八大浪费与改善
八大浪费产生的根源分析与改善措施

八大浪费产生的根源分析与改善措施八大浪费是指制造业中的致命浪费,包括过度生产、库存过多、运输过程中的速度缓慢、过度加工、等待、运输、不良品、人员的潜力不被充分利用。
以下是对八大浪费产生的根源进行分析,并提出相应的改善措施。
1.过度生产:过度生产是由于不准确的预测和计划导致的。
解决这个问题的关键是准确地预测市场需求和对现有供应链进行合理的规划。
建立准确的市场调研机制,与供应商和合作伙伴建立合理的合作关系,及时更新生产计划,确保生产量与需求相匹配。
2.库存过多:库存过多通常是由于生产过剩或者生产进度延误导致的。
解决库存过多的问题可以采取以下措施:优化供应链,减少生产延误;建立正确的库存控制策略,及时对库存进行监控与调整;加强与供应商的沟通,避免因供应链断裂导致的库存积压。
3.运输过程中的速度缓慢:运输过程中的速度缓慢通常是由于交通拥堵、交通规划不合理等原因导致的。
解决这个问题可以优化运输路线,减少拥堵情况;提前做好运输规划,合理安排出发时间和路线;采用先进的运输工具和技术,提高运输效率。
4.过度加工:过度加工通常是由于制造过程中存在着重复工序、不必要的加工等原因导致的。
解决过度加工问题可以进行价值流图分析,剔除不必要的工序;优化生产流程,减少重复加工;加强人员培训,提高工人对产品要求的理解。
5.等待:等待通常是由于制造过程中出现了生产线不平衡、原材料不足等问题导致的。
解决等待问题可以通过平衡生产线,减少生产环节之间的等待时间;建立完善的物料管理和供应链管理体系,确保原材料及时供应。
6.运输:运输过程中的不必要运输是造成时间和成本浪费的一个主要原因。
解决运输问题可以采取集中运输、合理安排运输路线和运输工具,减少不必要的运输环节;提高物流管理水平,优化物流流程,提高运输效率。
7.不良品:不良品是由于制造过程中出现质量问题导致的。
解决不良品问题可以通过加强质量管理,提高生产过程中的质量控制;加强员工培训,提高员工对产品质量的重视;完善检测机制,及时发现并解决质量问题。
八大浪费及改善技法

八大浪费及改善技法浪费是一种非常常见的现象,它指的是资源、时间、能源等被不合理或无效地使用的情况。
在我们的生活中,浪费无处不在,因此我们应该采取措施,减少浪费,提高资源利用效率。
以下是八大浪费及改善技法。
1.过度生产:过度生产是指制造过多的产品,超出市场的需求。
这导致了大量的资源、时间和能源的浪费。
为了解决这个问题,我们需要建立更好的市场研究机制,预测和满足消费者的需求。
2. 库存浪费:库存浪费指的是存储过多的货物或材料,导致它们长时间闲置,无法产生价值。
减少库存浪费的方法包括实施“精益生产”理念,以及与供应商建立更紧密的合作关系,实现Just-In-Time生产。
3.运输浪费:货物的长途运输会导致大量的能源和时间的浪费。
为了降低运输浪费,我们可以采取的措施包括优化运输路线、提高运输工具的效率和使用可再生能源等。
4.劳动力浪费:劳动力浪费是指员工的能力和时间的浪费。
为了减少劳动力浪费,我们可以通过改善员工的培训和提升技能,提高劳动力的生产效率。
此外,我们还可以优化工作流程,减少不必要的环节和重复的工作。
5.等待浪费:等待浪费是指在生产线上因为等待而导致的生产过程停滞。
为了减少等待浪费,我们可以采取的措施包括优化生产排程,提高设备的利用率,以及改进协调和沟通等。
6.不合理的工艺流程:不合理的工艺流程会导致生产效率低下和资源的浪费。
通过优化工艺流程,我们可以减少浪费。
这包括简化工艺流程,采用自动化和智能化的技术,以及减少不必要的步骤和行动等。
7.缺乏能源效率:能源是我们生产和生活中不可或缺的资源,但我们常常浪费能源。
为了提高能源效率,我们可以采取节能措施,如使用更高效的设备和技术,改变不合理的用电习惯。
8.舍弃浪费:舍弃浪费是指扔掉可以得到价值的废弃物。
为了减少舍弃浪费,我们应该实施垃圾分类和再循环利用的措施,例如回收废纸、塑料和玻璃等,减少资源的消耗。
在改善这八大浪费的过程中,我们应该意识到浪费是一种不可持续的行为,会给我们的环境和社会造成负面影响。
八大浪费5条建议
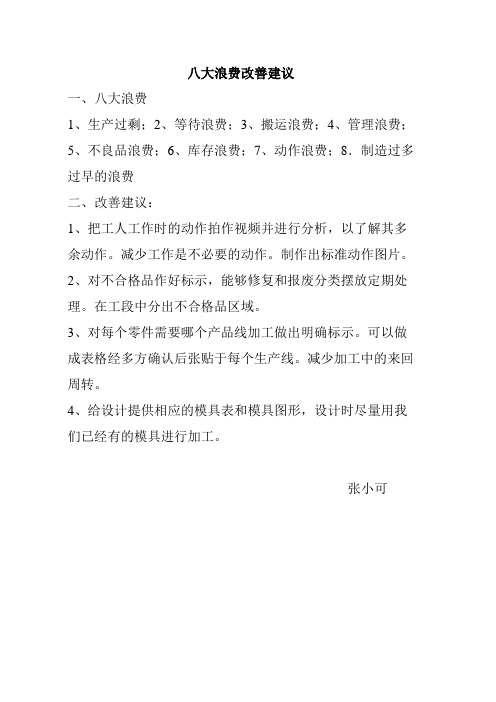
八大浪费改善建议
一、八大浪费
1、生产过剩;
2、等待浪费;
3、搬运浪费;
4、管理浪费;
5、不良品浪费;
6、库存浪费;
7、动作浪费;8.制造过多过早的浪费
二、改善建议:
1、把工人工作时的动作拍作视频并进行分析,以了解其多余动作。
减少工作是不必要的动作。
制作出标准动作图片。
2、对不合格品作好标示,能够修复和报废分类摆放定期处理。
在工段中分出不合格品区域。
3、对每个零件需要哪个产品线加工做出明确标示。
可以做成表格经多方确认后张贴于每个生产线。
减少加工中的来回周转。
4、给设计提供相应的模具表和模具图形,设计时尽量用我们已经有的模具进行加工。
张小可。
八大浪费识别和现场改善培训

