分热冲压生产线的配置包括开卷落料系统、加热炉系统、热冲压压力机、激光切割机、喷丸处理系统等,工序长,制造成本高,因此如何提升生产效率,降低制造成本,成为热冲压生产线的关键技术。
【总页数】2页(P9-10)
【作者】林平
【作者单位】东风模具冲压技术有限公司热冲压成形技术研究室
【正文语种】中文
【相关文献】
1.180 t/d杨木P-RC APMP生产线运行关键技术探讨
2.180t/d杨木P-RC APMP生产线运行关键技术探讨
3.特殊物料包装生产线发展趋势及关键技术探讨
4.陈腐垃圾分选处理生产线关键技术探讨
5.陈腐垃圾分选处理生产线关键技术探讨
因版权原因,仅展示原文概要,查看原文内容请购买。
- 1、下载文档前请自行甄别文档内容的完整性,平台不提供额外的编辑、内容补充、找答案等附加服务。
- 2、"仅部分预览"的文档,不可在线预览部分如存在完整性等问题,可反馈申请退款(可完整预览的文档不适用该条件!)。
- 3、如文档侵犯您的权益,请联系客服反馈,我们会尽快为您处理(人工客服工作时间:9:00-18:30)。
④
4、热冲压样模制作及样件试制
宝钢为国内汽车厂制作的12个热冲压样件
4、热冲压样模制作及样件试制
B柱
前纵梁
A柱
前保
上边板
零 件
模 具
宝钢为国内汽车厂制作热冲压样模和样件
内容
1. 热冲压零件/小总成协同设计 2. 3. 4. 5. 6. 7. 8. 9. 热冲压零件检测技术 热冲压装备技术 热冲压样模制作及样件试制 热冲压模具设计 热冲压模具制造和调试 热冲压零件的激光切割、喷丸及防锈处理 热冲压零件焊接工艺参数的优化 尚需攻克的技术难点
8. 热冲压零件焊接工艺参数的优化 9. 尚需攻克的技术难点
3、热冲压装备技术
① ② ③ ④ ⑤ ⑥ ⑦ ⑧
拆跺系统&打标站 加热炉 上料自动化设备 压机(高温测量仪) 下料自动化设备 零件堆跺系统 外部冷却系统 整线控制
3、热冲压装备技术
① 拆跺系统&打标站
3、热冲压装备技术
① 拆跺系统&打标站
8. 热冲压零件焊接工艺参数的优化 9. 尚需攻克的技术难点
4、热冲压样模制作及样件试制
ü 样模制作、样件试制是复杂车身零件热冲压量产模设计的
必经环节;
ü 样件制作、装配和整车试验是整车厂验证热冲压零件使用
性能的必经环节;
4、热冲压样模制作及样件试制
热冲压样模制作和样件试制流程
4、热冲压样模制作及样件试制
热冲压零件协同设计-关键要素
关键技术参数输入 热冲压条件下的热冲压条件下的成形极限
目前业内更多地是采用减薄率 分析热冲压成形性!
1、热冲压零件/小总成协同设计
热冲压零件协同设计-关键要素
关键技术参数输入 不同温度、不同应变速度下的应变曲线
1、热冲压零件/小总成协同设计
热冲压零件协同设计-关键要素
1、热冲压零件/小总成协同设计
热冲压零件协同设计-关键要素
热冲压分析模型建立
1、热冲压零件/小总成协同设计
热冲压零件协同设计-关键要素
关键技术参数输入 热冲压条件下的摩擦系数
1、热冲压零件/小总成协同设计
热冲压零件协同设计-关键要素
关键技术参数输入 热冲压条件下的热冲压条件下的成形极限
1、热冲压零件/小总成协同设计
热冲压零件协同设计-关键要素
关键技术参数输入 热冲压条件下的热冲压条件下的成形极限
镁合金的拉深试样(400度)
镁合金的FLD试样(300度)
1、热冲压零件/小总成协同设计
热冲压零件协同设计-关键要素
关键技术参数输入 热冲压条件下的热冲压条件下的成形极限
铝镁合金的FLD试样及其曲线(400度)
1、热冲压零件/小总成协同设计
CAE仿真分析、成形性评估和外形改进
热冲压CAE分析与试冲结果对比
零件外形优化
1、热冲压零件/小总成协同设计
热冲压零件协同设计-若干案例
凸台高度降低10mm
1、热冲压零件/小总成协同设计
热冲压零件协同设计-若干案例
1、热冲压零件/小总成协同设计
热冲压小总成协同设计
优化碰撞建技术 采用更好的假人模型 系统研究热冲压零件的合理选用及其相关零件的高强化方案 达到最佳的整车性能
4、热冲压样模制作及样件试制
4、热冲压样模制作及样件试制
热冲压样模制作和样件试制关键技术
① ② ③ ④ ⑤ ⑥ ⑦ ⑧ ⑨ ⑩
样模型面设计; 起皱缺陷的应对措施; 加热工艺的优化(加热温度、保温时间)及其环境温度的敏感性; 钢板传输方式 冲压速度; 冷却方式; 保压力; 保压时间; 激光切割工艺优化; 喷丸工艺优化。
3、热冲压装备技术
① 拆跺系统&打标站
3、热冲压装备技术
① 拆跺系统&打标站
3、热冲压装备技术
① 拆跺系统&打标站
3、热冲压装备技术
① 拆跺系统&打标站
FUNCTIONS
• Safe separation of blanks/profiles • Pre-centering • ID marking / Punching • Continuous operation • Automatic ejection of double blanks
