生物柴油粗甘油精制技术
粗甘油分离与精制工艺的研究
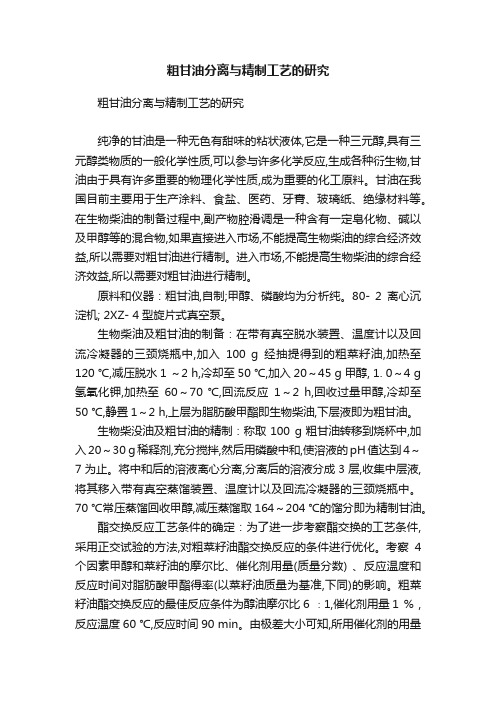
粗甘油分离与精制工艺的研究粗甘油分离与精制工艺的研究纯净的甘油是一种无色有甜味的粘状液体,它是一种三元醇,具有三元醇类物质的一般化学性质,可以参与许多化学反应,生成各种衍生物,甘油由于具有许多重要的物理化学性质,成为重要的化工原料。
甘油在我国目前主要用于生产涂料、食盐、医药、牙膏、玻璃纸、绝缘材料等。
在生物柴油的制备过程中,副产物腔滑调是一种含有一定皂化物、碱以及甲醇等的混合物,如果直接进入市场,不能提高生物柴油的综合经济效益,所以需要对粗甘油进行精制。
进入市场,不能提高生物柴油的综合经济效益,所以需要对粗甘油进行精制。
原料和仪器:粗甘油,自制;甲醇、磷酸均为分析纯。
80- 2离心沉淀机; 2XZ- 4型旋片式真空泵。
生物柴油及粗甘油的制备:在带有真空脱水装置、温度计以及回流冷凝器的三颈烧瓶中,加入100 g经抽提得到的粗菜籽油,加热至120 ℃,减压脱水1 ~2 h,冷却至50 ℃,加入20~45 g甲醇, 1. 0~4 g 氢氧化钾,加热至60~70 ℃,回流反应1~2 h,回收过量甲醇,冷却至50 ℃,静置1~2 h,上层为脂肪酸甲酯即生物柴油,下层液即为粗甘油。
生物柴没油及粗甘油的精制:称取100 g粗甘油转移到烧杯中,加入20~30 g稀释剂,充分搅拌,然后用磷酸中和,使溶液的pH值达到4~7为止。
将中和后的溶液离心分离,分离后的溶液分成3层,收集中层液,将其移入带有真空蒸馏装置、温度计以及回流冷凝器的三颈烧瓶中。
70 ℃常压蒸馏回收甲醇,减压蒸馏取164~204 ℃的馏分即为精制甘油。
酯交换反应工艺条件的确定:为了进一步考察酯交换的工艺条件,采用正交试验的方法,对粗菜籽油酯交换反应的条件进行优化。
考察4个因素甲醇和菜籽油的摩尔比、催化剂用量(质量分数) 、反应温度和反应时间对脂肪酸甲酯得率(以菜籽油质量为基准,下同)的影响。
粗菜籽油酯交换反应的最佳反应条件为醇油摩尔比6 ∶1,催化剂用量1 % ,反应温度60 ℃,反应时间90 min。
生物柴油副产物粗甘油精制的研究
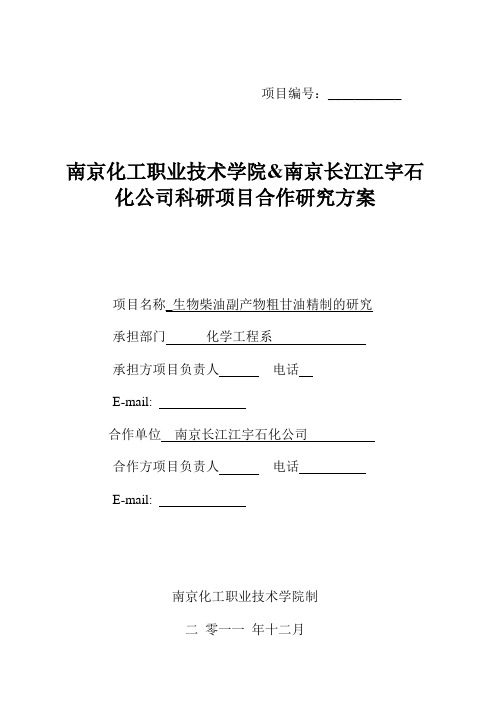
项目编号:___________
南京化工职业技术学院&南京长江江宇石化公司科研项目合作研究方案
项目名称_生物柴油副产物粗甘油精制的研究
承担部门化学工程系
承担方项目负责人电话
E-mail:
合作单位南京长江江宇石化公司
合作方项目负责人电话
E-mail:
南京化工职业技术学院制
二零一一年十二月
一、项目基本情况
二、项目的研究方向及预期效益
三、项目承担已有的基础条件
四、项目实施方案
五、项目的前景、预期经济社会及生态效益
六、计划进度(包括年度计划、完成时间)与具体考核指标
七、经费预算
就开展第一步和第二步两项研究,我们初步预计认为项目预计总经费5万元,其中申请学院经费 5.0 万元,合作单位投入 5.0 万元。
由于后面几步的研究工作中涉及的设备投入较大,要专门设立课题进行专门研究,因此后面的研究工作的开展等前期工作完成后,再进行讨论协商确定。
经费支出预算表
(单位:元)
八、承担部门意见、盖章合作部门或单位意见、盖章