提升产品质量
通过消除生产过程中的不良品和 返工,提高产品的一次性合格率。
优化工艺和设备,减少产品缺陷 和质量问题的出现。
提高员工的质量意识和技能水平, 确保产品质量的稳定和提高。
03
现场改善的方法与技巧
5S管理
整顿
对整理后的物品进行分类、标 识、定位,方便取用和归位。
清洁
维持整理、整顿、清扫后的状 态,形成制度化、规范化的管 理。
由于产品设计或制造过程中的缺陷, 导致产品不符合要求或性能下降。
过程
过于复杂的生产流程或工作方法,导 致效率低下。
识别方法与工具
方法
观察、记录和分析生产过程中的 各种活动,识别哪些是创造附加 值的,哪些不是。
工具
包括流程图、价值流图、5S管理 (整理、整顿、清洁、清洁检查 、素养)等。
案例分析
案例一
团队协作增强
培训后,员工之间的团队协作意识增强,能够更好地协同工 作,共同推进改善工作。
培训反馈与改进
反馈收集
通过问卷调查、面谈等方式收集员工对培训的反馈意见。
改进措施
根据员工的反馈意见,对培训内容、方式等进行调整和改进,以提高培训效果。
THANKS
感谢观看
不良品
由于产品设计或制造过程 中的缺陷,导致产品不符 合要求或性能下降。
定义与分类
等待时间
生产过程中的空闲时间, 等待原材料、零件或工具。
运输
不必要的物料和产品移动, 导致时间和资源和 成品,增加了存储和管理 成本。
定义与分类
动作
产品缺陷
不必要的操作或动作,如过多的检查、 搬运等。
料。
标准化作业
确保换模过程中的操作步骤和 作业方法标准化,提高换模效
八大浪费及改善技法

八大浪费及改善技法随着社会的发展,浪费资源的问题日益突出,对环境和经济造成了严重影响。
以下是八大浪费及改善技法:1.粮食浪费:粮食是人类的基本生活需求,但大量粮食被浪费。
改善的技法包括提高粮食加工和储存技术,完善食品追溯系统,减少超市及餐厅的食品浪费。
2.能源浪费:能源是推动经济发展和社会进步的重要支撑,不合理使用和浪费严重。
改善技法包括推广节能设备和技术,发展可再生能源,加强能源管理和监督。
3.水资源浪费:水资源短缺已经成为全球性问题,节约利用水资源至关重要。
改善技法包括鼓励居民节约用水、推广节水设施、加强水资源管理。
4.资金浪费:资金浪费主要体现在政府部门和企业的行为上。
改善技法包括强化财务管理,建立审计制度,提高资金使用效率。
5.时间浪费:时间是非常宝贵的资源,但人们经常陷入时间的浪费中。
改善技法包括合理规划时间、提高工作效率、减少社交娱乐时间的过度消耗。
6.交通浪费:交通堵塞及不合理安排造成大量时间和能源的浪费。
改善技法包括改善城市规划、完善交通基础设施、加强交通管理,推广绿色出行方式。
7.信息浪费:信息时代大量信息被浪费,而且信息泛滥导致人们忽略真正重要的信息。
改善技法包括培养良好的信息素养、加强信息筛选和传播的管理。
8.环境浪费:人们对环境资源的破坏和浪费严重威胁着人类的生存环境。
改善技法包括提高环境保护意识、推动绿色生产和消费、鼓励资源循环利用。
以上仅是八大浪费及改善技法的简要介绍,下面将对其中的一些技法进行详细阐述。
首先,粮食浪费时常发生在食品加工和储存过程中。
为了减少粮食浪费,应该提高食品加工设备的效率,减少食品加工过程中的损耗。
对于大型超市和餐厅,可以引入食品追溯系统,及时发现过期食品并予以淘汰或回收利用。
此外,还应加强对粮食资源的科学储存,减少因灰尘、虫害等因素造成的损耗。
其次,能源浪费主要源于能源使用的不合理和无序。
为了减少能源浪费,应推广节能设备和技术。
对于企事业单位和居民家庭,可以进行能源审核,鼓励节能行为,如替换高能耗设备,合理调整供暖温度等。
精益生产之如何改善八大浪费

精益生产之如何改善八大浪费随着科技的不断发展和市场竞争的加剧,企业在追求效益和竞争力方面面临着巨大的挑战。
精益生产作为一种有效的生产管理方法,可以帮助企业提高生产效率、降低成本并提供更好的产品和服务。
精益生产的核心理念是减少浪费。
在精益生产中,有八大浪费被认为是生产过程中最常见和最具破坏性的因素。
这八大浪费分别是:运输浪费、库存浪费、运动浪费、待料浪费、过程浪费、人才浪费、产品缺陷和非必要的代工。
要改善这八大浪费,企业可以采取以下措施:1. 运输浪费:企业可以通过优化物流系统和生产布局来减少运输环节,尽量将工作站安排在相邻位置,减少运输距离。
2. 库存浪费:企业可以采用“Just-in-Time”(即时生产)的原则,定期评估和调整库存水平,避免过多或过少的库存。
3. 运动浪费:企业可以通过重新设计工作站,优化工作流程,减少工人的移动和不必要的动作。
4. 待料浪费:企业可以通过提前做好生产准备工作,确保所需物料的及时提供,避免生产线的停滞。
5. 过程浪费:企业可以通过精细分析生产过程,找出存在的问题并采取相应的措施,以提高生产效率和质量。
6. 人才浪费:企业应充分发挥员工的潜力,提供培训和发展机会,让员工能够更好地参与到生产中来,减少人力资源的浪费。
7. 产品缺陷:企业应引入全面质量管理的理念,通过建立质量控制系统和严格的检测流程,尽量避免产品缺陷。
8. 非必要的代工:企业应充分评估自身的生产能力和需求,减少对外包和代工的依赖,提高自身的生产能力和竞争力。
总之,精益生产是一种全面优化生产过程的方法,通过减少浪费和提高效率,帮助企业实现长期可持续发展。
改善八大浪费,可以使企业在市场竞争中占据优势地位,并提供更好的产品和服务,满足客户的需求。
精益生产作为一种以减少浪费为核心的生产管理方法,在现代企业管理中扮演着至关重要的角色。
八大浪费是精益生产中常见的生产过程中的破坏性因素,包括运输浪费、库存浪费、运动浪费、待料浪费、过程浪费、人才浪费、产品缺陷和非必要的代工。
八大浪费之智力浪费介绍与改善