3、热冲压装备技术 <高速机械手 <机器人
③ 上料自动化设备
3、热冲压装备技术
③ 上料自动化设备
Press Robot CD40/60/120
3、热冲压装备技术
③ 上料自动化设备
采用快速机械手的优点:
(1)快速上料,2秒左右(用机器人上料一般需要5秒) (2)冲压前温度损失少; (3)氧化皮少。
1、热冲压零件/小总成协同设计
宝钢每年要承担数个车型数十个热冲压零件的CAE分析,涵盖了所有典 型热冲压零件,至今已经完成200多个零件的热冲压CAE分析。具备较强 的热冲压零件/小总成的协同设计能力。
内容
1. 热冲压零件/小总成协同设计 2. 3. 4. 5. 6. 7. 8. 9. 热冲压零件检测技术 热冲压装备技术 热冲压样模制作及样件试制 热冲压模具设计 热冲压模具制造和调试 热冲压零件的激光切割、喷丸及防锈处理 热冲压零件焊接工艺参数的优化 尚需攻克的技术难点
1、热冲压零件/小总成协同设计
热冲压零件协同设计-关键要素
热冲压模具型面设计
不同于一般冷冲压模具型面设计: (1)一般不设置拉延筋; (2)尽量不采用压边圈
1、热冲压零件/小总成协同设计
热冲压零件协同设计-关键要素
热冲压模具型面设计
1、热冲压零件/小总成协同设计
热冲压零件协同设计-关键要素
热冲压模具型面设计
② 加热炉
3、热冲压装备技术
② 加热炉
3、热冲压装备技术
② 加热炉
3、热冲压装备技术
② 加热炉
3、热冲压装备技术
② 加热炉
3、热冲压装备技术
② 加热炉
3、热冲压装备技术
② 加热炉
3、热冲压装备技术
② 加热炉
3、热冲压装备技术
② 加热炉
3、热冲压装备技术
② 加热炉
3、热冲压装备技术
Typical heating time, 2mm steel material
1000 900 800 700 600 °C 500 400 300 200 100 0 0 50 100 150 200 250 300 350 400 450
sec.
500
3、热冲压装备技术
② 加热炉
3、热冲压装备技术
② 加热炉
3、热冲压装备技术
② 加热炉
3、热冲压装备技术
② 加热炉
3、热冲压装备技术
② 加热炉
3、热冲压装备技术
② 加热炉
3、热冲压装备技术
② 加热炉
3、热冲压装备技术
② 加热炉
3、热冲压装备技术
② 加热炉
3、热冲压装备技术
② 加热炉
3、热冲压装备技术
② 加热炉
3、热冲压装备技术
4、热冲压样模制作及样件试制
宝钢热冲压样模制作和样件试制的优势
① ② ③ 掌握了热冲压样模设计、样件制作关键技术; 可以在3个月左右时间提供合格样件,供新车型装车、试验使用; 已经完成4款车型共12个零件的样模设计、制造和样件制作; 样件的尺寸精度和力学性能都达到行业先进水平:
ü ① ü 首次样件装配面90%以上符合+-0.5mm的尺寸公差要求; 样件屈服强度在1000Mpa以上,抗拉强度在1400Mpa以上,延伸率(80标距) 在5%以上; 均表现在优秀的碰撞成绩。
模具的快速定位
3、热冲压装备技术
④ 压机
发展趋势:
(1)大台面、多工位; (2)压力可控。
3、热冲压装备技术
⑤ 下料自动化设备
<高速机械手; <机器人
3、热冲压装备技术
⑥ 零件堆垛系统
3、热冲压装备技术
⑦ 外部冷却系统
功能:
提供循环冷却水,冷却压机和模具;
关键要素:
(1)使用纯水; (2)添加防锈剂; (3)最好配有蓄水池
② 加热炉
3、热冲压装备技术
② 加热炉
3、热冲压装备技术
② 加热炉
3、热冲压装备技术
② 加热炉
3、热冲压装备技术
② 加热炉
3、热冲压装备技术
② 加热炉
3、热冲压装备技术
② 加热炉
3、热冲压装备技术
② 加热炉
3、热冲压装备技术
② 加热炉
核心要素: (1)如何有效节省能耗-低碳、降成本; (2)高效的自动化控制-降低废品率; (3)断电保护。
3、热冲压装备技术
④ 压机
3、热冲压装备技术
④ 压机
采用蓄力器来提高冲压速度
3、热冲压装备技术
④ 压机
3、热冲压装备技术
④ 压机
温度检测
3、热冲压装备技术
④ 压机
• Minimum of leakage • Efficient oil cleaning and cooling system • Hydraulic unit away from furnace Oil collection slot is integrated in the tank unit
采用快速机械手的缺点:
价格相对贵。
3、热冲压装备技术
③ 上料自动化设备
上料夹持器(Grippers)
3、热冲压装备技术
③ 上料自动化设备
上料夹持器(Grippers)
配置气刀以在冲压之前清除模具上的氧化皮!
3、热冲压装备技术
④ 压机
3、热冲压装备技术
④ 压机