盖章盖章年月日年月日。
生物柴油生产技术

生物柴油生产技术生物柴油是一种可再生能源,由植物油或动物脂肪转化而来。
它被广泛认为是替代传统石油燃料的一种环保可持续发展解决方案。
本文将介绍生物柴油的生产技术及其在可再生能源领域的重要性。
一、生物柴油生产技术概述生物柴油的生产技术主要包括原料准备、酯化反应、脱水、精炼和纯化等步骤。
1. 原料准备:生物柴油的原料可以是多种油料作物的籽粒、植物的果实或者动物脂肪。
这些原料需要经过脱水、去杂等处理,以提高生物柴油的产率和质量。
2. 酯化反应:将原料中的油脂与醇类(如甲醇或乙醇)加热并加入催化剂,触发酯化反应。
这个反应过程中,油脂中的三酸甘油酯与醇类反应生成生物柴油和副产物甘油。
3. 脱水:酯化反应后,产生的混合物中存在大量的水分。
通过脱水操作可以去除水分,提高生物柴油的纯度和稳定性。
4. 精炼和纯化:脱水后的混合物需要经过精炼和纯化的处理,以去除杂质和颜色等不纯物质。
这一步骤可采用冷沉淀、蒸馏和脱臭等方法。
二、生物柴油的可再生性和环保性生物柴油的生产过程基于植物油和动物脂肪,是一种可再生资源。
相比于传统石油燃料,生物柴油可以减少温室气体排放,降低空气污染和对化石能源的依赖。
此外,生物柴油在燃烧过程中释放的二氧化碳可以被作物吸收,形成一个循环闭环,减少了对全球气候变化的负面影响。
生物柴油还具有较低的毒性,不含硫和芳香烃等有害物质,对环境和人体健康影响较小。
因此,生物柴油的生产和使用是可持续发展的一种解决方案,有助于推动能源结构转型和环境保护。
三、生物柴油的应用前景由于其可再生性和环保性,生物柴油在能源领域的应用前景广阔。
1. 交通运输领域:生物柴油可直接替代传统石油柴油,用于汽车、公交车、卡车等交通工具的燃料。
很多国家已经开始采用生物柴油作为替代燃料,以减少空气污染和碳排放。
2. 发电行业:生物柴油可用于发电机组的燃料,为电网提供清洁、可再生的能源。
这对于推动电力行业的可持续发展具有重要意义。
3. 化工领域:生物柴油的合成还可以产生许多有用的化学品,如润滑剂、溶剂、涂料等。
生物柴油副产物粗甘油精制工艺的研究
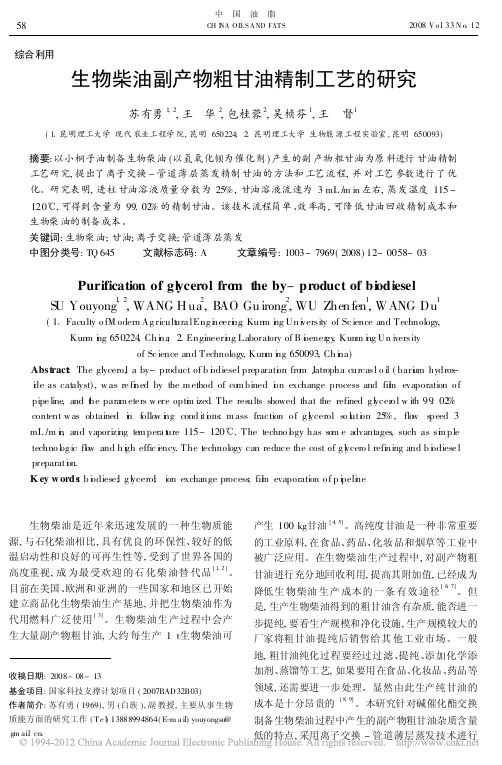
反应器中, 用稀硫酸调节 pH 至 5~ 6, 在 ( 50 5) 下酸化处理 30 m in; 上层酸化油返回生物柴油制备 系统作为生物柴油生产原料, 下层甘油溶液进入中
和反应器, 用氢氧化钡溶液调 pH 至 8. 0~ 8. 5, 静置 分层, 产生的硫酸钡沉淀从反应器底部排出, 得到的 稀甘油溶液依次通过阳离子交换柱、阴离子交换柱 以及阴阳离子混合交换柱, 除去各种杂质, 得到甘油 稀溶液; 甘油稀溶液进入短程管道蒸发器, 进行薄层 高效快速连续蒸发浓缩, 得到高纯度的甘油产品, 产 生的水蒸汽经冷凝后, 循环用于粗Байду номын сангаас油的稀释。 1. 4 分析方法
表 3 蒸发浓缩温度对产品质量的影响
项目
产品色泽 /H azen 产品中灰分 /% 产品中甘油 /% 蒸出水中甘油 /%
温度 / 105 110 115 120 125 15 15 15 15 15 0. 015 0. 015 0. 16 0. 016 0. 016 98. 78 98. 82 98. 99 99. 12 99. 13 0. 05 0. 04 0. 05 0. 05 0. 08