八大浪费之智力浪费介绍与改善智力浪费是指人们在思考、学习、创造等智力活动中出现的浪费行为。
智力浪费不仅会降低个人的智力水平和学习能力,还会浪费社会资源和人力资源。
以下是八大智力浪费及其改善方法。
1.信息过载:人们在信息时代面临大量的信息,难以有效地获取和处理。
改善方法是培养专注力和筛选信息的能力,选择有价值和有用的信息进行学习和思考。
2.孤立思考:许多人在学习和思考时习惯独自一人,容易陷入思维定势。
改善方法是积极参与集体智慧,与他人进行思路交流和碰撞,开拓自己的思维方式。
3.缺乏总结和反思:许多人只注重知识的获取,却忽略了对所学知识的总结和反思。
改善方法是养成总结和反思的习惯,通过思考和写作的方式将所学知识内化为自己的思维资产。
4.过度依赖工具:随着科技的发展,人们过度依赖手机、电脑等工具来进行记忆和思考,导致智力能力的退化。
改善方法是多进行脑力活动,比如读书、思考和解题,锻炼自己的大脑。
5.死记硬背:许多人在学习中只注重死记硬背,而忽视了理解和思考。
改善方法是培养综合和批判性思维能力,注重理解知识的本质和内在逻辑,而不仅仅是记忆表面的知识点。
6.缺乏实践与应用:许多人在学习中只停留在理论和概念层面,缺乏真实的实践和应用。
改善方法是将所学知识与实际生活和工作相结合,通过实践和探索来加深理解和应用能力。
7.智力洪水猛兽效应:人们在面对复杂或困难问题时常常会陷入焦虑和惧怕,导致智力水平受到限制。
改善方法是培养自信心和耐心,采用合适的学习方法和策略来应对挑战,克服智力障碍。
8.缺乏挑战和创新:许多人在学习和工作中只满足于应付任务和要求,缺乏探索和创新精神。
改善方法是勇于接受挑战,主动扩展自己的学识和思维领域,不断追求创新和突破。
为了改善智力浪费,个人需要培养自己的学习能力和思维方式。
可以通过坚持不懈的努力和刻意练习,逐渐改善自己的智力浪费行为。
同时,学校和教育机构也应该重视学生的智力发展和培养创新能力,提供多样化的学习环境和机会。
常见八大浪费和消除方法

常见八大浪费和消除方法在日常生活和工作中,我们会经常遇到各种浪费现象,这些浪费不仅消耗了资源和时间,还会降低工作效率和生活质量。
以下是常见的八大浪费和相应的消除方法。
1.非必要生产浪费:这种浪费包括过度生产、生产次品或废品、生产多余工作和指令等。
消除该浪费的方法是实施精益生产原则,分析生产过程中的不必要步骤和环节,优化生产流程,并监控和控制生产指令的发布。
2.库存浪费:库存浪费指储存成品、原材料或半成品的费用。
库存浪费的消除方法包括实施小批次生产,提高生产柔性和响应能力,通过供应链管理减少库存,并将库存量限制在合理的范围内。
3.运输浪费:运输浪费包括物料在生产、仓库和供应链中的多次搬运。
减少运输浪费的方法包括优化生产布局,减少生产线上的传送带长度,提高运输设备的效率,以及优化仓储管理和运输路线规划。
4.过度加工浪费:过度加工浪费指超过产品规格或顾客需求的加工。
减少过度加工浪费的方法包括明确产品规格和顾客需求,设立合理的加工标准,避免不必要的加工步骤和环节,以及提高员工技能和意识。
5.等待浪费:等待浪费指产品或工作在生产或供应链中等待的时间延误。
减少等待浪费的方法包括优化生产调度和物流流程,减少生产环节的停机时间和设备故障,以及提高生产和供应链的反应能力。
6.移动浪费:移动浪费指不必要的物料和人员移动。
减少移动浪费的方法包括优化工作布局,减少不必要的移动距离,提高物料存放和工具的易取性,以及改善工作环境和工作条件。
7.不必要的工艺浪费:不必要的工艺浪费指在生产过程中的不必要步骤和工艺。
消除不必要的工艺浪费的方法包括分析生产环节,识别和优化不必要的工艺和步骤,以及减少生产过程中的冗余操作。
8.缺陷浪费:缺陷浪费包括产品质量问题和返工造成的资源和时间浪费。
减少缺陷浪费的方法包括实施质量管理和质量控制措施,提高生产工艺和设备质量,以及设立合理的质量标准和检查流程。
总结起来,消除浪费需要从多个层面入手,包括优化生产流程、改善供应链管理、提高员工技能和意识、加强质量控制等。
八大浪费与改善方法案例
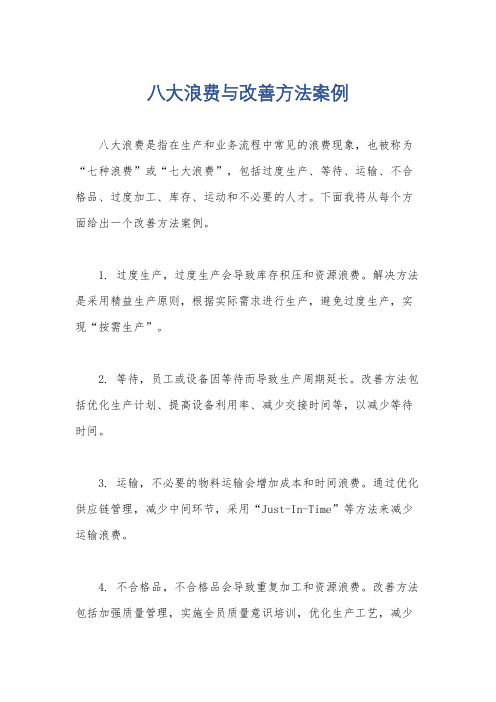
八大浪费与改善方法案例八大浪费是指在生产和业务流程中常见的浪费现象,也被称为“七种浪费”或“七大浪费”,包括过度生产、等待、运输、不合格品、过度加工、库存、运动和不必要的人才。
下面我将从每个方面给出一个改善方法案例。
1. 过度生产,过度生产会导致库存积压和资源浪费。
解决方法是采用精益生产原则,根据实际需求进行生产,避免过度生产,实现“按需生产”。
2. 等待,员工或设备因等待而导致生产周期延长。
改善方法包括优化生产计划、提高设备利用率、减少交接时间等,以减少等待时间。
3. 运输,不必要的物料运输会增加成本和时间浪费。
通过优化供应链管理,减少中间环节,采用“Just-In-Time”等方法来减少运输浪费。
4. 不合格品,不合格品会导致重复加工和资源浪费。
改善方法包括加强质量管理,实施全员质量意识培训,优化生产工艺,减少不合格品产生。
5. 过度加工,指超出产品要求的加工步骤,增加了成本和时间。
改善方法是重新评估生产流程,简化加工步骤,精简生产工艺。
6. 库存,过多的库存会增加资金占用和风险。
采用精益库存管理,通过精确预测和准确订单管理来降低库存水平,避免过多库存。
7. 运动,指员工不必要的移动或动作,增加了生产时间和疲劳。
改善方法包括优化工作站布局,减少不必要的移动,提高工作效率。
8. 不必要的人才,指员工的潜力未得到充分利用。
改善方法包括进行员工技能培训,激励员工提出改进建议,充分发挥员工的潜力。
通过以上改善方法案例,可以有效地减少八大浪费,提高生产效率,降低成本,增强企业竞争力。
同时,这些改善方法也体现了精益生产和持续改进的理念,对于企业的可持续发展具有重要意义。
精益生产之如何改善八大浪费

精益生产之如何改善八大浪费精益生产是一种通过精确分析和优化生产过程,减少浪费和提高效率的管理方法。
其中,八大浪费是指在生产过程中浪费了工时、资源和能源的现象。
本文将探讨如何通过精益生产的方法改善八大浪费。
第一,运输浪费。
运输浪费是指在产品生产、运输和分发过程中浪费了时间和资源。
通过优化生产和物流流程,降低运输次数和距离,可以减少运输浪费。
在制定运输计划时,应考虑最短路径、最佳装载和协调配送等因素。
第二,库存浪费。
库存浪费是指库存过多或过少对生产过程造成的损失。
通过精确预测需求,制定合理的库存管理策略,可以减少库存浪费。
同时,优化生产流程,减少等待时间和停顿,也可以减少库存浪费。
第三,移动浪费。
移动浪费是指在生产过程中不必要的移动造成的时间和资源浪费。
通过优化工作站布局,减少工人和物料的移动距离,可以减少移动浪费。
此外,合理安排工作流程,减少重复移动和任务转移,也可以减少移动浪费。
第四,过程浪费。
过程浪费是指生产过程中产生的不合格品和废品,导致资源的浪费。
通过制定和执行严格的质量控制措施,提高生产工艺和标准,可以降低过程浪费。
同时,培训员工加强技能和质量意识,也可以减少过程浪费。
第五,等待浪费。
等待浪费是指在生产过程中因为等待他人、设备或者信息而浪费的时间。
通过合理安排生产计划和任务分配,减少等待时间,可以减少等待浪费。
同时,提供及时和准确的信息,协调各个环节之间的关系,也可以减少等待浪费。
第六,不必要的运动浪费。
不必要的运动浪费是指在生产过程中不必要的动作导致的时间和能源浪费。
通过分析工作流程和使用合适的工具,减少不必要的动作和动作强度,可以降低不必要的运动浪费。
此外,培训员工正确使用工具和设备,也可以减少运动浪费。
第七,不合理的工艺浪费。
不合理的工艺浪费是指采用不合理的工艺和方法造成的资源和能源浪费。
通过对工艺流程的细致分析和改进,优化物料和能源的使用,可以减少不合理的工艺浪费。
同时,培训员工学习和掌握先进的工艺技术,也可以减少工艺浪费。
八大浪费及改善技法