以生物柴油制备中产生的副 产物粗甘油经酸 化、中和 处 理后 ( 处 理后 的 样品 中 甘油 质 量分 数 67. 54% 、灰分 2. 57% ) , 经稀释制成不同质量分数 的甘油溶液为原料, 在过柱流速为 3 mL /m in和室温 条件下进行离子交换柱净化试验, 结果见表 1。从 表 1可以看出, 离子交换柱的脱色效果非常显著, 不 同质量分数的甘油溶液经处理后, 基本都达到无色 透明状态; 甘油中无机盐分去除率随甘油质量分数 的降低而增加, 当甘油质量分数低于 25% 时盐分去 除率可达 99. 50% 以上, 且随甘油 质量分数继续降 低去除率变化不大; 4种质量分数的甘油溶液经离 子交换柱净化处理后的 pH 基本都在 7左右。从成 本和净化效果综合考虑, 以酯交换法制备生物柴油 ( 氢氧化钡为催化剂 ) 时产生的副产物粗甘油在本 试验条件下采用离子交换法净化的较佳甘油质量分 数为 25% 左右 (灰分含量大约为 1% )。
生物柴油副产物——甘油精制工艺优化研究
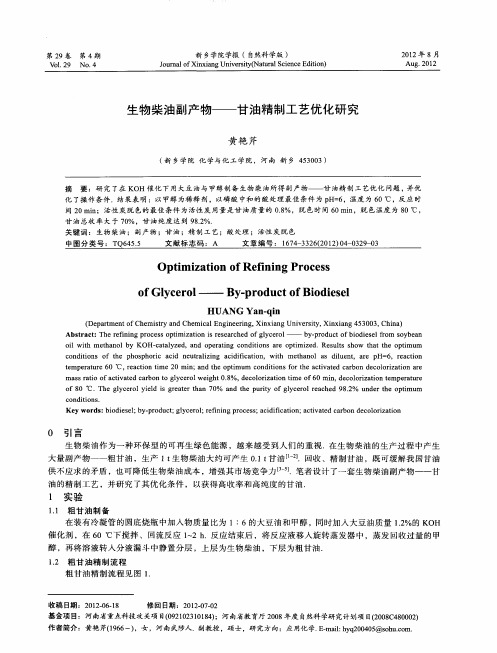
0 引 言
生物 柴油作 为一 种环 保 型的可 再生绿 色 能源 ,越来 越受 到人 们 的重视 .在生 物柴 油 的生 产 过程 中产 生 大量 副产物一 一粗 甘油 ,生产 1 生物 柴油 大约 可产生 01 甘油 [ .回收 、精 制 甘油 ,既可缓 解我 国甘 油 t .t
甘 油 总 收 率 大 于 7 % ,甘 油 纯 度 达 到 9 .%. 0 82
关键 词: 生物柴 油 ;副 产物 ;甘 油 ;精制 工 艺 ;酸 处理 ;活性炭 脱 色
中 图 分 类 号 : T 6 55 Q 4. 文 献 标 志 码 :A 文 章 编 号 : 1 7 — 3 62 1 ) 4 0 2 — 3 6 4 3 2 (0 2 0 — 3 9 0
Ab t a t her f i g p o e s o t z to sr s a c e fg y e o --— y- r d c fb o i s l r m o b a s r c :T e n n r c s p i a i n i e e r h d o l c r l-- —b ・ o u to i d e e o s y e n i mi -- -- -- p f
化 了操作 条件 .结果 表 明:以甲醇为稀 释 剂 ,以磷 酸 中和 的酸处理 最佳 条件 为 p = ,温度 为 6 H6 0℃ ,反应 时
间 2 mi 0 n;活性炭 脱 色的最佳 条件 为活 性炭 用量是甘 油质 量的 08 .%,脱 色时 间 6 0mi ,脱 色温度 为 8 n 0℃,
第2 9卷 第 4期
、, . N O. o129 4
新 乡学院学报 (自然科 学版 )
Jun l f n i gU iesyNa rl cec d in ora o xa nv r t( t a S i e io) Xi n i u n E t
棕榈油制生物柴油副产物甘油精制工艺研究