1. 管理板 2. 控制投入 3. 过剩生产
24
24
把握状态
消除浪费的步骤
分析原因
寻找消除方法 立即实践
制作小工具 决定维持管理方法
过剩生产
• 按节拍时间,制定标准作业 • 用看板控制序安排方法,重新安排作业
•人员过剩 •设备稼动过剩 •生产浪费大 •业务订单预测有误 •生产计划与统计错误
对策:
•顾客为中心的弹性生产系统
•单件流动—一个流生产线
•看板管理的贯彻 •快速换线换模 •少人化的作业方式 •均衡化生产
注意:
•生产速度快并不代表效率高 •设备余力并非一定是埋没成本 •生产能力过剩时,应尽量先考虑减
对策:
•自动化、标准作业
•防错装置
•在工程内做出品质保证
“三不政策”
•一个流的生产方式
•品保制度的确立及运行
•定期的设备、模夹具保养
•持注续意:开展“5S活动”
•能回收重做的不良
•能修理的不良
•误判的不良
10
➢多余动作浪费
❖是指员工的任何一个对生产流程来说不必要的动作 ❖在一个布局不合理的工位或没有遵循标准化操作的员工,过度
•
•
•
解决方案
• • • •
• • • •
• • • •
•
•
•
•
27
找出浪费因素表(2/2)
我工厂的现状
观察事例
库存
•
•
•
•
•
•
•
•
动作
•
•
•
•
•
•
•
•
精益生产八大浪费的改善方法
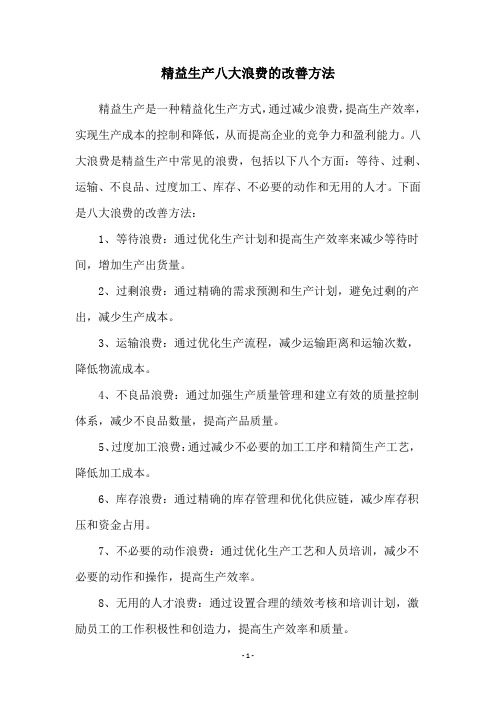
精益生产八大浪费的改善方法
精益生产是一种精益化生产方式,通过减少浪费,提高生产效率,实现生产成本的控制和降低,从而提高企业的竞争力和盈利能力。
八大浪费是精益生产中常见的浪费,包括以下八个方面:等待、过剩、运输、不良品、过度加工、库存、不必要的动作和无用的人才。
下面是八大浪费的改善方法:
1、等待浪费:通过优化生产计划和提高生产效率来减少等待时间,增加生产出货量。
2、过剩浪费:通过精确的需求预测和生产计划,避免过剩的产出,减少生产成本。
3、运输浪费:通过优化生产流程,减少运输距离和运输次数,降低物流成本。
4、不良品浪费:通过加强生产质量管理和建立有效的质量控制体系,减少不良品数量,提高产品质量。
5、过度加工浪费:通过减少不必要的加工工序和精简生产工艺,降低加工成本。
6、库存浪费:通过精确的库存管理和优化供应链,减少库存积压和资金占用。
7、不必要的动作浪费:通过优化生产工艺和人员培训,减少不必要的动作和操作,提高生产效率。
8、无用的人才浪费:通过设置合理的绩效考核和培训计划,激励员工的工作积极性和创造力,提高生产效率和质量。
在实际生产中,企业应根据自身情况,针对八大浪费进行相关的改善措施,不断提高生产效率和产品质量,提高企业的核心竞争力和盈利能力。
八大浪费改善建议

八大浪费改善建议
针对精益生产中的八大浪费,给出八大浪费改善建议如下:
1.做好自动化,愚巧化(防呆化)的生产方式,着重于工厂生产标准的建立,对生产的产品作出全数检查,以达到无停滞的流程作业。
2.在加工的过程中工程设计也该适量化,对作业内容要进行重新的评估,对生产中治工具进行改善,减少加工不必要的浪费,同时VE和VA的推动也同样重要。
3.改良生产现场布置,多数生产现场以u字形生产布置,以达到首尾接应的效果,减少路线的浪费,改良工人动作的浪费,减少工人在生产过程中一切和工作无关的动作,并改良其动作,以达到最省力情况下完成工作,减少不必要的动作浪费。
4.减少搬运的浪费最重要的是减少搬运的次数,所以企业生产还是要符合后拉式看板生产,以达到在接到订单后就生产所需产品的数量,生产完后直接运送到客户手里,以减少库存的产生,减少了搬运的次数。
5.库存的浪费最主要是库存意识的改革,在生产方式中要尽量符合平准化生产方式,使生产整流化,而且看板生产也要彻底贯彻实施,以减少库存产生。
6.工厂生产应该根据销售经验,合理安排生产计划,同时及时根据市场的变化,调整生产计划,以达到最小合理库存。
7.要合理安排工厂的生产计划,在生产前一天要将所需的原材料贮备好,生管要合理安排工厂生产的计划,在接单后,立即查询所需原材料的上游厂家的生产情况,并对工厂的生产有着统一的规划。
8.管理的浪费最主要是对工厂各部门进行协调管理,使各部门紧密结合在一起,注重于工厂各部门的合作,以达到对工厂资源的最合理的利用。
八大浪费改善建议

八大浪费改善建议在现代社会,资源是有限的,许多资源的浪费现象亟待改善。
以下是八大浪费改善建议:1.餐饮浪费:提倡节约粮食,避免大量食物浪费,可以鼓励采用小份量点餐,推广打包带走的文化,同时减少自助餐形式,避免粮食过度浪费。
2.能源浪费:鼓励使用清洁能源,提高能源利用效率。
政府可以制定相关政策,推广太阳能、风能等可再生能源的使用,同时加大对能源科技研发的投入,提高能源利用的效率。
3.水资源浪费:加强水资源的管理和保护,鼓励节约用水。
可以通过提高水价、宣传水资源的重要性和节约用水的方法,加强对用水行为的监管,减少浪费。
4.塑料浪费:大力推广减塑理念,减少塑料的使用。
可以鼓励使用环保袋、水杯替代塑料袋和塑料瓶,限制塑料袋和塑料制品的生产和使用,同时提倡塑料废弃物的回收利用。
5.交通浪费:提倡绿色出行,鼓励减少私家车的使用。
可以加强公共交通的发展,建设更多的地铁、轻轨等公共交通系统,提高公共交通的覆盖率和便利性,同时鼓励步行和骑行。
6.教育浪费:加强教育资源的配置和管理,避免教育资源的浪费。
可以完善教育资源的分布,减少富余资源的浪费,提高教育资源的使用效率,做到资源合理利用。
7.时间浪费:提倡科学时间管理,避免时间的浪费。
可以通过教育宣传,提高人们的时间意识,合理安排工作与生活,减少碎片化的时间浪费,提高工作效率。
8.钱财浪费:加强财务管理,避免金钱的浪费。
可以通过加强财务教育,提高人们的理财能力,避免过分消费和投资的风险,减少金钱的浪费。
综上所述,要改善八大浪费现象,需要社会各界的共同努力。
政府、企业、个人都应该意识到资源的有限性,从而制定相应的政策和措施,改善资源的使用效率,减少浪费,促进可持续发展。
八大浪费与解决方法

八大浪费与解决方法一、时间浪费时间浪费主要体现在人们的日常生活中,包括社交媒体上的无谓浏览、排队等待以及没有计划的工作等。
要解决时间浪费问题,可以采取以下措施:1.制定明确的计划:制定每日、每周或每月的计划,设定清晰的目标和时间安排,提高工作和生活效率。
2.管理社交媒体使用:限制每天使用社交媒体的时间并且合理选择使用的时间段,避免沉迷其中。
3.优化工作流程:通过合理安排工作流程,避免重复劳动或低效率工作,提高工作效率,节约时间。
二、能源浪费能源浪费是指人们在能源的使用过程中造成的浪费,例如电力浪费、汽车尾气等。
要解决能源浪费问题,可以采取以下措施:1.加强能源管理:建立科学的能源管理制度,优化能源供应体系,提高能源利用效率。
2.推广清洁能源:大力发展可再生能源,降低对传统能源的依赖,减少能源浪费。
3.提倡节约能源生活方式:鼓励人们采取节约能源的生活方式,例如降低室内温度、科学使用家电等,减少能源浪费。
三、粮食浪费粮食浪费主要包括粮食生产、加工、储存、运输和消费环节中的浪费。
要解决粮食浪费问题,可以采取以下措施:1.提高粮食生产效益:推行科学合理的农业生产模式,加强农业技术培训,提高农业生产效率。
2.完善粮食储存和运输设施:加强粮食储存设施建设,完善冷链运输系统,减少粮食损失。
3.强化食品安全意识:加强食品安全宣传教育,增强人们对粮食珍惜的意识,减少不必要的浪费。
四、水资源浪费水资源浪费主要体现在人们对水的滥用、污染等方面。
要解决水资源浪费问题,可以采取以下措施:1.推行节水措施:鼓励人们采取节约用水的生活方式,例如减少浴缸用水量、修复漏水等。
2.加强水资源管理:建立健全水资源管理制度,加强水资源的监控和调度,提高水资源利用效率。
3.提倡环保意识:加强环保教育,提高人们对保护水资源的重要性的认识,减少水污染和浪费。
五、资金浪费资金浪费主要指的是在投资、购物等方面的不理性使用和浪费。
要解决资金浪费问题,可以采取以下措施:1.理性消费:树立理性消费观念,避免盲目消费和奢侈浪费。
八大浪费产生的根源分析与改善措施

八大浪费产生的根源分析与改善措施一、八大浪费产生的根源分析1.库存浪费根源是由于原料、在制品、成品等超过了制程或客户所需的最合适的量,而造成及掩盖了其它浪费。
2.等待浪费的根源是由于生产原料供应中断、作业不平衡和生产计划安排不当等原因,造成员工不能为客户创造价值,而无事可做。
3.搬运浪费是由于搬运本身不但不能产生附加价值,而且,它会造成了物品移动所需空间的浪费、时间的浪费和人力工具的占用浪费等不良后果,它不仅增加了搬运的费用,还可能造成物品在搬运中丢失或者损坏。
4.品质不良浪费的根源是由于企业内出现不良品,进行处置时,而需要在时间、人力、物力上的投入,以及由此造成的相关损失。
5.动作浪费根源由于工位、物品、设备等布置不合理,使用工具和操作方法不得合适而造成的浪费。
6.过分加工浪费的根源在于加工作业中,做了与工序进度及加工精度无关的不必要的加工。
7.制造过多过或过早的浪费的根源在于生产超额完成任务,过多的制造和提前生产而造成浪费。
8.管理浪费是浪费的根源在于员工积极性不高,自主管理能力不强,以及管理制度不完善而造成的浪费二、如何有效改善或消除上述“浪费”?1.要消除库存浪费,我们要认识到“库存是万恶之源”,探求必要库存的原因,要合理使用库存规模的,降低库存,实现设备布置流水化,合理地安排生产计划均衡化生产。
降低库存是曝露生产现场问题的有效方式,目的是为了发现更多的浪费。
尽力将各种生产管理活动都变得“可视化”,用“一望而知”的颜色、形状、位置和独特的“看板”来区别和显示车间内的每一道工序、每一个规格、每一种状况,使所有现场人员在一目了然的环境下迅速发现各种异常和浪费。
例如:车间生产线因故障而停产一个小时,如果目前车间有两个小时的库存量,事情可能不会报告给中高层管理人员。
但是,如果车间库存仅为半小时的产量,那么就会发生无法向客户或者后道工序交货的问题,就会造成大混乱。
所以,两小时库存可以掩盖停产的问题;而半小时库存就会使问题表面化,就会促使企业尽快采取措施加以改进。
精益生产八大浪费的改善方法

精益生产八大浪费的改善方法
精益生产是一种流程优化的方法,旨在消除浪费并提高效率。
其中最重要的概念就是八大浪费,即:
1. 过度生产:过度生产会导致库存增加,占用空间和资金,造成浪费。
改善方法是采用按需生产模式,即根据市场需求进行生产,减少库存。
2. 等待:等待是一种浪费时间和资源的行为,可以通过优化流程和减少瓶颈来缩短等待时间。
3. 运输:运输浪费时间和成本,可以通过在生产线上进行加工和装配,减少产品运输。
4. 过度加工:过度加工意味着增加了生产成本,但并不会为产品增加价值。
可以通过检查和优化工序,减少不必要的加工。
5. 库存:库存是一种资金和空间的浪费,可以通过压缩生产周期,减少库存。
6. 返工和修补:返工和修补是一种成本高昂的浪费,可以通过提高生产的质量和流程控制来减少。
7. 过度处理:过度处理也会增加成本,但并不会为产品增加价值。
可以通过优化工艺和流程来减少过度处理。
8. 无用的员工:如果员工没有得到充分利用,他们的劳动力就会浪费。
可以通过培训,激励和优化流程来提高员工的工作效率。
总之,通过精益生产的八大浪费改善方法,企业可以提高生产效率,减少成本,提高质量,增强市场竞争力。
八大浪费改善案例