棕榈油制生物柴油副产物甘油精制工艺研究下载提示:该文档是本店铺精心编制而成的,希望大家下载后,能够帮助大家解决实际问题。
文档下载后可定制修改,请根据实际需要进行调整和使用,谢谢!本店铺为大家提供各种类型的实用资料,如教育随笔、日记赏析、句子摘抄、古诗大全、经典美文、话题作文、工作总结、词语解析、文案摘录、其他资料等等,想了解不同资料格式和写法,敬请关注!Download tips: This document is carefully compiled by this editor. I hope that after you download it, it can help you solve practical problems. The document can be customized and modified after downloading, please adjust and use it according to actual needs, thank you! In addition, this shop provides you with various types of practical materials, such as educational essays, diary appreciation, sentence excerpts, ancient poems, classic articles, topic composition, work summary, word parsing, copy excerpts, other materials and so on, want to know different data formats and writing methods, please pay attention!一、前言棕榈油制生物柴油是一种重要的可再生能源,在生产过程中会产生大量甘油副产物。
粗甘油提纯精甘油的工艺

粗甘油提纯精甘油的工艺
粗甘油提纯精甘油的工艺一般包括以下步骤:
1. 预处理:将粗甘油进行预处理,去除其中的杂质和不纯物质。
预处理的方法可以包括过滤、沉淀、离心等。
2. 酸化:加入酸性溶液(如硫酸或盐酸)与粗甘油进行酸化反应。
酸化的目的是将游离脂肪酸等酸性物质与甘油分离,并形成沉淀。
3. 分离:将酸化后的甘油溶液进行离心或过滤,分离出沉淀物。
这些沉淀物一般包括游离脂肪酸、杂质和其他不纯物质。
4. 中和:将分离后的甘油溶液进行中和处理,使其达到中性。
可以加入碱性溶液(如氢氧化钠或碳酸氢铵)与甘油进行反应,中和酸性物质。
5. 脱色:将中和后的甘油进行脱色处理,去除其中的色素。
脱色方法可以包括活性炭吸附、氧化剂氧化反应、继而与醇酸盐形成络合物、降解酸酱等。
6. 蒸馏:对脱色后的甘油进行蒸馏,以去除其中的挥发性物质和溶剂残留物。
7. 冷却:将蒸馏后的甘油进行冷却处理,使其凝结成为精甘油。
冷却可以采用自然冷却或冷却器冷却的方式。
8. 进一步提纯:精甘油可能还存在一些微量杂质,可以通过吸附、蒸发结晶等方法进一步提纯。
最终,经过以上工艺步骤,就可以得到纯净的精甘油。
不同厂家和需求的精甘油工艺细节可能会有所差异。
- 1、下载文档前请自行甄别文档内容的完整性,平台不提供额外的编辑、内容补充、找答案等附加服务。