八大浪费改善案例
八大浪费是精益生产中经常提到的概念,包括不良、修理的浪费,过分加工的浪费,动作的浪费,搬运的浪费,库存的浪费,制造过多过早的浪费,等待的浪费和管理的浪费。
以下是一些针对这些浪费的改善案例:
1. 不良、修理的浪费:某公司通过实施严格的质量控制体系,提高首次合格率,减少了不良品和需要返工的产品的数量。
2. 过分加工的浪费:某制造企业通过重新评估生产流程,优化了切割和打磨等工艺步骤,减少了不必要的加工工作,提高了生产效率。
3. 动作的浪费:某装配线引入了更为合理的物料摆放和输送方式,减少了工人的动作量,提高了工作效率。
4. 搬运的浪费:某工厂优化了物料配送流程,减少了中间环节和运输距离,降低了搬运成本。
5. 库存的浪费:某公司引入了实时库存管理系统,实现了库存的精准控制,减少了库存积压和浪费。
6. 制造过多过早的浪费:某生产车间引入了准时制生产方式,严格按照客户需求进行生产和排程,避免了过度生产和过早生产的问题。
7. 等待的浪费:某生产线引入了多能工制度,通过交叉培训和任务分配,减少了人员等待时间,提高了生产效率。
8. 管理的浪费:某企业通过引入先进的生产管理软件,简化了管理流程,提高了管理效率。
这些案例都是通过深入分析和优化生产和管理流程,消除了八大浪费中的一些问题点,提高了效率并降低了成本。
在实际操作中,需要针对企业具体情况制定相应的改善方案。
- 1、下载文档前请自行甄别文档内容的完整性,平台不提供额外的编辑、内容补充、找答案等附加服务。
- 2、"仅部分预览"的文档,不可在线预览部分如存在完整性等问题,可反馈申请退款(可完整预览的文档不适用该条件!)。
- 3、如文档侵犯您的权益,请联系客服反馈,我们会尽快为您处理(人工客服工作时间:9:00-18:30)。
八大浪费改善的思路与方法
工具,物料放在小臂范围内
八大浪费改善的思路与方法
物料依左右手拿的顺序去摆放
1 3 4 2
八大浪费改善的思路与方法
重量堕送
八大浪费改善的思路与方法
保持良好的姿势
工作台的设计:工作 台高度应在肘下一至 三寸
八大浪费改善的思路与方法 3、关于工具设备的设计
一.尽量使用工装或足踏工具,以解除手的“持住”动作.
根源
人机工程设计不妥 设备/工序设计不精益
工作标准不一致
工作场地有序安排和保洁 不当 等候时不必要移动
八大浪费之七:
等待
定义:
员工停下来监看自动化机器,或必须停下来等待上一道工 序完工、等待工具、供货、材料等,或因存货用完、机器故障停 工等因素导致员工没有工作可做。
现象
.资源利用率低 .设备闲置 .设备空转 .生产力降低 . 等候仓储空间 .不必要的测试 .不平衡的操作 .计划外停机
如何识别现场八大浪费
1、过 量生产 8、管 理 2、库 存
7、等 待
八大 浪费
6、多 余动作 5、过 度加工
3、搬 运
4、纠 正错误
八大浪费之一:
过量生产
定义:生产了过多过早的,超出客户或下游工序所需要的量
,过多过早的生产出未有订单的产品。
现象:
过量原材料 额外的库存 过度占用空间 物流不平衡 过度浪费搬运与处理 额外的设备占用
2、库存的改善思路:减少库存量
加强经销商管理,提高 市场预测准确性
拉动生产方式
准时化生产 精益布局,缩短周期
八大浪费改善的思路与方法
2、库存的改善思路:减少库存量
八大浪费改善的思路与方法
3、搬运的改善思路:分析搬运是否必须?
搬运是一种不增值的活动
尽可能使搬运精简
尽可能的避免搬运
八大浪费改善的思路与方法
根源
.以防万一的逻辑 .缺乏沟通 .过多/重复的批准程序 .未确定用户的需求 .缺乏边界样品或客户规格要求
八大浪费之六:
多余动作浪费
定义:任何对生产/服务不增值的人员/机器的动作。
现象
较长的步行距离 较长的制造周期 资源使用不当 寻找工具/ 材料 过度的伸展/ 弯腰 等候期间额外的忙乱动作
例:市场需求100件/天
假效率与真效率?
厂长A: 10个人1天生产 100件产品 厂长B: 10个人1天生产 120件产品 厂长C: 8个人1天生产 100件产品
无效率
假效率
真效率
八大浪费改善的思路与方法
1、过量生产 的改善思路: 识别真假效率
按照需求数量生产-真效率 多做的造成库存-假效率
八大浪费改善的思路与方法
工场中有各种各样的传送带, 其优点为:
因为能等距离地传送物品,所以 适合及时管理方式; 搬运活性高,因为搬运和作业同 时进行,所以不会发生取放物品 的浪费.
搬运方法
29
八大浪费改善的思路与方法 搬运的方法
搬运方法
3)定量和定时搬运
定量搬运是后工序到前工序 去取要使用一定量的物品的 方式。是否需要搬运,不是由 时间决定,而是由使用量决定 的. 定时搬运是在特定时间搬运 难的场合.
根源
.材料放置不当 .生产计划不均衡 .设施布局不当 .工作场地保洁不当 .缺乏对资源的管理 .工序不均衡 .供应链管理混乱
八大浪费之四:
纠正错误(不良品浪费 )
定义:返工,返修,报废造成的人工、机器、材料的额外付
出。
现象
.返工、返修与报废 .客户退货 .客户失去信心 .错过交货期 .有害废弃物产生 .处理成本高 .公用设施成本高 .忙于救火,而非预防
二.可能时应将两种以上工具合并. 三.对手指的工作负荷应依其本能予以分配. 四.手柄之设计应可能使其与手之接触面积增大. 五.机器设备之操作杆、开关、手柄之位置应在工作者正 常作业范围内,以尽量少移动位置或变动其姿势.
4
八大浪费改善的思路与方法
工装
气枪
八大浪费改善的思路与方法
改善后
30
八大浪费改善的思路与方法 搬运的方法
搬运方法
4)消除孤岛作业
产生原因:不考虑人和机器的平衡就推进自动化。 影响:作业者常被分隔作业,无法互帮;产生空手 等待的浪费;无法实现“少人化”的生产. 半成 品浪费;搬运的浪费。
31
八大浪费改善的思路与方法
4、纠正错误(不良)的改善思路:5X5W 1H法,又称5 * 5 何法、质疑创意法,简称五五法;5M1E法
根源
.工作负荷不平衡 .无计划维护 .较长时间的设置 .质量问题 .生产计划不均衡 .低效布局 . 不一致的工作方法
八大浪费之八:
管理的浪费
定义:
基于工厂的管理和运作方式使公司不能获至最大利润而 造成的浪费.是竞争力强弱的表现。
现象
.生产力低 .资源利用率低 .资本利润低 .技术能力薄弱 .研发周期长 .交付周期过长 .人员涣散
简单地说,浪费就是指顾客不愿意为你 付钱的那些过程(即不增加价值的行为)。
2、重新认识“浪费”
认识增值与非增值
• 增值:技术工艺图纸中的所有活动
• 非增值?
2、重新认识“浪费”
某权威机构对企业增值与非增值活动的统计: 增值
制造 过程 非增值
(约95%) (<5%)
必要非增值(约60%)
不必要非增值(约35%)
八大浪费-精益生产之培训资料
目录
1 经营思想概述 重新认识“浪费”
2 3
4
如何识别现场八大浪费
八大浪费改善的思路与方法
1、经营思想概述
导论:
独占经营模式
传统的微利模式
市场化的赢利模式
省则赚!
1、经营思想概述
核心:
售价 利润
提高售价
X
关键是 降低成 本!!!!!!
成本
1、经营思想概述
企业最终目的:
5W: WHERE 何处,在什么地方,在什么~空間 WHEN 何时,在什么时候, ~时间 WHAT 何者,是什么东西/事,~生产对象 WHO 何人,是什么人做/生产主体 WHY 为何,为什么如此 1H: HOW 如何,怎么做的 5X是五次,表示对问题的质疑不要只问一次而要多问几次,不是刚 好只问5次可多亦可少,类似我们的“打破砂锅问到底”之精神.
根源
.以防万一的逻辑 .误用自动化 .换模工序时间长 .生产计划不均衡 .工作负荷不平衡 .部门间缺乏交流 •不合理的奖励制度
八大浪费之二:
库存
定义:各工序之间的库存或由原材料库存超过必需要的量
。任何超过客户按时所要求的必要的产品或服务供应。
现象
•额外仓储及搬运 •在制品包装 •公用设施成本高 •盘点困难 •需求更多的处理资源 (人、设备、货架、 仓库、系统)
最 短 的 时 间
最 低 的 成 本
最 高 的 效 率
最 少 浪 费
您的关注点是什么?
1、经营思想概述
识别“价值”。
关注价值
2、重新认识“浪费”
讨论:什么是“浪费”?
请简述生活中你所认为的“浪费”是什么?
2、重新认识“浪费”
精益生产中的 “浪费”
浪费---凡是超出增加产品价值所绝对必 须的最少量的物料、设备、人力、场地和时 间的部分都是浪费。
根源
•产品的复杂性 •为了加大保险库存 •生产计划不均衡 •市场预测/ 管理不力 •工作负荷不平衡 •供应商货运不确定 •换型时间长 •不合理的奖励制度
八大浪费之三:
搬运
定义:任何不为生产过程所必需的物料搬动或信息流转。
现象
过度和过长的搬运 过度的搬运设备 大面积储存区 过量配送人员 质量降低 过度能源消耗 损坏或丢失物品
根源
.过程控制薄弱 .作业员控制失误 .材料质量有问题 .缺少防错措施 .设备故障 .产品设计不良 .环境不良
八大浪费之五:
过度加工
定义:从用户的观点看,对产品或服务没有增加价值的
努力 。
现象
.没完没了的修饰 .外加设备 .频繁的分类,测试,检验 .额外的复印件/过多的信息 .能源过度消耗 .额外的加工工序
二.除休息外,双手不应同时空闲;
三.双手的动作应对称、反向并同时完成.
38
八大浪费改善的思路与方法
1、关于人体的运用
级别 1 2 3 4 运动驱轴 指 手 肘 肩 节 腕 人体运动部位 手指 手指及手掌 手指,手掌及前臂 手指,手掌,前臂及上臂
5
身 躯
手指,手掌,前臂,上臂及肩
在满足动作需要的情况下,人体的动作应尽量应 用最低等级.
八大浪费改善的思路与方法
4、纠正错误(不良)的改善思路:5X5W 1H法:又称5 * 5 何法、质疑创意法,简称五五法。
5M1E分析法:通过对5M1E分析找出造成不良的原因 5M1E : 人员(Manpower) 机器(Machine) 材料(Material) 方法(Method) 测量(Measurement) 环境(Environment)
根源
.管理能力低:素质;执行力 (速度/准度/精度) .技术层次:认知度不高,把 握度低 .标准化:可行性不高,推广 度不广 .企业整体素质不高
八大浪费回顾
1、过 量生产 8、管 理 2、库 存
7、等 待
八大 浪费
6、多 余动作 5、过 度加工 4、纠 正错误
3、搬 运
八大浪费改善的思路与方法
1、过量生产 的改善思路: 识别真假效率
八大浪费改善的思路与方法
5、过度加工的改善思路:正确识别顾客需求。
只做顾客真正需要的!