- 2、"仅部分预览"的文档,不可在线预览部分如存在完整性等问题,可反馈申请退款(可完整预览的文档不适用该条件!)。
- 3、如文档侵犯您的权益,请联系客服反馈,我们会尽快为您处理(人工客服工作时间:9:00-18:30)。
生物柴油粗甘油精制技术
一、项目概述:
甘油法环氧氯丙烷项目需要用到大量的精甘油作为原料,而在生物柴油及油脂化工的生产过程中,会产生一定量的副产物粗甘油,所以上马一套甘油精制设备对粗甘油进行精制,用于合成环氧氯丙烷的配套或进入市场,不但能降低环氧氯丙烷的生产成本500-1000元,还能给企业带来良好的经济效益和社会效益。
纯净的甘油是一种无色有甜味的粘状液体,它是一种三元醇,具有三元醇类物质的一般化学性质,可以参与许多化学反应,生成各种衍生物,甘油由于具有许多重要的物理化学性质,成为重要的化工原料。
甘油在我国目前主要用于生产涂料、食品、医药、牙膏、玻璃纸、绝缘材料等。
工业用途
1、用作制造硝化甘油、醇酸树脂和环氧树脂。
2、在医学方面,用以制取各种制剂、溶剂、吸湿剂、防冻剂和甜味剂,配剂外用软膏或栓剂等。
用于甘油制取的硝化甘油。
3、在涂料工业中用以制取各种醇酸树脂、聚酯树脂、缩水甘油醚和环氧树脂等。
4、纺织和印染工业中用以制取润滑剂、吸湿剂、织物防皱缩处理剂、扩散剂和渗透剂。
5、在食品工业中用作甜味剂、烟草剂的吸湿剂和溶剂。
6、在造纸、化妆品、制革、照相、印刷、金属加工、电工材料和橡胶等工业中都有着广泛的用途。
7、并用作汽车和飞机燃料以及油田的防冻剂。
根据甘油的用途不同以及生产过程中消耗的不同,可有不同的精制方法。
一般情况下,甘油的精制可分为蒸馏与脱色精制法、精馏与脱色精制法(能源
消耗较高)、离子交换与排斥精制法。
各法比较有如下区别:
1、
蒸馏与脱色精制法:产生废渣少,投资省,制造费用低。
2、
精馏与脱色精制法:产生废渣多,投资高,制造费用高。
3、离子交换与排斥精制法:投资高,制造费用稍高,废水量大。
所以工业生产中多采用蒸馏与脱色精制法制得工业用甘油。
如果甘油作为特殊用途使用时,如食用、药用等,无论采用哪一种精制方法,其工艺过程中都要有离子交换工序才能保证甘油能符合质量标准要求。
二、精制工艺简介:
根据实际需求公司采用真空蒸馏与脱色精制法,蒸馏过程中高沸点组分留在蒸馏釜中,从粗甘油中分离出来。
而低沸点组分在气化后成为以甘油和水蒸气为主体的混合气体,利用甘油与水沸点的差异,通过三级部分冷凝后即可得到纯度较高的精甘油和甘油浓度较低的甜水(淡甘油)。
精甘油根据蒸馏工艺和操作条件的不同往往呈淡黄色甚至黄色,需要经过活性炭脱色处理,经过滤后才能得到成品精制甘油。
工艺流程简图:见图1
图1
主要设备;1-粗甘油储罐;2-泵;3-蒸馏预热器;4-蒸馏釜;5-旋风分离器;6-第一组冷凝器;7-第二组冷凝器;8-第三组冷凝器;9-粗甘油储罐粗甘油预热器蒸馏釜三级冷凝脱色釜压滤机
甜水回蒸精甘油
活性炭
受槽;10-打料泵;11-蒸馏甘油中间储罐;12-打料泵;13-脱色釜;14-打料泵;15-压滤机;16-精甘油储罐;17-真空系统、18-循环水泵;19-导热油炉。
三、工艺流程说明
含量约80%的粗甘油从贮罐放入粗甘油进料预热储槽,依靠压力差(真空)被吸入蒸馏锅。
在蒸馏残压-0.95-(-0.88)MPa和液相温度180~210℃条件下进行蒸馏。
直接水蒸汽量汽量根据蒸馏温度进行调节,不宜太大。
从蒸馏锅馏出的甘油蒸汽,经汽液分离器捕沫后在第一冷凝器部分冷凝。
其出口汽相温度约180℃左右,第一冷凝器用约140℃的饱和热水为冷媒,在汽包和第一冷凝器壳程之间进行自然循环,并部分汽化,得到的二次蒸汽可用于充汽与预热粗甘油。
循环热水的温度可用控制汽包内蒸汽的压力来实现,并由此间接地调节每一冷凝器出口甘油汽相的温度。
汽包的液位由补充水泵从热水罐送来,液面与泵联锁控制。
从第一冷凝器排出的未冷凝甘油蒸汽进入第二冷凝器,气相出口温度控制在140℃左右,使大部分甘油冷凝。
第二冷凝器用循环软水为冷媒,冷水温度可根据二冷出口甘油气相温度而定,一般为80~100℃。
二冷循环水的温度由一台换热器控制。
从二冷排出的未冷凝气体,含有少量甘油的水蒸汽,在第三冷凝器回收得到浓度稍低的甜水,回到蒸发工段或者复蒸馏。
三冷出口的气体温度约50~60℃。
第三冷凝器用循环冷却水为冷却介质。
循环冷却水的用量有一台调节阀控制。
蒸馏系统用水环泵抽真空。
水环泵的用水要求洁净低温(小于15度)。
从一冷器和二冷器冷凝的精甘油分别收集在甘油暂受器中。
然后泵送至脱色锅,加入适量活性碳脱色后,用泵送入压滤机过滤而得精甘油。
精甘油经分析室含量检测,根据检测结果进行含量指标调节,符合成品甘油质量要求后,进入精甘油罐,计量包装和交库。
三、技术改进:
针对生产过程中存在的问题,结合实际情况做了一些有利的改进,实际运行来看,效果明显,不仅有利于减少工人的操作量,而且对于提高甘油的收率,降低制造成本有明显的效果。
1、因精甘油接收罐较小,出料操作频繁,需不断地破除接收罐的真空,同时还会对蒸馏系统造成影响。
针对这种情况,最初做了各种方案:有改自控系统出料、加大接收罐、真空出料。
通过对比了解最终确定投入少、且有效减少操作量的真空出料方案,改造后,除最初阶段回甜水需人工操作外,正常蒸馏时可自动出料,无需人工频繁操作。
2、粗甘油的预处理,粗甘油因含有大量的杂质:如油酸,脂类、皂化物、盐等,进蒸馏釜之前要预处理,人工捞取油脂等漂浮物,气味臭且很难捞干净,会对蒸馏釜造成影响,收率降低,能耗提高。
甘油预热地池也很容易形成盐类堆积,造成换热效果差,进料堵,还要停车清盐作业。
通过了解预处理方式,确定采取机械式分离方案,即使通过特殊的机械,对粗甘油进行预处理,不仅去除杂质效果较好,还大大减少人工操作。
3、甜水回收甘油,在生产中发现,直接往蒸馏釜回甜水会造成蒸馏出料明显减小或停顿,严重影响产量提高。
经查阅相关资料,采用闪蒸脱水方式对甜水进行单独处理,脱水效果较理想,使得甜水中的甘油得到有效的回收。
4、废渣的处理:粗甘油蒸馏两天左右,随着蒸馏釜中的高沸物增多,温度升高,也越来越难蒸。
就必须进行排渣处理,每次排出的稠渣约有十多吨。
因含有盐分等很难焚烧处理,目前有收购费油渣的公司,但对油渣要求要尽量无水无盐。
所以结合一些资料,对费油渣做初步的处理,使的盐分分离出来,有机物成分出售。
总结:通过对粗甘油精炼生产过程中问题的了解,不断改进优化,节约人工成本,降低消耗,废物回收利用,使精甘油项目市场竞争力不断提高,为行业的发展做出了贡献,取得了较好的经济效益和社会效益。